LAND ROVER DISCOVERY 1999 Workshop Manual
Manufacturer: LAND ROVER, Model Year: 1999, Model line: DISCOVERY, Model: LAND ROVER DISCOVERY 1999Pages: 1529, PDF Size: 34.8 MB
Page 211 of 1529
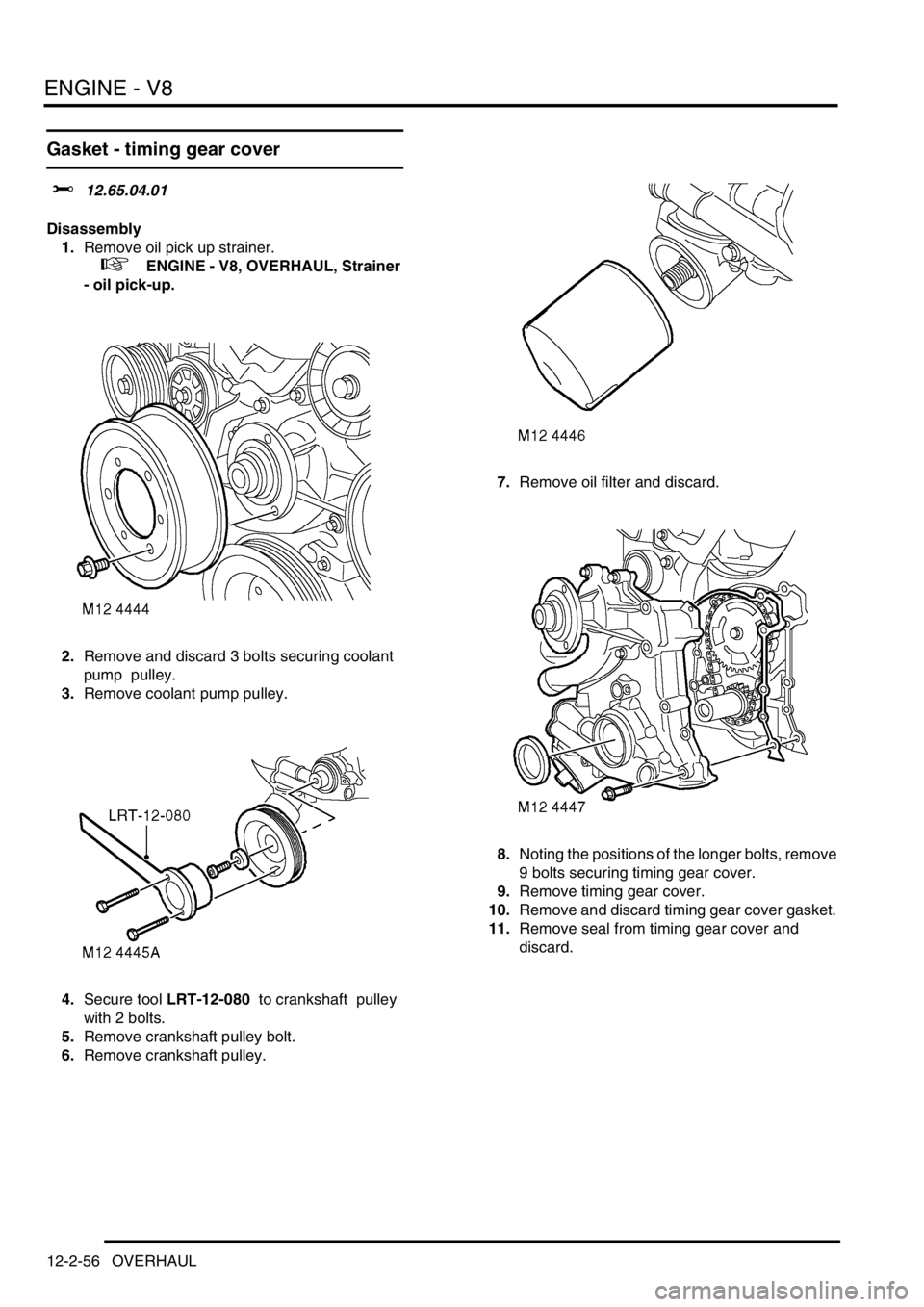
ENGINE - V8
12-2-56 OVERHAUL
Gasket - timing gear cover
$% 12.65.04.01
Disassembly
1.Remove oil pick up strainer.
+ ENGINE - V8, OVERHAUL, Strainer
- oil pick-up.
2.Remove and discard 3 bolts securing coolant
pump pulley.
3.Remove coolant pump pulley.
4.Secure tool LRT-12-080 to crankshaft pulley
with 2 bolts.
5.Remove crankshaft pulley bolt.
6.Remove crankshaft pulley. 7.Remove oil filter and discard.
8.Noting the positions of the longer bolts, remove
9 bolts securing timing gear cover.
9.Remove timing gear cover.
10.Remove and discard timing gear cover gasket.
11.Remove seal from timing gear cover and
discard.
Page 212 of 1529
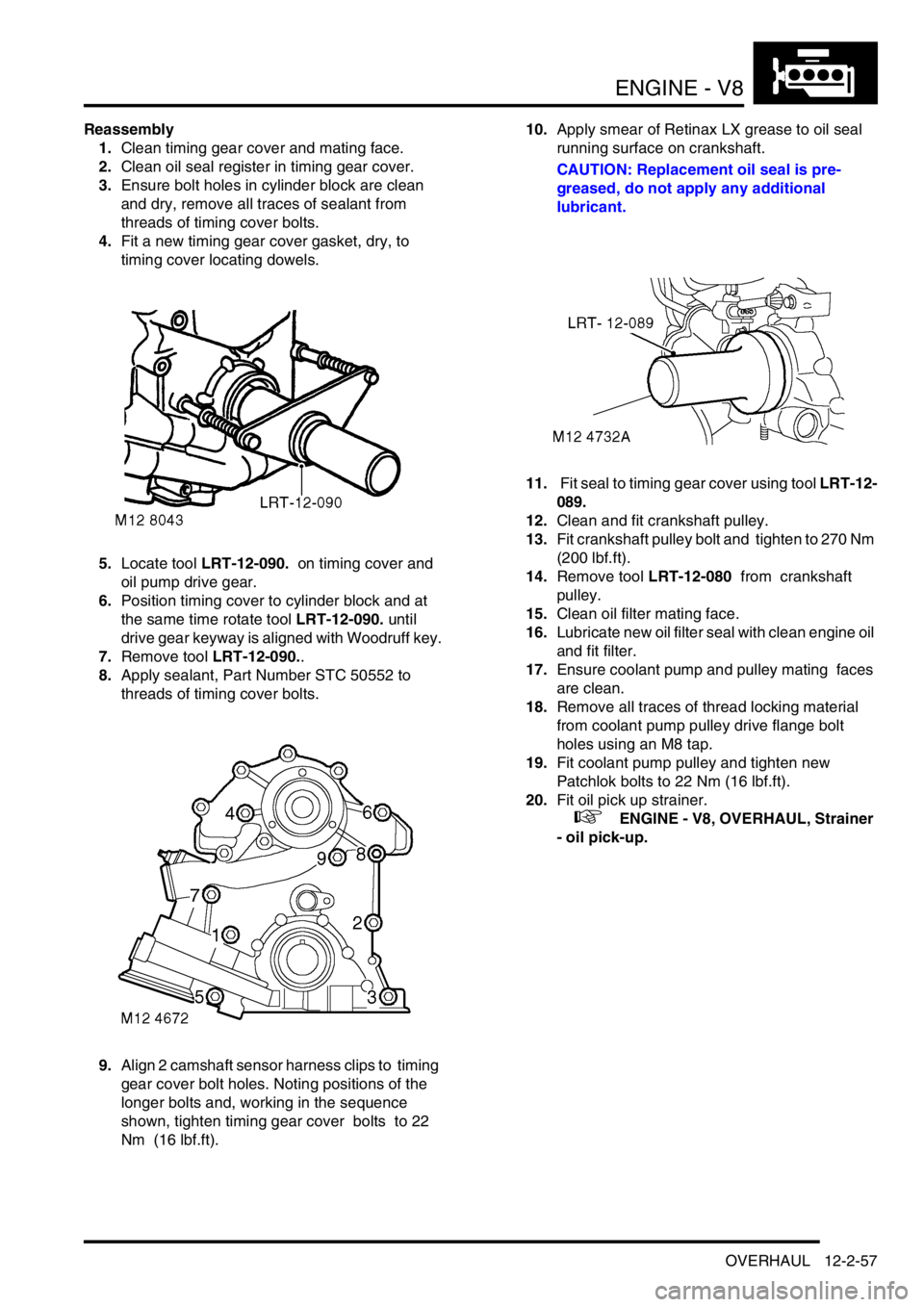
ENGINE - V8
OVERHAUL 12-2-57
Reassembly
1.Clean timing gear cover and mating face.
