LAND ROVER DISCOVERY 1995 Workshop Manual
Manufacturer: LAND ROVER, Model Year: 1995, Model line: DISCOVERY, Model: LAND ROVER DISCOVERY 1995Pages: 873, PDF Size: 12.89 MB
Page 291 of 873
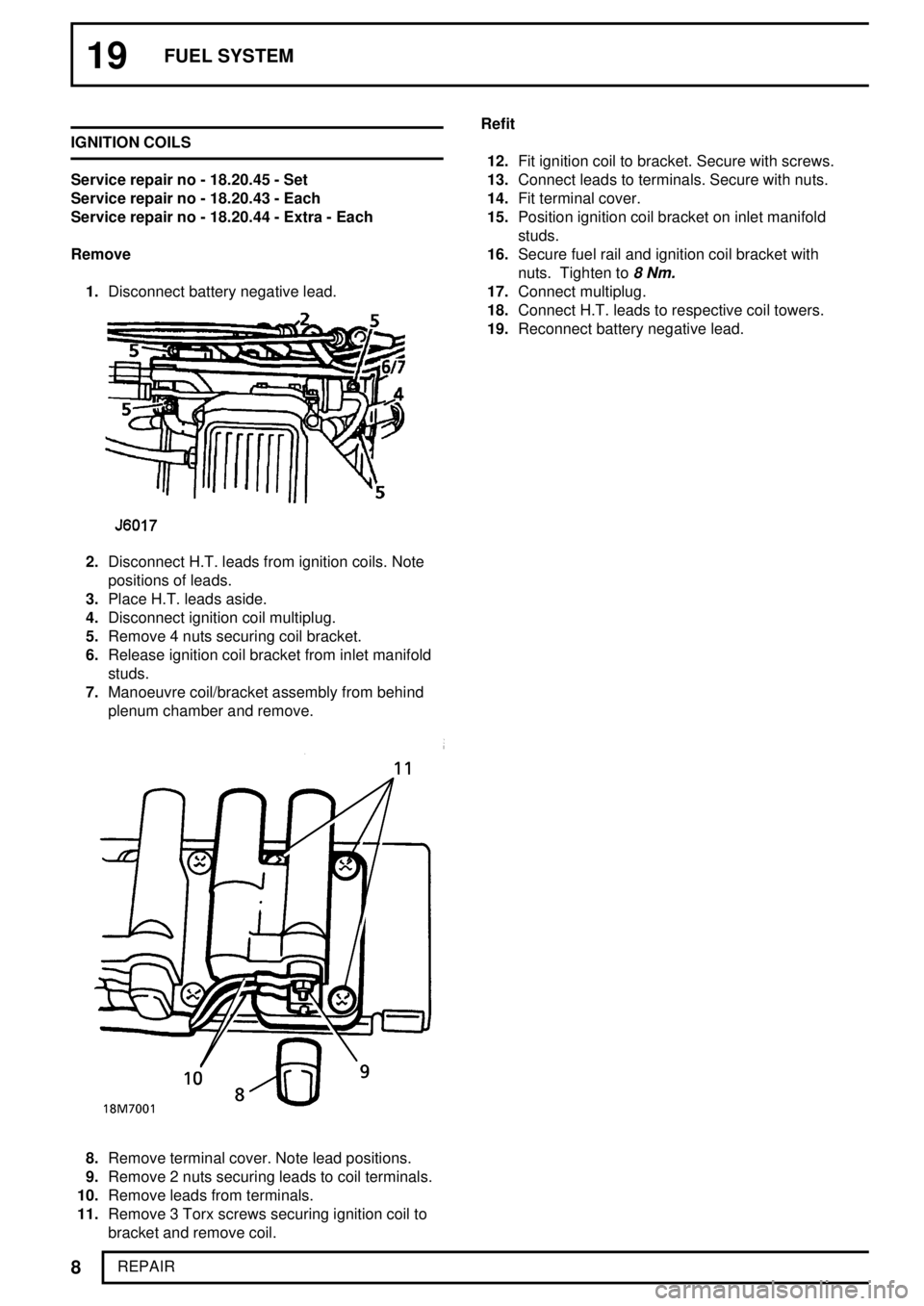
19FUEL SYSTEM
8
REPAIR IGNITION COILS
Service repair no - 18.20.45 - Set
Service repair no - 18.20.43 - Each
Service repair no - 18.20.44 - Extra - Each
Remove
1.Disconnect battery negative lead.
2.Disconnect H.T. leads from ignition coils. Note
positions of leads.
3.Place H.T. leads aside.
4.Disconnect ignition coil multiplug.
5.Remove 4 nuts securing coil bracket.
6.Release ignition coil bracket from inlet manifold
studs.
7.Manoeuvre coil/bracket assembly from behind
plenum chamber and remove.
8.Remove terminal cover. Note lead positions.
9.Remove 2 nuts securing leads to coil terminals.
10.Remove leads from terminals.
11.Remove 3 Torx screws securing ignition coil to
bracket and remove coil.Refit
12.Fit ignition coil to bracket. Secure with screws.
13.Connect leads to terminals. Secure with nuts.
14.Fit terminal cover.
15.Position ignition coil bracket on inlet manifold
studs.
16.Secure fuel rail and ignition coil bracket with
nuts. Tighten to
8 Nm.
17.Connect multiplug.
18.Connect H.T. leads to respective coil towers.
19.Reconnect battery negative lead.
