check engine JEEP CJ 1953 Repair Manual
[x] Cancel search | Manufacturer: JEEP, Model Year: 1953, Model line: CJ, Model: JEEP CJ 1953Pages: 376, PDF Size: 19.96 MB
Page 104 of 376
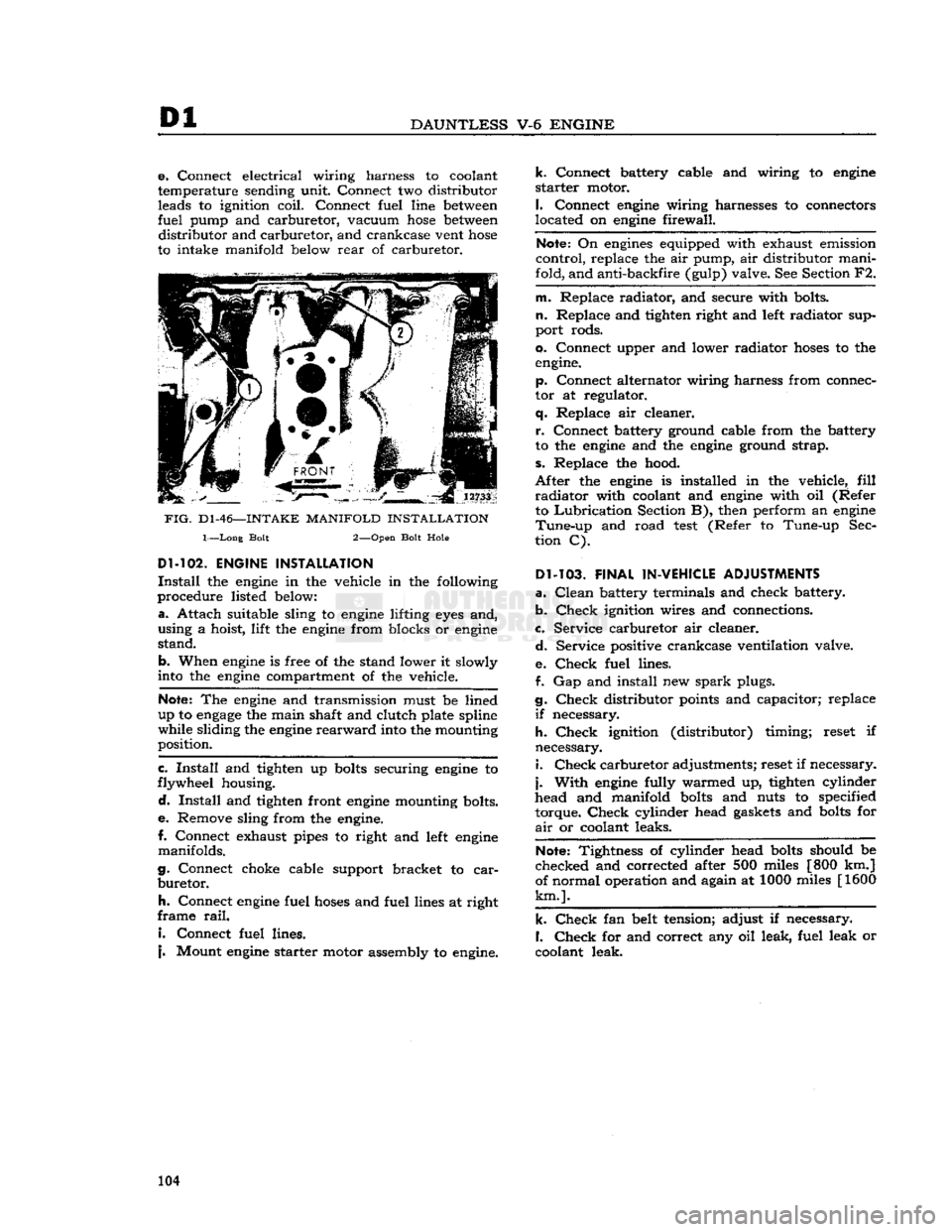
Dl
DAUNTLESS
V-6
ENGINE
e.
Connect electrical wiring harness to coolant
temperature sending unit. Connect two distributor leads to ignition coil. Connect fuel line
between
fuel pump and carburetor, vacuum
hose
between
distributor and carburetor, and crankcase vent
hose
to intake manifold
below
rear
of carburetor.
FIG.
D1-46—-INTAKE
MANIFOLD
INSTALLATION
1—Long Bolt 2—Open Bolt Hole
Dl-102.
ENGINE INSTALLATION
Install
the
engine
in the vehicle in the following
procedure listed
below:
a.
Attach suitable sling to
engine
lifting
eyes
and,
using a hoist, lift the
engine
from blocks or
engine
stand.
b. When
engine
is free of the stand lower it slowly
into
the
engine
compartment of the vehicle.
Note:
The
engine
and transmission must be lined
up to
engage
the main shaft and clutch plate spline
while sliding the
engine
rearward
into
the mounting
position.
c.
Install
and tighten up
bolts
securing
engine
to
flywheel housing.
d.
Install
and tighten front
engine
mounting bolts.
e.
Remove sling from the
engine.
I.
Connect exhaust pipes to right and
left
engine
manifolds.
g. Connect choke cable support bracket to
car
buretor.
h.
Connect
engine
fuel
hoses
and fuel lines at right
frame
rail.
I.
Connect fuel lines.
j.
Mount
engine
starter motor assembly to
engine.
k.
Connect battery cable and wiring to
engine
starter
motor.
I.
Connect
engine
wiring harnesses to connectors
located on
engine
firewall.
Note:
On
engines
equipped with exhaust emission
control, replace the air pump, air distributor mani
fold, and anti-backfire (gulp) valve. See Section F2.
m. Replace radiator, and secure with bolts,
n.
Replace and tighten right and
left
radiator sup
port rods.
0. Connect upper and lower radiator
hoses
to the
engine.
p. Connect alternator wiring harness from connec
tor at regulator,
q.
Replace air cleaner.
r.
Connect battery ground cable from the battery
to the
engine
and the
engine
ground strap,
s.
Replace the hood.
After
the
engine
is installed in the vehicle,
fill
radiator
with coolant and
engine
with oil (Refer to
Lubrication
Section B), then perform an
engine
Tune-up
and road
test
(Refer to Tune-up Sec
tion C).
Dl-103.
FINAL IN-VEHICLE ADJUSTMENTS
a.
Clean
battery terminals and check battery.
b.
Check
ignition wires and connections.
c. Service carburetor air cleaner.
d.
Service positive crankcase ventilation valve.
e.
Check
fuel lines.
f. Gap and install new
spark
plugs.
g.
Check
distributor
points
and capacitor; replace
if
necessary.
h.
Check
ignition (distributor) timing; reset if
necessary. 1.
Check
carburetor adjustments; reset if necessary,
j.
With
engine
fully warmed up, tighten cylinder
head and manifold
bolts
and nuts to specified
torque.
Check
cylinder head
gaskets
and
bolts
for
air
or coolant leaks.
Note:
Tightness of cylinder head
bolts
should be
checked and corrected after 500 miles [800 km.]
of normal operation and again at 1000 miles [1600
km.].
k.
Check
fan belt tension; adjust if necessary.
I.
