LAND ROVER DISCOVERY 2002 Workshop Manual
Manufacturer: LAND ROVER, Model Year: 2002, Model line: DISCOVERY, Model: LAND ROVER DISCOVERY 2002Pages: 1672, PDF Size: 46.1 MB
Page 571 of 1672
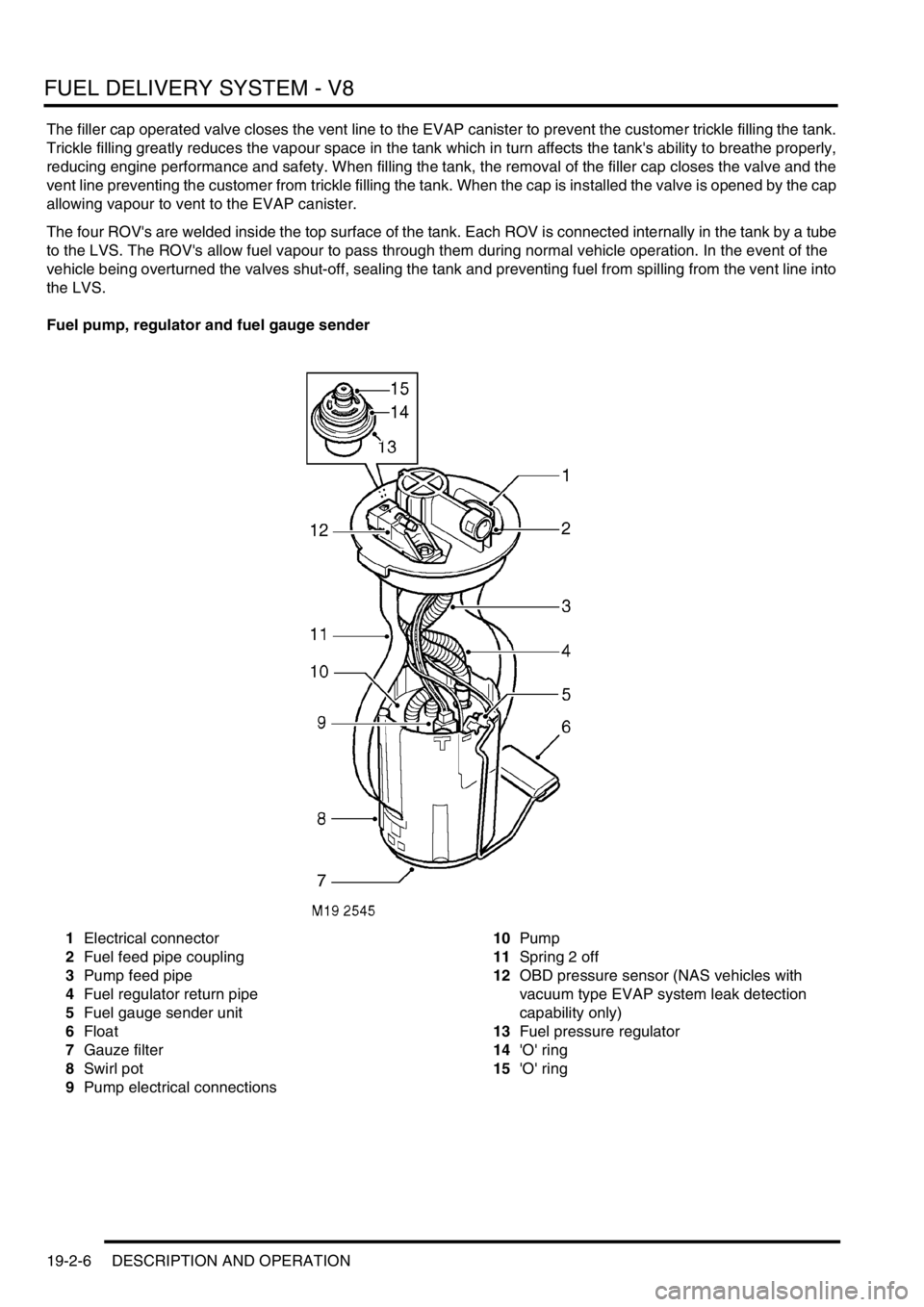
FUEL DELIVERY SYSTEM - V8
19-2-6 DESCRIPTION AND OPERATION
The filler cap operated valve closes the vent line to the EVAP canister to prevent the customer trickle filling the tank.
Trickle filling greatly reduces the vapour space in the tank which in turn affects the tank's ability to breathe properly,
reducing engine performance and safety. When filling the tank, the removal of the filler cap closes the valve and the
vent line preventing the customer from trickle filling the tank. When the cap is installed the valve is opened by the cap
allowing vapour to vent to the EVAP canister.
The four ROV's are welded inside the top surface of the tank. Each ROV is connected internally in the tank by a tube
to the LVS. The ROV's allow fuel vapour to pass through them during normal vehicle operation. In the event of the
vehicle being overturned the valves shut-off, sealing the tank and preventing fuel from spilling from the vent line into
the LVS.
