check engine JEEP CJ 1953 User Guide
[x] Cancel search | Manufacturer: JEEP, Model Year: 1953, Model line: CJ, Model: JEEP CJ 1953Pages: 376, PDF Size: 19.96 MB
Page 19 of 376
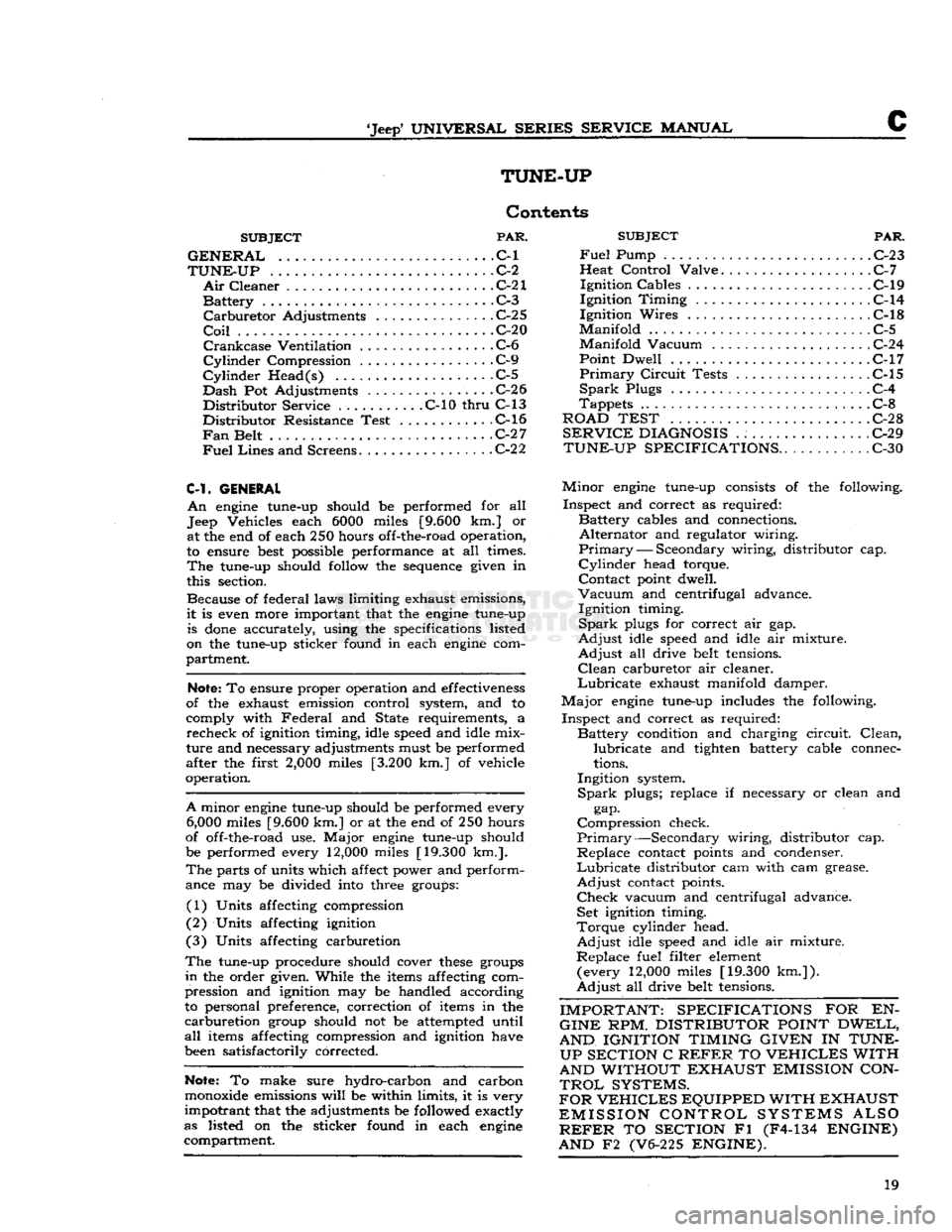
Jeep*
UNIVERSAL SERIES SERVICE
MANUAL
c
TUNE-UP
Contents
SUBJECT
PAR.
GENERAL
C-l
TUNE-UP
.C-2
Air
Cleaner
C-21
Battery
. C-3
Carburetor
Adjustments
C-2 5
Coil
C-20
Crankcase
Ventilation C-6
Cylinder
Compression C-9
Cylinder
Head(s) .C-5
Dash
Pot Adjustments .C-26
Distributor
Service C-10
thru
C-13
Distributor
Resistance Test C-l6
Fan
Belt
C-2 7
Fuel
Lines
and Screens
C-2
2
C-l.
GENERAL
An
engine tune-up should be performed for all
Jeep Vehicles each 6000 miles [9.600 km.] or at the end of each 250 hours off-the-road operation,
to ensure best possible performance at all times.
The
tune-up should follow the sequence given in
this section.
Because of federal laws limiting exhaust emissions,
it
is even more important that the engine tune-up is
done
accurately, using the specifications listed
on the tune-up sticker found in each engine com
partment.
Note;
To ensure proper operation and effectiveness
of the exhaust emission control system, and to
comply with
Federal
and State requirements, a
recheck
of ignition timing, idle speed and idle mix
ture
and necessary adjustments must be performed
after the first
2,000
miles [3.200 km.] of vehicle
operation.
A
minor engine tune-up should be performed every
6,000
miles [9.600 km.] or at the end of 250 hours
of off-the-road use.
Major
engine tune-up should
be performed every 12,000 miles [19.300 km.].
The
parts of units which affect power and perform
ance may be divided into three groups:
(1) Units affecting compression
(2) Units affecting ignition
(3) Units affecting carburetion
The
tune-up procedure should cover
these
groups
in
the order given. While the items affecting com
pression and ignition may be handled according
to personal preference, correction of items in the
carburetion
group should not be attempted until
all
items affecting compression and ignition have
been satisfactorily corrected.
Note:
To make sure hydro-carbon and carbon
monoxide emissions
will
be within limits, it is very
impotrant
that the adjustments be followed exactly
as listed on the sticker found in each engine compartment.
SUBJECT
PAR.
Fuel
Pump . . C-23
Heat
Control
Valve C-7
Ignition
Cables C-19
Ignition
Timing
. C-14
Ignition
Wires C-l8
Manifold
C-5
Manifold
Vacuum C-24
Point
Dwell C-17
Primary
Circuit
Tests
.................
C-15
Spark
Plugs C-4
Tappets
C-8
ROAD TEST C-2
8
SERVICE
DIAGNOSIS
. : C-29
TUNE-UP SPECIFICATIONS..
C-30
Minor
engine tune-up consists of the following.
Inspect
and correct as required:
Battery
cables and connections.
Alternator
and regulator wiring.
Primary
— Secondary wiring, distributor cap.
Cylinder
head torque.
Contact
point dwell.
Vacuum
and centrifugal advance.
Ignition
timing.
Spark
plugs for correct air gap.
Adjust
idle speed and idle air mixture.
Adjust
all drive belt tensions.
Clean
carburetor air cleaner.
Lubricate
exhaust manifold damper.
Major
engine tune-up includes the following.
Inspect
and correct as required:
Battery
condition and charging
circuit.
Clean,
lubricate
and tighten battery cable connec
tions.
Ingition
system.
Spark
plugs; replace if necessary or clean and gap.
Compression
check.
Primary—Secondary
wiring, distributor cap.
Replace
contact points and condenser.
Lubricate
distributor cam with cam grease.
Adjust
contact points.
Check
vacuum and centrifugal advance. Set ignition timing.
Torque
cylinder head.
Adjust
idle speed and idle air mixture.
Replace
fuel filter element (every 12,000 miles [19.300
km.]).
Adjust
all drive belt tensions.
IMPORTANT: SPECIFICATIONS
FOR EN-
GINE
RPM.
DISTRIBUTOR POINT DWELL,
AND IGNITION TIMING GIVEN
IN
TUNE- UP SECTION
C
REFER
TO
VEHICLES
WITH
AND WITHOUT EXHAUST EMISSION CON
TROL
SYSTEMS.
FOR
VEHICLES
EQUIPPED WITH EXHAUST
EMISSION CONTROL SYSTEMS ALSO
REFER
TO
SECTION
Fl (F4-134
ENGINE)
AND
F2 (V6-225
ENGINE).
