check engine MAZDA 626 1987 Workshop Manual
[x] Cancel search | Manufacturer: MAZDA, Model Year: 1987, Model line: 626, Model: MAZDA 626 1987Pages: 1865, PDF Size: 94.35 MB
Page 635 of 1865
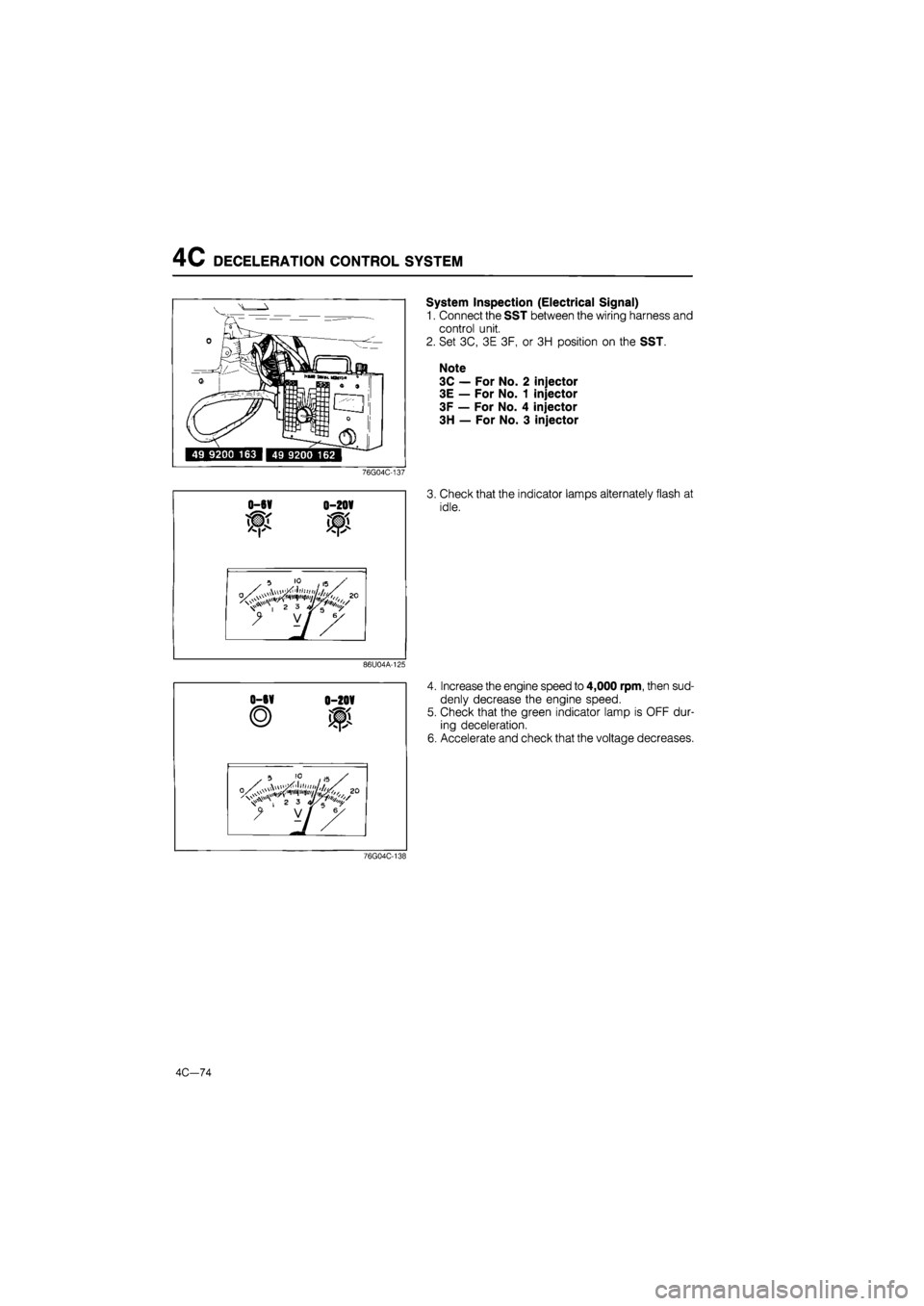
4C DECELERATION CONTROL SYSTEM
System Inspection (Electrical Signal)
1. Connect the SST between the wiring harness and
control unit.
2. Set 3C, 3E 3F, or 3H position on the SST.
Note
3C — For No. 2 injector
3E — For No. 1 injector
3F — For No. 4 injector
3H — For No. 3 injector
76G04C-137
3. Check that the indicator lamps alternately flash at
idle.
86U04A-125
0-6V 0-20V
® $
4. Increase the engine speed to 4,000 rpm, then sud-
denly decrease the engine speed.
5. Check that the green indicator lamp is OFF dur-
ing deceleration.
