sensor MITSUBISHI LANCER EVOLUTION 2007 Service Repair Manual
[x] Cancel search | Manufacturer: MITSUBISHI, Model Year: 2007, Model line: LANCER EVOLUTION, Model: MITSUBISHI LANCER EVOLUTION 2007Pages: 1449, PDF Size: 56.82 MB
Page 642 of 1449

MPI -Troubleshooting13A-110
Terminal No.Normal condition Check condition (Engine condition) Check item
12Power supplyIgnition switch: “ON”System voltage
25
19Air flow sensor reset
signal
Engine: Idle operation0-1V
signal
Engine speed: 3,000 r/min6-9V
21Fan controllerRadiator fan is not operating0 - 0.3 V
Radiator fan is operating0.7 V or more
22Fuel pump relay 2Ignition switch: “ON”System voltage
Engine: Idle operation1 V or less
24A/C load signalDEngine:
Idle operation
DA/C switch: ON
(A/C compressor
runs)DOutdoor air
sensor ambient
temperature:
18_C or more
DA/C setting
temperature:
Minimum
temperature
DA/C air volume:
Maximum1 V or less
DA/C setting
temperature:
indoor
temperature
DA/C air volume:
MinimumSystem voltage
32Condenser fan motor
relay (HI)Fan inactive state
(Engine coolant temperature: 90_C or less)System voltage
Fan high-speed rotation state
(Engine coolant temperature: 105_C or more)1 V or less
33Alternator G terminalDEngine: After warm-up, idle operation
DRadiator fan: Not operating
DHeadlamp: OFF→ON
DStop lamp: OFF→ON
DRear defogger switch: OFF→ONVoltage increases by
0.2 - 3.5 V
34Condenser fan motor
relay (LOW)Fan inactive state
(Engine coolant temperature: 90_C or less)System voltage
Fan low-speed rotation state (Engine coolant
temperature: 95 - 100_C or more)1 V or less
35Intercooler water
spraylamp
Ignition switch: “ON”System voltage
spraylamp
Ignition switch: “LOCK” (OFF)1 V or less
36Engine warning lampIgnition switch: “LOCK” (OFF)→“ON”1 V or less→System
voltage (After several se-
conds have elapsed)
Page 643 of 1449
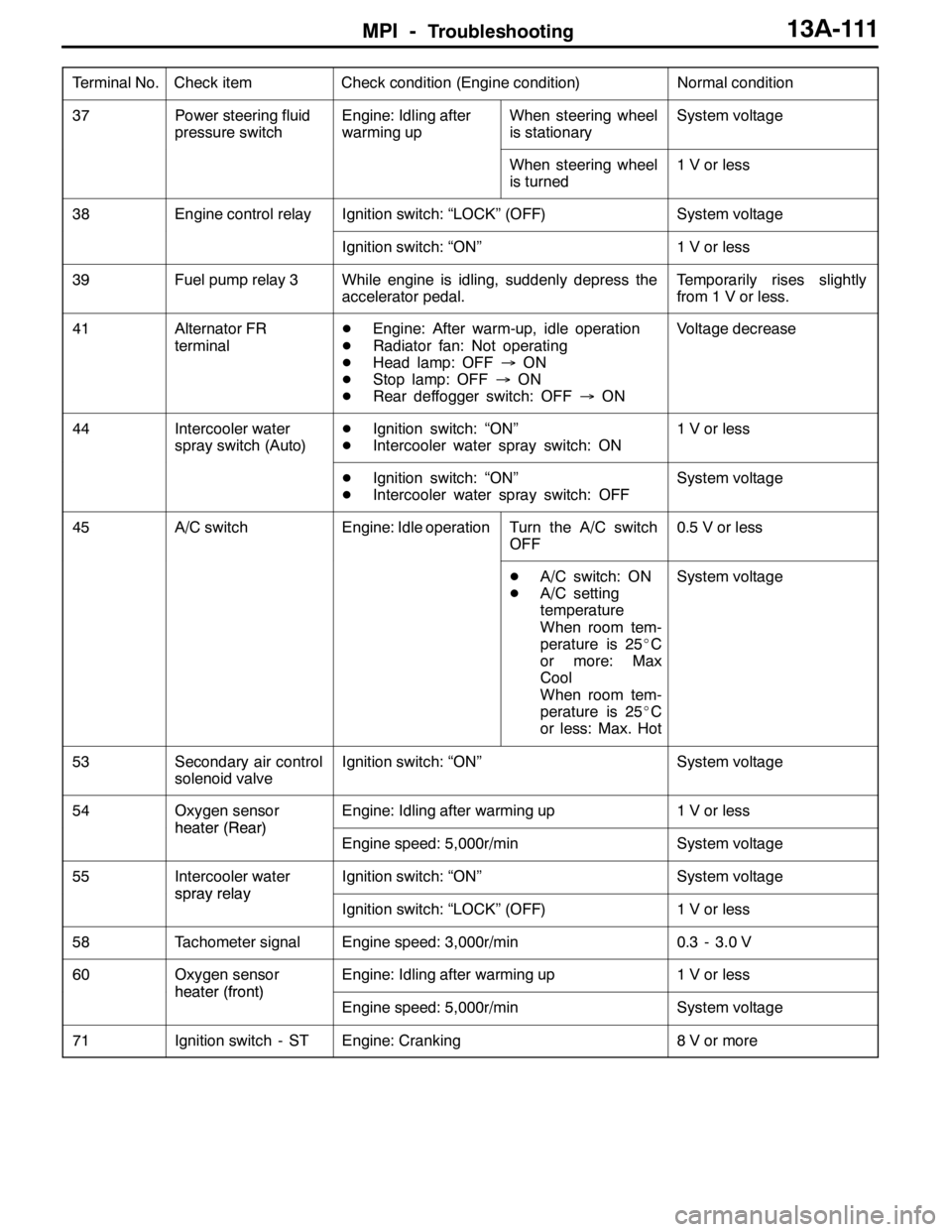
MPI -Troubleshooting13A-111
Terminal No.Normal condition Check condition (Engine condition) Check item
37Power steering fluid
pressure switchEngine: Idling after
warming upWhen steering wheel
is stationarySystem voltage
When steering wheel
is turned1 V or less
38Engine control relayIgnition switch: “LOCK” (OFF)System voltage
Ignition switch: “ON”1 V or less
39Fuel pump relay 3While engine is idling, suddenly depress the
accelerator pedal.Temporarily rises slightly
from 1 V or less.
