check engine JEEP CJ 1953 Workshop Manual
[x] Cancel search | Manufacturer: JEEP, Model Year: 1953, Model line: CJ, Model: JEEP CJ 1953Pages: 376, PDF Size: 19.96 MB
Page 85 of 376
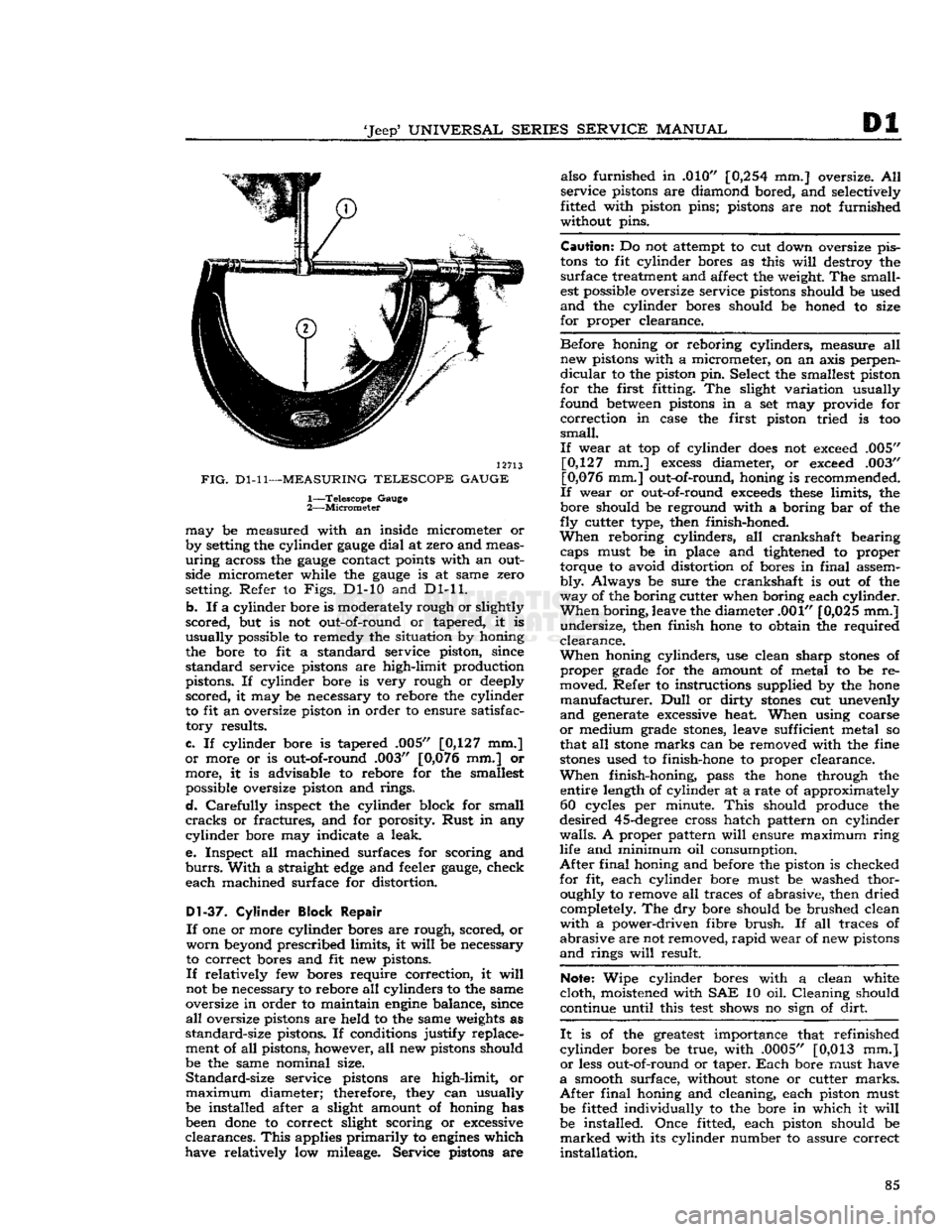
'Jeep*
UNIVERSAL
SERIES SERVICE
MANUAL
Dl
12713
FIG.
Dl-11—MEASURING
TELESCOPE GAUGE
1—
Telescope
Gauge
2—
Micrometer
may
be measured with an inside micrometer or
by setting the cylinder
gauge
dial
at zero and meas
uring
across the
gauge
contact points with an outside micrometer while the
gauge
is at same zero
setting. Refer to
Figs.
Dl-10 and Dl-11.
b.
If a cylinder bore is moderately rough or slightly
scored,
but is not out-of-round or tapered, it is
usually
possible to remedy the situation by honing
the bore to fit a standard service piston, since
standard
service pistons are high-limit production
pistons. If cylinder bore is very rough or deeply
scored,
it may be necessary to rebore the cylinder
to fit an oversize piston in order to ensure satisfac
tory
results.
c.
If cylinder bore is tapered .005" [0,127 mm.]
or
more or is out-of-round .003" [0,076 mm.] or
more,
it is advisable to rebore for the smallest possible oversize piston and rings.
d.
Carefully
inspect the cylinder block for small
cracks
or fractures, and for porosity.
Rust
in any
cylinder
bore may indicate a leak.
e.
Inspect all machined surfaces for scoring and
burrs.
With
a straight
edge
and feeler
gauge,
check
each
machined surface for distortion.
D1-37.
Cylinder Block Repair
If
one or more cylinder bores are rough, scored, or
worn
beyond prescribed limits, it
will
be necessary
to correct bores and fit new pistons.
If
relatively few bores require correction, it
will
not be necessary to rebore all cylinders to the same
oversize in order to maintain
engine
balance, since
all
oversize pistons are held to the same weights as
standard-size
pistons. If conditions justify replace
ment of all pistons, however, all new pistons should
be the same nominal size.
Standard-size
service pistons are high-limit, or
maximum
diameter; therefore, they can usually be installed after a slight amount of honing has
been
done
to correct slight scoring or excessive
clearances.
This
applies
primarily
to
engines
which
have relatively low mileage. Service pistons are also furnished in .010"
[0,254
mm.] oversize. All
service
pistons are diamond bored, and selectively
fitted with piston pins; pistons are not furnished
without pins.
Caution:
Do not attempt to cut down oversize pis
tons
to fit cylinder bores as this
will
destroy the
surface
treatment and affect the weight. The small
est possible oversize service pistons should be used
and
the cylinder bores should be honed to size
for
proper clearance.
Before
honing or reboring cylinders, measure all new pistons with a micrometer, on an axis perpen
dicular
to the piston pin. Select the smallest piston
for
the first fitting. The slight variation usually
found between pistons in a set may provide for
correction
in case the first piston tried is too
small.
If
wear at top of cylinder
does
not exceed .005" [0,127 mm.]
excess
diameter, or exceed .003"
[0,076 mm.] out-of-round, honing is recommended.
If
wear or out-of-round
exceeds
these
limits, the
bore should be reground with a boring bar of the
fly
cutter type, then finish-honed.
When
reboring cylinders, all crankshaft bearing caps must be in place and tightened to proper
torque to avoid distortion of bores in
final
assem
bly.
Always be sure the crankshaft is out of the
way
of the boring cutter when boring each cylinder.
When
boring, leave the diameter .001" [0,025 mm.]
undersize,
then finish hone to obtain the required
clearance.
When
honing cylinders, use clean sharp
stones
of
proper
grade for the amount of metal to be re
moved. Refer to instructions supplied by the hone
manufacturer.
Dull
or dirty
stones
cut unevenly
and
generate excessive heat. When using coarse
or
medium grade
stones,
leave sufficient metal so
that all
stone
marks can be removed with the fine
stones
used to finish-hone to proper clearance.
When
finish-honing, pass the hone through the entire length of cylinder at a rate of approximately 60 cycles per minute.
This
should produce the
desired
45-degree
cross hatch pattern on cylinder
walls.
A proper pattern
will
ensure maximum
ring
life and minimum oil consumption.
After
final
honing and before the piston is checked
for
fit, each cylinder bore must be washed thor oughly to remove all traces of abrasive, then dried completely. The dry bore should be brushed clean
with
a power-driven fibre
brush.
If all traces of
abrasive
are not removed,
rapid
wear of new pistons
and
rings
will
result.
Note:
Wipe cylinder bores with a clean white
cloth,
moistened with SAE 10 oil. Cleaning should
continue until this
test
shows no sign of
dirt.
It
is of the greatest importance that refinished
cylinder
bores be true, with .0005" [0,013 mm.]
or
less out-of-round or taper.
Each
bore must have
a
smooth surface, without
stone
or cutter
marks.
After
final
honing and cleaning, each piston must be fitted individually to the bore in which it
will
be installed. Once fitted, each piston should be
marked
with its cylinder number to assure correct
installation.
