abs MITSUBISHI LANCER EVOLUTION X 2008 Workshop Manual
[x] Cancel search | Manufacturer: MITSUBISHI, Model Year: 2008, Model line: LANCER EVOLUTION X, Model: MITSUBISHI LANCER EVOLUTION X 2008Pages: 241, PDF Size: 8.26 MB
Page 6 of 241
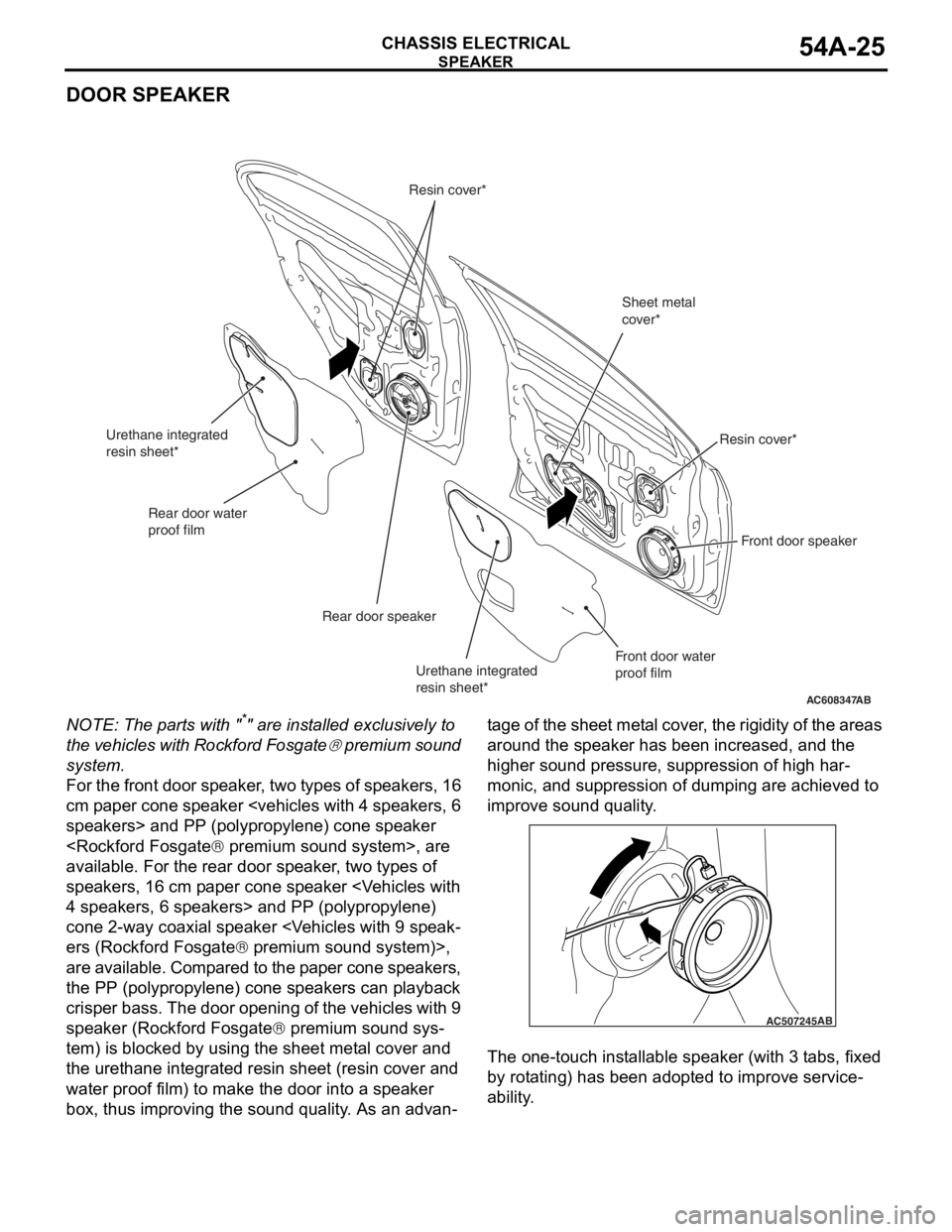
SPEAKER
CHASSIS ELECTRICAL54A-25
DOOR SPEAKER
NOTE: The parts with "*" are installed exclusively to
the vehicles with Rockford Fosgate
® premium sound
system.
For the front door speaker, two types of speakers, 16
cm paper cone speaker
available. For the rear door speaker, two types of
speakers, 16 cm paper cone speaker
cone 2-way coaxial speaker
ers (Rockford Fosgate® premium sound system)>,
are available. Compared to the paper cone speakers,
the PP (polypropylene) cone speakers can playback
crisper bass. The door opening of the vehicles with 9
speaker (Rockford Fosgate
® premium sound sys-
tem) is blocked by using the sheet metal cover and
the urethane integrated resin sheet (resin cover and
water proof film) to make the door into a speaker
box, thus improving the sound quality. As an advan
-
tage of the sheet metal cover, the rigidity of the areas
around the speaker has been increased, and the
higher sound pressure, suppression of high har
-
monic, and suppression of dumping are achieved to
improve sound quality.
The one-touch installable speaker (with 3 tabs, fixed
by rotating) has been adopted to improve service
-
ability.
