sensor LAND ROVER FREELANDER 2001 User Guide
[x] Cancel search | Manufacturer: LAND ROVER, Model Year: 2001, Model line: FREELANDER, Model: LAND ROVER FREELANDER 2001Pages: 1007, PDF Size: 23.47 MB
Page 50 of 1007
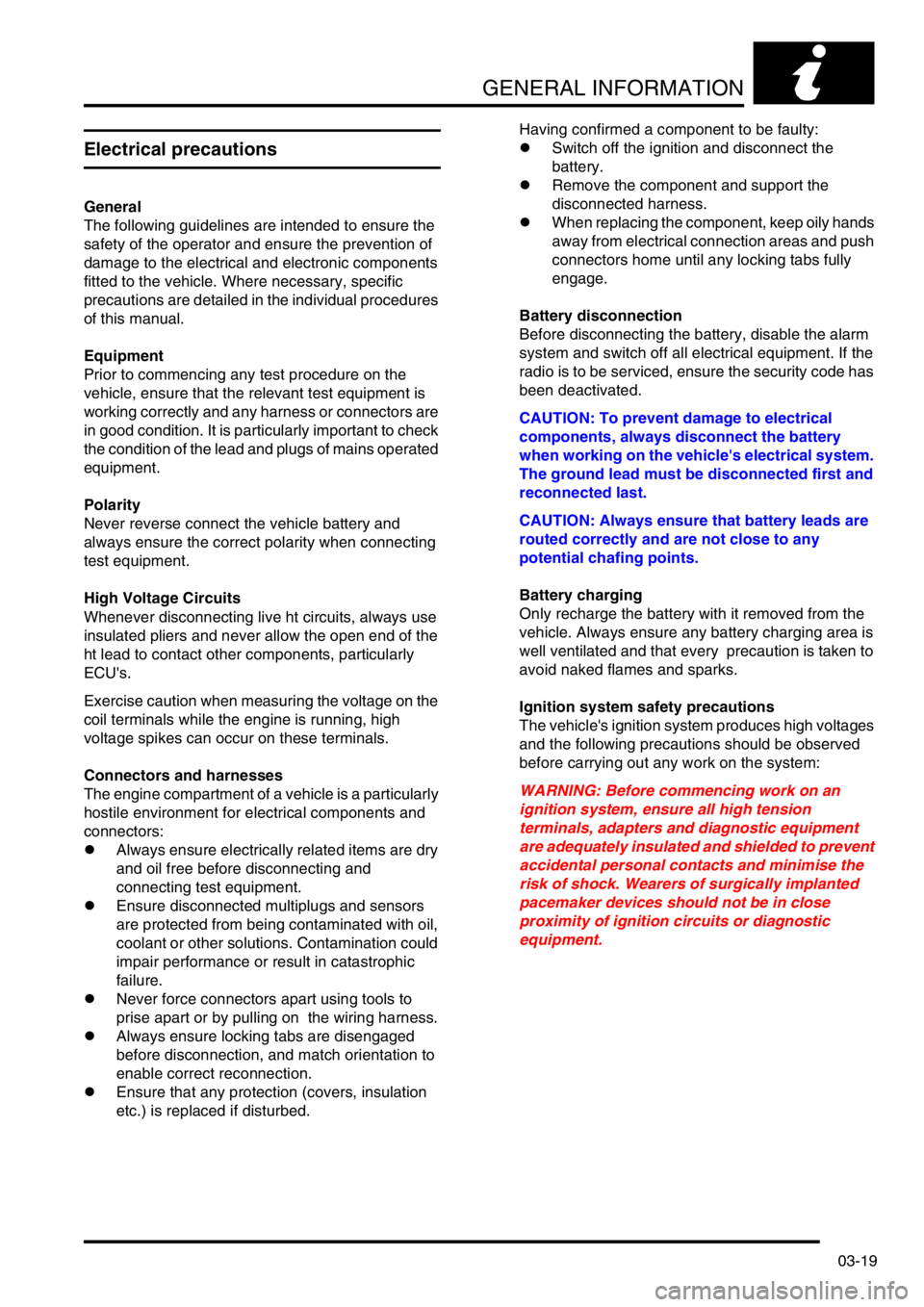
GENERAL INFORMATION
03-19
Electrical precautions
General
The following guidelines are intended to ensure the
safety of the operator and ensure the prevention of
damage to the electrical and electronic components
fitted to the vehicle. Where necessary, specific
precautions are detailed in the individual procedures
of this manual.
Equipment
Prior to commencing any test procedure on the
vehicle, ensure that the relevant test equipment is
working correctly and any harness or connectors are
in good condition. It is particularly important to check
the condition of the lead and plugs of mains operated
equipment.
Polarity
Never reverse connect the vehicle battery and
always ensure the correct polarity when connecting
test equipment.
High Voltage Circuits
Whenever disconnecting live ht circuits, always use
insulated pliers and never allow the open end of the
ht lead to contact other components, particularly
ECU's.
Exercise caution when measuring the voltage on the
coil terminals while the engine is running, high
voltage spikes can occur on these terminals.
Connectors and harnesses
The engine compartment of a vehicle is a particularly
hostile environment for electrical components and
connectors:
lAlways ensure electrically related items are dry
and oil free before disconnecting and
connecting test equipment.
lEnsure disconnected multiplugs and sensors
are protected from being contaminated with oil,
coolant or other solutions. Contamination could
impair performance or result in catastrophic
failure.
lNever force connectors apart using tools to
prise apart or by pulling on the wiring harness.
lAlways ensure locking tabs are disengaged
before disconnection, and match orientation to
enable correct reconnection.
lEnsure that any protection (covers, insulation
etc.) is replaced if disturbed.Having confirmed a component to be faulty:
lSwitch off the ignition and disconnect the
battery.
lRemove the component and support the
disconnected harness.
lWhen replacing the component, keep oily hands
away from electrical connection areas and push
connectors home until any locking tabs fully
engage.
Battery disconnection
Before disconnecting the battery, disable the alarm
system and switch off all electrical equipment. If the
radio is to be serviced, ensure the security code has
been deactivated.
CAUTION: To prevent damage to electrical
components, always disconnect the battery
when working on the vehicle's electrical system.
The ground lead must be disconnected first and
reconnected last.
CAUTION: Always ensure that battery leads are
routed correctly and are not close to any
potential chafing points.
Battery charging
Only recharge the battery with it removed from the
vehicle. Always ensure any battery charging area is
well ventilated and that every precaution is taken to
avoid naked flames and sparks.
Ignition system safety precautions
The vehicle's ignition system produces high voltages
and the following precautions should be observed
before carrying out any work on the system:
WARNING: Before commencing work on an
ignition system, ensure all high tension
terminals, adapters and diagnostic equipment
are adequately insulated and shielded to prevent
accidental personal contacts and minimise the
risk of shock. Wearers of surgically implanted
pacemaker devices should not be in close
proximity of ignition circuits or diagnostic
equipment.
