sensor MITSUBISHI LANCER EVOLUTION 2007 Service Repair Manual
[x] Cancel search | Manufacturer: MITSUBISHI, Model Year: 2007, Model line: LANCER EVOLUTION, Model: MITSUBISHI LANCER EVOLUTION 2007Pages: 1449, PDF Size: 56.82 MB
Page 722 of 1449
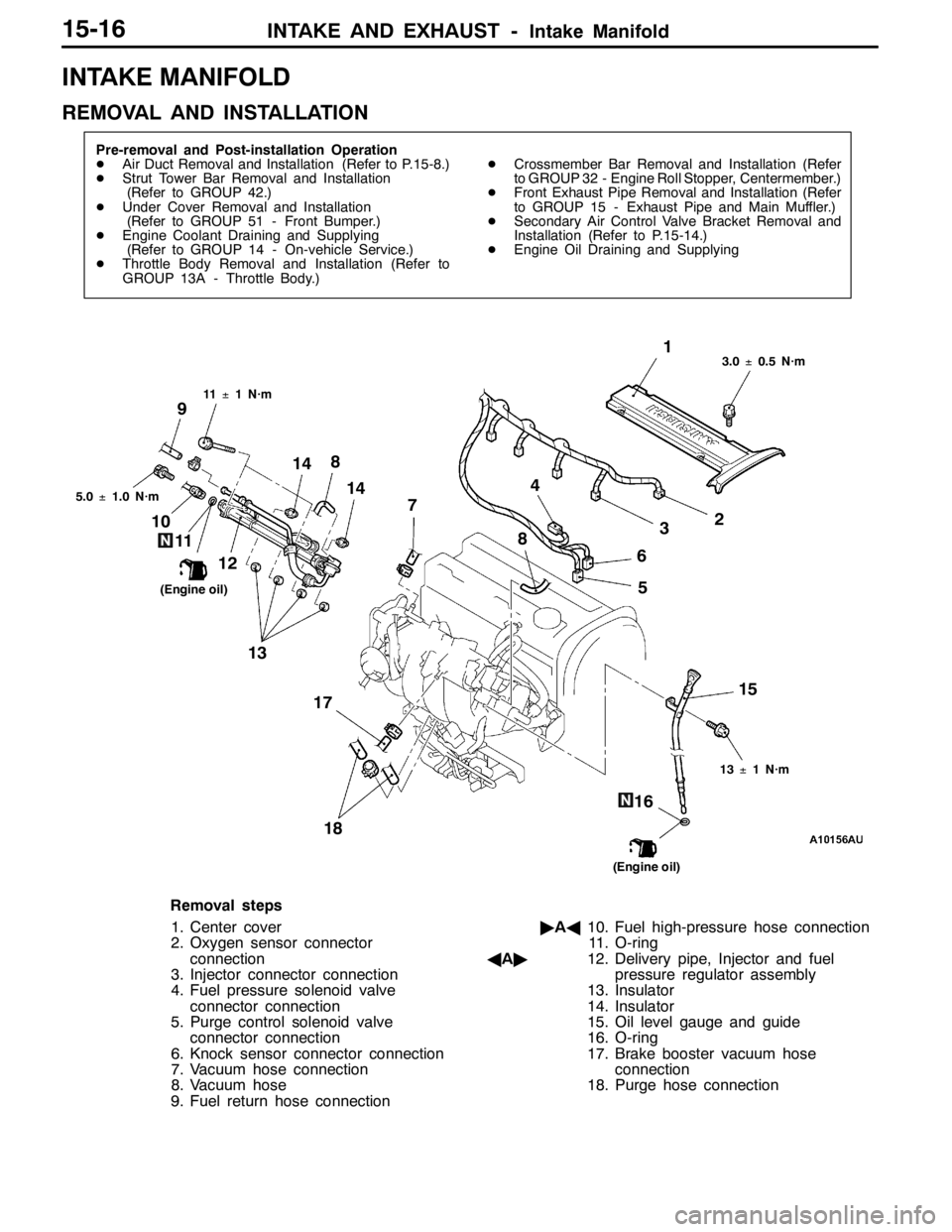
INTAKE AND EXHAUST -Intake Manifold15-16
INTAKE MANIFOLD
REMOVAL AND INSTALLATION
Pre-removal and Post-installation Operation
DAir Duct Removal and Installation (Refer to P.15-8.)
DStrut Tower Bar Removal and Installation
(Refer to GROUP 42.)
DUnder Cover Removal and Installation
(Refer to GROUP 51 - Front Bumper.)
DEngine Coolant Draining and Supplying
(Refer to GROUP 14 - On-vehicle Service.)
DThrottle Body Removal and Installation (Refer to
GROUP 13A - Throttle Body.)DCrossmember Bar Removal and Installation (Refer
to GROUP 32 - Engine Roll Stopper, Centermember.)
DFront Exhaust Pipe Removal and Installation (Refer
to GROUP 15 - Exhaust Pipe and Main Muffler.)
DSecondary Air Control Valve Bracket Removal and
Installation (Refer to P.15-14.)
