LAND ROVER DISCOVERY 2002 Workshop Manual
Manufacturer: LAND ROVER, Model Year: 2002, Model line: DISCOVERY, Model: LAND ROVER DISCOVERY 2002Pages: 1672, PDF Size: 46.1 MB
Page 561 of 1672
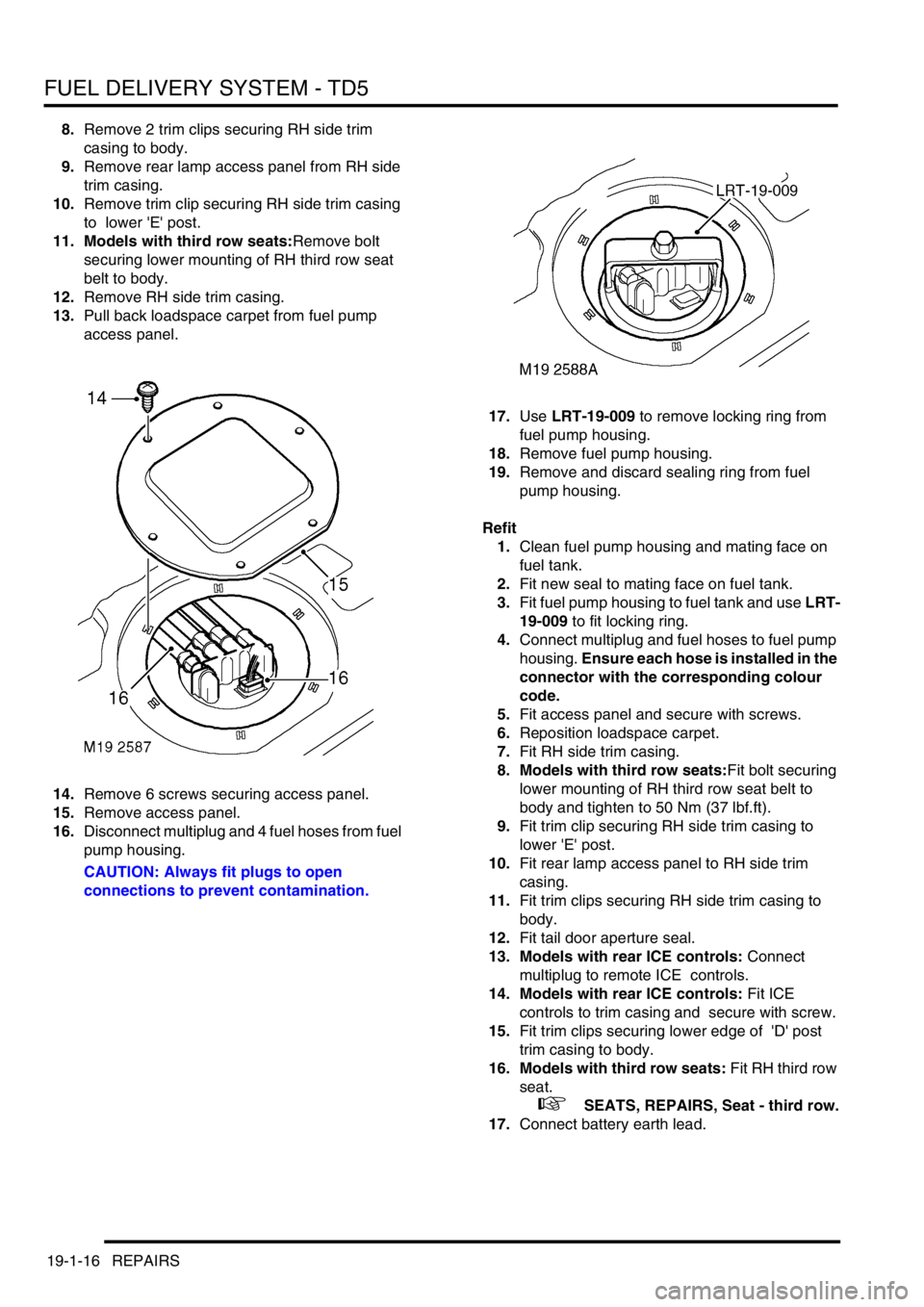
FUEL DELIVERY SYSTEM - TD5
19-1-16 REPAIRS
8.Remove 2 trim clips securing RH side trim
casing to body.
9.Remove rear lamp access panel from RH side
trim casing.
10.Remove trim clip securing RH side trim casing
to lower 'E' post.
11. Models with third row seats:Remove bolt
securing lower mounting of RH third row seat
belt to body.
12.Remove RH side trim casing.
13.Pull back loadspace carpet from fuel pump
access panel.
14.Remove 6 screws securing access panel.
15.Remove access panel.
16.Disconnect multiplug and 4 fuel hoses from fuel
pump housing.
CAUTION: Always fit plugs to open
connections to prevent contamination.17.Use LRT-19-009 to remove locking ring from
fuel pump housing.
18.Remove fuel pump housing.
19.Remove and discard sealing ring from fuel
pump housing.
Refit
1.Clean fuel pump housing and mating face on
fuel tank.
2.Fit new seal to mating face on fuel tank.
3.Fit fuel pump housing to fuel tank and use LRT-
19-009 to fit locking ring.
4.Connect multiplug and fuel hoses to fuel pump
housing. Ensure each hose is installed in the
connector with the corresponding colour
code.
5.Fit access panel and secure with screws.
6.Reposition loadspace carpet.
7.Fit RH side trim casing.
8. Models with third row seats:Fit bolt securing
lower mounting of RH third row seat belt to
body and tighten to 50 Nm (37 lbf.ft).
9.Fit trim clip securing RH side trim casing to
lower 'E' post.
10.Fit rear lamp access panel to RH side trim
casing.
11.Fit trim clips securing RH side trim casing to
body.
12.Fit tail door aperture seal.
13. Models with rear ICE controls: Connect
multiplug to remote ICE controls.
14. Models with rear ICE controls: Fit ICE
controls to trim casing and secure with screw.
15.Fit trim clips securing lower edge of 'D' post
trim casing to body.
16. Models with third row seats: Fit RH third row
seat.
+ SEATS, REPAIRS, Seat - third row.
17.Connect battery earth lead.
