sensor MITSUBISHI LANCER EVOLUTION 2007 Service Repair Manual
[x] Cancel search | Manufacturer: MITSUBISHI, Model Year: 2007, Model line: LANCER EVOLUTION, Model: MITSUBISHI LANCER EVOLUTION 2007Pages: 1449, PDF Size: 56.82 MB
Page 846 of 1449
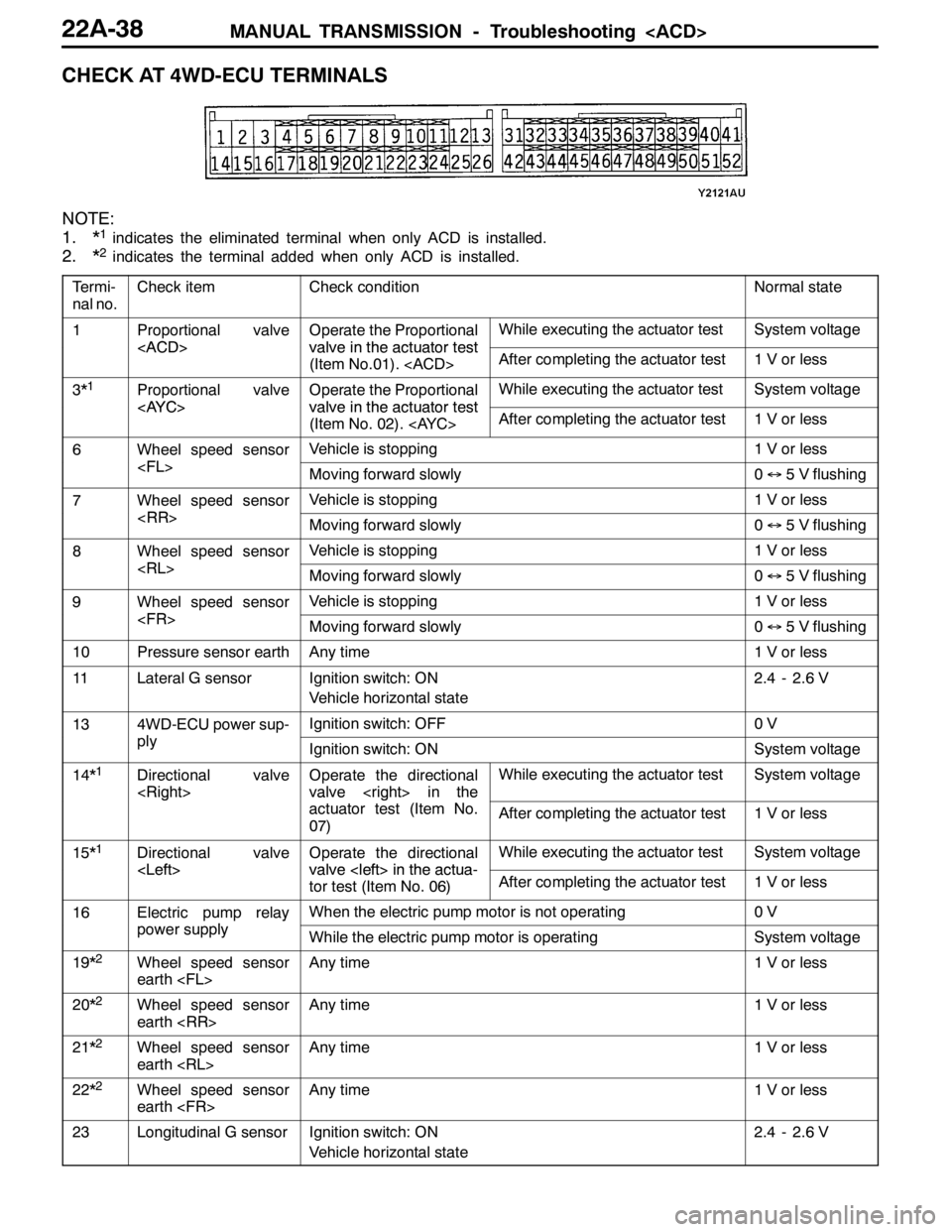
MANUAL TRANSMISSION - Troubleshooting
CHECK AT 4WD-ECU TERMINALS
NOTE:
1. *1indicates the eliminated terminal when only ACD is installed.
2. *2indicates the terminal added when only ACD is installed.
Termi-
nal no.
Check itemCheck conditionNormal state
1Proportional valve
Operate the Proportional
valveintheactuatortest
While executing the actuator testSystem voltage
(Item No.01).
3*1Proportional valve
Operate the Proportional
valveintheactuatortest
While executing the actuator testSystem voltage
(Item No. 02).
6Wheel speed sensor
FL
Vehicle is stopping1 V or lessp
7Wheel speed sensor
RR
Vehicle is stopping1 V or lessp
8Wheel speed sensor
RL
Vehicle is stopping1 V or lessp
9Wheel speed sensor
FR
Vehicle is stopping1 V or lessp
10Pressure sensor earthAny time1 V or less
11Lateral G sensorIgnition switch: ON
Vehicle horizontal state2.4 - 2.6 V
134WD-ECU power sup-
l
Ignition switch: OFF0Vpp
plyIgnition switch: ONSystem voltage
14*1Directional valve
valve
actuator test (Item No.
