LAND ROVER DISCOVERY 2002 Workshop Manual
Manufacturer: LAND ROVER, Model Year: 2002, Model line: DISCOVERY, Model: LAND ROVER DISCOVERY 2002Pages: 1672, PDF Size: 46.1 MB
Page 551 of 1672
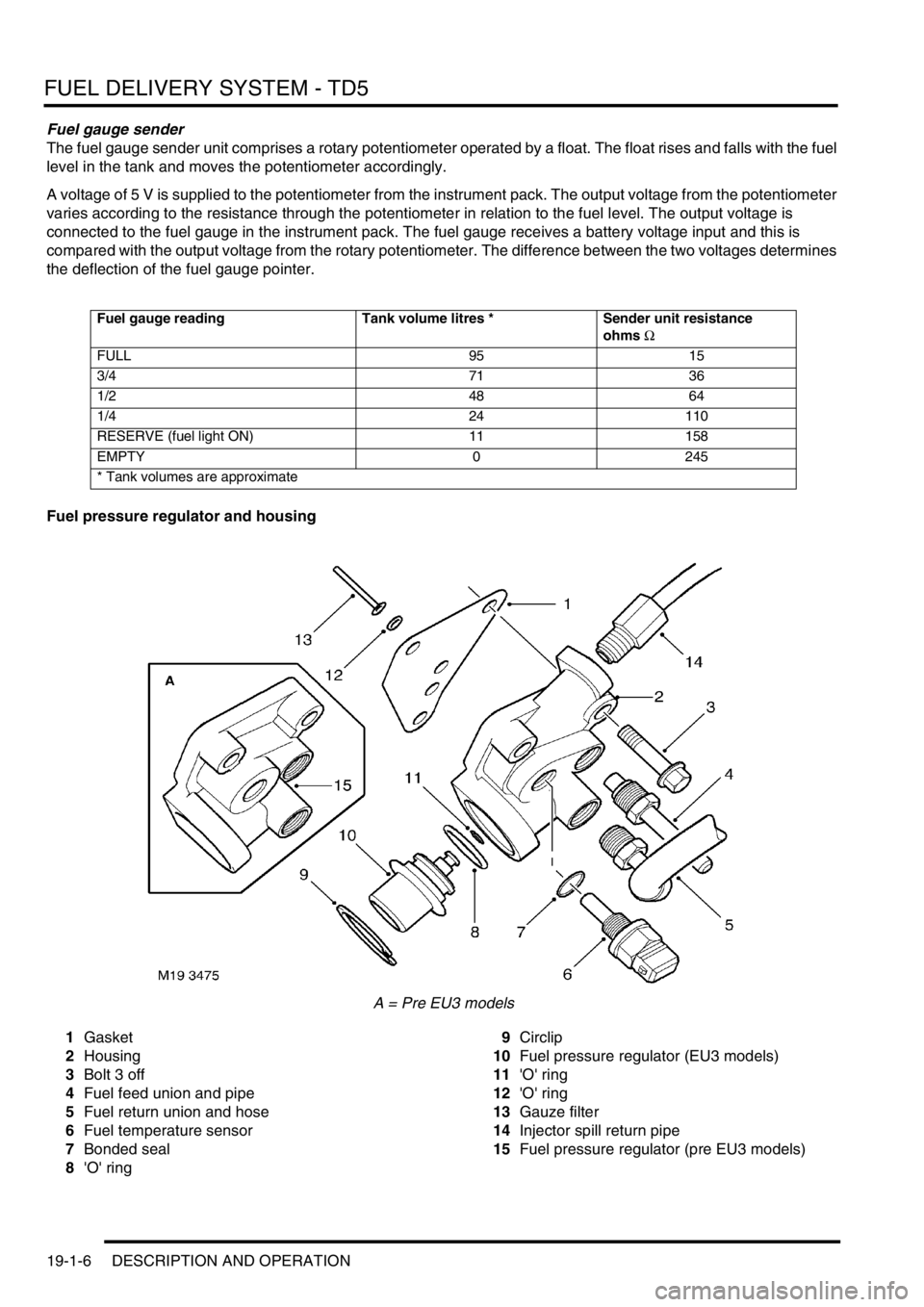
FUEL DELIVERY SYSTEM - TD5
19-1-6 DESCRIPTION AND OPERATION
Fuel gauge sender
The fuel gauge sender unit comprises a rotary potentiometer operated by a float. The float rises and falls with the fuel
level in the tank and moves the potentiometer accordingly.
A voltage of 5 V is supplied to the potentiometer from the instrument pack. The output voltage from the potentiometer
varies according to the resistance through the potentiometer in relation to the fuel level. The output voltage is
connected to the fuel gauge in the instrument pack. The fuel gauge receives a battery voltage input and this is
compared with the output voltage from the rotary potentiometer. The difference between the two voltages determines
the deflection of the fuel gauge pointer.
