light MAZDA MX-5 1994 Repair Manual
[x] Cancel search | Manufacturer: MAZDA, Model Year: 1994, Model line: MX-5, Model: MAZDA MX-5 1994Pages: 1708, PDF Size: 82.34 MB
Page 440 of 1708
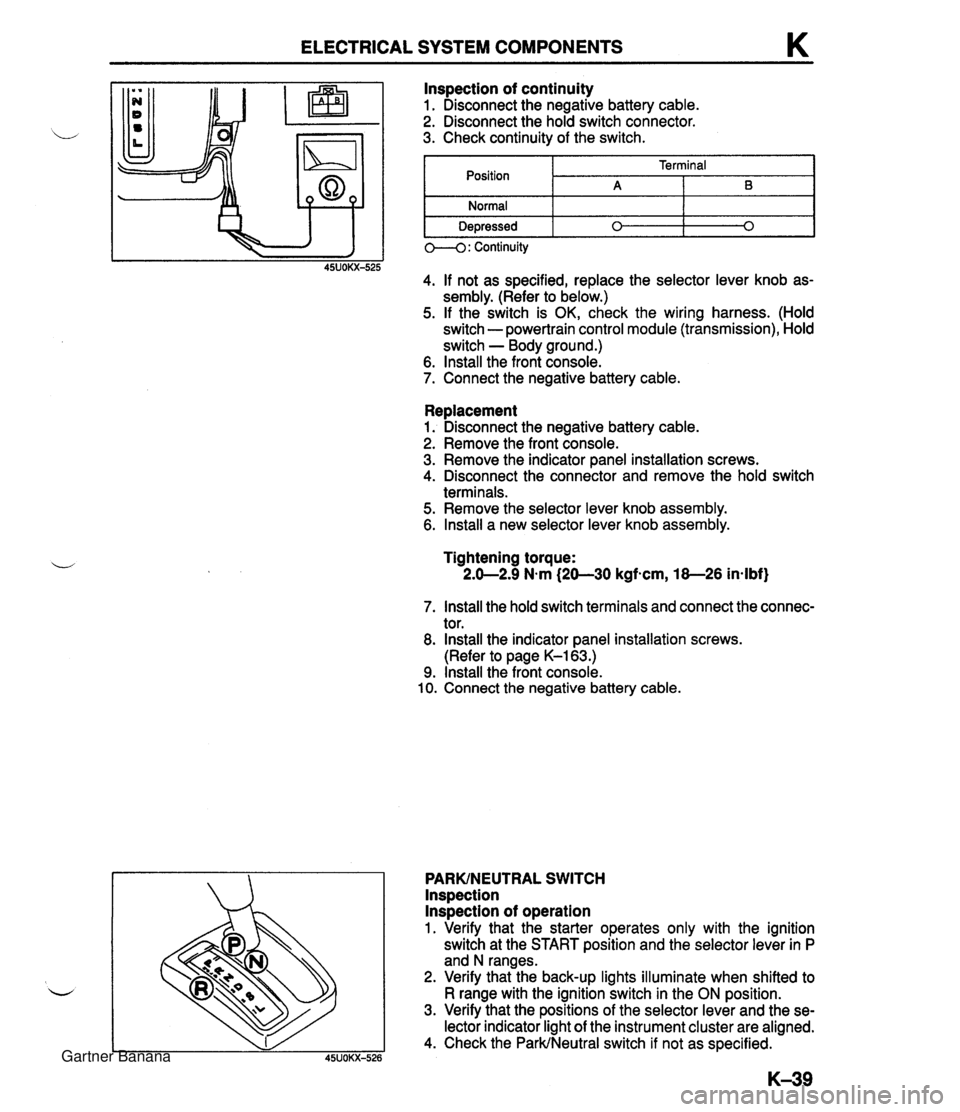
ELECTRICAL SYSTEM COMPONENTS K Replacement 1. Disconnect the negative battery cable. 2. Remove the front console. 3. Remove the indicator panel installation screws. 4. Disconnect the connector and remove the hold switch terminals. 5. Remove the selector lever knob assembly. 6. lnstall a new selector lever knob assembly. lnspection of continuity 1. Disconnect the negative battery cable. 2. Disconnect the hold switch connector. 3. Check continuity of the switch. Tightening torque: 2.0-2.9 N.m (20-30 kgfscm, 18-26 in-lbf) Position Normal Depressed 7. lnstall the hold switch terminals and connect the connec- tor. 8. lnstall the indicator panel installation screws. (Refer to page K-163.) 9. lnstall the front console. 10. Connect the negative battery cable. PARKINEUTRAL SWITCH lnspection lnspection of operation 1. Verify that the starter operates only with the ignition switch at the START position and the selector lever in P and N ranges. 2. Verify that the back-up lights illuminate when shifted to R range with the ignition switch in the ON position. 3. Verify that the positions of the selector lever and the se- lector indicator light of the instrument cluster are aligned. 4. Check the ParkINeutral switch if not as specified. 0--4: Continuity 45UOKX-525 4. If not as specified, replace the selector lever knob as- sembly. (Refer to below.) 5. If the switch is OK, check the wiring harness. (Hold switch - powertrain control module (transmission), Hold switch - Body ground.) 6. lnstall the front console. 7. Connect the negative battery cable. Terminal A 0 B 0 Gartner Banana