07)After completing the actuator test1 V or less
15*1Directional valve
Operate the directional
valve
While executing the actuator testSystem voltage
tor test (Item No. 06)After completing the actuator test1 V or less
16Electric pump relay
l
When the electric pump motor is not operating0Vppy
power supplyWhile the electric pump motor is operatingSystem voltage
19*2Wheel speed sensor
earth
20*2Wheel speed sensor
earth
21*2Wheel speed sensor
earth
22*2Wheel speed sensor
earth
23Longitudinal G sensorIgnition switch: ON
Vehicle horizontal state2.4 - 2.6 V
Page 847 of 1449
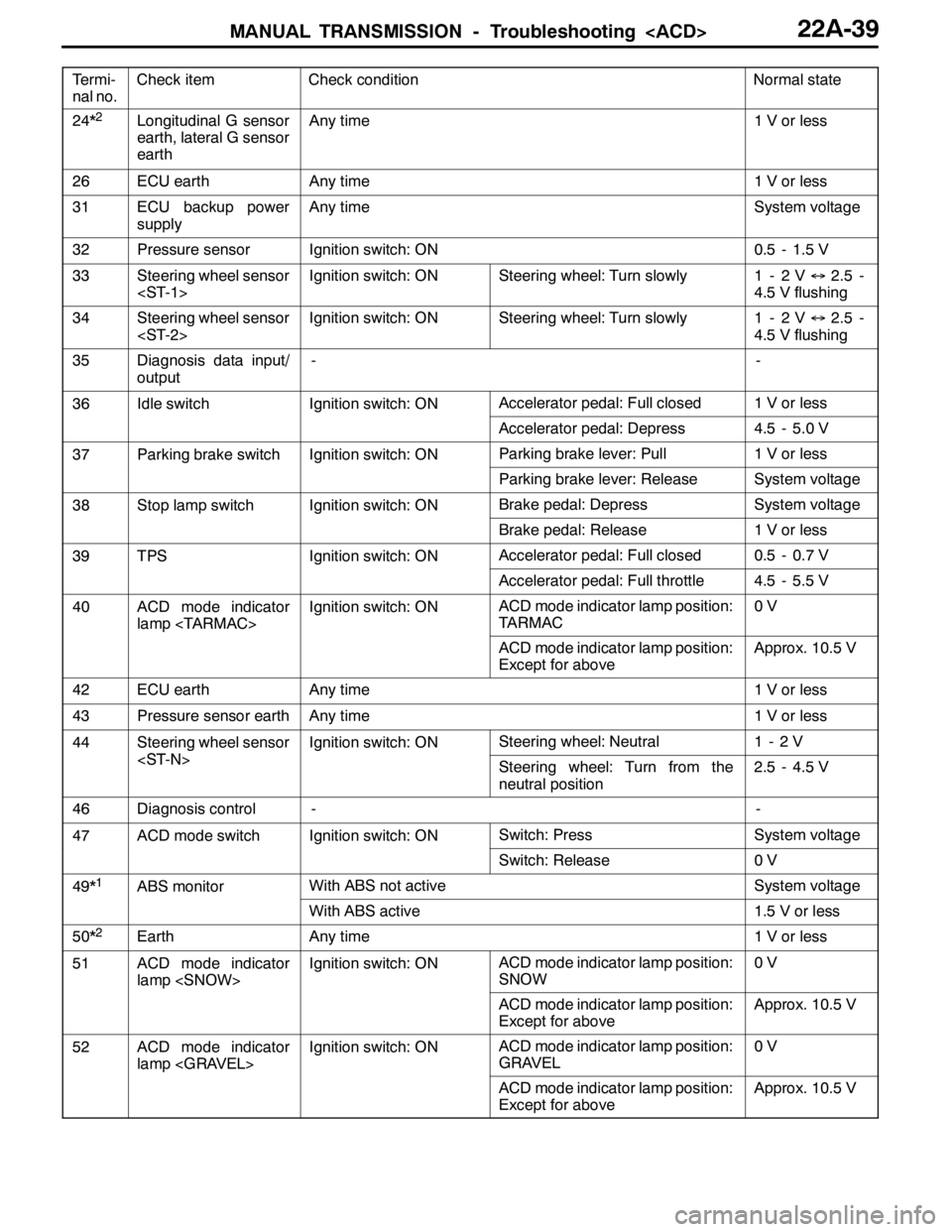
MANUAL TRANSMISSION - Troubleshooting
Termi-
nal no.Normal state Check condition Check item
24*2Longitudinal G sensor
earth, lateral G sensor
earthAny time1 V or less
26ECU earthAny time1 V or less
31ECU backup power
supplyAny timeSystem voltage
32Pressure sensorIgnition switch: ON0.5 - 1.5 V
33Steering wheel sensor
4.5 V flushing
34Steering wheel sensor
4.5 V flushing
35Diagnosis data input/
output--
36Idle switchIgnition switch: ONAccelerator pedal: Full closed1 V or lessg
Accelerator pedal: Depress4.5 - 5.0 V
37Parking brake switchIgnition switch: ONParking brake lever: Pull1 V or lessgg
Parking brake lever: ReleaseSystem voltage
38Stop lamp switchIgnition switch: ONBrake pedal: DepressSystem voltageppg
Brake pedal: Release1 V or less
39TPSIgnition switch: ONAccelerator pedal: Full closed0.5 - 0.7 Vg
Accelerator pedal: Full throttle4.5 - 5.5 V
40ACD mode indicator
lamp
TARMAC0V
p
ACD mode indicator lamp position:
Except for aboveApprox. 10.5 V
42ECU earthAny time1 V or less
43Pressure sensor earthAny time1 V or less
44Steering wheel sensor
STN
Ignition switch: ONSteering wheel: Neutral1-2Vg
g
Steering wheel: Turn from the
neutral position2.5 - 4.5 V
46Diagnosis control--
47ACD mode switchIgnition switch: ONSwitch: PressSystem voltageg
Switch: Release0V
49*1ABS monitorWith ABS not activeSystem voltage
With ABS active1.5 V or less
50*2EarthAny time1 V or less
51ACD mode indicator
lamp