Page 292 of 873
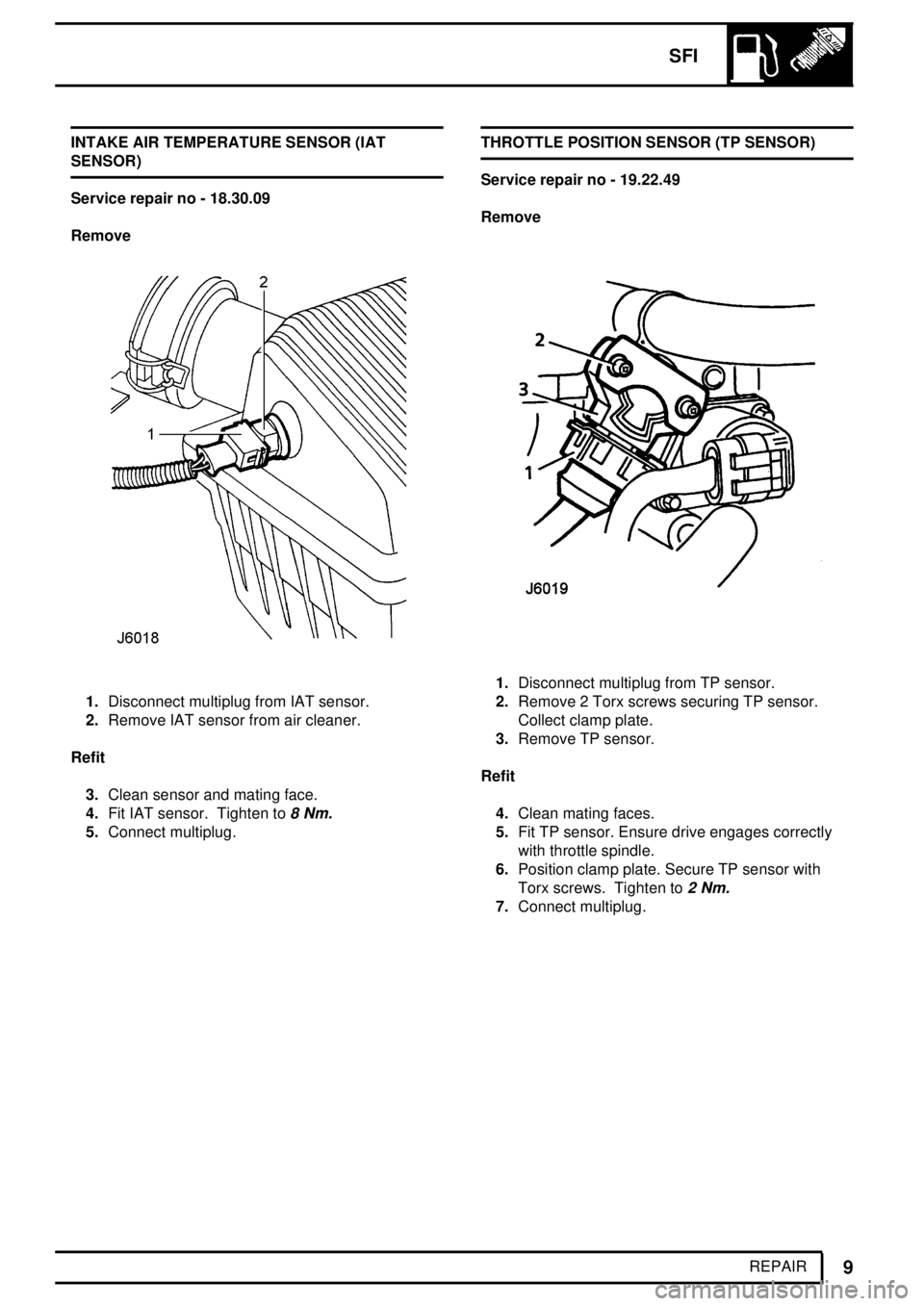
SFI
9
REPAIR INTAKE AIR TEMPERATURE SENSOR (IAT
SENSOR)
Service repair no - 18.30.09
Remove
1.Disconnect multiplug from IAT sensor.
2.Remove IAT sensor from air cleaner.
Refit
3.Clean sensor and mating face.
4.Fit IAT sensor. Tighten to
8 Nm.
5.Connect multiplug.THROTTLE POSITION SENSOR (TP SENSOR)
Service repair no - 19.22.49
Remove
1.Disconnect multiplug from TP sensor.
2.Remove 2 Torx screws securing TP sensor.
Collect clamp plate.
3.Remove TP sensor.
Refit
4.Clean mating faces.
5.Fit TP sensor. Ensure drive engages correctly
with throttle spindle.
6.Position clamp plate. Secure TP sensor with
Torx screws. Tighten to
2 Nm.
7.Connect multiplug.
Page 293 of 873
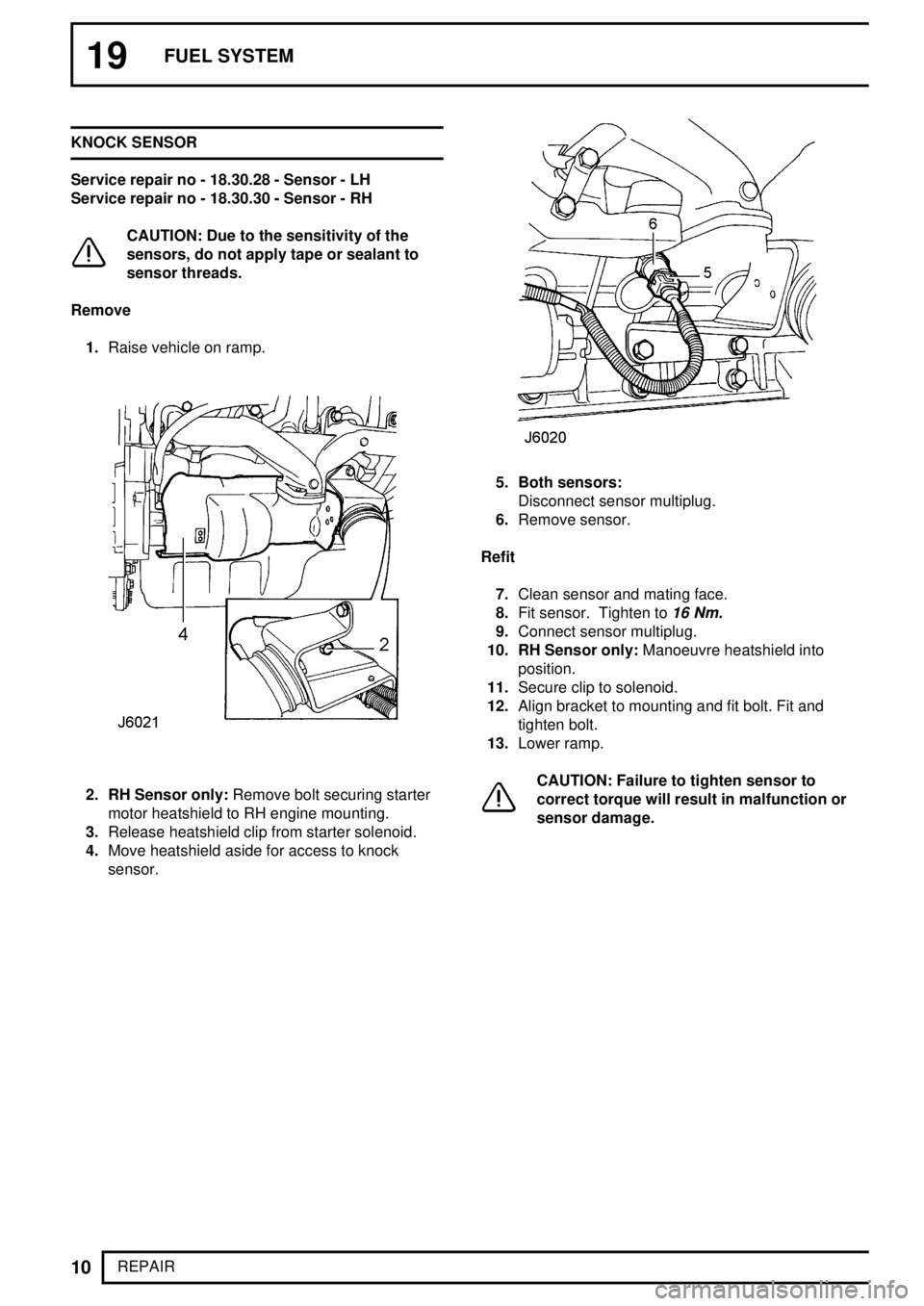
19FUEL SYSTEM
10
REPAIR KNOCK SENSOR
Service repair no - 18.30.28 - Sensor - LH
Service repair no - 18.30.30 - Sensor - RH
CAUTION: Due to the sensitivity of the
sensors, do not apply tape or sealant to
sensor threads.
