ESP MAZDA 626 1987 Workshop Manual
[x] Cancel search | Manufacturer: MAZDA, Model Year: 1987, Model line: 626, Model: MAZDA 626 1987Pages: 1865, PDF Size: 94.35 MB
Page 4 of 1865
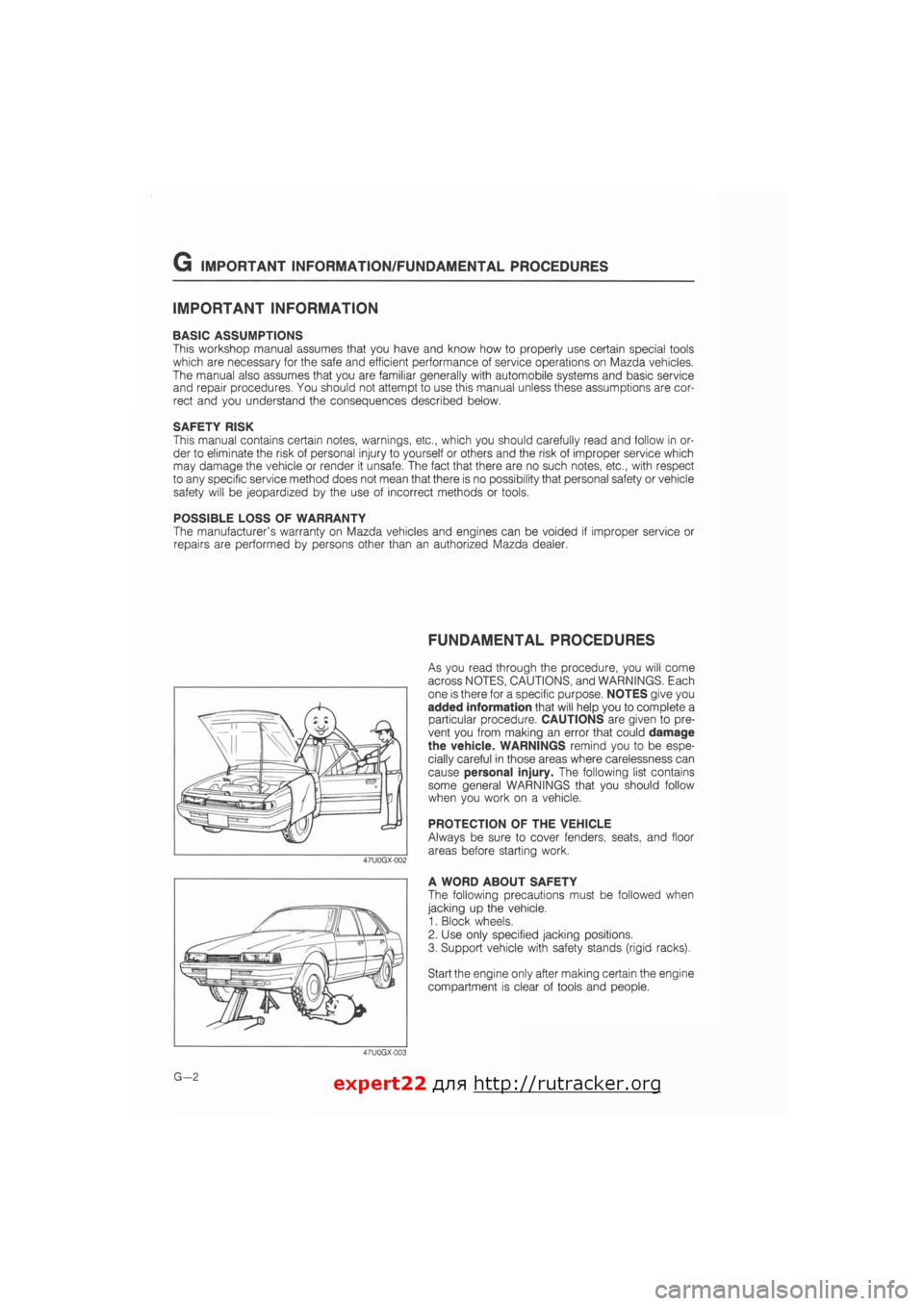
G IMPORTANT INFORMATION/FUNDAMENTAL PROCEDURES
IMPORTANT INFORMATION
BASIC ASSUMPTIONS
This workshop manual assumes that you have arid know how to properly use certain special tools
which are necessary for the safe and efficient performance of service operations on Mazda vehicles.
The manual also assumes that you are familiar generally with automobile systems and basic service
and repair procedures. You should not attempt to use this manual unless these assumptions are cor-
rect and you understand the consequences described below.
SAFETY RISK
This manual contains certain notes, warnings, etc., which you should carefully read and follow in or-
der to eliminate the risk of personal injury to yourself or others and the risk of improper service which
may damage the vehicle or render it unsafe. The fact that there are no such notes, etc., with respect
to any specific service method does not mean that there is no possibility that personal safety or vehicle
safety will be jeopardized by the use of incorrect methods or tools.
POSSIBLE LOSS OF WARRANTY
The manufacturer's warranty on Mazda vehicles and engines can be voided if improper service or
repairs are performed by persons other than an authorized Mazda dealer.
FUNDAMENTAL PROCEDURES
As you read through the procedure, you will come
across NOTES, CAUTIONS, and WARNINGS. Each
one is there for a specific purpose. NOTES give you
added information that will help you to complete a
particular procedure. CAUTIONS are given to pre-
vent you from making an error that could damage
the vehicle. WARNINGS remind you to be espe-
cially careful in those areas where carelessness can
cause personal injury. The following list contains
some general WARNINGS that you should follow
when you work on a vehicle.
PROTECTION OF THE VEHICLE
Always be sure to cover fenders, seats, and floor
areas before starting work.
A WORD ABOUT SAFETY
The following precautions must be followed when
jacking up the vehicle.
1. Block wheels.
2. Use only specified jacking positions.
3. Support vehicle with safety stands (rigid racks).
Start the engine only after making certain the engine
compartment is clear of tools and people.
