check engine MAZDA 626 1987 Workshop Manual
[x] Cancel search | Manufacturer: MAZDA, Model Year: 1987, Model line: 626, Model: MAZDA 626 1987Pages: 1865, PDF Size: 94.35 MB
Page 528 of 1865
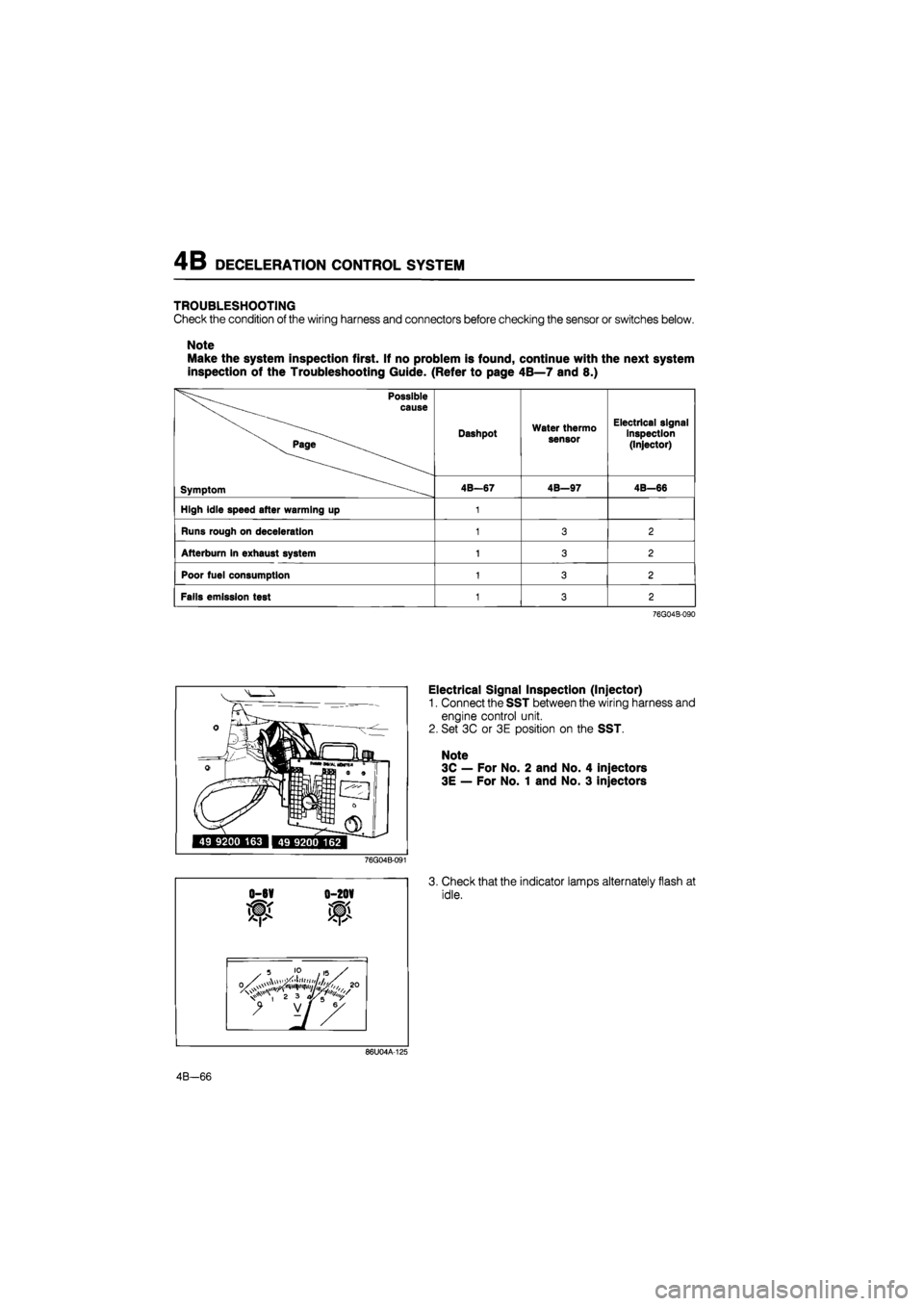
4B DECELERATION CONTROL SYSTEM
TROUBLESHOOTING
Check the condition of the wiring harness and connectors before checking the sensor or switches below.
Note
Make the system inspection first. If no problem is found, continue with the next system
inspection of the Troubleshooting Guide. (Refer to page 4B—7 and 8.)
Possible
^^ cause
Symptom
Dashpot Water thermo
sensor
Electrical signal
inspection
(Injector)
Possible
^^ cause
Symptom 4B—67 4B—97 4B-66
High idle speed after warming up 1
Runs rough on deceleration 1 3 2
Afterburn in exhaust system 1 3 2
Poor fuel consumption 1 3 2
Fails emission test 1 3 2
76G04B-090
Electrical Signal Inspection (Injector)
1. Connect the SST between the wiring harness and
engine control unit.
2. Set 3C or 3E position on the SST.
Note
3C — For No. 2 and No. 4 injectors
3E — For No. 1 and No. 3 injectors
76G04B-091
0-6V 0-20V
3. Check that the indicator lamps alternately flash at
idle.