Check
for and correct any oil leak, fuel leak or
coolant leak. 104
Page 113 of 376
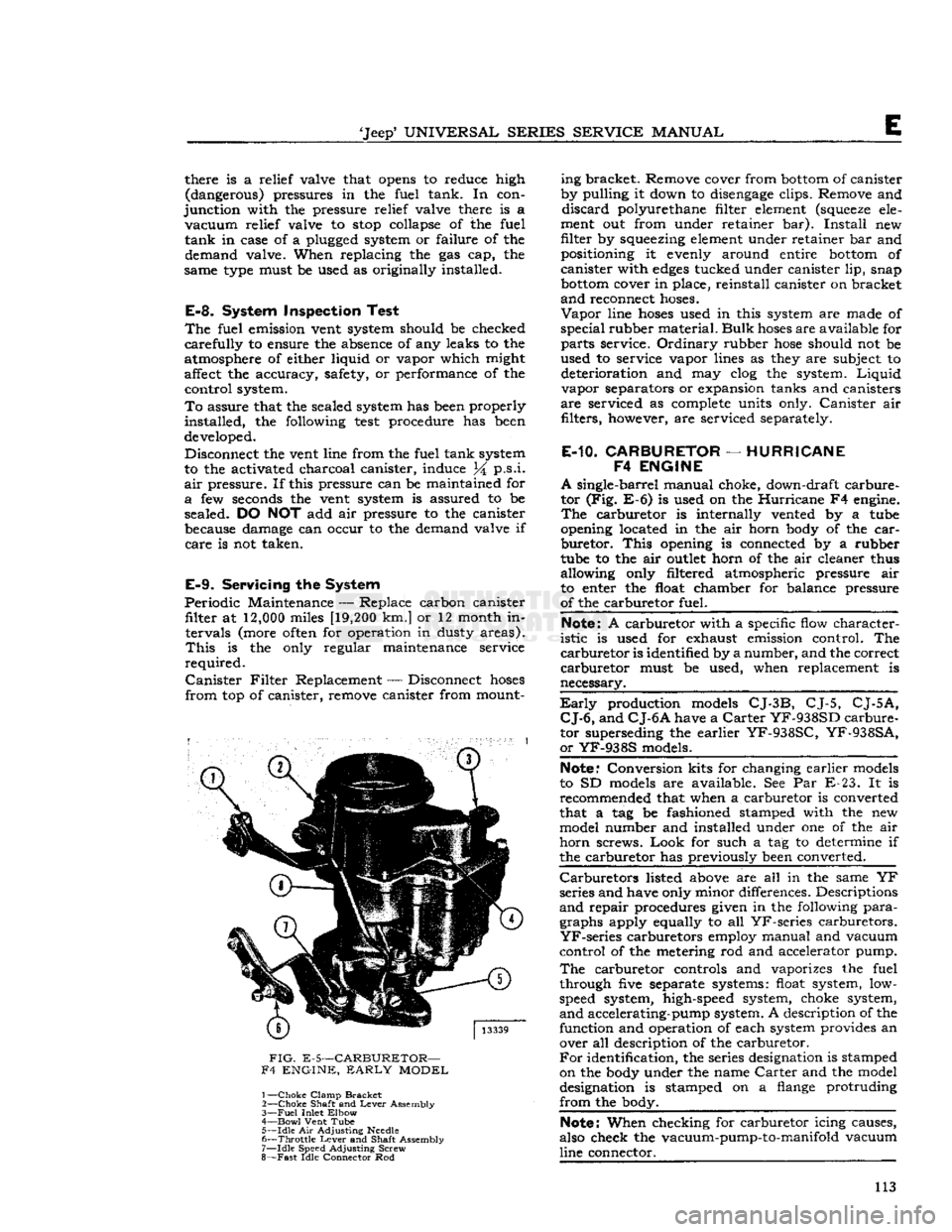
'Jeep*
UNIVERSAL
SERIES
SERVICE
MANUAL
E
there is a relief valve that
opens
to reduce high
(dangerous) pressures in the fuel tank. In con
junction
with the pressure relief valve there is a
vacuum
relief valve to
stop
collapse of the fuel
tank
in case of a plugged system or failure of the demand valve. When replacing the gas cap, the
same type must be used as originally installed.
E-8.
System Inspection Test
The
fuel emission vent system should be checked
carefully
to ensure the absence of any leaks to the
atmosphere of either liquid or vapor which might
affect the accuracy, safety, or performance of the control system.
To
assure that the sealed system has been properly
installed,
the following
test
procedure has been
developed.
Disconnect the vent line from the fuel tank system
to the activated charcoal canister, induce l/i p.s.i.
air
pressure. If this pressure can be maintained for
a
few seconds the vent system is assured to be sealed. DO NOT add air pressure to the canister
because damage can occur to the demand valve if
care
is not taken.
E-9.
Servicing the System
Periodic
Maintenance — Replace carbon canister filter at
12,000
miles
[19,200
km.] or 12 month intervals (more
often
for operation in dusty areas).
This
is the only regular maintenance service
required.
Canister
Filter
Replacement — Disconnect
hoses
from
top of canister, remove canister from mount
-
t
FIG.
E-5—CARBURETOR—
F4 ENGINE,
EARLY
MODEL
1—
Choke
Clamp
Bracket
2—
Choke
Shaft and
Lever
Assembly
3—
Fuel
Inlet
Elbow
4—
Bowl
Vent Tube 5—
Idle
Air Adjusting
Needle
6—
Throttle
Lever
and Shaft Assembly
7—
Idle
Speed Adjusting Screw
8—
Fast
Idle Connector Rod ing bracket. Remove cover from
bottom
of canister
by pulling it down to
disengage
clips. Remove and
discard
polyurethane filter element
(squeeze
ele
ment out from under retainer bar).
Install
new
filter by squeezing element under retainer bar and positioning it evenly around entire
bottom
of
canister with
edges
tucked under canister lip, snap
bottom
cover in place, reinstall canister on bracket
and
reconnect
hoses.
Vapor
line
hoses
used in this system are made of
special
rubber material.
Bulk
hoses
are available for
parts
service.
Ordinary
rubber
hose
should not be
used to service vapor lines as they are subject to deterioration and may clog the system.
Liquid
vapor separators or expansion tanks and canisters
are
serviced as complete units only.
Canister
air filters, however, are serviced separately.
E-10.
CARBURETOR
—
HURRICANE
F4
ENGINE
A
single-barrel manual choke, down-draft carbure
tor (Fig. E-6) is used on the
Hurricane
F4 engine.
The
carburetor is internally vented by a tube
opening located in the air horn body of the
car
buretor.
This
opening is connected by a rubber
tube to the air
outlet
horn of the air cleaner thus
allowing only filtered atmospheric pressure air
to enter the float chamber for balance pressure
of the carburetor fuel.
Note:
A carburetor with a specific flow character
istic
is used for exhaust emission control. The
carburetor
is identified by a number, and the correct
carburetor
must be used, when replacement is
necessary.
Early
production models
CJ-3B,
CJ-5,
CJ-5A,
CJ-6,
and
CJ-6A
have a
Carter
YF-938SD
carbure
tor superseding the earlier
YF-938SC,
YF-938SA,
or
YF-938S
models.
Note."
Conversion kits for changing earlier models
to SD models are available. See Par E-23. It is recommended that when a carburetor is converted
that a tag be fashioned stamped with the new model number and installed under one of the air
horn
screws.
Look
for such a tag to determine if
the carburetor has previously been converted.
Carburetors
listed above are all in the same YF
series and have only minor differences. Descriptions
and
repair procedures given in the following
para
graphs apply equally to all
YF-series
carburetors.
YF-series
carburetors employ manual and vacuum
control of the metering rod and accelerator pump.
The
carburetor controls and vaporizes the fuel
through five separate systems: float system, low-
speed system, high-speed system, choke system,
and
accelerating-pump system. A description of the function and operation of each system provides an over all description of the carburetor.
For
identification, the series designation is stamped
on the body under the name
Carter
and the model
designation is stamped on a flange protruding
from
the body.
Note:
When checking for carburetor icing causes,
also check the vacuum-pump-to-manifold vacuum
line connector. 113
Page 115 of 376
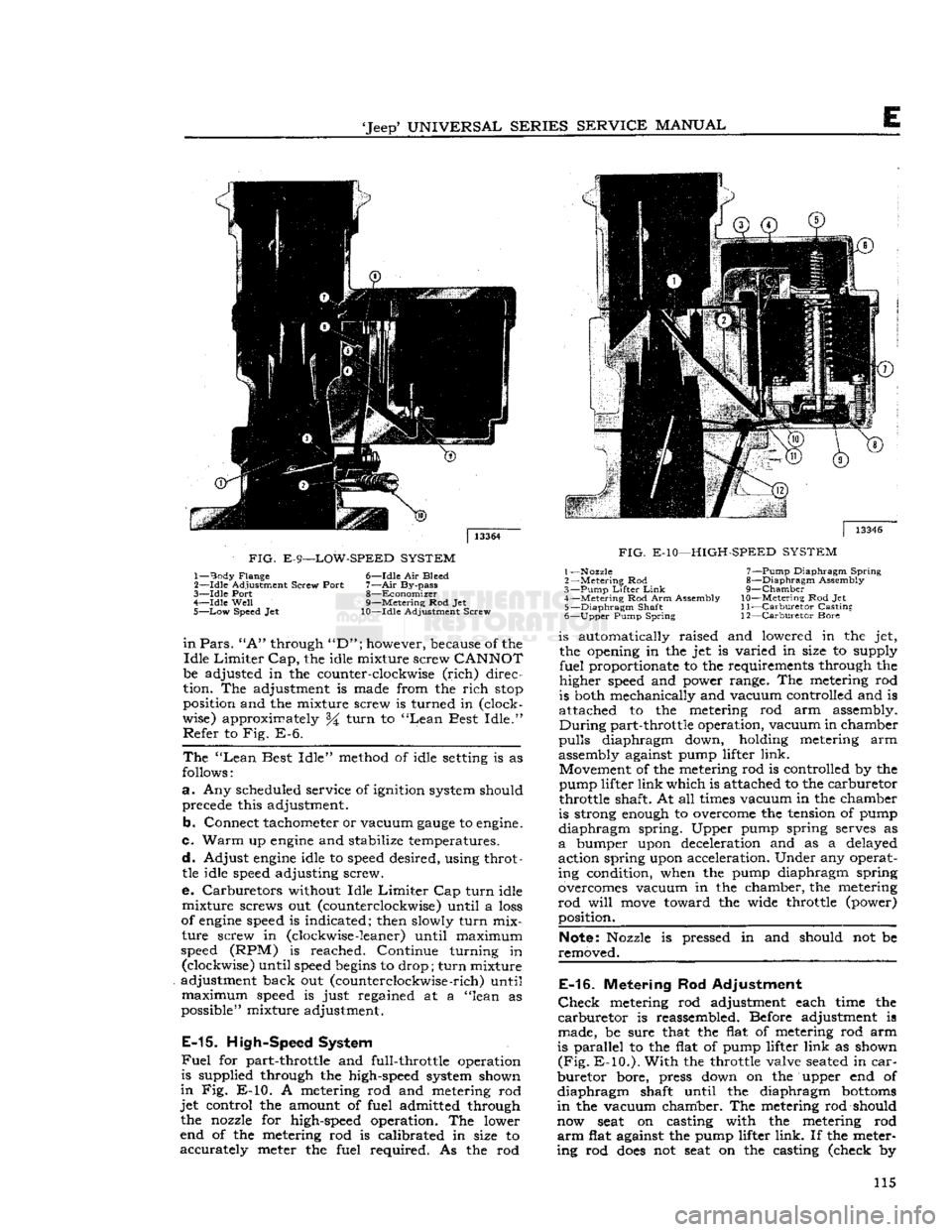
'Jeep*
UNIVERSAL
SERIES
SERVICE
MANUAL
E
FIG.