G—2 expert22 fl/i* http://rutracker.org
Page 11 of 1865
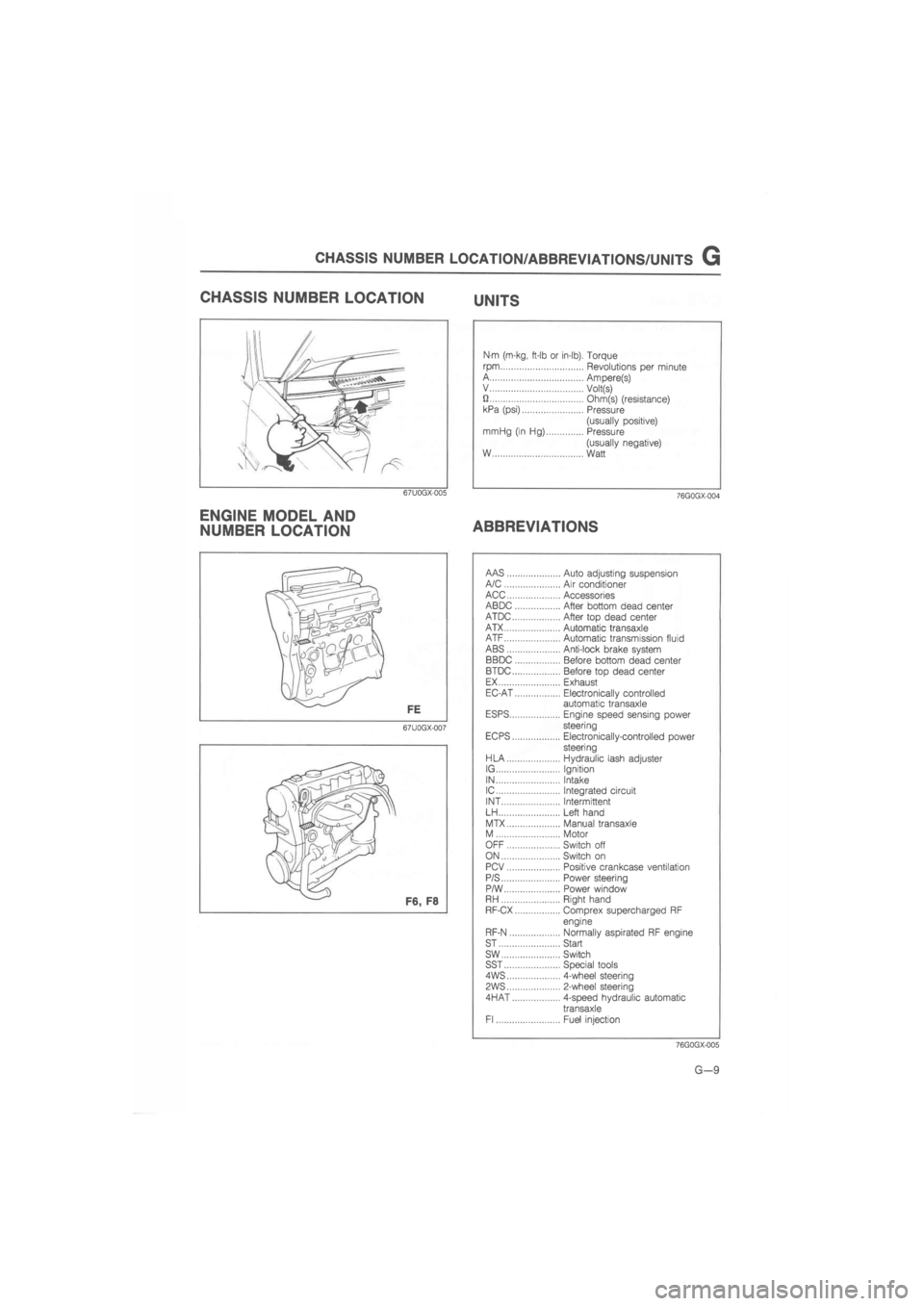
CHASSIS NUMBER LOCATION/ABBREVIATIONS/UNITS G
CHASSIS NUMBER LOCATION UNITS
67U0GX-005
ENGINE MODEL AND
NUMBER LOCATION
Nm (m-kg, ft-lb or in-lb). Torque
rpm Revolutions per minute A Ampere(s) V Volt(s) U Ohm(s) (resistance) kPa (psi) Pressure
(usually positive) mrriHg (in Hg) Pressure
(usually negative) W Watt
76G0GX-004
ABBREVIATIONS
67U0GX-007
AAS Auto adjusting suspension A/C Air conditioner ACC Accessories ABDC After bottom dead center ATDC After top dead center ATX Automatic transaxle ATF Automatic transmission fluid ABS Anti-lock brake system BBDC Before bottom dead center BTDC Before top dead center EX Exhaust EC-AT Electronically controlled automatic transaxle ESPS Engine speed sensing power steering EC PS Electronically-controlled power steering HLA Hydraulic lash adjuster IG Ignition IN Intake IC Integrated circuit INT Intermittent LH Left hand
MTX Manual transaxle M Motor OFF Switch off ON Switch on PCV Positive crankcase ventilation P/S Power steering P/W Power window RH Right hand RF-CX Comprex supercharged RF
engine
RF-N Normally aspirated RF engine ST Start sw Switch SST Special tools 4WS 4-wheel steering
PWS 2-wheel steering
4HAT 4-speed hydraulic automatic
transaxle Fl Fuel injection
76GQGX-005
G—9
Page 81 of 1865
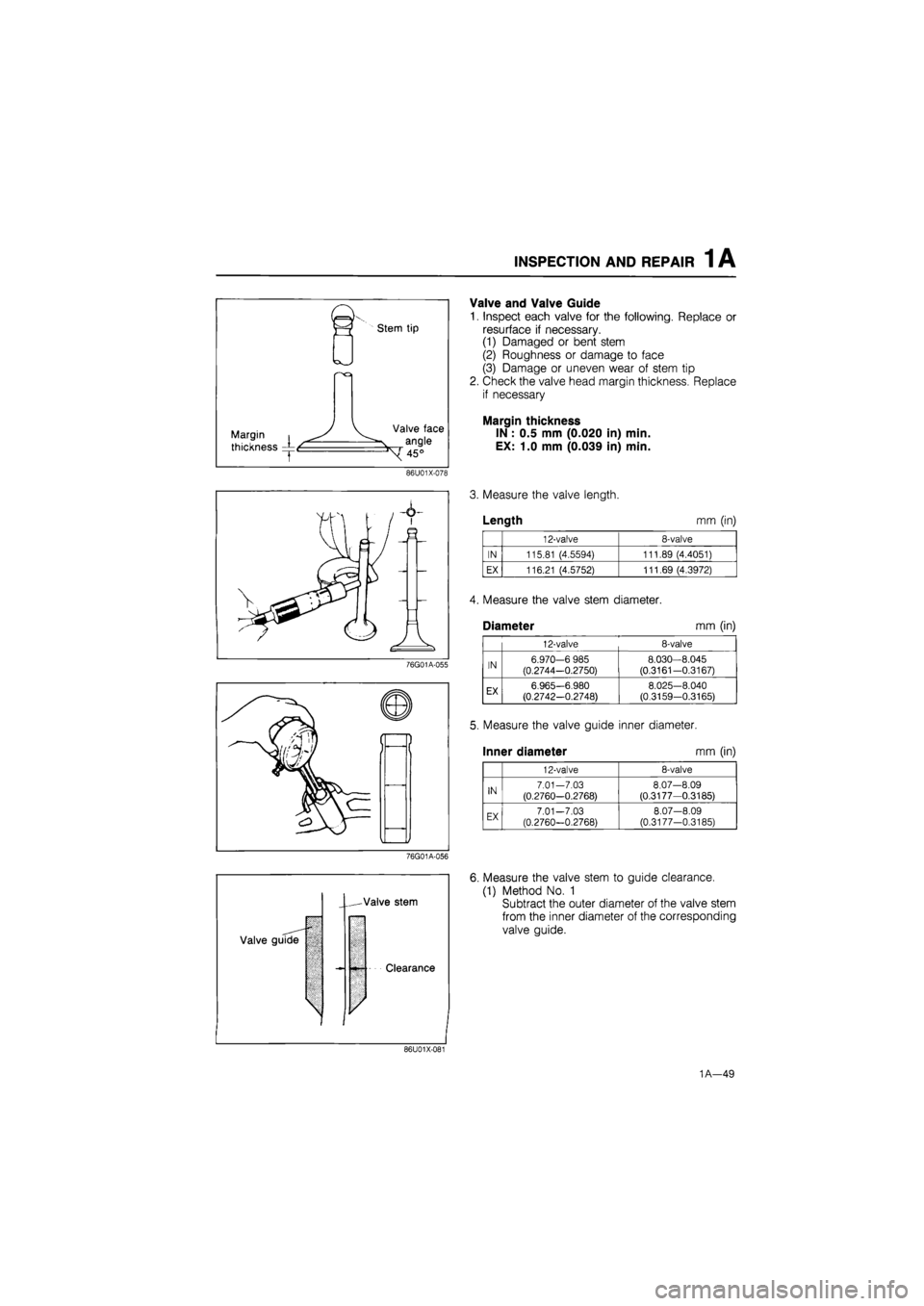
INSPECTION AND REPAIR 1 A
