sensor LAND ROVER DISCOVERY 1995 Owner's Guide
[x] Cancel search | Manufacturer: LAND ROVER, Model Year: 1995, Model line: DISCOVERY, Model: LAND ROVER DISCOVERY 1995Pages: 873, PDF Size: 12.89 MB
Page 166 of 873
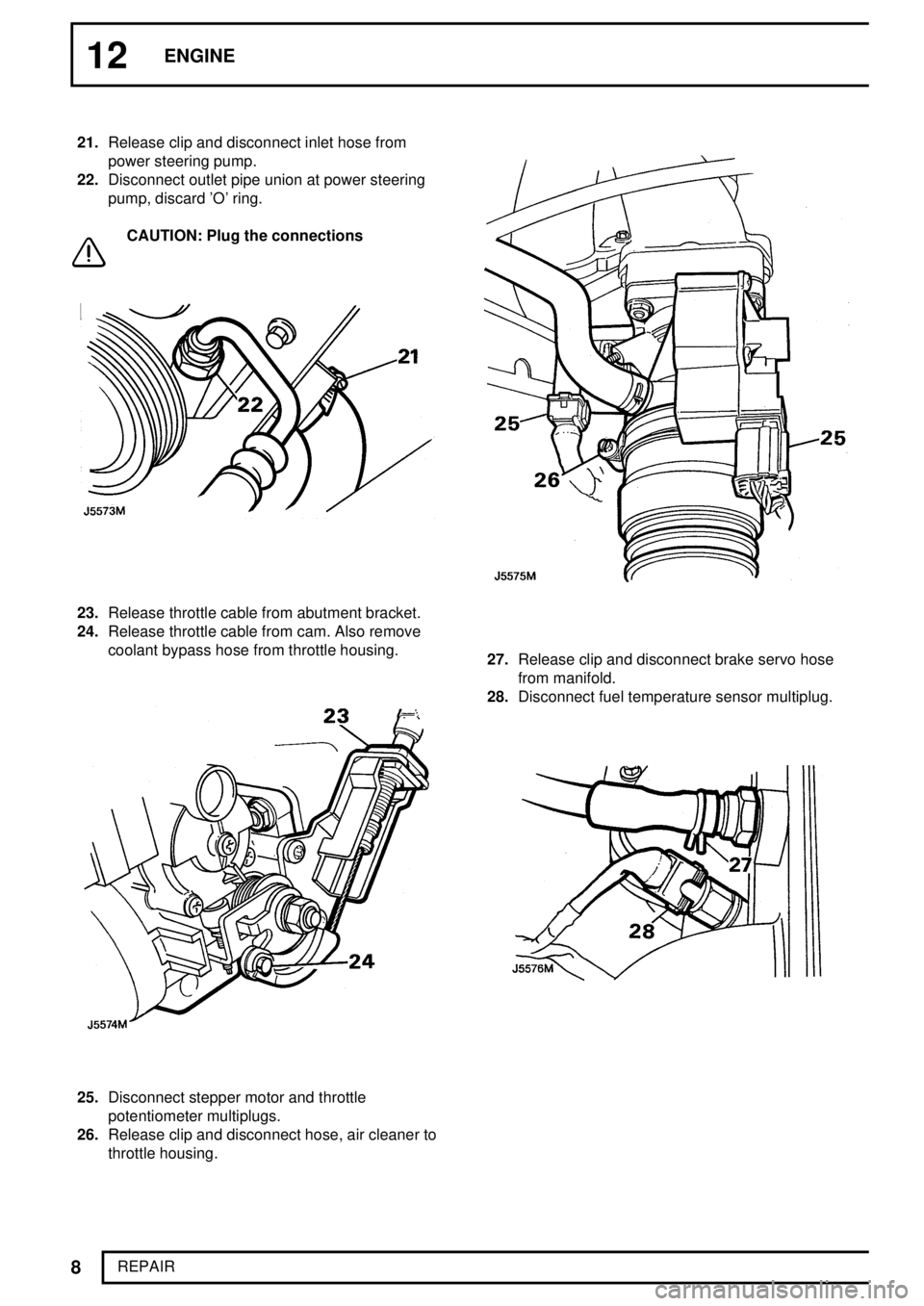
12ENGINE
8
REPAIR 21.Release clip and disconnect inlet hose from
power steering pump.
22.Disconnect outlet pipe union at power steering
pump, discard 'O' ring.
CAUTION: Plug the connections
23.Release throttle cable from abutment bracket.
24.Release throttle cable from cam. Also remove
coolant bypass hose from throttle housing.
25.Disconnect stepper motor and throttle
potentiometer multiplugs.
26.Release clip and disconnect hose, air cleaner to
throttle housing.
27.Release clip and disconnect brake servo hose
from manifold.
28.Disconnect fuel temperature sensor multiplug.