6. Accelerate and check that the voltage decreases.
76G04C-138
4C—74
Page 637 of 1865
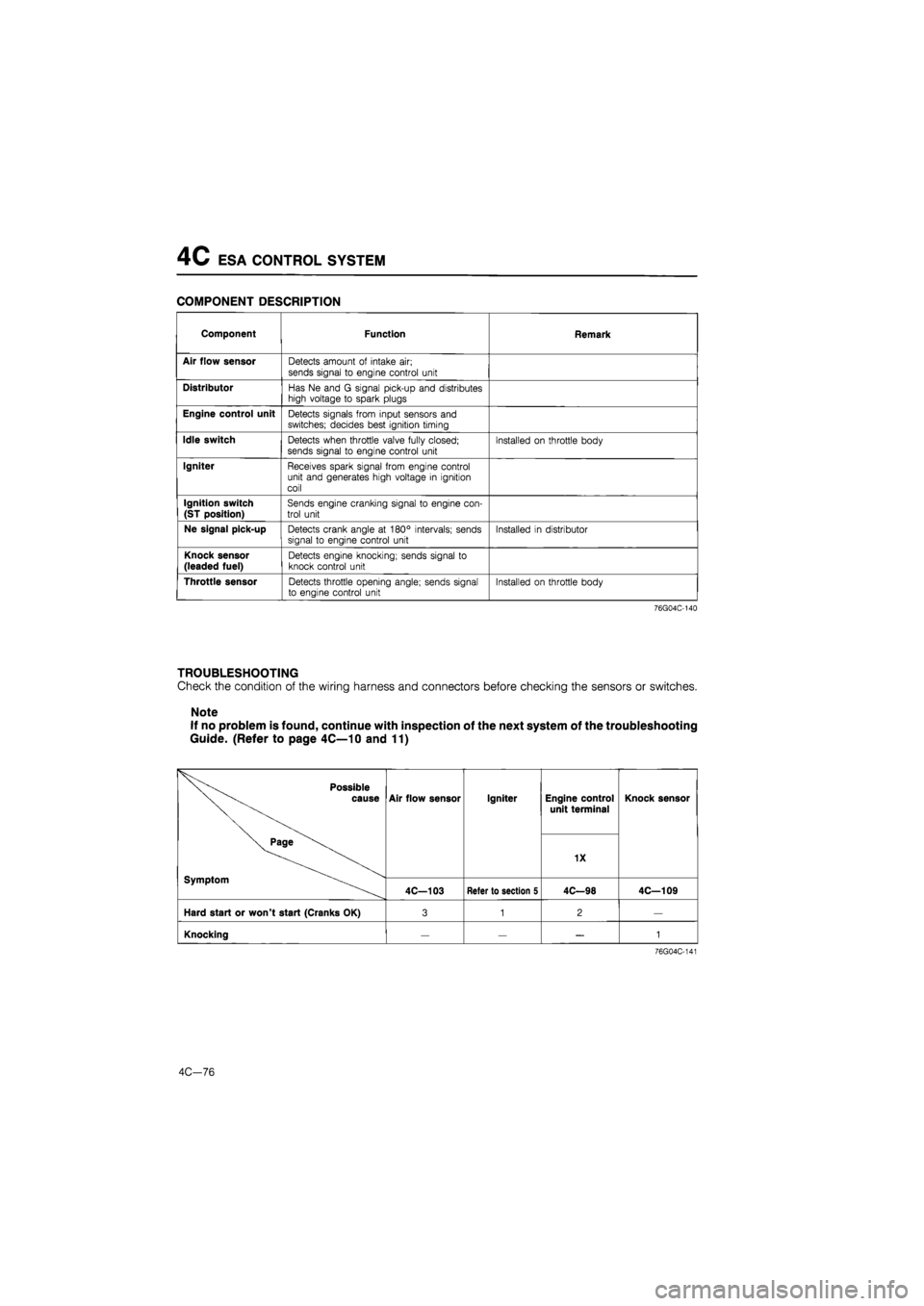
4C ESA CONTROL SYSTEM
COMPONENT DESCRIPTION
Component Function Remark
Air flow sensor Detects amount of intake air;
sends signal to engine control unit
Distributor Has Ne and G signal pick-up and distributes high voltage to spark plugs
Engine control unit Detects signals from input sensors and switches; decides best ignition timing
Idle switch Detects when throttle valve fully closed; sends signal to engine control unit Installed on throttle body
Igniter Receives spark signal from engine control unit and generates high voltage in ignition coil
Ignition switch
(ST position) Sends engine cranking signal to engine con-trol unit
Ne signal pick-up Detects crank angle at 180° intervals; sends signal to engine control unit Installed in distributor
Knock sensor (leaded fuel) Detects engine knocking; sends signal to knock control unit
Throttle sensor Detects throttle opening angle; sends signal to engine control unit Installed on throttle body
76G04C-140
TROUBLESHOOTING
Check the condition of the wiring harness and connectors before checking the sensors or switches.
Note
If no problem is found, continue with inspection of the next system of the troubleshooting
Guide. (Refer to page 4C—10 and 11)
Possible cause
Page
Symptom
Air flow sensor Igniter Engine control
unit terminal Knock sensor Possible cause
Page
Symptom
Air flow sensor Igniter
1X
Knock sensor Possible cause
Page
Symptom
4C—103 Refer to section 5 4C—98 4C—109
Hard start or won't start (Cranks OK) 3 1 2 —
Knocking — 1
76G04C-141
4C-76
Page 639 of 1865
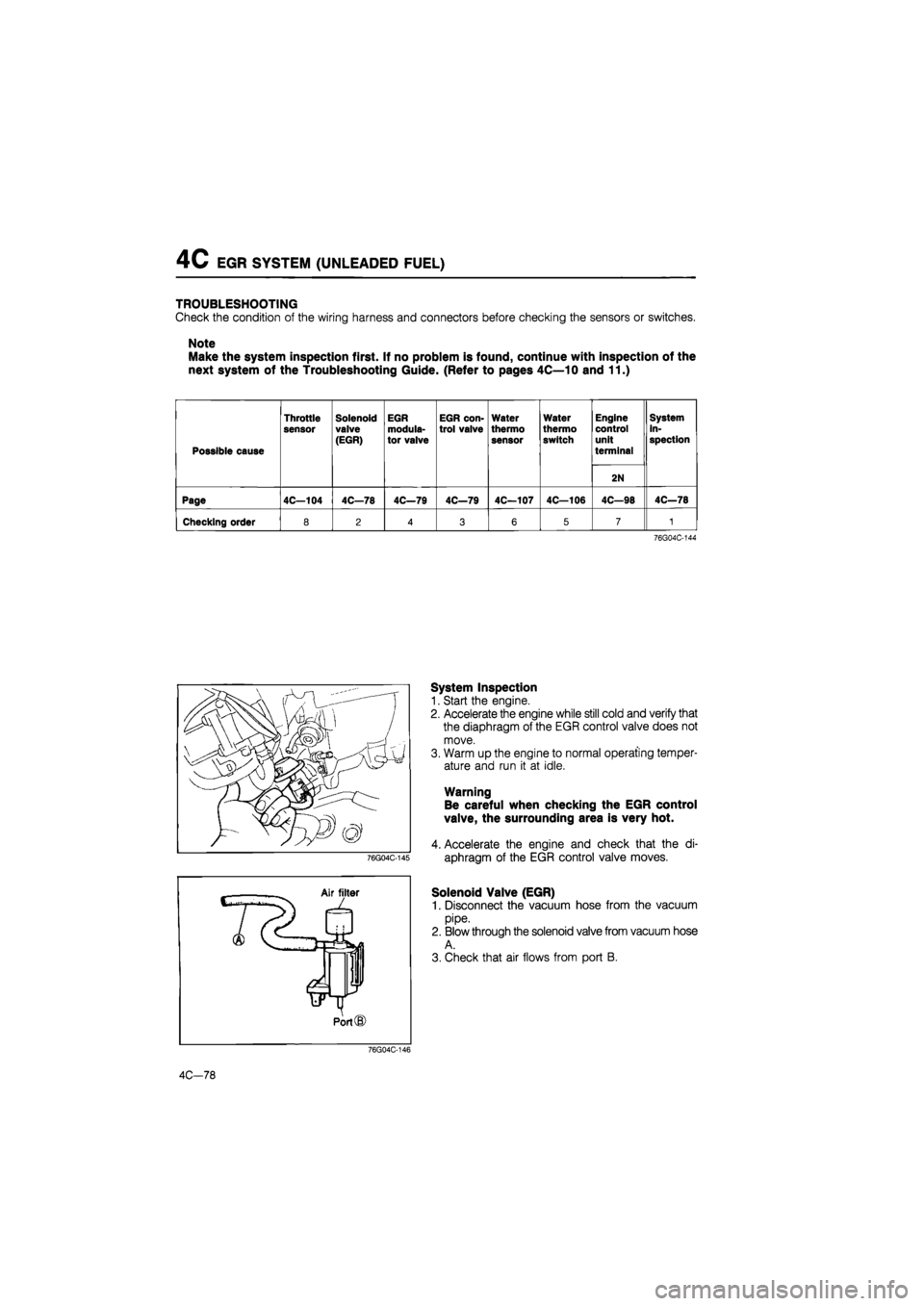
4C EGR SYSTEM (UNLEADED FUEL)
TROUBLESHOOTING
Check the condition of the wiring harness and connectors before checking the sensors or switches.