Fuel pump, regulator and fuel gauge sender
1Electrical connector
2Fuel feed pipe coupling
3Pump feed pipe
4Fuel regulator return pipe
5Fuel gauge sender unit
6Float
7Gauze filter
8Swirl pot
9Pump electrical connections10Pump
11Spring 2 off
12OBD pressure sensor (NAS vehicles with
vacuum type EVAP system leak detection
capability only)
13Fuel pressure regulator
14'O' ring
15'O' ring
Page 572 of 1672
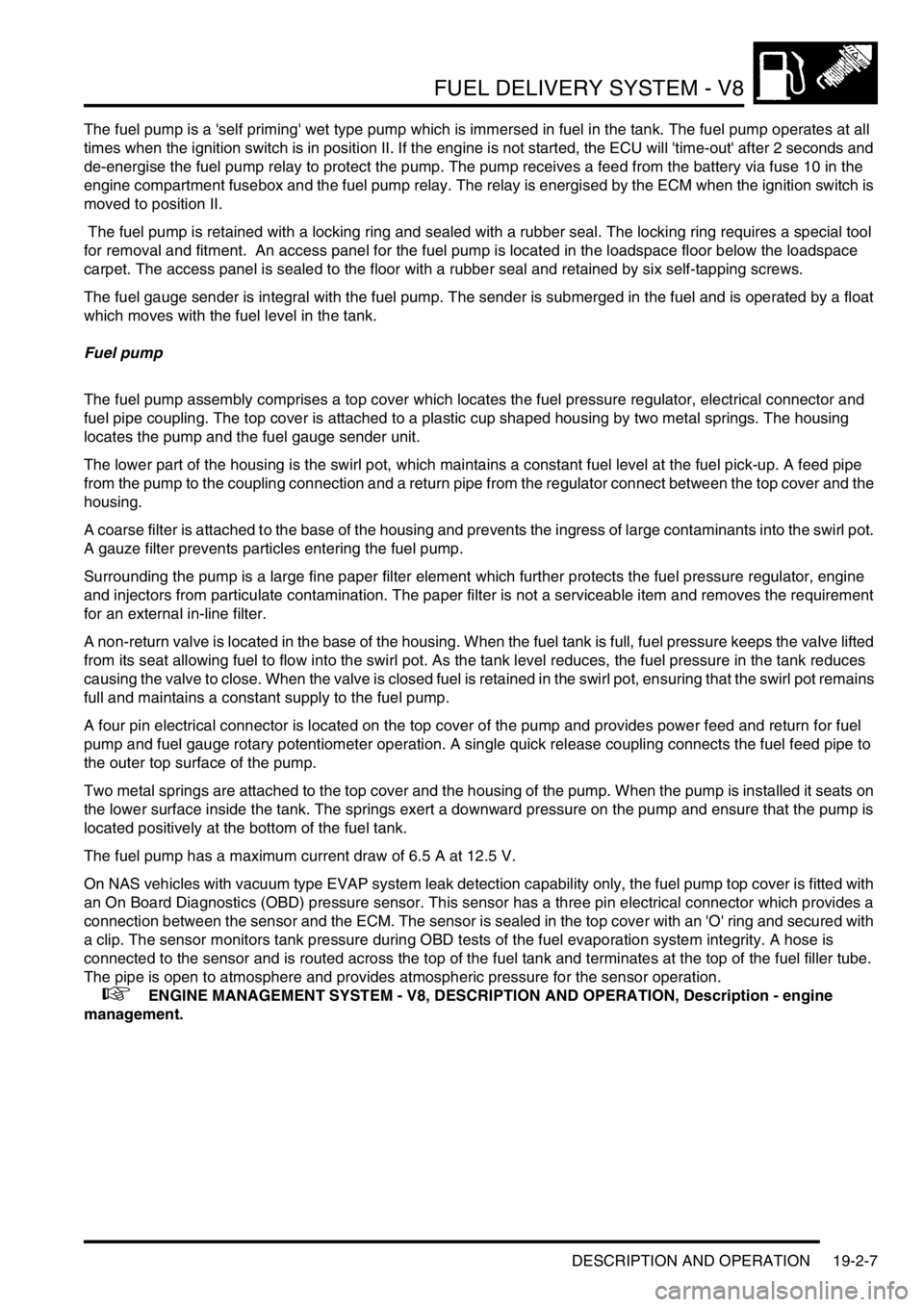
FUEL DELIVERY SYSTEM - V8
DESCRIPTION AND OPERATION 19-2-7
The fuel pump is a 'self priming' wet type pump which is immersed in fuel in the tank. The fuel pump operates at all
times when the ignition switch is in position II. If the engine is not started, the ECU will 'time-out' after 2 seconds and
de-energise the fuel pump relay to protect the pump. The pump receives a feed from the battery via fuse 10 in the
engine compartment fusebox and the fuel pump relay. The relay is energised by the ECM when the ignition switch is
moved to position II.
The fuel pump is retained with a locking ring and sealed with a rubber seal. The locking ring requires a special tool
for removal and fitment. An access panel for the fuel pump is located in the loadspace floor below the loadspace
carpet. The access panel is sealed to the floor with a rubber seal and retained by six self-tapping screws.
The fuel gauge sender is integral with the fuel pump. The sender is submerged in the fuel and is operated by a float
which moves with the fuel level in the tank.
Fuel pump
The fuel pump assembly comprises a top cover which locates the fuel pressure regulator, electrical connector and
fuel pipe coupling. The top cover is attached to a plastic cup shaped housing by two metal springs. The housing
locates the pump and the fuel gauge sender unit.
The lower part of the housing is the swirl pot, which maintains a constant fuel level at the fuel pick-up. A feed pipe
from the pump to the coupling connection and a return pipe from the regulator connect between the top cover and the
housing.
A coarse filter is attached to the base of the housing and prevents the ingress of large contaminants into the swirl pot.
A gauze filter prevents particles entering the fuel pump.
Surrounding the pump is a large fine paper filter element which further protects the fuel pressure regulator, engine
and injectors from particulate contamination. The paper filter is not a serviceable item and removes the requirement
for an external in-line filter.
A non-return valve is located in the base of the housing. When the fuel tank is full, fuel pressure keeps the valve lifted
from its seat allowing fuel to flow into the swirl pot. As the tank level reduces, the fuel pressure in the tank reduces
causing the valve to close. When the valve is closed fuel is retained in the swirl pot, ensuring that the swirl pot remains
full and maintains a constant supply to the fuel pump.
A four pin electrical connector is located on the top cover of the pump and provides power feed and return for fuel
pump and fuel gauge rotary potentiometer operation. A single quick release coupling connects the fuel feed pipe to
the outer top surface of the pump.
Two metal springs are attached to the top cover and the housing of the pump. When the pump is installed it seats on
the lower surface inside the tank. The springs exert a downward pressure on the pump and ensure that the pump is
located positively at the bottom of the fuel tank.
The fuel pump has a maximum current draw of 6.5 A at 12.5 V.
On NAS vehicles with vacuum type EVAP system leak detection capability only, the fuel pump top cover is fitted with
an On Board Diagnostics (OBD) pressure sensor. This sensor has a three pin electrical connector which provides a
connection between the sensor and the ECM. The sensor is sealed in the top cover with an 'O' ring and secured with
a clip. The sensor monitors tank pressure during OBD tests of the fuel evaporation system integrity. A hose is
connected to the sensor and is routed across the top of the fuel tank and terminates at the top of the fuel filler tube.
The pipe is open to atmosphere and provides atmospheric pressure for the sensor operation.
+ ENGINE MANAGEMENT SYSTEM - V8, DESCRIPTION AND OPERATION, Description - engine
management.
