engine MAZDA PROTEGE 1992 Owners Manual
[x] Cancel search | Manufacturer: MAZDA, Model Year: 1992, Model line: PROTEGE, Model: MAZDA PROTEGE 1992Pages: 1164, PDF Size: 81.9 MB
Page 172 of 1164
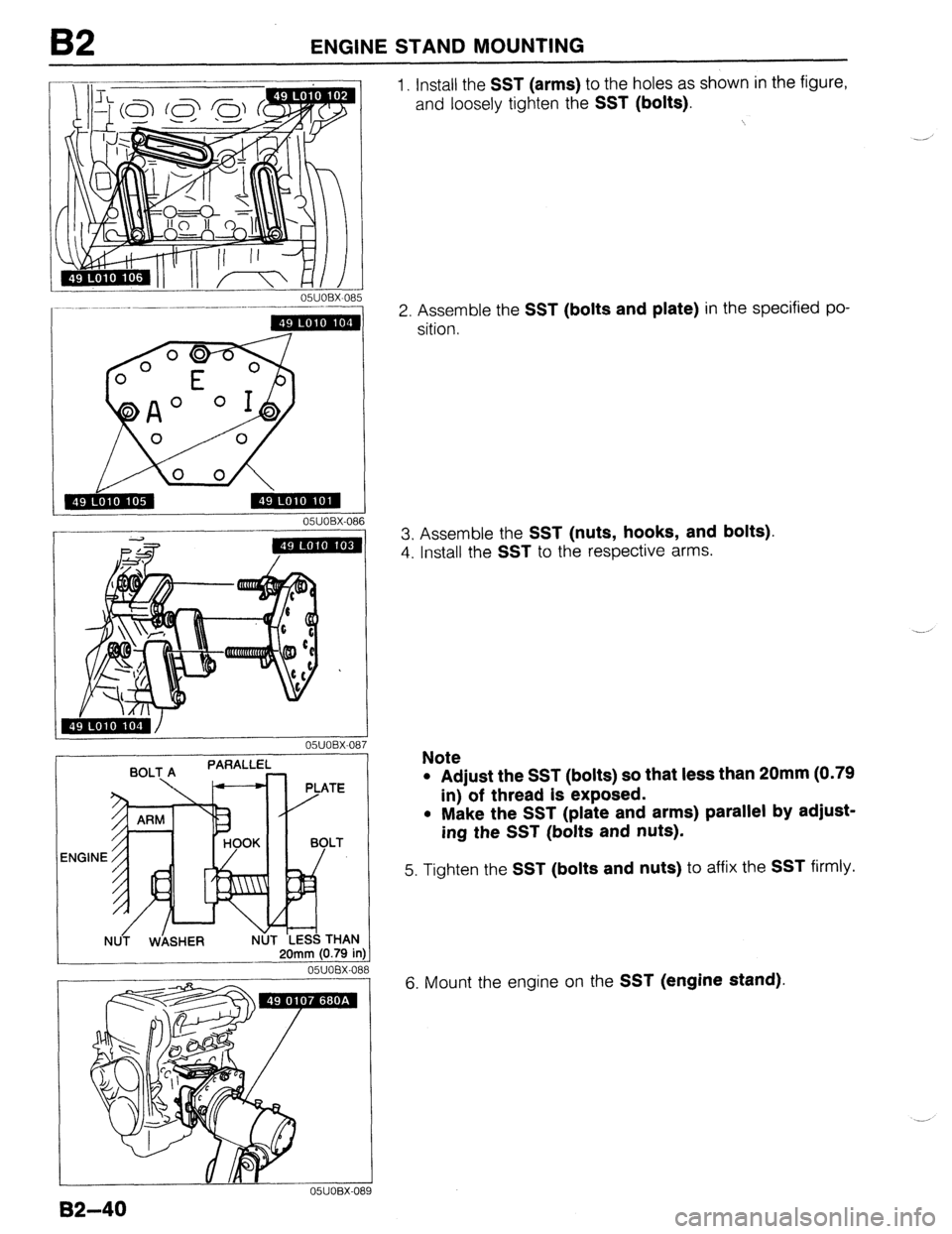
B2 ENGINE STAND MOUNTING
051JOBX-08
05UOBX.086
20mm (0.79 in 20mm (0.79 in
05UOEX-OE
05UOBX-01
1. Install the SST (arms) to the holes as shown in the figure,
and loosely tighten the
SST (bolts).
2. Assemble the SST (bolts and plate) in the specified po-
sition.
3. Assemble the
SST (nuts, hooks, and bolts).
4. Install the SST to the respective arms.
Note
l Adjust the SST (bolts) so that less than 20mm (0.79
in) of thread is exposed.
l Make the SST (plate and arms) parallel by adjust-
ing the SST (bolts and nuts).
5. Tighten the SST (bolts and nuts) to affix the SST firmly.
6. Mount the engine on the
SST (engine stand).
