sensor LAND ROVER DISCOVERY 1995 Repair Manual
[x] Cancel search | Manufacturer: LAND ROVER, Model Year: 1995, Model line: DISCOVERY, Model: LAND ROVER DISCOVERY 1995Pages: 873, PDF Size: 12.89 MB
Page 238 of 873
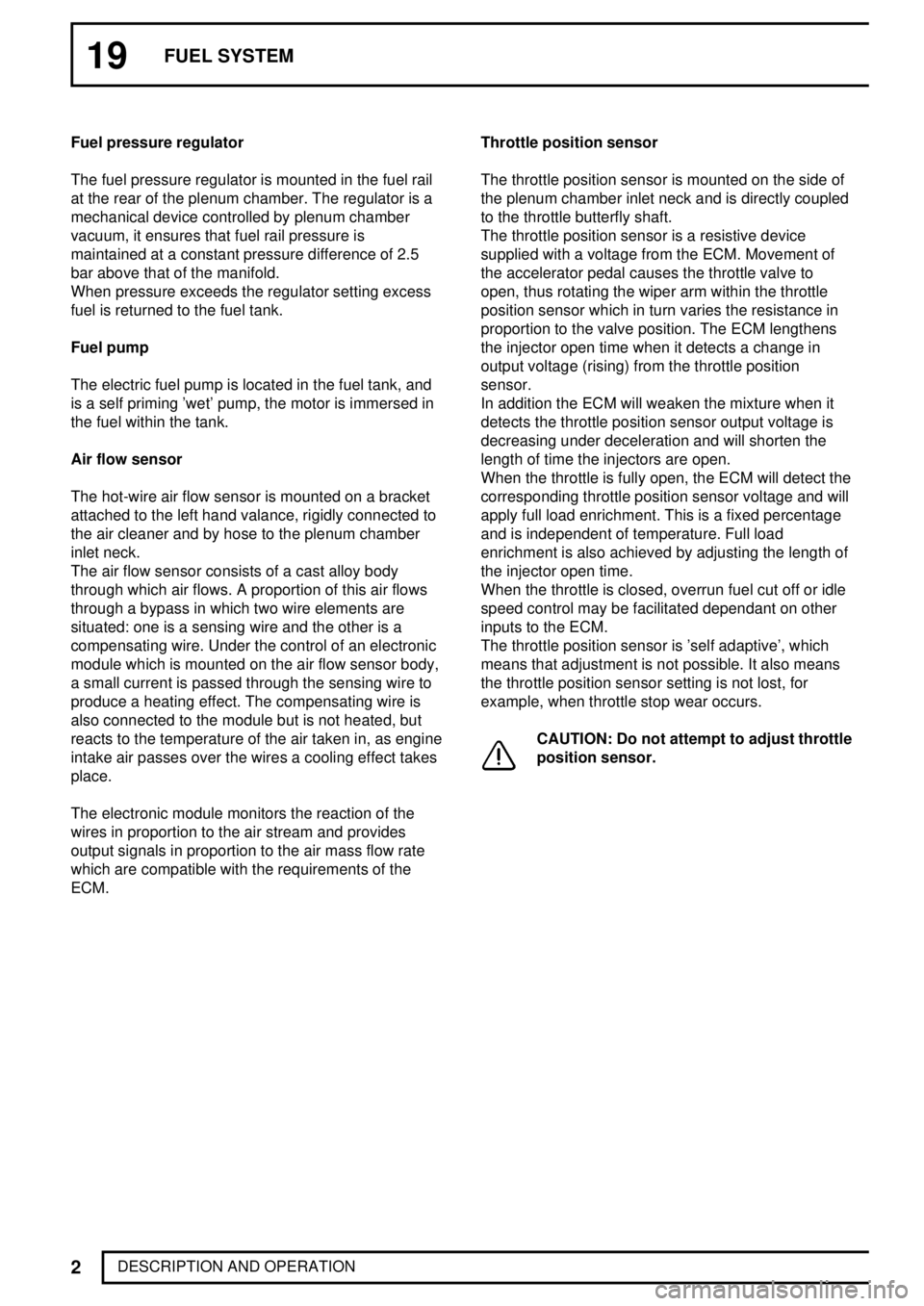
19FUEL SYSTEM
2
DESCRIPTION AND OPERATION Fuel pressure regulator
The fuel pressure regulator is mounted in the fuel rail
at the rear of the plenum chamber. The regulator is a
mechanical device controlled by plenum chamber
vacuum, it ensures that fuel rail pressure is
maintained at a constant pressure difference of 2.5
bar above that of the manifold.
When pressure exceeds the regulator setting excess
fuel is returned to the fuel tank.
Fuel pump
The electric fuel pump is located in the fuel tank, and
is a self priming 'wet' pump, the motor is immersed in
the fuel within the tank.
Air flow sensor
The hot-wire air flow sensor is mounted on a bracket
attached to the left hand valance, rigidly connected to
the air cleaner and by hose to the plenum chamber
inlet neck.
The air flow sensor consists of a cast alloy body
through which air flows. A proportion of this air flows
through a bypass in which two wire elements are
situated: one is a sensing wire and the other is a
compensating wire. Under the control of an electronic
module which is mounted on the air flow sensor body,
a small current is passed through the sensing wire to
produce a heating effect. The compensating wire is
also connected to the module but is not heated, but
reacts to the temperature of the air taken in, as engine
intake air passes over the wires a cooling effect takes
place.
The electronic module monitors the reaction of the
wires in proportion to the air stream and provides
output signals in proportion to the air mass flow rate
which are compatible with the requirements of the
ECM.Throttle position sensor
The throttle position sensor is mounted on the side of
the plenum chamber inlet neck and is directly coupled
to the throttle butterfly shaft.
The throttle position sensor is a resistive device
supplied with a voltage from the ECM. Movement of
the accelerator pedal causes the throttle valve to
open, thus rotating the wiper arm within the throttle
position sensor which in turn varies the resistance in
proportion to the valve position. The ECM lengthens
the injector open time when it detects a change in
output voltage (rising) from the throttle position
sensor.
In addition the ECM will weaken the mixture when it
detects the throttle position sensor output voltage is
decreasing under deceleration and will shorten the
length of time the injectors are open.
When the throttle is fully open, the ECM will detect the
corresponding throttle position sensor voltage and will
apply full load enrichment. This is a fixed percentage
and is independent of temperature. Full load
enrichment is also achieved by adjusting the length of
the injector open time.