Page 573 of 1672
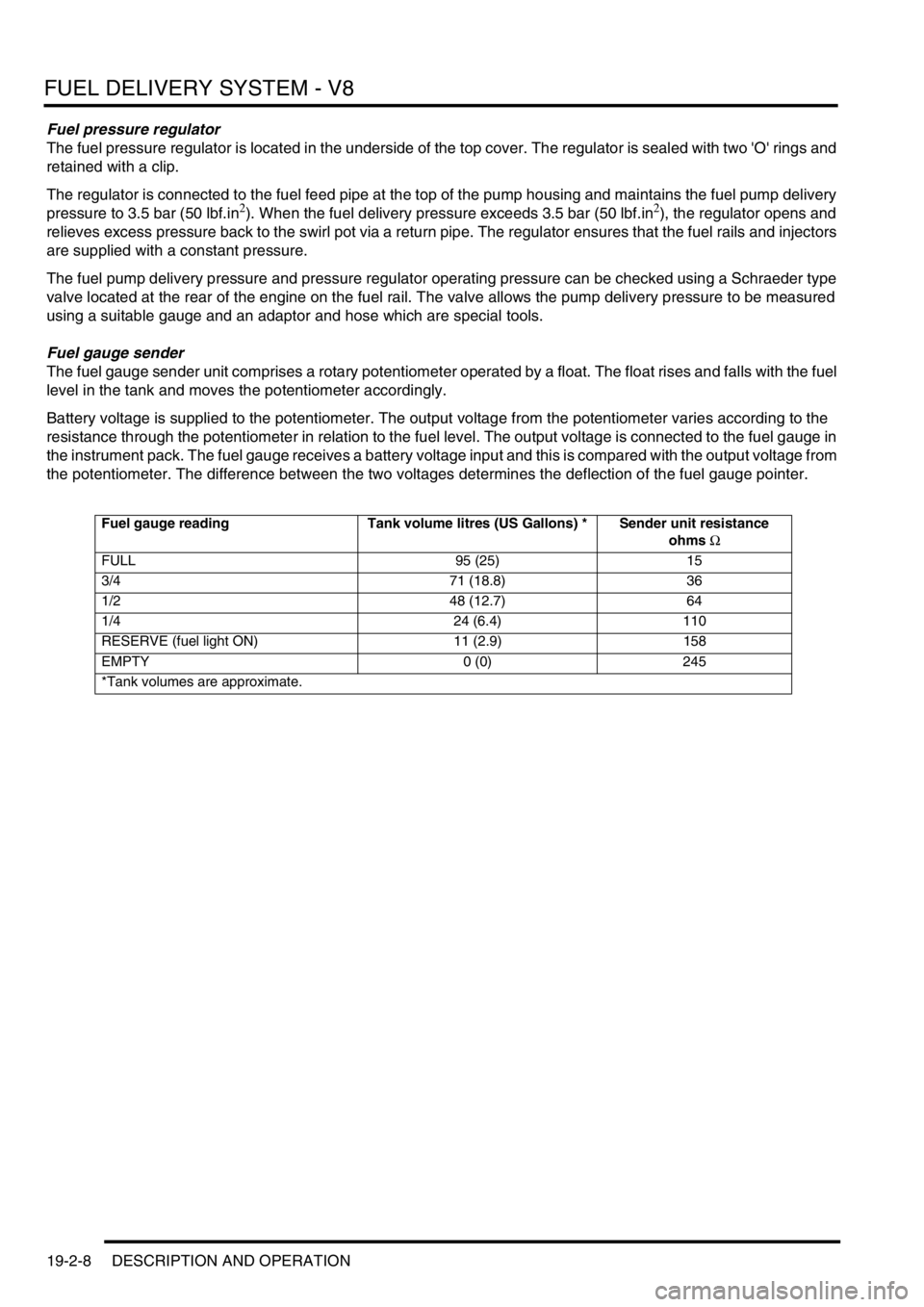
FUEL DELIVERY SYSTEM - V8
19-2-8 DESCRIPTION AND OPERATION
Fuel pressure regulator
The fuel pressure regulator is located in the underside of the top cover. The regulator is sealed with two 'O' rings and
retained with a clip.
The regulator is connected to the fuel feed pipe at the top of the pump housing and maintains the fuel pump delivery
pressure to 3.5 bar (50 lbf.in
2). When the fuel delivery pressure exceeds 3.5 bar (50 lbf.in2), the regulator opens and
relieves excess pressure back to the swirl pot via a return pipe. The regulator ensures that the fuel rails and injectors
are supplied with a constant pressure.
The fuel pump delivery pressure and pressure regulator operating pressure can be checked using a Schraeder type
valve located at the rear of the engine on the fuel rail. The valve allows the pump delivery pressure to be measured
using a suitable gauge and an adaptor and hose which are special tools.
Fuel gauge sender
The fuel gauge sender unit comprises a rotary potentiometer operated by a float. The float rises and falls with the fuel
level in the tank and moves the potentiometer accordingly.
Battery voltage is supplied to the potentiometer. The output voltage from the potentiometer varies according to the
resistance through the potentiometer in relation to the fuel level. The output voltage is connected to the fuel gauge in
the instrument pack. The fuel gauge receives a battery voltage input and this is compared with the output voltage from
the potentiometer. The difference between the two voltages determines the deflection of the fuel gauge pointer.
Fuel gauge reading Tank volume litres (US Gallons) * Sender unit resistance
ohms Ω
FULL 95 (25) 15
3/4 71 (18.8) 36
1/2 48 (12.7) 64
1/4 24 (6.4) 110
RESERVE (fuel light ON) 11 (2.9) 158
EMPTY 0 (0) 245
*Tank volumes are approximate.
