MAZDA 626 1987 Workshop Manual
Manufacturer: MAZDA, Model Year: 1987, Model line: 626, Model: MAZDA 626 1987Pages: 1865, PDF Size: 94.35 MB
Page 1801 of 1865
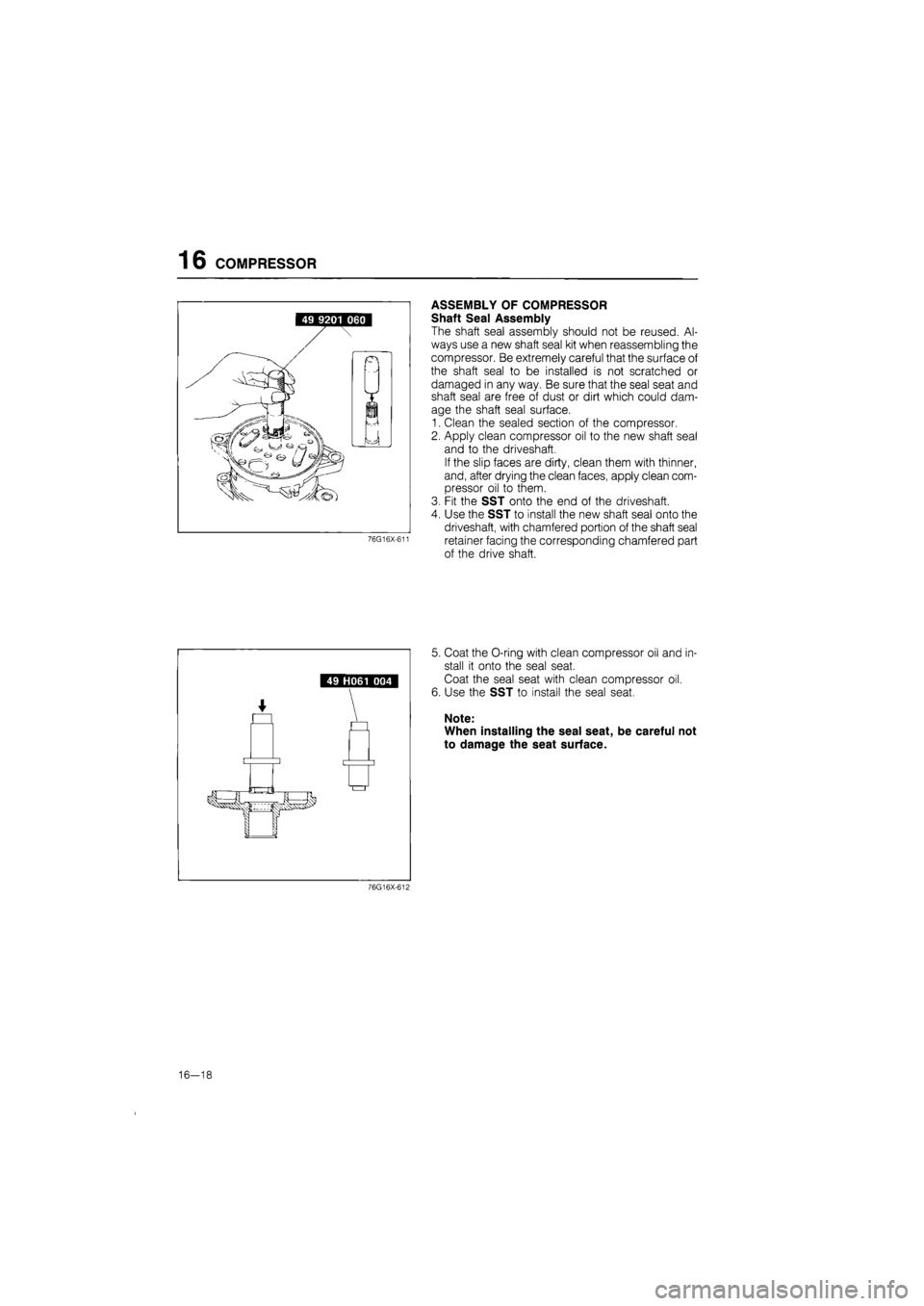
16 COMPRESSOR
76G16X-611
ASSEMBLY OF COMPRESSOR
Shaft Seal Assembly
The shaft seal assembly should not be reused. Al-
ways use a new shaft seal kit when reassembling the
compressor. Be extremely careful that the surface of
the shaft seal to be installed is not scratched or
damaged in any way. Be sure that the seal seat and
shaft seal are free of dust or dirt which could dam-
age the shaft seal surface.
1. Clean the sealed section of the compressor.
2. Apply clean compressor oil to the new shaft seal
and to the driveshaft.
If the slip faces are dirty, clean them with thinner,
and, after drying the clean faces, apply clean com-
pressor oil to them.
3. Fit the SST onto the end of the driveshaft.
4. Use the SST to install the new shaft seal onto the
driveshaft, with chamfered portion of the shaft seal
retainer facing the corresponding chamfered part
of the drive shaft.
5. Coat the O-ring with clean compressor oil and in-
stall it onto the seal seat.
Coat the seal seat with clean compressor oil.
6. Use the SST to install the seal seat.
Note:
When installing the seal seat, be careful not
to damage the seat surface.