When the throttle is closed, overrun fuel cut off or idle
speed control may be facilitated dependant on other
inputs to the ECM.
The throttle position sensor is 'self adaptive', which
means that adjustment is not possible. It also means
the throttle position sensor setting is not lost, for
example, when throttle stop wear occurs.
CAUTION: Do not attempt to adjust throttle
position sensor.
Page 239 of 873
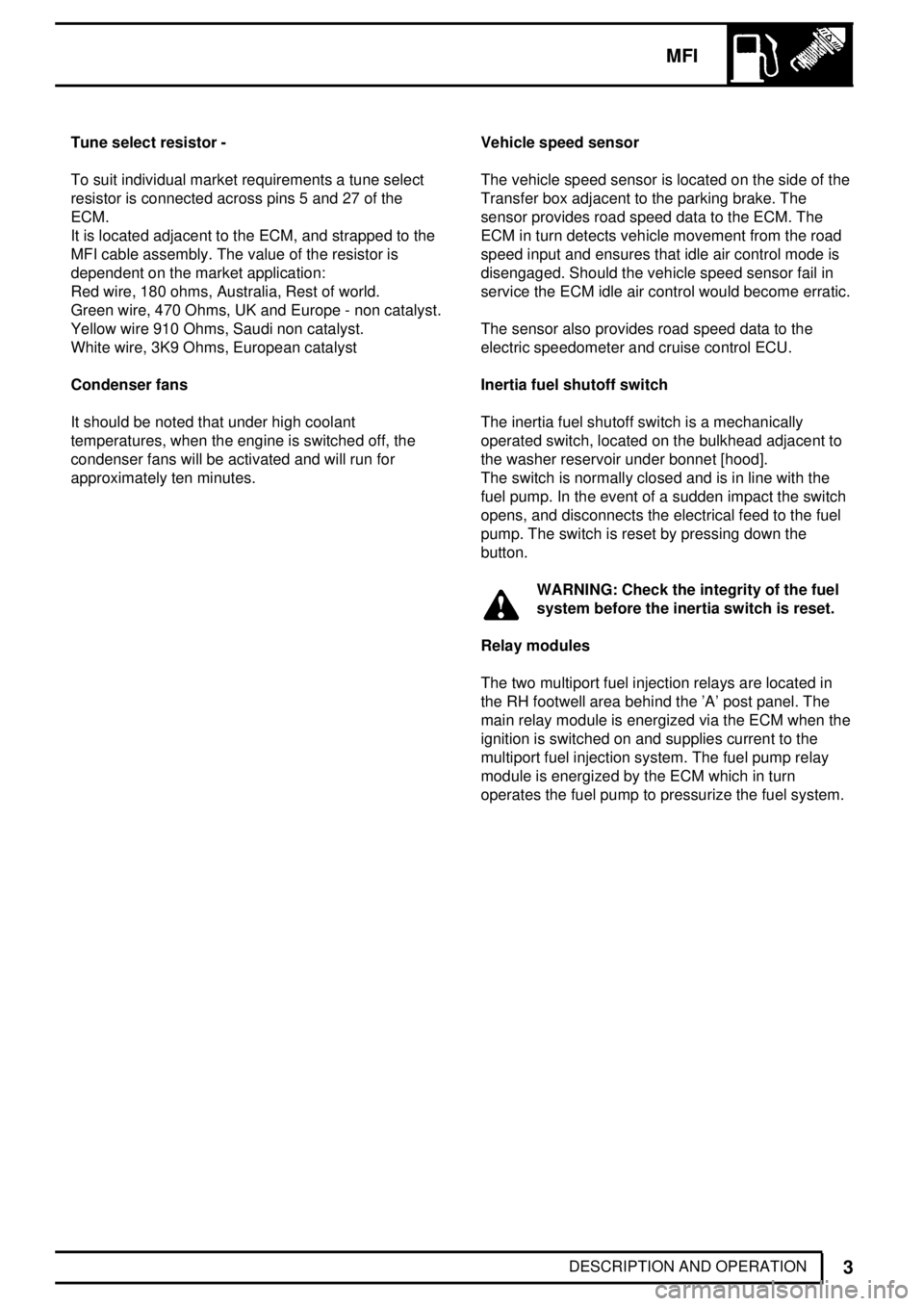
MFI
3
DESCRIPTION AND OPERATION Tune select resistor -
To suit individual market requirements a tune select
resistor is connected across pins 5 and 27 of the
ECM.
It is located adjacent to the ECM, and strapped to the
MFI cable assembly. The value of the resistor is
dependent on the market application:
Red wire, 180 ohms, Australia, Rest of world.
Green wire, 470 Ohms, UK and Europe - non catalyst.
Yellow wire 910 Ohms, Saudi non catalyst.
White wire, 3K9 Ohms, European catalyst
Condenser fans
It should be noted that under high coolant
temperatures, when the engine is switched off, the
condenser fans will be activated and will run for
approximately ten minutes.Vehicle speed sensor
The vehicle speed sensor is located on the side of the
Transfer box adjacent to the parking brake. The
sensor provides road speed data to the ECM. The
ECM in turn detects vehicle movement from the road
speed input and ensures that idle air control mode is
disengaged. Should the vehicle speed sensor fail in
service the ECM idle air control would become erratic.
The sensor also provides road speed data to the
electric speedometer and cruise control ECU.
Inertia fuel shutoff switch
The inertia fuel shutoff switch is a mechanically
operated switch, located on the bulkhead adjacent to
the washer reservoir under bonnet [hood].
The switch is normally closed and is in line with the
fuel pump. In the event of a sudden impact the switch
opens, and disconnects the electrical feed to the fuel
pump. The switch is reset by pressing down the
button.
WARNING: Check the integrity of the fuel
system before the inertia switch is reset.
Relay modules
The two multiport fuel injection relays are located in
the RH footwell area behind the 'A' post panel. The
main relay module is energized via the ECM when the
ignition is switched on and supplies current to the
multiport fuel injection system. The fuel pump relay
module is energized by the ECM which in turn
operates the fuel pump to pressurize the fuel system.