41Alternator FR
terminalDEngine: After warm-up, idle operation
DRadiator fan: Not operating
DHead lamp: OFF→ON
DStop lamp: OFF→ON
DRear deffogger switch: OFF→ONVoltage decrease
44Intercooler water
spray switch (Auto)DIgnition switch: “ON”
DIntercooler water spray switch: ON1 V or less
DIgnition switch: “ON”
DIntercooler water spray switch: OFFSystem voltage
45A/C switchEngine: Idle operationTurn the A/C switch
OFF0.5 V or less
DA/C switch: ON
DA/C setting
temperature
When room tem-
perature is 25_C
or more: Max
Cool
When room tem-
perature is 25_C
or less: Max. HotSystem voltage
53Secondary air control
solenoid valveIgnition switch: “ON”System voltage
54Oxygen sensor
heater(Rear)
Engine: Idling after warming up1 V or less
heater(Rear)
Engine speed: 5,000r/minSystem voltage
55Intercooler water
sprayrelay
Ignition switch: “ON”System voltage
spray relay
Ignition switch: “LOCK” (OFF)1 V or less
58Tachometer signalEngine speed: 3,000r/min0.3 - 3.0 V
60Oxygen sensor
heater(front)
Engine: Idling after warming up1 V or less
heater(front)
Engine speed: 5,000r/minSystem voltage
71Ignition switch - STEngine: Cranking8 V or more
Page 644 of 1449
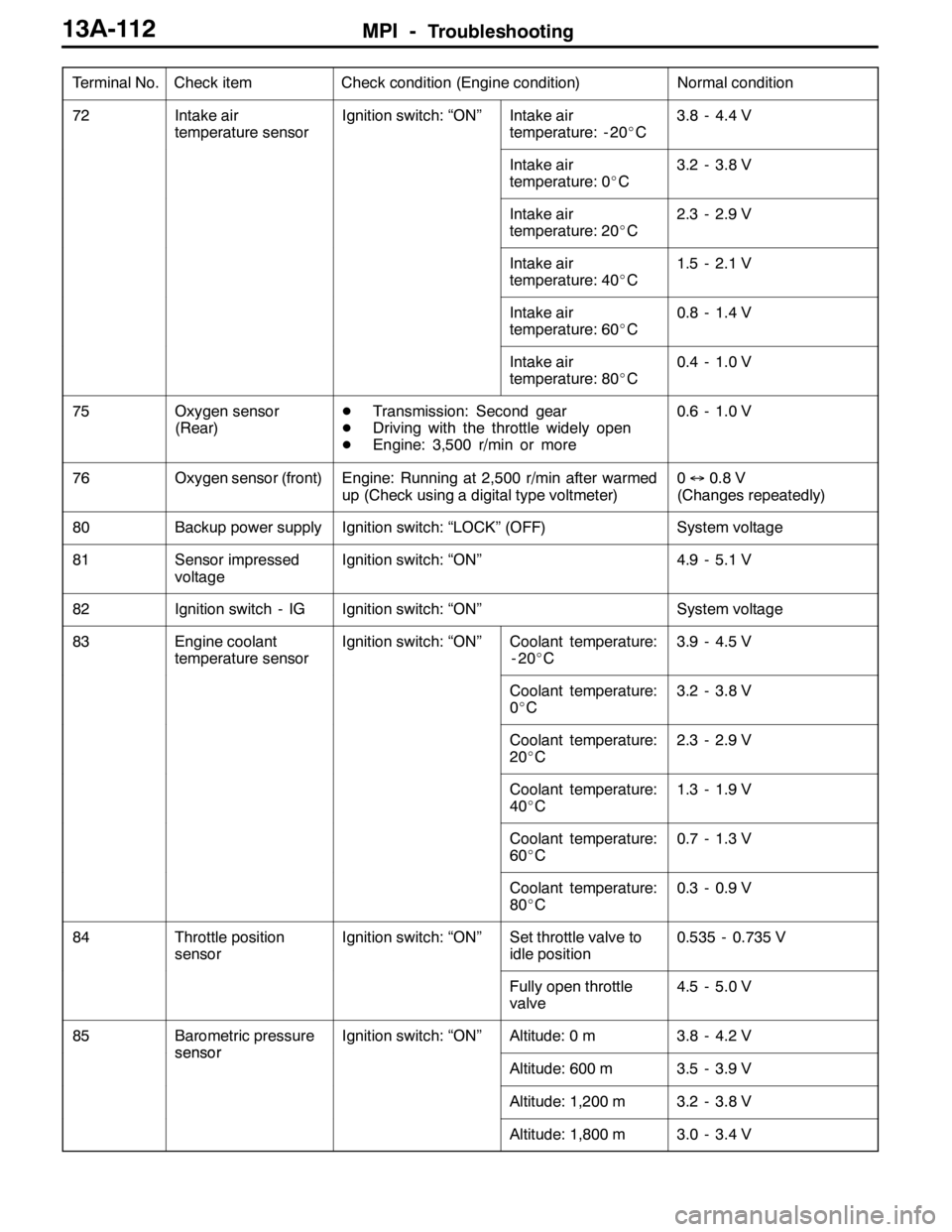
MPI -Troubleshooting13A-112
Terminal No.Normal condition Check condition (Engine condition) Check item
72Intake air
temperature sensorIgnition switch: “ON”Intake air
temperature: - 20_C3.8 - 4.4 V
Intake air
temperature: 0_C3.2 - 3.8 V
Intake air
temperature: 20_C2.3 - 2.9 V
Intake air
