battery MAZDA MX-5 1994 Manual Online
[x] Cancel search | Manufacturer: MAZDA, Model Year: 1994, Model line: MX-5, Model: MAZDA MX-5 1994Pages: 1708, PDF Size: 82.34 MB
Page 270 of 1708
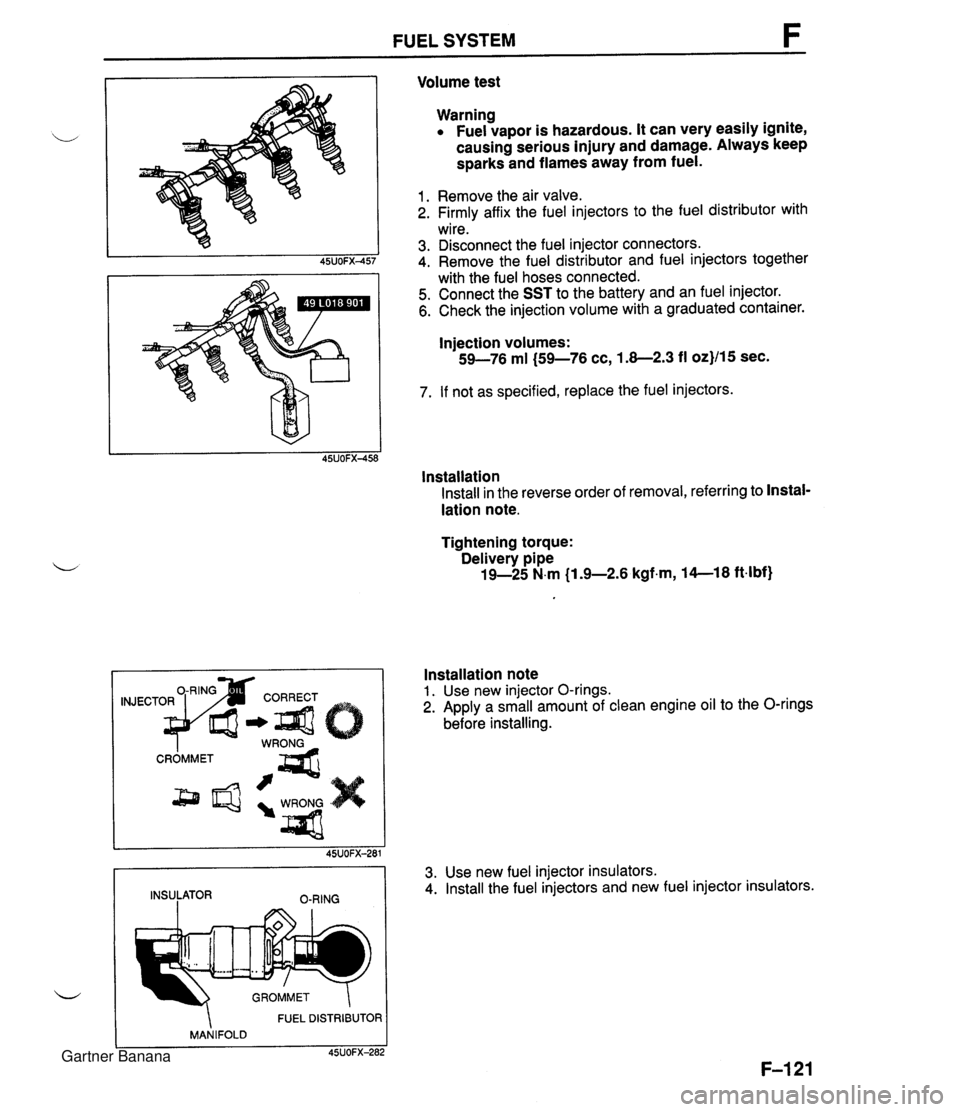
FUEL SYSTEM Volume test Warning Fuel vapor is hazardous. It can very easily ignite, causing serious injury and damage. Always keep sparks and flames away from fuel. 1. Remove the air valve. 2. Firmly affix the fuel injectors to the fuel distributor with wire. 3. Disconnect the fuel injector connectors. 4. Remove the fuel distributor and fuel injectors together with the fuel hoses connected. 5. Connect the SST to the battery and an fuel injector. 6. Check the injection volume with a graduated container. Injection volumes: 59-76 ml (59-76 cc, 1.8-2.3 fl oz}/15 sec. 7. If not as specified, replace the fuel injectors. lnstallation Install in the reverse order of removal, referring to Instal- lation note. Tightening torque: Delivery pipe 19-25 N.m (1 .%2.6 kgfm, 14--18 ft4bf) FUEL DISTRIBUTOR MANIFOLD C 45UOFX-282 Installation note 1. Use new injector O-rings. 2. Apply a small amount of clean engine oil to the O-rings before installing. 45UOFX-281 INSULATOR O-RING 3. Use new fuel injector insulators. 4. Install the fuel injectors and new fuel injector insulators. Gartner Banana
Page 272 of 1708
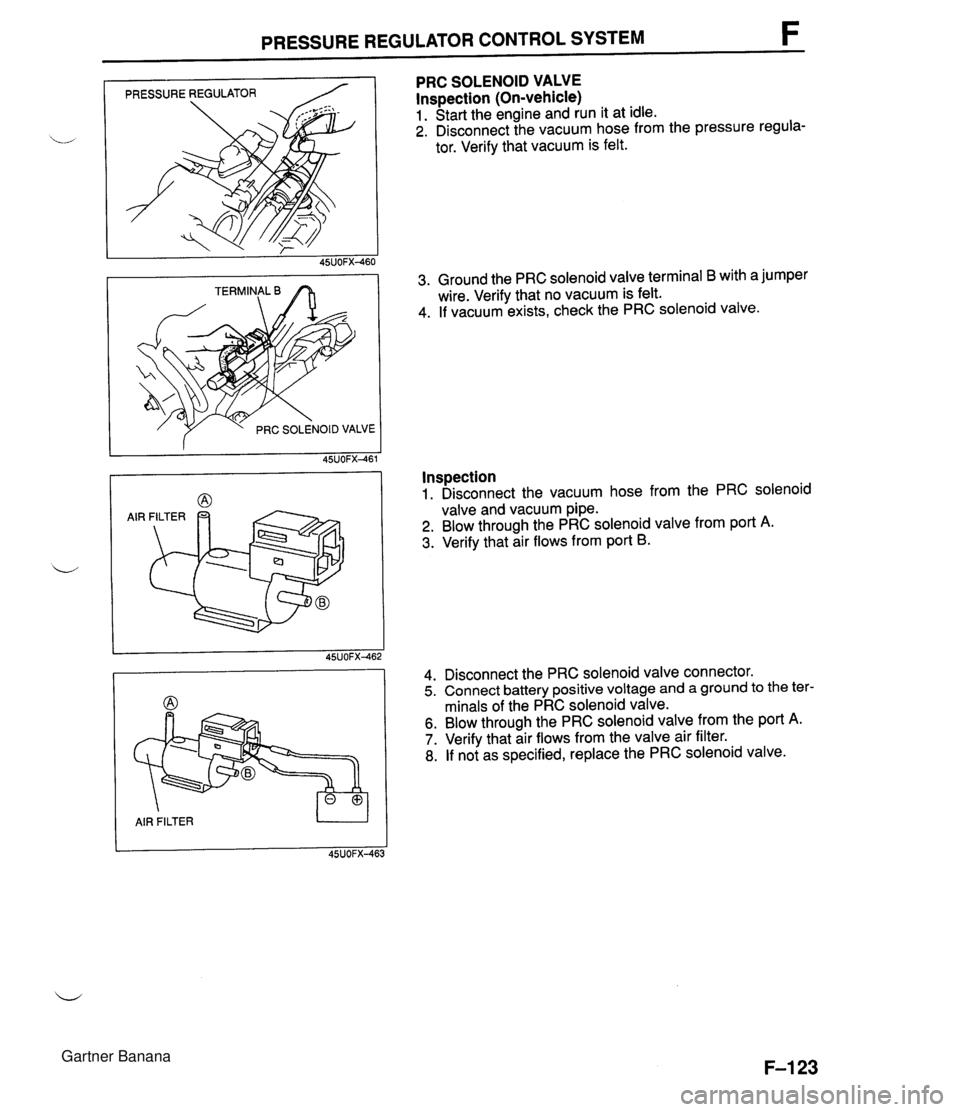
PRESSURE REGULATOR CONTROL SYSTEM F PRESSURE REGULATOR / f PRC SOLENOID VALVE AIR FILTER U PRC SOLENOID VALVE lnspection (On-vehicle) 1. Start the engine and run it at idle. 2. Disconnect the vacuum hose from the pressure regula- tor. Verify that vacuum is felt. 3. Ground the PRC solenoid valve terminal B with a