Page 562 of 1672
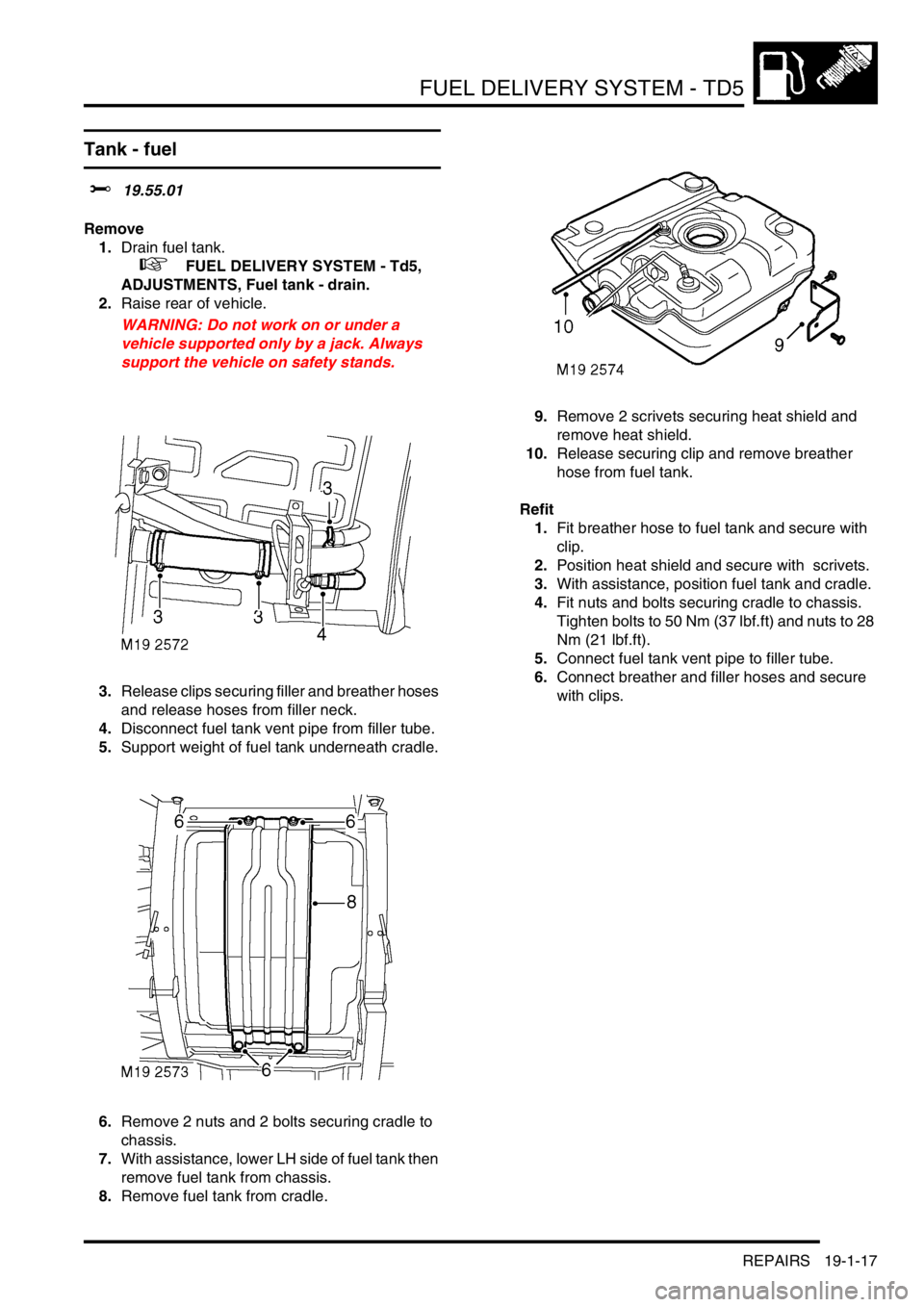
FUEL DELIVERY SYSTEM - TD5
REPAIRS 19-1-17
Tank - fuel
$% 19.55.01
Remove
1.Drain fuel tank.
+ FUEL DELIVERY SYSTEM - Td5,
ADJUSTMENTS, Fuel tank - drain.
2.Raise rear of vehicle.
WARNING: Do not work on or under a
vehicle supported only by a jack. Always
support the vehicle on safety stands.
3.Release clips securing filler and breather hoses
and release hoses from filler neck.
4.Disconnect fuel tank vent pipe from filler tube.
5.Support weight of fuel tank underneath cradle.
6.Remove 2 nuts and 2 bolts securing cradle to
chassis.
7.With assistance, lower LH side of fuel tank then
remove fuel tank from chassis.
8.Remove fuel tank from cradle.9.Remove 2 scrivets securing heat shield and
remove heat shield.
10.Release securing clip and remove breather
hose from fuel tank.
Refit
1.Fit breather hose to fuel tank and secure with
clip.
2.Position heat shield and secure with scrivets.
3.With assistance, position fuel tank and cradle.
4.Fit nuts and bolts securing cradle to chassis.
Tighten bolts to 50 Nm (37 lbf.ft) and nuts to 28
Nm (21 lbf.ft).
5.Connect fuel tank vent pipe to filler tube.
6.Connect breather and filler hoses and secure
with clips.
