LAND ROVER DISCOVERY 1995 Workshop Manual
Manufacturer: LAND ROVER, Model Year: 1995, Model line: DISCOVERY, Model: LAND ROVER DISCOVERY 1995Pages: 873, PDF Size: 12.89 MB
Page 311 of 873
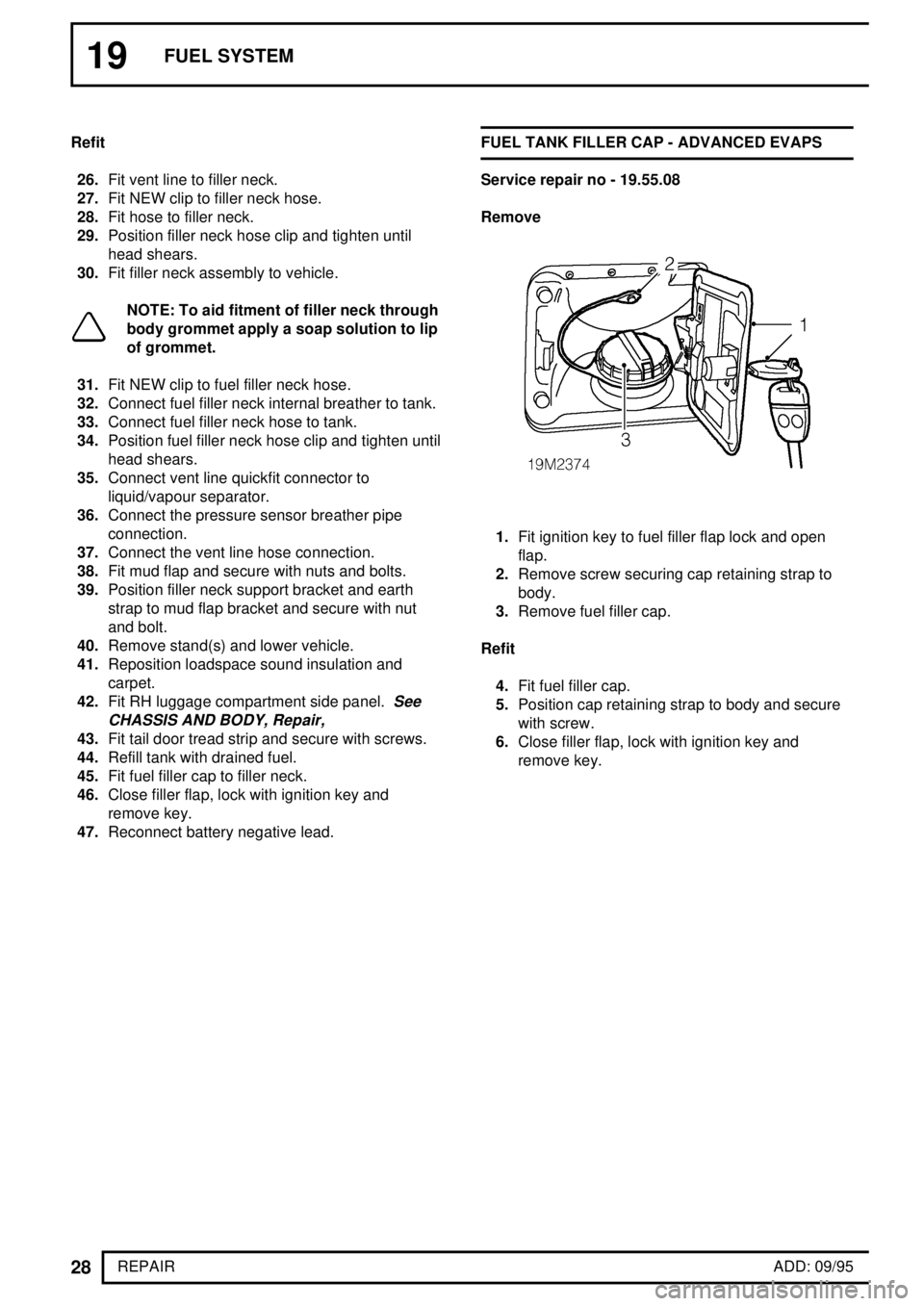
19FUEL SYSTEM
28
REPAIRADD: 09/95 Refit
26.Fit vent line to filler neck.
27.Fit NEW clip to filler neck hose.
28.Fit hose to filler neck.
29.Position filler neck hose clip and tighten until
head shears.
30.Fit filler neck assembly to vehicle.
NOTE: To aid fitment of filler neck through
body grommet apply a soap solution to lip
of grommet.
31.Fit NEW clip to fuel filler neck hose.
32.Connect fuel filler neck internal breather to tank.
33.Connect fuel filler neck hose to tank.
34.Position fuel filler neck hose clip and tighten until
head shears.
35.Connect vent line quickfit connector to
liquid/vapour separator.
36.Connect the pressure sensor breather pipe
connection.
37.Connect the vent line hose connection.
38.Fit mud flap and secure with nuts and bolts.
39.Position filler neck support bracket and earth
strap to mud flap bracket and secure with nut
and bolt.
40.Remove stand(s) and lower vehicle.
41.Reposition loadspace sound insulation and
carpet.
42.Fit RH luggage compartment side panel.
See
CHASSIS AND BODY, Repair,
43.Fit tail door tread strip and secure with screws.
44.Refill tank with drained fuel.
45.Fit fuel filler cap to filler neck.
46.Close filler flap, lock with ignition key and
remove key.
47.Reconnect battery negative lead.FUEL TANK FILLER CAP - ADVANCED EVAPS
Service repair no - 19.55.08
Remove
1.Fit ignition key to fuel filler flap lock and open
flap.
2.Remove screw securing cap retaining strap to
body.
3.Remove fuel filler cap.
Refit
4.Fit fuel filler cap.
5.Position cap retaining strap to body and secure
with screw.
6.Close filler flap, lock with ignition key and
remove key.
