service MITSUBISHI ECLIPSE 1993 Workshop Manual
[x] Cancel search | Manufacturer: MITSUBISHI, Model Year: 1993, Model line: ECLIPSE, Model: MITSUBISHI ECLIPSE 1993Pages: 57, PDF Size: 4.18 MB
Page 2 of 57
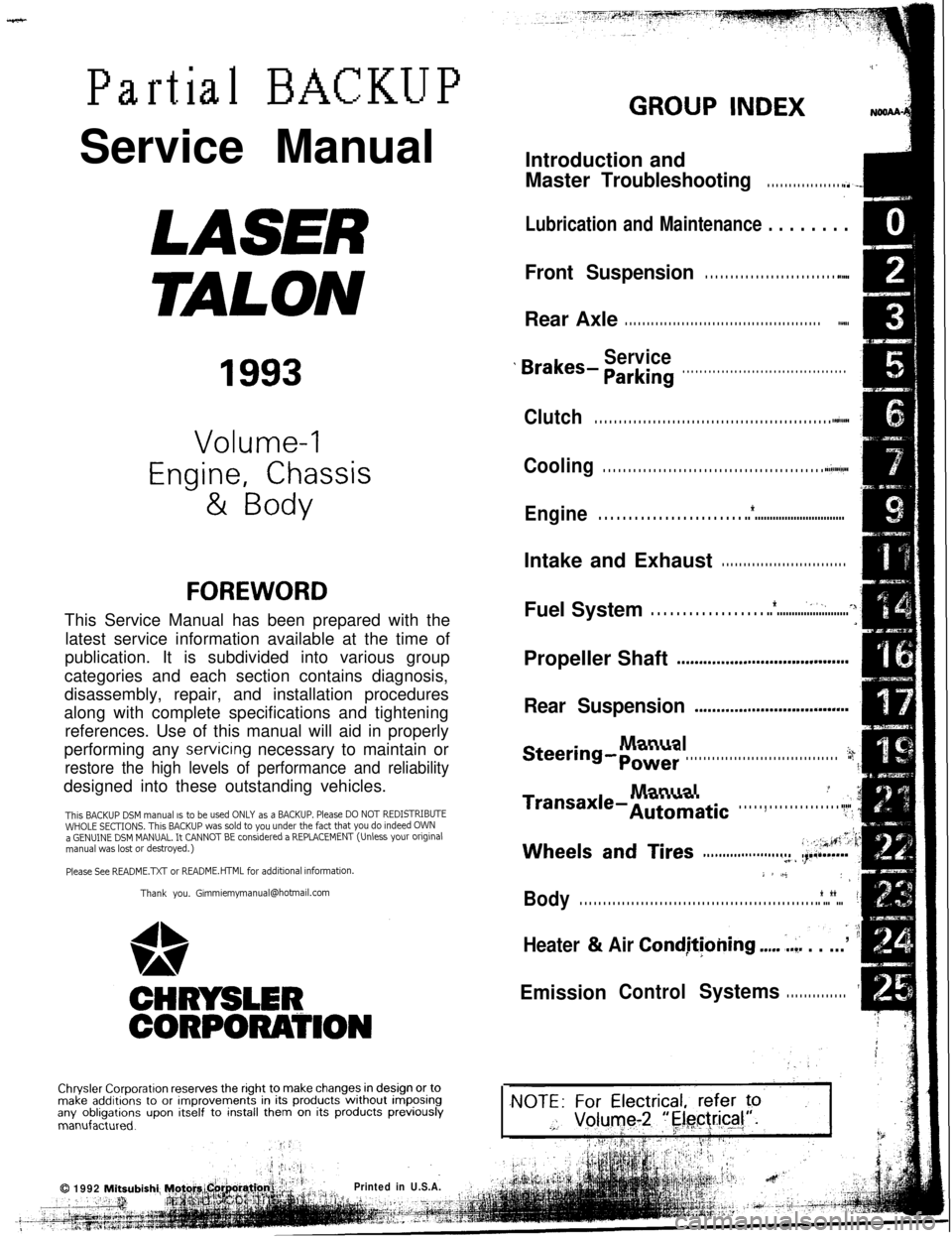
Partial BACKUPService Manual
.i’
GROUP INDEXNOSAl
LASER
TALON
1993
Volume-l
Engine, Chassis& Body
FOREWORDThis Service Manual has been prepared with the
latest service information available at the time of
publication. It is subdivided into various group
categories and each section contains diagnosis,
disassembly, repair, and installation procedures
along with complete specifications and tightening
references. Use of this manual will aid in properly
performing any
servicrng necessary to maintain or
restore the high levels of performance and reliabilitydesigned into these outstanding vehicles.
This BACKUP DSM manual IS to be used ONLY as a BACKUP. Please DO NOT REDISTRIBUTEWHOLE SECTIONS. This BACKUP was sold to you under the fact that you do indeed OWNa GENUINE DSM MANUAL. It CANNOT BE considered a REPLACEMENT (Unless your orlglnalmanual was lost or destroyed.)Please See
README.N or README.HTML for additional Information.
Thank you. G~mm~emymanual@hotma~l.com
CHRYSLER
CORPORATION
Chrysler Corporation reserves the right to make changes in design or tomake additions to or improvements in its products without imposingany obligations upon itself to install them on its products previouslymanufactured.Introduction and
Master
Troubleshooting.-I. . . . . . . . . . . . . . . . . . i
Lubrication and Maintenance . . . . . . . .El
Front Suspension. . . . . . . . . . . . . . . . . . . . . . . . . . . ..A..tiRear Axle
. . . . . . . . . . . . . . . . . . . . . . . . . . . . . . . . . . . . . . . . . . . . . ..~...
Service’ Brakes- Parking. . . . . . . . . . . . . . . . . . . . . . . . . . . . . . . . . . . . . .
Clutch. . . . . . . . . . . . . . . . . . . . . . . . . . . . . . . . . . . . . . . . . . . . . . . . . ..~.....
Cooling. . . . . . . . . . . . . . . . . . . . . . . . . . . . . . . . . . . . . . . . . . . . ..~.....~~..
Engine. . . . . . . . . . . . . . . . . . . . . . . . ..*..............................Intake and Exhaust
. . . . . . . . . . . . . . . . . . . . . . . . . . . . .Fuel System
‘,,, .*. . . . . . . . . . . . . . . . . . ..*........................4Propeller Shaft
..,.....,....,.................m.......
Rear Suspension.*........s........................
ManualSteering-po,er.h. . . . . . . . . . . . . . . . . . . . . . . . . . . . . . . . . . . ..$\
ManualiTransaxle-Automatic:. . . . . , . . . . . . . . . . . . . . r+:,
Wheels and Tires_. .;,:.;*&i. . . . . . . . . . . . . . . . . . . . . . ..&......
j 8 .A$: >
Body. . . . . . . . . . . . . . . . . . . . . . . . . . . . . . . . . . . . . . . . . . . . . . . . . . ..*...**...
Heater & Air CondjtJoning ..,.. ,.,. . . ...’
EmissionControlSystems1. . . . . . . . . . . . . .