82-40
Page 173 of 1164
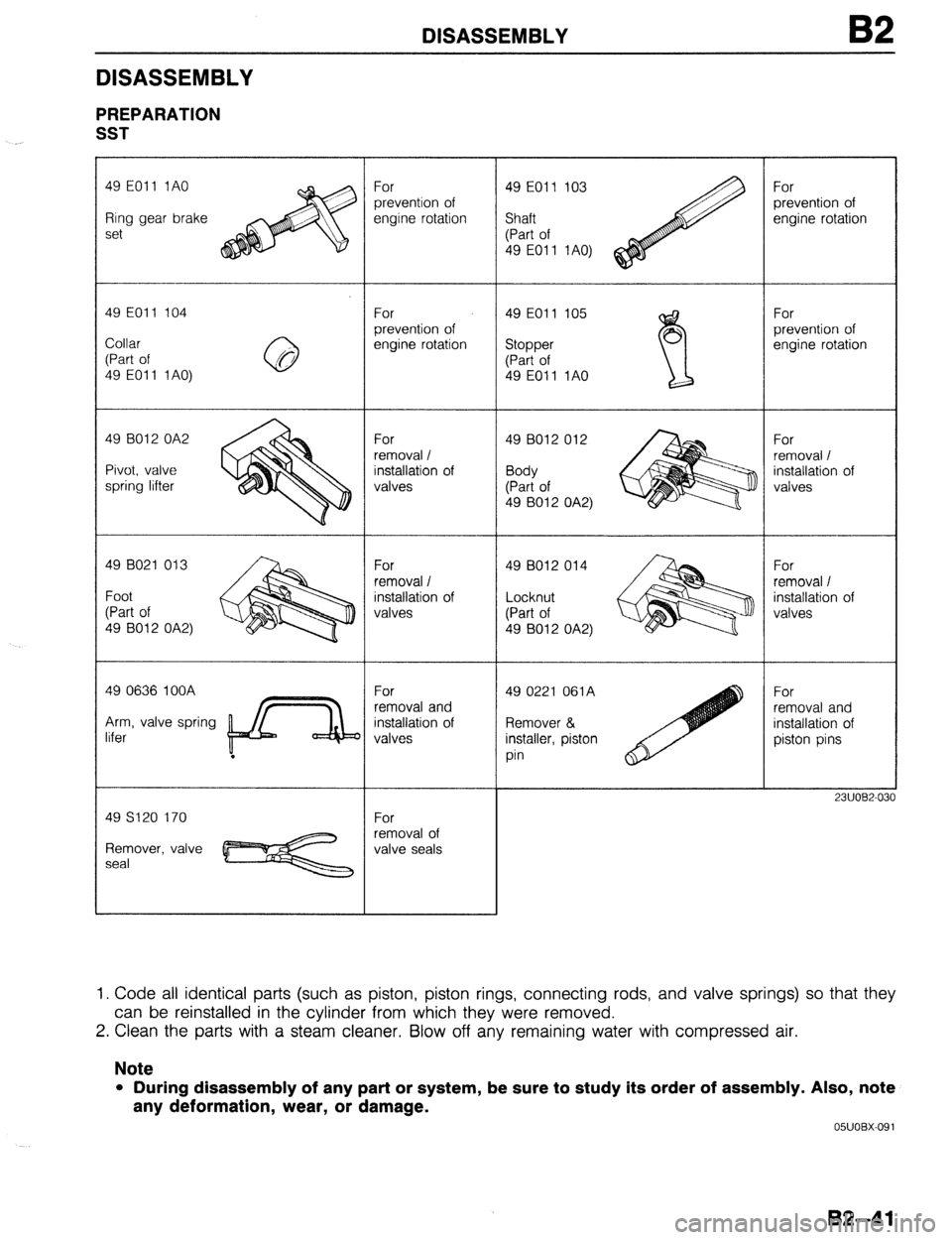
DISASSEMBLY B2
DISASSEMBLY
PREPARATION
SST
._
49 EOll 1AO
Ring gear brake
set
49 EOll 104
Collar
(Part of
49 EOI 1 1 AO)
49 8012 OA2
Pivot, valve
spring lifter
49 B021 013
Foot
(Part of
49 B012 OA2)
49 0636 IOOA
Arm, valve spring
lifer
.
Remover, valve
seal For
prevention of
engine rotation
For
prevention of
engine rotation
For
removal /
installation of
valves
For
removal /
installation of
valves
For
removal and
installation of
valves
For
removal of
valve seals 49 EOll 103
Shaft
(Part of
49 EOll 1AO)
49 EOll 105 49 EOll 105
Stopper Stopper 0
(Part of (Part of
49 E011 1AO 49 E011 1AO
w
49 B012 012
Body
(Part of
49 8012 OA2)
49 8012 014
Locknut
(Part of
49 8012 OA2)
49 0221 061A
Remover &
installer, piston
pin For
prevention of
engine rotation
For
prevention of
engine rotation
For
removal /
installation of
valves
For
removal /
installation of
valves
For
removal and
installation of
piston pins
2311082.03
1. Code all identical parts (such as piston, piston rings, connecting rods, and valve springs) so that they
can be reinstalled in the cylinder from which they were removed.