E-9—LOW-SPEED
SYSTEM
1—
Body
Flange 6—Idle Air Bleed
2—
-Idle
Adjustment Screw Port
7—Air
By-pass
3—
Idle
Port 8—Economizer
4—
Idle
Well
9—Metering Rod Jet
5—
Low
Speed Jet 10—Idle Adjustment Screw
in
Pars.
"A"
through
"D";
however, because of the
Idle
Limiter
Cap,
the idle mixture screw
CANNOT
be adjusted in the counter-clockwise
(rich)
direc
tion. The adjustment is made from the
rich
stop
position and the mixture screw is turned in (clock
wise) approximately %
turn
to
"Lean
Best
Idle."
Refer
to Fig. E-6.
The
"Lean
Best
Idle"
method of idle
setting
is as
follows:
a.
Any scheduled service of ignition system should precede this adjustment.
b.
Connect tachometer or vacuum
gauge
to
engine.
c.
Warm
up
engine
and stabilize temperatures.
d.
Adjust
engine
idle to
speed
desired, using throttle idle
speed
adjusting screw.
e. Carburetors without Idle
Limiter
Cap
turn
idle
mixture
screws out (counterclockwise) until a
loss
of
engine
speed
is indicated; then slowly
turn
mix
ture
screw in (clockwise
-leaner)
until maximum
speed
(RPM) is reached. Continue turning in (clockwise) until
speed
begins
to drop;
turn
mixture
adjustment back out (counterclockwise
-rich)
until
maximum
speed
is just regained at a "lean as
possible" mixture adjustment.
E-15.
High-Speed System
Fuel
for part-throttle and full-throttle operation
is supplied through the high-speed system shown
in
Fig. E-10. A metering rod and metering rod
jet
control the amount of fuel admitted through the nozzle for high-speed operation. The lower
end of the metering rod is calibrated in size to
accurately
meter the fuel required. As the rod
|
13346
FIG.
E-10—HIGH-SPEED
SYSTEM
1—Nozzle 7—Pump Diaphragm
Spring
2
—Metering
Rod 8—Diaphragm Assembly
3—
Pump
Lifter
Link
9—Chamber
4—
Metering
Rod Arm Assembly
10—Metering
Rod Jet 5—
Diaphragm
Shaft
11—Carburetor
Casting
6—
Upper
Pump Spring 12—Carburetor Bore is automatically raised and lowered in the jet,
the opening in the jet is varied in size to supply
fuel
proportionate to the requirements through the
higher
speed
and power range. The metering rod
is both mechanically and vacuum controlled and is
attached to the metering rod arm assembly.
During
part-throttle operation, vacuum in chamber
pulls
diaphragm down, holding metering arm
assembly against pump lifter
link.
Movement of the metering rod is controlled by the
pump lifter
link
which is attached to the carburetor
throttle shaft. At all
times
vacuum in the chamber
is strong
enough
to overcome the tension of pump
diaphragm
spring. Upper pump spring serves as
a
bumper upon deceleration and as a delayed
action spring upon acceleration. Under any operat ing condition, when the pump diaphragm spring
overcomes vacuum in the chamber, the metering
rod
will
move
toward the wide throttle (power) position.
Note:
Nozzle is pressed in and should not be
removed.
E-16.
Metering Rod Adjustment
Check
metering rod adjustment each time the
carburetor
is reassembled. Before adjustment is
made, be sure that the flat of metering rod arm
is parallel to the flat of pump lifter
link
as shown
(Fig.
E-10.).
With
the throttle valve
seated
in
car
buretor
bore, press down on the upper end of
diaphragm
shaft until the diaphragm
bottoms
in
the vacuum chamber. The metering rod should
now
seat
on casting with the metering rod
arm
flat against the pump lifter
link.
If the meter
ing rod
does
not
seat
on the casting (check by 115
Page 116 of 376

E
FUEL
SYSTEM
pressing downward on metering rod) or
seats
be
fore the metering rod arm makes flat contact with the pump lifter link, make adjustment by bending
the lip on the metering rod arm.
E-17.
Choke System
The
choke system consists of a manually-operated
choke valve, a fast-idle connecting rod, and a fast-
idle arm. The choke valve is offset-spring loaded to prevent over-choking during the starting warm-
up period. When the choke valve is moved to a closed position for starting, the fast idle connector
rod
in Fig. E-ll revolves the fast idle link.
This
action increases the
engine
idle speed to prevent stalling during the warm-up period. A fast-idle
connector rod return spring prevents partial closing
of the choke valve. pump lifter which is connected to the throttle.
This
movement forces fuel from the chamber
above the diaphragm through discharge pump check valve and discharge pump jet.
This
auxiliary discharge of fuel supplies
engine
requirements for
quick
acceleration and heavy loads. When the
throttle is closed, the diaphragm is again pulled
down by high vacuum and another measured
charge of fuel enters the chamber above the
diaphragm
through the intake passage to be
available for the next cycle of operation.
Note:
The pump jet (see insert drawing in Fig.
E-12)
projecting into the air stream is permanently pressed into the carburetor body and should not
be removed. Also, carburetor design makes it im possible to adjust the pump stroke.
FIG.
E-ll—FAST
IDLE
ADJUSTMENT
1—Fast
Idle
Connector Rod
2—Fast
Idle
Link
E-18.
Fast
Idle Adjustment
With
the choke held in wide open position, lip (No. 1) (Fig.
E-ll)
on the fast-idle rod should con
tact the
boss
on the body casting. Adjust by bend
ing the fast-idle link at
offset
as shown by (No. 2).
E-19.
Accelerating Pump System
The
accelerating pump system shown in Fig. E-12
provides a measured amount of fuel for rapid acceleration and smooth
engine
operation when
the throttle is opened at lower speeds. In operation,
vacuum
is applied to the underside of diaphragm
at all times when the
engine
is running.
Lower
and
more uniform vacuum is provided by vacuum
restriction
and vacuum bleed passage. When the
diaphragm
is in its maximum down position at
low throttle resulting from high vacuum in chamber the chamber above the diaphragm is full of fuel
which
has been admitted through intake passage.
When
the throttle is opened, vacuum drops in the
chamber and the diaphragm is initially forced
upward
by the spring on the diaphragm shaft.
The
upward motion is picked up by accelerator
|
13347
FIG.
E-12—ACCELERATING
PUMP
SYSTEM
1—
Pump
Fuel
Passage
6—Intake
Passage
2—
Discharge
Pump Jet 7—Diaphragm
3—
Pump
Check
Valve
Ball
8—Vacuum Chamber 4—
Bail
Check
Weight
9—Vacuum
Restriction
Jet
5—
Pump
Lifter
Arm 10—Vacuum Bleed Passage
E-20.
Accelerating Pump Maintenance
If
engine
acceleration is unsatisfactory, remove the
pump diaphragm and check the diaphragm for wear
or
damage. Then remove the pump check retainer
ring
located directly above the pump check weight
and
pump ball check. Pump ball check must seat
properly
as a leak
will
cause poor acceleration performance. Inspect and replace all worn or
damaged parts.
Clean
and blow out all passages
with
compressed air.