2.Clean oil seal register in timing gear cover.
3.Ensure bolt holes in cylinder block are clean
and dry, remove all traces of sealant from
threads of timing cover bolts.
4.Fit a new timing gear cover gasket, dry, to
timing cover locating dowels.
5.Locate tool LRT-12-090. on timing cover and
oil pump drive gear.
6.Position timing cover to cylinder block and at
the same time rotate tool LRT-12-090. until
drive gear keyway is aligned with Woodruff key.
7.Remove tool LRT-12-090..
8.Apply sealant, Part Number STC 50552 to
threads of timing cover bolts.
9.Align 2 camshaft sensor harness clips to timing
gear cover bolt holes. Noting positions of the
longer bolts and, working in the sequence
shown, tighten timing gear cover bolts to 22
Nm (16 lbf.ft). 10.Apply smear of Retinax LX grease to oil seal
running surface on crankshaft.
CAUTION: Replacement oil seal is pre-
greased, do not apply any additional
lubricant.
11. Fit seal to timing gear cover using tool LRT-12-
089.
12.Clean and fit crankshaft pulley.
13.Fit crankshaft pulley bolt and tighten to 270 Nm
(200 lbf.ft).
14.Remove tool LRT-12-080 from crankshaft
pulley.
15.Clean oil filter mating face.
16.Lubricate new oil filter seal with clean engine oil
and fit filter.
17.Ensure coolant pump and pulley mating faces
are clean.
18.Remove all traces of thread locking material
from coolant pump pulley drive flange bolt
holes using an M8 tap.
19.Fit coolant pump pulley and tighten new
Patchlok bolts to 22 Nm (16 lbf.ft).
20.Fit oil pick up strainer.
+ ENGINE - V8, OVERHAUL, Strainer
- oil pick-up.
Page 213 of 1529
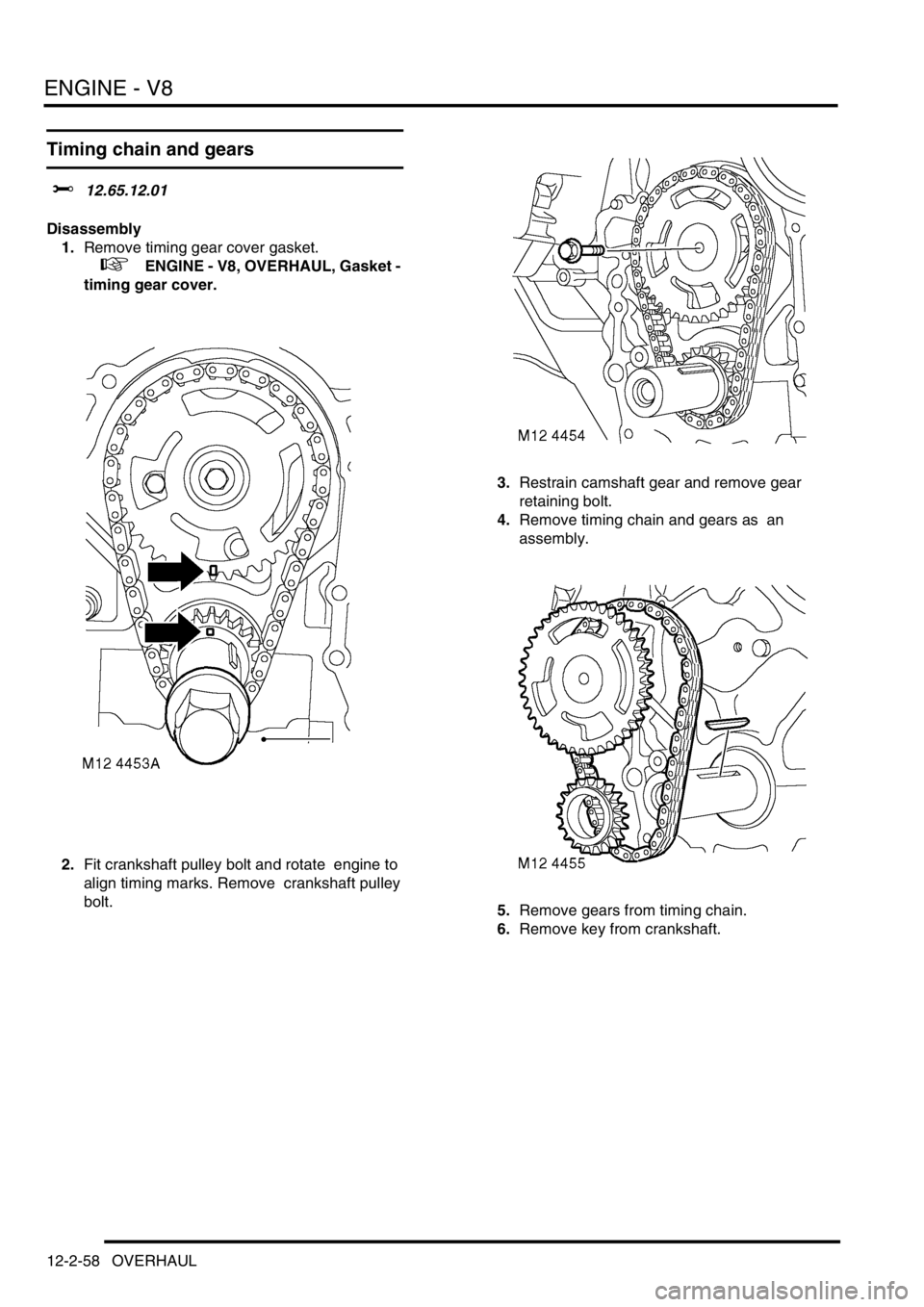
ENGINE - V8
12-2-58 OVERHAUL
Timing chain and gears
$% 12.65.12.01
Disassembly
1.Remove timing gear cover gasket.