85
Page 86 of 376
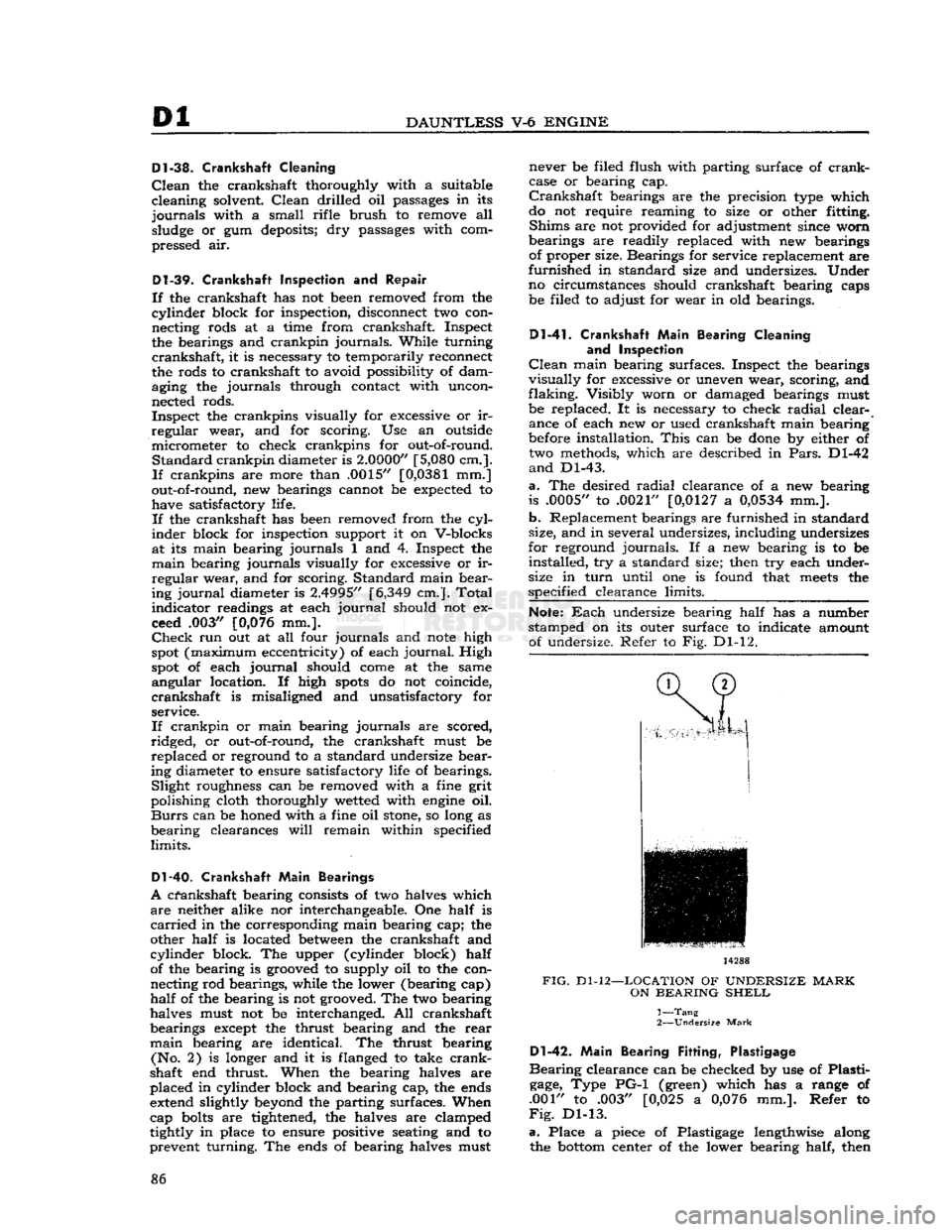
Dl
DAUNTLESS
V-6
ENGINE
Dl-38.
Crankshaft
Cleaning
Clean
the crankshaft thoroughly with a suitable
cleaning solvent.
Clean
drilled oil
passages
in its
journals
with a small rifle brush to remove all
sludge
or gum deposits; dry
passages
with com
pressed air.
Dl-39.
Crankshaft
Inspection
and
Repair
If
the crankshaft has not
been
removed from the
cylinder
block for inspection, disconnect two con necting rods at a time from crankshaft. Inspect
the bearings and crankpin journals. While turning
crankshaft,
it is necessary to temporarily reconnect
the rods to crankshaft to avoid possibility of dam aging the journals through contact with uncon
nected rods.
Inspect the crankpins visually for excessive or ir
regular
wear, and for scoring. Use an
outside
micrometer to check crankpins for out-of-round.
Standard
crankpin
diameter is
2.0000"
[5,080
cm.].
If
crankpins are more than .0015"
[0,0381
mm.]
out-of-round, new bearings cannot be
expected
to
have satisfactory life.
If
the crankshaft has
been
removed from the
cyl
inder
block for inspection support it on V-blocks
at its main bearing journals 1 and 4. Inspect the
main
bearing journals visually for excessive or ir
regular
wear, and for scoring. Standard main bear
ing
journal
diameter is 2.4995"
[6,349
cm.].
Total
indicator readings at each
journal
should not ex
ceed .003"
[0,076
mm.].
Check
run out at all four journals and
note
high
spot
(maximum eccentricity) of each
journal.
High
spot
of each
journal
should
come
at the same
angular
location. If high
spots
do not coincide,
crankshaft
is misaligned and unsatisfactory for
service.
If
crankpin or main bearing journals are scored,
ridged, or out-of-round, the crankshaft must be replaced or reground to a standard undersize bear
ing diameter to ensure satisfactory life of bearings. Slight roughness can be removed with a fine grit
polishing cloth thoroughly
wetted
with
engine
oil.
Burrs
can
be
honed with a fine oil
stone,
so long as
bearing clearances
will
remain within specified
limits.
Dl-40.
Crankshaft
Main
Bearings
A
crankshaft bearing consists of two halves which
are
neither alike nor interchangeable. One half is
carried
in the corresponding main bearing cap; the
other half is located
between
the crankshaft and
cylinder
block. The upper (cylinder block) half
of the bearing is grooved to supply oil to the con necting rod bearings, while the lower (bearing cap)
half
of the bearing is not grooved. The two bearing
halves must not be interchanged. All crankshaft
bearings
except
the thrust bearing and the
rear
main
bearing are identical. The thrust bearing (No. 2) is longer and it is flanged to take
crank
shaft end thrust. When the bearing halves are
placed in cylinder block and bearing cap, the
ends
extend slightly beyond the parting surfaces. When
cap
bolts
are tightened, the halves are clamped
tightly in place to ensure positive seating and to
prevent turning. The
ends
of bearing halves must never be filed flush with parting surface of
crank
case or bearing cap.
Crankshaft
bearings are the precision type which
do not require reaming to size or other fitting.
Shims
are not provided for adjustment since worn
bearings are readily replaced with new bearings of proper size. Bearings for service replacement are
furnished
in standard size and undersizes. Under no circumstances should crankshaft bearing caps
be filed to adjust for wear in old bearings.
Dl-41.
Crankshaft
Main
Bearing
Cleaning
and
Inspection
Clean
main bearing surfaces. Inspect the bearings
visually
for excessive or uneven wear, scoring, and
flaking.
Visibly worn or damaged bearings must
be replaced. It is necessary to check
radial
clear ance of each new or used crankshaft main bearing
before installation.
This
can be
done
by either of two methods, which are described in
Pars.
Dl-42
and
Dl-43.
a.
The desired
radial
clearance of a new bearing
is .0005" to .0021"
[0,0127
a
0,0534
mm.].
b. Replacement bearings are furnished in standard
size, and in several undersizes, including undersizes
for reground journals. If a new bearing is to be installed, try a standard size; then try each under
size in turn until one is found that
meets
the
specified clearance limits.
Note:
Each
undersize bearing half has a number
stamped on its outer surface to indicate amount of undersize. Refer to Fig. Dl-12. 14288
FIG.
Dl-12—LOCATION
OF
UNDERSIZE
MARK
ON
BEARING
SHELL
1—
Tang
2—
Undersize
Mark
Dl-42.
Main
Bearing
Fitting,
Plastigage
Bearing
clearance can be checked by use of Plasti
gage,
Type PG-1 (green) which has a range of
.001" to .003" [0,025 a
0,076
mm.]. Refer to
Fig.
Dl-13.
a.
Place a piece of Plastigage lengthwise along the
bottom
center of the lower bearing half, then 86
Page 87 of 376
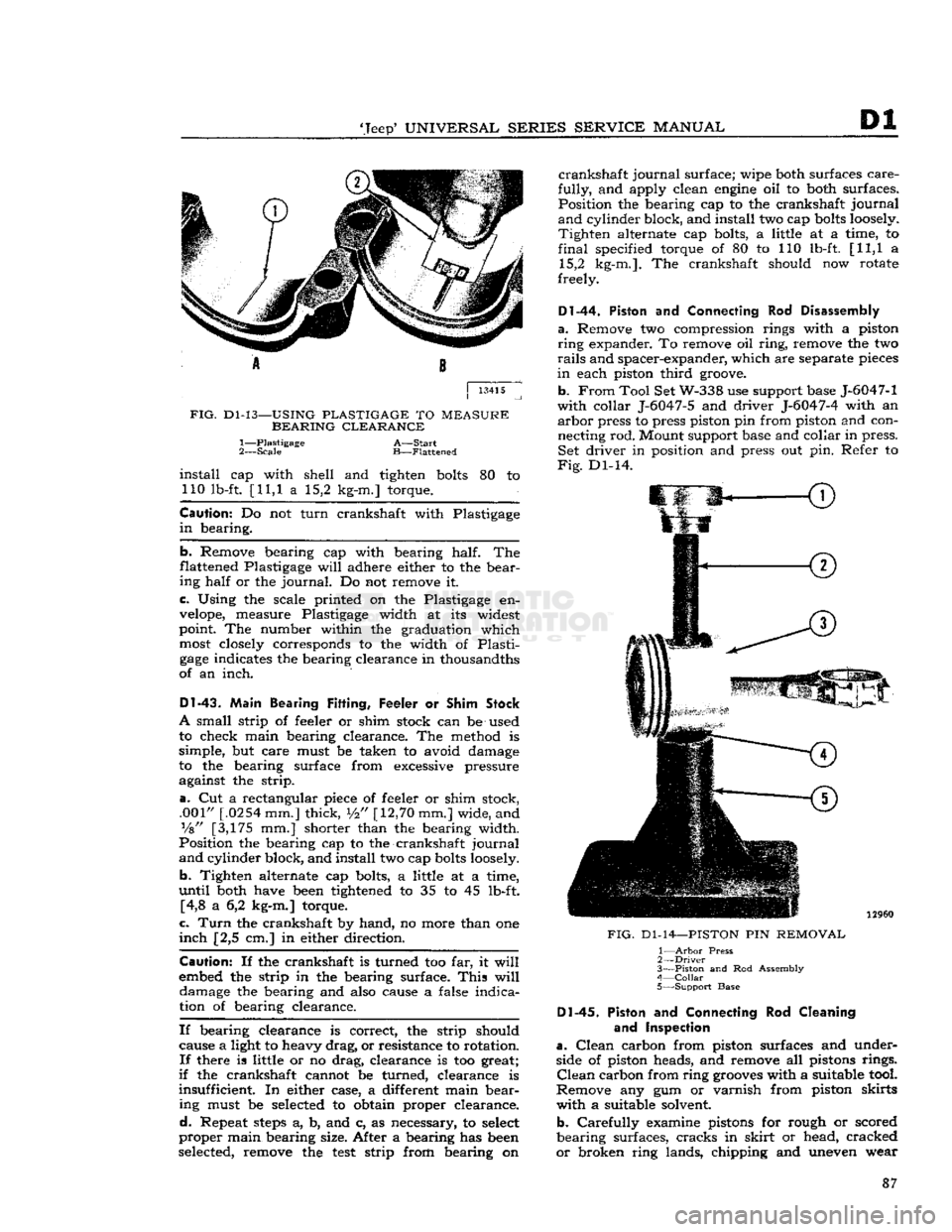
'Jeep'
UNIVERSAL
SERIES SERVICE
MANUAL
Dl
A 8
j
13415
FIG.