Page 167 of 873
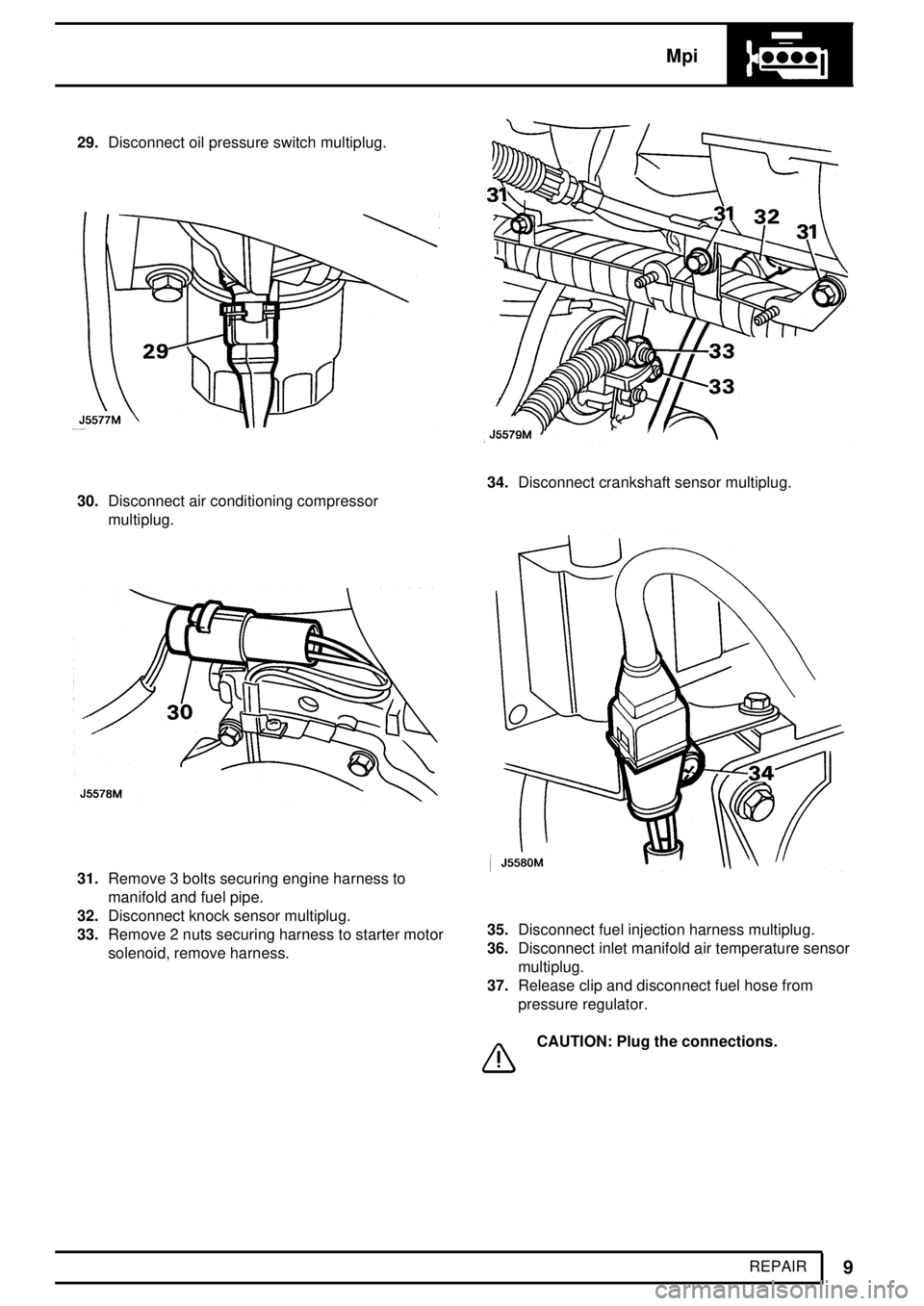
Mpi
9
REPAIR 29.Disconnect oil pressure switch multiplug.
30.Disconnect air conditioning compressor
multiplug.
31.Remove 3 bolts securing engine harness to
manifold and fuel pipe.
32.Disconnect knock sensor multiplug.
33.Remove 2 nuts securing harness to starter motor
solenoid, remove harness.
34.Disconnect crankshaft sensor multiplug.
35.Disconnect fuel injection harness multiplug.
36.Disconnect inlet manifold air temperature sensor
multiplug.
37.Release clip and disconnect fuel hose from
pressure regulator.
CAUTION: Plug the connections.
Page 171 of 873
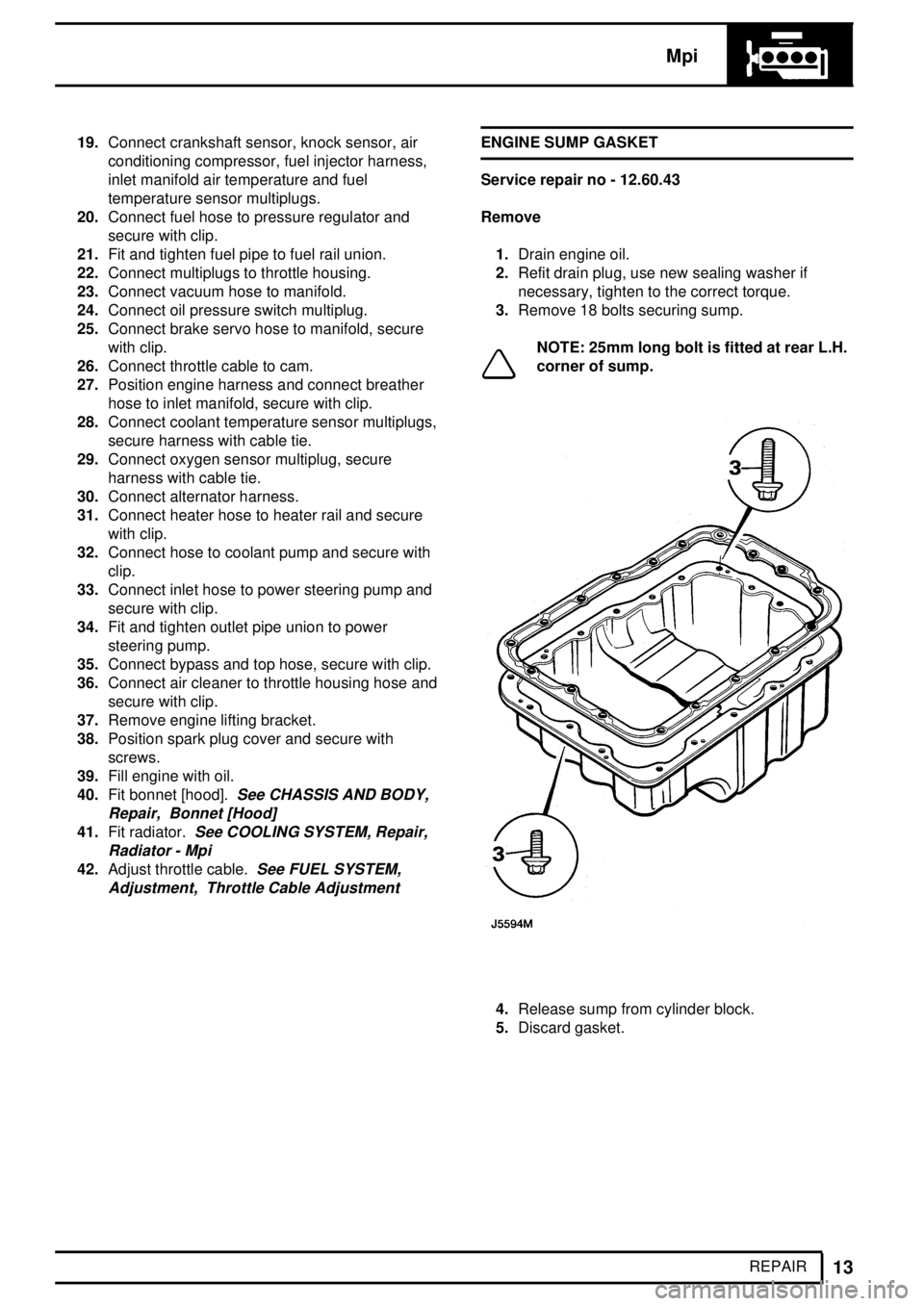
Mpi
13
REPAIR 19.Connect crankshaft sensor, knock sensor, air
conditioning compressor, fuel injector harness,
inlet manifold air temperature and fuel
temperature sensor multiplugs.
20.Connect fuel hose to pressure regulator and
secure with clip.
21.Fit and tighten fuel pipe to fuel rail union.
22.Connect multiplugs to throttle housing.
23.Connect vacuum hose to manifold.
24.Connect oil pressure switch multiplug.
25.Connect brake servo hose to manifold, secure
with clip.
26.Connect throttle cable to cam.
27.Position engine harness and connect breather
hose to inlet manifold, secure with clip.
28.Connect coolant temperature sensor multiplugs,
secure harness with cable tie.
29.Connect oxygen sensor multiplug, secure
harness with cable tie.
30.Connect alternator harness.
31.Connect heater hose to heater rail and secure
with clip.
32.Connect hose to coolant pump and secure with
clip.
33.Connect inlet hose to power steering pump and
secure with clip.
34.Fit and tighten outlet pipe union to power
steering pump.
35.Connect bypass and top hose, secure with clip.
36.Connect air cleaner to throttle housing hose and
secure with clip.
37.Remove engine lifting bracket.
38.Position spark plug cover and secure with
screws.
39.Fill engine with oil.
40.Fit bonnet [hood].
See CHASSIS AND BODY,
Repair, Bonnet [Hood]
41.Fit radiator.See COOLING SYSTEM, Repair,
Radiator - Mpi
42.Adjust throttle cable.See FUEL SYSTEM,
Adjustment, Throttle Cable Adjustment
ENGINE SUMP GASKET
Service repair no - 12.60.43
Remove
1.Drain engine oil.
2.Refit drain plug, use new sealing washer if
necessary, tighten to the correct torque.
3.Remove 18 bolts securing sump.
NOTE: 25mm long bolt is fitted at rear L.H.
corner of sump.
4.Release sump from cylinder block.
5.Discard gasket.
Page 173 of 873
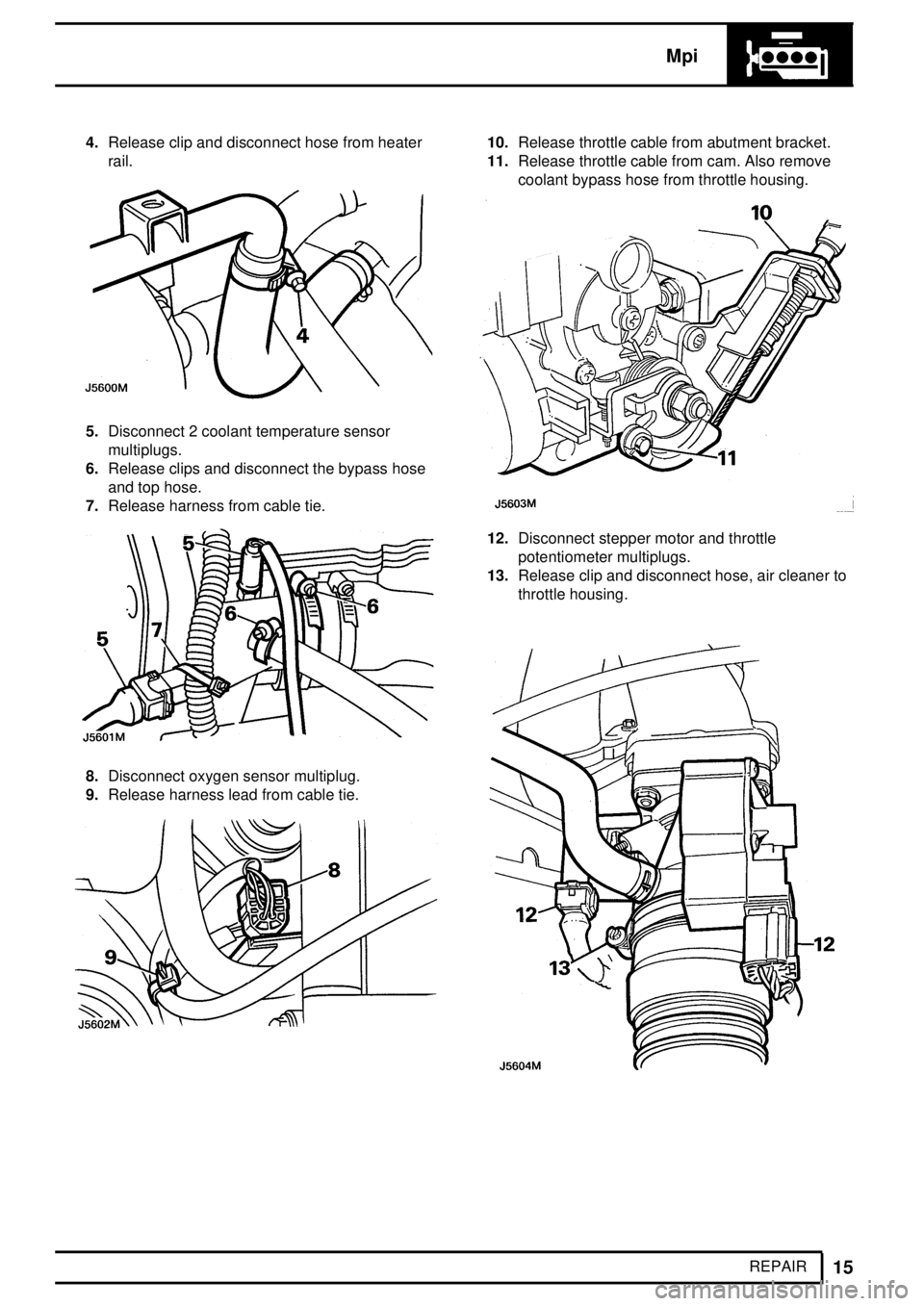
Mpi
15
REPAIR 4.Release clip and disconnect hose from heater
rail.
5.Disconnect 2 coolant temperature sensor
multiplugs.
6.Release clips and disconnect the bypass hose
and top hose.
7.Release harness from cable tie.
8.Disconnect oxygen sensor multiplug.
9.Release harness lead from cable tie.
10.Release throttle cable from abutment bracket.
11.Release throttle cable from cam. Also remove
coolant bypass hose from throttle housing.
12.Disconnect stepper motor and throttle
potentiometer multiplugs.
13.Release clip and disconnect hose, air cleaner to
throttle housing.
Page 174 of 873
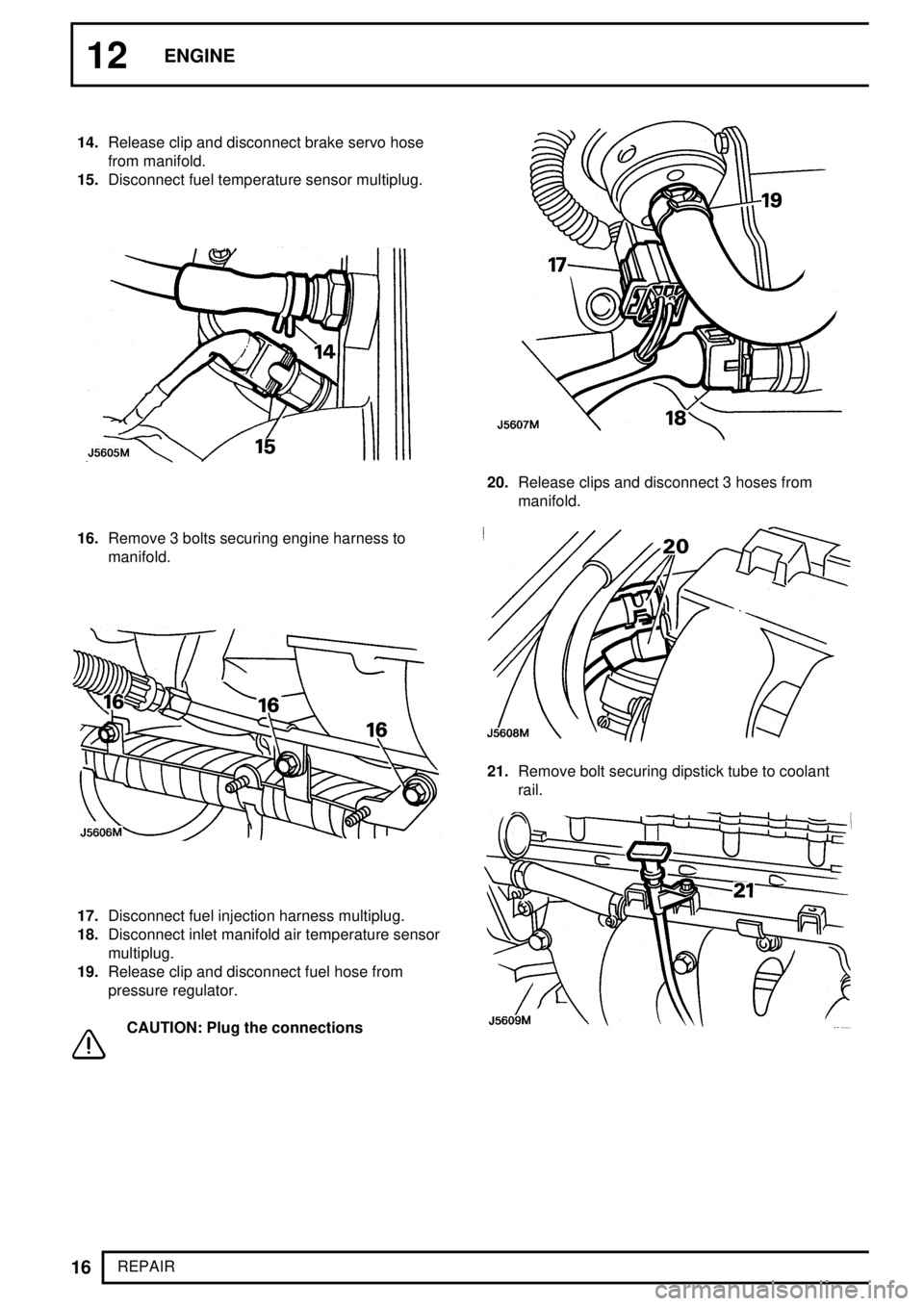
12ENGINE
16
REPAIR 14.Release clip and disconnect brake servo hose
from manifold.
15.Disconnect fuel temperature sensor multiplug.
16.Remove 3 bolts securing engine harness to
manifold.
17.Disconnect fuel injection harness multiplug.
18.Disconnect inlet manifold air temperature sensor
multiplug.
19.Release clip and disconnect fuel hose from
pressure regulator.
CAUTION: Plug the connections
20.Release clips and disconnect 3 hoses from
manifold.
21.Remove bolt securing dipstick tube to coolant
rail.
Page 176 of 873
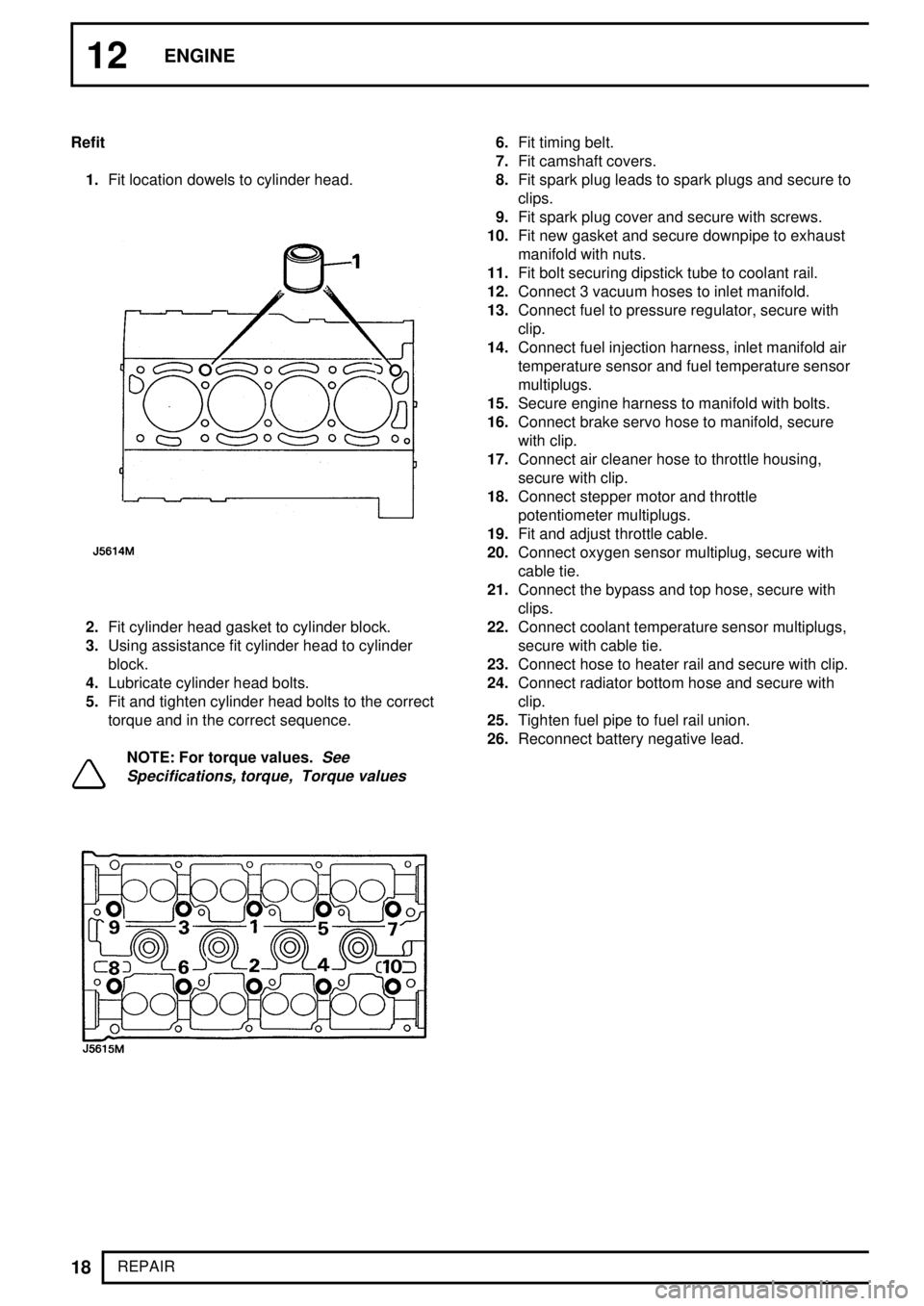
12ENGINE
18
REPAIR Refit
1.Fit location dowels to cylinder head.
2.Fit cylinder head gasket to cylinder block.
3.Using assistance fit cylinder head to cylinder
block.
4.Lubricate cylinder head bolts.
5.Fit and tighten cylinder head bolts to the correct
torque and in the correct sequence.
NOTE: For torque values.See
Specifications, torque, Torque values
6.Fit timing belt.
7.Fit camshaft covers.
8.Fit spark plug leads to spark plugs and secure to
clips.
9.Fit spark plug cover and secure with screws.
10.Fit new gasket and secure downpipe to exhaust
manifold with nuts.
11.Fit bolt securing dipstick tube to coolant rail.
12.Connect 3 vacuum hoses to inlet manifold.
13.Connect fuel to pressure regulator, secure with
clip.
14.Connect fuel injection harness, inlet manifold air
temperature sensor and fuel temperature sensor
multiplugs.
15.Secure engine harness to manifold with bolts.
16.Connect brake servo hose to manifold, secure
with clip.
17.Connect air cleaner hose to throttle housing,
secure with clip.
18.Connect stepper motor and throttle
potentiometer multiplugs.
19.Fit and adjust throttle cable.
20.Connect oxygen sensor multiplug, secure with
cable tie.
21.Connect the bypass and top hose, secure with
clips.
22.Connect coolant temperature sensor multiplugs,
secure with cable tie.
23.Connect hose to heater rail and secure with clip.
24.Connect radiator bottom hose and secure with
clip.
25.Tighten fuel pipe to fuel rail union.
26.Reconnect battery negative lead.
Page 182 of 873
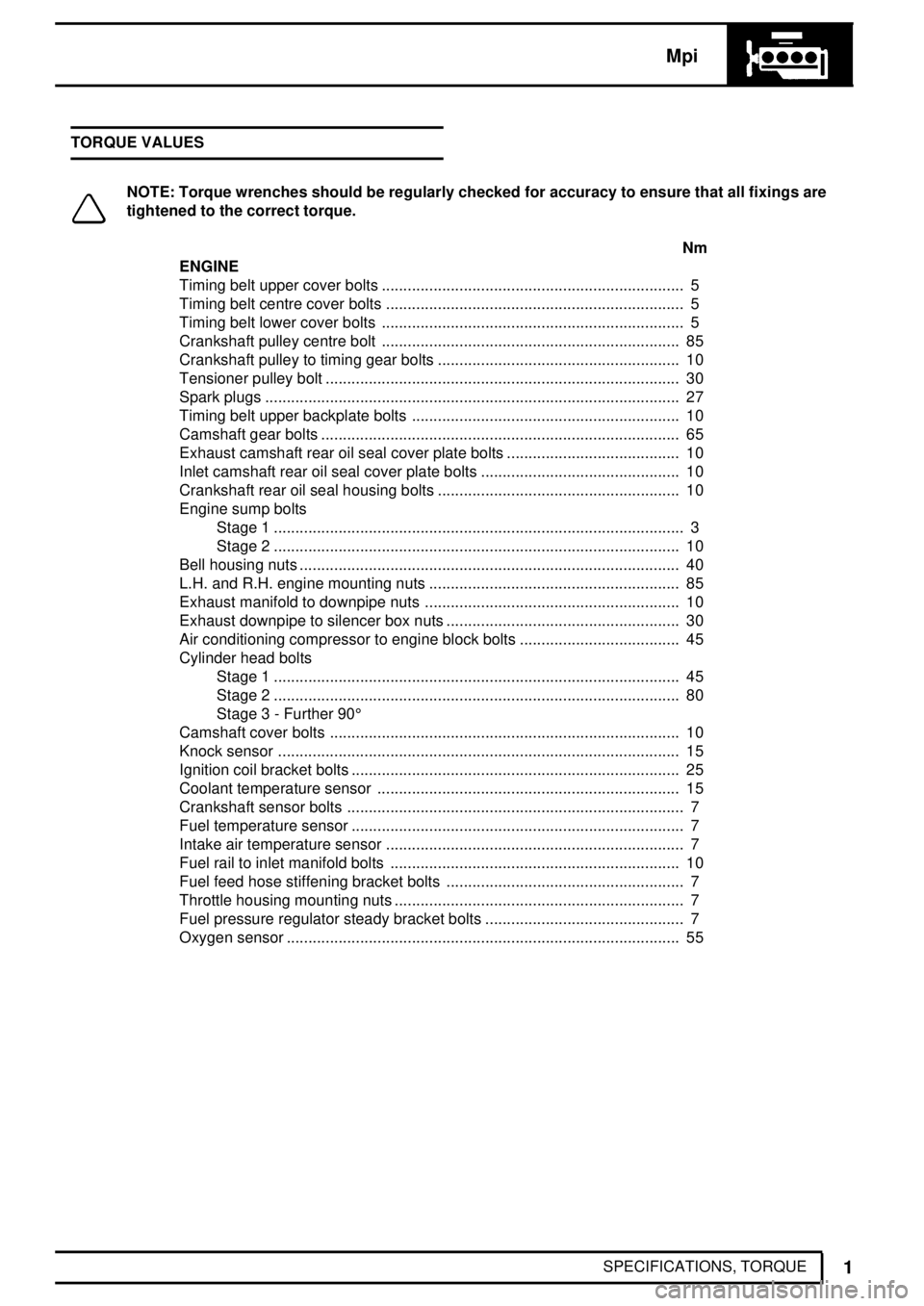
Mpi
1
SPECIFICATIONS, TORQUE TORQUE VALUES
NOTE: Torque wrenches should be regularly checked for accuracy to ensure that all fixings are
tightened to the correct torque.
Nm
ENGINE
Timing belt upper cover bolts 5......................................................................
Timing belt centre cover bolts 5.....................................................................
Timing belt lower cover bolts 5......................................................................
Crankshaft pulley centre bolt 85.....................................................................
Crankshaft pulley to timing gear bolts 10........................................................
Tensioner pulley bolt 30..................................................................................
Spark plugs 27................................................................................................
Timing belt upper backplate bolts 10..............................................................
Camshaft gear bolts 65...................................................................................
Exhaust camshaft rear oil seal cover plate bolts 10........................................
Inlet camshaft rear oil seal cover plate bolts 10..............................................
Crankshaft rear oil seal housing bolts 10........................................................
Engine sump bolts
Stage 1 3...............................................................................................
Stage 2 10..............................................................................................
Bell housing nuts 40........................................................................................
L.H. and R.H. engine mounting nuts 85..........................................................
Exhaust manifold to downpipe nuts 10...........................................................
Exhaust downpipe to silencer box nuts 30......................................................
Air conditioning compressor to engine block bolts 45.....................................
Cylinder head bolts
Stage 1 45..............................................................................................
Stage 2 80..............................................................................................
Stage 3 - Further 90°
Camshaft cover bolts 10.................................................................................
Knock sensor 15.............................................................................................
Ignition coil bracket bolts 25............................................................................
Coolant temperature sensor 15......................................................................
Crankshaft sensor bolts 7..............................................................................
Fuel temperature sensor 7.............................................................................
Intake air temperature sensor 7.....................................................................
Fuel rail to inlet manifold bolts 10...................................................................
Fuel feed hose stiffening bracket bolts 7.......................................................
Throttle housing mounting nuts 7...................................................................
Fuel pressure regulator steady bracket bolts 7..............................................
Oxygen sensor 55...........................................................................................
Page 188 of 873
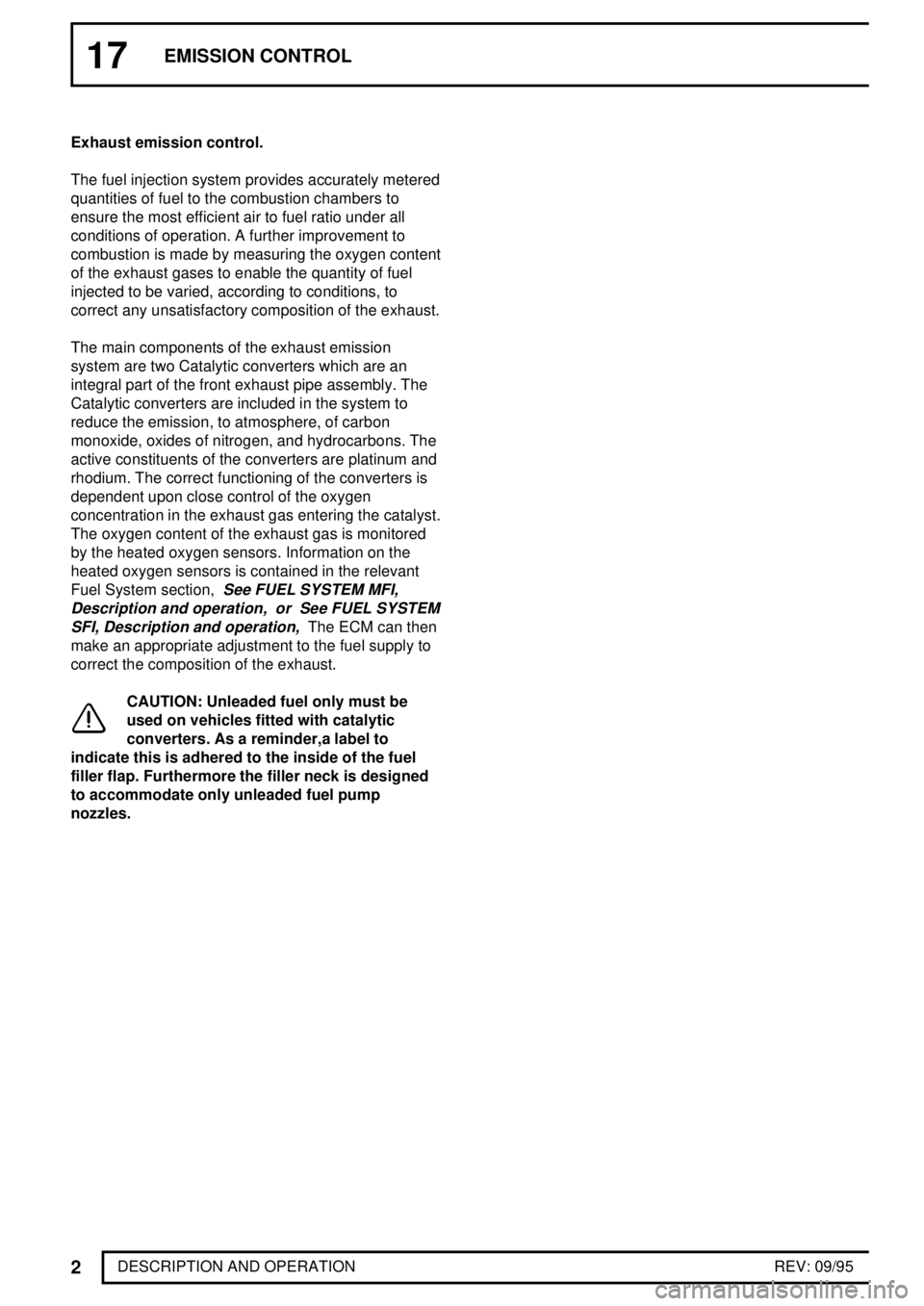
17EMISSION CONTROL
2
DESCRIPTION AND OPERATION REV: 09/95 Exhaust emission control.
The fuel injection system provides accurately metered
quantities of fuel to the combustion chambers to
ensure the most efficient air to fuel ratio under all
conditions of operation. A further improvement to
combustion is made by measuring the oxygen content
of the exhaust gases to enable the quantity of fuel
injected to be varied, according to conditions, to
correct any unsatisfactory composition of the exhaust.
The main components of the exhaust emission
system are two Catalytic converters which are an
integral part of the front exhaust pipe assembly. The
Catalytic converters are included in the system to
reduce the emission, to atmosphere, of carbon
monoxide, oxides of nitrogen, and hydrocarbons. The
active constituents of the converters are platinum and
rhodium. The correct functioning of the converters is
dependent upon close control of the oxygen
concentration in the exhaust gas entering the catalyst.
The oxygen content of the exhaust gas is monitored
by the heated oxygen sensors. Information on the
heated oxygen sensors is contained in the relevant
Fuel System section,
See FUEL SYSTEM MFI,
Description and operation, or See FUEL SYSTEM
SFI, Description and operation,
The ECM can then
make an appropriate adjustment to the fuel supply to
correct the composition of the exhaust.
CAUTION: Unleaded fuel only must be
used on vehicles fitted with catalytic
converters. As a reminder,a label to
indicate this is adhered to the inside of the fuel
filler flap. Furthermore the filler neck is designed
to accommodate only unleaded fuel pump
nozzles.
Page 189 of 873
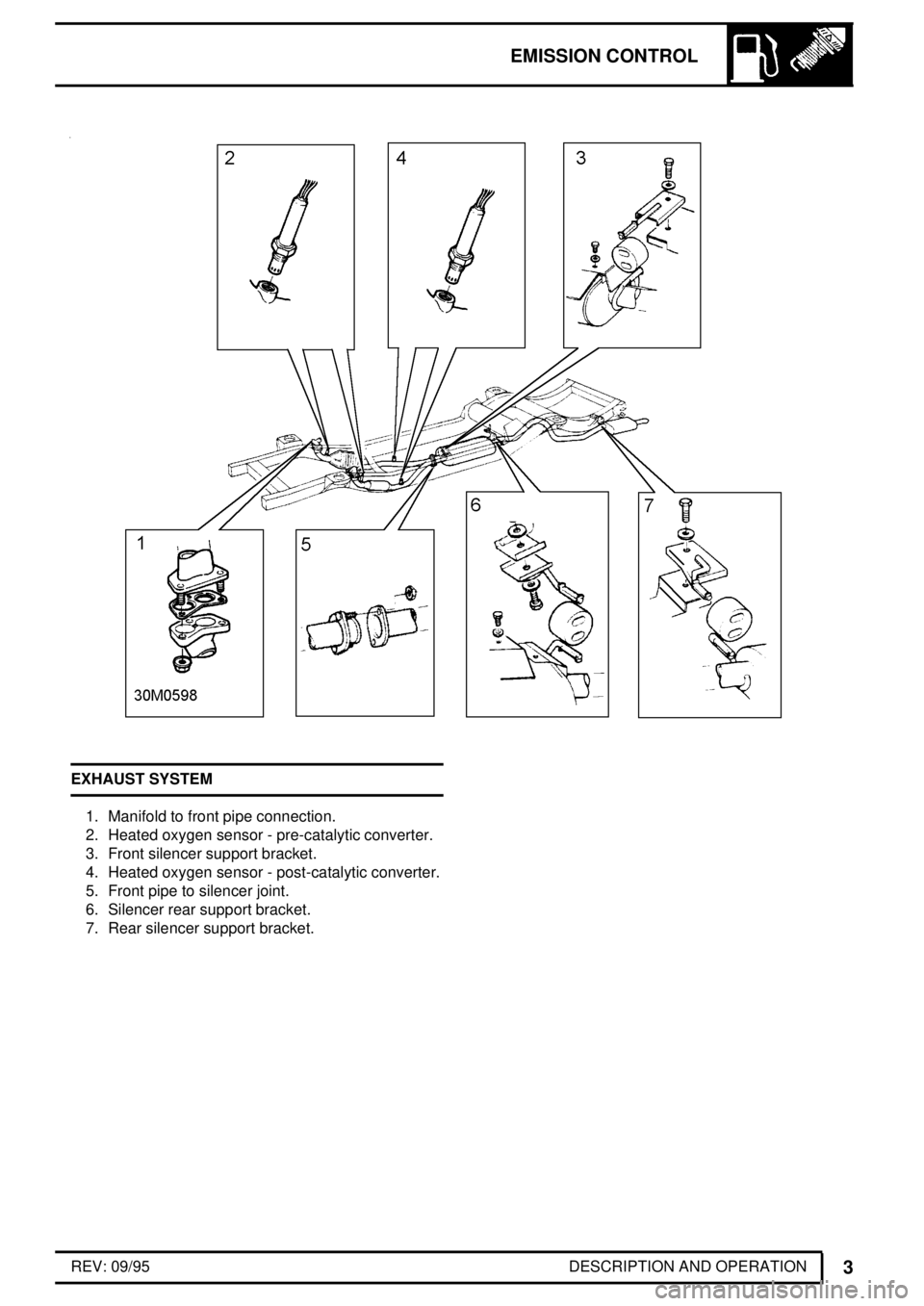
EMISSION CONTROL
3
DESCRIPTION AND OPERATION REV: 09/95
EXHAUST SYSTEM
1. Manifold to front pipe connection.
2. Heated oxygen sensor - pre-catalytic converter.
3. Front silencer support bracket.
4. Heated oxygen sensor - post-catalytic converter.
5. Front pipe to silencer joint.
6. Silencer rear support bracket.
7. Rear silencer support bracket.
Page 193 of 873
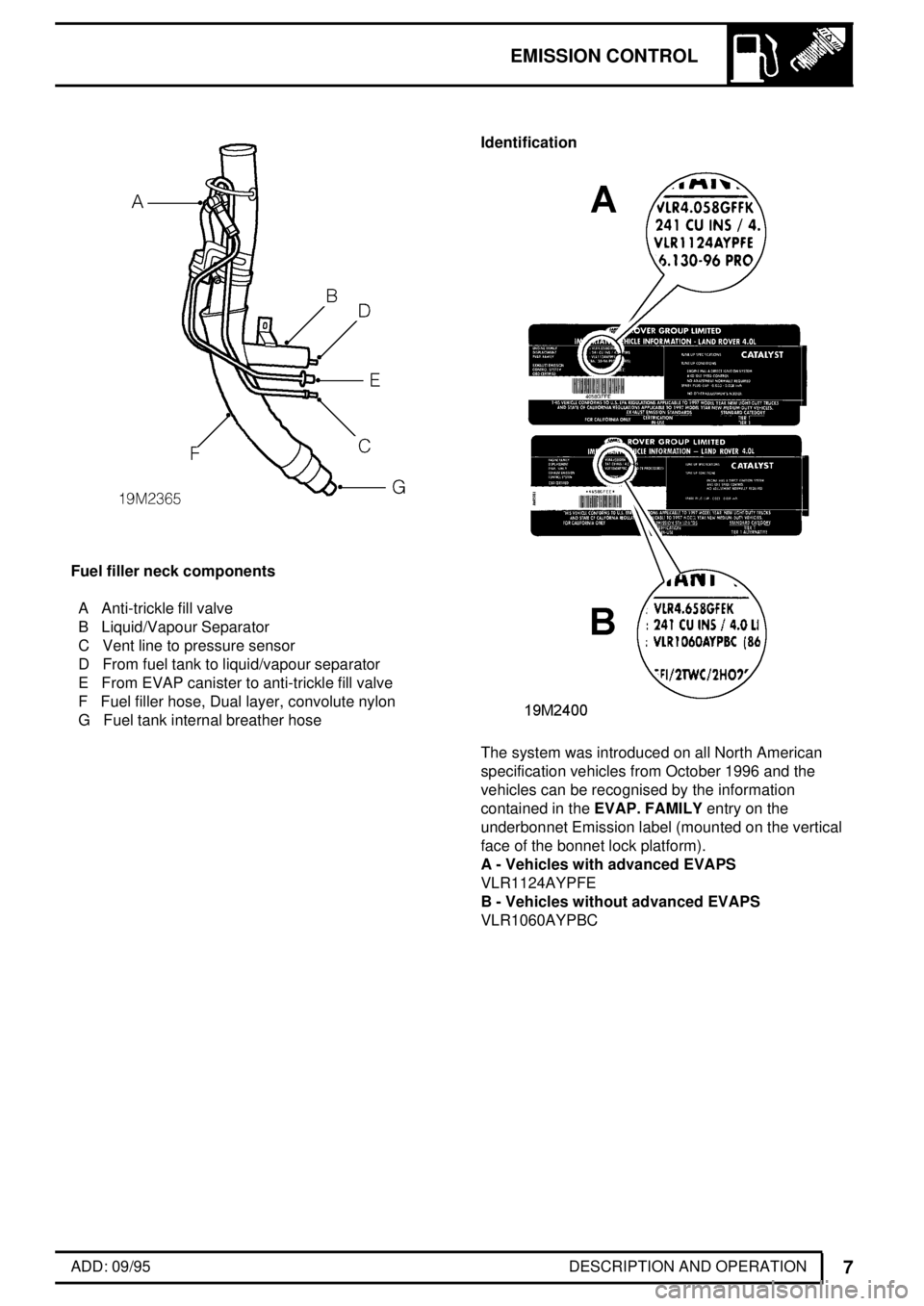
EMISSION CONTROL
7
DESCRIPTION AND OPERATION ADD: 09/95
Fuel filler neck components
A Anti-trickle fill valve
B Liquid/Vapour Separator
C Vent line to pressure sensor
D From fuel tank to liquid/vapour separator
E From EVAP canister to anti-trickle fill valve
F Fuel filler hose, Dual layer, convolute nylon
G Fuel tank internal breather hoseIdentification
The system was introduced on all North American
specification vehicles from October 1996 and the
vehicles can be recognised by the information
contained in theEVAP. FAMILYentry on the
underbonnet Emission label (mounted on the vertical
face of the bonnet lock platform).
A - Vehicles with advanced EVAPS
VLR1124AYPFE
B - Vehicles without advanced EVAPS
VLR1060AYPBC