Page 563 of 1672
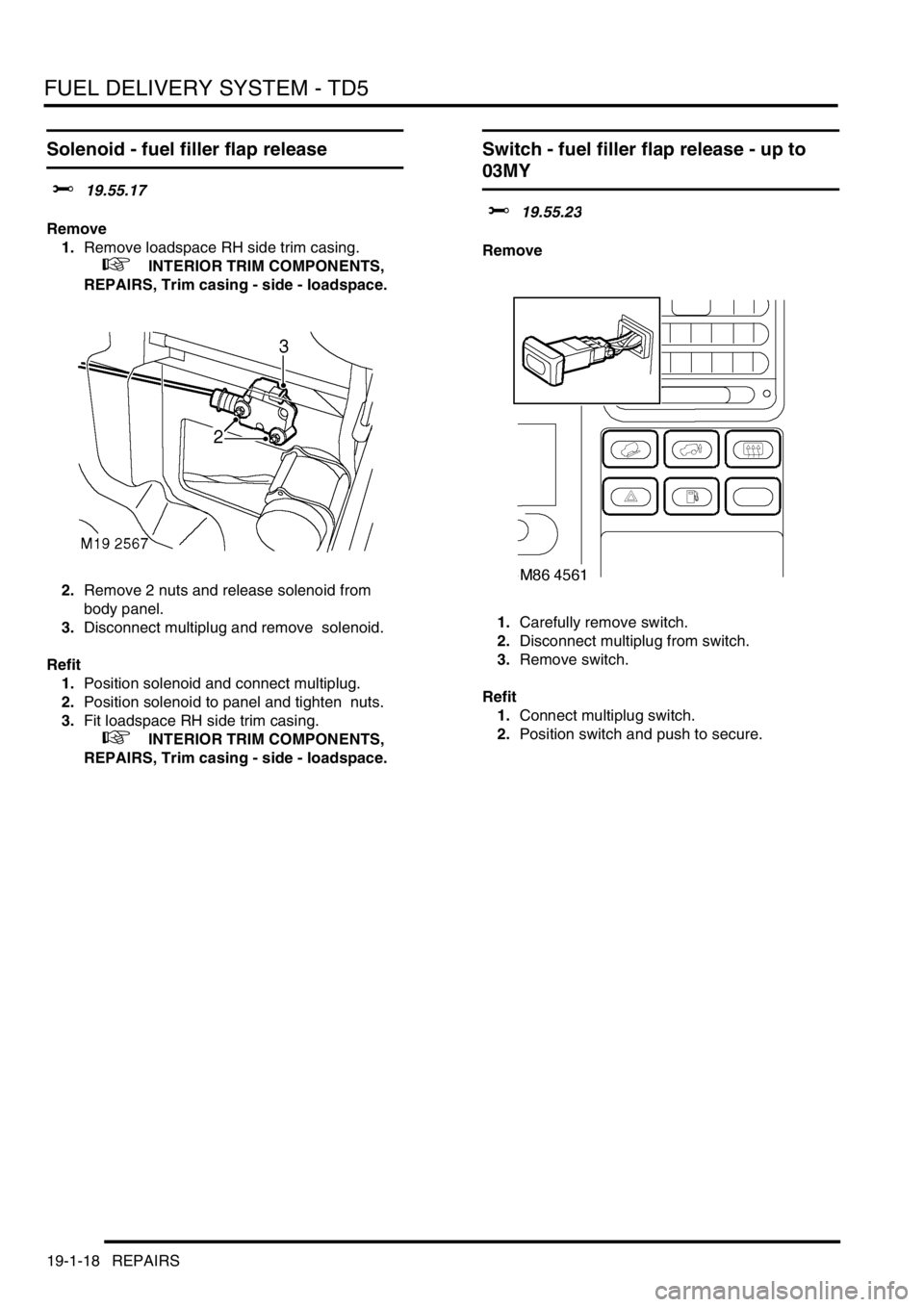
FUEL DELIVERY SYSTEM - TD5
19-1-18 REPAIRS
Solenoid - fuel filler flap release
$% 19.55.17
Remove
1.Remove loadspace RH side trim casing.
+ INTERIOR TRIM COMPONENTS,
REPAIRS, Trim casing - side - loadspace.
2.Remove 2 nuts and release solenoid from
body panel.
3.Disconnect multiplug and remove solenoid.
Refit
1.Position solenoid and connect multiplug.
2.Position solenoid to panel and tighten nuts.
3.Fit loadspace RH side trim casing.
+ INTERIOR TRIM COMPONENTS,
REPAIRS, Trim casing - side - loadspace.
Switch - fuel filler flap release - up to
03MY
$% 19.55.23
Remove
1.Carefully remove switch.
2.Disconnect multiplug from switch.
3.Remove switch.
Refit
1.Connect multiplug switch.
2.Position switch and push to secure.
Page 564 of 1672
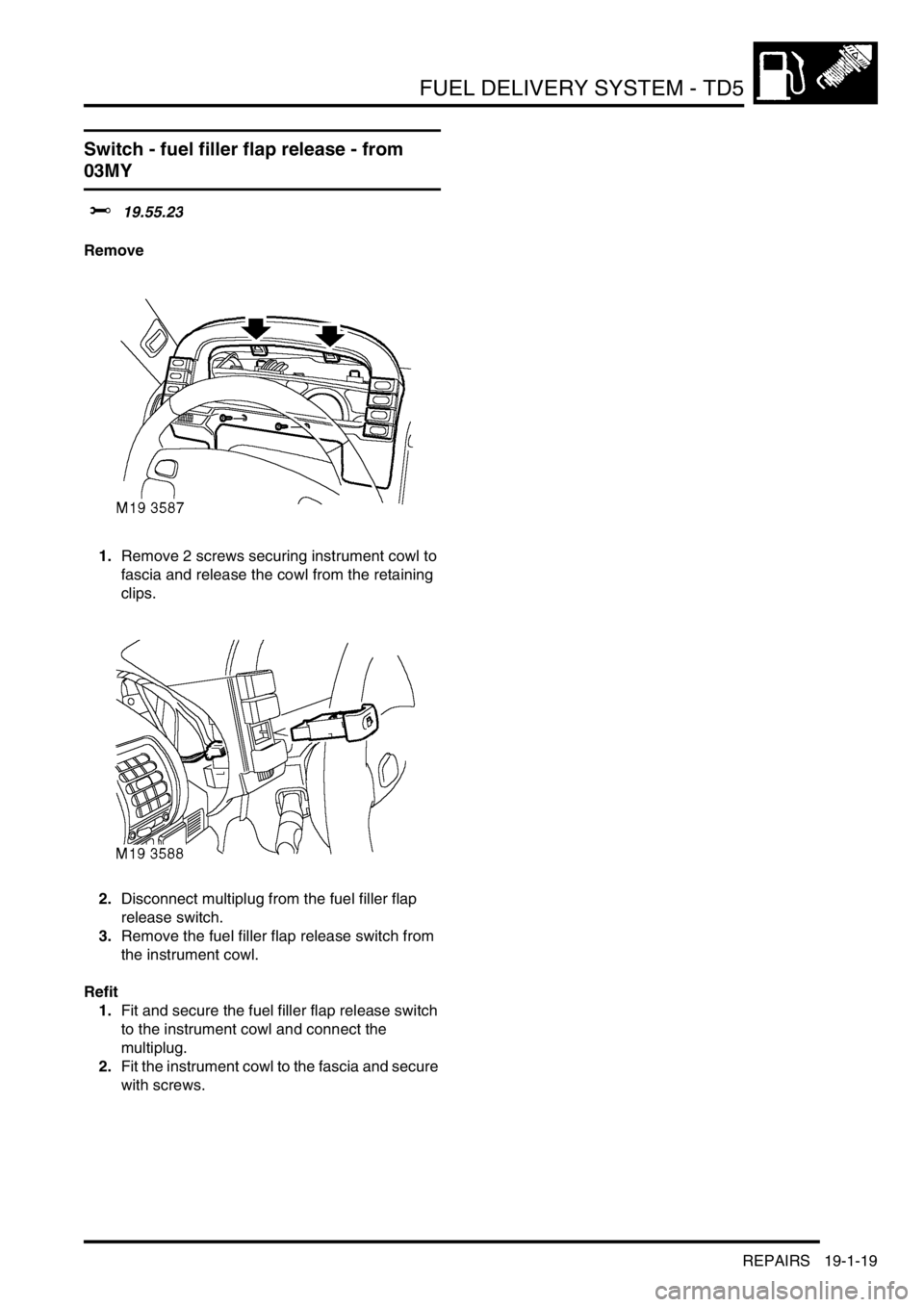
FUEL DELIVERY SYSTEM - TD5
REPAIRS 19-1-19
Switch - fuel filler flap release - from
03MY
$% 19.55.23
Remove
1.Remove 2 screws securing instrument cowl to
fascia and release the cowl from the retaining
clips.