Note
Make the system inspection first. If no problem is found, continue with inspection of the
next system of the Troubleshooting Guide. (Refer to pages 4C—10 and 11.)
Possible cause
Throttle
sensor
Solenoid valve
(EGR)
EGR
modula-
tor valve
EGR con-trol valve
Water
thermo
sensor
Water
thermo switch
Engine control unit
terminal
System in-spection
2N
Page 4C—104 4C—78 4C—79 4C—79 4C—107 4C—106 4C—98 4C—78
Checking order 8 2 4 3 6 5 7 1
76G04C-144
System Inspection
1. Start the engine.
2. Accelerate the engine while still cold and verify that
the diaphragm of the EGR control valve does not
move.
3. Warm up the engine to normal operating temper-
ature and run it at idle.
Warning
Be careful when checking the EGR control
valve, the surrounding area is very hot.
4. Accelerate the engine and check that the di-
aphragm of the EGR control valve moves.
Solenoid Valve (EGR)
1. Disconnect the vacuum hose from the vacuum
pipe.
2. Blow through the solenoid valve from vacuum hose
A.
3. Check that air flows from port B.
76G04C-146
4C-78
Page 640 of 1865
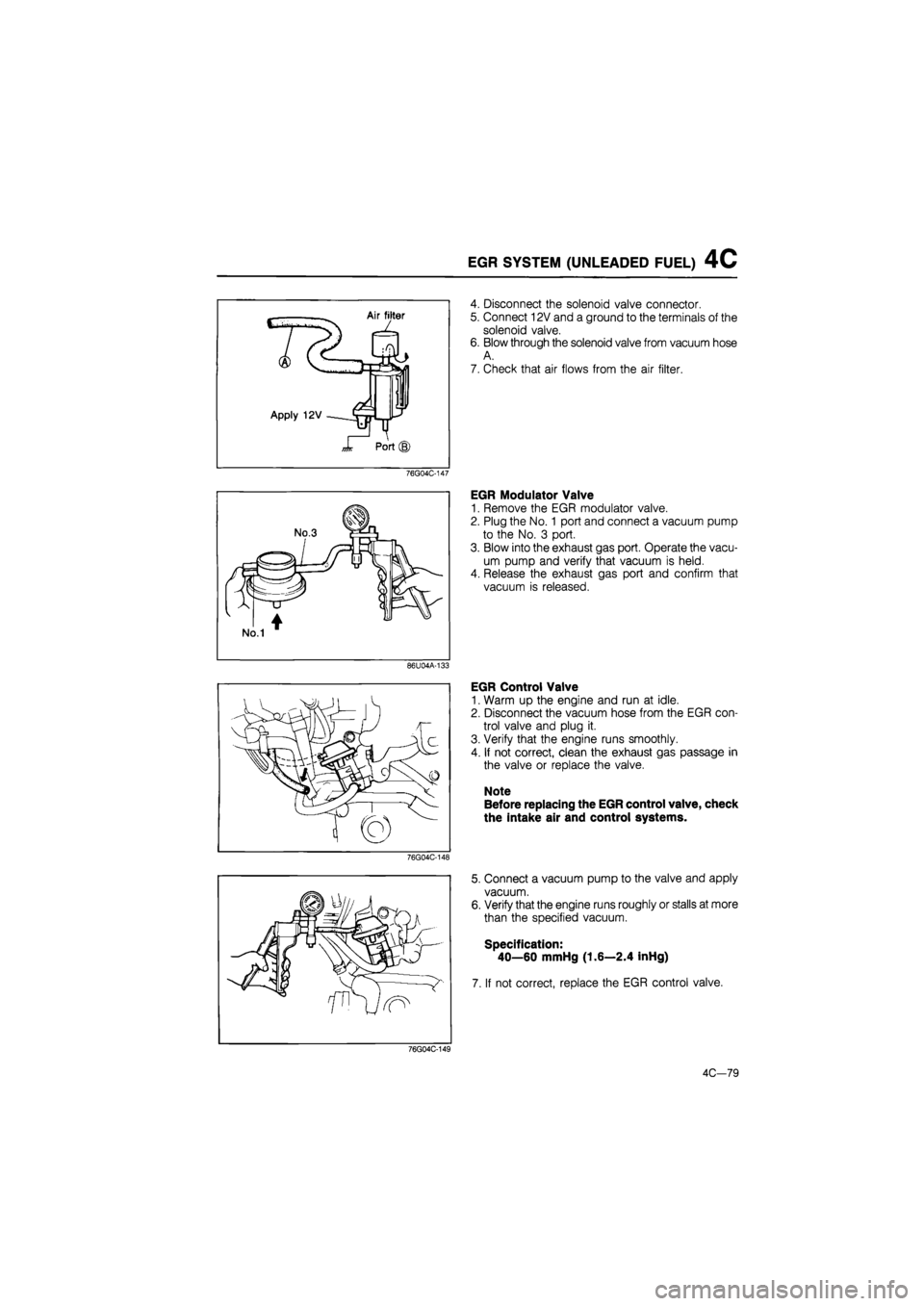
EGR SYSTEM (UNLEADED FUEL) 4C
Apply 12V
J* Port
76G04C-147
86U04A-133
76G04C-148
4. Disconnect the solenoid valve connector.
5. Connect 12V and a ground to the terminals of the
solenoid valve.