Page 574 of 1672
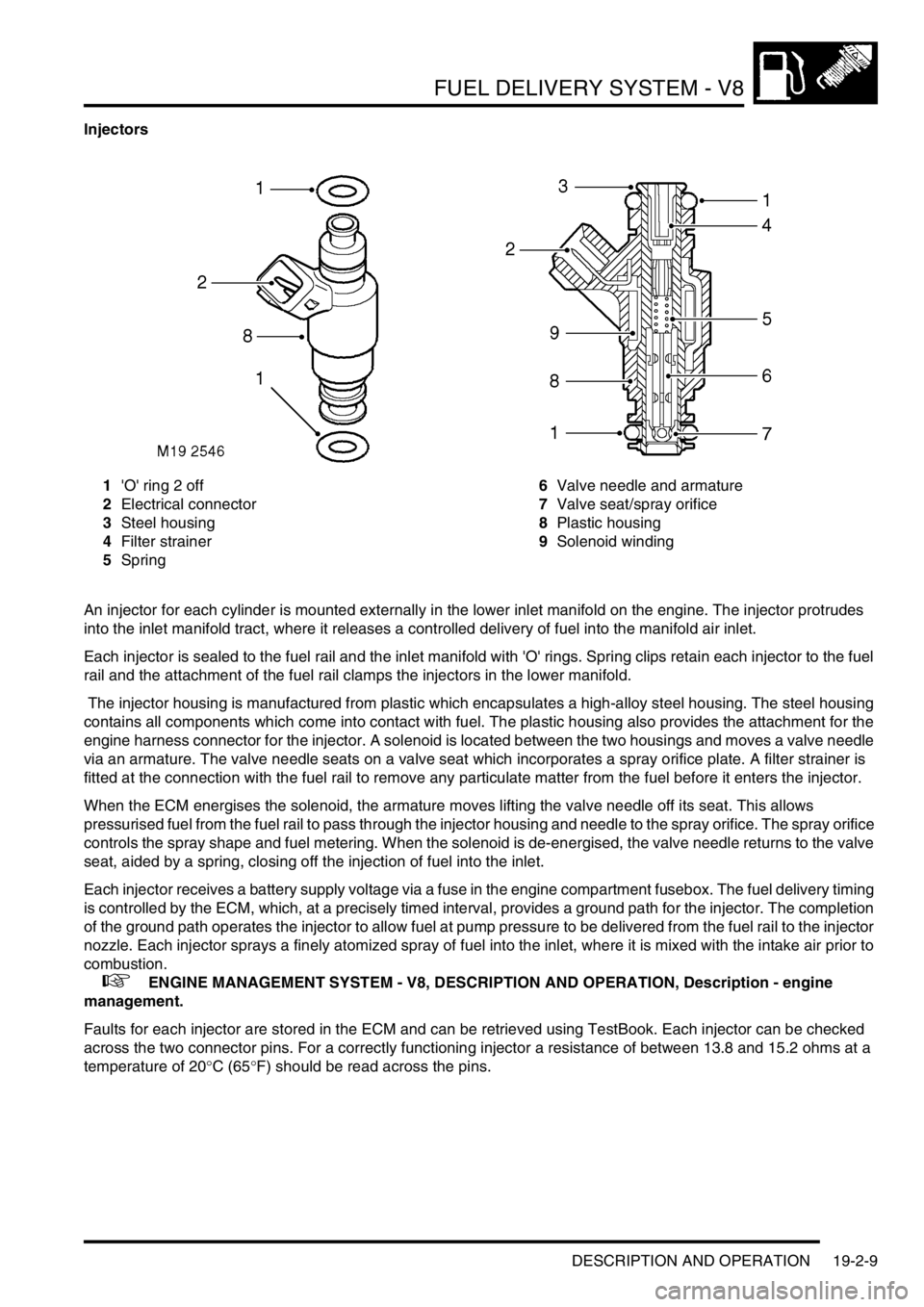
FUEL DELIVERY SYSTEM - V8
DESCRIPTION AND OPERATION 19-2-9
Injectors
1'O' ring 2 off
2Electrical connector
3Steel housing
4Filter strainer
5Spring6Valve needle and armature
7Valve seat/spray orifice
8Plastic housing
9Solenoid winding
An injector for each cylinder is mounted externally in the lower inlet manifold on the engine. The injector protrudes
into the inlet manifold tract, where it releases a controlled delivery of fuel into the manifold air inlet.
Each injector is sealed to the fuel rail and the inlet manifold with 'O' rings. Spring clips retain each injector to the fuel
rail and the attachment of the fuel rail clamps the injectors in the lower manifold.
The injector housing is manufactured from plastic which encapsulates a high-alloy steel housing. The steel housing
contains all components which come into contact with fuel. The plastic housing also provides the attachment for the
engine harness connector for the injector. A solenoid is located between the two housings and moves a valve needle
via an armature. The valve needle seats on a valve seat which incorporates a spray orifice plate. A filter strainer is
fitted at the connection with the fuel rail to remove any particulate matter from the fuel before it enters the injector.
When the ECM energises the solenoid, the armature moves lifting the valve needle off its seat. This allows
pressurised fuel from the fuel rail to pass through the injector housing and needle to the spray orifice. The spray orifice
controls the spray shape and fuel metering. When the solenoid is de-energised, the valve needle returns to the valve
seat, aided by a spring, closing off the injection of fuel into the inlet.
Each injector receives a battery supply voltage via a fuse in the engine compartment fusebox. The fuel delivery timing
is controlled by the ECM, which, at a precisely timed interval, provides a ground path for the injector. The completion
of the ground path operates the injector to allow fuel at pump pressure to be delivered from the fuel rail to the injector
nozzle. Each injector sprays a finely atomized spray of fuel into the inlet, where it is mixed with the intake air prior to
combustion.
+ ENGINE MANAGEMENT SYSTEM - V8, DESCRIPTION AND OPERATION, Description - engine
management.
Faults for each injector are stored in the ECM and can be retrieved using TestBook. Each injector can be checked
across the two connector pins. For a correctly functioning injector a resistance of between 13.8 and 15.2 ohms at a
temperature of 20
°C (65°F) should be read across the pins.