temperature: 40_C1.5 - 2.1 V
Intake air
temperature: 60_C0.8 - 1.4 V
Intake air
temperature: 80_C0.4 - 1.0 V
75Oxygen sensor
(Rear)DTransmission: Second gear
DDriving with the throttle widely open
DEngine: 3,500 r/min or more0.6 - 1.0 V
76Oxygen sensor (front)Engine: Running at 2,500 r/min after warmed
up (Check using a digital type voltmeter)0↔0.8 V
(Changes repeatedly)
80Backup power supplyIgnition switch: “LOCK” (OFF)System voltage
81Sensor impressed
voltageIgnition switch: “ON”4.9 - 5.1 V
82Ignition switch - IGIgnition switch: “ON”System voltage
83Engine coolant
temperature sensorIgnition switch: “ON”Coolant temperature:
-20_C3.9 - 4.5 V
Coolant temperature:
0_C3.2 - 3.8 V
Coolant temperature:
20_C2.3 - 2.9 V
Coolant temperature:
40_C1.3 - 1.9 V
Coolant temperature:
60_C0.7 - 1.3 V
Coolant temperature:
80_C0.3 - 0.9 V
84Throttle position
sensorIgnition switch: “ON”Set throttle valve to
idle position0.535 - 0.735 V
Fully open throttle
valve4.5 - 5.0 V
85Barometric pressure
sensor
Ignition switch: “ON”Altitude: 0 m3.8 - 4.2 V
sensor
Altitude: 600 m3.5 - 3.9 V
Altitude: 1,200 m3.2 - 3.8 V
Altitude: 1,800 m3.0 - 3.4 V
Page 645 of 1449
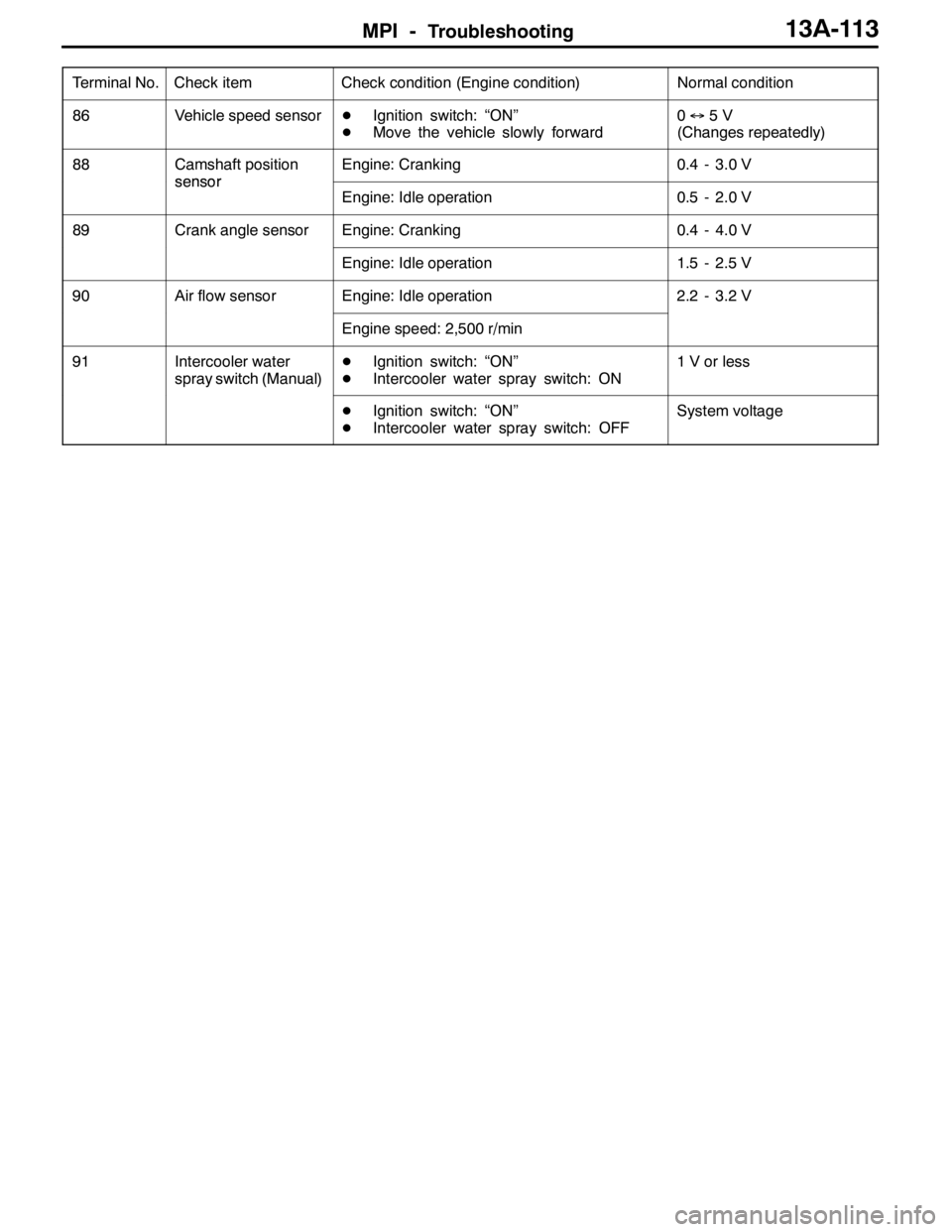
MPI -Troubleshooting13A-113
Terminal No.Normal condition Check condition (Engine condition) Check item
86Vehicle speed sensorDIgnition switch: “ON”
DMove the vehicle slowly forward0↔5V
(Changes repeatedly)
88Camshaft position
sensor
Engine: Cranking0.4 - 3.0 V
sensor
Engine: Idle operation0.5 - 2.0 V
