LAND ROVER DISCOVERY 2002 Workshop Manual
Manufacturer: LAND ROVER, Model Year: 2002, Model line: DISCOVERY, Model: LAND ROVER DISCOVERY 2002Pages: 1672, PDF Size: 46.1 MB
Page 541 of 1672
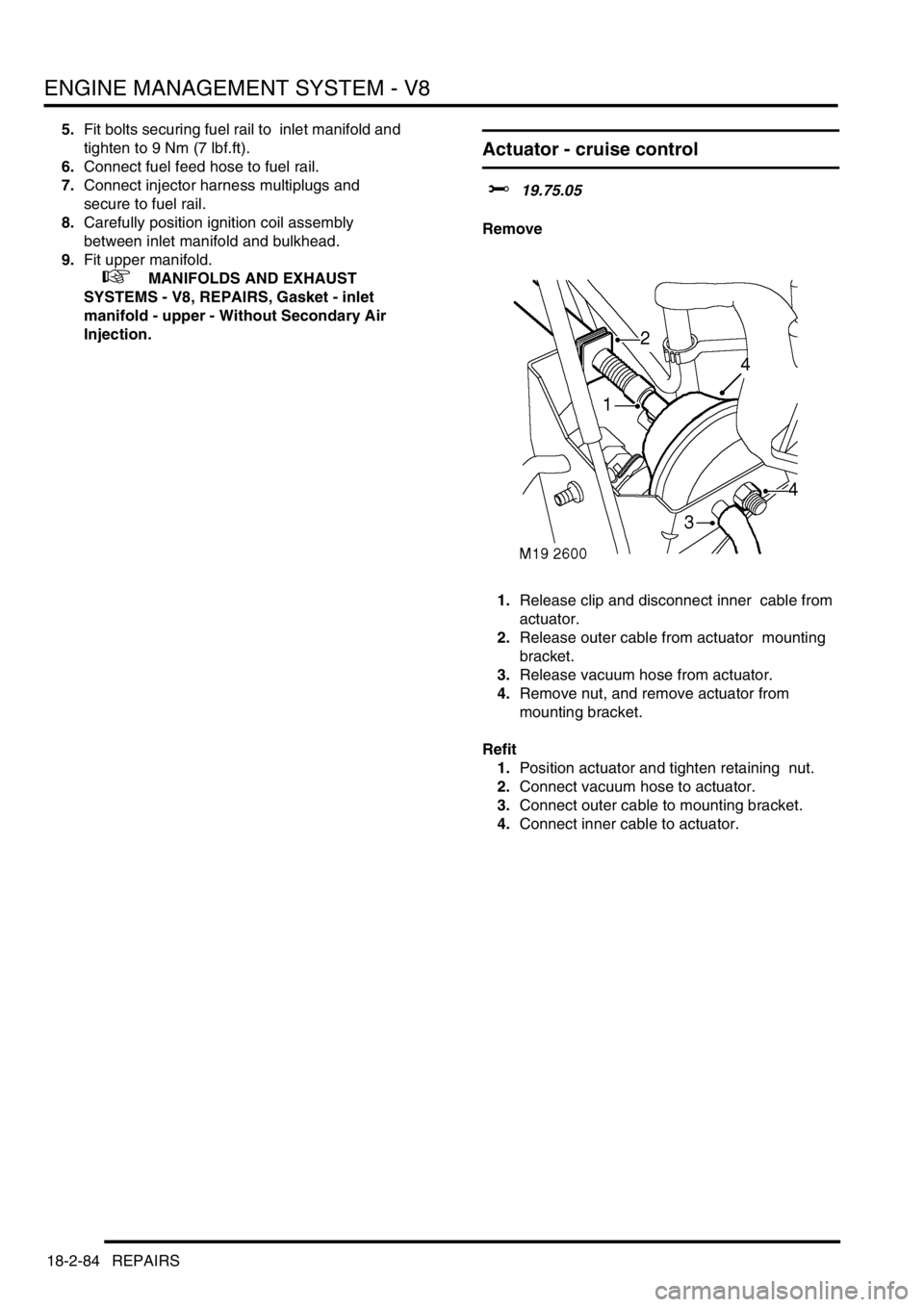
ENGINE MANAGEMENT SYSTEM - V8
18-2-84 REPAIRS
5.Fit bolts securing fuel rail to inlet manifold and
tighten to 9 Nm (7 lbf.ft).
6.Connect fuel feed hose to fuel rail.
7.Connect injector harness multiplugs and
secure to fuel rail.
8.Carefully position ignition coil assembly
between inlet manifold and bulkhead.
9.Fit upper manifold.
+ MANIFOLDS AND EXHAUST
SYSTEMS - V8, REPAIRS, Gasket - inlet
manifold - upper - Without Secondary Air
Injection.
Actuator - cruise control
$% 19.75.05
Remove
1.Release clip and disconnect inner cable from
actuator.
2.Release outer cable from actuator mounting
bracket.
3.Release vacuum hose from actuator.
4.Remove nut, and remove actuator from
mounting bracket.
Refit
1.Position actuator and tighten retaining nut.
2.Connect vacuum hose to actuator.
3.Connect outer cable to mounting bracket.
4.Connect inner cable to actuator.