86U04A-125
4B—66
Page 529 of 1865
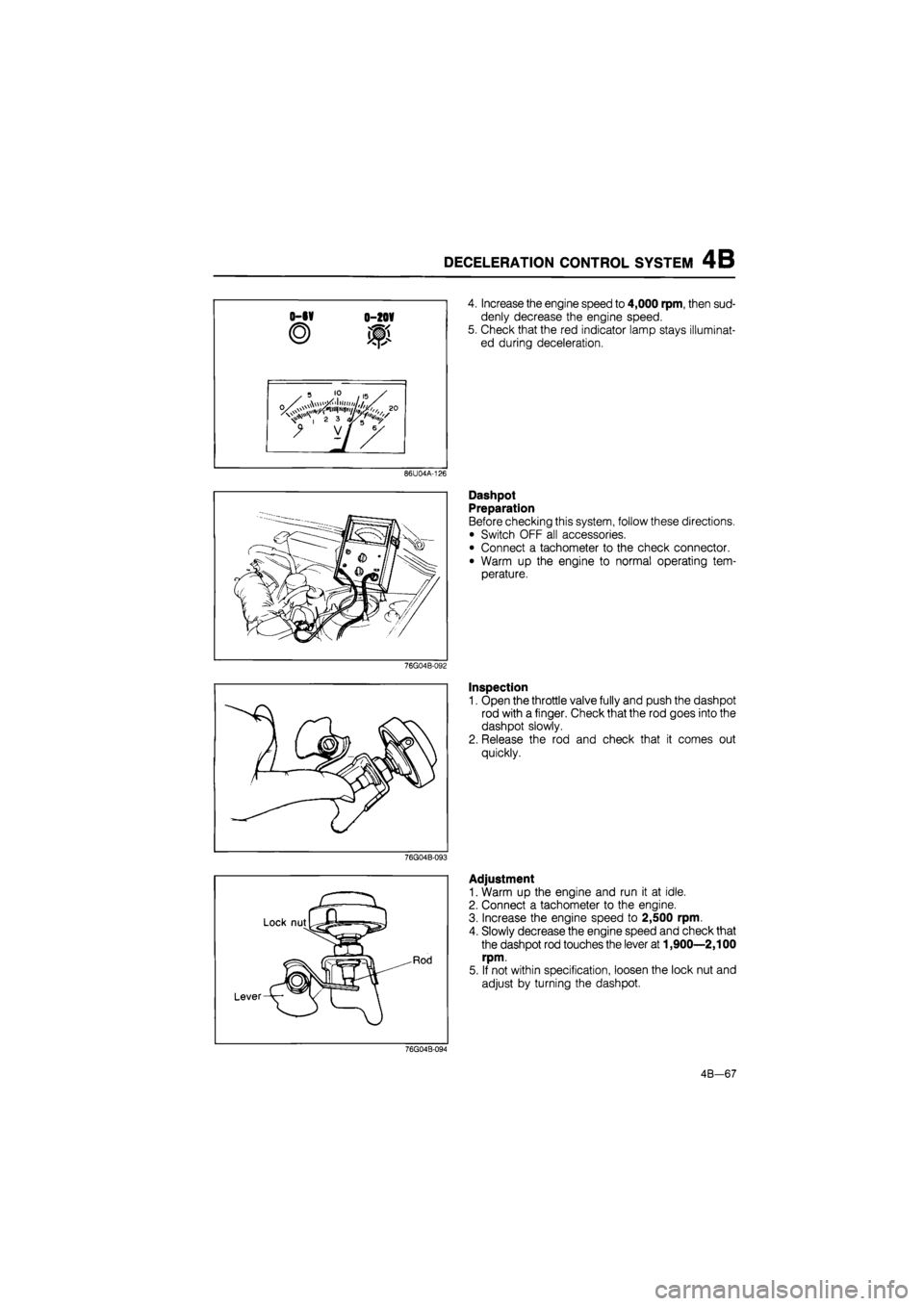
DECELERATION CONTROL SYSTEM 4B
86U04A-126
76G04B-092
76G04B-093
Lock nutLg*
rJpM
Lever-V- y"
4. Increase the engine speed to 4,000 rpm, then sud-
denly decrease the engine speed.
5. Check that the red indicator lamp stays illuminat-
ed during deceleration.
Dashpot
Preparation
Before checking this system, follow these directions.
• Switch OFF all accessories.
• Connect a tachometer to the check connector.
• Warm up the engine to normal operating tem-
perature.
Inspection
1. Open the throttle valve fully and push the dashpot
rod with a finger. Check that the rod goes into the
dashpot slowly.
2. Release the rod and check that it comes out
quickly.
Adjustment
1. Warm up the engine and run it at idle.
2. Connect a tachometer to the engine.
3. Increase the engine speed to 2,500 rpm.
4. Slowly decrease the engine speed and check that
the dashpot rod touches the lever at 1,900—2,100
rpm.
5. If not within specification, loosen the lock nut and
adjust by turning the dashpot.
76G04B-094
4B-67
Page 531 of 1865
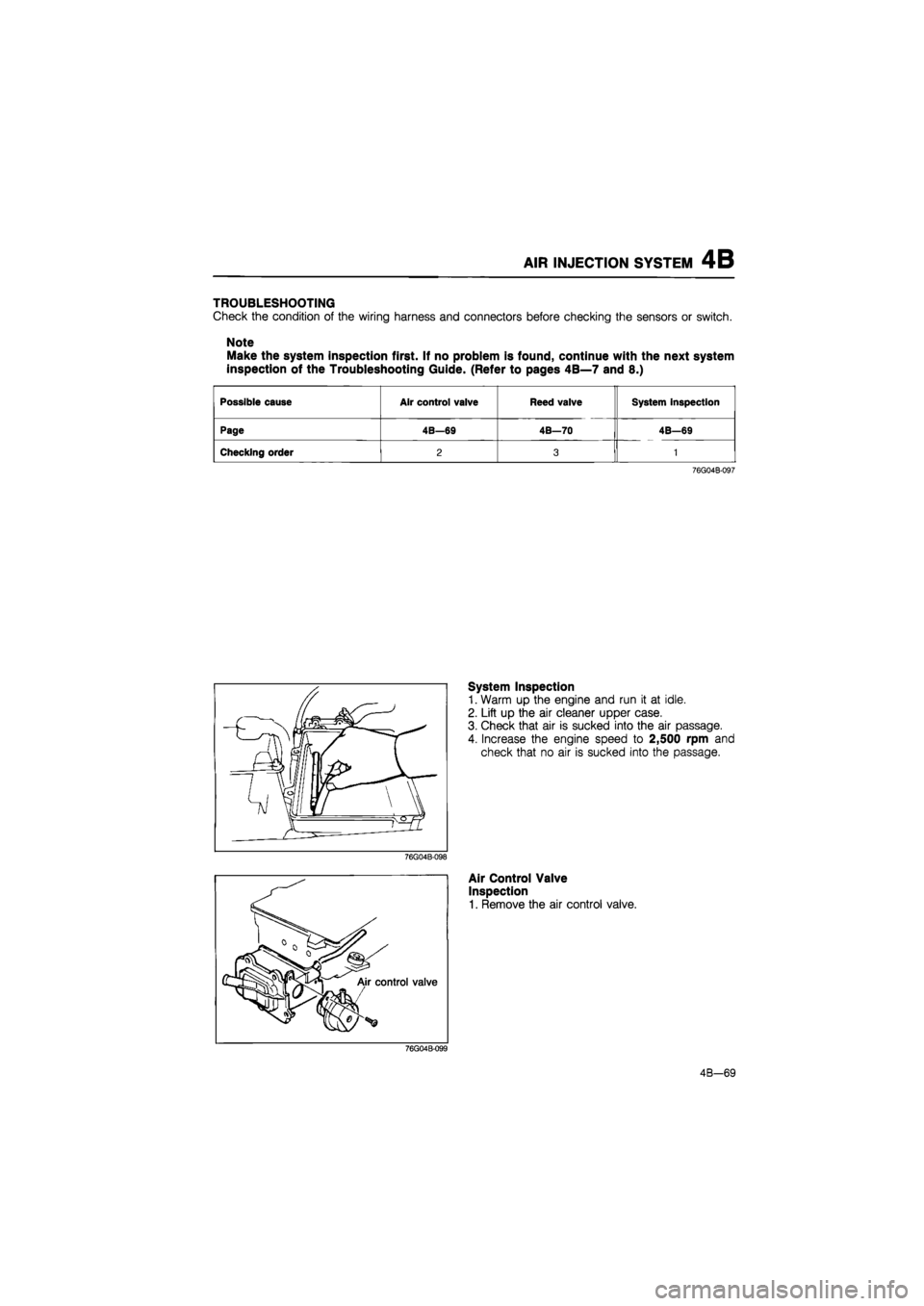
AIR INJECTION SYSTEM 4B
TROUBLESHOOTING
Check the condition of the wiring harness and connectors before checking the sensors or switch.