DEngine Oil Draining and Supplying
1
2
3 4
5 6 7
8 10
11
1214
13
15
16 17
18
9
11±1 N·m3.0±0.5 N·m
13±1 N·m
(Engine oil)
(Engine oil) 5.0±1.0 N·m
14 8
Removal steps
1. Center cover
2. Oxygen sensor connector
connection
3. Injector connector connection
4. Fuel pressure solenoid valve
connector connection
5. Purge control solenoid valve
connector connection
6. Knock sensor connector connection
7. Vacuum hose connection
8. Vacuum hose
9. Fuel return hose connection"AA10. Fuel high-pressure hose connection
11. O-ring
AA"12. Delivery pipe, Injector and fuel
pressure regulator assembly
13. Insulator
14. Insulator
15. Oil level gauge and guide
16. O-ring
17. Brake booster vacuum hose
connection
18. Purge hose connection
Page 725 of 1449
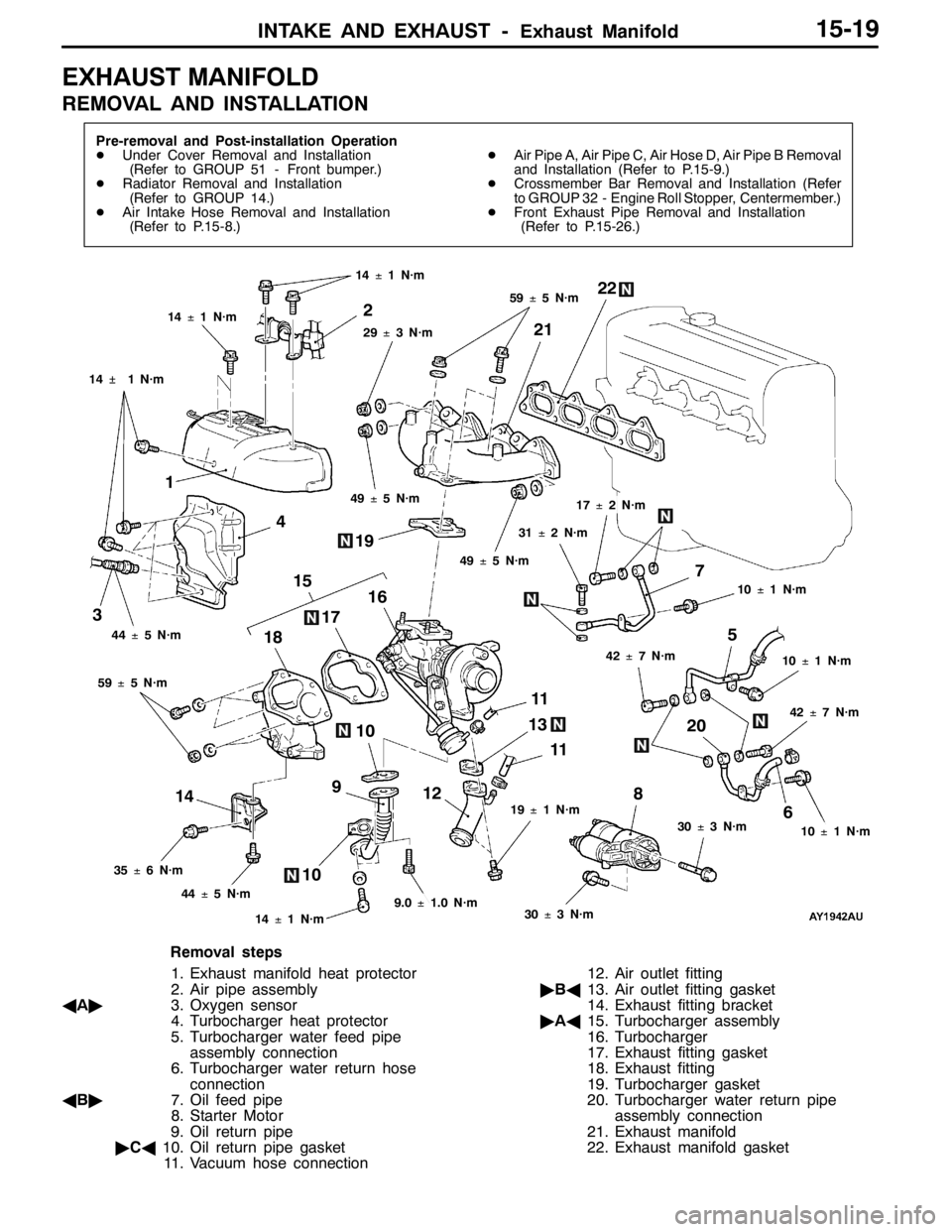
INTAKE AND EXHAUST -Exhaust Manifold15-19
EXHAUST MANIFOLD
REMOVAL AND INSTALLATION
Pre-removal and Post-installation Operation
DUnder Cover Removal and Installation
(Refer to GROUP 51 - Front bumper.)
DRadiator Removal and Installation
(Refer to GROUP 14.)
DAir Intake Hose Removal and Installation
(Refer to P.15-8.)DAir Pipe A, Air Pipe C, Air Hose D, Air Pipe B Removal
and Installation (Refer to P.15-9.)
DCrossmember Bar Removal and Installation (Refer
to GROUP 32 - Engine Roll Stopper, Centermember.)
DFront Exhaust Pipe Removal and Installation
(Refer to P.15-26.)