2.Disconnect multiplug from the fuel filler flap
release switch.
3.Remove the fuel filler flap release switch from
the instrument cowl.
Refit
1.Fit and secure the fuel filler flap release switch
to the instrument cowl and connect the
multiplug.
2.Fit the instrument cowl to the fascia and secure
with screws.
Page 565 of 1672
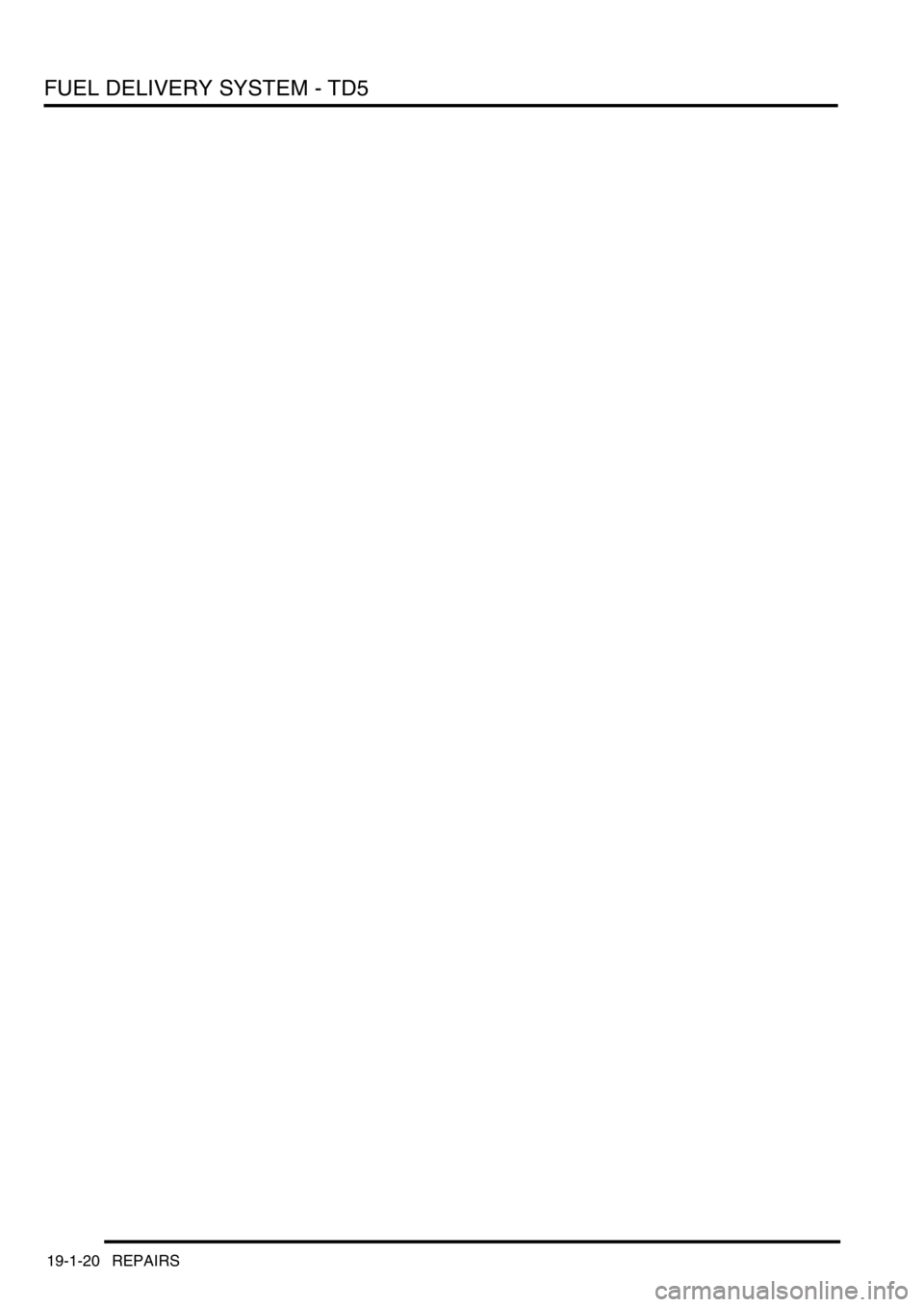
FUEL DELIVERY SYSTEM - TD5
19-1-20 REPAIRS
Page 566 of 1672
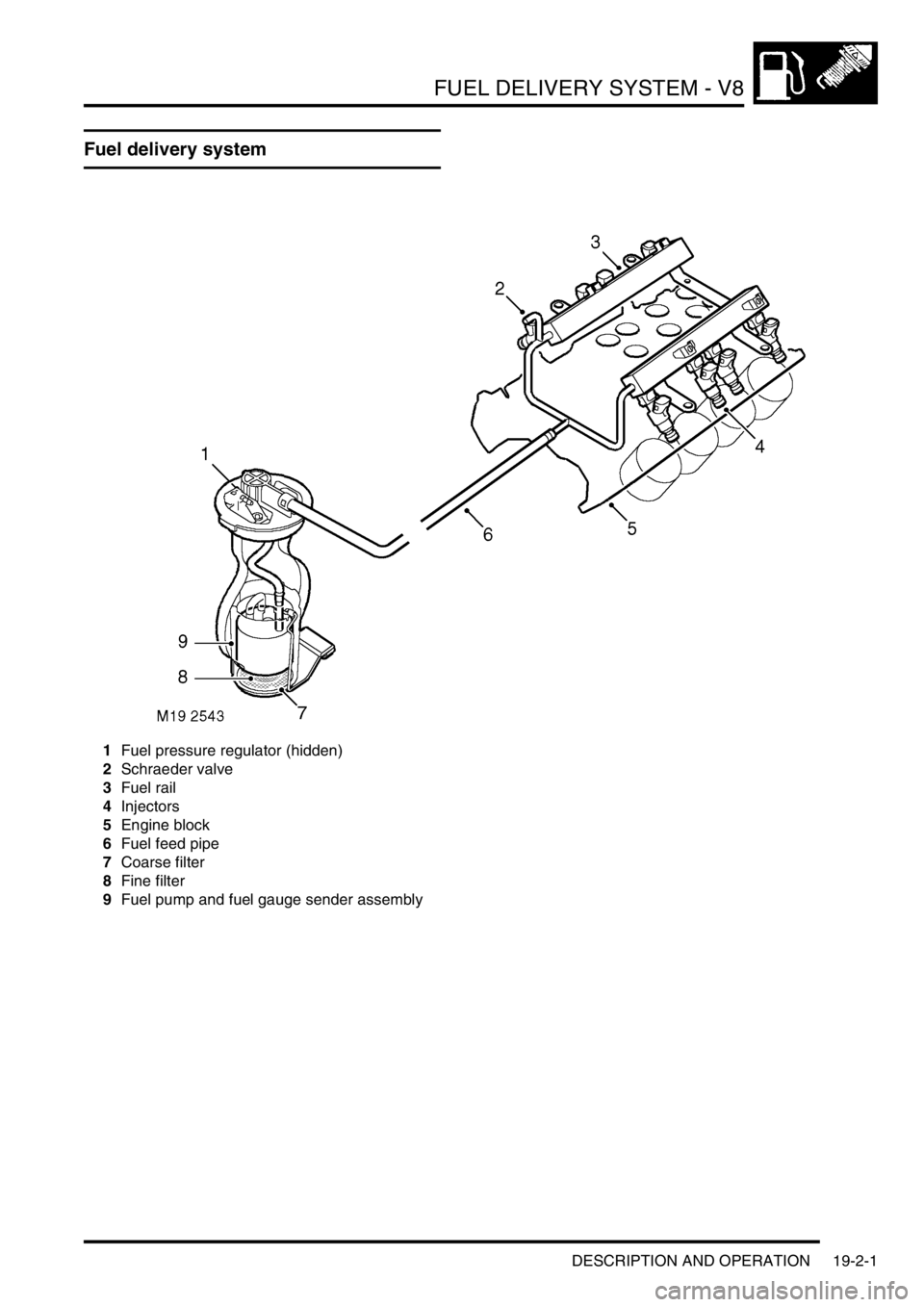
FUEL DELIVERY SYSTEM - V8
DESCRIPTION AND OPERATION 19-2-1
FUEL DELIVERY SYST EM - V8 DESCRIPTION AND OPERAT ION
Fuel delivery system
1Fuel pressure regulator (hidden)
2Schraeder valve
3Fuel rail
4Injectors
5Engine block
6Fuel feed pipe
7Coarse filter
8Fine filter
9Fuel pump and fuel gauge sender assembly
Page 567 of 1672
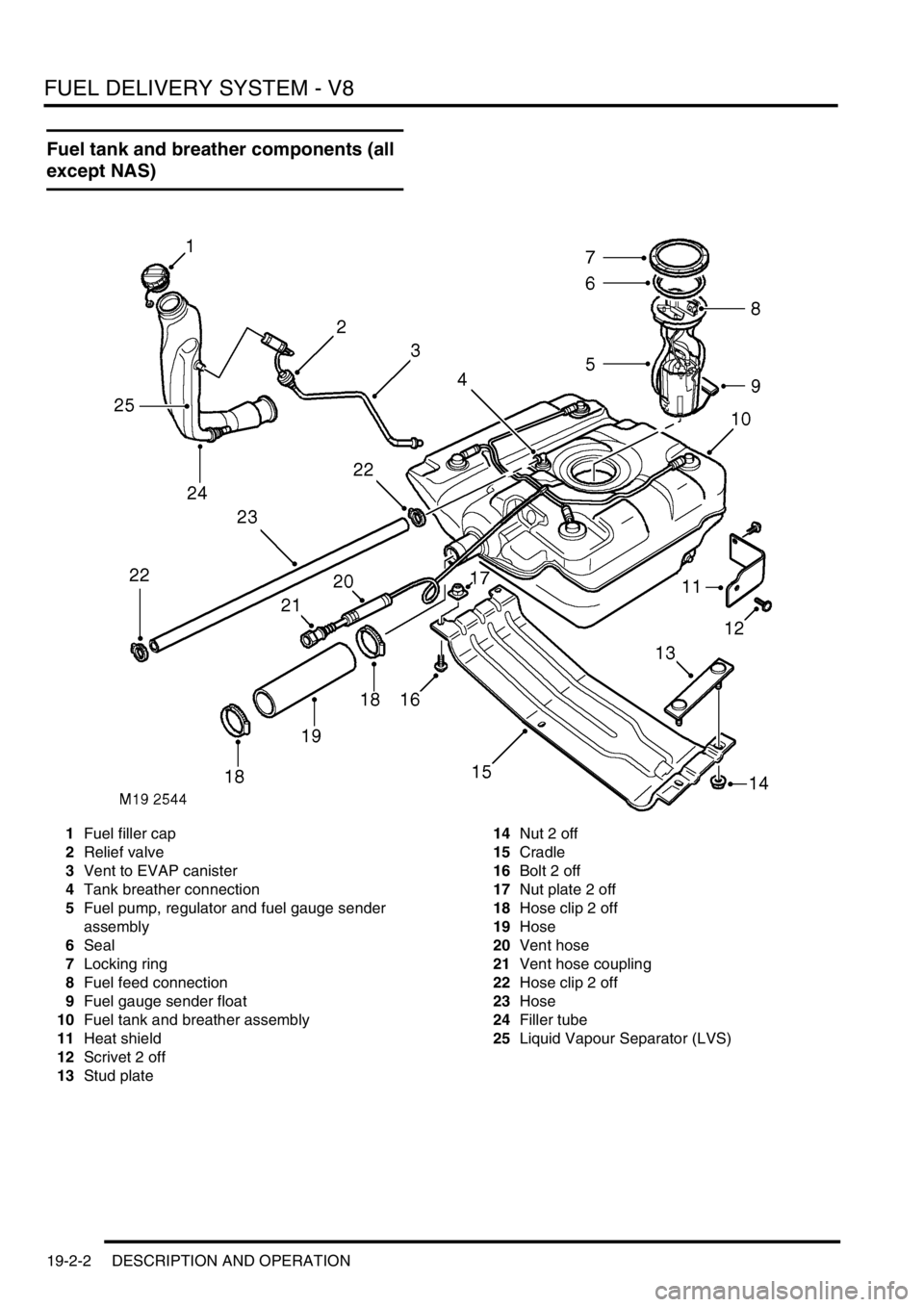
FUEL DELIVERY SYSTEM - V8
19-2-2 DESCRIPTION AND OPERATION
Fuel tank and breather components (all
except NAS)
1Fuel filler cap
2Relief valve
3Vent to EVAP canister
4Tank breather connection
5Fuel pump, regulator and fuel gauge sender
assembly
6Seal
7Locking ring
8Fuel feed connection
9Fuel gauge sender float
10Fuel tank and breather assembly
11Heat shield
12Scrivet 2 off
13Stud plate14Nut 2 off
15Cradle
16Bolt 2 off
17Nut plate 2 off
18Hose clip 2 off
19Hose
20Vent hose
21Vent hose coupling
22Hose clip 2 off
23Hose
24Filler tube