SNOW0V
p
ACD mode indicator lamp position:
Except for aboveApprox. 10.5 V
52ACD mode indicator
lamp
GRAVEL0V
p
ACD mode indicator lamp position:
Except for aboveApprox. 10.5 V
Page 852 of 1449
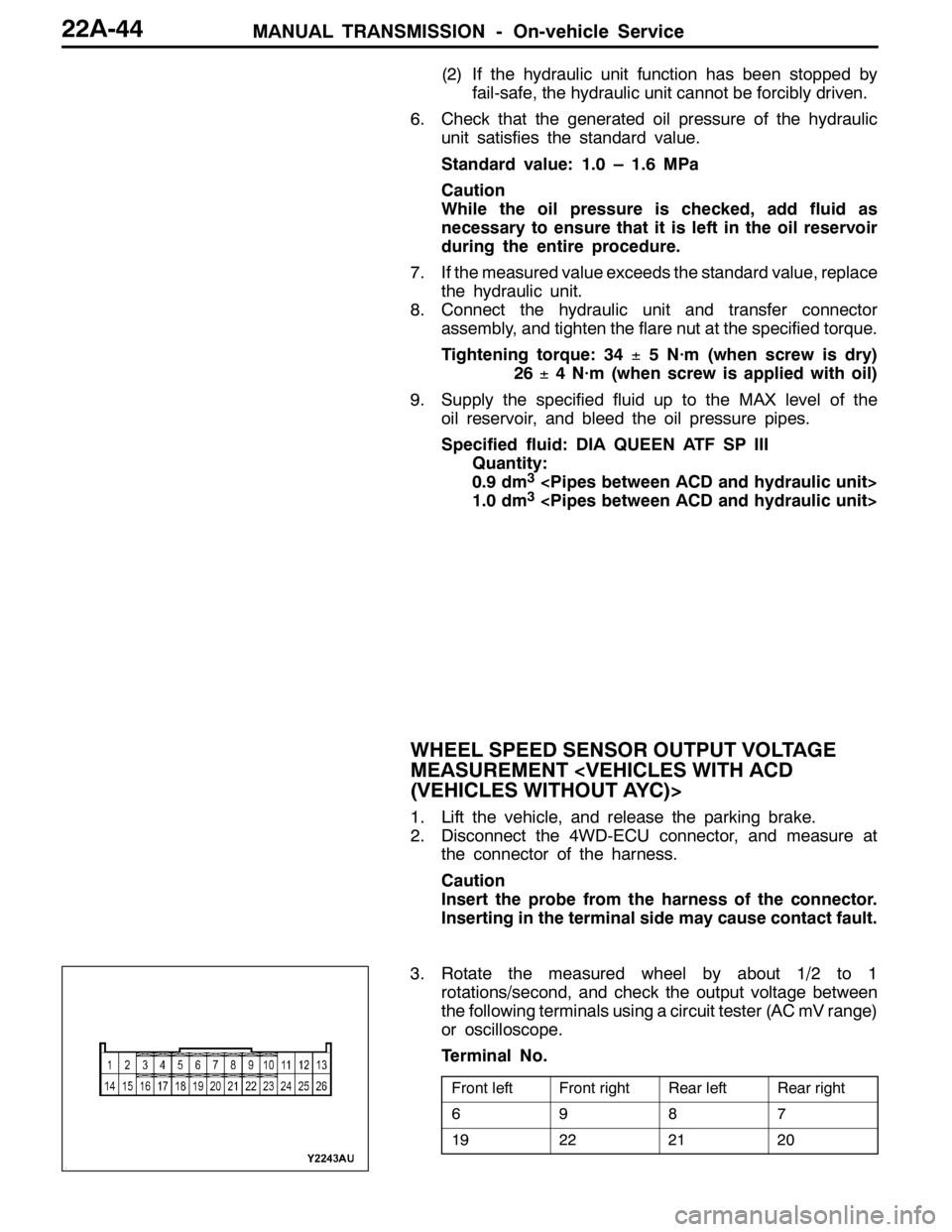
MANUAL TRANSMISSION - On-vehicle Service22A-44
(2) If the hydraulic unit function has been stopped by
fail-safe, the hydraulic unit cannot be forcibly driven.
6. Check that the generated oil pressure of the hydraulic
unit satisfies the standard value.
Standard value: 1.0 – 1.6 MPa
Caution
While the oil pressure is checked, add fluid as
necessary to ensure that it is left in the oil reservoir
during the entire procedure.
7. If the measured value exceeds the standard value, replace
the hydraulic unit.
8. Connect the hydraulic unit and transfer connector
assembly, and tighten the flare nut at the specified torque.
Tightening torque: 34±5 N·m (when screw is dry)
26±4 N·m (when screw is applied with oil)
9. Supply the specified fluid up to the MAX level of the
oil reservoir, and bleed the oil pressure pipes.
Specified fluid: DIA QUEEN ATF SP III
Quantity:
0.9 dm
3
1.0 dm3
WHEEL SPEED SENSOR OUTPUT VOLTAGE
MEASUREMENT
1. Lift the vehicle, and release the parking brake.
2. Disconnect the 4WD-ECU connector, and measure at
the connector of the harness.
Caution
Insert the probe from the harness of the connector.
Inserting in the terminal side may cause contact fault.
3. Rotate the measured wheel by about 1/2 to 1
rotations/second, and check the output voltage between
the following terminals using a circuit tester (AC mV range)
or oscilloscope.
Terminal No.
Front leftFront rightRear leftRear right
6987
19222120
Page 853 of 1449
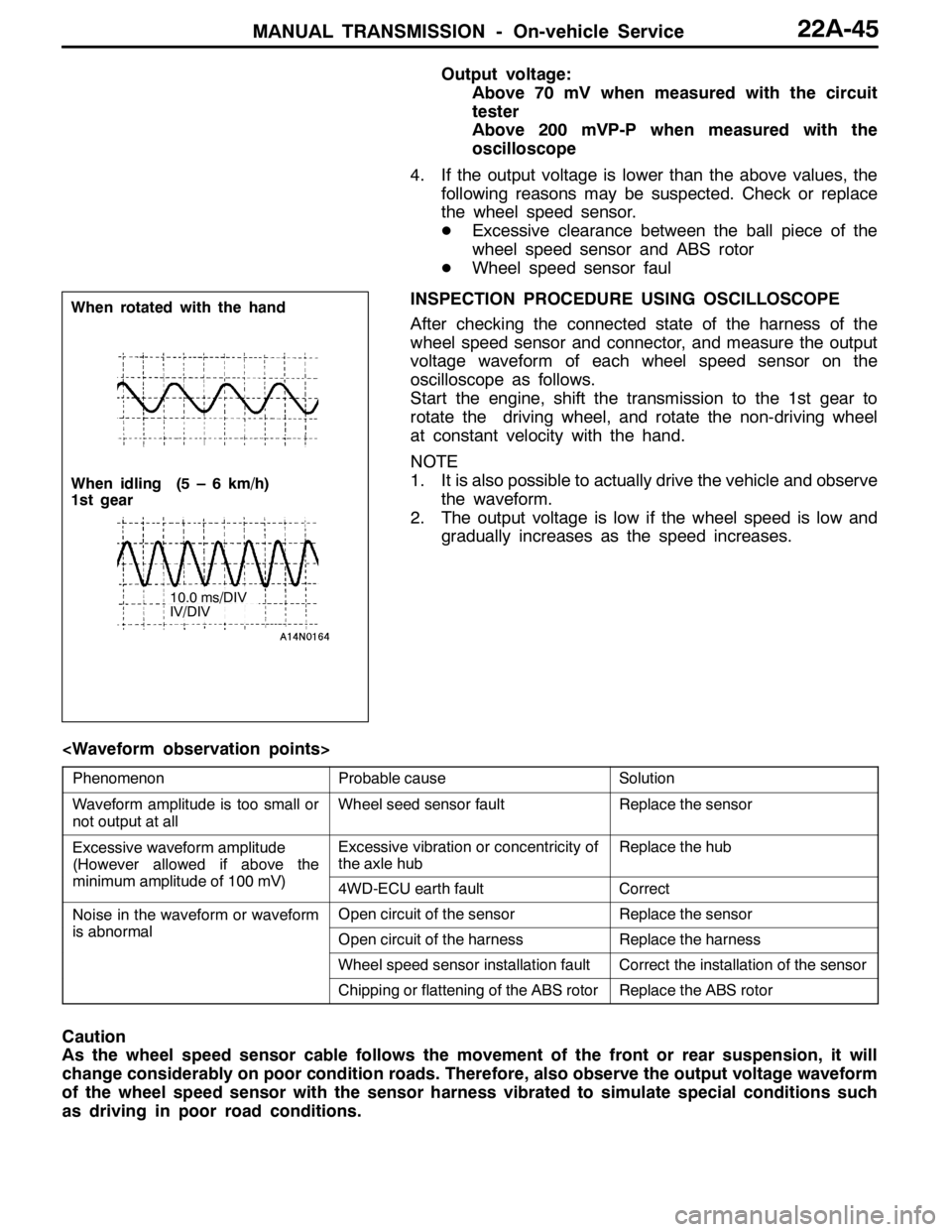
MANUAL TRANSMISSION - On-vehicle Service22A-45
Output voltage:
Above 70 mV when measured with the circuit
tester
Above 200 mVP-P when measured with the
oscilloscope
4. If the output voltage is lower than the above values, the
following reasons may be suspected. Check or replace
the wheel speed sensor.
