ECU MITSUBISHI ECLIPSE 1990 User Guide
[x] Cancel search | Manufacturer: MITSUBISHI, Model Year: 1990, Model line: ECLIPSE, Model: MITSUBISHI ECLIPSE 1990Pages: 391, PDF Size: 15.27 MB
Page 200 of 391
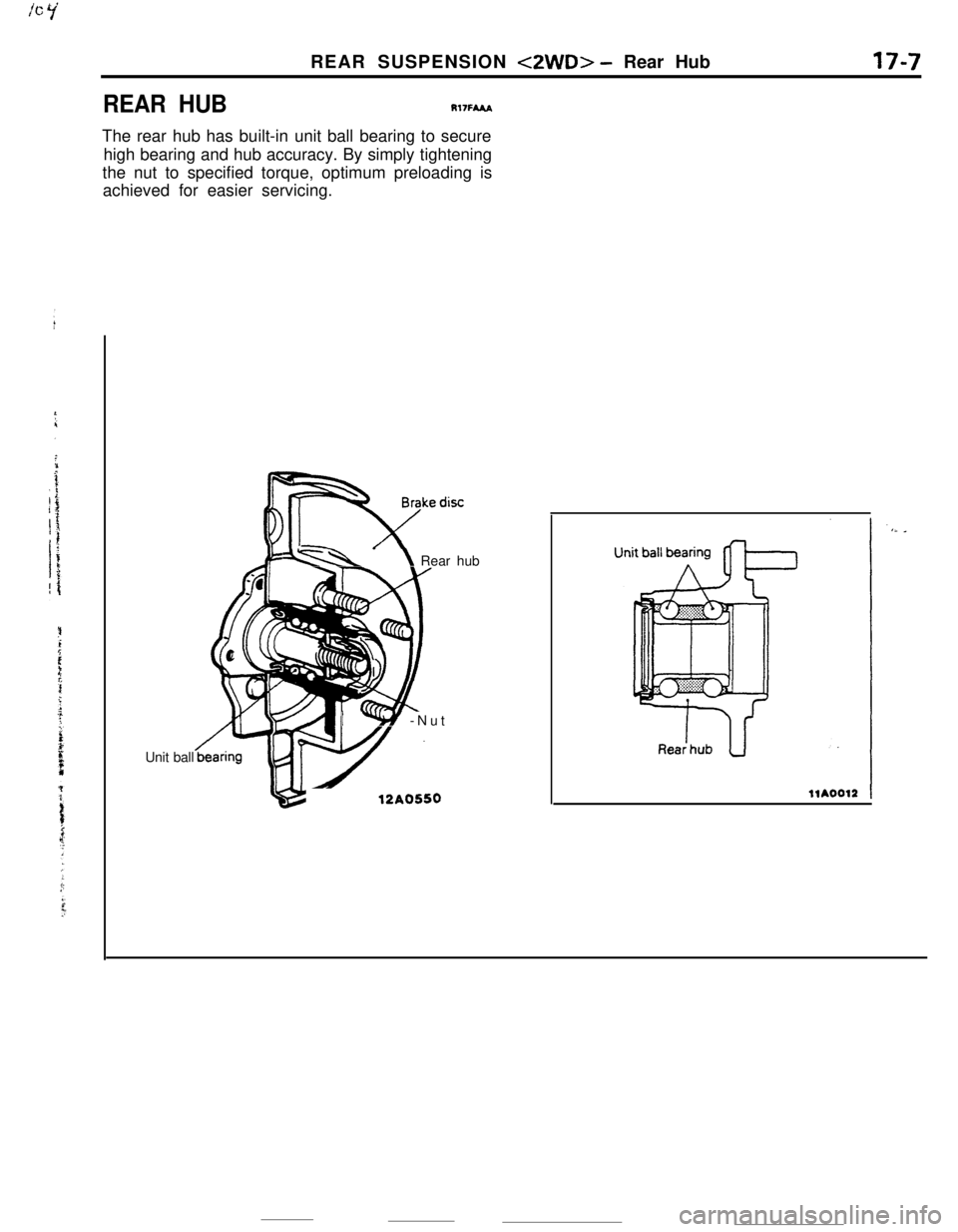
/cY
REAR HUBREAR SUSPENSION
<2WD> - Rear Hub
Rl7FMA
17-7The rear hub has built-in unit ball bearing to secure
high bearing and hub accuracy. By simply tightening
the nut to specified torque, optimum preloading is
achieved for easier servicing.