Page 312 of 873
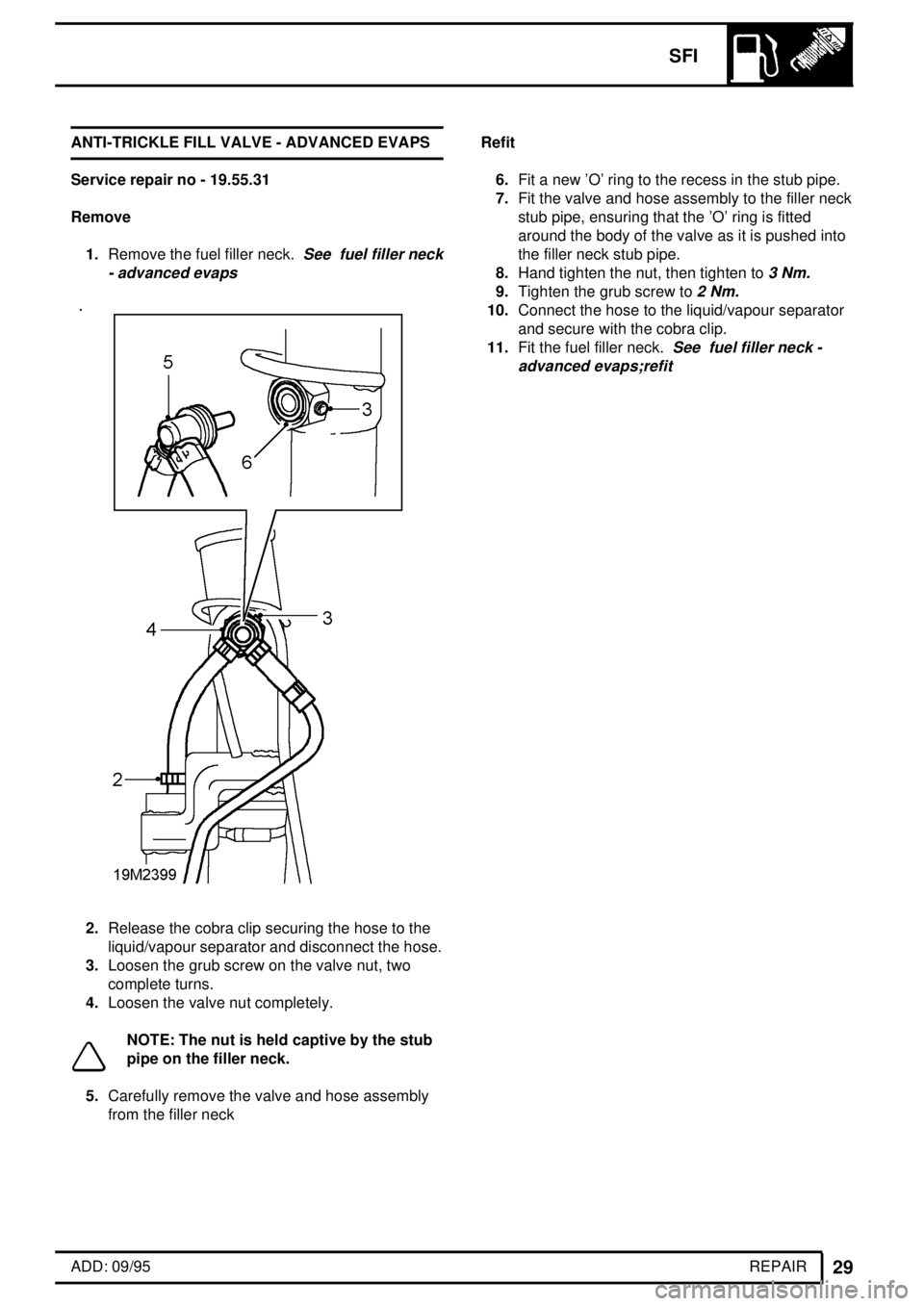
SFI
29
REPAIR ADD: 09/95 ANTI-TRICKLE FILL VALVE - ADVANCED EVAPS
Service repair no - 19.55.31
Remove
1.Remove the fuel filler neck.
See fuel filler neck
- advanced evaps
2.Release the cobra clip securing the hose to the
liquid/vapour separator and disconnect the hose.
3.Loosen the grub screw on the valve nut, two
complete turns.
4.Loosen the valve nut completely.
NOTE: The nut is held captive by the stub
pipe on the filler neck.
5.Carefully remove the valve and hose assembly
from the filler neckRefit
6.Fit a new 'O' ring to the recess in the stub pipe.
7.Fit the valve and hose assembly to the filler neck
stub pipe, ensuring that the 'O' ring is fitted
around the body of the valve as it is pushed into
the filler neck stub pipe.
8.Hand tighten the nut, then tighten to
3 Nm.
9.Tighten the grub screw to2 Nm.
10.Connect the hose to the liquid/vapour separator
and secure with the cobra clip.
11.Fit the fuel filler neck.
See fuel filler neck -
advanced evaps;refit
Page 313 of 873
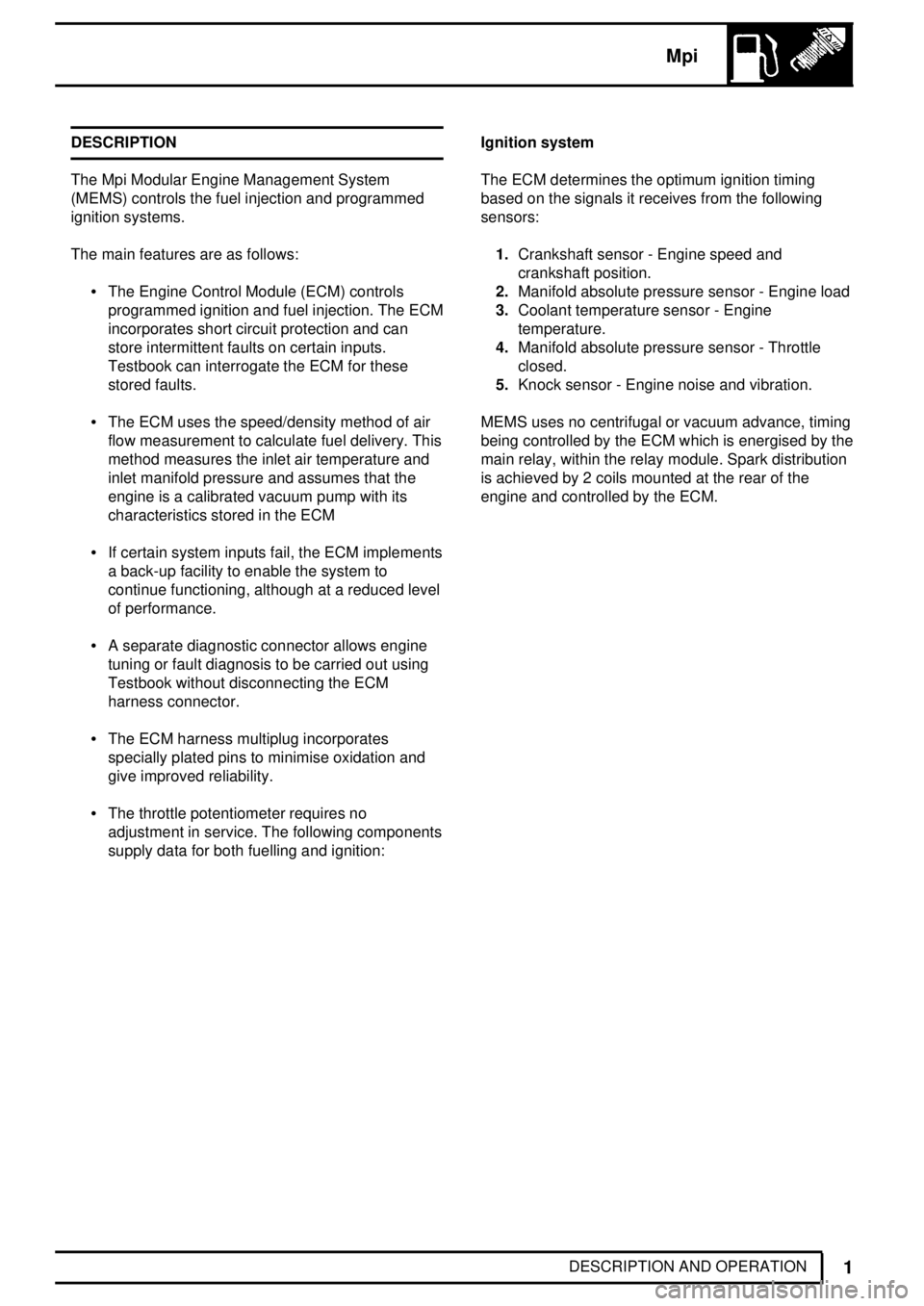
Mpi
1
DESCRIPTION AND OPERATION DESCRIPTION
The Mpi Modular Engine Management System
(MEMS) controls the fuel injection and programmed
ignition systems.