jumper wire. Verify that no vacuum is felt. 4. If vacuum exists, check the PRC solenoid valve. Inspection 1. Disconnect the vacuum hose from the PRC solenoid valve and vacuum pipe. 2. Blow through the PRC solenoid valve from port A. 3. Verify that air flows from port B. 4. Disconnect the PRC solenoid valve connector. 5. Connect battery positive voltage and a ground to the ter- minals of the PRC solenoid valve. 6. Blow through the PRC solenoid valve from the port A. 7. Verify that air flows from the valve air filter. 8. If not as specified, replace the PRC solenoid valve. Gartner Banana
Page 274 of 1708
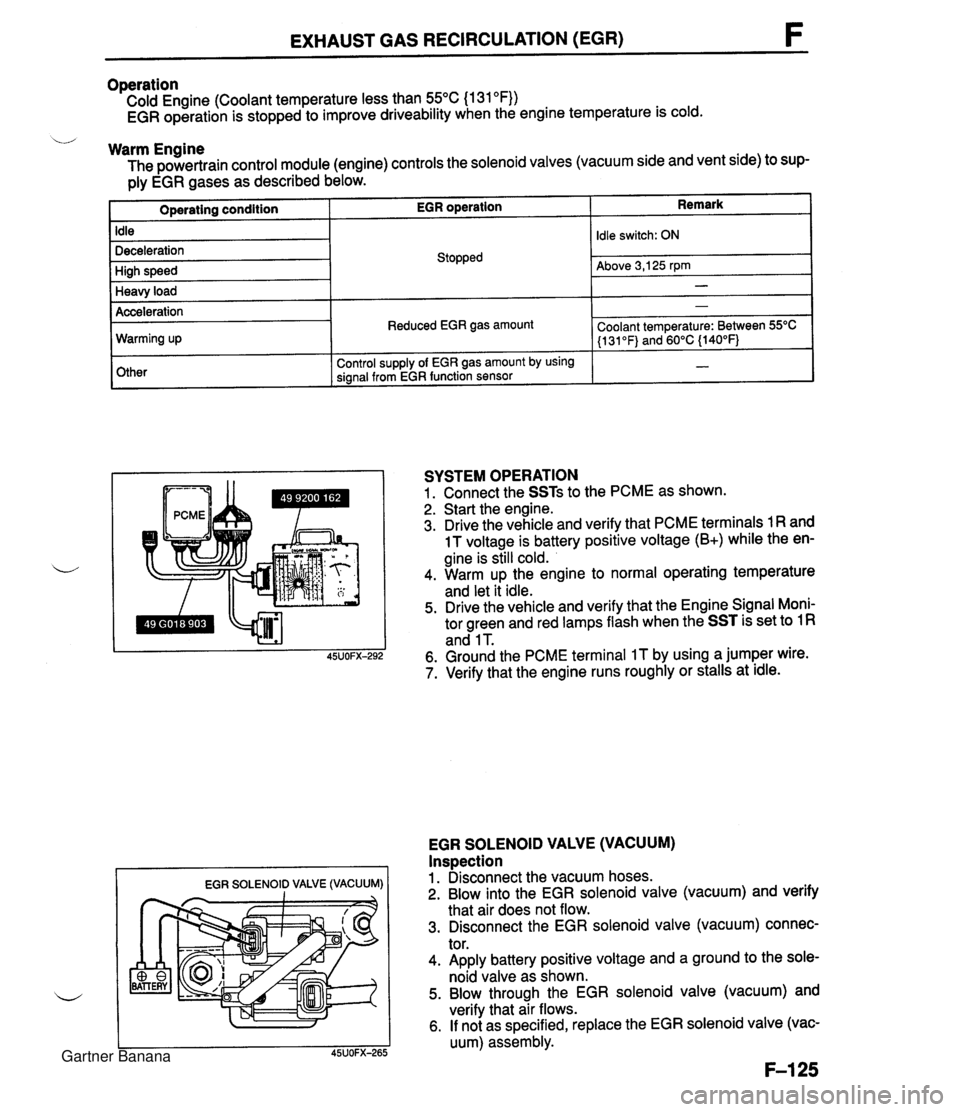
EXHAUST GAS RECIRCULATION (EGR) Operation Cold Engine (Coolant temperature less than 55°C (1 31 OF)) EGR operation is stopped to improve driveability when the engine temperature is cold. u Warm Engine The powertrain control module (engine) controls the solenoid valves (vacuum side and vent side) to sup- ply EGR gases as described below. Remark Operating condition Idle Deceleration High speed Heavy load EGR SOLENOID VALVE (VACUUM) I I EGR operation Acceleration Warming up Other SYSTEM OPERATION 1. Connect the SSTs to the PCME as shown. 2. Start the engine. 3. Drive the vehicle and verify that PCME terminals 1 R and 1 T voltage is battery positive voltage (B+) while the en- gine is still cold. 4. Warm up the engine to normal operating temperature and let it idle. 5. Drive the vehicle and verify that the Engine Signal Moni- tor green and red lamps flash when the SST is set to 1 R and 1 T. 6. Ground the PCME terminal IT by using a jumper wire. 7. Verify that the engine runs roughly or stalls at idle. Stopped EGR SOLENOID VALVE (VACUUM) Inspection 1. Disconnect the vacuum hoses. 