Dl-13—USING
PLASTIGAGE
TO
MEASURE
BEARING CLEARANCE
1— Plastigage
A—Start
2—
Scale
B—Flattened
install
cap with shell and tighten
bolts
80 to 110 lb-ft. [11,1 a 15,2 kg-m.] torque.
Caution:
Do not turn crankshaft with Plastigage
in
bearing.
b.
Remove bearing cap with bearing half. The
flattened Plastigage
will
adhere either to the bear ing half or the
journal.
Do not remove it.
c. Using the scale printed on the Plastigage en
velope,
measure Plastigage width at its widest
point. The number within the graduation which
most
closely corresponds to the width of Plasti
gage
indicates the bearing clearance in thousandths
of an inch.
DI-43.
Main Bearing
Fitting,
Feeler or
Shim
Stock
A
small strip of feeler or shim stock can be used
to check main bearing clearance. The method is
simple, but care must be taken to avoid damage
to the bearing surface from excessive pressure against the strip.
a.
Cut a rectangular piece of feeler or shim stock, .001"
[.0254
mm.] thick,
i/2"
[12,70
mm.] wide, and
Vs"
[3,175 mm.] shorter than the bearing width.
Position the bearing cap to the crankshaft journal
and
cylinder block, and install two cap
bolts
loosely.
b.
Tighten alternate cap bolts, a little at a time,
until
both have
been
tightened to 35 to 45 lb-ft. [4,8 a 6,2 kg-m.] torque.
c.
Turn
the crankshaft by hand, no more than one
inch
[2,5 cm.] in either direction.
Caution:
If the crankshaft is turned too far, it
will
embed the strip in the bearing surface.
This
will
damage the bearing and also cause a false indication of bearing clearance.
If
bearing clearance is correct, the strip should cause a light to heavy drag, or resistance to rotation.
If
there is little or no drag, clearance is too great;
if
the crankshaft cannot be turned, clearance is
insufficient. In either case, a different main bear ing must be
selected
to obtain proper clearance.
d.
Repeat
steps
a, b, and c, as necessary, to
select
proper main bearing size. After a bearing has
been
selected, remove the
test
strip from bearing on
crankshaft
journal surface; wipe both surfaces care
fully,
and apply clean
engine
oil to both surfaces. Position the bearing cap to the crankshaft journal
and
cylinder block, and install two cap
bolts
loosely.
Tighten
alternate cap bolts, a little at a time, to
final
specified torque of 80 to 110 lb-ft. [11,1 a 15,2 kg-m.]. The crankshaft should now rotate
freely.
Dl-44.
Piston
and
Connecting
Rod
Disassembly
a.
Remove two compression rings with a piston
ring
expander. To remove oil ring, remove the two
rails
and spacer-expander, which are separate
pieces
in
each piston third
groove.
b.
From
Tool Set W-338 use support base J-6047-1
with collar J-6047-5 and driver J-6047-4 with an
arbor
press to press piston pin from piston and con
necting rod. Mount support base and collar in press. Set driver in position and press out pin. Refer to
Fig.
Dl-14.
FIG.
Dl-14—PISTON
PIN
REMOVAL
1—
Arbor
Press
2—
Driver
3—
Piston
and Rod Assembly
4—
Collar
•
5—Support Base Dl-45.
Piston
and
Connecting
Rod
Cleaning
and Inspection
a.
Clean
carbon from piston surfaces and under
side of piston heads, and remove all pistons rings.
Clean
carbon from ring
grooves
with a suitable tool.
Remove any gum or varnish from piston skirts with a suitable solvent.
b.
Carefully examine pistons for rough or scored
bearing surfaces, cracks in
skirt
or head, cracked
or
broken ring lands, chipping and uneven wear 87
Page 88 of 376
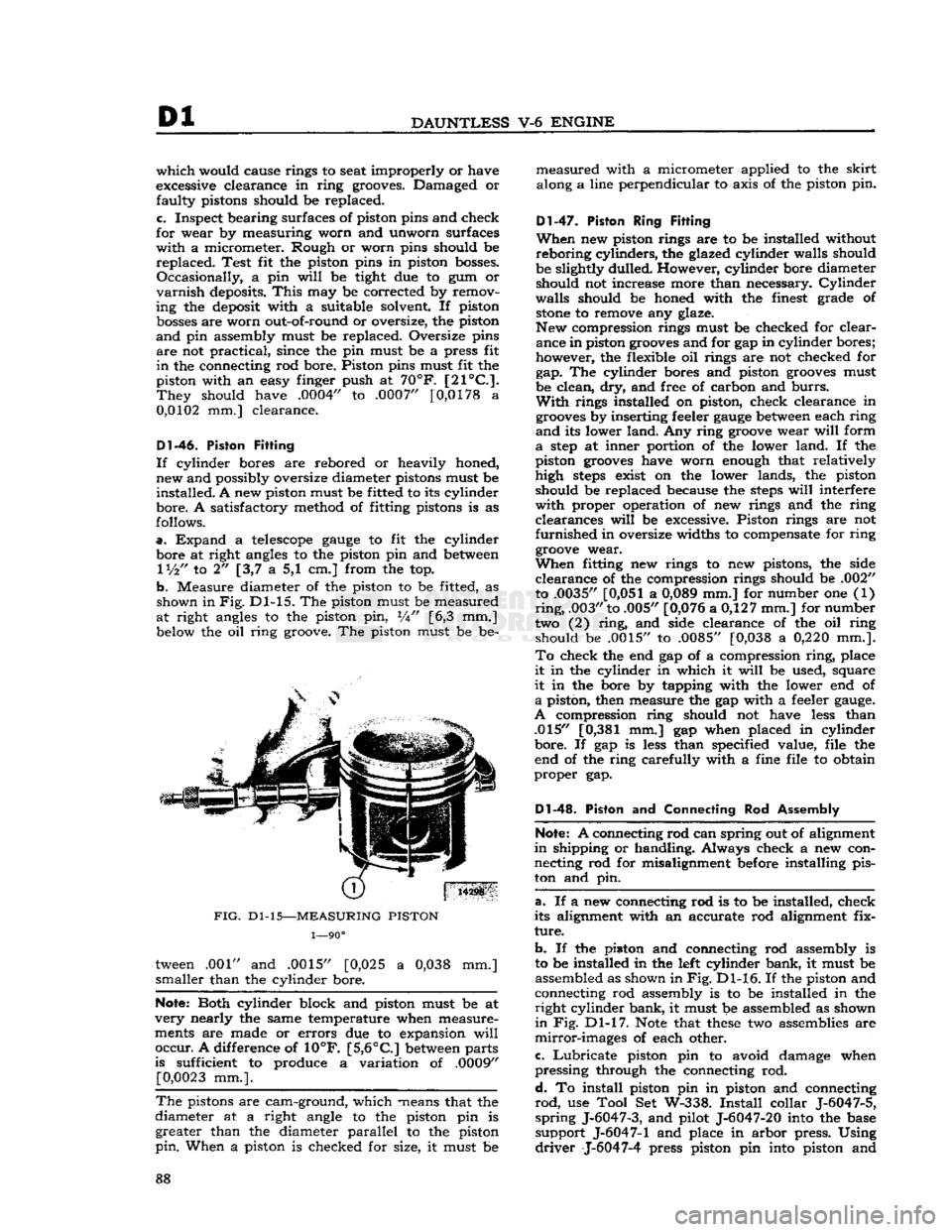
Pi
DAUNTLESS
¥-6
ENGINE
which
would cause rings to seat improperly or have
excessive clearance in
ring
grooves. Damaged or
faulty
pistons should be replaced,
c.
Inspect bearing surfaces of piston pins and check
for
wear by measuring worn and unworn surfaces
with
a micrometer. Rough or worn pins should be
replaced.
Test fit the piston pins in piston
bosses.
Occasionally,
a pin
will
be tight due to gum or
varnish
deposits.
This
may be corrected by remov
ing
the deposit with a suitable solvent. If piston
bosses
are worn out-of-round or oversize, the piston
and
pin assembly must be replaced. Oversize pins
are
not
practical,
since the pin must be a press fit
in
the connecting rod bore. Piston pins must fit the
piston with an easy finger push at
70°F.
[21°C.].
They
should have .0004" to .0007"
[0,0178
a
0,0102
mm.] clearance.
Dl-46.
Piston Fitting
If
cylinder bores are rebored or heavily honed,
new and possibly oversize diameter pistons must be
installed.
A new piston must be fitted to its cylinder
bore.
A satisfactory method of fitting pistons is as
follows.
a.
Expand
a
telescope
gauge
to fit the cylinder bore at right angles to the piston pin and
between
1
Vi"
to 2" [3,7 a 5,1 cm.] from the top.
b.
Measure diameter of the piston to be fitted, as
shown in
Fig.
Dl-15. The piston must be measured
at
right angles to the piston pin, W [6,3 mm.] below the oil
ring
groove. The piston must be be-
FIG.
Dl-15—MEASURING
PISTON
1—90°
tween .001" and .0015" [0,025 a
0,038
mm.]
smaller
than the cylinder bore.
Note:
Both cylinder block and piston must be at
very
nearly the same temperature when measure
ments are made or
errors
due to expansion
will
occur.
A difference of 10°F.
[5,6°C]
between
parts
is sufficient to produce a variation of .0009"
[0,0023
mm.].
