Body MITSUBISHI LANCER 2005 Service Manual
[x] Cancel search | Manufacturer: MITSUBISHI, Model Year: 2005, Model line: LANCER, Model: MITSUBISHI LANCER 2005Pages: 788, PDF Size: 45.98 MB
Page 206 of 788
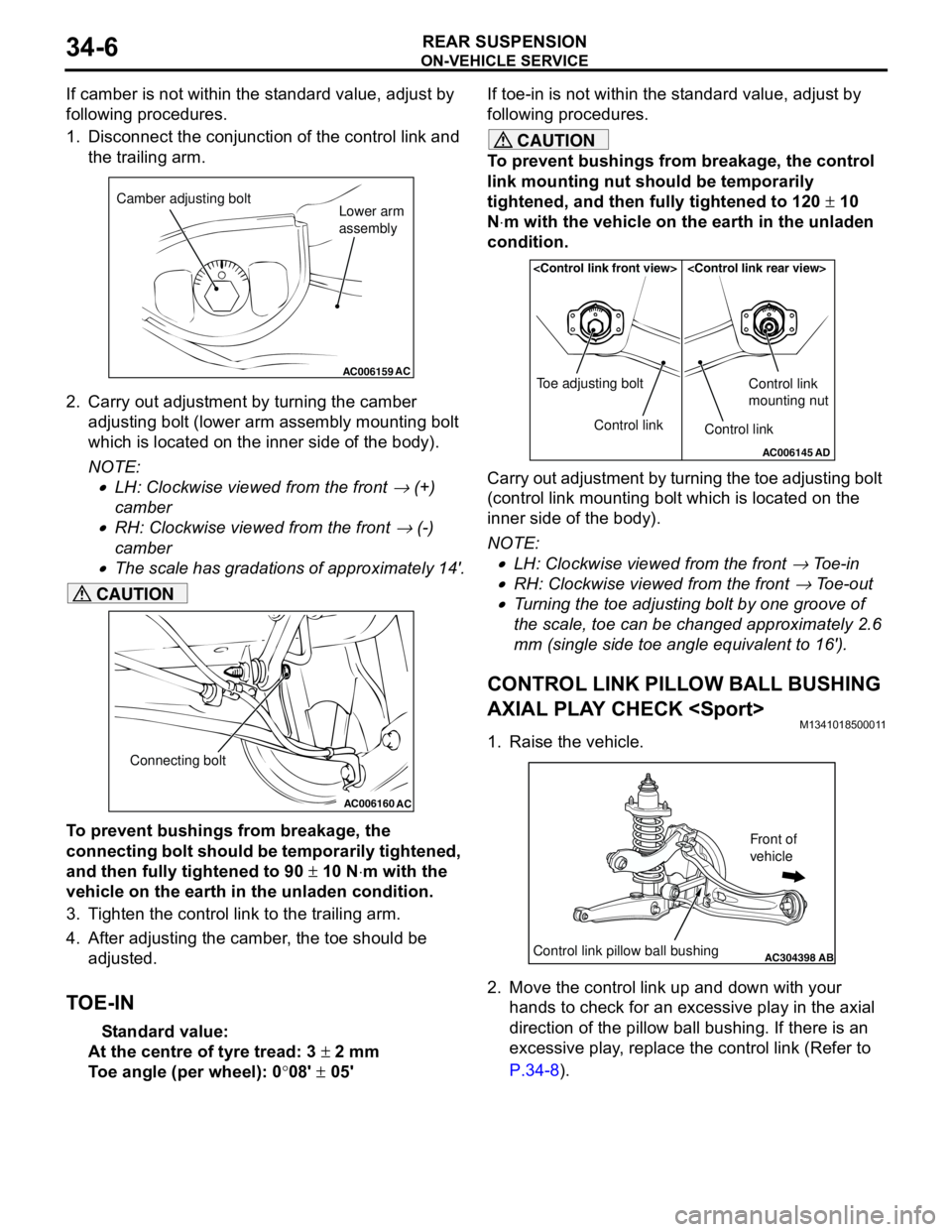
ON-VEHICLE SERVICE
REAR SUSPENSION34-6
If camber is not within the standard value, adjust by
following procedures.
1. Disconnect the conjunction of the control link and
the trailing arm.
2. Carry out adjustment by turning the camber
adjusting bolt (lower arm assembly mounting bolt
which is located on the inner side of the body).
NOTE: .
•LH: Clockwise viewed from the front → (+)
camber
•RH: Clockwise viewed from the front → (-)
camber
•The scale has gradations of approximately 14'.
CAUTION
To prevent bushings from breakage, the
connecting bolt should be temporarily tightened,
and then fully tightened to 90 ± 10 N⋅m with the
vehicle on the earth in the unladen condition.
3. Tighten the control link to the trailing arm.
4. After adjusting the camber, the toe should be
adjusted.
TOE-IN
Standard value:
At the centre of tyre tread: 3 ± 2 mm
Toe angle (per wheel): 0°08' ± 05'If toe-in is not within the standard value, adjust by
following procedures.
CAUTION
To prevent bushings from breakage, the control
link mounting nut should be temporarily
tightened, and then fully tightened to 120 ± 10
N⋅m with the vehicle on the earth in the unladen
condition.
Carry out adjustment by turning the toe adjusting bolt
(control link mounting bolt which is located on the
inner side of the body).
NOTE: .
•LH: Clockwise viewed from the front → Toe-in
•RH: Clockwise viewed from the front → Toe-out
•Turning the toe adjusting bolt by one groove of
the scale, toe can be changed approximately 2.6
mm (single side toe angle equivalent to 16').
CONTROL LINK PILLOW BALL BUSHING
AXIAL PLAY CHECK
M1341018500011
1. Raise the vehicle.
2. Move the control link up and down with your
hands to check for an excessive play in the axial
direction of the pillow ball bushing. If there is an
excessive play, replace the control link (Refer to
P.34-8).