2. Blow into the EGR solenoid valve (vacuum) and verify that air does not flow. 3. Disconnect the EGR solenoid valve (vacuum) connec- tor. 4. Apply battery positive voltage and a ground to the sole- noid valve as shown. 5. Blow through the EGR solenoid valve (vacuum) and verify that air flows. 6. If not as specified, replace the EGR solenoid valve (vac- uum) assembly. Idle switch: ON Above 3,125 rpm - Reduced EGR gas amount Control supply of EGR gas amount by using signal from EGR function sensor - Coolant temperature: Between 55OC (1 31 OF) and 60°C {140°F) - Gartner Banana
Page 275 of 1708
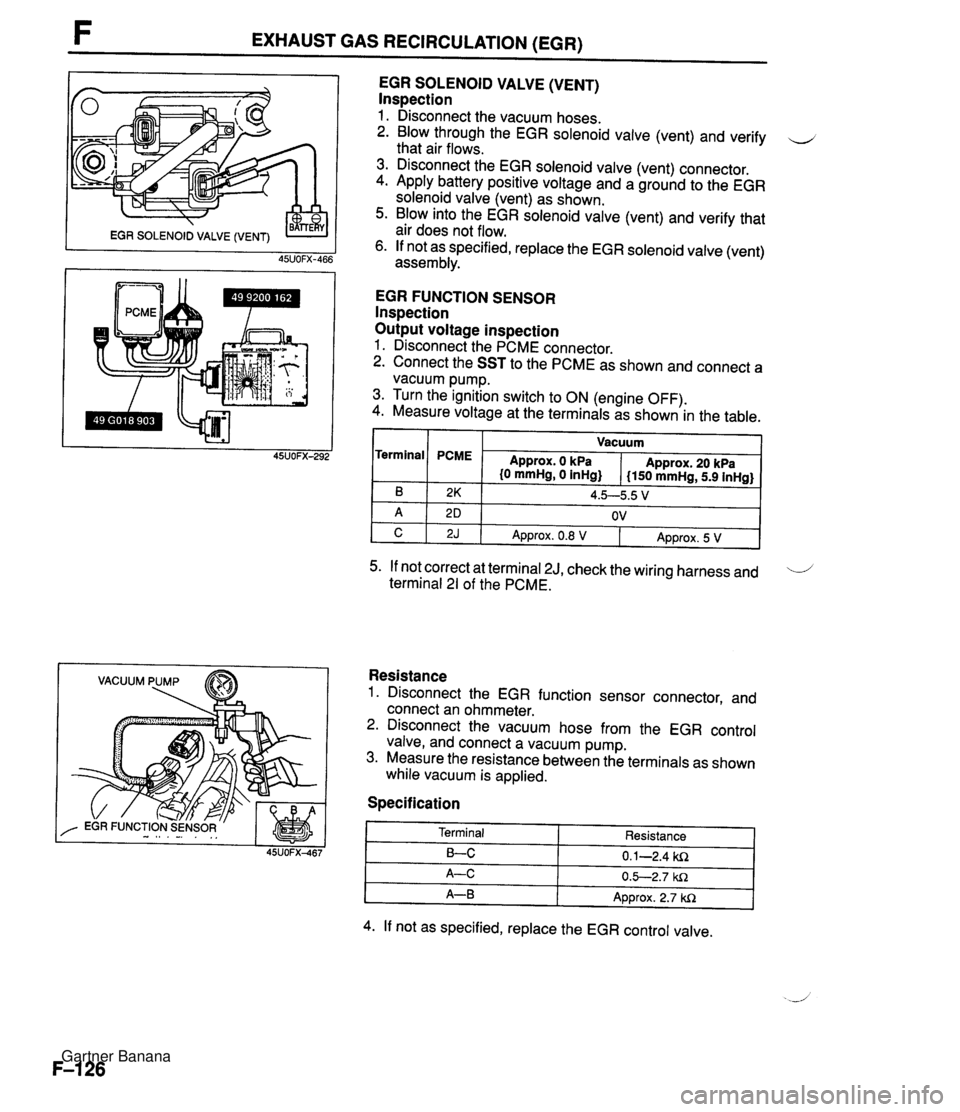
F EXHAUST GAS RECIRCULATION (EGR) VACUUM PUMP EGR SOLENOID VALVE (VENT) lnspection 1. Disconnect the vacuum hoses. 2. Blow through the EGR solenoid valve (vent) and verify u that air flows. 3. Disconnect the EGR solenoid valve (vent) connector. 4. Apply battery positive voltage and a ground to the EGR solenoid valve (vent) as shown. 5. Blow into the EGR solenoid valve (vent) and verify that air does not flow. 6. If not as specified, replace the EGR solenoid valve (vent) assembly. EGR FUNCTION SENSOR lnspection Output voltage inspection 1. Disconnect the PCME connector. 2. Connect the SST to the PCME as shown and connect a vacuum pump. 3. Turn the ignition switch to ON (engine OFF). 4. Measure voltage at the terminals as shown in the table. I I Vacuum I Terminal 5. If not correct at terminal 2J, check the wiring harness and 'i terminal 21 of the PCME. B A C Resistance 1. Disconnect the EGR function sensor connector, and connect an ohmmeter. 