19
Page 20 of 376
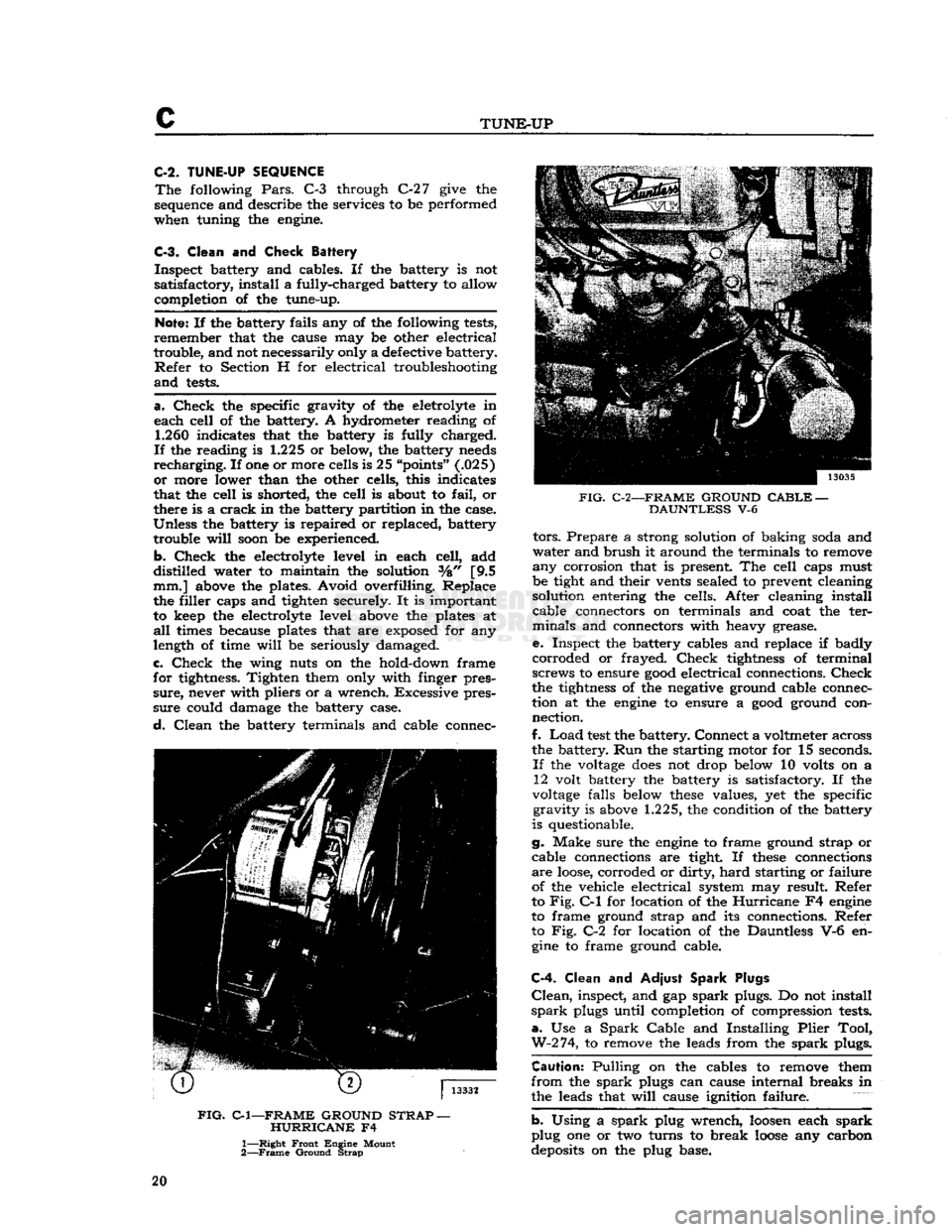
c
TUNE-UP
C-2.
TUNE-UP SEQUENCE
The
following
Pars.
C-3 through
C-2
7
give the
sequence and describe the services to be performed
when tuning the engine.
C-3.
Clean
and
Check
Battery
Inspect
battery and cables. If the battery is not
satisfactory, install a fully-charged battery to allow
completion of the tune-up.
Note: If the battery fails any of the following tests,
remember that the cause may be other electrical
trouble, and not necessarily only a defective battery.
Refer
to Section H for electrical troubleshooting
and
tests.
a.
Check
the specific gravity of the eletrolyte in
each cell of the battery. A hydrometer reading of 1.260 indicates that the battery is fully charged.
If
the reading is 1.225 or below, the battery
needs
recharging.
If one or more cells is 25 "points" (.025)
or
more lower than the other cells, this indicates
that the cell is shorted, the cell is about to
fail,
or
there is a
crack
in the battery partition in the case.
Unless the battery is repaired or replaced, battery trouble
will
soon be experienced.
b.
Check
the electrolyte level in each cell, add
distilled
water to maintain the solution %" [9.5
mm.] above the plates. Avoid overfilling. Replace
the filler caps and tighten securely. It is important
to keep the electrolyte level above the plates at
all
times because plates that are exposed for any
length of time
will
be seriously damaged.
c.
Check
the wing nuts on the hold-down frame
for tightness. Tighten them only with finger pres
sure,
never with pliers or a wrench. Excessive pres
sure
could damage the battery case.
d.
Clean
the battery terminals and cable connec-
FIG.
C-l—FRAME
GROUND
STRAP
—
HURRICANE
F4
1—
Right
Front
Engine Mount
2—
Frame
Ground
Strap
DAUNTLESS
V-6
tors.
Prepare a strong solution of baking soda and
water
and brush it around the terminals to remove
any
corrosion that is present. The cell caps must
be tight and their vents sealed to prevent cleaning
solution entering the cells. After cleaning install
cable connectors on terminals and coat the ter
minals
and connectors with heavy grease.
e. Inspect the battery cables and replace if badly
corroded
or frayed.
Check
tightness of terminal
screws to ensure
good
electrical connections.
Check
the tightness of the negative ground cable connec tion at the engine to ensure a
good
ground con nection.
f.
Load
test
the battery. Connect a voltmeter across the battery. Run the starting motor for 15 seconds.
If
the voltage
does
not drop below 10 volts on a 12 volt battery the battery is satisfactory. If the
voltage falls below
these
values, yet the specific
gravity
is above
1.225,
the condition of the battery
is questionable.
g.
Make sure the engine to frame ground strap or
cable connections are tight. If
these
connections
are
loose,
corroded or dirty,
hard
starting or failure
of the vehicle electrical system may result. Refer
to
Fig.
C-l
for location of the
Hurricane
F4 engine
to frame ground strap and its connections. Refer to Fig. C-2 for location of the Dauntless V-6 en gine to frame ground cable.
C-4.
Clean and
Adjust
Spark Plugs
Clean,
inspect, and gap
spark
plugs. Do not install
spark
plugs until completion of compression tests.
a.
Use a
Spark
Cable
and Installing
Plier
Tool,
W-2
74,
to remove the leads from the
spark
plugs.
Caution:
Pulling on the cables to remove them
from
the
spark
plugs can cause internal breaks in
the leads that
will
cause ignition failure.
b.
Using a
spark
plug wrench, loosen each
spark
plug one or two turns to break
loose
any carbon
deposits on the plug base. 20
Page 21 of 376
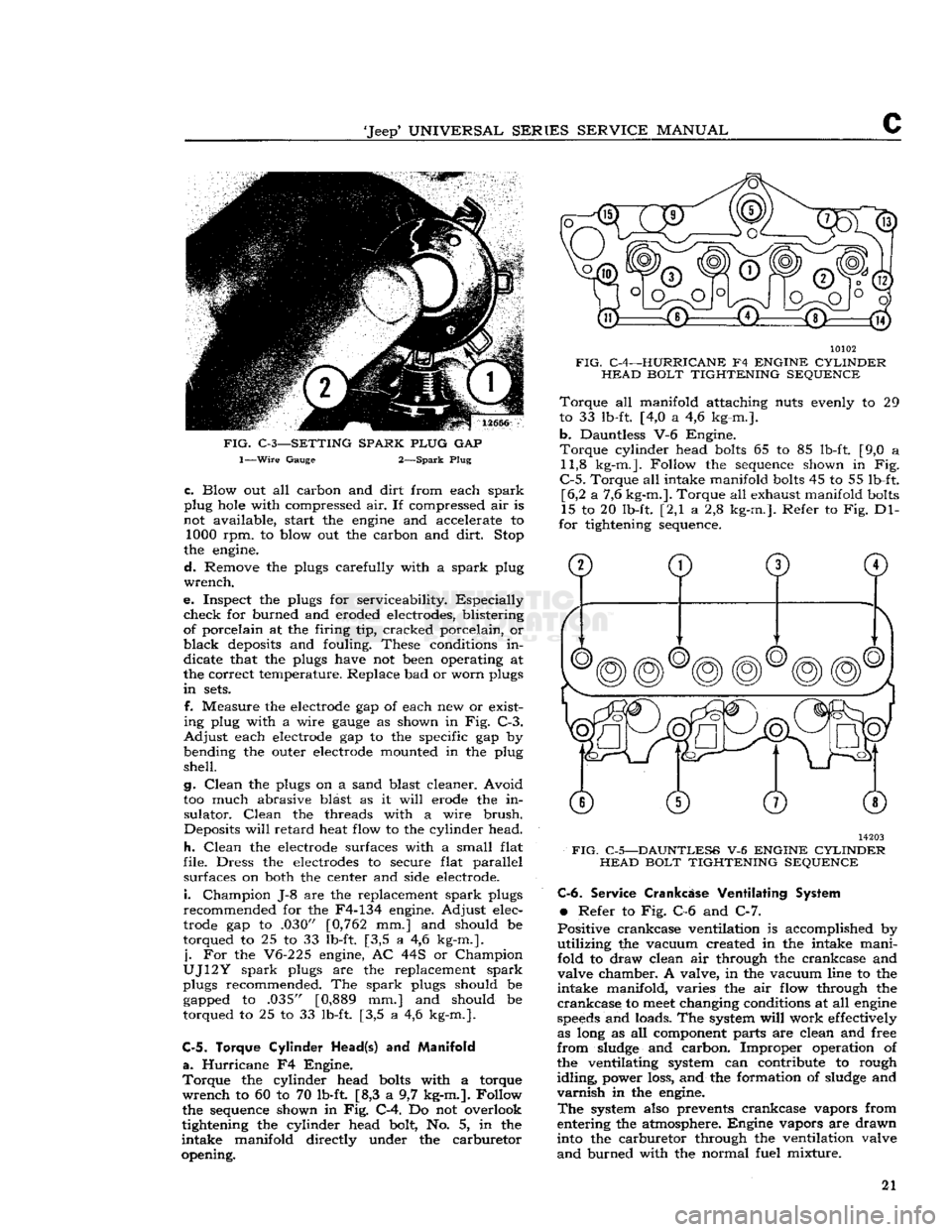
'Jeep'
UNIVERSAL SERIES SERVICE
MANUAL
FIG.