+ ENGINE - V8, OVERHAUL, Gasket -
timing gear cover.
2.Fit crankshaft pulley bolt and rotate engine to
align timing marks. Remove crankshaft pulley
bolt. 3.Restrain camshaft gear and remove gear
retaining bolt.
4.Remove timing chain and gears as an
assembly.
5.Remove gears from timing chain.
6.Remove key from crankshaft.
Page 214 of 1529
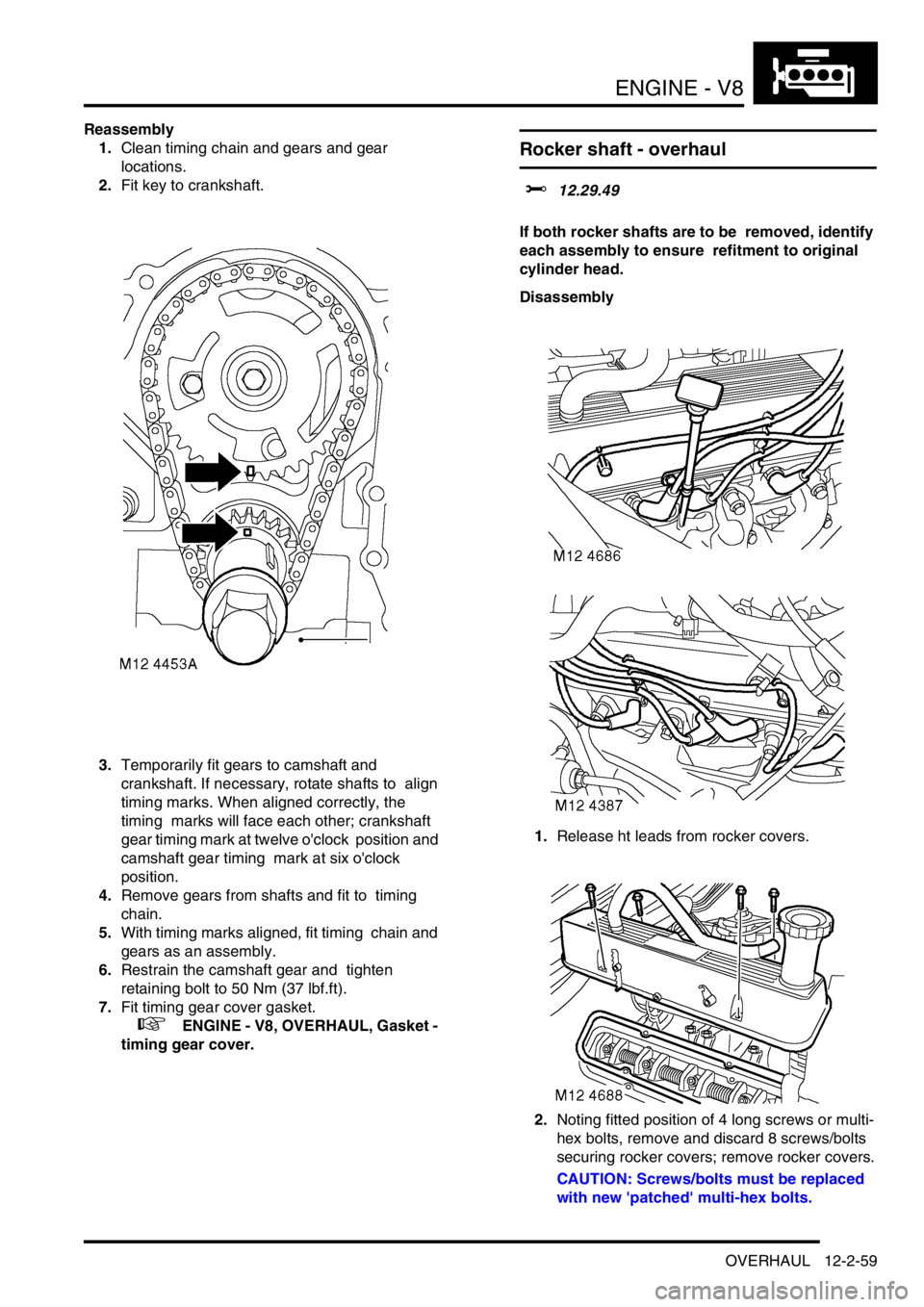
ENGINE - V8
OVERHAUL 12-2-59
Reassembly
1.Clean timing chain and gears and gear
locations.
2.Fit key to crankshaft.
3.Temporarily fit gears to camshaft and
crankshaft. If necessary, rotate shafts to align
timing marks. When aligned correctly, the
timing marks will face each other; crankshaft
gear timing mark at twelve o'clock position and
camshaft gear timing mark at six o'clock
position.
4.Remove gears from shafts and fit to timing
chain.
5.With timing marks aligned, fit timing chain and
gears as an assembly.
6.Restrain the camshaft gear and tighten
retaining bolt to 50 Nm (37 lbf.ft).
7.Fit timing gear cover gasket.
+ ENGINE - V8, OVERHAUL, Gasket -
timing gear cover.
Rocker shaft - overhaul
$% 12.29.49
If both rocker shafts are to be removed, identify
each assembly to ensure refitment to original
cylinder head.
Disassembly
1.Release ht leads from rocker covers.
2.Noting fitted position of 4 long screws or multi-
hex bolts, remove and discard 8 screws/bolts
securing rocker covers; remove rocker covers.
CAUTION: Screws/bolts must be replaced
with new 'patched' multi-hex bolts.