Remove
1.Raise vehicle on ramp.
2. RH Sensor only:Remove bolt securing starter
motor heatshield to RH engine mounting.
3.Release heatshield clip from starter solenoid.
4.Move heatshield aside for access to knock
sensor.
5. Both sensors:
Disconnect sensor multiplug.
6.Remove sensor.
Refit
7.Clean sensor and mating face.
8.Fit sensor. Tighten to
16 Nm.
9.Connect sensor multiplug.
10. RH Sensor only:Manoeuvre heatshield into
position.
11.Secure clip to solenoid.
12.Align bracket to mounting and fit bolt. Fit and
tighten bolt.
13.Lower ramp.
CAUTION: Failure to tighten sensor to
correct torque will result in malfunction or
sensor damage.
Page 294 of 873
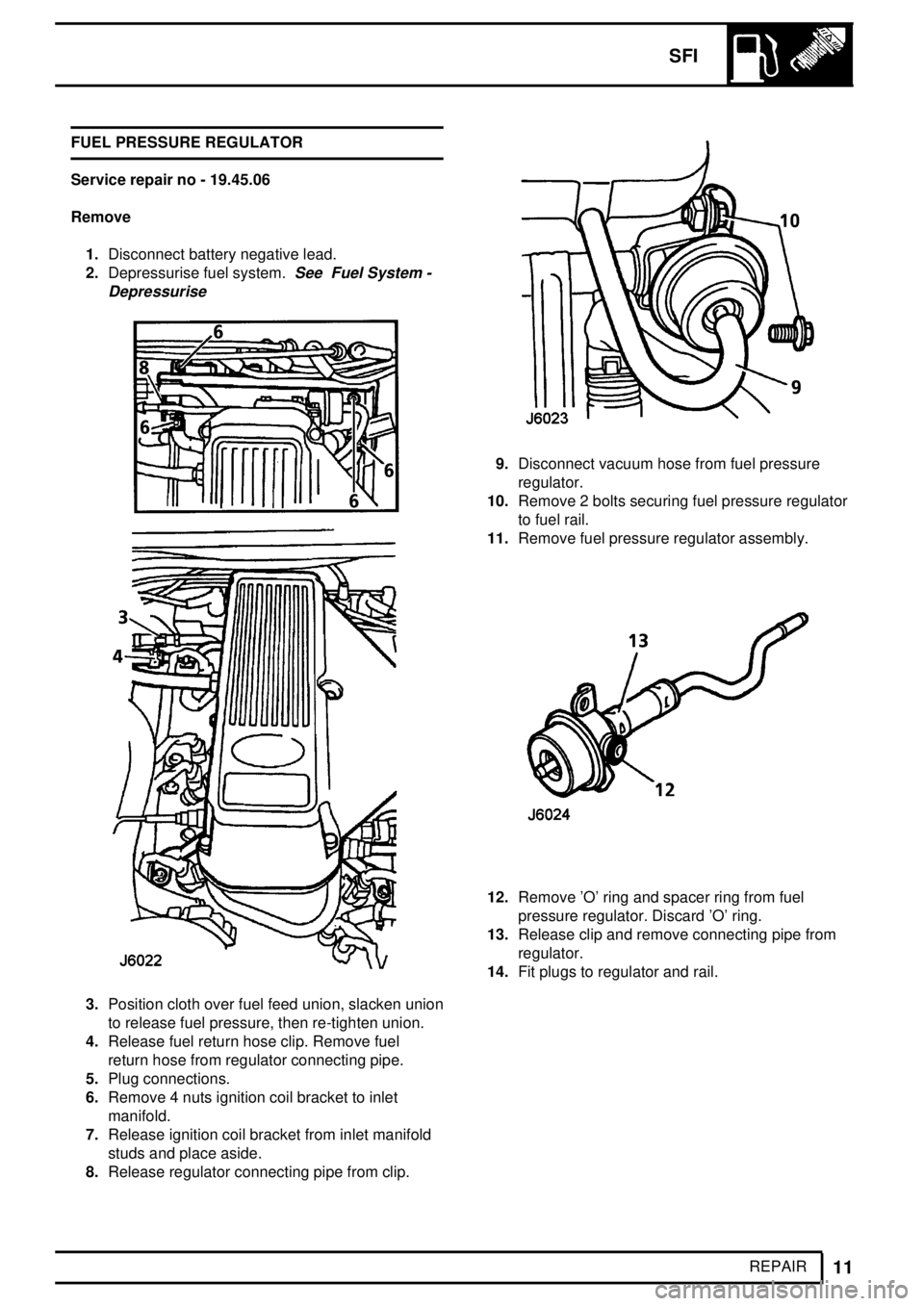
SFI
11
REPAIR FUEL PRESSURE REGULATOR
Service repair no - 19.45.06
Remove
1.Disconnect battery negative lead.
2.Depressurise fuel system.
See Fuel System -
Depressurise
3.Position cloth over fuel feed union, slacken union
to release fuel pressure, then re-tighten union.