Page 542 of 1672
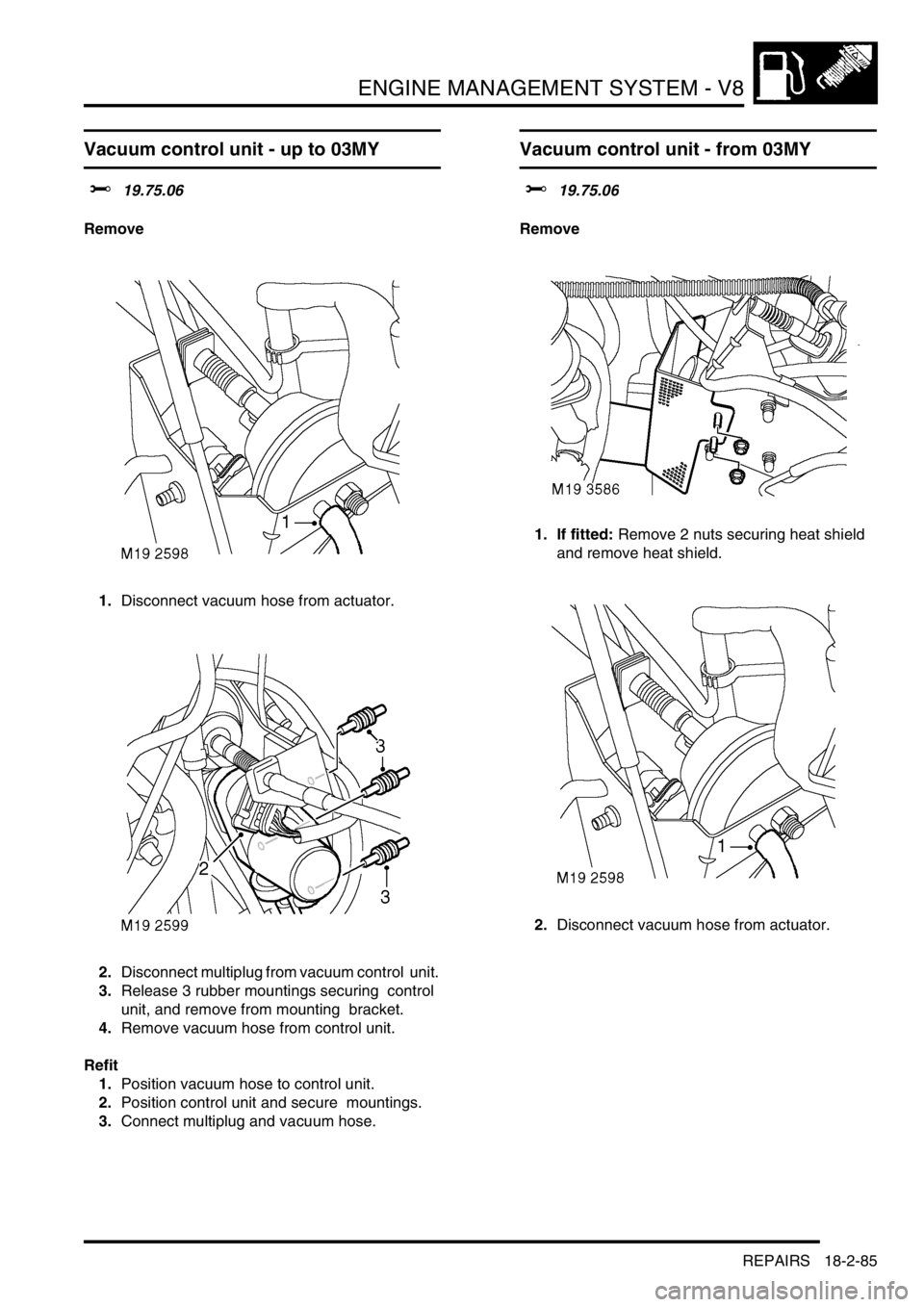
ENGINE MANAGEMENT SYSTEM - V8
REPAIRS 18-2-85
Vacuum control unit - up to 03MY
$% 19.75.06
Remove
1.Disconnect vacuum hose from actuator.
2.Disconnect multiplug from vacuum control unit.
3.Release 3 rubber mountings securing control
unit, and remove from mounting bracket.
4.Remove vacuum hose from control unit.
Refit
1.Position vacuum hose to control unit.
2.Position control unit and secure mountings.
3.Connect multiplug and vacuum hose.
Vacuum control unit - from 03MY
$% 19.75.06
Remove
1. If fitted: Remove 2 nuts securing heat shield
and remove heat shield.
2.Disconnect vacuum hose from actuator.
Page 543 of 1672
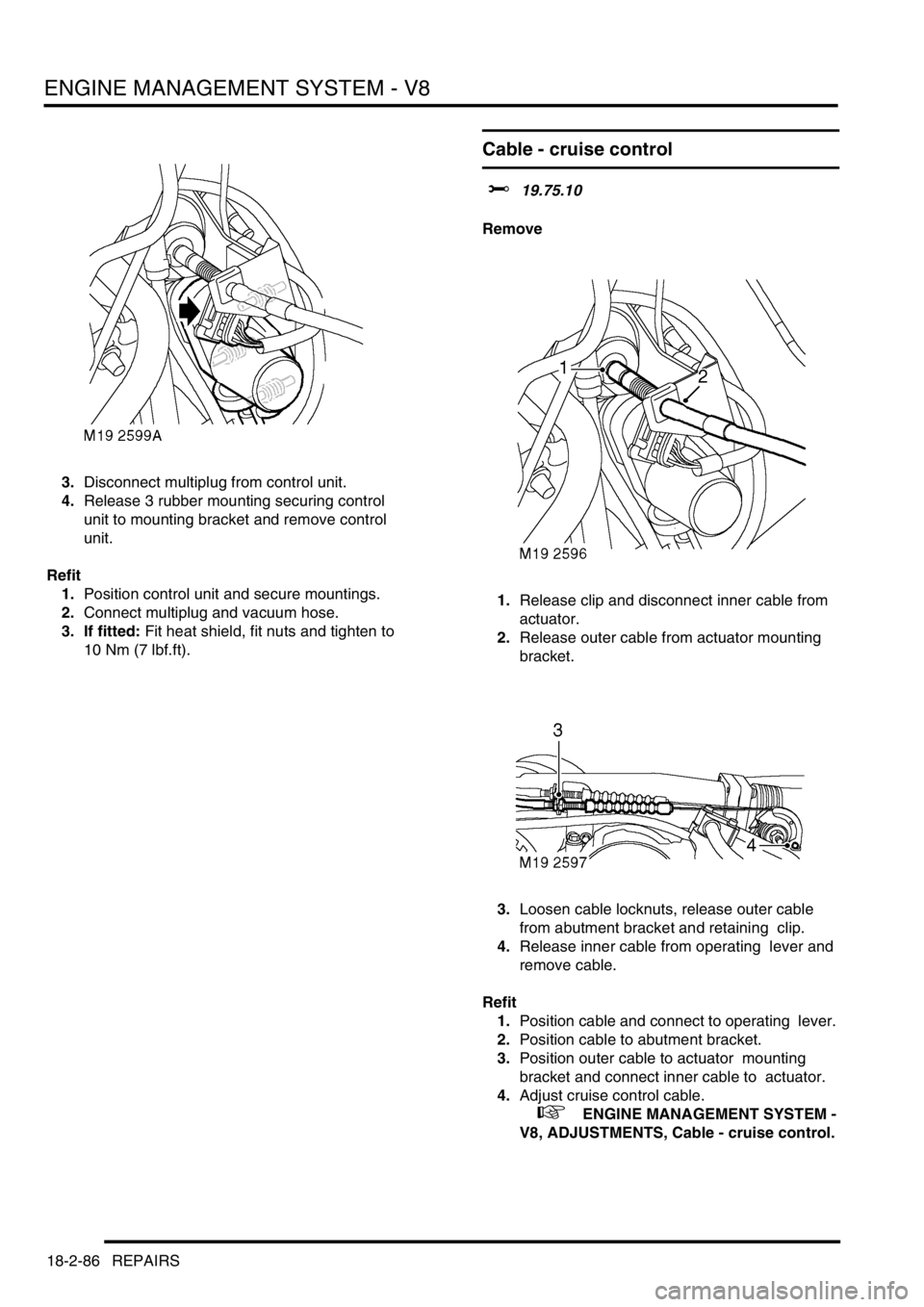
ENGINE MANAGEMENT SYSTEM - V8
18-2-86 REPAIRS
3.Disconnect multiplug from control unit.