Fuel pressure regulator and housing
A = Pre EU3 models
1Gasket
2Housing
3Bolt 3 off
4Fuel feed union and pipe
5Fuel return union and hose
6Fuel temperature sensor
7Bonded seal
8'O' ring9Circlip
10Fuel pressure regulator (EU3 models)
11'O' ring
12'O' ring
13Gauze filter
14Injector spill return pipe
15Fuel pressure regulator (pre EU3 models)
Fuel gauge reading Tank volume litres * Sender unit resistance
ohms Ω
FULL 95 15
3/4 71 36
1/2 48 64
1/4 24 110
RESERVE (fuel light ON) 11 158
EMPTY 0 245
* Tank volumes are approximate
Page 552 of 1672
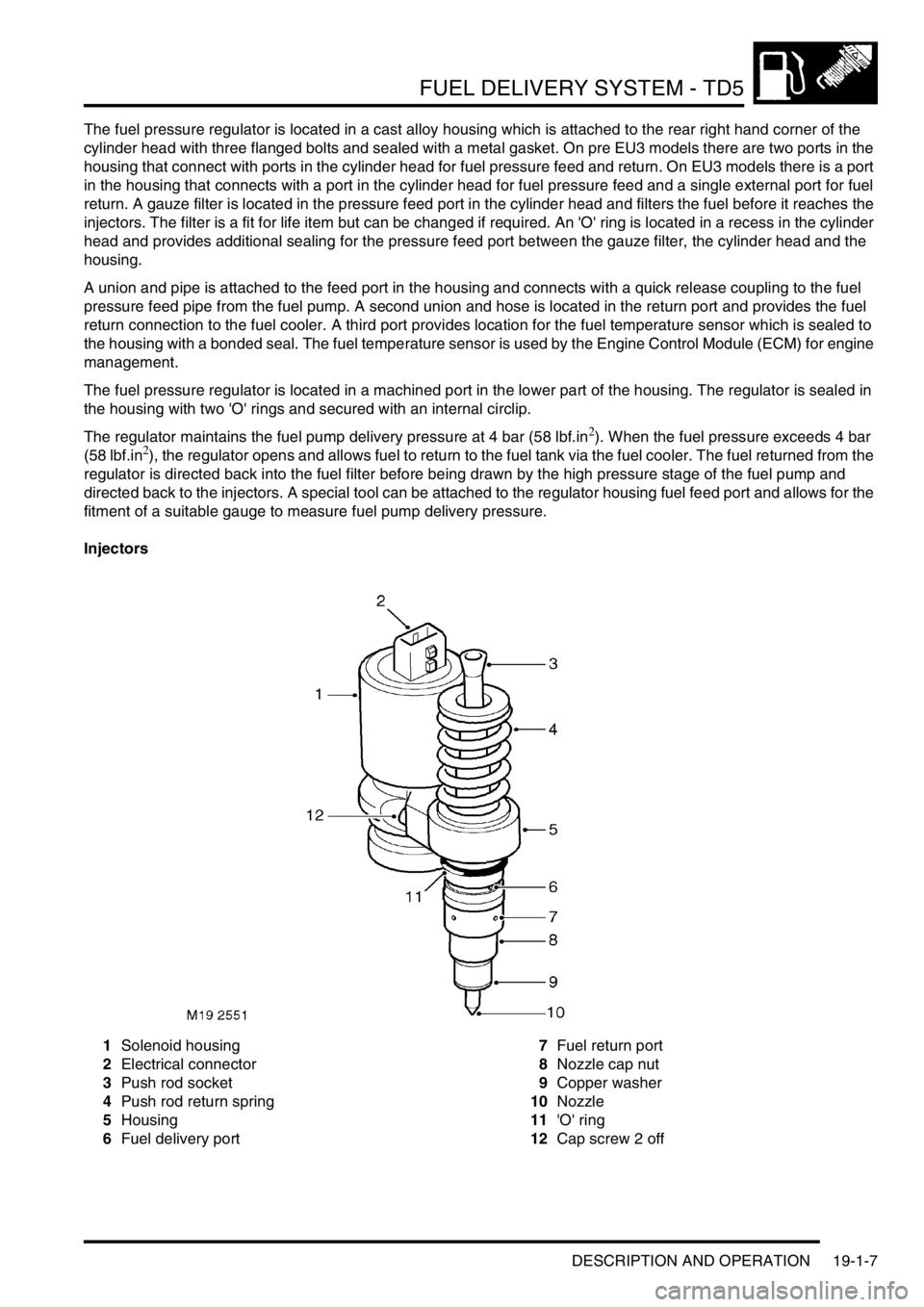
FUEL DELIVERY SYSTEM - TD5
DESCRIPTION AND OPERATION 19-1-7
The fuel pressure regulator is located in a cast alloy housing which is attached to the rear right hand corner of the
cylinder head with three flanged bolts and sealed with a metal gasket. On pre EU3 models there are two ports in the
housing that connect with ports in the cylinder head for fuel pressure feed and return. On EU3 models there is a port
in the housing that connects with a port in the cylinder head for fuel pressure feed and a single external port for fuel
return. A gauze filter is located in the pressure feed port in the cylinder head and filters the fuel before it reaches the
injectors. The filter is a fit for life item but can be changed if required. An 'O' ring is located in a recess in the cylinder
head and provides additional sealing for the pressure feed port between the gauze filter, the cylinder head and the
housing.
A union and pipe is attached to the feed port in the housing and connects with a quick release coupling to the fuel
pressure feed pipe from the fuel pump. A second union and hose is located in the return port and provides the fuel
return connection to the fuel cooler. A third port provides location for the fuel temperature sensor which is sealed to
the housing with a bonded seal. The fuel temperature sensor is used by the Engine Control Module (ECM) for engine
management.
The fuel pressure regulator is located in a machined port in the lower part of the housing. The regulator is sealed in
the housing with two 'O' rings and secured with an internal circlip.
The regulator maintains the fuel pump delivery pressure at 4 bar (58 lbf.in
2). When the fuel pressure exceeds 4 bar
(58 lbf.in2), the regulator opens and allows fuel to return to the fuel tank via the fuel cooler. The fuel returned from the
regulator is directed back into the fuel filter before being drawn by the high pressure stage of the fuel pump and
directed back to the injectors. A special tool can be attached to the regulator housing fuel feed port and allows for the
fitment of a suitable gauge to measure fuel pump delivery pressure.
Injectors
1Solenoid housing
2Electrical connector
3Push rod socket
4Push rod return spring
5Housing
6Fuel delivery port7Fuel return port
8Nozzle cap nut
9Copper washer
10Nozzle
11'O' ring
12Cap screw 2 off
Page 553 of 1672
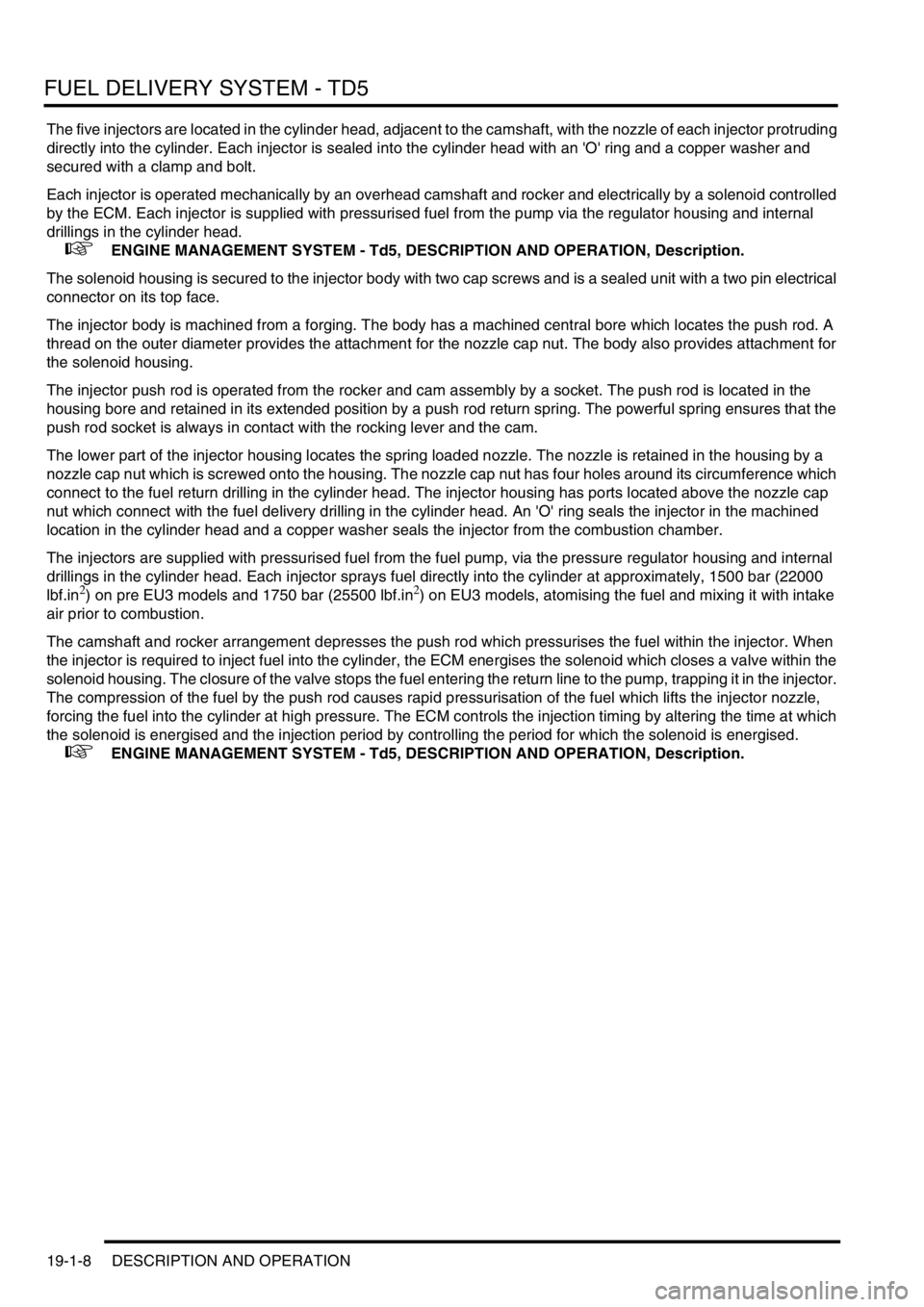
FUEL DELIVERY SYSTEM - TD5
19-1-8 DESCRIPTION AND OPERATION