13 12
3
6 5
8
9
11 192122
14¶1 N·m
4
7
11
12 15
16
17
18
20
1010
14
14±1 N·m
14±1 N·m
29±3 N·m
59±5 N·m
49±5 N·m
44±5 N·m
59±5 N·m
35±6 N·m
44±5 N·m
14±1 N·m9.0±1.0 N·m30±3 N·m
30±3 N·m10±1 N·m
42±7 N·m
10±1 N·m
10±1 N·m
17±2 N·m
31±2 N·m
49±5 N·m
42±7 N·m
19±1 N·m
Removal steps
1. Exhaust manifold heat protector
2. Air pipe assembly
AA"3. Oxygen sensor
4. Turbocharger heat protector
5. Turbocharger water feed pipe
assembly connection
6. Turbocharger water return hose
connection
AB"7. Oil feed pipe
8. Starter Motor
9. Oil return pipe
"CA10. Oil return pipe gasket
11. Vacuum hose connection12. Air outlet fitting
"BA13. Air outlet fitting gasket
14. Exhaust fitting bracket
"AA15. Turbocharger assembly
16. Turbocharger
17. Exhaust fitting gasket
18. Exhaust fitting
19. Turbocharger gasket
20. Turbocharger water return pipe
assembly connection
21. Exhaust manifold
22. Exhaust manifold gasket
Page 726 of 1449
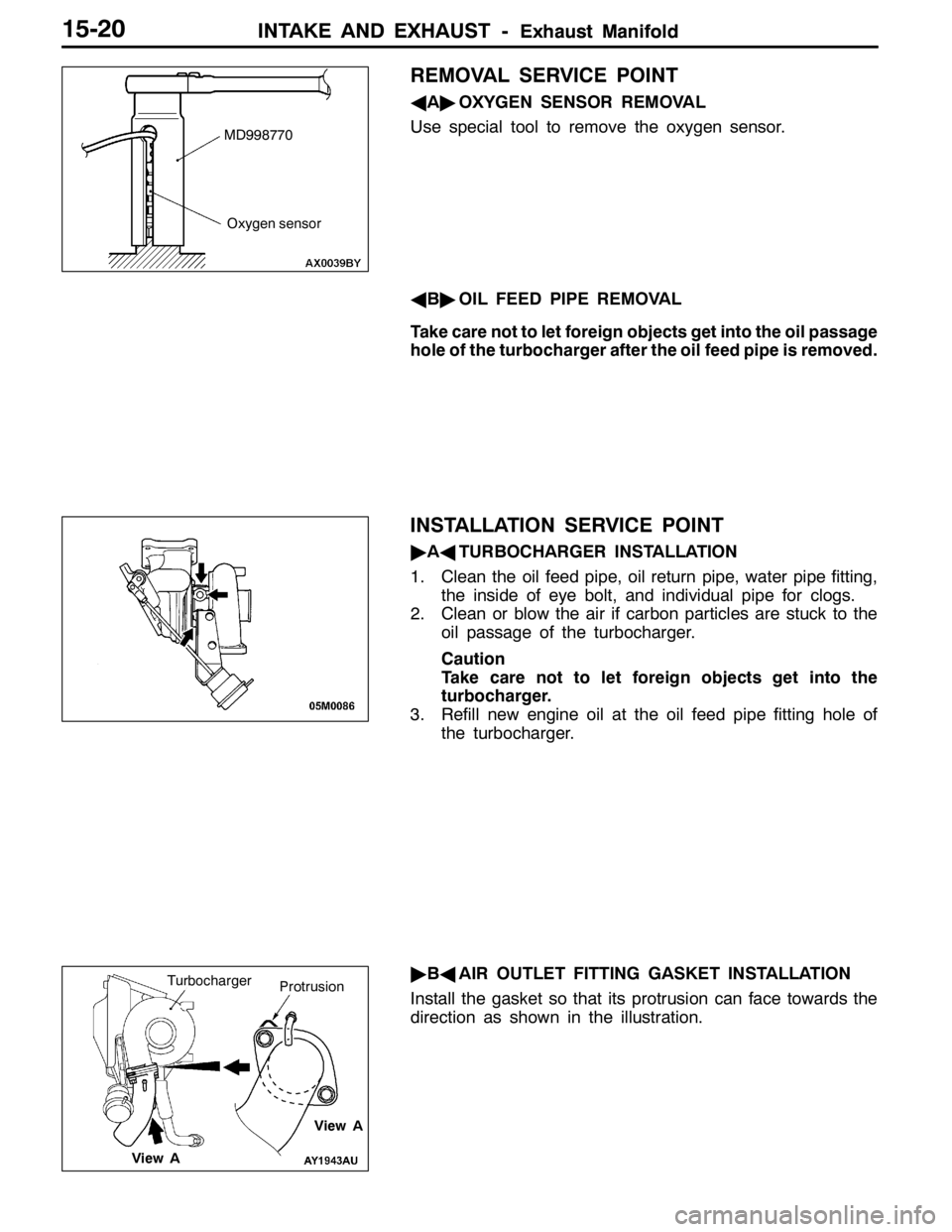
INTAKE AND EXHAUST -Exhaust ManifoldINTAKE AND EXHAUST -Exhaust Manifold15-20
REMOVAL SERVICE POINT
AA"OXYGEN SENSOR REMOVAL
Use special tool to remove the oxygen sensor.
AB"OIL FEED PIPE REMOVAL
Take care not to let foreign objects get into the oil passage
hole of the turbocharger after the oil feed pipe is removed.
INSTALLATION SERVICE POINT
"AATURBOCHARGER INSTALLATION
1. Clean the oil feed pipe, oil return pipe, water pipe fitting,
the inside of eye bolt, and individual pipe for clogs.
2. Clean or blow the air if carbon particles are stuck to the
oil passage of the turbocharger.
Caution
Take care not to let foreign objects get into the
turbocharger.
3. Refill new engine oil at the oil feed pipe fitting hole of
the turbocharger.
"BAAIR OUTLET FITTING GASKET INSTALLATION
Install the gasket so that its protrusion can face towards the
direction as shown in the illustration.