Note
Make the system inspection first. If no problem is found, continue with the next system
inspection of the Troubleshooting Guide. (Refer to pages 4B—7 and 8.)
Possible cause Air control valve Reed valve System inspection
Page 4B—69 4B—70 4B—69
Checking order 2 3 1
76G04B-097
System Inspection
1. Warm up the engine and run it at idle.
2. Lift up the air cleaner upper case.
3. Check that air is sucked into the air passage.
4. Increase the engine speed to 2,500 rpm and
check that no air is sucked into the passage.
Air Control Valve
Inspection
1. Remove the air control valve.
4B-69
Page 532 of 1865
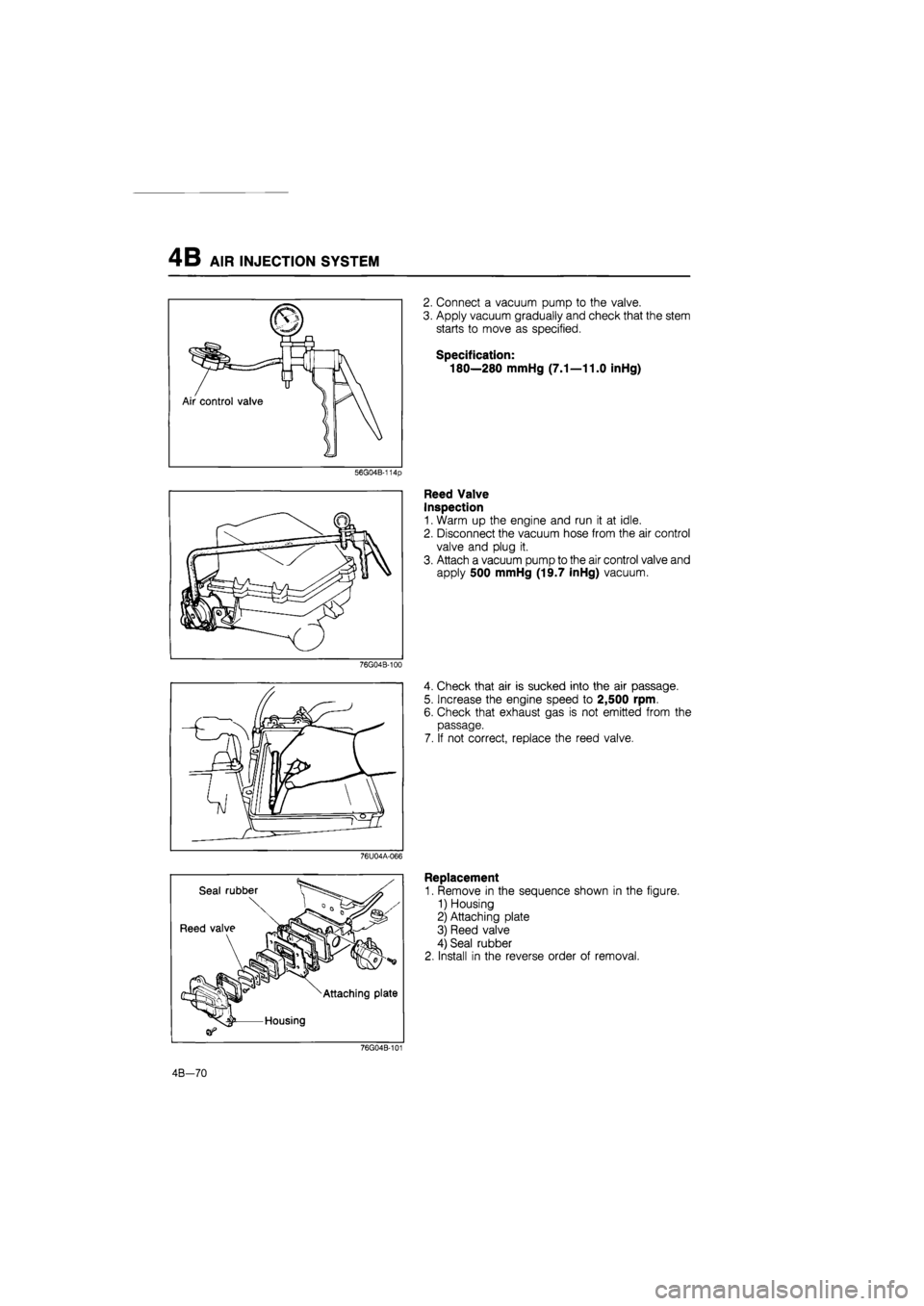
4B AIR INJECTION SYSTEM
56G04B-114p
76G04B-100
76U04A-066
2. Connect a vacuum pump to the valve.
3. Apply vacuum gradually and check that the stem
starts to move as specified.