The main features are as follows:
·The Engine Control Module (ECM) controls
programmed ignition and fuel injection. The ECM
incorporates short circuit protection and can
store intermittent faults on certain inputs.
Testbook can interrogate the ECM for these
stored faults.
·The ECM uses the speed/density method of air
flow measurement to calculate fuel delivery. This
method measures the inlet air temperature and
inlet manifold pressure and assumes that the
engine is a calibrated vacuum pump with its
characteristics stored in the ECM
·If certain system inputs fail, the ECM implements
a back-up facility to enable the system to
continue functioning, although at a reduced level
of performance.
·A separate diagnostic connector allows engine
tuning or fault diagnosis to be carried out using
Testbook without disconnecting the ECM
harness connector.
·The ECM harness multiplug incorporates
specially plated pins to minimise oxidation and
give improved reliability.
·The throttle potentiometer requires no
adjustment in service. The following components
supply data for both fuelling and ignition:Ignition system
The ECM determines the optimum ignition timing
based on the signals it receives from the following
sensors:
1.Crankshaft sensor - Engine speed and
crankshaft position.
2.Manifold absolute pressure sensor - Engine load
3.Coolant temperature sensor - Engine
temperature.
4.Manifold absolute pressure sensor - Throttle
closed.
5.Knock sensor - Engine noise and vibration.
MEMS uses no centrifugal or vacuum advance, timing
being controlled by the ECM which is energised by the
main relay, within the relay module. Spark distribution
is achieved by 2 coils mounted at the rear of the
engine and controlled by the ECM.
Page 314 of 873
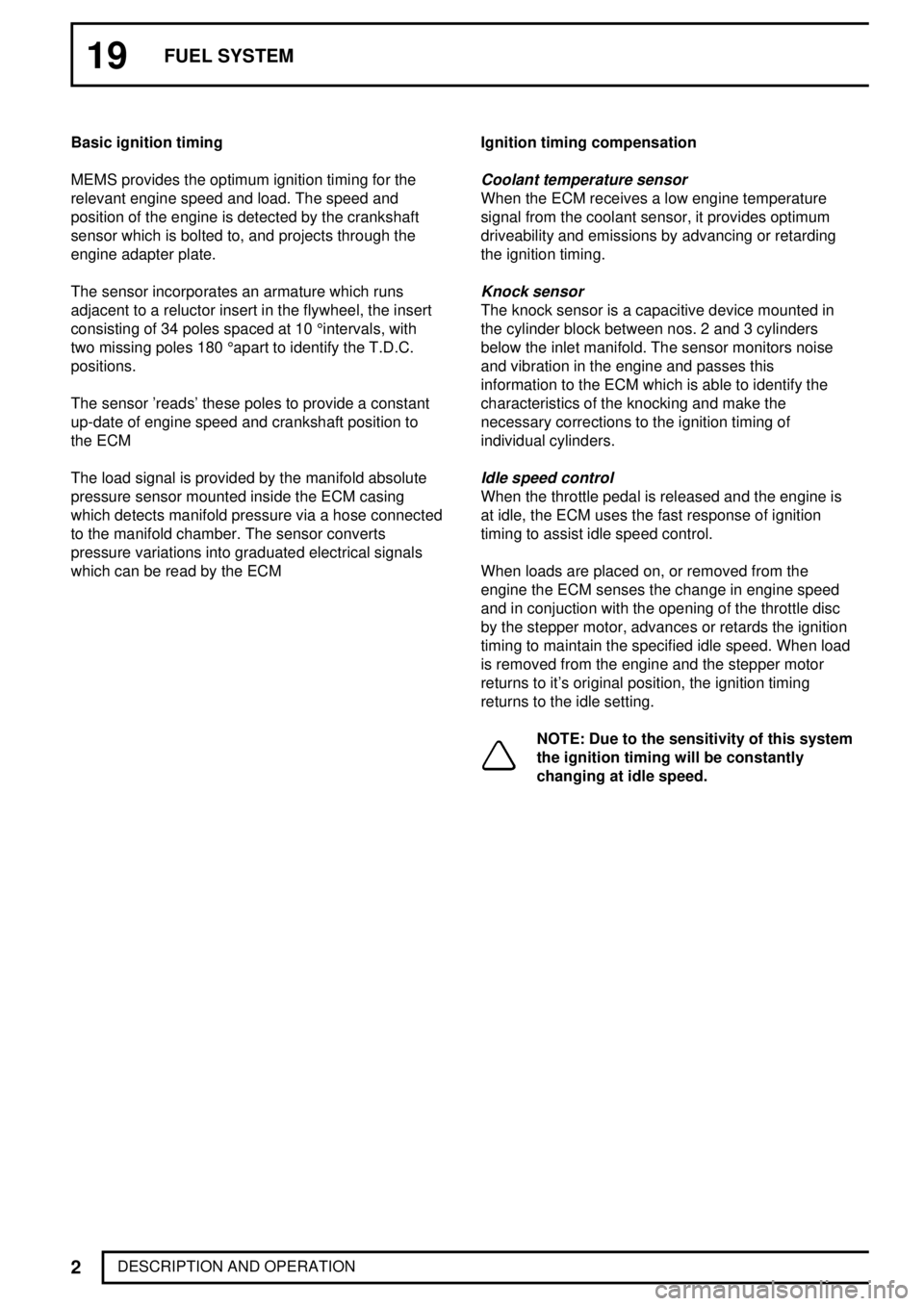
19FUEL SYSTEM
2
DESCRIPTION AND OPERATION Basic ignition timing
MEMS provides the optimum ignition timing for the
relevant engine speed and load. The speed and
position of the engine is detected by the crankshaft
sensor which is bolted to, and projects through the
engine adapter plate.