Page 575 of 1672
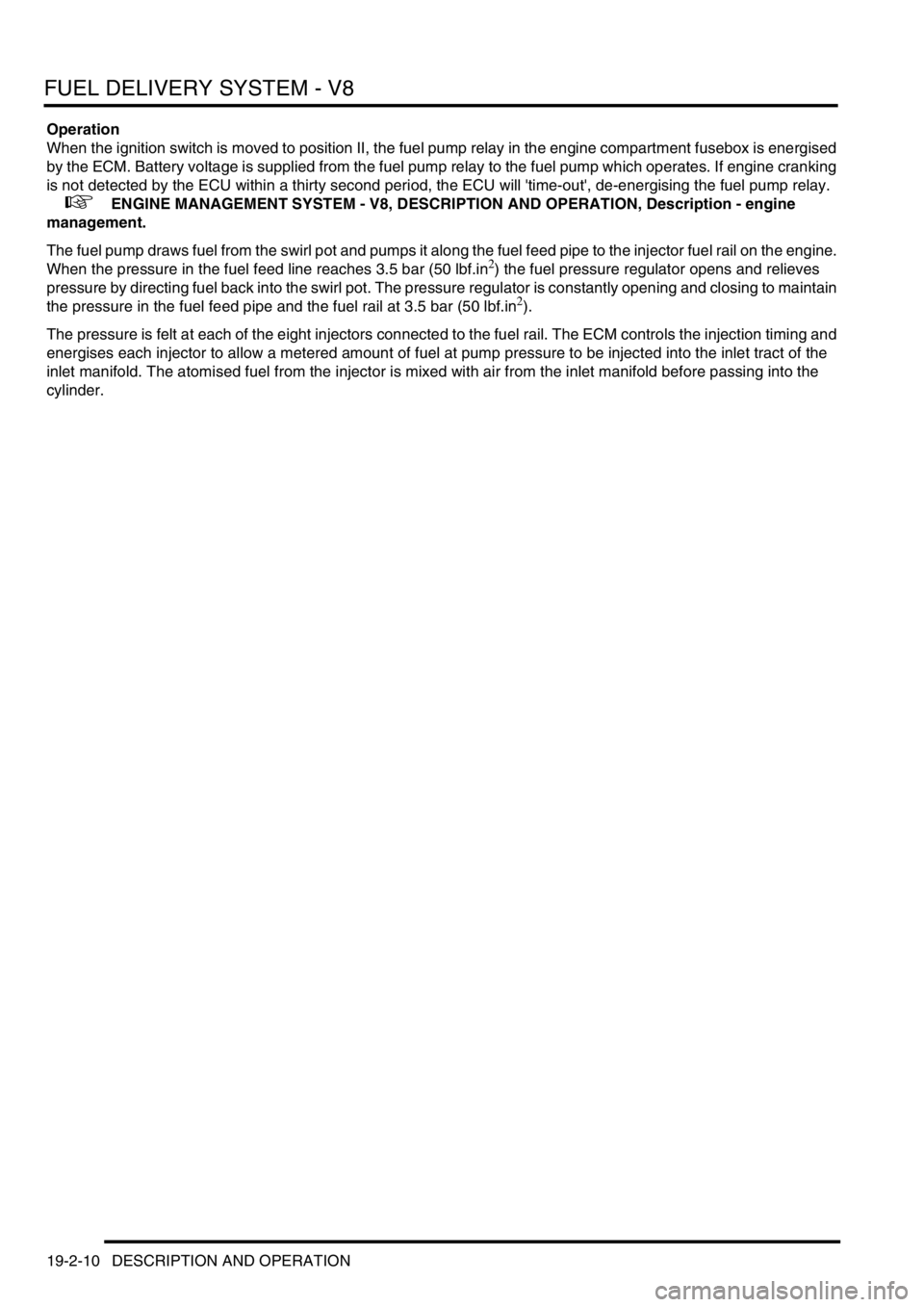
FUEL DELIVERY SYSTEM - V8
19-2-10 DESCRIPTION AND OPERATION
Operation
When the ignition switch is moved to position II, the fuel pump relay in the engine compartment fusebox is energised
by the ECM. Battery voltage is supplied from the fuel pump relay to the fuel pump which operates. If engine cranking
is not detected by the ECU within a thirty second period, the ECU will 'time-out', de-energising the fuel pump relay.
+ ENGINE MANAGEMENT SYSTEM - V8, DESCRIPTION AND OPERATION, Description - engine
management.
The fuel pump draws fuel from the swirl pot and pumps it along the fuel feed pipe to the injector fuel rail on the engine.
When the pressure in the fuel feed line reaches 3.5 bar (50 lbf.in
2) the fuel pressure regulator opens and relieves
pressure by directing fuel back into the swirl pot. The pressure regulator is constantly opening and closing to maintain
the pressure in the fuel feed pipe and the fuel rail at 3.5 bar (50 lbf.in
2).
The pressure is felt at each of the eight injectors connected to the fuel rail. The ECM controls the injection timing and
energises each injector to allow a metered amount of fuel at pump pressure to be injected into the inlet tract of the
inlet manifold. The atomised fuel from the injector is mixed with air from the inlet manifold before passing into the
cylinder.
Page 576 of 1672

FUEL DELIVERY SYSTEM - V8
ADJUSTMENTS 19-2-11
ADJUST ME NTS
Fuel tank - drain
$% 19.55.02
Drain
1.Disconnect both leads from battery.
WARNING: Always disconnect the negative
lead first. Disconnection of the positive lead
while the negative lead is connected could
result in a short circuit through accidental
grounding and cause personal injury.
2.Connect TestBook to vehicle and depressurise
fuel system.
3.Remove fuel pump.
+ FUEL DELIVERY SYSTEM - V8,
REPAIRS, Pump - fuel.
4.Using a fuel recovery appliance, drain the fuel
from the tank into a sealed container. Follow
the manufacturers instructions for the
connection and safe use of the appliance.
Refill
1.Fit fuel pump unit.
+ FUEL DELIVERY SYSTEM - V8,
REPAIRS, Pump - fuel.
2.Refill fuel tank with extracted fuel.
3.Connect battery leads, positive lead first.