Page 71 of 1007
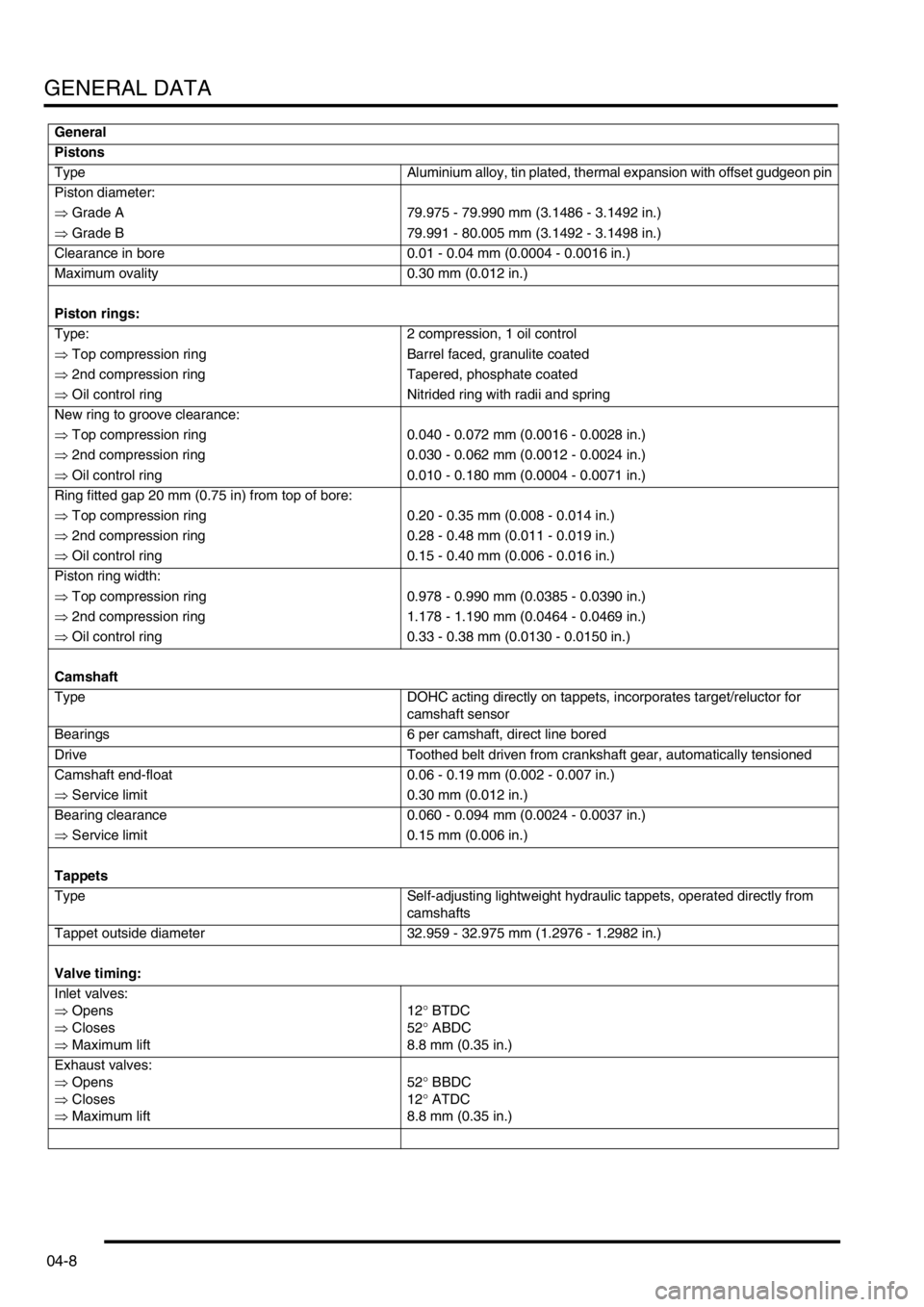
GENERAL DATA
04-8
Pistons
Type Aluminium alloy, tin plated, thermal expansion with offset gudgeon pin
Piston diameter:
⇒ Grade A 79.975 - 79.990 mm (3.1486 - 3.1492 in.)
⇒ Grade B 79.991 - 80.005 mm (3.1492 - 3.1498 in.)
Clearance in bore 0.01 - 0.04 mm (0.0004 - 0.0016 in.)
Maximum ovality 0.30 mm (0.012 in.)
Piston rings:
Type: 2 compression, 1 oil control
⇒ Top compression ring Barrel faced, granulite coated
⇒ 2nd compression ring Tapered, phosphate coated
⇒ Oil control ring Nitrided ring with radii and spring
New ring to groove clearance:
⇒ Top compression ring 0.040 - 0.072 mm (0.0016 - 0.0028 in.)
⇒ 2nd compression ring 0.030 - 0.062 mm (0.0012 - 0.0024 in.)
⇒ Oil control ring 0.010 - 0.180 mm (0.0004 - 0.0071 in.)
Ring fitted gap 20 mm (0.75 in) from top of bore:
⇒ Top compression ring 0.20 - 0.35 mm (0.008 - 0.014 in.)
⇒ 2nd compression ring 0.28 - 0.48 mm (0.011 - 0.019 in.)
⇒ Oil control ring 0.15 - 0.40 mm (0.006 - 0.016 in.)
Piston ring width:
⇒ Top compression ring 0.978 - 0.990 mm (0.0385 - 0.0390 in.)
⇒ 2nd compression ring 1.178 - 1.190 mm (0.0464 - 0.0469 in.)
⇒ Oil control ring 0.33 - 0.38 mm (0.0130 - 0.0150 in.)
Camshaft
Type DOHC acting directly on tappets, incorporates target/reluctor for
camshaft sensor
Bearings 6 per camshaft, direct line bored
Drive Toothed belt driven from crankshaft gear, automatically tensioned
Camshaft end-float 0.06 - 0.19 mm (0.002 - 0.007 in.)
⇒ Service limit 0.30 mm (0.012 in.)
Bearing clearance 0.060 - 0.094 mm (0.0024 - 0.0037 in.)
⇒ Service limit 0.15 mm (0.006 in.)
Tappets
Type Self-adjusting lightweight hydraulic tappets, operated directly from
camshafts
Tappet outside diameter 32.959 - 32.975 mm (1.2976 - 1.2982 in.)
Valve timing:
Inlet valves:
⇒ Opens
⇒ Closes
⇒ Maximum lift12° BTDC
52° ABDC
8.8 mm (0.35 in.)