C-3—SETTING SPARK PLUG
GAP
1—Wire
Gauge 2—Spark Plug
c.
Blow out all carbon and
dirt
from each
spark
plug hole with compressed air. If compressed air is
not available, start the engine and accelerate to 1000 rpm. to blow out the carbon and
dirt.
Stop
the engine.
d.
Remove the plugs carefully with a
spark
plug
wrench.
e. Inspect the plugs for serviceability. Especially
check
for burned and eroded electrodes, blistering
of porcelain at the firing tip, cracked porcelain, or
black
deposits and fouling. These conditions in
dicate that the plugs have not been operating at
the correct temperature. Replace bad or worn plugs
in
sets.
f. Measure the electrode gap of each new or exist
ing plug with a wire
gauge
as shown in Fig. C-3.
Adjust
each electrode gap to the specific gap by
bending the outer electrode mounted in the plug
shell.
g.
Clean
the plugs on a sand blast cleaner. Avoid
too much abrasive blast as it
will
erode the in
sulator.
Clean
the threads with a wire
brush.
Deposits
will
retard
heat flow to the cylinder head.
h.
Clean
the electrode surfaces with a small flat
file. Dress the electrodes to secure flat parallel surfaces on both the center and side electrode.
i.
Champion J-8 are the replacement
spark
plugs
recommended for the F4-134 engine. Adjust elec
trode gap to .030" [0,762 mm.] and should be
torqued to 25 to 33 lb-ft. [3,5 a 4,6 kg-m.].
j.
For the V6-225 engine, AC 44S or Champion
UJ12Y
spark
plugs are the replacement
spark
plugs recommended. The
spark
plugs should be gapped to .035" [0,889 mm.] and should be
torqued to 25 to 33 lb-ft. [3,5 a 4,6 kg-m.].
C-5. Torque Cylinder
Head(s)
and
Manifold
a.
Hurricane
F4 Engine.
Torque
the cylinder head bolts with a torque
wrench
to 60 to 70 lb-ft [8,3 a 9,7 kg-m.]. Follow
the sequence shown in Fig. C-4. Do not overlook
tightening the cylinder head bolt, No. 5, in the
intake
manifold directly under the carburetor
opening. 10102
FIG.
C-4—HURRICANE
F4
ENGINE CYLINDER HEAD BOLT TIGHTENING SEQUENCE
Torque
all manifold attaching nuts evenly to 29
to 33 lb-ft. [4,0 a 4,6 kg-m.].
b.
Dauntless V-6 Engine.
Torque
cylinder head bolts 65 to 85 lb-ft. [9,0 a 11,8 kg-m.]. Follow the sequence shown in Fig.
C-5.
Torque all intake manifold bolts 45 to 55 lb-ft. [6,2 a 7,6 kg-m.]. Torque all exhaust manifold bolts
15 to 20 lb-ft. [2,1 a 2,8 kg-m.]. Refer to Fig. Dl-
for tightening sequence. 14203
FIG.
C-5—DAUNTLESS
V-6
ENGINE CYLINDER HEAD BOLT TIGHTENING SEQUENCE C-6.
Service
Crankcase
Ventilating System
•
Refer to Fig. C-6 and C-7.
Positive crankcase ventilation is accomplished by
utilizing
the vacuum created in the intake mani
fold to draw clean air through the crankcase and
valve chamber. A valve, in the vacuum line to the
intake
manifold, varies the air flow through the
crankcase
to
meet
changing conditions at all engine
speeds
and loads. The system
will
work effectively as long as all component parts are clean and free
from
sludge and carbon. Improper operation of the ventilating system can contribute to rough
idling,
power loss, and the formation of sludge and
varnish
in the engine.
The
system also prevents crankcase vapors from
entering the atmosphere. Engine vapors are drawn
into the carburetor through the ventilation valve
and
burned with the normal fuel mixture. 21
Page 23 of 376
![JEEP CJ 1953 User Guide
Jeep
UNIVERSAL SERIES SERVICE
MANUAL
C The
valve, connecting pipes, and
hoses
must be
inspected and serviced at intervals of
2,000
[3.200
km.],
6,000
[9.600 km.] and 12,000 [19.300 km JEEP CJ 1953 User Guide
Jeep
UNIVERSAL SERIES SERVICE
MANUAL
C The
valve, connecting pipes, and
hoses
must be
inspected and serviced at intervals of
2,000
[3.200
km.],
6,000
[9.600 km.] and 12,000 [19.300 km](/img/16/57040/w960_57040-22.png)
'Jeep'
UNIVERSAL SERIES SERVICE
MANUAL
C The
valve, connecting pipes, and
hoses
must be
inspected and serviced at intervals of
2,000
[3.200
km.],
6,000
[9.600 km.] and 12,000 [19.300 km.]
miles, continuing each
6,000
miles [9.600 km.] of
vehicle operation thereafter. It may be necessary to inspect and clean the system more frequently
under
adverse driving or weather conditions.
Replace
the valve each 12,000 miles [19.300 km.],
a.
Dauntless V-6 Engine.
Filtered
air from the carburetor air cleaner enters the engine crankcase through a hose. The ventilation valve is mounted on the right cylinder bank
rocker
arm cover (Fig. C-7) and is connected by a
hose
to a fitting at the base of the carburetor at the
intake
manifold opening. The valve varies the air
flow through the crankcase to
meet
changing condi
tions at all engine
speeds
and loads. To check the operation of the system, remove the valve with the
hose
attached from the rocker arm cover.
With
the engine running at fast idle, a vacuum must be felt
at the open end of the ventilation valve. If no
vacuum
is present, the valve and
hose
should be
inspected and cause of the restriction determined.
To
check the valve disconnect it from the air
13334
FIG.