The sensor incorporates an armature which runs
adjacent to a reluctor insert in the flywheel, the insert
consisting of 34 poles spaced at 10°intervals, with
two missing poles 180°apart to identify the T.D.C.
positions.
The sensor 'reads' these poles to provide a constant
up-date of engine speed and crankshaft position to
the ECM
The load signal is provided by the manifold absolute
pressure sensor mounted inside the ECM casing
which detects manifold pressure via a hose connected
to the manifold chamber. The sensor converts
pressure variations into graduated electrical signals
which can be read by the ECMIgnition timing compensation
Coolant temperature sensor
When the ECM receives a low engine temperature
signal from the coolant sensor, it provides optimum
driveability and emissions by advancing or retarding
the ignition timing.
Knock sensor
The knock sensor is a capacitive device mounted in
the cylinder block between nos. 2 and 3 cylinders
below the inlet manifold. The sensor monitors noise
and vibration in the engine and passes this
information to the ECM which is able to identify the
characteristics of the knocking and make the
necessary corrections to the ignition timing of
individual cylinders.
Idle speed control
When the throttle pedal is released and the engine is
at idle, the ECM uses the fast response of ignition
timing to assist idle speed control.
When loads are placed on, or removed from the
engine the ECM senses the change in engine speed
and in conjuction with the opening of the throttle disc
by the stepper motor, advances or retards the ignition
timing to maintain the specified idle speed. When load
is removed from the engine and the stepper motor
returns to it's original position, the ignition timing
returns to the idle setting.
NOTE: Due to the sensitivity of this system
the ignition timing will be constantly
changing at idle speed.
Page 315 of 873
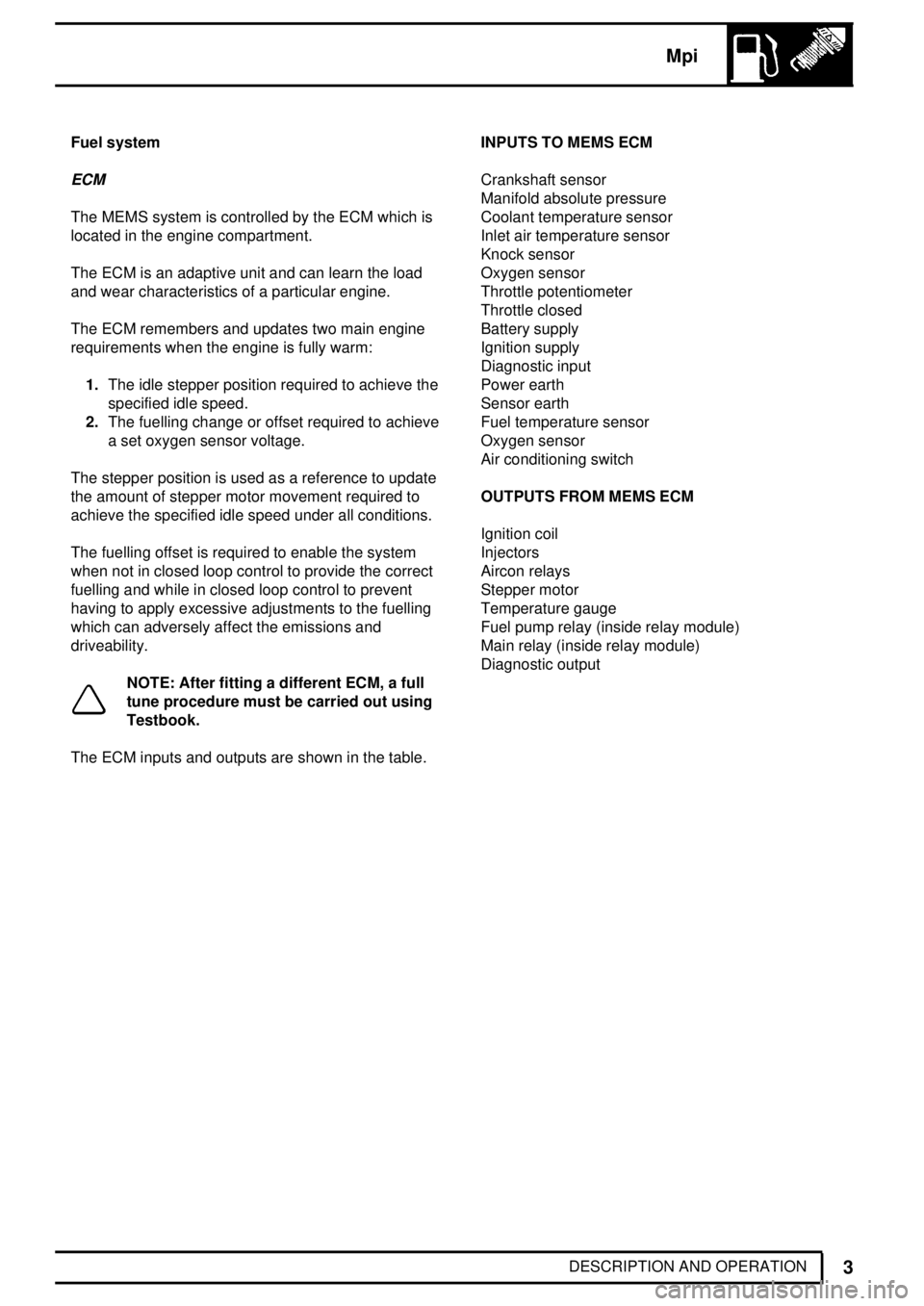
Mpi
3
DESCRIPTION AND OPERATION Fuel system
ECM
The MEMS system is controlled by the ECM which is
located in the engine compartment.
The ECM is an adaptive unit and can learn the load
and wear characteristics of a particular engine.
The ECM remembers and updates two main engine
requirements when the engine is fully warm:
1.The idle stepper position required to achieve the
specified idle speed.
2.The fuelling change or offset required to achieve
a set oxygen sensor voltage.
The stepper position is used as a reference to update
the amount of stepper motor movement required to
achieve the specified idle speed under all conditions.
The fuelling offset is required to enable the system
when not in closed loop control to provide the correct
fuelling and while in closed loop control to prevent
having to apply excessive adjustments to the fuelling
which can adversely affect the emissions and
driveability.
NOTE: After fitting a different ECM, a full
tune procedure must be carried out using
Testbook.