MD998770
Oxygen sensor
View A
View A
TurbochargerProtrusion
Page 732 of 1449
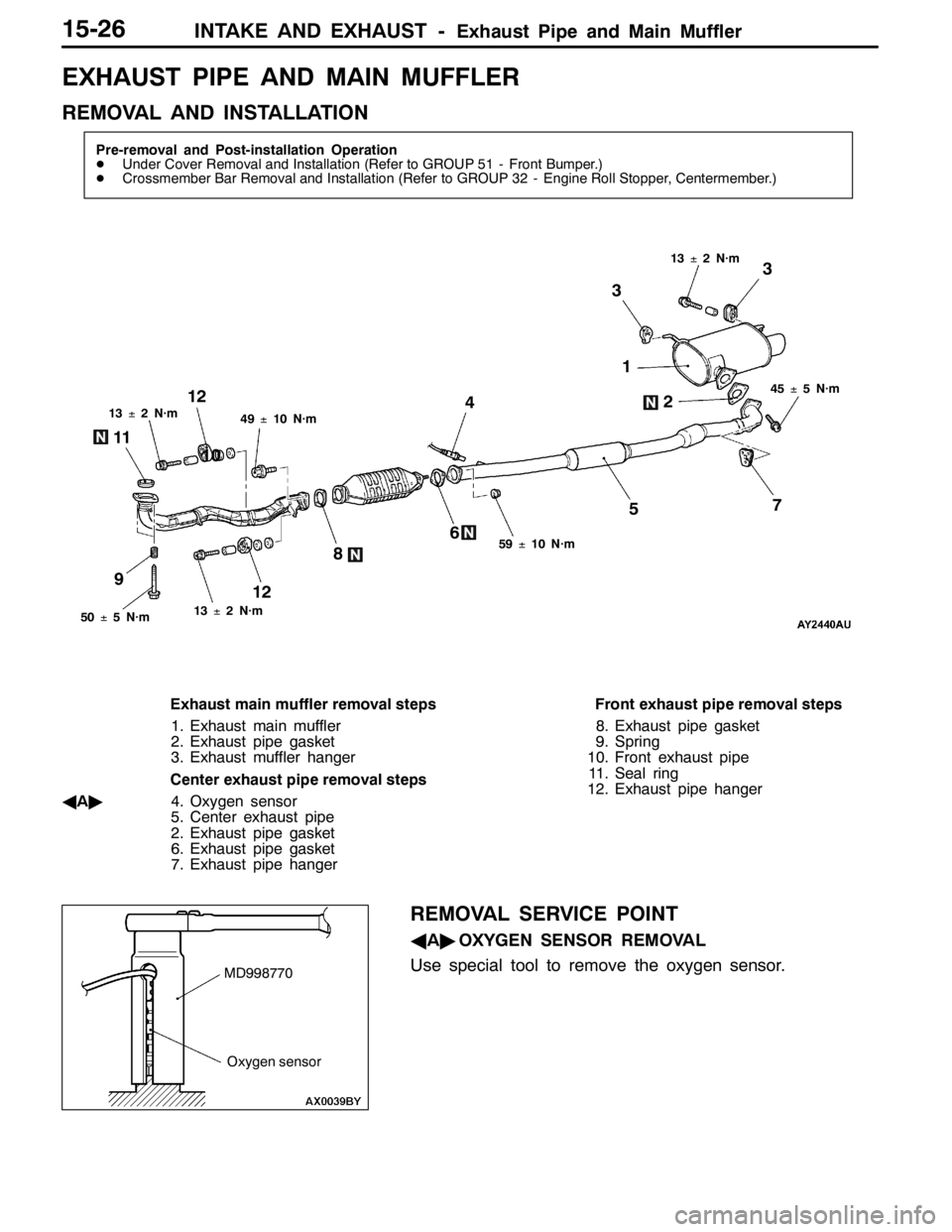
INTAKE AND EXHAUST -Exhaust Pipe and Main Muffler15-26
EXHAUST PIPE AND MAIN MUFFLER
REMOVAL AND INSTALLATION
Pre-removal and Post-installation Operation
DUnder Cover Removal and Installation (Refer to GROUP 51 - Front Bumper.)
DCrossmember Bar Removal and Installation (Refer to GROUP 32 - Engine Roll Stopper, Centermember.)
91
2 3
5
8
11
6 12
10
3
7
12
13±2 N·m
50±5 N·m13±2 N·m49±10 N·m
59±10 N·m13±2 N·m
45±5 N·m4
Exhaust main muffler removal steps
1. Exhaust main muffler
2. Exhaust pipe gasket
3. Exhaust muffler hanger
Center exhaust pipe removal steps
AA"4. Oxygen sensor
5. Center exhaust pipe
2. Exhaust pipe gasket
6. Exhaust pipe gasket
7. Exhaust pipe hangerFront exhaust pipe removal steps
8. Exhaust pipe gasket
9. Spring
10. Front exhaust pipe
11. Seal ring
12. Exhaust pipe hanger
REMOVAL SERVICE POINT
AA"OXYGEN SENSOR REMOVAL
Use special tool to remove the oxygen sensor.
MD998770
Oxygen sensor
Page 733 of 1449
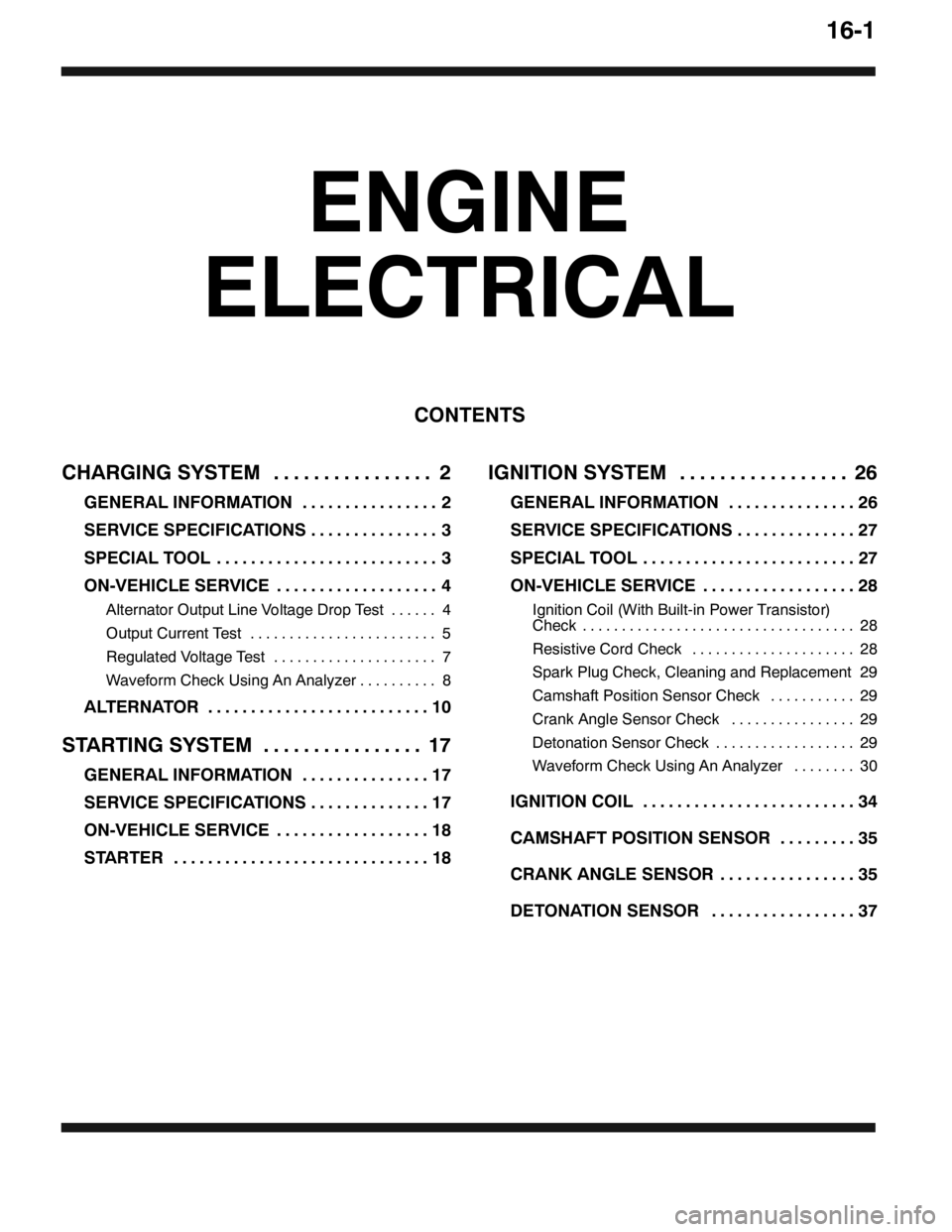
16-1
ENGINE
ELECTRICAL
CONTENTS
CHARGING SYSTEM 2................