C-9—POSITIVE CRANKCASE VENTILATION SYSTEM
— F4
ENGINE (TYPICAL)
1—Valve
Open 2—Valve Closed
23
Page 24 of 376
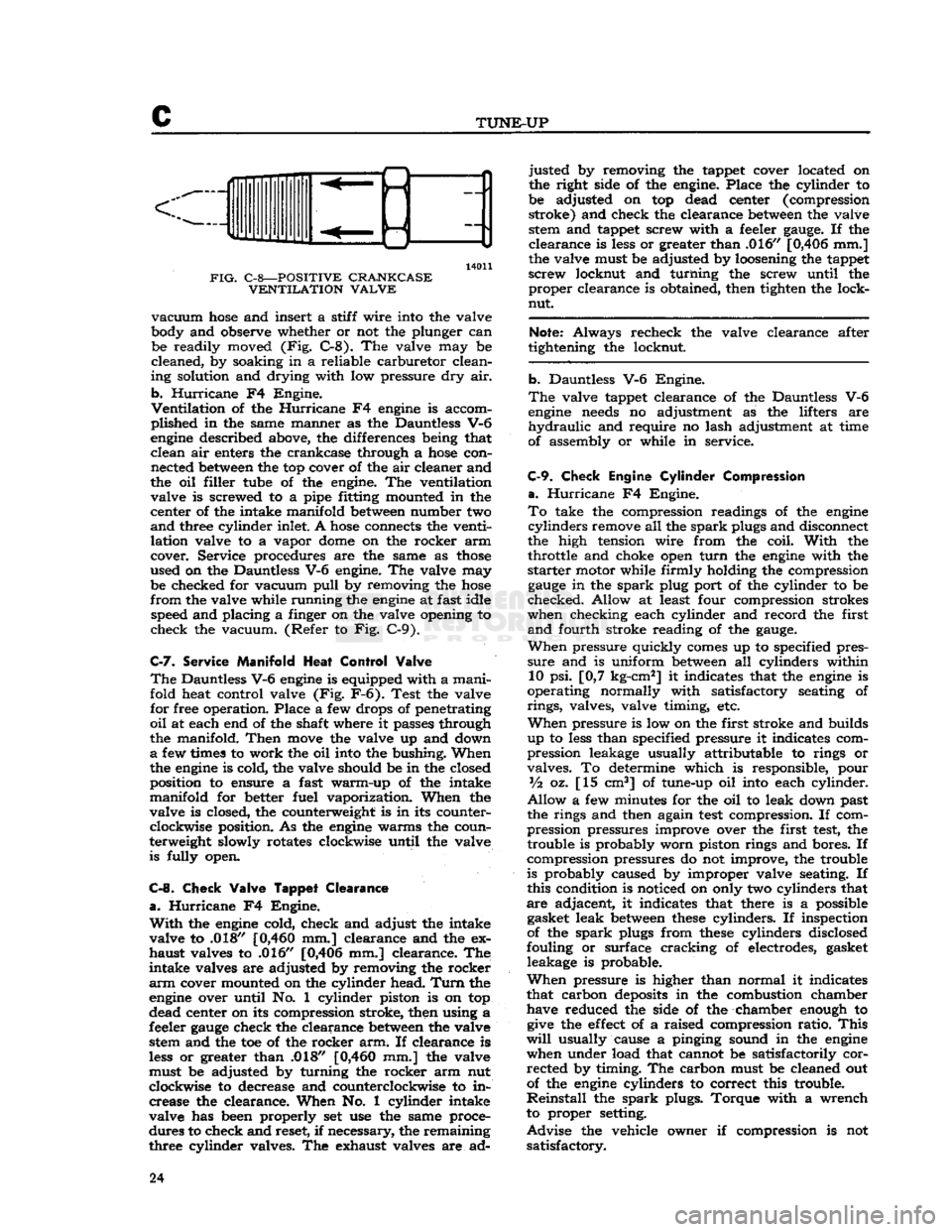
c
TUNE-UP
14011
FIG.
C-8—POSITIVE CRANKCASE VENTILATION VALVE
vacuum
hose
and insert a stiff wire into the valve
body and observe whether or not the plunger can be readily moved (Fig. C-8). The valve may be
cleaned, by soaking in a reliable carburetor clean
ing solution and drying with low pressure dry air.
b.
Hurricane
F4 Engine.
Ventilation
of the
Hurricane
F4
engine
is accom
plished in the same manner as the Dauntless V-6
engine
described above, the differences being that clean air enters the crankcase through a
hose
con nected
between
the top cover of the air cleaner and
the oil filler tube of the engine. The ventilation valve is screwed to a pipe fitting mounted in the
center of the intake manifold
between
number two
and
three cylinder inlet. A
hose
connects the venti
lation valve to a vapor
dome
on the rocker arm
cover. Service procedures are the same as
those
used on the Dauntless V-6 engine. The valve may be checked for vacuum
pull
by removing the
hose
from
the valve while running the
engine
at fast idle speed and placing a finger on the valve opening to
check the vacuum. (Refer to Fig. C-9).
C-7.
Service
Manifold
Heat
Control
Valve
The
Dauntless V-6
engine
is equipped with a manifold heat control valve (Fig. F-6). Test the valve
for free operation. Place a few drops of penetrating
oil
at each end of the shaft where it passes through
the manifold.
Then
move
the valve up and down
a
few times to work the oil into the bushing. When
the
engine
is cold, the valve should be in the closed
position to ensure a fast warm-up of the intake
manifold for better fuel vaporization. When the
valve is closed, the counterweight is in its counter clockwise position. As the
engine
warms the coun
terweight slowly rotates clockwise until the valve is fully open.
C-8.
Check
Valve
Tappet
Clearance
a.
Hurricane
F4 Engine.
With
the
engine
cold, check and adjust the intake
valve to .018"
[0,460
mm.] clearance and the ex
haust valves to .016" [0,406 mm.] clearance. The
intake valves are adjusted by removing the rocker
arm
cover mounted on the cylinder head.
Turn
the
engine
over until No. 1 cylinder piston is on top
dead center on its compression stroke, then using a
feeler
gauge
check the clearance
between
the valve stem and the toe of the rocker arm. If clearance is
less
or greater than .018"
[0,460
mm.] the valve
must be adjusted by turning the rocker arm nut
clockwise to decrease and counterclockwise to in crease the clearance. When No. 1 cylinder intake
valve has been properly set use the same proce
dures to check and reset, if necessary, the remaining
three cylinder valves. The exhaust valves are ad justed by removing the tappet cover located on
the right side of the engine. Place the cylinder to
be adjusted on top dead center (compression stroke) and check the clearance
between
the valve stem and tappet screw with a feeler
gauge.
If the
clearance is
less
or greater than .016" [0,406 mm.]
the valve must be adjusted by loosening the tappet
screw locknut and turning the screw until the proper clearance is obtained, then tighten the lock-
nut.
Note:
Always recheck the valve clearance after
tightening the locknut.
b. Dauntless V-6 Engine.
The
valve tappet clearance of the Dauntless V-6
engine
needs
no adjustment as the lifters are
hydraulic
and require no lash adjustment at time
of assembly or while in service.
C-9.
Check
Engine
Cylinder
Compression
a.
Hurricane
F4 Engine.
To
take the compression readings of the
engine
cylinders
remove all the
spark
plugs and disconnect
the high tension wire from the coil.
With
the throttle and choke open
turn
the
engine
with the
starter
motor while firmly holding the compression
gauge
in the
spark
plug port of the cylinder to be
checked. Allow at least four compression strokes
when checking each cylinder and record the first
and
fourth stroke reading of the
gauge.
When
pressure quickly
comes
up to specified pres
sure
and is uniform
between
all cylinders within 10 psi. [0,7 kg-cm2] it indicates that the
engine
is
operating normally with satisfactory seating of
rings,
valves, valve timing, etc.
When
pressure is low on the first stroke and builds
up to
less
than specified pressure it indicates com
pression leakage usually attributable to rings or
valves. To determine which is responsible, pour
Vz
oz. [15 cm3] of tune-up oil into each cylinder.
Allow
a few minutes for the oil to leak down past
the rings and then again
test
compression. If com
pression pressures improve over the first
test,
the trouble is probably worn piston rings and bores. If
compression pressures do not improve, the trouble
is probably caused by improper valve seating. If
this condition is noticed on only two cylinders that
are adjacent, it indicates that there is a possible gasket leak
between
these
cylinders. If inspection
of the
spark
plugs from
these
cylinders disclosed
fouling or surface cracking of electrodes, gasket leakage is probable.
When
pressure is higher than normal it indicates
that carbon
deposits
in the combustion chamber have reduced the side of the chamber enough to
give
the
effect
of a raised compression ratio.
This
will
usually cause a pinging sound in the
engine
when under load that cannot be satisfactorily corrected by timing. The carbon must be cleaned out
of the
engine
cylinders to correct this trouble.
Reinstall
the
spark
plugs. Torque with a wrench
to proper setting.