Page 240 of 873
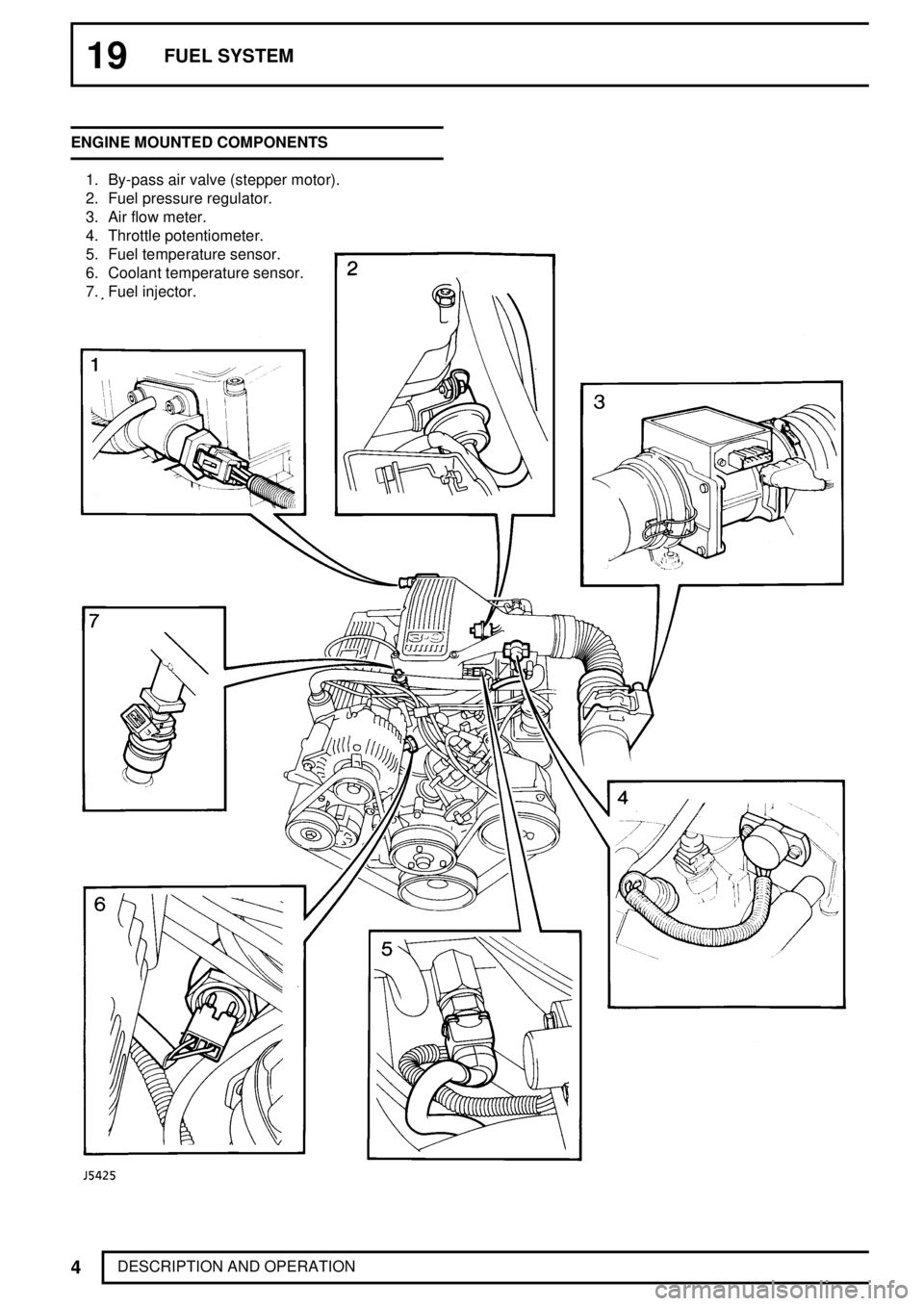
19FUEL SYSTEM
4
DESCRIPTION AND OPERATION ENGINE MOUNTED COMPONENTS
1. By-pass air valve (stepper motor).
2. Fuel pressure regulator.
3. Air flow meter.
4. Throttle potentiometer.
5. Fuel temperature sensor.
6. Coolant temperature sensor.
7. Fuel injector.
Page 247 of 873
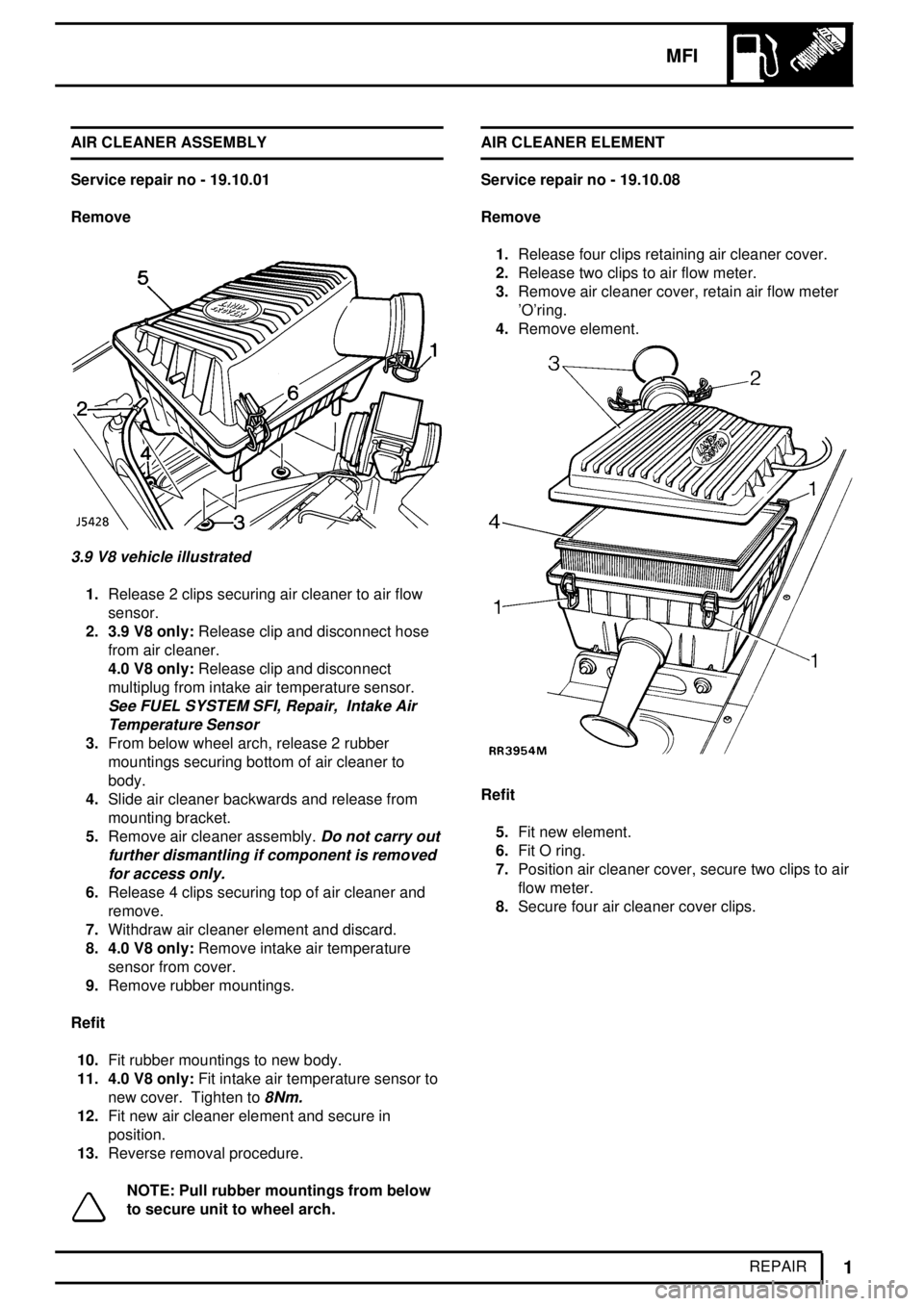
MFI
1
REPAIR AIR CLEANER ASSEMBLY
Service repair no - 19.10.01
Remove
3.9 V8 vehicle illustrated
1.Release 2 clips securing air cleaner to air flow
sensor.
