abs MITSUBISHI LANCER EVOLUTION X 2008 User Guide
[x] Cancel search | Manufacturer: MITSUBISHI, Model Year: 2008, Model line: LANCER EVOLUTION X, Model: MITSUBISHI LANCER EVOLUTION X 2008Pages: 241, PDF Size: 8.26 MB
Page 102 of 241
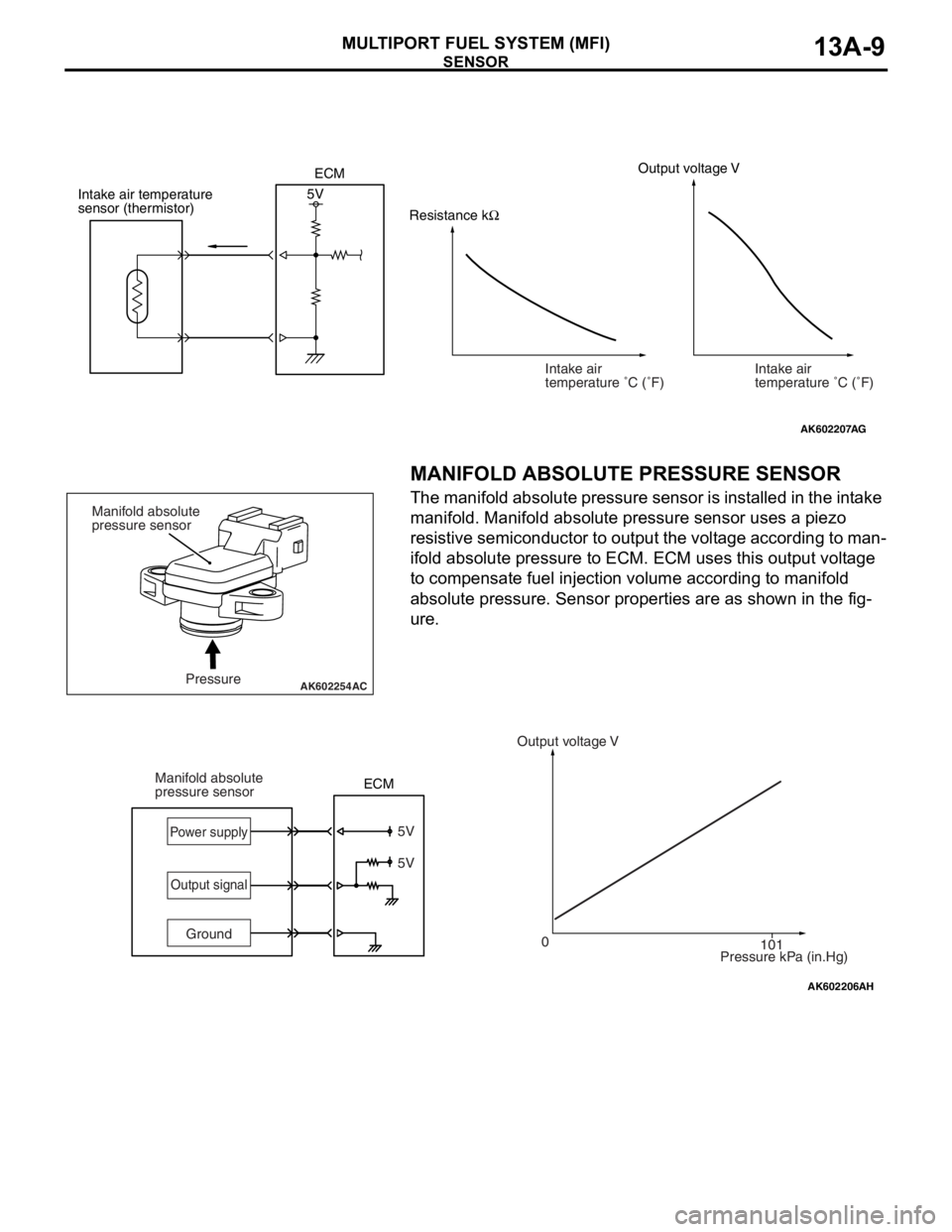
SENSOR
MULTIPORT FUEL SYSTEM (MFI)13A-9
.
MANIFOLD ABSOLUTE PRESSURE SENSOR
The manifold absolute pressure sensor is installed in the intake
manifold. Manifold absolute pressure sensor uses a piezo
resistive semiconductor to output the voltage according to man
-
ifold absolute pressure to ECM. ECM uses this output voltage
to compensate fuel injection volume according to manifold
absolute pressure. Sensor properties are as shown in the fig
-
ure.
.
AK602207
Intake air
temperature C ( F)
AG
Resistance kΩOutput voltage V
Intake air temperature
sensor (thermistor)5V
Intake air
temperature C ( F) ECM
AK602254 ACPressure Manifold absolute
pressure sensor
AK602206AH
5V
0
101 5V
GroundOutput voltage V
Pressure kPa (in.Hg) Manifold absolute
pressure sensorPower supply
Output signal
ECM
Page 122 of 241
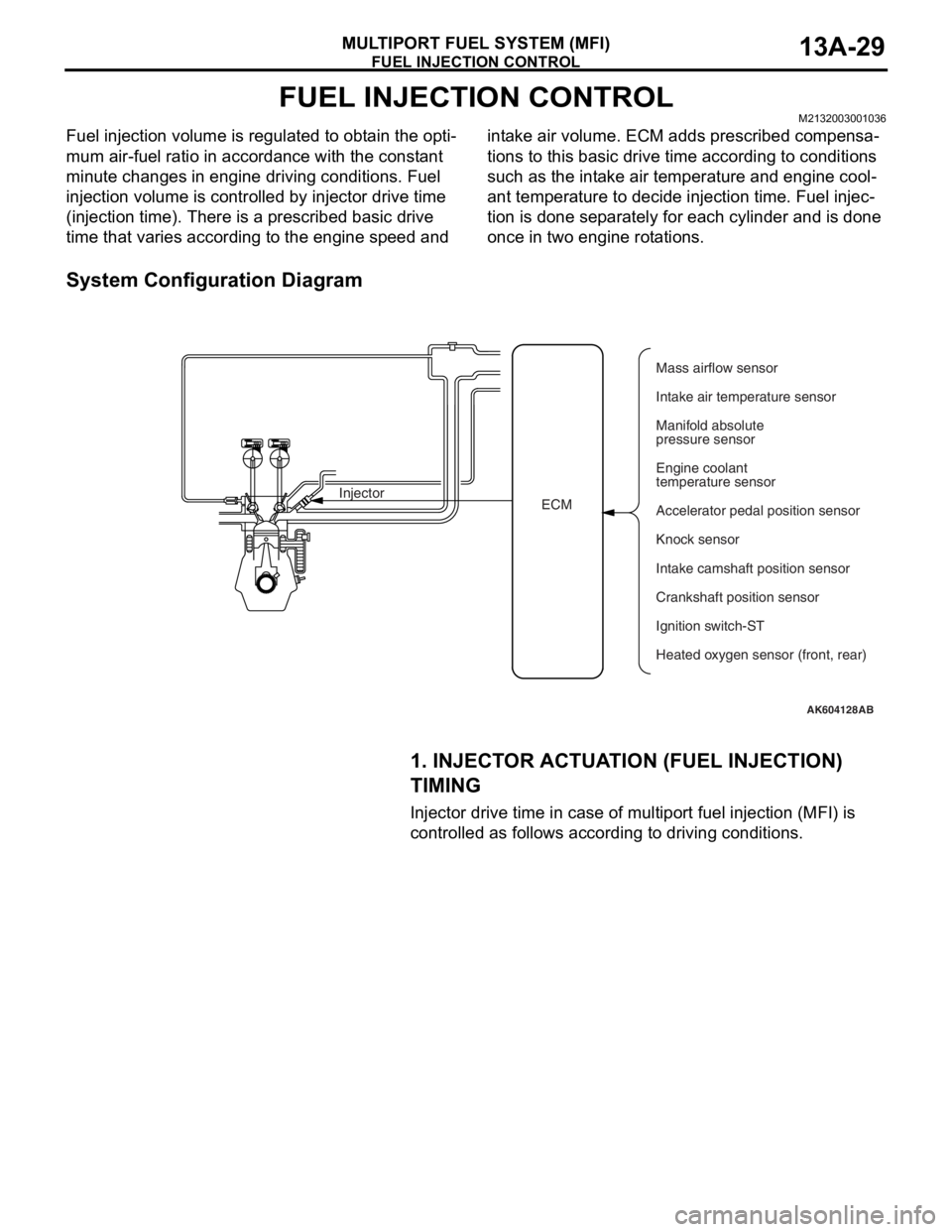
FUEL INJECTION CONTROL
MULTIPORT FUEL SYSTEM (MFI)13A-29
FUEL INJECTION CONTROLM2132003001036
Fuel injection volume is regulated to obtain the opti-
mum air-fuel ratio in accordance with the constant
minute changes in engine driving conditions. Fuel
injection volume is controlled by injector drive time
(injection time). There is a prescribed basic drive
time that varies according to the engine speed and intake air volume. ECM adds prescribed compensa
-
tions to this basic drive time according to conditions
such as the intake air temperature and engine cool
-
ant temperature to decide injection time. Fuel injec-
tion is done separately for each cylinder and is done
once in two engine rotations.
System Configuration Diagram
1. INJECTOR ACTUATION (FUEL INJECTION)
TIMING
Injector drive time in case of multiport fuel injection (MFI) is
controlled as follows according to driving conditions.
AK604128AB
ECM InjectorMass airflow sensor
Intake air temperature sensor
Manifold absolute
pressure sensor
Engine coolant
temperature sensor
Accelerator pedal position sensor
Knock sensor
Intake camshaft position sensor
Ignition switch-ST
Heated oxygen sensor (front, rear) Crankshaft position sensor
Page 125 of 241
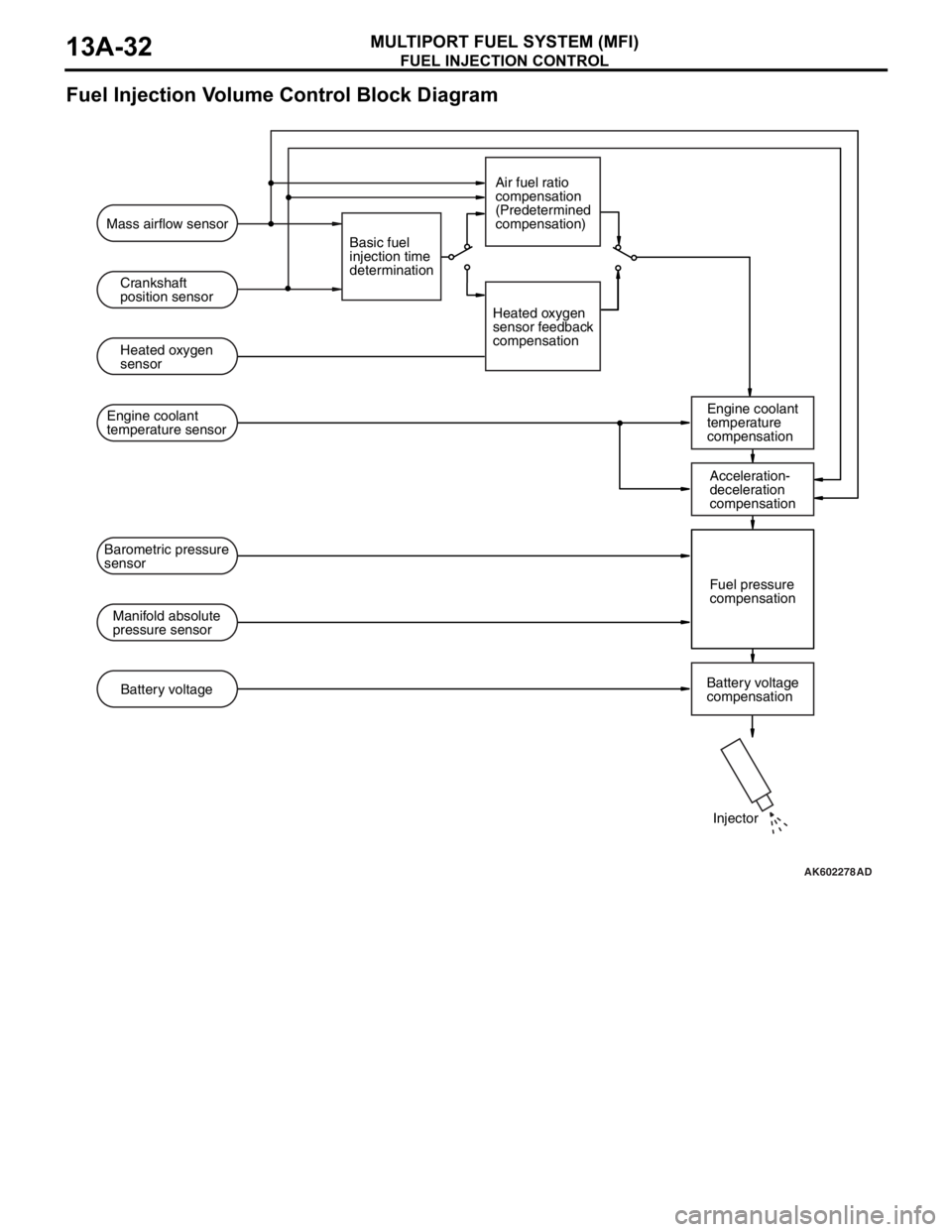
FUEL INJECTION CONTROL
MULTIPORT FUEL SYSTEM (MFI)13A-32
Fuel Injection Volume Control Block Diagram
.
AK602278AD
Mass airflow sensor
Crankshaft
position sensor
Heated oxygen
sensor
Engine coolant
temperature
compensation Engine coolant
temperature sensor
Manifold absolute
pressure sensorFuel pressure
compensation Barometric pressure
sensor
Battery voltage
compensation Battery voltageBasic fuel
injection time
determinationAir fuel ratio
compensation
(Predetermined
compensation)
Heated oxygen
sensor feedback
compensation
Injector Acceleration-
deceleration
compensation
Page 126 of 241
![MITSUBISHI LANCER EVOLUTION X 2008 User Guide FUEL INJECTION CONTROL
MULTIPORT FUEL SYSTEM (MFI)13A-33
[Injector basic drive time]
Fuel injection is performed once per cycle for each cylinder.
Basic drive time refers to fuel injection volume (in MITSUBISHI LANCER EVOLUTION X 2008 User Guide FUEL INJECTION CONTROL
MULTIPORT FUEL SYSTEM (MFI)13A-33
[Injector basic drive time]
Fuel injection is performed once per cycle for each cylinder.
Basic drive time refers to fuel injection volume (in](/img/19/57326/w960_57326-125.png)
FUEL INJECTION CONTROL
MULTIPORT FUEL SYSTEM (MFI)13A-33
[Injector basic drive time]
Fuel injection is performed once per cycle for each cylinder.
Basic drive time refers to fuel injection volume (injector drive
time) to achieve theoretical air-fuel ratio for the intake air vol
-
ume of 1 cycle of 1 cylinder. Fuel injection volume changes
according to the pressure difference (injected fuel pressure)
between manifold absolute pressure and fuel pressure (con
-
stant). So, injected fuel pressure compensation is made to
injector drive time for theoretical air-fuel ratio to arrive at basic
drive time.
Intake air volume of each cycle of 1 cylinder is calculated by
ECM based on the mass airflow sensor signal and crankshaft
position sensor signal. Also, during engine start, the map value
prescribed by the engine coolant temperature sensor signal is
used as basic drive time.
.
AK602279AC
Basic fuel
injection timeFuel injection pressure compensation Intake air amount per cycle per cylinder
Theoretical air-fuel ratio
Page 127 of 241
![MITSUBISHI LANCER EVOLUTION X 2008 User Guide FUEL INJECTION CONTROL
MULTIPORT FUEL SYSTEM (MFI)13A-34
[Injector drive time compensation]
After calculating the injector basic drive time, the ECM makes
the following compensations to control the o MITSUBISHI LANCER EVOLUTION X 2008 User Guide FUEL INJECTION CONTROL
MULTIPORT FUEL SYSTEM (MFI)13A-34
[Injector drive time compensation]
After calculating the injector basic drive time, the ECM makes
the following compensations to control the o](/img/19/57326/w960_57326-126.png)
FUEL INJECTION CONTROL
MULTIPORT FUEL SYSTEM (MFI)13A-34
[Injector drive time compensation]
After calculating the injector basic drive time, the ECM makes
the following compensations to control the optimum fuel injec
-
tion volume according to driving conditions.
List of main compensations for fuel injection control
.
[Fuel limit control during deceleration]
ECM limits fuel when decelerating downhill to prevent exces-
sive rise of catalytic converter temperature and to improve fuel
efficiency.
.
[Fuel-cut control when over-run]
When engine speed exceeds a prescribed limit (6,600 r/min),
ECM cuts fuel supply to prevent overrunning and thus protect
the engine. Also, if engine speed exceeds 4,000 r/min for 15
seconds while vehicle is stationary (no load), it cuts fuel supply
and controls the throttle valve opening angle to protect the
engine.
CompensationsContent
Heated oxygen sensor feedback compensationThe heated oxygen sensor signal is used for
making the compensation to get air-fuel ratio with
best cleaning efficiency of the 3-way catalytic
converter. This compensation might not be made
sometimes in order to improve drivability,
depending on driving conditions. (Air-fuel ratio
compensation is made.)
Air-fuel ratio compensationUnder driving conditions where heated oxygen
sensor feedback compensation is not performed,
compensation is made based on pre-set map
values that vary according to engine speed and
intake air volume.
Engine coolant temperature compensationCompensation is made according to the engine
coolant temperature. The lower the engine coolant
temperature, the greater the fuel injection volume.
Acceleration/ Deceleration compensationCompensation is made according to change in
intake air volume. During acceleration, fuel injection
volume is increased. Also, during deceleration, fuel
injection volume is decreased.
Fuel injection compensationCompensation is made according to the pressure
difference between atmospheric pressure and
manifold absolute pressure. The greater the
difference in pressure, the shorter the injector drive
time.
Battery voltage compensationCompensation is made depending on battery
voltage. The lower the battery voltage, the greater
the injector drive signal time.
Learning value for fuel compensationCompensation amount is learned to compensate
feedback of heated oxygen sensor. This allows
system to compensate in accordance with engine
characteristics.
Page 128 of 241
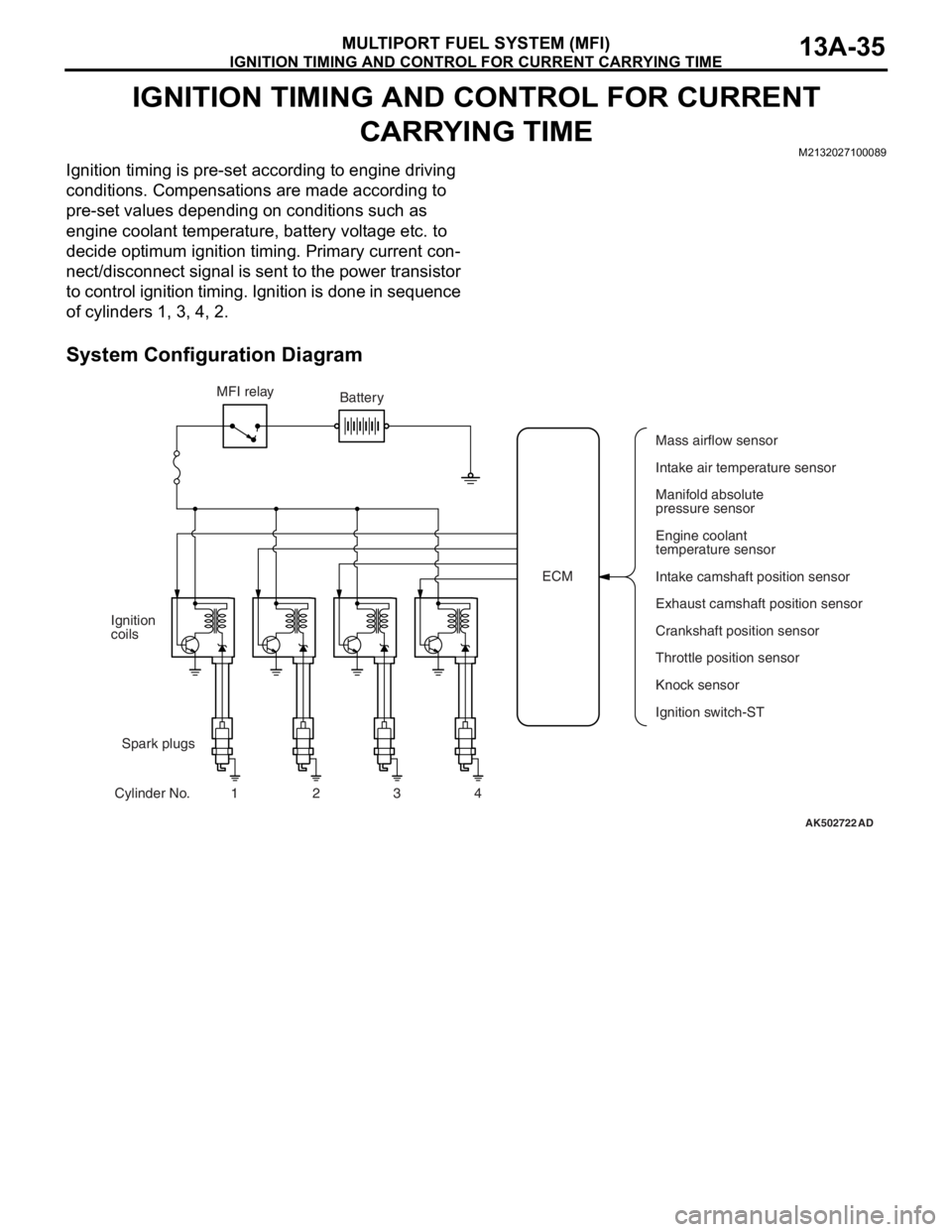
IGNITION TIMING AND CONTROL FOR CURRENT CARRYING TIME
MULTIPORT FUEL SYSTEM (MFI)13A-35
IGNITION TIMING AND CONTROL FOR CURRENT
CARRYING TIME
M2132027100089
Ignition timing is pre-set according to engine driving
conditions. Compensations are made according to
pre-set values depending on conditions such as
engine coolant temperature, battery voltage etc. to
decide optimum ignition timing. Primary current con
-
nect/disconnect signal is sent to the power transistor
to control ignition timing. Ignition is done in sequence
of cylinders 1, 3, 4, 2.
System Configuration Diagram
AK502722AD
ECM MFI relay
Spark plugs Ignition
coils
Cylinder No. 1 2 3 4Battery
Mass airflow sensor
Intake air temperature sensor
Manifold absolute
pressure sensor
Engine coolant
temperature sensor
Intake camshaft position sensor
Exhaust camshaft position sensor
Crankshaft position sensor
Knock sensor
Ignition switch-ST Throttle position sensor
Page 130 of 241
![MITSUBISHI LANCER EVOLUTION X 2008 User Guide IGNITION TIMING AND CONTROL FOR CURRENT CARRYING TIME
MULTIPORT FUEL SYSTEM (MFI)13A-37
2. Spark-advance control and current carrying
time control
.
[During start]
ECM initiates ignition at fixed ign MITSUBISHI LANCER EVOLUTION X 2008 User Guide IGNITION TIMING AND CONTROL FOR CURRENT CARRYING TIME
MULTIPORT FUEL SYSTEM (MFI)13A-37
2. Spark-advance control and current carrying
time control
.
[During start]
ECM initiates ignition at fixed ign](/img/19/57326/w960_57326-129.png)
IGNITION TIMING AND CONTROL FOR CURRENT CARRYING TIME
MULTIPORT FUEL SYSTEM (MFI)13A-37
2. Spark-advance control and current carrying
time control
.
[During start]
ECM initiates ignition at fixed ignition timing (5° BTDC) syn-
chronized with the crankshaft position sensor signal.
.
[During normal operation]
After determining the basic spark-advance based on the intake
air volume and engine speed, ECM makes compensations
based on input from various sensors to control the optimum
spark-advance and current carrying time.
List of main compensations for spark-advance control and current carrying time control
.
[Control for checking ignition timing]
During basic ignition timing set mode for M.U.T.-III actuator test
function, sparking is done with fixed ignition timing (5
° BTDC)
synchronized with crankshaft position sensor signal.
CompensationsContent
Intake air temperature compensationCompensation is made according to intake air
temperature. The higher the intake air temperature
the greater the delay in ignition timing.
Engine coolant temperature compensationCompensation is made according to engine coolant
temperature. The lower the engine coolant
temperature the greater the advance in ignition
timing.
Knocking compensationCompensation is made according to generation of
knocking. The greater the knocking the greater the
delay in ignition timing.
Stable idle compensationCompensation is made according to change in idle
speed. In case engine speed becomes lower than
target speed, ignition timing is advanced.
Delay compensation when changing shiftDuring change of shift, sparking is delayed
compared to normal ignition timing to reduce
engine output torque and absorb the shock of the
shift change.
Battery voltage compensationCompensation is made depending on battery
voltage. The lower the battery voltage the greater
the current carrying time and when battery voltage
is high current carrying time is shortened.
Page 133 of 241

MIVEC (Mitsubishi Innovative Valve Timing Electronic Control System)
MULTIPORT FUEL SYSTEM (MFI)13A-40
MIVEC (Mitsubishi Innovative Valve Timing Electronic
Control System)
M2132023500212
MIVEC is the system which continuously varies and
controls the opening and closing timings of the intake
valve and the exhaust valve.
System Configuration Diagram
MIVEC allows the optimum valve timing to be con-
trolled in accordance with the engine operation and
the idling stability to be improved, as well as the out
-
put and the torque to be better in all the operation
ranges.
•The ECM assesses the engine operation through
the signals from each sensor.
•Based on the assessed information, the ECM
sends the duty signal to the intake engine oil con
-
trol valve and exhaust engine oil control valve as
well as controls the spool valve position.
•Changing the spool valve position allows the oil
pressure to be divided into the retarded chamber
and the advanced chamber, as well as allows the
phases of the intake camshaft and the exhaust
camshaft to be continuously changed.
AK604826AB
Crankshaft
position sensor
Manifold absolute
pressure sensor
Intake camshaft
position sensorECMSpool valve
To oil pan
To oil pan Oil pressureAdvance direction Spool valve movementRetard direction Intake engine oil control valve
Retard chamber
Advance chamber
Spring
Crankshaft
position sensor
Manifold absolute
pressure sensor
Exhaust camshaft
position sensorECMSpool valve
To oil pan
To oil pan Oil pressureRetard direction Spool valve movementAdvance direction Exhaust engine oil control valve
Advance chamber
Retard chamber
Spring
Page 151 of 241
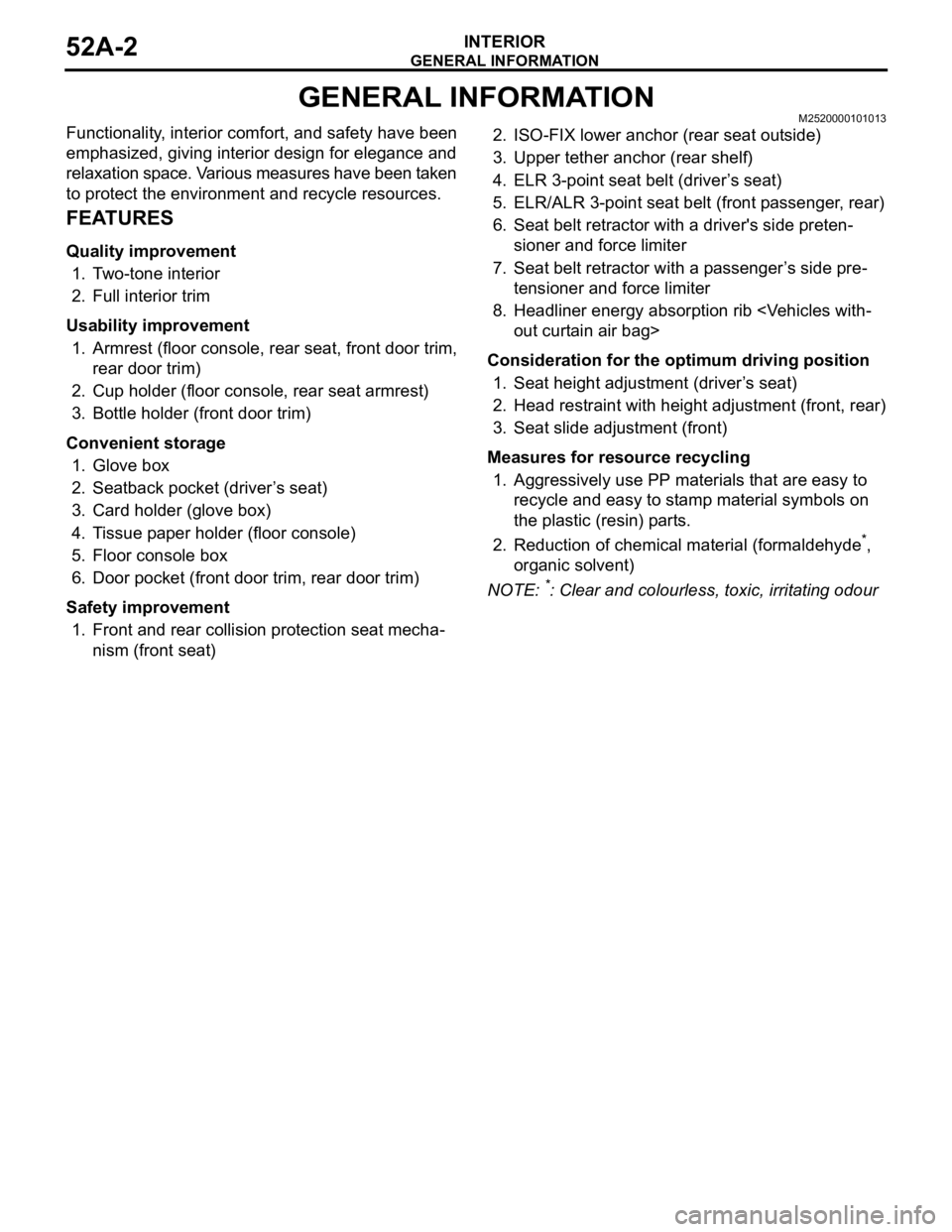
GENERAL INFORMATION
INTERIOR52A-2
GENERAL INFORMATIONM2520000101013
Functionality, interior comfort, and safety have been
emphasized, giving interior design for elegance and
relaxation space. Various measures have been taken
to protect the environment and recycle resources.
FEATURES
Quality improvement
1. Two-tone interior
2. Full interior trim
Usability improvement
1. Armrest (floor console, rear seat, front door trim, rear door trim)
2. Cup holder (floor console, rear seat armrest)
3. Bottle holder (front door trim)
Convenient storage
1. Glove box
2. Seatback pocket (driver’s seat)
3. Card holder (glove box)
4. Tissue paper holder (floor console)
5. Floor console box
6. Door pocket (front door trim, rear door trim)
Safety improvement
1. Front and rear collision protection seat mecha-
nism (front seat)
2. ISO-FIX lower anchor (rear seat outside)
3. Upper tether anchor (rear shelf)
4. ELR 3-point seat belt (driver’s seat)
5. ELR/ALR 3-point seat belt (front passenger, rear)
6. Seat belt retractor with a driver's side preten-
sioner and force limiter
7. Seat belt retractor with a passenger’s side pre-
tensioner and force limiter
8. Headliner energy absorption rib
Consideration for the optimum driving position
1. Seat height adjustment (driver’s seat)
2. Head restraint with height adjustment (front, rear)
3. Seat slide adjustment (front)
Measures for resource recycling
1. Aggressively use PP materials that are easy to recycle and easy to stamp material symbols on
the plastic (resin) parts.
2. Reduction of chemical material (formaldehyde*,
organic solvent)
NOTE: *: Clear and colourless, toxic, irritating odour
Page 159 of 241
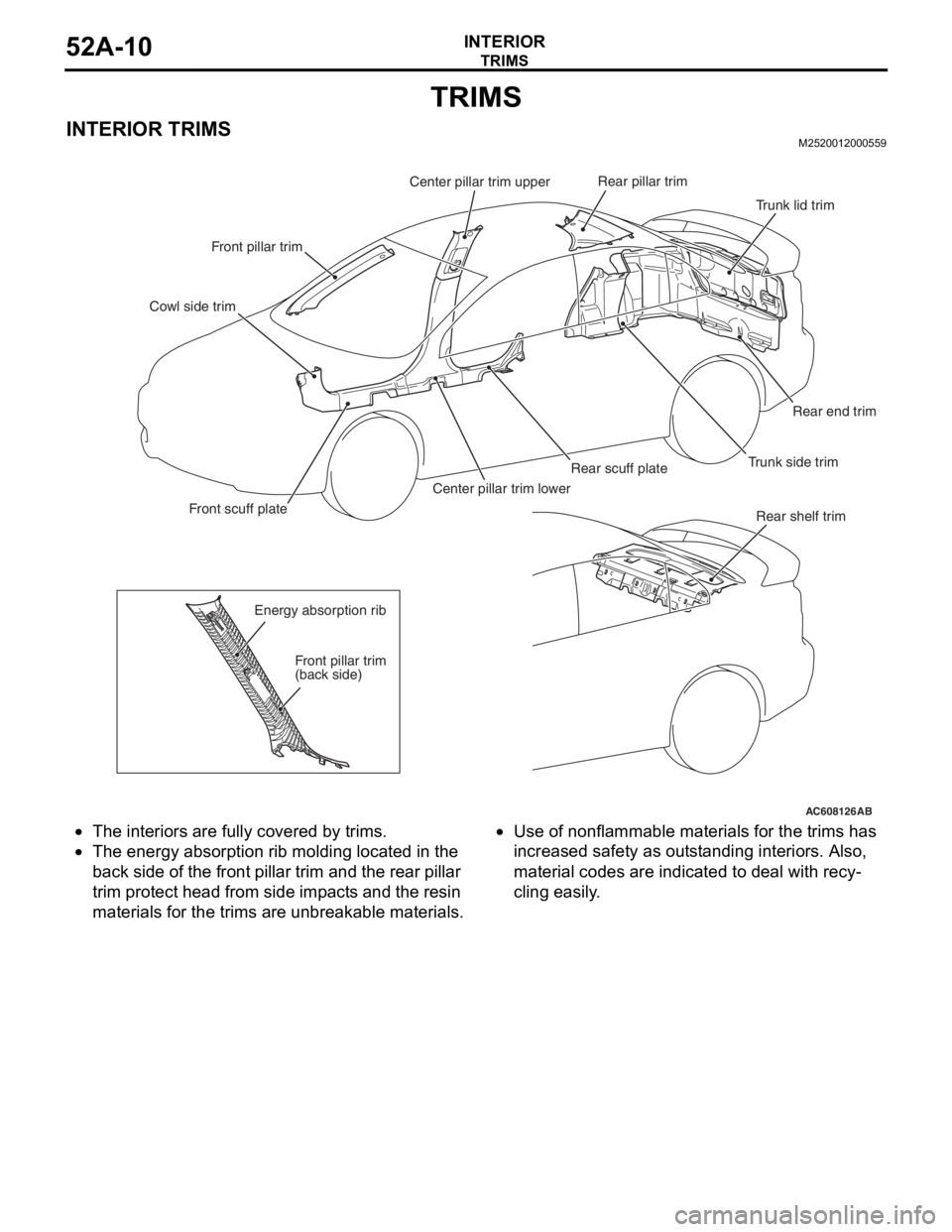
TRIMS
INTERIOR52A-10
TRIMS
INTERIOR TRIMSM2520012000559
•The interiors are fully covered by trims.
•The energy absorption rib molding located in the
back side of the front pillar trim and the rear pillar
trim protect head from side impacts and the resin
materials for the trims are unbreakable materials.
•Use of nonflammable materials for the trims has
increased safety as outstanding interiors. Also,
material codes are indicated to deal with recy
-
cling easily.
AC608126
Energy absorption ribFront pillar trim
(back side)
Front pillar trim
Cowl side trim Center pillar trim upper
Rear pillar trim
Front scuff plate Center pillar trim lower
Rear scuff plate
Trunk side trimRear end trim
AB
Rear shelf trim Trunk lid trim