Note
that when testing the pump for discharge volume with the carburetor
off the engine, only half of the maximum pump capacity
will
be discharged. When the
engine
is
operating, vacuum controls the balance of dis charge. 116
Page 118 of 376
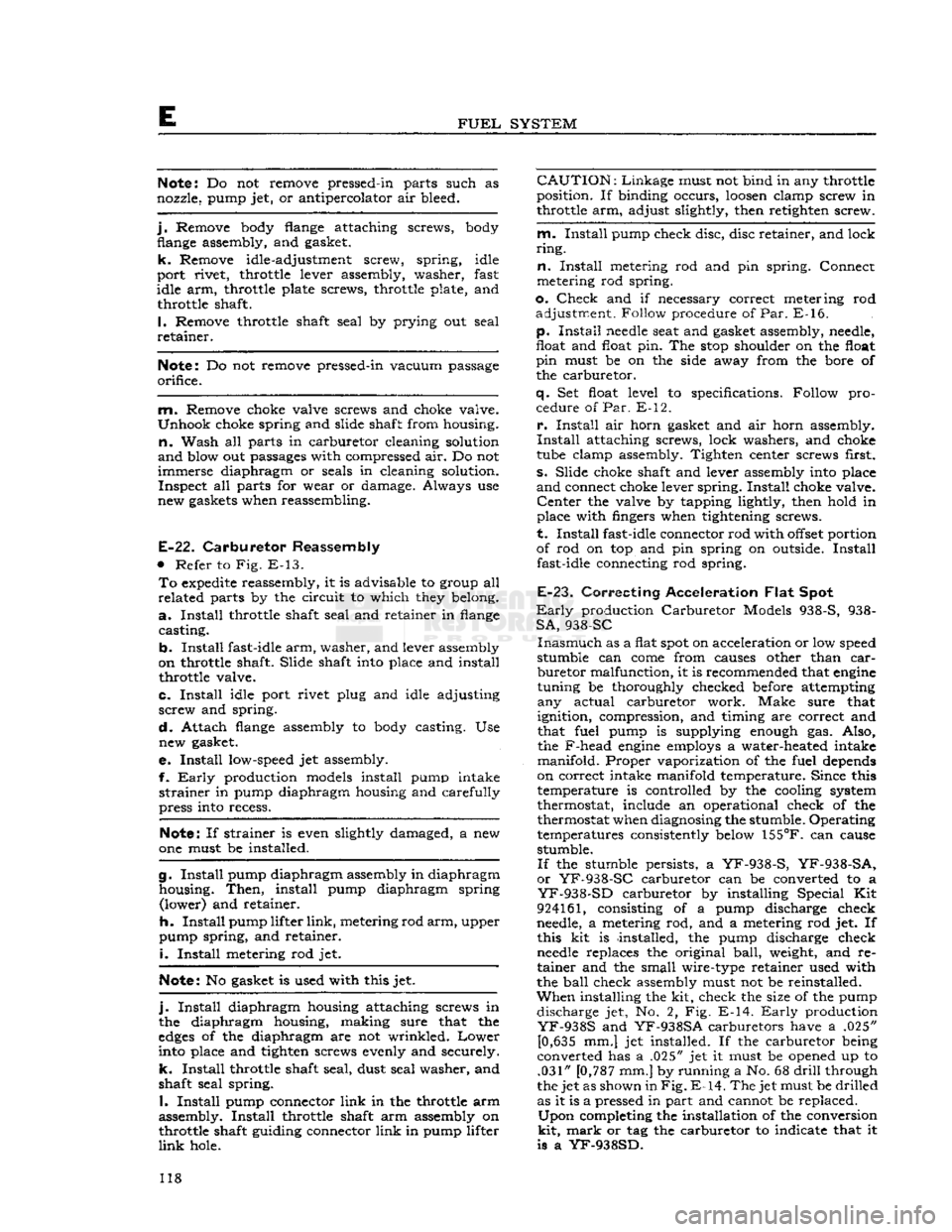
E
FUEL
SYSTEM
Note:
Do not remove pressed-in parts such as
nozzle, pump jet, or antipercolator air bleed.
j.
Remove body flange attaching screws, body flange assembly, and gasket.
k.
Remove idle-adjustment screw, spring, idle
port
rivet, throttle lever assembly, washer, fast
idle arm, throttle plate screws, throttle plate, and throttle shaft.
1. Remove throttle shaft seal by prying out seal
retainer.
Note:
Do not remove pressed-in vacuum passage
orifice.
m.
Remove choke valve screws and choke valve.
Unhook
choke spring and slide shaft from housing,
n.
Wash all parts in carburetor cleaning solution
and
blow out passages with compressed air. Do not immerse diaphragm or seals in cleaning solution.
Inspect
all parts for wear or damage. Always use
new gaskets when reassembling.
E-22.
Carburetor
Reassembly
•
Refer to Fig. E-13.
To
expedite
reassembly, it is advisable to group all
related
parts by the circuit to which they belong.
a.
Install
throttle shaft seal and retainer in flange casting.
b.
Install
fast-idle
arm,
washer, and lever assembly
on throttle shaft. Slide shaft into place and install throttle valve.
c.
Install
idle port rivet plug and idle adjusting
screw
and spring.
d.
Attach flange assembly to body casting. Use new gasket.
e.
Install
low-speed jet assembly.
f.
Early
production models install pump intake
strainer
in pump diaphragm housing and carefully
press into recess.
Note:
If strainer is even slightly damaged, a new
one must be installed.
g.
Install
pump diaphragm assembly in diaphragm housing.
Then,
install pump diaphragm spring
(lower)
and retainer.
h.
Install
pump lifter
link,
metering rod
arm,
upper
pump spring, and retainer.
I.
Install
metering rod jet.
Note:
No gasket is used with this jet.
j.
Install
diaphragm housing attaching screws in
the diaphragm housing, making sure that the
edges
of the diaphragm are not wrinkled.
Lower
into place and tighten screws evenly and securely,
k.
Install
throttle shaft seal, dust seal washer, and
shaft seal spring.
I.
Install
pump connector
link
in the throttle arm
assembly.
Install
throttle shaft arm assembly on
throttle shaft guiding connector
link
in pump lifter
link
hole.
CAUTION:
Linkage
must not bind in any throttle
position. If binding occurs,
loosen
clamp screw in
throttle arm, adjust slightly, then retighten screw.
m.
Install
pump check disc, disc retainer, and lock
ring.
n.
Install
metering rod and pin spring. Connect
metering rod spring.
o.
Check
and if necessary correct meter ing rod adjustment. Follow procedure of
Par.
E-16.
p.
Install
needle
seat and gasket assembly, needle,
float
and
float pin. The
stop
shoulder on the float
pin
must be on the side away from the bore of
the carburetor.
q.
Set float level to specifications. Follow pro cedure of
Par.
E-12.
r.
Install
air horn gasket and air horn assembly.
Install
attaching screws, lock washers, and choke
tube clamp assembly. Tighten center screws first,
s. Slide choke shaft and lever assembly into place
and
connect choke lever
spring.
Install
choke valve.
Center
the valve by tapping lightly, then hold in
place with fingers when tightening screws,
t.
Install
fast-idle connector rod with
offset
portion
of rod on top and pin spring on outside.
Install
fast-idle connecting rod spring.
E-23.
Correcting Acceleration
Flat
Spot
Early
production
Carburetor
Models 938-S, 938-
SA,
938-SC
Inasmuch
as a flat
spot
on acceleration or low speed
stumble can
come
from causes other than
car
buretor
malfunction, it is recommended that
engine
tuning be thoroughly checked before attempting
any
actual carburetor work. Make sure that
ignition, compression, and timing are correct and
that fuel pump is supplying enough gas. Also, the F-head
engine
employs a water-heated intake
manifold.
Proper vaporization of the fuel depends
on correct intake manifold temperature. Since this
temperature is controlled by the cooling system
thermostat, include an operational check of the
thermostat when diagnosing the stumble. Operating
temperatures consistently below
155°F.
can cause stumble.
If
the stumble persists, a
YF-938-S,
YF-938-SA,
or
YF-938-SC
carburetor can be converted to a
YF-938-SD
carburetor by installing Special Kit
924161, consisting of a pump discharge check
needle, a metering rod, and a metering rod jet. If this kit is installed, the pump discharge check
needle
replaces the original
ball,
weight, and re
tainer
and the small wire-type retainer used with
the
ball
check assembly must not be reinstalled.
When
installing the kit, check the size of the pump discharge jet, No. 2, Fig. E-14.
Early
production
YF-938S
and
YF-938SA
carburetors have a .025" [0,635 mm.] jet installed. If the carburetor being
converted has a .025" jet it must be opened up to .031" [0,787 mm.] by running a No. 68
drill
through
the jet as shown in
Fig.
E-14.
The jet must be drilled
as it is a pressed in part and cannot be replaced.
Upon
completing the installation of the conversion
kit,
mark
or tag the carburetor to indicate that it
is a
YF-938SD.