Exhaust valves:
⇒ Opens
⇒ Closes
⇒ Maximum lift52° BBDC
12° ATDC
8.8 mm (0.35 in.) General
Page 73 of 1007

GENERAL DATA
04-10
Sensors:
Crankshaft sensor Siemens NSC 100630, Hall effect acting on profiled target on flywheel
Camshaft sensor:
⇒ Make / Type ITT NSC 100610 +0, Hall effect acting on camshaft reluctor ring
⇒ Ring TGN 100050
Oxygen sensor:
⇒ Make / Type NTK - MHK 100720
⇒ Heating element (nominal) 7 Watts
⇒ Sensor voltage - High≈ 900 mV
⇒ Sensor voltage - Low≈ 40 mV
Throttle potentiometer:
⇒ Make / Type CTS - MJC 100020
⇒ Total track resistance 4 kΩ ± 20%
⇒ Sensor supply voltage 5V ± 4%
TMAP sensor:
⇒ Make / Type Motorola - MHK 100820
⇒ Sensor supply voltage 5V ± 4%
Coolant temperature sensor:
⇒ Make / Type AB Electronik - MEK 100170; NTC thermistor bead
Oil temperature sensor
⇒ Make / Type AB Elektronik - MEK100170; NTC thermistor bead General
Page 77 of 1007
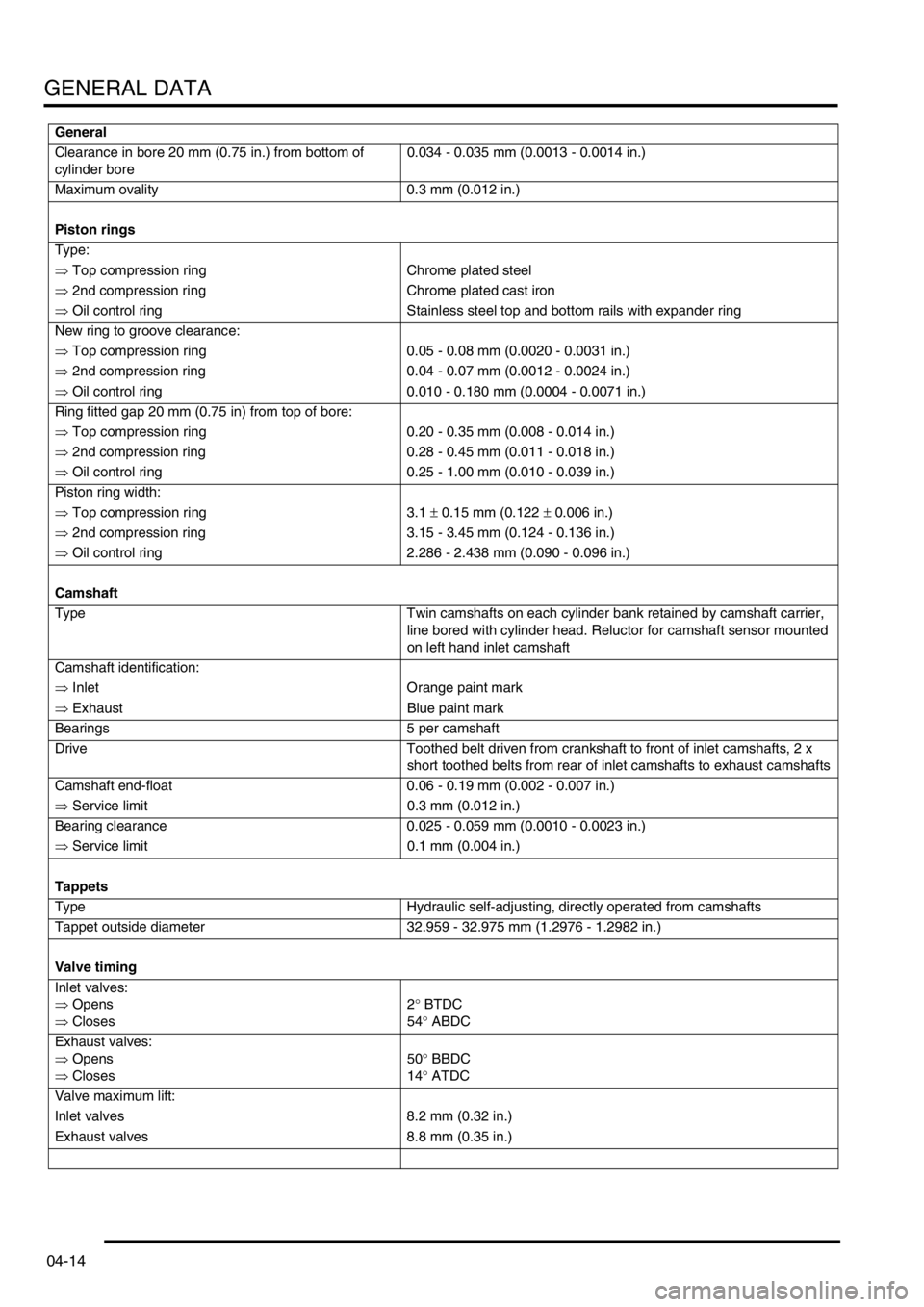
GENERAL DATA
04-14
Clearance in bore 20 mm (0.75 in.) from bottom of
cylinder bore0.034 - 0.035 mm (0.0013 - 0.0014 in.)
Maximum ovality 0.3 mm (0.012 in.)
Piston rings
Type:
⇒ Top compression ring Chrome plated steel
⇒ 2nd compression ring Chrome plated cast iron
⇒ Oil control ring Stainless steel top and bottom rails with expander ring
New ring to groove clearance:
⇒ Top compression ring 0.05 - 0.08 mm (0.0020 - 0.0031 in.)
⇒ 2nd compression ring 0.04 - 0.07 mm (0.0012 - 0.0024 in.)
⇒ Oil control ring 0.010 - 0.180 mm (0.0004 - 0.0071 in.)
Ring fitted gap 20 mm (0.75 in) from top of bore:
⇒ Top compression ring 0.20 - 0.35 mm (0.008 - 0.014 in.)
⇒ 2nd compression ring 0.28 - 0.45 mm (0.011 - 0.018 in.)
⇒ Oil control ring 0.25 - 1.00 mm (0.010 - 0.039 in.)
Piston ring width:
⇒ Top compression ring 3.1 ± 0.15 mm (0.122 ± 0.006 in.)
⇒ 2nd compression ring 3.15 - 3.45 mm (0.124 - 0.136 in.)
⇒ Oil control ring 2.286 - 2.438 mm (0.090 - 0.096 in.)
Camshaft
Type Twin camshafts on each cylinder bank retained by camshaft carrier,
line bored with cylinder head. Reluctor for camshaft sensor mounted
on left hand inlet camshaft
Camshaft identification:
⇒ Inlet Orange paint mark
⇒ Exhaust Blue paint mark
Bearings 5 per camshaft
Drive Toothed belt driven from crankshaft to front of inlet camshafts, 2 x
short toothed belts from rear of inlet camshafts to exhaust camshafts
Camshaft end-float 0.06 - 0.19 mm (0.002 - 0.007 in.)
⇒ Service limit 0.3 mm (0.012 in.)
Bearing clearance 0.025 - 0.059 mm (0.0010 - 0.0023 in.)
⇒ Service limit 0.1 mm (0.004 in.)
Tappets
Type Hydraulic self-adjusting, directly operated from camshafts
Tappet outside diameter 32.959 - 32.975 mm (1.2976 - 1.2982 in.)
Valve timing
Inlet valves:
⇒ Opens
⇒ Closes2° BTDC
54° ABDC
Exhaust valves:
⇒ Opens
⇒ Closes50° BBDC
14° ATDC
Valve maximum lift:
Inlet valves 8.2 mm (0.32 in.)