0 1992 Mitsubishi)L-.”:
Printed in U.S.A.
Page 3 of 57
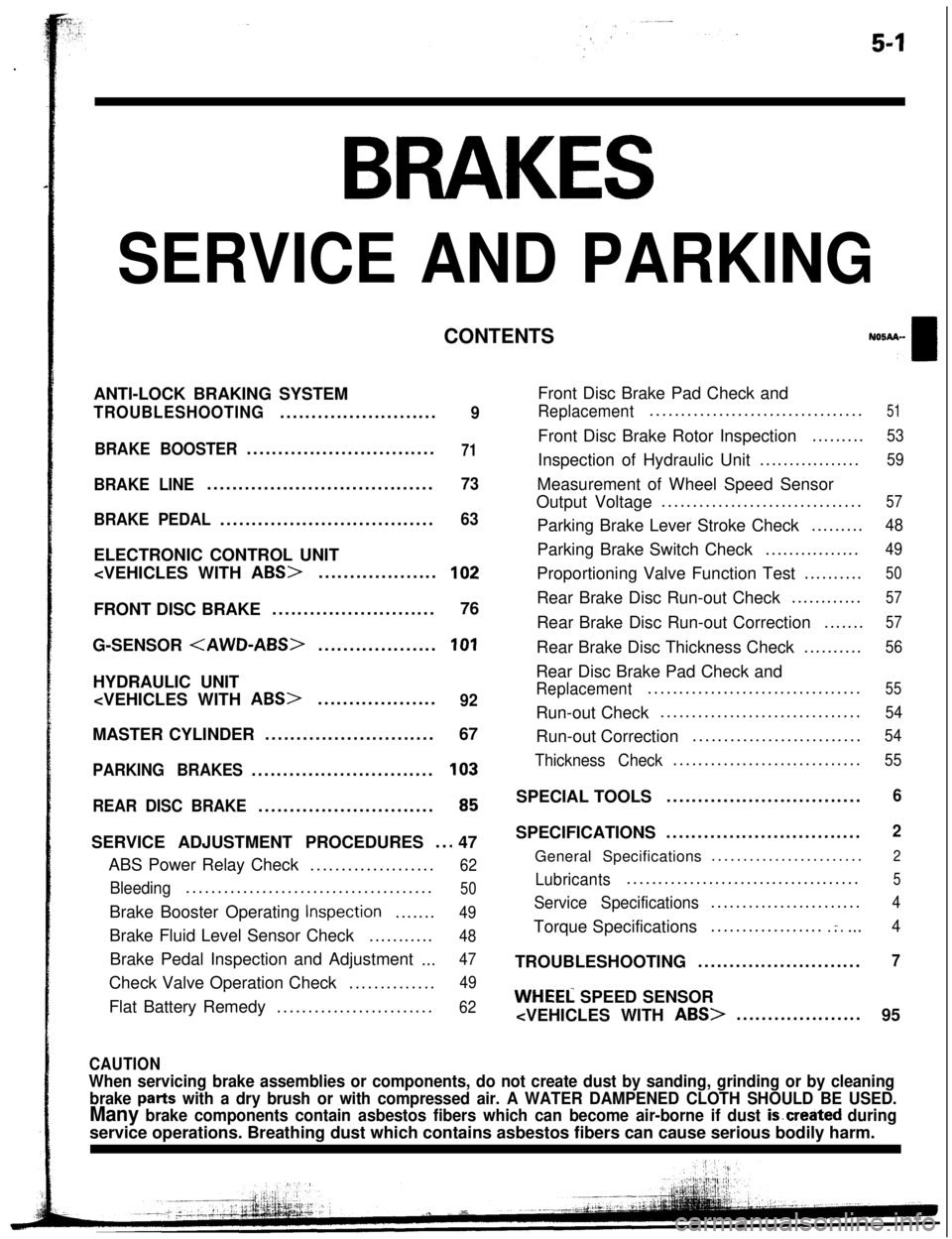
BRAKES
SERVICE AND PARKINGCONTENTS
ANTI-LOCK BRAKING SYSTEM
TROUBLESHOOTING.........................9
BRAKE BOOSTER..............................
71
BRAKE LINE....................................73
BRAKE PEDAL..................................
63ELECTRONIC CONTROL UNIT
G-SENSOR
PARKING BRAKES.............................103
REAR DISC BRAKE............................
65SERVICE ADJUSTMENT PROCEDURES
..a 47
ABS Power Relay Check....................
62
Bleeding.......................................50Brake Booster Operating
Inspection.......49Brake Fluid Level Sensor Check...........
48Brake Pedal Inspection and Adjustment
...
47Check Valve Operation Check..............
49Flat Battery Remedy.........................
62Front Disc Brake Pad Check and
Replacement..................................51Front Disc Brake Rotor Inspection.........
53Inspection of Hydraulic Unit.................
59Measurement of Wheel Speed Sensor
Output Voltage................................
57Parking Brake Lever Stroke Check.........
48Parking Brake Switch Check................
49Proportioning Valve Function Test..........
50Rear Brake Disc Run-out Check............
57Rear Brake Disc Run-out Correction.......
57Rear Brake Disc Thickness Check..........
56Rear Disc Brake Pad Check and
Replacement..................................55Run-out Check................................
54Run-out Correction...........................
54
Thickness Check..............................55SPECIAL TOOLS...............................
6SPECIFICATIONS...............................
2General Specifications........................
2
Lubricants.....................................5
Service Specifications........................4Torque Specifications..................
.:....4TROUBLESHOOTING..........................
7
WHEEL SPEED SENSOR
95
CAUTION
When servicing brake assemblies or components, do not create dust by sanding, grinding or by cleaning
brake
parts with a dry brush or with compressed air. A WATER DAMPENED CLOTH SHOULD BE USED.
Many brake components contain asbestos fibers which can become air-borne if dust is.created duringservice operations. Breathing dust which contains asbestos fibers can cause serious bodily harm.