6. Blow through the solenoid valve from vacuum hose
A.
7. Check that air flows from the air filter.
EGR Modulator Valve
1. Remove the EGR modulator valve.
2. Plug the No. 1 port and connect a vacuum pump
to the No. 3 port.
3. Blow into the exhaust gas port. Operate the vacu-
um pump and verify that vacuum is held.
4. Release the exhaust gas port and confirm that
vacuum is released.
EGR Control Valve
1. Warm up the engine and run at idle.
2. Disconnect the vacuum hose from the EGR con-
trol valve and plug it.
3. Verify that the engine runs smoothly.
4. If not correct, clean the exhaust gas passage in
the valve or replace the valve.
Note
Before replacing the EGR control valve, check
the intake air and control systems.
5. Connect a vacuum pump to the valve and apply
vacuum.
6. Verify that the engine runs roughly or stalls at more
than the specified vacuum.
Specification:
40—60 mmHg (1.6—2.4 inHg)
7. If not correct, replace the EGR control valve.
76G04C-149
4C-79
Page 641 of 1865
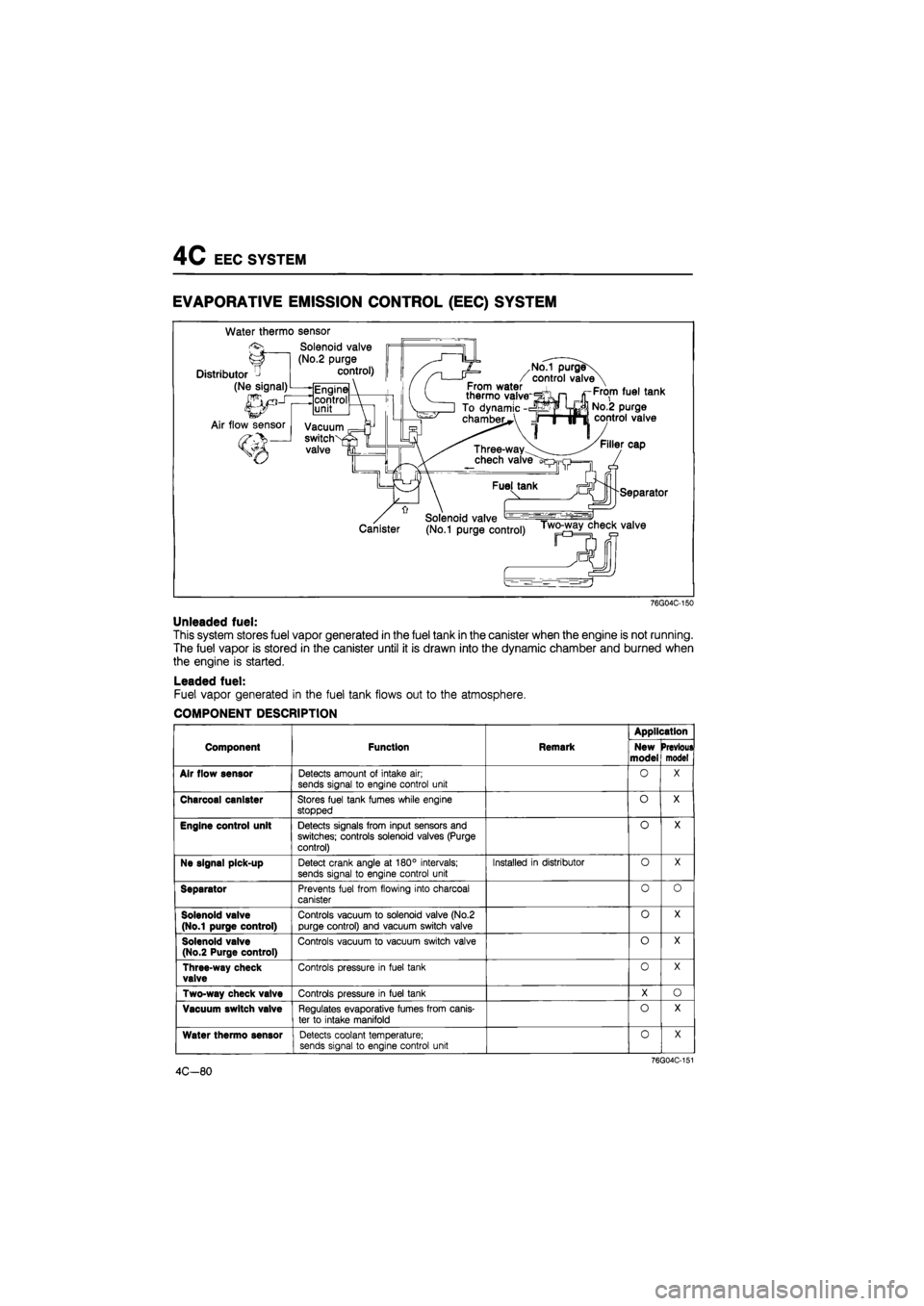
4C EEC SYSTEM
EVAPORATIVE EMISSION CONTROL
(EEC)
SYSTEM
Water thermo sensor
76G04C-150
Unleaded fuel:
This system stores fuel vapor generated in the fuel tank in the canister when the engine is not running.
The fuel vapor is stored in the canister until it is drawn into the dynamic chamber and burned when
the engine is started.
Leaded fuel:
Fuel vapor generated in the fuel tank flows out to the atmosphere.