DExcessive clearance between the ball piece of the
wheel speed sensor and ABS rotor
DWheel speed sensor faul
INSPECTION PROCEDURE USING OSCILLOSCOPE
After checking the connected state of the harness of the
wheel speed sensor and connector, and measure the output
voltage waveform of each wheel speed sensor on the
oscilloscope as follows.
Start the engine, shift the transmission to the 1st gear to
rotate the driving wheel, and rotate the non-driving wheel
at constant velocity with the hand.
NOTE
1. It is also possible to actually drive the vehicle and observe
the waveform.
2. The output voltage is low if the wheel speed is low and
gradually increases as the speed increases.
PhenomenonProbable causeSolution
Waveform amplitude is too small or
not output at allWheel seed sensor faultReplace the sensor
Excessive waveform amplitude
(However allowed if above the
iilit df100V)
Excessive vibration or concentricity of
the axle hubReplace the hub
(
minimum amplitude of 100 mV)4WD-ECU earth faultCorrect
Noise in the waveform or waveform
ibl
Open circuit of the sensorReplace the sensor
is abnormalOpen circuit of the harnessReplace the harness
Wheel speed sensor installation faultCorrect the installation of the sensor
Chipping or flattening of the ABS rotorReplace the ABS rotor
Caution
As the wheel speed sensor cable follows the movement of the front or rear suspension, it will
change considerably on poor condition roads. Therefore, also observe the output voltage waveform
of the wheel speed sensor with the sensor harness vibrated to simulate special conditions such
as driving in poor road conditions.
When rotated with the hand
When idling (5 – 6 km/h)
1st gear
10.0 ms/DIV
IV/DIV
Page 857 of 1449
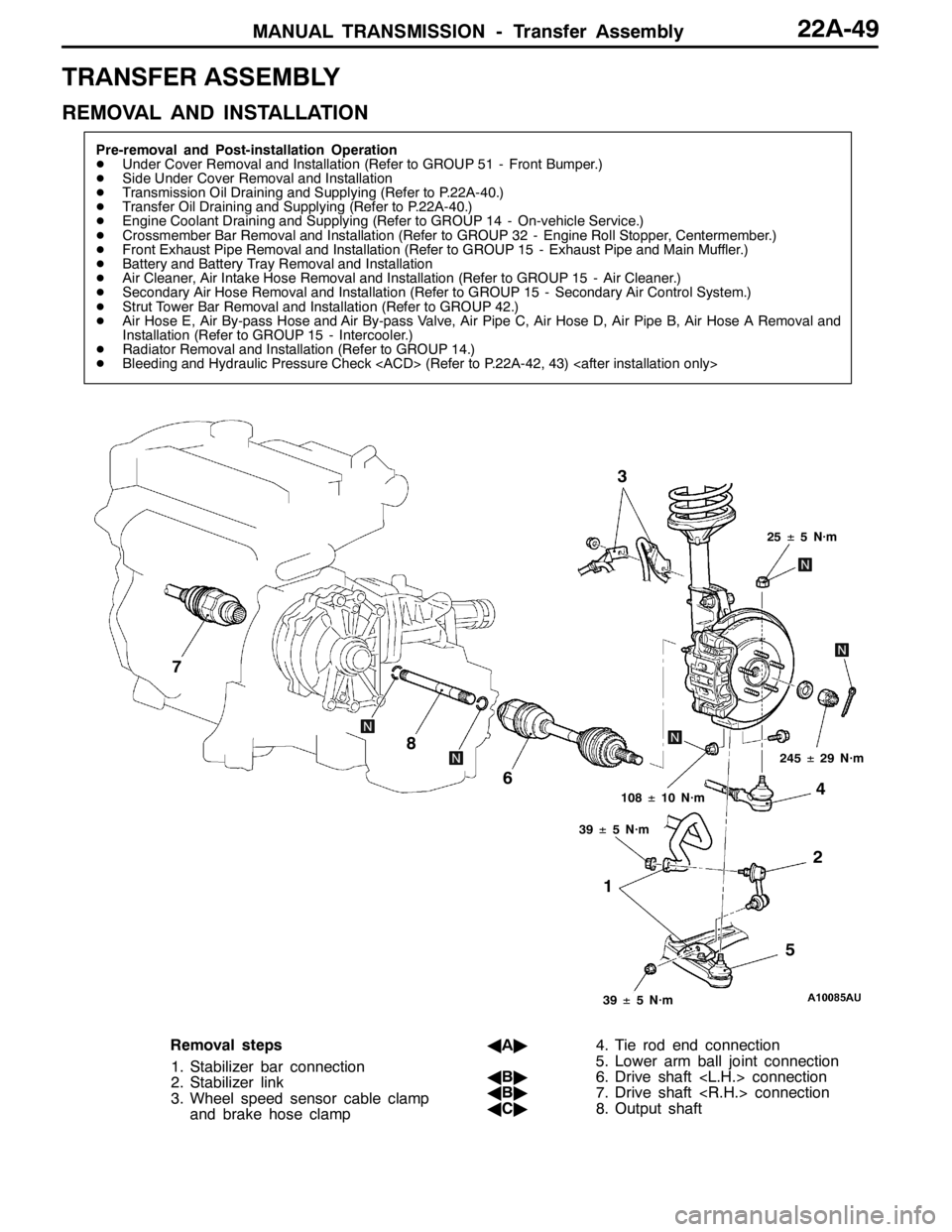
MANUAL TRANSMISSION - Transfer Assembly22A-49
TRANSFER ASSEMBLY
REMOVAL AND INSTALLATION
Pre-removal and Post-installation Operation
DUnder Cover Removal and Installation (Refer to GROUP 51 - Front Bumper.)