2. Clean the parts with a steam cleaner. Blow off any remaining water with compressed air.
Note
l During disassembly of any part or system, be sure to study its order of assembly. Also, note
any deformation, wear, or damage.
05UOBX-091
B2-41
Page 174 of 1164
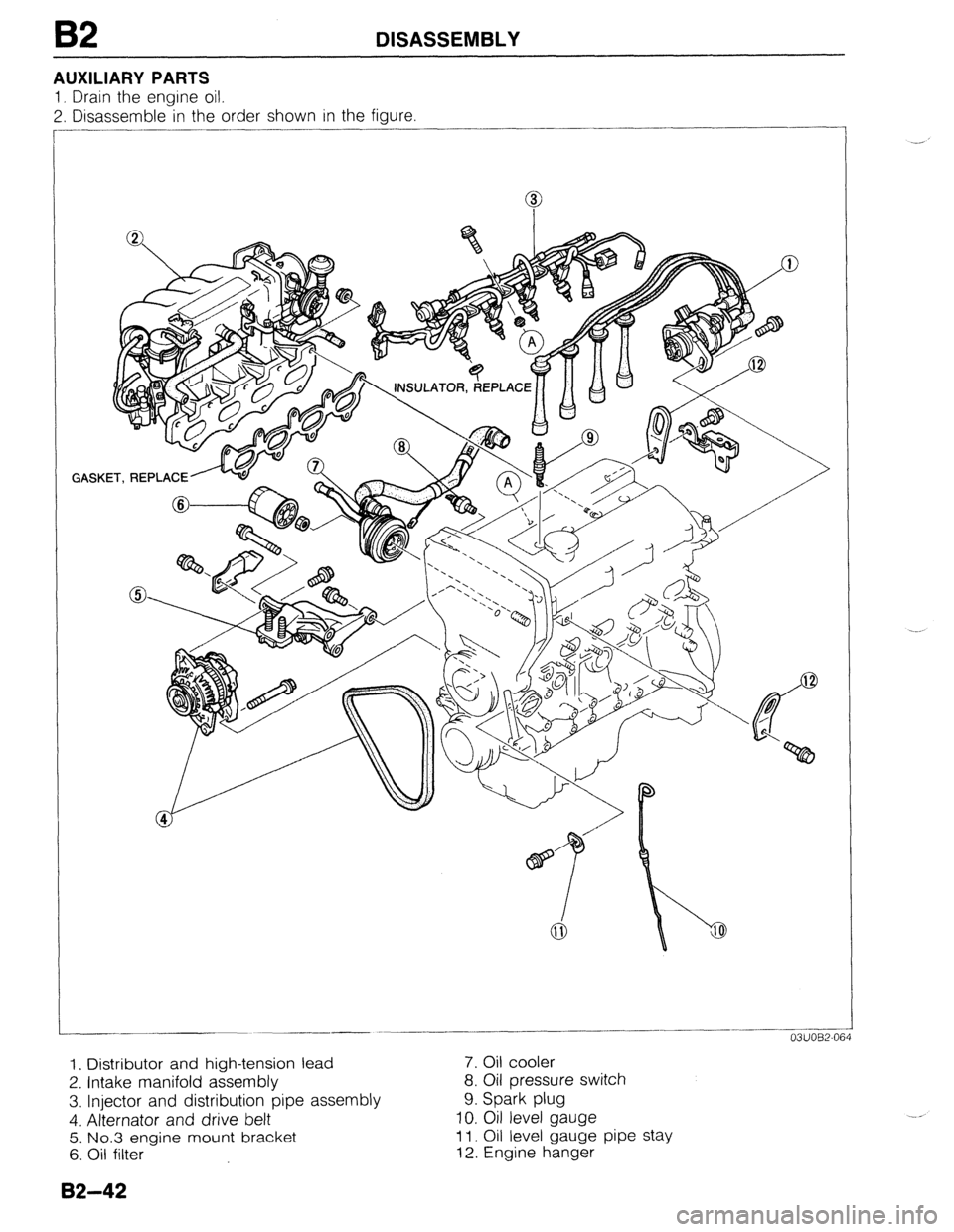
B2 DISASSEMBLY
AUXILIARY PARTS
1, Drain the engine oil.
2. Disassemble in the order shown in the figure
GASKET, REPLACE ..______-.
-___ -
03UOB2-064
1. Distributor and high-tension lead 7. Oil cooler
2. Intake manifold assembly 8. Oil pressure switch
3. Injector and distribution pipe assembly 9. Spark plug
4. Alternator and drive belt 10. Oil level gauge
5. No.3 engine mount bracket 11. Oil level gauge pipe stay
6. Oil filter 12. Engine hanger
82-42
Page 198 of 1164
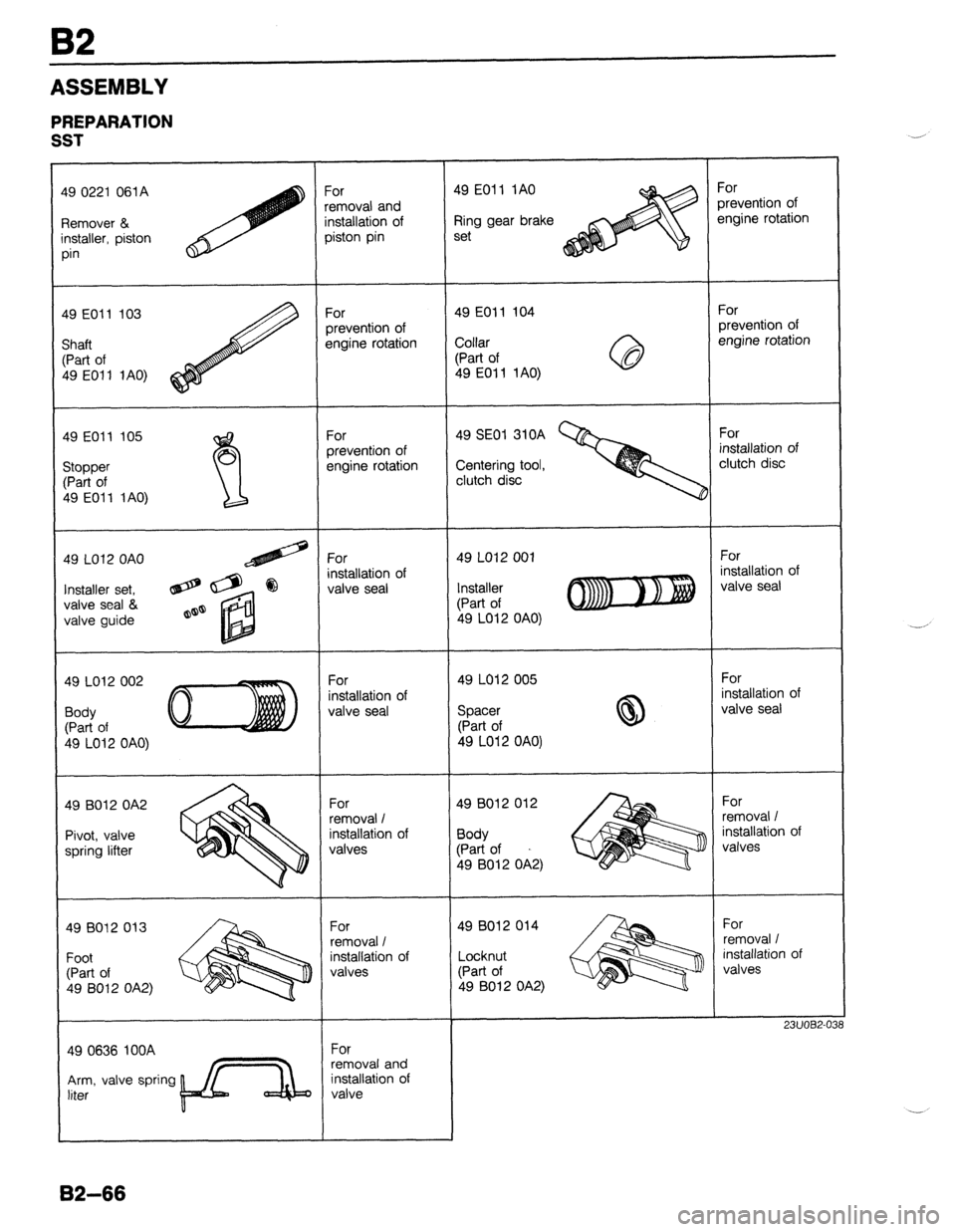
B2
ASSEMBLY
PREPARATION
SST
For
xevention of
sngine rotation For
removal and
installation of
piston pin 49 EOII IA0
Ring gear brake
set 49 0221 061A
Remover &
installer, piston
pin
For
prevention of
engine rotation For
prevention of
engine rotation 49 EOll 104
Collar
(Part of
49 EOl 1 1 AO) 49 E011 103
Shaft
(Part of
49 E011 iA0)
For
installation of
clutch disc For
prevention of