118
Page 119 of 376
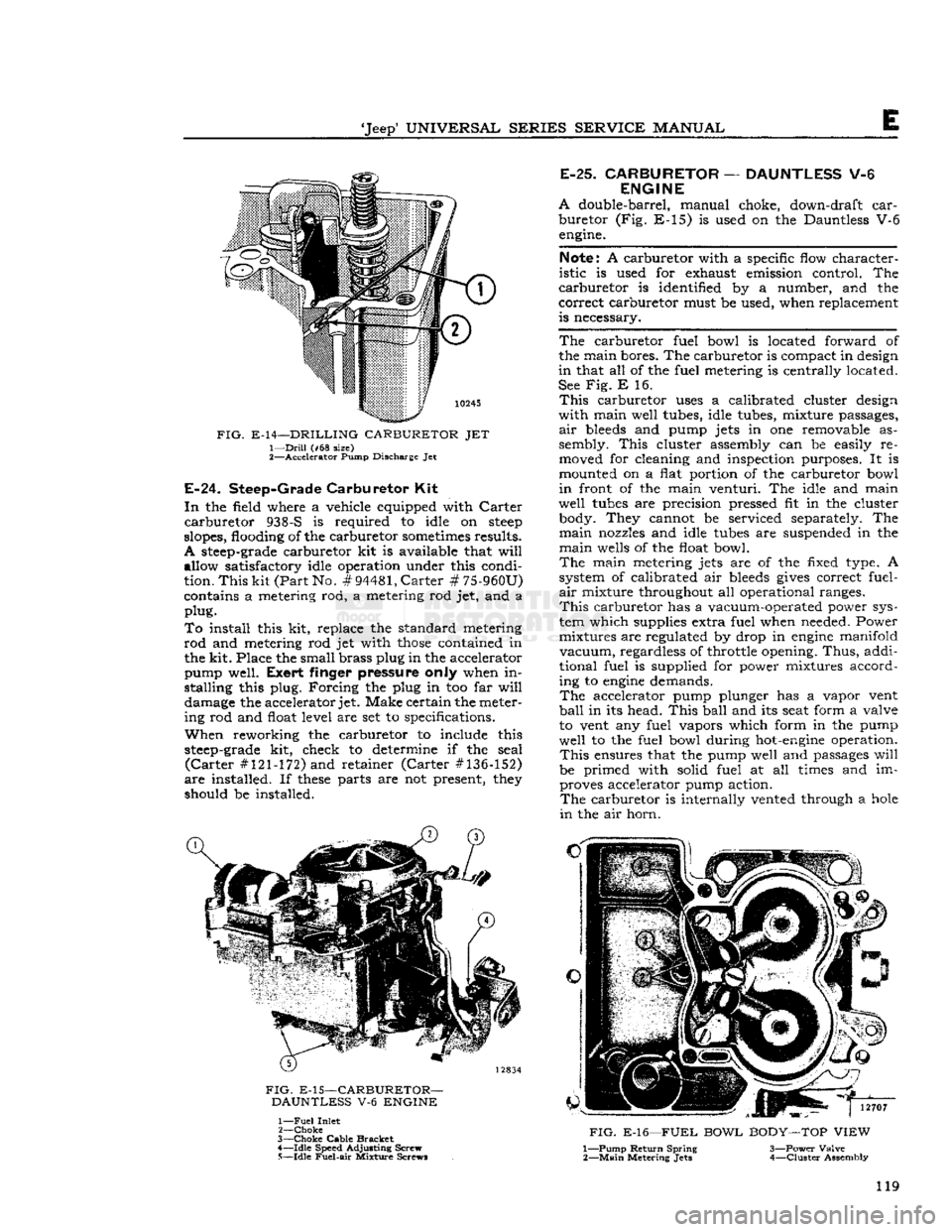
'Jeep'
UNIVERSAL
SERIES SERVICE
MANUAL
E
FIG.
E-14—DRILLING CARBURETOR JET 1—
Drill
(#68 size)
2—
Accelerator
Pump Discharge Jet
E-24.
Steep-Grade
Carburetor
Kit
In
the
field
where a vehicle equipped
with
Carter carburetor 938-S is required to
idle
on
steep
slopes,
flooding
of the carburetor sometimes results.
A
steep-grade
carburetor kit is available that
will
allow satisfactory
idle
operation under this condi
tion.
This kit (Part
No.
#94481,
Carter # 75-960U)
contains a metering rod, a metering rod jet, and a
plug.
To
install
this kit, replace the standard metering
rod
and metering rod jet
with
those
contained in the
kit.
Place the small
brass
plug
in the accelerator
pump
well.
Exert
finger pressure only when in
stalling
this
plug.
Forcing the
plug
in too far
will
damage
the accelerator
jet.
Make certain the meter
ing
rod and
float
level
are set to specifications.
When
reworking
the carburetor to include this
steep-grade
kit, check to determine if the seal (Carter #121-172) and retainer (Carter #136-152)
are installed. If
these
parts are not present, they
should
be installed.
FIG.
E-15—CARBURETOR-
DAUNTLESS V-6 ENGINE 1—
Fuel
Inlet
2—
Choke
3—
Choke
Cable
Bracket
4—
Idle
Speed Adjusting Screw 5—
Idle
Fuel-air
Mixture Screws
E-25.
CARBURETOR
—
DAUNTLESS
V-6
ENGINE
A
double-barrel, manual choke, down-draft car
buretor (Fig. E-15) is used on the Dauntless V-6 engine.
Note: A carburetor
with
a specific
flow
character
istic
is used for exhaust emission
control.
The
carburetor is
identified
by a number, and the
correct carburetor must be used, when replacement
is
necessary.
The carburetor
fuel
bowl
is located
forward
of
the main bores. The carburetor is compact in design
in
that all of the
fuel
metering is centrally located.
See Fig. E 16.
This
carburetor
uses
a calibrated cluster design
with
main
well
tubes,
idle
tubes, mixture
passages,
air
bleeds and pump jets in one removable as
sembly.
This cluster assembly can be easily re
moved
for cleaning and inspection purposes. It is
mounted
on a
flat
portion
of the carburetor
bowl
in
front
of the main
venturi.
The
idle
and main
well
tubes
are precision
pressed
fit in the cluster
body.
They cannot be serviced separately. The
main
nozzles and
idle
tubes
are
suspended
in the
main
wells of the
float
bowl.
The main metering jets are of the
fixed
type. A
system of calibrated air bleeds gives correct
fuel-
air
mixture throughout all operational
ranges.
This
carburetor has a vacuum-operated power sys
tem
which
supplies extra
fuel
when needed. Power
mixtures
are regulated by drop in engine
manifold
vacuum,
regardless of throttle opening. Thus, addi
tional
fuel
is supplied for power mixtures accord
ing
to engine demands.
The accelerator pump plunger has a vapor vent
ball
in its head. This
ball
and its
seat
form
a valve
to
vent any
fuel
vapors
which
form
in the pump
well
to the
fuel
bowl
during hot-engine operation.
This
ensures
that the pump
well
and
passages
will
be primed
with
solid
fuel
at all times and im proves accelerator pump action. The carburetor is
internally
vented through a hole
in
the air horn.
FIG.
E-16—FUEL BOWL BODY—TOP VIEW
1— Pump Return Spring 3—Power
Valve
2—
Main
Metering
Jets
4—Cluster Assembly
119
Page 121 of 376
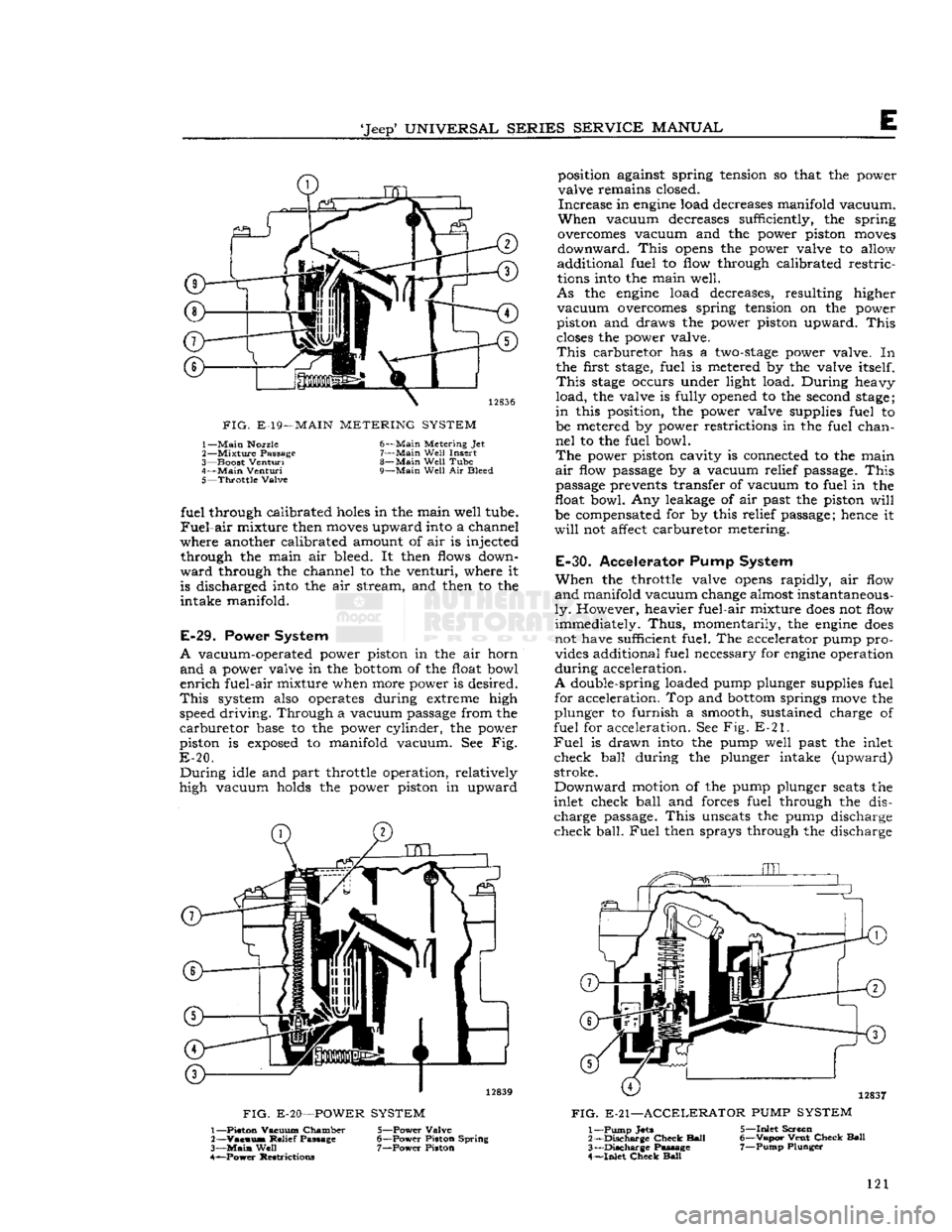
'Jeep'
UNIVERSAL SERIES SERVICE
MANUAL
FIG.