DSide Under Cover Removal and Installation
DTransmission Oil Draining and Supplying (Refer to P.22A-40.)
DTransfer Oil Draining and Supplying (Refer to P.22A-40.)
DEngine Coolant Draining and Supplying (Refer to GROUP 14 - On-vehicle Service.)
DCrossmember Bar Removal and Installation (Refer to GROUP 32 - Engine Roll Stopper, Centermember.)
DFront Exhaust Pipe Removal and Installation (Refer to GROUP 15 - Exhaust Pipe and Main Muffler.)
DBattery and Battery Tray Removal and Installation
DAir Cleaner, Air Intake Hose Removal and Installation (Refer to GROUP 15 - Air Cleaner.)
DSecondary Air Hose Removal and Installation (Refer to GROUP 15 - Secondary Air Control System.)
DStrut Tower Bar Removal and Installation (Refer to GROUP 42.)
DAir Hose E, Air By-pass Hose and Air By-pass Valve, Air Pipe C, Air Hose D, Air Pipe B, Air Hose A Removal and
Installation (Refer to GROUP 15 - Intercooler.)
DRadiator Removal and Installation (Refer to GROUP 14.)
DBleeding and Hydraulic Pressure Check
12 3
4
5 6 7
8
25±5 N·m
108±10 N·m
39±5 N·m
39±5 N·m
245±29 N·m
Removal steps
1. Stabilizer bar connection
2. Stabilizer link
3. Wheel speed sensor cable clamp
and brake hose clampAA"4. Tie rod end connection
5. Lower arm ball joint connection
AB"6. Drive shaft
AB"7. Drive shaft
AC"8. Output shaft
Page 860 of 1449
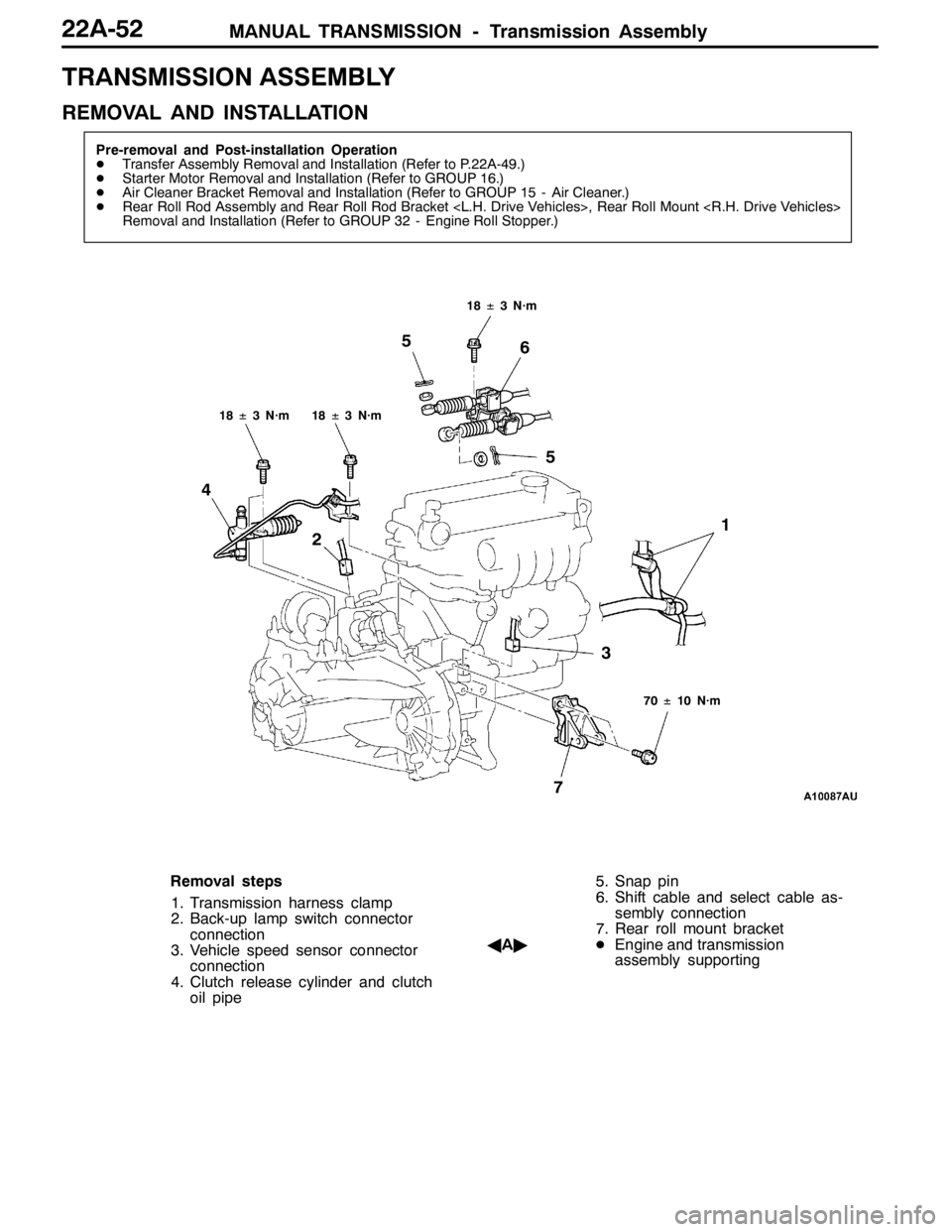
MANUAL TRANSMISSION - Transmission Assembly22A-52
TRANSMISSION ASSEMBLY
REMOVAL AND INSTALLATION
Pre-removal and Post-installation Operation
DTransfer Assembly Removal and Installation (Refer to P.22A-49.)
DStarter Motor Removal and Installation (Refer to GROUP 16.)
DAir Cleaner Bracket Removal and Installation (Refer to GROUP 15 - Air Cleaner.)
DRear Roll Rod Assembly and Rear Roll Rod Bracket
Removal and Installation (Refer to GROUP 32 - Engine Roll Stopper.)