GENERAL INFORMATION 2................
SERVICE SPECIFICATIONS 3...............
SPECIAL TOOL 3..........................
ON-VEHICLE SERVICE 4...................
Alternator Output Line Voltage Drop Test 4......
Output Current Test 5........................
Regulated Voltage Test 7.....................
Waveform Check Using An Analyzer 8..........
ALTERNATOR 10..........................
STARTING SYSTEM 17................
GENERAL INFORMATION 17...............
SERVICE SPECIFICATIONS 17..............
ON-VEHICLE SERVICE 18..................
STARTER 18..............................
IGNITION SYSTEM 26.................
GENERAL INFORMATION 26...............
SERVICE SPECIFICATIONS 27..............
SPECIAL TOOL 27.........................
ON-VEHICLE SERVICE 28..................
Ignition Coil (With Built-in Power Transistor)
Check 28...................................
Resistive Cord Check 28.....................
Spark Plug Check, Cleaning and Replacement 29
Camshaft Position Sensor Check 29...........
Crank Angle Sensor Check 29................
Detonation Sensor Check 29..................
Waveform Check Using An Analyzer 30........
IGNITION COIL 34.........................
CAMSHAFT POSITION SENSOR 35.........
CRANK ANGLE SENSOR 35................
DETONATION SENSOR 37.................
Page 743 of 1449

ENGINE ELECTRICAL -Charging System16-11
1
234
5
8.8±1.0 N·m 22±4 N·m
23±3 N·m11±1 N·m
13±1 N·m
8
(Engine oil)
679
10
20±2 N·m 36±6 N·m
1211
44±10 N·m
14±3 N·m
13
1415 18
1617
9.0±1.0 N·m
9.0±1.0 N·m5.0±1.0 N·m
Removal steps
1. Oil level gauge and guide assembly
2. O-ring
3. Fuel pressure solenoid valve
connector
4. Fuel pressure solenoid valve
assembly
5. Detonation sensor connector
6. Purge control solenoid valve
connector
7. Purge control solenoid valve assembly
8. Injector connector
AA"9. Delivery pipe, injector, and fuel
pressure regulator assembly10. Insulator
11. Insulator
AB"12. Drive belt
13. Alternator connector
DEngine mounting
(Refer to GROUP 32.)
AC"14. Alternator
15. Water pump pulley
16. Alternator brace
17. Oxygen sensor connector
18. Alternator brace stay
Page 758 of 1449
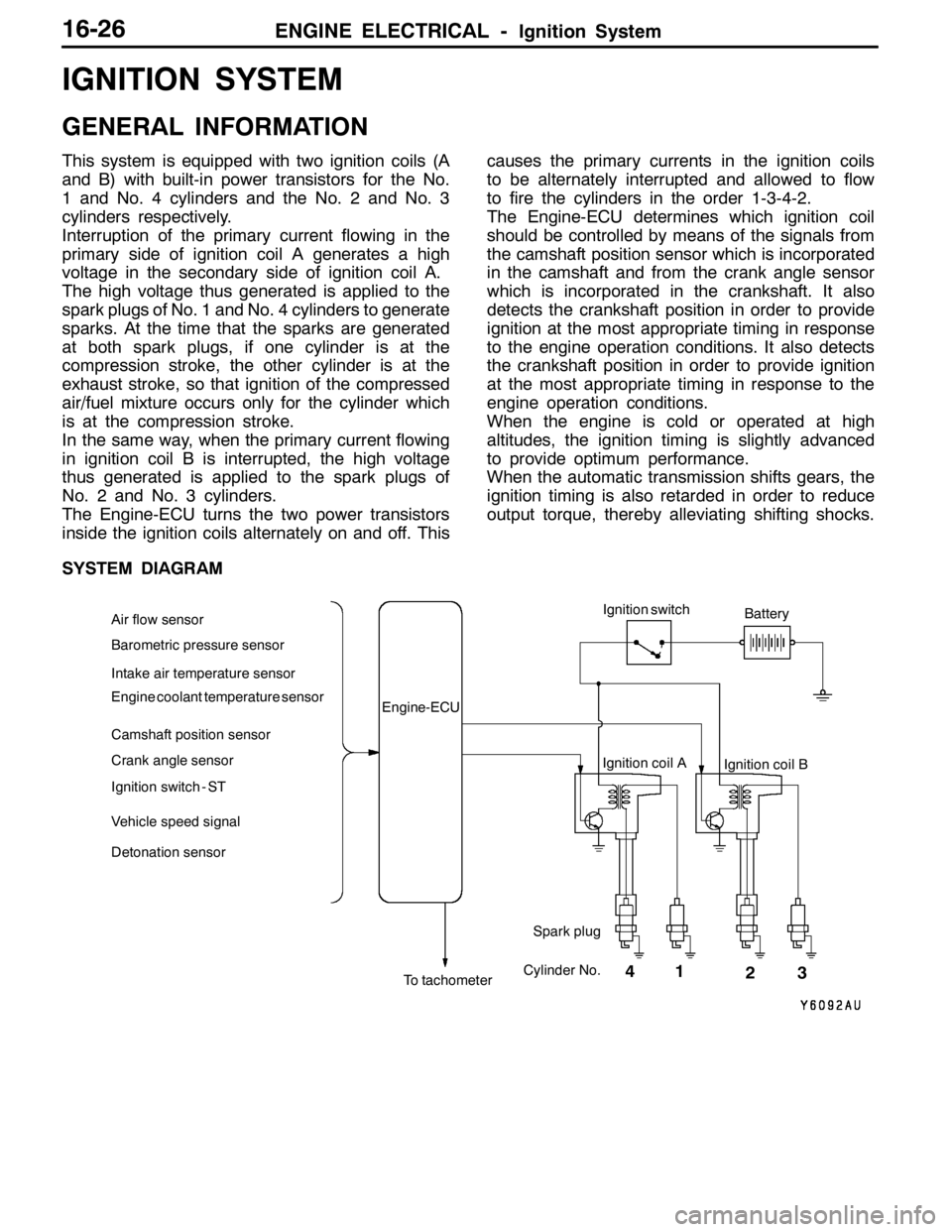
ENGINE ELECTRICAL -Ignition System16-26
IGNITION SYSTEM
GENERAL INFORMATION
This system is equipped with two ignition coils (A
and B) with built-in power transistors for the No.