The ECM inputs and outputs are shown in the table.INPUTS TO MEMS ECM
Crankshaft sensor
Manifold absolute pressure
Coolant temperature sensor
Inlet air temperature sensor
Knock sensor
Oxygen sensor
Throttle potentiometer
Throttle closed
Battery supply
Ignition supply
Diagnostic input
Power earth
Sensor earth
Fuel temperature sensor
Oxygen sensor
Air conditioning switch
OUTPUTS FROM MEMS ECM
Ignition coil
Injectors
Aircon relays
Stepper motor
Temperature gauge
Fuel pump relay (inside relay module)
Main relay (inside relay module)
Diagnostic output
Page 316 of 873
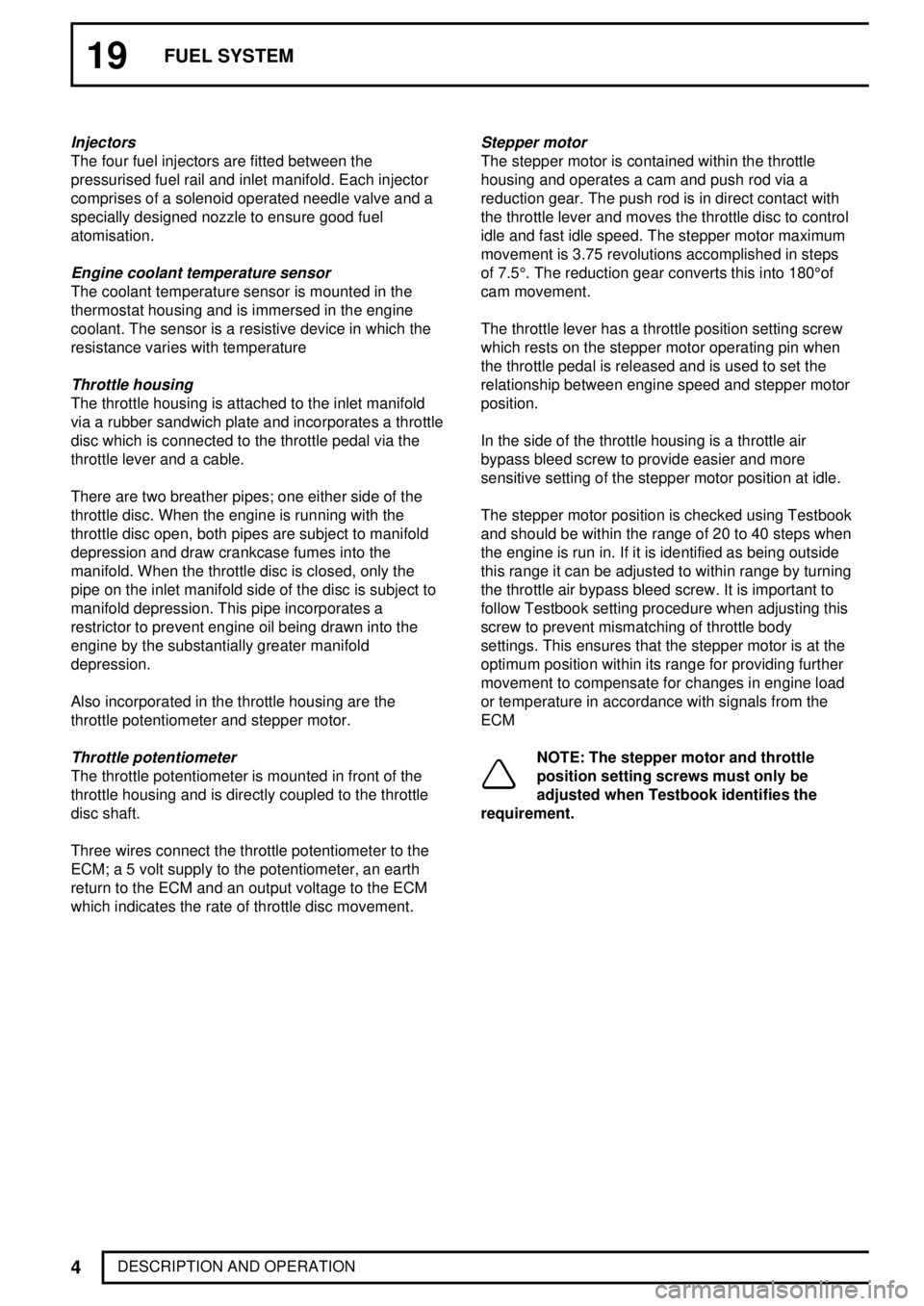
19FUEL SYSTEM
4
DESCRIPTION AND OPERATION
Injectors
The four fuel injectors are fitted between the
pressurised fuel rail and inlet manifold. Each injector
comprises of a solenoid operated needle valve and a
specially designed nozzle to ensure good fuel
atomisation.
Engine coolant temperature sensor
The coolant temperature sensor is mounted in the
thermostat housing and is immersed in the engine
coolant. The sensor is a resistive device in which the
resistance varies with temperature
Throttle housing
The throttle housing is attached to the inlet manifold
via a rubber sandwich plate and incorporates a throttle
disc which is connected to the throttle pedal via the
throttle lever and a cable.
There are two breather pipes; one either side of the
throttle disc. When the engine is running with the
throttle disc open, both pipes are subject to manifold
depression and draw crankcase fumes into the
manifold. When the throttle disc is closed, only the
pipe on the inlet manifold side of the disc is subject to
manifold depression. This pipe incorporates a
restrictor to prevent engine oil being drawn into the
engine by the substantially greater manifold
depression.
Also incorporated in the throttle housing are the
throttle potentiometer and stepper motor.
Throttle potentiometer
The throttle potentiometer is mounted in front of the
throttle housing and is directly coupled to the throttle
disc shaft.
Three wires connect the throttle potentiometer to the
ECM; a 5 volt supply to the potentiometer, an earth
return to the ECM and an output voltage to the ECM
which indicates the rate of throttle disc movement.
Stepper motor
The stepper motor is contained within the throttle
housing and operates a cam and push rod via a
reduction gear. The push rod is in direct contact with
the throttle lever and moves the throttle disc to control
idle and fast idle speed. The stepper motor maximum
movement is 3.75 revolutions accomplished in steps
of 7.5°. The reduction gear converts this into 180°of
cam movement.
The throttle lever has a throttle position setting screw
which rests on the stepper motor operating pin when
the throttle pedal is released and is used to set the
relationship between engine speed and stepper motor
position.
In the side of the throttle housing is a throttle air
bypass bleed screw to provide easier and more
sensitive setting of the stepper motor position at idle.
The stepper motor position is checked using Testbook
and should be within the range of 20 to 40 steps when
the engine is run in. If it is identified as being outside
this range it can be adjusted to within range by turning
the throttle air bypass bleed screw. It is important to
follow Testbook setting procedure when adjusting this
screw to prevent mismatching of throttle body
settings. This ensures that the stepper motor is at the
optimum position within its range for providing further
movement to compensate for changes in engine load
or temperature in accordance with signals from the
ECM
NOTE: The stepper motor and throttle
position setting screws must only be
adjusted when Testbook identifies the
requirement.