AC006159AC
Camber adjusting bolt
Lower arm
assembly
AC006160
AC
Connecting bolt
AC006145AD
Control link Toe adjusting boltControl link
Control link
mounting nut
AC304398ABControl link pillow ball bushing
Front of
vehicle
Page 209 of 788
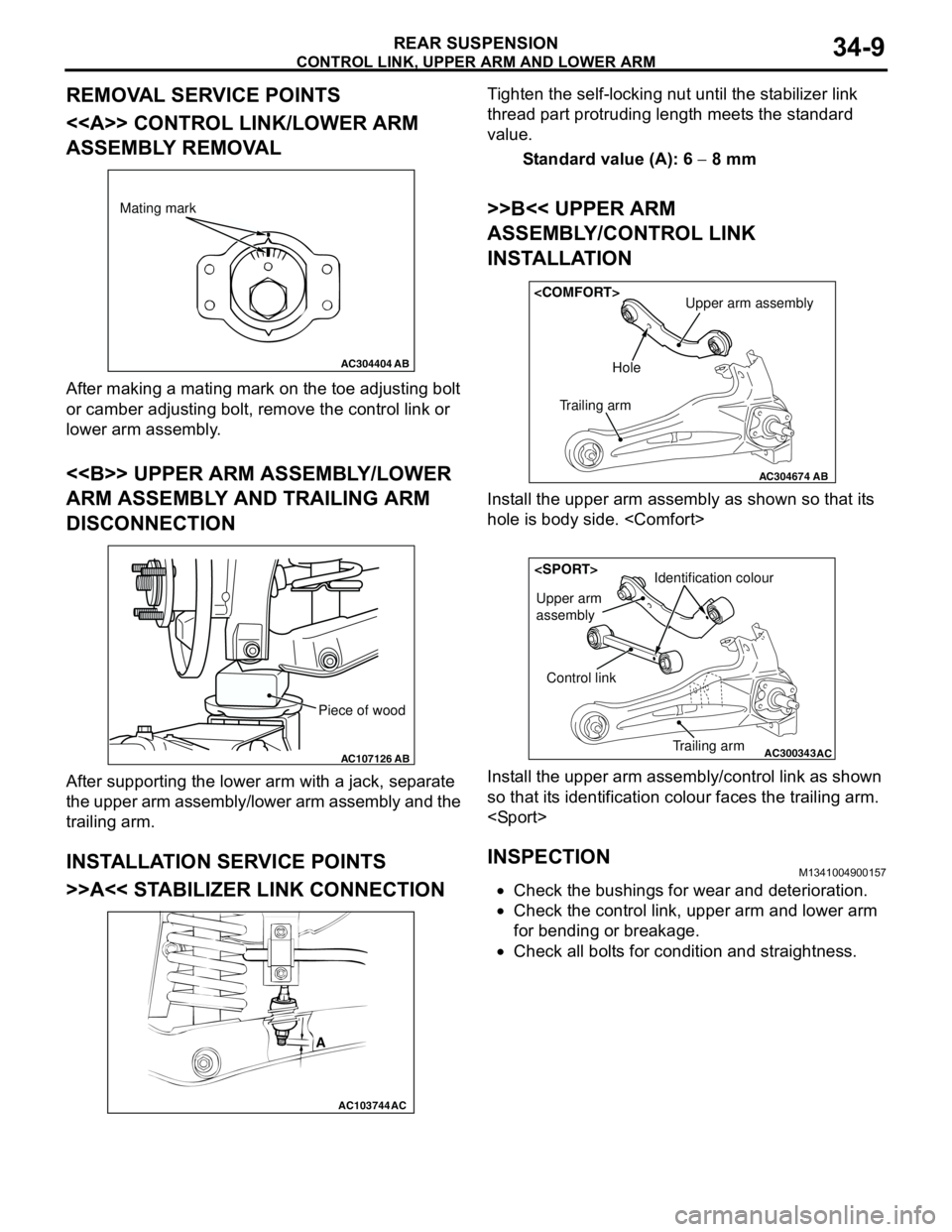
Page 213 of 788
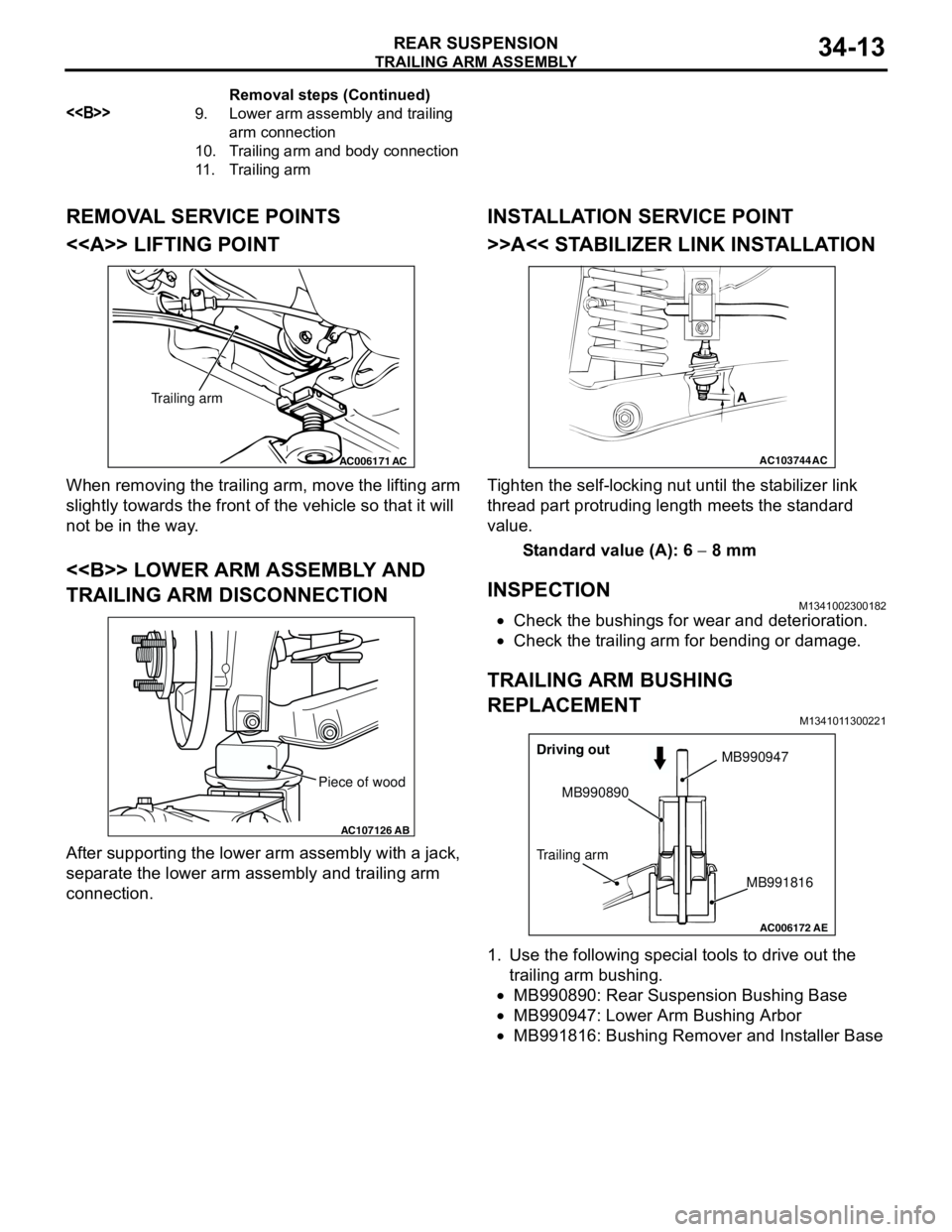
Page 218 of 788
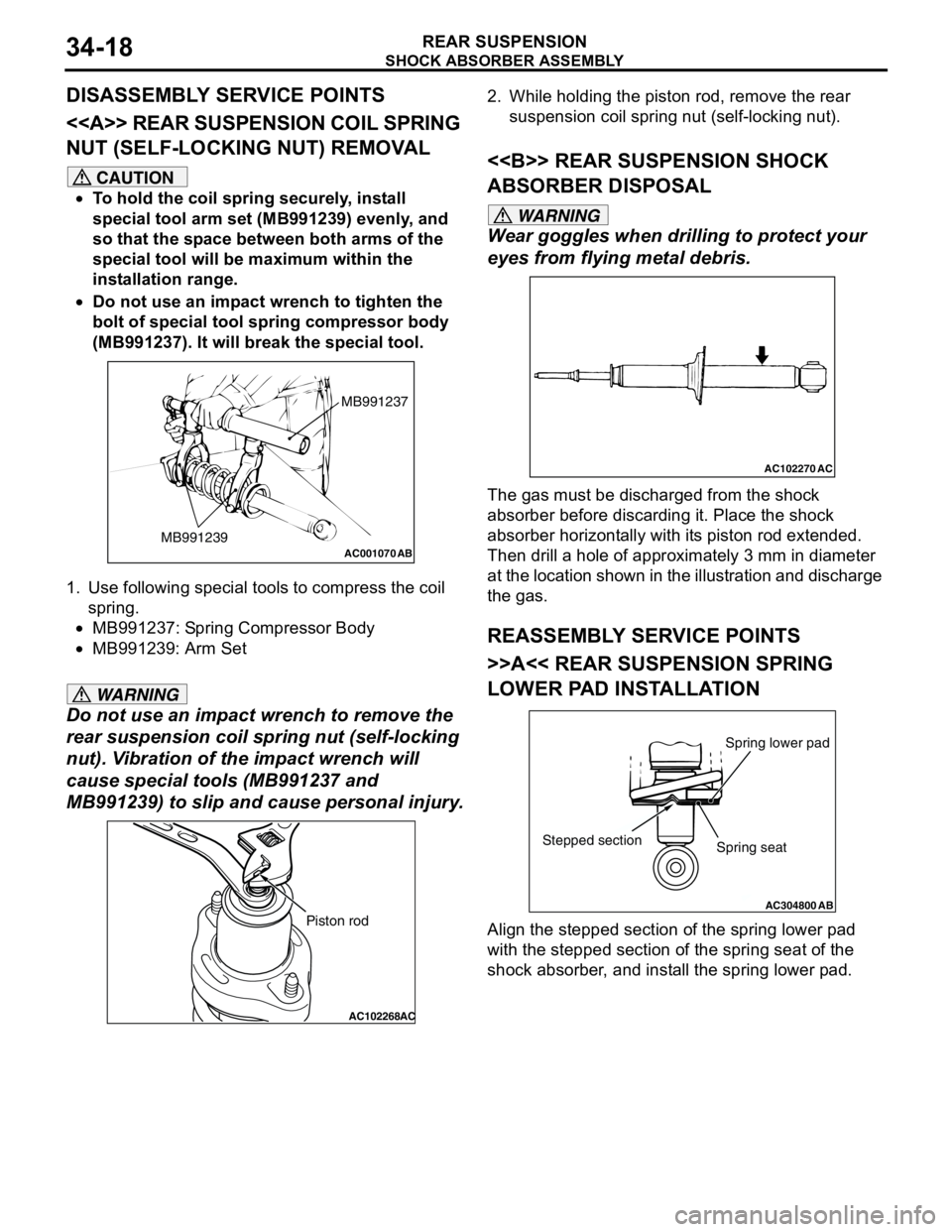
Page 219 of 788
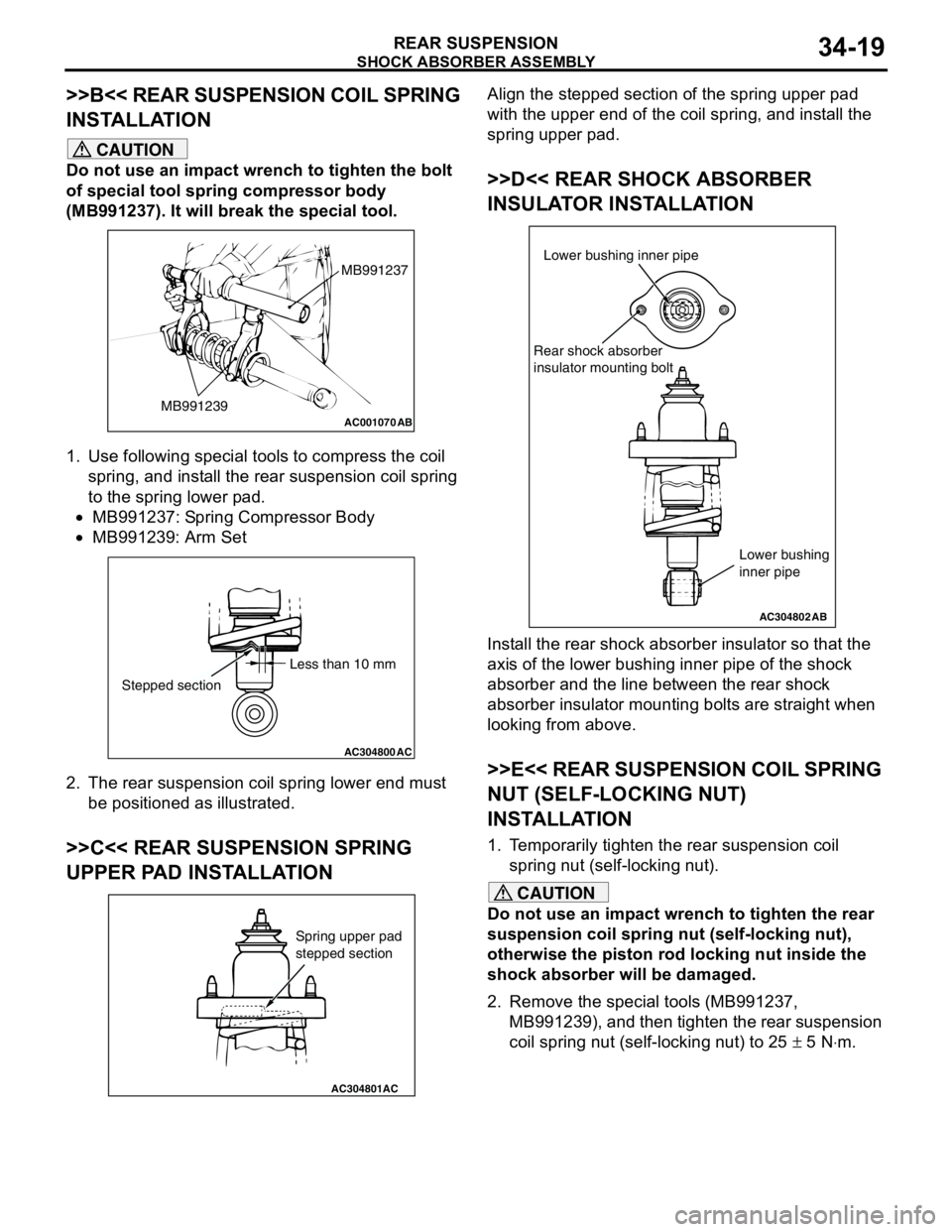
SHOCK ABSORBER ASSEMBLY
REAR SUSPENSION34-19
>>B<< REAR SUSPENSION COIL SPRING
INSTALLATION
CAUTION
Do not use an impact wrench to tighten the bolt
of special tool spring compressor body
(MB991237). It will break the special tool.
1. Use following special tools to compress the coil
spring, and install the rear suspension coil spring
to the spring lower pad.
•MB991237: Spring Compressor Body
•MB991239: Arm Set
2. The rear suspension coil spring lower end must
be positioned as illustrated.
>>C<< REAR SUSPENSION SPRING
UPPER PAD INSTALLATION
Align the stepped section of the spring upper pad
with the upper end of the coil spring, and install the
spring upper pad.
>>D<< REAR SHOCK ABSORBER
INSULATOR INSTALLATION
Install the rear shock absorber insulator so that the
axis of the lower bushing inner pipe of the shock
absorber and the line between the rear shock
absorber insulator mounting bolts are straight when
looking from above.
>>E<< REAR SUSPENSION COIL SPRING
NUT (SELF-LOCKING NUT)
INSTALLATION
1. Temporarily tighten the rear suspension coil
spring nut (self-locking nut).
CAUTION
Do not use an impact wrench to tighten the rear
suspension coil spring nut (self-locking nut),
otherwise the piston rod locking nut inside the
shock absorber will be damaged.
2. Remove the special tools (MB991237,
MB991239), and then tighten the rear suspension
coil spring nut (self-locking nut) to 25 ± 5 N⋅m.