Exhaust valves 8.8 mm (0.35 in.) General
Page 79 of 1007
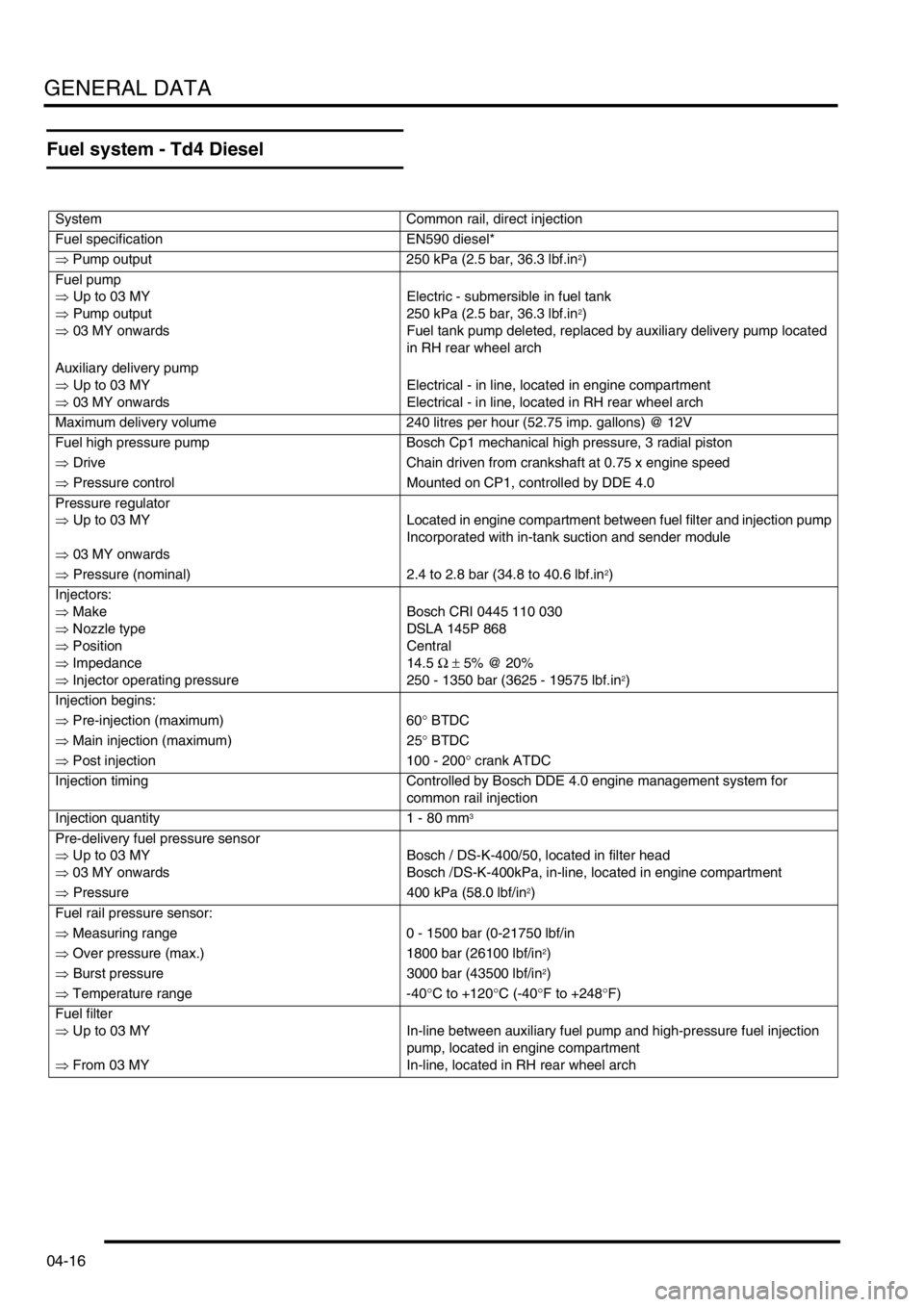
GENERAL DATA
04-16
Fuel system - Td4 Diesel
System Common rail, direct injection
Fuel specification EN590 diesel*
⇒ Pump output 250 kPa (2.5 bar, 36.3 lbf.in
2)
Fuel pump
⇒ Up to 03 MY
⇒ Pump output
⇒ 03 MY onwardsElectric - submersible in fuel tank
250 kPa (2.5 bar, 36.3 lbf.in
2)
Fuel tank pump deleted, replaced by auxiliary delivery pump located
in RH rear wheel arch
Auxiliary delivery pump
⇒ Up to 03 MY
⇒ 03 MY onwardsElectrical - in line, located in engine compartment
Electrical - in line, located in RH rear wheel arch
Maximum delivery volume 240 litres per hour (52.75 imp. gallons) @ 12V
Fuel high pressure pump Bosch Cp1 mechanical high pressure, 3 radial piston
⇒ Drive Chain driven from crankshaft at 0.75 x engine speed
⇒ Pressure control Mounted on CP1, controlled by DDE 4.0
Pressure regulator
⇒ Up to 03 MY
⇒ 03 MY onwardsLocated in engine compartment between fuel filter and injection pump
Incorporated with in-tank suction and sender module
⇒ Pressure (nominal) 2.4 to 2.8 bar (34.8 to 40.6 lbf.in
2)
Injectors:
⇒ Make
⇒ Nozzle type
⇒ Position
⇒ Impedance
⇒ Injector operating pressureBosch CRI 0445 110 030
DSLA 145P 868
Central
14.5 Ω ± 5% @ 20%
250 - 1350 bar (3625 - 19575 lbf.in
2)
Injection begins:
⇒ Pre-injection (maximum) 60° BTDC
⇒ Main injection (maximum) 25° BTDC
⇒ Post injection 100 - 200° crank ATDC
Injection timing Controlled by Bosch DDE 4.0 engine management system for
common rail injection
Injection quantity 1 - 80 mm
3
Pre-delivery fuel pressure sensor
⇒ Up to 03 MY
⇒ 03 MY onwardsBosch / DS-K-400/50, located in filter head
Bosch /DS-K-400kPa, in-line, located in engine compartment
⇒ Pressure 400 kPa (58.0 lbf/in
2)
Fuel rail pressure sensor:
⇒ Measuring range 0 - 1500 bar (0-21750 lbf/in
⇒ Over pressure (max.) 1800 bar (26100 lbf/in
2)
⇒ Burst pressure 3000 bar (43500 lbf/in
2)
⇒ Temperature range -40°C to +120°C (-40°F to +248°F)
Fuel filter
