LAND ROVER DISCOVERY 1995 Workshop Manual
Manufacturer: LAND ROVER, Model Year: 1995, Model line: DISCOVERY, Model: LAND ROVER DISCOVERY 1995Pages: 873, PDF Size: 12.89 MB
Page 281 of 873
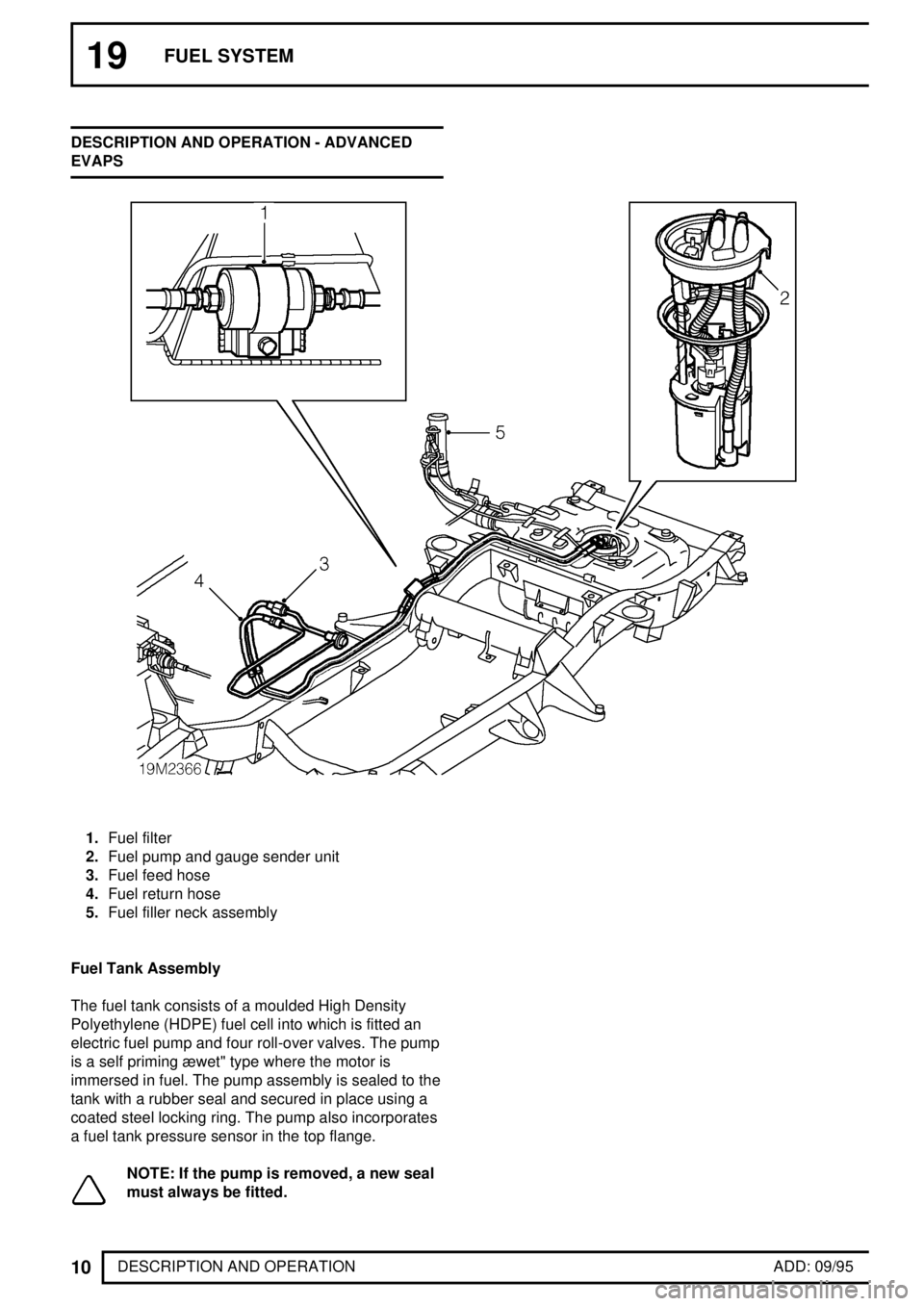
19FUEL SYSTEM
10
DESCRIPTION AND OPERATION ADD: 09/95 DESCRIPTION AND OPERATION - ADVANCED
EVAPS
1.Fuel filter
2.Fuel pump and gauge sender unit
3.Fuel feed hose
4.Fuel return hose
5.Fuel filler neck assembly
Fuel Tank Assembly
The fuel tank consists of a moulded High Density
Polyethylene (HDPE) fuel cell into which is fitted an
electric fuel pump and four roll-over valves. The pump
is a self priming ñwet" type where the motor is
immersed in fuel. The pump assembly is sealed to the
tank with a rubber seal and secured in place using a
coated steel locking ring. The pump also incorporates
a fuel tank pressure sensor in the top flange.
NOTE: If the pump is removed, a new seal
must always be fitted.