AC001070
MB991237
MB991239
AB
AC304800AC
Less than 10 mm
Stepped section
AC304801AC
Spring upper pad
stepped section
AC304802
Lower bushing inner pipe
Rear shock absorber
insulator mounting bolt
AB
Lower bushing
inner pipe
Page 250 of 788
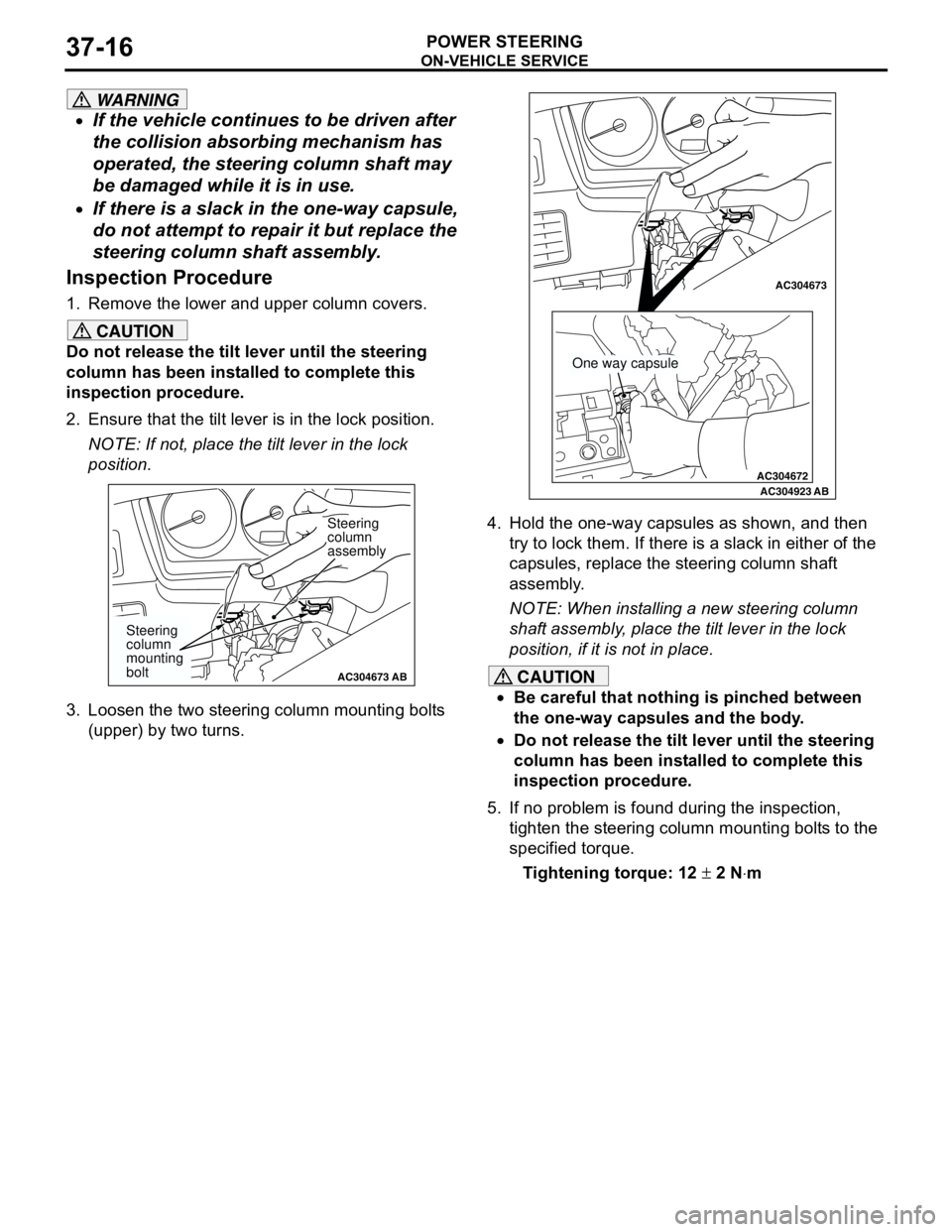
ON-VEHICLE SERVICE
POWER STEERING37-16
WARNING
•If the vehicle continues to be driven after
the collision absorbing mechanism has
operated, the steering column shaft may
be damaged while it is in use.
•If there is a slack in the one-way capsule,
do not attempt to repair it but replace the
steering column shaft assembly.
Inspection Procedure
1. Remove the lower and upper column covers.
CAUTION
Do not release the tilt lever until the steering
column has been installed to complete this
inspection procedure.
2. Ensure that the tilt lever is in the lock position.
NOTE: If not, place the tilt lever in the lock
position.
3. Loosen the two steering column mounting bolts
(upper) by two turns.4. Hold the one-way capsules as shown, and then
try to lock them. If there is a slack in either of the
capsules, replace the steering column shaft
assembly.
NOTE: When installing a new steering column
shaft assembly, place the tilt lever in the lock
position, if it is not in place.
CAUTION
•Be careful that nothing is pinched between
the one-way capsules and the body.
•Do not release the tilt lever until the steering
column has been installed to complete this
inspection procedure.
5. If no problem is found during the inspection,
tighten the steering column mounting bolts to the
specified torque.
Tightening torque: 12 ± 2 N⋅m
AC304673AC304673
Steering
column
assembly
AB
Steering
column
mounting
bolt
AC304672
AC304673AC304673
AC304923AB
One way capsule
Page 275 of 788
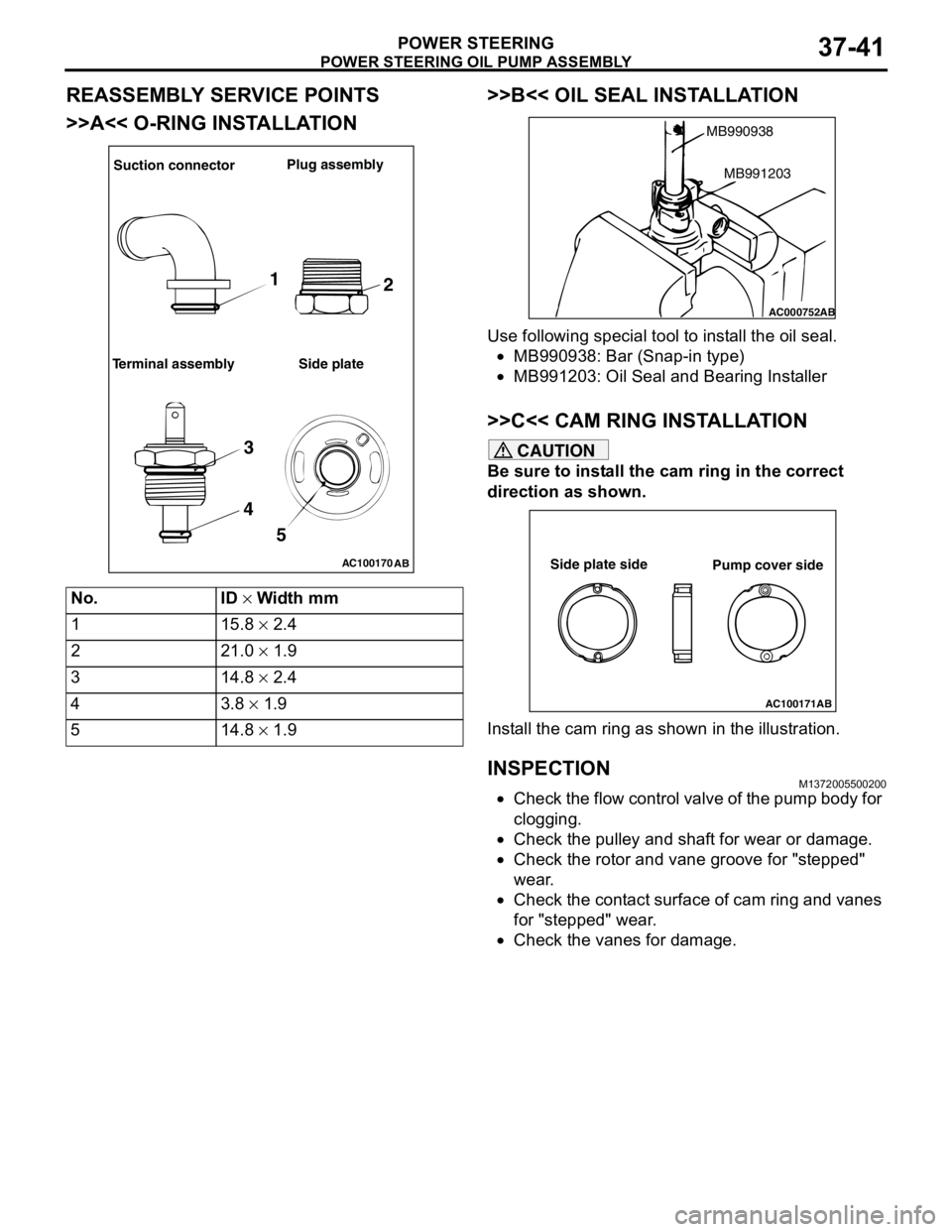
POWER STEERING OIL PUMP ASSEMBLY
POWER STEERING37-41
REASSEMBLY SERVICE POINTS
>>A<< O-RING INSTALLATION>>B<< OIL SEAL INSTALLATION
Use following special tool to install the oil seal.