COMPONENT DESCRIPTION
Application
Component Function Remark New
model Prevtoui model
Air flow sensor Detects amount of intake air; sends signal to engine control unit
O X
Charcoal canister Stores fuel tank fumes while engine stopped
o X
Engine control unit Detects signals from input sensors and
switches; controls solenoid valves (Purge
control)
o X
Ne signal pick-up Detect crank angle at 180° intervals; sends signal to engine control unit
Installed in distributor o X
Separator Prevents fuel from flowing into charcoal canister
o o
Solenoid valve
(No.1 purge control)
Controls vacuum to solenoid valve (No.2
purge control) and vacuum switch valve
0 X
Solenoid valve (No.2 Purge control)
Controls vacuum to vacuum switch valve o X
Three-way check valve Controls pressure in fuel tank o X
Two-way check valve Controls pressure in fuel tank X o
Vacuum switch valve Regulates evaporative fumes from canis-ter to intake manifold
o X
Water thermo sensor Detects coolant temperature; sends signal to engine control unit
0 X
76G04C-151
4C-80
Page 642 of 1865
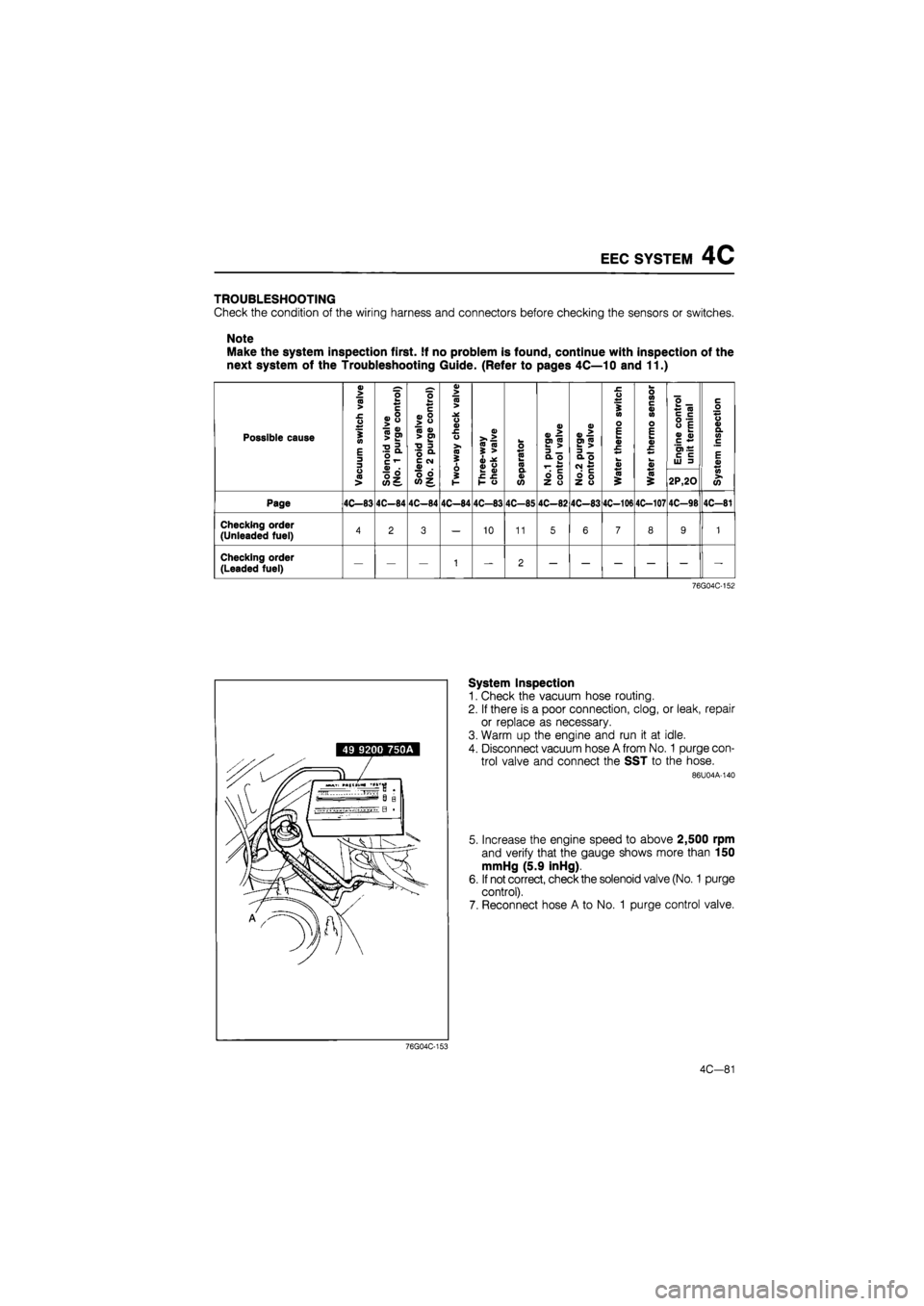
EEC SYSTEM
4C
TROUBLESHOOTING
Check
the
condition
of the
wiring harness
and
connectors before checking
the
sensors
or
switches.
Note
Make
the
system inspection first.
If no
problem
is
found, continue with inspection
of the
next system
of the
Troubleshooting Guide. (Refer
to
pages 4C—10
and 11.)
Possible cause
« > (0 >
£ O
S in
E 3 3
Solenoid
valve
(No.
1 purge
control)
Solenoid
valve
(No.
2 purge
control)
Two-way
check
valve
a>
>. >
i
S
i
^
3>
o
o CO k n
V
*
£
3
_
a
o
k. T-
a>
E»S 3
_
a
o
CM
£
£ O
S in o E tm a> £
w V
o ID C a> in o E k a> £ **
a>
Engine
control
unit
terminal
c o +s o a> a. w c
E a> O <0 >
Solenoid
valve
(No.
1 purge
control)
Solenoid
valve
(No.
2 purge
control)
Two-way
check
valve
>-
0)
£
£
1-
o
Q. d) > o
fe
Z
o
ofe Z
O
(0 (0 $ 2P,20
in
(O
Page 4C—83 4C-84 4C-84 4C—84 4C-83 4C-85 4C-82 4C-83 4C-106 4C-107 4C—98 4C-81
Checking order (Unleaded fuel) 4 2 3 — 10 11 5 6 7 8 9 1
Checking order
(Leaded fuel) — — — 1 — 2
76G04C-152
System Inspection
1. Check
the
vacuum hose routing.
2. If there
is a
poor connection, clog,
or
leak, repair
or replace
as
necessary.
3. Warm
up the
engine
and run it at
idle.
4. Disconnect vacuum hose
A
from
No. 1
purge con-
trol valve
and
connect
the SST to the
hose.
86U04A-140
5. Increase
the
engine speed
to
above 2,500
rpm
and verify that
the
gauge shows more than
150
mmHg
(5.9
inHg).
6. If not correct, check the solenoid valve (No.
1
purge
control).
7. Reconnect hose
A to No. 1
purge control valve.