Page 577 of 1672
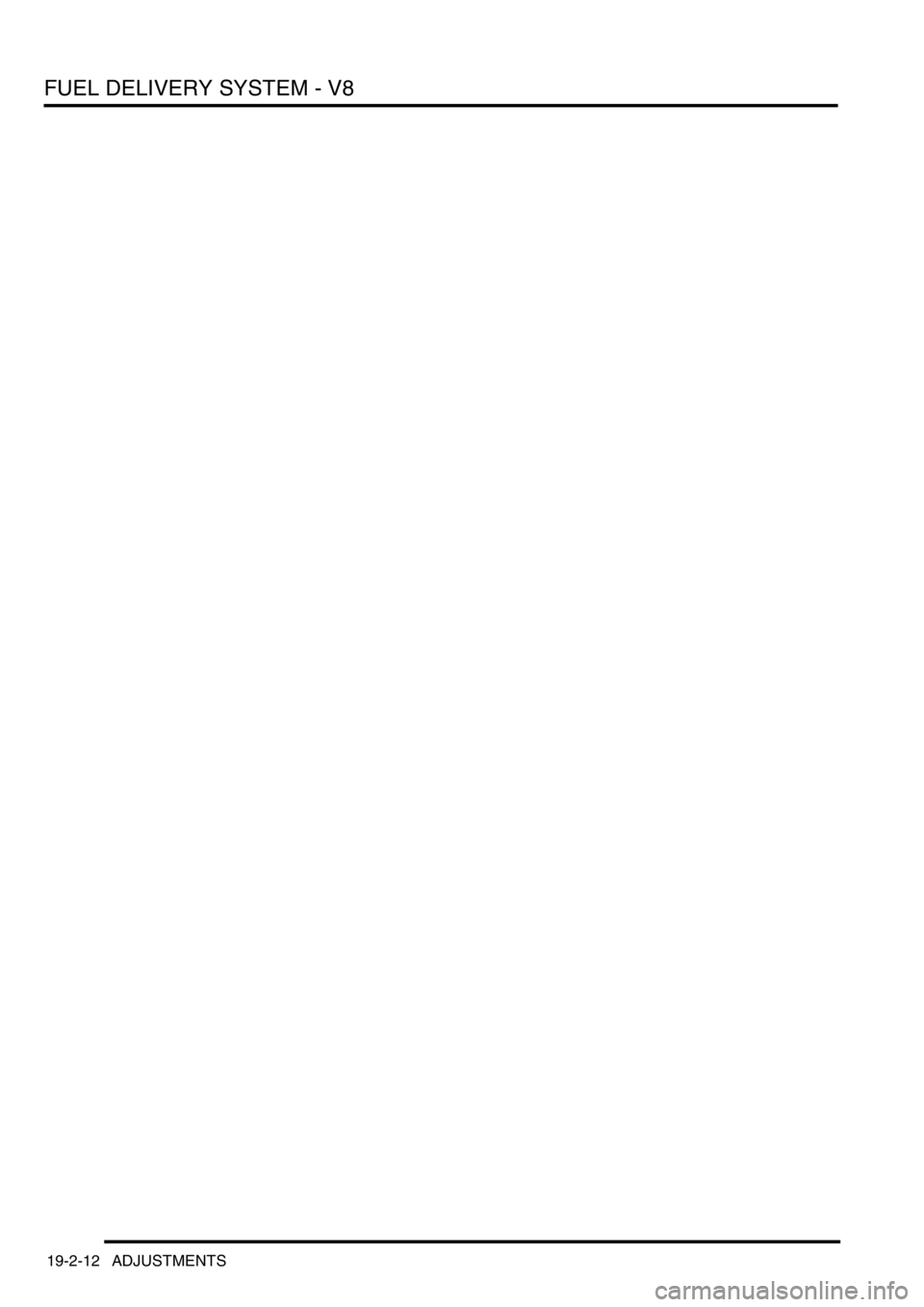
FUEL DELIVERY SYSTEM - V8
19-2-12 ADJUSTMENTS
Page 578 of 1672
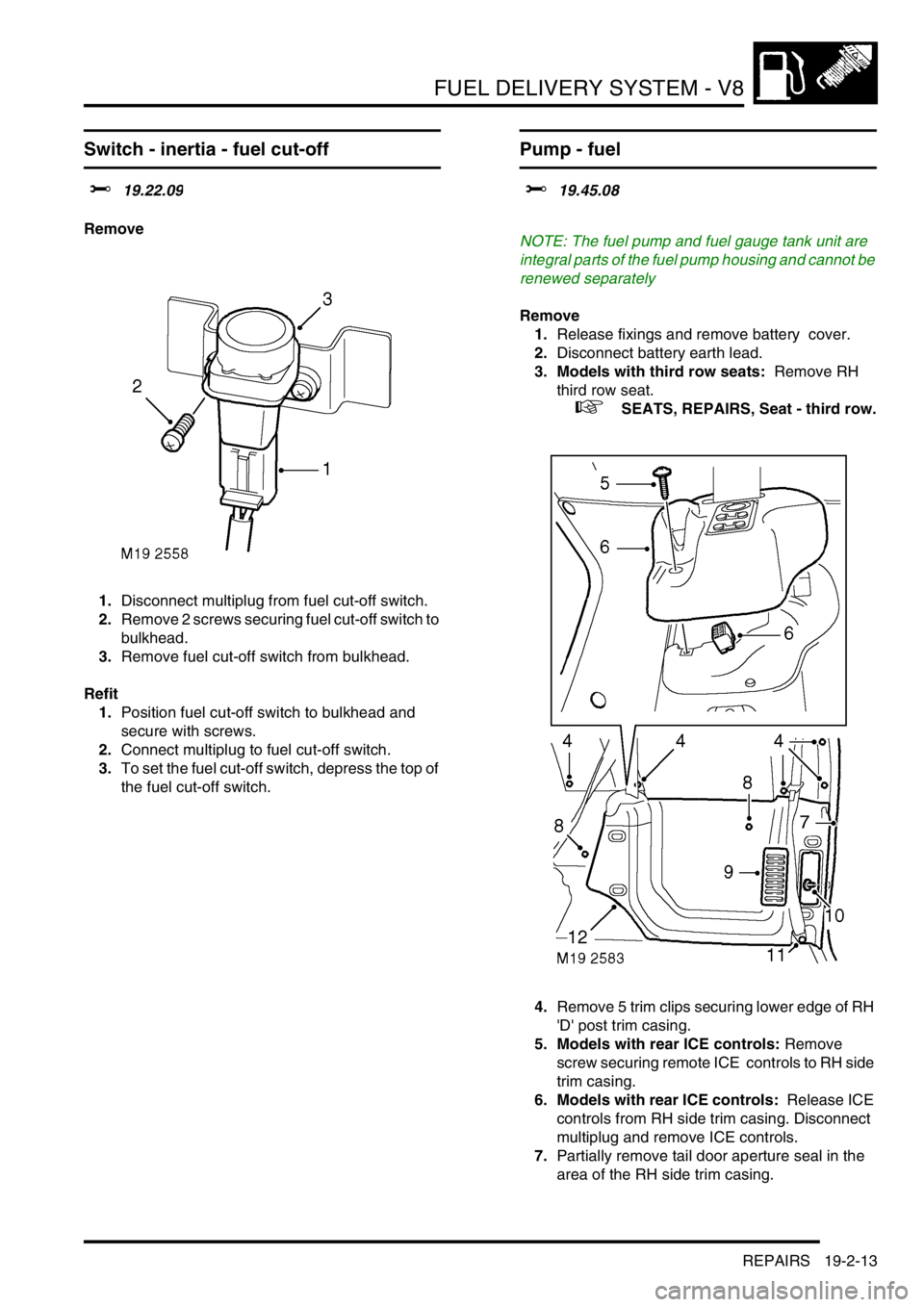
FUEL DELIVERY SYSTEM - V8
REPAIRS 19-2-13
REPAIRS
Switch - inertia - fuel cut-off
$% 19.22.09
Remove
1.Disconnect multiplug from fuel cut-off switch.