The five injectors are located in the cylinder head, adjacent to the camshaft, with the nozzle of each injector protruding
directly into the cylinder. Each injector is sealed into the cylinder head with an 'O' ring and a copper washer and
secured with a clamp and bolt.
Each injector is operated mechanically by an overhead camshaft and rocker and electrically by a solenoid controlled
by the ECM. Each injector is supplied with pressurised fuel from the pump via the regulator housing and internal
drillings in the cylinder head.
+ ENGINE MANAGEMENT SYSTEM - Td5, DESCRIPTION AND OPERATION, Description.
The solenoid housing is secured to the injector body with two cap screws and is a sealed unit with a two pin electrical
connector on its top face.
The injector body is machined from a forging. The body has a machined central bore which locates the push rod. A
thread on the outer diameter provides the attachment for the nozzle cap nut. The body also provides attachment for
the solenoid housing.
The injector push rod is operated from the rocker and cam assembly by a socket. The push rod is located in the
housing bore and retained in its extended position by a push rod return spring. The powerful spring ensures that the
push rod socket is always in contact with the rocking lever and the cam.
The lower part of the injector housing locates the spring loaded nozzle. The nozzle is retained in the housing by a
nozzle cap nut which is screwed onto the housing. The nozzle cap nut has four holes around its circumference which
connect to the fuel return drilling in the cylinder head. The injector housing has ports located above the nozzle cap
nut which connect with the fuel delivery drilling in the cylinder head. An 'O' ring seals the injector in the machined
location in the cylinder head and a copper washer seals the injector from the combustion chamber.
The injectors are supplied with pressurised fuel from the fuel pump, via the pressure regulator housing and internal
drillings in the cylinder head. Each injector sprays fuel directly into the cylinder at approximately, 1500 bar (22000
lbf.in
2) on pre EU3 models and 1750 bar (25500 lbf.in2) on EU3 models, atomising the fuel and mixing it with intake
air prior to combustion.
The camshaft and rocker arrangement depresses the push rod which pressurises the fuel within the injector. When
the injector is required to inject fuel into the cylinder, the ECM energises the solenoid which closes a valve within the
solenoid housing. The closure of the valve stops the fuel entering the return line to the pump, trapping it in the injector.
The compression of the fuel by the push rod causes rapid pressurisation of the fuel which lifts the injector nozzle,
forcing the fuel into the cylinder at high pressure. The ECM controls the injection timing by altering the time at which
the solenoid is energised and the injection period by controlling the period for which the solenoid is energised.
+ ENGINE MANAGEMENT SYSTEM - Td5, DESCRIPTION AND OPERATION, Description.
