sensor LAND ROVER DISCOVERY 1995 Repair Manual
[x] Cancel search | Manufacturer: LAND ROVER, Model Year: 1995, Model line: DISCOVERY, Model: LAND ROVER DISCOVERY 1995Pages: 873, PDF Size: 12.89 MB
Page 214 of 873
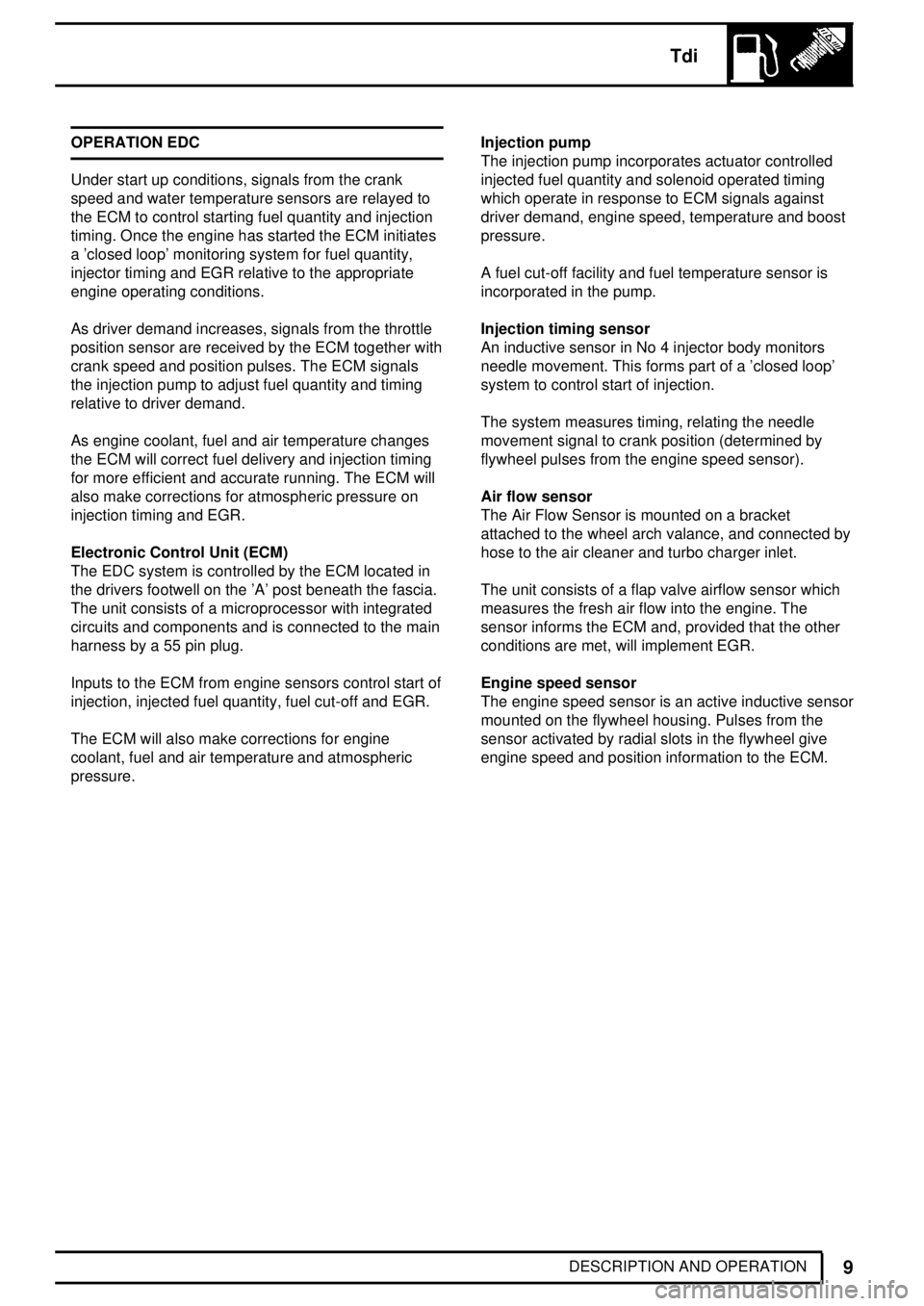
Tdi
9
DESCRIPTION AND OPERATION OPERATION EDC
Under start up conditions, signals from the crank
speed and water temperature sensors are relayed to
the ECM to control starting fuel quantity and injection
timing. Once the engine has started the ECM initiates
a 'closed loop' monitoring system for fuel quantity,
injector timing and EGR relative to the appropriate
engine operating conditions.
As driver demand increases, signals from the throttle
position sensor are received by the ECM together with
crank speed and position pulses. The ECM signals
the injection pump to adjust fuel quantity and timing
relative to driver demand.
As engine coolant, fuel and air temperature changes
the ECM will correct fuel delivery and injection timing
for more efficient and accurate running. The ECM will
also make corrections for atmospheric pressure on
injection timing and EGR.
Electronic Control Unit (ECM)
The EDC system is controlled by the ECM located in
the drivers footwell on the 'A' post beneath the fascia.
The unit consists of a microprocessor with integrated
circuits and components and is connected to the main
harness by a 55 pin plug.
Inputs to the ECM from engine sensors control start of
injection, injected fuel quantity, fuel cut-off and EGR.
The ECM will also make corrections for engine
coolant, fuel and air temperature and atmospheric
pressure.Injection pump
The injection pump incorporates actuator controlled
injected fuel quantity and solenoid operated timing
which operate in response to ECM signals against
driver demand, engine speed, temperature and boost
pressure.
A fuel cut-off facility and fuel temperature sensor is
incorporated in the pump.
Injection timing sensor
An inductive sensor in No 4 injector body monitors
needle movement. This forms part of a 'closed loop'
system to control start of injection.
The system measures timing, relating the needle
movement signal to crank position (determined by
flywheel pulses from the engine speed sensor).
Air flow sensor
The Air Flow Sensor is mounted on a bracket
attached to the wheel arch valance, and connected by
hose to the air cleaner and turbo charger inlet.
The unit consists of a flap valve airflow sensor which
measures the fresh air flow into the engine. The
sensor informs the ECM and, provided that the other
conditions are met, will implement EGR.
Engine speed sensor
The engine speed sensor is an active inductive sensor
mounted on the flywheel housing. Pulses from the
sensor activated by radial slots in the flywheel give
engine speed and position information to the ECM.
Page 215 of 873
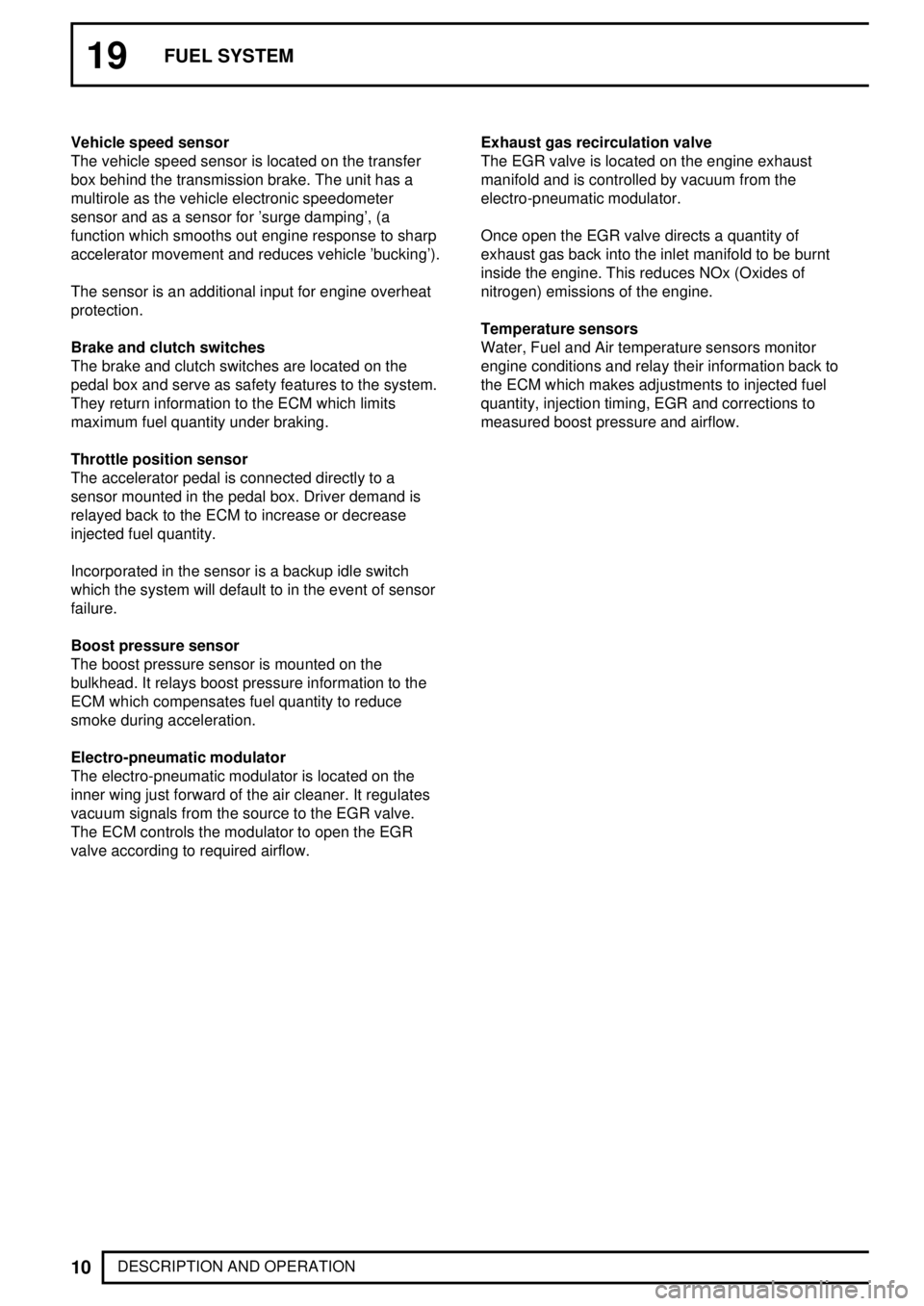
19FUEL SYSTEM
10
DESCRIPTION AND OPERATION Vehicle speed sensor
The vehicle speed sensor is located on the transfer
box behind the transmission brake. The unit has a
multirole as the vehicle electronic speedometer
sensor and as a sensor for 'surge damping', (a
function which smooths out engine response to sharp
accelerator movement and reduces vehicle 'bucking').
The sensor is an additional input for engine overheat
protection.
Brake and clutch switches
The brake and clutch switches are located on the
pedal box and serve as safety features to the system.
They return information to the ECM which limits
maximum fuel quantity under braking.
Throttle position sensor
The accelerator pedal is connected directly to a
sensor mounted in the pedal box. Driver demand is
relayed back to the ECM to increase or decrease
injected fuel quantity.
Incorporated in the sensor is a backup idle switch
which the system will default to in the event of sensor
failure.
Boost pressure sensor
The boost pressure sensor is mounted on the
bulkhead. It relays boost pressure information to the
ECM which compensates fuel quantity to reduce
smoke during acceleration.
Electro-pneumatic modulator
The electro-pneumatic modulator is located on the
inner wing just forward of the air cleaner. It regulates
vacuum signals from the source to the EGR valve.
The ECM controls the modulator to open the EGR
valve according to required airflow.Exhaust gas recirculation valve
The EGR valve is located on the engine exhaust
manifold and is controlled by vacuum from the
electro-pneumatic modulator.
Once open the EGR valve directs a quantity of
exhaust gas back into the inlet manifold to be burnt
inside the engine. This reduces NOx (Oxides of
nitrogen) emissions of the engine.
Temperature sensors
Water, Fuel and Air temperature sensors monitor
engine conditions and relay their information back to
the ECM which makes adjustments to injected fuel
quantity, injection timing, EGR and corrections to
measured boost pressure and airflow.
Page 216 of 873
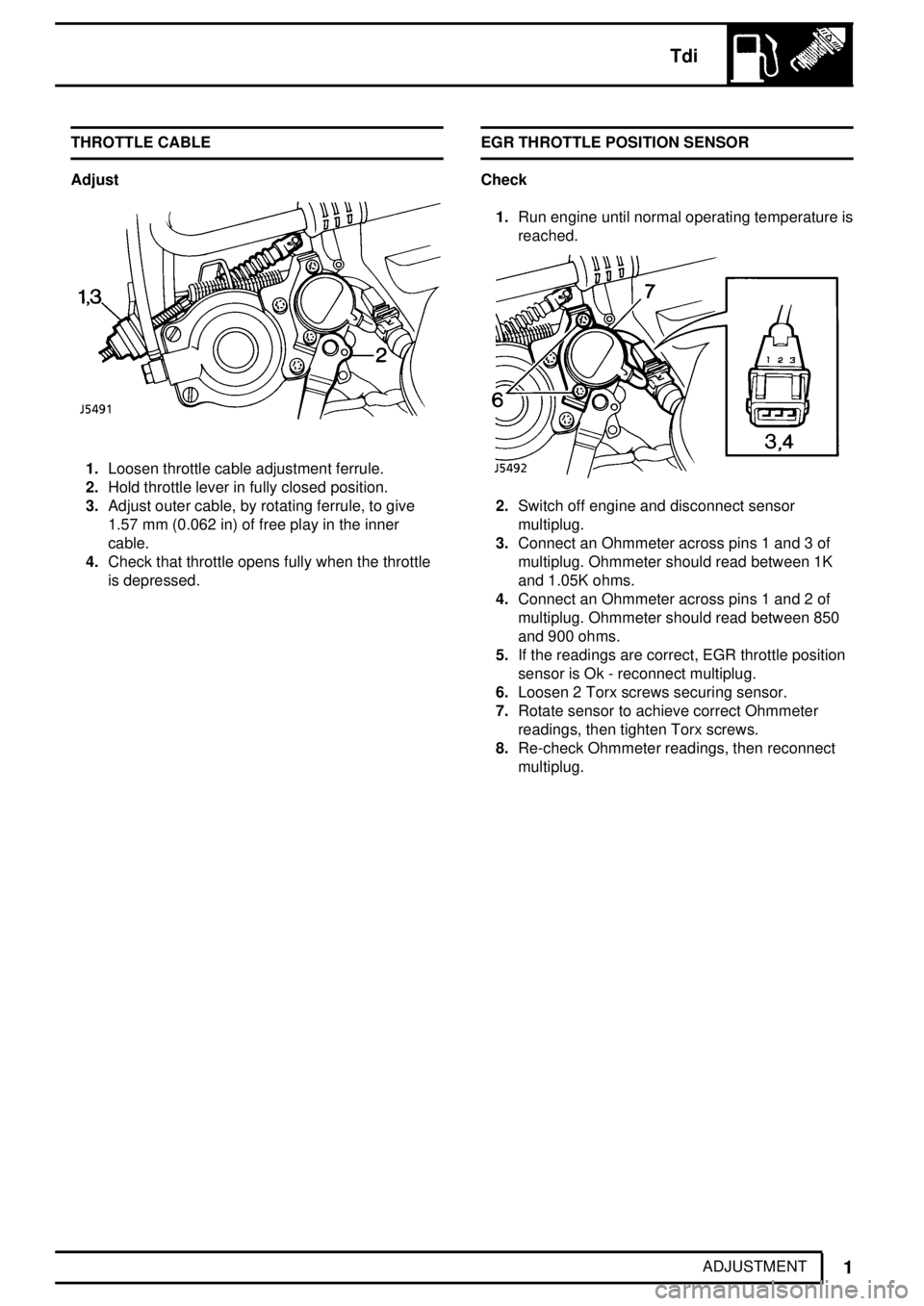
Tdi
1
ADJUSTMENT THROTTLE CABLE
Adjust
1.Loosen throttle cable adjustment ferrule.
2.Hold throttle lever in fully closed position.
3.Adjust outer cable, by rotating ferrule, to give
1.57 mm (0.062 in) of free play in the inner
cable.
4.Check that throttle opens fully when the throttle
is depressed.EGR THROTTLE POSITION SENSOR
Check
1.Run engine until normal operating temperature is
reached.
2.Switch off engine and disconnect sensor
multiplug.
3.Connect an Ohmmeter across pins 1 and 3 of
multiplug. Ohmmeter should read between 1K
and 1.05K ohms.
4.Connect an Ohmmeter across pins 1 and 2 of
multiplug. Ohmmeter should read between 850
and 900 ohms.
5.If the readings are correct, EGR throttle position
sensor is Ok - reconnect multiplug.
6.Loosen 2 Torx screws securing sensor.
7.Rotate sensor to achieve correct Ohmmeter
readings, then tighten Torx screws.
8.Re-check Ohmmeter readings, then reconnect
multiplug.
Page 227 of 873
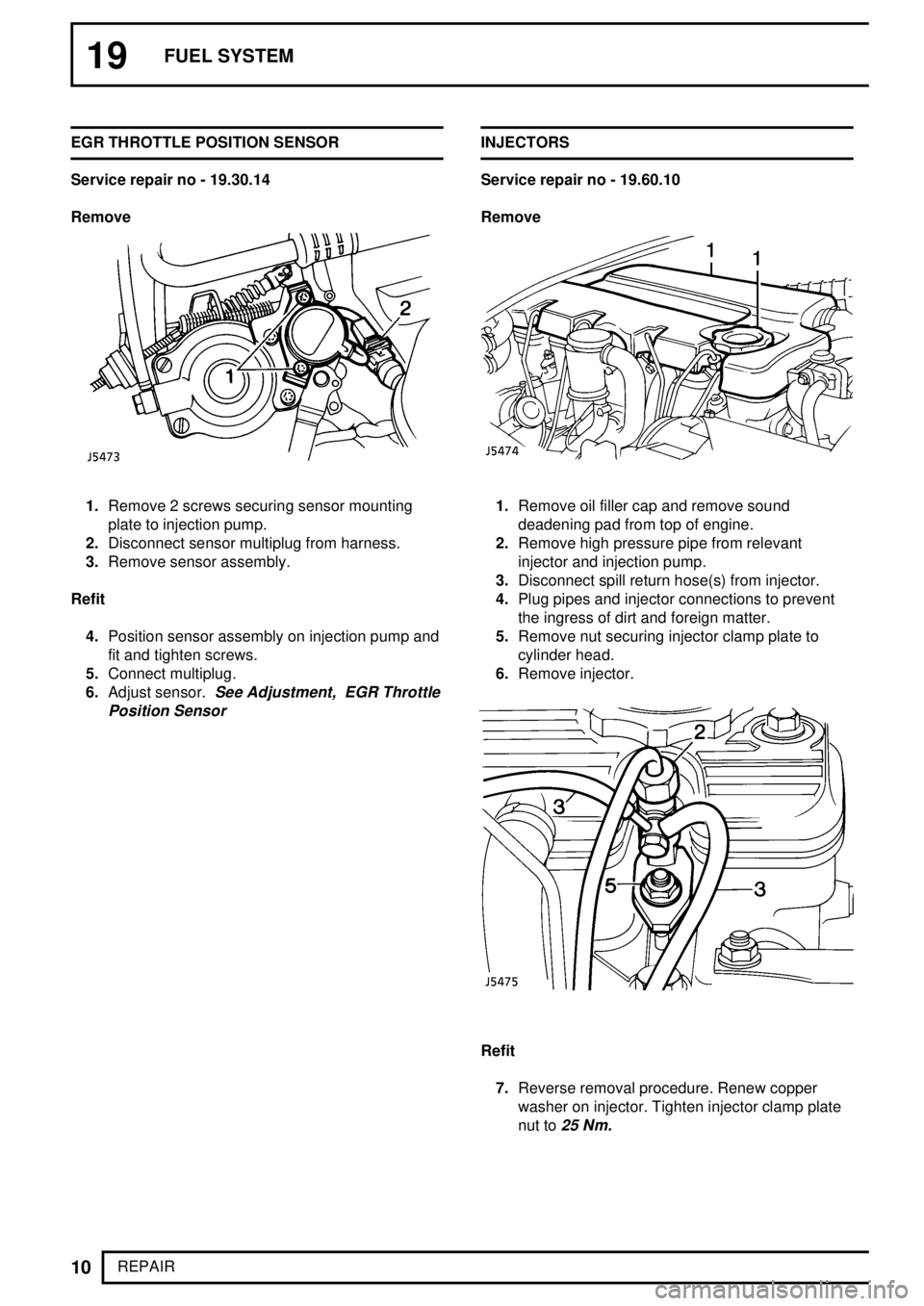
19FUEL SYSTEM
10
REPAIR EGR THROTTLE POSITION SENSOR
Service repair no - 19.30.14
Remove
1.Remove 2 screws securing sensor mounting
plate to injection pump.
2.Disconnect sensor multiplug from harness.
3.Remove sensor assembly.
Refit
4.Position sensor assembly on injection pump and
fit and tighten screws.
5.Connect multiplug.
6.Adjust sensor.
See Adjustment, EGR Throttle
Position Sensor
INJECTORS
Service repair no - 19.60.10
Remove
1.Remove oil filler cap and remove sound
deadening pad from top of engine.
2.Remove high pressure pipe from relevant
injector and injection pump.
3.Disconnect spill return hose(s) from injector.
4.Plug pipes and injector connections to prevent
the ingress of dirt and foreign matter.
5.Remove nut securing injector clamp plate to
cylinder head.
6.Remove injector.
Refit
7.Reverse removal procedure. Renew copper
washer on injector. Tighten injector clamp plate
nut to
25 Nm.
Page 232 of 873
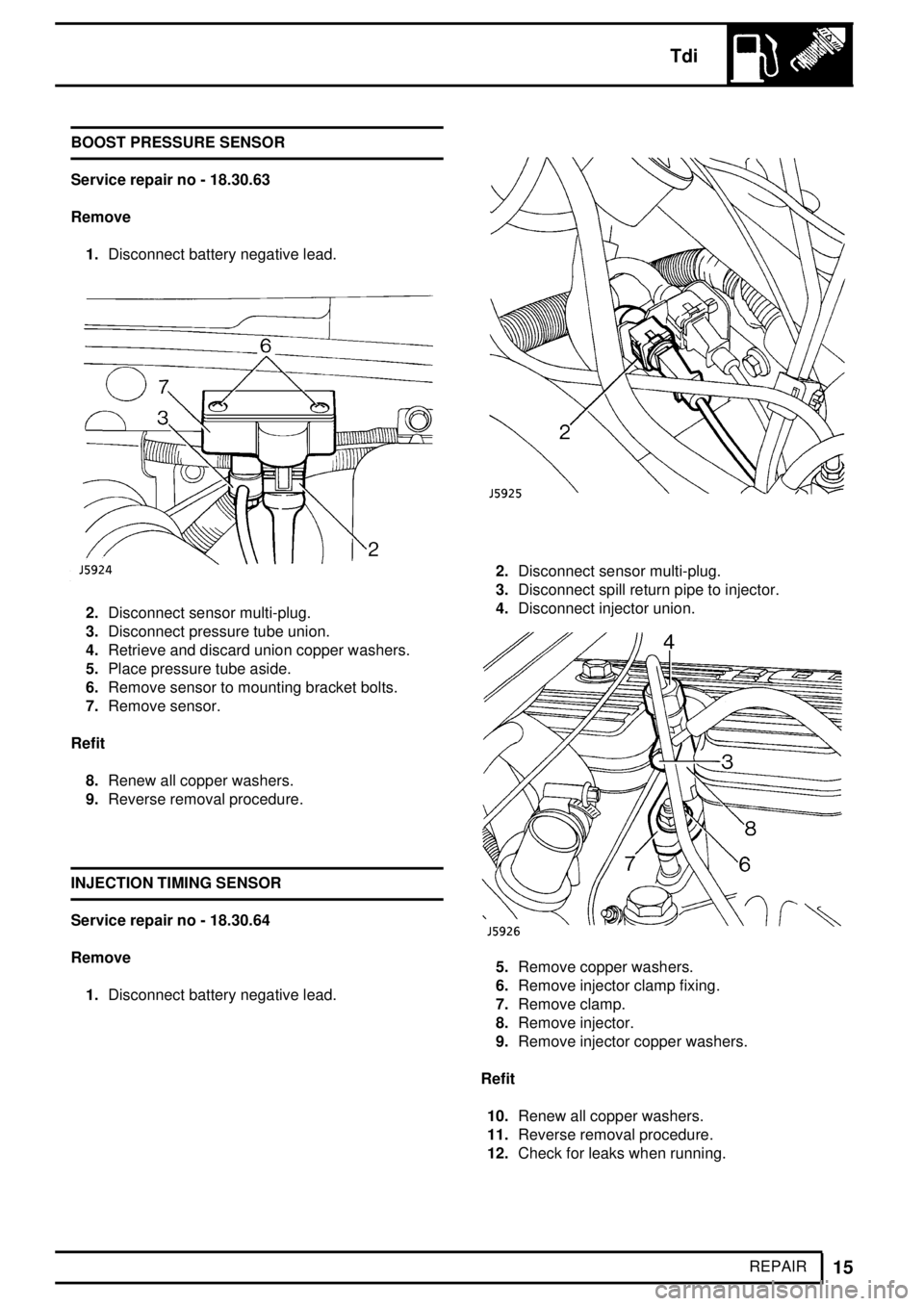
Tdi
15
REPAIR BOOST PRESSURE SENSOR
Service repair no - 18.30.63
Remove
1.Disconnect battery negative lead.
2.Disconnect sensor multi-plug.
3.Disconnect pressure tube union.
4.Retrieve and discard union copper washers.
5.Place pressure tube aside.
6.Remove sensor to mounting bracket bolts.
7.Remove sensor.
Refit
8.Renew all copper washers.
9.Reverse removal procedure.
INJECTION TIMING SENSOR
Service repair no - 18.30.64
Remove
1.Disconnect battery negative lead.
2.Disconnect sensor multi-plug.
3.Disconnect spill return pipe to injector.
4.Disconnect injector union.
5.Remove copper washers.
6.Remove injector clamp fixing.
7.Remove clamp.
8.Remove injector.
9.Remove injector copper washers.
Refit
10.Renew all copper washers.
11.Reverse removal procedure.
12.Check for leaks when running.
Page 233 of 873
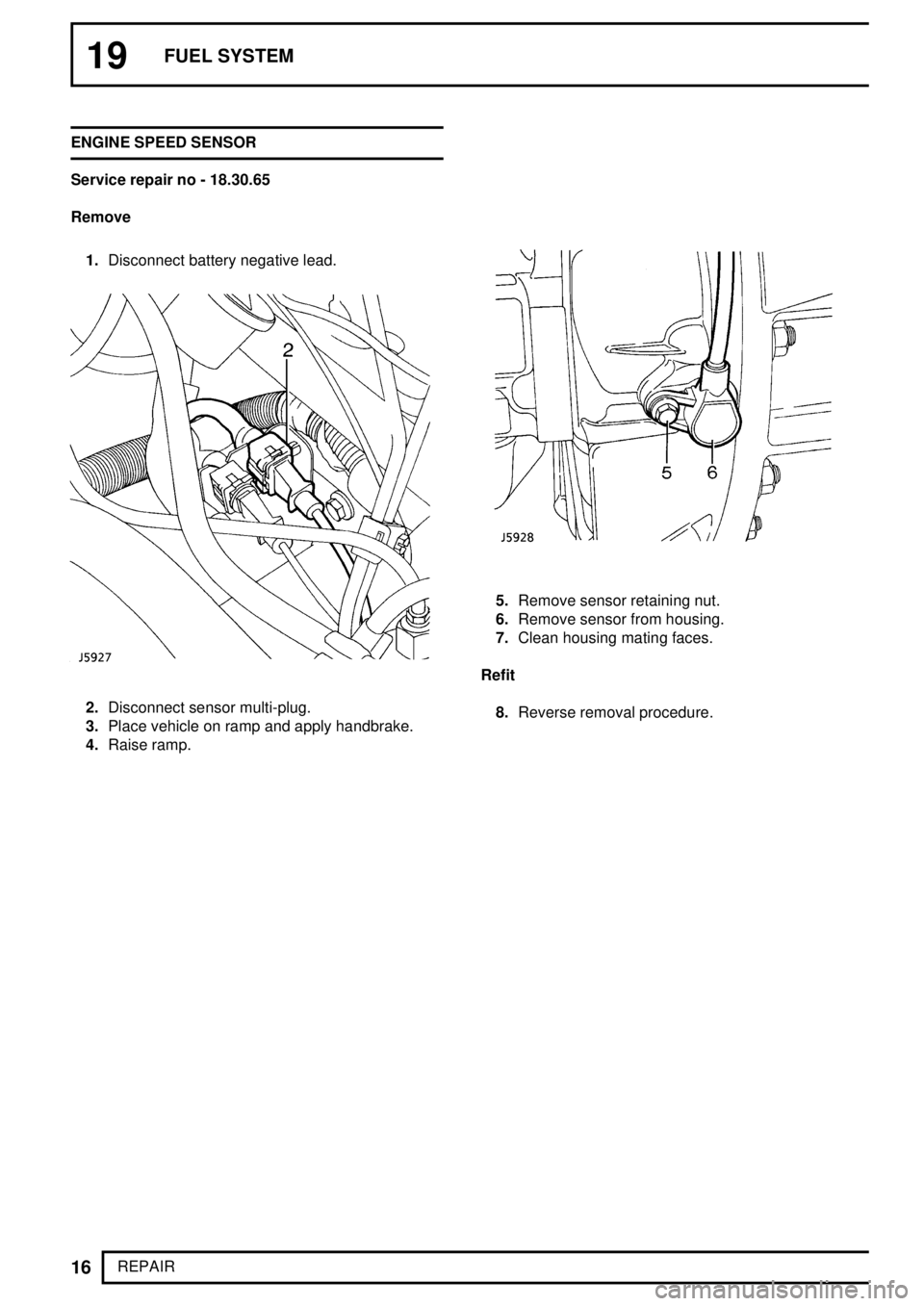
19FUEL SYSTEM
16
REPAIR ENGINE SPEED SENSOR
Service repair no - 18.30.65
Remove
1.Disconnect battery negative lead.
2.Disconnect sensor multi-plug.
3.Place vehicle on ramp and apply handbrake.
4.Raise ramp.
5.Remove sensor retaining nut.
6.Remove sensor from housing.
7.Clean housing mating faces.
Refit
8.Reverse removal procedure.
Page 234 of 873
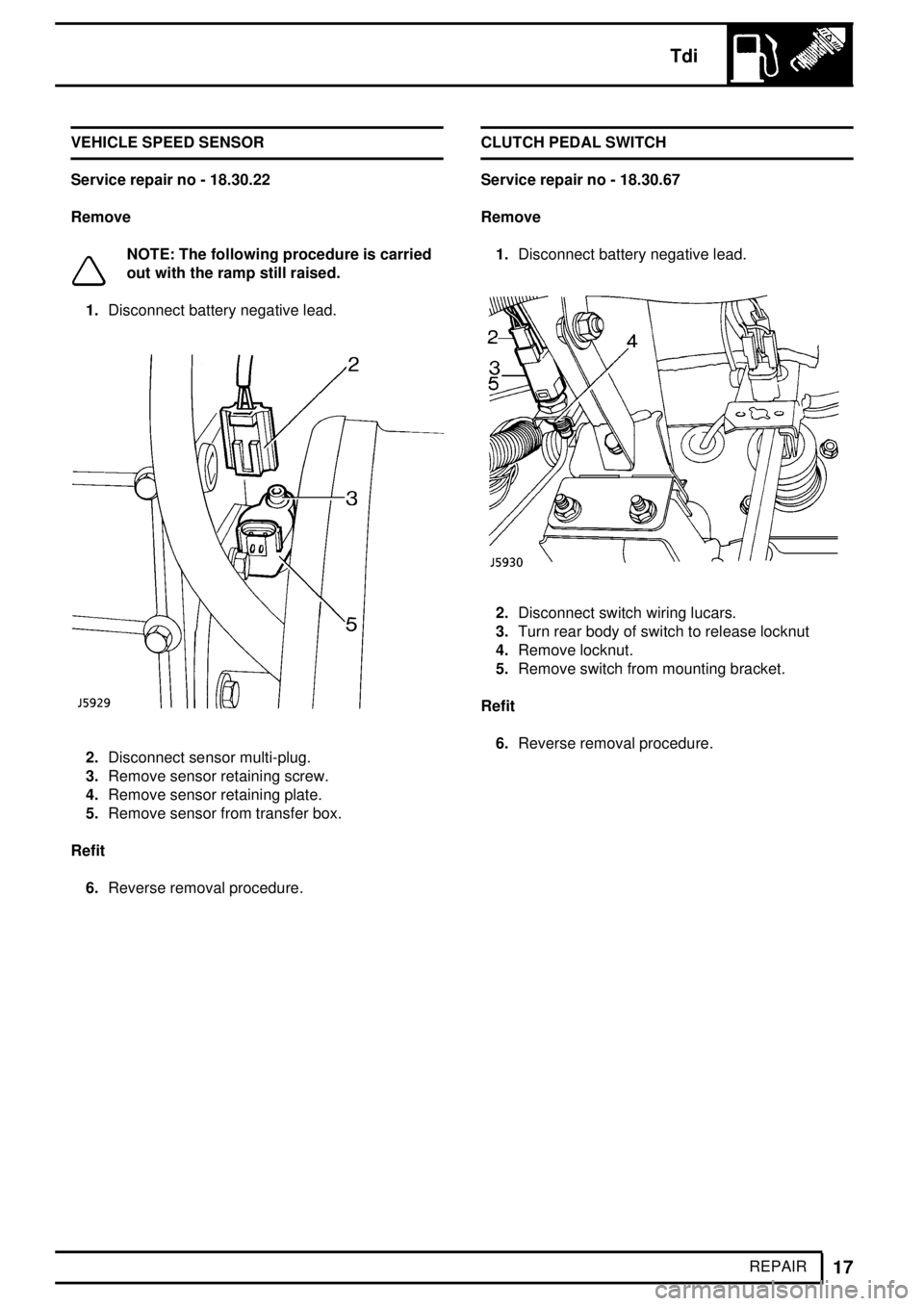
Tdi
17
REPAIR VEHICLE SPEED SENSOR
Service repair no - 18.30.22
Remove
NOTE: The following procedure is carried
out with the ramp still raised.
1.Disconnect battery negative lead.
2.Disconnect sensor multi-plug.
3.Remove sensor retaining screw.
4.Remove sensor retaining plate.
5.Remove sensor from transfer box.
Refit
6.Reverse removal procedure.CLUTCH PEDAL SWITCH
Service repair no - 18.30.67
Remove
1.Disconnect battery negative lead.
2.Disconnect switch wiring lucars.
3.Turn rear body of switch to release locknut
4.Remove locknut.
5.Remove switch from mounting bracket.
Refit
6.Reverse removal procedure.
Page 235 of 873
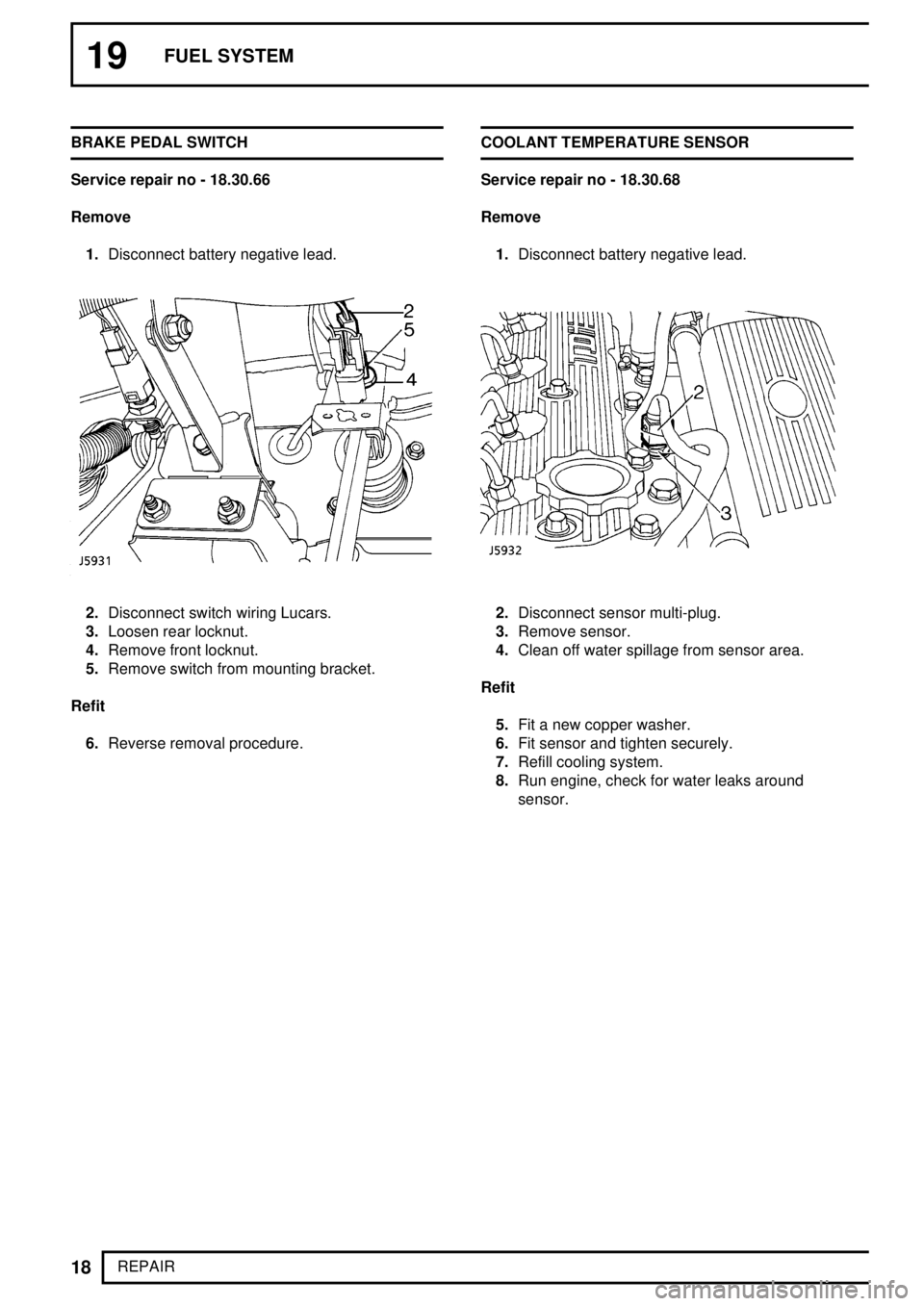
19FUEL SYSTEM
18
REPAIR BRAKE PEDAL SWITCH
Service repair no - 18.30.66
Remove
1.Disconnect battery negative lead.
2.Disconnect switch wiring Lucars.
3.Loosen rear locknut.
4.Remove front locknut.
5.Remove switch from mounting bracket.
Refit
6.Reverse removal procedure.COOLANT TEMPERATURE SENSOR
Service repair no - 18.30.68
Remove
1.Disconnect battery negative lead.2.Disconnect sensor multi-plug.
3.Remove sensor.
4.Clean off water spillage from sensor area.
Refit
5.Fit a new copper washer.
6.Fit sensor and tighten securely.
7.Refill cooling system.
8.Run engine, check for water leaks around
sensor.
Page 236 of 873
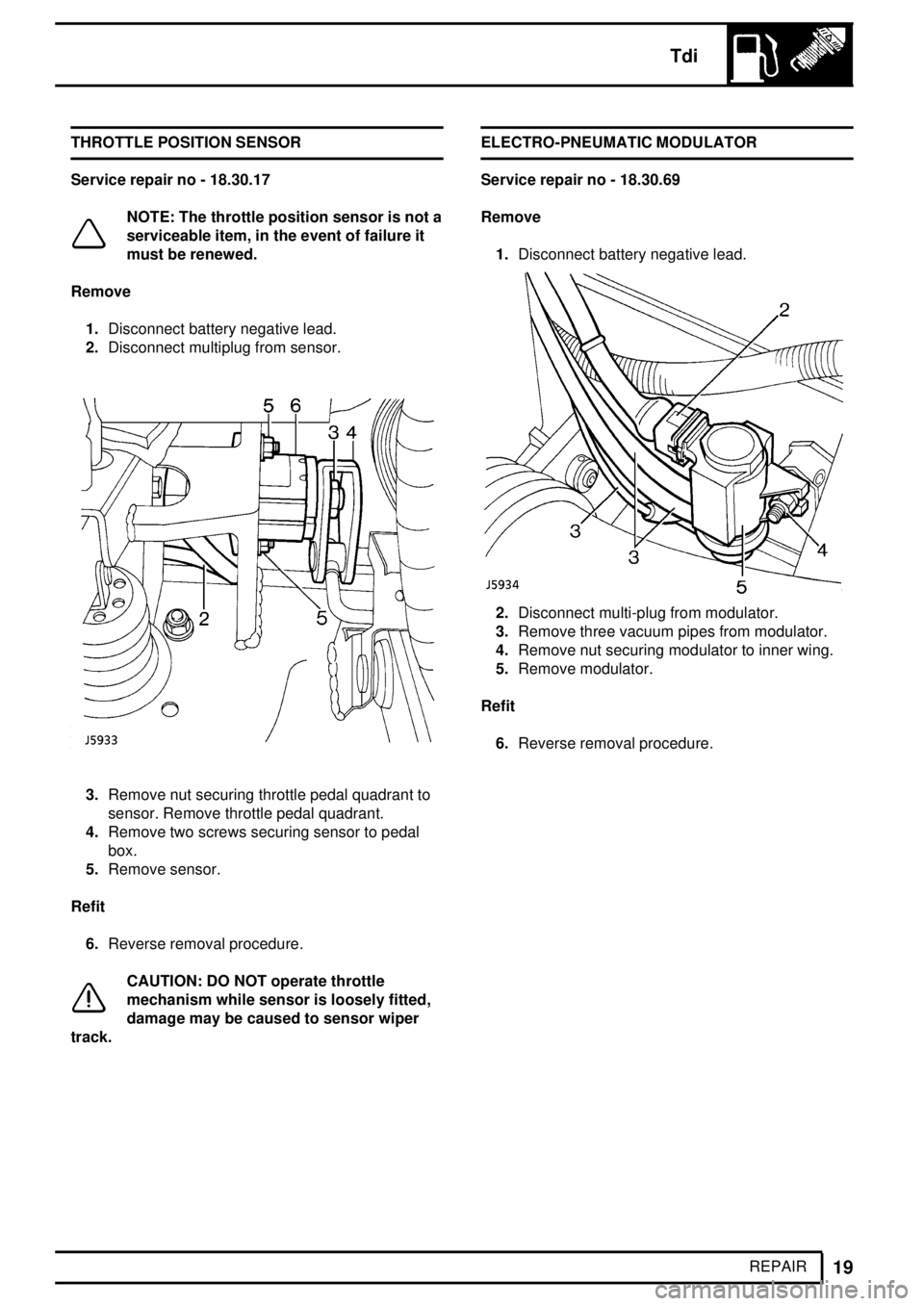
Tdi
19
REPAIR THROTTLE POSITION SENSOR
Service repair no - 18.30.17
NOTE: The throttle position sensor is not a
serviceable item, in the event of failure it
must be renewed.
Remove
1.Disconnect battery negative lead.
2.Disconnect multiplug from sensor.
3.Remove nut securing throttle pedal quadrant to
sensor. Remove throttle pedal quadrant.
4.Remove two screws securing sensor to pedal
box.
5.Remove sensor.
Refit
6.Reverse removal procedure.
CAUTION: DO NOT operate throttle
mechanism while sensor is loosely fitted,
damage may be caused to sensor wiper
track.ELECTRO-PNEUMATIC MODULATOR
Service repair no - 18.30.69
Remove
1.Disconnect battery negative lead.
2.Disconnect multi-plug from modulator.
3.Remove three vacuum pipes from modulator.
4.Remove nut securing modulator to inner wing.
5.Remove modulator.
Refit
6.Reverse removal procedure.
Page 237 of 873
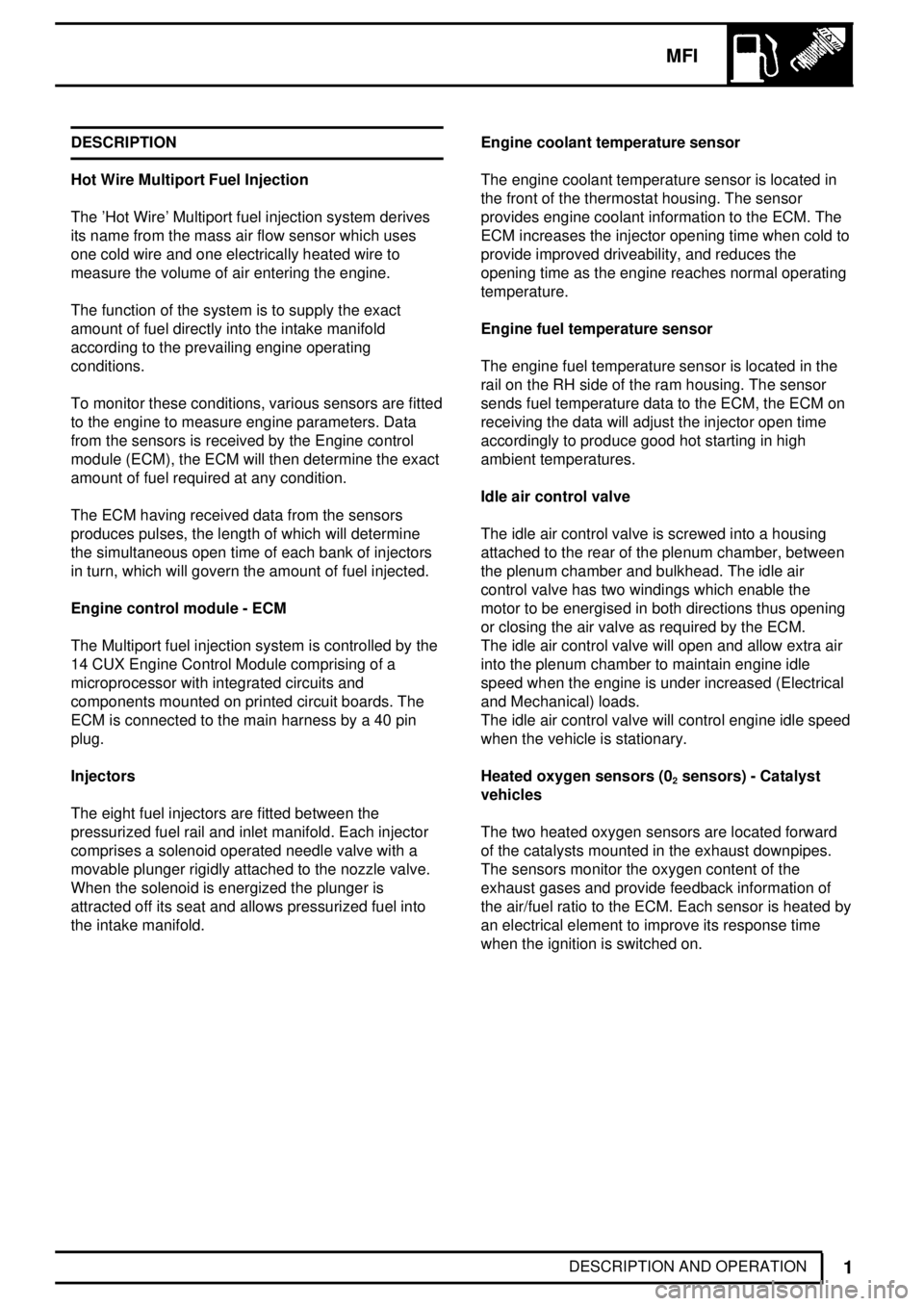
MFI
1
DESCRIPTION AND OPERATION DESCRIPTION
Hot Wire Multiport Fuel Injection
The 'Hot Wire' Multiport fuel injection system derives
its name from the mass air flow sensor which uses
one cold wire and one electrically heated wire to
measure the volume of air entering the engine.
The function of the system is to supply the exact
amount of fuel directly into the intake manifold
according to the prevailing engine operating
conditions.
To monitor these conditions, various sensors are fitted
to the engine to measure engine parameters. Data
from the sensors is received by the Engine control
module (ECM), the ECM will then determine the exact
amount of fuel required at any condition.
The ECM having received data from the sensors
produces pulses, the length of which will determine
the simultaneous open time of each bank of injectors
in turn, which will govern the amount of fuel injected.
Engine control module - ECM
The Multiport fuel injection system is controlled by the
14 CUX Engine Control Module comprising of a
microprocessor with integrated circuits and
components mounted on printed circuit boards. The
ECM is connected to the main harness by a 40 pin
plug.
Injectors
The eight fuel injectors are fitted between the
pressurized fuel rail and inlet manifold. Each injector
comprises a solenoid operated needle valve with a
movable plunger rigidly attached to the nozzle valve.
When the solenoid is energized the plunger is
attracted off its seat and allows pressurized fuel into
the intake manifold.Engine coolant temperature sensor
The engine coolant temperature sensor is located in
the front of the thermostat housing. The sensor
provides engine coolant information to the ECM. The
ECM increases the injector opening time when cold to
provide improved driveability, and reduces the
opening time as the engine reaches normal operating
temperature.
Engine fuel temperature sensor
The engine fuel temperature sensor is located in the
rail on the RH side of the ram housing. The sensor
sends fuel temperature data to the ECM, the ECM on
receiving the data will adjust the injector open time
accordingly to produce good hot starting in high
ambient temperatures.
Idle air control valve
The idle air control valve is screwed into a housing
attached to the rear of the plenum chamber, between
the plenum chamber and bulkhead. The idle air
control valve has two windings which enable the
motor to be energised in both directions thus opening
or closing the air valve as required by the ECM.
The idle air control valve will open and allow extra air
into the plenum chamber to maintain engine idle
speed when the engine is under increased (Electrical
and Mechanical) loads.
The idle air control valve will control engine idle speed
when the vehicle is stationary.
Heated oxygen sensors (0
2sensors) - Catalyst
vehicles
The two heated oxygen sensors are located forward
of the catalysts mounted in the exhaust downpipes.
The sensors monitor the oxygen content of the
exhaust gases and provide feedback information of
the air/fuel ratio to the ECM. Each sensor is heated by
an electrical element to improve its response time
when the ignition is switched on.