2.Remove 2 screws securing fuel cut-off switch to
bulkhead.
3.Remove fuel cut-off switch from bulkhead.
Refit
1.Position fuel cut-off switch to bulkhead and
secure with screws.
2.Connect multiplug to fuel cut-off switch.
3.To set the fuel cut-off switch, depress the top of
the fuel cut-off switch.
Pump - fuel
$% 19.45.08
NOTE: The fuel pump and fuel gauge tank unit are
integral parts of the fuel pump housing and cannot be
renewed separately
Remove
1.Release fixings and remove battery cover.
2.Disconnect battery earth lead.
3. Models with third row seats: Remove RH
third row seat.
+ SEATS, REPAIRS, Seat - third row.
4.Remove 5 trim clips securing lower edge of RH
'D' post trim casing.
5. Models with rear ICE controls: Remove
screw securing remote ICE controls to RH side
trim casing.
6. Models with rear ICE controls: Release ICE
controls from RH side trim casing. Disconnect
multiplug and remove ICE controls.
7.Partially remove tail door aperture seal in the
area of the RH side trim casing.
Page 579 of 1672
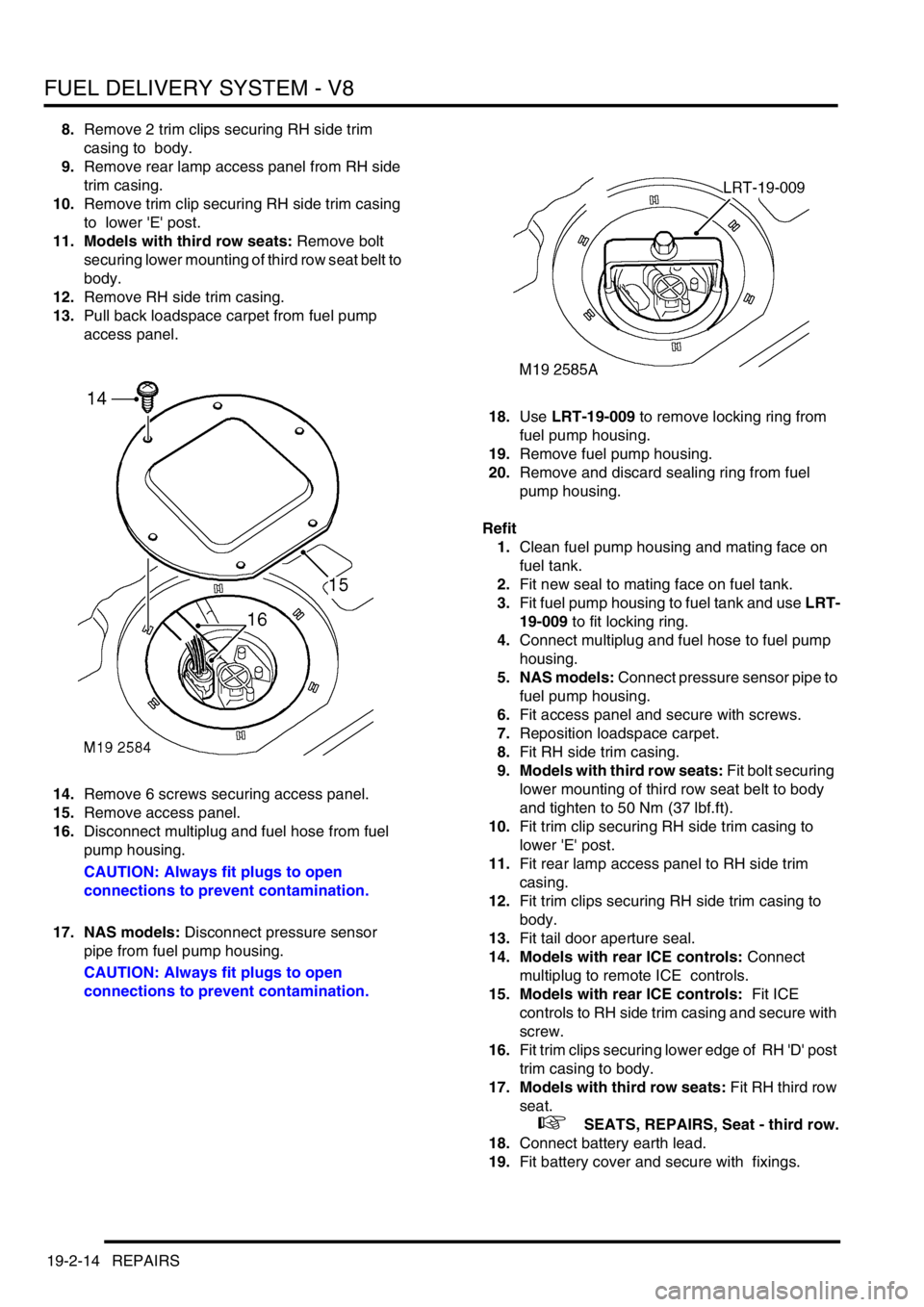
FUEL DELIVERY SYSTEM - V8
19-2-14 REPAIRS
8.Remove 2 trim clips securing RH side trim
casing to body.
9.Remove rear lamp access panel from RH side
trim casing.
10.Remove trim clip securing RH side trim casing
to lower 'E' post.
11. Models with third row seats: Remove bolt
securing lower mounting of third row seat belt to
body.
12.Remove RH side trim casing.
13.Pull back loadspace carpet from fuel pump
access panel.
14.Remove 6 screws securing access panel.
15.Remove access panel.
16.Disconnect multiplug and fuel hose from fuel
pump housing.
CAUTION: Always fit plugs to open
connections to prevent contamination.
17. NAS models: Disconnect pressure sensor
pipe from fuel pump housing.
CAUTION: Always fit plugs to open
connections to prevent contamination.18.Use LRT-19-009 to remove locking ring from
fuel pump housing.
19.Remove fuel pump housing.
20.Remove and discard sealing ring from fuel
pump housing.
Refit
1.Clean fuel pump housing and mating face on
fuel tank.
2.Fit new seal to mating face on fuel tank.
3.Fit fuel pump housing to fuel tank and use LRT-
19-009 to fit locking ring.