Advise
the vehicle owner if compression is not satisfactory. 24
Page 25 of 376
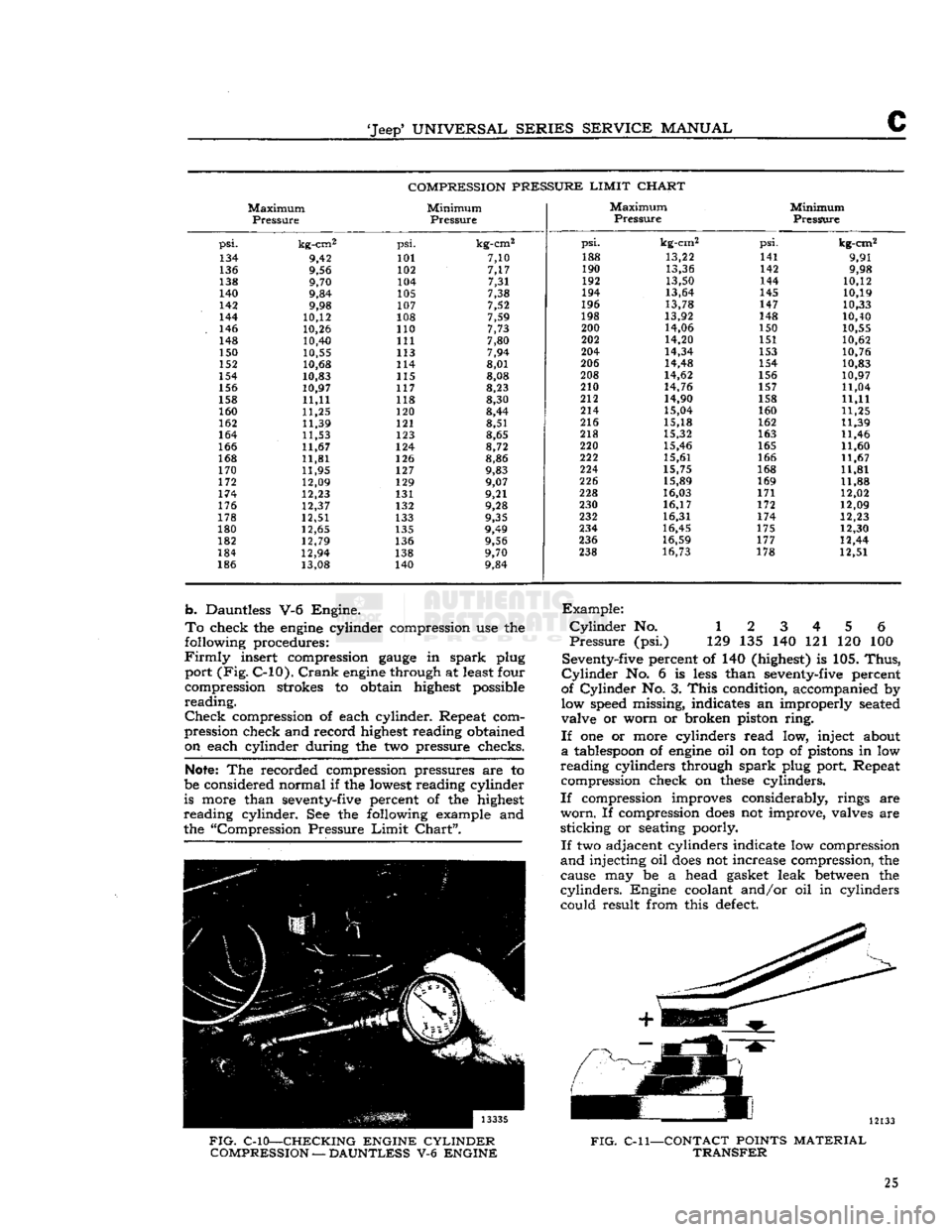
'Jeep*
UNIVERSAL SERIES SERVICE
MANUAL
COMPRESSION PRESSURE LIMIT CHART
Maximum
Pressure
Minimum
Pressure
Maximum
Pressure
Minimum
Pressure
psi.
kg-cm2
psi.
kg-cm2
psi.
kg-cm2
psi.
kg-cm2
134 9,42 101 7,10
188
13,22 141
9,91
136 9,56 102 7,17 190
13,36 142
9,98
138 9,70 104 7,31 192
13,50 144 10,12
140 9,84 105 7,38 194
13,64 145
10,19
142 9,98 107 7,52 196
13,78 147 10,33
144 10,12 108 7,59 198
13,92
148 10,40
146 10,26 110 7,73 200
14,06 150 10,55
148 10,40 111 7,80
202
14,20 151
10,62
150 10,55 113 7,94 204
14,34 153
10,76
152 10,68 114 8,01 206
14,48 154 10,83
154 10,83
115 8,08 208
14,62 156
10,97
156 10,97 117 8,23
210
14,76 157 11,04
158 11,11 118 8,30 212
14,90
158 11,11
160 11,25 120
8,44 214
15,04 160
11,25
162 11,39 121 8,51 216
15,18 162 11,39
164 11,53
123 8,65 218
15,32 163
11,46
166 11,67 124 8,72 220
15,46 165 11,60
168 11,81 126 8,86 222
15,61 166
11,67
170 11,95 127 9,83 224
15,75 168 11,81
172 12,09 129 9,07 226
15,89 169
11,88
174 12,23 131 9,21 228
16,03 171 12,02
176 12,37 132 9,28 230
16,17 172
12,09
178 12,51 133 9,35 232
16,31
174 12,23
180 12,65 135 9,49
234
16,45 175 12,30
182 12,79 136 9,56 236
16,59 177 12,44
184 12,94 138 9,70
238
16,73 178 12,51
186 13,08 140 9,84
b.
Dauntless V-6 Engine.
To
check the
engine
cylinder compression use the
following procedures:
Firmly
insert compression
gauge
in
spark
plug
port
(Fig.
C-10).
Crank
engine
through at least four
compression strokes to obtain highest possible
reading.
Check
compression of each cylinder. Repeat com
pression check and record highest reading obtained on each cylinder during the two pressure checks.
Note:
The recorded compression pressures are to
be considered normal if the lowest reading cylinder
is more than seventy-five percent of the highest
reading
cylinder. See the following example and
the "Compression Pressure
Limit
Chart".
Example:
Cylinder
No. 1 2 3 4 5 6
Pressure
(psi.) 129 135 140 121 120 100
Seventy-five percent of 140 (highest) is 105.
Thus,
Cylinder
No. 6 is
less
than seventy-five percent
of
Cylinder
No. 3.
This
condition, accompanied by low speed missing, indicates an improperly seated
valve or worn or broken piston
ring.
If
one or more cylinders read low, inject about
a
tablespoon of
engine
oil on top of pistons in low
reading
cylinders through
spark
plug port. Repeat compression check on
these
cylinders.
If
compression improves considerably, rings are
worn.
If compression
does
not improve, valves are
sticking
or seating poorly.
If
two adjacent cylinders indicate low compression
and
injecting oil
does
not increase compression, the
cause may be a head gasket leak
between
the
cylinders.
Engine coolant and/or oil in cylinders could result from this
defect.
FIG.
C-10—CHECKING ENGINE CYLINDER
COMPRESSION
—
DAUNTLESS
V-6
ENGINE
FIG.
C-l
1—CONTACT
POINTS
MATERIAL
TRANSFER
25
Page 26 of 376
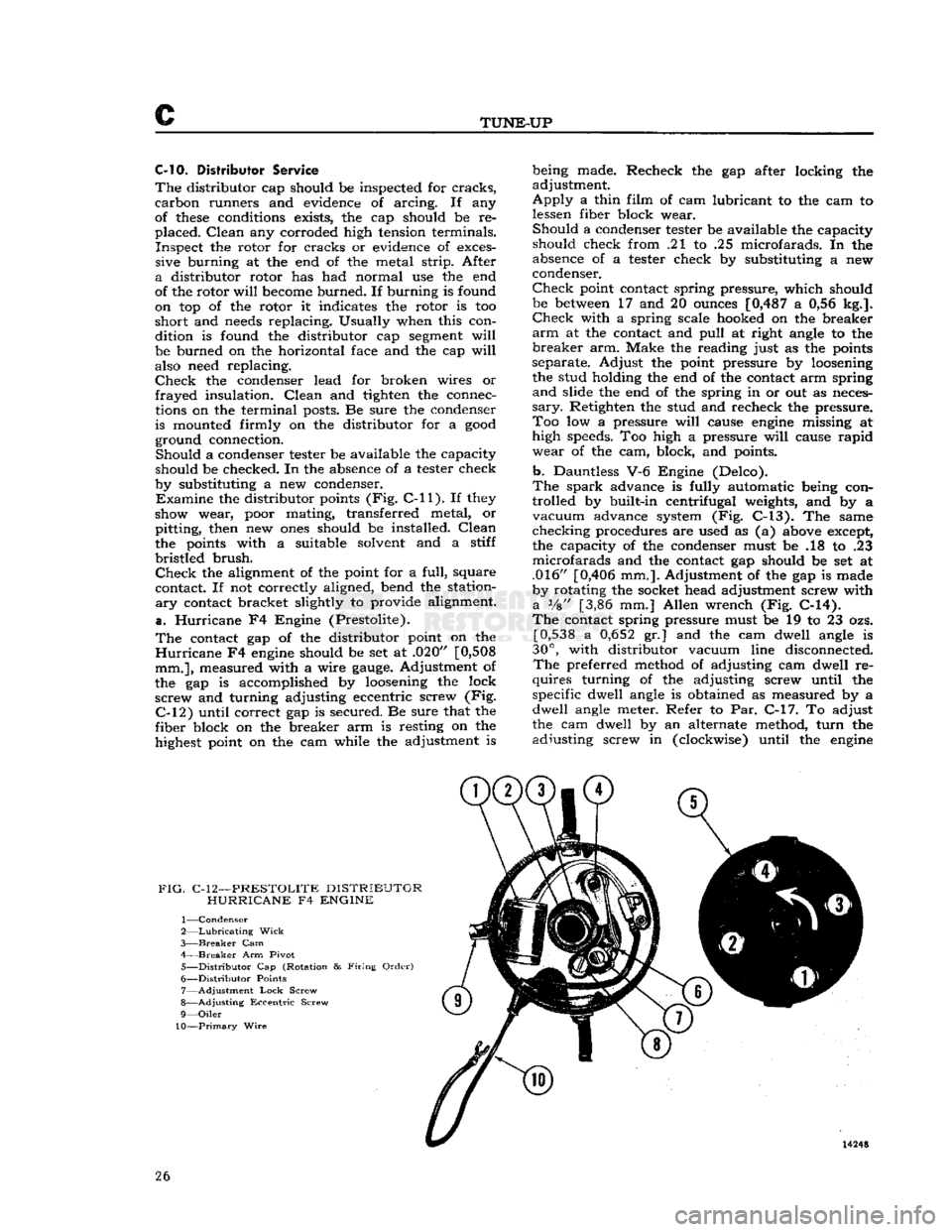
c
TUNE-UP
C-10.