Page 554 of 1672
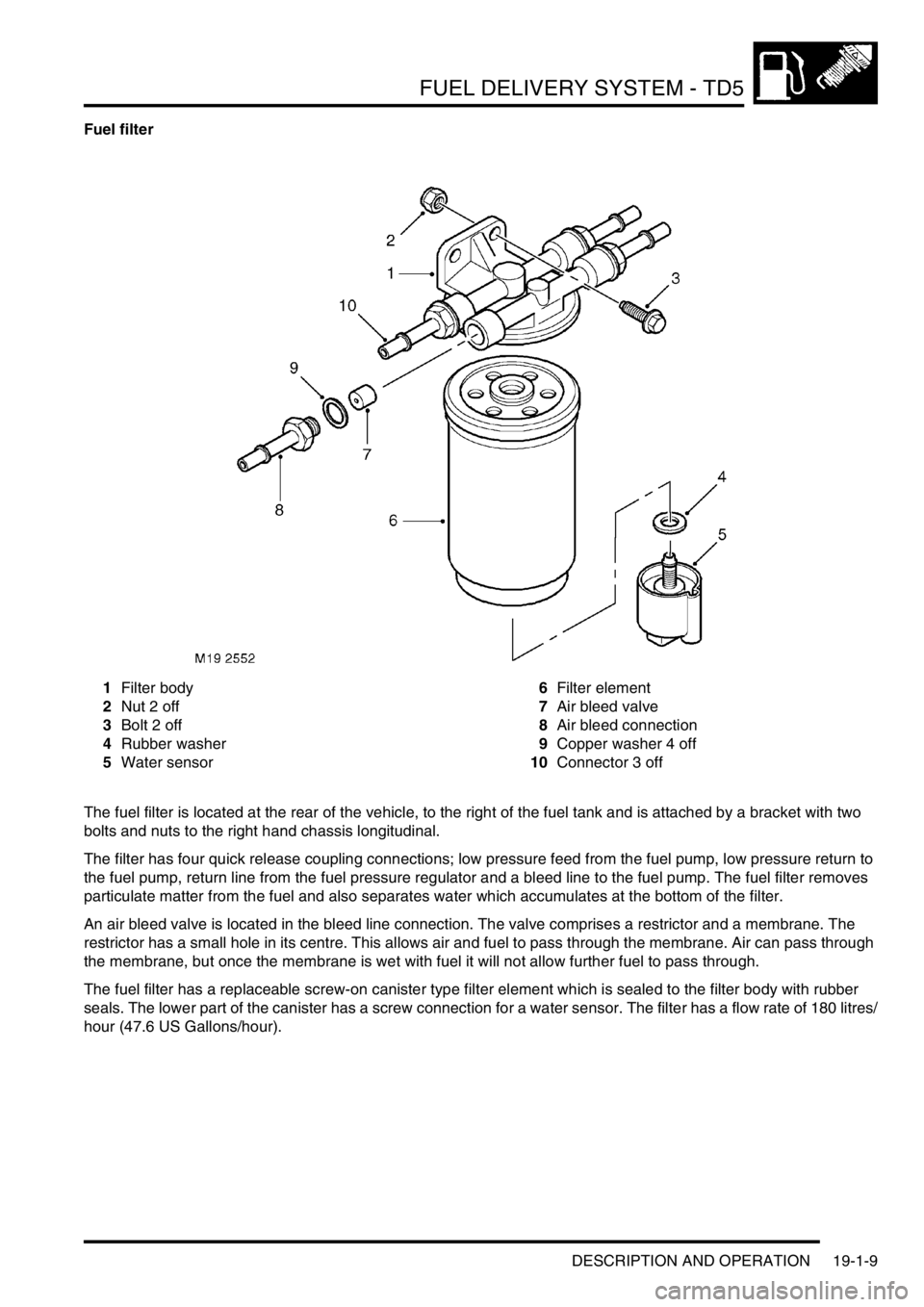
FUEL DELIVERY SYSTEM - TD5
DESCRIPTION AND OPERATION 19-1-9
Fuel filter
1Filter body
2Nut 2 off
3Bolt 2 off
4Rubber washer
5Water sensor6Filter element
7Air bleed valve
8Air bleed connection
9Copper washer 4 off
10Connector 3 off
The fuel filter is located at the rear of the vehicle, to the right of the fuel tank and is attached by a bracket with two
bolts and nuts to the right hand chassis longitudinal.
The filter has four quick release coupling connections; low pressure feed from the fuel pump, low pressure return to
the fuel pump, return line from the fuel pressure regulator and a bleed line to the fuel pump. The fuel filter removes
particulate matter from the fuel and also separates water which accumulates at the bottom of the filter.
An air bleed valve is located in the bleed line connection. The valve comprises a restrictor and a membrane. The
restrictor has a small hole in its centre. This allows air and fuel to pass through the membrane. Air can pass through
the membrane, but once the membrane is wet with fuel it will not allow further fuel to pass through.
The fuel filter has a replaceable screw-on canister type filter element which is sealed to the filter body with rubber
seals. The lower part of the canister has a screw connection for a water sensor. The filter has a flow rate of 180 litres/
hour (47.6 US Gallons/hour).
Page 555 of 1672
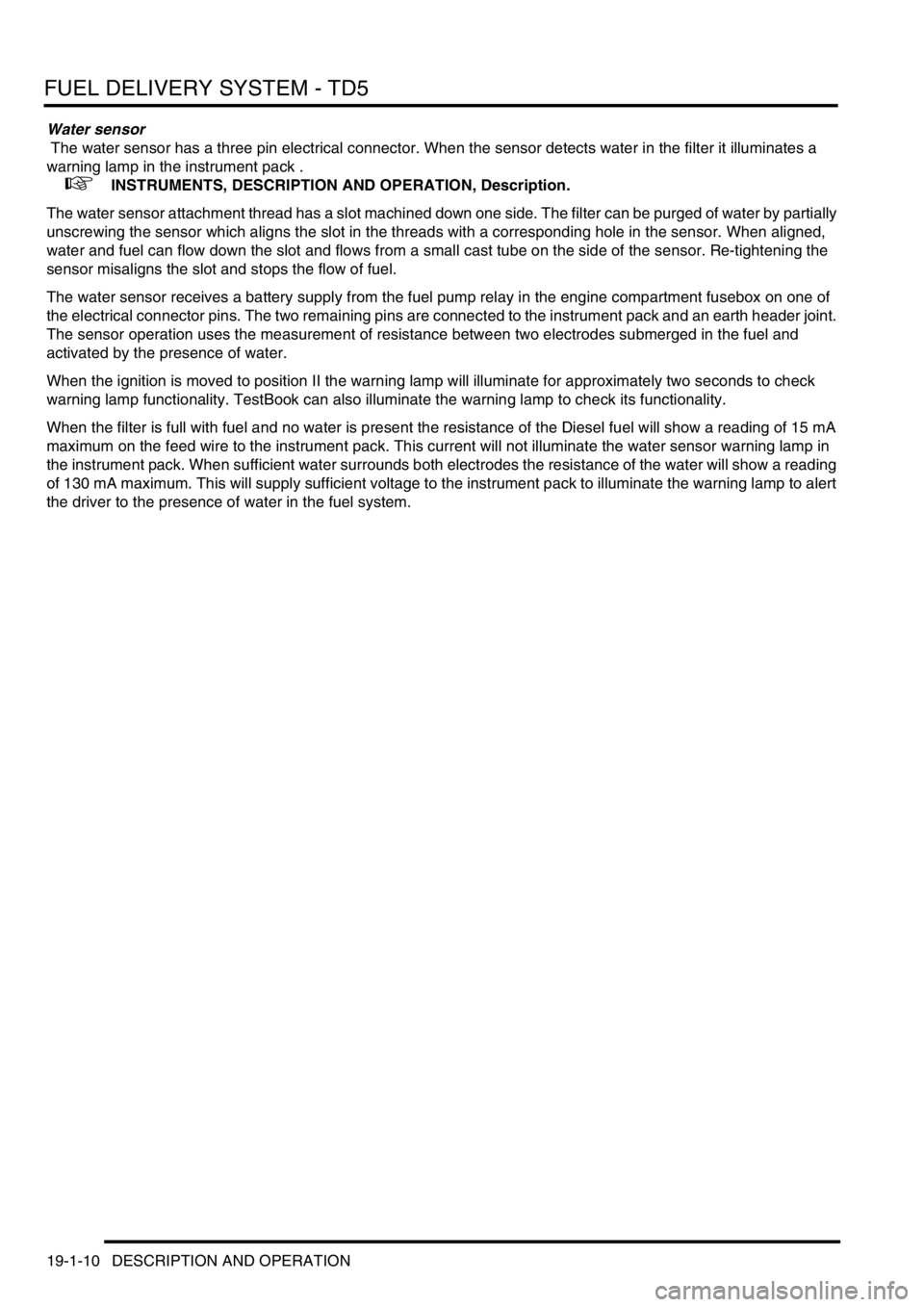
FUEL DELIVERY SYSTEM - TD5
19-1-10 DESCRIPTION AND OPERATION
Water sensor
The water sensor has a three pin electrical connector. When the sensor detects water in the filter it illuminates a
warning lamp in the instrument pack .