2. 3.9 V8 only:Release clip and disconnect hose
from air cleaner.
4.0 V8 only:Release clip and disconnect
multiplug from intake air temperature sensor.
See FUEL SYSTEM SFI, Repair, Intake Air
Temperature Sensor
3.From below wheel arch, release 2 rubber
mountings securing bottom of air cleaner to
body.
4.Slide air cleaner backwards and release from
mounting bracket.
5.Remove air cleaner assembly.
Do not carry out
further dismantling if component is removed
for access only.
6.Release 4 clips securing top of air cleaner and
remove.
7.Withdraw air cleaner element and discard.
8. 4.0 V8 only:Remove intake air temperature
sensor from cover.
9.Remove rubber mountings.
Refit
10.Fit rubber mountings to new body.
11. 4.0 V8 only:Fit intake air temperature sensor to
new cover. Tighten to
8Nm.
12.Fit new air cleaner element and secure in
position.
13.Reverse removal procedure.
NOTE: Pull rubber mountings from below
to secure unit to wheel arch.AIR CLEANER ELEMENT
Service repair no - 19.10.08
Remove
1.Release four clips retaining air cleaner cover.
2.Release two clips to air flow meter.
3.Remove air cleaner cover, retain air flow meter
'O'ring.
4.Remove element.
Refit
5.Fit new element.
6.Fit O ring.
7.Position air cleaner cover, secure two clips to air
flow meter.
8.Secure four air cleaner cover clips.
Page 248 of 873
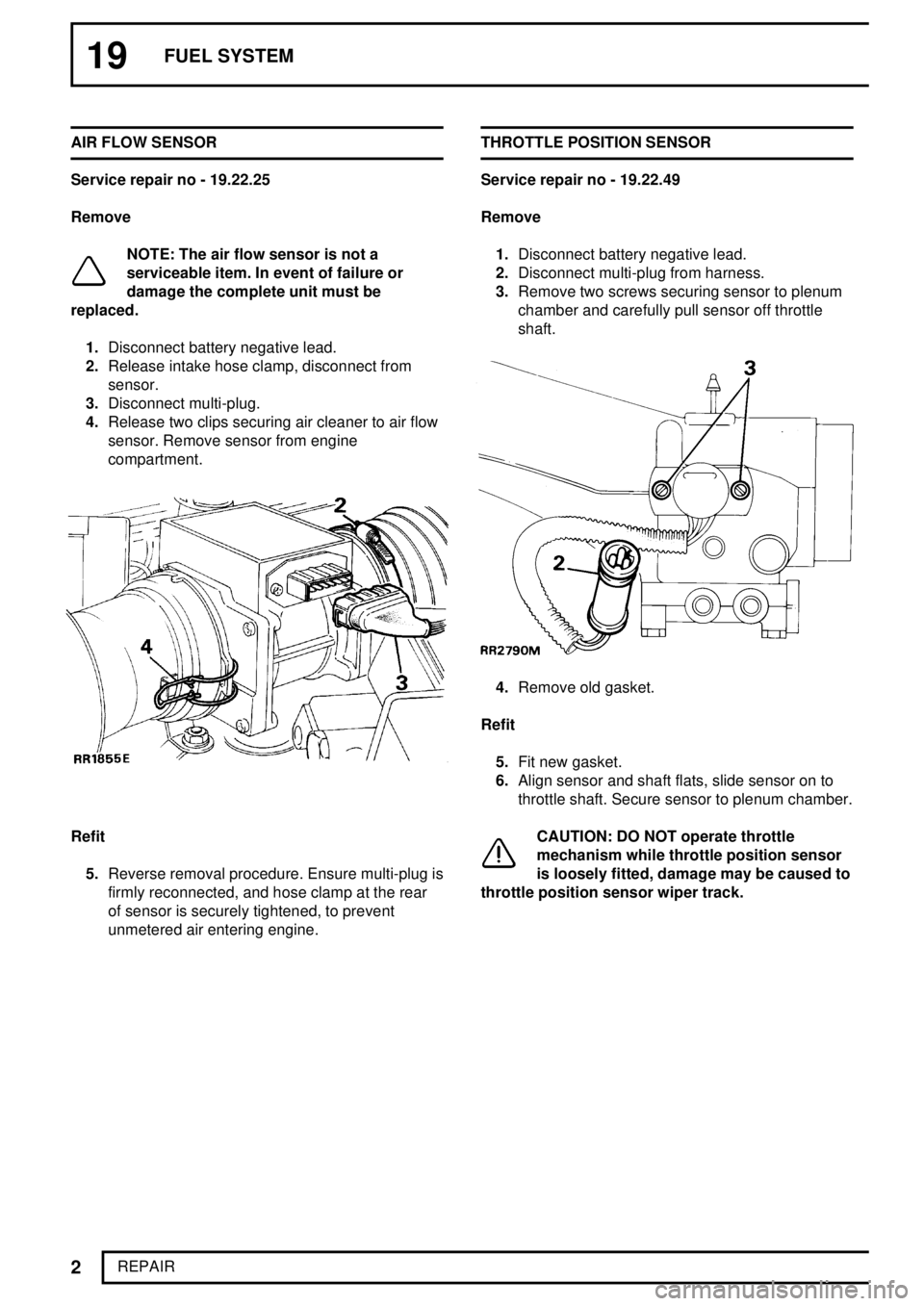
19FUEL SYSTEM
2
REPAIR AIR FLOW SENSOR
Service repair no - 19.22.25
Remove
NOTE: The air flow sensor is not a
serviceable item. In event of failure or
damage the complete unit must be
replaced.