The
pistons are cam-ground, which means that the
diameter at a right angle to the piston pin is
greater
than the diameter
parallel
to the piston
pin.
When a piston is checked for size, it must be
measured
with a micrometer applied to the
skirt
along a line
perpendicular
to axis of the piston pin.
Dl-47.
Piston Ring Fitting
When
new piston rings are to be installed without
reboring
cylinders,
the glazed cylinder walls should
be slightly dulled. However, cylinder bore diameter
should
not increase more than necessary.
Cylinder
walls
should be honed with the finest grade of
stone
to remove any glaze.
New compression rings must be checked for clear ance in piston
grooves
and for gap in cylinder bores;
however, the flexible oil rings are not checked for gap. The cylinder bores and piston
grooves
must
be clean, dry, and free of carbon and
burrs.
With
rings installed on piston, check clearance in
grooves
by inserting feeler
gauge
between
each
ring
and
its lower
land.
Any
ring
groove
wear
will
form
a
step
at inner portion of the lower
land.
If the
piston
grooves
have worn enough that relatively
high
steps
exist on the lower lands, the piston
should
be replaced because the
steps
will
interfere
with
proper operation of new rings and the
ring
clearances
will
be excessive. Piston rings are not
furnished
in oversize widths to compensate for
ring
groove
wear.
When
fitting new rings to new pistons, the side
clearance
of the compression rings should be .002" to .0035"
[0,051
a
0,089
mm.] for number one (1)
ring,
.003" to .005" [0,076 a 0,127 mm.] for number
two (2)
ring,
and side clearance of the oil
ring
should
be .0015" to .0085" [0,038 a
0,220
mm.].
To
check the end gap of a compression
ring,
place
it
in the cylinder in which it
will
be used, square
it
in the bore by tapping with the lower end of
a
piston, then measure the gap with a feeler
gauge.
A
compression
ring
should not have
less
than .015"
[0,381
mm.] gap when placed in cylinder
bore.
If gap is
less
than specified value, file the
end of the
ring
carefully with a fine file to obtain
proper
gap.
Dl-48.
Piston and Connecting Rod Assembly
Note:
A connecting rod can spring out of alignment
in
shipping or handling. Always check a new con
necting rod for misalignment before installing pis
ton and pin.
a.
If a new connecting rod is to be installed, check
its alignment with an accurate rod alignment fix
ture.
b.
If the piston and connecting rod assembly is
to be installed in the left cylinder bank, it must be assembled as shown in
Fig.
Dl-16. If the piston and
connecting rod assembly is to be installed in the
right
cylinder bank, it must be assembled as shown
in
Fig. Dl-17.
Note
that
these
two assemblies are
mirror-images
of each other.
c.
Lubricate
piston pin to avoid damage when
pressing
through the connecting rod.
d.
To install piston pin in piston and connecting
rod,
use
Tool
Set W-338.
Install
collar J-6047-5,
spring
J-6047-3, and pilot J-6047-20 into the base
support
J-6047-1 and place in
arbor
press. Using
driver
J-6047-4 press piston pin into piston and 88
Page 90 of 376
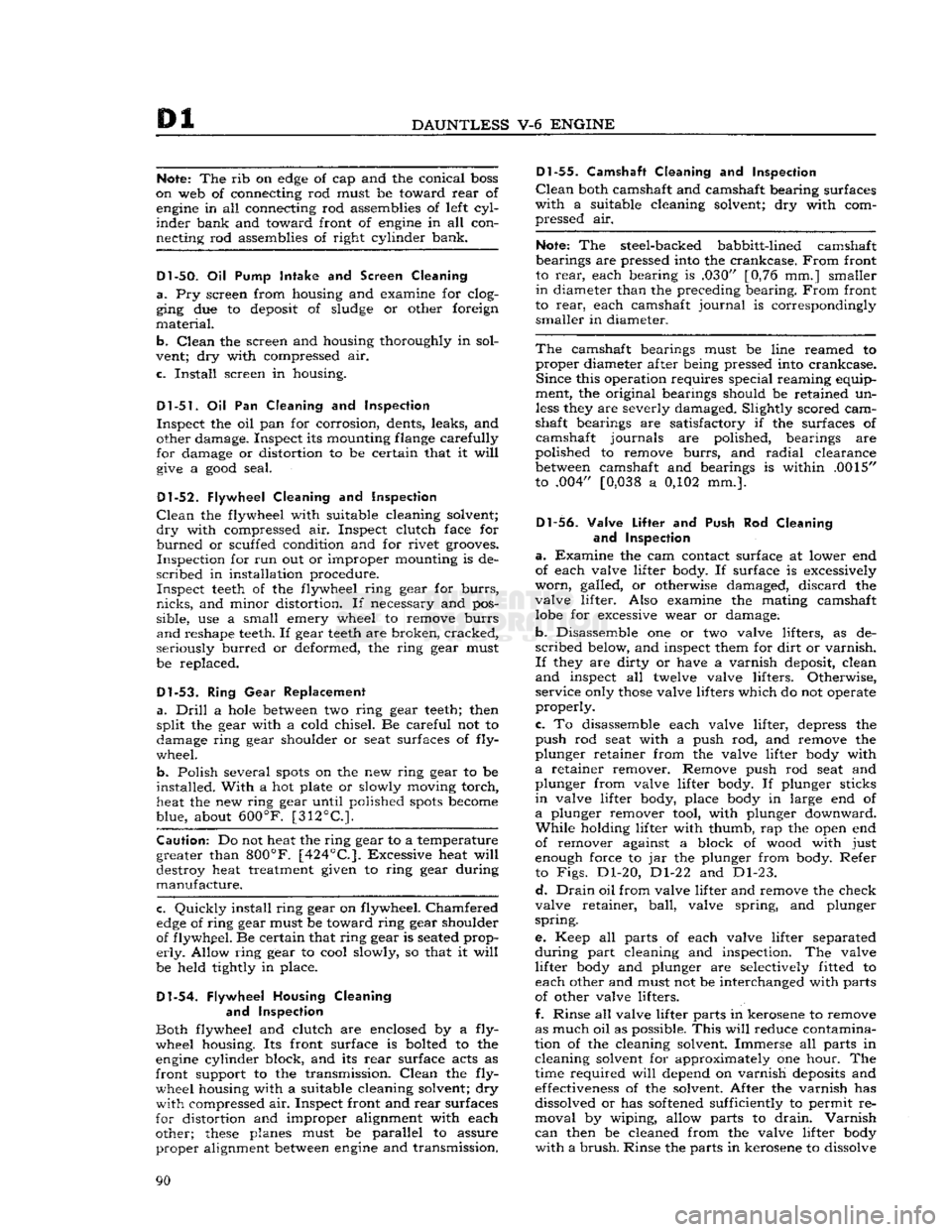
DAUNTLESS
V-6
ENGINE
Note:
The rib on
edge
of cap and the conical
boss
on web of connecting rod must be toward
rear
of
engine
in all connecting rod assemblies of left
cyl
inder
bank and toward front of
engine
in all connecting rod assemblies of right cylinder bank.
Dl-50.
Oil
Pump Intake
and
Screen Cleaning
a.
Pry screen from housing and examine for clog
ging due to deposit of sludge or other foreign
material.
b.
Clean
the screen and housing thoroughly in sol
vent; dry with compressed air.
c.
Install
screen in housing.
Dl-51.
Oil Pan Cleaning and Inspection
Inspect
the oil pan for corrosion, dents, leaks, and
other damage. Inspect its mounting flange carefully
for damage or distortion to be certain that it
will
give
a
good
seal.
Dl-52.
Flywheel Cleaning
and
Inspection
Clean
the flywheel with suitable cleaning solvent;
dry
with compressed air. Inspect clutch face for
burned
or scuffed condition and for rivet grooves.
Inspection
for run out or improper mounting is de
scribed
in installation procedure.
Inspect
teeth
of the flywheel
ring
gear for
burrs,
nicks,
and minor distortion. If necessary and pos
sible, use a small emery wheel to remove
burrs
and
reshape teeth. If gear
teeth
are broken,
cracked,
seriously
burred
or deformed, the
ring
gear must be replaced.
Dl-53.
Ring Gear Replacement
a.
Drill
a
hole
between
two
ring
gear teeth; then
split
the gear with a cold chisel. Be careful not to
damage
ring
gear shoulder or seat surfaces of fly
wheel.
b.
Polish several
spots
on the new
ring
gear to be
installed.
With
a hot plate or slowly moving torch,
heat the new
ring
gear until polished
spots
become
blue, about
600°F.
[312°C.].
Caution:
Do not heat the
ring
gear to a temperature
greater than
800°F.
[424°C.].
Excessive heat
will
destroy heat treatment given to
ring
gear during
manufacture.
c.
Quickly
install
ring
gear on flywheel. Chamfered
edge
of
ring
gear must be toward
ring
gear shoulder
of flywheel. Be certain that
ring
gear is seated prop
erly.
Allow
ring
gear to cool slowly, so that it
will
be held tightly in place.
Dl-54.
Flywheel Housing Cleaning and Inspection
Both
flywheel and clutch are enclosed by a fly
wheel housing. Its front surface is bolted to the
engine
cylinder block, and its
rear
surface acts as
front
support to the transmission.
Clean
the fly wheel housing with a suitable cleaning solvent; dry
with
compressed air. Inspect front and
rear
surfaces
for distortion and improper alignment with each
other;
these
planes must be
parallel
to assure
proper
alignment
between
engine
and transmission.
Dl-55.
Camshaft Cleaning
and
Inspection
Clean
both camshaft and camshaft bearing surfaces
with
a suitable cleaning solvent; dry with com
pressed air.
Note:
The steel-backed babbitt-lined camshaft
bearings are pressed into the crankcase.
From
front
to
rear,
each bearing is .030" [0,76 mm.] smaller
in
diameter than the preceding bearing.
From
front
to
rear,
each camshaft
journal
is correspondingly
smaller
in diameter.
The
camshaft bearings must be line reamed to
proper
diameter after being pressed into crankcase.