76G16X-612
16-18
Page 1802 of 1865
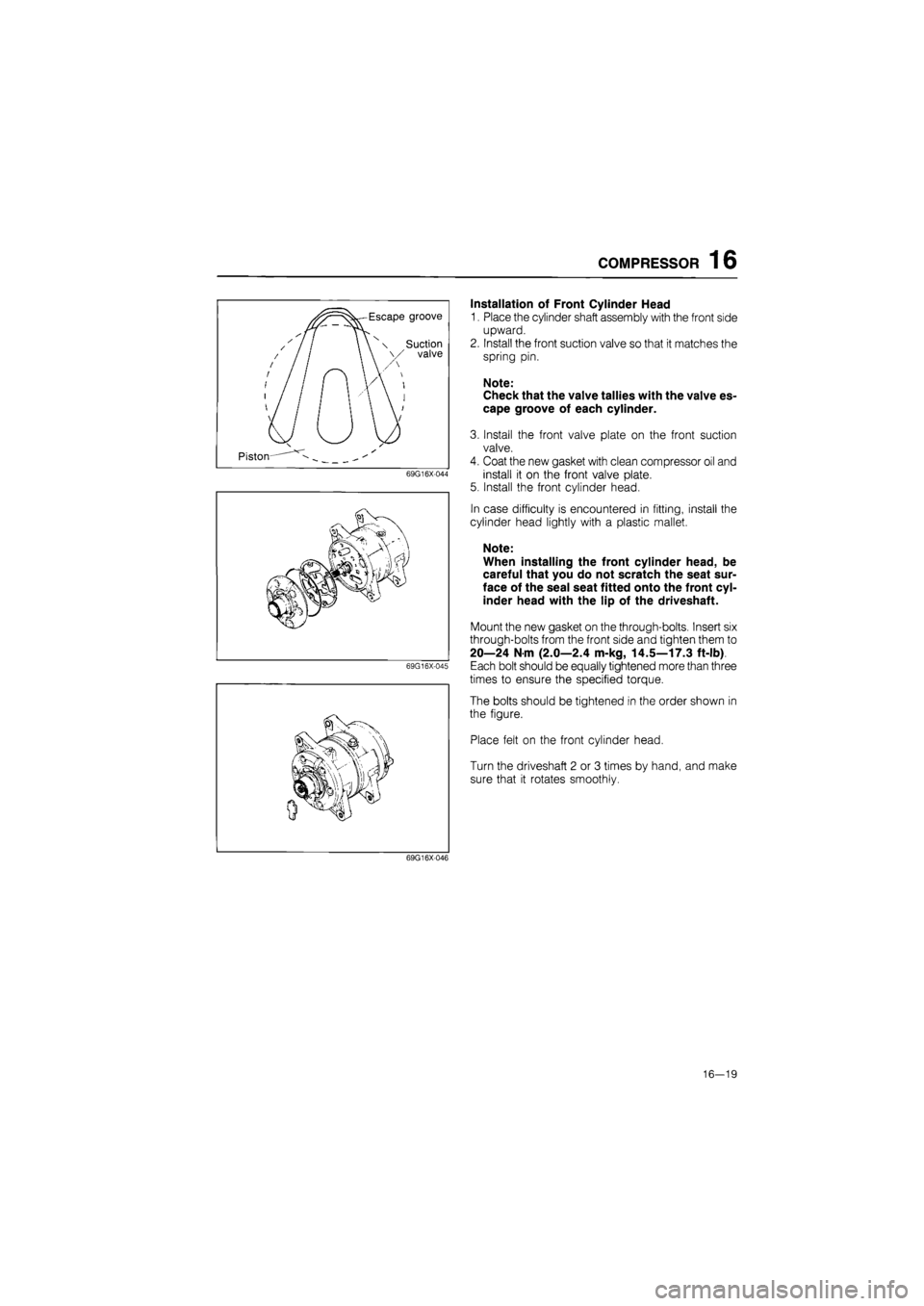
COMPRESSOR 16
Escape groove
^ / / / / j / / ' / / / / /
' / / I / /
1 \ \ x Suction \ \ \/ valve
n W: \ / / y /
I u
Piston— ^
69G16X-044
69G16X-045
Installation of Front Cylinder Head
1. Place the cylinder shaft assembly with the front side
upward.
2. Install the front suction valve so that it matches the
spring pin.
Note:
Check that the valve tallies with the valve es-
cape groove of each cylinder.
3. Install the front valve plate on the front suction
valve.
4. Coat the new gasket with clean compressor oil and
install it on the front valve plate.
5. Install the front cylinder head.
In case difficulty is encountered in fitting, install the
cylinder head lightly with a plastic mallet.
Note:
When installing the front cylinder head, be
careful that you do not scratch the seat sur-
face of the seal seat fitted onto the front cyl-
inder head with the lip of the driveshaft.
Mount the new gasket on the through-bolts. Insert six
through-bolts from the front side and tighten them to
20—24 N m (2.0—2.4 m-kg, 14.5—17.3 ft-lb)
Each bolt should be equally tightened more than three
times to ensure the specified torque.
The bolts should be tightened in the order shown in
the figure.
Place felt on the front cylinder head.
Turn the driveshaft 2 or 3 times by hand, and make
sure that it rotates smoothly.