25Liquid Vapour Separator (LVS)
Page 568 of 1672
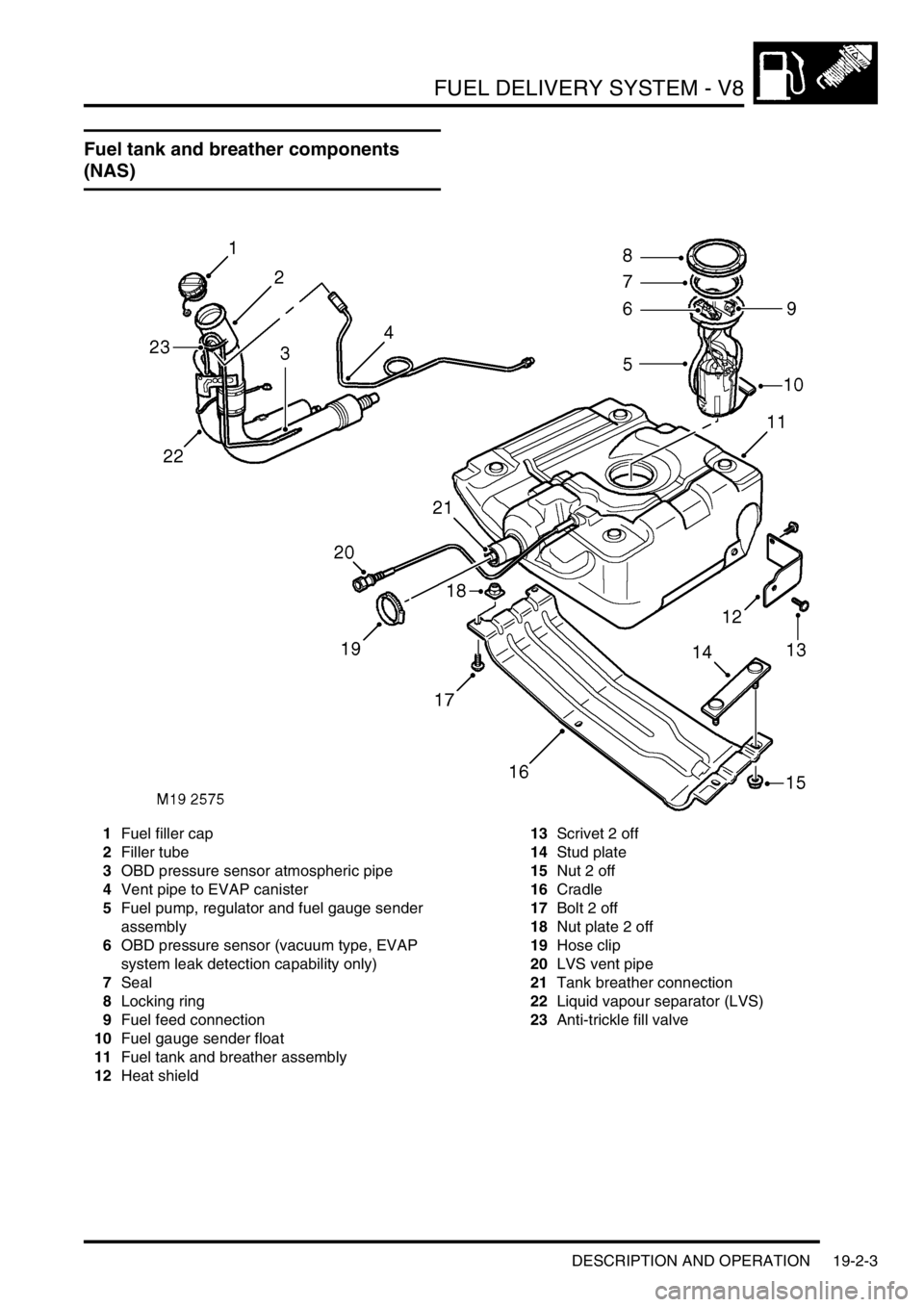
FUEL DELIVERY SYSTEM - V8
DESCRIPTION AND OPERATION 19-2-3
Fuel tank and breather components
(NAS)
1Fuel filler cap
2Filler tube
3OBD pressure sensor atmospheric pipe
4Vent pipe to EVAP canister
5Fuel pump, regulator and fuel gauge sender
assembly
6OBD pressure sensor (vacuum type, EVAP
system leak detection capability only)
7Seal
8Locking ring
9Fuel feed connection
10Fuel gauge sender float
11Fuel tank and breather assembly
12Heat shield13Scrivet 2 off
14Stud plate
15Nut 2 off
16Cradle
17Bolt 2 off
18Nut plate 2 off
19Hose clip
20LVS vent pipe
21Tank breather connection
22Liquid vapour separator (LVS)
23Anti-trickle fill valve
Page 569 of 1672
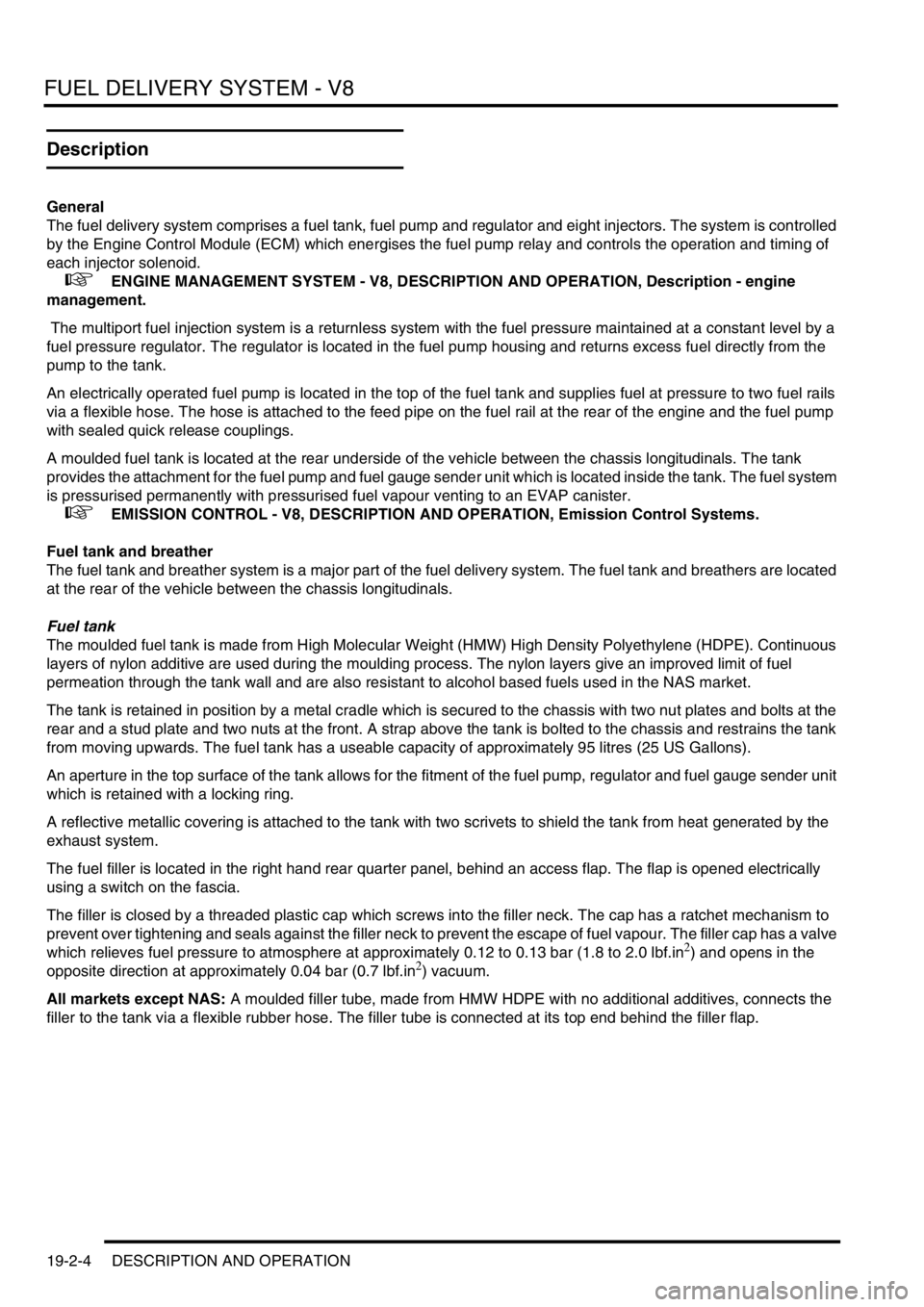
FUEL DELIVERY SYSTEM - V8
19-2-4 DESCRIPTION AND OPERATION
Description
General
The fuel delivery system comprises a fuel tank, fuel pump and regulator and eight injectors. The system is controlled
by the Engine Control Module (ECM) which energises the fuel pump relay and controls the operation and timing of
each injector solenoid.
+ ENGINE MANAGEMENT SYSTEM - V8, DESCRIPTION AND OPERATION, Description - engine
management.
The multiport fuel injection system is a returnless system with the fuel pressure maintained at a constant level by a