4C-81
76G04C-153
Page 643 of 1865
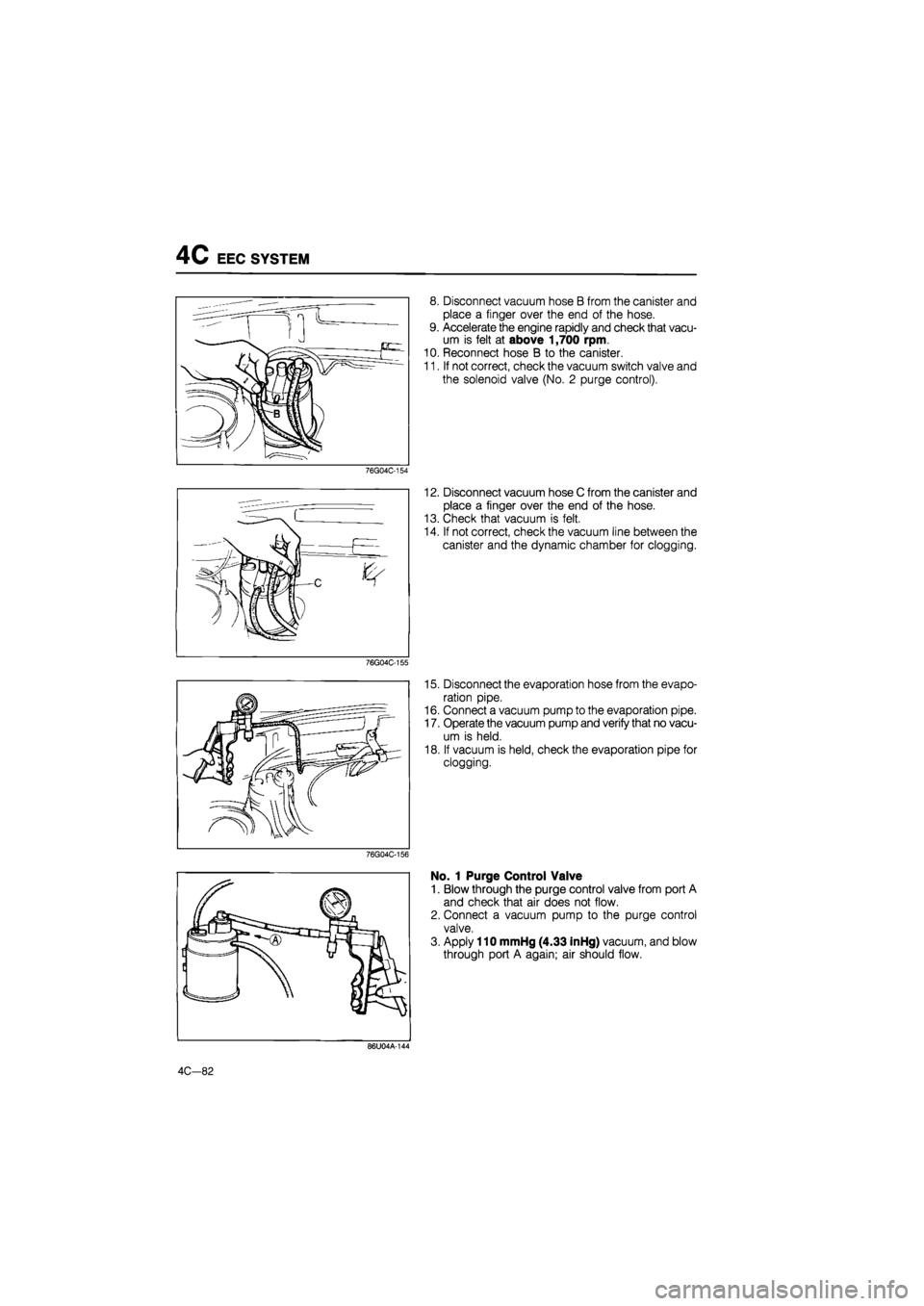
4C EEC SYSTEM
76G04C-154
76G04C-155
76G04C-156
8. Disconnect vacuum hose B from the canister and
place a finger over the end of the hose.
9. Accelerate the engine rapidly and check that vacu-
um is felt at above 1,700 rpm.
10. Reconnect hose B to the canister.
11. If not correct, check the vacuum switch valve and
the solenoid valve (No. 2 purge control).
12. Disconnect vacuum hose C from the canister and
place a finger over the end of the hose.
13. Check that vacuum is felt.
14. If not correct, check the vacuum line between the
canister and the dynamic chamber for clogging.
15. Disconnect the evaporation hose from the evapo-
ration pipe.
16. Connect a vacuum pump to the evaporation pipe.
17. Operate the vacuum pump and verify that no vacu-
um is held.
18. If vacuum is held, check the evaporation pipe for
clogging.
No. 1 Purge Control Valve
1. Blow through the purge control valve from port A
and check that air does not flow.
2. Connect a vacuum pump to the purge control
valve.
3. Apply 110 mmHg (4.33 inHg) vacuum, and blow
through port A again; air should flow.