1.Disconnect battery negative lead.
2.Release intake hose clamp, disconnect from
sensor.
3.Disconnect multi-plug.
4.Release two clips securing air cleaner to air flow
sensor. Remove sensor from engine
compartment.
Refit
5.Reverse removal procedure. Ensure multi-plug is
firmly reconnected, and hose clamp at the rear
of sensor is securely tightened, to prevent
unmetered air entering engine.THROTTLE POSITION SENSOR
Service repair no - 19.22.49
Remove
1.Disconnect battery negative lead.
2.Disconnect multi-plug from harness.
3.Remove two screws securing sensor to plenum
chamber and carefully pull sensor off throttle
shaft.
4.Remove old gasket.
Refit
5.Fit new gasket.
6.Align sensor and shaft flats, slide sensor on to
throttle shaft. Secure sensor to plenum chamber.
CAUTION: DO NOT operate throttle
mechanism while throttle position sensor
is loosely fitted, damage may be caused to
throttle position sensor wiper track.
Page 249 of 873
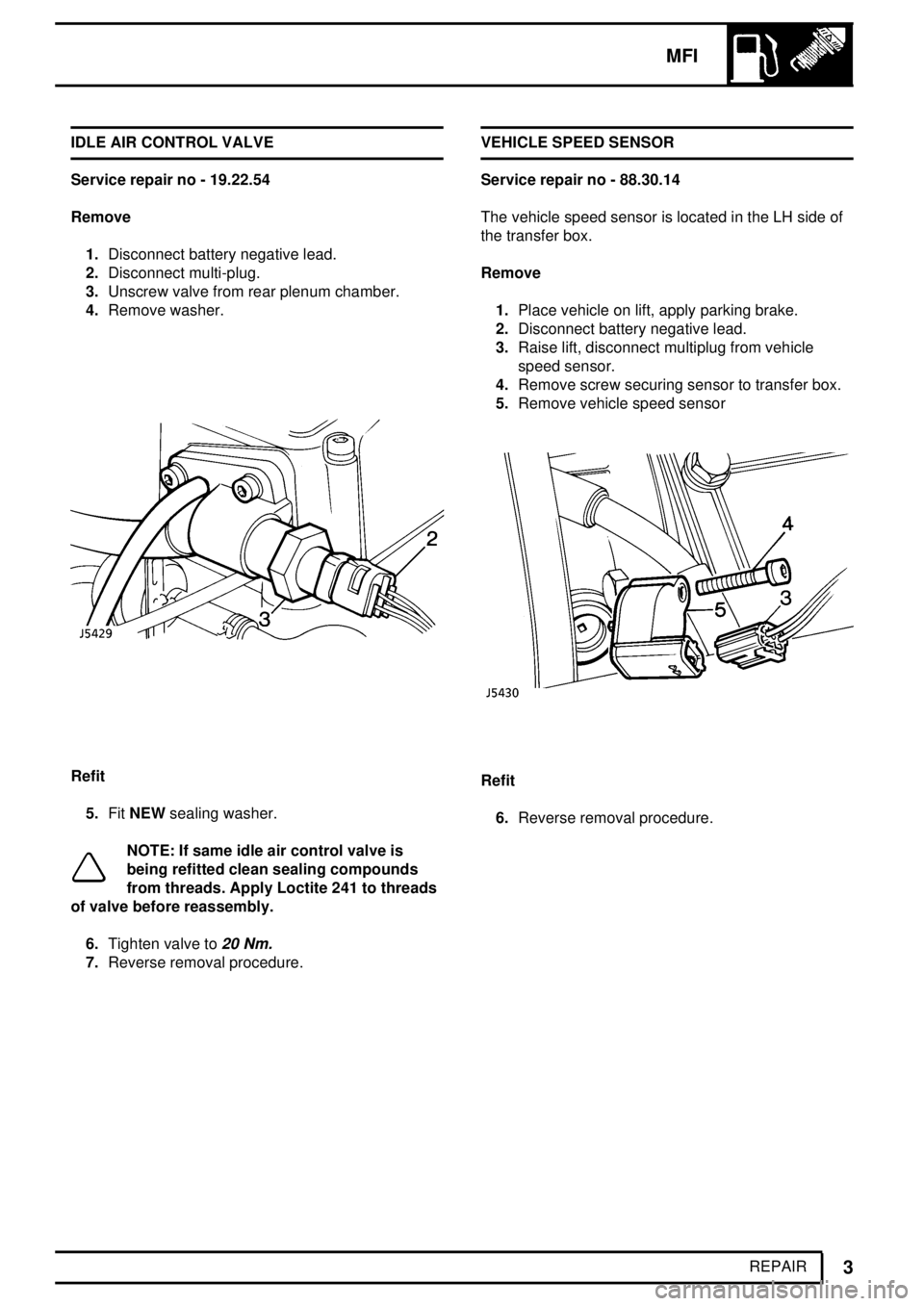
MFI
3
REPAIR IDLE AIR CONTROL VALVE
Service repair no - 19.22.54
Remove
1.Disconnect battery negative lead.
2.Disconnect multi-plug.
3.Unscrew valve from rear plenum chamber.
4.Remove washer.
Refit
5.FitNEWsealing washer.
NOTE: If same idle air control valve is
being refitted clean sealing compounds
from threads. Apply Loctite 241 to threads
of valve before reassembly.
6.Tighten valve to
20 Nm.
7.Reverse removal procedure.VEHICLE SPEED SENSOR
Service repair no - 88.30.14
The vehicle speed sensor is located in the LH side of
the transfer box.
