check oil MAZDA MX-5 1994 Owner's Guide
[x] Cancel search | Manufacturer: MAZDA, Model Year: 1994, Model line: MX-5, Model: MAZDA MX-5 1994Pages: 1708, PDF Size: 82.34 MB
Page 319 of 1708
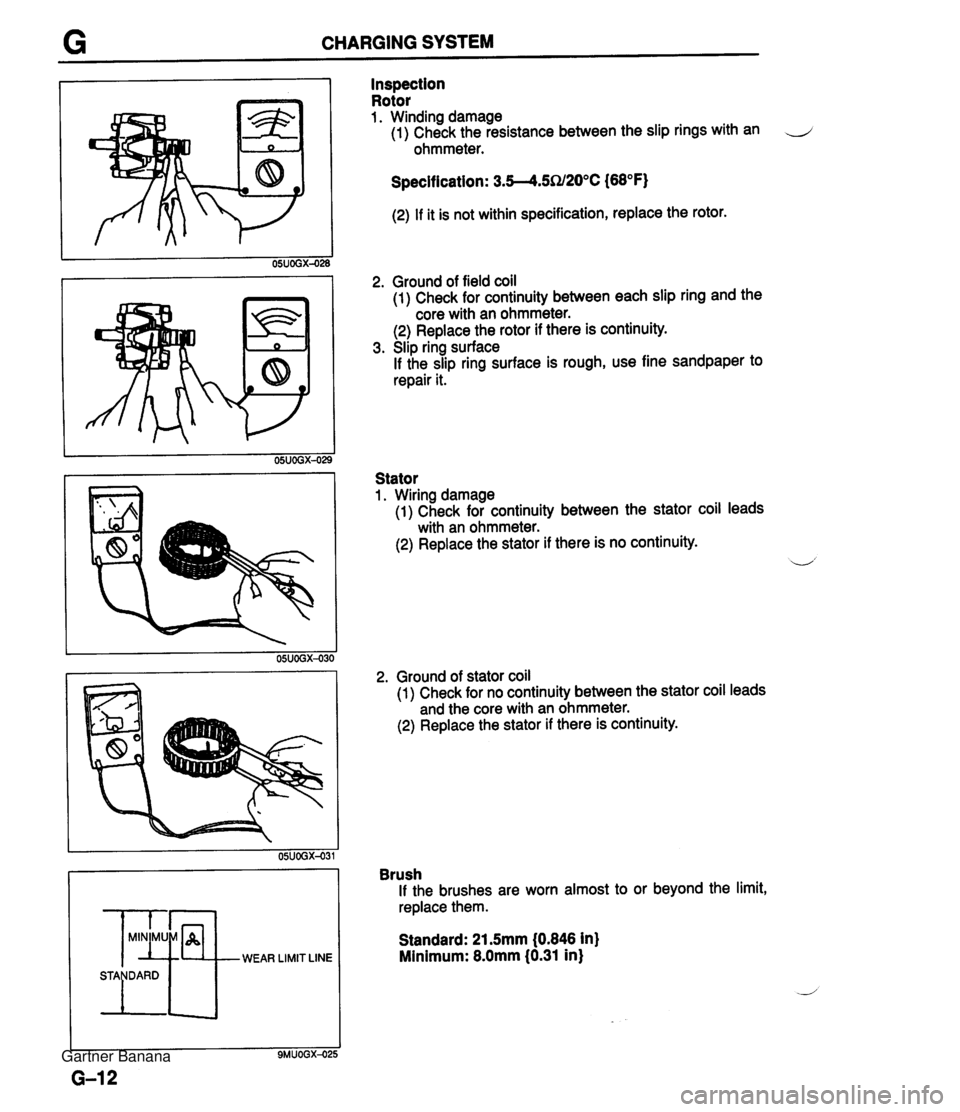
G CHARGING SYSTEM WEAR LIMIT LINE Inspection Rotor 1. Winding damage (1) Check the resistance between the slip rings with an J ohmmeter. Specification: 3.5--4.5SU20°C (68°F) (2) If it is not within specification, replace the rotor. 2. Ground of field coil (1) Check for continuity between each slip ring and the core with an ohmmeter. (2) Replace the rotor if there is continuity. 3. Slip ring surface If the slip ring surface is rough, use fine sandpaper to repair it. Stator 1. Wiring damage (1) Check for continuity between the stator coil leads with an ohmmeter. (2) Replace the stator if there is no continuity. 2. Ground of stator coil (1)~heck for no continuity between the stator coil leads and the core with an ohmmeter. (2) Replace the stator if there is continuity. Brush If the brushes are worn almost to or beyond the limit, replace them. Standard: 21.5mm (0.846 in) Minimum: 8.0mm (0.31 in) Gartner Banana
Page 321 of 1708
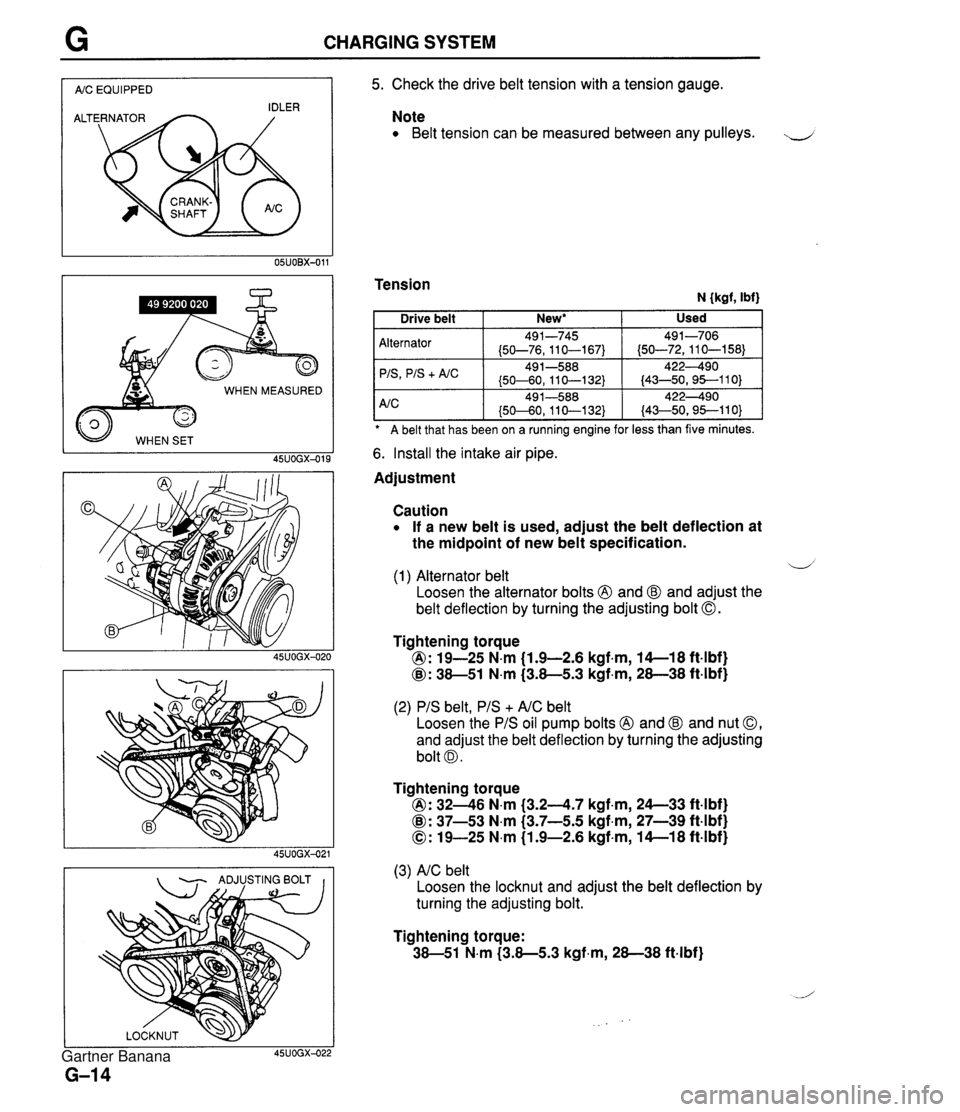
CHARGING SYSTEM I AIC EQUIPPED I WHEN MEASURED 45UOGX-015 - ADJUSTING BOLT I I 5. Check the drive belt tension with a tension gauge. Note Belt tension can be measured between any pulleys. J Tension N {kgf, Ibf) A belt that has been on a ruining engine for less than five minutes. Alternator 'IS
+ A/C 6. Install the intake air pipe. Used Drive belt Adjustment New* I Caution If a new belt is used, adjust the belt deflection at the midpoint of new belt specification. 491-745 (50-76,110-167) 49 1-588 (50-60, 11 0-1 32) d (1) Alternator belt Loosen the alternator bolts @ and @ and adjust the belt deflection by turning the adjusting bolt 0. 491-706 (50-72,110-158) 422490 (43-50,95--110) Tightening torque @: 19-25 N.m (1.9-2.6 kgf.m, 14-1 8 ft4bf) @: 38-51 N.m (3.8-5.3 kgf,m, 28-38 ft-lbf) (2) PIS belt, PIS + AIC belt Loosen the PIS oil pump bolts @ and @ and nut 0, and adjust the belt deflection by turning the adjusting bolt 0. Tightening torque @: 3246 N.m (3.24.7 kgf.m, 24--33 ft4bf) @: 37-53 N.m (3.7-5.5 kgf,m, 27-39 ft-lbf) 0: 19-25 N.m (1.9-2.6 kgf-m, 14-1 8 ft-lbf) (3) AIC belt Loosen the locknut and adjust the belt deflection by turning the adjusting bolt. Tightening torque: 38-51 N.m (3.8-5.3 kgf-m, 28-38 ft-lbf) Gartner Banana
Page 322 of 1708
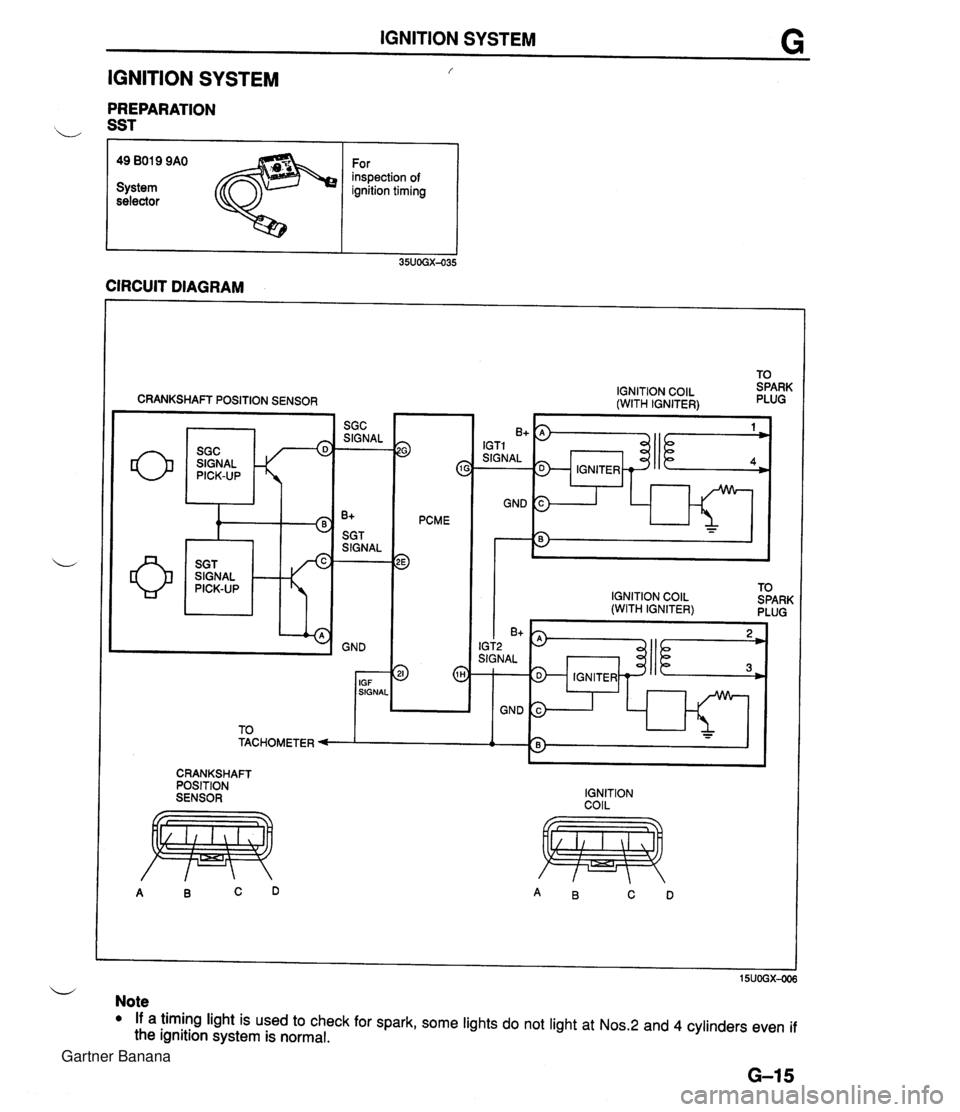
IGNITION SYSTEM G IGNITION SYSTEM f PREPARATION b SST r I I 49 BO19 9AO For inspection of System ignition timing selector CIRCUIT DIAGRAM CRANKSHAFT POSITION SENSOR SIGNAL w 9 c PCME 3 IGNITION COlL (WITH IGNITER) IGNITION COlL TO (WITH IGNITER) SPARK PLUG I I I 6'5) IGT2 SIGNAL 1 IGNITER - GND 3 1 h - - CRANKSHAFT POSITION SENSOR IGNITION COIL u Note If a timing light is used to check for spark, some lights do not light at Nos.2 and 4 cylinders even if the ignition system is normal. Gartner Banana
Page 323 of 1708
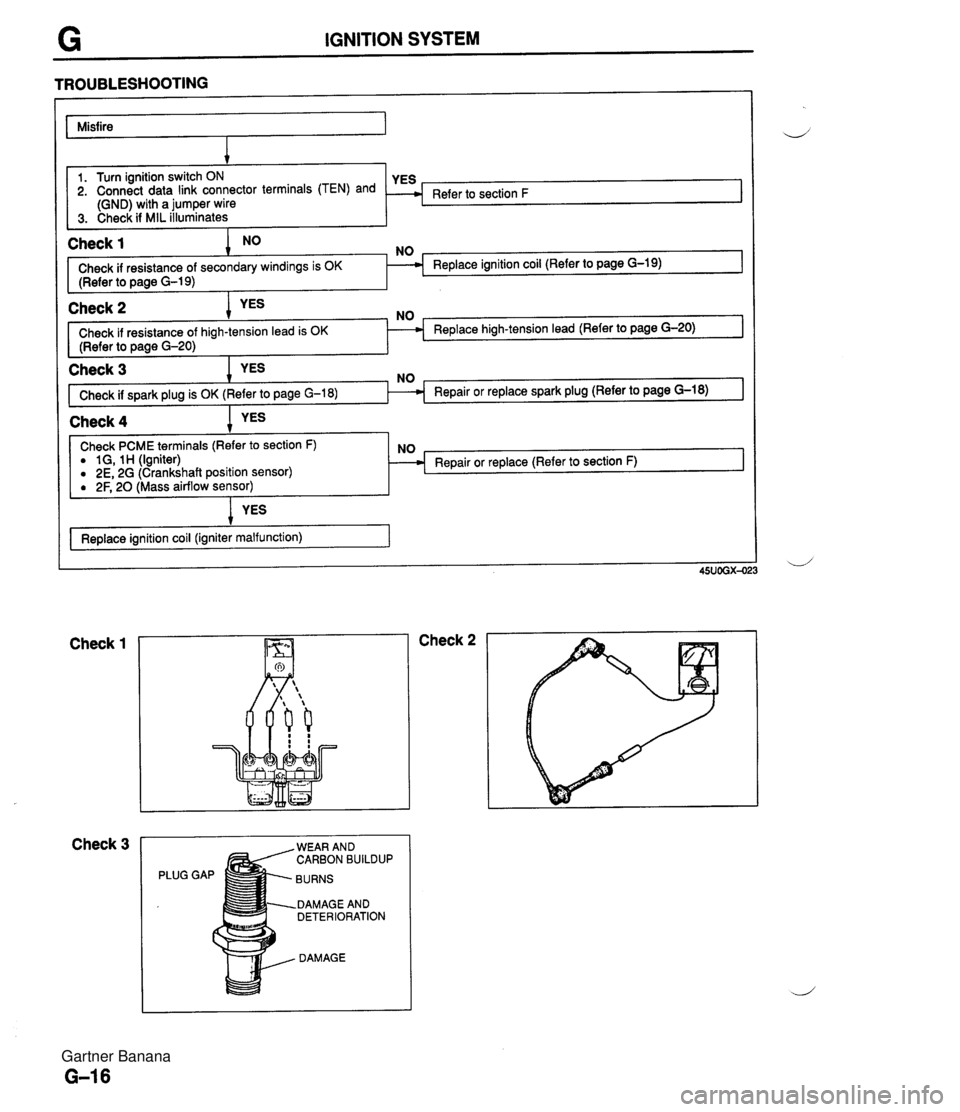
IGNITION SYSTEM TROUBLESHOOTING Misfire I 1 Check 1 NO NO 1. Turn ignition switch ON 2. Connect data link connector terminals (TEN) and (GND) with a jumper wire 3. Check if MIL illuminates I Check if resistance of secondary windings is OK Replace ignition coil (Refer to page G-19) (Refer to page G-19) I Refer to section F Check 2 Check if resistance of Replace high-tension lead (Refer to page G-20) (Refer to page G-20) I I Check 3 Check if spark plug is OK ( I Check 4 1 YES I Check PCME terminals (Refer to section F) a 1 G, 1 H (Igniter) 0 2E, 2G (Crankshaft position sensor) Repair or replace (Refer to section F) ( 2F, 20 ass airflow sensor) YES Replace ignition coil (igniter malfunction) 1 Check 1 Check 3 Check 2 PLUG WEAR AND CARBON BUILDUP BURNS DAMAGE AND DETERIORATION DAMAGE Gartner Banana
Page 324 of 1708
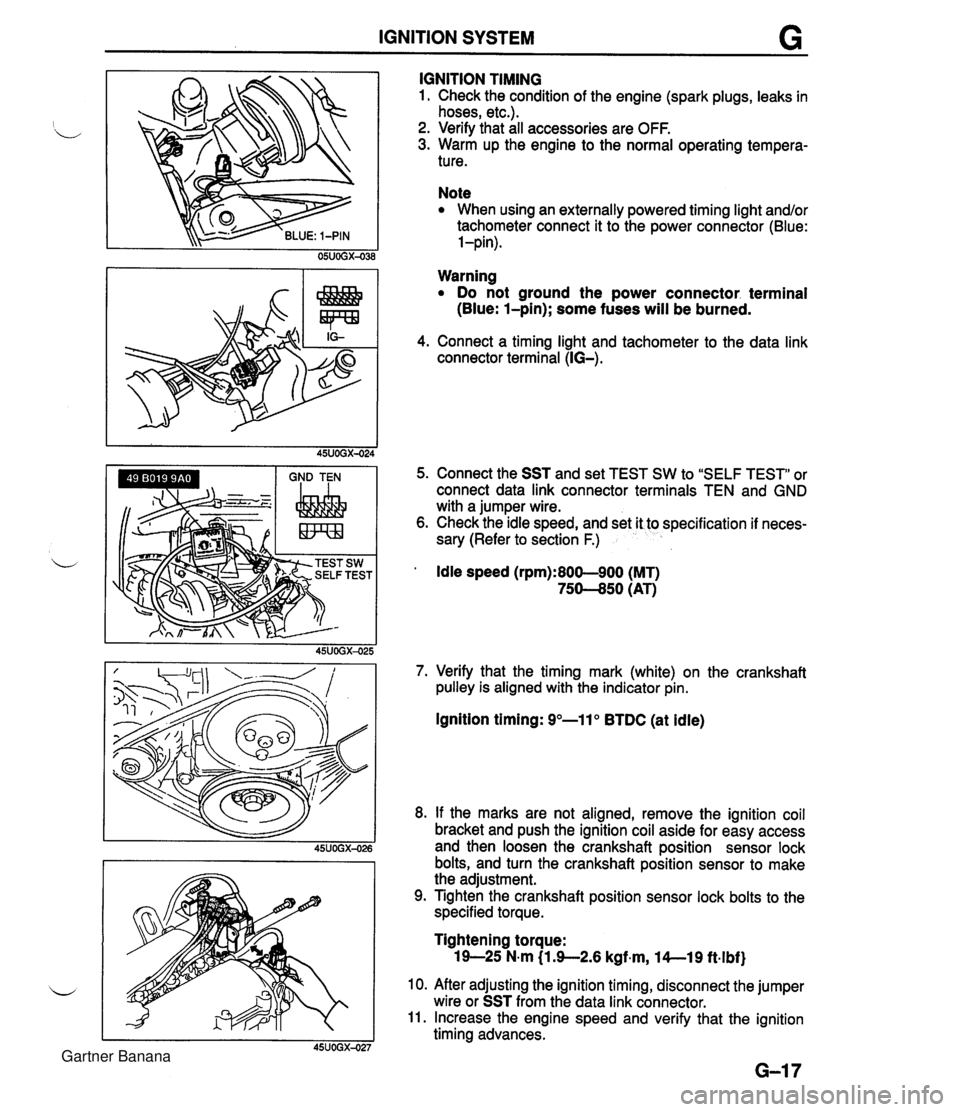
IGNITION SYSTEM G GND TEN I I I IGNITION TIMING 1. Check the condition of the engine (spark plugs, leaks in hoses, etc.). 2. Verify that all accessories are OFF. 3. Warm up the engine to the normal operating tempera- ture. Note When using an externally powered timing light and/or tachometer connect it to the power connector (Blue: l-pin). Warning Do not ground the power connector. terminal (Blue: l-pin); some fuses will be burned. 4. Connect a timing light and tachometer to the data link connector terminal (IG-). 5. Connect the SST and set TEST SW to "SELF TEST" or connect data link connector terminals TEN and GND with a jumper wire. 6. Check the idle speed, and set it to specification if neces- sary (Refer to section F.) ' Idle speed (rpm):800-900 (MT) 75-50 (AT) 7. Verify that the timing mark (white) on the crankshaft pulley is aligned with the indicator pin. Ignition timing: 9"-11" BTDC (at idle) 8. If the marks are not aligned, remove the ignition coil bracket and push the ignition coil aside for easy access and then loosen the crankshaft position sensor lock bolts, and turn the crankshaft position sensor to make the adjustment. 9. Tighten the crankshaft position sensor lock bolts to the specified torque. Tightening torque: 19-25 N-m (1 3-2.6 kgf~m, l4--19 ft.lbf) 10. After adjusting the ignition timing, disconnect the jumper wire or SST from the data link connector. 11. Increase the engine speed and verify that the ignition timing advances. Gartner Banana
Page 326 of 1708
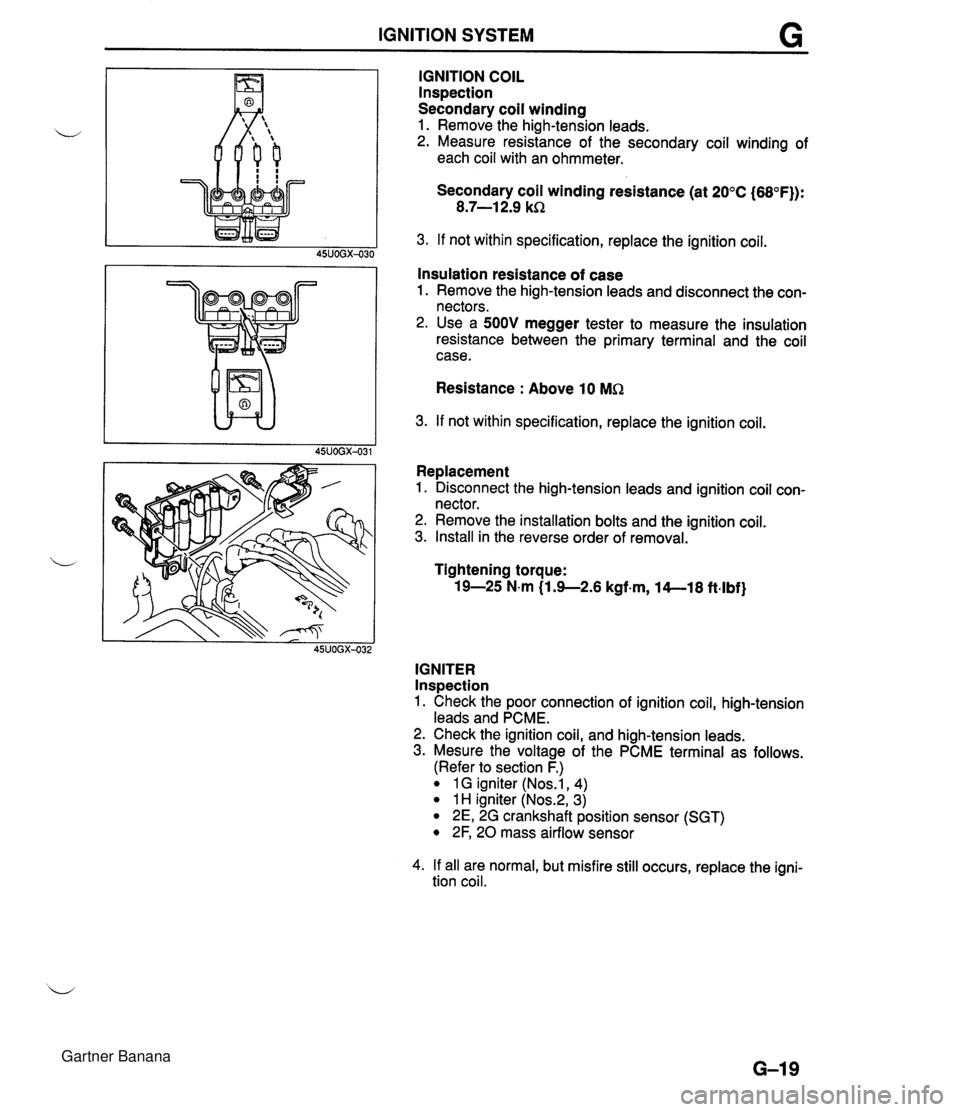
IGNITION SYSTEM IGNITION COIL lnspection Secondary coil winding 1. Remove the high-tension leads. u 2. Measure resistance of the secondary coil winding of each coil with an ohmmeter. Secondary coil winding resistance (at 20°C (68°F)): 8.7-1 2.9 kR 3. If not within specification, replace the ignition coil. 45UOGX-030 I I Insulation resistance of case 1. Remove the high-tension leads and disconnect the con- nectors. 2. Use a 500V megger tester to measure the insulation resistance between the primary terminal and the coil case. Resistance : Above 10 MR 3. If not within specification, replace the ignition coil. L I 45UOGX-031 Replacement 1. Disconnect the high-tension leads and ignition coil con- nector. 2. Remove the installation bolts and the ignition coil. 3. Install in the reverse order of removal. L Tightening torque: 19-25 N.m (1.9--2.6 kgf-m, 14--18 ft-lbf) 45UOGX-032 IGNITER Inspection 1. Check the poor connection of ignition coil, high-tension leads and PCME. 2. Check the ignition coil, and high-tension leads. 3. Mesure the voltage of the PCME terminal as follows. (Refer to section F.) 1 G igniter (Nos.1, 4) 1 H igniter (Nos.2, 3) 2E, 2G crankshaft position sensor (SGT) 2F, 20 mass airflow sensor 4. If all are normal, but misfire still occurs, replace the igni- tion coil. Gartner Banana
Page 333 of 1708

STARTING SYSTEM Inspection Armature 1. Ground of armature coil Check for no continuity between the commutator and the .J core with an ohmmeter. Check the entire circumference of the commutator. Replace the armature if there is conti- nuity. 2, Insulation of armature coil Check for no continuity between the commutator and the shaft with an ohmmeter. Check the entire circumference of the commutator. Replace the armature if there is conti- nuity. 3. Runout of commutator (1) Place the armature on V blocks, and measure the runout with a dial gauge. (2) Repair with a lathe if the runout is small or replace,the armature if necessary. -1' Runout: 0.03mm (0.001 in) 4. Outer diameter of commutator Replace the armature if the outer diameter of the com- mutator is at the grind limit or less. 5. Roughness of commutator surface If the commutator surface is dirty, wipe it with a cloth; if it is rough, repair it with a lathe or fine sandpaper. Grind limit: 30.8mm (1.21 in) 6. Segment groove depth If the depth of the molding between segments is at the depth limit or less, undercut the grooves to the standard depth. Standard depth: 0.5--0.8mm (0.02-4.03 in) Depth limit: 0.2mm (0.008 in) Gartner Banana
Page 334 of 1708
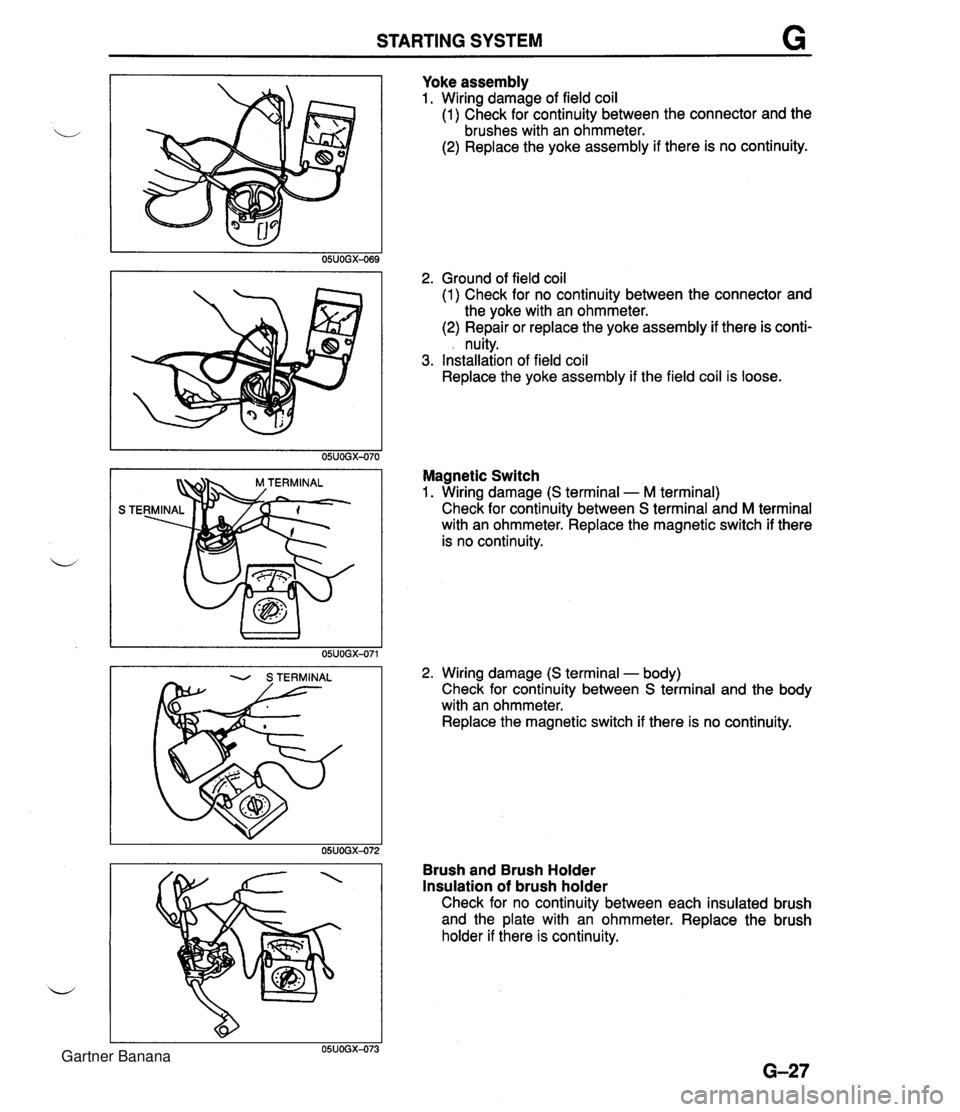
STARTING SYSTEM Yoke assembly 1. Wiring damage of field coil (1) Check for continuity between the connector and the brushes with an ohmmeter. (2) Replace the yoke assembly if there is no continuity. 2. Ground of field coil (1) Check for no continuity between the connector and the yoke with an ohmmeter. (2) Repair or replace the yoke assembly if there is conti- . nuity. 3. Installation of field coil Replace the yoke assembly if the field coil is loose. Magnetic Switch 1. Wiring damage (S terminal - M terminal) Check for continuity between S terminal and M terminal with an ohmmeter. Replace the magnetic switch if there is no continuity. 2. Wiring damage (S terminal - body) Check for continuity between S terminal and the body with an ohmmeter. Replace the magnetic switch if there is no continuity. Brush and Brush Holder Insulation of brush holder Check for no continuity between each insulated brush and the plate with an ohmmeter. Replace the brush holder if there is continuity. Gartner Banana
Page 362 of 1708
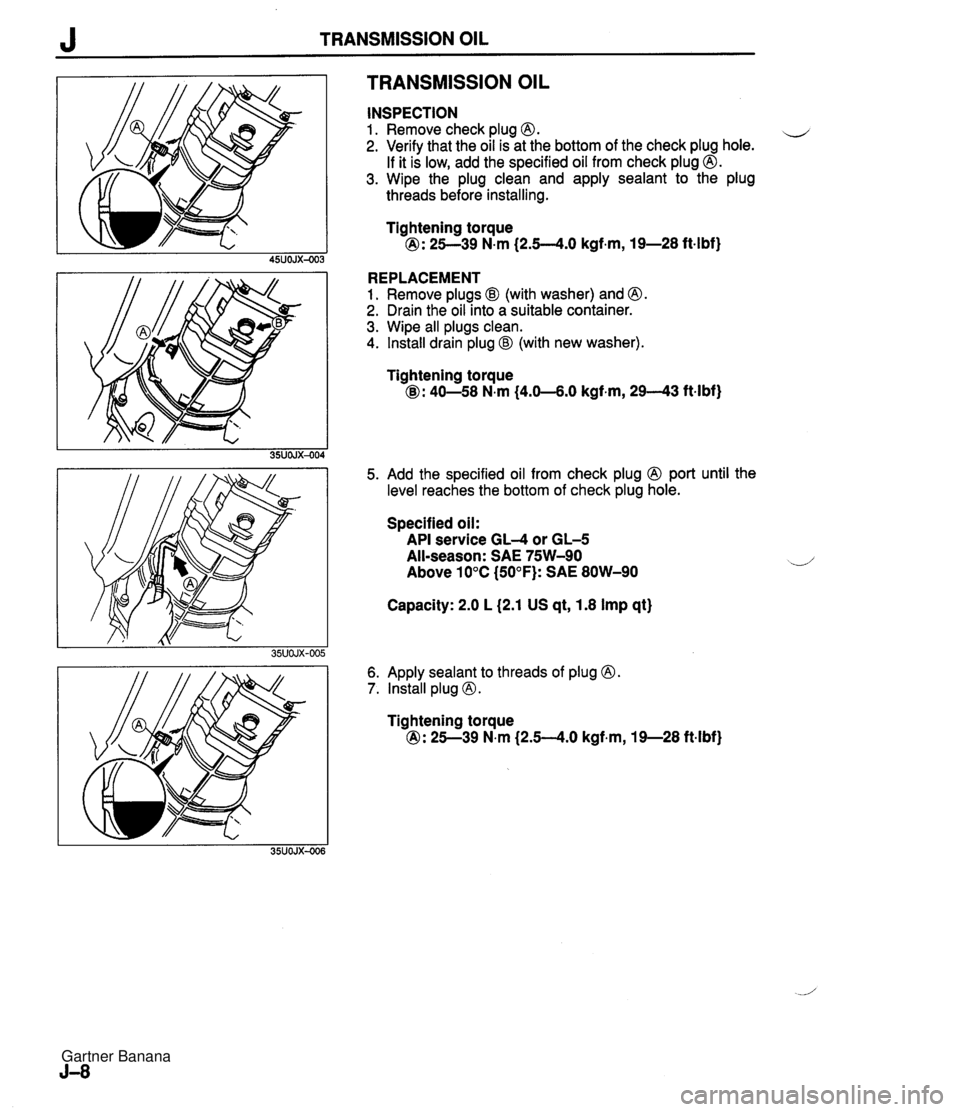
J TRANSMISSION OIL TRANSMISSION OIL INSPECTION 1. Remove check plug 0. u 2. Verify that the oil is at the bottom of the check plug hole. If it is low, add the specified oil from check plug @. 3. Wipe the plug clean and apply sealant to the plug threads before installing. Tightening torque @: 25--39 N.m (2.5--4.0 kgf.m, 19-28 ft4bf) REPLACEMENT 1. Remove plugs @I (with washer) and @. 2. Drain the oil into a suitable container. 3. Wipe all plugs clean. 4. Install drain plug @I (with new washer). Tightening torque @: 40-58 N.m (4.0-4.0 kgf.m, 2943 ftlbf) 5. Add the specified oil from check plug 0 port until the level reaches the bottom of check plug hole. Specified oil: API service GL-4 or GL-5 All-season: SAE 75W-90 Above 10°C (50°F): SAE 80W-90 Capacity: 2.0 L (2.1 US qt, 1.8 Imp qt) 6. Apply sealant to threads of plug 0. 7. lnstall plug @. Tightening torque @: 25--39 N.m (2.54.0 kgf.m, 19-28 ft-lbf) Gartner Banana