4.Release 3 rubber mounting securing control
unit to mounting bracket and remove control
unit.
Refit
1.Position control unit and secure mountings.
2.Connect multiplug and vacuum hose.
3. If fitted: Fit heat shield, fit nuts and tighten to
10 Nm (7 lbf.ft).
Cable - cruise control
$% 19.75.10
Remove
1.Release clip and disconnect inner cable from
actuator.
2.Release outer cable from actuator mounting
bracket.
3.Loosen cable locknuts, release outer cable
from abutment bracket and retaining clip.
4.Release inner cable from operating lever and
remove cable.
Refit
1.Position cable and connect to operating lever.
2.Position cable to abutment bracket.
3.Position outer cable to actuator mounting
bracket and connect inner cable to actuator.
4.Adjust cruise control cable.
+ ENGINE MANAGEMENT SYSTEM -
V8, ADJUSTMENTS, Cable - cruise control.
Page 544 of 1672
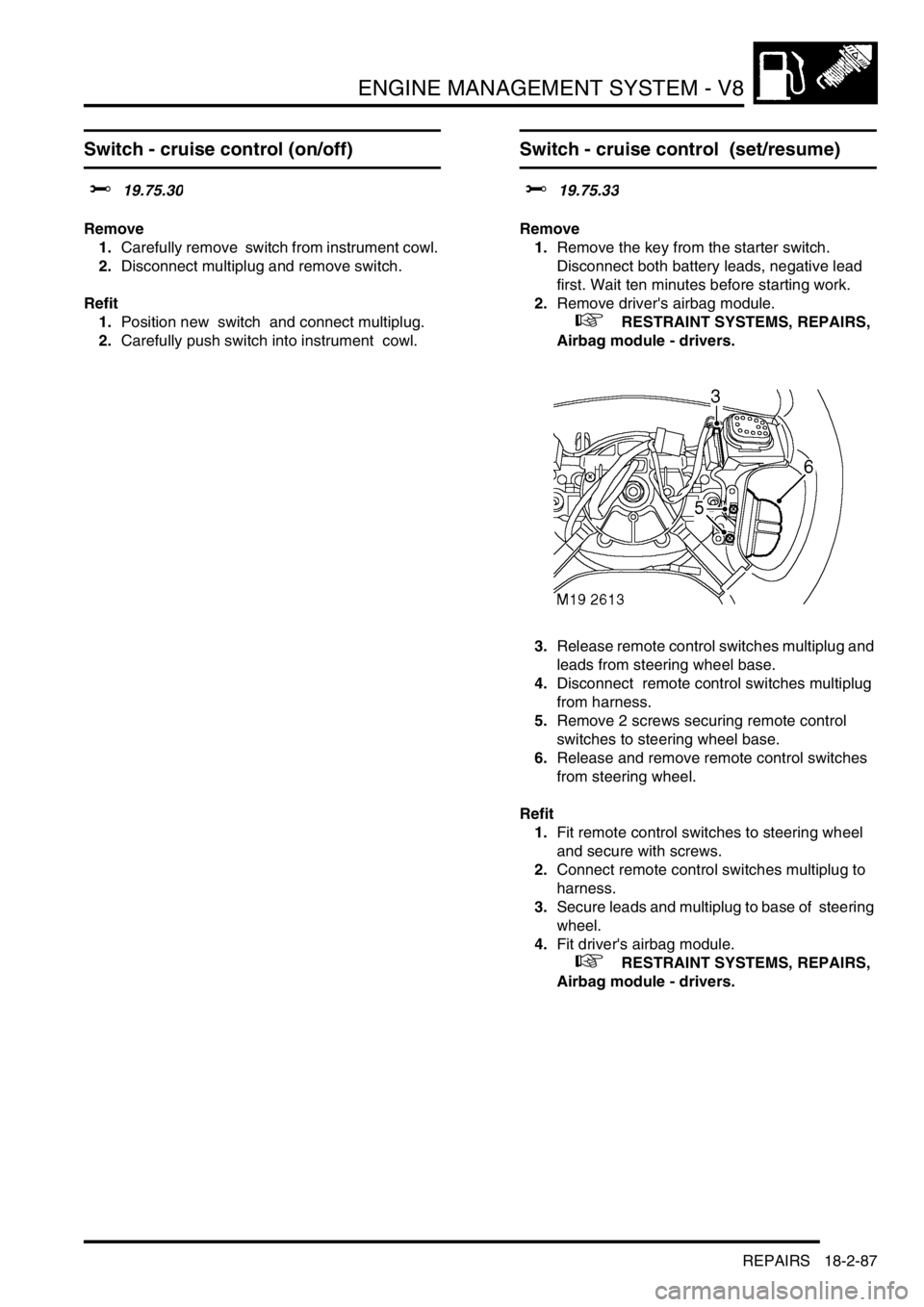
ENGINE MANAGEMENT SYSTEM - V8
REPAIRS 18-2-87
Switch - cruise control (on/off)
$% 19.75.30
Remove
1.Carefully remove switch from instrument cowl.
2.Disconnect multiplug and remove switch.
Refit
1.Position new switch and connect multiplug.
2.Carefully push switch into instrument cowl.
Switch - cruise control (set/resume)
$% 19.75.33
Remove
1.Remove the key from the starter switch.
Disconnect both battery leads, negative lead
first. Wait ten minutes before starting work.
2.Remove driver's airbag module.
+ RESTRAINT SYSTEMS, REPAIRS,
Airbag module - drivers.
3.Release remote control switches multiplug and
leads from steering wheel base.
4.Disconnect remote control switches multiplug
from harness.
5.Remove 2 screws securing remote control
switches to steering wheel base.
6.Release and remove remote control switches
from steering wheel.
Refit
1.Fit remote control switches to steering wheel
and secure with screws.
2.Connect remote control switches multiplug to
harness.
3.Secure leads and multiplug to base of steering
wheel.
4.Fit driver's airbag module.
+ RESTRAINT SYSTEMS, REPAIRS,
Airbag module - drivers.