1 and No. 4 cylinders and the No. 2 and No. 3
cylinders respectively.
Interruption of the primary current flowing in the
primary side of ignition coil A generates a high
voltage in the secondary side of ignition coil A.
The high voltage thus generated is applied to the
spark plugs of No. 1 and No. 4 cylinders to generate
sparks. At the time that the sparks are generated
at both spark plugs, if one cylinder is at the
compression stroke, the other cylinder is at the
exhaust stroke, so that ignition of the compressed
air/fuel mixture occurs only for the cylinder which
is at the compression stroke.
In the same way, when the primary current flowing
in ignition coil B is interrupted, the high voltage
thus generated is applied to the spark plugs of
No. 2 and No. 3 cylinders.
The Engine-ECU turns the two power transistors
inside the ignition coils alternately on and off. Thiscauses the primary currents in the ignition coils
to be alternately interrupted and allowed to flow
to fire the cylinders in the order 1-3-4-2.
The Engine-ECU determines which ignition coil
should be controlled by means of the signals from
the camshaft position sensor which is incorporated
in the camshaft and from the crank angle sensor
which is incorporated in the crankshaft. It also
detects the crankshaft position in order to provide
ignition at the most appropriate timing in response
to the engine operation conditions. It also detects
the crankshaft position in order to provide ignition
at the most appropriate timing in response to the
engine operation conditions.
When the engine is cold or operated at high