AC608347
Front door speaker
Rear door speaker
Sheet metal
cover*
Resin cover*
Resin cover*
AB
Front door water
proof film
Rear door water
proof film
Urethane integrated
resin sheet*
Urethane integrated
resin sheet*
AC507245AB
Page 7 of 241
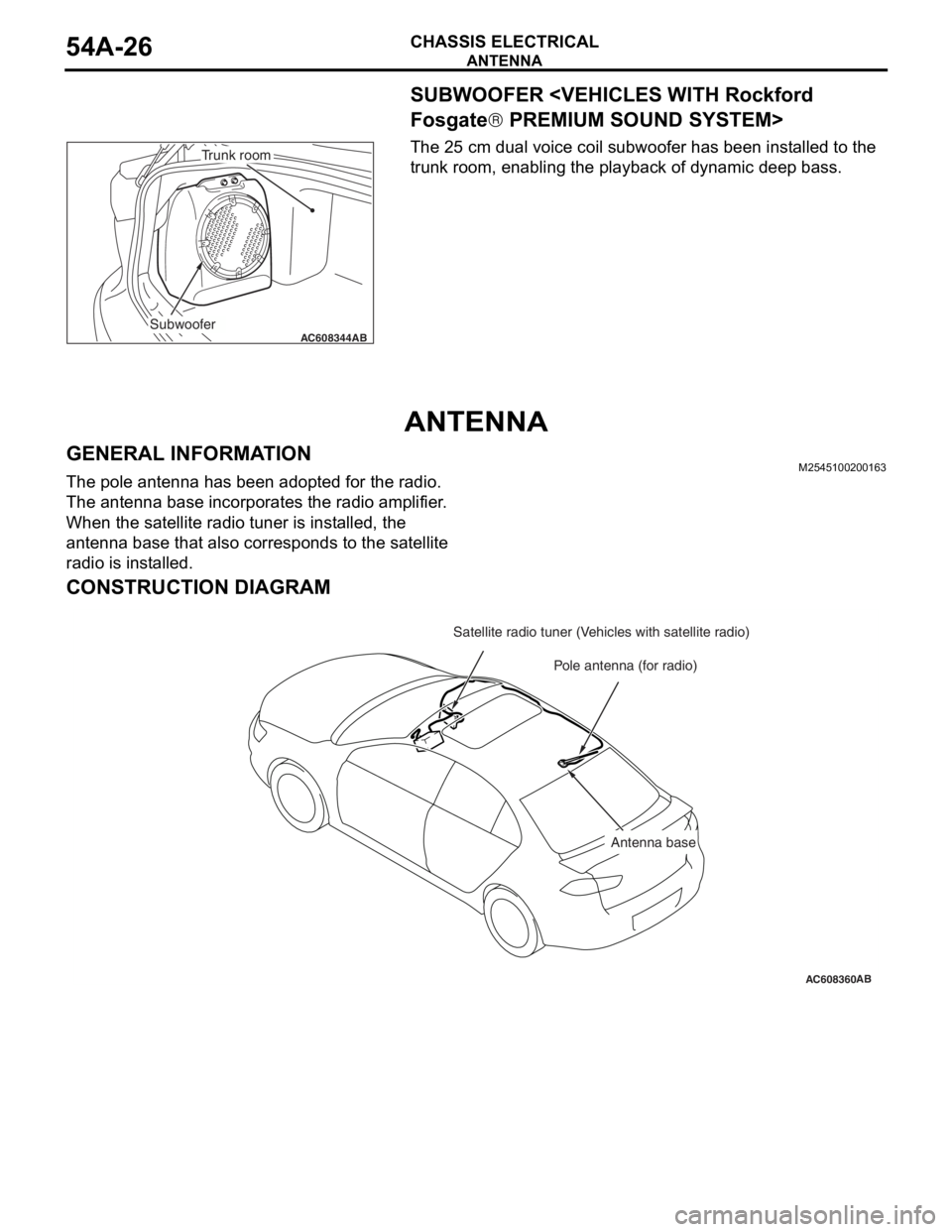
ANTENNA
CHASSIS ELECTRICAL54A-26
SUBWOOFER
® PREMIUM SOUND SYSTEM>
The 25 cm dual voice coil subwoofer has been installed to the
trunk room, enabling the playback of dynamic deep bass.
ANTENNA
GENERAL INFORMATIONM2545100200163
The pole antenna has been adopted for the radio.
The antenna base incorporates the radio amplifier.
When the satellite radio tuner is installed, the
antenna base that also corresponds to the satellite
radio is installed.
CONSTRUCTION DIAGRAM
AC608344ABSubwoofer
Trunk room
AC608360
Pole antenna (for radio)
AB
Satellite radio tuner (Vehicles with satellite radio)
Antenna base
Page 37 of 241
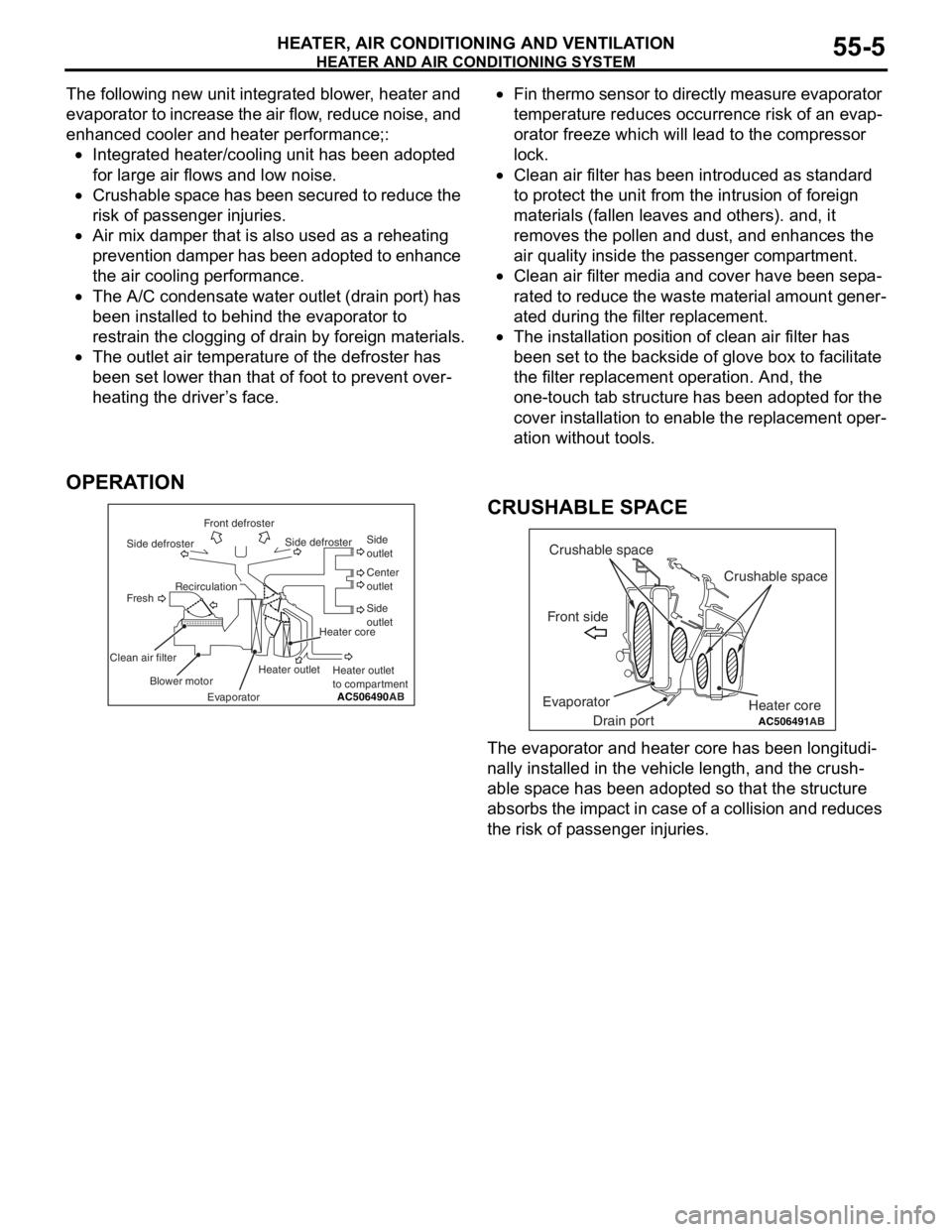
HEATER AND AIR CONDITIONING SYSTEM
HEATER, AIR CONDITIONING AND VENTILATION55-5
The following new unit integrated blower, heater and
evaporator to increase the air flow, reduce noise, and
enhanced cooler and heater performance;:
•Integrated heater/cooling unit has been adopted
for large air flows and low noise.