E-19—
MAIN
METERING SYSTEM
1—
Main
Nozzle
2—
Mixture
Passage
3—
Boost
Venturi
4—
Main
Venturi
5—
Throttle
Valve 6—
Main
Metering Jet
7—
Main
Well
Insert
8—
Main
Well
Tube
9—
Main
Well
Air Bleed fuel through calibrated
holes
in the main well tube.
Fuel-air
mixture then
moves
upward into a channel
where another calibrated amount of air is injected through the main air bleed. It then flows down
ward
through the channel to the venturi, where it is discharged into the air stream, and then to the
intake manifold.
E-29.
Power System
A
vacuum-operated power piston in the air horn
and
a power valve in the
bottom
of the float bowl
enrich
fuel-air mixture when more power is desired.
This
system also operates during extreme high
speed driving. Through a vacuum passage from the
carburetor
base to the power cylinder, the power
piston is
exposed
to manifold vacuum. See Fig.
E-20.
During
idle and part throttle operation, relatively
high vacuum holds the power piston in upward
FIG.
E-20—POWER
SYSTEM
position against spring tension so that the power
valve remains closed.
Increase
in
engine
load decreases manifold vacuum.
When
vacuum decreases sufficiently, the spring
overcomes vacuum and the power piston
moves
downward.
This
opens
the power valve to allow
additional fuel to flow through calibrated restric
tions into the main well.
As
the
engine
load decreases, resulting higher
vacuum
overcomes spring tension on the power
piston and draws the power piston upward.
This
closes
the power valve.
This
carburetor has a
two-stage
power valve. In
the first
stage,
fuel is metered by the valve itself.
This
stage
occurs under light load. During heavy
load,
the valve is fully opened to the second
stage;
in
this position, the power valve supplies fuel to
be metered by power restrictions in the fuel chan
nel
to the fuel bowl.
The
power piston cavity is connected to the main
air
flow passage by a vacuum relief passage.
This
passage prevents transfer of vacuum to fuel in the
float bowl. Any leakage of air past the piston
will
be compensated for by this relief passage; hence it
will
not affect carburetor metering.
E-30.
Accelerator Pump System
When
the throttle valve
opens
rapidly, air flow
and
manifold vacuum change almost instantaneous
ly.
However, heavier fuel-air mixture
does
not flow immediately.
Thus,
momentarily, the
engine
does
not have sufficient fuel. The accelerator pump pro vides additional fuel necessary for
engine
operation
during
acceleration.
A
double-spring loaded pump plunger supplies fuel for acceleration. Top and
bottom
springs
move
the
plunger to furnish a smooth, sustained charge of
fuel for acceleration. See Fig. E-21.
Fuel
is drawn into the pump well past the inlet
check ball during the plunger intake (upward)
stroke.
Downward
motion of the pump plunger
seats
the
inlet check ball and forces fuel through the dis charge
passage.
This
unseats
the pump discharge
check
ball.
Fuel
then sprays through the discharge
12837
FIG.
E-21—ACCELERATOR
PUMP
SYSTEM
1— Piston Vacuum Chamber
2—
Vacuus*
Relief Passage
3—
Main
Well
4— ^Power Restrictions 5— Power Valve
6— Power Piston Spring 7— Power Piston 1— Pump
Jets
2—
Discharge
Check
Ball
3—
Discharge
Passage
4—
Inlet
Check
Ball
5—
Inlet
Screen
6—
Vapor
Vent
Check
Ball
7—
Pump
Plunger
121
Page 122 of 376
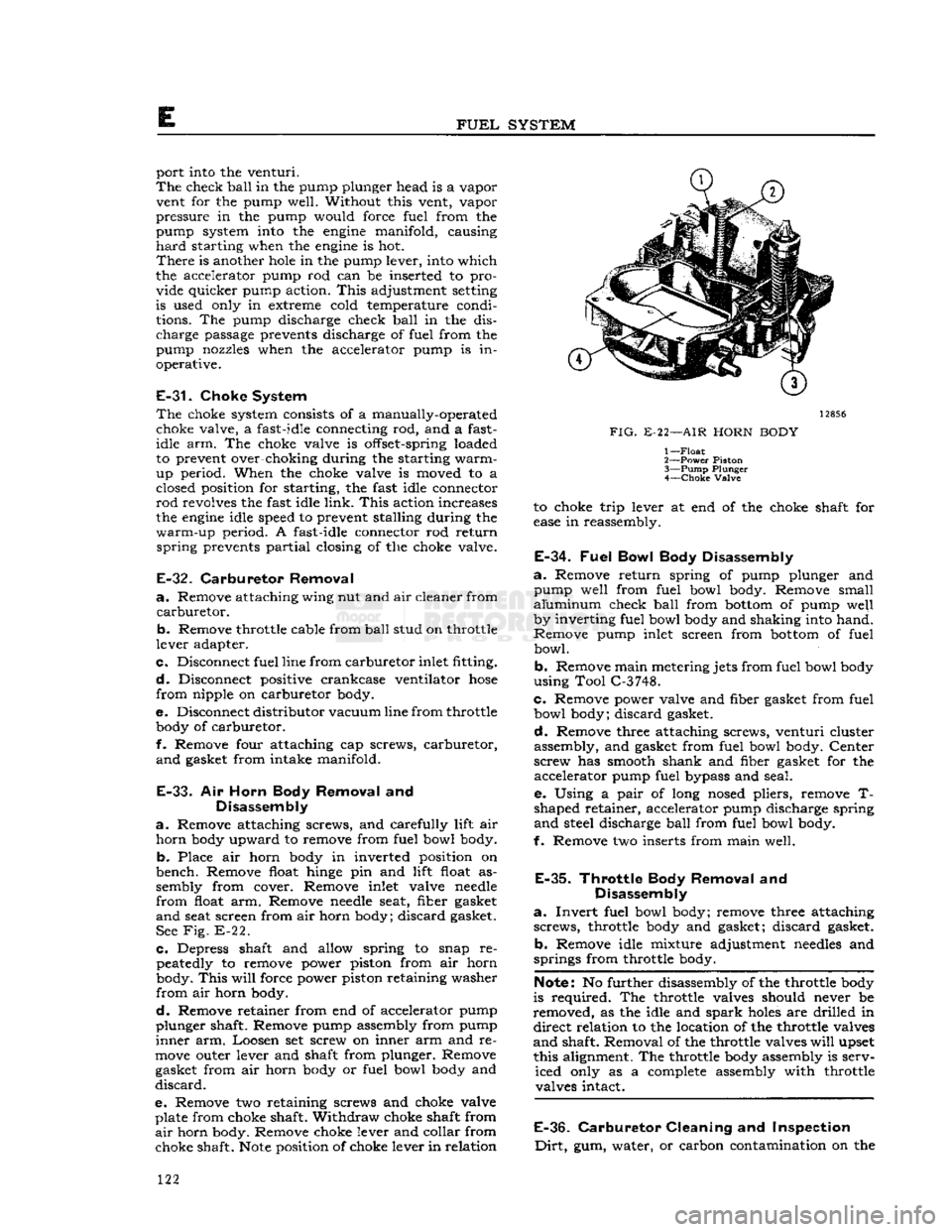
E
FUEL
SYSTEM
port into the venturi.
The
check
ball
in the pump plunger head is a vapor
vent for the pump well. Without this vent, vapor
pressure in the pump would force fuel from the
pump system into the
engine
manifold, causing
hard
starting when the
engine
is hot.
There
is another
hole
in the pump lever, into which
the accelerator pump rod can be inserted to pro vide quicker pump action.