69G16X046
16—19
Page 1803 of 1865
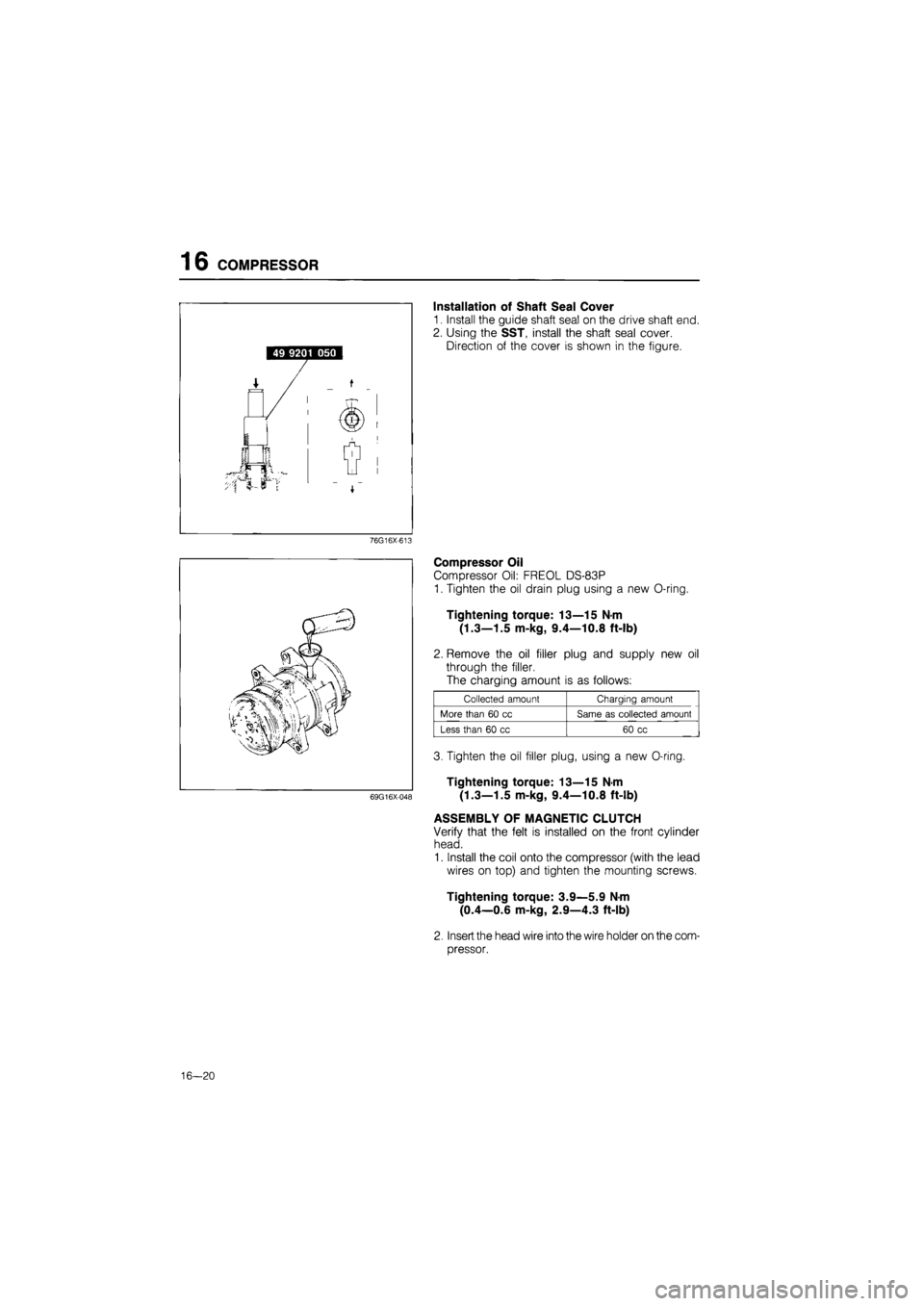
16 COMPRESSOR
Installation of Shaft Seal Cover
1. Install the guide shaft seal on the drive shaft end.
2. Using the SST, install the shaft seal cover.
Direction of the cover is shown in the figure.
76G16X-613
69G16X-048
Compressor Oil
Compressor Oil: FREOL DS-83P
1. Tighten the oil drain plug using a new O-ring.
Tightening torque: 13—15 N-m
(1.3—1.5 m-kg, 9.4—10.8 ft-lb)
2. Remove the oil filler plug and supply new oil
through the filler.
The charging amount is as follows:
Collected amount Charging amount
More than
60 cc
Same
as
collected amount
Less than
60 cc
60
cc
3. Tighten the oil filler plug, using a new O-ring.
Tightening torque: 13—15 N-m
(1.3—1.5 m-kg, 9.4—10.8 ft-lb)
ASSEMBLY OF MAGNETIC CLUTCH
Verify that the felt is installed on the front cylinder
head.
1. Install the coil onto the compressor (with the lead
wires on top) and tighten the mounting screws.
Tightening torque: 3.9—5.9 N-m
(0.4—0.6 m-kg, 2.9—4.3 ft-lb)
2. Insert the head wire into the wire holder on the com-
pressor.
16—20
Page 1804 of 1865
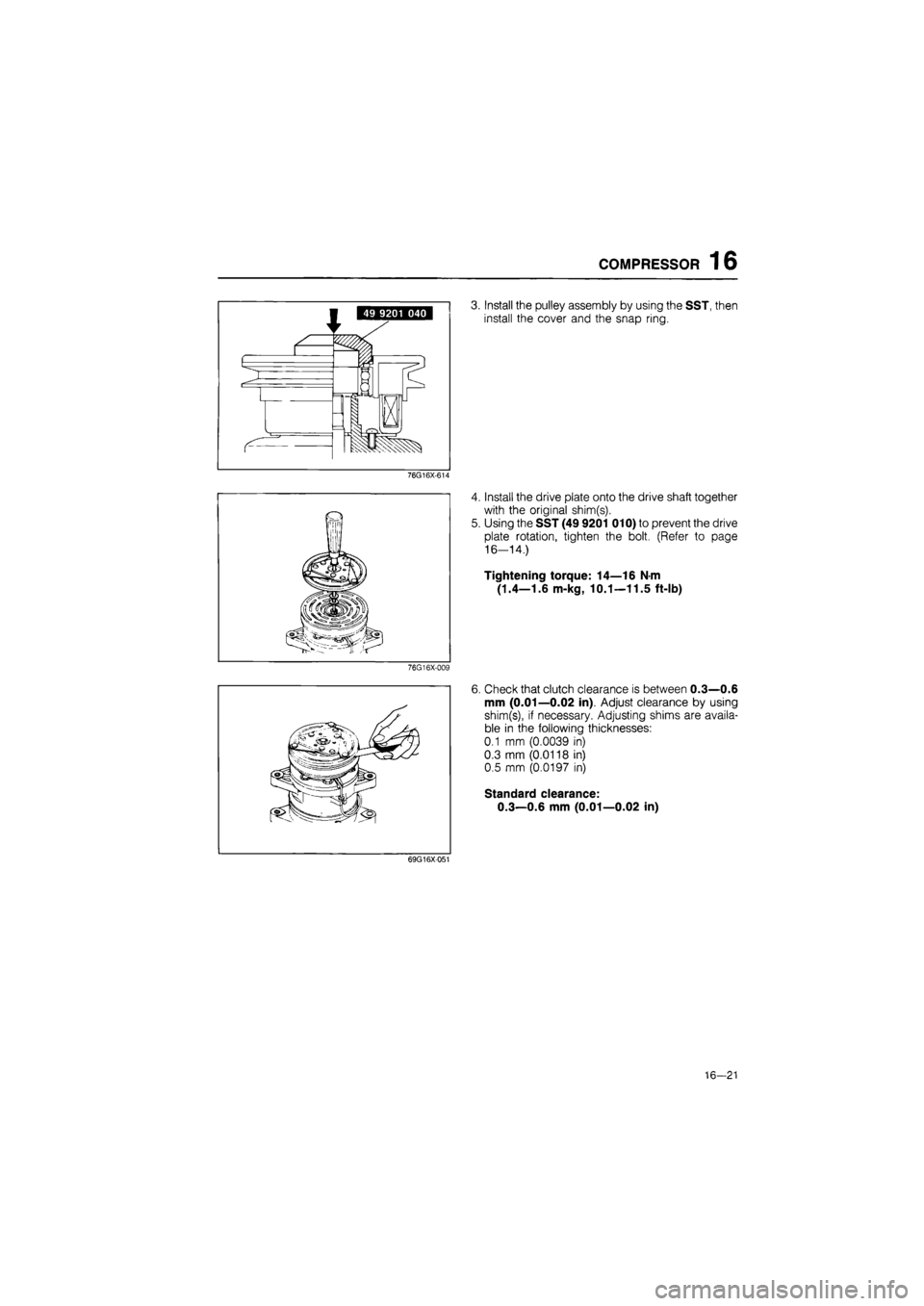
COMPRESSOR 16
3. Install the pulley assembly by using the SST, then
install the cover and the snap ring.