89Crank angle sensorEngine: Cranking0.4 - 4.0 V
Engine: Idle operation1.5 - 2.5 V
90Air flow sensorEngine: Idle operation2.2 - 3.2 V
Engine speed: 2,500 r/min
91Intercooler water
spray switch (Manual)DIgnition switch: “ON”
DIntercooler water spray switch: ON1 V or less
DIgnition switch: “ON”
DIntercooler water spray switch: OFFSystem voltage
Page 646 of 1449
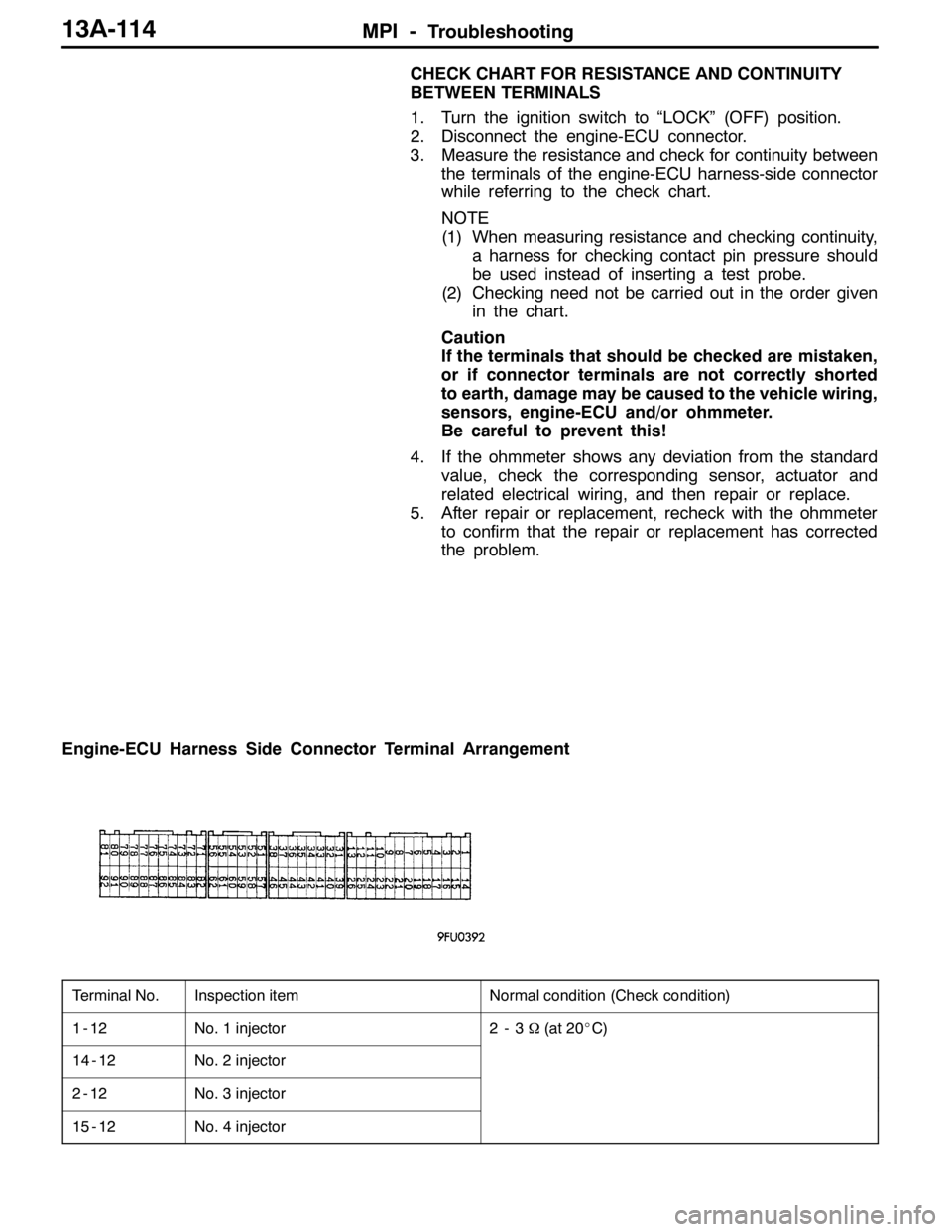
MPI -Troubleshooting13A-114
CHECK CHART FOR RESISTANCE AND CONTINUITY
BETWEEN TERMINALS
1. Turn the ignition switch to “LOCK” (OFF) position.
2. Disconnect the engine-ECU connector.
3. Measure the resistance and check for continuity between
the terminals of the engine-ECU harness-side connector
while referring to the check chart.
NOTE
(1) When measuring resistance and checking continuity,
a harness for checking contact pin pressure should
be used instead of inserting a test probe.
(2) Checking need not be carried out in the order given
in the chart.
Caution
If the terminals that should be checked are mistaken,
or if connector terminals are not correctly shorted
to earth, damage may be caused to the vehicle wiring,
sensors, engine-ECU and/or ohmmeter.
Be careful to prevent this!
4. If the ohmmeter shows any deviation from the standard
value, check the corresponding sensor, actuator and
related electrical wiring, and then repair or replace.
5. After repair or replacement, recheck with the ohmmeter
to confirm that the repair or replacement has corrected
the problem.