altitudes, the ignition timing is slightly advanced
to provide optimum performance.
When the automatic transmission shifts gears, the
ignition timing is also retarded in order to reduce
output torque, thereby alleviating shifting shocks.
SYSTEM DIAGRAM
Barometric pressure sensor
Intake air temperature sensor
Engine coolant temperature sensor
Camshaft position sensor
Crank angle sensor
Ignition switch - ST
Vehicle speed signalEngine-ECU
Ignition coil A
Ignition coil B Ignition switch
Spark plugBattery
To tachometerCylinder No. Air flow sensor
1 4
23
Detonation sensor
Page 759 of 1449
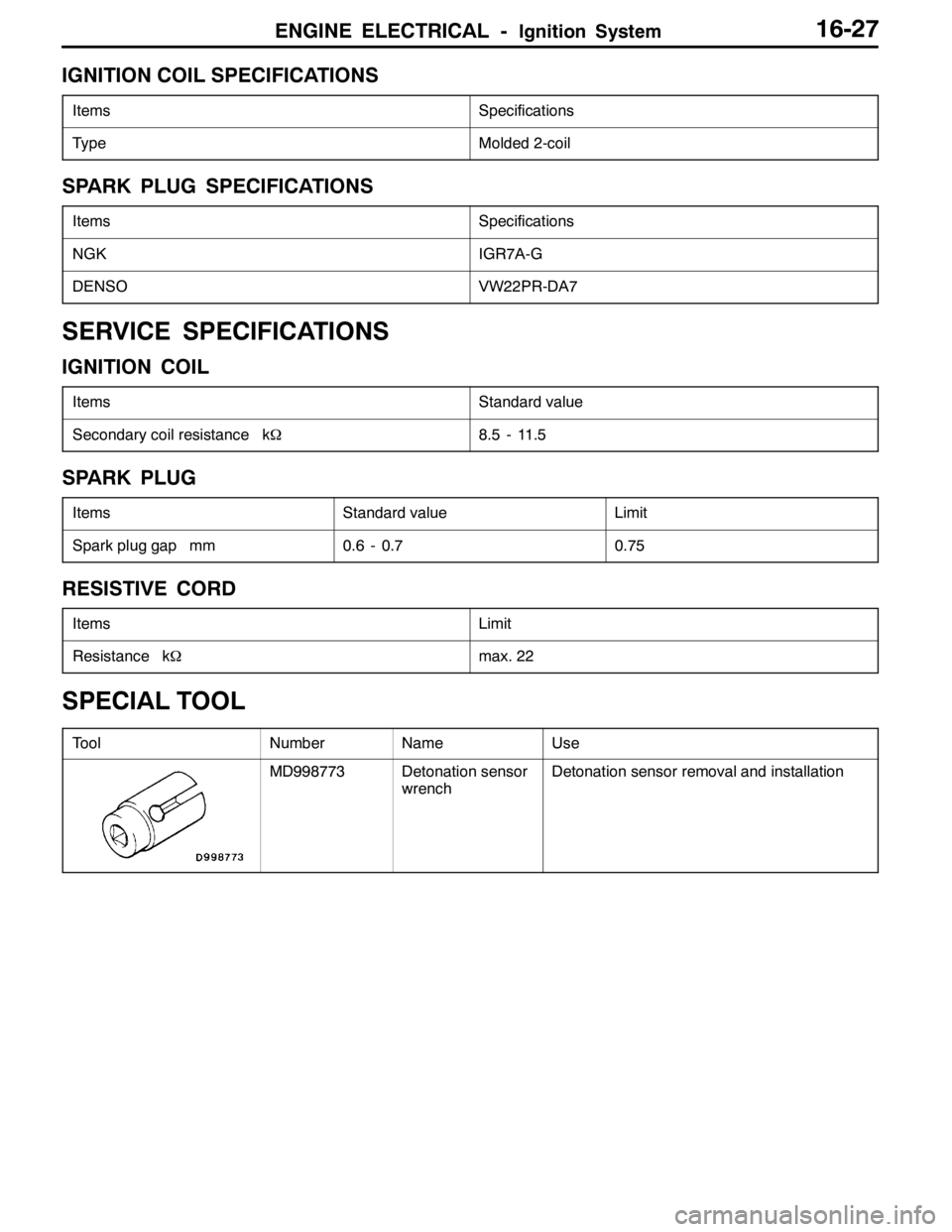
ENGINE ELECTRICAL -Ignition System16-27
IGNITION COIL SPECIFICATIONS
ItemsSpecifications
TypeMolded 2-coil
SPARK PLUG SPECIFICATIONS
ItemsSpecifications
NGKIGR7A-G
DENSOVW22PR-DA7
SERVICE SPECIFICATIONS
IGNITION COIL
ItemsStandard value
Secondary coil resistance kΩ8.5 - 11.5
SPARK PLUG
ItemsStandard valueLimit
Spark plug gap mm0.6 - 0.70.75
RESISTIVE CORD
ItemsLimit
Resistance kΩmax. 22
SPECIAL TOOL
ToolNumberNameUse
MD998773Detonation sensor
wrenchDetonation sensor removal and installation
Page 761 of 1449
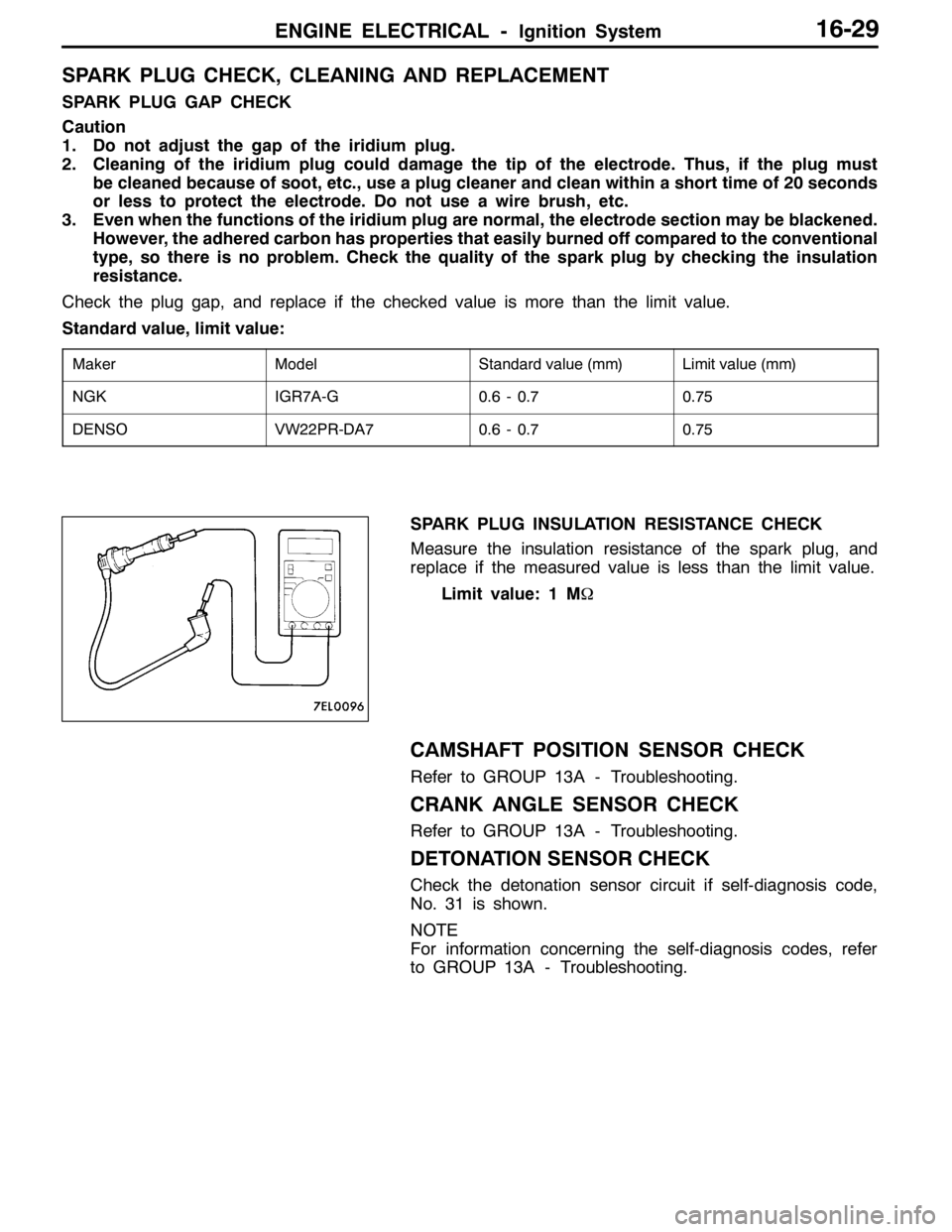
ENGINE ELECTRICAL -Ignition System16-29
SPARK PLUG CHECK, CLEANING AND REPLACEMENT
SPARK PLUG GAP CHECK
Caution
1. Do not adjust the gap of the iridium plug.
2. Cleaning of the iridium plug could damage the tip of the electrode. Thus, if the plug must
be cleaned because of soot, etc., use a plug cleaner and clean within a short time of 20 seconds
or less to protect the electrode. Do not use a wire brush, etc.