Specification:
180—280 mmHg (7.1—11.0 inHg)
Reed Valve
Inspection
1. Warm up the engine and run it at idle.
2. Disconnect the vacuum hose from the air control
valve and plug it.
3. Attach a vacuum pump to the air control valve and
apply 500 mmHg (19.7 inHg) vacuum.
4. Check that air is sucked into the air passage.
5. Increase the engine speed to 2,500 rpm.
6. Check that exhaust gas is not emitted from the
passage.
7. If not correct, replace the reed valve.
Replacement
1. Remove in the sequence shown in the figure.
1) Housing
2) Attaching plate
3) Reed valve
4) Seal rubber
2. Install in the reverse order of removal.
76G04B-101
4B—70
Page 534 of 1865
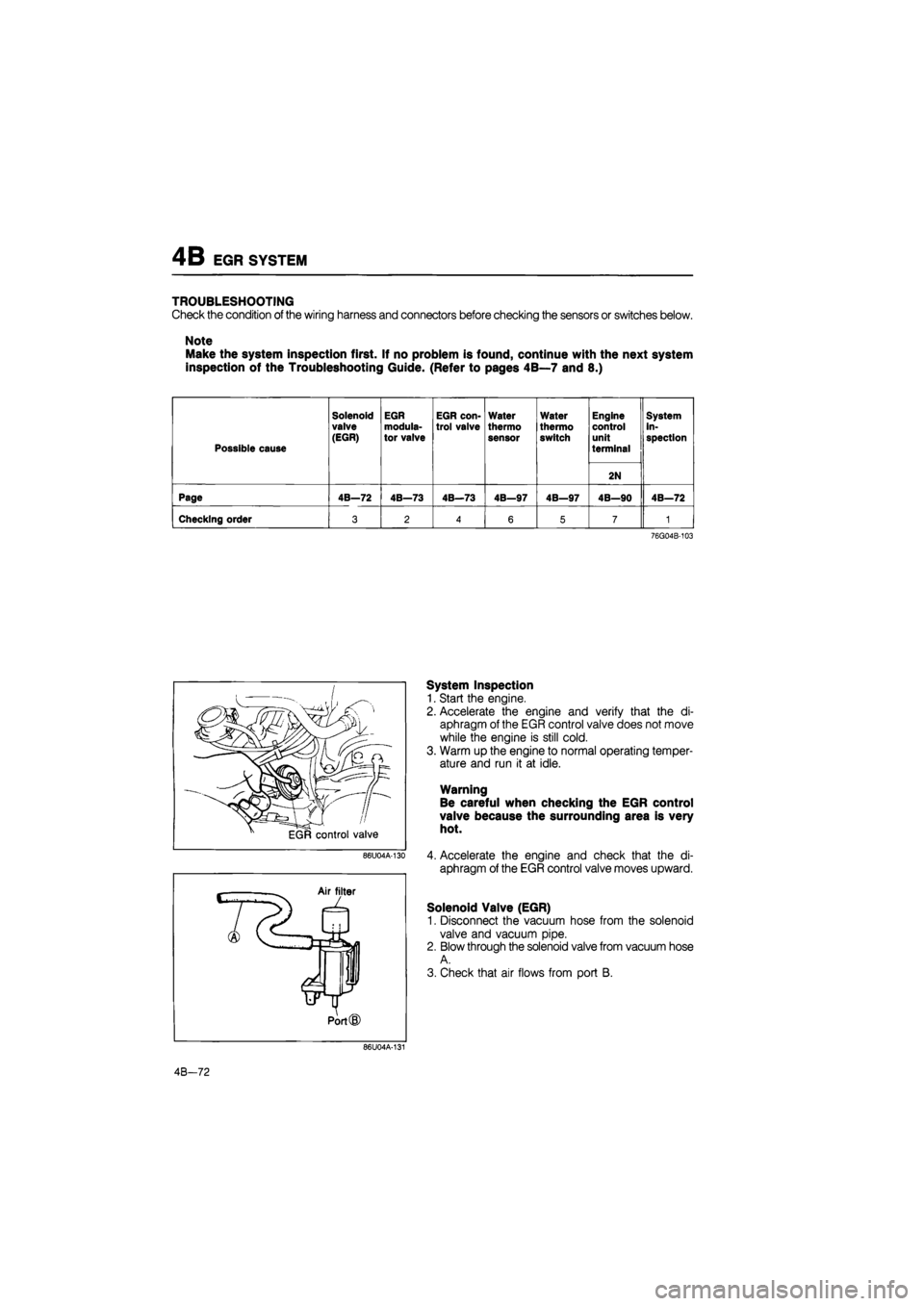
4B EGR SYSTEM
TROUBLESHOOTING
Check the condition of the wiring harness and connectors before checking the sensors or switches below.
Note
Make the system inspection first. If no problem is found, continue with the next system
inspection of the Troubleshooting Guide. (Refer to pages 4B—7 and 8.)
Possible cause
Solenoid
valve (EGR)
EGR modula-tor valve
EGR con-trol valve
Water
thermo sensor
Water
thermo switch
Engine control unit
terminal
System in-spection
2N
Page 4B—72 4B—73 4B—73 4B—97 4B—97 4B—90 4B—72
Checking order 3 2 4 6 5 7 1
76G04B-103
86U04A-130
System Inspection
1. Start the engine.
2. Accelerate the engine and verify that the di-
aphragm of the EGR control valve does not move
while the engine is still cold.
3. Warm up the engine to normal operating temper-
ature and run it at idle.
Warning
Be careful when checking the EGR control
valve because the surrounding area is very
hot.
4. Accelerate the engine and check that the di-
aphragm of the EGR control valve moves upward.
Solenoid Valve (EGR)
1. Disconnect the vacuum hose from the solenoid
valve and vacuum pipe.
2. Blow through the solenoid valve from vacuum hose
A.