Page 445 of 1708
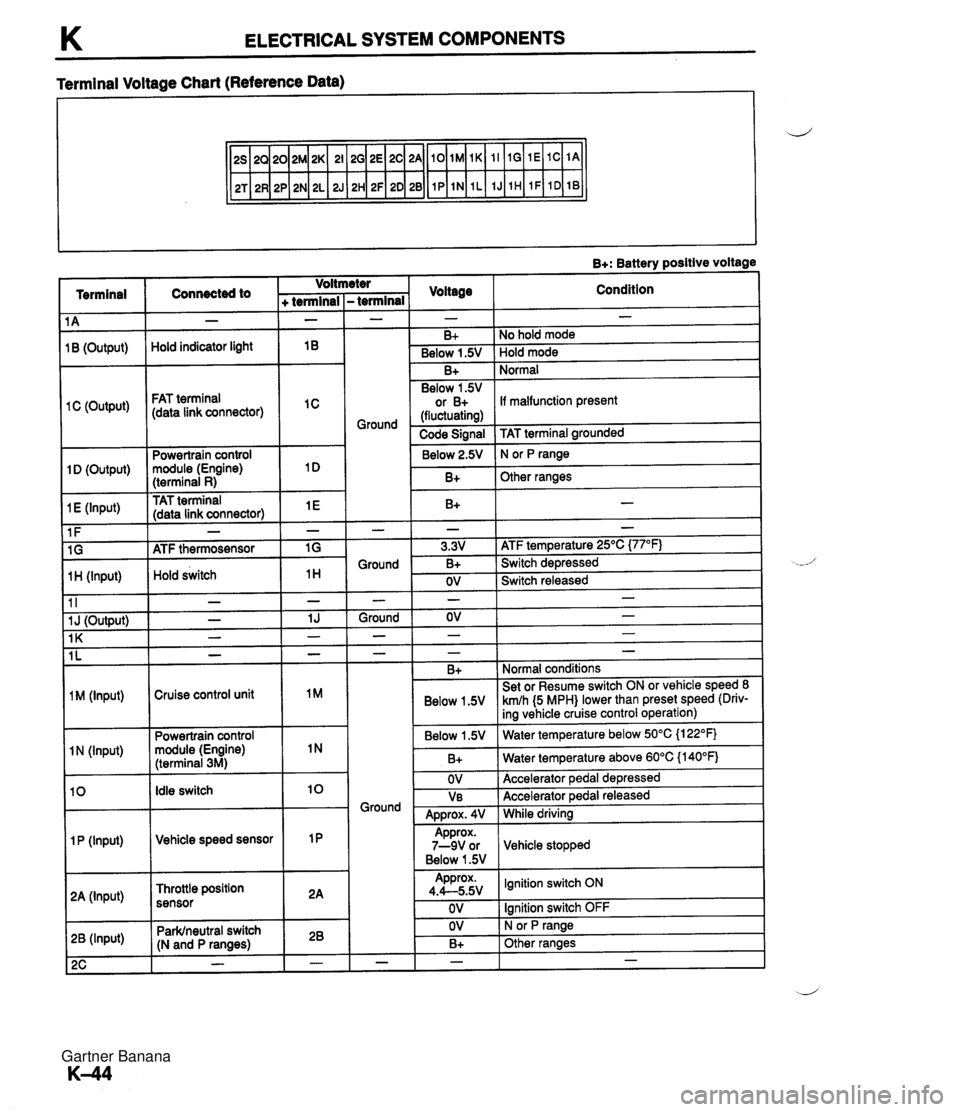
K ELECTRICAL SYSTEM COMPONENTS Terminal Voltage Chart (Reference Data) C Terminal B+: Battery positlve voltage y Hold indicator light Condition Connected to 16 (Output) B+ Below 1.5V - - - No hold mode Hold mode FAT terminal (data link connector) I IC Voltage - - Voltmeter B+ Below 1.5V or B+ I C (Output) - - -- -- - - - -- -- - - - - - - - A- +terminal Normal If malfunction resent Ground (fluctuating) I Code Sianal I TAT terminal wounded -terminal Powertrain control module (Engine) (terminal R) TAT terminal (data link connector) - I - Below 2.5V 1 N or P range 1 D (Output) I Bt ]Other ranges I 1 E (lnput) 1 F 1 G I ATF thermosensor I 1G 3.3V ATF temperature 25OC {77"F) Ground B+ Switch depressed .-,/ -~ - 1 H (Input) 1 I Hold switch 1 OV ] Switch released I I 1 J (Output) 1 K 1 M (lnput) Cruise control unit I lM 1 N (lnput) Powertrain control module (Engine) (terminal 3M) 1 lN Idle switch B+ OV - -- Ve Accelerator pedal released I ADDrox. 4V While drivina Water temperature above 60°C {I 40°F) Accelerator pedal de~ressed Below 1.5V Vehicle speed sensor 1 P (lnput) 1 P I Approx' I Ignition switch ON I 4.4-5.5V 2A (Input) Throttle position sensor 1 2A . . . - . - . OV I lanition switch OFF 1 ParWneutral switch (N and P ranges) I OV I N or P ranae I 26 (Input) I B+ I Other ranaes I Gartner Banana
Page 451 of 1708
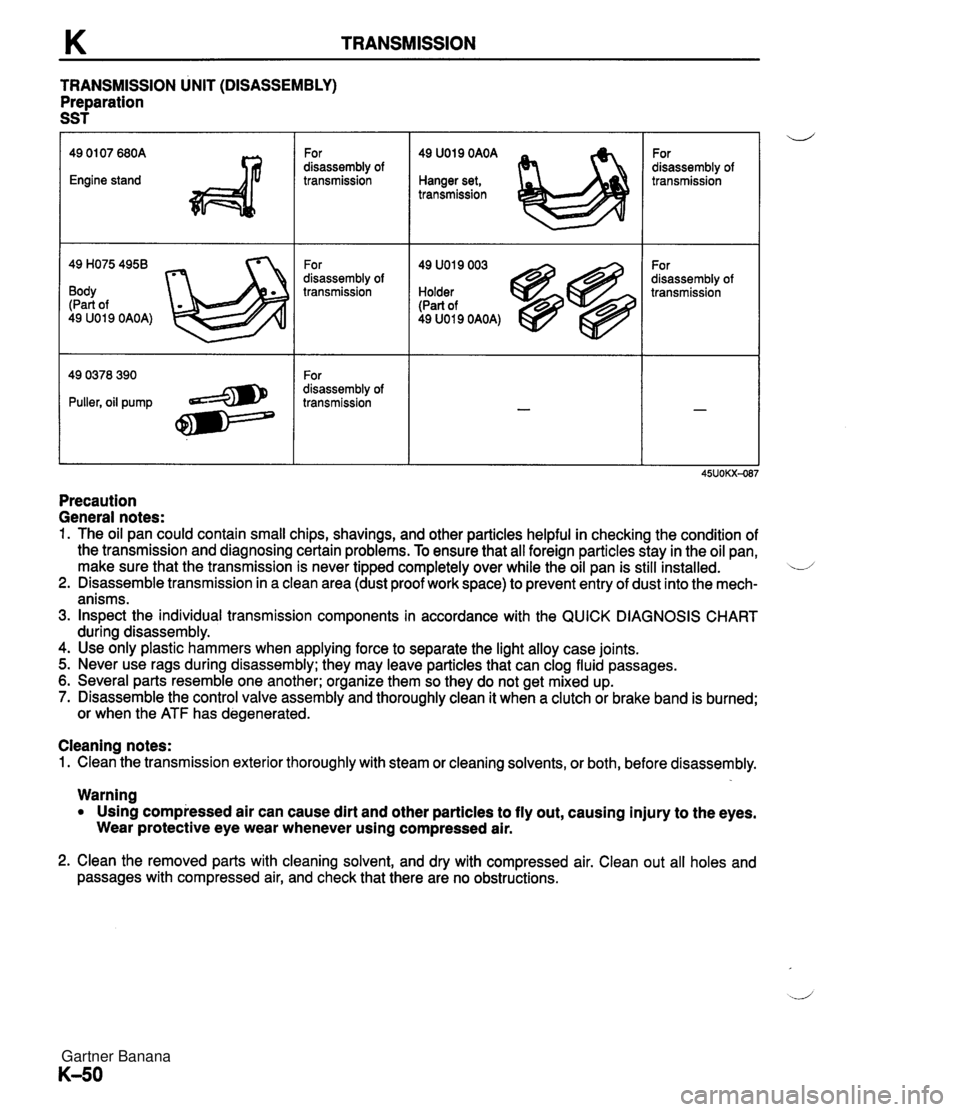