+ INSTRUMENTS, DESCRIPTION AND OPERATION, Description.
The water sensor attachment thread has a slot machined down one side. The filter can be purged of water by partially
unscrewing the sensor which aligns the slot in the threads with a corresponding hole in the sensor. When aligned,
water and fuel can flow down the slot and flows from a small cast tube on the side of the sensor. Re-tightening the
sensor misaligns the slot and stops the flow of fuel.
The water sensor receives a battery supply from the fuel pump relay in the engine compartment fusebox on one of
the electrical connector pins. The two remaining pins are connected to the instrument pack and an earth header joint.
The sensor operation uses the measurement of resistance between two electrodes submerged in the fuel and
activated by the presence of water.
When the ignition is moved to position II the warning lamp will illuminate for approximately two seconds to check
warning lamp functionality. TestBook can also illuminate the warning lamp to check its functionality.
When the filter is full with fuel and no water is present the resistance of the Diesel fuel will show a reading of 15 mA
maximum on the feed wire to the instrument pack. This current will not illuminate the water sensor warning lamp in
the instrument pack. When sufficient water surrounds both electrodes the resistance of the water will show a reading
of 130 mA maximum. This will supply sufficient voltage to the instrument pack to illuminate the warning lamp to alert
the driver to the presence of water in the fuel system.
Page 556 of 1672
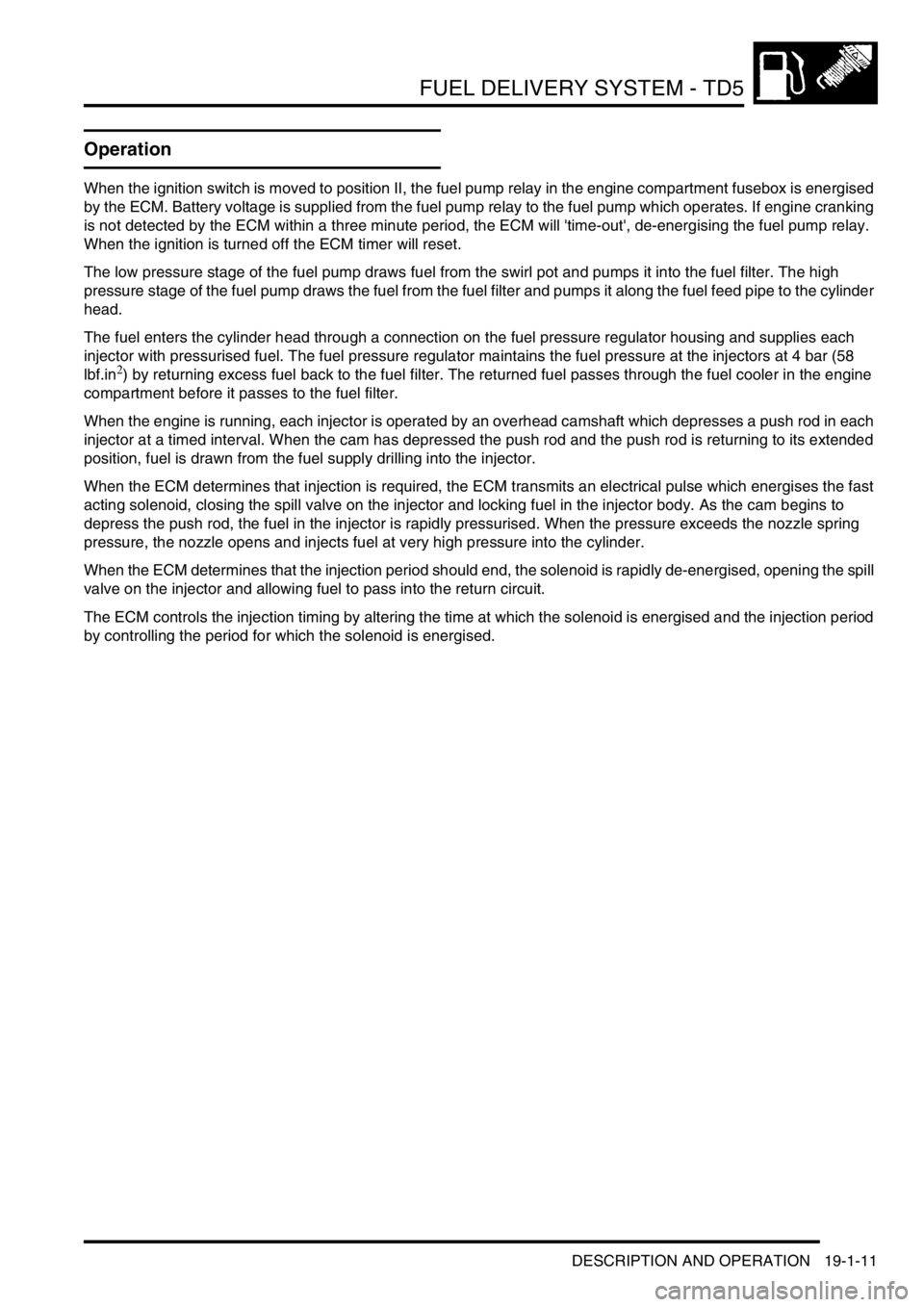
FUEL DELIVERY SYSTEM - TD5
DESCRIPTION AND OPERATION 19-1-11
Operation
When the ignition switch is moved to position II, the fuel pump relay in the engine compartment fusebox is energised
by the ECM. Battery voltage is supplied from the fuel pump relay to the fuel pump which operates. If engine cranking
is not detected by the ECM within a three minute period, the ECM will 'time-out', de-energising the fuel pump relay.
When the ignition is turned off the ECM timer will reset.
The low pressure stage of the fuel pump draws fuel from the swirl pot and pumps it into the fuel filter. The high
pressure stage of the fuel pump draws the fuel from the fuel filter and pumps it along the fuel feed pipe to the cylinder
head.