Engine-ECU Harness Side Connector Terminal Arrangement
Terminal No.Inspection itemNormal condition (Check condition)
1-12No. 1 injector2-3Ω(at 20_C)
14 - 12No. 2 injector
2-12No. 3 injector
15 - 12No. 4 injector
Page 647 of 1449
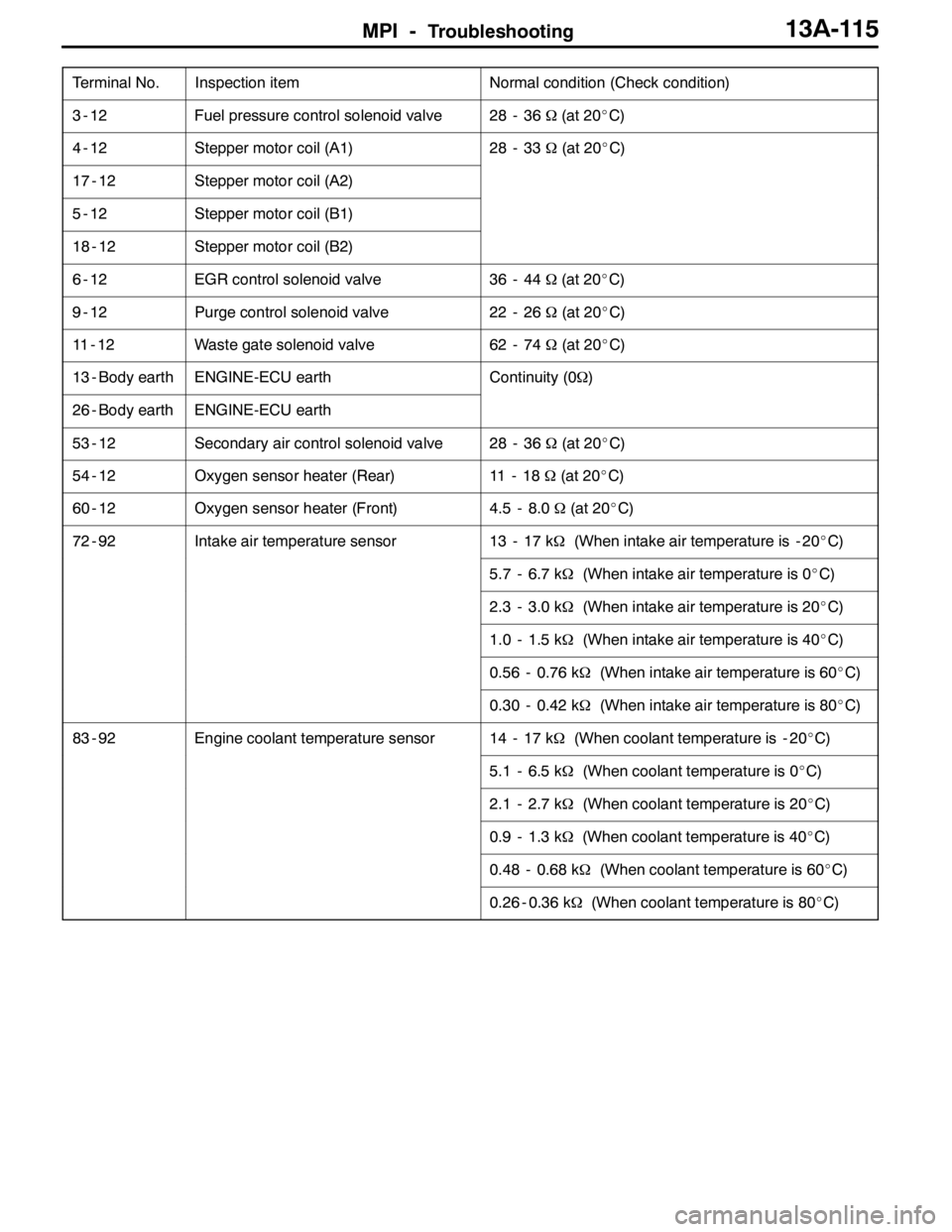
MPI -Troubleshooting13A-115
Terminal No. Normal condition (Check condition)Inspection item
3-12Fuel pressure control solenoid valve28 - 36Ω(at 20_C)
4-12Stepper motor coil (A1)28 - 33Ω(at 20_C)
17 - 12Stepper motor coil (A2)
5-12Stepper motor coil (B1)
18 - 12Stepper motor coil (B2)
6-12EGR control solenoid valve36 - 44Ω(at 20_C)
9-12Purge control solenoid valve22 - 26Ω(at 20_C)
11 - 1 2Waste gate solenoid valve62 - 74Ω(at 20_C)
13 - Body earthENGINE-ECU earthContinuity (0Ω)
26 - Body earthENGINE-ECU earth
53 - 12Secondary air control solenoid valve28 - 36Ω(at 20_C)
54 - 12Oxygen sensor heater (Rear)11 - 1 8Ω(at 20_C)
60 - 12Oxygen sensor heater (Front)4.5 - 8.0Ω(at 20_C)
72 - 92Intake air temperature sensor13 - 17 kΩ(When intake air temperature is - 20_C)
5.7 - 6.7 kΩ(When intake air temperature is 0_C)
2.3 - 3.0 kΩ(When intake air temperature is 20_C)
1.0 - 1.5 kΩ(When intake air temperature is 40_C)
0.56 - 0.76 kΩ(When intake air temperature is 60_C)
0.30 - 0.42 kΩ(When intake air temperature is 80_C)
83 - 92Engine coolant temperature sensor14 - 17 kΩ(When coolant temperature is - 20_C)
5.1 - 6.5 kΩ(When coolant temperature is 0_C)
2.1 - 2.7 kΩ(When coolant temperature is 20_C)