86U04A-144
4C—82
Page 647 of 1865
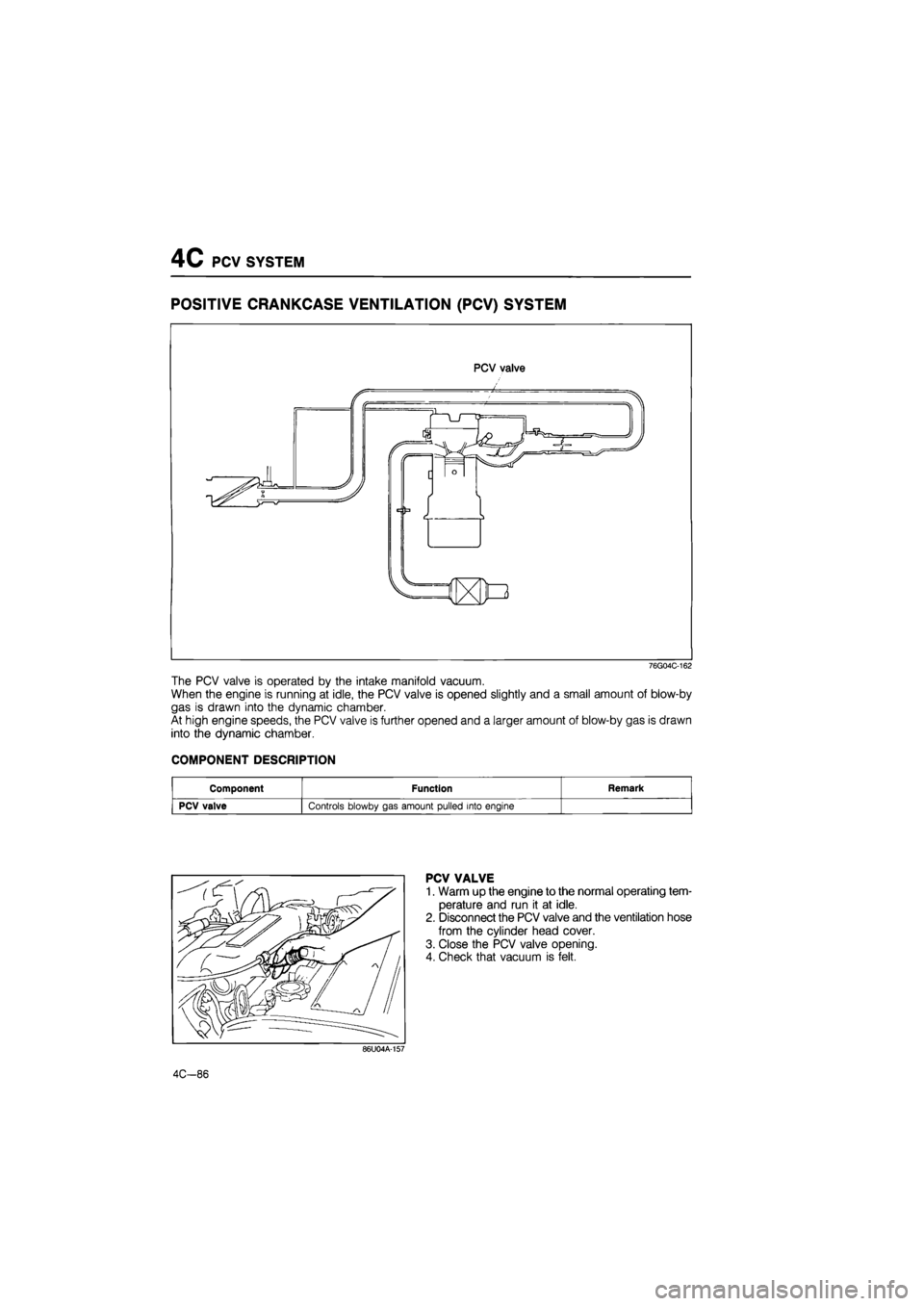
4C PCV SYSTEM
POSITIVE CRANKCASE VENTILATION
(PCV)
SYSTEM
PCV valve
76G04C-162
The PCV valve is operated by the intake manifold vacuum.
When the engine is running at idle, the PCV valve is opened slightly and a small amount of blow-by
gas is drawn into the dynamic chamber.
At high engine speeds, the PCV valve is further opened and a larger amount of blow-by gas is drawn
into the dynamic chamber.
COMPONENT DESCRIPTION
Component Function Remark
PCV valve Controls blowby gas amount pulled into engine
PCV VALVE
1. Warm up the engine to the normal operating tem-
perature and run it at idle.
2. Disconnect the PCV valve and the ventilation hose
from the cylinder head cover.
3. Close the PCV valve opening.
4. Check that vacuum is felt.
86U04A-157
4C-86
Page 658 of 1865
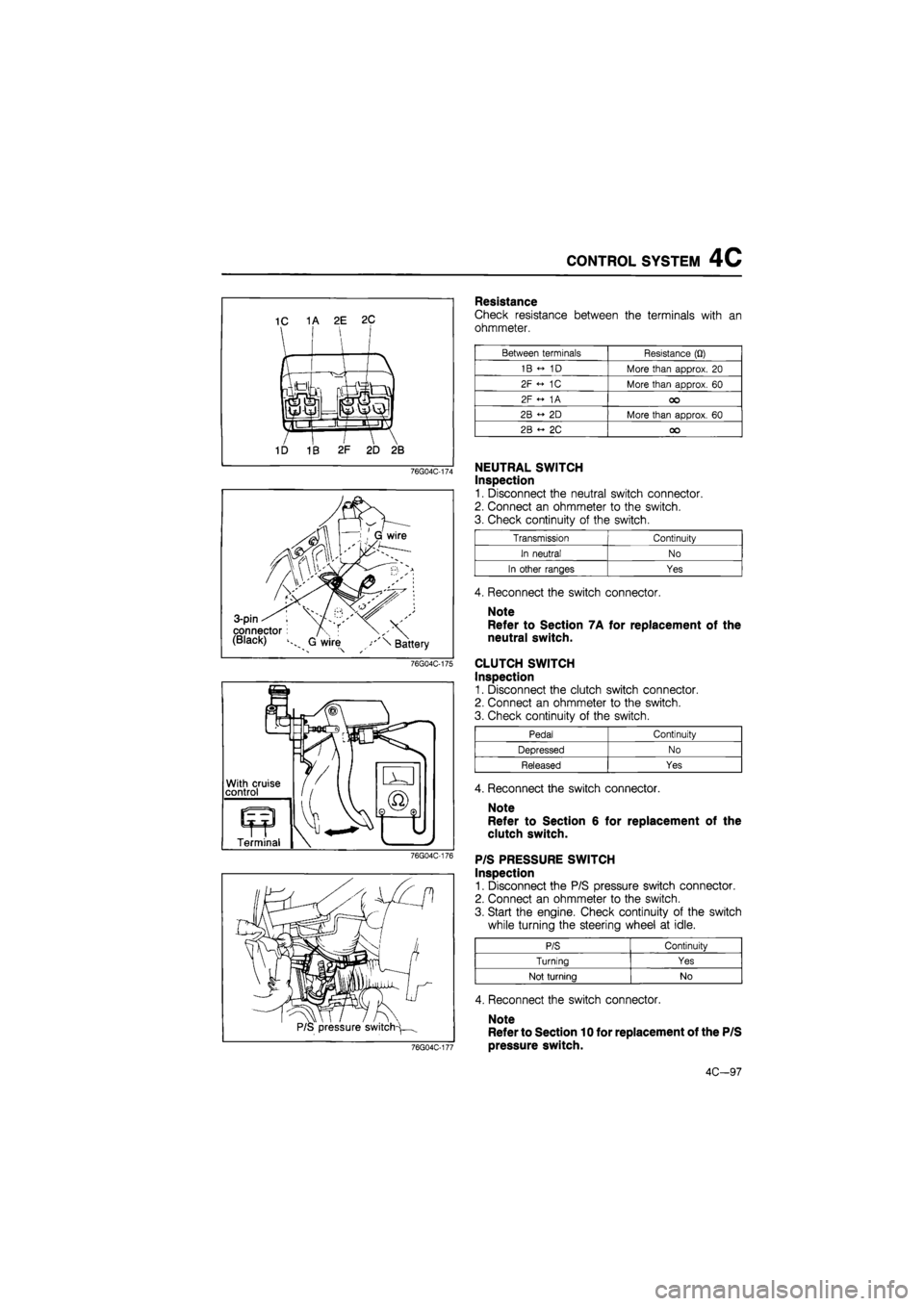
CONTROL SYSTEM 4C
Resistance
Check resistance between the terminals with an
ohmmeter.