engine rotation 49 EOll 105 49 EOll 105
49 SE01 310A
Centering tool,
clutch disc Stopper Stopper
(Part of (Part of
49 EOI 1 1 AO) 49 EOI 1 1 AO)
49 LO12 OAO
For
nstallation of
valve seal For
installation of
valve seal 49 LO12 001
Installer set, @@ @
valve seal &
valve guide a@ Installer
(Part of
49 LO12 OAO)
49 LO12 005
Spacer
(Part of
49 LO12 OAO) For
installation of
valve seal For
installation of
valve seal 49 LO12 002
Body
(Part of
b9 LO12 OAO)
For
removal I
installation of
valves 49 B012 012
Body
(Part of
49 9012 OA2) For
removal /
installation of
valves 49 8012 OA2
Pivot, valve
spring lifter
For
removal I
‘nstallation of
valves For
removal I
installation of
valves 49 B012 014
-ocknut
:Part of
49 B012 OA2) 49 8012 013
Foot
(Part of
49 8012 OA2)
23UOEi2-0:
For
removal and
installation of
valve 49 0636 IOOA
Arm, valve spring
liter
82-66
Page 199 of 1164
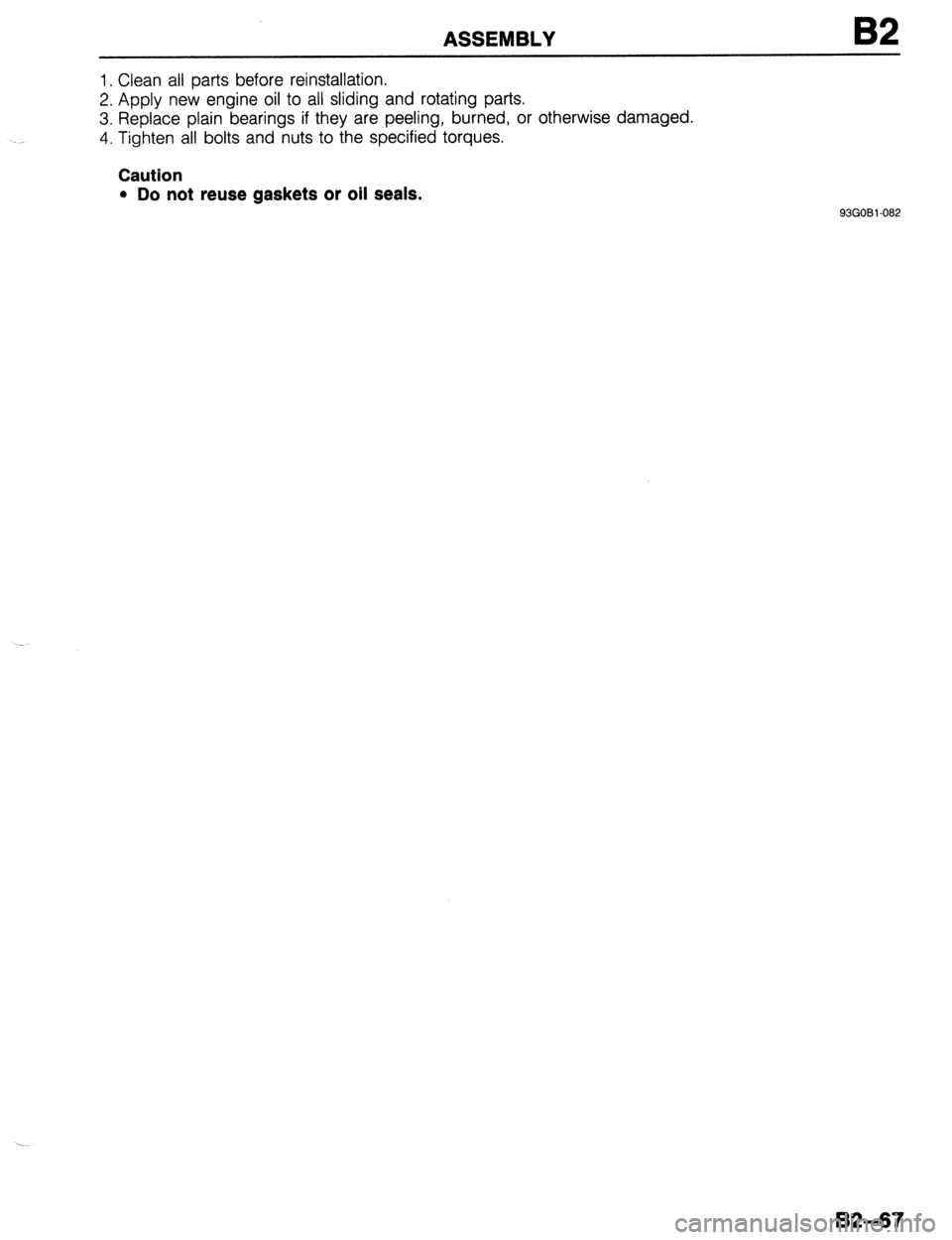
ASSEMBLY B2
1. Clean all parts before reinstallation.
2. Apply new engine oil to all sliding and rotating parts.
3. Replace plain bearings if they are peeling, burned, or otherwise damaged.
4. Tighten all bolts and nuts to the specified torques.
Caution
l Do not reuse gaskets or oil seals.