2. Disconnect the vacuum hose from the EGR control valve, and connect a vacuum pump. 3. Measure the resistance between the terminals as shown while vacuum is applied. PCME Specification 2K 2 D 2J Approx. 0 kPa {O mmHg, 0 inHg} 4. If not as specified, replace the EGR control valve. Approx. 20 kPa I150 mmHg, 5.9 inHg} 4.5--5.5 V OV Terminal LC A-C A-B Approx. 0.8 V Resistance 0.1-2.4 ki2 0.5-2.7 W1 Approx. 2.7 W1 Approx. 5 V Gartner Banana
Page 281 of 1708
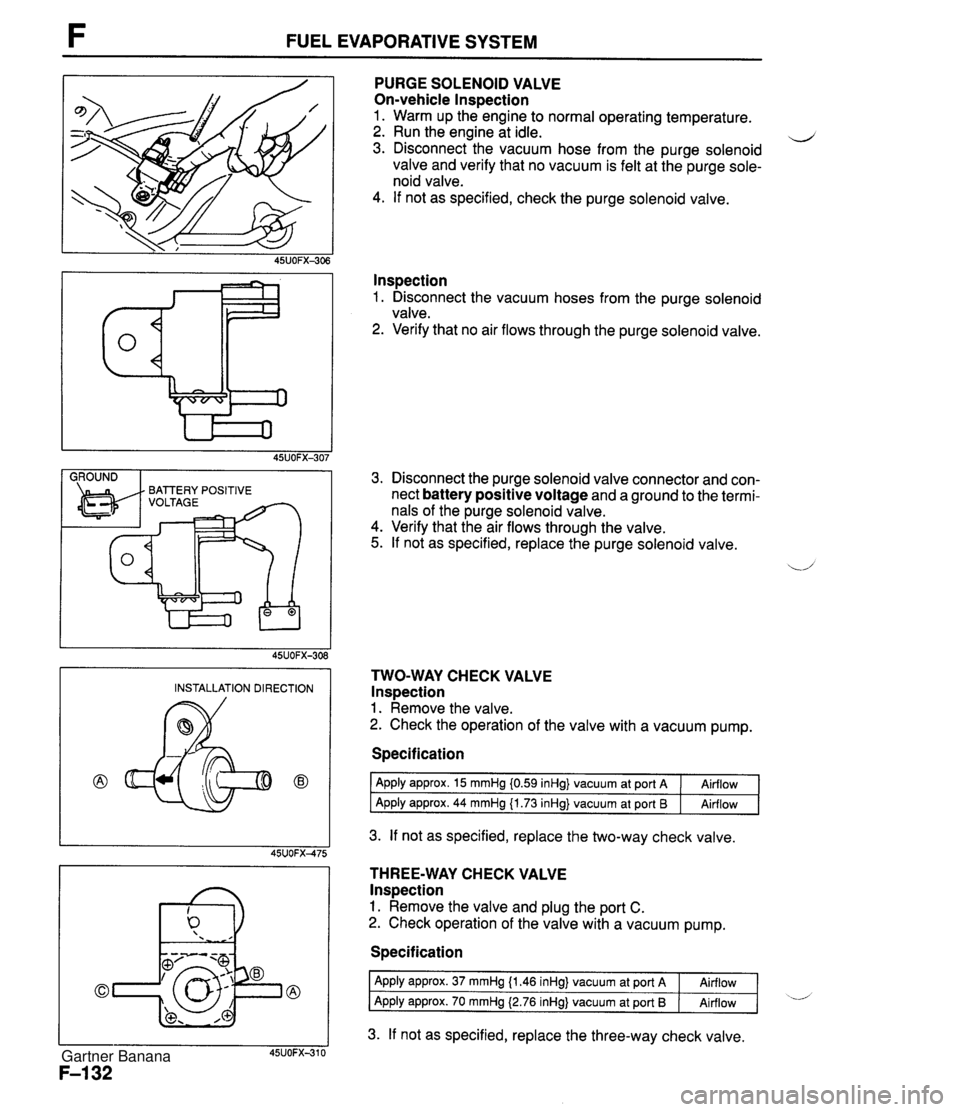
FUEL EVAPORATIVE SYSTEM I GROUND I PURGE SOLENOID VALVE On-vehicle lnspection 1. Warm up the engine to normal operating temperature. 2. Run the engine at idle. d 3. Disconnect the vacuum hose from the purge solenoid valve and verify that no vacuum is felt at the purge sole- noid valve. 4. If not as specified, check the purge solenoid valve. lnspection 1. Disconnect the vacuum hoses from the purge solenoid valve. 2. Verify that no air flows through the purge solenoid valve. 3. Disconnect the purge solenoid valve connector and con- nect battery positive voltage and a ground to the termi- nals of the purge solenoid valve. 4. Verify that the air flows through the valve. 5. If not as specified, replace the purge solenoid valve. TWO-WAY CHECK VALVE lnspection 1. Remove the valve. 2. Check the operation of the valve with a vacuum pump. INSTALLATION DIRECTION Specification I Apply approx. 15 mmHg i0.59 inHg} vacuum at port A 1 Airflow I 1 Agply apgrox. 44 mmH~ (1.73 inHd vacuum at Port 6 1 Airflow 1 3. If not as specified, replace the two-way check valve. THREE-WAY CHECK VALVE lnspection 1. Remove the valve and plug the port C. 2. Check operation of the valve with a vacuum pump. Specification 3. If not as specified, replace the three-way check valve. Apply approx. 37 mmHg {I -46 inHg} vacuum at port A Apply approx. 70 mmHg (2.76 inHg} vacuum at port I3 Airflow Airflow -d Gartner Banana