1
2
3 45
5 6
7
18±3 N·m18±3 N·m
18±3 N·m
70±10 N·m
Removal steps
1. Transmission harness clamp
2. Back-up lamp switch connector
connection
3. Vehicle speed sensor connector
connection
4. Clutch release cylinder and clutch
oil pipe5. Snap pin
6. Shift cable and select cable as-
sembly connection
7. Rear roll mount bracket
AA"DEngine and transmission
assembly supporting
Page 864 of 1449
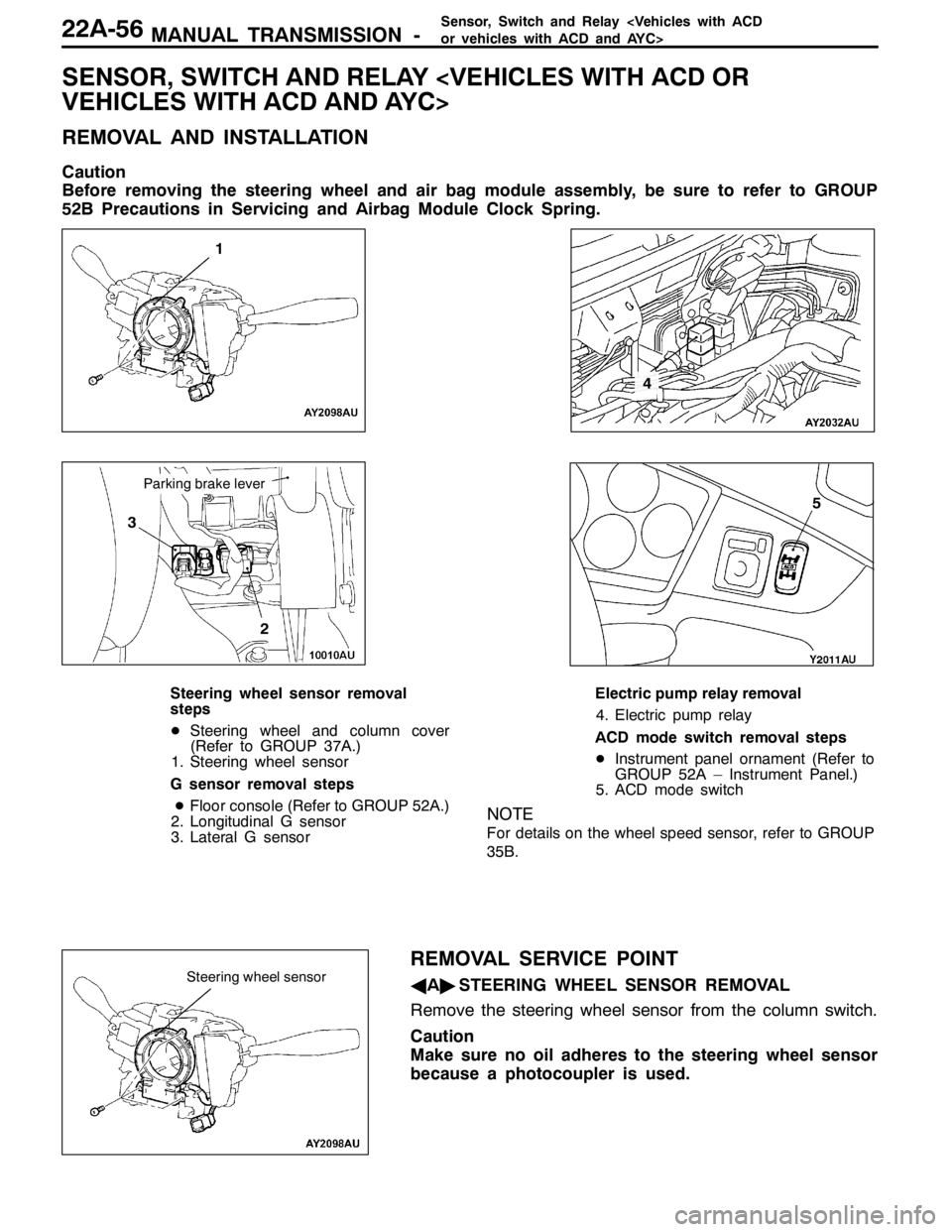
MANUAL TRANSMISSION -Sensor, Switch and Relay
SENSOR, SWITCH AND RELAY
REMOVAL AND INSTALLATION
Caution
Before removing the steering wheel and air bag module assembly, be sure to refer to GROUP
52B Precautions in Servicing and Airbag Module Clock Spring.
1
3
2
4
5
Parking brake lever
Steering wheel sensor removal
steps
DSteering wheel and column cover
(Refer to GROUP 37A.)
1. Steering wheel sensor
G sensor removal steps
DFloor console (Refer to GROUP 52A.)
2. Longitudinal G sensor
3. Lateral G sensorElectric pump relay removal
4. Electric pump relay
ACD mode switch removal steps
DInstrument panel ornament (Refer to
GROUP 52A – Instrument Panel.)
5. ACD mode switch
NOTE
For details on the wheel speed sensor, refer to GROUP
35B.
REMOVAL SERVICE POINT
AA"STEERING WHEEL SENSOR REMOVAL
Remove the steering wheel sensor from the column switch.
Caution
Make sure no oil adheres to the steering wheel sensor
because a photocoupler is used.Steering wheel sensor
Page 865 of 1449
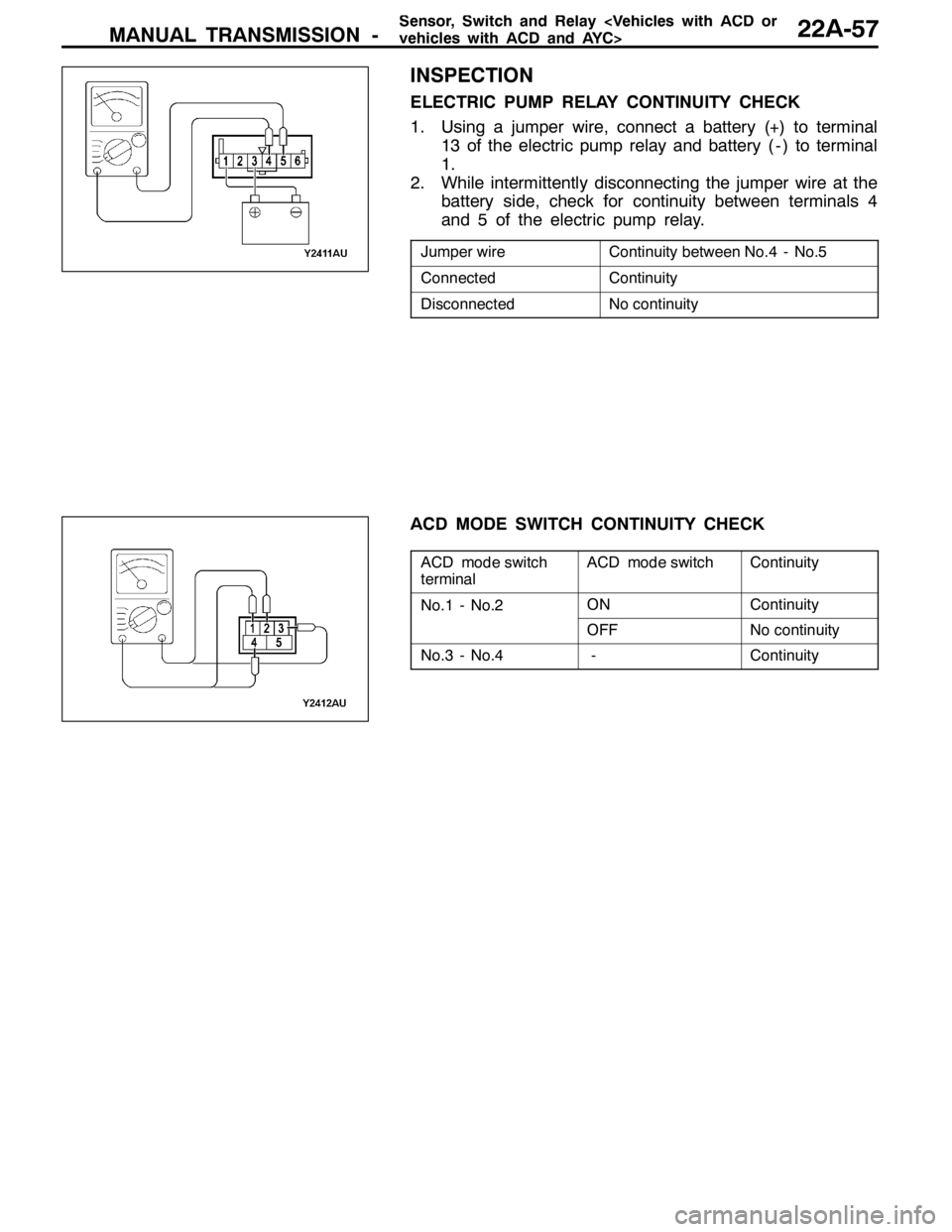
MANUAL TRANSMISSION -Sensor,SwitchandRelay
INSPECTION
ELECTRIC PUMP RELAY CONTINUITY CHECK
1. Using a jumper wire, connect a battery (+) to terminal
13 of the electric pump relay and battery ( - ) to terminal
1.
2. While intermittently disconnecting the jumper wire at the
battery side, check for continuity between terminals 4
and 5 of the electric pump relay.
Jumper wireContinuity between No.4 - No.5
ConnectedContinuity
DisconnectedNo continuity
ACD MODE SWITCH CONTINUITY CHECK
ACD mode switch
terminalACD mode switchContinuity
No.1 - No.2ONContinuity
OFFNo continuity
No.3 - No.4-Continuity
Page 934 of 1449
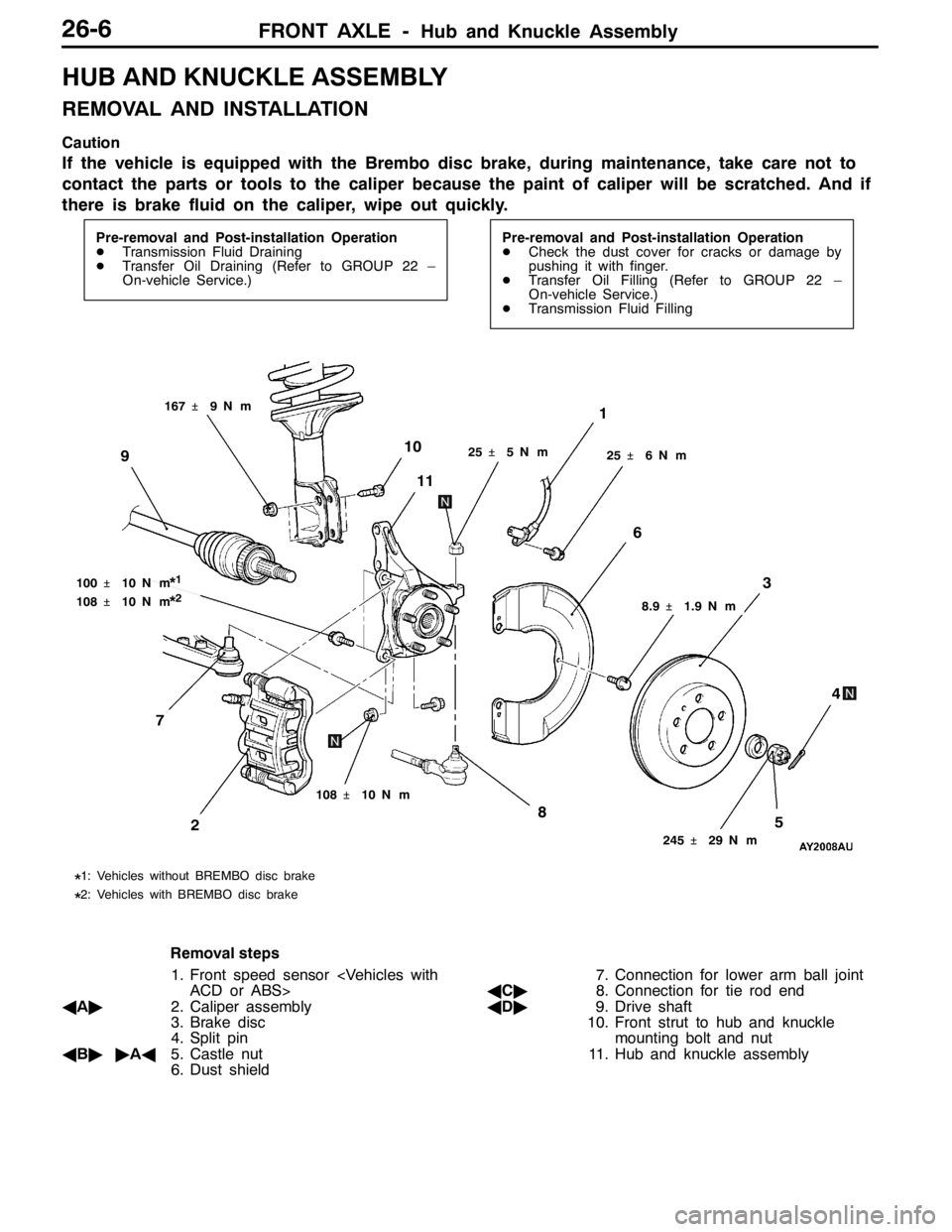
FRONT AXLE -Hub and Knuckle Assembly26-6
HUB AND KNUCKLE ASSEMBLY
REMOVAL AND INSTALLATION
Caution
If the vehicle is equipped with the Brembo disc brake, during maintenance, take care not to
contact the parts or tools to the caliper because the paint of caliper will be scratched. And if
there is brake fluid on the caliper, wipe out quickly.