93GOBl-082
B2-67
Page 200 of 1164
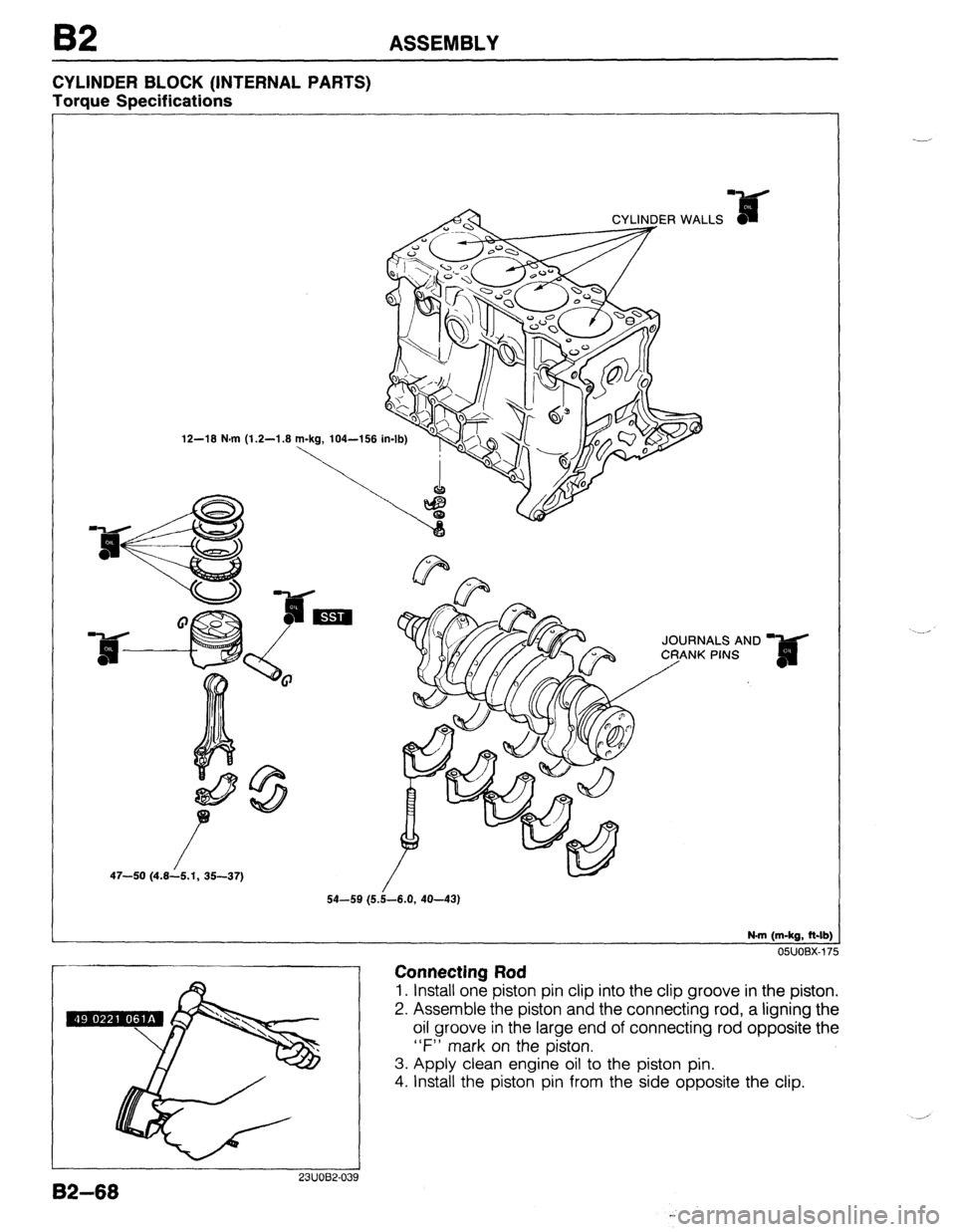
B2 ASSEMBLY
CYLINDER BLOCK (INTERNAL PARTS)
Torque Specifications
12-18 N.m (1.2-1.8
JOURNALS AND
47-50 (4.8--/6.1, 35-37)
N-m (m-kg, ft-lb)
Connecting Rod
o5uoBx-175
1. Install one piston pin clip into the clip groove in the piston.
2. Assemble the piston and the connecting rod, a ligning the
oil groove in the large end of connecting rod opposite the
“F” mark on the piston.
3. Apply clean engine oil to the piston pin.
4. Install the piston pin from the side opposite the clip.
I 23uor32.039
82-68
Page 201 of 1164
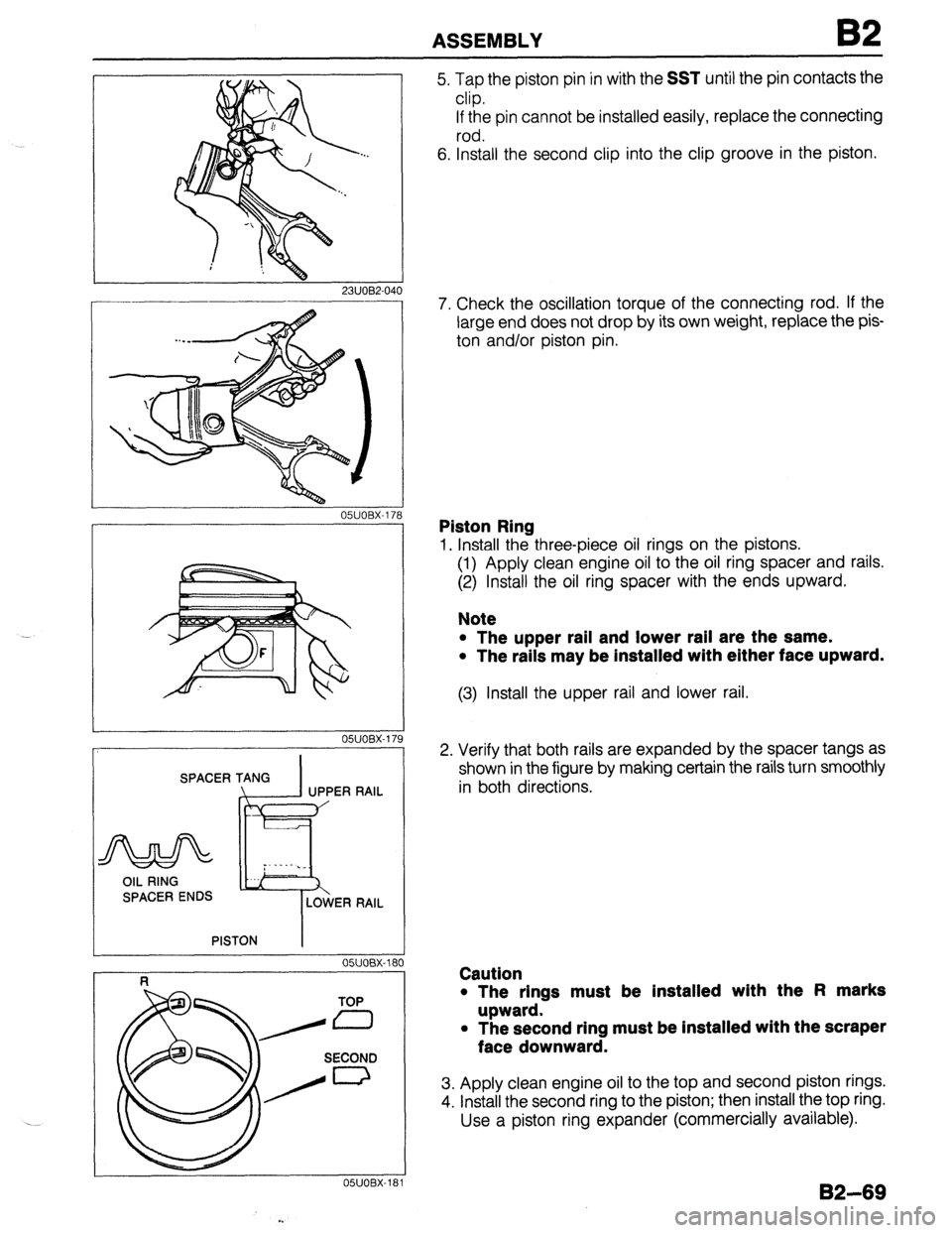
ASSEMBLY
2311082-04
05UOBX-17
OSUOBX-17
SPACER TANG
OIL RING
SPACER ENDS
-I
a
5. Tap the piston pin in with the SST until the pin contacts the
clip.
If the pin cannot be installed easily, replace the connecting
rod.
6. Install the second clip into the clip groove in the piston.
7. Check the oscillation torque of the connecting rod. If the