Page 215 of 1529
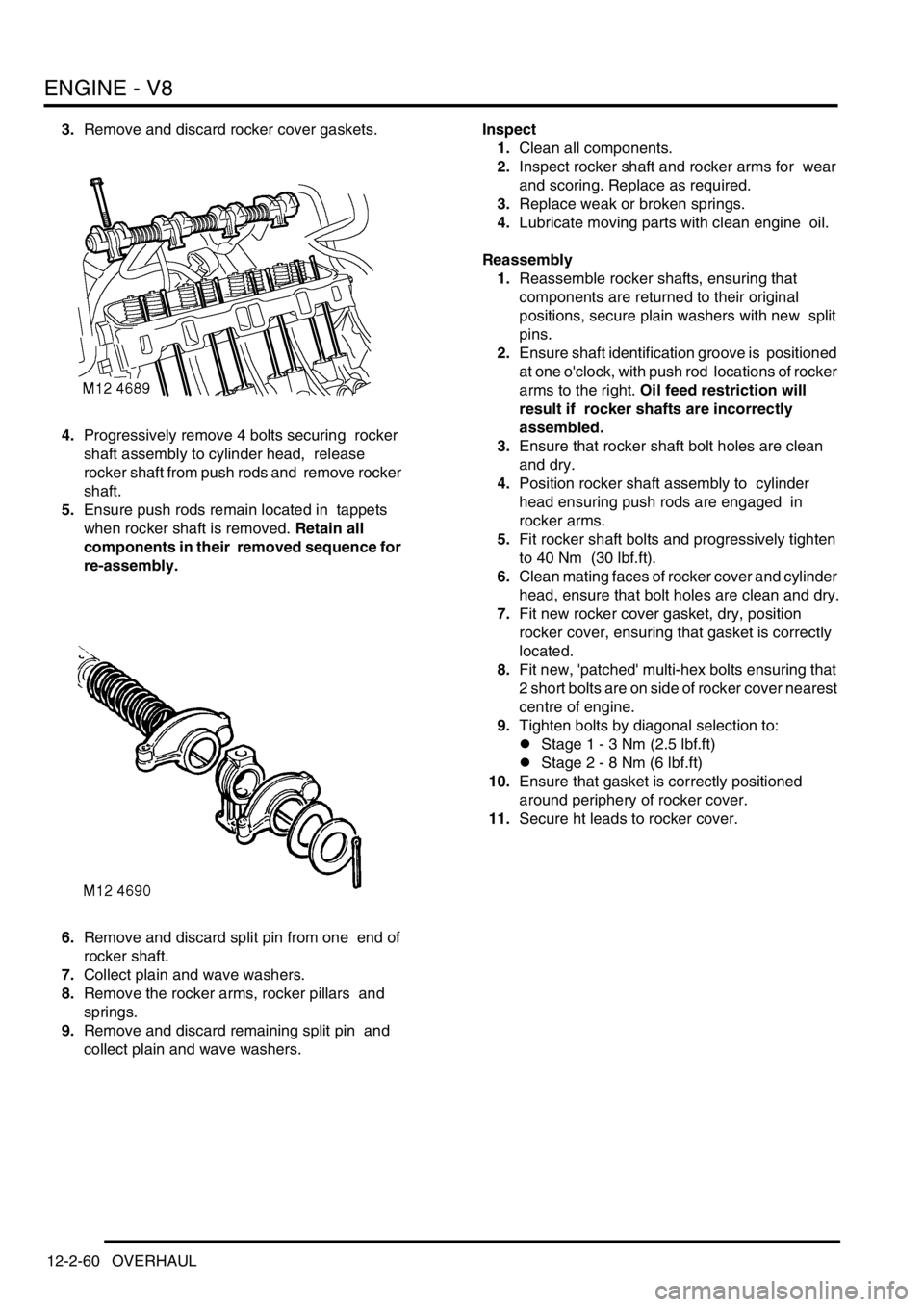
ENGINE - V8
12-2-60 OVERHAUL
3.Remove and discard rocker cover gaskets.
4.Progressively remove 4 bolts securing rocker
shaft assembly to cylinder head, release
rocker shaft from push rods and remove rocker
shaft.
5.Ensure push rods remain located in tappets
when rocker shaft is removed. Retain all
components in their removed sequence for
re-assembly.
6.Remove and discard split pin from one end of
rocker shaft.
7.Collect plain and wave washers.
8.Remove the rocker arms, rocker pillars and
springs.
9.Remove and discard remaining split pin and
collect plain and wave washers. Inspect
1.Clean all components.
2.Inspect rocker shaft and rocker arms for wear
and scoring. Replace as required.
3.Replace weak or broken springs.
4.Lubricate moving parts with clean engine oil.
Reassembly
1.Reassemble rocker shafts, ensuring that
components are returned to their original
positions, secure plain washers with new split
pins.
2.Ensure shaft identification groove is positioned
at one o'clock, with push rod locations of rocker
arms to the right. Oil feed restriction will
result if rocker shafts are incorrectly
assembled.
3.Ensure that rocker shaft bolt holes are clean
and dry.
4.Position rocker shaft assembly to cylinder
head ensuring push rods are engaged in
rocker arms.
5.Fit rocker shaft bolts and progressively tighten
to 40 Nm (30 lbf.ft).
6.Clean mating faces of rocker cover and cylinder
head, ensure that bolt holes are clean and dry.
7.Fit new rocker cover gasket, dry, position
rocker cover, ensuring that gasket is correctly
located.
8.Fit new, 'patched' multi-hex bolts ensuring that
2 short bolts are on side of rocker cover nearest
centre of engine.
9.Tighten bolts by diagonal selection to:
lStage 1 - 3 Nm (2.5 lbf.ft)
lStage 2 - 8 Nm (6 lbf.ft)
10.Ensure that gasket is correctly positioned
around periphery of rocker cover.
11.Secure ht leads to rocker cover.