Pre-removal and Post-installation Operation
DTransmission Fluid Draining
DTransfer Oil Draining (Refer to GROUP 22 –
On-vehicle Service.)Pre-removal and Post-installation Operation
DCheck the dust cover for cracks or damage by
pushing it with finger.
DTransfer Oil Filling (Refer to GROUP 22 –
On-vehicle Service.)
DTransmission Fluid Filling
25¶5N m
1
245¶29 N m
58
3
4
2
108¶10 N m
10
11
25¶6N m
6
9
100¶10 N m*1
108¶10 N m*2
167¶9N m
8.9¶1.9 N m
*1: Vehicles without BREMBO disc brake
*2: Vehicles with BREMBO disc brake
7
Removal steps
1. Front speed sensor
AA"2. Caliper assembly
3. Brake disc
4. Split pin
AB""AA5. Castle nut
6. Dust shield7. Connection for lower arm ball joint
AC"8. Connection for tie rod end
AD"9. Drive shaft
10. Front strut to hub and knuckle
mounting bolt and nut
11. Hub and knuckle assembly
Page 938 of 1449
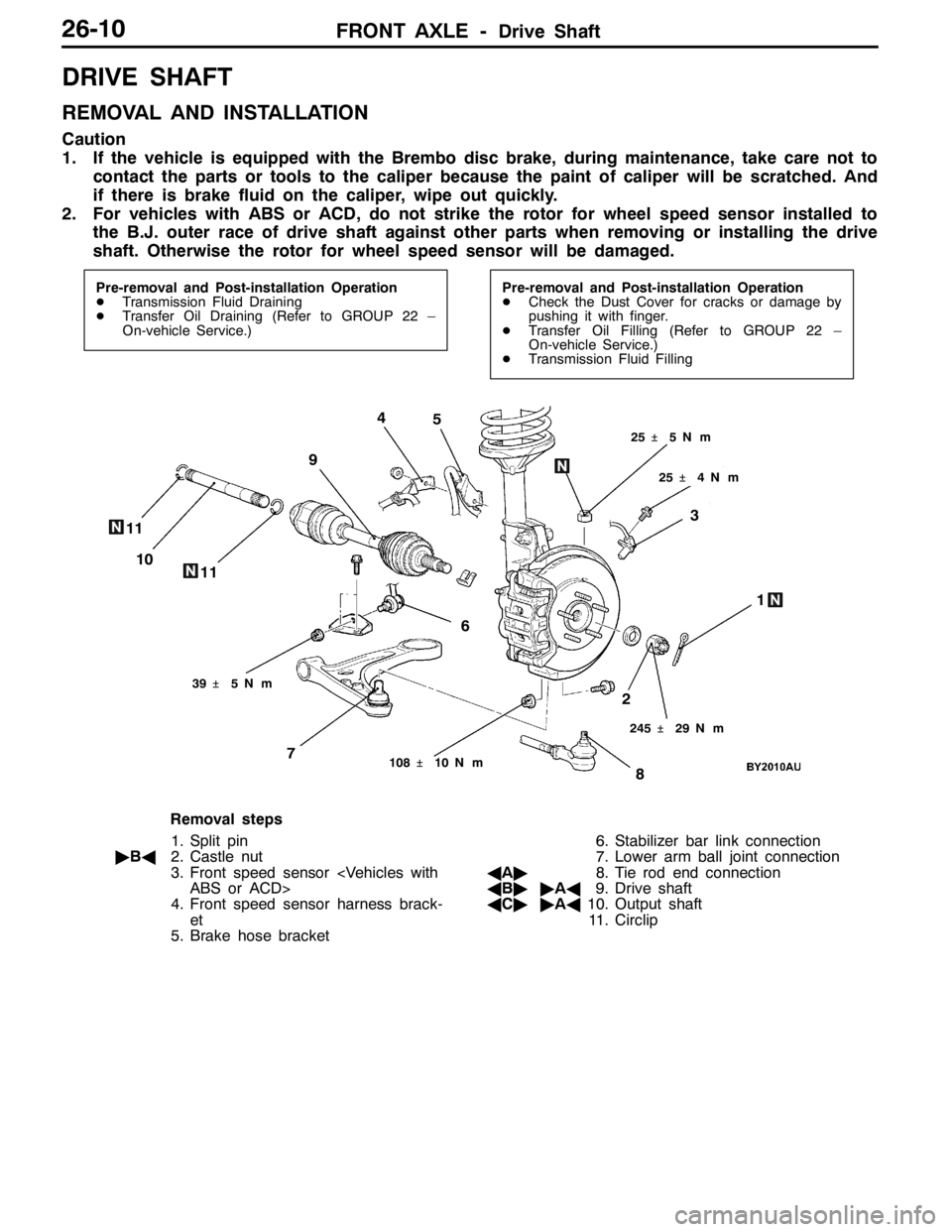
FRONT AXLE -Drive Shaft26-10
DRIVE SHAFT
REMOVAL AND INSTALLATION
Caution
1. If the vehicle is equipped with the Brembo disc brake, during maintenance, take care not to
contact the parts or tools to the caliper because the paint of caliper will be scratched. And
if there is brake fluid on the caliper, wipe out quickly.
2. For vehicles with ABS or ACD, do not strike the rotor for wheel speed sensor installed to
the B.J. outer race of drive shaft against other parts when removing or installing the drive
shaft. Otherwise the rotor for wheel speed sensor will be damaged.
Pre-removal and Post-installation Operation
DTransmission Fluid Draining
DTransfer Oil Draining (Refer to GROUP 22 –
On-vehicle Service.)Pre-removal and Post-installation Operation
DCheck the Dust Cover for cracks or damage by
pushing it with finger.
DTransfer Oil Filling (Refer to GROUP 22 –
On-vehicle Service.)
DTransmission Fluid Filling
1
6 9
8 5
74
3
2 11
25¶4N m 25¶5N m
245¶29 N m
108¶10 N m
10
11
39¶5N m
Removal steps
1. Split pin
"BA2. Castle nut
3. Front speed sensor
4. Front speed sensor harness brack-
et
5. Brake hose bracket6. Stabilizer bar link connection
7. Lower arm ball joint connection
AA"8. Tie rod end connection
AB""AA9. Drive shaft
AC""AA10. Output shaft
11. Circlip