large end does not drop by its own weight, replace the pis-
ton and/or piston pin.
Piston Ring
1. Install the three-piece oil rings on the pistons.
(1) Apply clean engine oil to the oil ring spacer and rails.
(2) Install the oil ring spacer with the ends upward.
Note
l The upper rail and lower rail are the same.
l The rails may be installed with either face upward.
(3) Install the upper rail and lower rail.
2. Verify that both rails are expanded by the spacer tangs as
shown in the figure by making certain the rails turn smoothly
in both directions.
Caution
l The rings must be installed with the Fl marks
upward.
l The second ring must be installed with the scraper
face downward.
3. Apply clean engine oil to the top and second piston rings.
4. install the second ring to the piston; then install the top ring.
Use a piston ring expander (commercially available).
132-69
Page 203 of 1164
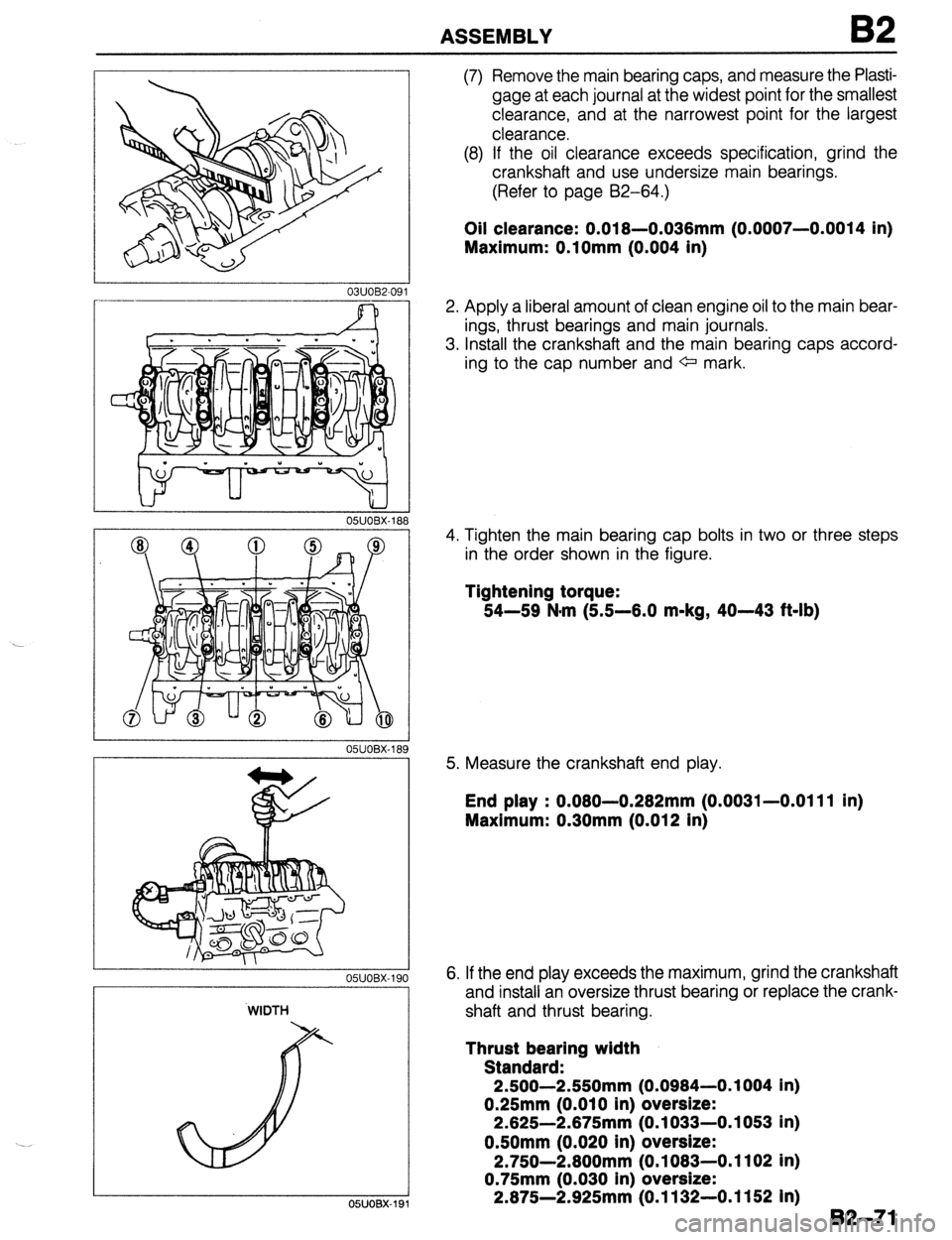
ASSEMBLY B2
r
03UOB2-09
__~~
05UOBX-188
.