Unit ball
a -\ Rear hub
/‘YLLY -Nut
12A0550
Page 205 of 391
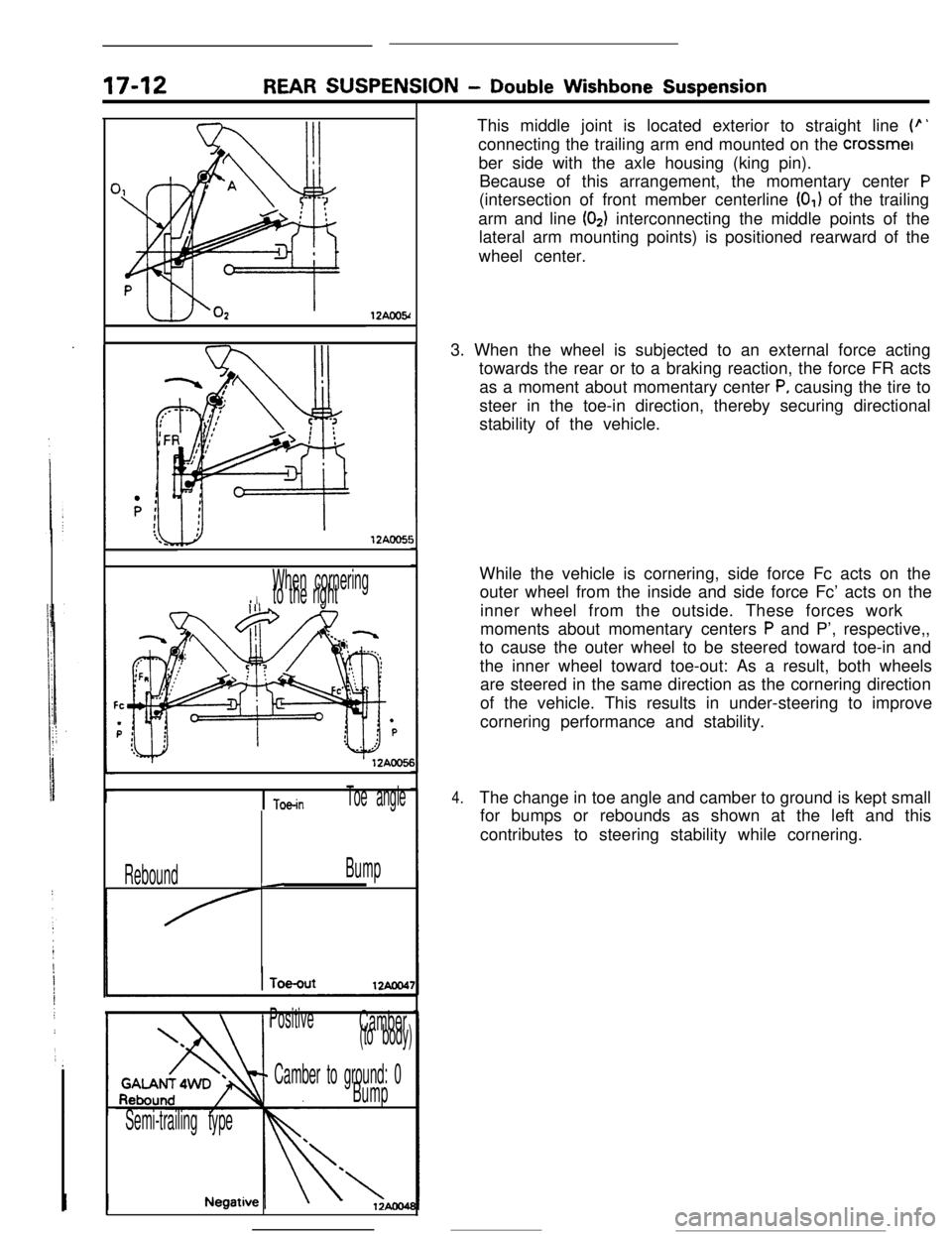
17-12REAR SUSPENSION - Double Wishbone Suspension
12AWY
lZAOOS!
When cornering. I.to the right
I Toe-inToe angle
ReboundBump-
PositiveCamber(to body)
- Camber to ground: 0
Bump
Semi-trailing typeThis middle joint is located exterior to straight line
(p’connecting the trailing arm end mounted on the crossmet
ber side with the axle housing (king pin).
Because of this arrangement, the momentary center
P(intersection of front member centerline
(0,) of the trailing
arm and line
(02) interconnecting the middle points of the
lateral arm mounting points) is positioned rearward of the
wheel center.
3. When the wheel is subjected to an external force acting
towards the rear or to a braking reaction, the force FR acts
as a moment about momentary center
P, causing the tire to
steer in the toe-in direction, thereby securing directional
stability of the vehicle.
While the vehicle is cornering, side force Fc acts on the
outer wheel from the inside and side force Fc’ acts on the
inner wheel from the outside. These forces work
moments about momentary centers
P and P’, respective,,
to cause the outer wheel to be steered toward toe-in and
the inner wheel toward toe-out: As a result, both wheels
are steered in the same direction as the cornering direction
of the vehicle. This results in under-steering to improve
cornering performance and stability.
4.The change in toe angle and camber to ground is kept small
for bumps or rebounds as shown at the left and this
contributes to steering stability while cornering.
Page 213 of 391
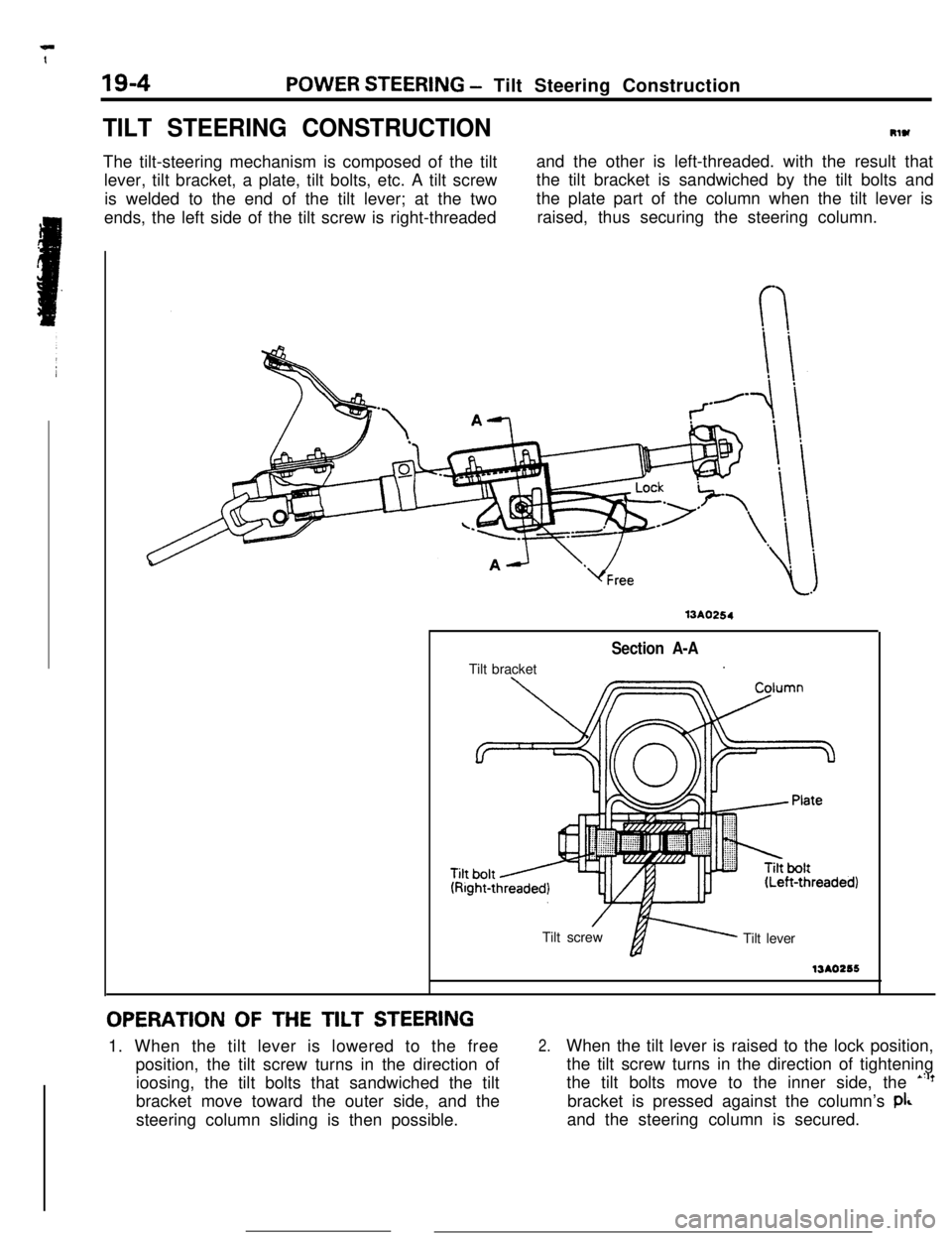
19-4POWER STEERING - Tilt Steering Construction
TILT STEERING CONSTRUCTIONRlW
The tilt-steering mechanism is composed of the tilt
lever, tilt bracket, a plate, tilt bolts, etc. A tilt screw
is welded to the end of the tilt lever; at the two
ends, the left side of the tilt screw is right-threadedand the other is left-threaded. with the result that
the tilt bracket is sandwiched by the tilt bolts and
the plate part of the column when the tilt lever is
raised, thus securing the steering column.
13A0254Tilt bracket
Section A-A.
’Tilt screwfi Tilt lever13AO256
OPERATION OF THE TILT STEERING1. When the tilt lever is lowered to the free
position, the tilt screw turns in the direction of
ioosing, the tilt bolts that sandwiched the tilt
bracket move toward the outer side, and the
steering column sliding is then possible.
2.When the tilt lever is raised to the lock position,
the tilt screw turns in the direction of tightening
the tilt bolts move to the inner side, the
*“?bracket is pressed against the column’s
pi&and the steering column is secured.
Page 215 of 391
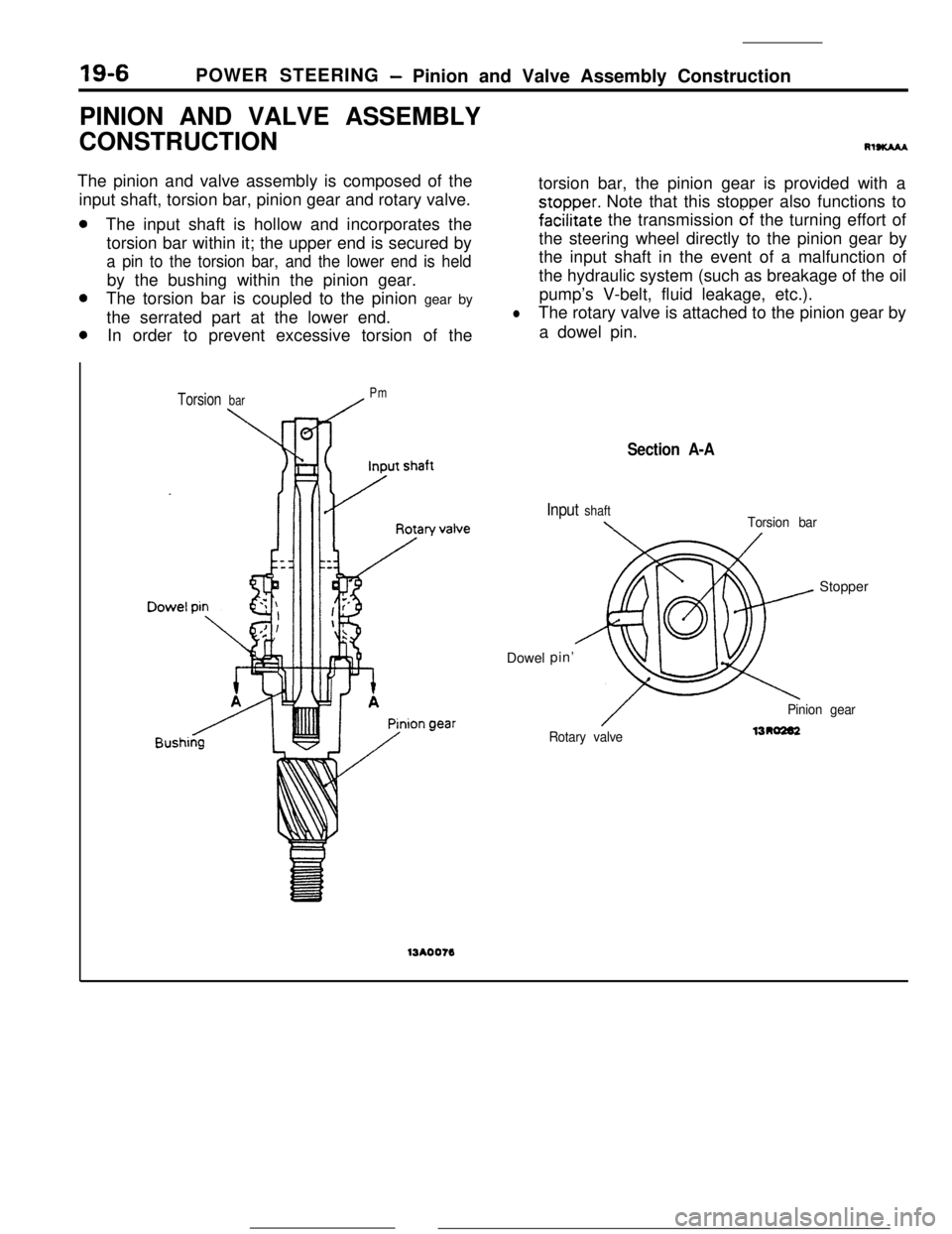
19-6POWER STEERING- Pinion and Valve Assembly Construction
PINION AND VALVE ASSEMBLY
CONSTRUCTION
RISKAMThe pinion and valve assembly is composed of the
input shaft, torsion bar, pinion gear and rotary valve.torsion bar, the pinion gear is provided with a
stopper. Note that this stopper also functions to
The input shaft is hollow and incorporates the
fa&tate the transmission 6i the turning effort of
torsion bar within it; the upper end is secured bythe steering wheel directly to the pinion gear by
a pin to the torsion bar, and the lower end is heldthe input shaft in the event of a malfunction of
by the bushing within the pinion gear.the hydraulic system (such as breakage of the oil
The torsion bar is coupled to the pinion gear bypump’s V-belt, fluid leakage, etc.).
the serrated part at the lower end.
lThe rotary valve is attached to the pinion gear by
In order to prevent excessive torsion of thea dowel pin.
Torsion barPm13AOO76Dowel
Section A-A
Input shaft\Torsion barpin’Stopper
/Rotary valvePinion gear1310202
Page 233 of 391
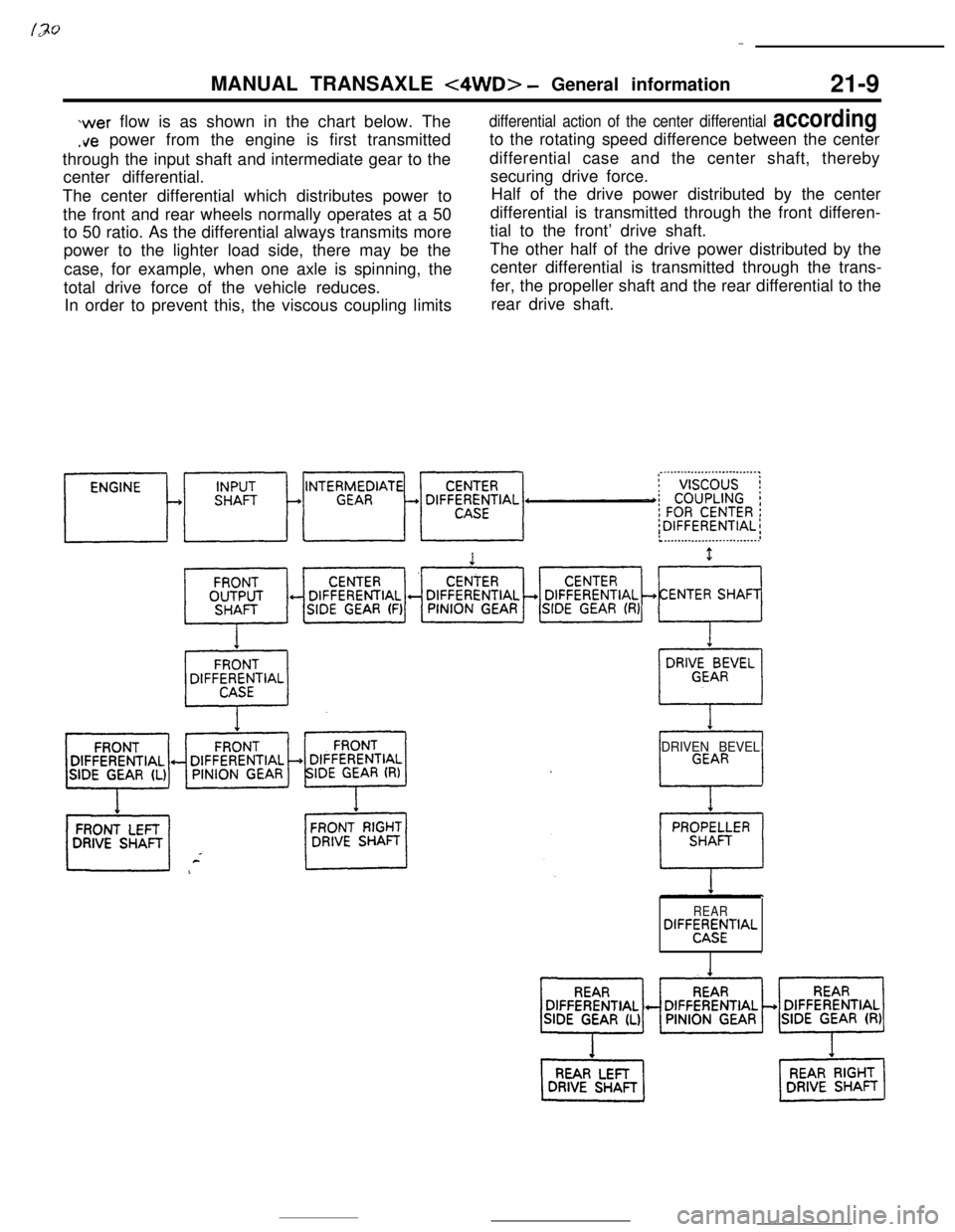
-MANUAL TRANSAXLE
<4WD> - General information
21-9
wer flow is as shown in the chart below. The
.ire power from the engine is first transmitted
through the input shaft and intermediate gear to the
center differential.
The center differential which distributes power to
the front and rear wheels normally operates at a 50
to 50 ratio. As the differential always transmits more
power to the lighter load side, there may be the
case, for example, when one axle is spinning, the
total drive force of the vehicle reduces.
In order to prevent this, the viscous coupling limits
differential action of the center differential accordingto the rotating speed difference between the center
differential case and the center shaft, thereby
securing drive force.
Half of the drive power distributed by the center
differential is transmitted through the front differen-
tial to the front’ drive shaft.
The other half of the drive power distributed by the
center differential is transmitted through the trans-
fer, the propeller shaft and the rear differential to the
rear drive shaft.
DRIVEN BEVEL
REARDIFF~;MfTIAL
,
Page 234 of 391
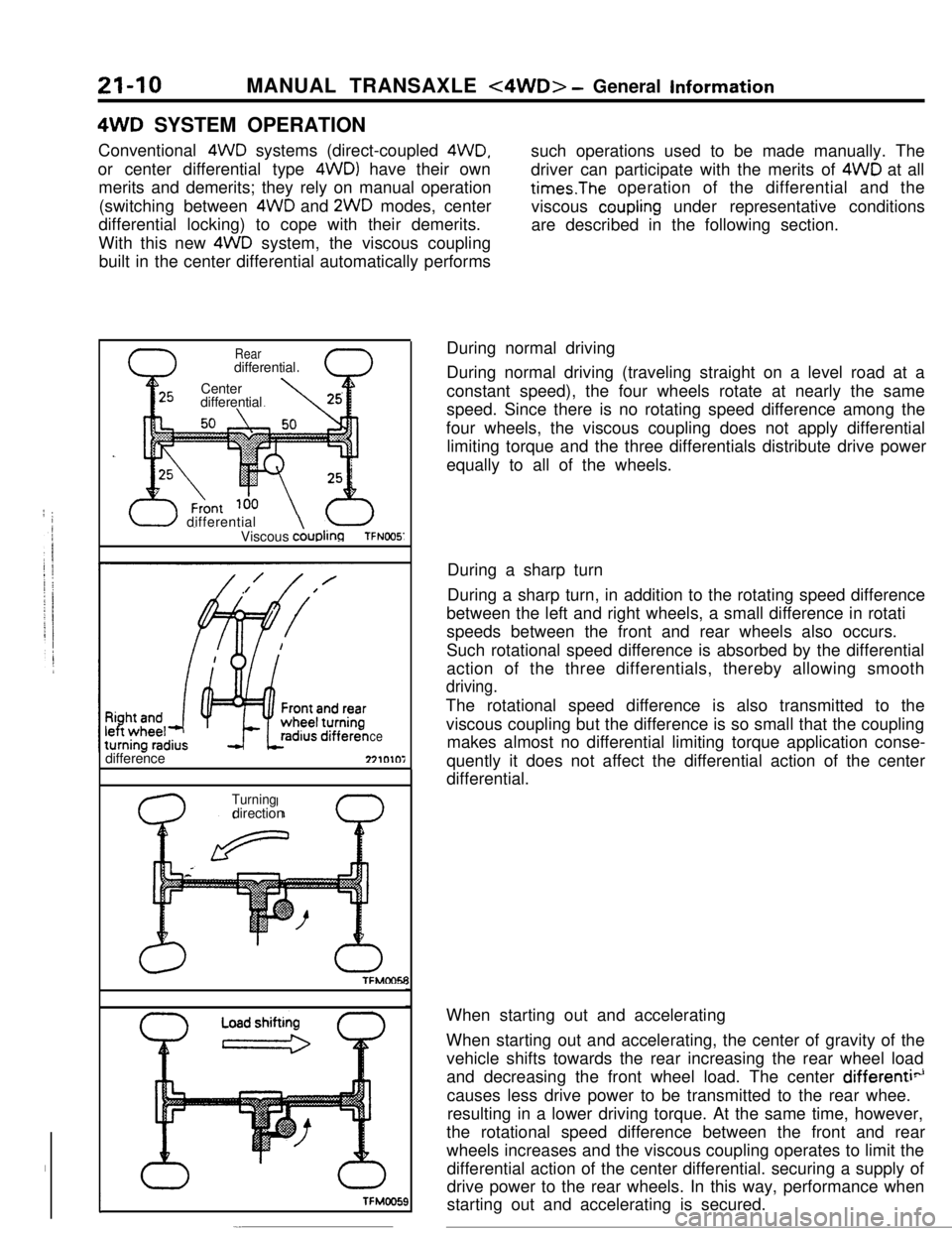
21-10MANUAL TRANSAXLE <4WD> - General Information4WD SYSTEM OPERATION
Conventional 4WD systems (direct-coupled
4WD,or center differential type 4WDl have their own
merits and demerits; they rely on manual operation
(switching between 4WD and 2WD modes, center
differential locking) to cope with their demerits.
With this new 4WD system, the viscous coupling
built in the center differential automatically performssuch operations used to be made manually. The
driver can participate with the merits of 4WD at alltimes.The operation of the differential and the
viscous
coupling under representative conditions
are described in the following section.
I
Reardifferential
Center
differential
U differential
Viscous AuDk?TFNOO5’difference
ce271010i
TFMMYTFMMY
0
Turningdirection
ITFMOO!X
-.During normal driving
During normal driving (traveling straight on a level road at a
constant speed), the four wheels rotate at nearly the same
speed. Since there is no rotating speed difference among the
four wheels, the viscous coupling does not apply differential
limiting torque and the three differentials distribute drive power
equally to all of the wheels.
During a sharp turn
During a sharp turn, in addition to the rotating speed difference
between the left and right wheels, a small difference in rotati
speeds between the front and rear wheels also occurs.
Such rotational speed difference is absorbed by the differential
action of the three differentials, thereby allowing smooth
driving.The rotational speed difference is also transmitted to the
viscous coupling but the difference is so small that the coupling
makes almost no differential limiting torque application conse-
quently it does not affect the differential action of the center
differential.
When starting out and accelerating
When starting out and accelerating, the center of gravity of the
vehicle shifts towards the rear increasing the rear wheel load
and decreasing the front wheel load. The center
differenti”causes less drive power to be transmitted to the rear whee.
resulting in a lower driving torque. At the same time, however,
the rotational speed difference between the front and rear
wheels increases and the viscous coupling operates to limit the
differential action of the center differential. securing a supply of
drive power to the rear wheels. In this way, performance when
starting out and accelerating is secured.
Page 237 of 391
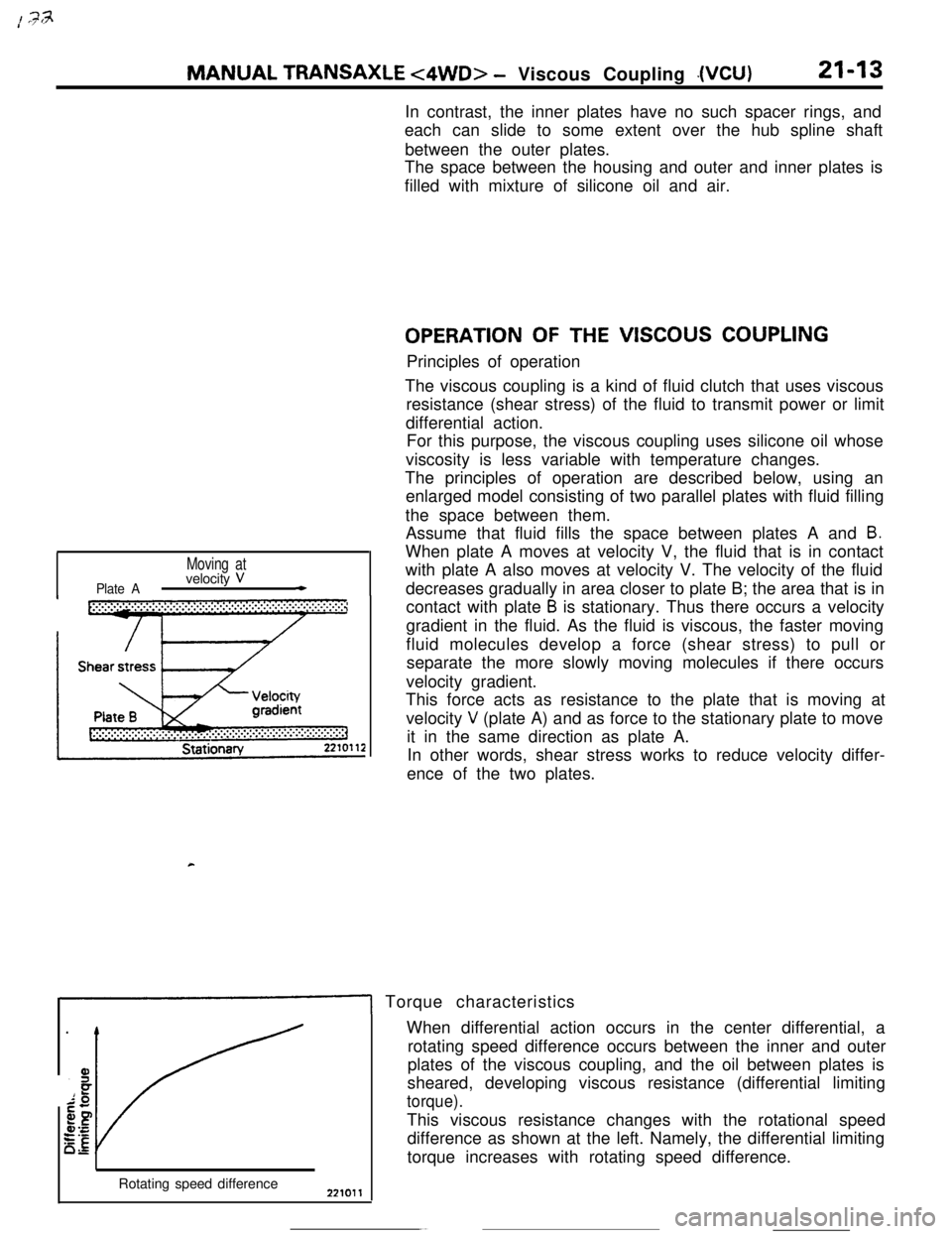
MANUAL TRANSAXLE <4WD> - Viscous Coupling .(VClJ)21-13In contrast, the inner plates have no such spacer rings, and
each can slide to some extent over the hub spline shaft
between the outer plates.
The space between the housing and outer and inner plates is
filled with mixture of silicone oil and air.
Plate A
Moving atvelocity V*
OPERATION OF THE VISCOUS COUPLINGPrinciples of operation
The viscous coupling is a kind of fluid clutch that uses viscous
resistance (shear stress) of the fluid to transmit power or limit
differential action.
For this purpose, the viscous coupling uses silicone oil whose
viscosity is less variable with temperature changes.
The principles of operation are described below, using an
enlarged model consisting of two parallel plates with fluid filling
the space between them.
Assume that fluid fills the space between plates A and
B.When plate A moves at velocity V, the fluid that is in contact
with plate A also moves at velocity V. The velocity of the fluid
decreases gradually in area closer to plate B; the area that is in
contact with plate
B is stationary. Thus there occurs a velocity
gradient in the fluid. As the fluid is viscous, the faster moving
fluid molecules develop a force (shear stress) to pull or
separate the more slowly moving molecules if there occurs
velocity gradient.
This force acts as resistance to the plate that is moving at
velocity
V (plate A) and as force to the stationary plate to move
it in the same direction as plate A.
In other words, shear stress works to reduce velocity differ-
ence of the two plates.
1 Torque characteristics
Rotating speed differenceWhen differential action occurs in the center differential, a
rotating speed difference occurs between the inner and outer
plates of the viscous coupling, and the oil between plates is
sheared, developing viscous resistance (differential limiting
torque).This viscous resistance changes with the rotational speed
difference as shown at the left. Namely, the differential limiting
torque increases with rotating speed difference.
Page 336 of 391
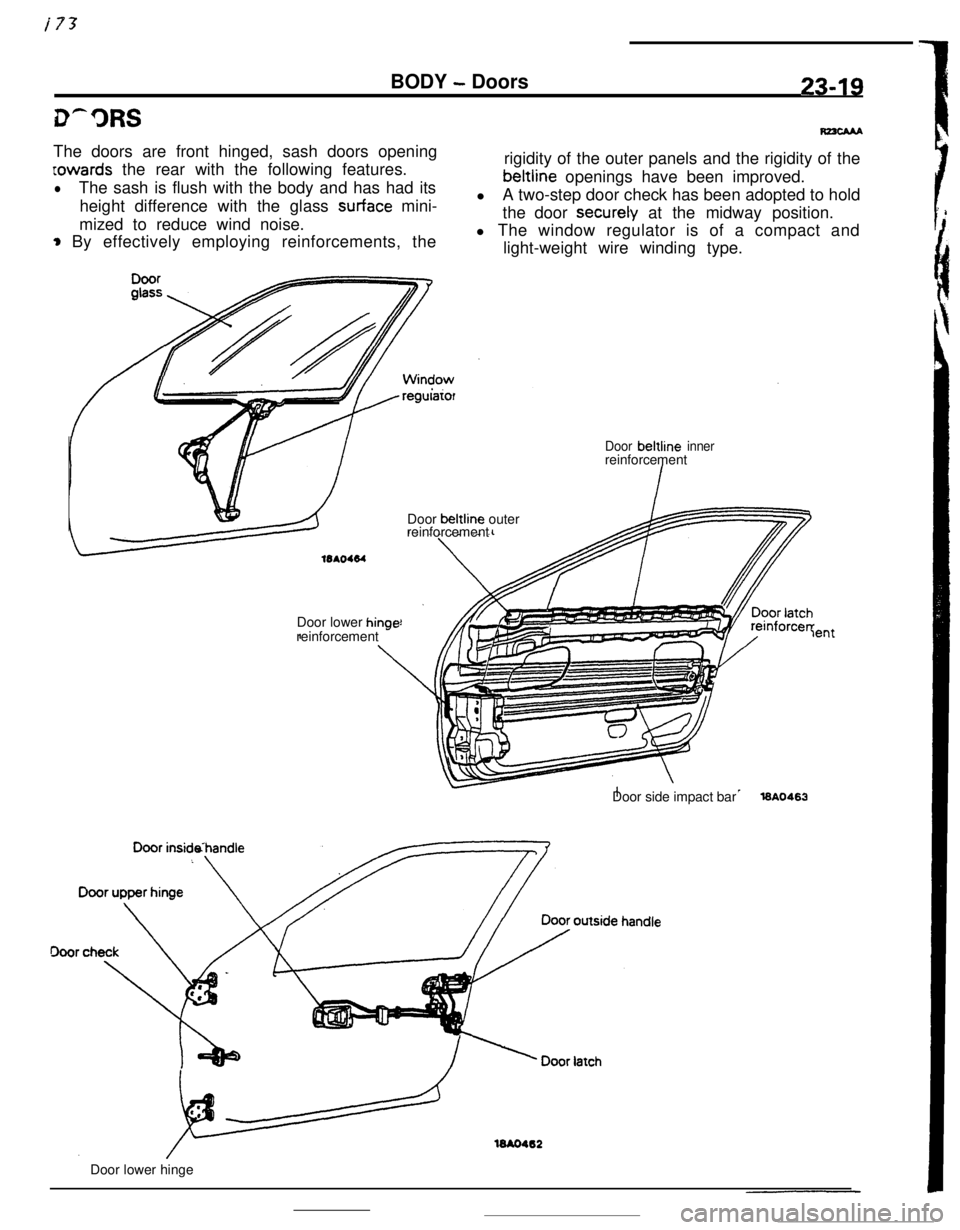
i73BODY
- Doors23-19The doors are front hinged, sash doors opening
Lowards the rear with the following features.
lThe sash is flush with the body and has had its
height difference with the glass
surface mini-
mized to reduce wind noise.
* By effectively employing reinforcements, the
regularorrigidity of the outer panels and the rigidity of thebeltline openings have been improved.
lA two-step door check has been adopted to hold
the door securely at the midway position.
l The window regulator is of a compact and
light-weight wire winding type.
Door beltline innerreinforcement
Door beltline outer
reinforcement
Door lower
hinr-reinforcement *-lentDoor side impact bar
l6A0463
16AO462Door lower hinge