The fuel enters the cylinder head through a connection on the fuel pressure regulator housing and supplies each
injector with pressurised fuel. The fuel pressure regulator maintains the fuel pressure at the injectors at 4 bar (58
lbf.in
2) by returning excess fuel back to the fuel filter. The returned fuel passes through the fuel cooler in the engine
compartment before it passes to the fuel filter.
When the engine is running, each injector is operated by an overhead camshaft which depresses a push rod in each
injector at a timed interval. When the cam has depressed the push rod and the push rod is returning to its extended
position, fuel is drawn from the fuel supply drilling into the injector.
When the ECM determines that injection is required, the ECM transmits an electrical pulse which energises the fast
acting solenoid, closing the spill valve on the injector and locking fuel in the injector body. As the cam begins to
depress the push rod, the fuel in the injector is rapidly pressurised. When the pressure exceeds the nozzle spring
pressure, the nozzle opens and injects fuel at very high pressure into the cylinder.
When the ECM determines that the injection period should end, the solenoid is rapidly de-energised, opening the spill
valve on the injector and allowing fuel to pass into the return circuit.
The ECM controls the injection timing by altering the time at which the solenoid is energised and the injection period
by controlling the period for which the solenoid is energised.
Page 557 of 1672
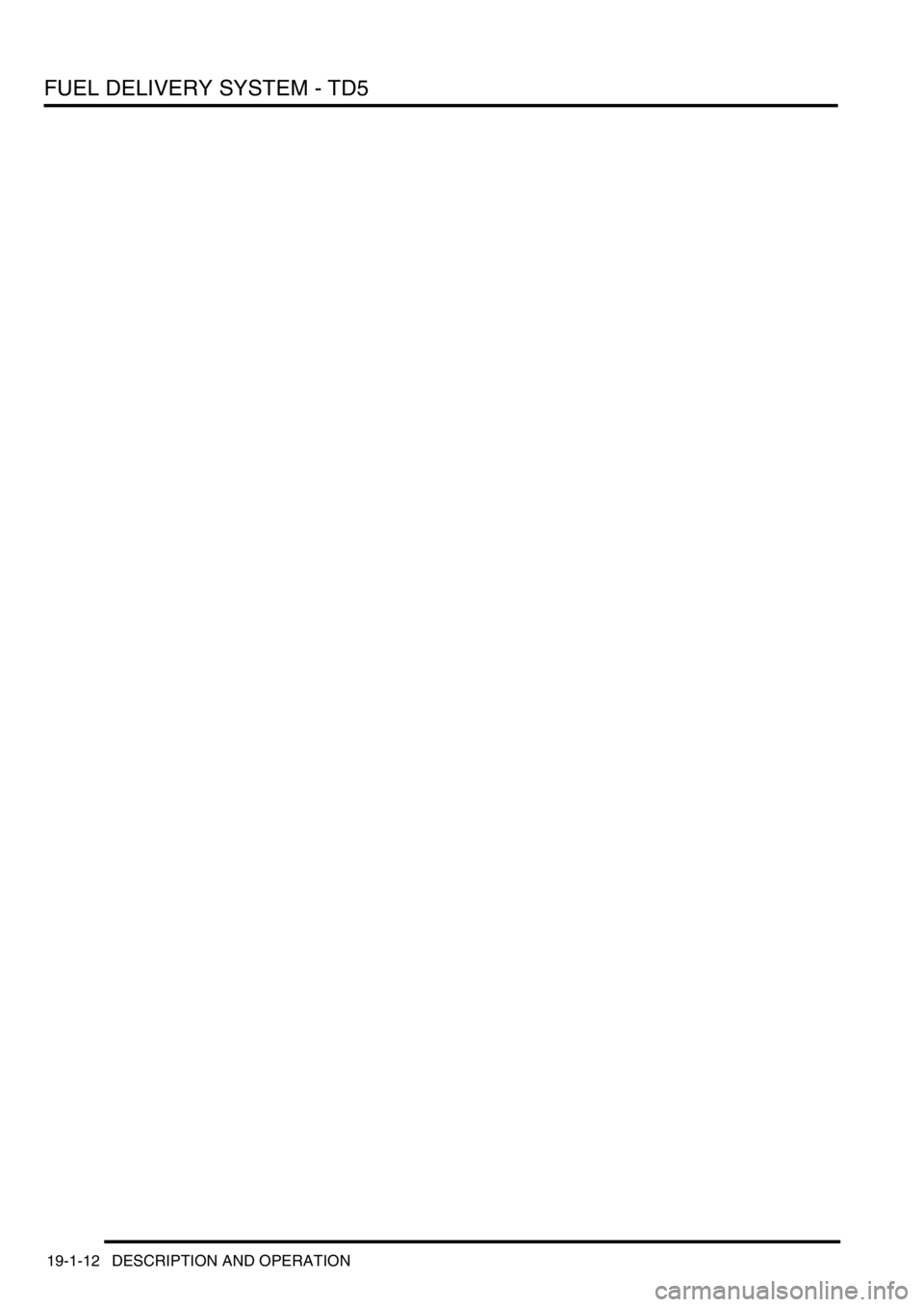