⇒ Up to 03 MY
⇒ From 03 MYIn-line between auxiliary fuel pump and high-pressure fuel injection
pump, located in engine compartment
In-line, located in RH rear wheel arch
Page 94 of 1007
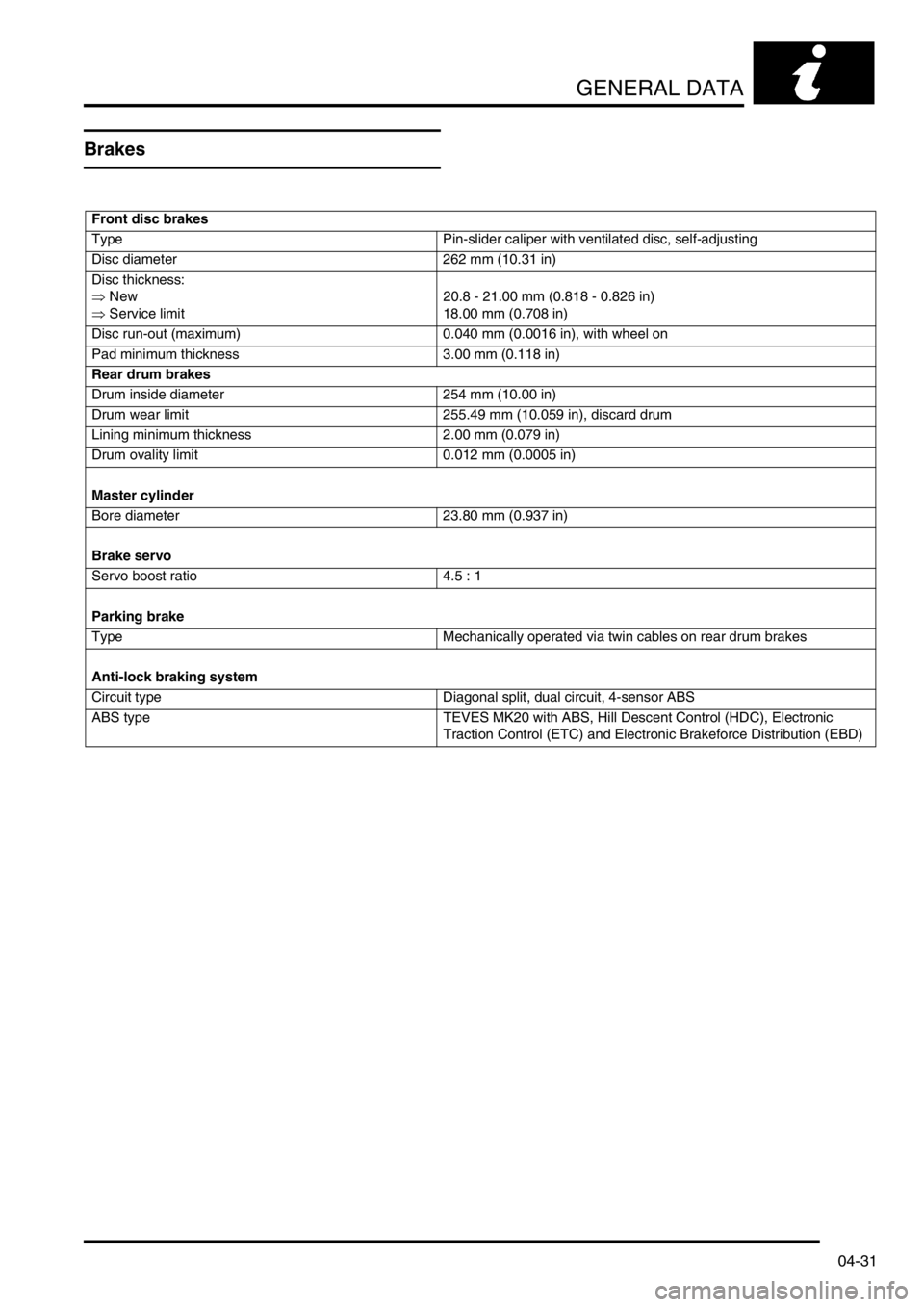
GENERAL DATA
04-31
Brakes
Front disc brakes
Type Pin-slider caliper with ventilated disc, self-adjusting
Disc diameter 262 mm (10.31 in)
Disc thickness:
⇒ New
⇒ Service limit20.8 - 21.00 mm (0.818 - 0.826 in)
18.00 mm (0.708 in)
Disc run-out (maximum) 0.040 mm (0.0016 in), with wheel on
Pad minimum thickness 3.00 mm (0.118 in)
Rear drum brakes
Drum inside diameter 254 mm (10.00 in)
Drum wear limit 255.49 mm (10.059 in), discard drum
Lining minimum thickness 2.00 mm (0.079 in)
Drum ovality limit 0.012 mm (0.0005 in)
Master cylinder
Bore diameter 23.80 mm (0.937 in)
Brake servo
Servo boost ratio 4.5 : 1
Parking brake
Type Mechanically operated via twin cables on rear drum brakes
Anti-lock braking system
Circuit type Diagonal split, dual circuit, 4-sensor ABS
ABS type TEVES MK20 with ABS, Hill Descent Control (HDC), Electronic
Traction Control (ETC) and Electronic Brakeforce Distribution (EBD)
Page 96 of 1007
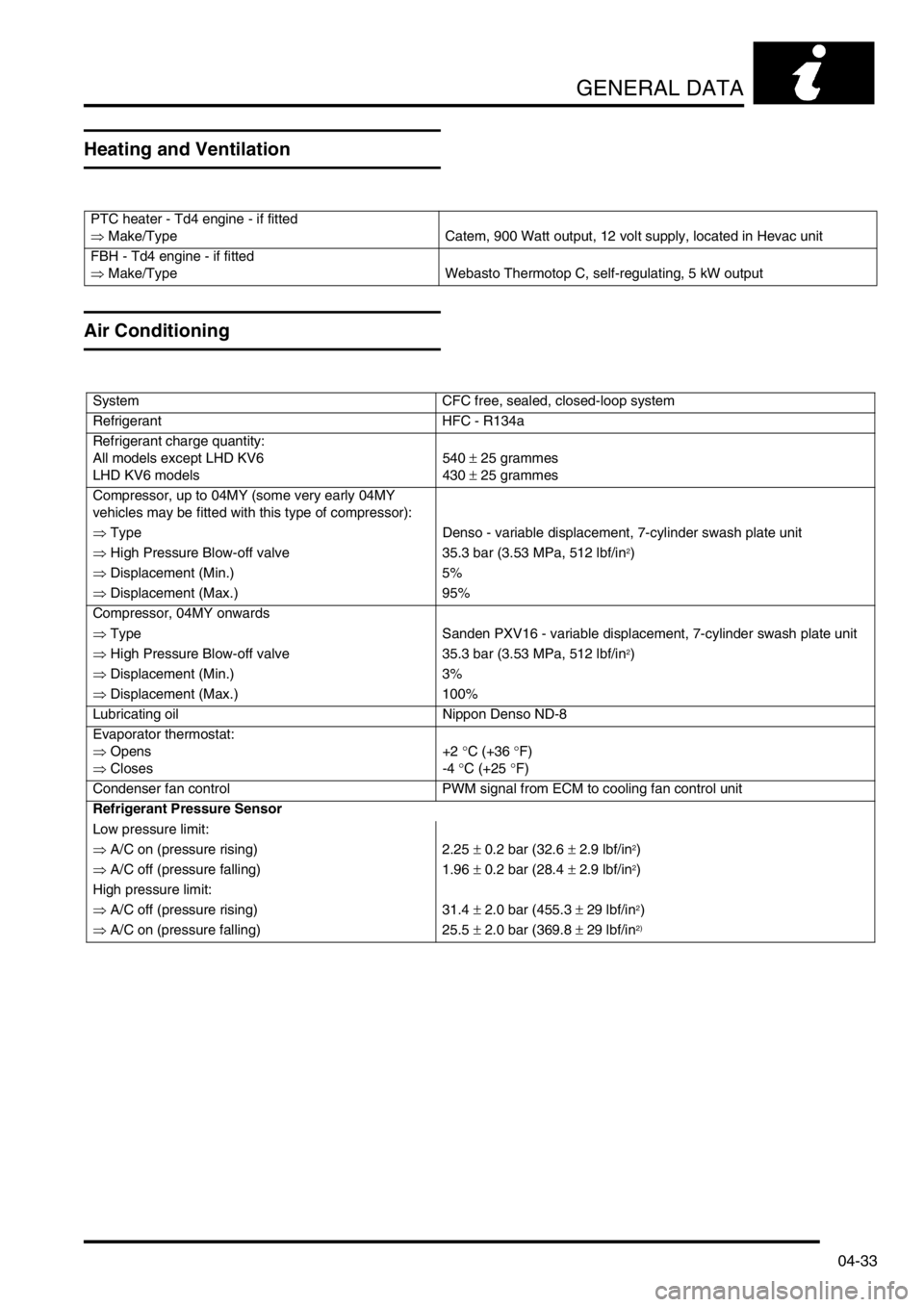
GENERAL DATA
04-33
Heating and Ventilation
Air Conditioning
PTC heater - Td4 engine - if fitted
⇒ Make/Type Catem, 900 Watt output, 12 volt supply, located in Hevac unit
FBH - Td4 engine - if fitted
⇒ Make/Type Webasto Thermotop C, self-regulating, 5 kW output
System CFC free, sealed, closed-loop system
Refrigerant HFC - R134a
Refrigerant charge quantity:
All models except LHD KV6
LHD KV6 models540 ± 25 grammes
430 ± 25 grammes
Compressor, up to 04MY (some very early 04MY
vehicles may be fitted with this type of compressor):
⇒ Type Denso - variable displacement, 7-cylinder swash plate unit
⇒ High Pressure Blow-off valve 35.3 bar (3.53 MPa, 512 lbf/in
2)
⇒ Displacement (Min.) 5%
⇒ Displacement (Max.) 95%
Compressor, 04MY onwards
⇒ Type Sanden PXV16 - variable displacement, 7-cylinder swash plate unit