TRANSMISSION TRANSMISSION UNIT (DISASSEMBLY) Preparation SST 49 H075 4958 Body (Part of 49 U019 OAOA) For disassembly of transmission For disassembly of transmission For disassembly of transmission 49 U019 OAOA Hanger set, transmission 49 U019 003 Holder (Part of 49 U019 OAOA) For disassembly of transmission For disassembly of transmission Precaution General notes: 1. The oil pan could contain small chips, shavings, and other particles helpful in checking the condition of the transmission and diagnosing certain problems. To ensure that all foreign particles stay in the oil pan, make sure that the transmission is never tipped completely over while the oil pan is still installed. L/ 2. Disassemble transmission in a clean area (dust proof work space) to prevent entry of dust into the mech- anisms. 3. Inspect the individual transmission components in accordance with the QUICK DIAGNOSIS CHART during disassembly. 4. Use only plastic hammers when applying force to separate the light alloy case joints. 5. Never use rags during disassembly; they may leave particles that can clog fluid passages. 6. Several parts resemble one another; organize them so they do not get mixed up. 7. Disassemble the control valve assembly and thoroughly clean it when a clutch or brake band is burned; or when the ATF has degenerated. Cleaning notes: 1. Clean the transmission exterior thoroughly with steam or cleaning solvents, or both, before disassembly. Warning Using compressed air can cause dirt and other particles to fly out, causing injury to the eyes. Wear protective eye wear whenever using compressed air. 2. Clean the removed parts with cleaning solvent, and dry with compressed air. Clean out all holes and passages with compressed air, and check that there are no obstructions. Gartner Banana