Page 367 of 1708
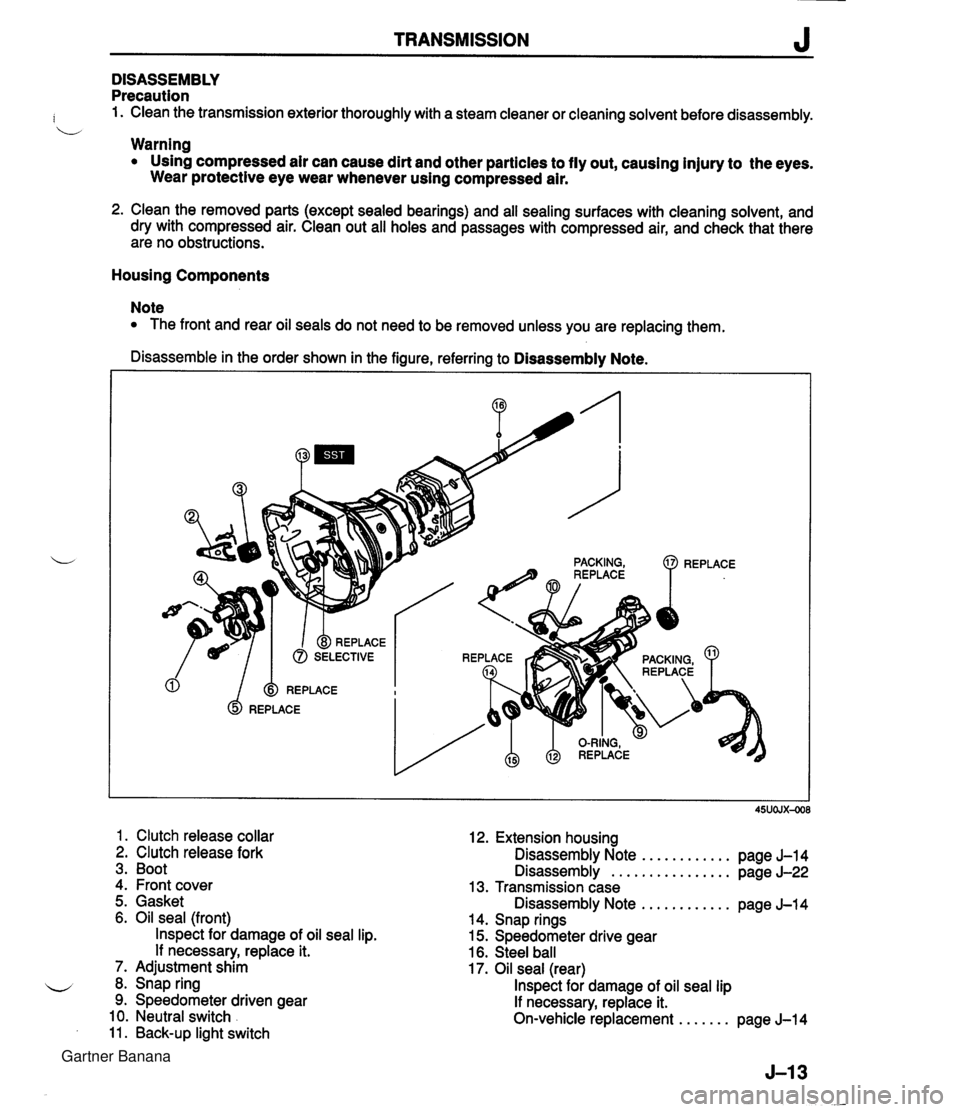
TRANSMISSION J DISASSEMBLY Precaution : 1. Clean the transmission exterior thoroughly with a steam cleaner or cleaning solvent before disassembly. b Warning Using compressed air can cause dirt and other particles to fly out, causing injury to the eyes. Wear protective eye wear whenever using compressed air. 2. Clean the removed parts (except sealed bearings) and all sealing surfaces with cleaning solvent, and dry with compressed air. Clean out all holes and passages with compressed air, and check that there are no obstructions. Housing Components Note The front and rear oil seals do not need to be removed unless you are replacing them. Disassemble in the order shown in the figure, referring to Disassembly Note. 1. Clutch release collar 2. Clutch release fork 3. Boot 4. Front cover 12. Extension housing Disassembly Note ............ page J-14 Disassembly ................ page J-22 13. Transmission case 5. Gasket Disassembly Note ............ pane J-14 6. Oil seal (front) lnspect for damage of oil seal lip. If necessary, replace it. 7. Adjustment shim 8. Snap ring 9. Speedometer driven gear 10. Neutral switch 11. Back-up light switch . - 14. Snap rings 15. Speedometer drive gear 16. Steel ball 17. Oil seal (rear) lnspect for damage of oil seal lip If necessary, replace it. On-vehicle replacement ....... page J-14 Gartner Banana