Page 285 of 1708
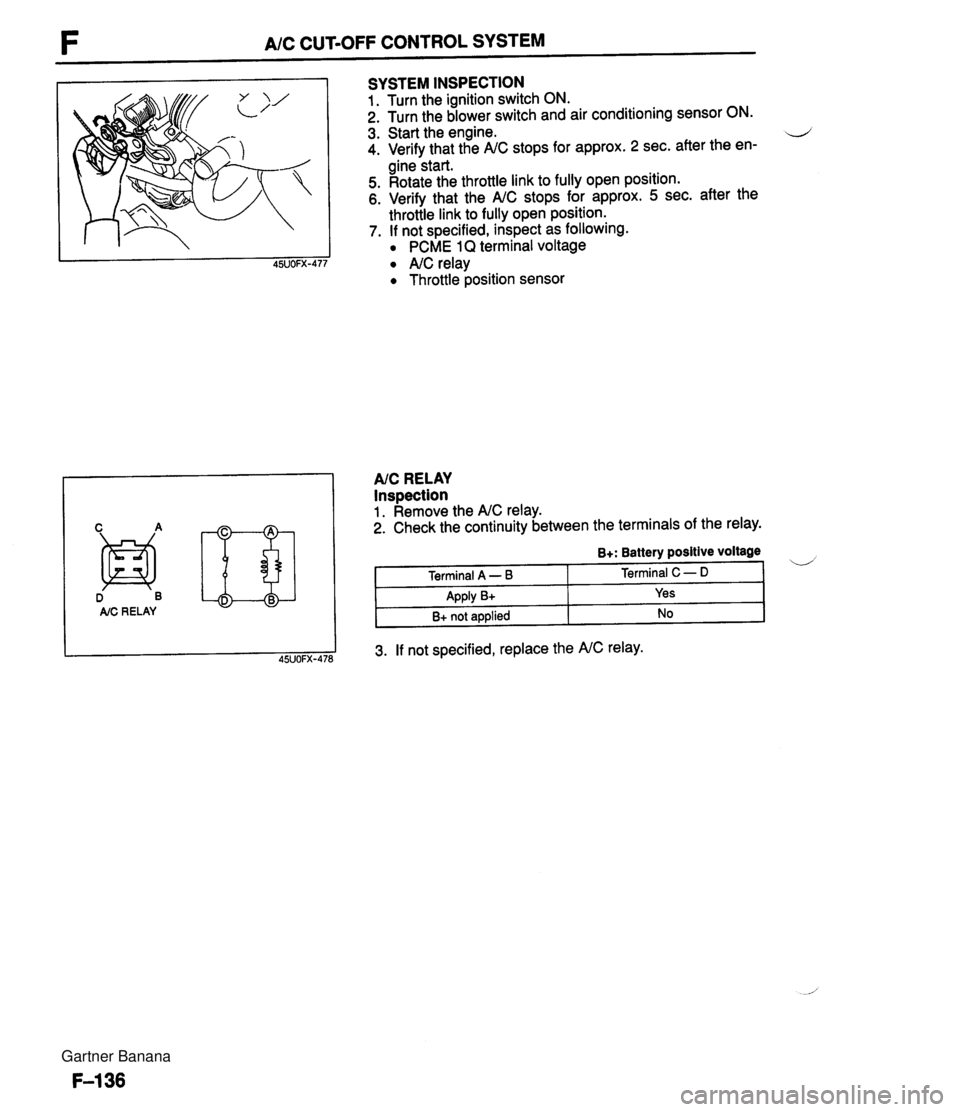
F A/C CUT-OFF CONTROL SYSTEM D B AIC RE LAY SYSTEM INSPECTION 1. Turn the ignition switch ON. 2. Turn the blower switch and air conditioning sensor ON. 3. Start the engine. d 4. Verify that the A/C stops for approx. 2 sec. after the en- gine start. 5. Rotate the throttle link to fully open position. 6. Verify that the A/C stops for approx. 5 sec. after the throttle link to fully open position. 7. If not specified, inspect as following. PCME 1Q terminal voltage A/C relay Throttle position sensor AIC RELAY Inspection 1. Remove the A/C relay. 2. Check the continuity between the terminals of the relay. 3. If not specified, replace the A/C relay. B+: Battery positive voltage Terminal A - B Apply B+ B+ not applied Terminal C - D Yes No Gartner Banana
Page 289 of 1708
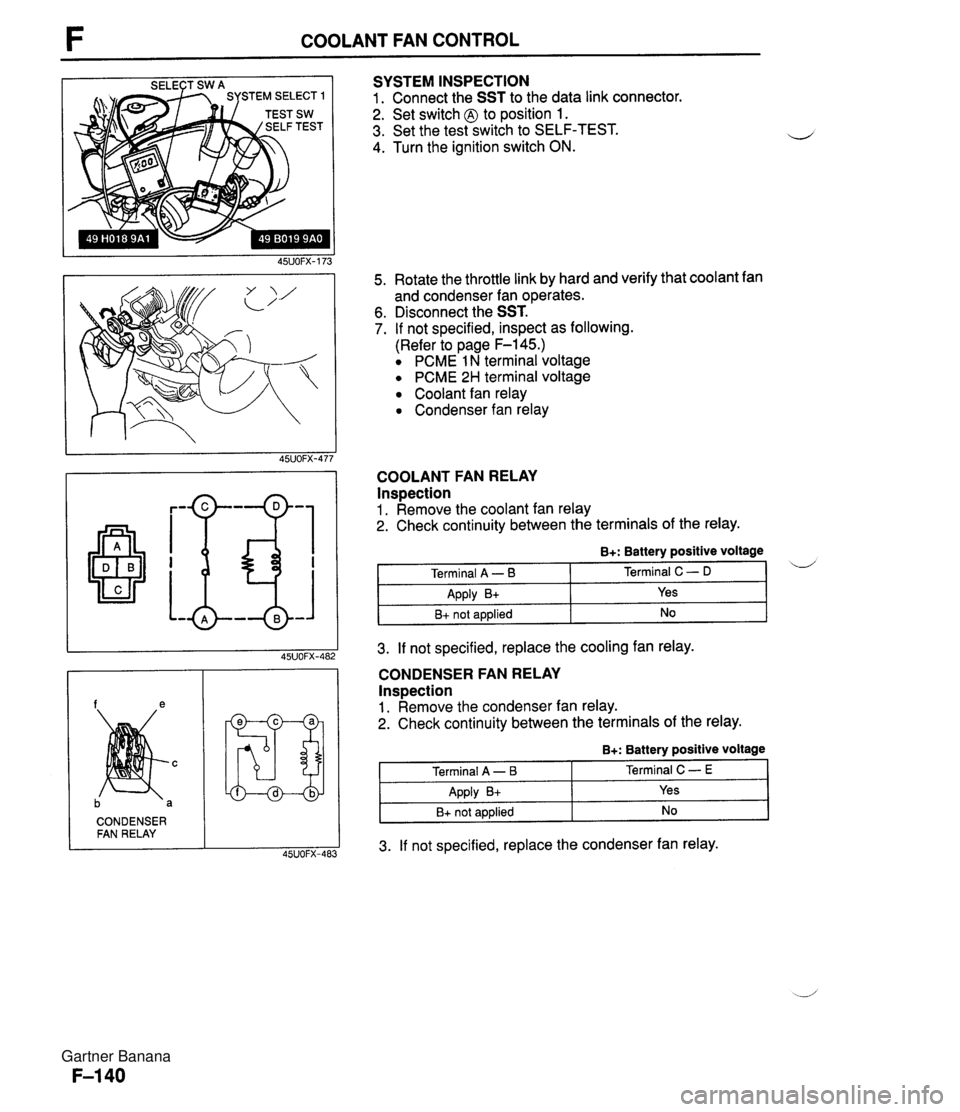
COOLANT FAN CONTROL SYSTEM INSPECTION 1. Connect the SST to the data link connector. 2. Set switch @ to position 1. 3. Set the test switch to SELF-TEST. 4. Turn the ignition switch ON. 5. Rotate the throttle link by hard and verify that coolant fan and condenser fan operates. 6. Disconnect the SST. 7. If not specified, inspect as following. (Refer to page F-145.) PCME 1 N terminal voltage PCME 2H terminal voltage Coolant fan relay Condenser fan relay COOLANT FAN RELAY lnspection 1. Remove the coolant fan relay 2. Check continuity between the terminals of the relay. CONDENSER FAN RELAY 3. If not specified, replace the cooling fan relay. B+: Battery positive voltage CONDENSER FAN RELAY Inspection 1. Remove the condenser fan relay. 