⇒ High Pressure Blow-off valve 35.3 bar (3.53 MPa, 512 lbf/in
2)
⇒ Displacement (Min.) 3%
⇒ Displacement (Max.) 100%
Lubricating oil Nippon Denso ND-8
Evaporator thermostat:
⇒ Opens
⇒ Closes+2 °C (+36 °F)
-4 °C (+25 °F)
Condenser fan control PWM signal from ECM to cooling fan control unit
Refrigerant Pressure Sensor
Low pressure limit:
⇒ A/C on (pressure rising) 2.25 ± 0.2 bar (32.6 ± 2.9 lbf/in
2)
⇒ A/C off (pressure falling) 1.96 ± 0.2 bar (28.4 ± 2.9 lbf/in
2)
High pressure limit:
⇒ A/C off (pressure rising) 31.4 ± 2.0 bar (455.3 ± 29 lbf/in
2)
⇒ A/C on (pressure falling) 25.5 ± 2.0 bar (369.8 ± 29 lbf/in
2)
Page 107 of 1007
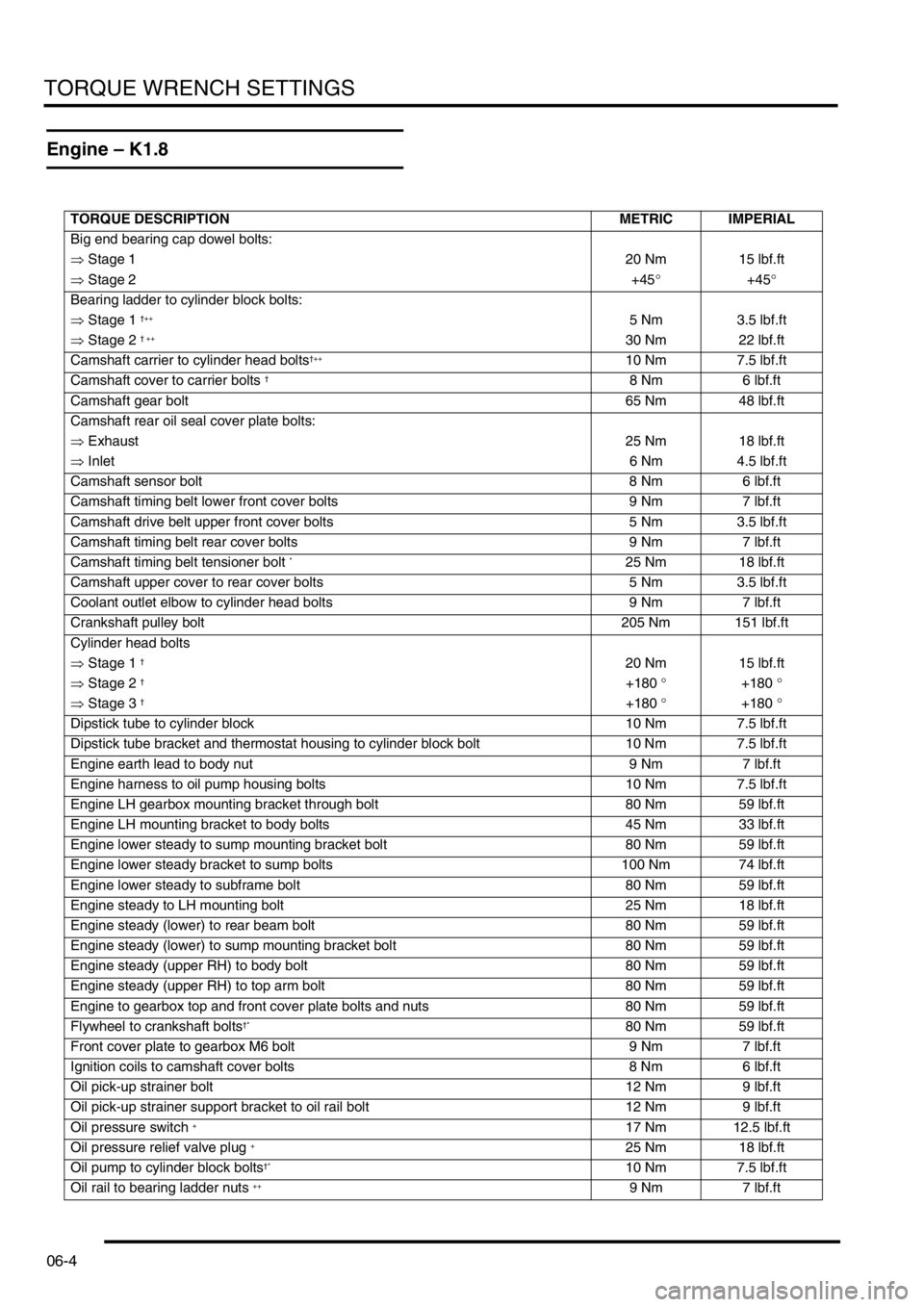
TORQUE WRENCH SETTINGS
06-4
Engine – K1.8
TORQUE DESCRIPTION METRIC IMPERIAL
Big end bearing cap dowel bolts:
⇒ Stage 120 Nm 15 lbf.ft
⇒ Stage 2+45°+45°
Bearing ladder to cylinder block bolts:
⇒ Stage 1
†++5 Nm 3.5 lbf.ft
⇒ Stage 2
† ++30 Nm 22 lbf.ft
Camshaft carrier to cylinder head bolts
†++10 Nm 7.5 lbf.ft
Camshaft cover to carrier bolts
†8 Nm 6 lbf.ft
Camshaft gear bolt 65 Nm 48 lbf.ft
Camshaft rear oil seal cover plate bolts:
⇒ Exhaust25 Nm 18 lbf.ft
⇒ Inlet6 Nm 4.5 lbf.ft
Camshaft sensor bolt 8 Nm 6 lbf.ft
Camshaft timing belt lower front cover bolts 9 Nm 7 lbf.ft
Camshaft drive belt upper front cover bolts 5 Nm 3.5 lbf.ft
Camshaft timing belt rear cover bolts 9 Nm 7 lbf.ft
Camshaft timing belt tensioner bolt
* 25 Nm 18 lbf.ft
Camshaft upper cover to rear cover bolts 5 Nm 3.5 lbf.ft
Coolant outlet elbow to cylinder head bolts 9 Nm 7 lbf.ft
Crankshaft pulley bolt 205 Nm 151 lbf.ft
Cylinder head bolts
⇒ Stage 1
†20 Nm 15 lbf.ft
⇒ Stage 2
†+180 °+180 °
⇒ Stage 3
†+180 °+180 °
Dipstick tube to cylinder block 10 Nm 7.5 lbf.ft
Dipstick tube bracket and thermostat housing to cylinder block bolt 10 Nm 7.5 lbf.ft
Engine earth lead to body nut 9 Nm 7 lbf.ft
Engine harness to oil pump housing bolts 10 Nm 7.5 lbf.ft
Engine LH gearbox mounting bracket through bolt 80 Nm 59 lbf.ft