•Crushable space has been secured to reduce the
risk of passenger injuries.
•Air mix damper that is also used as a reheating
prevention damper has been adopted to enhance
the air cooling performance.
•The A/C condensate water outlet (drain port) has
been installed to behind the evaporator to
restrain the clogging of drain by foreign materials.
•The outlet air temperature of the defroster has
been set lower than that of foot to prevent over
-
heating the driver’s face.
•Fin thermo sensor to directly measure evaporator
temperature reduces occurrence risk of an evap
-
orator freeze which will lead to the compressor
lock.
•Clean air filter has been introduced as standard
to protect the unit from the intrusion of foreign
materials (fallen leaves and others). and, it
removes the pollen and dust, and enhances the
air quality inside the passenger compartment.
•Clean air filter media and cover have been sepa-
rated to reduce the waste material amount gener-
ated during the filter replacement.
•The installation position of clean air filter has
been set to the backside of glove box to facilitate
the filter replacement operation. And, the
one-touch tab structure has been adopted for the
cover installation to enable the replacement oper
-
ation without tools.
OPERATION
.
CRUSHABLE SPACE
The evaporator and heater core has been longitudi-
nally installed in the vehicle length, and the crush-
able space has been adopted so that the structure
absorbs the impact in case of a collision and reduces
the risk of passenger injuries.
AC506490AB Front defroster
Side defrosterSide defrosterSide
outlet
Side
outlet Center
outlet
Heater core
Heater outlet
to compartment Recirculation
Fresh
Clean air filter
Blower motor
EvaporatorHeater outlet
AC506491
Crushable space
Crushable space
Front side
Drain port EvaporatorHeater coreAB
Page 72 of 241
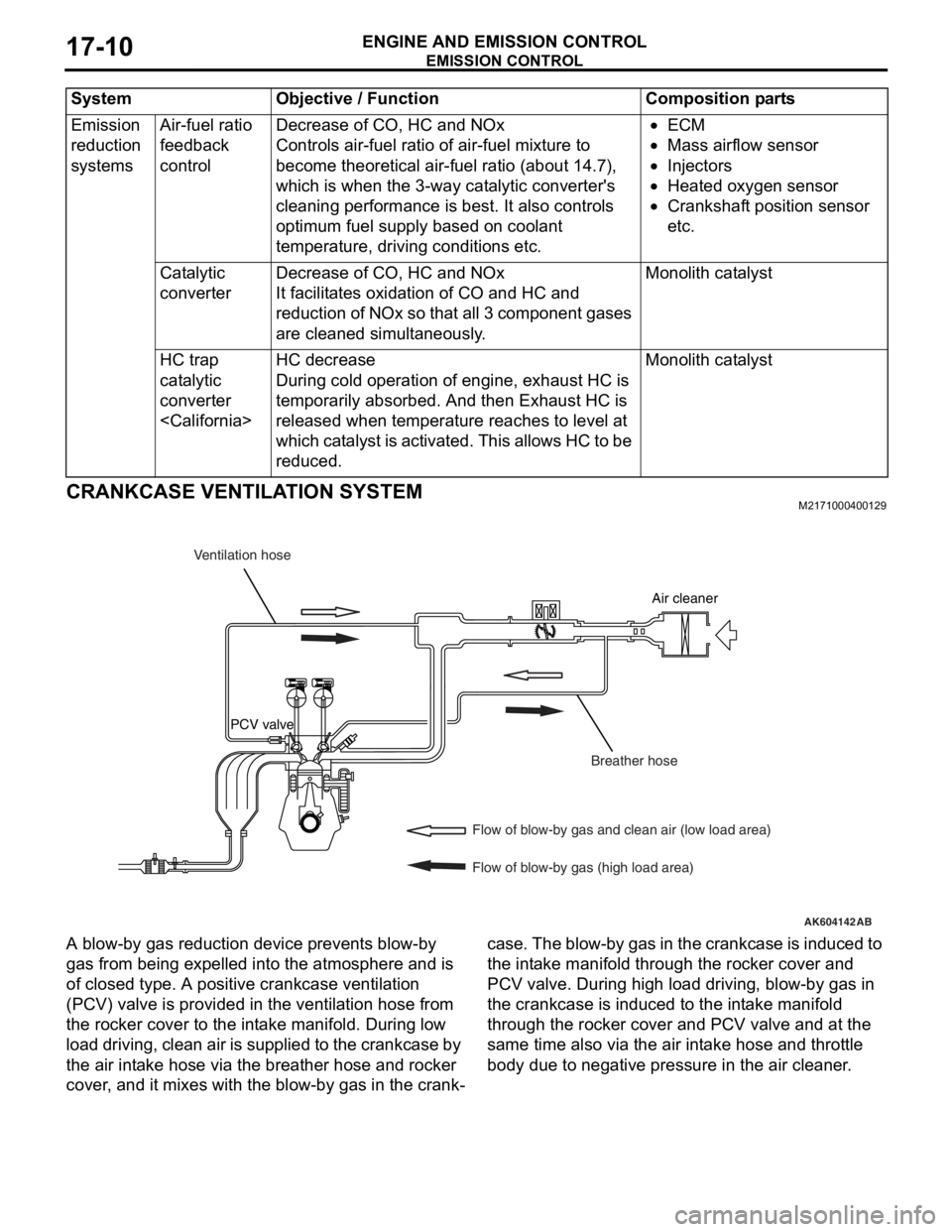
EMISSION CONTROL
ENGINE AND EMISSION CONTROL17-10
CRANKCASE VENTILATION SYSTEMM2171000400129
A blow-by gas reduction device prevents blow-by
gas from being expelled into the atmosphere and is
of closed type. A positive crankcase ventilation
(PCV) valve is provided in the ventilation hose from
the rocker cover to the intake manifold. During low
load driving, clean air is supplied to the crankcase by
the air intake hose via the breather hose and rocker
cover, and it mixes with the blow-by gas in the crank
-
case. The blow-by gas in the crankcase is induced to
the intake manifold through the rocker cover and
PCV valve. During high load driving, blow-by gas in
the crankcase is induced to the intake manifold
through the rocker cover and PCV valve and at the
same time also via the air intake hose and throttle
body due to negative pressure in the air cleaner.