2. Check continuity between the terminals of the relay. i/ Terminal A - B Apply B+ B+ not applied 3. If not specified, replace the condenser fan relay. Terminal C - D Yes No B+: Battery positive voltage Terminal A - I3 Apply B+ B+ not applied Terminal C - E Yes No Gartner Banana
Page 292 of 1708
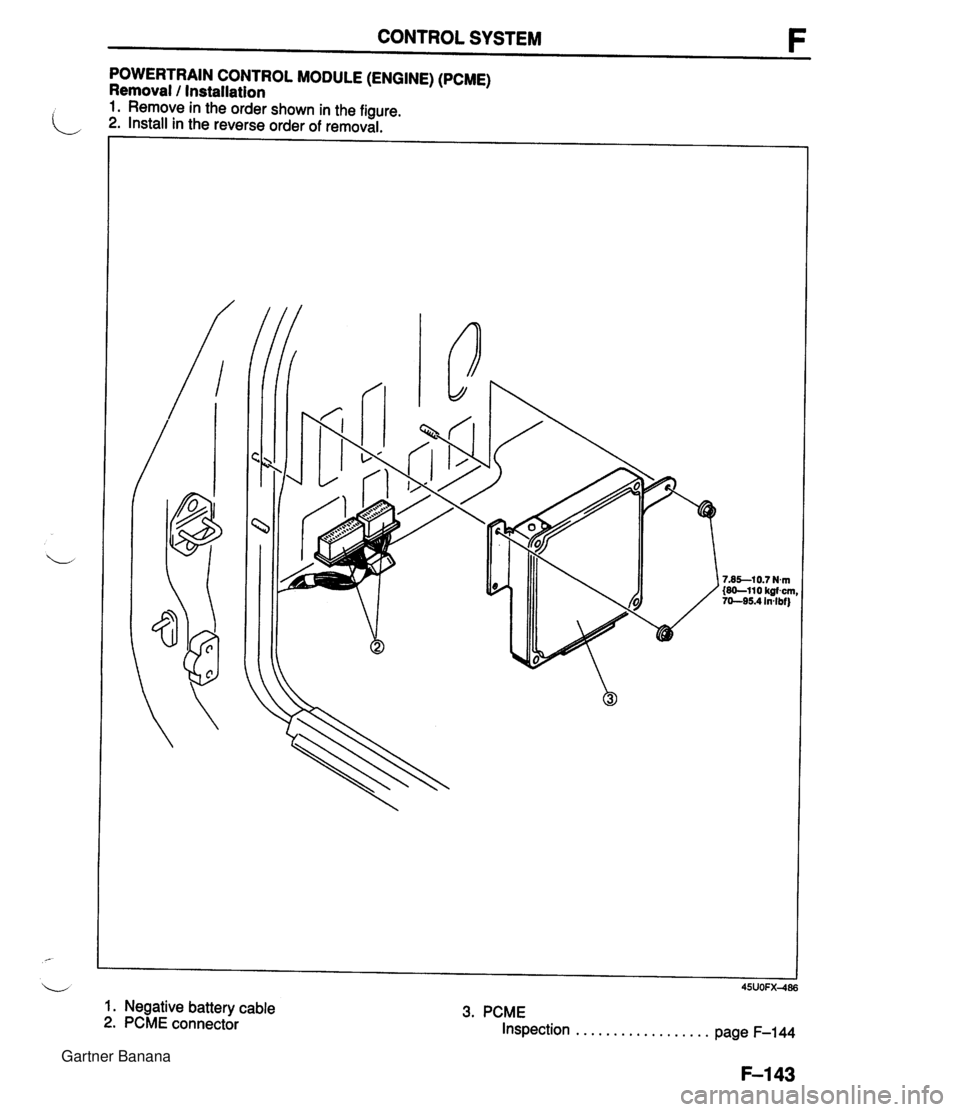
CONTROL SYSTEM F POWERTRAIN CONTROL MODULE (ENGINE) (PCME) Removal l Installation 1. Remove in the order shown in the figure. L 2. Install in the reverse order of removal. 1. Negative battery cable 2. PCME connector 3. PCME Inspection . . . . . . . . . . . . . . . . . . page F-144 Gartner Banana
Page 294 of 1708

CONTROL SYSTEM F Terminal voltage B+: Battery positive voltage Test condition I Voltage I Remark - - - - - - - - - - - - - - - - - - Connection to Battery Constant Ignition switch OFF Main relay - B+ OV lgnition switch (Start position) For backup - Ignition switch ON While cranking Lamp illuminated for 3 sec. after 1 4.5-5.5V ianition switch OFF+ON 1 B+ Approx. 1 OV Ignition switch ON - - OV Data link connector (MEN terminal) Test switch at "SELF-TEST" .. Lamp not illuminated after 3 sec. Test switch at "02 MONITOR" at idle Monitor lam illuminated & 4.5-5.5v . . I Malfunction indicator IighVData link connector (FEN ter- minal) With Self-Diagnosis Checker and System Selector Test switch at "02 MONITOR" at idle Monitor lamp not illuminated Light illuminated and buzzer sounded for 3 sec. after ignition switch OFF-ON B+ tor tesiswitch at "SELF-TEST" With Self-Diagnosis checker and system selector Below 2.5V 1 Light illuminated and buzzer