Page 545 of 1672
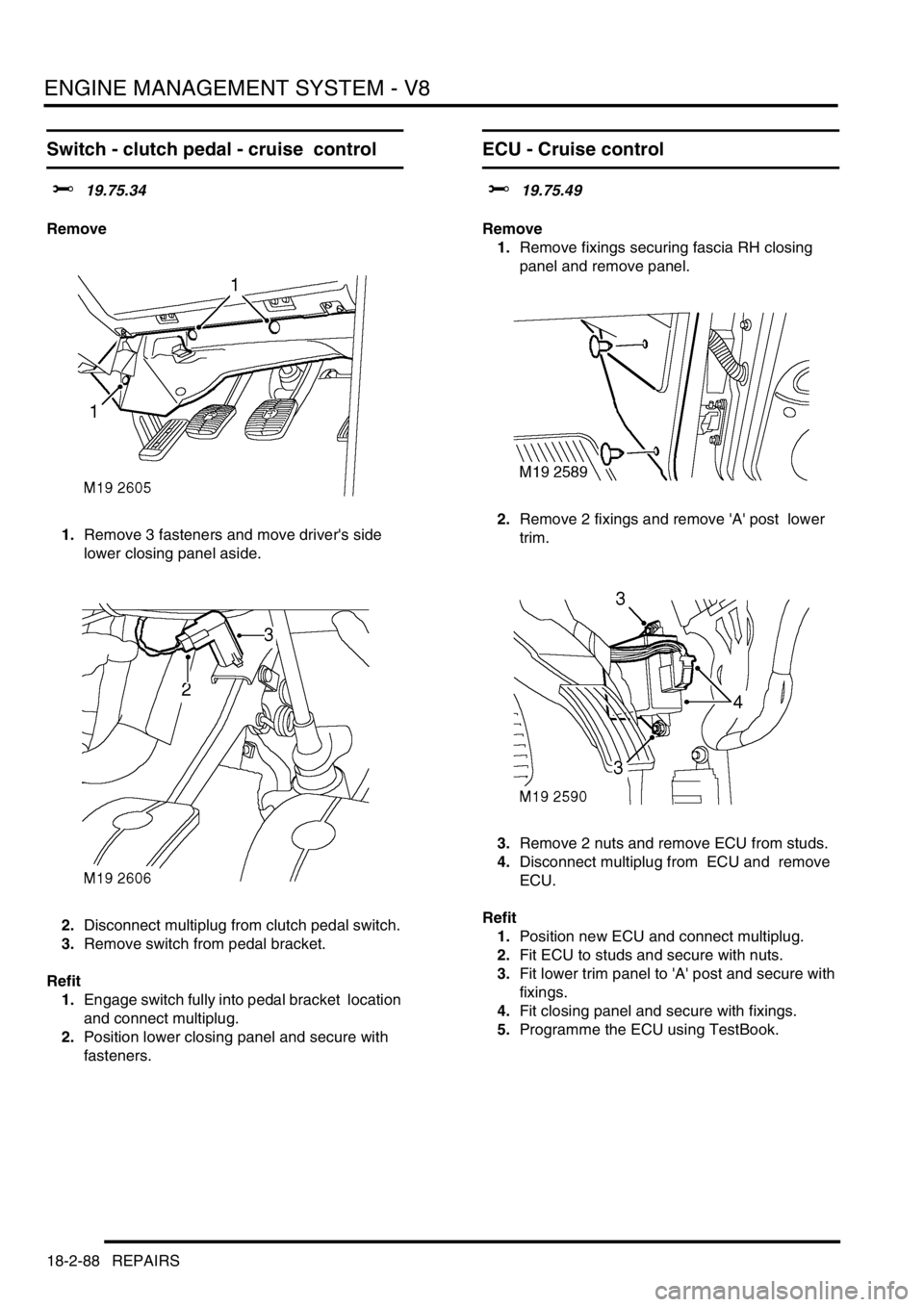
ENGINE MANAGEMENT SYSTEM - V8
18-2-88 REPAIRS
Switch - clutch pedal - cruise control
$% 19.75.34
Remove
1.Remove 3 fasteners and move driver's side
lower closing panel aside.
2.Disconnect multiplug from clutch pedal switch.
3.Remove switch from pedal bracket.
Refit
1.Engage switch fully into pedal bracket location
and connect multiplug.
2.Position lower closing panel and secure with
fasteners.
ECU - Cruise control
$% 19.75.49
Remove
1.Remove fixings securing fascia RH closing
panel and remove panel.
2.Remove 2 fixings and remove 'A' post lower
trim.
3.Remove 2 nuts and remove ECU from studs.
4.Disconnect multiplug from ECU and remove
ECU.
Refit
1.Position new ECU and connect multiplug.
2.Fit ECU to studs and secure with nuts.
3.Fit lower trim panel to 'A' post and secure with
fixings.
4.Fit closing panel and secure with fixings.
5.Programme the ECU using TestBook.