FUEL DELIVERY SYSTEM - TD5
19-1-12 DESCRIPTION AND OPERATION
Page 558 of 1672
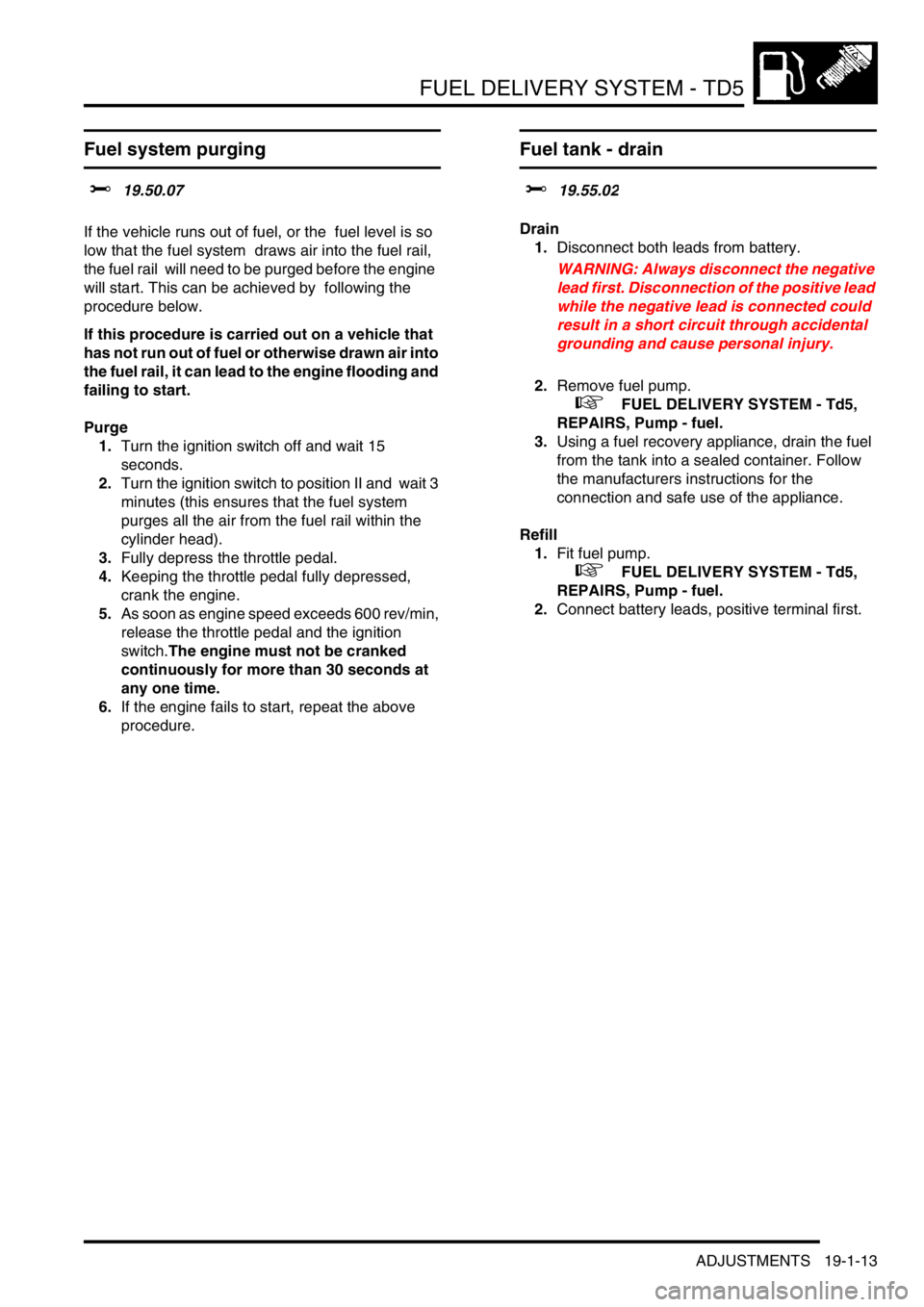
FUEL DELIVERY SYSTEM - TD5
ADJUSTMENTS 19-1-13
ADJUST ME NTS
Fuel system purging
$% 19.50.07
If the vehicle runs out of fuel, or the fuel level is so
low that the fuel system draws air into the fuel rail,
the fuel rail will need to be purged before the engine
will start. This can be achieved by following the
procedure below.
If this procedure is carried out on a vehicle that
has not run out of fuel or otherwise drawn air into
the fuel rail, it can lead to the engine flooding and
failing to start.
Purge
1.Turn the ignition switch off and wait 15
seconds.
2.Turn the ignition switch to position II and wait 3
minutes (this ensures that the fuel system
purges all the air from the fuel rail within the
cylinder head).
3.Fully depress the throttle pedal.
4.Keeping the throttle pedal fully depressed,
crank the engine.
5.As soon as engine speed exceeds 600 rev/min,
release the throttle pedal and the ignition
switch.The engine must not be cranked
continuously for more than 30 seconds at
any one time.
6.If the engine fails to start, repeat the above
procedure.
Fuel tank - drain
$% 19.55.02
Drain
1.Disconnect both leads from battery.
WARNING: Always disconnect the negative
lead first. Disconnection of the positive lead
while the negative lead is connected could
result in a short circuit through accidental
grounding and cause personal injury.
2.Remove fuel pump.
+ FUEL DELIVERY SYSTEM - Td5,
REPAIRS, Pump - fuel.
3.Using a fuel recovery appliance, drain the fuel