sounded 1 Below 2.5V I With System Selec- Light not illuminated and buzzer not sounded after 3 sec. I Light not illuminated and buzzer 1 n. 1 B+ not sound I D+ 1 - #I, 4 lgniter (in IG COIL) #2,3 Igniter (in IG COIL) Powertrain control module (transmis- sion) - Ignition switch ON Idle Ignition switch ON Idle lgnition switch ON (Engine coolant temp, below 60°C {I 40°F)) Ignition switch ON AtC relay Air conditioning sensor ON at idle Air conditioning sensor OFF at idle Ground (MT) - OV Approx. 0.2V OV Approx. 0.2V Below 1 .OV B+ Below 2.5V B+ - - - - , * Open (AT) - Ignition switch ON ( Below 1 .O V I Engine coolant temp. I Below .OV I ldle Above 97°C (206.6OF1 Ignition switch ON I I B+ Ignition switch ON Coolant fan relay B+ . - Other conditions lgnition switch On dround data link connector TEN terminal I Blow 1.0" I B+ Vehicle speed sensor ldle switch OFF While driving Vehicle sto~wed ldle switch (in throttle position sensor) 2-5V 1 or 7V . , Accelerator pedal released Accelerator ~edal de~ressed - Stoplight switch OV B+ Brake pedal released Brake ~edal deoressed lgnition switch ON Steering pressure sensor OV B+ I I - Ignition switch ON B+ - PIS ON (at idle) PIS OFF (at idle) Air conditioning sensor Air conditioning sensor ON (Igni- tion switch ON) Air conditioning sensor OFF (Igni- tion switch ON) OV B+ - Below 2.5V B+ Blower motor ON Gartner Banana
Page 295 of 1708
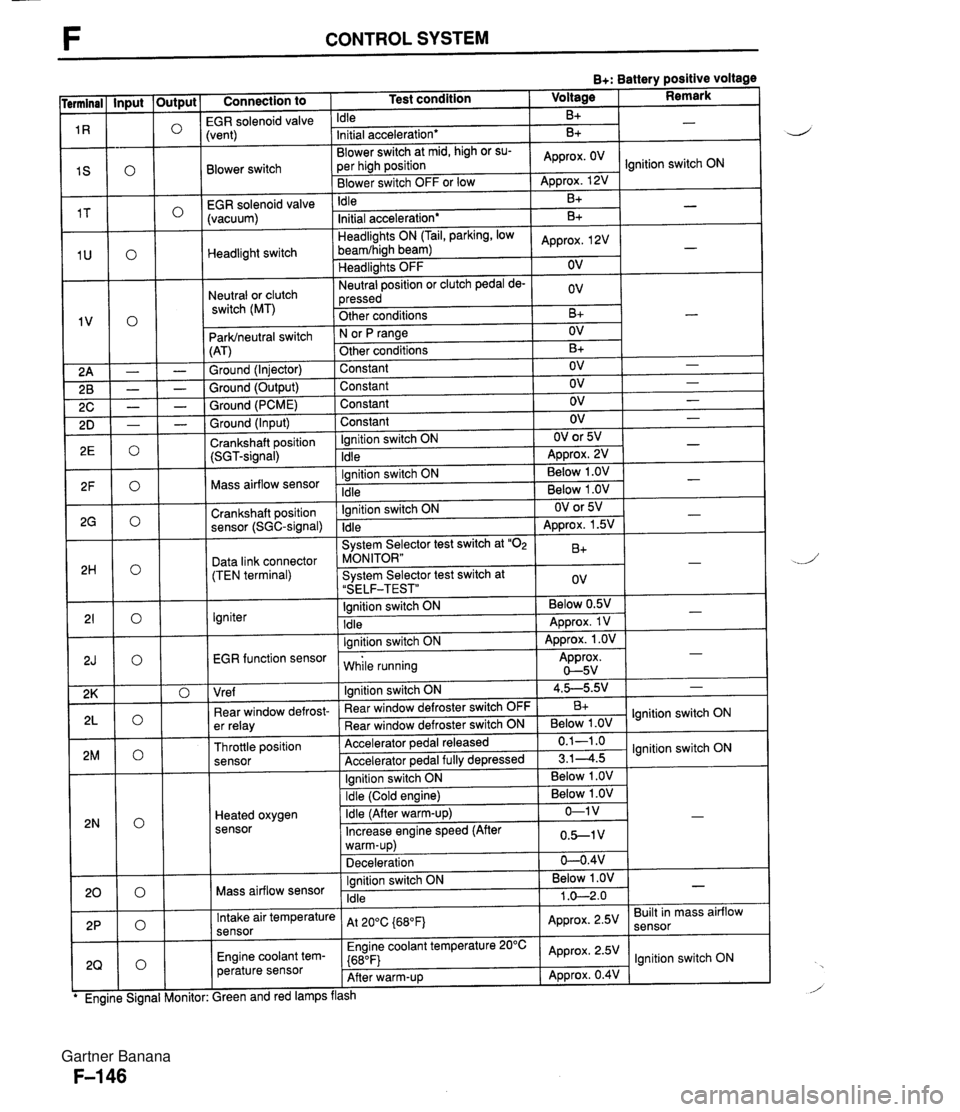
F CONTROL SYSTEM B+: Battery positive voltage Connection to 1 Test condition 1 Voltage I Remark I -- EGR solenoid valvi Idle B+ Blower switch -- EGR solenoid valve (vacuum) :vent) Initial acceleration* Blower switch at mid, high or su- per high position Blower switch OFF or low Headlight switch Neutral or clutch switch (MT) B+ Idle ParWneutral switch (AT) Ground (Injector) Ground (Output) Ground (PCME) Approx. OV - Approx. 