Engine LH mounting bracket to body bolts 45 Nm 33 lbf.ft
Engine lower steady to sump mounting bracket bolt 80 Nm 59 lbf.ft
Engine lower steady bracket to sump bolts 100 Nm 74 lbf.ft
Engine lower steady to subframe bolt 80 Nm 59 lbf.ft
Engine steady to LH mounting bolt 25 Nm 18 lbf.ft
Engine steady (lower) to rear beam bolt 80 Nm 59 lbf.ft
Engine steady (lower) to sump mounting bracket bolt 80 Nm 59 lbf.ft
Engine steady (upper RH) to body bolt 80 Nm 59 lbf.ft
Engine steady (upper RH) to top arm bolt 80 Nm 59 lbf.ft
Engine to gearbox top and front cover plate bolts and nuts 80 Nm 59 lbf.ft
Flywheel to crankshaft bolts
†*80 Nm 59 lbf.ft
Front cover plate to gearbox M6 bolt 9 Nm 7 lbf.ft
Ignition coils to camshaft cover bolts 8 Nm 6 lbf.ft
Oil pick-up strainer bolt 12 Nm 9 lbf.ft
Oil pick-up strainer support bracket to oil rail bolt 12 Nm 9 lbf.ft
Oil pressure switch
+17 Nm 12.5 lbf.ft
Oil pressure relief valve plug
+25 Nm 18 lbf.ft
Oil pump to cylinder block bolts
†*10 Nm 7.5 lbf.ft
Oil rail to bearing ladder nuts
++9 Nm 7 lbf.ft
Page 108 of 1007
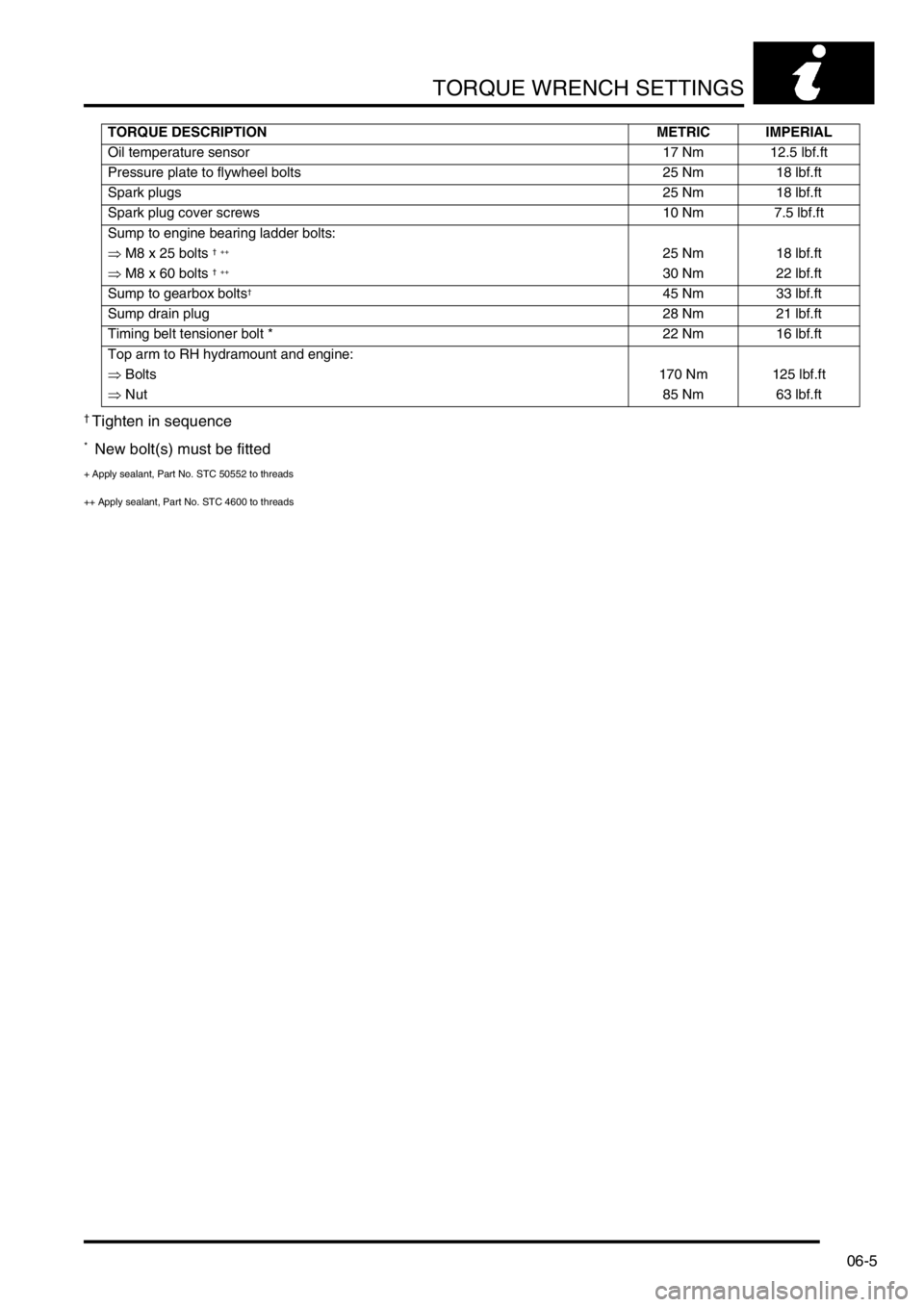
TORQUE WRENCH SETTINGS
06-5
† Tighten in sequence
* New bolt(s) must be fitted
+ Apply sealant, Part No. STC 50552 to threads
++ Apply sealant, Part No. STC 4600 to threads
Oil temperature sensor 17 Nm 12.5 lbf.ft
Pressure plate to flywheel bolts 25 Nm 18 lbf.ft
Spark plugs25 Nm 18 lbf.ft
Spark plug cover screws 10 Nm 7.5 lbf.ft
Sump to engine bearing ladder bolts:
⇒ M8 x 25 bolts
† ++25 Nm 18 lbf.ft
⇒ M8 x 60 bolts
† ++30 Nm 22 lbf.ft
Sump to gearbox bolts
†45 Nm 33 lbf.ft
Sump drain plug28 Nm 21 lbf.ft
Timing belt tensioner bolt * 22 Nm 16 lbf.ft
Top arm to RH hydramount and engine:
⇒ Bolts170 Nm 125 lbf.ft
⇒ Nut85 Nm 63 lbf.ft TORQUE DESCRIPTION METRIC IMPERIAL
Page 109 of 1007
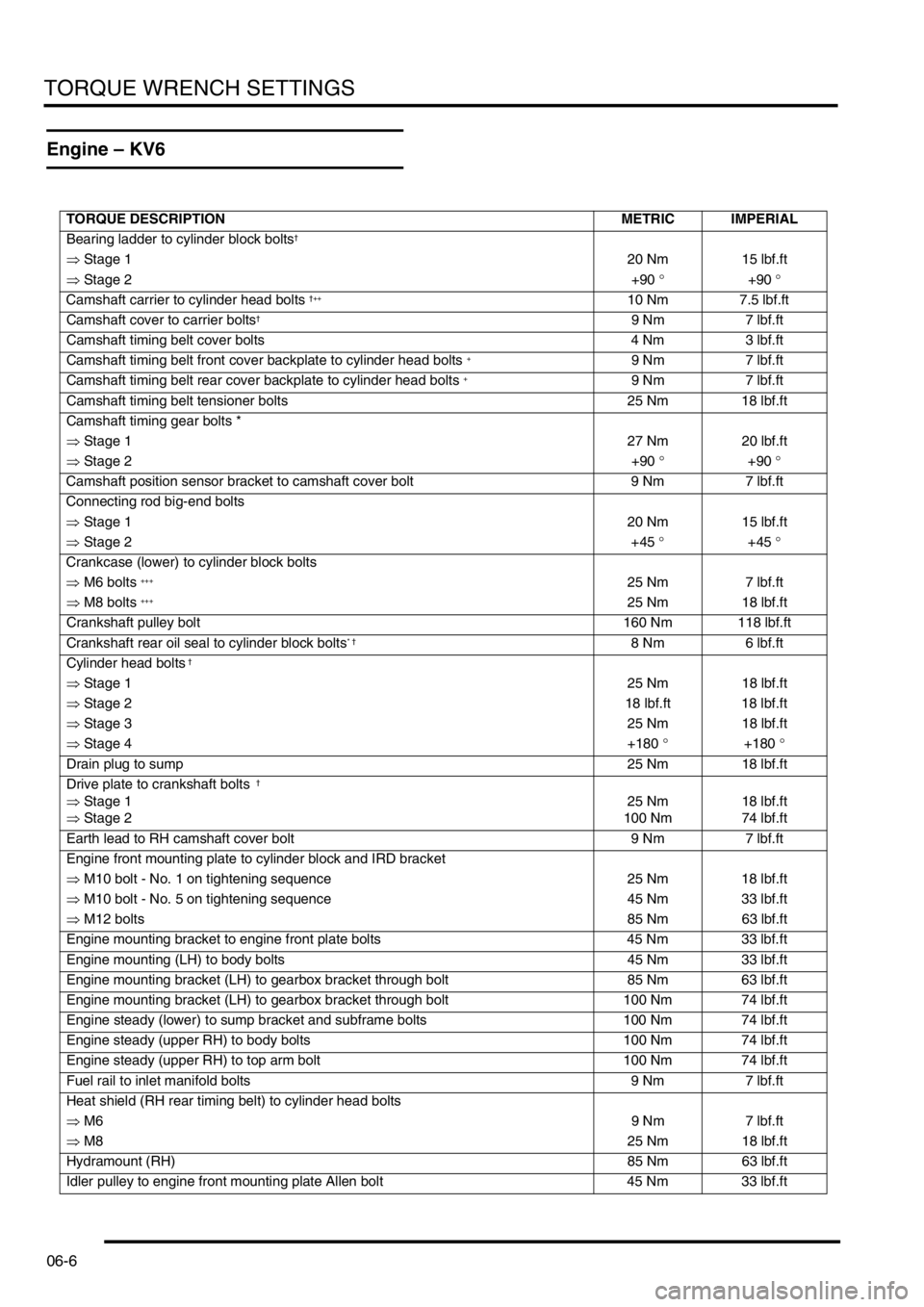
TORQUE WRENCH SETTINGS
06-6
Engine – KV6
TORQUE DESCRIPTION METRIC IMPERIAL
Bearing ladder to cylinder block bolts
†
⇒ Stage 120 Nm 15 lbf.ft
⇒ Stage 2+90 °+90 °