fuel pressure regulator. The regulator is located in the fuel pump housing and returns excess fuel directly from the
pump to the tank.
An electrically operated fuel pump is located in the top of the fuel tank and supplies fuel at pressure to two fuel rails
via a flexible hose. The hose is attached to the feed pipe on the fuel rail at the rear of the engine and the fuel pump
with sealed quick release couplings.
A moulded fuel tank is located at the rear underside of the vehicle between the chassis longitudinals. The tank
provides the attachment for the fuel pump and fuel gauge sender unit which is located inside the tank. The fuel system
is pressurised permanently with pressurised fuel vapour venting to an EVAP canister.
+ EMISSION CONTROL - V8, DESCRIPTION AND OPERATION, Emission Control Systems.
Fuel tank and breather
The fuel tank and breather system is a major part of the fuel delivery system. The fuel tank and breathers are located
at the rear of the vehicle between the chassis longitudinals.
Fuel tank
The moulded fuel tank is made from High Molecular Weight (HMW) High Density Polyethylene (HDPE). Continuous
layers of nylon additive are used during the moulding process. The nylon layers give an improved limit of fuel
permeation through the tank wall and are also resistant to alcohol based fuels used in the NAS market.
The tank is retained in position by a metal cradle which is secured to the chassis with two nut plates and bolts at the
rear and a stud plate and two nuts at the front. A strap above the tank is bolted to the chassis and restrains the tank
from moving upwards. The fuel tank has a useable capacity of approximately 95 litres (25 US Gallons).
An aperture in the top surface of the tank allows for the fitment of the fuel pump, regulator and fuel gauge sender unit
which is retained with a locking ring.
A reflective metallic covering is attached to the tank with two scrivets to shield the tank from heat generated by the
exhaust system.
The fuel filler is located in the right hand rear quarter panel, behind an access flap. The flap is opened electrically
using a switch on the fascia.
The filler is closed by a threaded plastic cap which screws into the filler neck. The cap has a ratchet mechanism to
prevent over tightening and seals against the filler neck to prevent the escape of fuel vapour. The filler cap has a valve
which relieves fuel pressure to atmosphere at approximately 0.12 to 0.13 bar (1.8 to 2.0 lbf.in
2) and opens in the
opposite direction at approximately 0.04 bar (0.7 lbf.in2) vacuum.
All markets except NAS: A moulded filler tube, made from HMW HDPE with no additional additives, connects the
filler to the tank via a flexible rubber hose. The filler tube is connected at its top end behind the filler flap.