Distributor
Service
The
distributor cap should be inspected for
cracks,
carbon runners and evidence of arcing. If any
of
these
conditions exists, the cap should be re
placed.
Clean
any corroded high tension terminals. Inspect the rotor for cracks or evidence of
exces
sive burning at the end of the metal strip. After
a
distributor rotor has had normal use the end
of the rotor
will
become
burned. If burning is found
on top of the rotor it indicates the rotor is too
short and
needs
replacing. Usually when this con
dition is found the distributor cap
segment
will
be burned on the horizontal face and the cap
will
also need replacing.
Check
the condenser lead for broken wires or
frayed
insulation.
Clean
and tighten the connec
tions
on the terminal
posts.
Be sure the condenser
is mounted firmly on the distributor for a
good
ground connection. Should a condenser tester be available the capacity
should be checked. In the absence of a tester check
by substituting a new condenser.
Examine
the distributor
points
(Fig.
C-ll).
If
they
show wear, poor mating, transferred metal, or pitting, then new
ones
should be installed.
Clean
the
points
with a suitable solvent and a stiff
bristled brush.
Check
the alignment of the point for a
full,
square
contact. If not correctly aligned, bend the station
ary
contact bracket slightly to provide alignment,
a.
Hurricane F4 Engine (Prestolite).
The
contact gap of the distributor point on the
Hurricane
F4
engine
should be set at .020"
[0,508
mm.],
measured with a wire
gauge.
Adjustment of
the gap is accomplished by
loosening
the lock screw and turning adjusting eccentric screw (Fig.
C-12)
until correct gap is secured. Be sure that the
fiber block on the breaker arm is resting on the
highest point on the cam while the adjustment is being made. Recheck the gap after locking the
adjustment.
Apply
a thin film of cam lubricant to the cam to
lessen fiber block wear. Should a condenser tester be available the capacity
should check from .21 to .25 microfarads. In the
absence of a tester check by substituting a new
condenser.
Check
point contact spring pressure, which should
be
between
17 and 20
ounces
[0,487
a 0,56 kg.].
Check
with a spring scale hooked on the breaker
arm
at the contact and pull at right
angle
to the
breaker
arm. Make the reading just as the
points
separate. Adjust the point pressure by
loosening
the stud holding the end of the contact arm spring
and
slide the end of the spring in or out as neces
sary.
Retighten the stud and recheck the pressure. Too low a pressure
will
cause
engine
missing at
high
speeds.
Too high a pressure
will
cause rapid wear of the cam, block, and points.
b. Dauntless V-6 Engine (Delco).
The
spark advance is fully automatic being con
trolled by built-in centrifugal weights, and by a vacuum advance system (Fig.
C-13).
The same
checking procedures are used as (a)
above
except,
the capacity of the condenser must be .18 to .23 microfarads and the contact gap should be set at
.016"
[0,406
mm.]. Adjustment of the gap is made
by rotating the socket head adjustment screw with
a
Vs" [3,86 mm.] Allen wrench (Fig.
C-14).
The
contact spring pressure must be 19 to 23 ozs.
[0,538
a
0,652
gr.] and the cam dwell
angle
is
30°,
with distributor vacuum line disconnected.
The
preferred method of adjusting cam dwell re
quires turning of the adjusting screw until the specific dwell
angle
is obtained as measured by a
dwell
angle
meter. Refer to Par. C-l7. To adjust
the cam dwell by an alternate method, turn the adjusting screw in (clockwise) until the
engine
FIG.
C-12—PRESTOLITE DISTRIBUTOR HURRICANE F4 ENGINE
1— Condenser
2—
Lubricating
Wick
3—
Breaker
Cam
4—
Breaker
Arm Pivot 5—
Distributor
Cap (Rotation &
Firing
Order)
6—
Distributor
Points 7— Adjustment
Lock
Screw
8—
Adjusting
Eccentric
Screw
9—
Oiler
10—Primary
Wire
26
Page 27 of 376
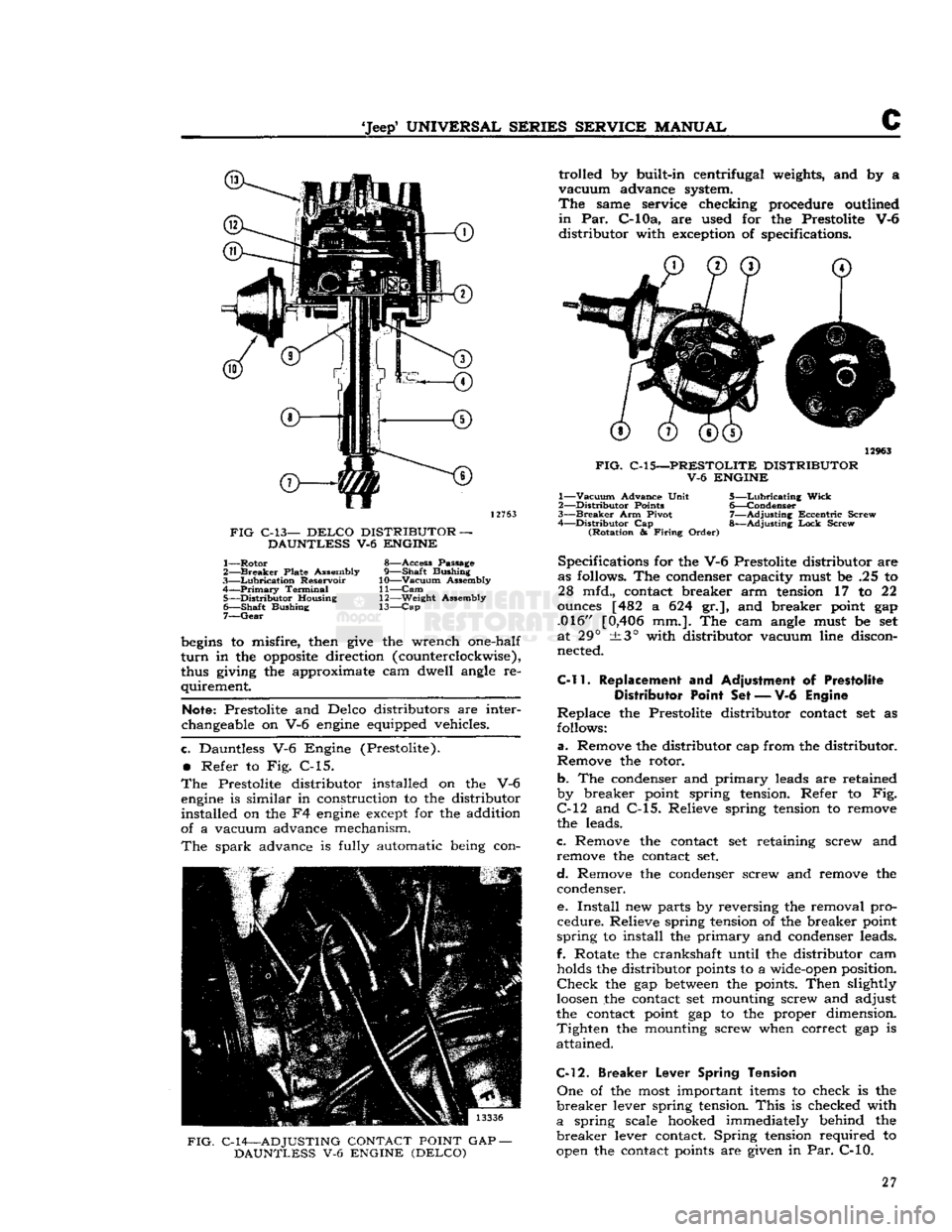
'Jeep*
UNIVERSAL
SERIES SERVICE
MANUAL
C
12763
FIG
C-13—
DELCO
DISTRIBUTOR —
DAUNTLESS V-6 ENGINE
1—
Rotor
8—Access Passage
2—
Breaker
Plate Assembly 9—Shaft Bushing
3—
Lubrication
Reservoir 10—Vacuum Assembly
4—
Primary
Terminal
11—Cam
5—
Distributor
Housing 12—Weight Assembly 6—
Shaft
Bushing 13—Cap
7—
Gear
begins
to misfire, then
give
the wrench one-half
turn
in the
opposite
direction (counterclockwise),
thus giving the approximate cam dwell angle re
quirement
Note:
Prestolite and Delco distributors are inter
changeable on V-6
engine
equipped vehicles.
c.