Camshaft carrier to cylinder head bolts
†++10 Nm 7.5 lbf.ft
Camshaft cover to carrier bolts
†9 Nm 7 lbf.ft
Camshaft timing belt cover bolts 4 Nm 3 lbf.ft
Camshaft timing belt front cover backplate to cylinder head bolts
+9 Nm 7 lbf.ft
Camshaft timing belt rear cover backplate to cylinder head bolts
+9 Nm 7 lbf.ft
Camshaft timing belt tensioner bolts 25 Nm 18 lbf.ft
Camshaft timing gear bolts *
⇒ Stage 127 Nm 20 lbf.ft
⇒ Stage 2+90 °+90 °
Camshaft position sensor bracket to camshaft cover bolt 9 Nm 7 lbf.ft
Connecting rod big-end bolts
⇒ Stage 120 Nm 15 lbf.ft
⇒ Stage 2+45 °+45 °
Crankcase (lower) to cylinder block bolts
⇒ M6 bolts
+++25 Nm 7 lbf.ft
⇒ M8 bolts
+++25 Nm 18 lbf.ft
Crankshaft pulley bolt 160 Nm 118 lbf.ft
Crankshaft rear oil seal to cylinder block bolts
* † 8 Nm 6 lbf.ft
Cylinder head bolts
†
⇒ Stage 125 Nm 18 lbf.ft
⇒ Stage 218 lbf.ft 18 lbf.ft
⇒ Stage 325 Nm 18 lbf.ft
⇒ Stage 4+180 °+180 °
Drain plug to sump 25 Nm 18 lbf.ft
Drive plate to crankshaft bolts
†
⇒ Stage 1
⇒ Stage 225 Nm
100 Nm18 lbf.ft
74 lbf.ft
Earth lead to RH camshaft cover bolt 9 Nm 7 lbf.ft
Engine front mounting plate to cylinder block and IRD bracket
⇒ M10 bolt - No. 1 on tightening sequence 25 Nm 18 lbf.ft
⇒ M10 bolt - No. 5 on tightening sequence 45 Nm 33 lbf.ft
⇒ M12 bolts85 Nm 63 lbf.ft
Engine mounting bracket to engine front plate bolts 45 Nm 33 lbf.ft
Engine mounting (LH) to body bolts 45 Nm 33 lbf.ft
Engine mounting bracket (LH) to gearbox bracket through bolt 85 Nm 63 lbf.ft
Engine mounting bracket (LH) to gearbox bracket through bolt 100 Nm 74 lbf.ft
Engine steady (lower) to sump bracket and subframe bolts 100 Nm 74 lbf.ft
Engine steady (upper RH) to body bolts 100 Nm 74 lbf.ft
Engine steady (upper RH) to top arm bolt 100 Nm 74 lbf.ft
Fuel rail to inlet manifold bolts 9 Nm 7 lbf.ft
Heat shield (RH rear timing belt) to cylinder head bolts
⇒ M69 Nm 7 lbf.ft
⇒ M825 Nm 18 lbf.ft
Hydramount (RH)85 Nm 63 lbf.ft
Idler pulley to engine front mounting plate Allen bolt 45 Nm 33 lbf.ft