•MB990938: Bar (Snap-in type)
•MB991203: Oil Seal and Bearing Installer
>>C<< CAM RING INSTALLATION
CAUTION
Be sure to install the cam ring in the correct
direction as shown.
Install the cam ring as shown in the illustration.
INSPECTIONM1372005500200
•Check the flow control valve of the pump body for
clogging.
•Check the pulley and shaft for wear or damage.
•Check the rotor and vane groove for "stepped"
wear.
•Check the contact surface of cam ring and vanes
for "stepped" wear.
•Check the vanes for damage. No. ID × Width mm
1 15.8 × 2.4
2 21.0 × 1.9
3 14.8 × 2.4
43.8 × 1.9
5 14.8 × 1.9
AC100170
AB
Suction connectorPlug assembly
Terminal assembly Side plate
1
2
3
4
5
AC000752
MB990938
AB
MB991203
AC100171AB
Side plate side
Pump cover side
Page 276 of 788
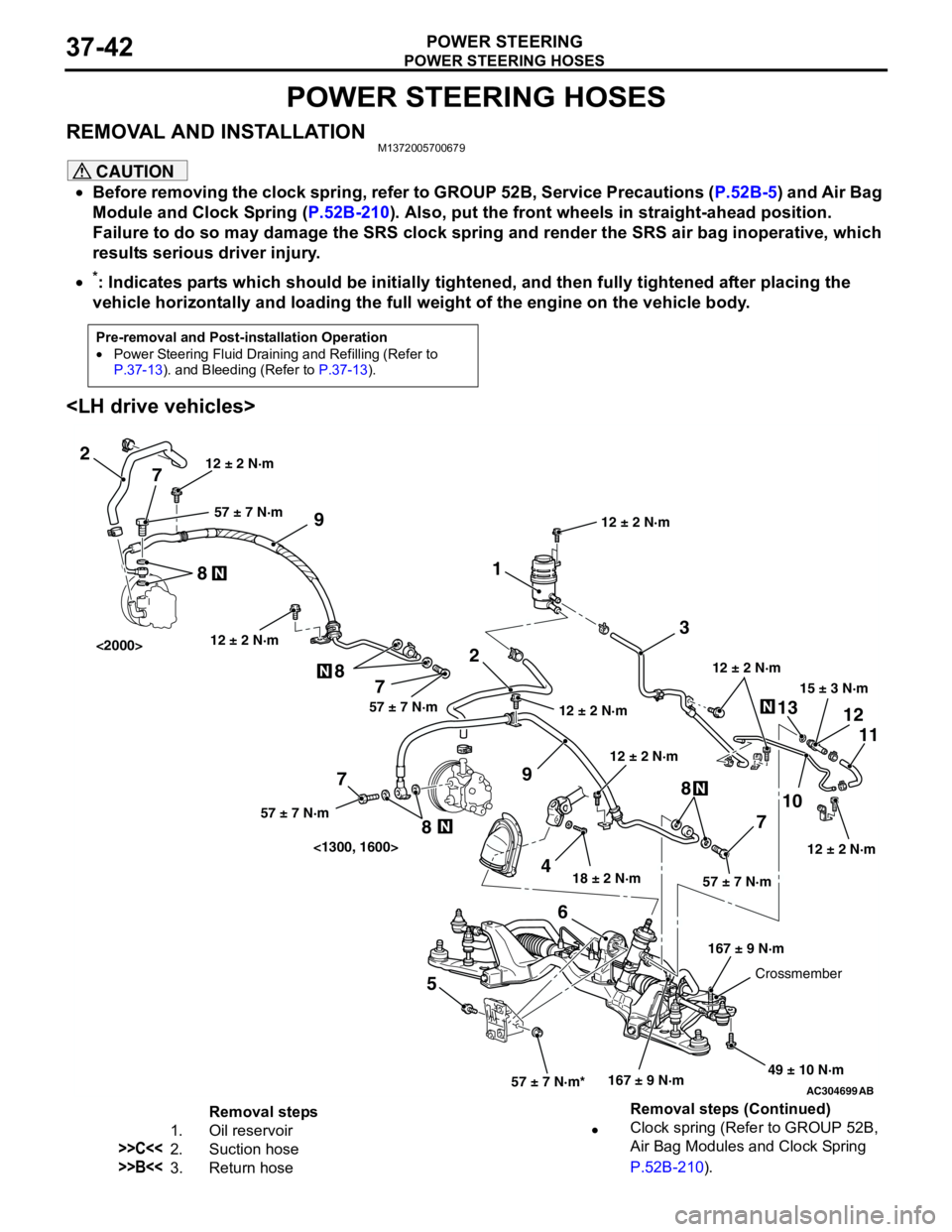
POWER STEERING HOSES
POWER STEERING37-42
POWER STEERING HOSES
REMOVAL AND INSTALLATIONM1372005700679
CAUTION
•Before removing the clock spring, refer to GROUP 52B, Service Precautions (P.52B-5) and Air Bag
Module and Clock Spring (P.52B-210). Also, put the front wheels in straight-ahead position.