OWOBX-19(
WIDTH
I
05UOBX-19
(7) Remove the main bearing caps, and measure the Plasti-
gage at each journal at the widest point for the smallest
clearance, and at the narrowest point for the largest
clearance.
(8) If the oil clearance exceeds specification, grind the
crankshaft and use undersize main bearings.
(Refer to page B2-64.)
Oil clearance: 0.018-0.036mm (0.0007-0.0014 in)
Maximum: O.lOmm (0.004 in)
2. Apply a liberal amount of clean engine oil to the main bear-
ings, thrust bearings and main journals.
3. Install the crankshaft and the main bearing caps accord-
ing to the cap number and C= mark.
4. Tighten the main bearing cap bolts in two or three steps
in the order shown in the figure.
Tightening torque:
54-59 N*m (5.5-6.0 m-kg, 40-43 ft-lb)
5. Measure the crankshaft end play.
End play : 0.080-0.282mm (0.0031-0.0111 in)
Maximum: 0.30mm (0.012 in)
6. If the end play exceeds the maximum, grind the crankshaft
and install an oversize thrust bearing or replace the crank-
shaft and thrust bearing.
Thrust bearlng width
Standard:
2.500-2.550mm (0.0984-0.1004 in)
0.25mm (0.010 in) oversize:
2.625-2.675mm (0.1033-0.1053 in)
0.50mm (0.020 in) oversize:
2.750-2.800mm (0.1083-0.1102 in)
0.75mm (0.030 in) oversize:
2.875-2.925mm (0.1132-0.1152 In)
B2-71
Page 204 of 1164
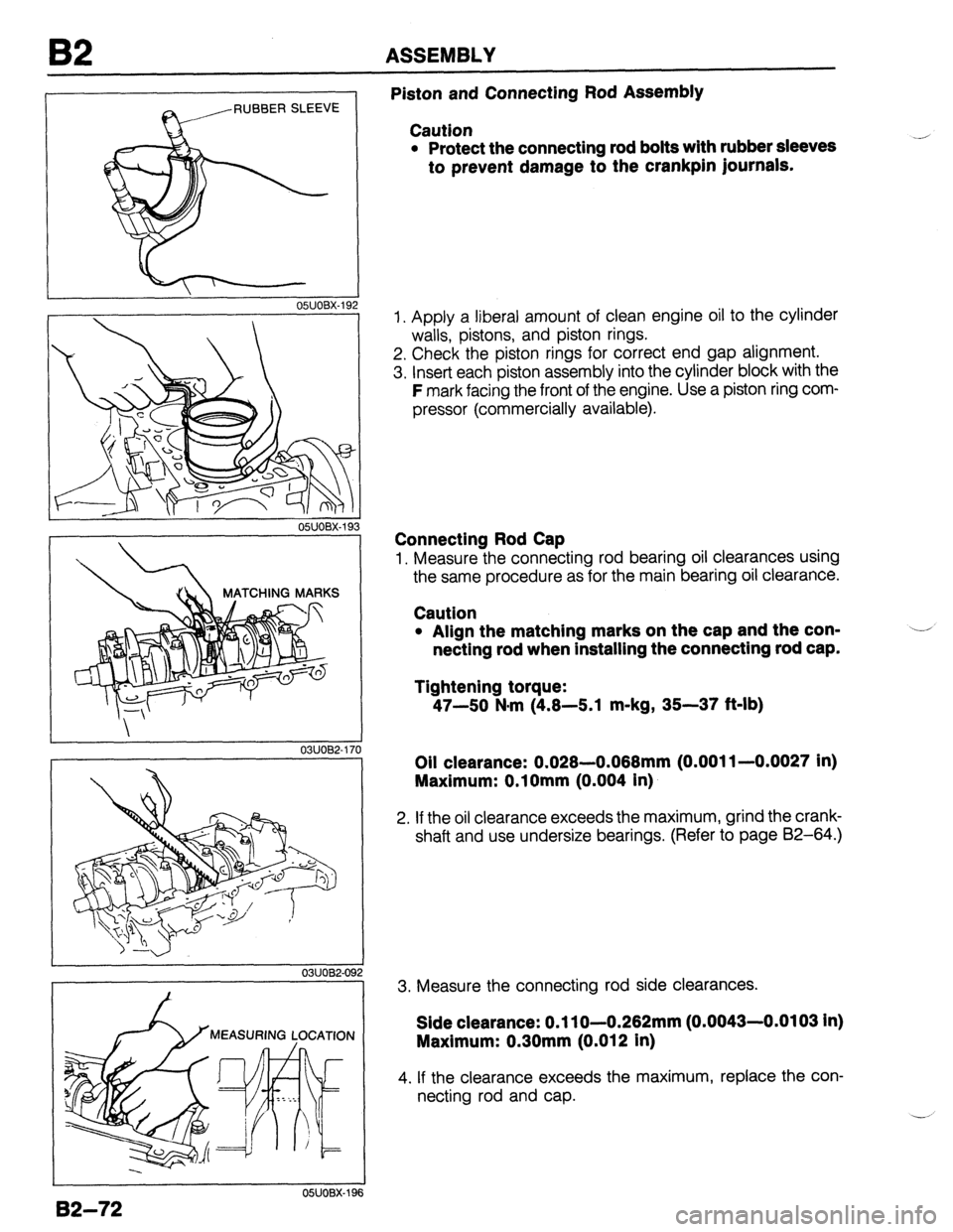
B2 ASSEMBLY
RUBBER SLEEVE
I
OYJOBX-192
03UOB2-17
03UOB2-09 2 '0
05UOBX-196 Piston and Connecting Rod Assembly
Caution
l Protect the connecting rod bolts with rubber sleeves
to prevent damage to the crankpin journals.