Stem tip
Margin
thickness
Valve face
angle
45°
86U01X-078
76G01A-055
(
—SY/ in
76G01A-056
Valve guide
-Valve stem
Clearance
V
Valve and Valve Guide
1. Inspect each valve for the following. Replace or
resurface if necessary.
(1) Damaged or bent stem
(2) Roughness or damage to face
(3) Damage or uneven wear of stem tip
2. Check the valve head margin thickness. Replace
if necessary
Margin thickness
IN : 0.5 mm (0.020 in) min.
EX: 1.0 mm (0.039 in) min.
3. Measure the valve length.
Length mm (in)
12-valve 8-valve
IN 115.81 (4.5594) 111.89 (4.4051)
EX 116.21 (4.5752) 111.69 (4.3972)
Measure the valve stem diameter.
Diameter mm (in)
12-valve 8-valve
IN 6.970-6 985
(0.2744-0.2750)
8.030—8.045
(0.3161-0.3167)
EX 6.965-6.980 (0.2742-0.2748) 8.025-8.040 (0.3159-0.3165)
5. Measure the valve guide inner diameter.
Inner diameter mm (in)
12-valve 8-valve
IN 7.01-7.03 (0.2760—0.2768) 8.07—8.09
(0.3177—0.3185)
EX 7.01-7.03
(0.2760-0.2768)
8.07-8.09
(0.3177-0.3185)
6. Measure the valve stem to guide clearance.
(1) Method No. 1
Subtract the outer diameter of the valve stem
from the inner diameter of the corresponding
valve guide.
86U01X-117
1A—49
Page 167 of 1865
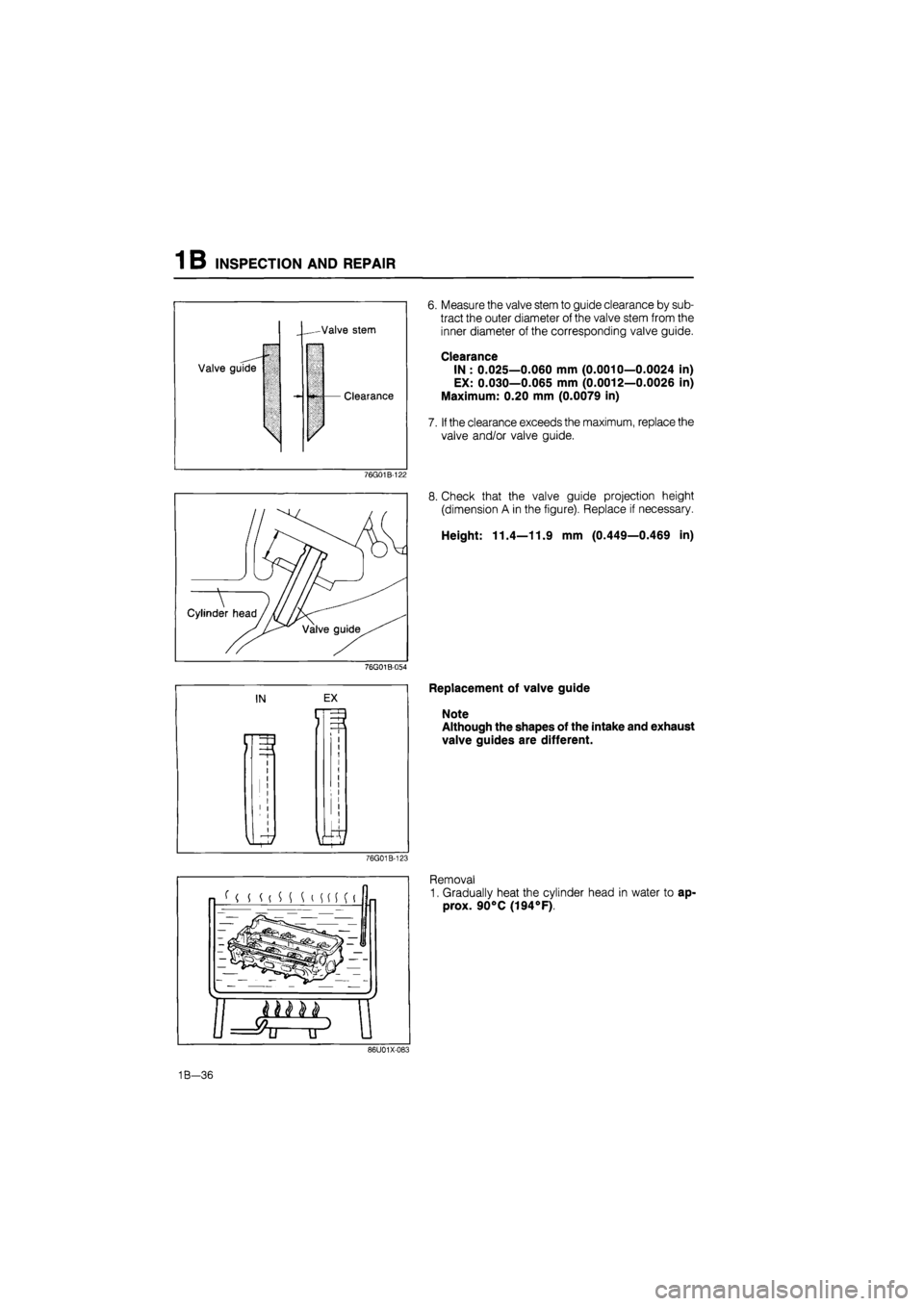
1 B INSPECTION AND REPAIR
Valve guide
-Valve stem
I/
Clearance
6. Measure the valve stem to guide clearance by sub-
tract the outer diameter of the valve stem from the
inner diameter of the corresponding valve guide.
Clearance
IN : 0.025—0.060 mm (0.0010—0.0024 in)
EX: 0.030—0.065 mm (0.0012—0.0026 in)
Maximum: 0.20 mm (0.0079 in)
7. If the clearance exceeds the maximum, replace the
valve and/or valve guide.
76G01B-122
76G01B-054
8. Check that the valve guide projection height
(dimension A in the figure). Replace if necessary.
Height: 11.4—11.9 mm (0.449—0.469 in)
Replacement of valve guide
Note
Although the shapes of the intake and exhaust
valve guides are different.
76G01B-123
Removal
1. Gradually heat the cylinder head in water to ap-
prox. 90°C (194°F).
86U01X-083
1B-36
Page 260 of 1865
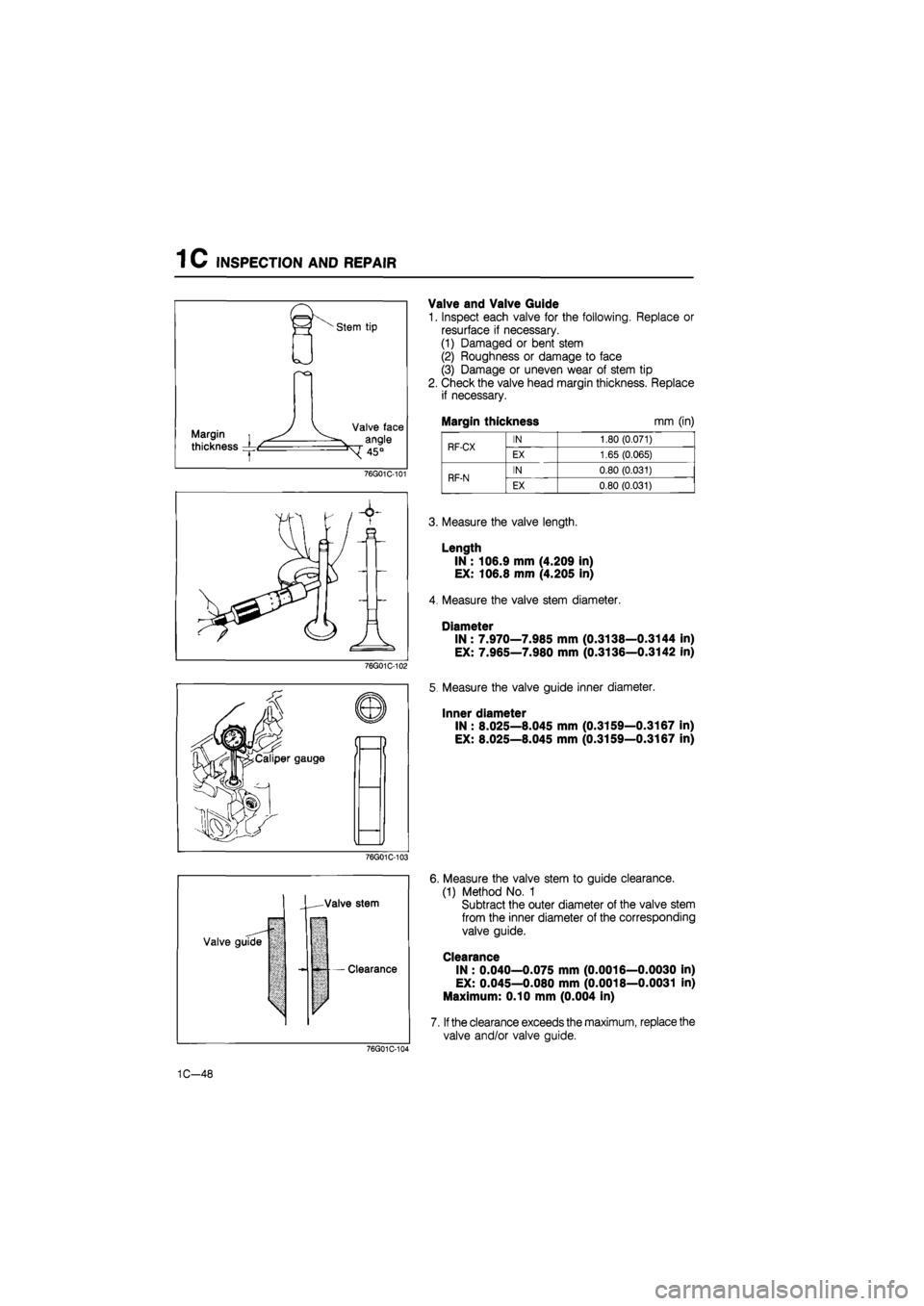
1C INSPECTION AND REPAIR
Stem tip
Margin i
thickness
T
Valve face
angle
^45°
76G01C-101
76G01C-102
" & ©
JMFc
•^Caliper gauge
^V^r "M
m
Valve and Valve Guide
1. Inspect each valve for the following. Replace or
resurface if necessary.
(1) Damaged or bent stem
(2) Roughness or damage to face
(3) Damage or uneven wear of stem tip
2. Check the valve head margin thickness. Replace
if necessary.
Margin thickness mm (in)
RF-CX IN 1.80 (0.071) RF-CX EX 1.65 (0.065)
RF-N IN 0.80 (0.031) RF-N EX 0.80 (0.031)
3. Measure the valve length.
Length
IN : 106.9 mm (4.209 in)
EX: 106.8 mm (4.205 in)
4. Measure the valve stem diameter.
Diameter
IN : 7.970—7.985 mm (0.3138—0.3144 in)
EX: 7.965—7.980 mm (0.3136—0.3142 in)
5. Measure the valve guide inner diameter.
Inner diameter
IN : 8.025—8.045 mm (0.3159—0.3167 in)
EX: 8.025—8.045 mm (0.3159—0.3167 in)
76G01C-103
-Valve stem
Valve guide
Clearance
V
6. Measure the valve stem to guide clearance.
(1) Method No. 1
Subtract the outer diameter of the valve stem
from the inner diameter of the corresponding
valve guide.
Clearance
IN : 0.040—0.075 mm (0.0016—0.0030 in)
EX: 0.045—0.080 mm (0.0018—0.0031 in)
Maximum: 0.10 mm (0.004 in)
7.
If
the clearance exceeds the maximum, replace the
valve and/or valve guide.
76G01C-111
1C-48
Page 503 of 1865
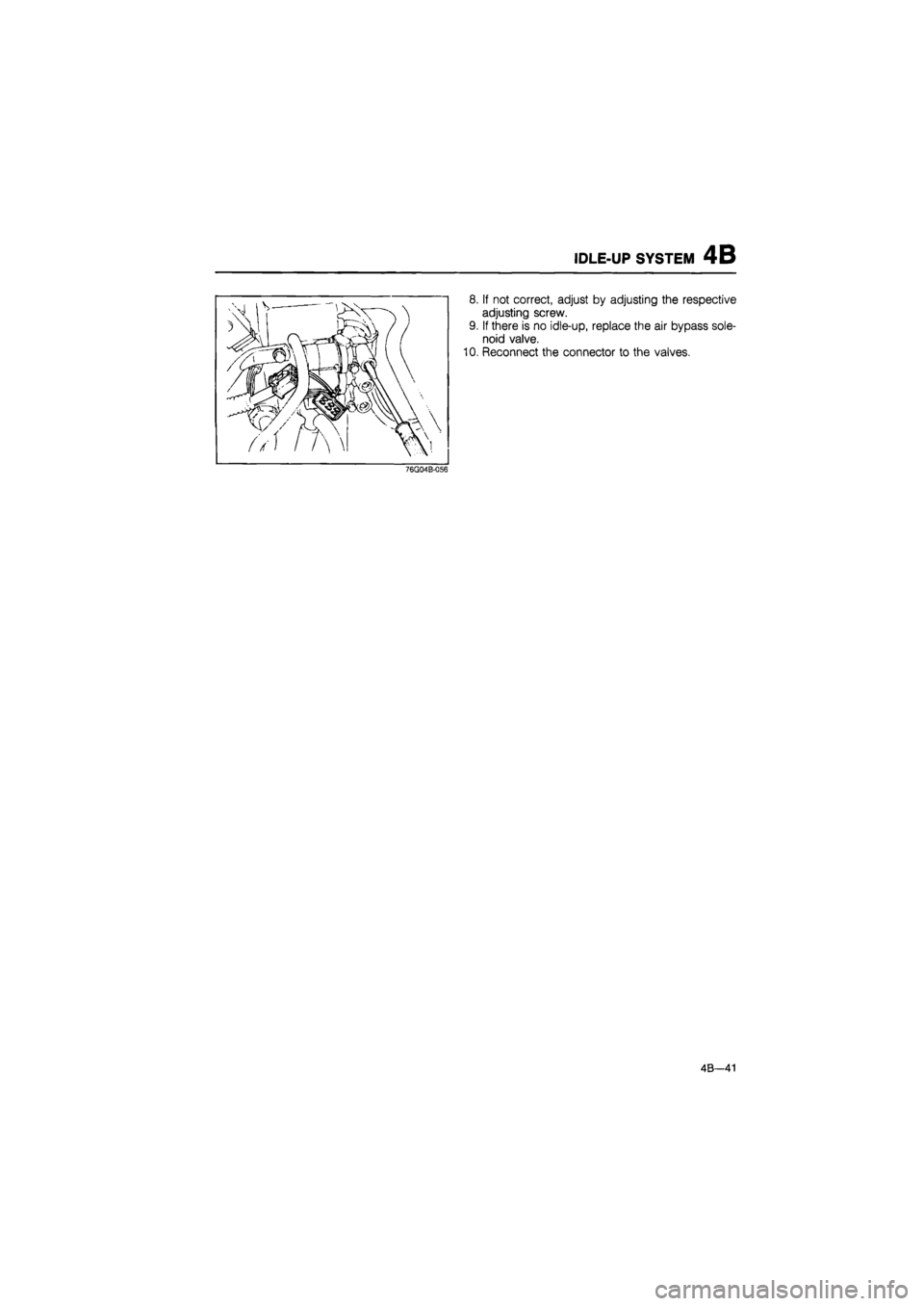
IDLE-UP SYSTEM 4B
8. If not correct, adjust by adjusting the respective
adjusting screw.
9. If there is no idle-up, replace the air bypass sole-
noid valve.
10. Reconnect the connector to the valves.
76G04B-056
4B—41
Page 513 of 1865
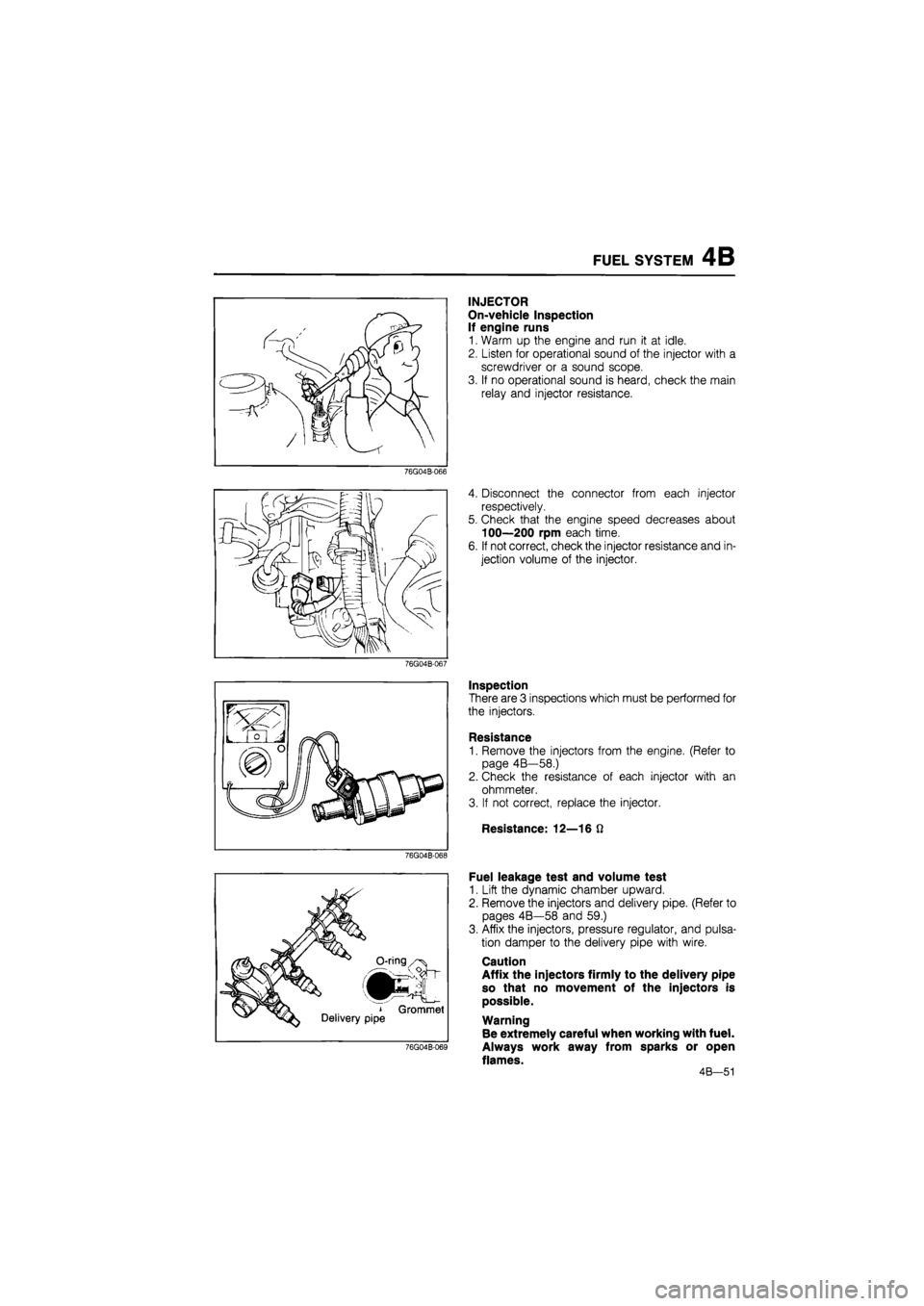
FUEL SYSTEM 4B
INJECTOR
On-vehicle Inspection
If engine runs
1. Warm up the engine and run it at idle.
2. Listen for operational sound of the injector with a
screwdriver or a sound scope.
3. If no operational sound is heard, check the main
relay and injector resistance.
76G04B-066
4. Disconnect the connector from each injector
respectively.
5. Check that the engine speed decreases about
100—200 rpm each time.
6. If not correct, check the injector resistance and in-
jection volume of the injector.
76G04B-067
Inspection
There are 3 inspections which must be performed for
the injectors.
Resistance
1. Remove the injectors from the engine. (Refer to
page 4B—58.)
2. Check the resistance of each injector with an
ohmmeter.
3. If not correct, replace the injector.
Resistance: 12—16 ft
76G04B-068
' Grommet Delivery pipe
76G04B-069
Fuel leakage test and volume test
1. Lift the dynamic chamber upward.
2. Remove the injectors and delivery pipe. (Refer to
pages 4B—58 and 59.)
3. Affix the injectors, pressure regulator, and pulsa-
tion damper to the delivery pipe with wire.
Caution
Affix the injectors firmly to the delivery pipe
so that no movement of the injectors is
possible.
Warning
Be extremely careful when working with fuel.
Always work away from sparks or open
flames.
4B—51
Page 600 of 1865
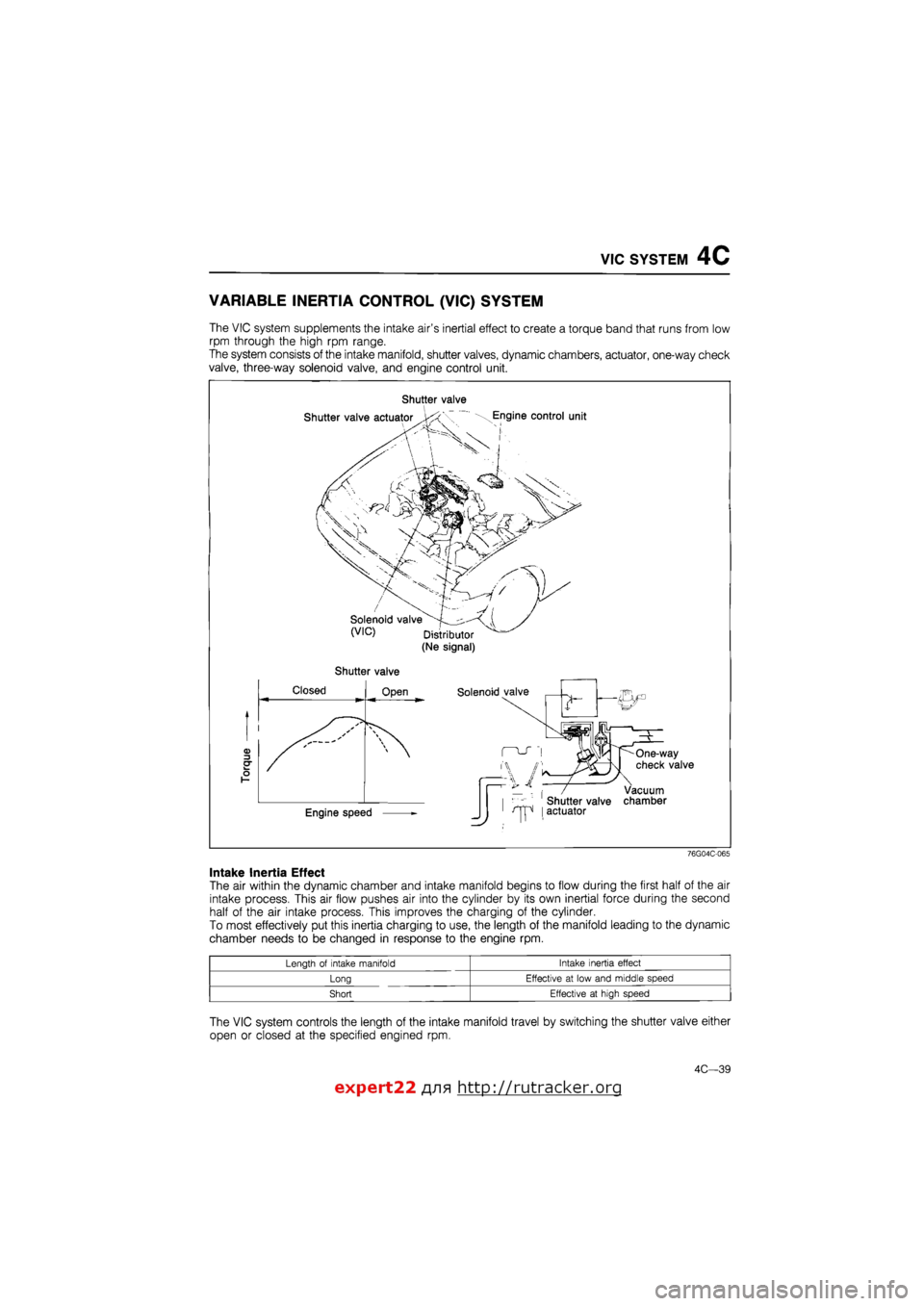
VIC SYSTEM 4C
VARIABLE INERTIA CONTROL
(VIC)
SYSTEM
The VIC system supplements the intake air's inertial effect to create a torque band that runs from low
rpm through the high rpm range.
The system consists of the intake manifold, shutter valves, dynamic chambers, actuator, one-way check
valve, three-way solenoid valve, and engine control unit.
Shutter valve
Shutter valve
76G04C-065
Intake Inertia Effect
The air within the dynamic chamber and intake manifold begins to flow during the first half of the air
intake process. This air flow pushes air into the cylinder by its own inertial force during the second
half of the air intake process. This improves the charging of the cylinder.
To most effectively put this inertia charging to use, the length of the manifold leading to the dynamic
chamber needs to be changed in response to the engine rpm.
Length of intake manifold Intake inertia effect
Long Effective at low and middle speed
Short Effective at high speed
The VIC system controls the length of the intake manifold travel by switching the shutter valve either
open or closed at the specified engined rpm.
expert22 fl/i* http://rutracker.org
4C—39
Page 619 of 1865
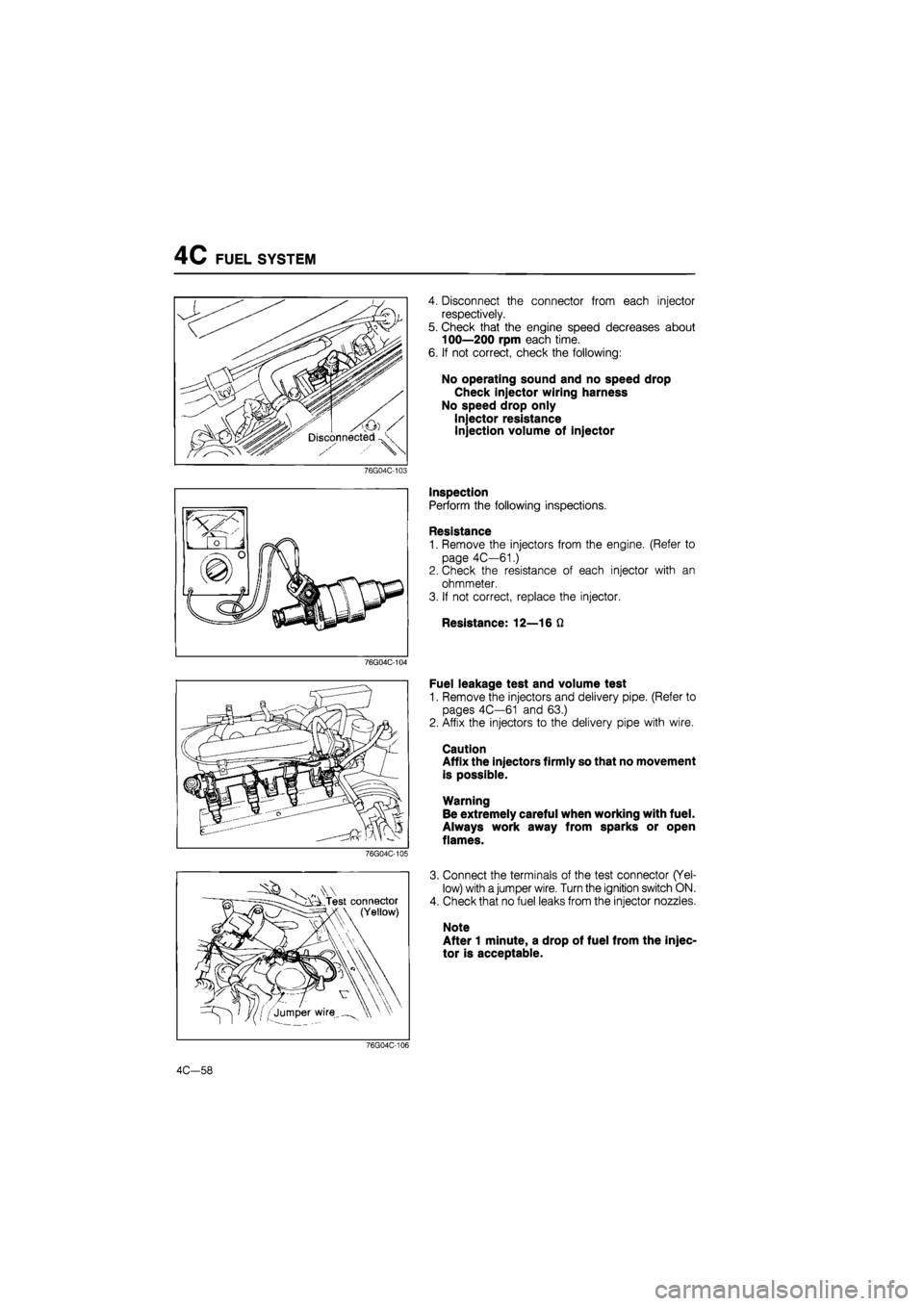
4C FUEL SYSTEM
76G04C-103
76G04C-104
76G04C-105
- s A Test connector I \ (Yellow)
4. Disconnect the connector from each injector
respectively.
5. Check that the engine speed decreases about
100—200 rpm each time.
6. If not correct, check the following:
No operating sound and no speed drop
Check injector wiring harness
No speed drop only
Injector resistance
Injection volume of injector
Inspection
Perform the following inspections.
Resistance
1. Remove the injectors from the engine. (Refer to
page 4C—61.)
2. Check the resistance of each injector with an
ohmmeter.
3. If not correct, replace the injector.
Resistance: 12—16 Q
Fuel leakage test and volume test
1. Remove the injectors and delivery pipe. (Refer to
pages 4C—61 and 63.)
2. Affix the injectors to the delivery pipe with wire.
Caution
Affix the injectors firmly so that no movement
is possible.
Warning
Be extremely careful when working with fuel.
Always work away from sparks or open
flames.
3. Connect the terminals of the test connector (Yel-
low) with a jumper wire. Turn the ignition switch ON.
4. Check that no fuel leaks from the injector nozzles.
Note
After 1 minute, a drop of fuel from the injec-
tor is acceptable.
76G04C-106
4C—58
Page 890 of 1865
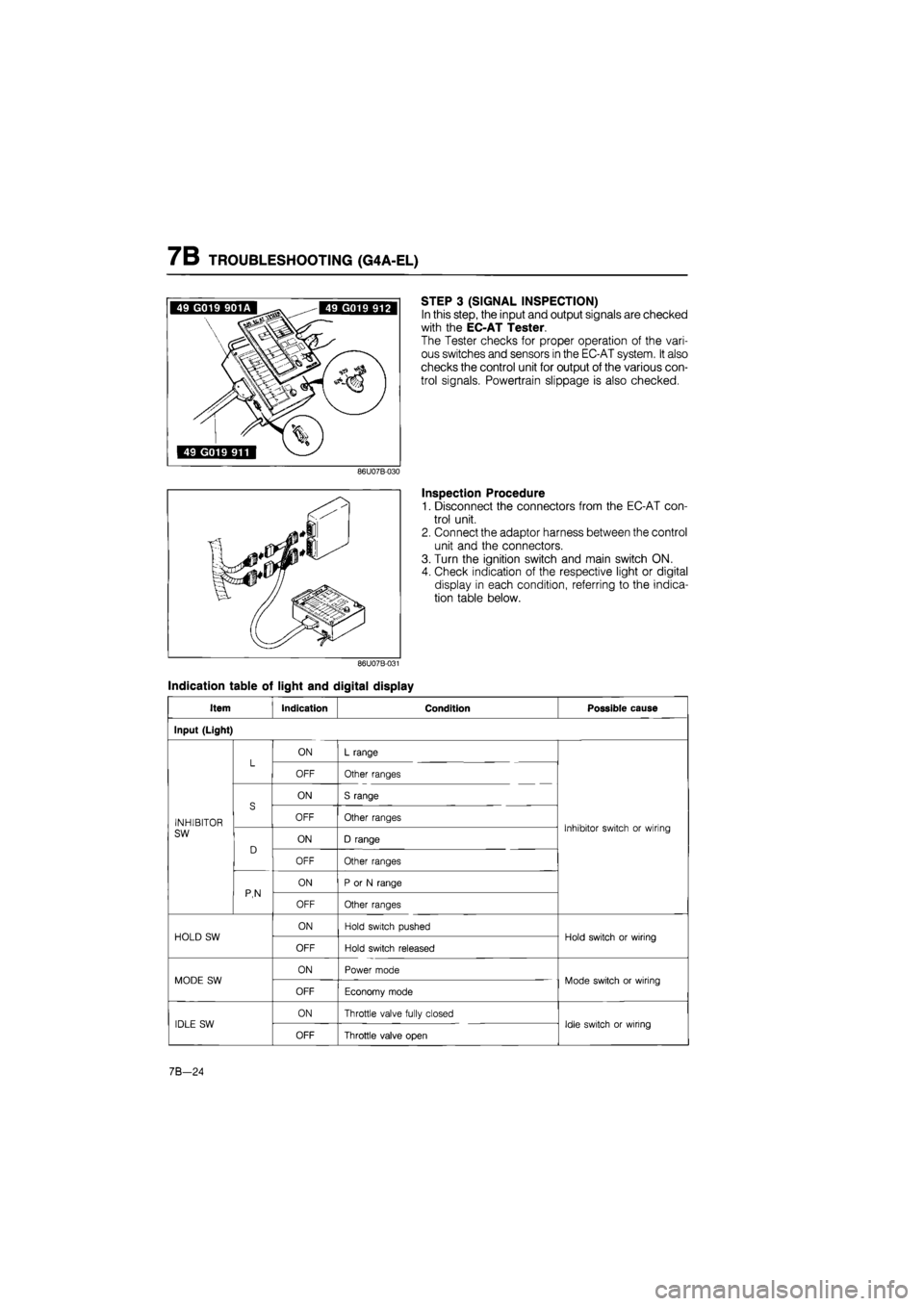
7B TROUBLESHOOTING (G4A-EL)
STEP 3 (SIGNAL INSPECTION)
In this step, the input and output signals are checked
with the EC-AT Tester.
The Tester checks for proper operation of the vari-
ous switches and sensors in the EC-AT system. It also
checks the control unit for output of the various con-
trol signals. Powertrain slippage is also checked.
Inspection Procedure
1. Disconnect the connectors from the EC-AT con-
trol unit.
2. Connect the adaptor harness between the control
unit and the connectors.
3. Turn the ignition switch and main switch ON.
4. Check indication of the respective light or digital
display in each condition, referring to the indica-
tion table below.
Indication table of light and digital display
Item Indication Condition Possible cause
Input (Light)
L ON L range L OFF Other ranges
S
ON S range
INHIBITOR
S OFF Other ranges Inhibitor switch or wiring SW
D ON D range
Inhibitor switch or wiring
D
OFF Other ranges
P,N
ON P or N range P,N OFF Other ranges
HOLD SW ON Hold switch pushed Hold switch or wiring HOLD SW
OFF Hold switch released
Hold switch or wiring
MODE SW ON Power mode Mode switch or wiring MODE SW
OFF Economy mode
Mode switch or wiring
IDLE SW ON Throttle valve fully closed Idle switch or wiring IDLE SW
OFF Throttle valve open
Idle switch or wiring
7B-24