Since
this operation requires special reaming equip
ment, the original bearings should be retained un
less
they are severly damaged. Slightly scored cam
shaft bearings are satisfactory if the surfaces of camshaft journals are polished, bearings are
polished to remove
burrs,
and
radial
clearance
between
camshaft and bearings is within .0015"
to .004" [0,038 a 0,102 mm.].
Dl-56.
Valve Lifter
and
Push
Rod
Cleaning and Inspection
a.
Examine the cam contact surface at lower end of each valve lifter body. If surface is excessively
worn,
galled, or otherwise damaged, discard the
valve lifter. Also examine the mating camshaft
lobe
for excessive wear or damage.
b.
Disassemble one or two valve lifters, as de
scribed
below, and inspect them for
dirt
or
varnish.
If
they are dirty or have a varnish deposit, clean
and
inspect all twelve valve lifters. Otherwise,
service
only
those
valve lifters which do not operate
properly.
c.
To disassemble each valve lifter, depress the
push
rod seat with a push rod, and remove the
plunger retainer from the valve lifter body with
a
retainer remover. Remove push rod seat and
plunger from valve lifter body. If plunger sticks
in
valve lifter body, place body in large end of
a
plunger remover tool, with plunger downward.
While
holding lifter with thumb, rap the open end
of remover against a block of wood with just enough force to jar the plunger from body. Refer to
Figs.
Dl-20, Dl-22 and Dl-23.
d.
Drain
oil from valve lifter and remove the check
valve retainer,
ball,
valve spring, and plunger
spring.
e. Keep all parts of each valve lifter separated
during
part cleaning and inspection. The valve
lifter
body and plunger are selectively fitted to each other and must not be interchanged with parts
of other valve lifters.
f. Rinse all valve lifter parts in kerosene to remove as much oil as possible.
This
will
reduce contamina
tion of the cleaning solvent. Immerse all parts in cleaning solvent for approximately one hour. The
time required
will
depend on varnish
deposits
and
effectiveness
of the solvent. After the varnish has
dissolved or has
softened
sufficiently to permit re
moval
by wiping, allow parts to
drain.
Varnish
can
then be cleaned from the valve lifter body
with
a
brush.
Rinse the parts in kerosene to dissolve 90
Page 92 of 376
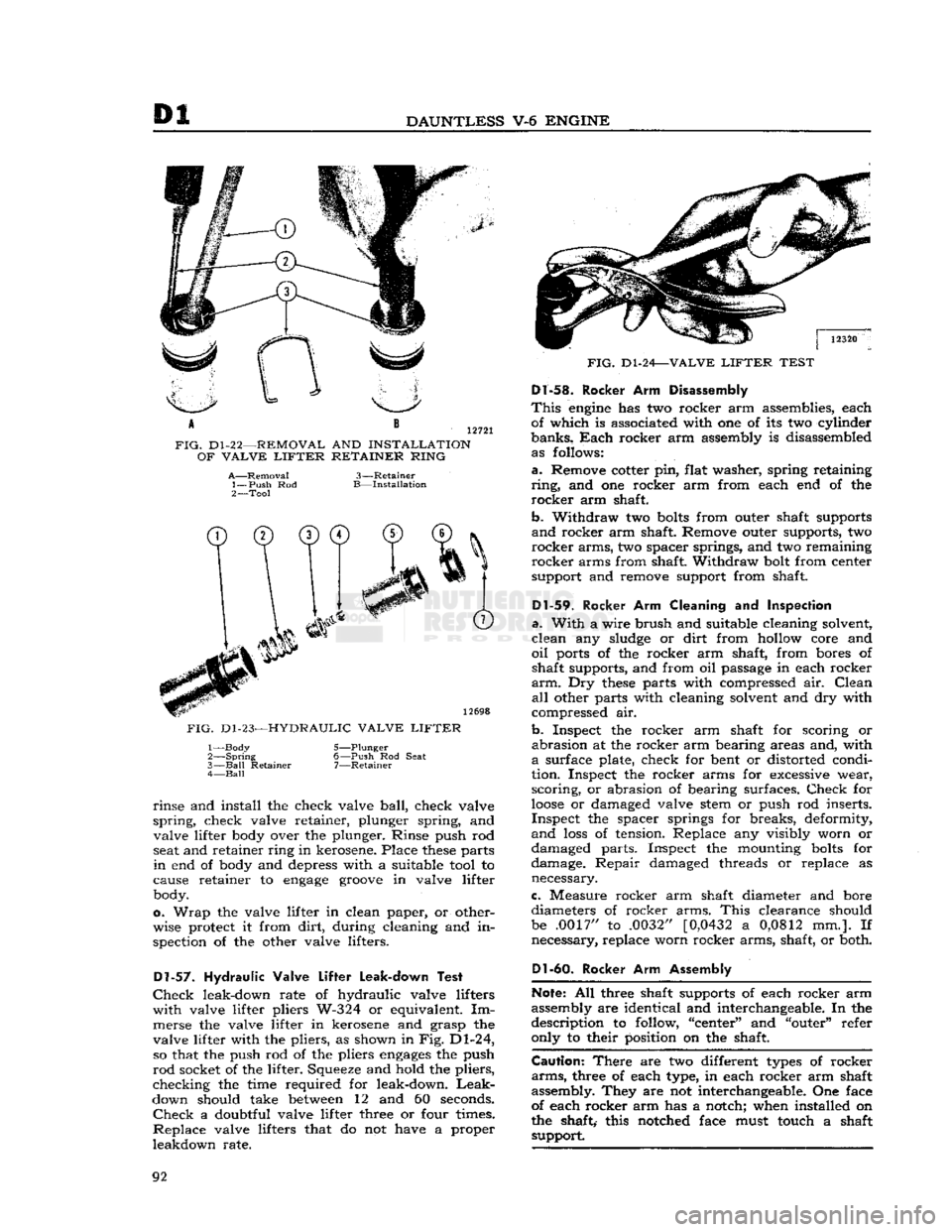
Di
DAUNTLESS
V-6
ENGINE
12721
FIG.
D1-22—REMOVAL
AND
INSTALLATION
OF
VALVE
LIFTER
RETAINER
RING
A—Removal'
1—
Push
Rod
2—
Tool
3-
B-
-Retainer
-Installation
T)
0
© ©
6
FIG.
D1-23—HYDRAULIC
VALVE
LIFTER
1—
Body
2—
Spring
3—
Ball
Retainer
4—
Ball
5— -Plunger
6—
Push
Rod
Seat
7—
-Retainer
rinse
and
install
the
check valve
ball,
check valve
spring,
check valve retainer, plunger spring,
and
valve lifter body over
the
plunger. Rinse push
rod
seat and retainer ring in kerosene. Place
these
parts
in
end of
body and depress with
a
suitable tool
to
cause retainer
to
engage
groove
in
valve lifter body.
o.
Wrap
the
valve lifter
in
clean paper,
or
other
wise protect
it
from
dirt,
during cleaning
and in
spection
of the
other valve lifters.
Dl-57.
Hydraulic Valve
Lifter
Leak-down
Test
Check
leak-down rate
of
hydraulic valve lifters
with
valve lifter pliers W-324
or
equivalent.
Im
merse
the
valve lifter
in
kerosene
and
grasp
the
valve lifter with
the
pliers,
as
shown
in
Fig. Dl-24, so that
the
push rod
of the
pliers
engages
the
push
rod
socket
of
the lifter. Squeeze and hold
the
pliers,
checking
the
time required
for
leak-down.
Leak-
down should take
between
12 and 60
seconds.
Check
a
doubtful valve lifter three
or
four times.
Replace
valve lifters that
do not
have
a
proper
leakdown rate.
FIG.
Dl-24—VALVE
LIFTER
TEST
Dl-58.
Rocker
Arm
Disassembly
This
engine
has two
rocker arm assemblies, each of which
is
associated with
one of its two
cylinder
banks.
Each
rocker arm assembly
is
disassembled as follows:
a.
Remove cotter pin, flat washer, spring retaining
ring,
and one
rocker
arm
from each
end of the
rocker
arm shaft.
b.
Withdraw
two
bolts
from outer shaft supports
and
rocker arm shaft. Remove outer supports,
two
rocker
arms, two spacer springs, and
two
remaining
rocker
arms from shaft. Withdraw bolt from center
support
and
remove support from shaft.
Dl-59.
Rocker
Arm Cleaning and
Inspection
a.
With
a
wire brush and suitable cleaning solvent,
clean
any
sludge
or
dirt
from hollow core
and
oil
ports
of the
rocker
arm
shaft, from bores
of
shaft supports, and from
oil
passage
in
each rocker
arm.
Dry
these
parts with compressed
air.
Clean
all
other parts with cleaning solvent and dry with
compressed
air.
b.
Inspect
the
rocker
arm
shaft
for
scoring
or
abrasion
at the
rocker arm bearing areas and, with
a
surface plate, check
for
bent
or
distorted condi
tion. Inspect
the
rocker arms
for
excessive wear,
scoring,
or
abrasion
of
bearing surfaces.
Check
for
loose
or
damaged valve stem
or
push
rod
inserts.
Inspect
the
spacer springs
for
breaks, deformity,
and
loss
of
tension. Replace
any
visibly worn
or
damaged parts. Inspect
the
mounting
bolts
for
damage.
Repair
damaged threads
or
replace
as
necessary.
c.
Measure rocker
arm
shaft diameter
and
bore
diameters
of
rocker arms.
This
clearance should be .0017"
to
.0032"
[0,0432
a
0,0812
mm.]. If
necessary, replace worn rocker arms, shaft,
or
both.
Dl-60.
Rocker
Arm Assembly
Note:
All three shaft supports
of
each rocker arm
assembly are identical and interchangeable. In
the
description
to
follow, "center"
and
"outer" refer only
to
their position
on the
shaft.
Caution:
There
are two
different
types
of
rocker
arms,
three
of
each type,
in
each rocker arm shaft
assembly. They
are not
interchangeable. One face
of each rocker arm
has a
notch; when installed
on
the shaft, this notched face must touch
a
shaft support.
92
Page 94 of 376
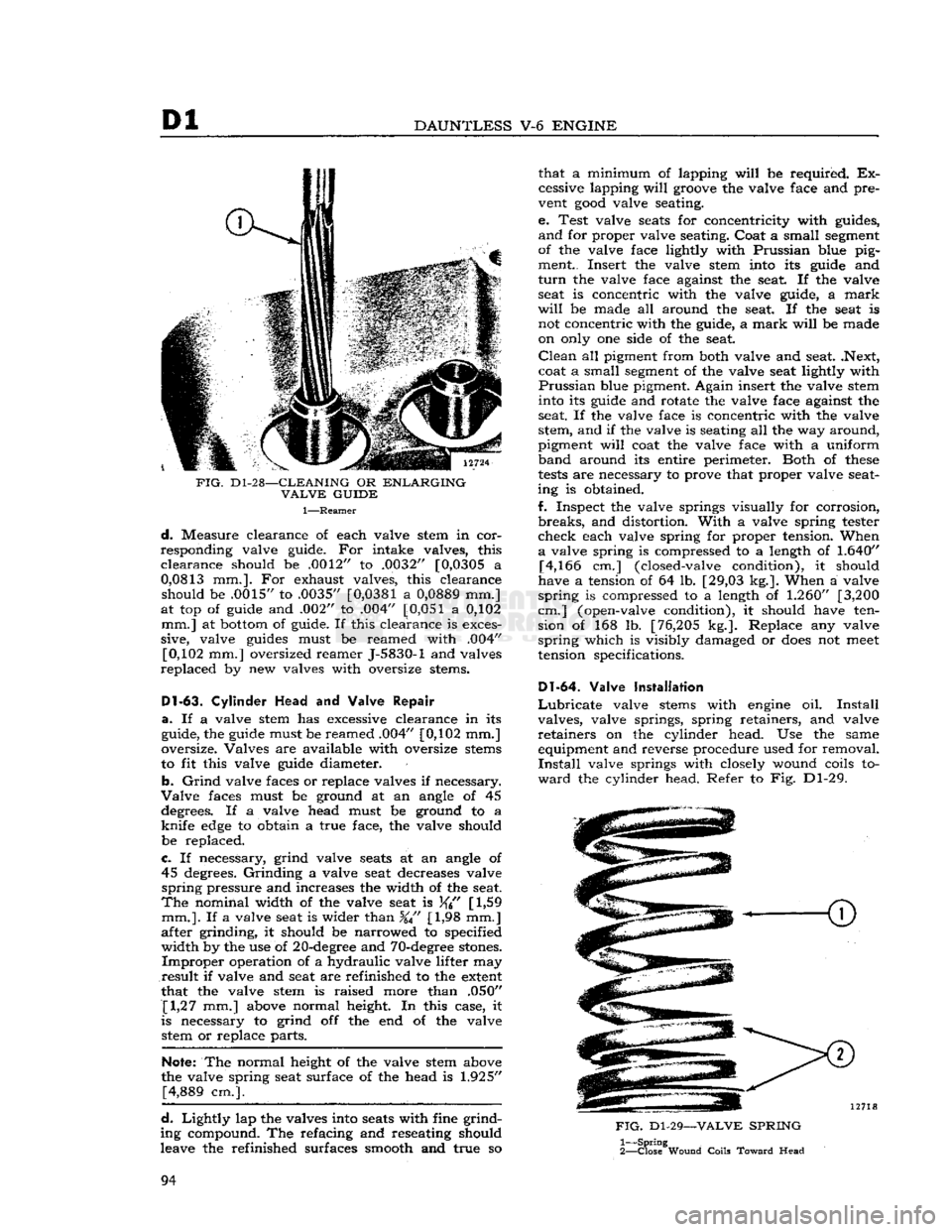
Dl
DAUNTLESS
V-6
ENGINE
FIG.
D1-28—CLEANING
OR
ENLARGING
VALVE
GUIDE
1—Reamer
d.
Measure clearance of each valve stem in cor
responding valve guide. For intake valves, this
clearance
should be .0012" to .0032" [0,0305 a
0,0813
mm.]. For exhaust valves, this clearance should be .0015" to .0035"
[0,0381
a
0,0889
mm.]
at top of guide and .002" to .004"
[0,051
a 0,102 mm.] at bottom of guide. If this clearance is exces
sive, valve guides must be reamed with .004" [0,102 mm.] oversized reamer J-5830-1 and valves
replaced
by new valves with oversize stems.
Dl-63.
Cylinder
Head
and Valve
Repair
a.
If a valve stem has excessive clearance in its
guide, the guide must be reamed .004" [0,102 mm.]
oversize. Valves are available with oversize stems
to fit this valve guide diameter.
b.
Grind
valve faces or replace valves if necessary.
Valve
faces must be ground at an angle of 45 degrees. If a valve head must be ground to a
knife
edge
to obtain a true face, the valve should
be replaced.
c.
If necessary, grind valve seats at an angle of 45 degrees.
Grinding
a valve seat decreases valve
spring
pressure and increases the width of the seat.
The
nominal width of the valve seat is
[
1,59
mm.].
If a valve seat is wider than %" [1,98 mm.]
after grinding, it should be narrowed to specified
width
by the use of 20-degree and 70-degree stones.
Improper
operation of a hydraulic valve lifter may
result
if valve and seat are refinished to the extent
that the valve stem is raised more than .050" [1,27 mm.] above normal height. In this case, it
is necessary to grind off the end of the valve stetti or replace parts.
Note:
The normal height of the valve stem above
the valve spring seat surface of the head is
1.925"
[4,889 cm.].
d.
Lightly
lap the valves into seats with fine grind
ing compound. The refacing and reseating should
leave the refinished surfaces smooth and true so that a minimum of lapping
will
be required. Ex
cessive lapping
will
groove the valve face and pre
vent
good
valve seating.
e. Test valve seats for concentricity with guides,
and
for proper valve seating. Coat a small segment
of the valve face lightly with Prussian blue pig ment.. Insert the valve stem into its guide and
turn
the valve face against the seat. If the valve seat is concentric with the valve guide, a
mark
will
be made all around the seat. If the seat is not concentric with the guide, a
mark
will
be made
on only one side of the seat.
Clean
all pigment from both valve and seat. .Next,
coat a small segment of the valve seat lightly with
Prussian
blue pigment. Again insert the valve stem into its guide and rotate the valve face against the
seat. If the valve face is concentric with the valve
stem, and if the valve is seating all the way around,
pigment
will
coat the valve face with a uniform
band
around its entire perimeter. Both of
these
tests
are necessary to prove that proper valve seat
ing is obtained.
f. Inspect the valve springs visually for corrosion,
breaks,
and distortion.
With
a valve spring tester
check
each valve spring for proper tension. When
a
valve spring is compressed to a length of
1.640"
[4,166 cm.] (closed-valve condition), it should
have a tension of 64 lb. [29,03 kg.]. When a valve
spring
is compressed to a length of
1.260"
[3,200
cm.] (open-valve condition), it should have ten sion of 168 lb. [76,205 kg.]. Replace any valve
spring
which is visibly damaged or
does
not
meet
tension specifications.
Dl-64.
Valve Installation
Lubricate
valve stems with engine oil.
Install
valves, valve springs, spring retainers, and valve
retainers
on the cylinder head. Use the same equipment and reverse procedure used for removal.
Install
valve springs with closely wound coils to
ward
the cylinder head. Refer to Fig. Dl-29.
FIG.
Dl-29—VALVE
SPRING
1—
Spring
2—
Close
Wound
Coils
Toward
Head
94
Page 95 of 376
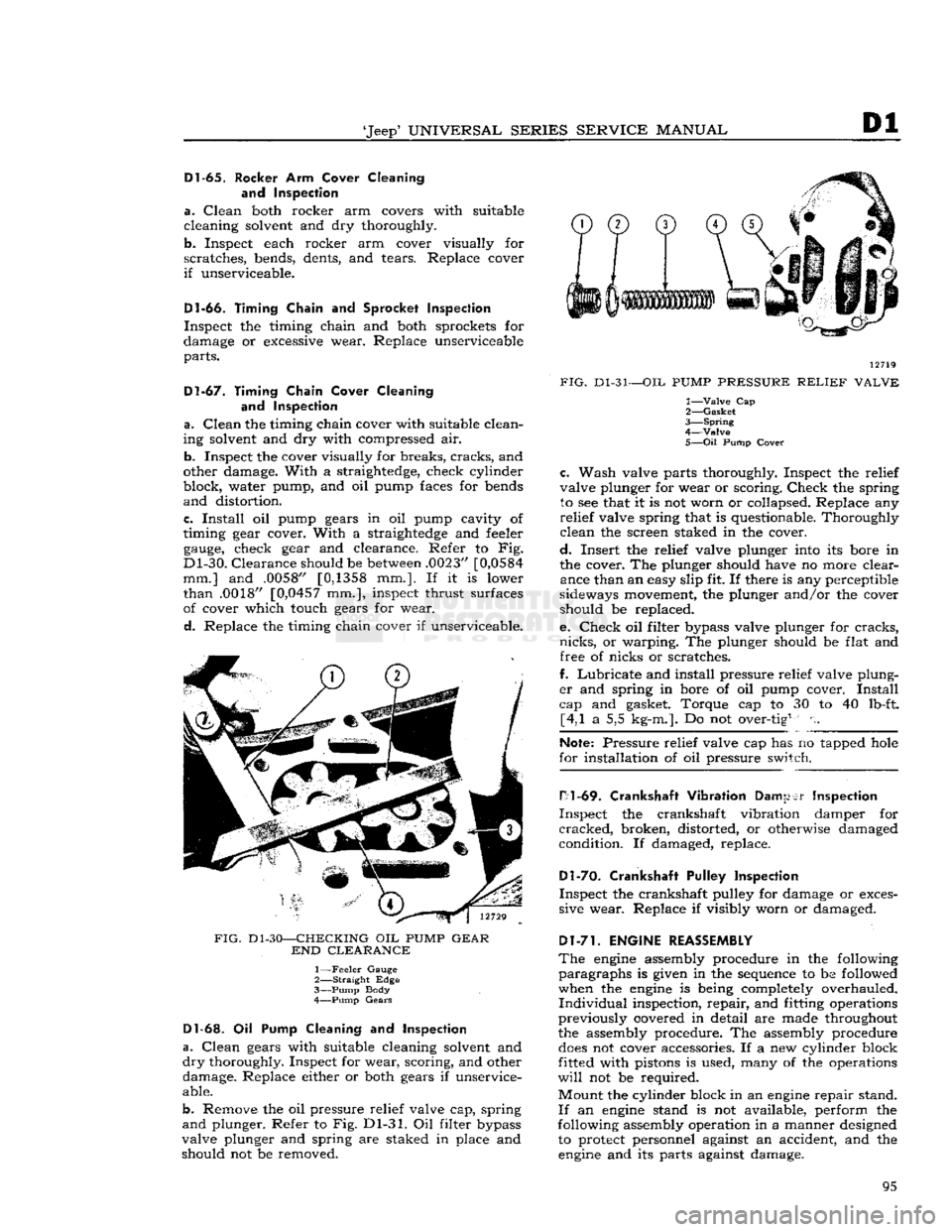
'Jeep*
UNIVERSAL
SERIES
SERVICE
MANUAL
Dl
Dl-65.
Rocker Arm Cover Cleaning
and Inspection
a.
Clean
both rocker arm covers with suitable
cleaning solvent and dry thoroughly.
b.
Inspect each rocker arm cover visually for
scratches,
bends, dents, and tears. Replace cover
if
unserviceable.
Dl-66.
Timing Chain
and
Sprocket Inspection
Inspect
the timing chain and both sprockets for
damage or excessive wear. Replace unserviceable
parts.
Dl-67.
Timing Chain Cover Cleaning and Inspection
a.
Clean
the timing chain cover with suitable clean
ing solvent and dry with compressed air.
b.
Inspect the cover visually for breaks,
cracks,
and
other damage.
With
a straightedge, check cylinder
block, water pump, and oil pump faces for bends
and
distortion.
c.
Install
oil pump gears in oil pump cavity of
timing gear cover.
With
a straightedge and feeler
gauge,
check gear and clearance. Refer to Fig.
Dl-30.
Clearance
should be
between
.0023"
[0,0584
mm.] and .0058"
[0,1358
mm.]. If it is lower
than
.0018" [0,0457 mm.], inspect thrust surfaces
of cover which touch gears for wear.
d.
Replace the timing chain cover if unserviceable.
FIG.
Dl-30—CHECKING
OIL
PUMP
GEAR
END
CLEARANCE
1—
Feeler
Gauge
2—
Straight
Edge
3—
Pump
Body
4—
Pump
Gears
Dl-63.
Oil Pump Cleaning and
Inspection
a.
Clean
gears with suitable cleaning solvent and
dry
thoroughly. Inspect for wear, scoring, and other damage. Replace either or both gears if unservice
able.
b.
Remove the oil pressure relief valve cap, spring
and
plunger. Refer to Fig. Dl-31. Oil filter bypass
valve plunger and spring are staked in place and should not be removed. 12719
FIG.
Dl-31—OIL
PUMP
PRESSURE
RELIEF
VALVE
1—
Valve
Cap
2—
Gasket
3—
Spring
4—Valve
5—
Oil
Pump
Cover
c.
Wash valve parts thoroughly. Inspect the relief
valve plunger for wear or scoring.
Check
the spring to see that it is not worn or collapsed. Replace any
relief
valve spring that is questionable. Thoroughly
clean
the screen staked in the cover.
d.
Insert the relief valve plunger into its bore in
the cover. The plunger should have no more clear ance than an easy slip fit. If there is any perceptible
sideways movement, the plunger and/or the cover should be replaced.
e.
Check
oil filter bypass valve plunger for
cracks,
nicks,
or warping. The plunger should be flat and free of nicks or scratches.
f.
Lubricate
and install pressure relief valve plung
er
and spring in bore of oil pump cover.
Install
cap and gasket. Torque cap to 30 to 40 lb-ft. [4,1 a 5,5 kg-m.]. Do not over-tig1 n.
Note:
Pressure relief valve cap has no tapped
hole
for installation of oil pressure switch.
H1
-69.
Crankshaft Vibration
Damper
Inspection
Inspect
the crankshaft vibration damper for
cracked,
broken, distorted, or otherwise damaged
condition. If damaged, replace.
Dl-70.
Crankshaft Pulley Inspection
Inspect
the crankshaft pulley for damage or exces
sive wear. Replace if visibly worn or damaged.
Dl-71.
ENGINE REASSEMBLY
The
engine
assembly procedure in the following
paragraphs
is given in the sequence to be followed
when the
engine
is being completely overhauled.
Individual
inspection,
repair,
and fitting operations
previously covered in detail are made throughout
the assembly procedure. The assembly procedure
does
not cover accessories. If a new cylinder block
fitted with pistons is used, many of the operations
will
not be required.
Mount
the cylinder block in an
engine
repair stand.
If
an
engine
stand is not available, perform the
following assembly operation in a manner designed to protect personnel against an accident, and the
engine
and its parts against damage. 95
Page 96 of 376
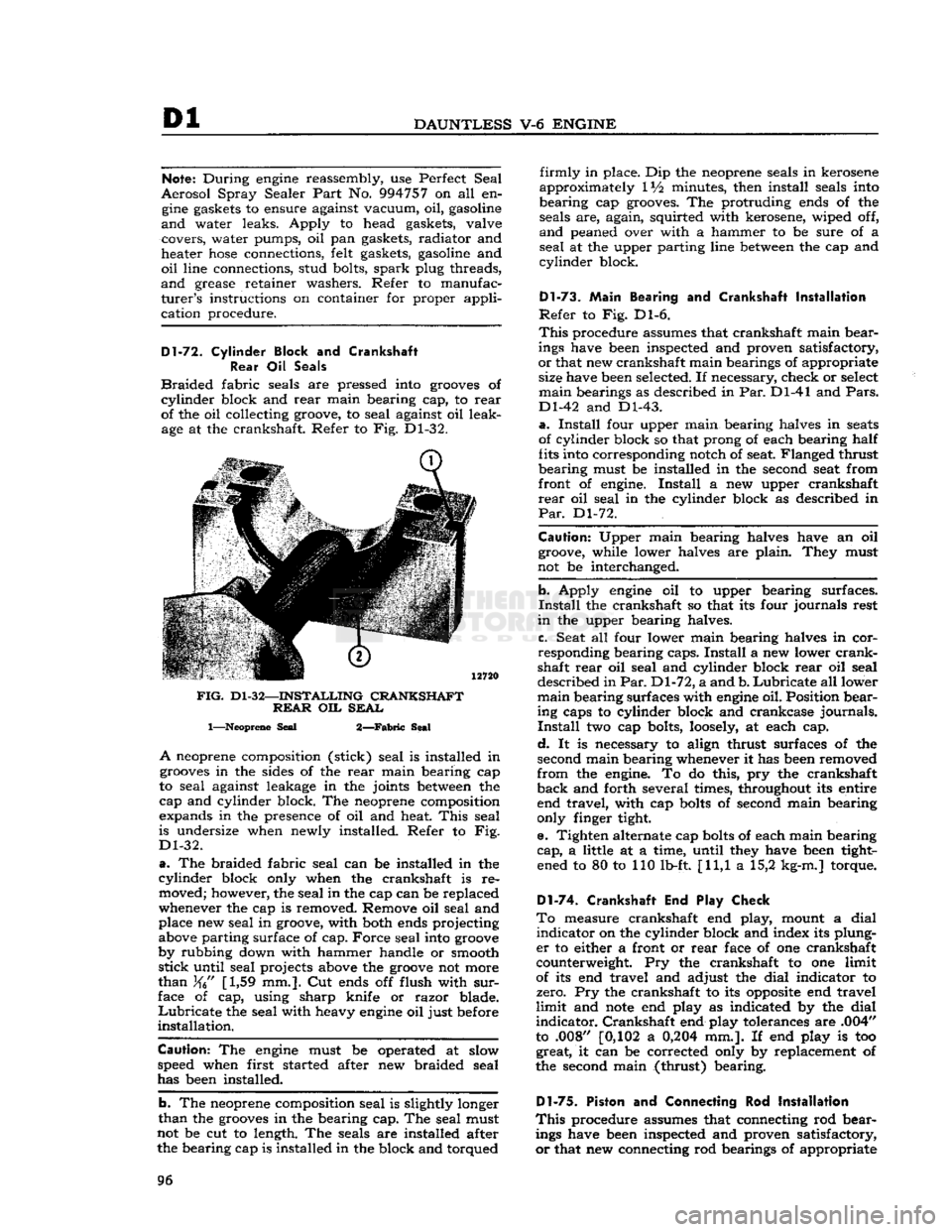
Dl
DAUNTLESS
V-6
ENGINE
Note:
During
engine
reassembly, use Perfect Seal
Aerosol
Spray Sealer
Part
No.
994757
on all en
gine
gaskets to ensure against vacuum, oil, gasoline
and
water leaks. Apply to head gaskets, valve covers, water pumps, oil pan gaskets, radiator and
heater
hose
connections, felt gaskets, gasoline and
oil
line connections, stud bolts, spark plug threads,
and
grease retainer washers. Refer to manufac
turer's
instructions on container for proper appli
cation procedure.
Dl-72.
Cylinder
Block
and Crankshaft
Rear
Oil Seals
Braided
fabric seals are pressed into
grooves
of
cylinder
block and
rear
main bearing cap, to
rear
of the oil collecting groove, to seal against oil leak age at the crankshaft. Refer to Fig. Dl-32.
FIG.
Dl-32—INSTALLING
CRANKSHAFT REAR
OIL
SEAL
1—Neoprene
Seal
2—Fabric
Seal
A
neoprene composition (stick) seal is installed in
grooves
in the sides of the
rear
main bearing cap
to seal against leakage in the joints
between
the
cap and cylinder block. The neoprene composition
expands in the presence of oil and heat.
This
seal
is undersize when newly installed. Refer to Fig.
Dl-32.
a.