Page 216 of 1529
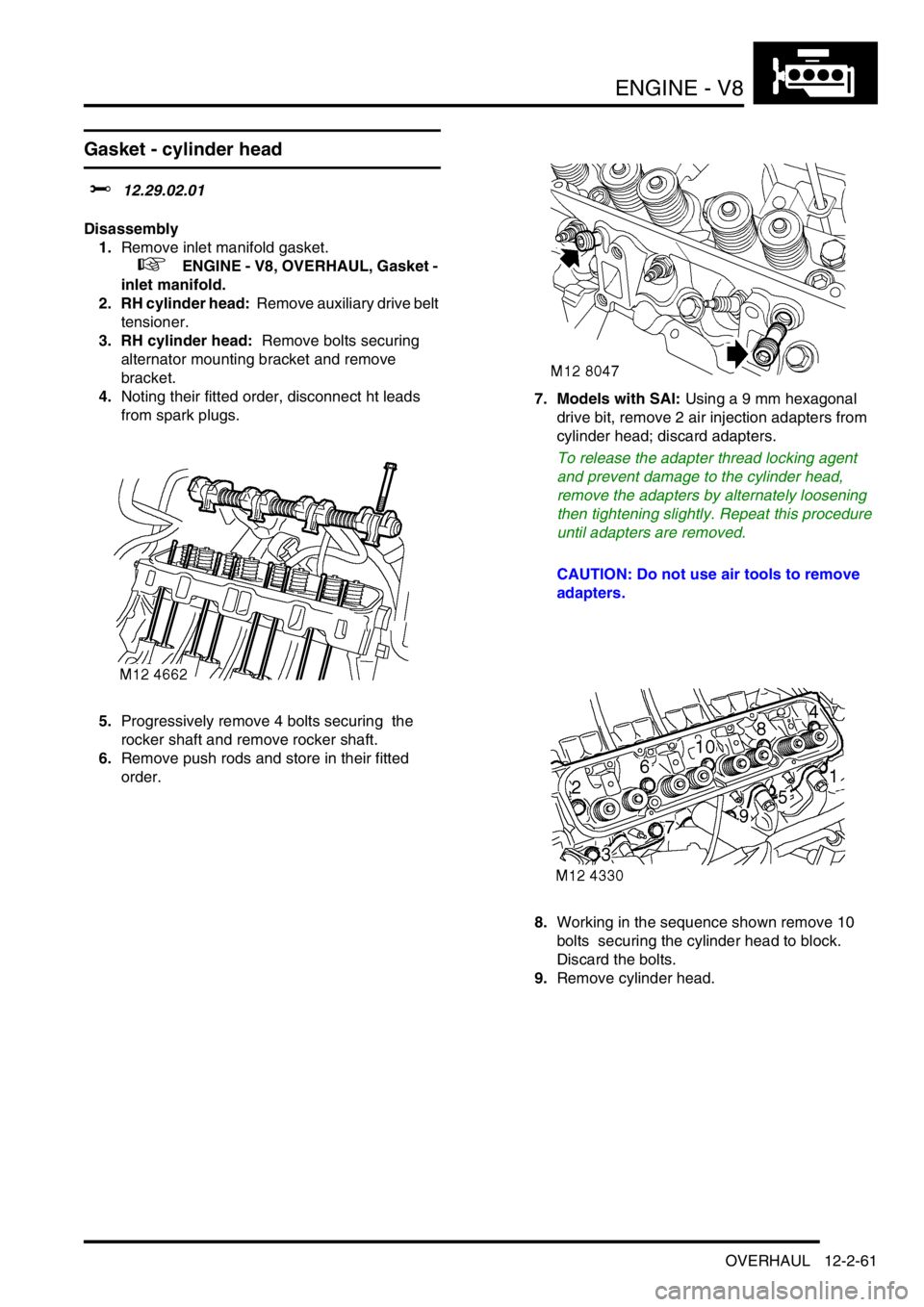
ENGINE - V8
OVERHAUL 12-2-61
Gasket - cylinder head
$% 12.29.02.01
Disassembly
1.Remove inlet manifold gasket.
+ ENGINE - V8, OVERHAUL, Gasket -
inlet manifold.
2. RH cylinder head: Remove auxiliary drive belt
tensioner.
3. RH cylinder head: Remove bolts securing
alternator mounting bracket and remove
bracket.
4.Noting their fitted order, disconnect ht leads
from spark plugs.
5.Progressively remove 4 bolts securing the
rocker shaft and remove rocker shaft.
6.Remove push rods and store in their fitted
order. 7. Models with SAI: Using a 9 mm hexagonal
drive bit, remove 2 air injection adapters from
cylinder head; discard adapters.
To release the adapter thread locking agent
and prevent damage to the cylinder head,
remove the adapters by alternately loosening
then tightening slightly. Repeat this procedure
until adapters are removed.
CAUTION: Do not use air tools to remove
adapters.
8.Working in the sequence shown remove 10
bolts securing the cylinder head to block.
Discard the bolts.
9.Remove cylinder head.
Page 217 of 1529
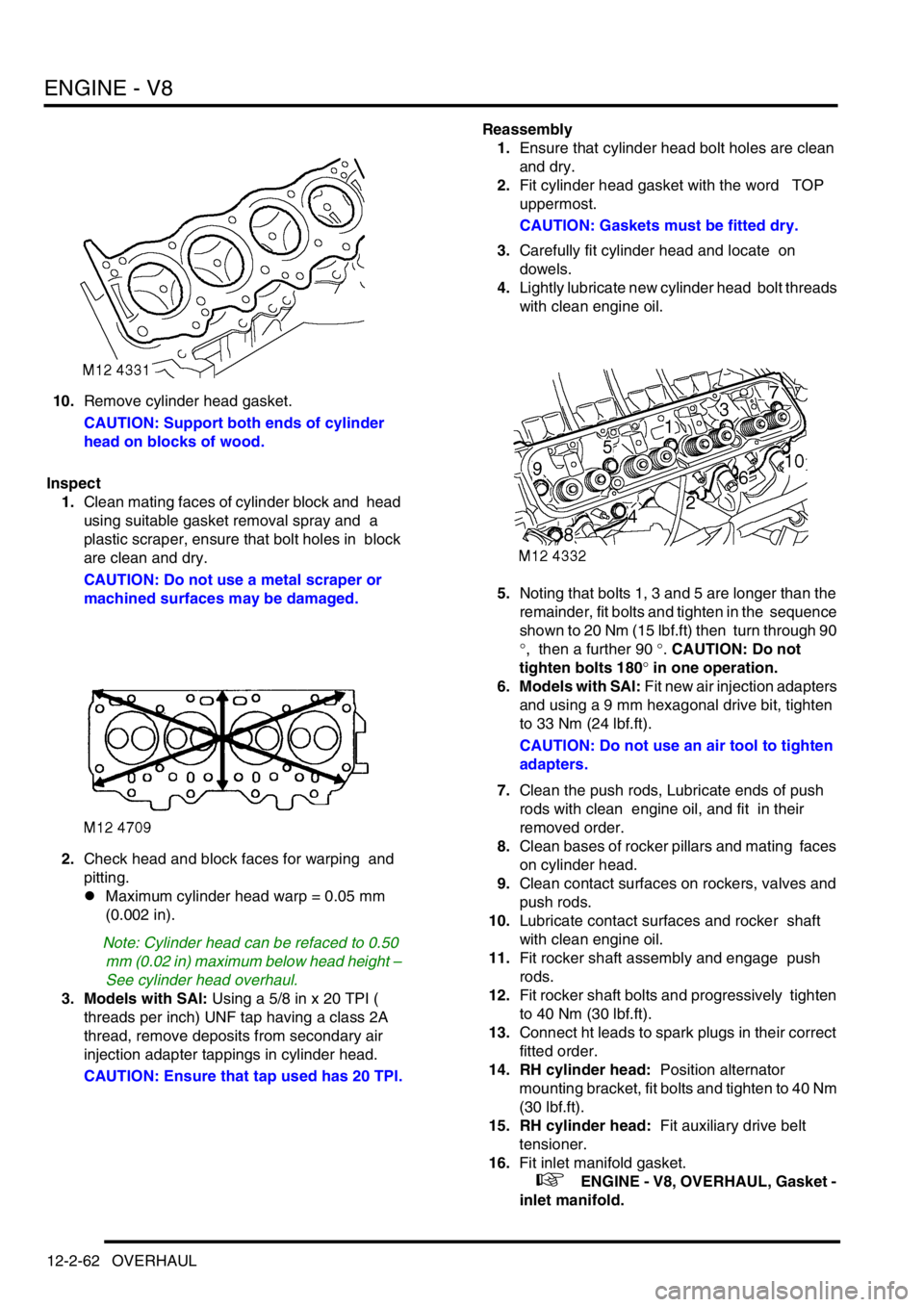
ENGINE - V8
12-2-62 OVERHAUL
10.Remove cylinder head gasket.