Page 546 of 1672
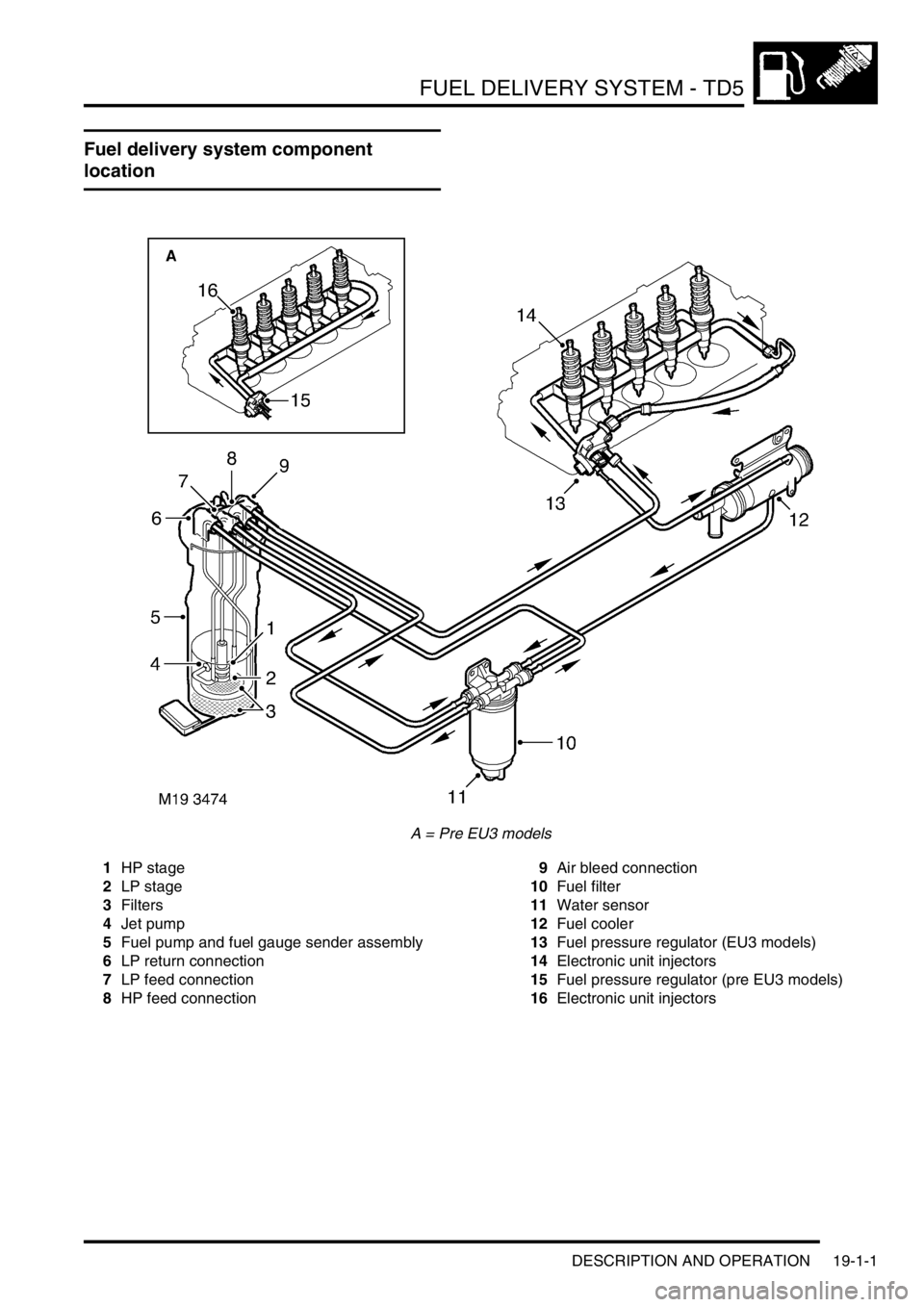
FUEL DELIVERY SYSTEM - TD5
DESCRIPTION AND OPERATION 19-1-1
FUEL DELIVERY SYST EM - Td5 DESCRIPTION AND OPERAT ION
Fuel delivery system component
location
A = Pre EU3 models
1HP stage
2LP stage
3Filters
4Jet pump
5Fuel pump and fuel gauge sender assembly
6LP return connection
7LP feed connection
8HP feed connection9Air bleed connection
10Fuel filter
11Water sensor
12Fuel cooler
13Fuel pressure regulator (EU3 models)
14Electronic unit injectors
15Fuel pressure regulator (pre EU3 models)
16Electronic unit injectors
Page 547 of 1672
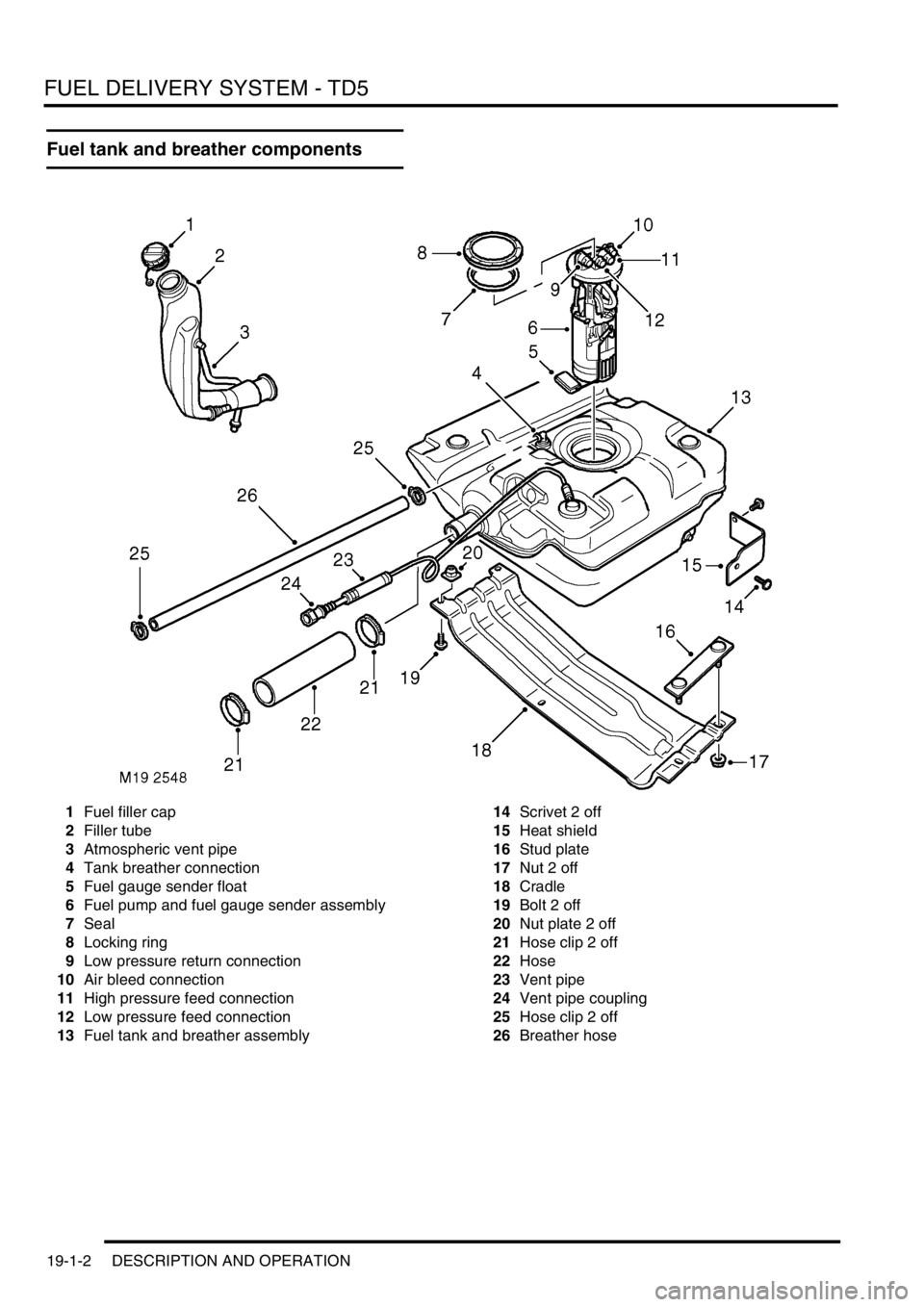
FUEL DELIVERY SYSTEM - TD5
19-1-2 DESCRIPTION AND OPERATION
Fuel tank and breather components
1Fuel filler cap
2Filler tube
3Atmospheric vent pipe
4Tank breather connection
5Fuel gauge sender float
6Fuel pump and fuel gauge sender assembly
7Seal
8Locking ring
9Low pressure return connection
10Air bleed connection
11High pressure feed connection
12Low pressure feed connection
13Fuel tank and breather assembly14Scrivet 2 off
15Heat shield
16Stud plate
17Nut 2 off
18Cradle
19Bolt 2 off
20Nut plate 2 off
21Hose clip 2 off
22Hose
23Vent pipe
24Vent pipe coupling
25Hose clip 2 off
26Breather hose
Page 548 of 1672
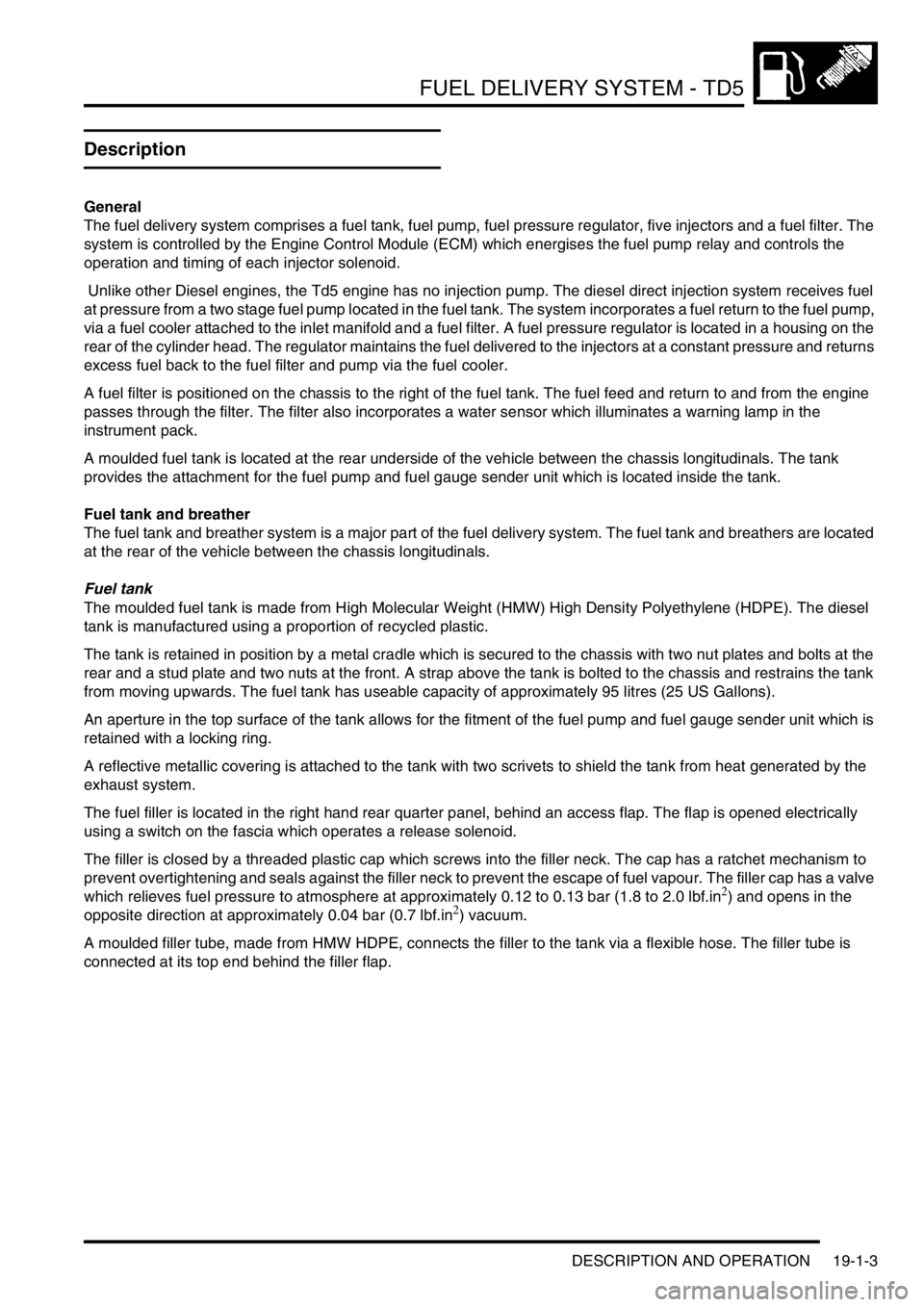
FUEL DELIVERY SYSTEM - TD5
DESCRIPTION AND OPERATION 19-1-3
Description
General
The fuel delivery system comprises a fuel tank, fuel pump, fuel pressure regulator, five injectors and a fuel filter. The
system is controlled by the Engine Control Module (ECM) which energises the fuel pump relay and controls the
operation and timing of each injector solenoid.
Unlike other Diesel engines, the Td5 engine has no injection pump. The diesel direct injection system receives fuel
at pressure from a two stage fuel pump located in the fuel tank. The system incorporates a fuel return to the fuel pump,
via a fuel cooler attached to the inlet manifold and a fuel filter. A fuel pressure regulator is located in a housing on the
rear of the cylinder head. The regulator maintains the fuel delivered to the injectors at a constant pressure and returns
excess fuel back to the fuel filter and pump via the fuel cooler.
A fuel filter is positioned on the chassis to the right of the fuel tank. The fuel feed and return to and from the engine
passes through the filter. The filter also incorporates a water sensor which illuminates a warning lamp in the
instrument pack.
A moulded fuel tank is located at the rear underside of the vehicle between the chassis longitudinals. The tank
provides the attachment for the fuel pump and fuel gauge sender unit which is located inside the tank.
Fuel tank and breather
The fuel tank and breather system is a major part of the fuel delivery system. The fuel tank and breathers are located
at the rear of the vehicle between the chassis longitudinals.
Fuel tank
The moulded fuel tank is made from High Molecular Weight (HMW) High Density Polyethylene (HDPE). The diesel
tank is manufactured using a proportion of recycled plastic.
The tank is retained in position by a metal cradle which is secured to the chassis with two nut plates and bolts at the
rear and a stud plate and two nuts at the front. A strap above the tank is bolted to the chassis and restrains the tank
from moving upwards. The fuel tank has useable capacity of approximately 95 litres (25 US Gallons).
An aperture in the top surface of the tank allows for the fitment of the fuel pump and fuel gauge sender unit which is
retained with a locking ring.
A reflective metallic covering is attached to the tank with two scrivets to shield the tank from heat generated by the
exhaust system.
The fuel filler is located in the right hand rear quarter panel, behind an access flap. The flap is opened electrically
using a switch on the fascia which operates a release solenoid.
The filler is closed by a threaded plastic cap which screws into the filler neck. The cap has a ratchet mechanism to
prevent overtightening and seals against the filler neck to prevent the escape of fuel vapour. The filler cap has a valve
which relieves fuel pressure to atmosphere at approximately 0.12 to 0.13 bar (1.8 to 2.0 lbf.in
2) and opens in the
opposite direction at approximately 0.04 bar (0.7 lbf.in2) vacuum.
A moulded filler tube, made from HMW HDPE, connects the filler to the tank via a flexible hose. The filler tube is
connected at its top end behind the filler flap.
Page 549 of 1672
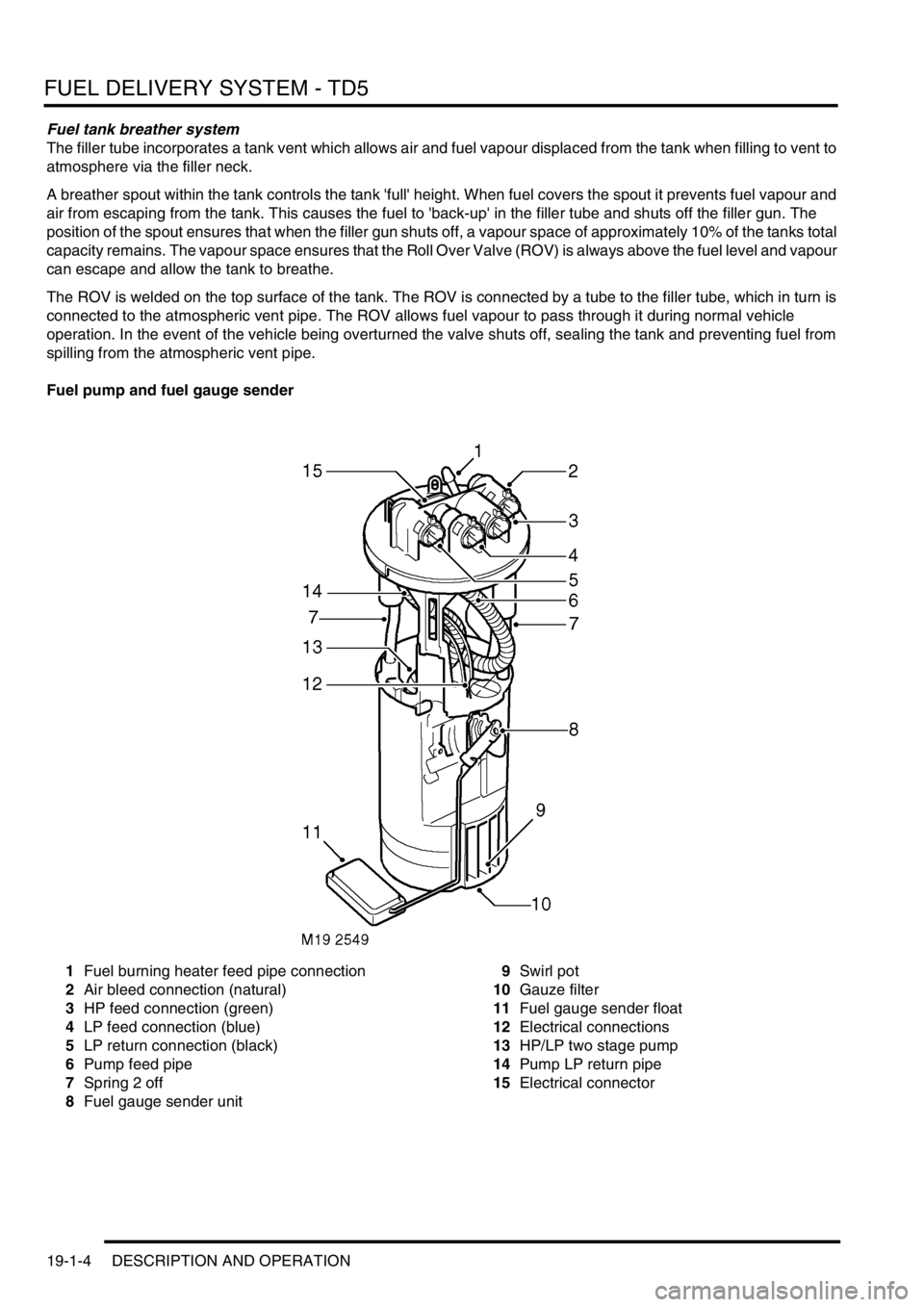
FUEL DELIVERY SYSTEM - TD5
19-1-4 DESCRIPTION AND OPERATION
Fuel tank breather system
The filler tube incorporates a tank vent which allows air and fuel vapour displaced from the tank when filling to vent to
atmosphere via the filler neck.
A breather spout within the tank controls the tank 'full' height. When fuel covers the spout it prevents fuel vapour and
air from escaping from the tank. This causes the fuel to 'back-up' in the filler tube and shuts off the filler gun. The
position of the spout ensures that when the filler gun shuts off, a vapour space of approximately 10% of the tanks total
capacity remains. The vapour space ensures that the Roll Over Valve (ROV) is always above the fuel level and vapour
can escape and allow the tank to breathe.
The ROV is welded on the top surface of the tank. The ROV is connected by a tube to the filler tube, which in turn is
connected to the atmospheric vent pipe. The ROV allows fuel vapour to pass through it during normal vehicle
operation. In the event of the vehicle being overturned the valve shuts off, sealing the tank and preventing fuel from
spilling from the atmospheric vent pipe.
Fuel pump and fuel gauge sender
1Fuel burning heater feed pipe connection
2Air bleed connection (natural)
3HP feed connection (green)
4LP feed connection (blue)
5LP return connection (black)
6Pump feed pipe
7Spring 2 off
8Fuel gauge sender unit9Swirl pot
10Gauze filter
11Fuel gauge sender float
12Electrical connections
13HP/LP two stage pump
14Pump LP return pipe
15Electrical connector
Page 550 of 1672
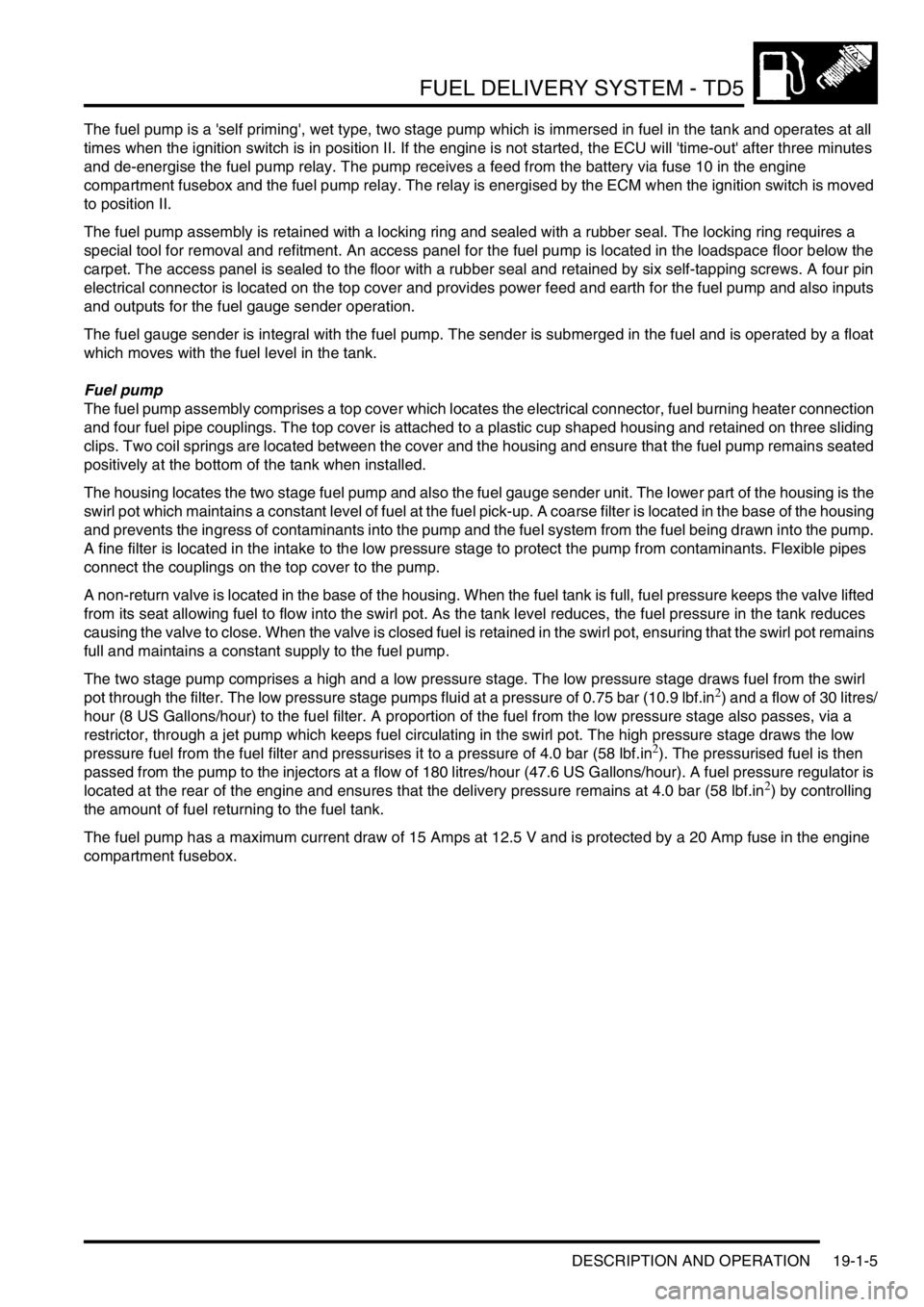
FUEL DELIVERY SYSTEM - TD5
DESCRIPTION AND OPERATION 19-1-5
The fuel pump is a 'self priming', wet type, two stage pump which is immersed in fuel in the tank and operates at all
times when the ignition switch is in position II. If the engine is not started, the ECU will 'time-out' after three minutes
and de-energise the fuel pump relay. The pump receives a feed from the battery via fuse 10 in the engine
compartment fusebox and the fuel pump relay. The relay is energised by the ECM when the ignition switch is moved
to position II.
The fuel pump assembly is retained with a locking ring and sealed with a rubber seal. The locking ring requires a
special tool for removal and refitment. An access panel for the fuel pump is located in the loadspace floor below the
carpet. The access panel is sealed to the floor with a rubber seal and retained by six self-tapping screws. A four pin
electrical connector is located on the top cover and provides power feed and earth for the fuel pump and also inputs
and outputs for the fuel gauge sender operation.
The fuel gauge sender is integral with the fuel pump. The sender is submerged in the fuel and is operated by a float
which moves with the fuel level in the tank.
Fuel pump
The fuel pump assembly comprises a top cover which locates the electrical connector, fuel burning heater connection
and four fuel pipe couplings. The top cover is attached to a plastic cup shaped housing and retained on three sliding
clips. Two coil springs are located between the cover and the housing and ensure that the fuel pump remains seated
positively at the bottom of the tank when installed.
The housing locates the two stage fuel pump and also the fuel gauge sender unit. The lower part of the housing is the
swirl pot which maintains a constant level of fuel at the fuel pick-up. A coarse filter is located in the base of the housing
and prevents the ingress of contaminants into the pump and the fuel system from the fuel being drawn into the pump.
A fine filter is located in the intake to the low pressure stage to protect the pump from contaminants. Flexible pipes
connect the couplings on the top cover to the pump.
A non-return valve is located in the base of the housing. When the fuel tank is full, fuel pressure keeps the valve lifted
from its seat allowing fuel to flow into the swirl pot. As the tank level reduces, the fuel pressure in the tank reduces
causing the valve to close. When the valve is closed fuel is retained in the swirl pot, ensuring that the swirl pot remains
full and maintains a constant supply to the fuel pump.
The two stage pump comprises a high and a low pressure stage. The low pressure stage draws fuel from the swirl
pot through the filter. The low pressure stage pumps fluid at a pressure of 0.75 bar (10.9 lbf.in
2) and a flow of 30 litres/
hour (8 US Gallons/hour) to the fuel filter. A proportion of the fuel from the low pressure stage also passes, via a
restrictor, through a jet pump which keeps fuel circulating in the swirl pot. The high pressure stage draws the low
pressure fuel from the fuel filter and pressurises it to a pressure of 4.0 bar (58 lbf.in
2). The pressurised fuel is then
passed from the pump to the injectors at a flow of 180 litres/hour (47.6 US Gallons/hour). A fuel pressure regulator is
located at the rear of the engine and ensures that the delivery pressure remains at 4.0 bar (58 lbf.in
2) by controlling
the amount of fuel returning to the fuel tank.
The fuel pump has a maximum current draw of 15 Amps at 12.5 V and is protected by a 20 Amp fuse in the engine
compartment fusebox.