76G16X-614
4. Install the drive plate onto the drive shaft together
with the original shim(s).
5. Using the SST (49 9201 010) to prevent the drive
plate rotation, tighten the bolt. (Refer to page
16-14.)
Tightening torque: 14—16 N-m
(1.4—1.6 m-kg, 10.1—11.5 ft-lb)
76G16X-009
6. Check that clutch clearance is between 0.3—0.6
mm (0.01—0.02 in). Adjust clearance by using
shim(s), if necessary. Adjusting shims are availa-
ble in the following thicknesses:
0.1 mm (0.0039 in)
0.3 mm (0.0118 in)
0.5 mm (0.0197 in)
Standard clearance:
0.3—0.6 mm (0.01—0.02 in)
69G16X-051
16—21
Page 1805 of 1865
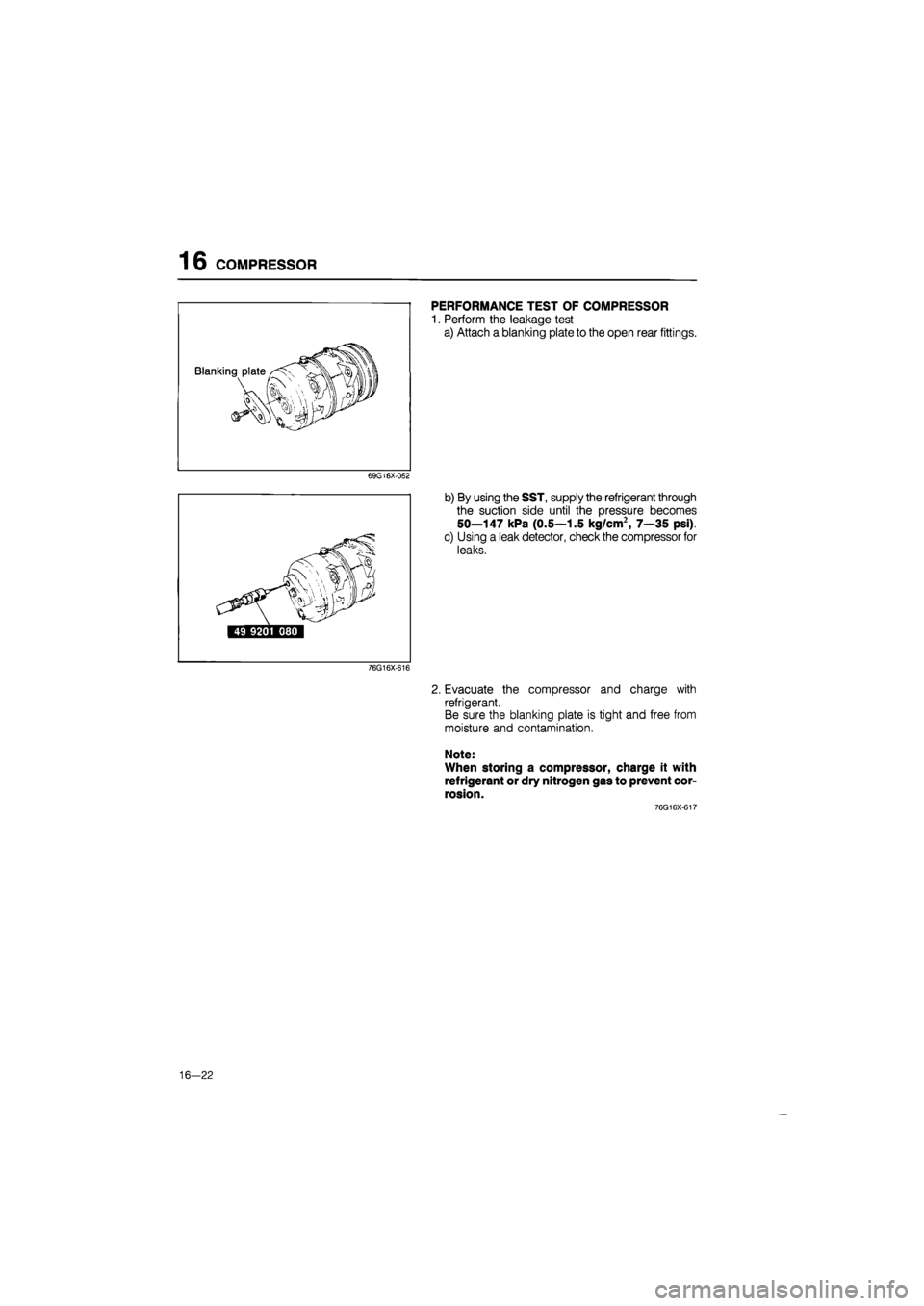
16 COMPRESSOR
PERFORMANCE TEST OF COMPRESSOR
1. Perform the leakage test
a) Attach a blanking plate to the open rear fittings.
69G16X-OS2
b) By using the SST, supply the refrigerant through
the suction side until the pressure becomes
50—147 kPa (0.5—1.5 kg/cm2, 7—35 psi).
c) Using a leak detector, check the compressor for
leaks.
76G16X-616
2. Evacuate the compressor and charge with
refrigerant.
Be sure the blanking plate is tight and free from
moisture and contamination.
Note:
When storing a compressor, charge it with
refrigerant or dry nitrogen gas to prevent cor-
rosion.
76G16X-617
16—22
Page 1806 of 1865
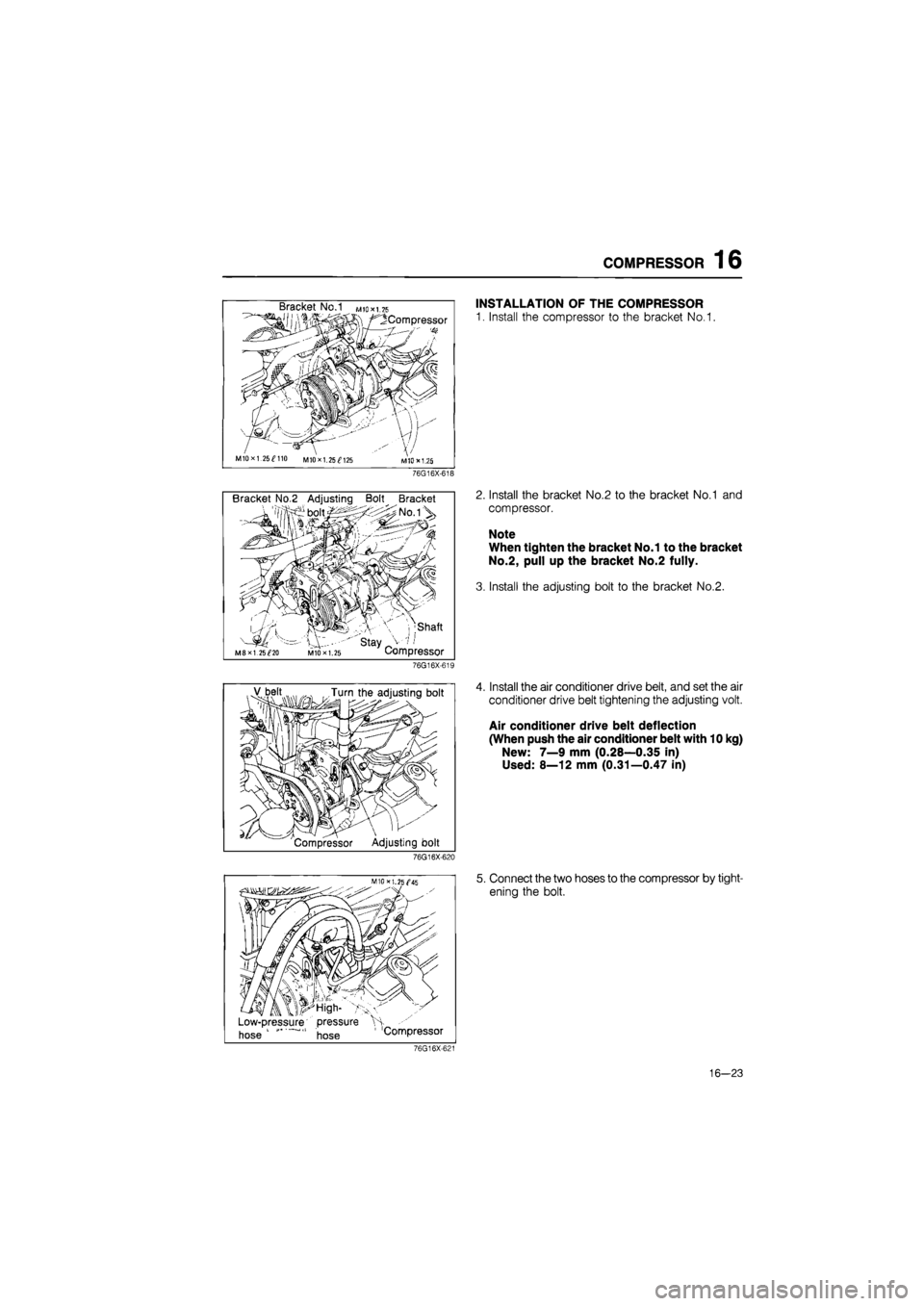
COMPRESSOR 16
Bracket No/I mio*i.75
/^Compressor
V'
MIOxl.25^110 M10X1.25^125 M1DX1.2S
76G16X-618
Bracket No.2 Adjusting Bolt Bracket
• boit/:> X ;>No.iV
•S3-
f'f
// mi
I 1 I 1 Shaft
M8 x 1.25^20 • ' Stay V-;,' M10X1.25 Compressor 76G16X-619
V belt Turn the adjusting bolt
Compressor Adjusting bolt
76G16X-620
MIOxl. 25^45
Low-pressure' pressure "H
hose hose Compressor
INSTALLATION OF THE COMPRESSOR
1. Install the compressor to the bracket No.1.
2. Install the bracket No.2 to the bracket No.1 and
compressor.
Note
When tighten the bracket No.1 to the bracket
No.2, pull up the bracket No.2 fully.
3. Install the adjusting bolt to the bracket No.2.
4. Install the air conditioner drive belt, and set the air
conditioner drive belt tightening the adjusting volt.
Air conditioner drive belt deflection
(When push the air conditioner belt with 10 kg)
New: 7—9 mm (0.28—0.35 in)
Used: 8—12 mm (0.31—0.47 in)
5. Connect the two hoses to the compressor by tight-
ening the bolt.
76G16X-621
16—23
Page 1807 of 1865
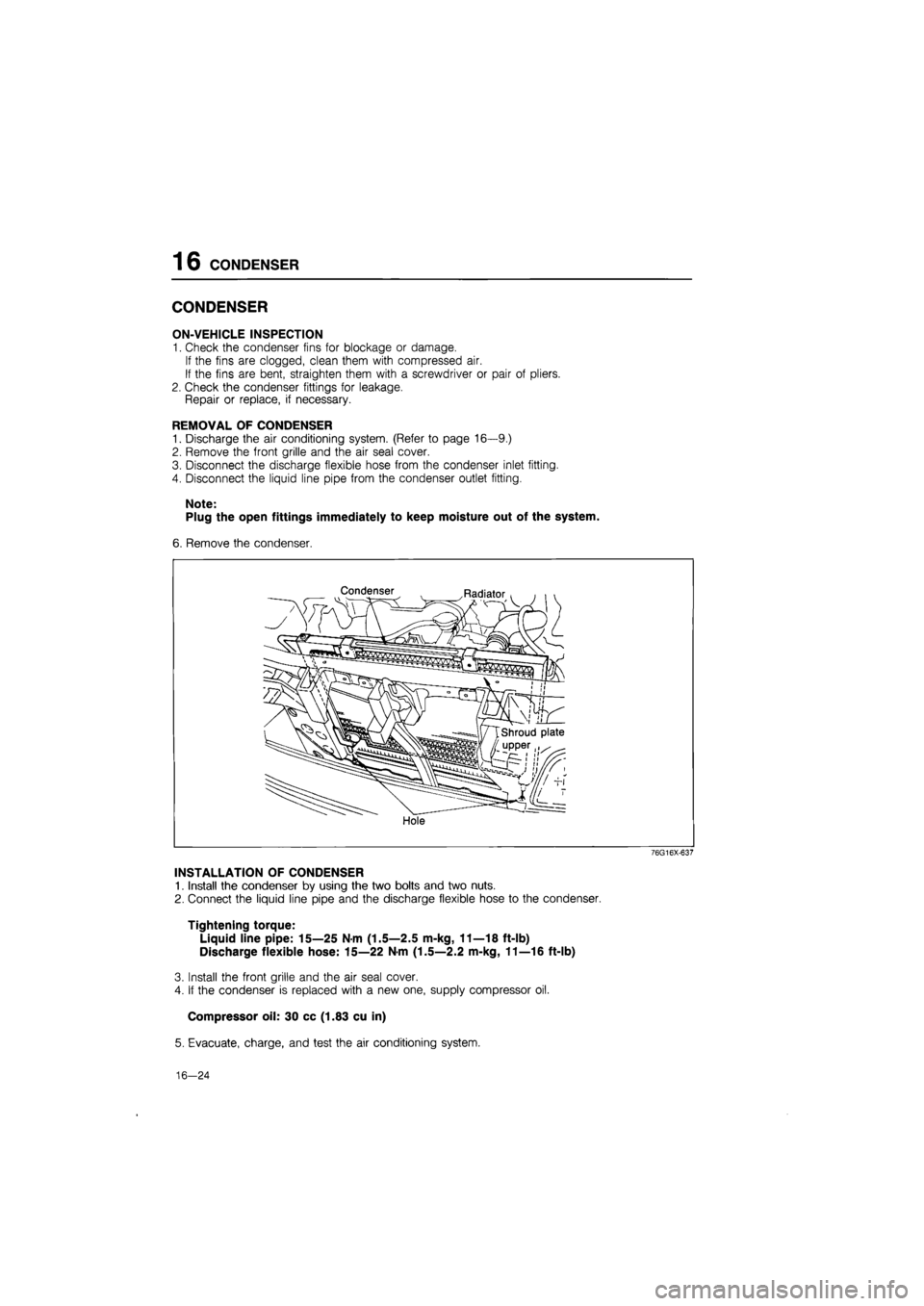
16 CONDENSER
CONDENSER
ON-VEHICLE INSPECTION
1. Check the condenser fins for blockage or damage.
If the fins are clogged, clean them with compressed air.
If the fins are bent, straighten them with a screwdriver or pair of pliers.
2. Check the condenser fittings for leakage.
Repair or replace, if necessary.
REMOVAL OF CONDENSER
1. Discharge the air conditioning system. (Refer to page 16—9.)
2. Remove the front grille and the air seal cover.
3. Disconnect the discharge flexible hose from the condenser inlet fitting.
4. Disconnect the liquid line pipe from the condenser outlet fitting.
Note:
Plug the open fittings immediately to keep moisture out of the system.
6. Remove the condenser.
Condenser Radiator
Hole
76G16X-637
INSTALLATION OF CONDENSER
1. Install the condenser by using the two bolts and two nuts.
2. Connect the liquid line pipe and the discharge flexible hose to the condenser.
Tightening torque:
Liquid line pipe: 15—25 Nm (1.5—2.5 m-kg, 11—18 ft-lb)
Discharge flexible hose: 15—22 N-m (1.5—2.2 m-kg, 11—16 ft-lb)
3. Install the front grille and the air seal cover.
4. If the condenser is replaced with a new one, supply compressor oil.
Compressor oil: 30 cc (1.83 cu in)
5. Evacuate, charge, and test the air conditioning system.
16—24
Page 1808 of 1865
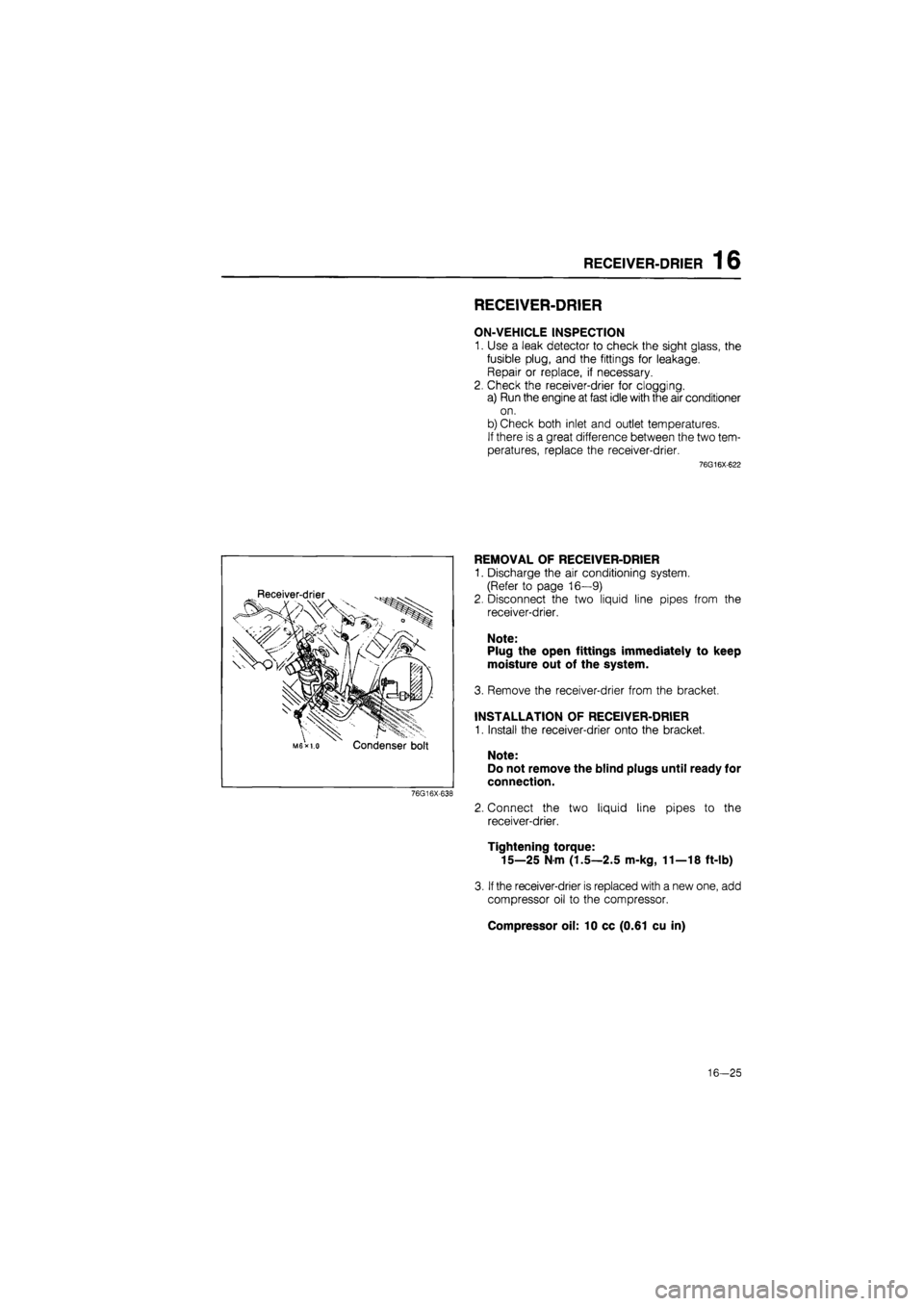
RECEIVER-DRIER 16
RECEIVER-DRIER
ON-VEHICLE INSPECTION
1. Use a leak detector to check the sight glass, the
fusible plug, and the fittings for leakage.
Repair or replace, if necessary.
2. Check the receiver-drier for clogging.
a) Run the engine at fast idle with the air conditioner
on.
b) Check both inlet and outlet temperatures.
If there is a great difference between the two tem-
peratures, replace the receiver-drier.
76G16X-622
Receiver-drier
Condenser bolt
76G16X-638
REMOVAL OF RECEIVER-DRIER
1. Discharge the air conditioning system.
(Refer to page 16—9)
2. Disconnect the two liquid line pipes from the
receiver-drier.
Note:
Plug the open fittings immediately to keep
moisture out of the system.
3. Remove the receiver-drier from the bracket.
INSTALLATION OF RECEIVER-DRIER
1. Install the receiver-drier onto the bracket.
Note:
Do not remove the blind plugs until ready for
connection.
2. Connect the two liquid line pipes to the
receiver-drier.
Tightening torque:
15—25 N m (1.5—2.5 m-kg, 11—18 ft-lb)
3.
If
the receiver-drier is replaced with a new one, add
compressor oil to the compressor.
Compressor oil: 10 cc (0.61 cu in)
16-25
Page 1809 of 1865
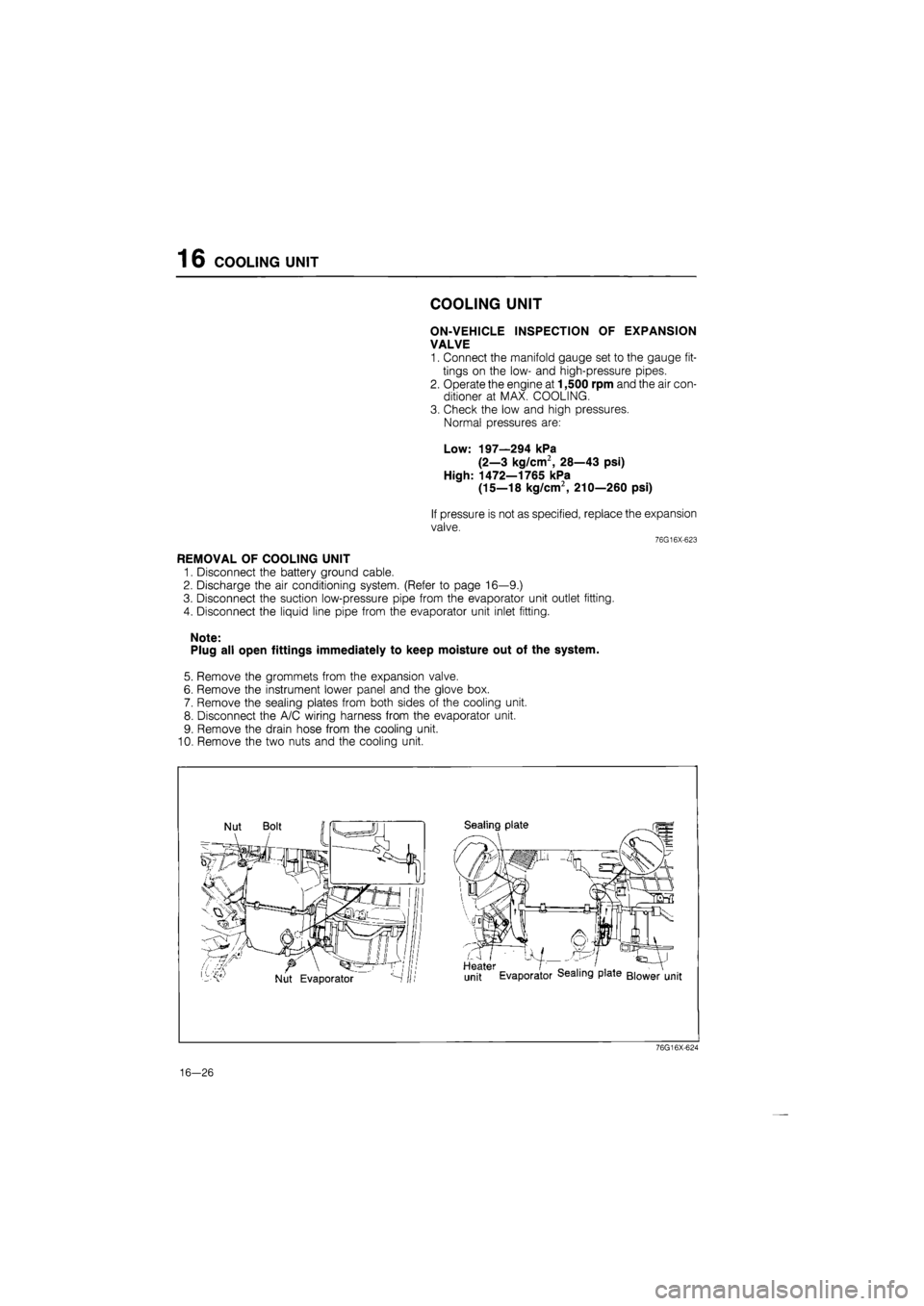
16 COOLING UNIT
COOLING UNIT
ON-VEHICLE INSPECTION OF EXPANSION
VALVE
1. Connect the manifold gauge set to the gauge fit-
tings on the low- and high-pressure pipes.