This
adjustment setting
is used only in extreme cold temperature condi tions. The pump discharge check
ball
in the dis
charge passage prevents discharge of fuel from the
pump nozzles when the accelerator pump is in
operative.
E-31.
Choke System
The
choke system consists of a manually-operated
choke valve, a fast-idle connecting rod, and a fast-
idle arm. The choke valve is offset-spring loaded
to prevent over-choking during the starting
warm-
up period. When the choke valve is moved to a
closed position for starting, the fast idle connector
rod
revolves the fast idle
link.
This
action increases
the
engine
idle speed to prevent stalling during the
warm-up
period. A fast-idle connector rod return
spring
prevents
partial
closing of the choke valve.
E-32.
Carburetor
Removal
a.
Remove attaching wing nut and air cleaner from
carburetor.
b. Remove throttle cable from
ball
stud on throttle
lever adapter.
c.
Disconnect fuel line from carburetor inlet fitting.
d.
Disconnect positive crankcase ventilator
hose
from
nipple on carburetor body.
e. Disconnect distributor vacuum line from throttle body of carburetor.
f. Remove four attaching cap screws, carburetor,
and
gasket from intake manifold.
E-33.
Air
Horn
Body Removal and Disassembly
a.
Remove attaching screws, and carefully lift air
horn
body upward to remove from fuel bowl body.
b. Place air horn body in inverted position on
bench. Remove float hinge pin and lift float as sembly from cover. Remove inlet valve
needle
from
float arm. Remove
needle
seat, fiber gasket
and
seat screen from air horn body; discard gasket. See Fig. E-22.
c.
Depress shaft and allow spring to snap re peatedly to remove power piston from air horn body.
This
will
force power piston retaining washer
from
air horn body.
d.
Remove retainer from end of accelerator pump
plunger shaft. Remove pump assembly from pump
inner
arm. Loosen set screw on inner arm and re
move
outer lever and shaft from plunger. Remove gasket from air horn body or fuel bowl body and
discard.
e. Remove two retaining screws and choke valve plate from choke shaft. Withdraw choke shaft from
air
horn body. Remove choke lever and collar from
choke shaft.
Note
position of choke lever in relation
12856
FIG.
E-22—AIR HORN BODY
1
—
Float
2— Power Piston
3—
Pump
Plunger
4—
Choke
Valve to choke trip lever at end of the choke shaft for
ease
in reassembly.
E-34.
Fuel
Bowl Body Disassembly
a.
Remove return spring of pump plunger and pump well from fuel bowl body. Remove small
aluminum
check
ball
from
bottom
of pump well
by inverting fuel bowl body and shaking into hand. Remove pump inlet screen from
bottom
of fuel bowl.
b. Remove main metering jets from fuel bowl body
using Tool C-3748.
c.
Remove power valve and fiber gasket from fuel bowl body; discard gasket.
d.
Remove three attaching screws, venturi cluster
assembly, and gasket from fuel bowl body. Center
screw has smooth shank and fiber gasket for the accelerator pump fuel bypass and seal.
e. Using a
pair
of long nosed pliers, remove T-
shaped retainer, accelerator pump discharge spring
and
steel discharge
ball
from fuel bowl body.
f. Remove two inserts from main well.
E-35.
Throttle Body Removal and Disassembly
a.
Invert
fuel bowl body; remove three attaching
screws,
throttle body and gasket; discard gasket.
b. Remove idle mixture adjustment
needles
and
springs from throttle body.
Note:
No further disassembly of the throttle body
is required. The throttle valves should never be
removed, as the idle and
spark
holes
are drilled in
direct
relation to the location of the throttle valves
and
shaft. Removal of the throttle valves
will
upset
this alignment. The throttle body assembly is serv iced only as a complete assembly with throttle valves intact.
E-36.
Carburetor
Cleaning and Inspection
Dirt,
gum, water, or carbon contamination on the 122
Page 125 of 376
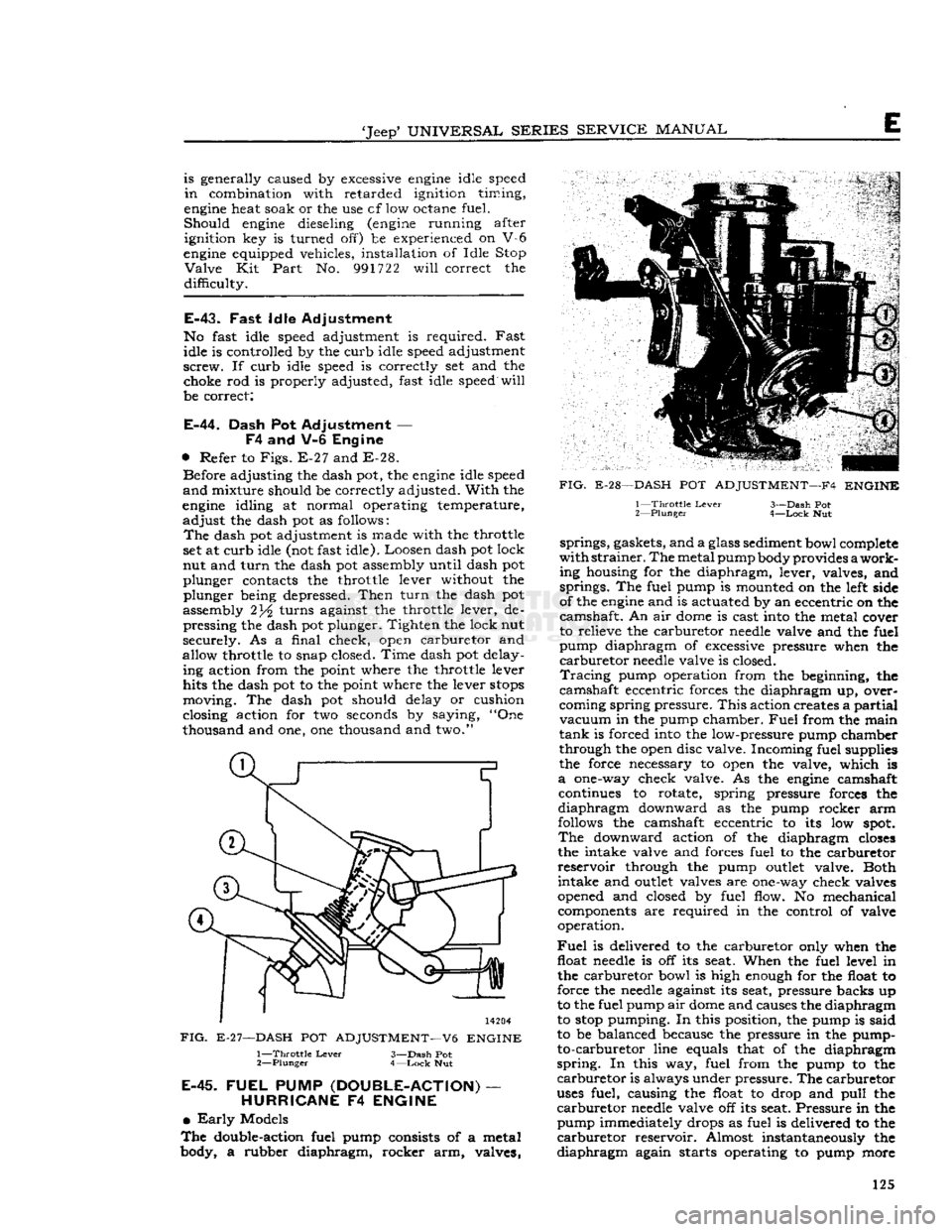
'Jeep'
UNIVERSAL
SERIES
SERVICE
MANUAL
E
is generally caused by excessive
engine
idle speed
in
combination with retarded ignition timing,
engine
heat soak or the use cf low octane fuel.
Should
engine
dieseling
(engine
running after ignition key is turned off) be experienced on V-6
engine
equipped vehicles, installation of Idle Stop
Valve
Kit
Part
No.
991722
will
correct the
difficulty.
E-43.
Fast
Idle Adjustment
No fast idle speed adjustment is required.
Fast
idle is controlled by the curb idle speed adjustment
screw.
If curb idle speed is correctly set and the choke rod is properly adjusted, fast idle speed
will
be correct;
E-44.
Dash Pot Adjustment —
F4
and V-6 Engine
•
Refer to
Figs.
E-27 and E-28. Before adjusting the dash pot, the
engine
idle speed
and
mixture should be correctly adjusted.
With
the
engine
idling at normal operating temperature,
adjust
the dash pot as follows:
The
dash pot adjustment is made with the throttle
set at curb idle (not fast idle). Loosen dash pot lock
nut and
turn
the dash pot assembly until dash pot
plunger contacts the throttle lever without the plunger being depressed.
Then
turn
the dash pot
assembly 2turns against the throttle lever, de pressing the dash pot plunger. Tighten the lock nut
securely. As a final check, open carburetor and
allow throttle to snap closed. Time dash pot delay ing action from the point where the throttle lever
hits the dash pot to the point where the lever
stops
moving. The dash pot should delay or cushion
closing action for two seconds by saying, "One
thousand and one, one thousand and two."
14204
FIG.
E-27—DASH
POT
ADJUSTMENT—V6
ENGINE
1—
Throttle
Lever
3—Dash Pot
2—
Plunger
4—Lock
Nut
E-45.
FUEL
PUMP
(DOUBLE-ACTION)
—
HURRICANE
F4
ENGINE
•
Early
Models
The
double-action fuel pump consists of a metal
body, a rubber diaphragm, rocker arm, valves,
FIG.
E-28—DASH
POT
ADJUSTMENT—F4
ENGINE
1—
Throttle
Lever
3—Dash Pot
2—
Plunger
4—Lock
Nut springs, gaskets, and a glass sediment bowl complete
with
strainer.
The
metal pump body provides
a
work
ing housing for the diaphragm, lever, valves, and springs. The fuel pump is mounted on the left side
of the
engine
and is actuated by an eccentric on the
camshaft. An air
dome
is cast into the metal cover
to relieve the carburetor
needle
valve and the fuel
pump diaphragm of excessive pressure when the
carburetor
needle
valve is closed.
Tracing
pump operation from the beginning, the
camshaft eccentric forces the diaphragm up, over
coming spring pressure.
This
action creates a
partial
vacuum
in the pump chamber.
Fuel
from the main
tank
is forced into the low-pressure pump chamber
through the open disc valve. Incoming fuel supplies
the force necessary to open the valve, which is
a
one-way check valve. As the
engine
camshaft continues to rotate, spring pressure forces the
diaphragm
downward as the pump rocker arm
follows the camshaft eccentric to its low
spot.
The
downward action of the diaphragm
closes
the intake valve and forces fuel to the carburetor
reservoir
through the pump
outlet
valve. Both intake and
outlet
valves are one-way check valves
opened and closed by fuel flow. No mechanical components are required in the control of valve
operation.
Fuel
is delivered to the carburetor only when the float
needle
is off its seat. When the fuel level in the carburetor bowl is high enough for the float to
force the
needle
against its seat, pressure backs up
to the fuel pump air
dome
and causes the diaphragm
to
stop
pumping. In this position, the pump is said
to be balanced because the pressure in the pump- to-carburetor line equals that of the diaphragm
spring.
In this way, fuel from the pump to the
carburetor
is always under pressure. The carburetor
uses
fuel, causing the float to drop and
pull
the
carburetor
needle
valve off its seat. Pressure in the pump immediately drops as fuel is delivered to the
carburetor
reservoir. Almost instantaneously the
diaphragm
again starts operating to pump more 125
Page 126 of 376
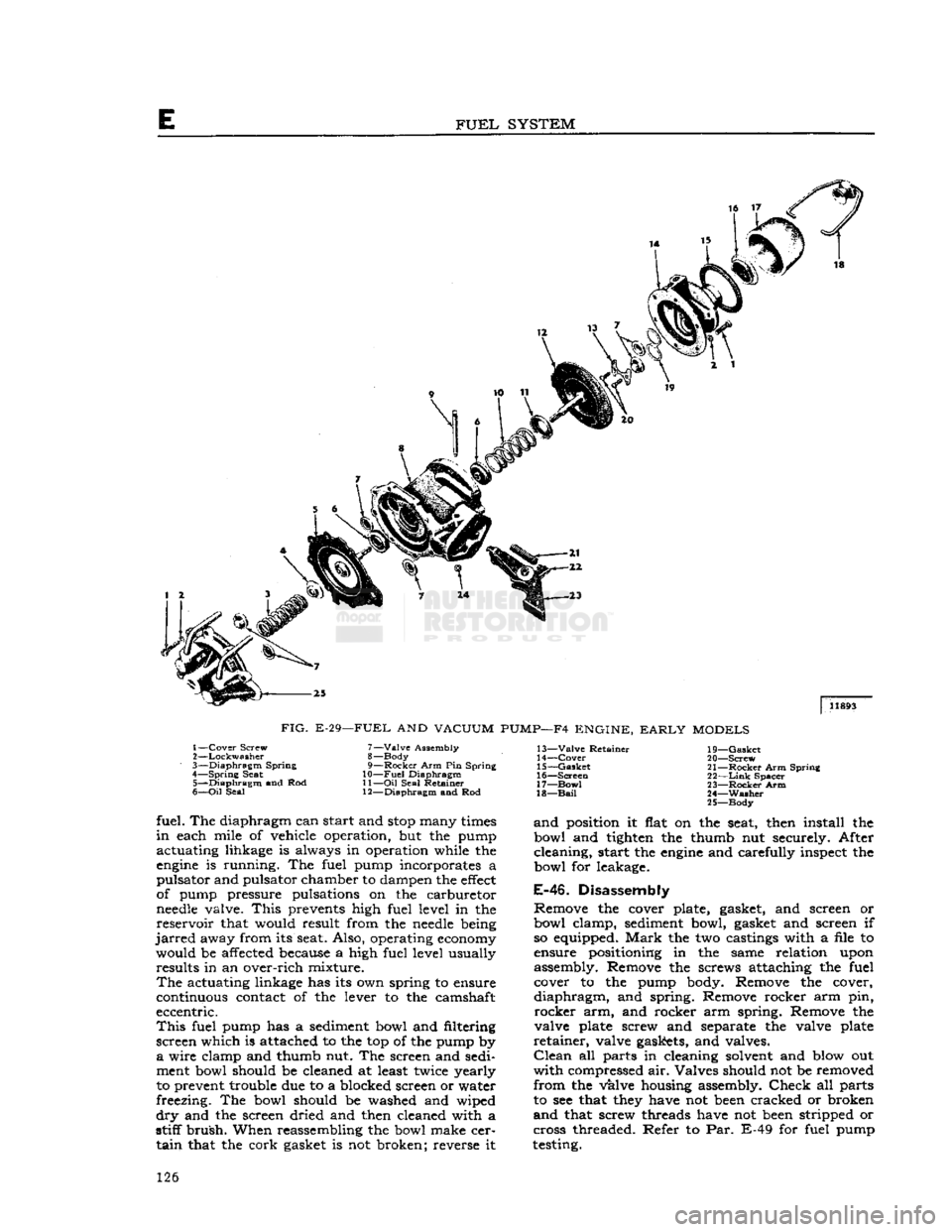
FUEL
SYSTEM
|
11893
FIG.
E-29—FUEL
AND
VACUUM
PUMP—F4
ENGINE,
EARLY
MODELS
1—
Cover
Screw
2—
Lockwasher
3—
Diaphragm
Spring
4—
Spring
Seat 5—
Diaphragm
and Rod
6—
Oil
Seal 7—
Valve
Assembly
8— Body
9—
Rocker
Arm Pin Spring
10—
Fuel
Diaphragm
11—
Oil
Seal Retainer
12—
Diaphragm
and Rod 13—
Valve
Retainer
14—
Cover
15—
Gasket
16—
Screen
17—
Bow!
18—
Bail
19—
Gasket
20—
Screw
21—
Rocker
Arm Spring
22—
Link
Spacer
23—
Rocker
Arm
24—
Washer
25—
Body
fuel. The diaphragm can start and
stop
many
times
in
each mile of vehicle operation, but the pump
actuating lihkage is always in operation while the
engine
is running. The fuel pump incorporates a
pulsator and pulsator chamber to dampen the
effect
of pump pressure pulsations on the carburetor
needle
valve.
This
prevents high fuel level in the
reservoir
that would result from the
needle
being
jarred
away from its seat. Also, operating
economy
would be affected because a high fuel level usually results in an over-rich mixture.
The
actuating linkage has its own spring to ensure
continuous contact of the lever to the camshaft
eccentric.
This
fuel pump has a sediment bowl and filtering
screen which is attached to the top of the pump by
a
wire clamp and thumb nut. The screen and sedi
ment bowl should be cleaned at least twice yearly
to prevent trouble due to a blocked screen or water
freezing. The bowl should be washed and wiped
dry
and the screen dried and then cleaned with a
stiff
brush.
When reassembling the bowl make cer
tain
that the cork gasket is not broken; reverse it
and
position it flat on the seat, then install the
bowl and tighten the thumb nut securely. After
cleaning, start the
engine
and carefully inspect the
bowl for leakage.
E-46.
Disassembly
Remove the cover plate, gasket, and screen or
bowl clamp, sediment bowl, gasket and screen if so equipped.
Mark
the two castings with a file to
ensure positioning in the same relation upon
assembly. Remove the screws attaching the fuel cover to the pump body. Remove the cover,
diaphragm,
and spring. Remove rocker arm pin,
rocker
arm, and rocker arm spring. Remove the
valve plate screw and separate the valve plate
retainer,
valve gaskets, and valves.
Clean
all parts in cleaning solvent and blow out
with
compressed air. Valves should not be removed
from
the valve housing assembly.
Check
all parts
to see that
they
have not
been
cracked or broken
and
that screw threads have not
been
stripped or
cross threaded. Refer to Par. E-49 for fuel pump
testing. 126