Dauntless V-6 Engine (Prestolite).
•
Refer to Fig. C-l5.
The
Prestolite distributor installed on the V-6
engine
is similar in construction to the distributor
installed on the F4
engine
except for the addition
of a vacuum advance mechanism.
The
spark advance is fully automatic being con-
FIG.
C-14—ADJUSTING CONTACT POINT GAP —
DAUNTLESS V-6 ENGINE (DELCO) trolled by built-in centrifugal weights, and by a
vacuum
advance system.
The
same service checking procedure outlined
in
Par.
C-lOa,
are used for the Prestolite V-6
distributor
with exception of specifications. 12963
FIG.
C-15—-PRESTOLITE DISTRIBUTOR V-6 ENGINE
1—
Vacuum
Advance Unit
5—Lubricating
Wick
2—
Distributor
Points 6—Condenser
3—
Breaker
Arm Pivot 7—Adjusting
Eccentric
Screw
4—
Distributor
Cap 8—Adjusting
Lock
Screw
(Rotation
&
Firing
Order)
Specifications for the V-6 Prestolite distributor are
as follows. The condenser capacity must be .25 to 28 mfd., contact breaker arm tension 17 to 22
ounces [482 a 624 gr.], and breaker point gap .016" [0,406 mm.]. The cam angle must be set
at 29° ±3° with distributor vacuum line discon
nected.
C-11.
Replacement and Adjustment of Prestolite
Distributor Point
Set — V-6
Engine
Replace
the Prestolite distributor contact set as
follows:
a.
Remove the distributor cap from the distributor.
Remove the rotor.
b. The condenser and primary leads are retained
by breaker point spring tension. Refer to Fig.
C-12
and C-15. Relieve spring tension to remove
the leads.
c. Remove the contact set retaining screw and remove the contact set.
d.
Remove the condenser screw and remove the condenser.
e.
Install
new parts by reversing the removal pro
cedure. Relieve spring tension of the breaker point
spring
to install the primary and condenser leads.
f.
Rotate the crankshaft until the distributor cam
holds the distributor points to a wide-open position.
Check
the gap
between
the points. Then slightly
loosen
the contact set mounting screw and adjust
the contact point gap to the proper dimension.
Tighten
the mounting screw when correct gap is attained.
C-12. Breaker
Lever
Spring Tension
One
of the most important items to check is the
breaker
lever spring tension.
This
is checked with
a
spring scale hooked immediately behind the
breaker
lever contact. Spring tension required to
open the contact points are given in Par. C-10. 27
Page 28 of 376
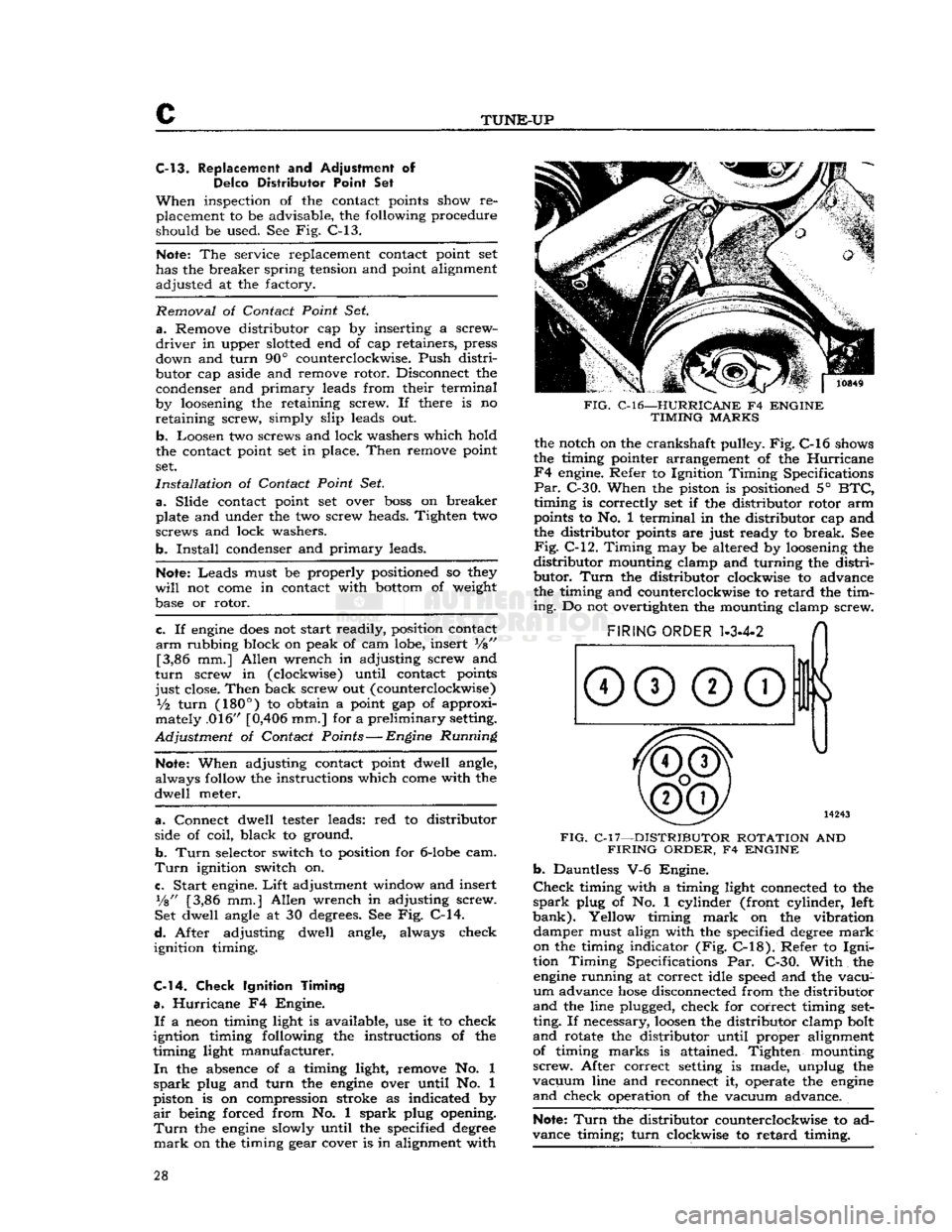
c
TUNE-UP
C-13. Replacement and Adjustment of
Delco
Distributor Point Set
When
inspection of the contact points show re placement to be advisable, the following procedure
should be used. See Fig. C-13.
Note:
The service replacement contact point set
has the breaker spring tension and point alignment
adjusted at the factory.
Removal
of
Contact Point
Set
a.
Remove distributor cap by inserting a screw
driver
in upper slotted end of cap retainers,
press
down and turn 90° counterclockwise. Push distri
butor cap aside and remove rotor. Disconnect the condenser and primary leads from their terminal
by loosening the retaining screw. If there is no
retaining
screw, simply slip leads out.
b. Loosen two screws and lock
washers
which hold
the contact point set in place. Then remove point
set.
Installation
of
Contact Point
Set.
a.
Slide contact point set over
boss
on breaker
plate and under the two screw heads. Tighten two
screws and lock washers.
b.
Install
condenser and primary leads.
Note:
Leads must be properly positioned so they
will
not
come
in contact with
bottom
of weight
base or rotor.
c.
If
engine
does
not start readily, position contact
arm
rubbing block on peak of cam lobe, insert
V%"
[3,86 mm.] Allen wrench in adjusting screw and
turn
screw in (clockwise) until contact points
just
close. Then back screw out (counterclockwise)
V2
turn
(180°)
to obtain a point gap of approxi
mately .016" [0,406 mm.] for a preliminary setting.
Adjustment
of
Contact Points
—
Engine Running
Note:
When adjusting contact point dwell angle,
always follow the instructions which
come
with the
dwell
meter.
a.