4.Release fuel return hose clip. Remove fuel
return hose from regulator connecting pipe.
5.Plug connections.
6.Remove 4 nuts ignition coil bracket to inlet
manifold.
7.Release ignition coil bracket from inlet manifold
studs and place aside.
8.Release regulator connecting pipe from clip.
9.Disconnect vacuum hose from fuel pressure
regulator.
10.Remove 2 bolts securing fuel pressure regulator
to fuel rail.
11.Remove fuel pressure regulator assembly.
12.Remove 'O' ring and spacer ring from fuel
pressure regulator. Discard 'O' ring.
13.Release clip and remove connecting pipe from
regulator.
14.Fit plugs to regulator and rail.
Page 295 of 873
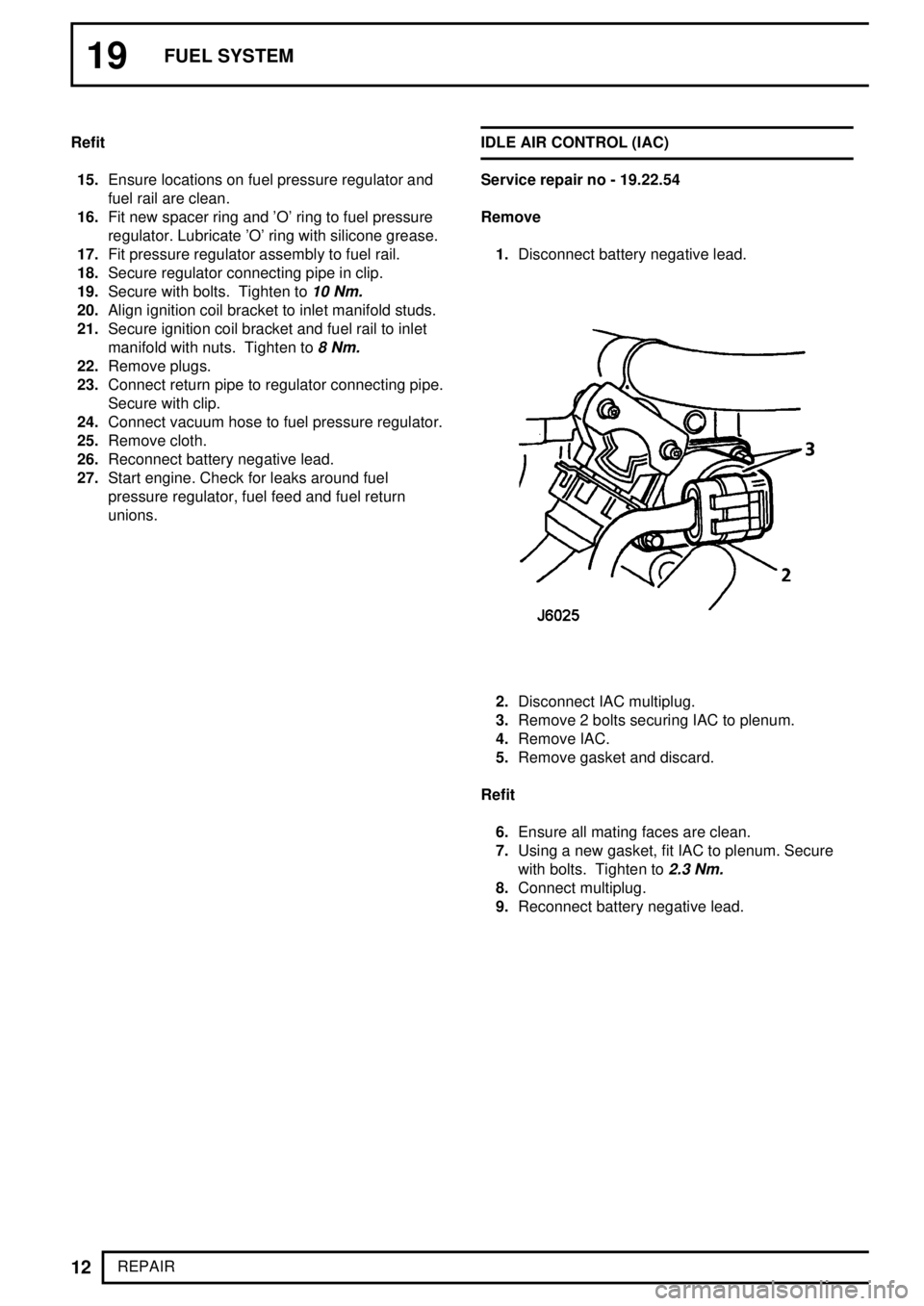
19FUEL SYSTEM
12
REPAIR Refit
15.Ensure locations on fuel pressure regulator and
fuel rail are clean.
16.Fit new spacer ring and 'O' ring to fuel pressure
regulator. Lubricate 'O' ring with silicone grease.
17.Fit pressure regulator assembly to fuel rail.
18.Secure regulator connecting pipe in clip.
19.Secure with bolts. Tighten to
10 Nm.
20.Align ignition coil bracket to inlet manifold studs.
21.Secure ignition coil bracket and fuel rail to inlet
manifold with nuts. Tighten to
8 Nm.
22.Remove plugs.
23.Connect return pipe to regulator connecting pipe.
Secure with clip.
24.Connect vacuum hose to fuel pressure regulator.
25.Remove cloth.
26.Reconnect battery negative lead.
27.Start engine. Check for leaks around fuel
pressure regulator, fuel feed and fuel return
unions.IDLE AIR CONTROL (IAC)
Service repair no - 19.22.54
Remove
1.Disconnect battery negative lead.
2.Disconnect IAC multiplug.
3.Remove 2 bolts securing IAC to plenum.
4.Remove IAC.
5.Remove gasket and discard.
Refit
6.Ensure all mating faces are clean.
7.Using a new gasket, fit IAC to plenum. Secure
with bolts. Tighten to
2.3 Nm.
8.Connect multiplug.
9.Reconnect battery negative lead.
Page 296 of 873
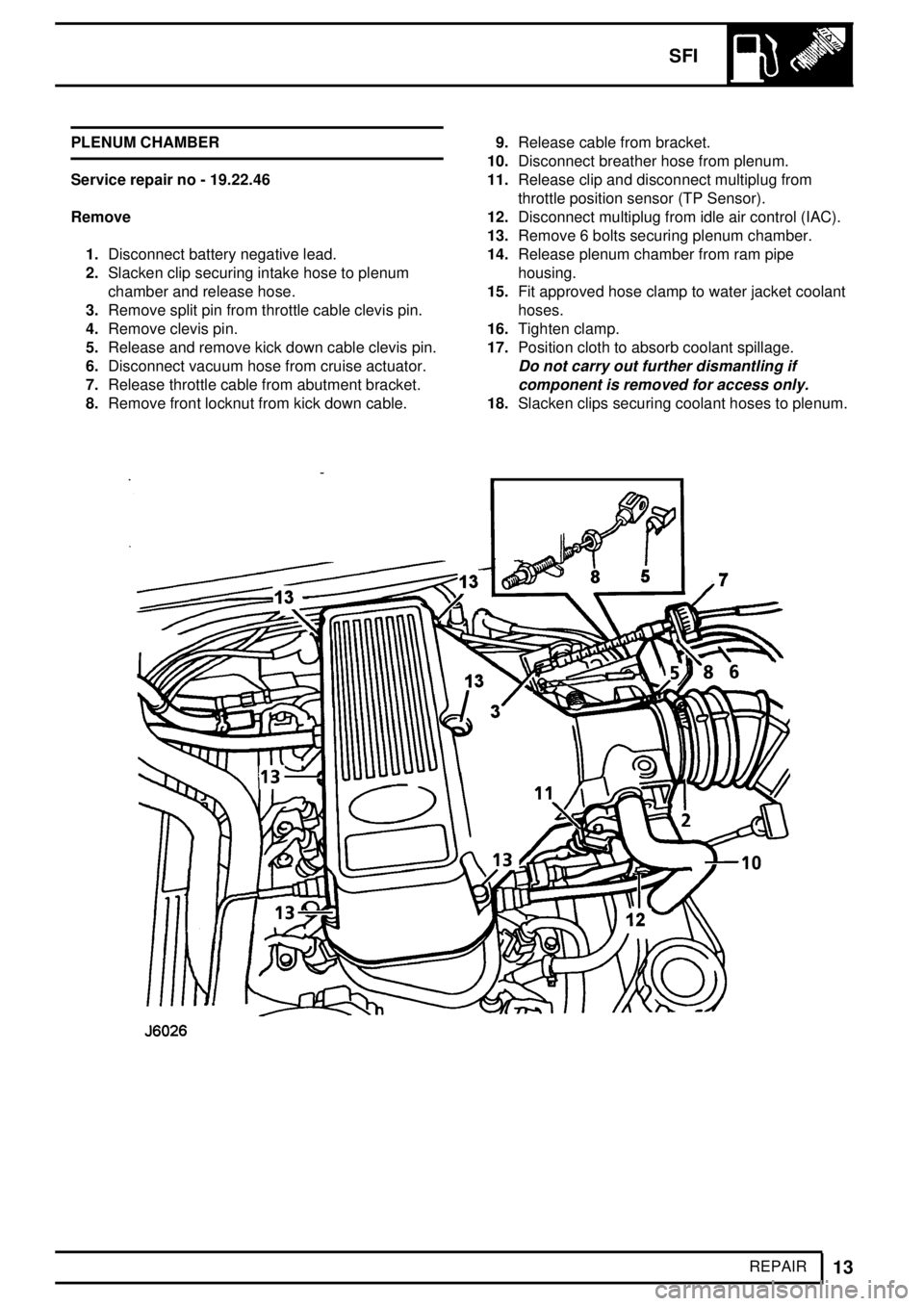
SFI
13
REPAIR PLENUM CHAMBER
Service repair no - 19.22.46
Remove
1.Disconnect battery negative lead.
2.Slacken clip securing intake hose to plenum
chamber and release hose.
3.Remove split pin from throttle cable clevis pin.
4.Remove clevis pin.
5.Release and remove kick down cable clevis pin.
6.Disconnect vacuum hose from cruise actuator.
7.Release throttle cable from abutment bracket.
8.Remove front locknut from kick down cable.9.Release cable from bracket.
10.Disconnect breather hose from plenum.
11.Release clip and disconnect multiplug from
throttle position sensor (TP Sensor).
12.Disconnect multiplug from idle air control (IAC).
13.Remove 6 bolts securing plenum chamber.
14.Release plenum chamber from ram pipe
housing.
15.Fit approved hose clamp to water jacket coolant
hoses.
16.Tighten clamp.
17.Position cloth to absorb coolant spillage.
Do not carry out further dismantling if
component is removed for access only.
18.Slacken clips securing coolant hoses to plenum.