CAUTION: Support both ends of cylinder
head on blocks of wood.
Inspect
1.Clean mating faces of cylinder block and head
using suitable gasket removal spray and a
plastic scraper, ensure that bolt holes in block
are clean and dry.
CAUTION: Do not use a metal scraper or
machined surfaces may be damaged.
2.Check head and block faces for warping and
pitting.
lMaximum cylinder head warp = 0.05 mm
(0.002 in).
Note: Cylinder head can be refaced to 0.50
mm (0.02 in) maximum below head height –
See cylinder head overhaul.
3. Models with SAI: Using a 5/8 in x 20 TPI (
threads per inch) UNF tap having a class 2A
thread, remove deposits from secondary air
injection adapter tappings in cylinder head.
CAUTION: Ensure that tap used has 20 TPI.Reassembly
1.Ensure that cylinder head bolt holes are clean
and dry.
2.Fit cylinder head gasket with the word TOP
uppermost.
CAUTION: Gaskets must be fitted dry.
3.Carefully fit cylinder head and locate on
dowels.
4.Lightly lubricate new cylinder head bolt threads
with clean engine oil.
5.Noting that bolts 1, 3 and 5 are longer than the
remainder, fit bolts and tighten in the sequence
shown to 20 Nm (15 lbf.ft) then turn through 90
°, then a further 90 °. CAUTION: Do not
tighten bolts 180° in one operation.
6. Models with SAI: Fit new air injection adapters
and using a 9 mm hexagonal drive bit, tighten
to 33 Nm (24 lbf.ft).
CAUTION: Do not use an air tool to tighten
adapters.
7.Clean the push rods, Lubricate ends of push
rods with clean engine oil, and fit in their
removed order.
8.Clean bases of rocker pillars and mating faces
on cylinder head.
9.Clean contact surfaces on rockers, valves and
push rods.
10.Lubricate contact surfaces and rocker shaft
with clean engine oil.
11.Fit rocker shaft assembly and engage push
rods.
12.Fit rocker shaft bolts and progressively tighten
to 40 Nm (30 lbf.ft).
13.Connect ht leads to spark plugs in their correct
fitted order.
14. RH cylinder head: Position alternator
mounting bracket, fit bolts and tighten to 40 Nm
(30 lbf.ft).
15. RH cylinder head: Fit auxiliary drive belt
tensioner.
16.Fit inlet manifold gasket.
+ ENGINE - V8, OVERHAUL, Gasket -
inlet manifold.
Page 218 of 1529
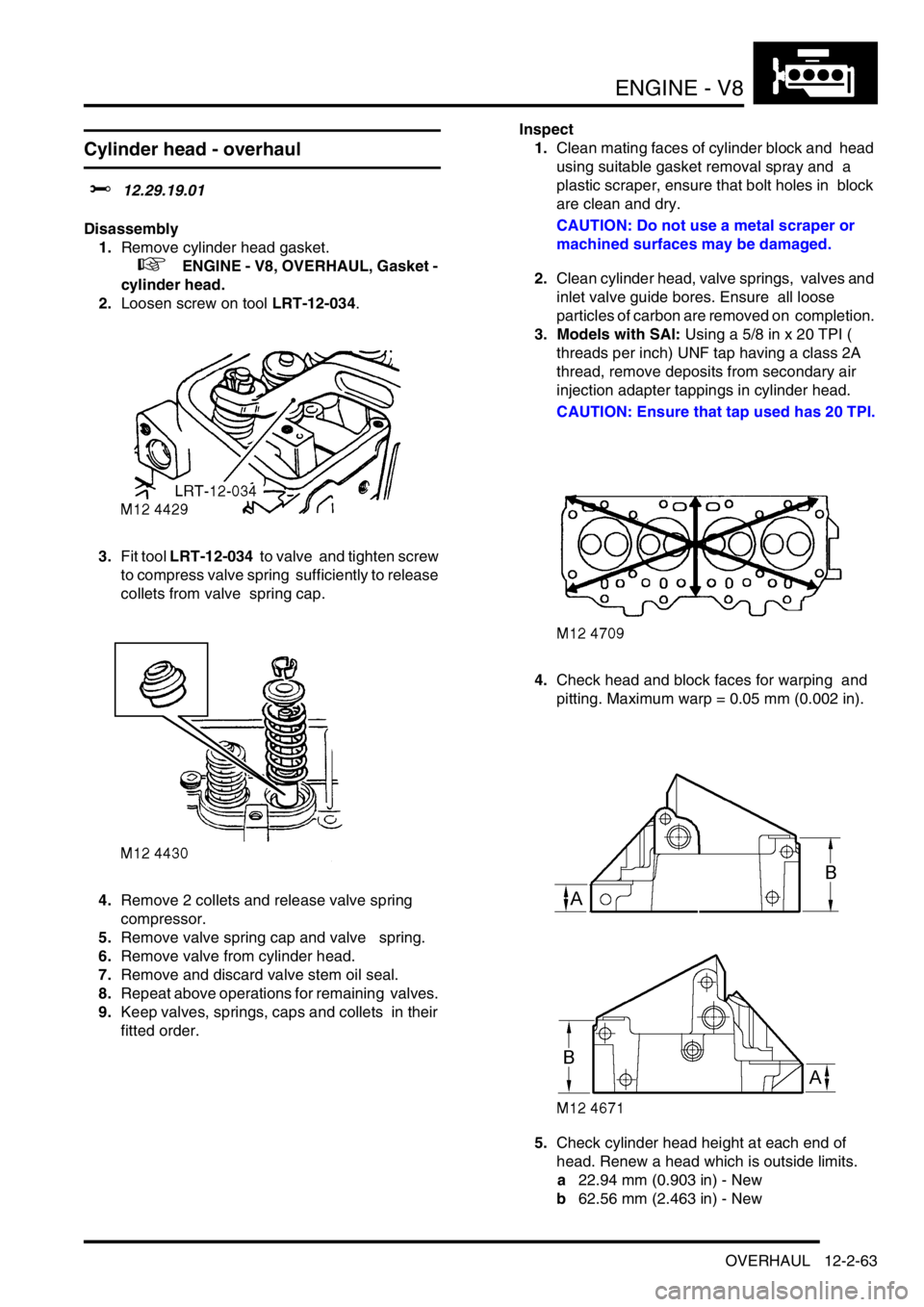
ENGINE - V8
OVERHAUL 12-2-63
Cylinder head - overhaul
$% 12.29.19.01
Disassembly
1.Remove cylinder head gasket.
+ ENGINE - V8, OVERHAUL, Gasket -
cylinder head.
2.Loosen screw on tool LRT-12-034.