3. Even when the functions of the iridium plug are normal, the electrode section may be blackened.
However, the adhered carbon has properties that easily burned off compared to the conventional
type, so there is no problem. Check the quality of the spark plug by checking the insulation
resistance.
Check the plug gap, and replace if the checked value is more than the limit value.
Standard value, limit value:
MakerModelStandard value (mm)Limit value (mm)
NGKIGR7A-G0.6 - 0.70.75
DENSOVW22PR-DA70.6 - 0.70.75
SPARK PLUG INSULATION RESISTANCE CHECK
Measure the insulation resistance of the spark plug, and
replace if the measured value is less than the limit value.
Limit value: 1 MΩ
CAMSHAFT POSITION SENSOR CHECK
Refer to GROUP 13A - Troubleshooting.
CRANK ANGLE SENSOR CHECK
Refer to GROUP 13A - Troubleshooting.
DETONATION SENSOR CHECK
Check the detonation sensor circuit if self-diagnosis code,
No. 31 is shown.
NOTE
For information concerning the self-diagnosis codes, refer
to GROUP 13A - Troubleshooting.
Page 767 of 1449
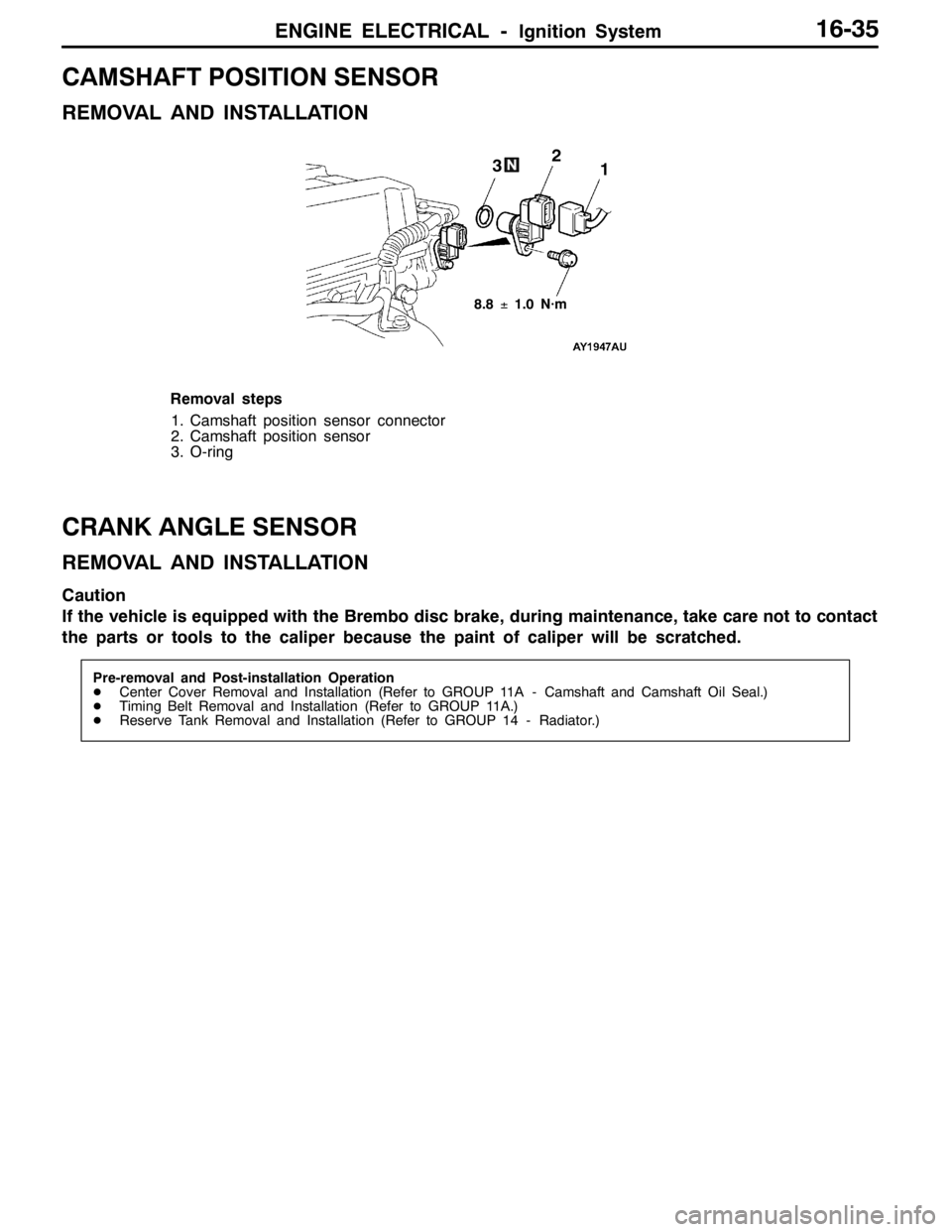
ENGINE ELECTRICAL -Ignition System16-35
CAMSHAFT POSITION SENSOR
REMOVAL AND INSTALLATION
1 2
3
8.8±1.0 N·m
Removal steps
1. Camshaft position sensor connector
2. Camshaft position sensor
3. O-ring
CRANK ANGLE SENSOR
REMOVAL AND INSTALLATION
Caution
If the vehicle is equipped with the Brembo disc brake, during maintenance, take care not to contact
the parts or tools to the caliper because the paint of caliper will be scratched.
Pre-removal and Post-installation Operation
DCenter Cover Removal and Installation (Refer to GROUP 11A - Camshaft and Camshaft Oil Seal.)
DTiming Belt Removal and Installation (Refer to GROUP 11A.)
DReserve Tank Removal and Installation (Refer to GROUP 14 - Radiator.)