Connect dwell tester leads: red to distributor
side of coil, black to ground.
b. Turn
selector switch to position for
6-lobe
cam.
Turn
ignition switch on.
c.
Start engine.
Lift
adjustment window and insert
Vs"
[3,86 mm.] Allen wrench in adjusting screw.
Set dwell angle at 30 degrees. See Fig. C-14.
d.
After adjusting dwell angle, always check
ignition timing.
C-14.
Check
Ignition
Timing
a.
Hurricane F4 Engine.
If
a neon timing light is available, use it to check
igntion timing following the instructions of the
timing light manufacturer.
In
the absence of a timing light, remove No. 1
spark
plug and turn the
engine
over until No. 1
piston is on compression stroke as indicated by
air
being forced from No. 1 spark plug opening.
Turn
the
engine
slowly until the specified
degree
mark
on the timing gear cover is in alignment with
FIG.
C-l6—HURRICANE
F4
ENGINE
TIMING
MARKS
the notch on the crankshaft pulley. Fig. C-l6 shows
the timing pointer arrangement of the Hurricane
F4
engine. Refer to Ignition Timing Specifications
Par.
C-30. When the piston is positioned 5°
BTC,
timing is correctly set if the distributor rotor arm
points to No. 1 terminal in the distributor cap and
the distributor points are just ready to break. See
Fig.
C-12. Timing may be altered by loosening the
distributor
mounting clamp and turning the distri
butor.
Turn
the distributor clockwise to advance
the timing and counterclockwise to retard the tim
ing.
Do not overtighten the mounting clamp screw.
FIG.
C-l7—DISTRIBUTOR ROTATION
AND
FIRING
ORDER,
F4
ENGINE b.
Dauntless V-6 Engine.
Check
timing with a timing light connected to the
spark
plug of No. 1 cylinder (front cylinder, left
bank).
Yellow timing
mark
on the vibration damper must align with the specified
degree
mark
on the timing indicator (Fig.
C-18).
Refer to
Igni
tion Timing Specifications Par. C-30. With the
engine
running at correct idle speed and the vacu
um
advance
hose
disconnected from the distributor
and
the line plugged, check for correct timing
set
ting. If necessary,
loosen
the distributor clamp bolt
and
rotate the distributor until proper alignment of timing marks is attained. Tighten mounting
screw.
After correct setting is made, unplug the
vacuum
line and reconnect it, operate the
engine
and
check operation of the vacuum advance.
Note:
Turn
the distributor counterclockwise to ad
vance timing; turn clockwise to retard timing. 28
Page 29 of 376
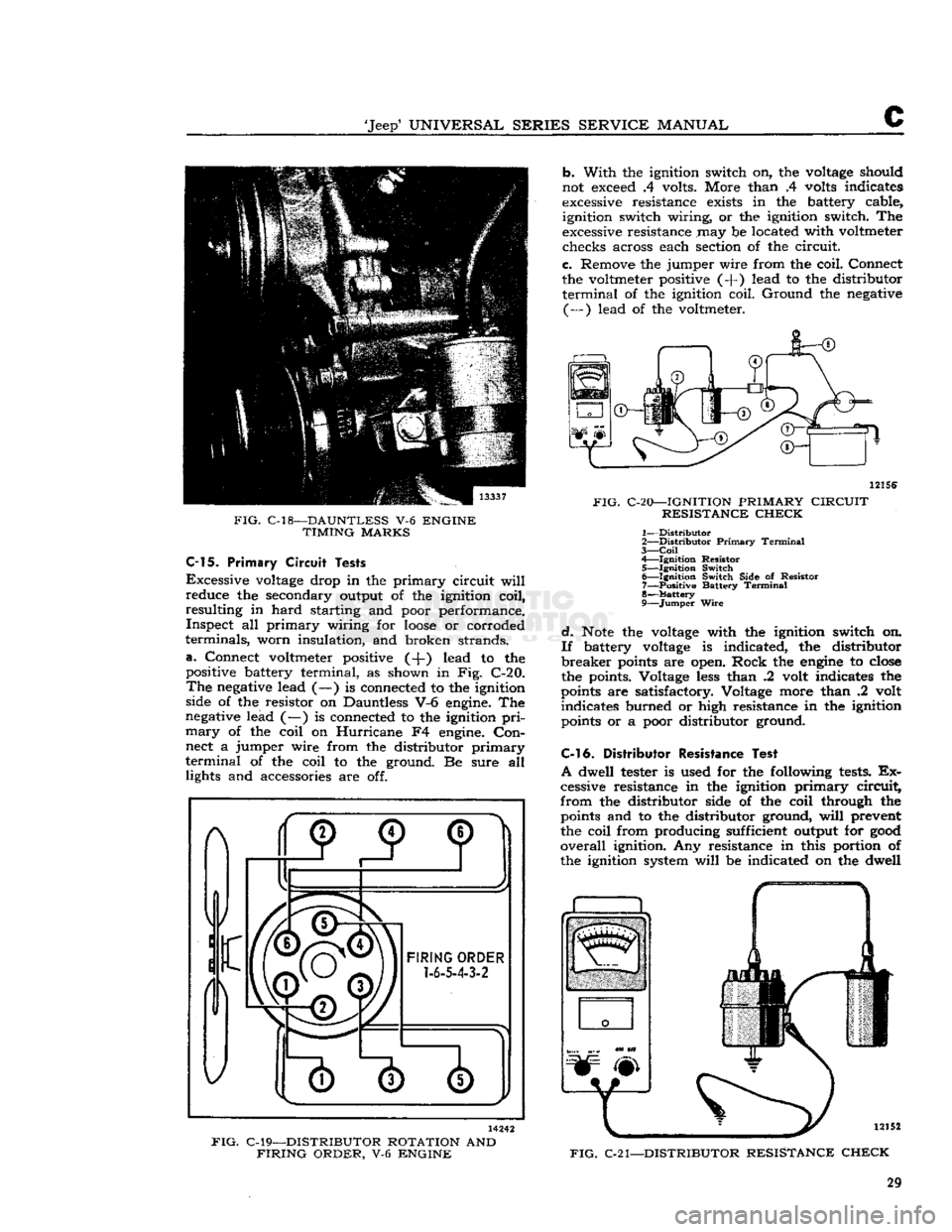
'Jeep'
UNIVERSAL
SERIES
SERVICE
MANUAL
C
FIG.
C-18—DAUNTLESS
V-6
ENGINE
TIMING
MARKS
C-15.
Primary
Circuit
Tests
Excessive
voltage
drop in the primary circuit
will
reduce the secondary output of the ignition coil,
resulting in hard starting and poor performance. Inspect all primary wiring for
loose
or corroded
terminals, worn insulation, and broken strands,
a.
Connect voltmeter positive (-J-) lead to the
positive battery terminal, as shown in Fig. C-20.
The
negative
lead (—) is connected to the ignition
side of the resistor on Dauntless V-6
engine.
The
negative
lead (—) is connected to the ignition
pri
mary
of the coil on Hurricane F4
engine.
Con
nect a jumper wire from the distributor primary
terminal
of the coil to the ground. Be sure all lights and accessories are off. b. With the ignition switch on, the
voltage
should
not
exceed
.4 volts. More than .4
volts
indicates
excessive
resistance
exists
in the battery cable, ignition switch wiring, or the ignition switch. The
excessive
resistance may be located with voltmeter checks across each section of the circuit.
c. Remove the jumper wire from the coil. Connect
the voltmeter positive (-f) lead to the distributor
terminal
of the ignition coil. Ground the
negative
(—) lead of the voltmeter.
12156
FIG.
C-20—IGNITION
PRIMARY
CIRCUIT
RESISTANCE
CHECK
1—
Distributor
2—
Distributor
Primary
Terminal
3—
Coil
4— Ignition Resistor 5— Ignition Switch 6— Ignition Switch Side of Resistor 7— Positive Battery
Terminal
8—
Battery
9—
Jumper
Wire
d.
Note
the
voltage
with the ignition switch on.
If
battery
voltage
is indicated, the distributor
breaker
points
are open. Rock the
engine
to
close
the points. Voltage
less
than .2 volt indicates the
points
are satisfactory. Voltage more than .2 volt indicates burned or high resistance in the ignition
points
or a poor distributor ground.
C-l
6. Distributor
Resistance
Test
A
dwell tester is used for the following
tests.
Ex
cessive resistance in the ignition primary circuit,
from the distributor side of the coil through the
points
and to the distributor ground,
will
prevent
the coil from producing sufficient output for
good
overall
ignition. Any resistance in this portion of
the ignition system
will
be indicated on the dwell
FIG.
C-21—DISTRIBUTOR
RESISTANCE
CHECK
14242
FIG.
C-19—DISTRIBUTOR
ROTATION
AND
FIRING
ORDER,
V-6
ENGINE
29