Emission
reduction
systemsAir-fuel ratio
feedback
controlDecrease of CO, HC and NOx
Controls air-fuel ratio of air-fuel mixture to
become theoretical air-fuel ratio (about 14.7),
which is when the 3-way catalytic converter's
cleaning performance is best. It also controls
optimum fuel supply based on coolant
temperature, driving conditions etc.
•ECM
•Mass airflow sensor
•Injectors
•Heated oxygen sensor
•Crankshaft position sensor
etc.
Catalytic
converterDecrease of CO, HC and NOx
It facilitates oxidation of CO and HC and
reduction of NOx so that all 3 component gases
are cleaned simultaneously.
Monolith catalyst
HC trap
catalytic
converter
During cold operation of engine, exhaust HC is
temporarily absorbed. And then Exhaust HC is
released when temperature reaches to level at
which catalyst is activated. This allows HC to be
reduced.
Monolith catalyst
System Objective / Function Composition parts
AK604142
Air cleaner
PCV valve
AB
Ventilation hose
Breather hose
Flow of blow-by gas and clean air (low load area)
Flow of blow-by gas (high load area)
Page 73 of 241

EMISSION CONTROL
ENGINE AND EMISSION CONTROL17-11
POSITIVE CRANKCASE VENTILATION (PCV)
VA LV E
PCV valve lifts the plunger according to negative pressure in
the intake manifold to create appropriate ventilation for the
crankcase.
EVAPORATIVE EMISSION CONTROL SYSTEMM2171000200147
HC (hydrocarbon) generated in the fuel tank are
adsorbed by the active carbon in the canister and
stored. HC stored in the canister is introduced to the
intake manifold when engine is in operation where it
is mixed with intake air and combusted. ECM intro
-
duces optimum HC amount according to driving con-
ditions and so performs duty control on the
evaporative emission purge solenoid. Also, the evap
-
orative emission purge solenoid is closed during
deceleration or immediately after engine start to
restrict change in air-fuel ratio and prevent engine
from stalling.
AK602324AC
Plunger
From
rocker
coverTo intake
manifold
Spring
AK604143
Evaporative emission
purge solenoid
Mass airflow sensor
ECM Intake air temperature sensor
Manifold absolute pressure
sensor
Engine coolant temperature
sensor
Throttle position sensor
Crankshaft position sensorEvaporative emission
canister
AB
MFI relay
Battery
Page 74 of 241
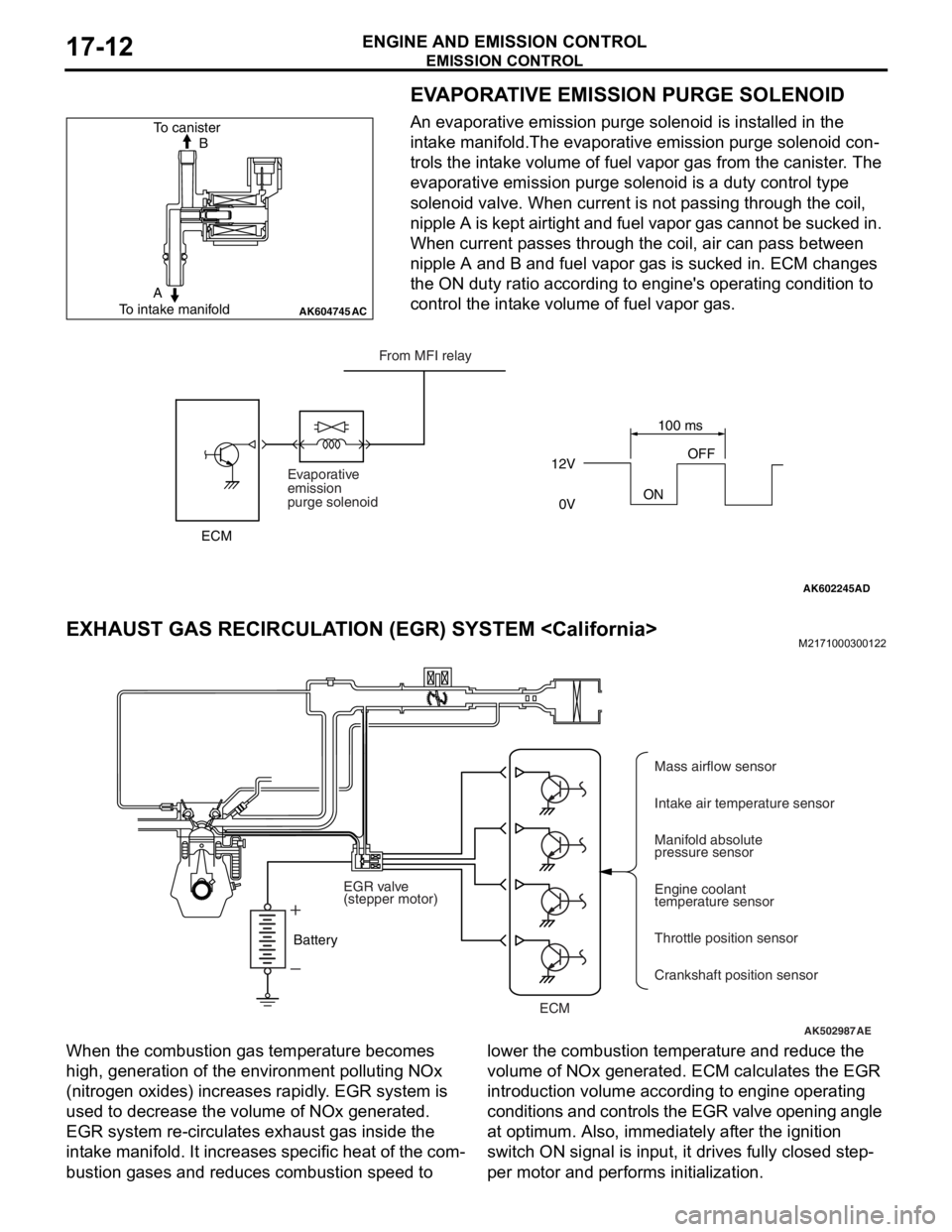
EMISSION CONTROL
ENGINE AND EMISSION CONTROL17-12
EVAPORATIVE EMISSION PURGE SOLENOID
An evaporative emission purge solenoid is installed in the
intake manifold.The evaporative emission purge solenoid con
-
trols the intake volume of fuel vapor gas from the canister. The
evaporative emission purge solenoid is a duty control type
solenoid valve. When current is not passing through the coil,
nipple A is kept airtight and fuel vapor gas cannot be sucked in.
When current passes through the coil, air can pass between
nipple A and B and fuel vapor gas is sucked in. ECM changes
the ON duty ratio according to engine's operating condition to
control the intake volume of fuel vapor gas.
EXHAUST GAS RECIRCULATION (EGR) SYSTEM
When the combustion gas temperature becomes
high, generation of the environment polluting NOx
(nitrogen oxides) increases rapidly. EGR system is
used to decrease the volume of NOx generated.
EGR system re-circulates exhaust gas inside the
intake manifold. It increases specific heat of the com
-
bustion gases and reduces combustion speed to lower the combustion temperature and reduce the
volume of NOx generated. ECM calculates the EGR
introduction volume according to engine operating
conditions and controls the EGR valve opening angle
at optimum. Also, immediately after the ignition
switch ON signal is input, it drives fully closed step
-
per motor and performs initialization.
AK604745AC
B To canister
To intake manifoldA
AK602245AD
12V
ONOFF
0V100 ms
Evaporative
emission
purge solenoidFrom MFI relay
ECM
AK502987AE
ECMMass airflow sensor
Intake air temperature sensor
Manifold absolute
pressure sensor
Engine coolant
temperature sensor
Throttle position sensor
Crankshaft position sensor BatteryEGR valve
(stepper motor)
Page 76 of 241
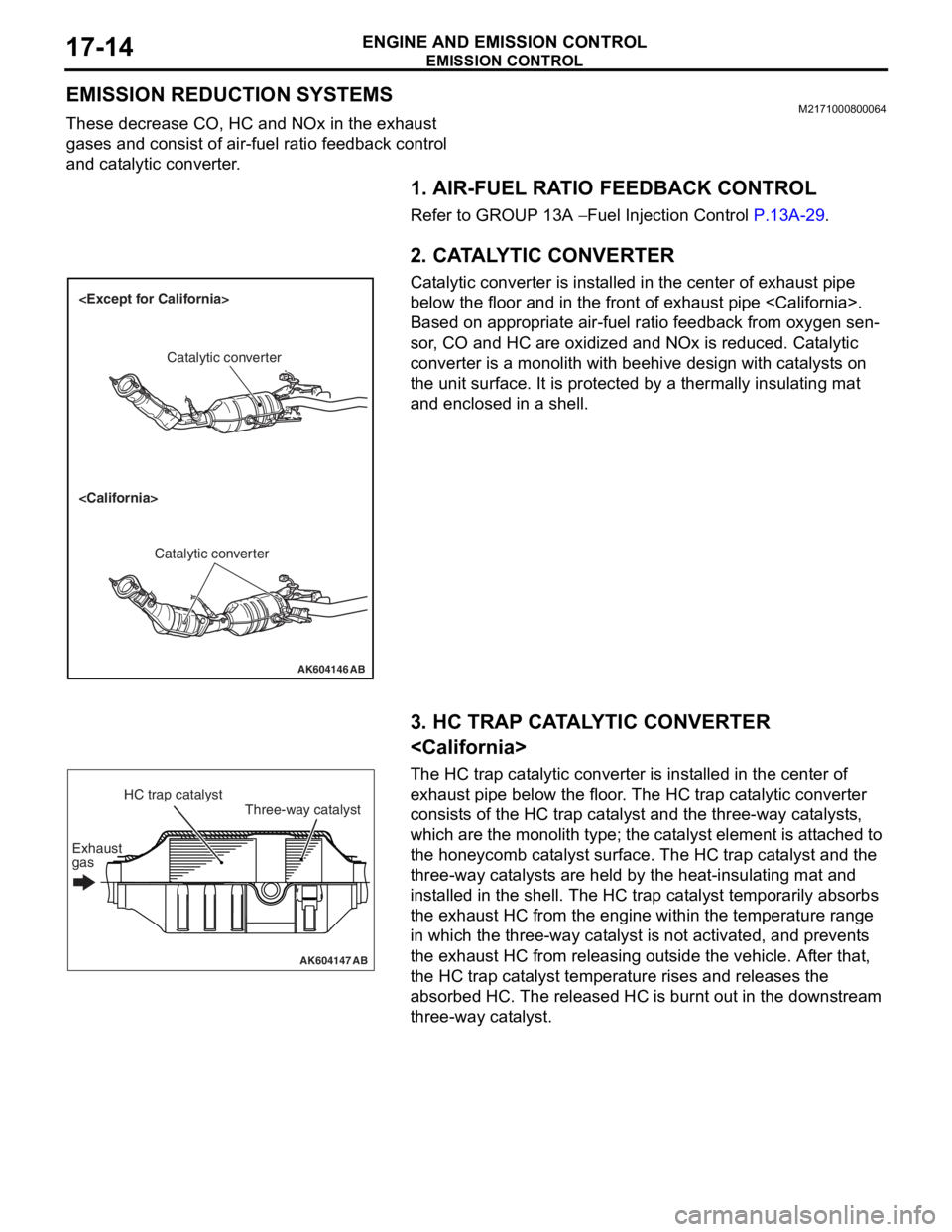
EMISSION CONTROL
ENGINE AND EMISSION CONTROL17-14
EMISSION REDUCTION SYSTEMSM2171000800064
These decrease CO, HC and NOx in the exhaust
gases and consist of air-fuel ratio feedback control
and catalytic converter.
1. AIR-FUEL RATIO FEEDBACK CONTROL
Refer to GROUP 13A − Fuel Injection Control P.13A-29.
2. CATALYTIC CONVERTER
Catalytic converter is installed in the center of exhaust pipe
below the floor and in the front of exhaust pipe
Based on appropriate air-fuel ratio feedback from oxygen sen
-
sor, CO and HC are oxidized and NOx is reduced. Catalytic
converter is a monolith with beehive design with catalysts on
the unit surface. It is protected by a thermally insulating mat
and enclosed in a shell.
3. HC TRAP CATALYTIC CONVERTER
The HC trap catalytic converter is installed in the center of
exhaust pipe below the floor. The HC trap catalytic converter
consists of the HC trap catalyst and the three-way catalysts,
which are the monolith type; the catalyst element is attached to
the honeycomb catalyst surface. The HC trap catalyst and the
three-way catalysts are held by the heat-insulating mat and
installed in the shell. The HC trap catalyst temporarily absorbs
the exhaust HC from the engine within the temperature range
in which the three-way catalyst is not activated, and prevents
the exhaust HC from releasing outside the vehicle. After that,
the HC trap catalyst temperature rises and releases the
absorbed HC. The released HC is burnt out in the downstream
three-way catalyst.
AK604146
Catalytic converter
Catalytic converter
AB
AK604147
Three-way catalyst HC trap catalyst
Exhaust
gas
AB
Page 97 of 241
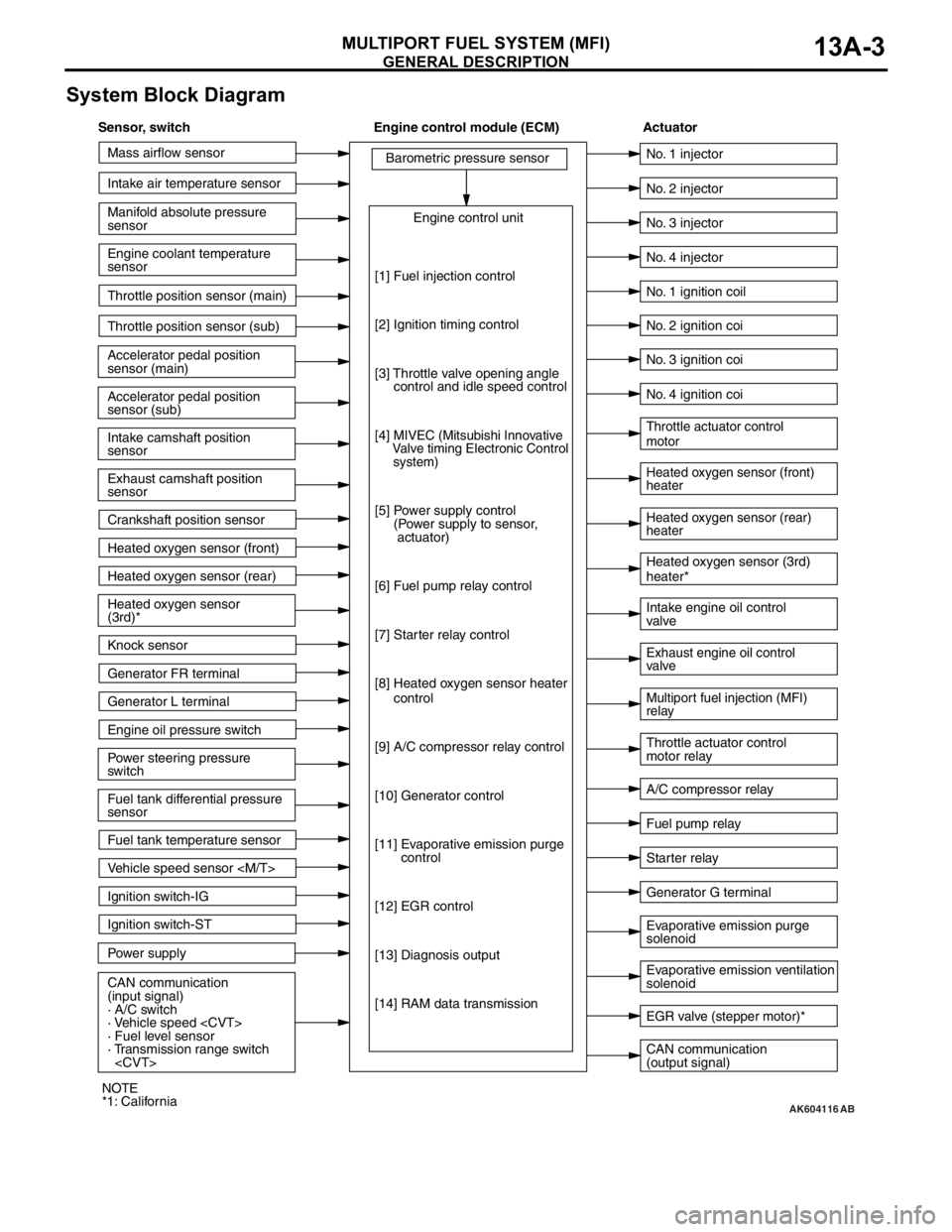
GENERAL DESCRIPTION
MULTIPORT FUEL SYSTEM (MFI)13A-3
System Block Diagram
AK604116
Mass airflow sensor
Intake air temperature sensor
Intake camshaft position
sensor
Exhaust camshaft position
sensor
Crankshaft position sensor Throttle position sensor (main)
Throttle position sensor (sub)
Accelerator pedal position
sensor (sub) Accelerator pedal position
sensor (main) Engine coolant temperature
sensor Manifold absolute pressure
sensor
Heated oxygen sensor (front)
Heated oxygen sensor (rear)
Power steering pressure
switch Engine oil pressure switch Generator L terminal
Ignition switch-ST
Power supply Ignition switch-IG
CAN communication
(input signal)
· A/C switch
· Vehicle speed
· Fuel level sensor
· Transmission range switch
sensor Heated oxygen sensor
(3rd)*
Knock sensor
Generator FR terminal
Fuel tank temperature sensor
Vehicle speed sensor
[1] Fuel injection control
[2] Ignition timing control
[3] Throttle valve opening angle
control and idle speed control
[4]
MIVEC (Mitsubishi Innovative
Valve timing Electronic Control
system)
[5] Power supply control
(Power supply to sensor,
actuator)
[6] Fuel pump relay control
[7] Starter relay control
[8] Heated oxygen sensor heater
control
[9] A/C compressor relay control
[10] Generator control
[11] Evaporative emission purge
control
[12] EGR control
[13] Diagnosis output
[14] RAM data transmission
CAN communication
(output signal) Intake engine oil control
valve
A/C compressor relay No. 2 injector
No. 3 injector
No. 4 injector
Heated oxygen sensor (front)
heater
Heated oxygen sensor (rear)
heater Throttle actuator control
motor
Throttle actuator control
motor relay No. 1 injector
No. 1 ignition coil
No. 2 ignition coi
No. 3 ignition coi
No. 4 ignition coi
Fuel pump relay
Generator G terminal Heated oxygen sensor (3rd)
heater*
Multiport fuel injection (MFI)
relay Exhaust engine oil control
valve
Evaporative emission ventilation
solenoid Evaporative emission purge
solenoid
EGR valve (stepper motor)*
Starter relay
AB
Sensor, switch Engine control module (ECM) Actuator
NOTE
*1: California
Page 98 of 241
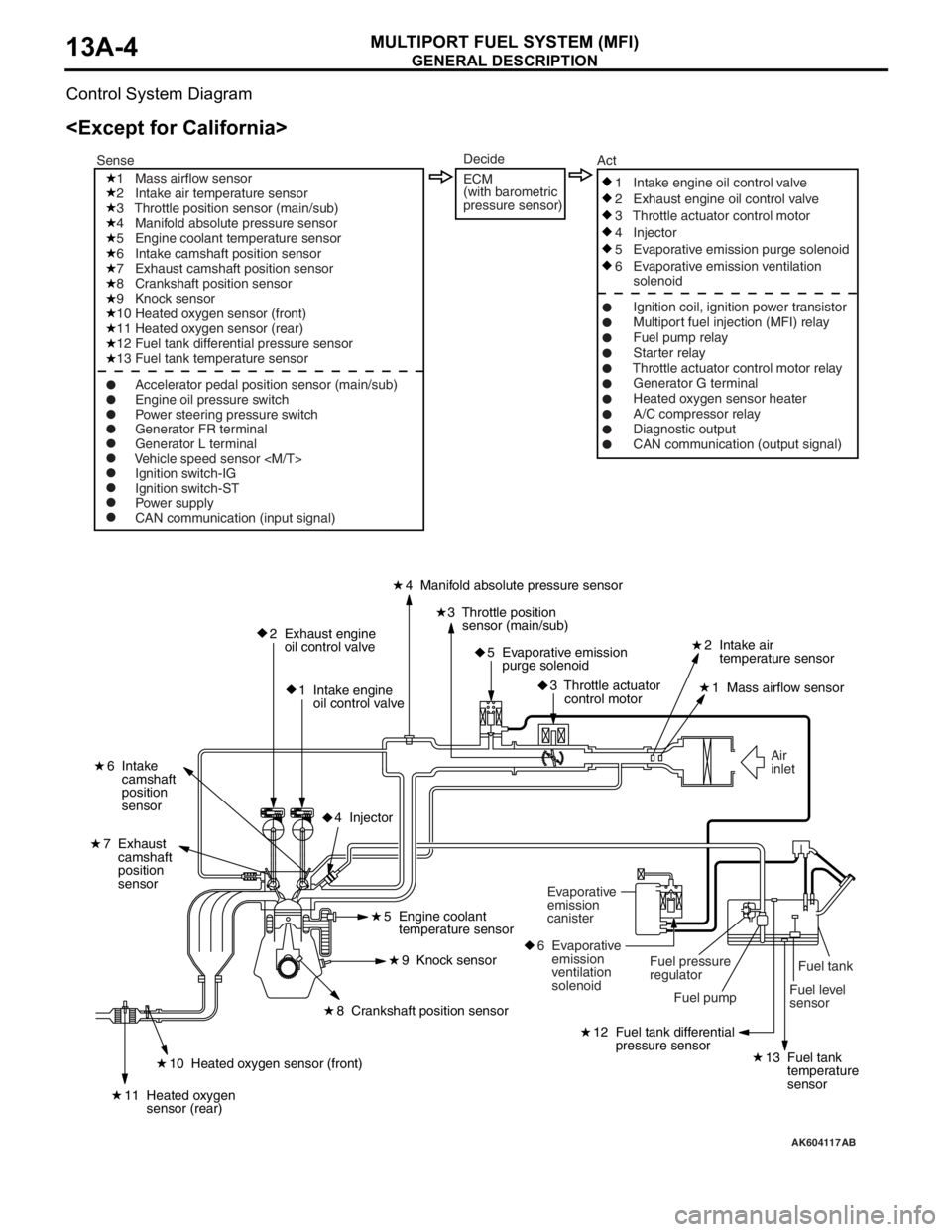
GENERAL DESCRIPTION
MULTIPORT FUEL SYSTEM (MFI)13A-4
Control System Diagram
AK604117
Fuel level
sensorFuel tank Air
inlet
2 Exhaust engine
oil control valve
1 Intake engine
oil control valve4 Manifold absolute pressure sensor
2 Intake air
temperature sensor
1 Mass airflow sensor
6 Intake
camshaft
position
sensor
7 Exhaust
camshaft
position
sensor
3 Throttle position
sensor (main/sub)
5 Evaporative emission
purge solenoid
3 Throttle actuator
control motor
12 Fuel tank differential
pressure sensor
13 Fuel tank
temperature
sensor10 Heated oxygen sensor (front)
11 Heated oxygen
sensor (rear)
8 Crankshaft position sensor5 Engine coolant
temperature sensor
9 Knock sensor
4 Injector
Fuel pump Fuel pressure
regulator Evaporative
emission
canister
6 Evaporative
emission
ventilation
solenoid
1 Mass airflow sensor
2 Intake air temperature sensor
3 Throttle position sensor (main/sub)
4 Manifold absolute pressure sensor
5 Engine coolant temperature sensor
6 Intake camshaft position sensor
7 Exhaust camshaft position sensor
8 Crankshaft position sensor
9 Knock sensor
10 Heated oxygen sensor (front)
11 Heated oxygen sensor (rear)
12 Fuel tank differential pressure sensor
13 Fuel tank temperature sensor
Ignition switch-IG
Ignition switch-ST
Power supply
CAN communication (input signal)1 Intake engine oil control valve
2 Exhaust engine oil control valve
3 Throttle actuator control motor
4 Injector
5 Evaporative emission purge solenoid
6 Evaporative emission ventilation
solenoid
Ignition coil, ignition power transistor
Multiport fuel injection (MFI) relay
Fuel pump relay
Starter relay
Throttle actuator control motor relay
Generator G terminal
Heated oxygen sensor heater
A/C compressor relay
Diagnostic output
CAN communication (output signal) SenseAct
Engine oil pressure switch
Power steering pressure switch
Generator FR terminal
Generator L terminal
Vehicle speed sensor
Decide
ECM
(with barometric
pressure sensor)
AB
Page 99 of 241
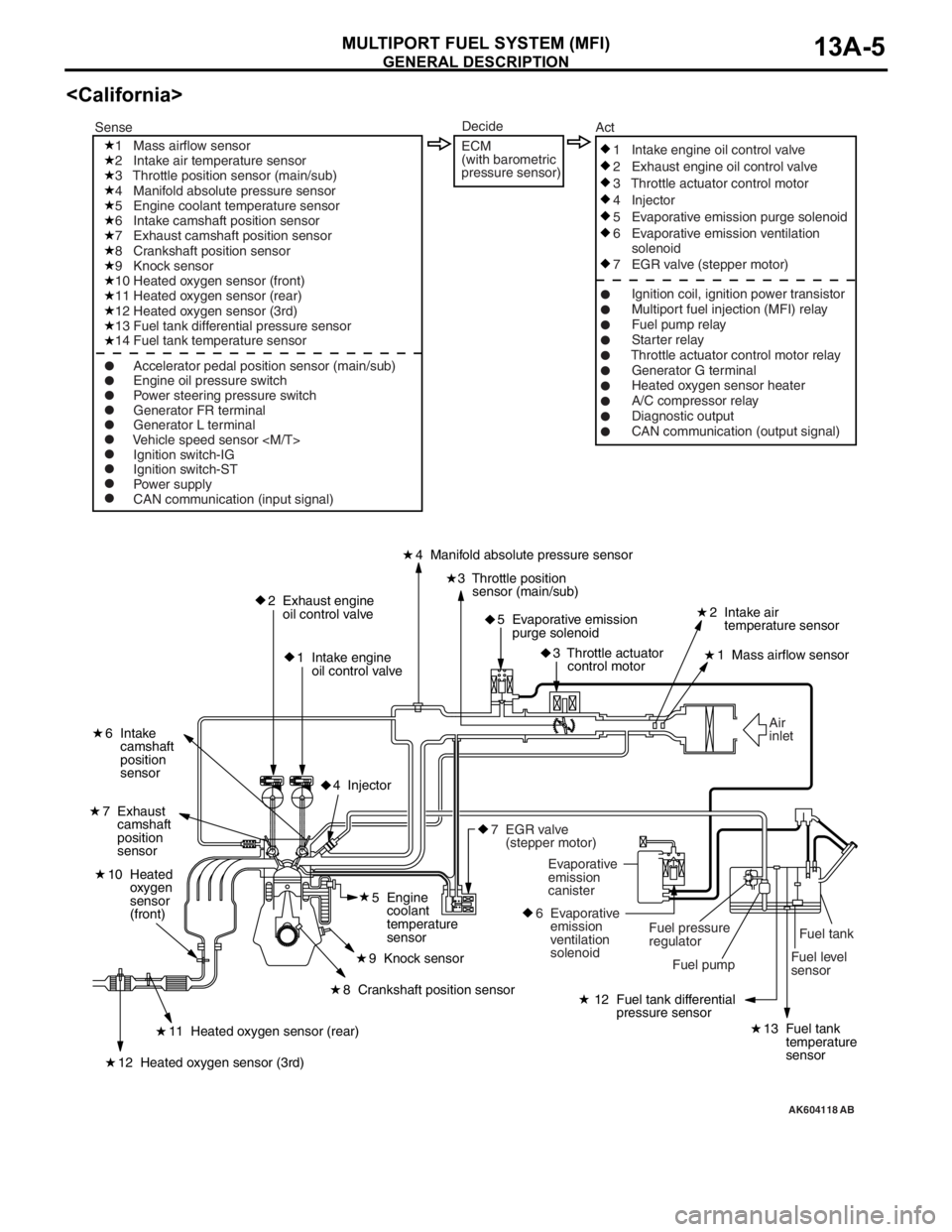
GENERAL DESCRIPTION
MULTIPORT FUEL SYSTEM (MFI)13A-5
AK604118
Fuel tank
Fuel level
sensor Air
inlet
2 Exhaust engine
oil control valve
1 Intake engine
oil control valve4 Manifold absolute pressure sensor
2 Intake air
temperature sensor
1 Mass airflow sensor
6 Intake
camshaft
position
sensor
7 Exhaust
camshaft
position
sensor
3 Throttle position
sensor (main/sub)
5 Evaporative emission
purge solenoid
3 Throttle actuator
control motor
12 Fuel tank differential
pressure sensor
13 Fuel tank
temperature
sensor11 Heated oxygen sensor (rear)
10 Heated
oxygen
sensor
(front)
12 Heated oxygen sensor (3rd)
8 Crankshaft position sensor5 Engine
coolant
temperature
sensor
9 Knock sensor
4 Injector
Fuel pump Fuel pressure
regulator Evaporative
emission
canister
6 Evaporative
emission
ventilation
solenoid
7 EGR valve
(stepper motor)
1 Mass airflow sensor
2 Intake air temperature sensor
3 Throttle position sensor (main/sub)
4 Manifold absolute pressure sensor
5 Engine coolant temperature sensor
6 Intake camshaft position sensor
7 Exhaust camshaft position sensor
8 Crankshaft position sensor
9 Knock sensor
10 Heated oxygen sensor (front)
11 Heated oxygen sensor (rear)
12 Heated oxygen sensor (3rd)
13 Fuel tank differential pressure sensor
14 Fuel tank temperature sensor
Ignition switch-IG
Ignition switch-ST
Power supply
CAN communication (input signal)1 Intake engine oil control valve
2 Exhaust engine oil control valve
3 Throttle actuator control motor
4 Injector
5 Evaporative emission purge solenoid
6 Evaporative emission ventilation
solenoid
7 EGR valve (stepper motor)
Ignition coil, ignition power transistor
Multiport fuel injection (MFI) relay
Fuel pump relay
Starter relay
Throttle actuator control motor relay
Generator G terminal
Heated oxygen sensor heater
A/C compressor relay
Diagnostic output
CAN communication (output signal) SenseAct
Engine oil pressure switch
Power steering pressure switch
Generator FR terminal
Generator L terminal
Vehicle speed sensor
Decide
ECM
(with barometric
pressure sensor)
AB