0.9 - 1.3 kΩ(When coolant temperature is 40_C)
0.48 - 0.68 kΩ(When coolant temperature is 60_C)
0.26 - 0.36 kΩ(When coolant temperature is 80_C)
Page 648 of 1449
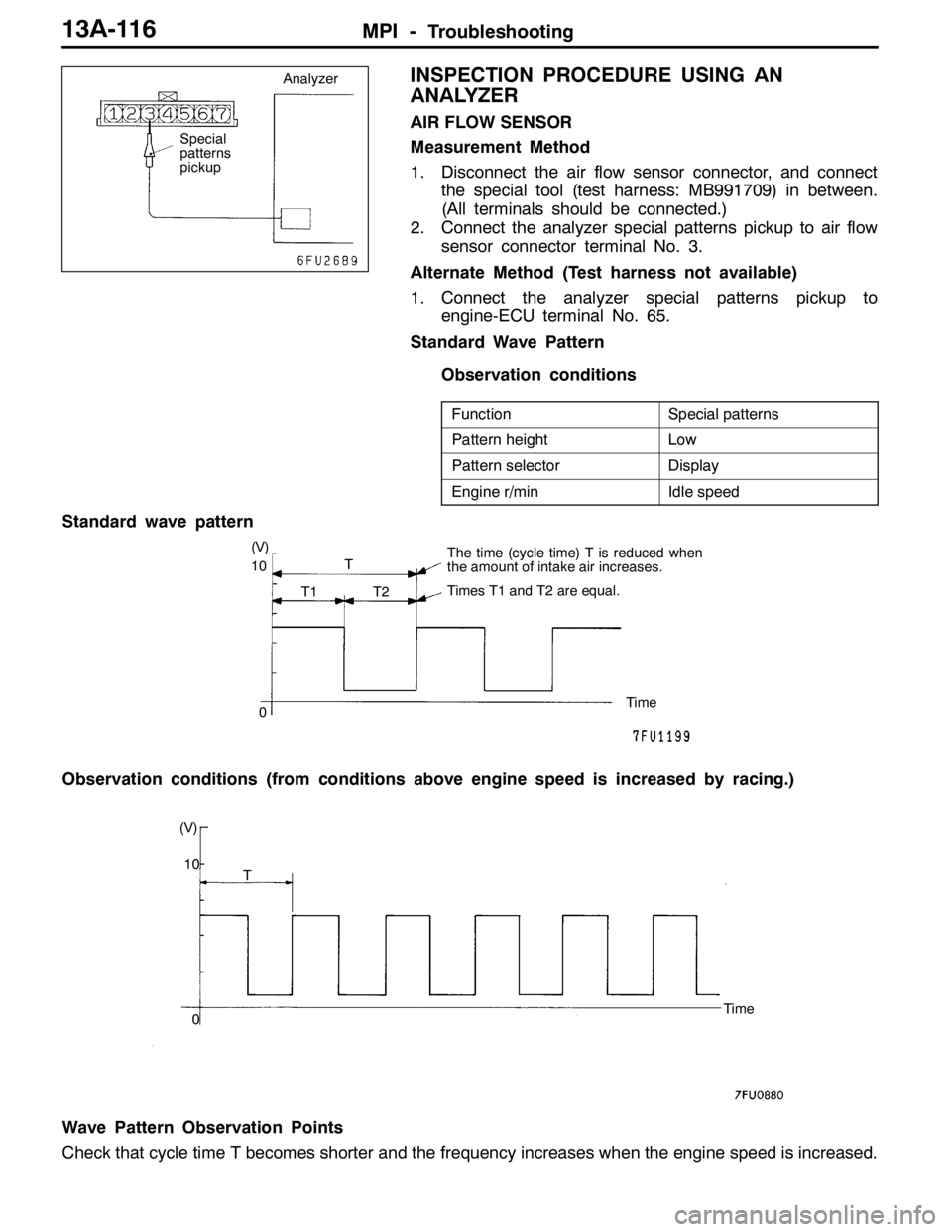
MPI -Troubleshooting13A-116
INSPECTION PROCEDURE USING AN
ANALYZER
AIR FLOW SENSOR
Measurement Method
1. Disconnect the air flow sensor connector, and connect
the special tool (test harness: MB991709) in between.
(All terminals should be connected.)
2. Connect the analyzer special patterns pickup to air flow
sensor connector terminal No. 3.
Alternate Method (Test harness not available)
1. Connect the analyzer special patterns pickup to
engine-ECU terminal No. 65.
Standard Wave Pattern
Observation conditions
FunctionSpecial patterns
Pattern heightLow
Pattern selectorDisplay
Engine r/minIdle speed
Standard wave pattern
(V)
10
0The time (cycle time) T is reduced when
the amount of intake air increases.
Times T1 and T2 are equal.
Time T
T1 T2
Observation conditions (from conditions above engine speed is increased by racing.)
Time (V)
10
0T
Wave Pattern Observation Points
Check that cycle time T becomes shorter and the frequency increases when the engine speed is increased.
Analyzer
Special
patterns
pickup
Page 649 of 1449
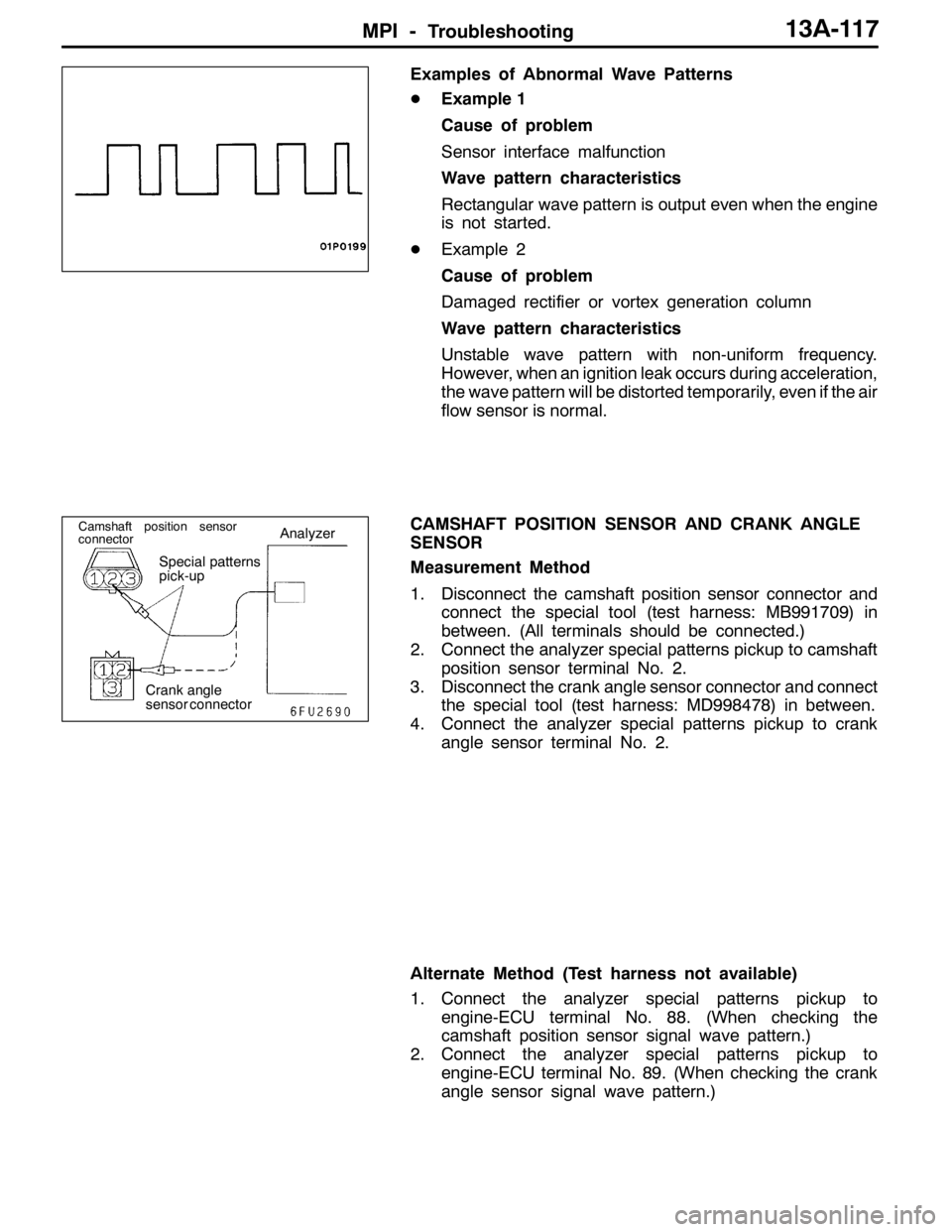
MPI -Troubleshooting13A-117
Examples of Abnormal Wave Patterns
DExample 1
Cause of problem
Sensor interface malfunction
Wave pattern characteristics
Rectangular wave pattern is output even when the engine
is not started.