Page 6 of 57
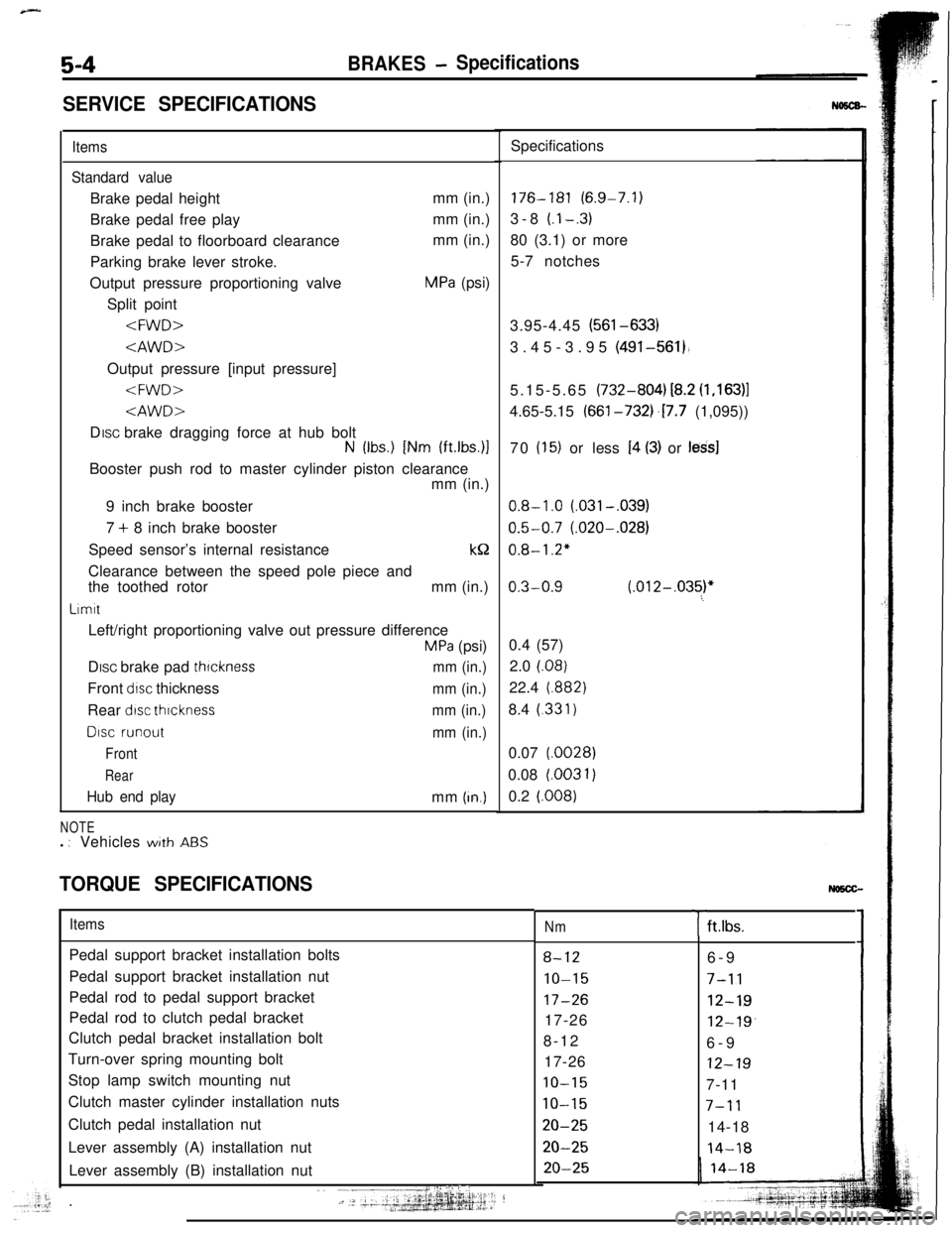
-
5-4BRAKES- Specifications
SERVICE SPECIFICATIONS
Items
Standard valueBrake pedal heightmm (in.)
Brake pedal free playmm (in.)
Brake pedal to floorboard clearancemm (in.)
Parking brake lever stroke.
Output pressure proportioning valve
MPa (psi)
Split point
N (Ibs.) [Nm (ft.lbs.)lBooster push rod to master cylinder piston clearance
mm (in.)
9 inch brake booster
7 + 8 inch brake booster
Speed sensor’s internal resistancek&
Clearance between the speed pole piece and
the toothed rotormm (in.)
LrmttLeft/right proportioning valve out pressure difference
MPa (psi)
DISC brake pad
thrcknessmm (in.)Front
drsc thicknessmm (in.)Rear
dtsc thrcknessmm (in.)
DISC runout
mm (in.)
Front
Rear
Hub end playmm (In.)
NOTEl : Vehicleswith ABS
TORQUE SPECIFICATIONSSpecifications176-181 (6.9-7.1)
3-8
(.l-.3)80 (3.1) or more
5-7 notches
3.95-4.45 (561-633)
3.45-3.95 (491-561).
5.15-5.65 (732-804) i8.2
(1,163)14.65-5.15 (661-732j.17.7 (1,095))
70
(15) or less I4 (3) or less]
0.8-1.0 (.031-,039)
0.5-0.7 (.020-.028)
0.8-1.2"
0.3-0.9 (.012-,035)"60.4 (57)
2.0
(.08)22.4
(.882)8.4
(.331)0.07
(.0028)0.08 l.0031)
0.2
(.008)
ItemsPedal support bracket installation bolts
Pedal support bracket installation nut
Pedal rod to pedal support bracket
Pedal rod to clutch pedal bracket
Clutch pedal bracket installation bolt
Turn-over spring mounting bolt
Stop lamp switch mounting nut
Clutch master cylinder installation nuts
Clutch pedal installation nut
Lever assembly (A) installation nut
Lever assembly (B) installation nut
I:: ::I .:‘i j ,:~~ -__j.-, .‘- ‘+‘+gg&p.~j:;.;1--?.+.k
Nm
8-12
IO-15
17-2617-26
8-12
17-26
10-15
10-15
20-25
20-25
20-25
Tft.lbs.
6-9
7-11
12-19
12-19.6-9
12-197-11
7-1114-18
14-18
Page 8 of 57
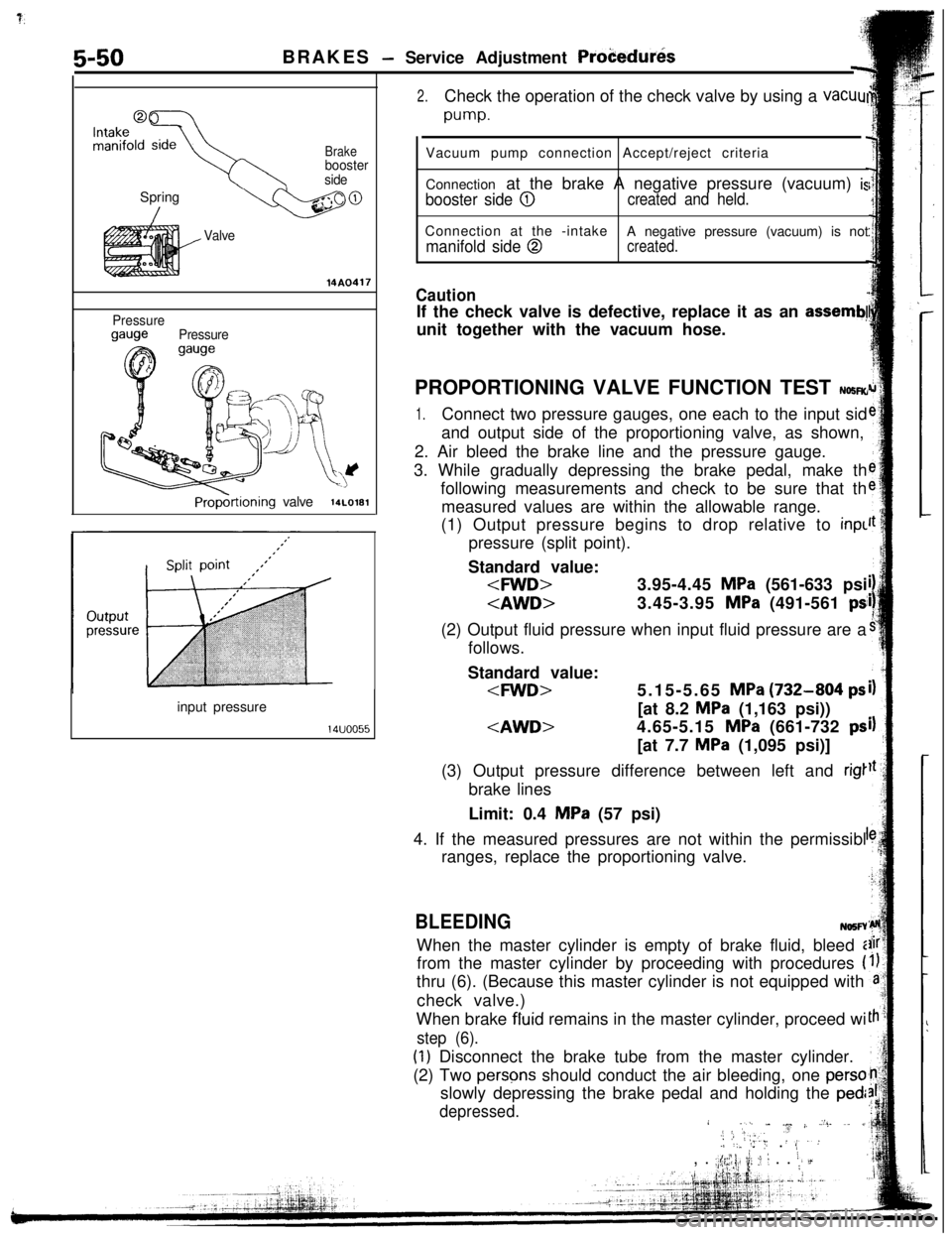
5-50BRAKES - Service Adjustment Proi?edur&
Brakebooster
sideSpring
’
/
Valve
Pressure
gaugePressure
PropGtioning valve14LO181input pressure
14uoo55
2.Check the operation of the check valve by using a vacuul
pump.Vacuum pump connection Accept/reject criteria
Connection at the brake A negative pressure (vacuum)
is
booster side @created and held.Connection at the -intake
manifold side @A negative pressure (vacuum) is notcreated.
CautionIf the check valve is defective, replace it as an
assemb!unit together with the vacuum hose.
PROPORTIONING VALVE FUNCTION TEST
NO!iR(r
1.Connect two pressure gauges, one each to the input sid
and output side of the proportioning valve, as shown,
2. Air bleed the brake line and the pressure gauge.
3. While gradually depressing the brake pedal, make th
following measurements and check to be sure that th
measured values are within the allowable range.
(1) Output pressure begins to drop relative to inpl
pressure (split point).
Standard value:
follows.
Standard value:
MPa (1,163 psi))
MPa (1,095 psi)]
(3) Output pressure difference between left and
rig1brake lines
Limit: 0.4
MPa (57 psi)
4. If the measured pressures are not within the permissibl
ranges, replace the proportioning valve.
BLEEDINGNo5FYWhen the master cylinder is empty of brake fluid, bleed i
from the master cylinder by proceeding with procedures
(thru (6). (Because this master cylinder is not equipped with
check valve.)
When brake fluid remains in the master cylinder, proceed wi
step (6).
(1) Disconnect the brake tube from the master cylinder.
(2) Two
persqs should conduct the air bleeding, one persoslowly depressing the brake pedal and holding the
ped:
depressed.i .I..[ j,‘I- .~ j, Z’:. ~. jl2;:‘,.Y .‘.:./ ‘:” ‘: ,, . 8,, .
.;$y; ii; :: 1 . . i;, d
Page 9 of 57
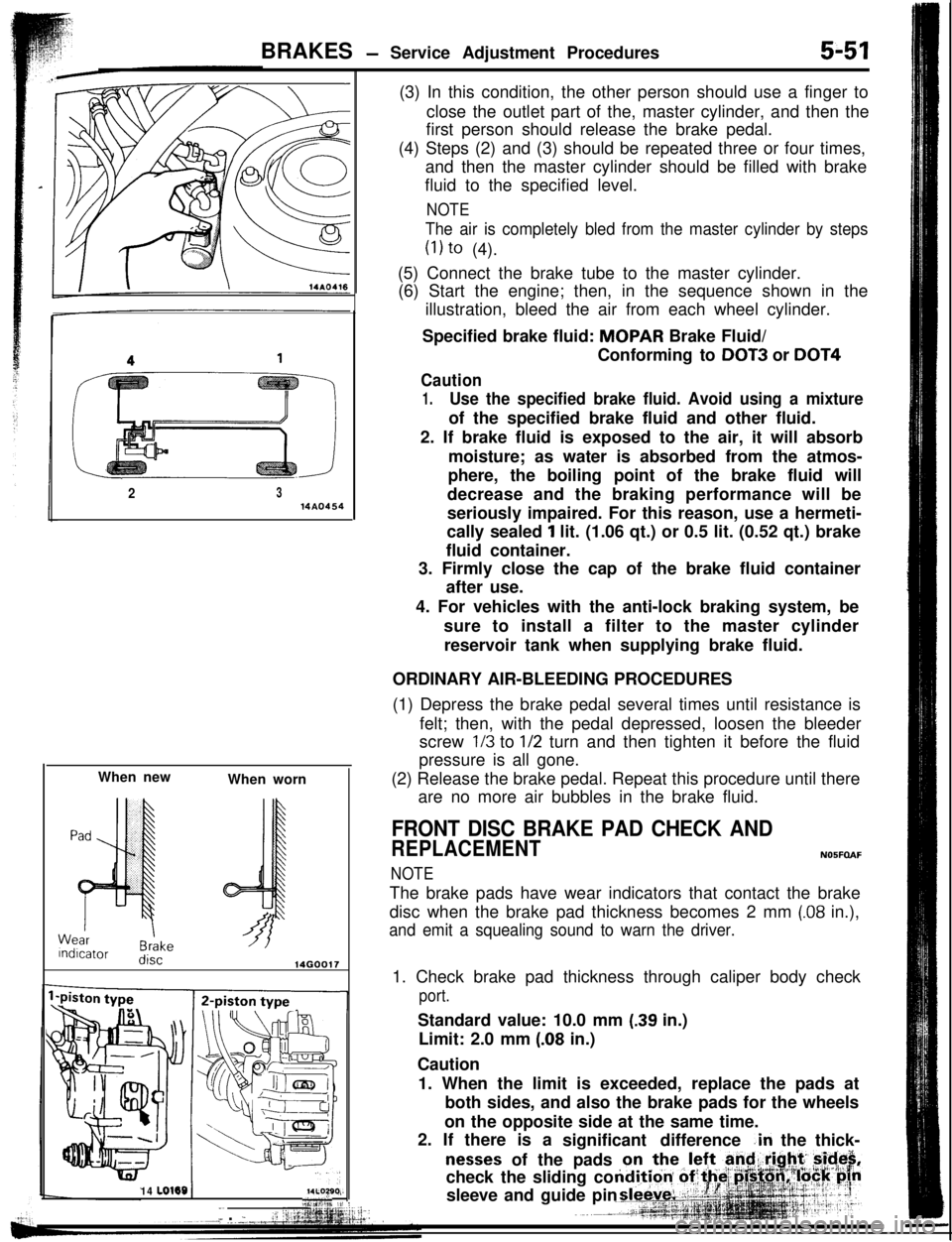
BRAKES - Service Adjustment Procedures5-51
2314A0454When new
When worn14G0017
1
14 LO169check the sliding coWsTm~3..“.W% ,Y :sleeve and guide pin-~I ._. ;;:i ‘.(3) In this condition, the other person should use a finger to
close the outlet part of the, master cylinder, and then the
first person should release the brake pedal.
(4) Steps (2) and (3) should be repeated three or four times,
and then the master cylinder should be filled with brake
fluid to the specified level.
NOTE
The air is completely bled from the master cylinder by steps
(1) to (4).
(5) Connect the brake tube to the master cylinder.
(6) Start the engine; then, in the sequence shown in the
illustration, bleed the air from each wheel cylinder.
Specified brake fluid: MOPAR Brake Fluid/
Conforming to
DOT3 or DOT4
Caution
1.Use the specified brake fluid. Avoid using a mixtureof the specified brake fluid and other fluid.
2. If brake fluid is exposed to the air, it will absorb
moisture; as water is absorbed from the atmos-
phere, the boiling point of the brake fluid will
decrease and the braking performance will be
seriously impaired. For this reason, use a hermeti-
cally sealed
1 lit. (1.06 qt.) or 0.5 lit. (0.52 qt.) brake
fluid container.
3. Firmly close the cap of the brake fluid container
after use.
4. For vehicles with the anti-lock braking system, be
sure to install a filter to the master cylinder
reservoir tank when supplying brake fluid.
ORDINARY AIR-BLEEDING PROCEDURES
(1) Depress the brake pedal several times until resistance is
felt; then, with the pedal depressed, loosen the bleeder
screw
l/3 to l/2 turn and then tighten it before the fluid
pressure is all gone.
(2) Release the brake pedal. Repeat this procedure until there
are no more air bubbles in the brake fluid.
FRONT DISC BRAKE PAD CHECK AND
REPLACEMENTN05FOAF
NOTEThe brake pads have wear indicators that contact the brake
disc when the brake pad thickness becomes 2 mm
(.08 in.),
and emit a squealing sound to warn the driver.1. Check brake pad thickness through caliper body check
port.Standard value: 10.0 mm
(.39 in.)
Limit: 2.0 mm
(.08 in.)
Caution
1. When the limit is exceeded, replace the pads at
both sides, and also the brake pads for the wheels
on the opposite side at the same time.
2. If there is a
significant difference
.in the thick-
nesses of the pads
Page 11 of 57
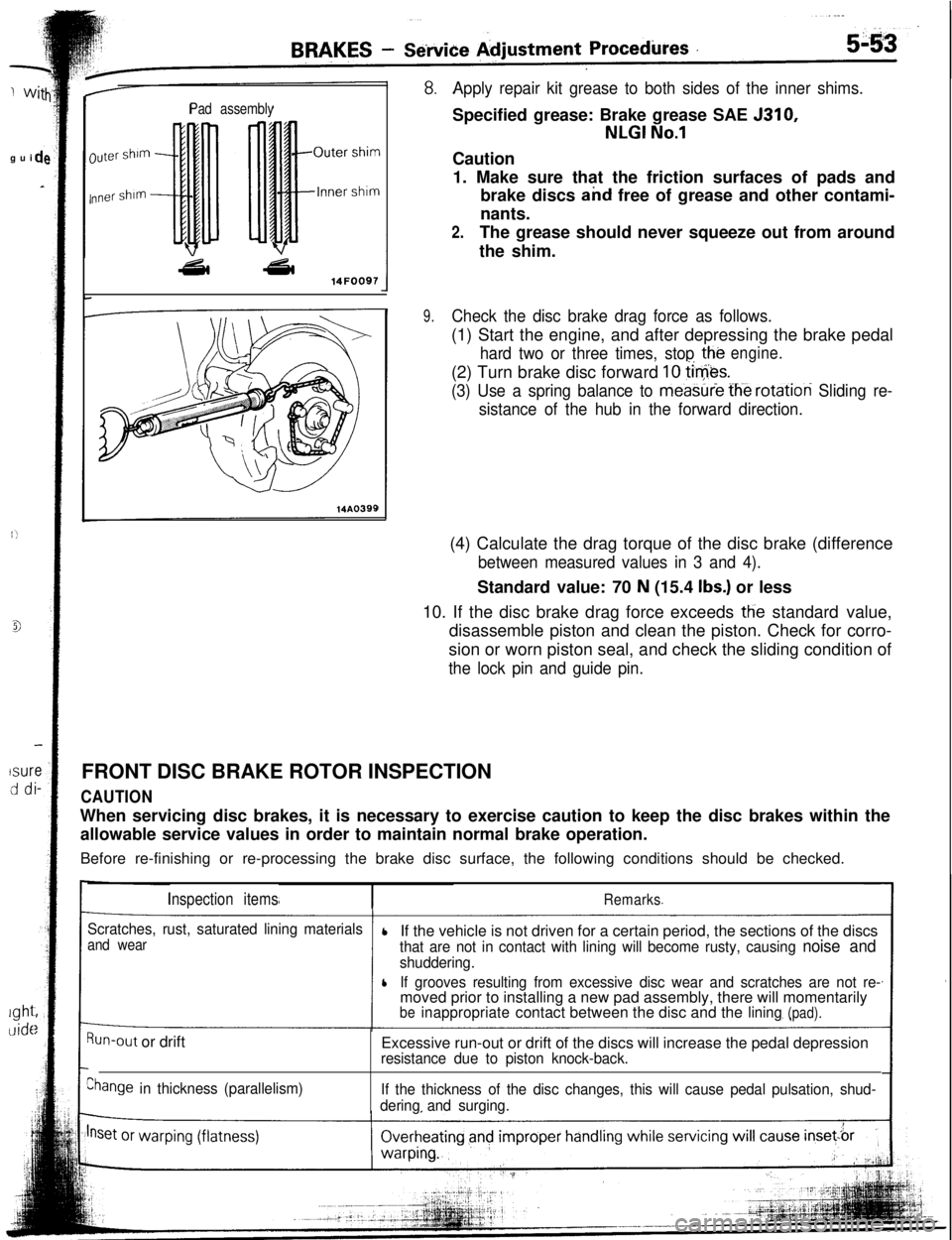
guiisur
dd
lght
clidc
Pad assembly
luter shim
nner shim
43l a14FOO97
14A0399
Apply repair kit grease to both sides of the inner shims.Specified grease: Brake grease SAE 5310,
NLGI No.1Caution
1. Make sure that the friction surfaces of pads and
brake discs and free of grease and other contami-
nants.
2.The grease should never squeeze out from around
the shim.
9.Check the disc brake drag force as follows.(1) Start the engine, and after depressing the brake pedal
hard two or three times, stop the(2) Turn brake disc forward
10 tie&.
engine.
(3) Use a spring balance to meastiie fh-e rotation Sliding re-
sistance of the hub in the forward direction.(4) Calculate the drag torque of the disc brake (difference
between measured values in 3 and 4).Standard value: 70
N (15.4 Ibs.) or less
10. If the disc brake drag force exceeds
tlie standard value,
disassemble piston and clean the piston. Check for corro-
sion or worn piston seal, and check the sliding condition of
the lock pin and guide pin.FRONT DISC BRAKE ROTOR INSPECTION
CAUTIONWhen servicing disc brakes, it is necessary to exercise caution to keep the disc brakes within the
allowable service values in order to maintain normal brake operation.
Before re-finishing or re-processing the brake disc surface, the following conditions should be checked.
Inspection itemsRemarks
Scratches, rust, saturated lining materials
and wearlIf the vehicle is not driven for a certain period, the sections of the discsthat are not in contact with lining will become rusty, causing noise and
shuddering.
lIf grooves resulting from excessive disc wear and scratches are not re-moved prior to installing a new pad assembly, there will momentarily
beinappropriatecontact between the disc and thelining(pad).
Run-out or drift
Ehange in thickness (parallelism)Excessive run-out or drift of the discs will increase the pedal depression
resistance due to piston knock-back.
If the thickness of the disc changes, this will cause pedal pulsation, shud-
deringand surging.
Page 14 of 57
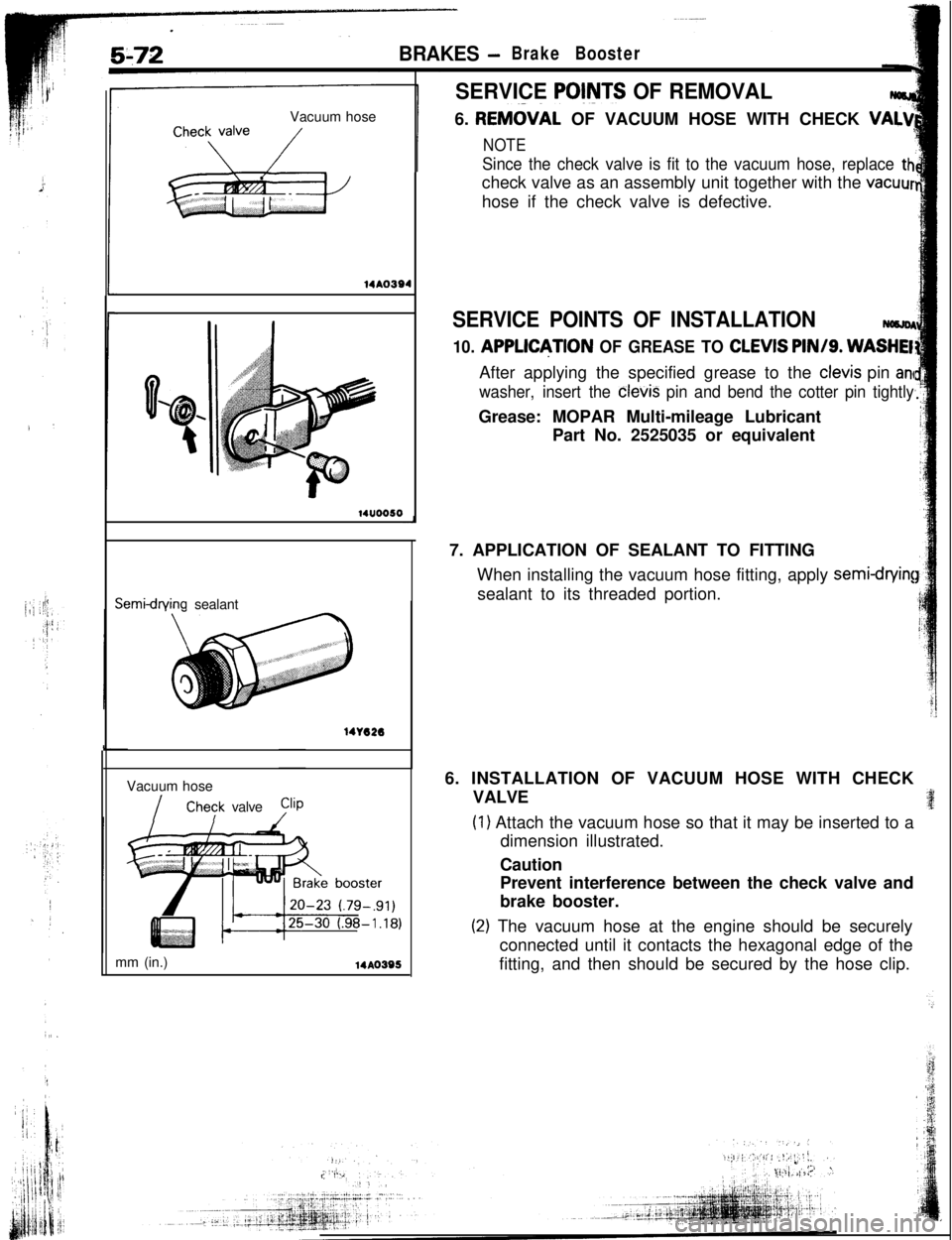
BRAKES -Brake BoosterVacuum hose
14AO39414u0050Semidrvina sealant
141626Vacuum hose
IChevk valve
mm (in.)
14AO395
SERVICE PO@JTS OF REMOVALNocm6.
REM&AL OF VACUUM HOSE WITH CHECK VA+
NOTE
Since the check valve is fit to the vacuum hose, replace thcheck valve as an assembly unit together with the
vacuurhose if the check valve is defective.
SERVICE POINTS OF INSTALLATION
10. APPLDJTION OF GREASE TO CLEVIS PIN/g. WASHEIAfter applying the specified grease to the
clevis pin an
washer, insert the
cievis pin and bend the cotter pin tightlyGrease: MOPAR Multi-mileage Lubricant
Part No. 2525035 or equivalent
7. APPLICATION OF SEALANT TO FITTING
When installing the vacuum hose fitting, apply
semi-cfryin!sealant to its threaded portion.
6. INSTALLATION OF VACUUM HOSE WITH CHECK
VALVE
(1) Attach the vacuum hose so that it may be inserted to a
dimension illustrated.
Caution
Prevent interference between the check valve and
brake booster.
(2) The vacuum hose at the engine should be securely
connected until it contacts the hexagonal edge of the
fitting, and then should be secured by the hose clip.
Page 17 of 57
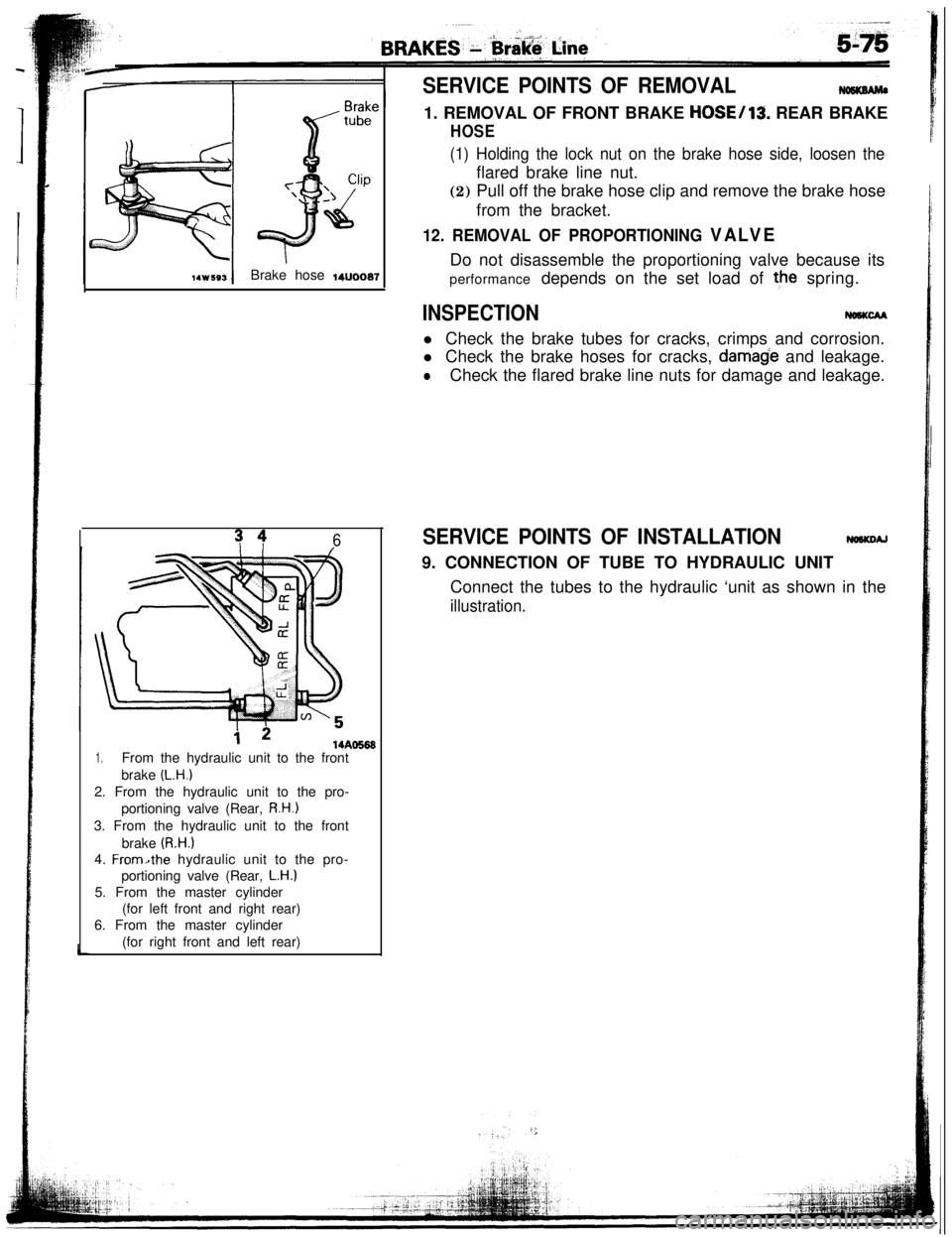
SERVICE POINTS OF REMOVAL
14w593Brake hose woo07
s 461. REMOVAL OF FRONT BRAKE
HOSE/13. REAR BRAKE
HOSE
(1) Holding the lock nut on the brake hose side, loosen theflared brake line nut.
(2) Pull off the brake hose clip and remove the brake hose
from the bracket.
12. REMOVAL OF PROPORTIONING VALVEDo not disassemble the proportioning valve because its
performance depends on the set load of the spring.
INSPECTIONNo6KcMl Check the brake tubes for cracks, crimps and corrosion.
l Check the brake hoses for cracks,
damade and leakage.
lCheck the flared brake line nuts for damage and leakage.
SERVICE POINTS OF INSTALLATIONNOSKOAJ9. CONNECTION OF TUBE TO HYDRAULIC UNIT
Connect the tubes to the hydraulic ‘unit as shown in the
illustration.
i 214AO5681.From the hydraulic unit to the front
brake
(L.H.)2. From the hydraulic unit to the pro-
portioning valve (Rear,
R.H.)3. From the hydraulic unit to the front
brake
(R.H.)4. From,the hydraulic unit to the pro-
portioning valve (Rear,
L.H.)5. From the master cylinder
(for left front and right rear)
6. From the master cylinder
(for right front and left rear)
Page 18 of 57
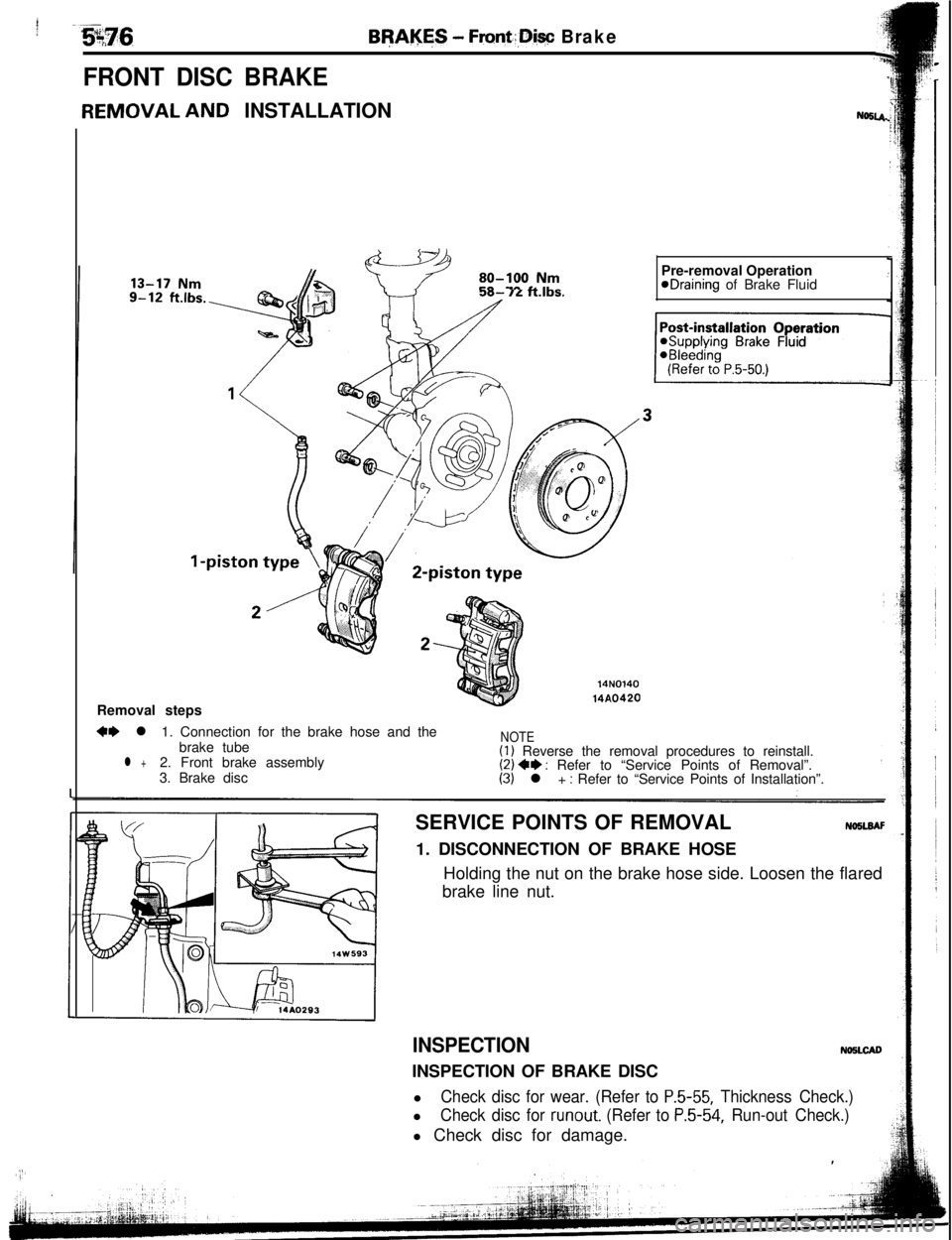
! -;-596
FRONT DISC BRAKE
Bf?Al$ES - Front.:,Diw Brake
REMOVAL AND INSTALLATIONN=U.
3U- IL l-LIDS.Y-i A
14N014014A0420Pre-removal Operation
eDraining of Brake Fluid
Removal steps
+e l1. Connection for the brake hose and the
brake tubeNOTE
l +2. Front brake assembly(1) Reverse the removal procedures to reinstall.
3. Brake disc(2) ++ : Refer to “Service Points of Removal”.(3) l + : Refer to “Service Points of Installation”.
SERVICE POINTS OF REMOVAL
No5LsAF1. DISCONNECTION OF BRAKE HOSE
Holding the nut on the brake hose side. Loosen the flared
brake line nut.
INSPECTIONNNiLCIDINSPECTION OF BRAKE DISC
l
Check disc for wear. (Refer to P.5-55, Thickness Check.)l
Check disc for runout. (Refer to P.5-54, Run-out Check.)l Check disc for damage.
Page 19 of 57
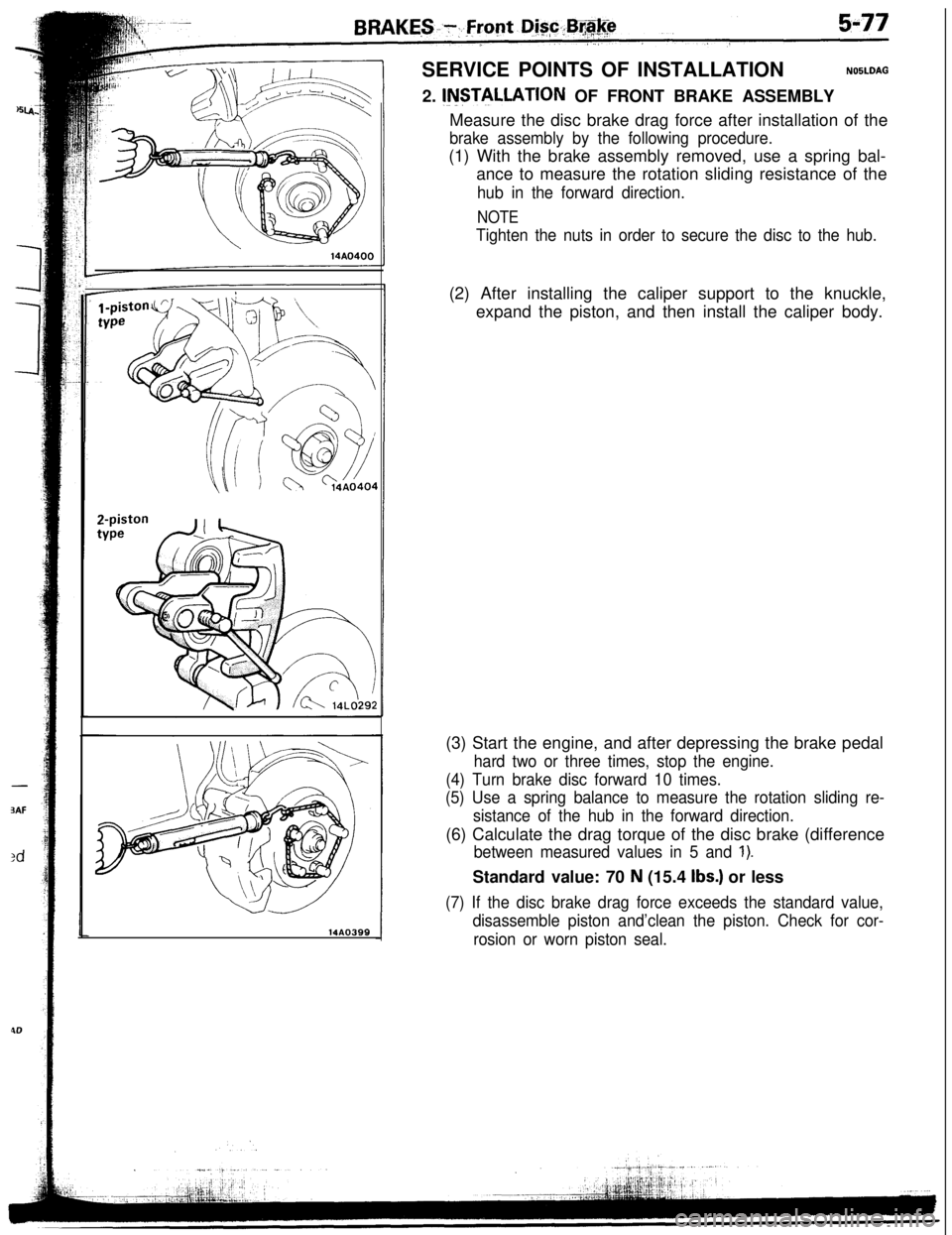
-
3AF
:dSERVICE POINTS OF INSTALLATION
NOBLDAG2.
INSTILLATION OF FRONT BRAKE ASSEMBLY
14AO399Measure the disc brake drag force after installation of the
brake assembly by the following procedure.(1) With the brake assembly removed, use a spring bal-
ance to measure the rotation sliding resistance of the
hub in the forward direction.
NOTE
Tighten the nuts in order to secure the disc to the hub.(2) After installing the caliper support to the knuckle,
expand the piston, and then install the caliper body.
(3) Start the engine, and after depressing the brake pedal
hard two or three times, stop the engine.
(4) Turn brake disc forward 10 times.
(5) Use a spring balance to measure the rotation sliding re-
sistance of the hub in the forward direction.(6) Calculate the drag torque of the disc brake (difference
between measured values in 5 and 1).Standard value: 70
N (15.4 Ibs.) or less
(7) If the disc brake drag force exceeds the standard value,
disassemble piston and’clean the piston. Check for cor-
rosion or worn piston seal.