Page 460 of 1708
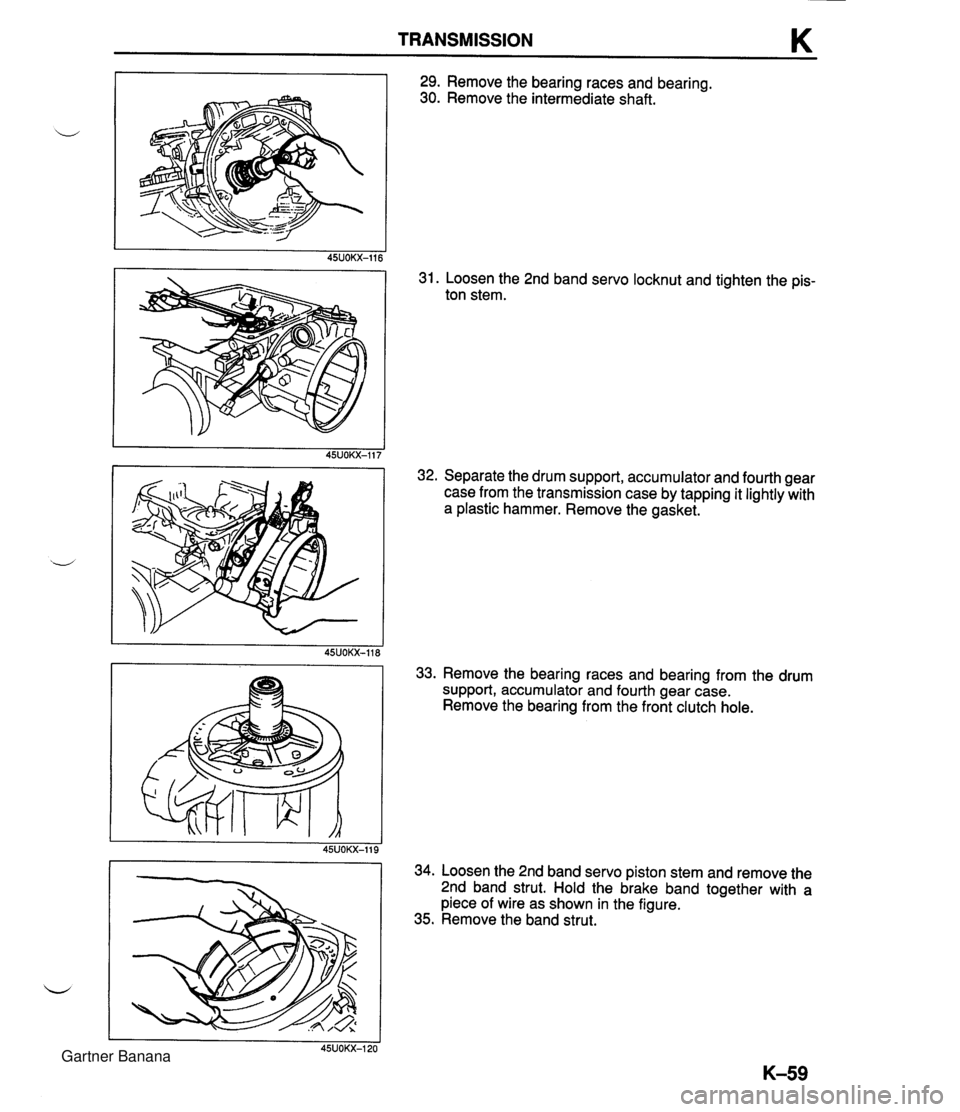
TRANSMISSION K 29. Remove the bearing races and bearing. 30. Remove the intermediate shaft. I 45UOKX-116 31. Loosen the 2nd band servo locknut and tighten the pis- ton stem. I 1 45UOKX-117 32. Separate the drum support, accumulator and fourth gear case from the transmission case by tapping it lightly with a plastic hammer. Remove the gasket. u 45UOKX-118 Remove the bearing races and bearing from the drum support, accumulator and fourth gear case. Remove the bearing from the front clutch hole. Loosen the 2nd band servo piston stem and remove the 2nd band strut. Hold the brake band together with a piece of wire as shown in the figure. Remove the band strut. Gartner Banana
Page 517 of 1708
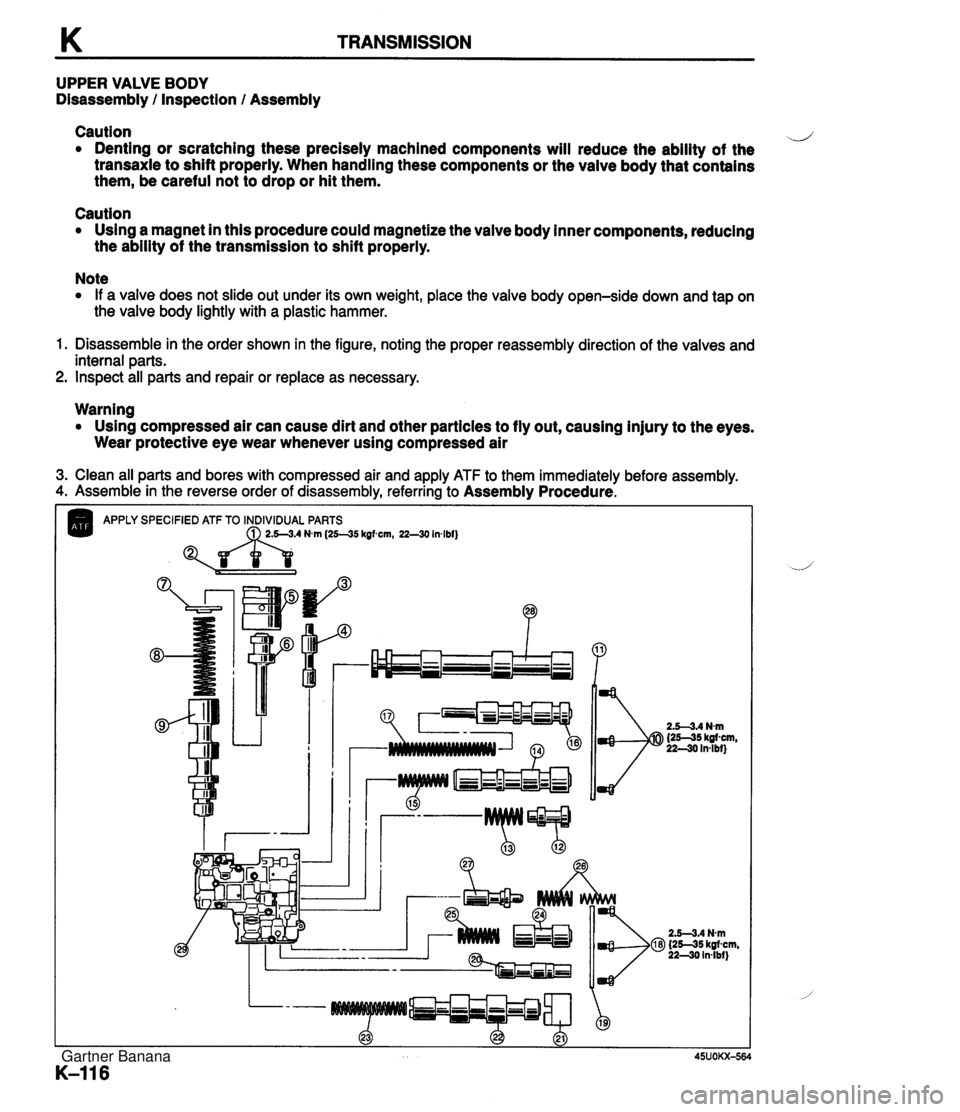
K TRANSMISSION UPPER VALVE BODY Disassembly / Inspection / Assembly Caution d Denting or scratching these precisely machined components will reduce the ability of the transaxle to shift properly. When handling these components or the valve body that contains them, be careful not to drop or hit them. Caution Using a magnet in this procedure could magnetize the valve body inner components, reducing the ability of the transmission to shift properly. Note If a valve does not slide out under its own weight, place the valve body open-side down and tap on the valve body lightly with a plastic hammer. 1. Disassemble in the order shown in the figure, noting the proper reassembly direction of the valves and internal parts. 2. Inspect all parts and repair or replace as necessary. Warning Using compressed air can cause dirt and other particles to fly out, causing injury to the eyes. Wear protective eye wear whenever using compressed air 3. Clean all parts and bores with compressed air and apply ATF to them immediately before assembly. 4. Assemble in the reverse order of disassembly, referring to Assembly Procedure. APPLY SPECIFIED ATF TO INDIVIDUAL PARTS Nvn (25--35 kgfwn, 22-30 Inlbf) Gartner Banana
Page 521 of 1708
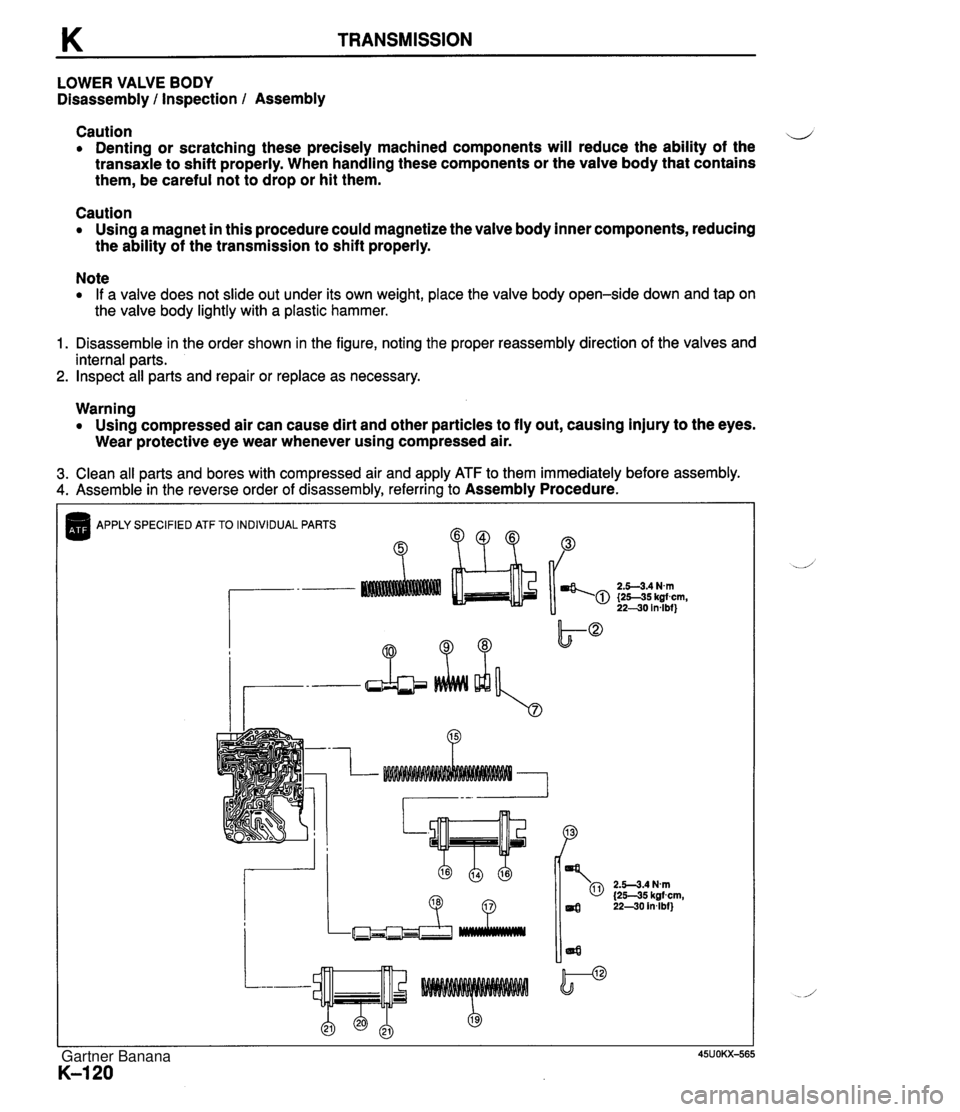
K TRANSMISSION LOWER VALVE BODY Disassembly l Inspection l Assembly Caution d Denting or scratching these precisely machined components will reduce the ability of the transaxle to shift properly. When handling these components or the valve body that contains them, be careful not to drop or hit them. Caution Using a magnet in this procedure could magnetize the valve body inner components, reducing the ability of the transmission to shift properly. Note If a valve does not slide out under its own weight, place the valve body open-side down and tap on the valve body lightly with a plastic hammer. 1. Disassemble in the order shown in the figure, noting the proper reassembly direction of the valves and internal parts. 2. Inspect all parts and repair or replace as necessary. Warning Using compressed air can cause dirt and other particles to fly out, causing injury to the eyes. Wear protective eye wear whenever using compressed air. 3. Clean all parts and bores with compressed air and apply ATF to them immediately before assembly. 4. Assemble in the reverse order of disassembly, referring to Assembly Procedure. APPLY SPECIFIED ATF TO INDIVIDUAL PARTS B ?? "P 2.5-3.4 Nm {25-35 kgfcm, 22-30 in4bf) Gartner Banana
Page 540 of 1708
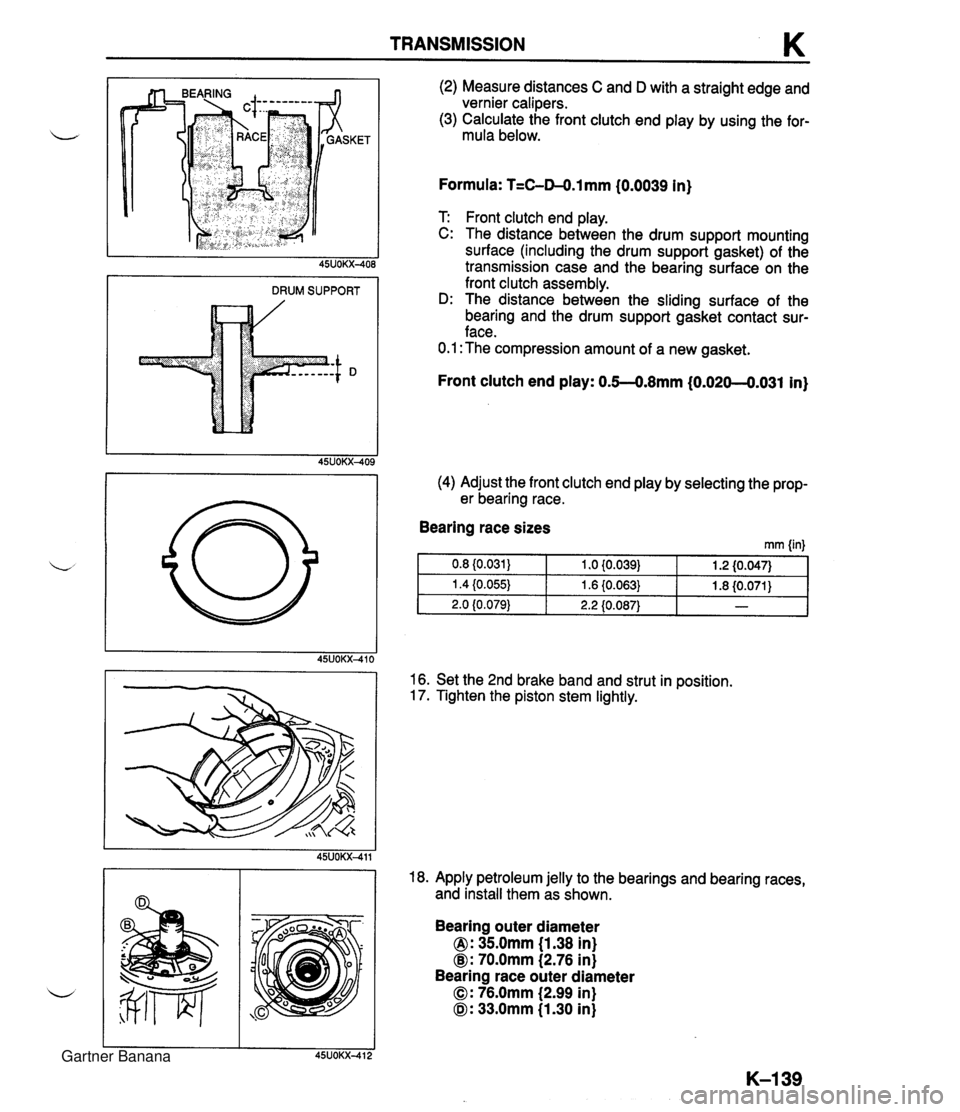
TRANSMISSION K DRUM SUPPORT (2) Measure distances C and D with a straight edge and vernier calipers. (3) Calculate the front clutch end play by using the for- mula below. Formula: T=C-04.1 mm {0.0039 In) T Front clutch end play. C: The distance between the drum support mounting surface (including the drum support gasket) of the transmission case and the bearing surface on the front clutch assembly. D: The distance between the sliding surface of the bearing and the drum support gasket contact sur- face. 0.1 :The compression amount of a new gasket. (4) Adjust the front clutch end play by selecting the prop- er bearing race. Front clutch end play: 0.5--0.8mm (0.020--0.031 in) Bearing race sizes rnm (in) 16. Set the 2nd brake band and strut in position. 17. Tighten the piston stem lightly. 18. Apply petroleum jelly to the bearings and bearing races, and install them as shown. Bearing outer diameter 0: 35.0mm (1.38 in) @: 70.0mm (2.76 in) Bearing race outer diameter 0: 76.0mm (2.99 in) 0: 33.0mm (1.30 in) Gartner Banana
Page 541 of 1708
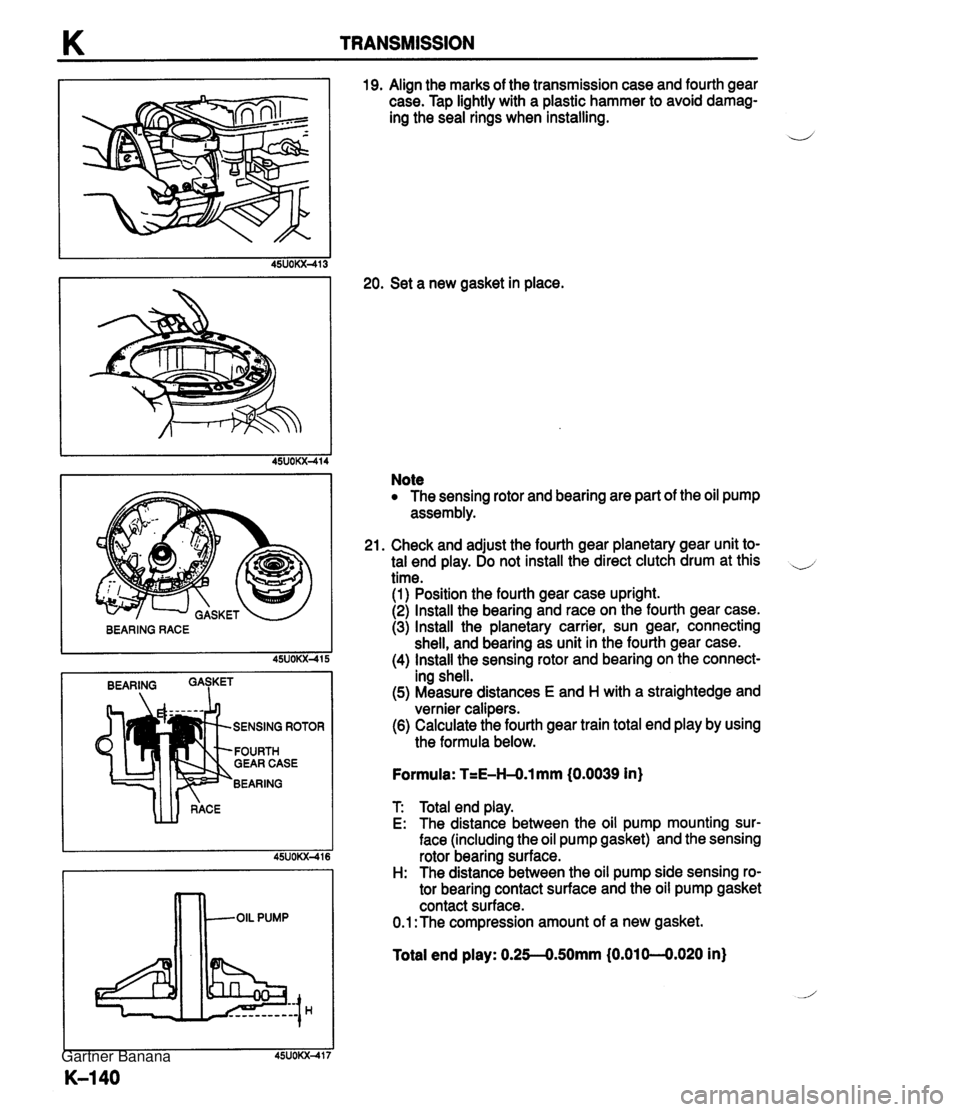
K TRANSMISSION I BEARING I SENSING ROTOR FOURTH GEAR CASE BEARING 19. Align the marks of the transmission case and fourth gear case. Tap lightly with a plastic hammer to avoid damag- ing the seal rings when installing. 20. Set a new gasket in place. Note The sensing rotor and bearing are part of the oil pump assembly. 21. Check and adjust the fourth gear planetary gear unit to- tal end play. Do not install the direct clutch drum at this .-, time. (1) Position the fourth gear case upright. (2) Install the bearing and race on the fourth gear case. (3) Install the planetary carrier, sun gear, connecting shell, and bearing as unit in the fourth gear case. (4) Install the sensing rotor and bearing on the connect- ing shell. (5) Measure distances E and H with a straightedge and vernier calipers. (6) Calculate the fourth gear train total end play by using the formula below. Formula: T=E-H-O.1 mm (0.0039 in) T Total end play. E: The distance between the oil pump mounting sur- face (including the oil pump gasket) and the sensing rotor bearing surface. H: The distance between the oil pump side sensing ro- tor bearing contact surface and the oil pump gasket contact surface. 0.1 :The compression amount of a new gasket. Total end play: 0.25-0.50mm (0.01 0-0.020 in} Gartner Banana
Page 550 of 1708
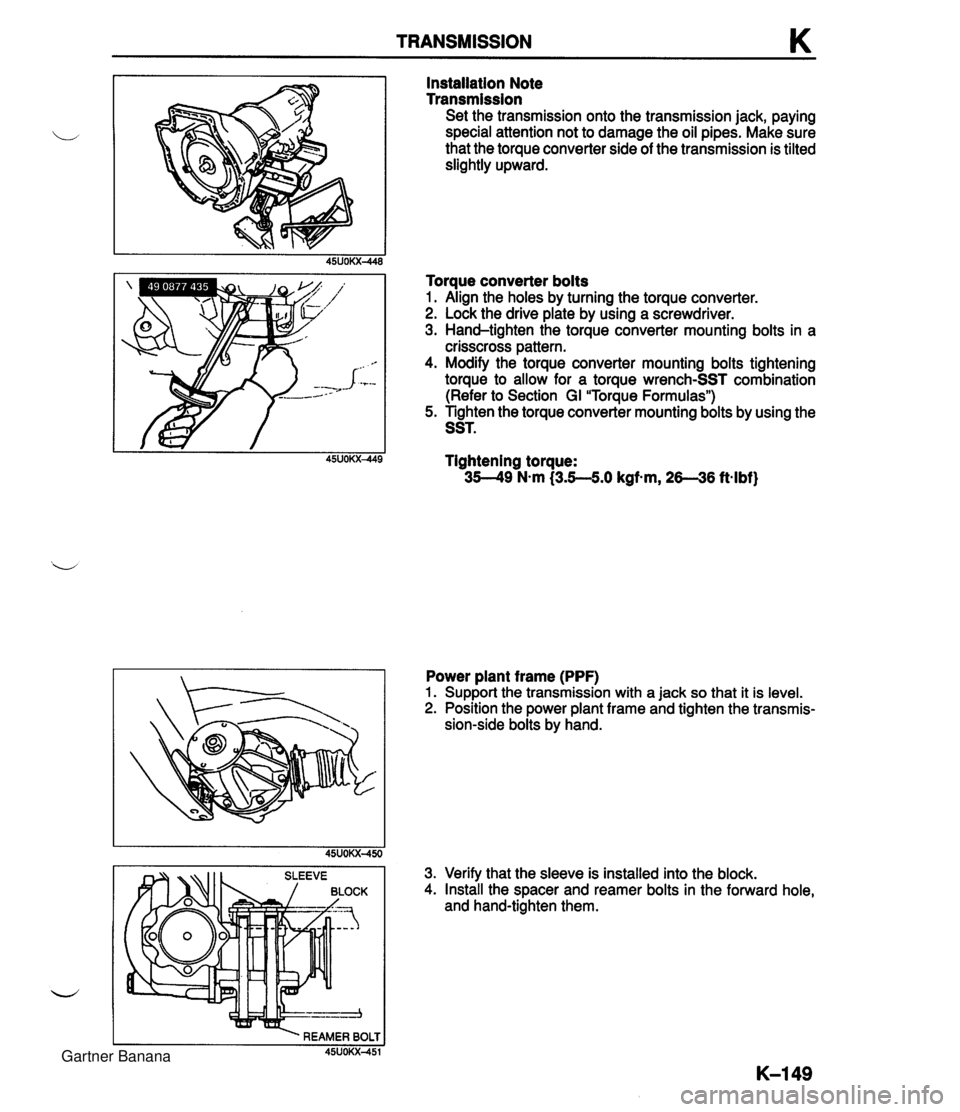
TRANSMISSION K Installation Note Transmission Set the transmission onto the transmission jack, paying special attention not to damage the oil pipes. Make sure that the torque converter side of the transmission is tilted slightly upward. Torque converter bolts 1. Align the holes by turning the torque converter. 2. Lock the drive plate by using a screwdriver. 3. Hand-tighten the torque converter mounting bolts in a crisscross pattern. 