from the tank into a sealed container. Follow
the manufacturers instructions for the
connection and safe use of the appliance.
Refill
1.Fit fuel pump.
+ FUEL DELIVERY SYSTEM - Td5,
REPAIRS, Pump - fuel.
2.Connect battery leads, positive terminal first.
Page 559 of 1672
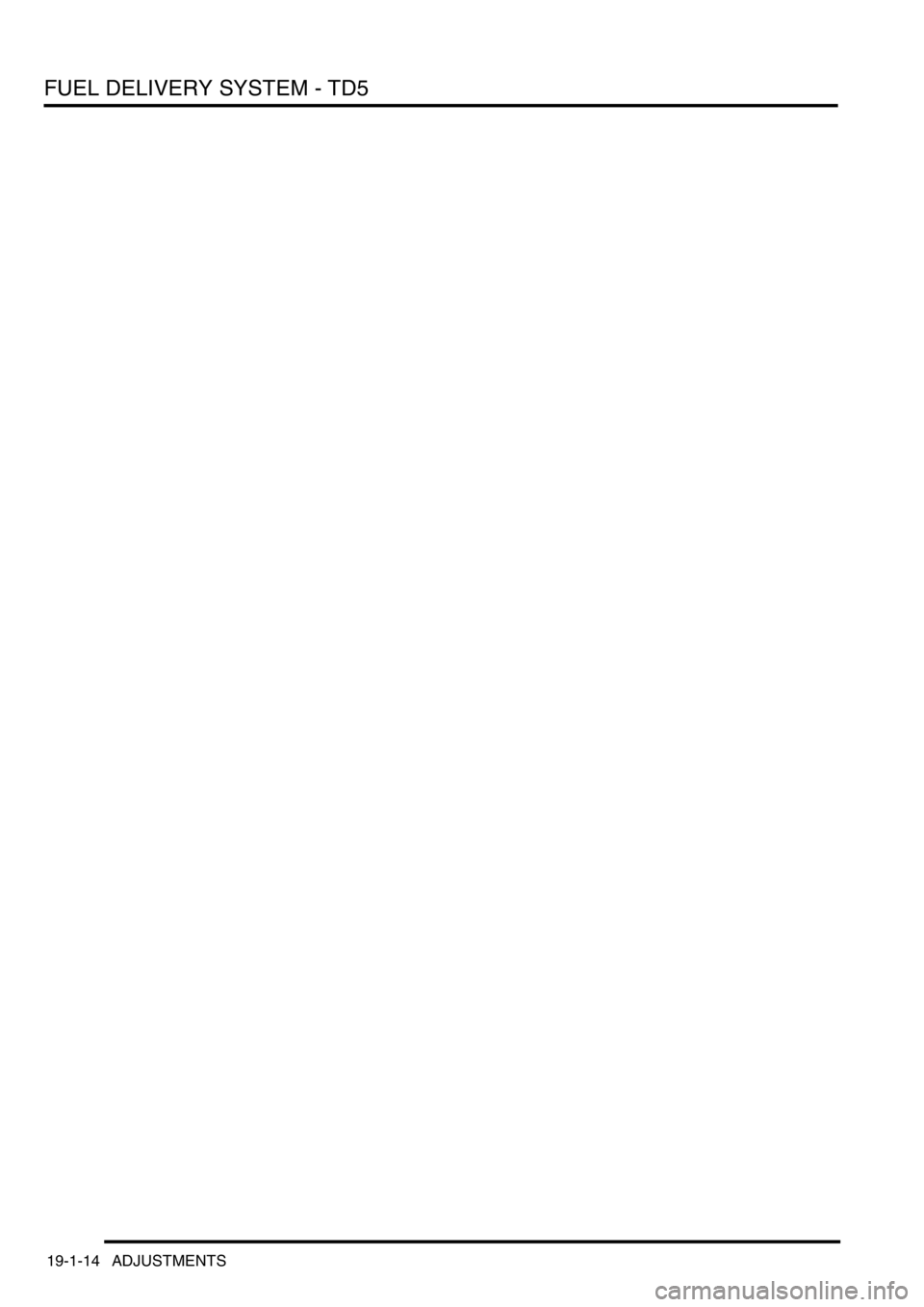
FUEL DELIVERY SYSTEM - TD5
19-1-14 ADJUSTMENTS
Page 560 of 1672
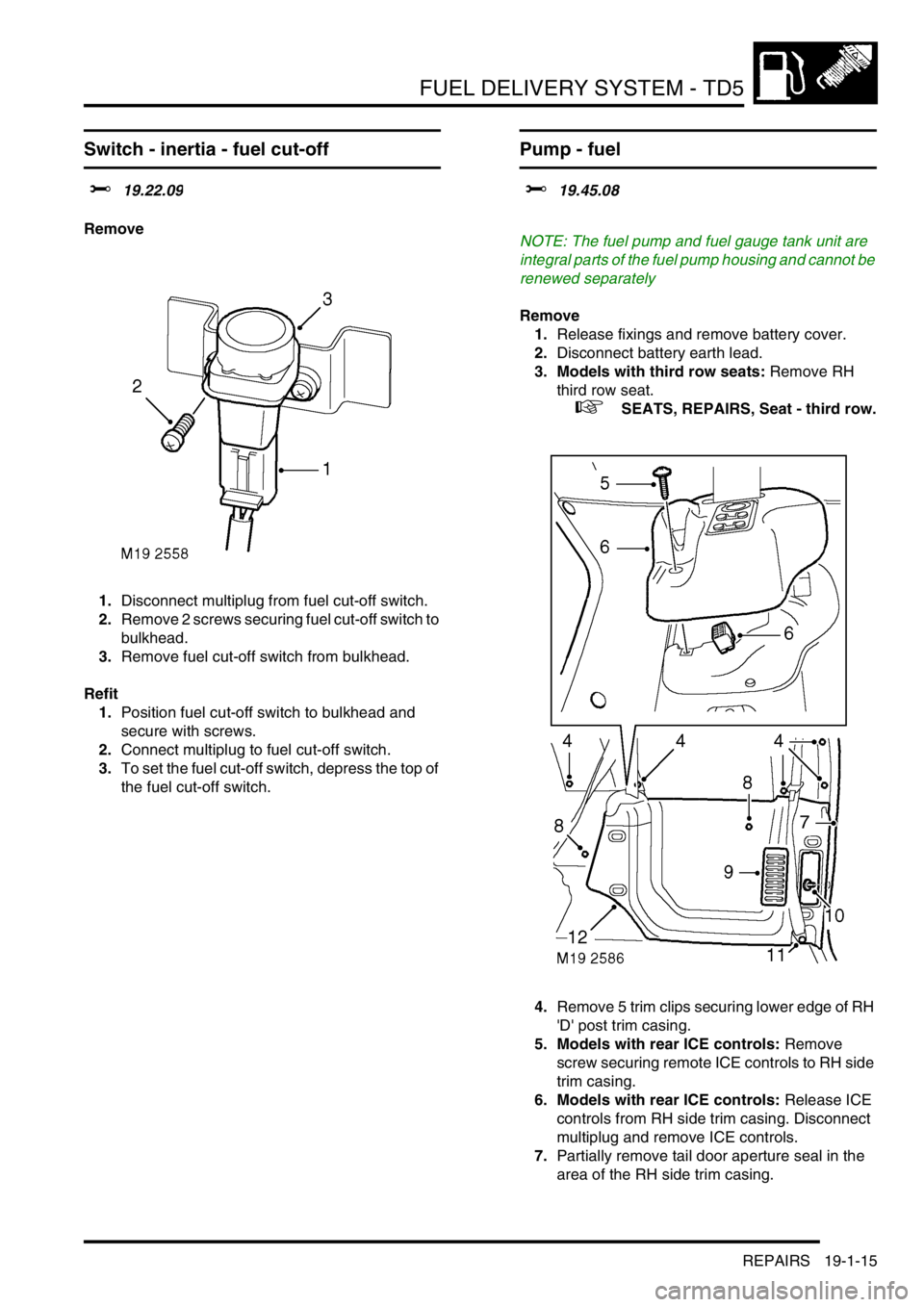
FUEL DELIVERY SYSTEM - TD5
REPAIRS 19-1-15
REPAIRS
Switch - inertia - fuel cut-off
$% 19.22.09
Remove
1.Disconnect multiplug from fuel cut-off switch.
2.Remove 2 screws securing fuel cut-off switch to
bulkhead.
3.Remove fuel cut-off switch from bulkhead.
Refit
1.Position fuel cut-off switch to bulkhead and
secure with screws.
2.Connect multiplug to fuel cut-off switch.
3.To set the fuel cut-off switch, depress the top of
the fuel cut-off switch.
Pump - fuel
$% 19.45.08
NOTE: The fuel pump and fuel gauge tank unit are
integral parts of the fuel pump housing and cannot be
renewed separately
Remove
1.Release fixings and remove battery cover.
2.Disconnect battery earth lead.
3. Models with third row seats: Remove RH
third row seat.
+ SEATS, REPAIRS, Seat - third row.
4.Remove 5 trim clips securing lower edge of RH
'D' post trim casing.
5. Models with rear ICE controls: Remove
screw securing remote ICE controls to RH side
trim casing.
6. Models with rear ICE controls: Release ICE
controls from RH side trim casing. Disconnect
multiplug and remove ICE controls.
7.Partially remove tail door aperture seal in the
area of the RH side trim casing.