Page 570 of 1672
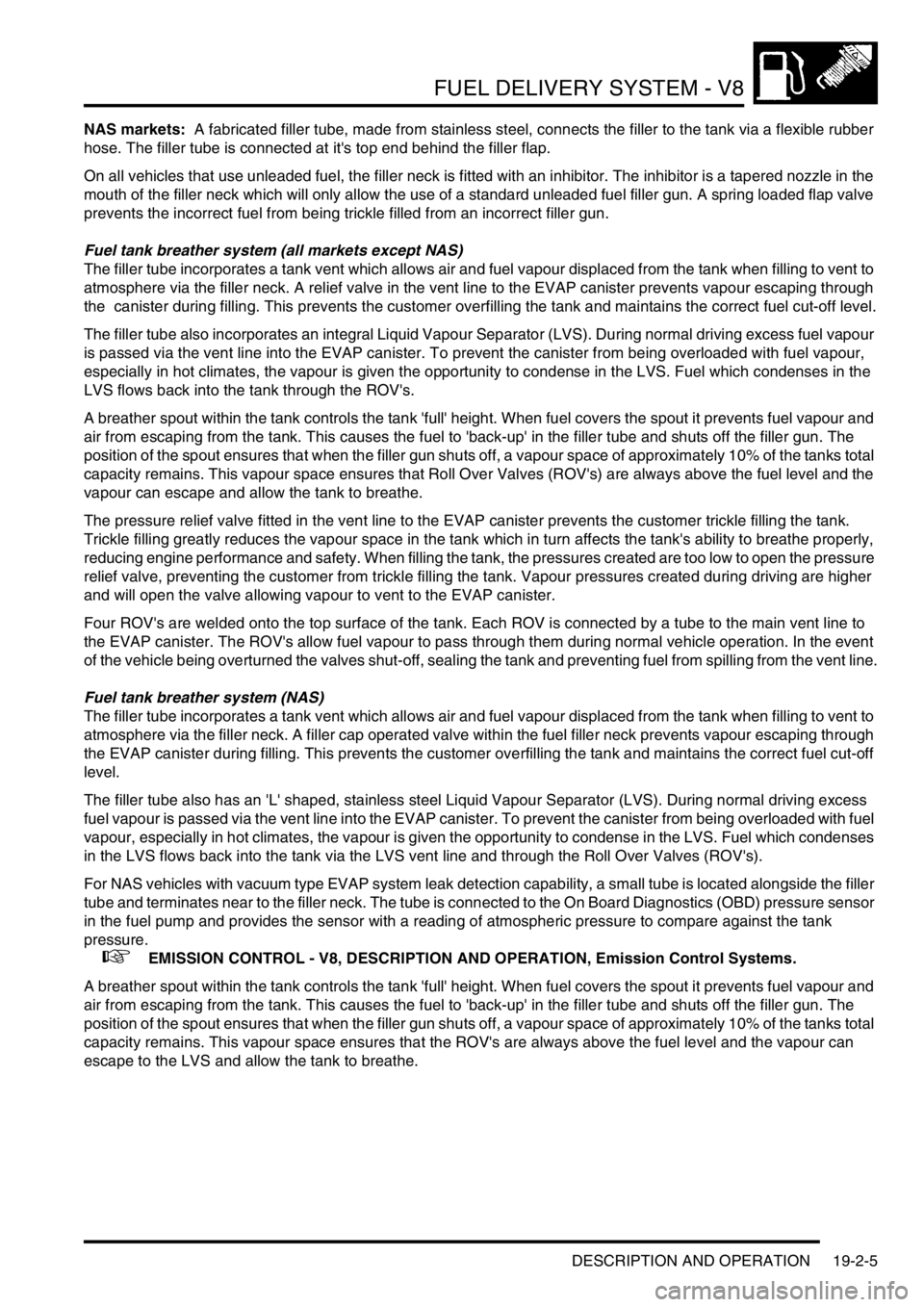
FUEL DELIVERY SYSTEM - V8
DESCRIPTION AND OPERATION 19-2-5
NAS markets: A fabricated filler tube, made from stainless steel, connects the filler to the tank via a flexible rubber
hose. The filler tube is connected at it's top end behind the filler flap.
On all vehicles that use unleaded fuel, the filler neck is fitted with an inhibitor. The inhibitor is a tapered nozzle in the
mouth of the filler neck which will only allow the use of a standard unleaded fuel filler gun. A spring loaded flap valve
prevents the incorrect fuel from being trickle filled from an incorrect filler gun.
Fuel tank breather system (all markets except NAS)
The filler tube incorporates a tank vent which allows air and fuel vapour displaced from the tank when filling to vent to
atmosphere via the filler neck. A relief valve in the vent line to the EVAP canister prevents vapour escaping through
the canister during filling. This prevents the customer overfilling the tank and maintains the correct fuel cut-off level.
The filler tube also incorporates an integral Liquid Vapour Separator (LVS). During normal driving excess fuel vapour
is passed via the vent line into the EVAP canister. To prevent the canister from being overloaded with fuel vapour,
especially in hot climates, the vapour is given the opportunity to condense in the LVS. Fuel which condenses in the
LVS flows back into the tank through the ROV's.
A breather spout within the tank controls the tank 'full' height. When fuel covers the spout it prevents fuel vapour and
air from escaping from the tank. This causes the fuel to 'back-up' in the filler tube and shuts off the filler gun. The
position of the spout ensures that when the filler gun shuts off, a vapour space of approximately 10% of the tanks total
capacity remains. This vapour space ensures that Roll Over Valves (ROV's) are always above the fuel level and the
vapour can escape and allow the tank to breathe.
The pressure relief valve fitted in the vent line to the EVAP canister prevents the customer trickle filling the tank.
Trickle filling greatly reduces the vapour space in the tank which in turn affects the tank's ability to breathe properly,
reducing engine performance and safety. When filling the tank, the pressures created are too low to open the pressure
relief valve, preventing the customer from trickle filling the tank. Vapour pressures created during driving are higher
and will open the valve allowing vapour to vent to the EVAP canister.
Four ROV's are welded onto the top surface of the tank. Each ROV is connected by a tube to the main vent line to
the EVAP canister. The ROV's allow fuel vapour to pass through them during normal vehicle operation. In the event
of the vehicle being overturned the valves shut-off, sealing the tank and preventing fuel from spilling from the vent line.
Fuel tank breather system (NAS)
The filler tube incorporates a tank vent which allows air and fuel vapour displaced from the tank when filling to vent to
atmosphere via the filler neck. A filler cap operated valve within the fuel filler neck prevents vapour escaping through
the EVAP canister during filling. This prevents the customer overfilling the tank and maintains the correct fuel cut-off
level.
The filler tube also has an 'L' shaped, stainless steel Liquid Vapour Separator (LVS). During normal driving excess
fuel vapour is passed via the vent line into the EVAP canister. To prevent the canister from being overloaded with fuel
vapour, especially in hot climates, the vapour is given the opportunity to condense in the LVS. Fuel which condenses
in the LVS flows back into the tank via the LVS vent line and through the Roll Over Valves (ROV's).
For NAS vehicles with vacuum type EVAP system leak detection capability, a small tube is located alongside the filler
tube and terminates near to the filler neck. The tube is connected to the On Board Diagnostics (OBD) pressure sensor
in the fuel pump and provides the sensor with a reading of atmospheric pressure to compare against the tank
pressure.
+ EMISSION CONTROL - V8, DESCRIPTION AND OPERATION, Emission Control Systems.
A breather spout within the tank controls the tank 'full' height. When fuel covers the spout it prevents fuel vapour and
air from escaping from the tank. This causes the fuel to 'back-up' in the filler tube and shuts off the filler gun. The
position of the spout ensures that when the filler gun shuts off, a vapour space of approximately 10% of the tanks total
capacity remains. This vapour space ensures that the ROV's are always above the fuel level and the vapour can
escape to the LVS and allow the tank to breathe.