3. Check that air flows from port B.
86U04A-131
4B-72
Page 535 of 1865
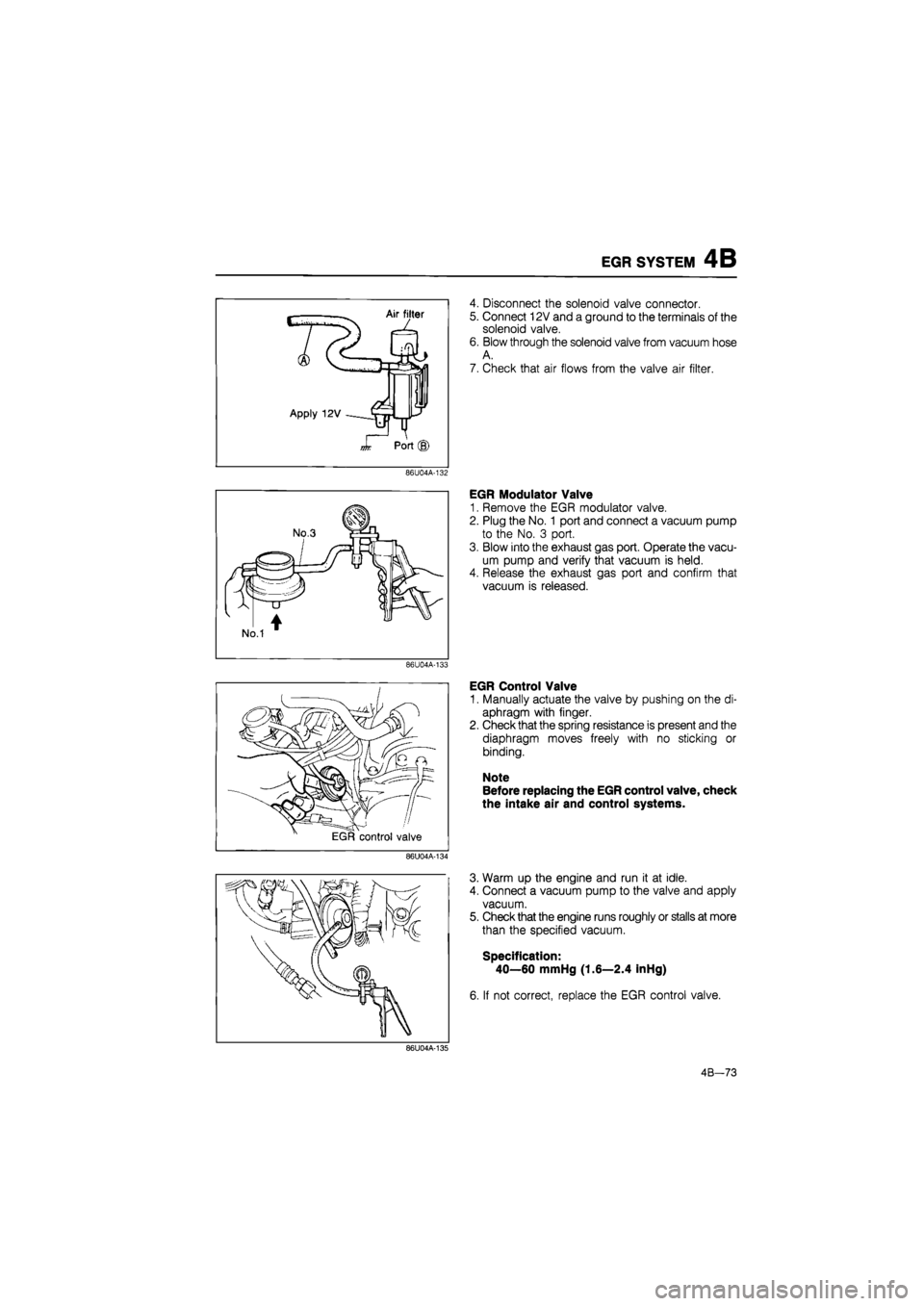
EGR SYSTEM 4B
Apply 12V
Air filter
L
Jt Port
4. Disconnect the solenoid valve connector.
5. Connect 12V and a ground to the terminals of the
solenoid valve.
6. Blow through the solenoid valve from vacuum hose
A.
7. Check that air flows from the valve air filter.
86U04A-132
86U04A-133
86U04A-134
EGR Modulator Valve
1. Remove the EGR modulator valve.
2. Plug the No. 1 port and connect a vacuum pump
to the No. 3 port.
3. Blow into the exhaust gas port. Operate the vacu-
um pump and verify that vacuum is held.
4. Release the exhaust gas port and confirm that
vacuum is released.
EGR Control Valve
1. Manually actuate the valve by pushing on the di-
aphragm with finger.
2. Check that the spring resistance is present and the
diaphragm moves freely with no sticking or
binding.
Note
Before replacing the EGR control valve, check
the intake air and control systems.
3. Warm up the engine and run it at idle.
4. Connect a vacuum pump to the valve and apply
vacuum.
5. Check that the engine runs roughly or stalls at more
than the specified vacuum.
Specification:
40—60 mmHg (1.6—2.4 inHg)