3.Fit tool LRT-12-034 to valve and tighten screw
to compress valve spring sufficiently to release
collets from valve spring cap.
4.Remove 2 collets and release valve spring
compressor.
5.Remove valve spring cap and valve spring.
6.Remove valve from cylinder head.
7.Remove and discard valve stem oil seal.
8.Repeat above operations for remaining valves.
9.Keep valves, springs, caps and collets in their
fitted order. Inspect
1.Clean mating faces of cylinder block and head
using suitable gasket removal spray and a
plastic scraper, ensure that bolt holes in block
are clean and dry.
CAUTION: Do not use a metal scraper or
machined surfaces may be damaged.
2.Clean cylinder head, valve springs, valves and
inlet valve guide bores. Ensure all loose
particles of carbon are removed on completion.
3. Models with SAI: Using a 5/8 in x 20 TPI (
threads per inch) UNF tap having a class 2A
thread, remove deposits from secondary air
injection adapter tappings in cylinder head.
CAUTION: Ensure that tap used has 20 TPI.
4.Check head and block faces for warping and
pitting. Maximum warp = 0.05 mm (0.002 in).
5.Check cylinder head height at each end of
head. Renew a head which is outside limits.
a22.94 mm (0.903 in) - New
b62.56 mm (2.463 in) - New
Page 219 of 1529
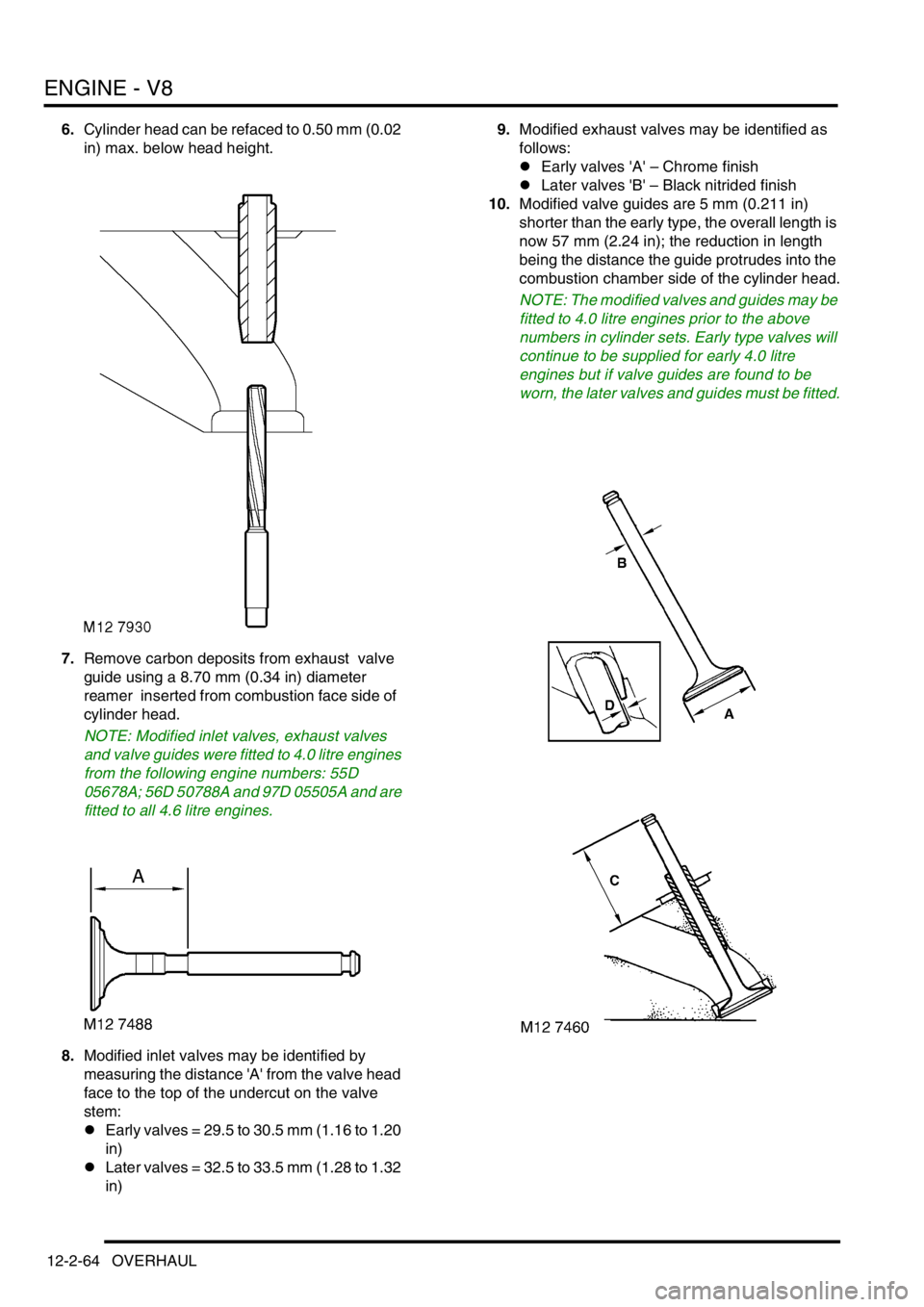
ENGINE - V8
12-2-64 OVERHAUL
6.Cylinder head can be refaced to 0.50 mm (0.02
in) max. below head height.
7.Remove carbon deposits from exhaust valve
guide using a 8.70 mm (0.34 in) diameter
reamer inserted from combustion face side of
cylinder head.
NOTE: Modified inlet valves, exhaust valves
and valve guides were fitted to 4.0 litre engines
from the following engine numbers: 55D
05678A; 56D 50788A and 97D 05505A and are
fitted to all 4.6 litre engines.
8.Modified inlet valves may be identified by
measuring the distance 'A' from the valve head
face to the top of the undercut on the valve
stem:
lEarly valves = 29.5 to 30.5 mm (1.16 to 1.20
in)
lLater valves = 32.5 to 33.5 mm (1.28 to 1.32
in)9.Modified exhaust valves may be identified as
follows:
lEarly valves 'A' – Chrome finish
lLater valves 'B' – Black nitrided finish
10.Modified valve guides are 5 mm (0.211 in)
shorter than the early type, the overall length is
now 57 mm (2.24 in); the reduction in length
being the distance the guide protrudes into the
combustion chamber side of the cylinder head.
NOTE: The modified valves and guides may be
fitted to 4.0 litre engines prior to the above
numbers in cylinder sets. Early type valves will
continue to be supplied for early 4.0 litre
engines but if valve guides are found to be
worn, the later valves and guides must be fitted.