Page 317 of 873
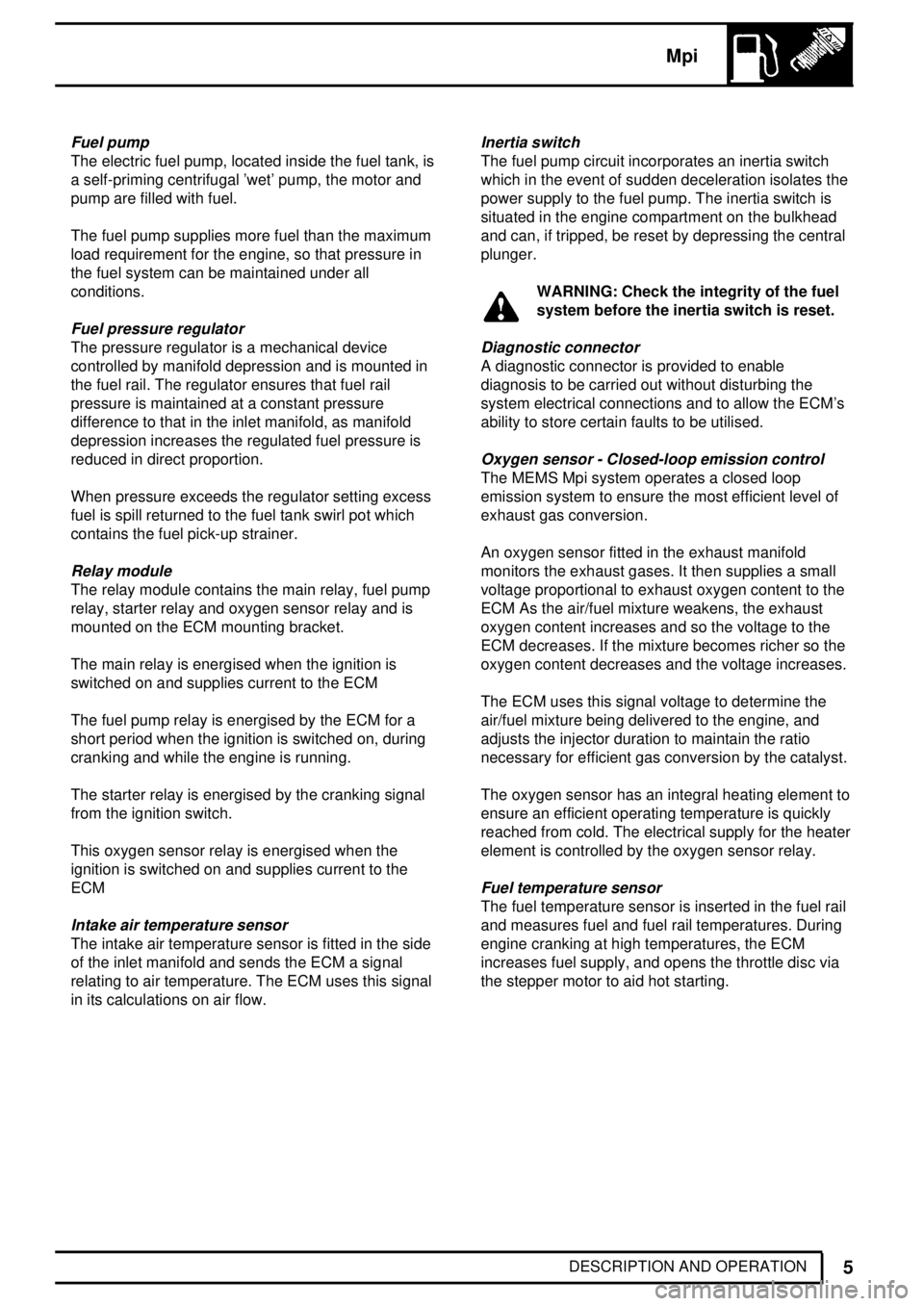
Mpi
5
DESCRIPTION AND OPERATION
Fuel pump
The electric fuel pump, located inside the fuel tank, is
a self-priming centrifugal 'wet' pump, the motor and
pump are filled with fuel.
The fuel pump supplies more fuel than the maximum
load requirement for the engine, so that pressure in
the fuel system can be maintained under all
conditions.
Fuel pressure regulator
The pressure regulator is a mechanical device
controlled by manifold depression and is mounted in
the fuel rail. The regulator ensures that fuel rail
pressure is maintained at a constant pressure
difference to that in the inlet manifold, as manifold
depression increases the regulated fuel pressure is
reduced in direct proportion.
When pressure exceeds the regulator setting excess
fuel is spill returned to the fuel tank swirl pot which
contains the fuel pick-up strainer.
Relay module
The relay module contains the main relay, fuel pump
relay, starter relay and oxygen sensor relay and is
mounted on the ECM mounting bracket.
The main relay is energised when the ignition is
switched on and supplies current to the ECM
The fuel pump relay is energised by the ECM for a
short period when the ignition is switched on, during
cranking and while the engine is running.
The starter relay is energised by the cranking signal
from the ignition switch.
This oxygen sensor relay is energised when the
ignition is switched on and supplies current to the
ECM
Intake air temperature sensor
The intake air temperature sensor is fitted in the side
of the inlet manifold and sends the ECM a signal
relating to air temperature. The ECM uses this signal
in its calculations on air flow.
Inertia switch
The fuel pump circuit incorporates an inertia switch
which in the event of sudden deceleration isolates the
power supply to the fuel pump. The inertia switch is
situated in the engine compartment on the bulkhead
and can, if tripped, be reset by depressing the central
plunger.
WARNING: Check the integrity of the fuel
system before the inertia switch is reset.
Diagnostic connector
A diagnostic connector is provided to enable
diagnosis to be carried out without disturbing the
system electrical connections and to allow the ECM's
ability to store certain faults to be utilised.
Oxygen sensor - Closed-loop emission control
The MEMS Mpi system operates a closed loop
emission system to ensure the most efficient level of
exhaust gas conversion.
An oxygen sensor fitted in the exhaust manifold
monitors the exhaust gases. It then supplies a small
voltage proportional to exhaust oxygen content to the
ECM As the air/fuel mixture weakens, the exhaust
oxygen content increases and so the voltage to the
ECM decreases. If the mixture becomes richer so the
oxygen content decreases and the voltage increases.
The ECM uses this signal voltage to determine the
air/fuel mixture being delivered to the engine, and
adjusts the injector duration to maintain the ratio
necessary for efficient gas conversion by the catalyst.
The oxygen sensor has an integral heating element to
ensure an efficient operating temperature is quickly
reached from cold. The electrical supply for the heater
element is controlled by the oxygen sensor relay.
Fuel temperature sensor
The fuel temperature sensor is inserted in the fuel rail
and measures fuel and fuel rail temperatures. During
engine cranking at high temperatures, the ECM
increases fuel supply, and opens the throttle disc via
the stepper motor to aid hot starting.
Page 318 of 873
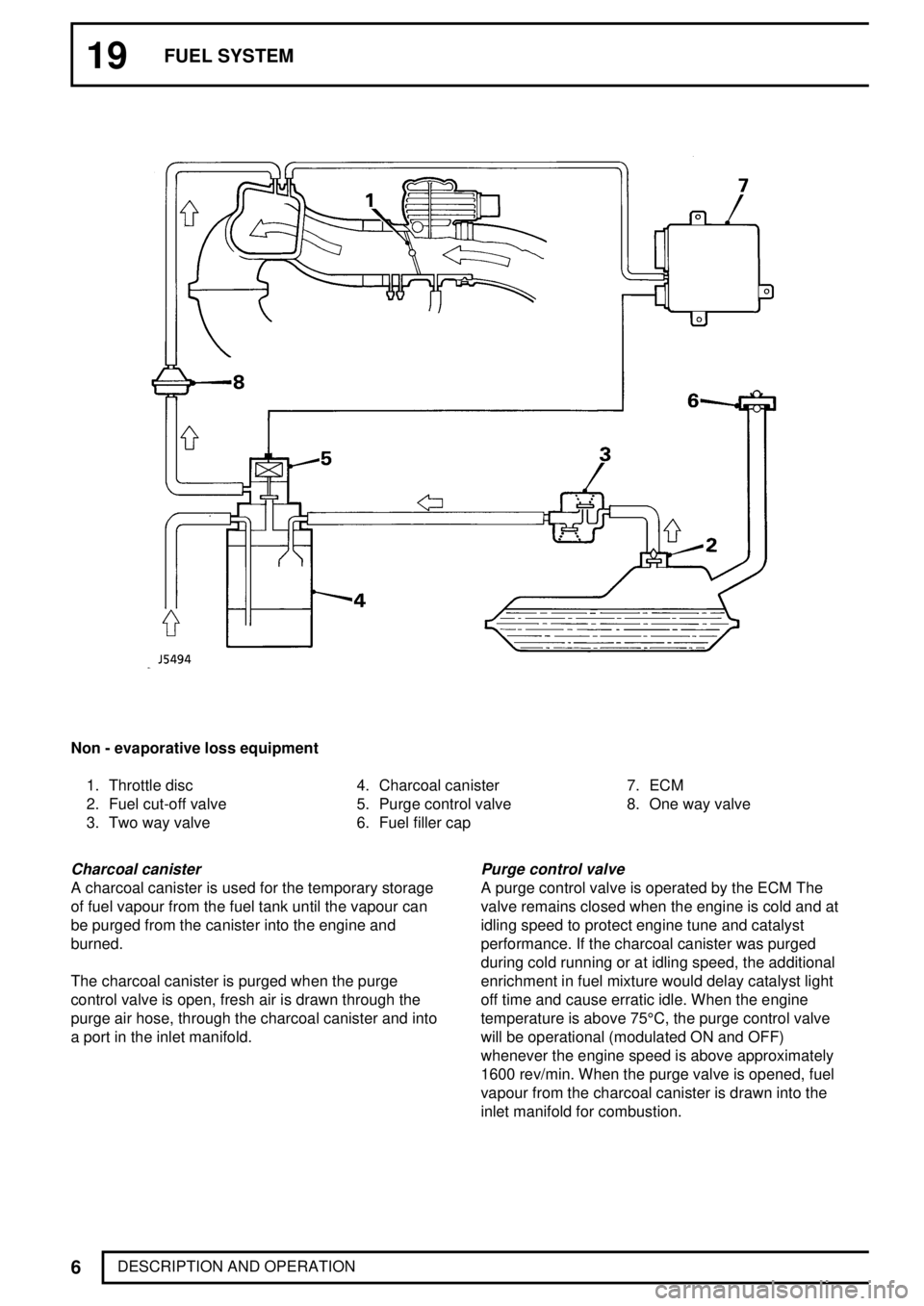
19FUEL SYSTEM
6
DESCRIPTION AND OPERATION
Non - evaporative loss equipment
1. Throttle disc
2. Fuel cut-off valve
3. Two way valve4. Charcoal canister
5. Purge control valve
6. Fuel filler cap7. ECM
8. One way valve
Charcoal canister
A charcoal canister is used for the temporary storage
of fuel vapour from the fuel tank until the vapour can
be purged from the canister into the engine and
burned.
The charcoal canister is purged when the purge
control valve is open, fresh air is drawn through the
purge air hose, through the charcoal canister and into
a port in the inlet manifold.
Purge control valve
A purge control valve is operated by the ECM The
valve remains closed when the engine is cold and at
idling speed to protect engine tune and catalyst
performance. If the charcoal canister was purged
during cold running or at idling speed, the additional
enrichment in fuel mixture would delay catalyst light
off time and cause erratic idle. When the engine
temperature is above 75°C, the purge control valve
will be operational (modulated ON and OFF)
whenever the engine speed is above approximately
1600 rev/min. When the purge valve is opened, fuel
vapour from the charcoal canister is drawn into the
inlet manifold for combustion.