Remove
1.Place vehicle on lift, apply parking brake.
2.Disconnect battery negative lead.
3.Raise lift, disconnect multiplug from vehicle
speed sensor.
4.Remove screw securing sensor to transfer box.
5.Remove vehicle speed sensor
Refit
6.Reverse removal procedure.
Page 251 of 873
![LAND ROVER DISCOVERY 1995 Repair Manual MFI
5
REPAIR INERTIA FUEL SHUTOFF SWITCH
Service repair no - 18.30.35
The inertia fuel shutoff switch is located on the
bulkhead next to the washer reservoir under bonnet
[hood].
Remove
1.Disconnect b LAND ROVER DISCOVERY 1995 Repair Manual MFI
5
REPAIR INERTIA FUEL SHUTOFF SWITCH
Service repair no - 18.30.35
The inertia fuel shutoff switch is located on the
bulkhead next to the washer reservoir under bonnet
[hood].
Remove
1.Disconnect b](/img/64/57248/w960_57248-250.png)
MFI
5
REPAIR INERTIA FUEL SHUTOFF SWITCH
Service repair no - 18.30.35
The inertia fuel shutoff switch is located on the
bulkhead next to the washer reservoir under bonnet
[hood].
Remove
1.Disconnect battery negative lead.
2.Disconnect multiplug from inertia switch.
3.Remove 2 screws securing inertia switch to
mounting bracket.
4.Remove inertia switch.
Refit
5.Position inertia switch to mounting bracket and
secure with screws.
6.Connect multiplug to inertia switch.
7.Reconnect battery negative lead.ENGINE FUEL TEMPERATURE SENSOR
Service repair no - 19.22.08
Remove
NOTE: Fuel leakage will not occur when
sensor is removed from fuel rail, therefore
it is not necessary to depressurise the fuel
system.
1.Disconnect battery negative lead.
2.Disconnect multi-plug from sensor.
3.Release sensor from fuel feed rail.
Refit
4.Reverse removal procedure. Ensure sensor is
tightened securely in fuel rail.
Page 252 of 873
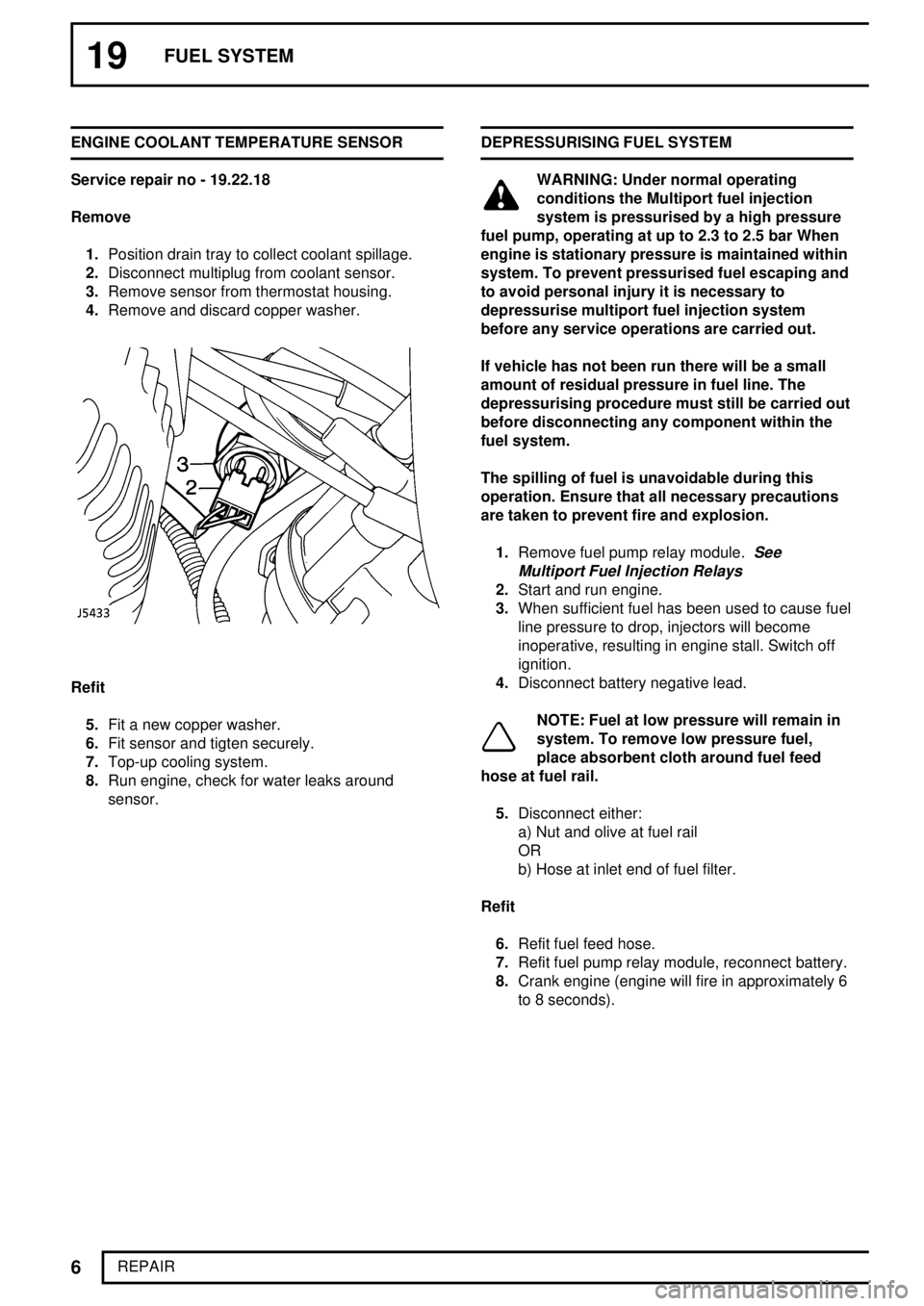
19FUEL SYSTEM
6
REPAIR ENGINE COOLANT TEMPERATURE SENSOR
Service repair no - 19.22.18
Remove
1.Position drain tray to collect coolant spillage.
2.Disconnect multiplug from coolant sensor.
3.Remove sensor from thermostat housing.
4.Remove and discard copper washer.
Refit
5.Fit a new copper washer.
6.Fit sensor and tigten securely.
7.Top-up cooling system.