Failure to do so may damage the SRS clock spring and render the SRS air bag inoperative, which
results serious driver injury.
•
*: Indicates parts which should be initially tightened, and then fully tightened after placing the
vehicle horizontally and loading the full weight of the engine on the vehicle body.
Pre-removal and Post-installation Operation
•Power Steering Fluid Draining and Refilling (Refer to
P.37-13). and Bleeding (Refer to P.37-13).
AC304699AB
15 ± 3 N·m
18 ± 2 N·m
167 ± 9 N·m 12 ± 2 N·m
49 ± 10 N·m 12 ± 2 N·m
57 ± 7 N·m*57 ± 7 N·m
3 1
2
9
13
10
711 12
568
12 ± 2 N·m12 ± 2 N·m
2
9
4 7 8
7 8
7
8
57 ± 7 N·m57 ± 7 N·m 57 ± 7 N·m
12 ± 2 N·m
167 ± 9 N·m
Crossmember 12 ± 2 N·m
<1300, 1600> <2000>
12 ± 2 N·m
Removal steps
1. Oil reservoir
>>C<<2. Suction hose
>>B<<3. Return hose•Clock spring (Refer to GROUP 52B,
Air Bag Modules and Clock Spring
P.52B-210). Removal steps (Continued)
Page 279 of 788
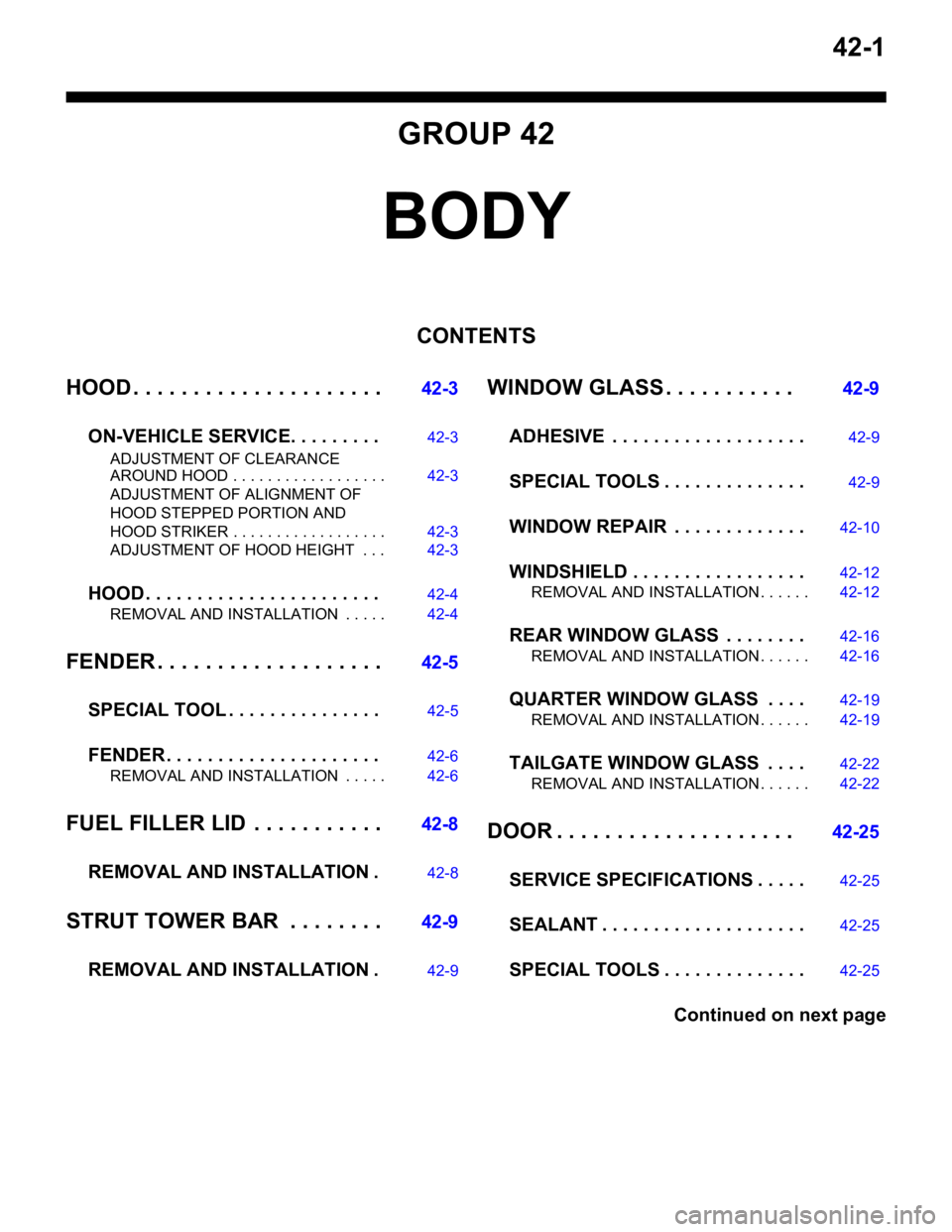
42-1
GROUP 42
BODY
CONTENTS
HOOD . . . . . . . . . . . . . . . . . . . . .
42-3
ON-VEHICLE SERVICE. . . . . . . . .
42-3
ADJUSTMENT OF CLEARANCE
AROUND HOOD . . . . . . . . . . . . . . . . . . 42-3
ADJUSTMENT OF ALIGNMENT OF
HOOD STEPPED PORTION AND
HOOD STRIKER . . . . . . . . . . . . . . . . . . 42-3
ADJUSTMENT OF HOOD HEIGHT . . . 42-3
HOOD . . . . . . . . . . . . . . . . . . . . . . .42-4
REMOVAL AND INSTALLATION . . . . . 42-4
FENDER . . . . . . . . . . . . . . . . . . .42-5
SPECIAL TOOL . . . . . . . . . . . . . . .