Page 319 of 873
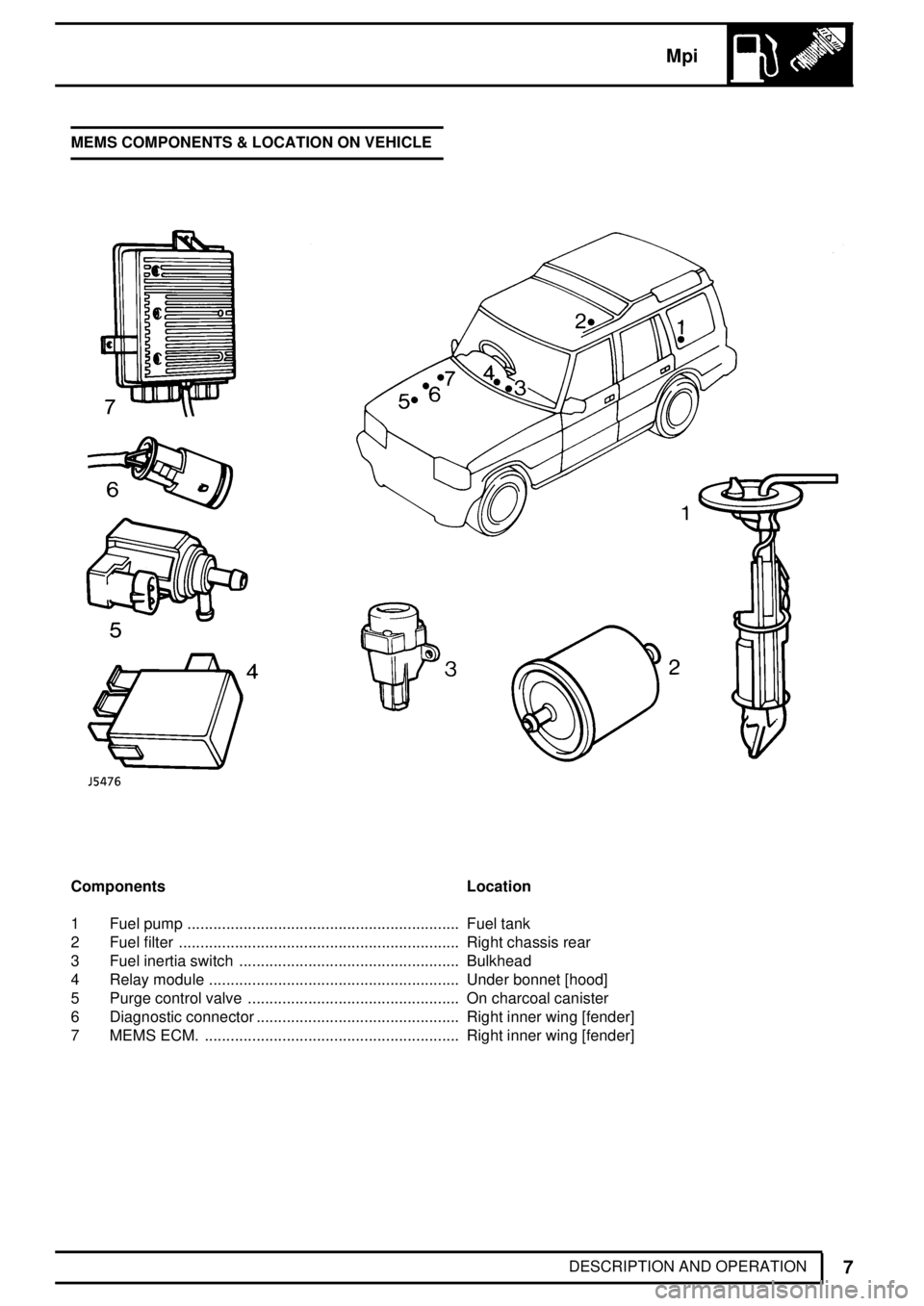
Mpi
7
DESCRIPTION AND OPERATION MEMS COMPONENTS & LOCATION ON VEHICLE
Components Location
1 Fuel pump Fuel tank...............................................................
2 Fuel filter Right chassis rear.................................................................
3 Fuel inertia switch Bulkhead...................................................
4 Relay module Under bonnet [hood]..........................................................
5 Purge control valve On charcoal canister.................................................
6 Diagnostic connector Right inner wing [fender]...............................................
7 MEMS ECM. Right inner wing [fender]...........................................................
Page 320 of 873
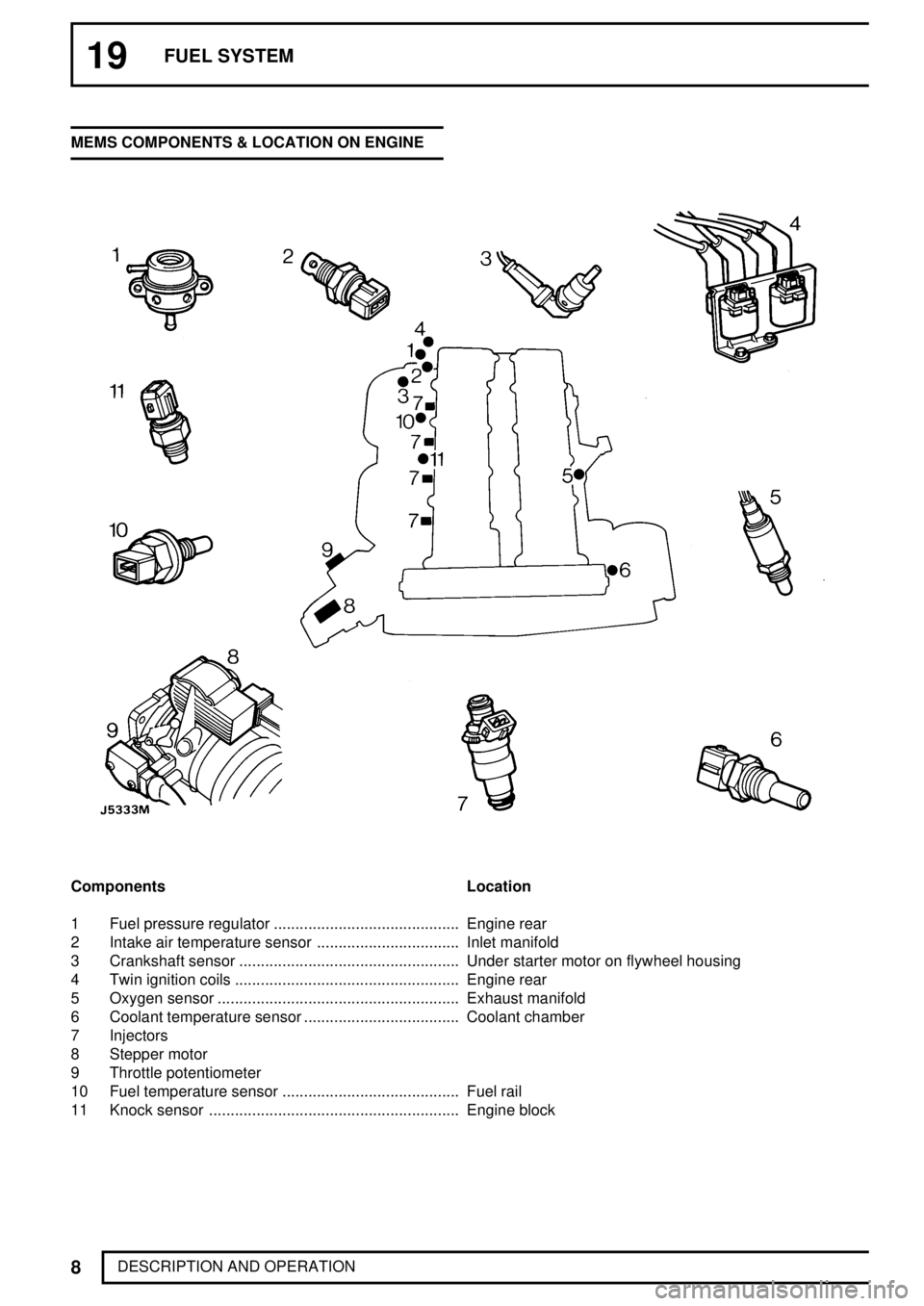
19FUEL SYSTEM
8
DESCRIPTION AND OPERATION MEMS COMPONENTS & LOCATION ON ENGINE
Components Location
1 Fuel pressure regulator Engine rear...........................................
2 Intake air temperature sensor Inlet manifold.................................
3 Crankshaft sensor Under starter motor on flywheel housing...................................................
4 Twin ignition coils Engine rear....................................................
5 Oxygen sensor Exhaust manifold........................................................
6 Coolant temperature sensor Coolant chamber....................................
7 Injectors
8 Stepper motor
9 Throttle potentiometer
10 Fuel temperature sensor Fuel rail.........................................
11 Knock sensor Engine block..........................................................