DExample 2
Cause of problem
Damaged rectifier or vortex generation column
Wave pattern characteristics
Unstable wave pattern with non-uniform frequency.
However, when an ignition leak occurs during acceleration,
the wave pattern will be distorted temporarily, even if the air
flow sensor is normal.
CAMSHAFT POSITION SENSOR AND CRANK ANGLE
SENSOR
Measurement Method
1. Disconnect the camshaft position sensor connector and
connect the special tool (test harness: MB991709) in
between. (All terminals should be connected.)
2. Connect the analyzer special patterns pickup to camshaft
position sensor terminal No. 2.
3. Disconnect the crank angle sensor connector and connect
the special tool (test harness: MD998478) in between.
4. Connect the analyzer special patterns pickup to crank
angle sensor terminal No. 2.
Alternate Method (Test harness not available)
1. Connect the analyzer special patterns pickup to
engine-ECU terminal No. 88. (When checking the
camshaft position sensor signal wave pattern.)
2. Connect the analyzer special patterns pickup to
engine-ECU terminal No. 89. (When checking the crank
angle sensor signal wave pattern.)
Crank angle
sensor connector
Camshaft position sensor
connectorAnalyzer
Special patterns
pick-up
Page 650 of 1449
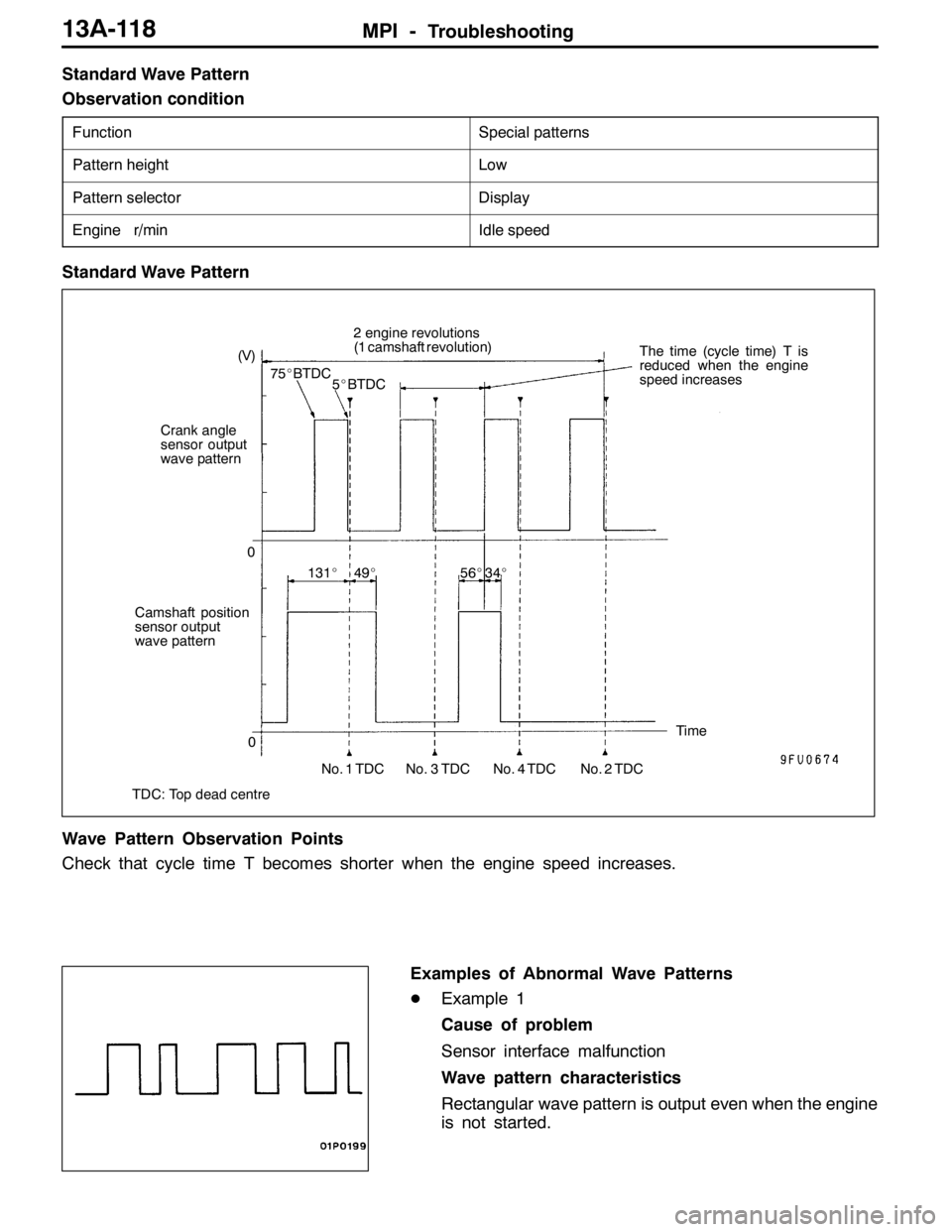
MPI -Troubleshooting13A-118
Standard Wave Pattern
Observation condition
FunctionSpecial patterns
Pattern heightLow
Pattern selectorDisplay
Engine r/minIdle speed
Standard Wave Pattern
Crank angle
sensor output
wave pattern(V)
75_BTDC2 engine revolutions
(1 camshaft revolution)
5_BTDCThe time (cycle time) T is
reduced when the engine
speed increases
0
Camshaft position
sensor output
wave pattern
TDC: Top dead centre131_49_
No. 1 TDC No. 3 TDC No. 4 TDC No. 2 TDCTime
056_34_
Wave Pattern Observation Points
Check that cycle time T becomes shorter when the engine speed increases.