Page 297 of 873
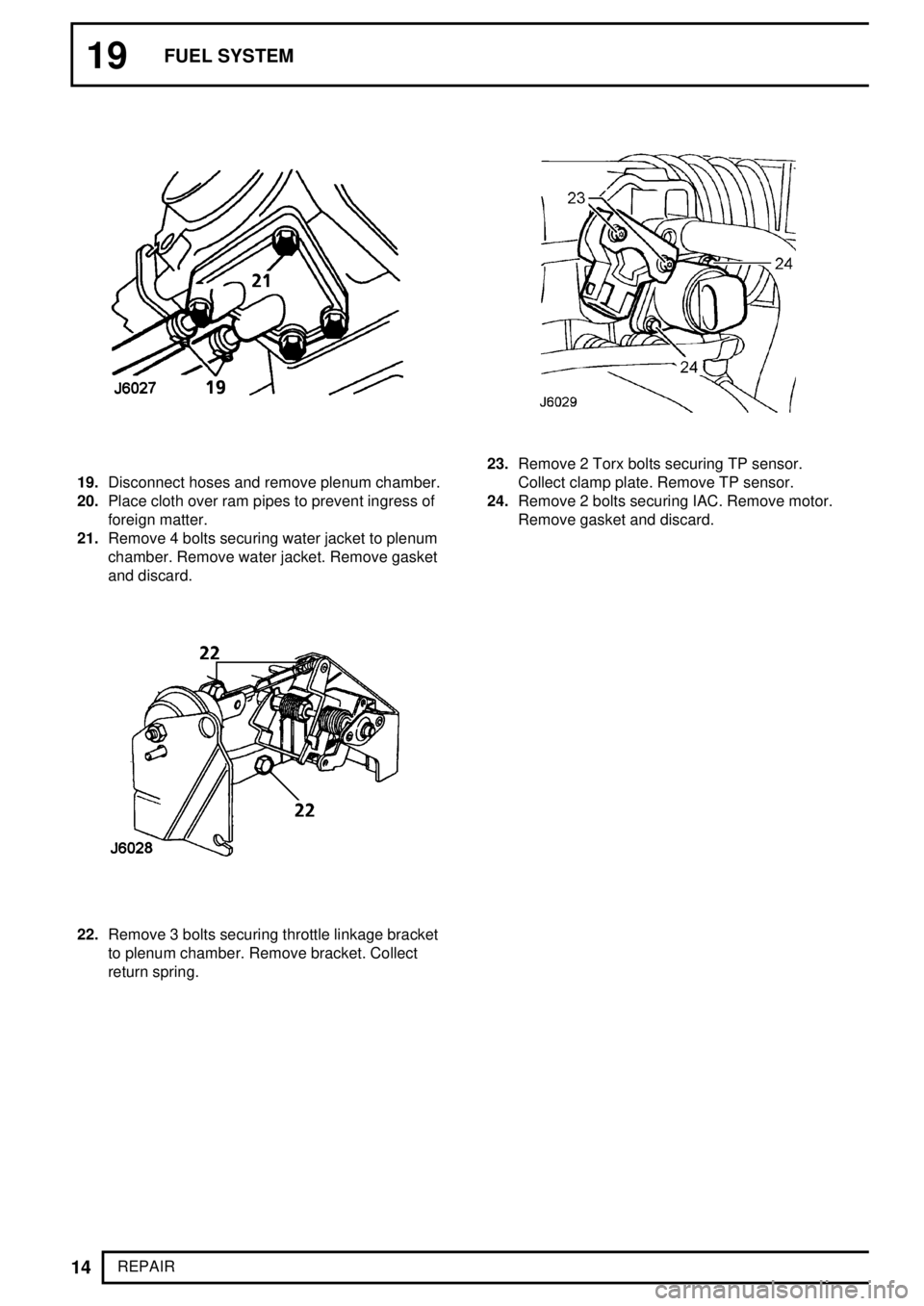
19FUEL SYSTEM
14
REPAIR
19.Disconnect hoses and remove plenum chamber.
20.Place cloth over ram pipes to prevent ingress of
foreign matter.
21.Remove 4 bolts securing water jacket to plenum
chamber. Remove water jacket. Remove gasket
and discard.
22.Remove 3 bolts securing throttle linkage bracket
to plenum chamber. Remove bracket. Collect
return spring.
23.Remove 2 Torx bolts securing TP sensor.
Collect clamp plate. Remove TP sensor.
24.Remove 2 bolts securing IAC. Remove motor.
Remove gasket and discard.
Page 298 of 873
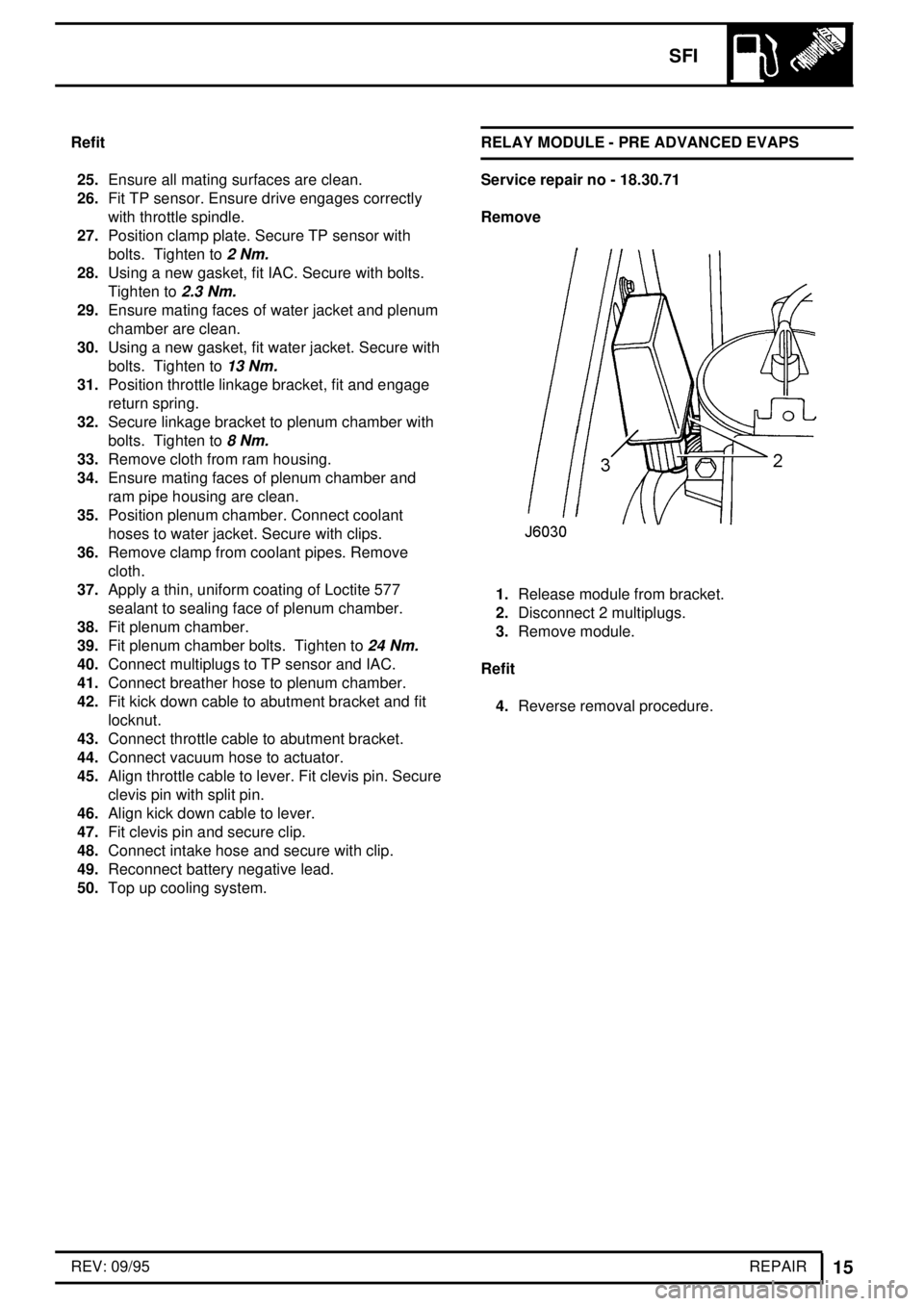
SFI
15
REPAIR REV: 09/95 Refit
25.Ensure all mating surfaces are clean.
26.Fit TP sensor. Ensure drive engages correctly
with throttle spindle.
27.Position clamp plate. Secure TP sensor with
bolts. Tighten to
2 Nm.
28.Using a new gasket, fit IAC. Secure with bolts.
Tighten to
2.3 Nm.
29.Ensure mating faces of water jacket and plenum
chamber are clean.
30.Using a new gasket, fit water jacket. Secure with
bolts. Tighten to
13 Nm.
31.Position throttle linkage bracket, fit and engage
return spring.
32.Secure linkage bracket to plenum chamber with
bolts. Tighten to
8 Nm.
33.Remove cloth from ram housing.
34.Ensure mating faces of plenum chamber and
ram pipe housing are clean.
35.Position plenum chamber. Connect coolant
hoses to water jacket. Secure with clips.
36.Remove clamp from coolant pipes. Remove
cloth.
37.Apply a thin, uniform coating of Loctite 577
sealant to sealing face of plenum chamber.
38.Fit plenum chamber.
39.Fit plenum chamber bolts. Tighten to
24 Nm.
40.Connect multiplugs to TP sensor and IAC.
41.Connect breather hose to plenum chamber.
42.Fit kick down cable to abutment bracket and fit
locknut.
43.Connect throttle cable to abutment bracket.
44.Connect vacuum hose to actuator.
45.Align throttle cable to lever. Fit clevis pin. Secure
clevis pin with split pin.
46.Align kick down cable to lever.
47.Fit clevis pin and secure clip.
48.Connect intake hose and secure with clip.
49.Reconnect battery negative lead.
50.Top up cooling system.RELAY MODULE - PRE ADVANCED EVAPS
Service repair no - 18.30.71
Remove
1.Release module from bracket.
2.Disconnect 2 multiplugs.
3.Remove module.
Refit
4.Reverse removal procedure.
Page 299 of 873
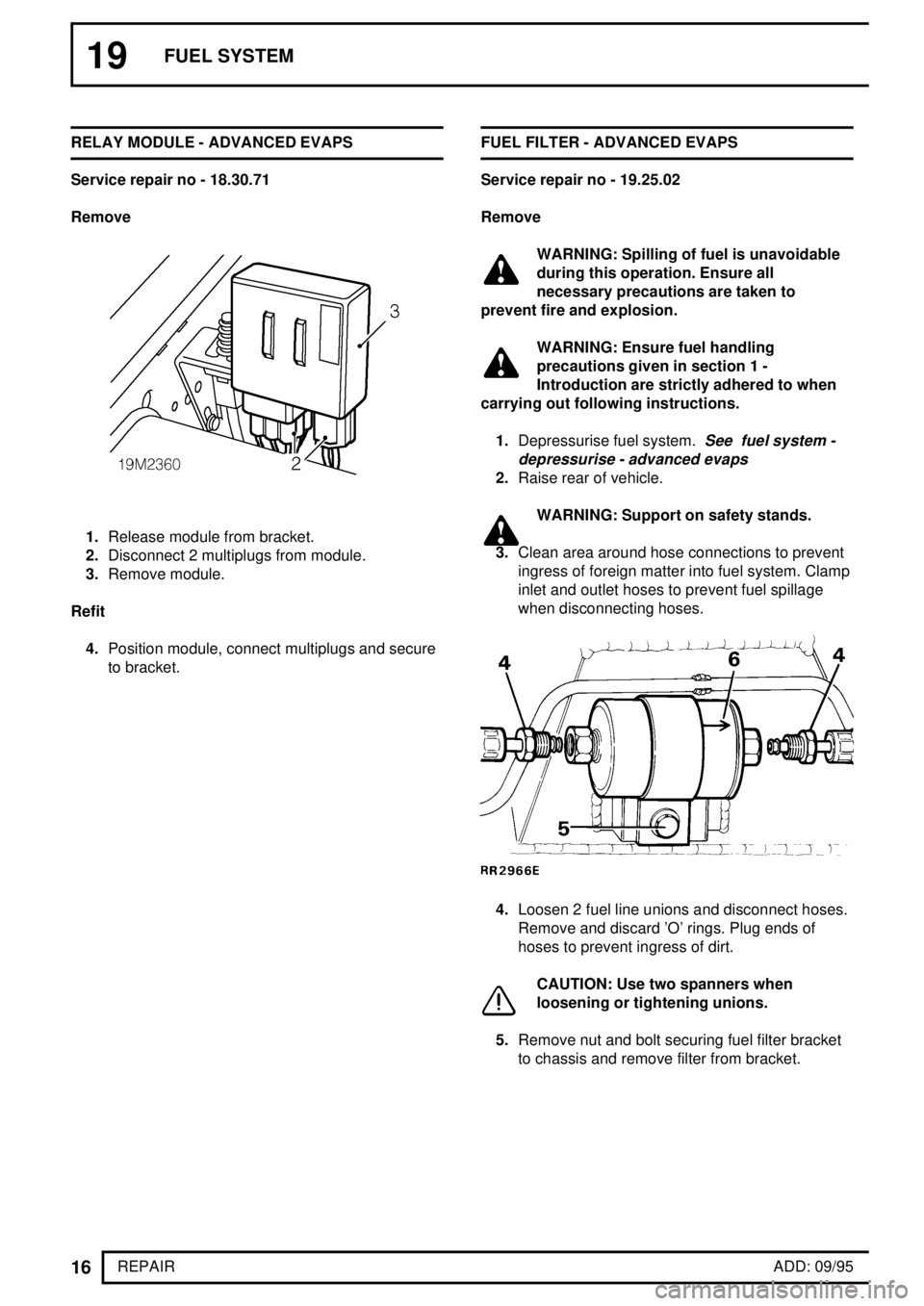
19FUEL SYSTEM
16
REPAIRADD: 09/95 RELAY MODULE - ADVANCED EVAPS
Service repair no - 18.30.71
Remove
1.Release module from bracket.
2.Disconnect 2 multiplugs from module.
3.Remove module.
Refit
4.Position module, connect multiplugs and secure
to bracket.FUEL FILTER - ADVANCED EVAPS
Service repair no - 19.25.02
Remove
WARNING: Spilling of fuel is unavoidable
during this operation. Ensure all
necessary precautions are taken to
prevent fire and explosion.
WARNING: Ensure fuel handling
precautions given in section 1 -
Introduction are strictly adhered to when
carrying out following instructions.
1.Depressurise fuel system.
See fuel system -
depressurise - advanced evaps
2.Raise rear of vehicle.
WARNING: Support on safety stands.
3.Clean area around hose connections to prevent
ingress of foreign matter into fuel system. Clamp
inlet and outlet hoses to prevent fuel spillage
when disconnecting hoses.
4.Loosen 2 fuel line unions and disconnect hoses.
Remove and discard 'O' rings. Plug ends of
hoses to prevent ingress of dirt.
CAUTION: Use two spanners when
loosening or tightening unions.
5.Remove nut and bolt securing fuel filter bracket
to chassis and remove filter from bracket.
Page 300 of 873
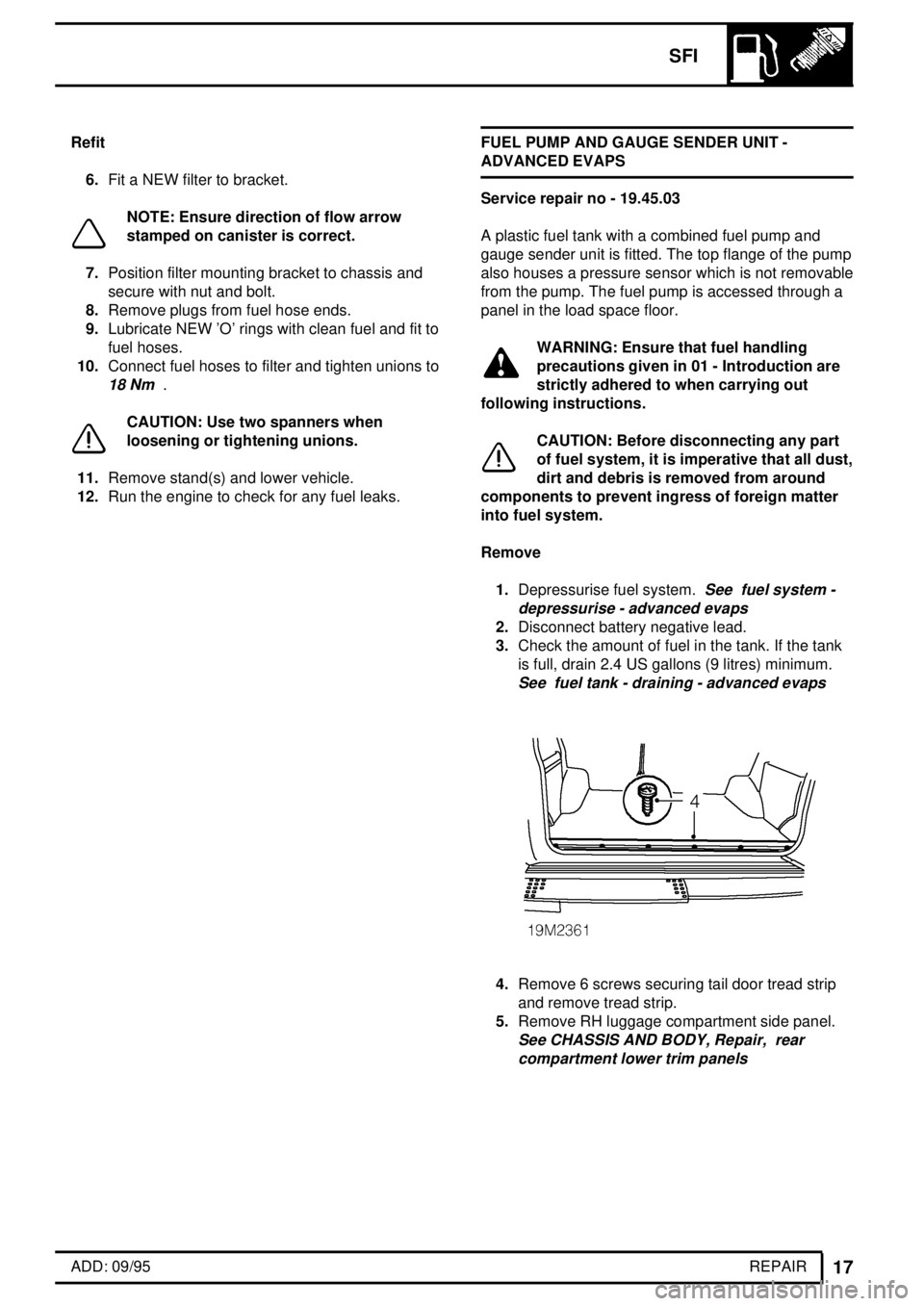
SFI
17
REPAIR ADD: 09/95 Refit
6.Fit a NEW filter to bracket.
NOTE: Ensure direction of flow arrow
stamped on canister is correct.
7.Position filter mounting bracket to chassis and
secure with nut and bolt.
8.Remove plugs from fuel hose ends.
9.Lubricate NEW 'O' rings with clean fuel and fit to
fuel hoses.
10.Connect fuel hoses to filter and tighten unions to
18 Nm.
CAUTION: Use two spanners when
loosening or tightening unions.
11.Remove stand(s) and lower vehicle.
12.Run the engine to check for any fuel leaks.FUEL PUMP AND GAUGE SENDER UNIT -
ADVANCED EVAPS
Service repair no - 19.45.03
A plastic fuel tank with a combined fuel pump and
gauge sender unit is fitted. The top flange of the pump
also houses a pressure sensor which is not removable
from the pump. The fuel pump is accessed through a
panel in the load space floor.
WARNING: Ensure that fuel handling
precautions given in 01 - Introduction are
strictly adhered to when carrying out
following instructions.
CAUTION: Before disconnecting any part
of fuel system, it is imperative that all dust,
dirt and debris is removed from around
components to prevent ingress of foreign matter
into fuel system.
Remove
1.Depressurise fuel system.
See fuel system -
depressurise - advanced evaps
2.Disconnect battery negative lead.
3.Check the amount of fuel in the tank. If the tank
is full, drain 2.4 US gallons (9 litres) minimum.
See fuel tank - draining - advanced evaps
4.Remove 6 screws securing tail door tread strip
and remove tread strip.
5.Remove RH luggage compartment side panel.
See CHASSIS AND BODY, Repair, rear
compartment lower trim panels