42-5
FENDER . . . . . . . . . . . . . . . . . . . . .42-6
REMOVAL AND INSTALLATION . . . . . 42-6
FUEL FILLER LID . . . . . . . . . . .42-8
REMOVAL AND INSTALLATION .
42-8
STRUT TOWER BAR . . . . . . . .42-9
REMOVAL AND INSTALLATION .
42-9
WINDOW GLASS . . . . . . . . . . . 42-9
ADHESIVE . . . . . . . . . . . . . . . . . . .
42-9
SPECIAL TOOLS . . . . . . . . . . . . . .42-9
WINDOW REPAIR . . . . . . . . . . . . .42-10
WINDSHIELD . . . . . . . . . . . . . . . . .42-12
REMOVAL AND INSTALLATION . . . . . . 42-12
REAR WINDOW GLASS . . . . . . . .42-16
REMOVAL AND INSTALLATION . . . . . . 42-16
QUARTER WINDOW GLASS . . . .42-19
REMOVAL AND INSTALLATION . . . . . . 42-19
TAILGATE WINDOW GLASS . . . .42-22
REMOVAL AND INSTALLATION . . . . . . 42-22
DOOR . . . . . . . . . . . . . . . . . . . . 42-25
SERVICE SPECIFICATIONS . . . . .
42-25
SEALANT . . . . . . . . . . . . . . . . . . . .42-25
SPECIAL TOOLS . . . . . . . . . . . . . .42-25
Continued on next page
Page 281 of 788
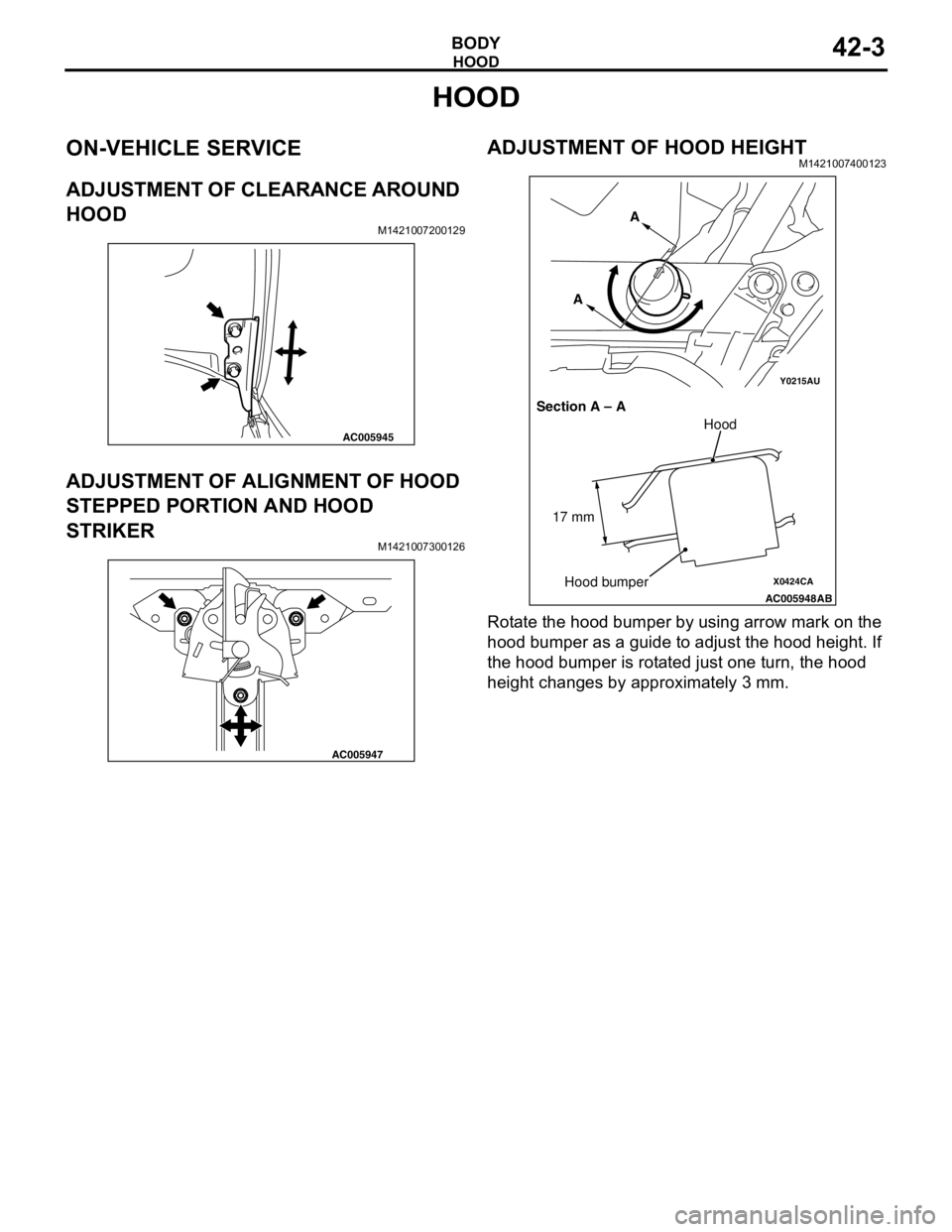
HOOD
BODY42-3
HOOD
ON-VEHICLE SERVICE
ADJUSTMENT OF CLEARANCE AROUND
HOOD
M1421007200129
ADJUSTMENT OF ALIGNMENT OF HOOD
STEPPED PORTION AND HOOD
STRIKER
M1421007300126
ADJUSTMENT OF HOOD HEIGHTM1421007400123
Rotate the hood bumper by using arrow mark on the
hood bumper as a guide to adjust the hood height. If
the hood bumper is rotated just one turn, the hood
height changes by approximately 3 mm.
AC005945
AC005947
Y0215AU
X0424CA
AC005948
AB
Section A – AA
A
Hood
Hood bumper 17 mm