4. Modify the torque converter mounting bolts tightening torque to allow for a torque wrench-SST combination (Refer to Section GI "Torque Formulas") 5. Tighten the torque converter mounting bolts by using the SST. Tightening torque: 35-49 N-m (3.5-5.0 kgf-m, 26--36 ft-lbf) Power plant frame (PPF) 1. Support the transmission with a jack so that it is level. 2. Position the power plant frame and tighten the transmis- sion-side bolts by hand. 3. Verify that the sleeve is installed into the block. 4. Install the spacer and reamer bolts in the forward hole, and hand-tighten them. Gartner Banana
Page 556 of 1708
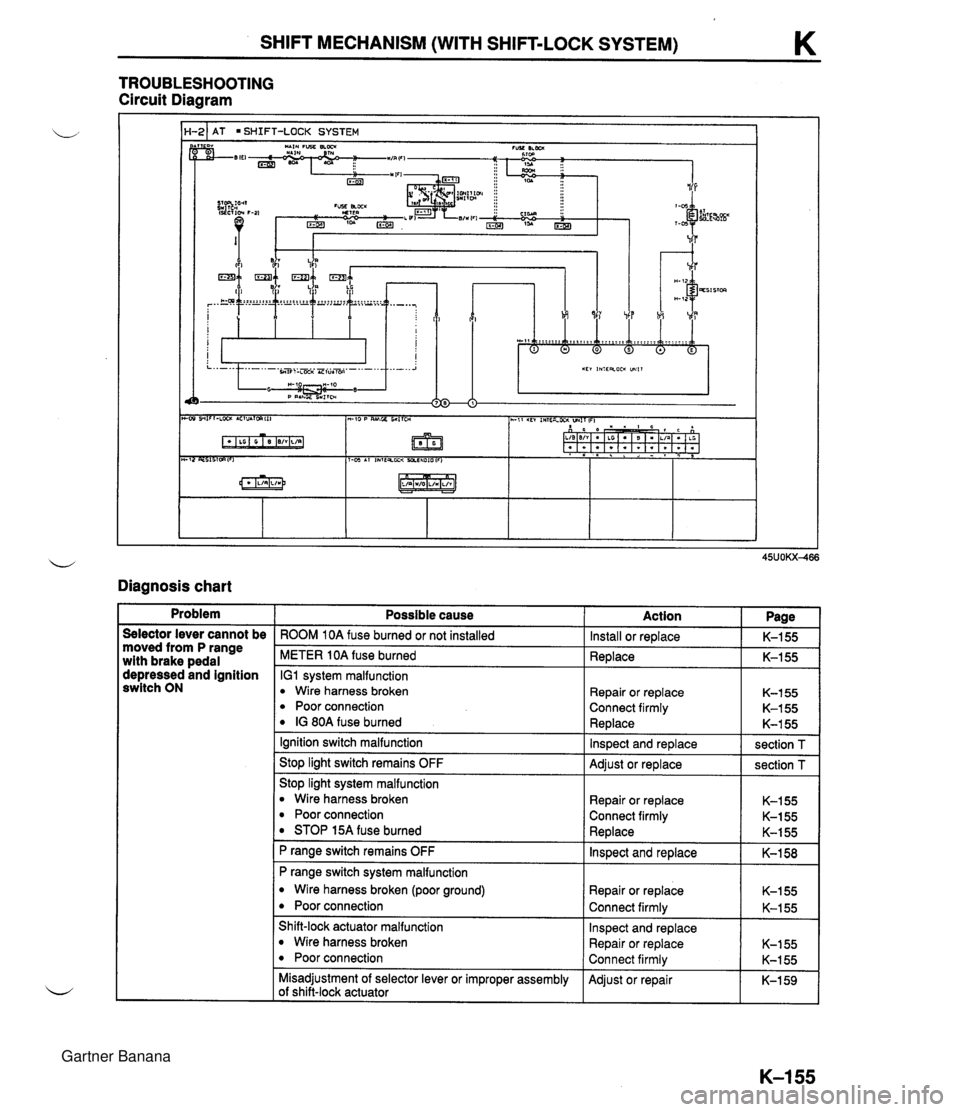
SHIFT MECHANISM (WITH SHIFT-LOCK SYSTEM) K TROUBLESHOOTING Circuit Diagram - 1-21 AT SHIFT-LOCK SYSTEM Diagnosis chart Problem -- Selector lever cannot be moved from P range with brake pedal depressed and ignition switch ON Possible cause ROOM 1 OA fuse burned or not installed METER 10A fuse burned IG1 system malfunction Wire harness broken Poor connection IG 80A fuse burned Ignition switch malfunction Stop light switch remains OFF Stop light system malfunction Wire harness broken Poor connection STOP 15A fuse burned P range switch remains OFF P range switch system malfunction Wire harness broken (poor ground) Poor connection Shift-lock actuator malfunction Wire harness broken Poor connection Misadjustrnent of selector lever or improper assembly of shift-lock actuator Action I Page Repair or replace Connect firmly Replace Install or replace Replace K-155 K-155 Repair or replace K-155 Connect firmly K-155 Replace K-155 Inspect and replace Adjust or replace section T section T Repair or replace Connect firmly Inspect and replace Repair or replace Connect firmly Adjust or repair K-155 K-I55 K-155 K-155 K-159 Gartner Banana