6. If not correct, replace the EGR control valve.
86U04A-135
4B-73
Page 536 of 1865
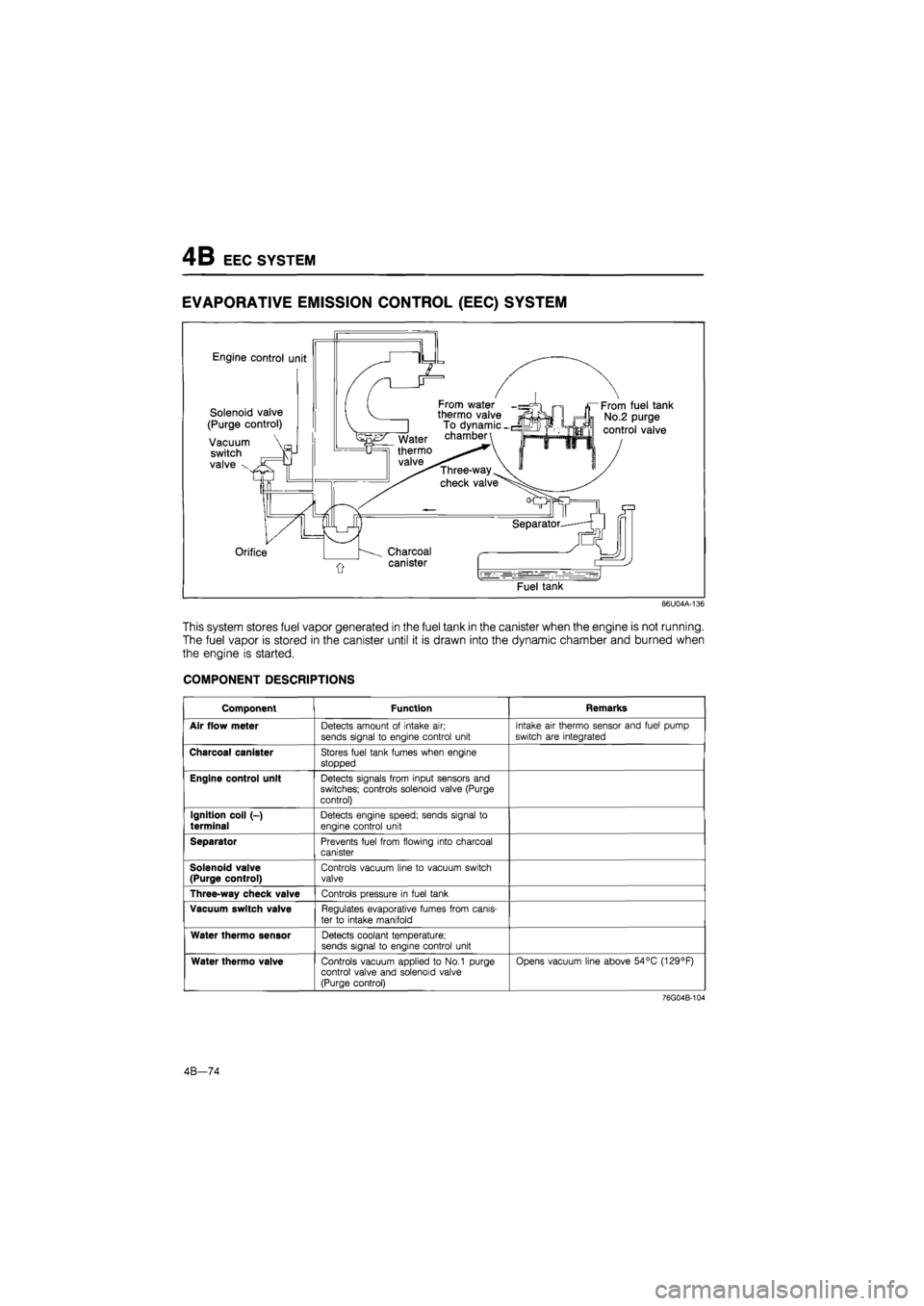
4B EEC SYSTEM
EVAPORATIVE EMISSION CONTROL
(EEC)
SYSTEM
Engine control unit
Solenoid valve
(Purge control)
Vacuum
switch
valve x
From water thermo valve To dynamic -chamber
Three-way
check valve
Orifice Charcoal
canister
From fuel tank
No.2 purge
control valve
Fuel tank
86U04A-136
This system stores fuel vapor generated in the fuel tank in the canister when the engine is not running.
The fuel vapor is stored in the canister until it is drawn into the dynamic chamber and burned when
the engine is started.
COMPONENT DESCRIPTIONS
Component Function Remarks
Air flow meter Detects amount of intake air; sends signal to engine control unit
Intake air thermo sensor and fuel pump
switch are integrated
Charcoal canister Stores fuel tank fumes when engine
stopped
Engine control unit Detects signals from input sensors and switches; controls solenoid valve (Purge control)
Ignition coil (-)
terminal Detects engine speed; sends signal to
engine control unit
Separator Prevents fuel from flowing into charcoal canister
Solenoid valve (Purge control) Controls vacuum line to vacuum switch valve
Three-way check valve Controls pressure in fuel tank
Vacuum switch valve Regulates evaporative fumes from canis-
ter to intake manifold
Water thermo sensor Detects coolant temperature; sends signal to engine control unit
Water thermo valve Controls vacuum applied to No.1 purge control valve and solenoid valve (Purge control)
Opens vacuum line above 54°C (129°F)
76G04B-104
4B—74
Page 537 of 1865
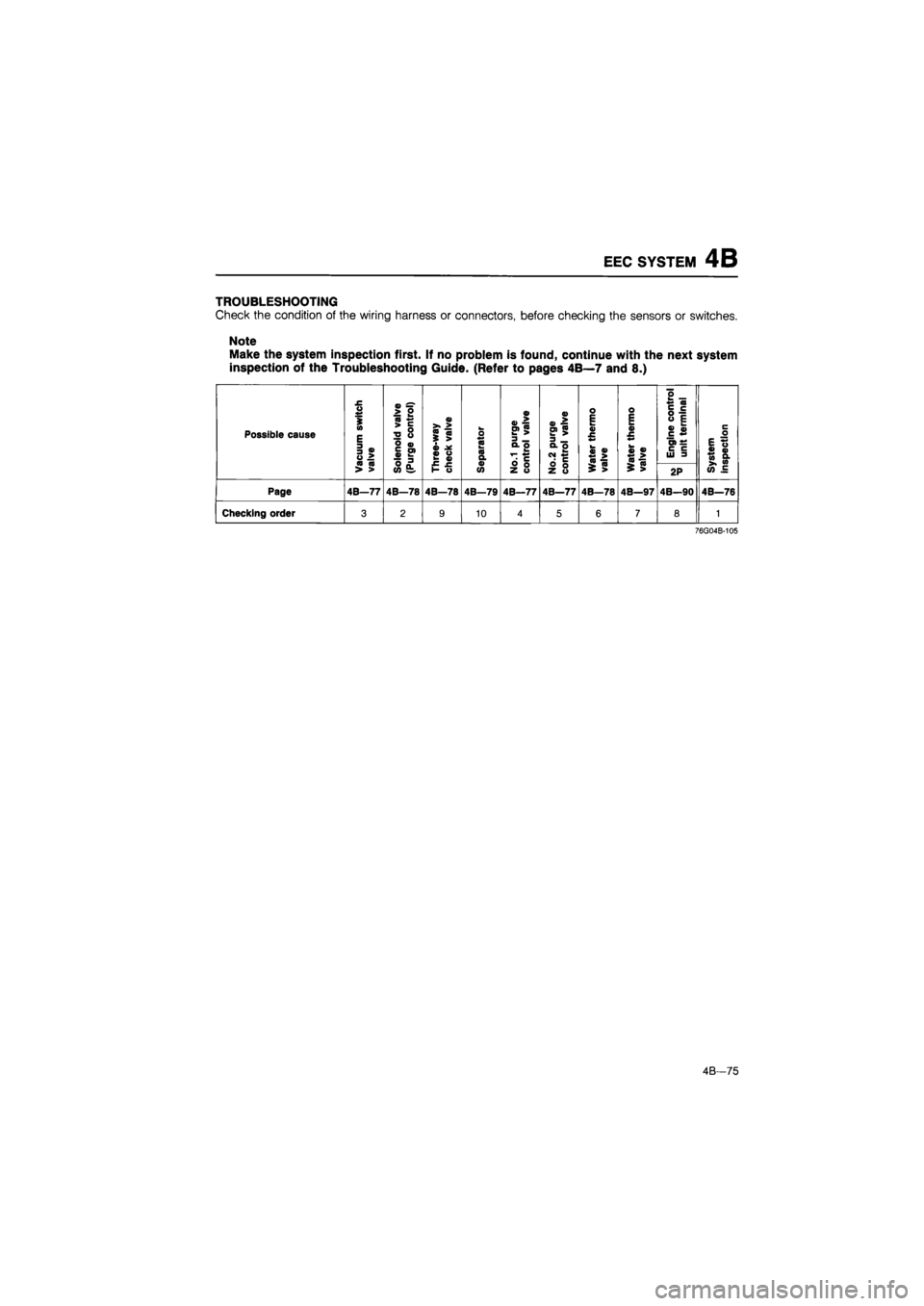
EEC SYSTEM
4B
TROUBLESHOOTING
Check
the
condition
of the
wiring harness
or
connectors, before checking
the
sensors
or
switches.
Note
Make the system inspection first.
If no
problem
is
found, continue with
the
next system
inspection
of the
Troubleshooting Guide. (Refer
to
pages 4B—7 and
8.)
Possible cause
Vacuum
switch
valve
Solenoid
valve
(Purge
control)
0)
<0
m
i
>
« «
o
•C
?
o ** «0 a a
No.1
purge
control
valve
No.2
purge
control
valve
Water
thermo
valve
o E tm 0) £
«>
0)
^
>
Engine
control
unit
terminal
System inspection Vacuum
switch
valve
Solenoid
valve
(Purge
control)
purge
control
valve
No.2
purge
control
valve
Water
thermo
valve
$
>
2P
System inspection
Page 4B—77 4B—78 4B—78 4B—79 4B—77 4B—77 4B—78 4B—97 4B—90 4B—76
Checking order 3 2 9 10 4 5 6 7 8 1
76G04B-105
4B—75
Page 538 of 1865
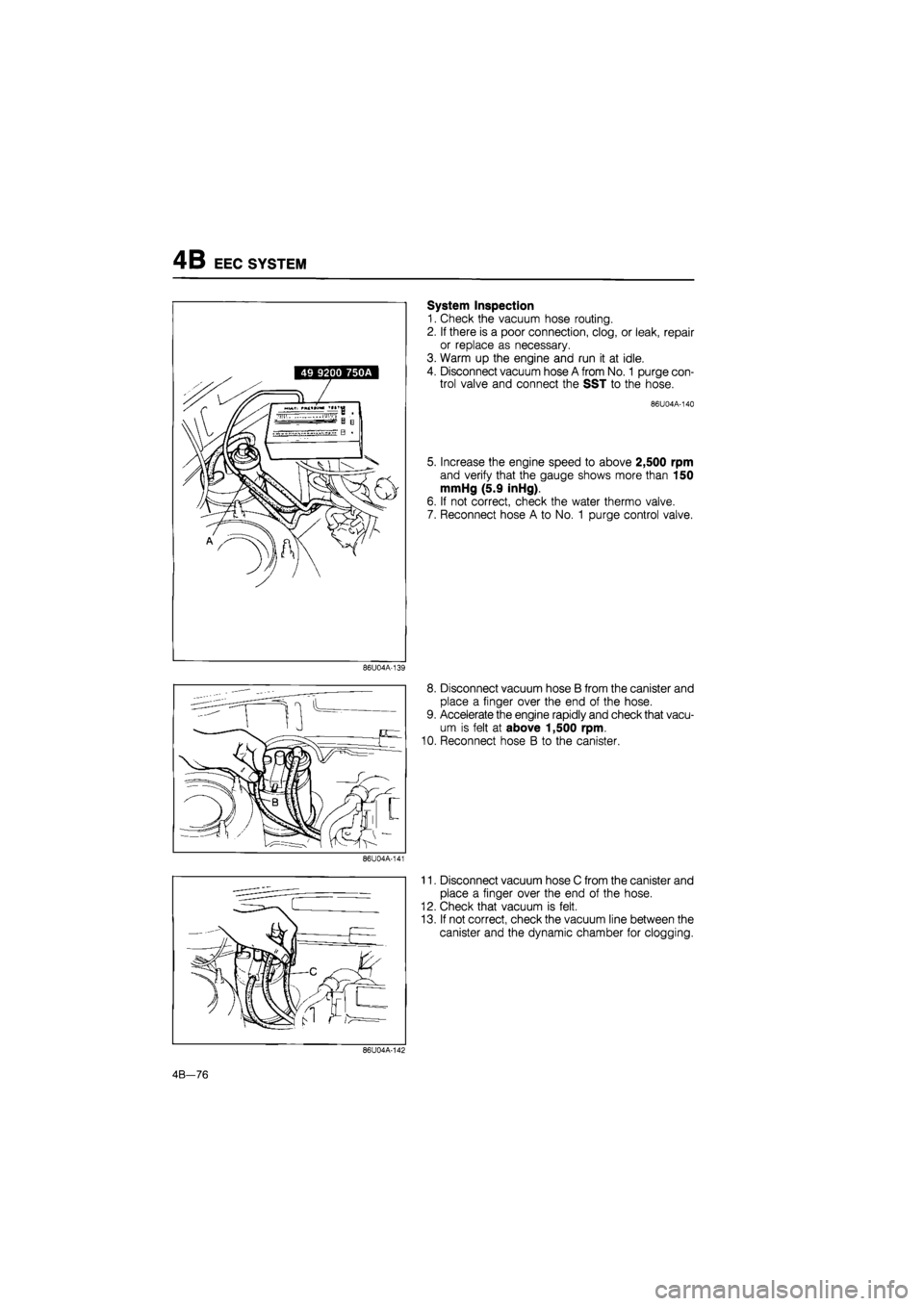
4B EEC SYSTEM
86U04A-139
86U04A-141
System Inspection
1. Check the vacuum hose routing.
2. If there is a poor connection, clog, or leak, repair
or replace as necessary.
3. Warm up the engine and run it at idle.
4. Disconnect vacuum hose A from No.
1
purge con-
trol valve and connect the SST to the hose.
86 U 04 A-140
5. Increase the engine speed to above 2,500 rpm
and verify that the gauge shows more than 150
mmHg (5.9 inHg).
6. If not correct, check the water thermo valve.
7. Reconnect hose A to No. 1 purge control valve.
8. Disconnect vacuum hose B from the canister and
place a finger over the end of the hose.
9. Accelerate the engine rapidly and check that vacu-
um is felt at above 1,500 rpm.
10. Reconnect hose B to the canister.
11. Disconnect vacuum hose C from the canister and
place a finger over the end of the hose.
12. Check that vacuum is felt.
13. If not correct, check the vacuum line between the
canister and the dynamic chamber for clogging.
86U04A-142
4B—76
Page 542 of 1865
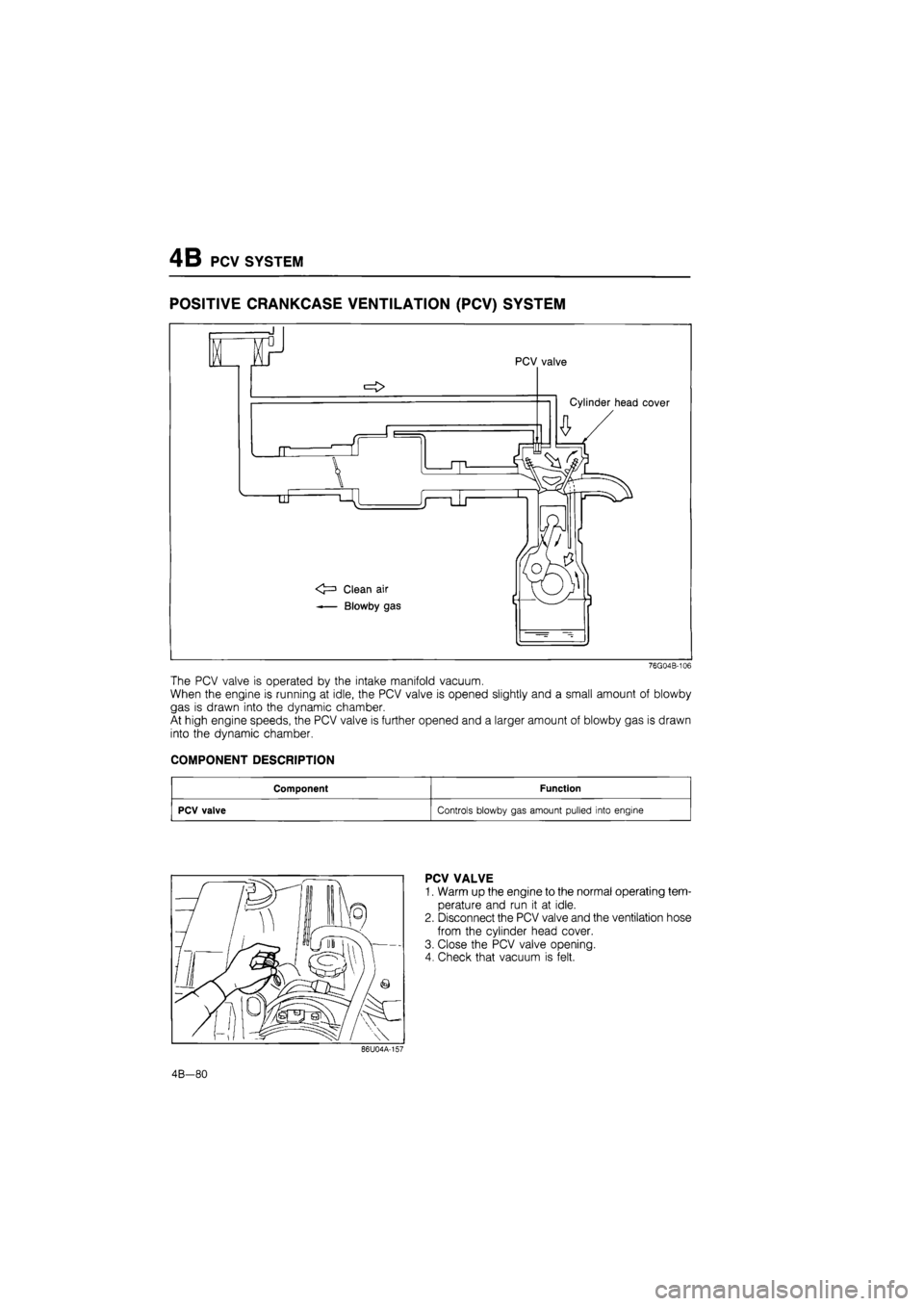
4B PCV SYSTEM
POSITIVE CRANKCASE VENTILATION
(PCV)
SYSTEM
76G04B-106
The PCV valve is operated by the intake manifold vacuum.
When the engine is running at idle, the PCV valve is opened slightly and a small amount of blowby
gas is drawn into the dynamic chamber.
At high engine speeds, the PCV valve is further opened and a larger amount of blowby gas is drawn
into the dynamic chamber.
COMPONENT DESCRIPTION
Component Function
PCV valve Controls blowby gas amount pulled into engine
PCV VALVE
1. Warm up the engine to the normal operating tem-
perature and run it at idle.
2. Disconnect the PCV valve and the ventilation hose
from the cylinder head cover.
3. Close the PCV valve opening.
4. Check that vacuum is felt.
4B—80