8.Run engine, check for water leaks around
sensor.DEPRESSURISING FUEL SYSTEM
WARNING: Under normal operating
conditions the Multiport fuel injection
system is pressurised by a high pressure
fuel pump, operating at up to 2.3 to 2.5 bar When
engine is stationary pressure is maintained within
system. To prevent pressurised fuel escaping and
to avoid personal injury it is necessary to
depressurise multiport fuel injection system
before any service operations are carried out.
If vehicle has not been run there will be a small
amount of residual pressure in fuel line. The
depressurising procedure must still be carried out
before disconnecting any component within the
fuel system.
The spilling of fuel is unavoidable during this
operation. Ensure that all necessary precautions
are taken to prevent fire and explosion.
1.Remove fuel pump relay module.
See
Multiport Fuel Injection Relays
2.Start and run engine.
3.When sufficient fuel has been used to cause fuel
line pressure to drop, injectors will become
inoperative, resulting in engine stall. Switch off
ignition.
4.Disconnect battery negative lead.
NOTE: Fuel at low pressure will remain in
system. To remove low pressure fuel,
place absorbent cloth around fuel feed
hose at fuel rail.
5.Disconnect either:
a) Nut and olive at fuel rail
OR
b) Hose at inlet end of fuel filter.
Refit
6.Refit fuel feed hose.
7.Refit fuel pump relay module, reconnect battery.
8.Crank engine (engine will fire in approximately 6
to 8 seconds).
Page 253 of 873
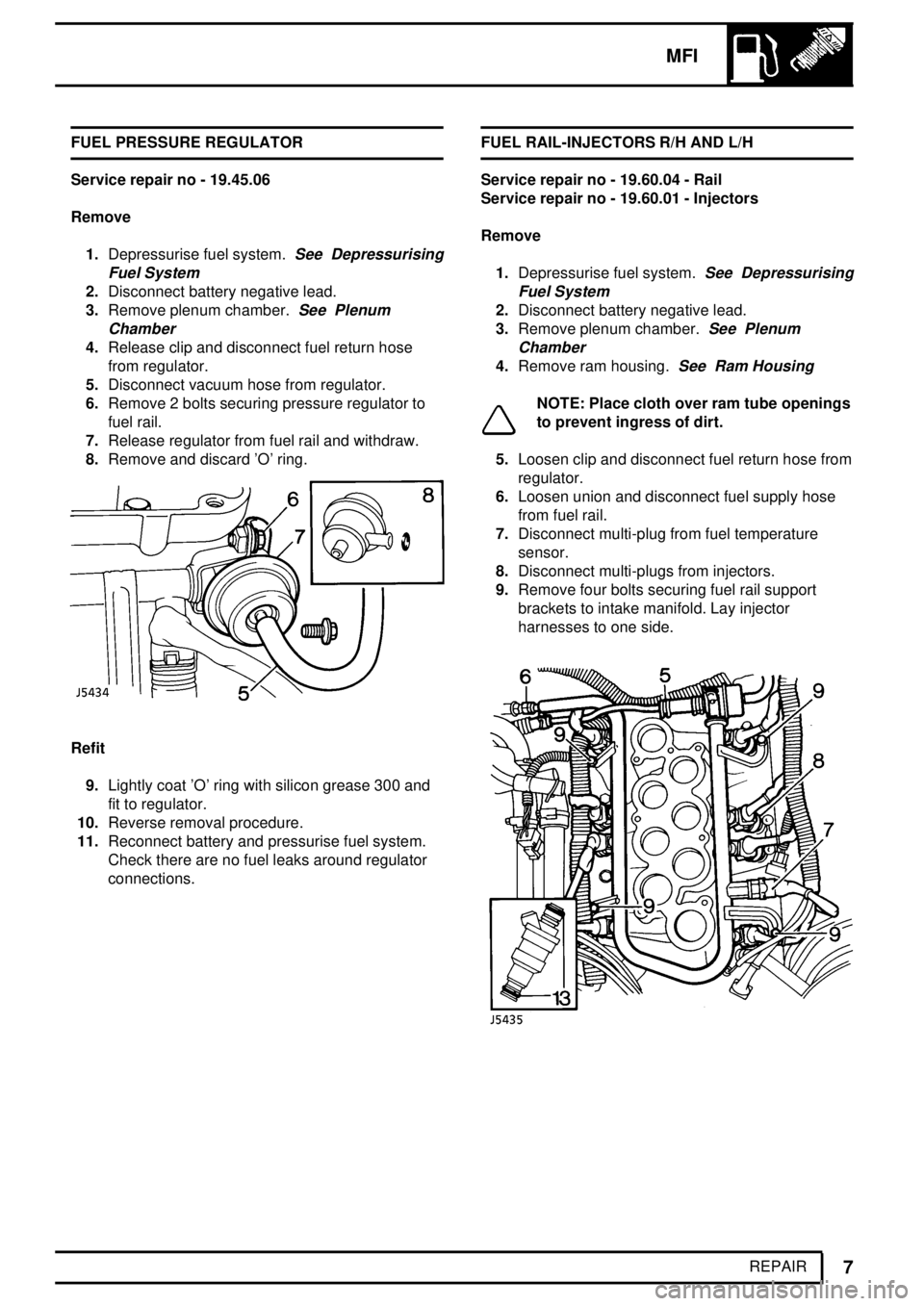
MFI
7
REPAIR FUEL PRESSURE REGULATOR
Service repair no - 19.45.06
Remove
1.Depressurise fuel system.
See Depressurising
Fuel System
2.Disconnect battery negative lead.
3.Remove plenum chamber.
See Plenum
Chamber
4.Release clip and disconnect fuel return hose
from regulator.
5.Disconnect vacuum hose from regulator.
6.Remove 2 bolts securing pressure regulator to
fuel rail.
7.Release regulator from fuel rail and withdraw.
8.Remove and discard 'O' ring.
Refit
9.Lightly coat 'O' ring with silicon grease 300 and
fit to regulator.
10.Reverse removal procedure.
11.Reconnect battery and pressurise fuel system.
Check there are no fuel leaks around regulator
connections.FUEL RAIL-INJECTORS R/H AND L/H
Service repair no - 19.60.04 - Rail
Service repair no - 19.60.01 - Injectors
Remove
1.Depressurise fuel system.
See Depressurising
Fuel System
2.Disconnect battery negative lead.
3.Remove plenum chamber.
See Plenum
Chamber
4.Remove ram housing.See Ram Housing
NOTE: Place cloth over ram tube openings
to prevent ingress of dirt.
5.Loosen clip and disconnect fuel return hose from
regulator.
6.Loosen union and disconnect fuel supply hose
from fuel rail.
7.Disconnect multi-plug from fuel temperature
sensor.
8.Disconnect multi-plugs from injectors.
9.Remove four bolts securing fuel rail support
brackets to intake manifold. Lay injector
harnesses to one side.
Page 254 of 873
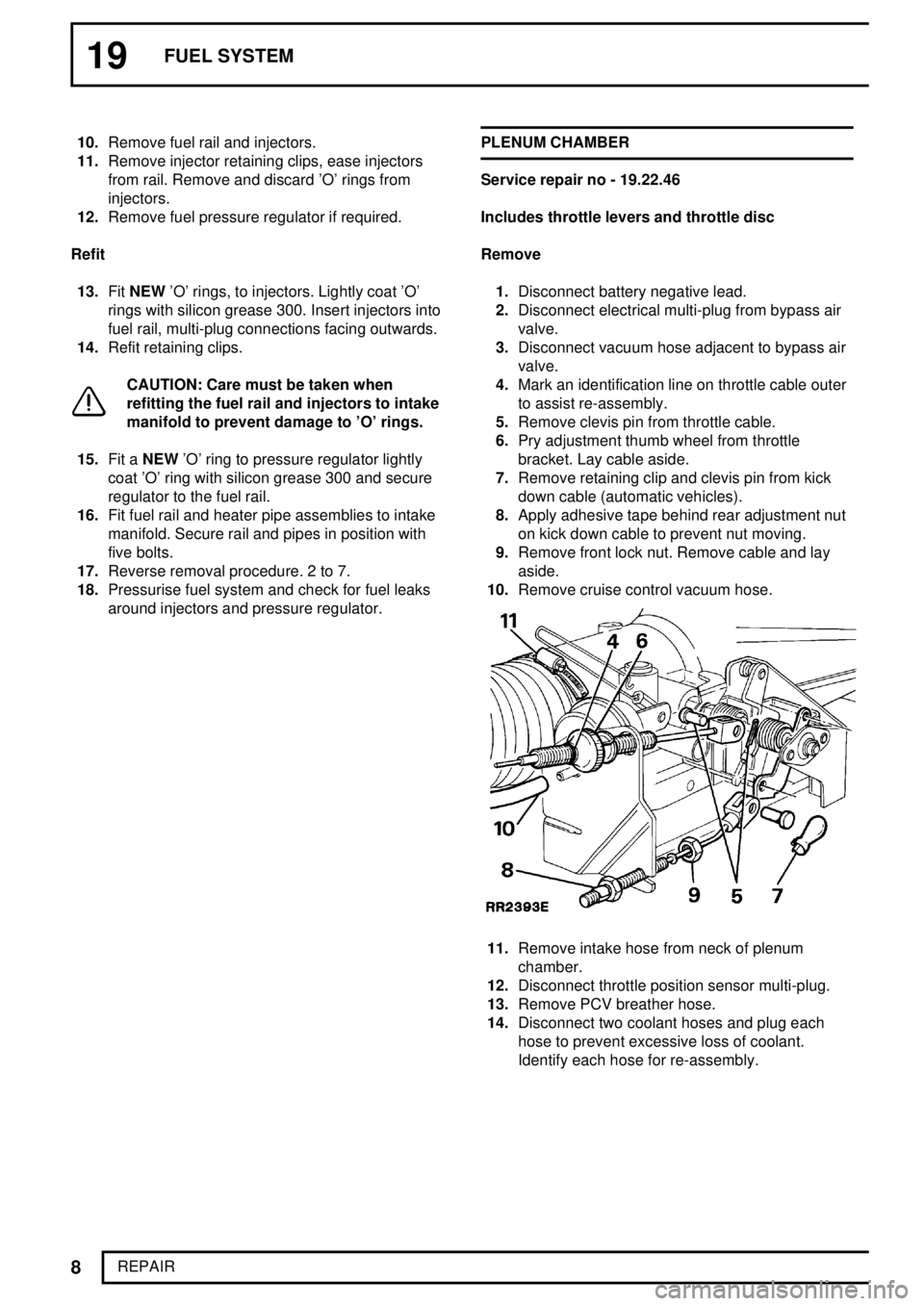
19FUEL SYSTEM
8
REPAIR 10.Remove fuel rail and injectors.
11.Remove injector retaining clips, ease injectors
from rail. Remove and discard 'O' rings from
injectors.
12.Remove fuel pressure regulator if required.
Refit
13.FitNEW'O' rings, to injectors. Lightly coat 'O'
rings with silicon grease 300. Insert injectors into
fuel rail, multi-plug connections facing outwards.
14.Refit retaining clips.
CAUTION: Care must be taken when
refitting the fuel rail and injectors to intake
manifold to prevent damage to 'O' rings.
15.Fit aNEW'O' ring to pressure regulator lightly
coat 'O' ring with silicon grease 300 and secure
regulator to the fuel rail.
16.Fit fuel rail and heater pipe assemblies to intake
manifold. Secure rail and pipes in position with
five bolts.
17.Reverse removal procedure. 2 to 7.
18.Pressurise fuel system and check for fuel leaks
around injectors and pressure regulator.PLENUM CHAMBER
Service repair no - 19.22.46
Includes throttle levers and throttle disc
Remove
1.Disconnect battery negative lead.
2.Disconnect electrical multi-plug from bypass air
valve.
3.Disconnect vacuum hose adjacent to bypass air
valve.
4.Mark an identification line on throttle cable outer
to assist re-assembly.
5.Remove clevis pin from throttle cable.
6.Pry adjustment thumb wheel from throttle
bracket. Lay cable aside.
7.Remove retaining clip and clevis pin from kick
down cable (automatic vehicles).
8.Apply adhesive tape behind rear adjustment nut
on kick down cable to prevent nut moving.
9.Remove front lock nut. Remove cable and lay
aside.
10.Remove cruise control vacuum hose.
11.Remove intake hose from neck of plenum
chamber.
12.Disconnect throttle position sensor multi-plug.
13.Remove PCV breather hose.
14.Disconnect two coolant hoses and plug each
hose to prevent excessive loss of coolant.
Identify each hose for re-assembly.