12V B+ Headlights ON (Tail, parking, low beamfhigh beam) Headlights OFF Neutral position or clutch pedal de- pressed Other conditions Ground (Input) Crankshaft position (SGT-signal) Ignition switch ON N or fJ range Other conditions Constant Constant Constant -. Mass airflow sensor .. . . EGR function sensor I while running Approx. 0-5v Initial acceleration* Approx, 2V OV ov B+ Constant Ignition switch ON Idle Crankshaft position sensor (SGC-signal) Data link connector (TEN terminal) Igniter I I I Vre f I lanition switch ON 1 4.5-5.9.' 1 - B+ - OV B+ OV OV OV Ignition switch ON Idle - - - OV OV or 5V ADD~OX. 2V - - Ignition switch ON Idle System Selector test switch at "02 MONITOR" System Selector test switch at "SELF-TEST" Ignition switch ON Idle lanition switch ON I . . I I 1 Ignition switch ON I Below 1 .OV I I - - . . Below 1 .OV Below 1 .OV ear window defrost- er relay Throttle position sensor Heated oxygen sensor - OV or 5V Approx. 1.5V B+ ov Below 0.5V Approx. 1 V Approx. 1 .OV - - - " Rear window defroster switch OFF Rear window defroster switch ON Accelerator pedal released Accelerator ~edal fullv de~ressed Mass airflow sensor B+ Below 1 .OV 0.1-1 .o 3.14.5 Intake air temperature sensor Engine coolant tem- perature sensor lgnition switch ON lgnition switch ON Ignition switch ON Idle ireen and red lamps flash At 200C {680Fj Engine coolant temperature 20°C {680F) After warm-up Below 1 .OV 1 .O-2.0 - Approx. 2.5V Approx. 2.5V Approx. 0.4V Built in mass airflow lgnition switch ON Gartner Banana