The braided fabric seal can be installed in the
cylinder
block only when the crankshaft is re moved; however, the seal in the cap can be replaced
whenever the cap is removed. Remove oil seal and place new seal in groove, with both ends projecting
above parting surface of cap. Force seal into
groove
by rubbing down with hammer handle or smooth
stick
until seal projects above the
groove
not more
than
[1,59 mm.]. Cut ends off flush with
sur
face of cap, using sharp knife or razor blade.
Lubricate
the seal with heavy
engine
oil just before
installation.
Caution:
The
engine
must be operated at slow
speed when first started after new braided seal
has been installed.
b. The neoprene composition seal is slightly longer
than
the
grooves
in the bearing cap. The seal must
not be cut to length. The seals are installed after the bearing cap is installed in the block and torqued
firmly
in place. Dip the neoprene seals in kerosene
approximately IV2 minutes, then install seals into
bearing cap grooves. The protruding ends of the seals are, again, squirted with kerosene, wiped off,
and
peaned over with a hammer to be sure of a
seal
at the upper parting line
between
the cap and
cylinder
block.
Dl-73.
Main
Bearing and Crankshaft
Installation
Refer
to Fig. Dl-6.
This
procedure assumes that crankshaft main bear
ings have been inspected and proven satisfactory,
or
that new crankshaft main bearings of appropriate size have been selected. If necessary, check or select
main
bearings as described in Par. Dl-41 and
Pars.
Dl-42 and Dl-43.
a.
Install
four upper main bearing halves in
seats
of cylinder block so that prong of each bearing half
fits into corresponding notch of seat. Flanged thrust
bearing must be installed in the second seat from
front of engine.
Install
a new upper crankshaft
rear
oil seal in the cylinder block as described in
Par.
Dl-72.
Caution:
Upper main bearing halves have an oil groove, while lower halves are plain. They must
not be interchanged.
b. Apply
engine
oil to upper bearing surfaces.
Install
the crankshaft so that its four journals rest
in
the upper bearing halves.
c. Seat all four lower main bearing halves in cor
responding bearing caps.
Install
a new lower
crank
shaft
rear
oil seal and cylinder block
rear
oil seal
described in
Par.
Dl-72, a and b.
Lubricate
all lower
main
bearing surfaces with
engine
oil. Position bear ing caps to cylinder block and crankcase journals.
Install
two cap bolts,
loosely,
at each cap.
d.
It is necessary to align thrust surfaces of the
second main bearing whenever it has been removed
from
the engine. To do this, pry the crankshaft
back
and forth several times, throughout its entire end travel, with cap
bolts
of second main bearing
only finger tight.
e. Tighten alternate cap
bolts
of each main bearing
cap,
a little at a time, until they have been tight ened to 80 to 110 lb-ft. [11,1 a 15,2 kg-m.] torque.
D1-74. Crankshaft End Play Check
To
measure crankshaft end play, mount a dial
indicator
on the cylinder block and index its plung
er
to either a front or
rear
face of one crankshaft
counterweight. Pry the crankshaft to one limit
of its end travel and adjust the dial indicator to
zero. Pry the crankshaft to its
opposite
end travel
limit
and
note
end play as indicated by the dial
indicator.
Crankshaft end play tolerances are .004"
to .008" [0,102 a
0,204
mm.]. If end play is too great, it can be corrected only by replacement of
the second main (thrust) bearing.
Dl-75.
Piston and Connecting Rod
Installation
This
procedure assumes that connecting rod bear ings have been inspected and proven satisfactory,
or
that new connecting rod bearings of appropriate 96
Page 97 of 376
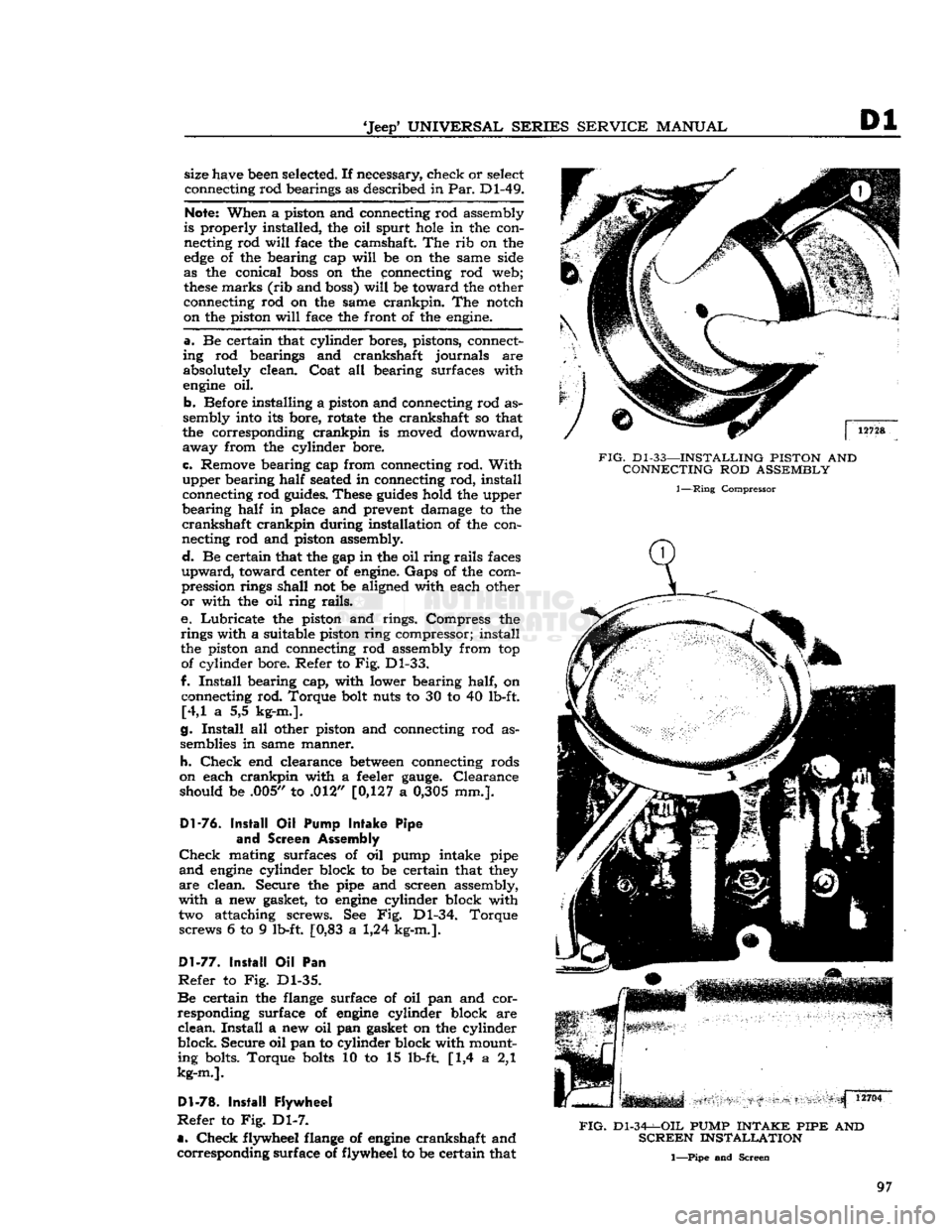
'Jeep'
UNIVERSAL
SERIES SERVICE
MANUAL
Dl
size have
been
selected. If necessary, check or
select
connecting rod bearings as described in Par. Dl-49.
Note:
When a piston and connecting rod assembly
is properly installed, the oil spurt
hole
in the con necting rod
will
face the camshaft. The rib on the
edge
of the bearing cap
will
be on the same side
as the conical
boss
on the connecting rod web;
these
marks (rib and boss)
will
be toward the other
connecting rod on the same crankpin. The notch
on the piston
will
face the front of the
engine.
a.
Be certain that cylinder bores, pistons, connect
ing rod bearings and crankshaft journals are absolutely clean. Coat all bearing surfaces with
engine
oil.
b. Before installing a piston and connecting rod as
sembly into its bore, rotate the crankshaft so that
the corresponding crankpin is moved downward, away from the cylinder bore.
c. Remove bearing cap from connecting rod. With
upper bearing half seated in connecting rod, install connecting rod guides. These
guides
hold the upper
bearing half in place and prevent damage to the
crankshaft
crankpin during installation of the con
necting rod and piston assembly.
d.
Be certain that the gap in the oil ring rails faces
upward,
toward center of
engine.
Gaps of the com
pression rings shall not be aligned with each other
or
with the oil ring
rails.
e. Lubricate the piston and rings. Compress the
rings with a suitable piston ring compressor; install
the piston and connecting rod assembly from top of cylinder bore. Refer to Fig. Dl-33.
f.
Install
bearing cap, with lower bearing half, on connecting rod. Torque bolt nuts to 30 to 40 lb-ft. [4,1 a 5,5 kg-m.].
g.
Install
all other piston and connecting rod as
semblies in same manner.
h.
Check
end clearance
between
connecting rods
on each crankpin with a feeler
gauge.
Clearance should be .005,/ to .012" [0,127 a
0,305
mm.].
Dl-76.
Install
Oil
Pump
Intake
Pipe
and
Screen Assembly
Check
mating surfaces of oil pump intake pipe
and
engine
cylinder block to be certain that they
are
clean. Secure the pipe and screen assembly,
with a new gasket, to
engine
cylinder block with two attaching screws. See Fig. Dl-34. Torque screws 6 to 9 lb-ft. [0,83 a 1,24 kg-m.].
Dl-77.
Install
Oil Pan
Refer
to Fig. Dl-35.
Be
certain the flange surface of oil pan and cor
responding surface of
engine
cylinder block are
clean.
Install
a new oil pan gasket on the cylinder
block.
Secure
oil pan to cylinder block with mount ing bolts. Torque
bolts
10 to 15 lb-ft [1,4 a 2,1
kg-m.].
Dl-78.
Install
Flywheel
Refer
to Fig. Dl-7.
a.
Check
flywheel flange of
engine
crankshaft and corresponding surface of flywheel to
be
certain that
FIG.
Dl-33—INSTALLING
PISTON
AND
CONNECTING
ROD
ASSEMBLY
1—Ring
Compressor
FIG.
Dl-34-^-OIL
PUMP
INTAKE PIPE
AND
SCREEN
INSTALLATION
1—Pipe and Screen
97