Between terminals Resistance (Q)
1B « 1D More than approx. 20
2F <- 1C More than approx. 60
2F « 1A oo
2B « 2D More than approx. 60
2B ~ 2C oo
NEUTRAL SWITCH
Inspection
1. Disconnect the neutral switch connector.
2. Connect an ohmmeter to the switch.
3. Check continuity of the switch.
Transmission Continuity
In neutral No
In other ranges Yes
4. Reconnect the switch connector.
Note
Refer to Section 7A for replacement of the
neutral switch.
CLUTCH SWITCH
Inspection
1. Disconnect the clutch switch connector.
2. Connect an ohmmeter to the switch.
3. Check continuity of the switch.
Pedal Continuity
Depressed No
Released Yes
4. Reconnect the switch connector.
Note
Refer to Section 6 for replacement of the
clutch switch.
P/S PRESSURE SWITCH
Inspection
1. Disconnect the P/S pressure switch connector.
2. Connect an ohmmeter to the switch.
3. Start the engine. Check continuity of the switch
while turning the steering wheel at idle.
P/S Continuity
Turning Yes
Not turning No
4. Reconnect the switch connector.
Note
Refer to Section 10 for replacement of the P/S
pressure switch.
4C-97
Page 659 of 1865
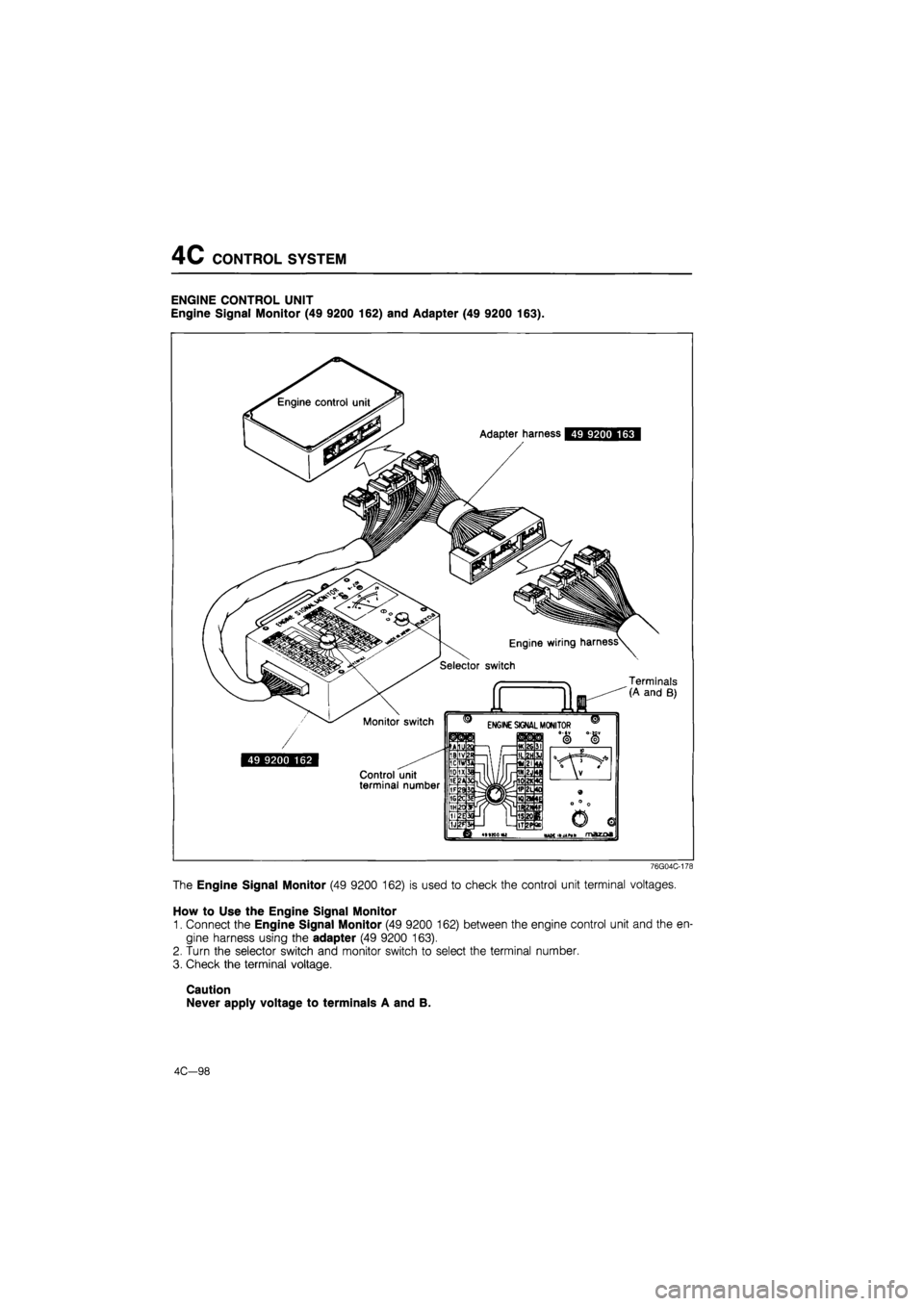
4C CONTROL SYSTEM
ENGINE CONTROL UNIT
Engine Signal Monitor (49 9200 162) and Adapter (49 9200 163).
Adapter harness 49 9200 163
Engine wiring harness^
Selector switch
' —
Monitor switch
49 9200 162
Control unit terminal number
Terminals (A and B)
Q IIIM«I
76G04C-178
The Engine Signal Monitor (49 9200 162) is used to check the control unit terminal voltages.
How to Use the Engine Signal Monitor
1. Connect the Engine Signal Monitor (49 9200 162) between the engine control unit and the en-
gine harness using the adapter (49 9200 163).
2. Turn the selector switch and monitor switch to select the terminal number.
3. Check the terminal voltage.
Caution
Never apply voltage to terminals A and B.
4C—98