1. Apply a liberal amount of clean engine oil to the cylinder
walls, pistons, and piston rings.
2. Check the piston rings for correct end gap alignment.
3. Insert each piston assembly into the cylinder block with the
F mark facing the front of the engine. Use a piston ring com-
pressor (commercially available).
Connecting Rod Cap
1. Measure the connecting rod bearing oil clearances using
the same procedure as for the main bearing oil clearance.
Caution
l Align the matching marks on the cap and the con-
netting rod when installing the connecting rod cap.
Tightening torque:
47-50 N-m (4.8-5.1 m-kg, 35-37 &lb)
Oil clearance: 0.028.0.088mm (0.001 l-0.0027 in)
Maximum: O.lOmm (0.004 in)
2. If the oil clearance exceeds the maximum, grind the crank-
shaft and use undersize bearings. (Refer to page 82-64.)
3. Measure the connecting rod side clearances.
Side clearance: 0.1 lo-0.282mm (0.0043-0.0103 in)
Maximum: 0.30mm (0.012 in)
4. If the clearance exceeds the maximum, replace the con-
necting rod and cap.
Page 205 of 1164
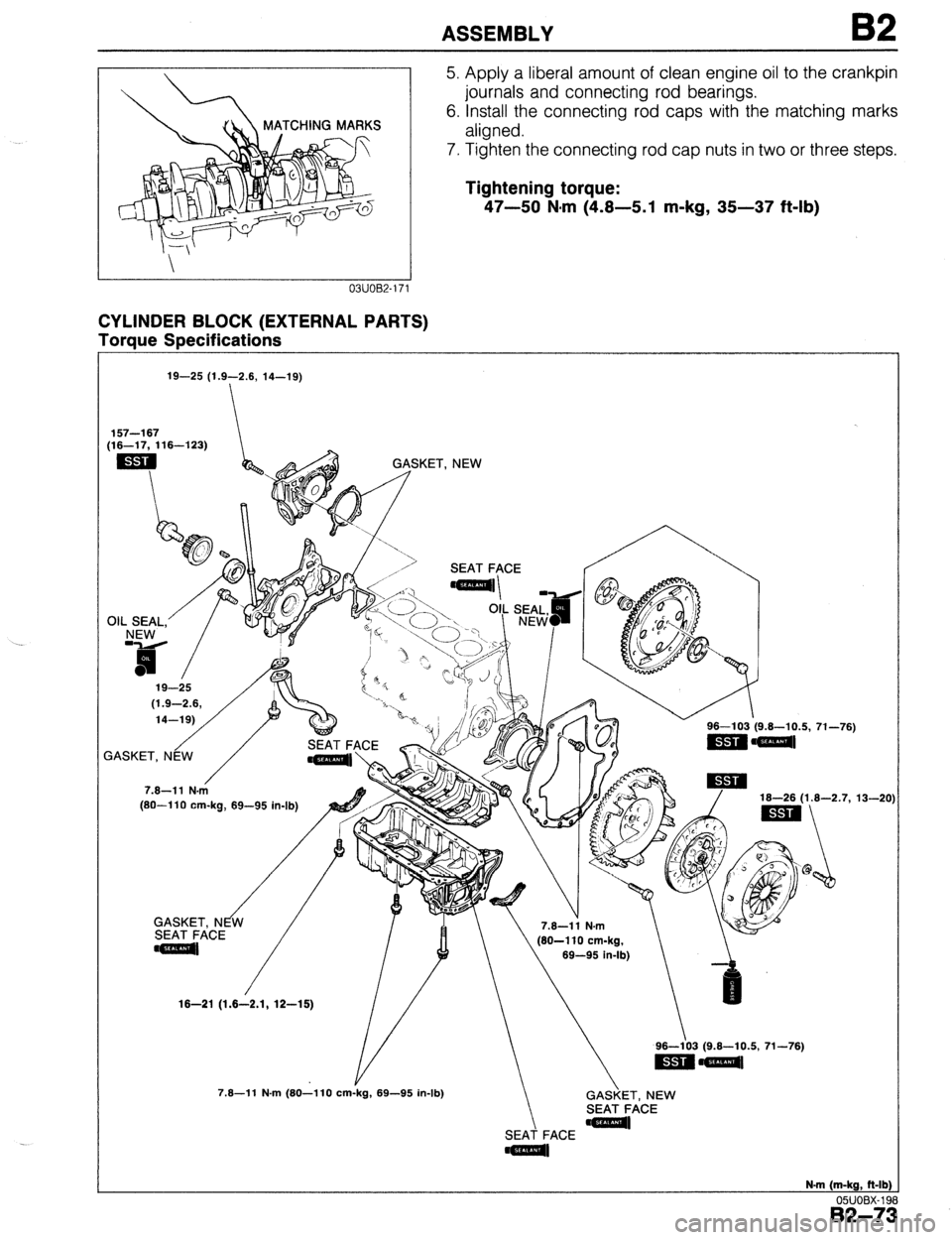
ASSEMBLY B2
MATCHING MARKS
CYLINDER BLOCK (EXTERNAL PARTS)
Toraue SPecifications 5. Apply a liberal amount of clean engine oil to the crankpin
journals and connecting rod bearings.
6. Install the connecting rod caps with the matching marks
aligned.
7. Tighten the connecting rod cap nuts in two or three steps.
Tightening torque:
47-50 N*m (4.8-5.1 m-kg, 35-37 ft-lb)
19-25 (1.9-2.6, 14-19)
157-l 67
(16-17, 116-1’23)
OIL SEAL.’
/ GASKET. NEW
[SO--110 cm-ka. 69-95 in-lb) 16-26 (1.6-2.7,
13-20
16-21
(1.6-2.1, 12-16)
GASKET, NEW
SEAT FACE
SEAT FACE
N-m (m-kg, ft-lb)
05UOBX-19
B2-7: