ESP LAND ROVER DISCOVERY 2002 Workshop Manual
[x] Cancel search | Manufacturer: LAND ROVER, Model Year: 2002, Model line: DISCOVERY, Model: LAND ROVER DISCOVERY 2002Pages: 1672, PDF Size: 46.1 MB
Page 37 of 1672
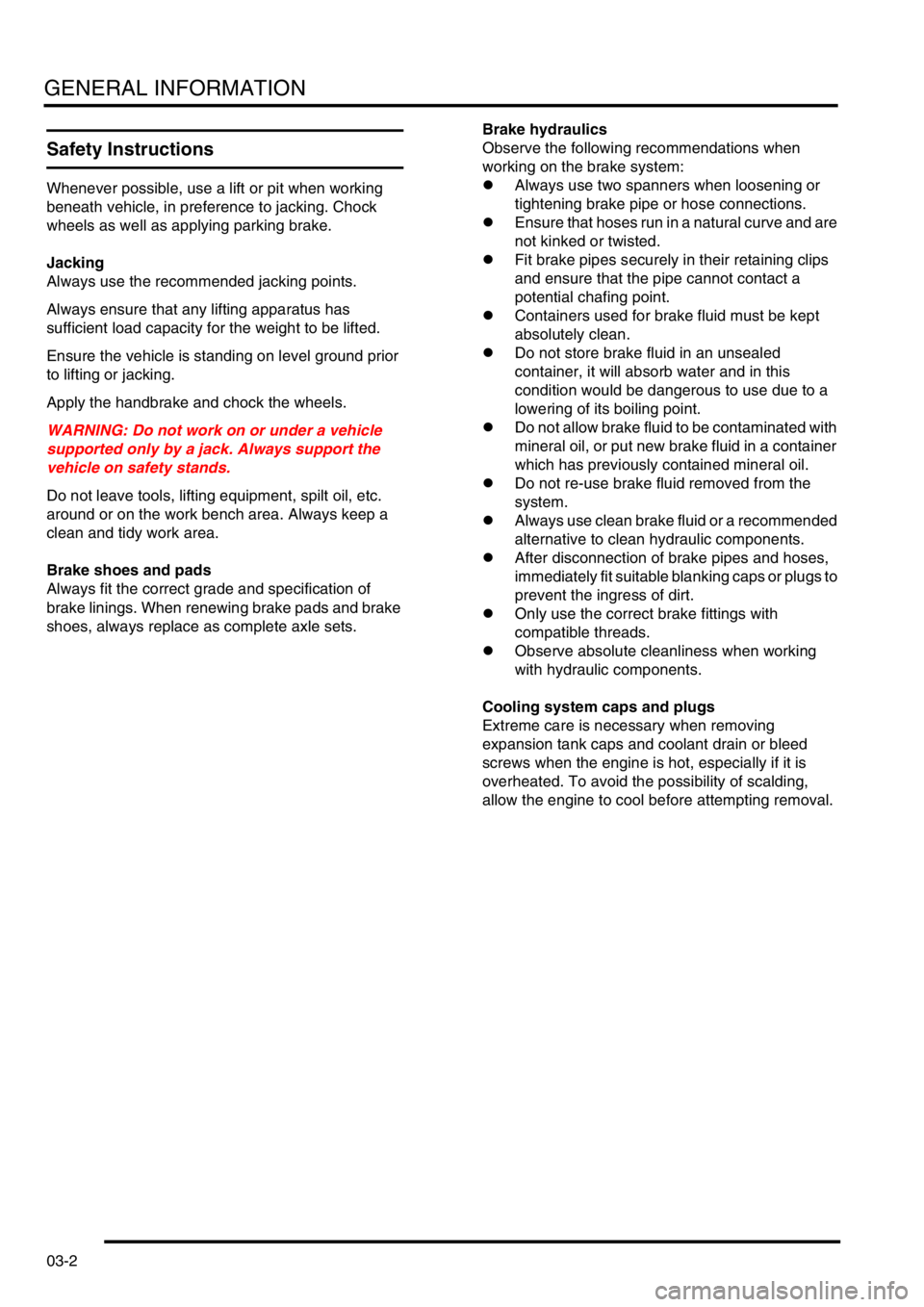
GENERAL INFORMATION
03-2
Safety Instructions
Whenever possible, use a lift or pit when working
beneath vehicle, in preference to jacking. Chock
wheels as well as applying parking brake.
Jacking
Always use the recommended jacking points.
Always ensure that any lifting apparatus has
sufficient load capacity for the weight to be lifted.
Ensure the vehicle is standing on level ground prior
to lifting or jacking.
Apply the handbrake and chock the wheels.
WARNING: Do not work on or under a vehicle
supported only by a jack. Always support the
vehicle on safety stands.
Do not leave tools, lifting equipment, spilt oil, etc.
around or on the work bench area. Always keep a
clean and tidy work area.
Brake shoes and pads
Always fit the correct grade and specification of
brake linings. When renewing brake pads and brake
shoes, always replace as complete axle sets.Brake hydraulics
Observe the following recommendations when
working on the brake system:
lAlways use two spanners when loosening or
tightening brake pipe or hose connections.
lEnsure that hoses run in a natural curve and are
not kinked or twisted.
lFit brake pipes securely in their retaining clips
and ensure that the pipe cannot contact a
potential chafing point.
lContainers used for brake fluid must be kept
absolutely clean.
lDo not store brake fluid in an unsealed
container, it will absorb water and in this
condition would be dangerous to use due to a
lowering of its boiling point.
lDo not allow brake fluid to be contaminated with
mineral oil, or put new brake fluid in a container
which has previously contained mineral oil.
lDo not re-use brake fluid removed from the
system.
lAlways use clean brake fluid or a recommended
alternative to clean hydraulic components.
lAfter disconnection of brake pipes and hoses,
immediately fit suitable blanking caps or plugs to
prevent the ingress of dirt.
lOnly use the correct brake fittings with
compatible threads.
lObserve absolute cleanliness when working
with hydraulic components.
Cooling system caps and plugs
Extreme care is necessary when removing
expansion tank caps and coolant drain or bleed
screws when the engine is hot, especially if it is
overheated. To avoid the possibility of scalding,
allow the engine to cool before attempting removal.
Page 40 of 1672
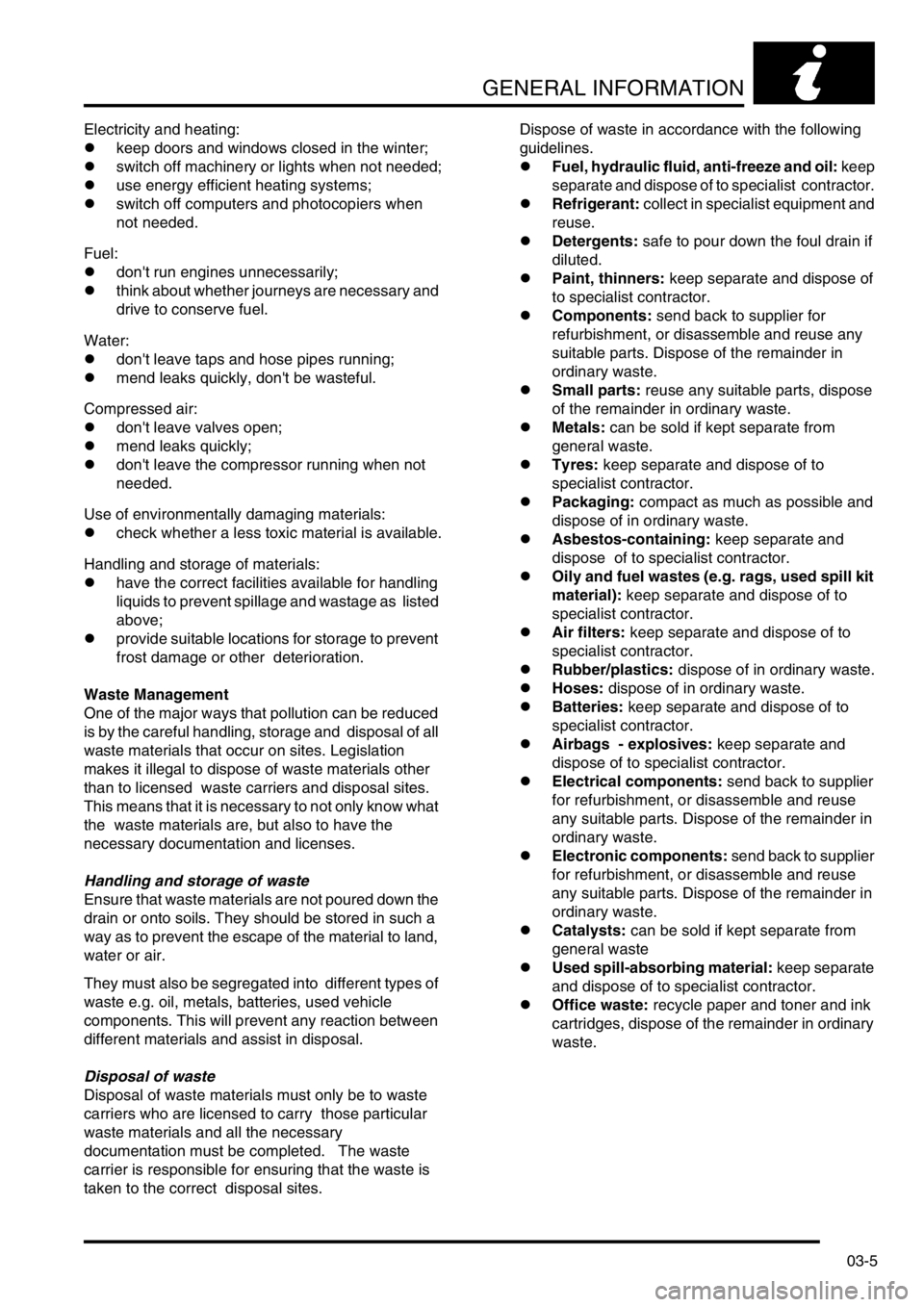
GENERAL INFORMATION
03-5
Electricity and heating:
lkeep doors and windows closed in the winter;
lswitch off machinery or lights when not needed;
luse energy efficient heating systems;
lswitch off computers and photocopiers when
not needed.
Fuel:
ldon't run engines unnecessarily;
lthink about whether journeys are necessary and
drive to conserve fuel.
Water:
ldon't leave taps and hose pipes running;
lmend leaks quickly, don't be wasteful.
Compressed air:
ldon't leave valves open;
lmend leaks quickly;
ldon't leave the compressor running when not
needed.
Use of environmentally damaging materials:
lcheck whether a less toxic material is available.
Handling and storage of materials:
lhave the correct facilities available for handling
liquids to prevent spillage and wastage as listed
above;
lprovide suitable locations for storage to prevent
frost damage or other deterioration.
Waste Management
One of the major ways that pollution can be reduced
is by the careful handling, storage and disposal of all
waste materials that occur on sites. Legislation
makes it illegal to dispose of waste materials other
than to licensed waste carriers and disposal sites.
This means that it is necessary to not only know what
the waste materials are, but also to have the
necessary documentation and licenses.
Handling and storage of waste
Ensure that waste materials are not poured down the
drain or onto soils. They should be stored in such a
way as to prevent the escape of the material to land,
water or air.
They must also be segregated into different types of
waste e.g. oil, metals, batteries, used vehicle
components. This will prevent any reaction between
different materials and assist in disposal.
Disposal of waste
Disposal of waste materials must only be to waste
carriers who are licensed to carry those particular
waste materials and all the necessary
documentation must be completed. The waste
carrier is responsible for ensuring that the waste is
taken to the correct disposal sites.Dispose of waste in accordance with the following
guidelines.
lFuel, hydraulic fluid, anti-freeze and oil: keep
separate and dispose of to specialist contractor.
lRefrigerant: collect in specialist equipment and
reuse.
lDetergents: safe to pour down the foul drain if
diluted.
lPaint, thinners: keep separate and dispose of
to specialist contractor.
lComponents: send back to supplier for
refurbishment, or disassemble and reuse any
suitable parts. Dispose of the remainder in
ordinary waste.
lSmall parts: reuse any suitable parts, dispose
of the remainder in ordinary waste.
lMetals: can be sold if kept separate from
general waste.
lTyres: keep separate and dispose of to
specialist contractor.
lPackaging: compact as much as possible and
dispose of in ordinary waste.
lAsbestos-containing: keep separate and
dispose of to specialist contractor.
lOily and fuel wastes (e.g. rags, used spill kit
material): keep separate and dispose of to
specialist contractor.
lAir filters: keep separate and dispose of to
specialist contractor.
lRubber/plastics: dispose of in ordinary waste.
lHoses: dispose of in ordinary waste.
lBatteries: keep separate and dispose of to
specialist contractor.
lAirbags - explosives: keep separate and
dispose of to specialist contractor.
lElectrical components: send back to supplier
for refurbishment, or disassemble and reuse
any suitable parts. Dispose of the remainder in
ordinary waste.
lElectronic components: send back to supplier
for refurbishment, or disassemble and reuse
any suitable parts. Dispose of the remainder in
ordinary waste.
lCatalysts: can be sold if kept separate from
general waste
lUsed spill-absorbing material: keep separate
and dispose of to specialist contractor.
lOffice waste: recycle paper and toner and ink
cartridges, dispose of the remainder in ordinary
waste.
Page 49 of 1672
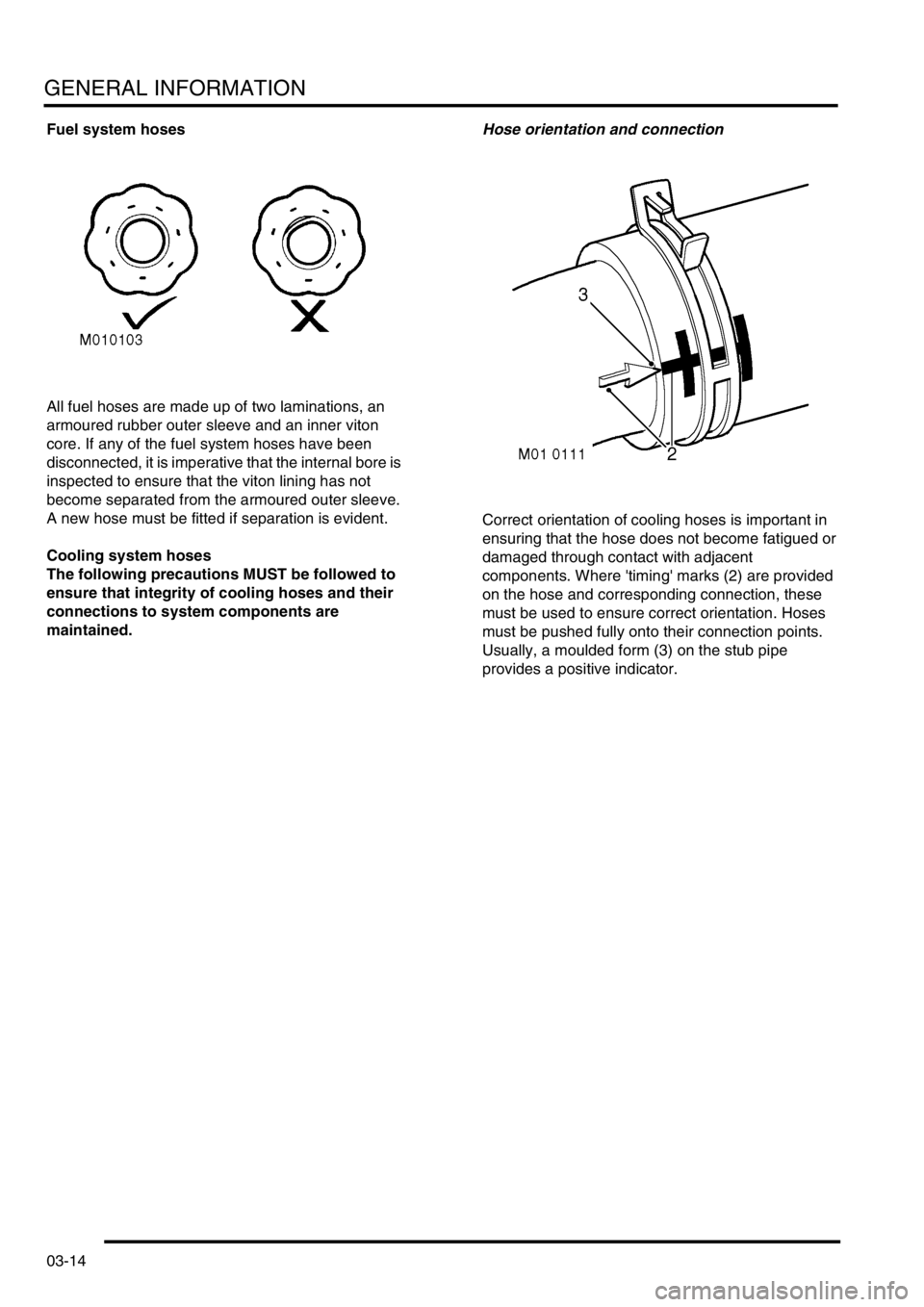
GENERAL INFORMATION
03-14
Fuel system hoses
All fuel hoses are made up of two laminations, an
armoured rubber outer sleeve and an inner viton
core. If any of the fuel system hoses have been
disconnected, it is imperative that the internal bore is
inspected to ensure that the viton lining has not
become separated from the armoured outer sleeve.
A new hose must be fitted if separation is evident.
Cooling system hoses
The following precautions MUST be followed to
ensure that integrity of cooling hoses and their
connections to system components are
maintained. Hose orientation and connection
Correct orientation of cooling hoses is important in
ensuring that the hose does not become fatigued or
damaged through contact with adjacent
components. Where 'timing' marks (2) are provided
on the hose and corresponding connection, these
must be used to ensure correct orientation. Hoses
must be pushed fully onto their connection points.
Usually, a moulded form (3) on the stub pipe
provides a positive indicator.
Page 53 of 1672
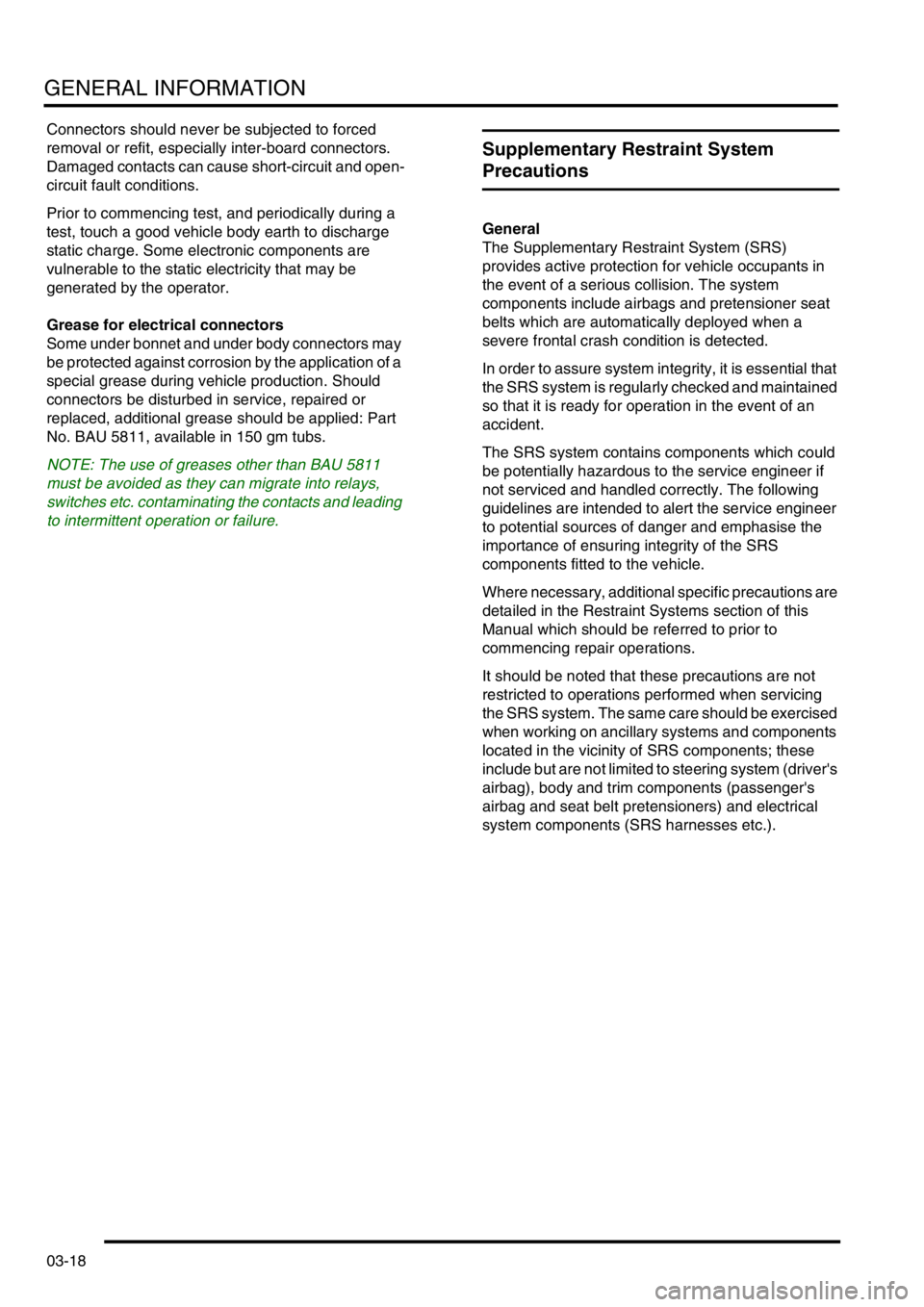
GENERAL INFORMATION
03-18
Connectors should never be subjected to forced
removal or refit, especially inter-board connectors.
Damaged contacts can cause short-circuit and open-
circuit fault conditions.
Prior to commencing test, and periodically during a
test, touch a good vehicle body earth to discharge
static charge. Some electronic components are
vulnerable to the static electricity that may be
generated by the operator.
Grease for electrical connectors
Some under bonnet and under body connectors may
be protected against corrosion by the application of a
special grease during vehicle production. Should
connectors be disturbed in service, repaired or
replaced, additional grease should be applied: Part
No. BAU 5811, available in 150 gm tubs.
NOTE: The use of greases other than BAU 5811
must be avoided as they can migrate into relays,
switches etc. contaminating the contacts and leading
to intermittent operation or failure.
Supplementary Restraint System
Precautions
General
The Supplementary Restraint System (SRS)
provides active protection for vehicle occupants in
the event of a serious collision. The system
components include airbags and pretensioner seat
belts which are automatically deployed when a
severe frontal crash condition is detected.
In order to assure system integrity, it is essential that
the SRS system is regularly checked and maintained
so that it is ready for operation in the event of an
accident.
The SRS system contains components which could
be potentially hazardous to the service engineer if
not serviced and handled correctly. The following
guidelines are intended to alert the service engineer
to potential sources of danger and emphasise the
importance of ensuring integrity of the SRS
components fitted to the vehicle.
Where necessary, additional specific precautions are
detailed in the Restraint Systems section of this
Manual which should be referred to prior to
commencing repair operations.
It should be noted that these precautions are not
restricted to operations performed when servicing
the SRS system. The same care should be exercised
when working on ancillary systems and components
located in the vicinity of SRS components; these
include but are not limited to steering system (driver's
airbag), body and trim components (passenger's
airbag and seat belt pretensioners) and electrical
system components (SRS harnesses etc.).
Page 59 of 1672
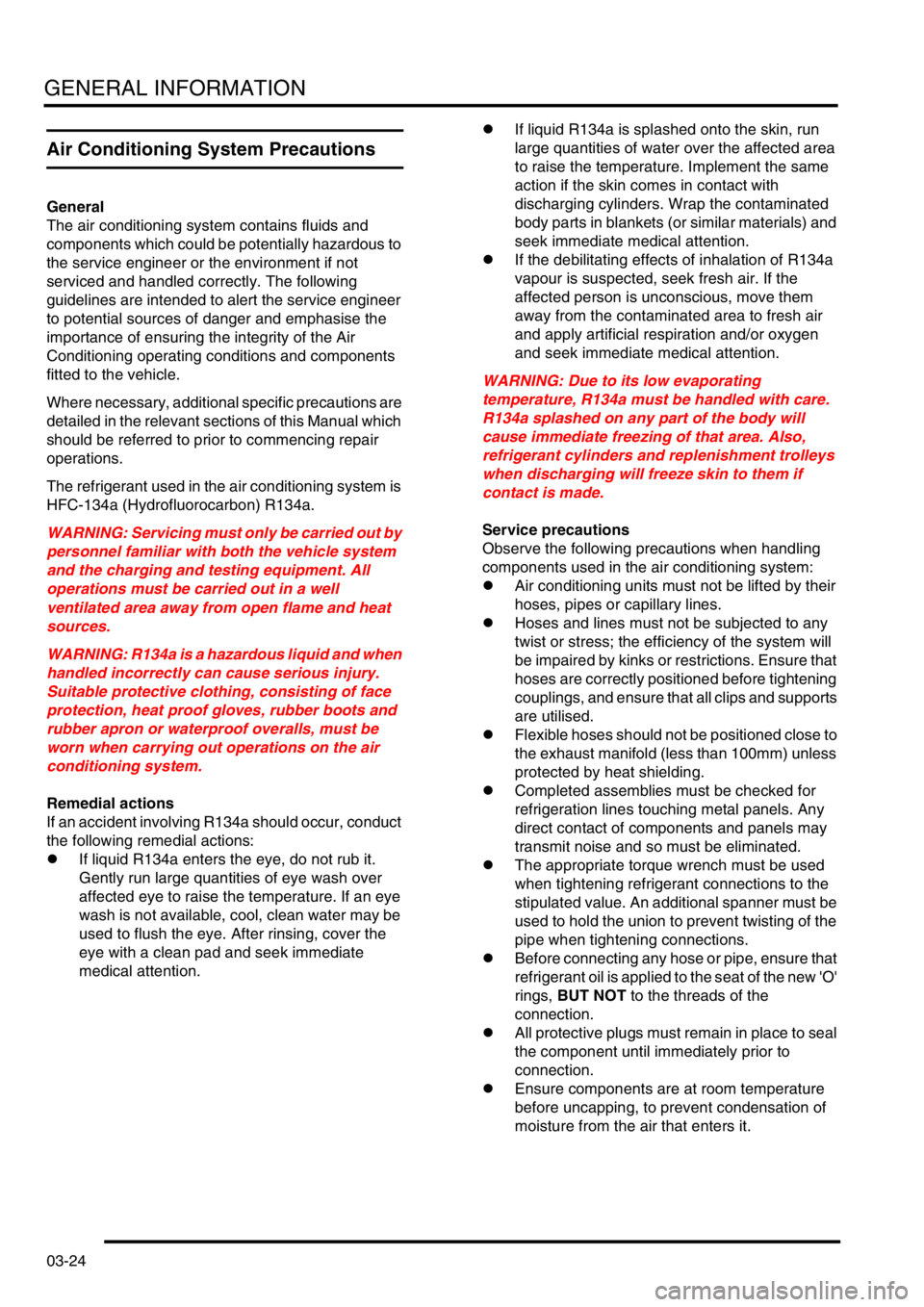
GENERAL INFORMATION
03-24
Air Conditioning System Precautions
General
The air conditioning system contains fluids and
components which could be potentially hazardous to
the service engineer or the environment if not
serviced and handled correctly. The following
guidelines are intended to alert the service engineer
to potential sources of danger and emphasise the
importance of ensuring the integrity of the Air
Conditioning operating conditions and components
fitted to the vehicle.
Where necessary, additional specific precautions are
detailed in the relevant sections of this Manual which
should be referred to prior to commencing repair
operations.
The refrigerant used in the air conditioning system is
HFC-134a (Hydrofluorocarbon) R134a.
WARNING: Servicing must only be carried out by
personnel familiar with both the vehicle system
and the charging and testing equipment. All
operations must be carried out in a well
ventilated area away from open flame and heat
sources.
WARNING: R134a is a hazardous liquid and when
handled incorrectly can cause serious injury.
Suitable protective clothing, consisting of face
protection, heat proof gloves, rubber boots and
rubber apron or waterproof overalls, must be
worn when carrying out operations on the air
conditioning system.
Remedial actions
If an accident involving R134a should occur, conduct
the following remedial actions:
lIf liquid R134a enters the eye, do not rub it.
Gently run large quantities of eye wash over
affected eye to raise the temperature. If an eye
wash is not available, cool, clean water may be
used to flush the eye. After rinsing, cover the
eye with a clean pad and seek immediate
medical attention.lIf liquid R134a is splashed onto the skin, run
large quantities of water over the affected area
to raise the temperature. Implement the same
action if the skin comes in contact with
discharging cylinders. Wrap the contaminated
body parts in blankets (or similar materials) and
seek immediate medical attention.
lIf the debilitating effects of inhalation of R134a
vapour is suspected, seek fresh air. If the
affected person is unconscious, move them
away from the contaminated area to fresh air
and apply artificial respiration and/or oxygen
and seek immediate medical attention.
WARNING: Due to its low evaporating
temperature, R134a must be handled with care.
R134a splashed on any part of the body will
cause immediate freezing of that area. Also,
refrigerant cylinders and replenishment trolleys
when discharging will freeze skin to them if
contact is made.
Service precautions
Observe the following precautions when handling
components used in the air conditioning system:
lAir conditioning units must not be lifted by their
hoses, pipes or capillary lines.
lHoses and lines must not be subjected to any
twist or stress; the efficiency of the system will
be impaired by kinks or restrictions. Ensure that
hoses are correctly positioned before tightening
couplings, and ensure that all clips and supports
are utilised.
lFlexible hoses should not be positioned close to
the exhaust manifold (less than 100mm) unless
protected by heat shielding.
lCompleted assemblies must be checked for
refrigeration lines touching metal panels. Any
direct contact of components and panels may
transmit noise and so must be eliminated.
lThe appropriate torque wrench must be used
when tightening refrigerant connections to the
stipulated value. An additional spanner must be
used to hold the union to prevent twisting of the
pipe when tightening connections.
lBefore connecting any hose or pipe, ensure that
refrigerant oil is applied to the seat of the new 'O'
rings, BUT NOT to the threads of the
connection.
lAll protective plugs must remain in place to seal
the component until immediately prior to
connection.
lEnsure components are at room temperature
before uncapping, to prevent condensation of
moisture from the air that enters it.
Page 61 of 1672
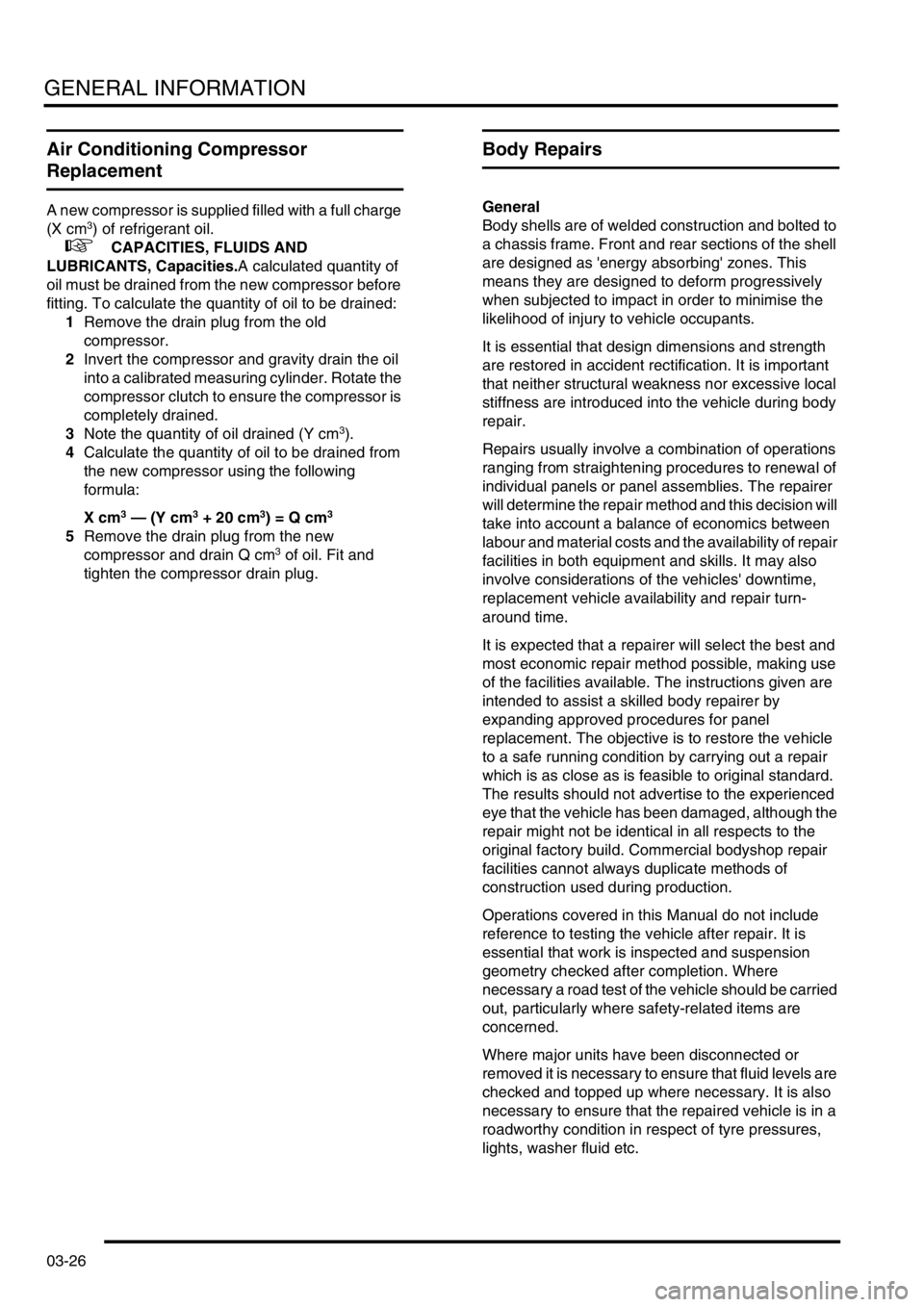
GENERAL INFORMATION
03-26
Air Conditioning Compressor
Replacement
A new compressor is supplied filled with a full charge
(X cm3) of refrigerant oil.
+ CAPACITIES, FLUIDS AND
LUBRICANTS, Capacities.A calculated quantity of
oil must be drained from the new compressor before
fitting. To calculate the quantity of oil to be drained:
1Remove the drain plug from the old
compressor.
2Invert the compressor and gravity drain the oil
into a calibrated measuring cylinder. Rotate the
compressor clutch to ensure the compressor is
completely drained.
3Note the quantity of oil drained (Y cm
3).
4Calculate the quantity of oil to be drained from
the new compressor using the following
formula:
X cm
3 — (Y cm3 + 20 cm3) = Q cm3
5Remove the drain plug from the new
compressor and drain Q cm3 of oil. Fit and
tighten the compressor drain plug.
Body Repairs
General
Body shells are of welded construction and bolted to
a chassis frame. Front and rear sections of the shell
are designed as 'energy absorbing' zones. This
means they are designed to deform progressively
when subjected to impact in order to minimise the
likelihood of injury to vehicle occupants.
It is essential that design dimensions and strength
are restored in accident rectification. It is important
that neither structural weakness nor excessive local
stiffness are introduced into the vehicle during body
repair.
Repairs usually involve a combination of operations
ranging from straightening procedures to renewal of
individual panels or panel assemblies. The repairer
will determine the repair method and this decision will
take into account a balance of economics between
labour and material costs and the availability of repair
facilities in both equipment and skills. It may also
involve considerations of the vehicles' downtime,
replacement vehicle availability and repair turn-
around time.
It is expected that a repairer will select the best and
most economic repair method possible, making use
of the facilities available. The instructions given are
intended to assist a skilled body repairer by
expanding approved procedures for panel
replacement. The objective is to restore the vehicle
to a safe running condition by carrying out a repair
which is as close as is feasible to original standard.
The results should not advertise to the experienced
eye that the vehicle has been damaged, although the
repair might not be identical in all respects to the
original factory build. Commercial bodyshop repair
facilities cannot always duplicate methods of
construction used during production.
Operations covered in this Manual do not include
reference to testing the vehicle after repair. It is
essential that work is inspected and suspension
geometry checked after completion. Where
necessary a road test of the vehicle should be carried
out, particularly where safety-related items are
concerned.
Where major units have been disconnected or
removed it is necessary to ensure that fluid levels are
checked and topped up where necessary. It is also
necessary to ensure that the repaired vehicle is in a
roadworthy condition in respect of tyre pressures,
lights, washer fluid etc.
Page 106 of 1672
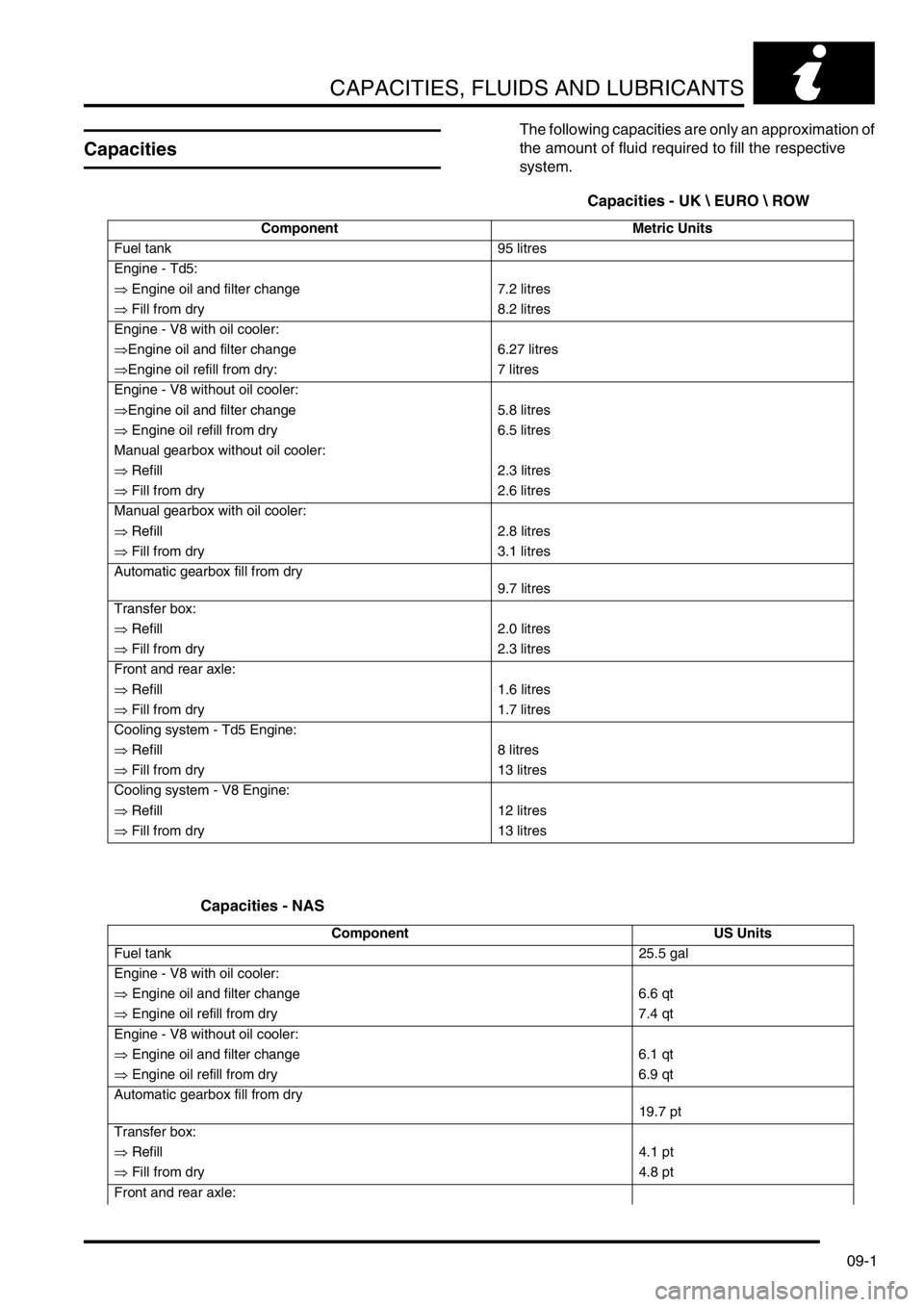
CAPACITIES, FLUIDS AND LUBRICANTS
09-1
CAPACITIES, FLUIDS AND LUBRICANTS
Capacities
The following capacities are only an approximation of
the amount of fluid required to fill the respective
system.
Capacities - UK EURO ROW
Capacities - NAS
Component Metric Units
Fuel tank 95 litres
Engine - Td5:
Engine oil and filter change 7.2 litres
Fill from dry 8.2 litres
Engine - V8 with oil cooler:
Engine oil and filter change 6.27 litres
Engine oil refill from dry: 7 litres
Engine - V8 without oil cooler:
Engine oil and filter change 5.8 litres
Engine oil refill from dry 6.5 litres
Manual gearbox without oil cooler:
Refill 2.3 litres
Fill from dry 2.6 litres
Manual gearbox with oil cooler:
Refill 2.8 litres
Fill from dry 3.1 litres
Automatic gearbox fill from dry
9.7 litres
Transfer box:
Refill 2.0 litres
Fill from dry 2.3 litres
Front and rear axle:
Refill 1.6 litres
Fill from dry 1.7 litres
Cooling system - Td5 Engine:
Refill 8 litres
Fill from dry 13 litres
Cooling system - V8 Engine:
Refill 12 litres
Fill from dry 13 litres
Component US Units
Fuel tank25.5 gal
Engine - V8 with oil cooler:
Engine oil and filter change 6.6 qt
Engine oil refill from dry 7.4 qt
Engine - V8 without oil cooler:
Engine oil and filter change 6.1 qt
Engine oil refill from dry 6.9 qt
Automatic gearbox fill from dry
19.7 pt
Transfer box:
Refill4.1 pt
Fill from dry 4.8 pt
Front and rear axle:
Page 164 of 1672
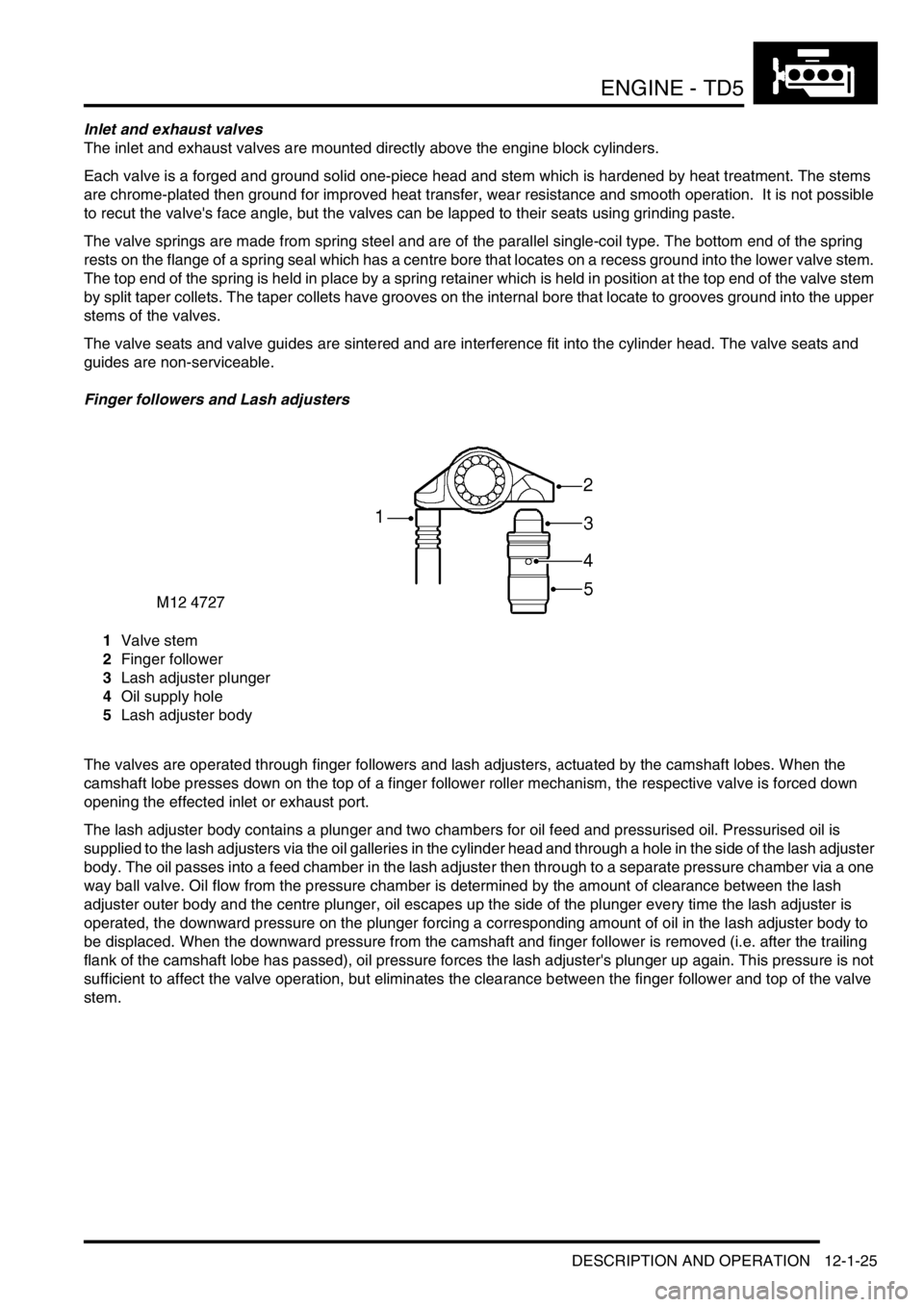
ENGINE - TD5
DESCRIPTION AND OPERATION 12-1-25
Inlet and exhaust valves
The inlet and exhaust valves are mounted directly above the engine block cylinders.
Each valve is a forged and ground solid one-piece head and stem which is hardened by heat treatment. The stems
are chrome-plated then ground for improved heat transfer, wear resistance and smooth operation. It is not possible
to recut the valve's face angle, but the valves can be lapped to their seats using grinding paste.
The valve springs are made from spring steel and are of the parallel single-coil type. The bottom end of the spring
rests on the flange of a spring seal which has a centre bore that locates on a recess ground into the lower valve stem.
The top end of the spring is held in place by a spring retainer which is held in position at the top end of the valve stem
by split taper collets. The taper collets have grooves on the internal bore that locate to grooves ground into the upper
stems of the valves.
The valve seats and valve guides are sintered and are interference fit into the cylinder head. The valve seats and
guides are non-serviceable.
Finger followers and Lash adjusters
1Valve stem
2Finger follower
3Lash adjuster plunger
4Oil supply hole
5Lash adjuster body
The valves are operated through finger followers and lash adjusters, actuated by the camshaft lobes. When the
camshaft lobe presses down on the top of a finger follower roller mechanism, the respective valve is forced down
opening the effected inlet or exhaust port.
The lash adjuster body contains a plunger and two chambers for oil feed and pressurised oil. Pressurised oil is
supplied to the lash adjusters via the oil galleries in the cylinder head and through a hole in the side of the lash adjuster
body. The oil passes into a feed chamber in the lash adjuster then through to a separate pressure chamber via a one
way ball valve. Oil flow from the pressure chamber is determined by the amount of clearance between the lash
adjuster outer body and the centre plunger, oil escapes up the side of the plunger every time the lash adjuster is
operated, the downward pressure on the plunger forcing a corresponding amount of oil in the lash adjuster body to
be displaced. When the downward pressure from the camshaft and finger follower is removed (i.e. after the trailing
flank of the camshaft lobe has passed), oil pressure forces the lash adjuster's plunger up again. This pressure is not
sufficient to affect the valve operation, but eliminates the clearance between the finger follower and top of the valve
stem.
Page 218 of 1672
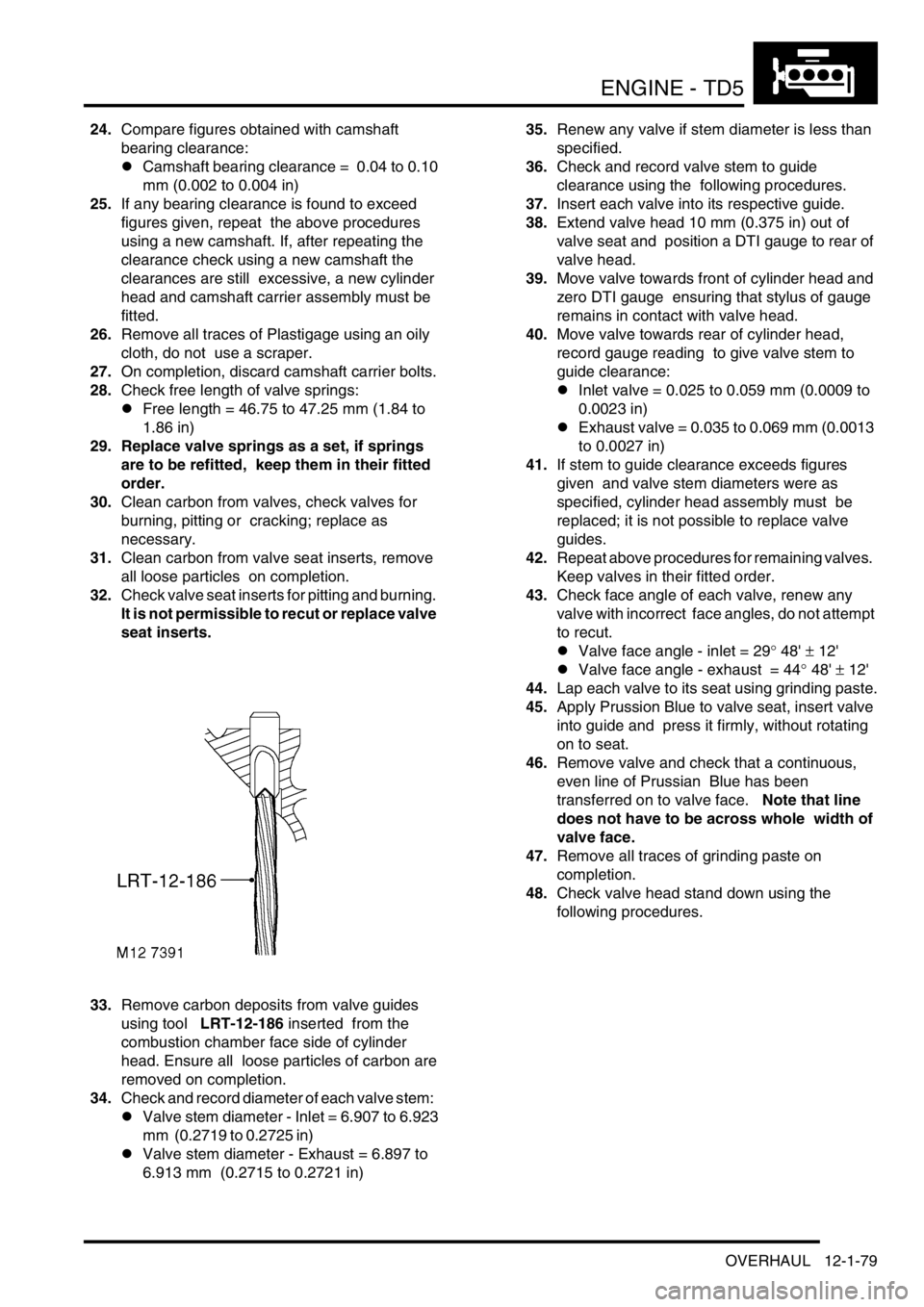
ENGINE - TD5
OVERHAUL 12-1-79
24.Compare figures obtained with camshaft
bearing clearance:
lCamshaft bearing clearance = 0.04 to 0.10
mm (0.002 to 0.004 in)
25.If any bearing clearance is found to exceed
figures given, repeat the above procedures
using a new camshaft. If, after repeating the
clearance check using a new camshaft the
clearances are still excessive, a new cylinder
head and camshaft carrier assembly must be
fitted.
26.Remove all traces of Plastigage using an oily
cloth, do not use a scraper.
27.On completion, discard camshaft carrier bolts.
28.Check free length of valve springs:
lFree length = 46.75 to 47.25 mm (1.84 to
1.86 in)
29. Replace valve springs as a set, if springs
are to be refitted, keep them in their fitted
order.
30.Clean carbon from valves, check valves for
burning, pitting or cracking; replace as
necessary.
31.Clean carbon from valve seat inserts, remove
all loose particles on completion.
32.Check valve seat inserts for pitting and burning.
It is not permissible to recut or replace valve
seat inserts.
33.Remove carbon deposits from valve guides
using tool LRT-12-186 inserted from the
combustion chamber face side of cylinder
head. Ensure all loose particles of carbon are
removed on completion.
34.Check and record diameter of each valve stem:
lValve stem diameter - Inlet = 6.907 to 6.923
mm (0.2719 to 0.2725 in)
lValve stem diameter - Exhaust = 6.897 to
6.913 mm (0.2715 to 0.2721 in)35.Renew any valve if stem diameter is less than
specified.
36.Check and record valve stem to guide
clearance using the following procedures.
37.Insert each valve into its respective guide.
38.Extend valve head 10 mm (0.375 in) out of
valve seat and position a DTI gauge to rear of
valve head.
39.Move valve towards front of cylinder head and
zero DTI gauge ensuring that stylus of gauge
remains in contact with valve head.
40.Move valve towards rear of cylinder head,
record gauge reading to give valve stem to
guide clearance:
lInlet valve = 0.025 to 0.059 mm (0.0009 to
0.0023 in)
lExhaust valve = 0.035 to 0.069 mm (0.0013
to 0.0027 in)
41.If stem to guide clearance exceeds figures
given and valve stem diameters were as
specified, cylinder head assembly must be
replaced; it is not possible to replace valve
guides.
42.Repeat above procedures for remaining valves.
Keep valves in their fitted order.
43.Check face angle of each valve, renew any
valve with incorrect face angles, do not attempt
to recut.
lValve face angle - inlet = 29
° 48' ± 12'
lValve face angle - exhaust = 44
° 48' ± 12'
44.Lap each valve to its seat using grinding paste.
45.Apply Prussion Blue to valve seat, insert valve
into guide and press it firmly, without rotating
on to seat.
46.Remove valve and check that a continuous,
even line of Prussian Blue has been
transferred on to valve face. Note that line
does not have to be across whole width of
valve face.
47.Remove all traces of grinding paste on
completion.
48.Check valve head stand down using the
following procedures.
Page 219 of 1672
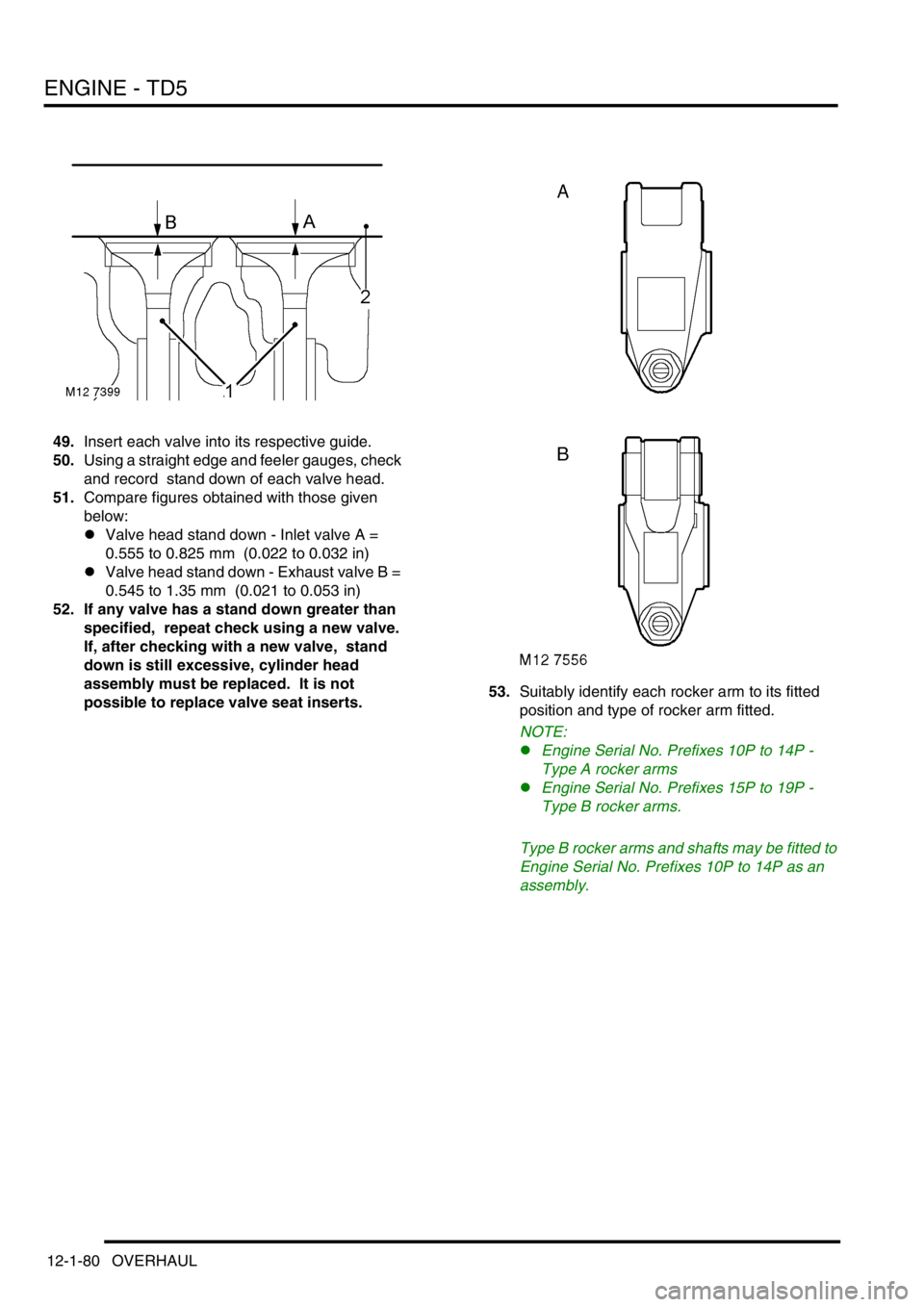
ENGINE - TD5
12-1-80 OVERHAUL
49.Insert each valve into its respective guide.
50.Using a straight edge and feeler gauges, check
and record stand down of each valve head.
51.Compare figures obtained with those given
below:
lValve head stand down - Inlet valve A =
0.555 to 0.825 mm (0.022 to 0.032 in)
lValve head stand down - Exhaust valve B =
0.545 to 1.35 mm (0.021 to 0.053 in)
52. If any valve has a stand down greater than
specified, repeat check using a new valve.
If, after checking with a new valve, stand
down is still excessive, cylinder head
assembly must be replaced. It is not
possible to replace valve seat inserts.53.Suitably identify each rocker arm to its fitted
position and type of rocker arm fitted.
NOTE:
lEngine Serial No. Prefixes 10P to 14P -
Type A rocker arms
lEngine Serial No. Prefixes 15P to 19P -
Type B rocker arms.
Type B rocker arms and shafts may be fitted to
Engine Serial No. Prefixes 10P to 14P as an
assembly.