2. Operate the engine at 1,500 rpm and the air con-
ditioner at MAX. COOLING.
3. Check the low and high pressures.
Normal pressures are:
Low: 197—294 kPa
(2—3 kg/cm2, 28—43 psi)
High: 1472—1765 kPa
(15—18 kg/cm2, 210—260 psi)
If pressure is not as specified, replace the expansion
valve.
76G16X-623
REMOVAL OF COOLING UNIT
1. Disconnect the battery ground cable.
2. Discharge the air conditioning system. (Refer to page 16—9.)
3. Disconnect the suction low-pressure pipe from the evaporator unit outlet fitting.
4. Disconnect the liquid line pipe from the evaporator unit inlet fitting.
Note:
Plug all open fittings immediately to keep moisture out of the system.
5. Remove the grommets from the expansion valve.
6. Remove the instrument lower panel and the glove box.
7. Remove the sealing plates from both sides of the cooling unit.
8. Disconnect the A/C wiring harness from the evaporator unit.
9. Remove the drain hose from the cooling unit.
10. Remove the two nuts and the cooling unit.
76G16X-624
16-26
Page 1810 of 1865
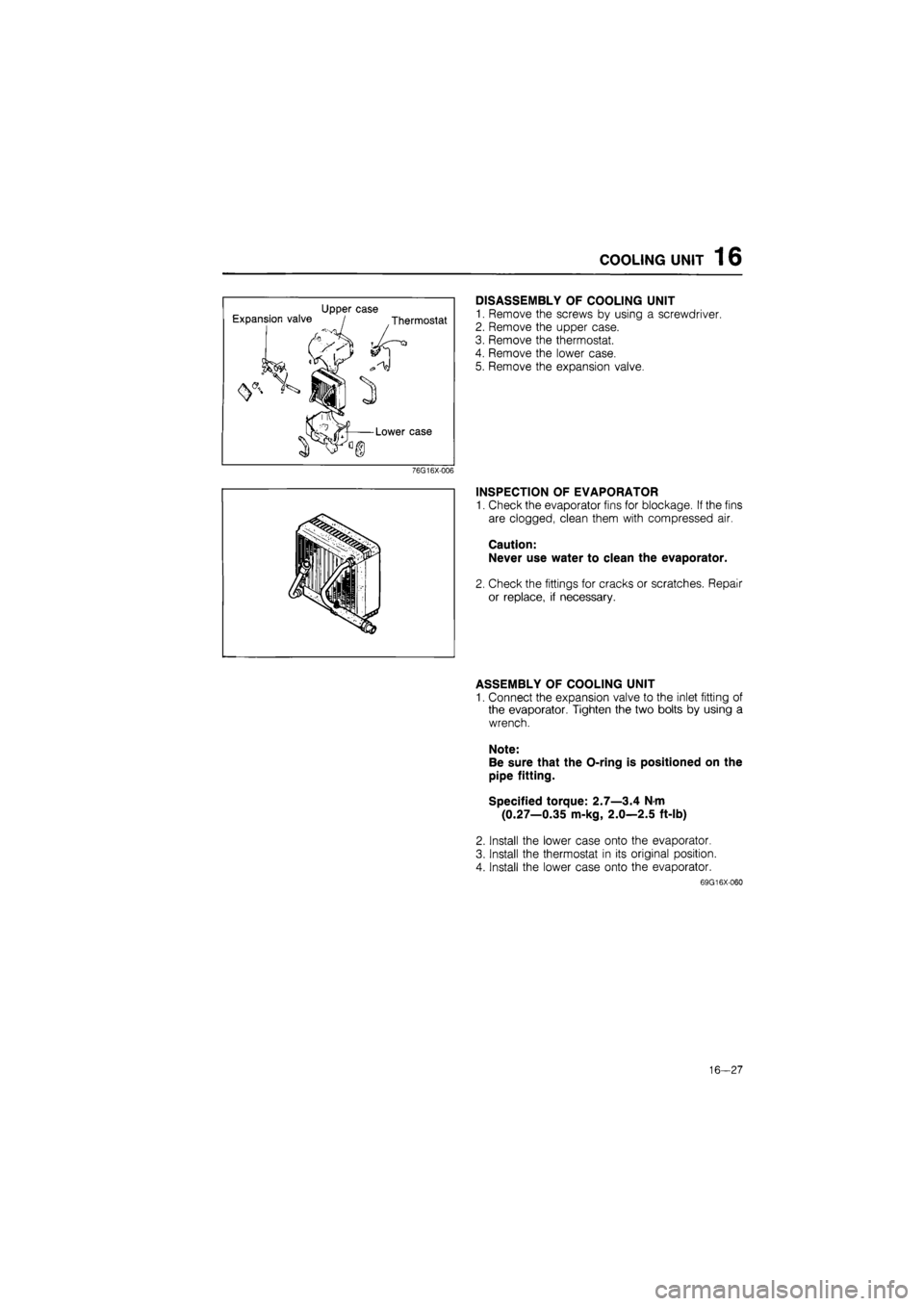
COOLING UNIT 1 6
Upper case Expansion valve / Thermostat
Lower case
76G16X-006
DISASSEMBLY OF COOLING UNIT
1. Remove the screws by using a screwdriver.
2. Remove the upper case.
3. Remove the thermostat.
4. Remove the lower case.
5. Remove the expansion valve.
INSPECTION OF EVAPORATOR
1. Check the evaporator fins for blockage. If the fins
are clogged, clean them with compressed air.
Caution:
Never use water to clean the evaporator.
2. Check the fittings for cracks or scratches. Repair
or replace, if necessary.
ASSEMBLY OF COOLING UNIT
1. Connect the expansion valve to the inlet fitting of
the evaporator. Tighten the two bolts by using a
wrench.
Note:
Be sure that the O-ring is positioned on the
pipe fitting.
Specified torque: 2.7—3.4 N-m
(0.27—0.35 m-kg, 2.0—2.5 ft-lb)
2. Install the lower case onto the evaporator.
3. Install the thermostat in its original position.
4. Install the lower case onto the evaporator.
69G16X-060
16—27