Examples of Abnormal Wave Patterns
DExample 1
Cause of problem
Sensor interface malfunction
Wave pattern characteristics
Rectangular wave pattern is output even when the engine
is not started.
Page 651 of 1449
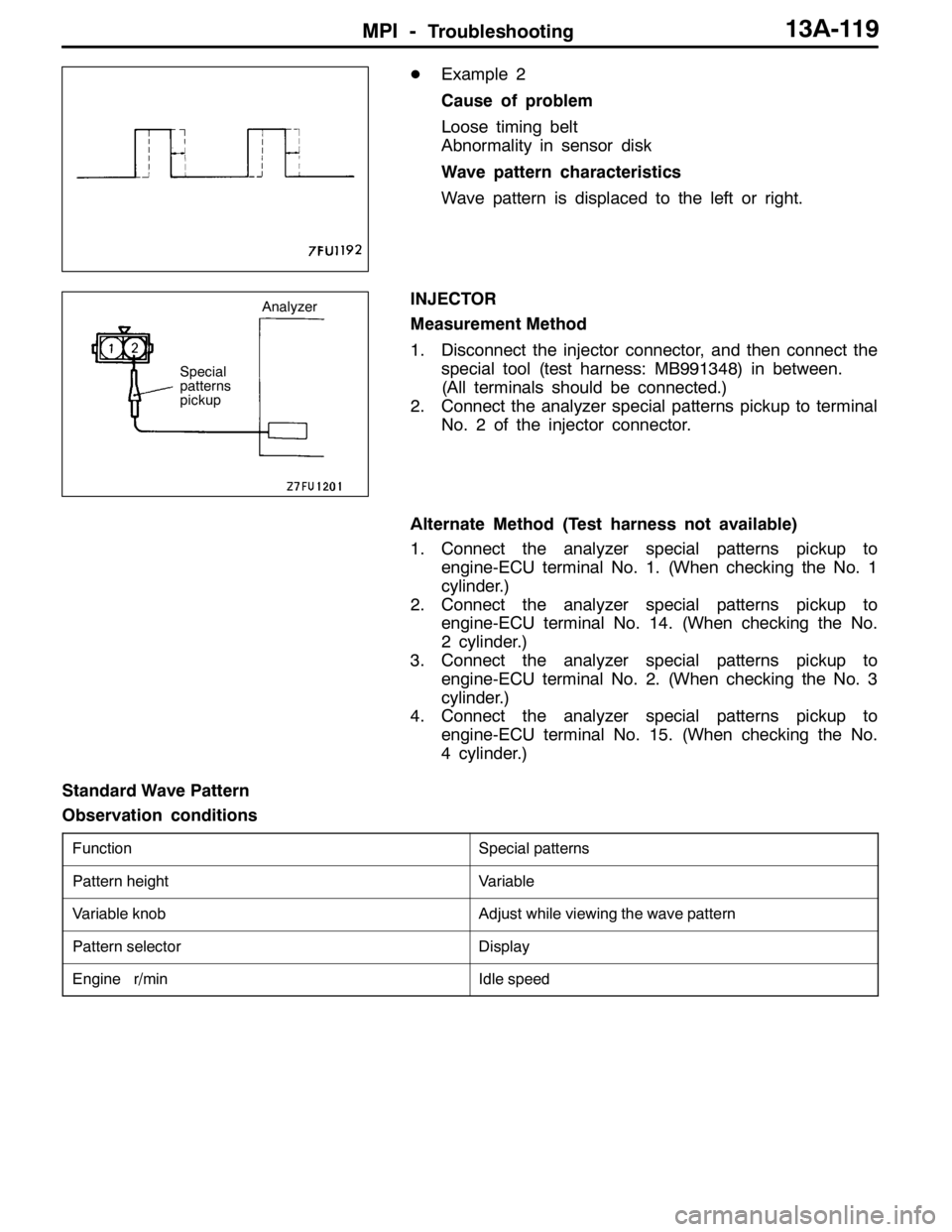
MPI -Troubleshooting13A-119
DExample 2
Cause of problem
Loose timing belt
Abnormality in sensor disk
Wave pattern characteristics
Wave pattern is displaced to the left or right.
INJECTOR
Measurement Method
1. Disconnect the injector connector, and then connect the
special tool (test harness: MB991348) in between.
(All terminals should be connected.)
2. Connect the analyzer special patterns pickup to terminal
No. 2 of the injector connector.
Alternate Method (Test harness not available)
1. Connect the analyzer special patterns pickup to
engine-ECU terminal No. 1. (When checking the No. 1
cylinder.)
2. Connect the analyzer special patterns pickup to
engine-ECU terminal No. 14. (When checking the No.
2 cylinder.)
3. Connect the analyzer special patterns pickup to
engine-ECU terminal No. 2. (When checking the No. 3
cylinder.)
4. Connect the analyzer special patterns pickup to
engine-ECU terminal No. 15. (When checking the No.
4 cylinder.)
Standard Wave Pattern
Observation conditions
FunctionSpecial patterns
Pattern heightVariable
Variable knobAdjust while viewing the wave pattern
Pattern selectorDisplay
Engine r/minIdle speed
Special
patterns
pickupAnalyzer