Page 220 of 1529
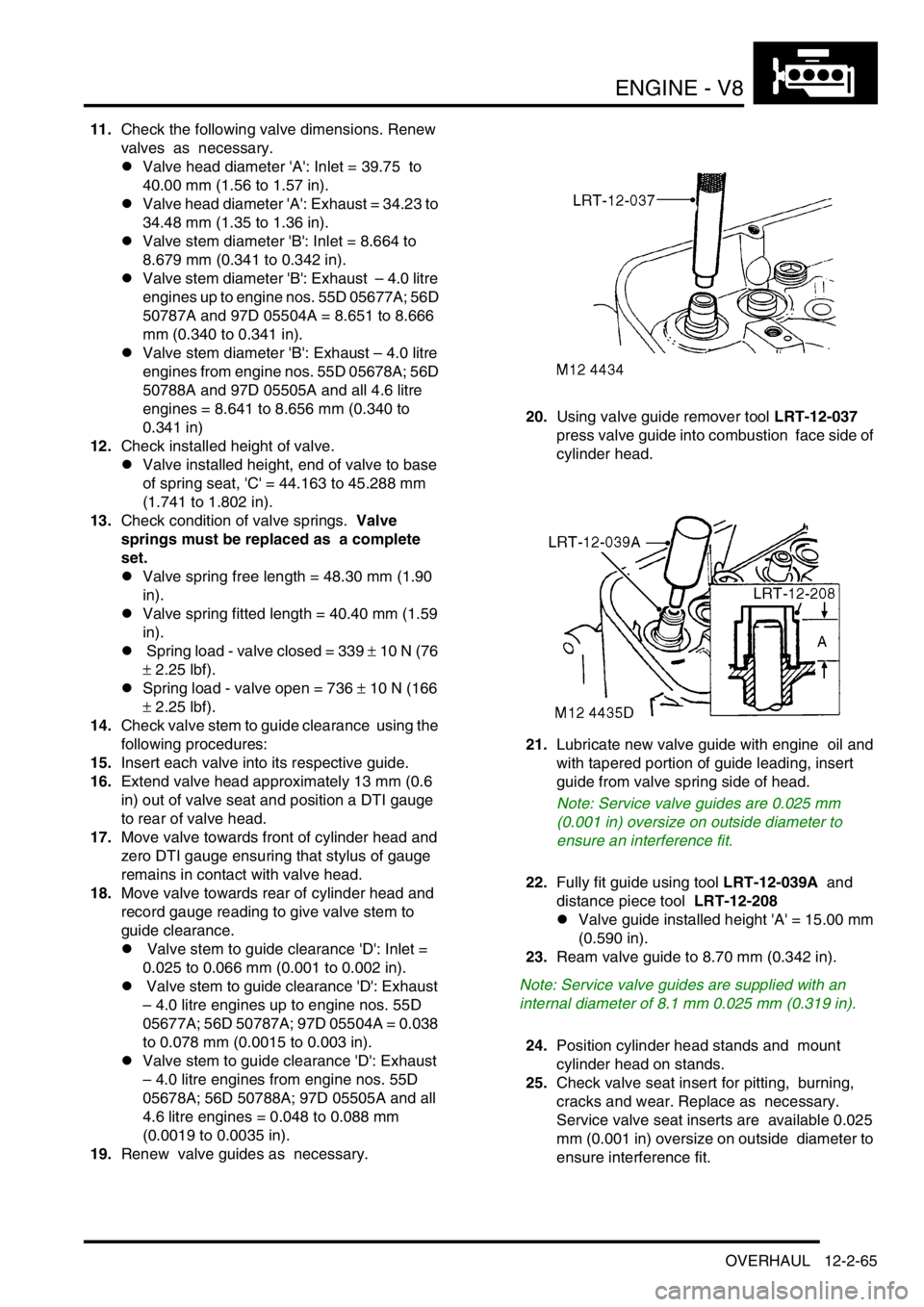
ENGINE - V8
OVERHAUL 12-2-65
11.Check the following valve dimensions. Renew
valves as necessary.
lValve head diameter 'A': Inlet = 39.75 to
40.00 mm (1.56 to 1.57 in).
lValve head diameter 'A': Exhaust = 34.23 to
34.48 mm (1.35 to 1.36 in).
lValve stem diameter 'B': Inlet = 8.664 to
8.679 mm (0.341 to 0.342 in).
lValve stem diameter 'B': Exhaust – 4.0 litre
engines up to engine nos. 55D 05677A; 56D
50787A and 97D 05504A = 8.651 to 8.666
mm (0.340 to 0.341 in).
lValve stem diameter 'B': Exhaust – 4.0 litre
engines from engine nos. 55D 05678A; 56D
50788A and 97D 05505A and all 4.6 litre
engines = 8.641 to 8.656 mm (0.340 to
0.341 in)
12.Check installed height of valve.
lValve installed height, end of valve to base
of spring seat, 'C' = 44.163 to 45.288 mm
(1.741 to 1.802 in).
13.Check condition of valve springs. Valve
springs must be replaced as a complete
set.
lValve spring free length = 48.30 mm (1.90
in).
lValve spring fitted length = 40.40 mm (1.59
in).
l Spring load - valve closed = 339 ± 10 N (76
± 2.25 lbf).
lSpring load - valve open = 736 ± 10 N (166
± 2.25 lbf).
14.Check valve stem to guide clearance using the
following procedures:
15.Insert each valve into its respective guide.
16.Extend valve head approximately 13 mm (0.6
in) out of valve seat and position a DTI gauge
to rear of valve head.
17.Move valve towards front of cylinder head and
zero DTI gauge ensuring that stylus of gauge
remains in contact with valve head.
18.Move valve towards rear of cylinder head and
record gauge reading to give valve stem to
guide clearance.
l Valve stem to guide clearance 'D': Inlet =
0.025 to 0.066 mm (0.001 to 0.002 in).
l Valve stem to guide clearance 'D': Exhaust
– 4.0 litre engines up to engine nos. 55D
05677A; 56D 50787A; 97D 05504A = 0.038
to 0.078 mm (0.0015 to 0.003 in).
lValve stem to guide clearance 'D': Exhaust
– 4.0 litre engines from engine nos. 55D
05678A; 56D 50788A; 97D 05505A and all
4.6 litre engines = 0.048 to 0.088 mm
(0.0019 to 0.0035 in).
19.Renew valve guides as necessary. 20.Using valve guide remover tool LRT-12-037
press valve guide into combustion face side of
cylinder head.
21.Lubricate new valve guide with engine oil and
with tapered portion of guide leading, insert
guide from valve spring side of head.
Note: Service valve guides are 0.025 mm
(0.001 in) oversize on outside diameter to
ensure an interference fit.
22.Fully fit guide using tool LRT-12-039A and
distance piece tool LRT-12-208
lValve guide installed height 'A' = 15.00 mm
(0.590 in).
23.Ream valve guide to 8.70 mm (0.342 in).
Note: Service valve guides are supplied with an
internal diameter of 8.1 mm 0.025 mm (0.319 in).
24.Position cylinder head stands and mount
cylinder head on stands.
25.Check valve seat insert for pitting, burning,
cracks and wear. Replace as necessary.
Service valve seat inserts are available 0.025
mm (0.001 in) oversize on outside diameter to
ensure interference fit.