4.Connect multiplug and fuel hose to fuel pump
housing.
5. NAS models: Connect pressure sensor pipe to
fuel pump housing.
6.Fit access panel and secure with screws.
7.Reposition loadspace carpet.
8.Fit RH side trim casing.
9. Models with third row seats: Fit bolt securing
lower mounting of third row seat belt to body
and tighten to 50 Nm (37 lbf.ft).
10.Fit trim clip securing RH side trim casing to
lower 'E' post.
11.Fit rear lamp access panel to RH side trim
casing.
12.Fit trim clips securing RH side trim casing to
body.
13.Fit tail door aperture seal.
14. Models with rear ICE controls: Connect
multiplug to remote ICE controls.
15. Models with rear ICE controls: Fit ICE
controls to RH side trim casing and secure with
screw.
16.Fit trim clips securing lower edge of RH 'D' post
trim casing to body.
17. Models with third row seats: Fit RH third row
seat.
+ SEATS, REPAIRS, Seat - third row.
18.Connect battery earth lead.
19.Fit battery cover and secure with fixings.
Page 580 of 1672
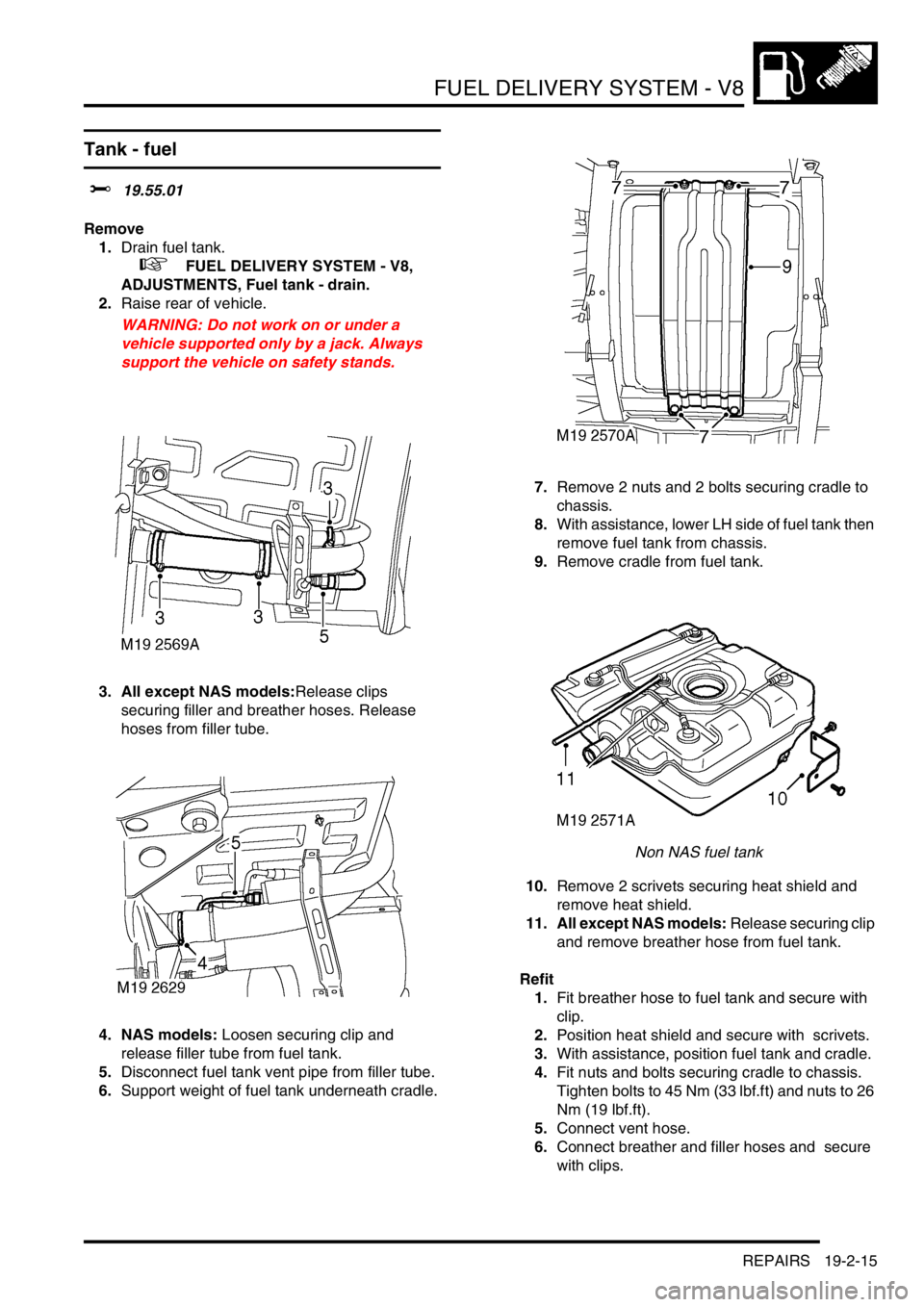
FUEL DELIVERY SYSTEM - V8
REPAIRS 19-2-15
Tank - fuel
$% 19.55.01
Remove
1.Drain fuel tank.
+ FUEL DELIVERY SYSTEM - V8,
ADJUSTMENTS, Fuel tank - drain.
2.Raise rear of vehicle.
WARNING: Do not work on or under a
vehicle supported only by a jack. Always
support the vehicle on safety stands.
3. All except NAS models:Release clips
securing filler and breather hoses. Release
hoses from filler tube.
4. NAS models: Loosen securing clip and
release filler tube from fuel tank.
5.Disconnect fuel tank vent pipe from filler tube.
6.Support weight of fuel tank underneath cradle. 7.Remove 2 nuts and 2 bolts securing cradle to
chassis.
8.With assistance, lower LH side of fuel tank then
remove fuel tank from chassis.
9.Remove cradle from fuel tank.
Non NAS fuel tank
10.Remove 2 scrivets securing heat shield and
remove heat shield.
11. All except NAS models: Release securing clip
and remove breather hose from fuel tank.
Refit
1.Fit breather hose to fuel tank and secure with
clip.
2.Position heat shield and secure with scrivets.
3.With assistance, position fuel tank and cradle.
4.Fit nuts and bolts securing cradle to chassis.
Tighten bolts to 45 Nm (33 lbf.ft) and nuts to 26
Nm (19 lbf.ft).
5.Connect vent hose.
6.Connect breather and filler hoses and secure
with clips.