Page 282 of 873
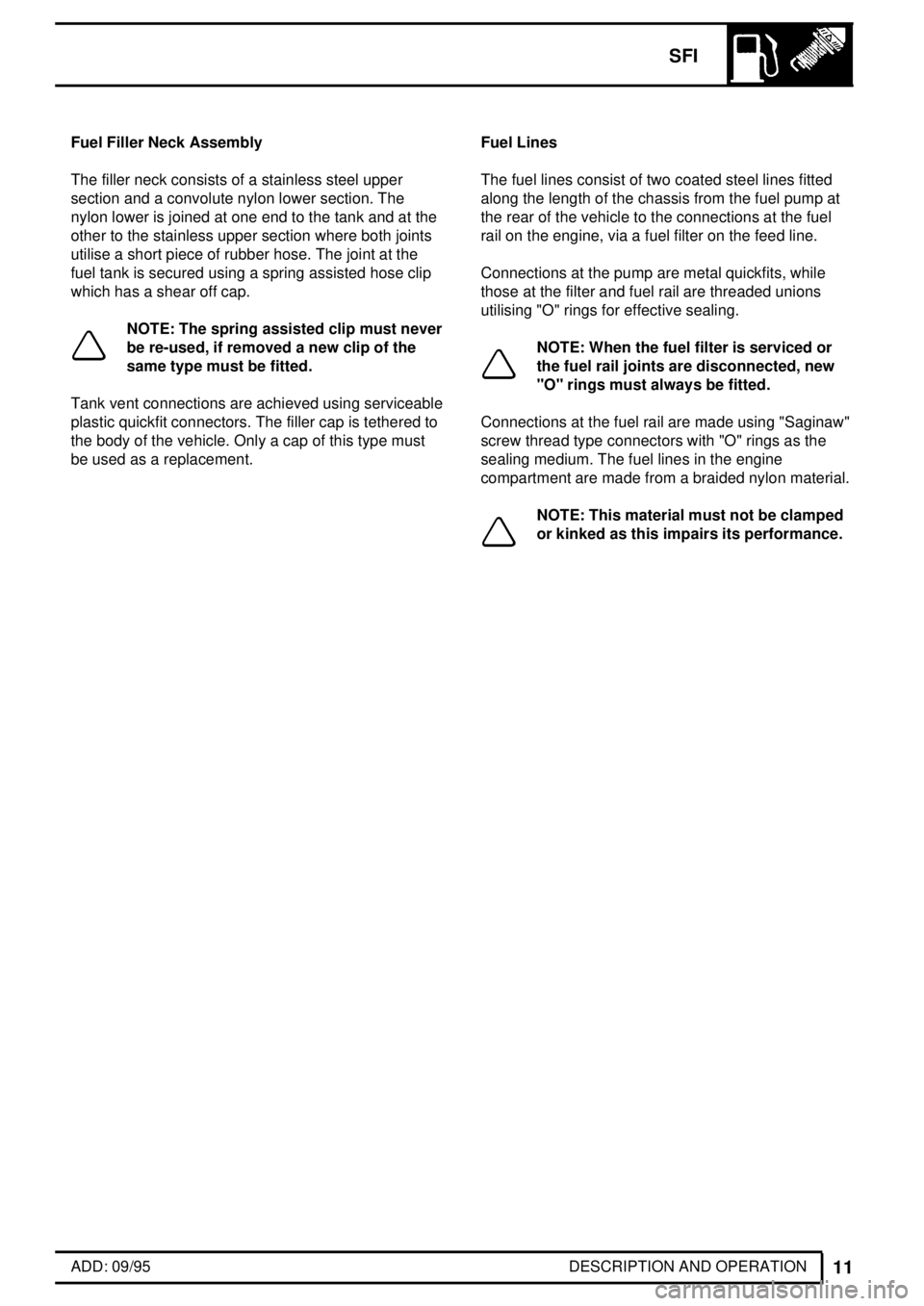
SFI
11
DESCRIPTION AND OPERATION ADD: 09/95 Fuel Filler Neck Assembly
The filler neck consists of a stainless steel upper
section and a convolute nylon lower section. The
nylon lower is joined at one end to the tank and at the
other to the stainless upper section where both joints
utilise a short piece of rubber hose. The joint at the
fuel tank is secured using a spring assisted hose clip
which has a shear off cap.
NOTE: The spring assisted clip must never
be re-used, if removed a new clip of the
same type must be fitted.
Tank vent connections are achieved using serviceable
plastic quickfit connectors. The filler cap is tethered to
the body of the vehicle. Only a cap of this type must
be used as a replacement.Fuel Lines
The fuel lines consist of two coated steel lines fitted
along the length of the chassis from the fuel pump at
the rear of the vehicle to the connections at the fuel
rail on the engine, via a fuel filter on the feed line.
Connections at the pump are metal quickfits, while
those at the filter and fuel rail are threaded unions
utilising "O" rings for effective sealing.
NOTE: When the fuel filter is serviced or
the fuel rail joints are disconnected, new
"O" rings must always be fitted.
Connections at the fuel rail are made using "Saginaw"
screw thread type connectors with "O" rings as the
sealing medium. The fuel lines in the engine
compartment are made from a braided nylon material.
NOTE: This material must not be clamped
or kinked as this impairs its performance.
Page 283 of 873
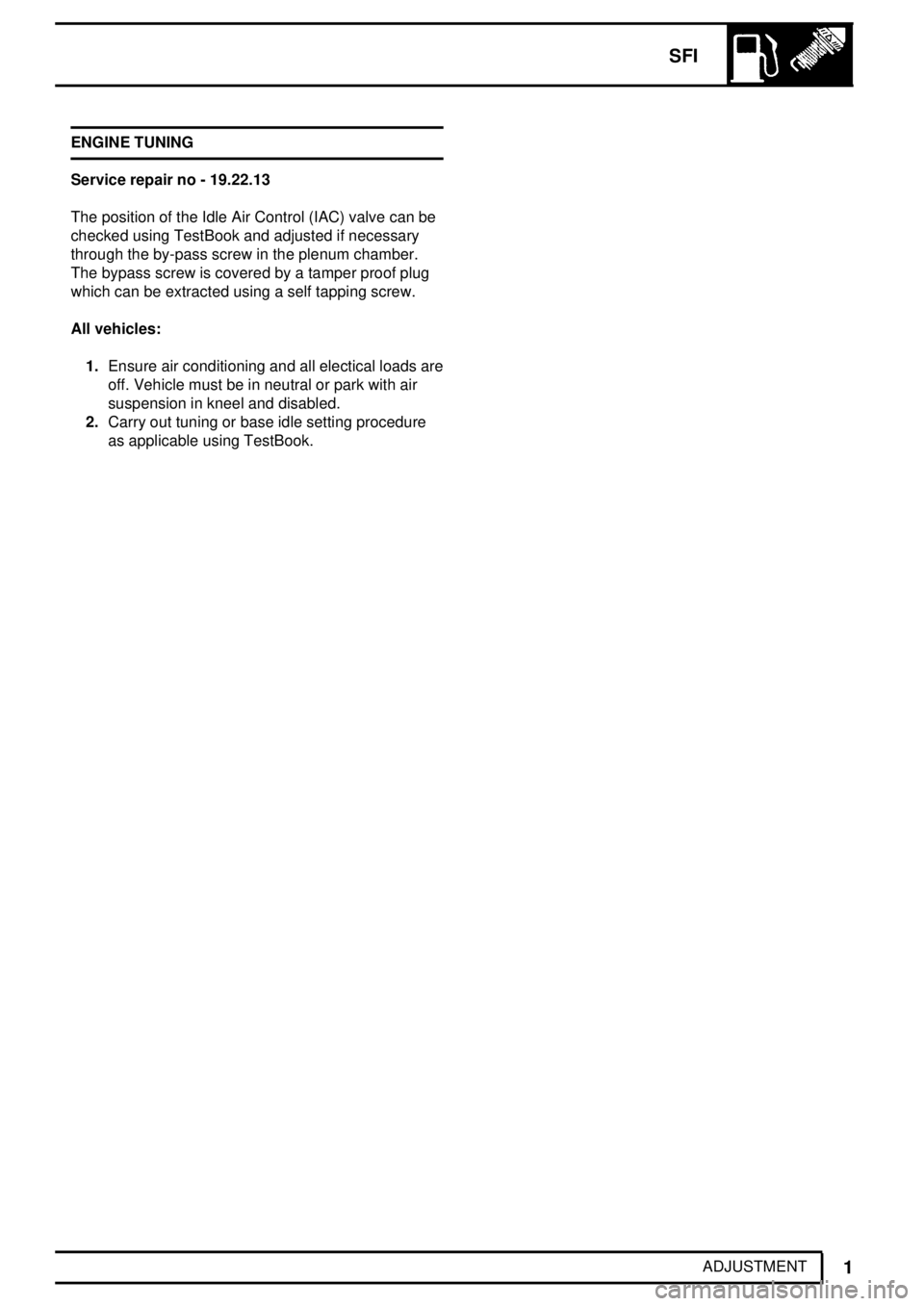
SFI
1
ADJUSTMENT ENGINE TUNING
Service repair no - 19.22.13
The position of the Idle Air Control (IAC) valve can be
checked using TestBook and adjusted if necessary
through the by-pass screw in the plenum chamber.
The bypass screw is covered by a tamper proof plug
which can be extracted using a self tapping screw.
All vehicles:
1.Ensure air conditioning and all electical loads are
off. Vehicle must be in neutral or park with air
suspension in kneel and disabled.
2.Carry out tuning or base idle setting procedure
as applicable using TestBook.
Page 284 of 873
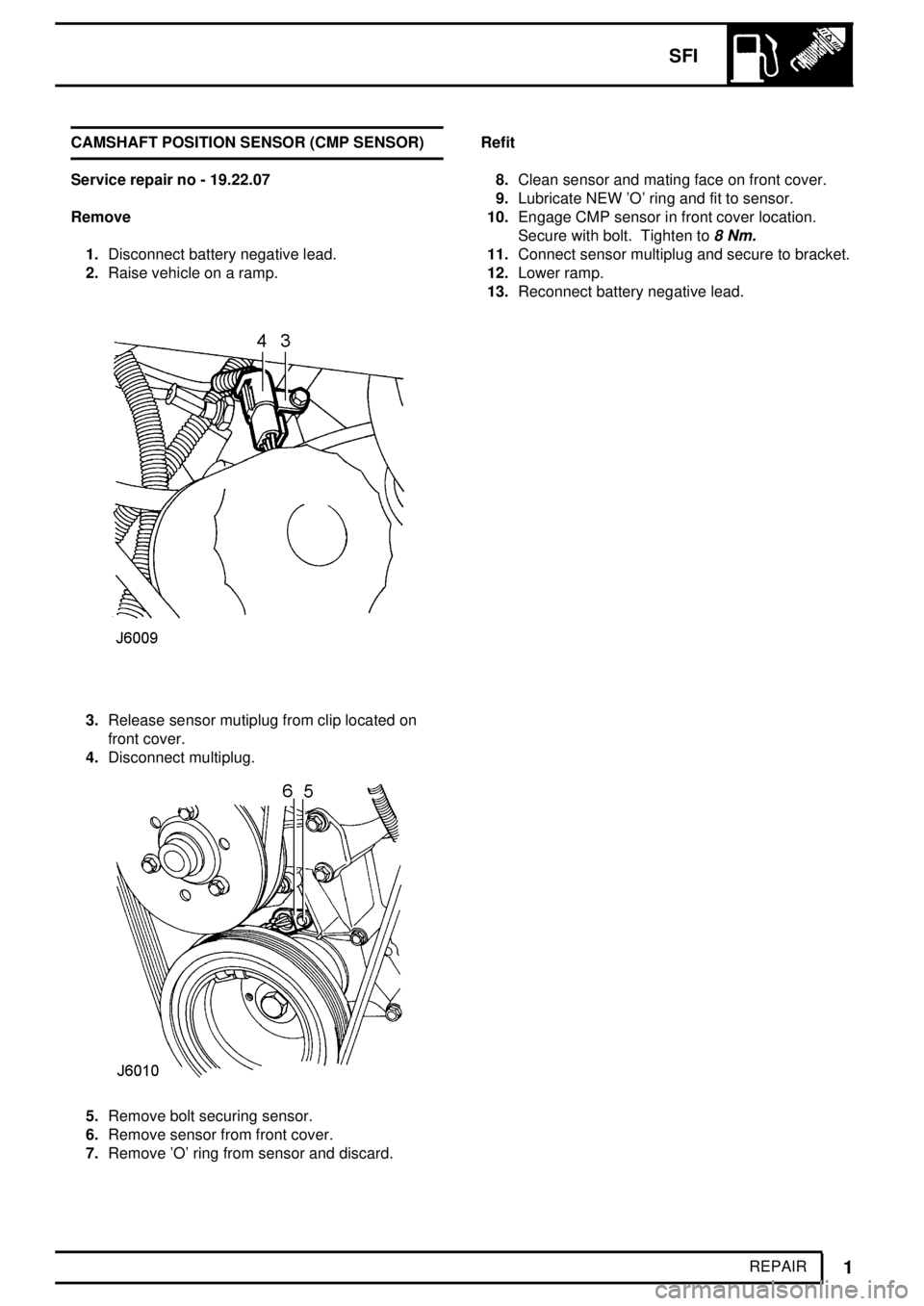
SFI
1
REPAIR CAMSHAFT POSITION SENSOR (CMP SENSOR)
Service repair no - 19.22.07
Remove
1.Disconnect battery negative lead.
2.Raise vehicle on a ramp.
3.Release sensor mutiplug from clip located on
front cover.
4.Disconnect multiplug.
5.Remove bolt securing sensor.
6.Remove sensor from front cover.
7.Remove 'O' ring from sensor and discard.Refit
8.Clean sensor and mating face on front cover.
9.Lubricate NEW 'O' ring and fit to sensor.
10.Engage CMP sensor in front cover location.
Secure with bolt. Tighten to
8 Nm.
11.Connect sensor multiplug and secure to bracket.
12.Lower ramp.
13.Reconnect battery negative lead.
Page 285 of 873
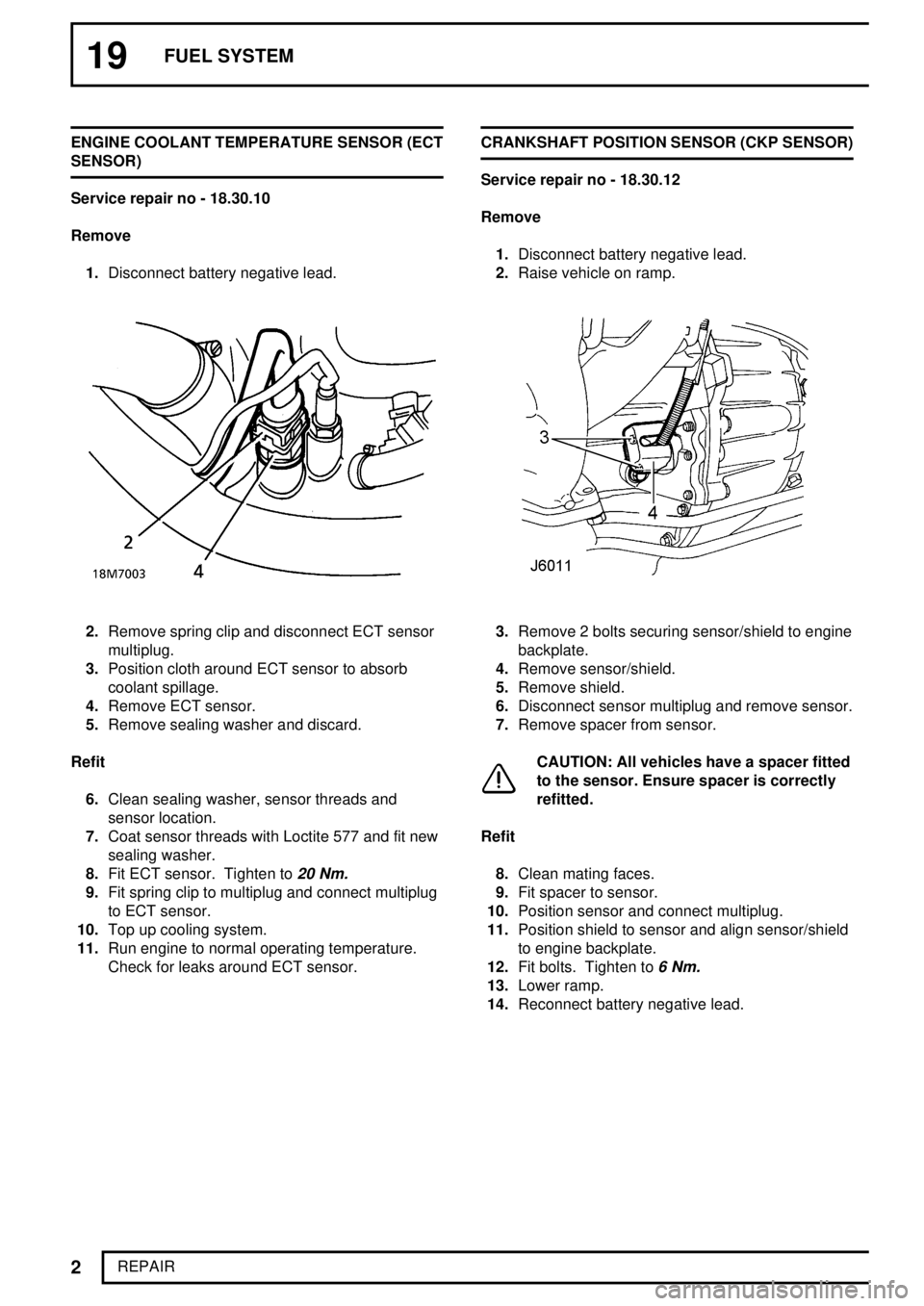
19FUEL SYSTEM
2
REPAIR ENGINE COOLANT TEMPERATURE SENSOR (ECT
SENSOR)
Service repair no - 18.30.10
Remove
1.Disconnect battery negative lead.
2.Remove spring clip and disconnect ECT sensor
multiplug.
3.Position cloth around ECT sensor to absorb
coolant spillage.
4.Remove ECT sensor.
5.Remove sealing washer and discard.
Refit
6.Clean sealing washer, sensor threads and
sensor location.
7.Coat sensor threads with Loctite 577 and fit new
sealing washer.
8.Fit ECT sensor. Tighten to
20 Nm.
9.Fit spring clip to multiplug and connect multiplug
to ECT sensor.
10.Top up cooling system.
11.Run engine to normal operating temperature.
Check for leaks around ECT sensor.CRANKSHAFT POSITION SENSOR (CKP SENSOR)
Service repair no - 18.30.12
Remove
1.Disconnect battery negative lead.
2.Raise vehicle on ramp.
3.Remove 2 bolts securing sensor/shield to engine
backplate.
4.Remove sensor/shield.
5.Remove shield.
6.Disconnect sensor multiplug and remove sensor.
7.Remove spacer from sensor.
CAUTION: All vehicles have a spacer fitted
to the sensor. Ensure spacer is correctly
refitted.
Refit
8.Clean mating faces.
9.Fit spacer to sensor.
10.Position sensor and connect multiplug.
11.Position shield to sensor and align sensor/shield
to engine backplate.
12.Fit bolts. Tighten to
6 Nm.
13.Lower ramp.
14.Reconnect battery negative lead.
Page 286 of 873
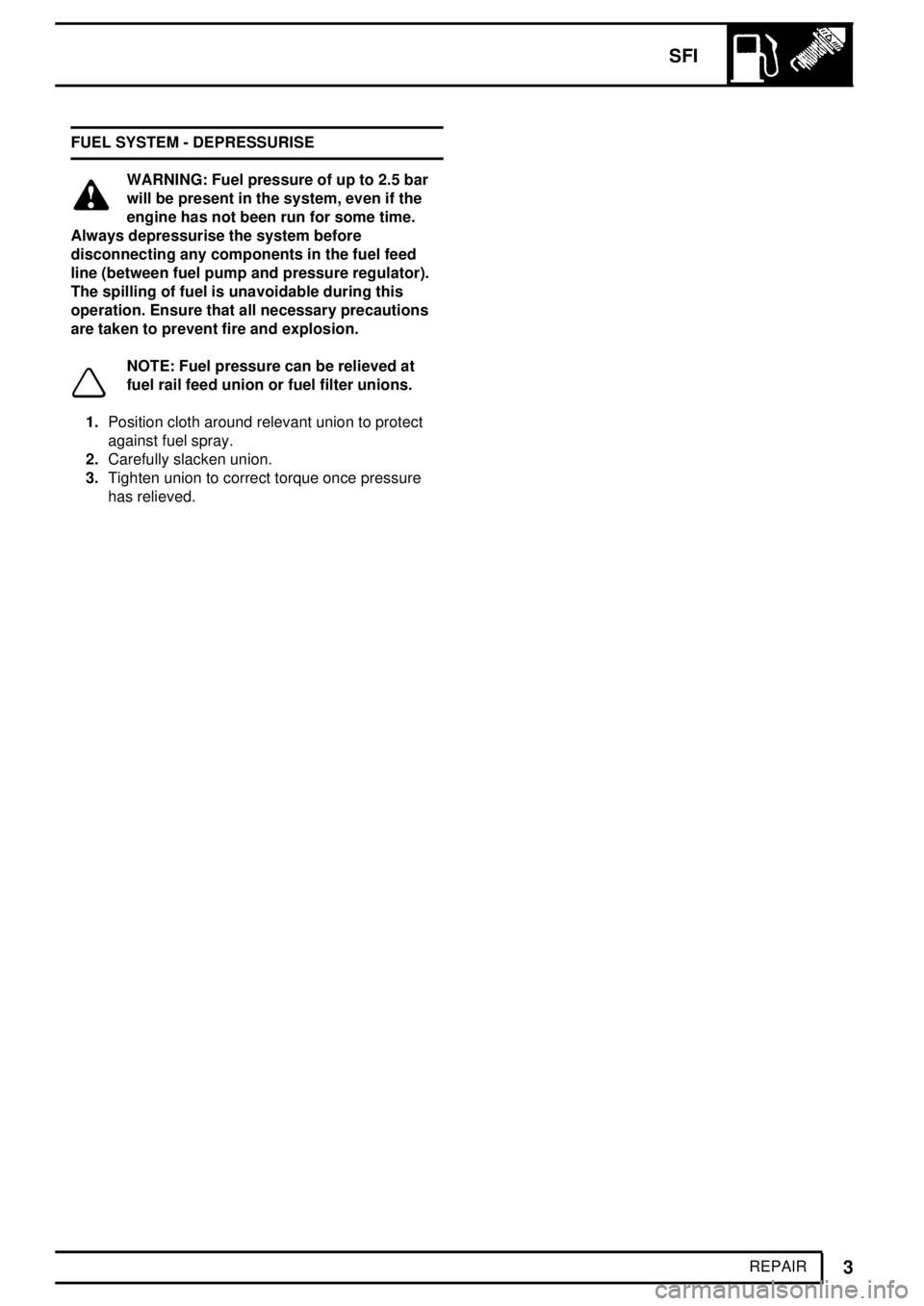
SFI
3
REPAIR FUEL SYSTEM - DEPRESSURISE
WARNING: Fuel pressure of up to 2.5 bar
will be present in the system, even if the
engine has not been run for some time.
Always depressurise the system before
disconnecting any components in the fuel feed
line (between fuel pump and pressure regulator).
The spilling of fuel is unavoidable during this
operation. Ensure that all necessary precautions
are taken to prevent fire and explosion.
NOTE: Fuel pressure can be relieved at
fuel rail feed union or fuel filter unions.
1.Position cloth around relevant union to protect
against fuel spray.
2.Carefully slacken union.
3.Tighten union to correct torque once pressure
has relieved.
Page 287 of 873
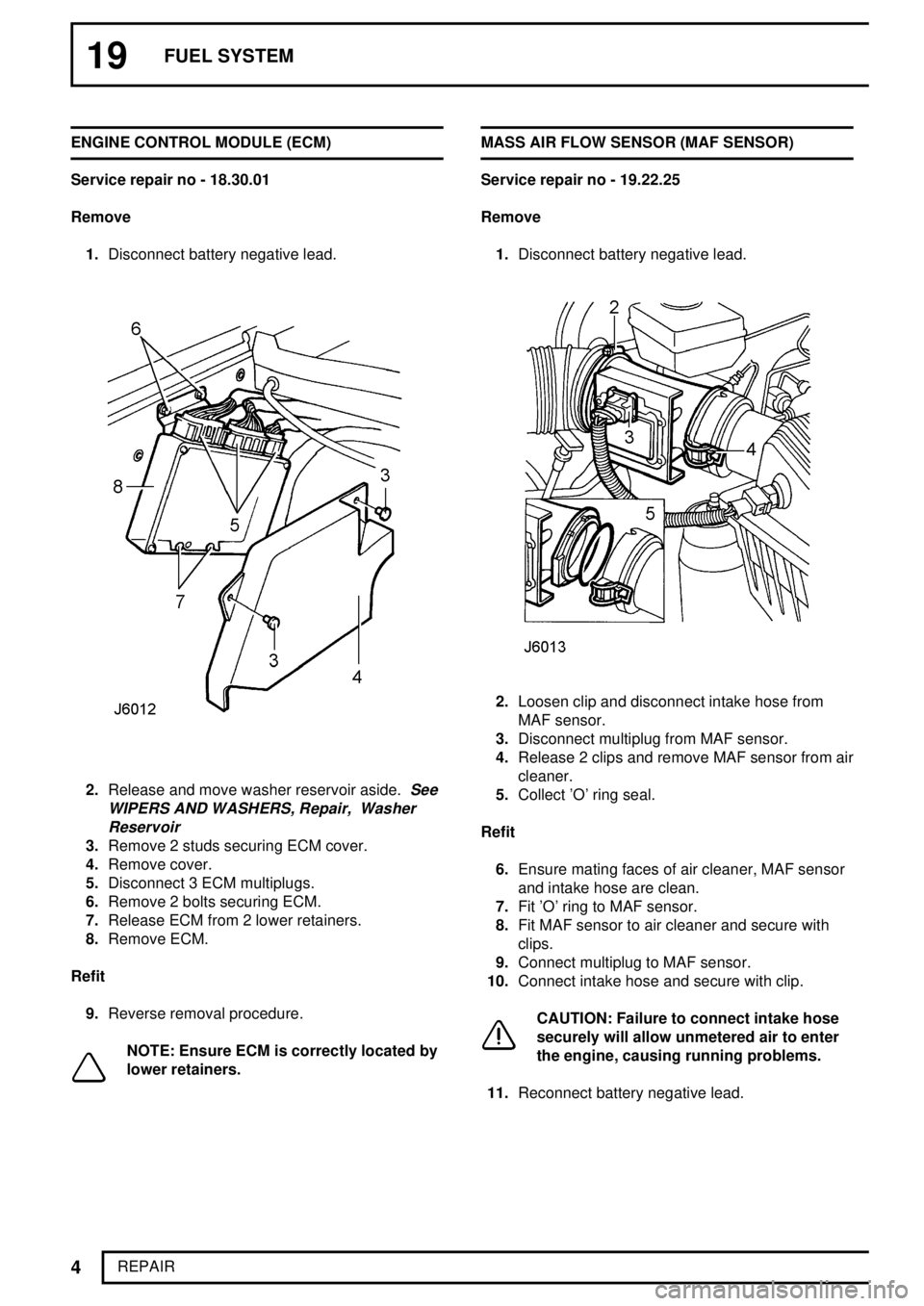
19FUEL SYSTEM
4
REPAIR ENGINE CONTROL MODULE (ECM)
Service repair no - 18.30.01
Remove
1.Disconnect battery negative lead.
2.Release and move washer reservoir aside.See
WIPERS AND WASHERS, Repair, Washer
Reservoir
3.Remove 2 studs securing ECM cover.
4.Remove cover.
5.Disconnect 3 ECM multiplugs.
6.Remove 2 bolts securing ECM.
7.Release ECM from 2 lower retainers.
8.Remove ECM.
Refit
9.Reverse removal procedure.
NOTE: Ensure ECM is correctly located by
lower retainers.MASS AIR FLOW SENSOR (MAF SENSOR)
Service repair no - 19.22.25
Remove
1.Disconnect battery negative lead.
2.Loosen clip and disconnect intake hose from
MAF sensor.
3.Disconnect multiplug from MAF sensor.
4.Release 2 clips and remove MAF sensor from air
cleaner.
5.Collect 'O' ring seal.
Refit
6.Ensure mating faces of air cleaner, MAF sensor
and intake hose are clean.
7.Fit 'O' ring to MAF sensor.
8.Fit MAF sensor to air cleaner and secure with
clips.
9.Connect multiplug to MAF sensor.
10.Connect intake hose and secure with clip.
CAUTION: Failure to connect intake hose
securely will allow unmetered air to enter
the engine, causing running problems.
11.Reconnect battery negative lead.
Page 288 of 873
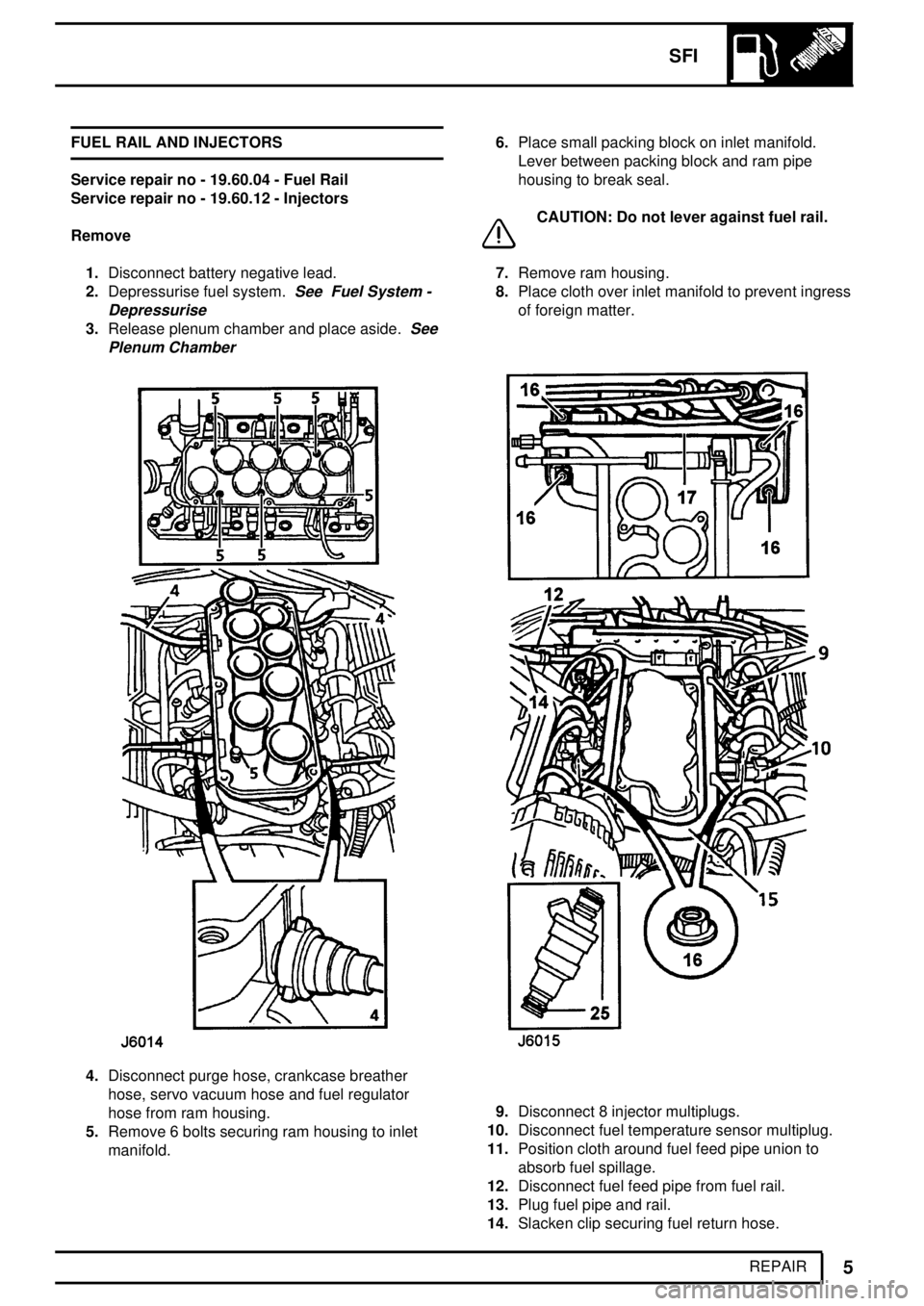
SFI
5
REPAIR FUEL RAIL AND INJECTORS
Service repair no - 19.60.04 - Fuel Rail
Service repair no - 19.60.12 - Injectors
Remove
1.Disconnect battery negative lead.
2.Depressurise fuel system.
See Fuel System -
Depressurise
3.Release plenum chamber and place aside.See
Plenum Chamber
4.Disconnect purge hose, crankcase breather
hose, servo vacuum hose and fuel regulator
hose from ram housing.
5.Remove 6 bolts securing ram housing to inlet
manifold.6.Place small packing block on inlet manifold.
Lever between packing block and ram pipe
housing to break seal.
CAUTION: Do not lever against fuel rail.
7.Remove ram housing.
8.Place cloth over inlet manifold to prevent ingress
of foreign matter.
9.Disconnect 8 injector multiplugs.
10.Disconnect fuel temperature sensor multiplug.
11.Position cloth around fuel feed pipe union to
absorb fuel spillage.
12.Disconnect fuel feed pipe from fuel rail.
13.Plug fuel pipe and rail.
14.Slacken clip securing fuel return hose.
Page 289 of 873
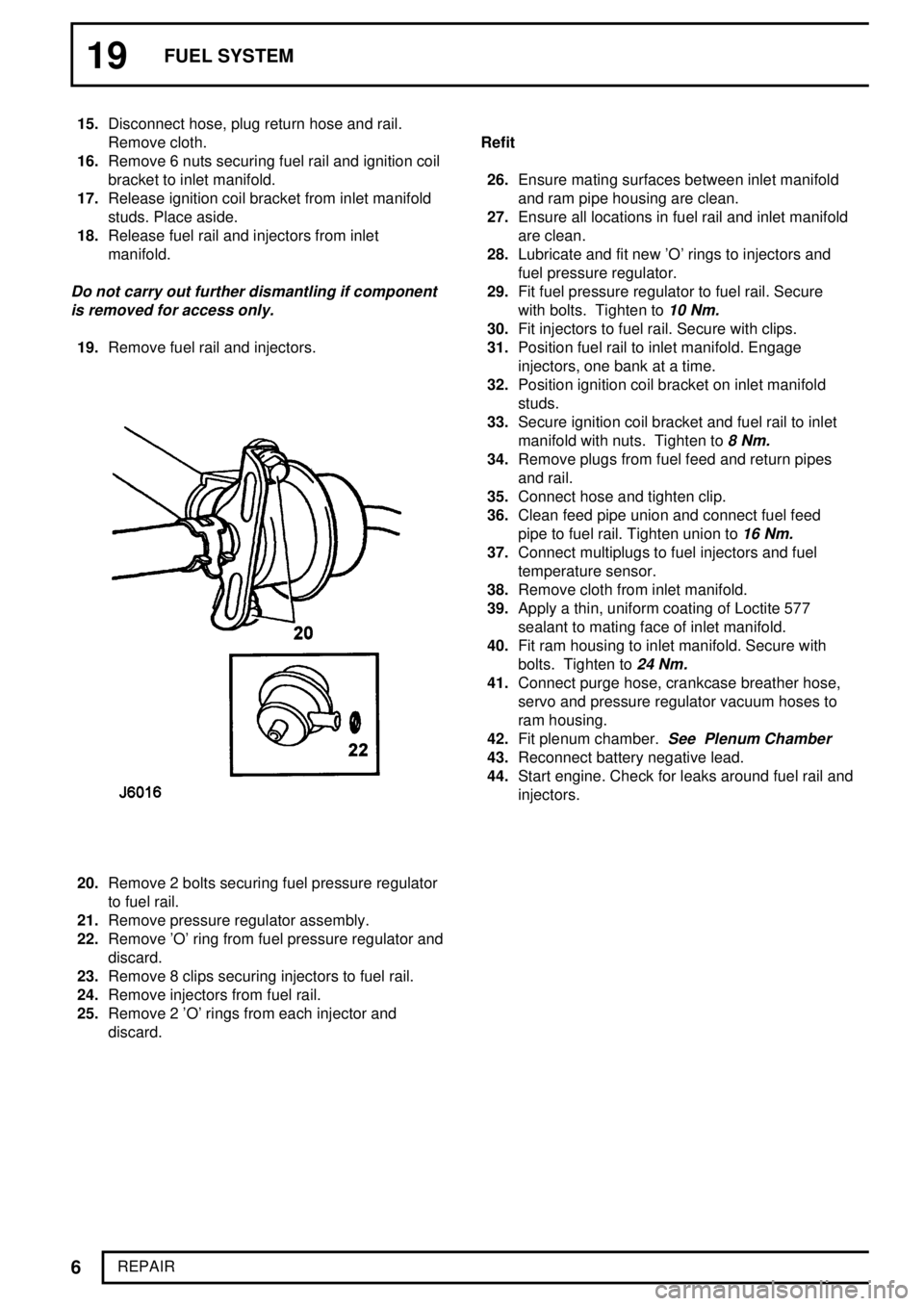
19FUEL SYSTEM
6
REPAIR 15.Disconnect hose, plug return hose and rail.
Remove cloth.
16.Remove 6 nuts securing fuel rail and ignition coil
bracket to inlet manifold.
17.Release ignition coil bracket from inlet manifold
studs. Place aside.
18.Release fuel rail and injectors from inlet
manifold.
Do not carry out further dismantling if component
is removed for access only.
19.Remove fuel rail and injectors.
20.Remove 2 bolts securing fuel pressure regulator
to fuel rail.
21.Remove pressure regulator assembly.
22.Remove 'O' ring from fuel pressure regulator and
discard.
23.Remove 8 clips securing injectors to fuel rail.
24.Remove injectors from fuel rail.
25.Remove 2 'O' rings from each injector and
discard.Refit
26.Ensure mating surfaces between inlet manifold
and ram pipe housing are clean.
27.Ensure all locations in fuel rail and inlet manifold
are clean.
28.Lubricate and fit new 'O' rings to injectors and
fuel pressure regulator.
29.Fit fuel pressure regulator to fuel rail. Secure
with bolts. Tighten to
10 Nm.
30.Fit injectors to fuel rail. Secure with clips.
31.Position fuel rail to inlet manifold. Engage
injectors, one bank at a time.
32.Position ignition coil bracket on inlet manifold
studs.
33.Secure ignition coil bracket and fuel rail to inlet
manifold with nuts. Tighten to
8 Nm.
34.Remove plugs from fuel feed and return pipes
and rail.
35.Connect hose and tighten clip.
36.Clean feed pipe union and connect fuel feed
pipe to fuel rail. Tighten union to
16 Nm.
37.Connect multiplugs to fuel injectors and fuel
temperature sensor.
38.Remove cloth from inlet manifold.
39.Apply a thin, uniform coating of Loctite 577
sealant to mating face of inlet manifold.
40.Fit ram housing to inlet manifold. Secure with
bolts. Tighten to
24 Nm.
41.Connect purge hose, crankcase breather hose,
servo and pressure regulator vacuum hoses to
ram housing.
42.Fit plenum chamber.
See Plenum Chamber
43.Reconnect battery negative lead.
44.Start engine. Check for leaks around fuel rail and
injectors.
Page 290 of 873
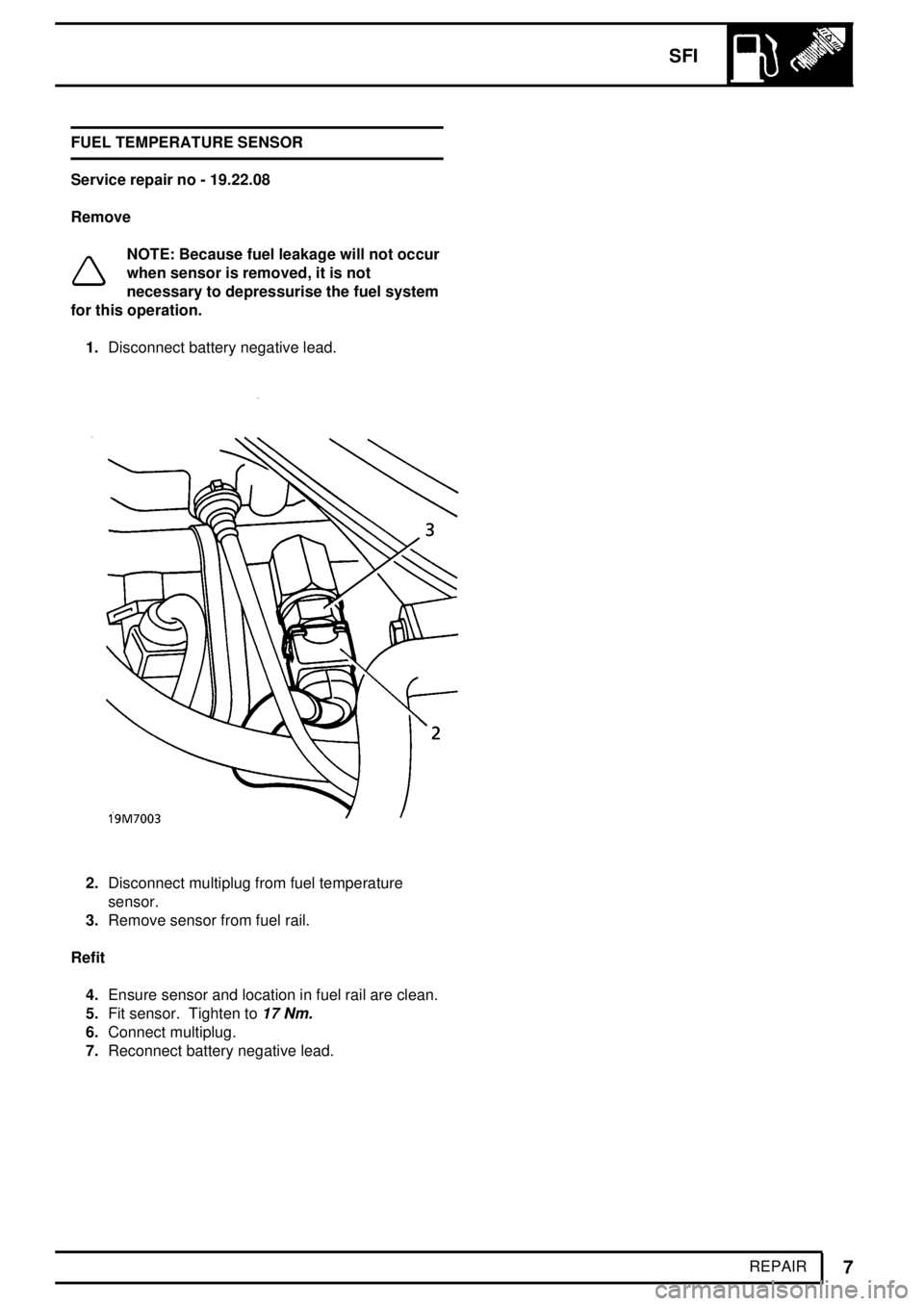
SFI
7
REPAIR FUEL TEMPERATURE SENSOR
Service repair no - 19.22.08
Remove
NOTE: Because fuel leakage will not occur
when sensor is removed, it is not
necessary to depressurise the fuel system
for this operation.
1.Disconnect battery negative lead.
2.Disconnect multiplug from fuel temperature
sensor.
3.Remove sensor from fuel rail.
Refit
4.Ensure sensor and location in fuel rail are clean.
5.Fit sensor. Tighten to
17 Nm.
6.Connect multiplug.
7.Reconnect battery negative lead.