MITSUBISHI MONTERO 1998 Service Manual
Manufacturer: MITSUBISHI, Model Year: 1998, Model line: MONTERO, Model: MITSUBISHI MONTERO 1998Pages: 1501, PDF Size: 25.81 MB
Page 101 of 1501
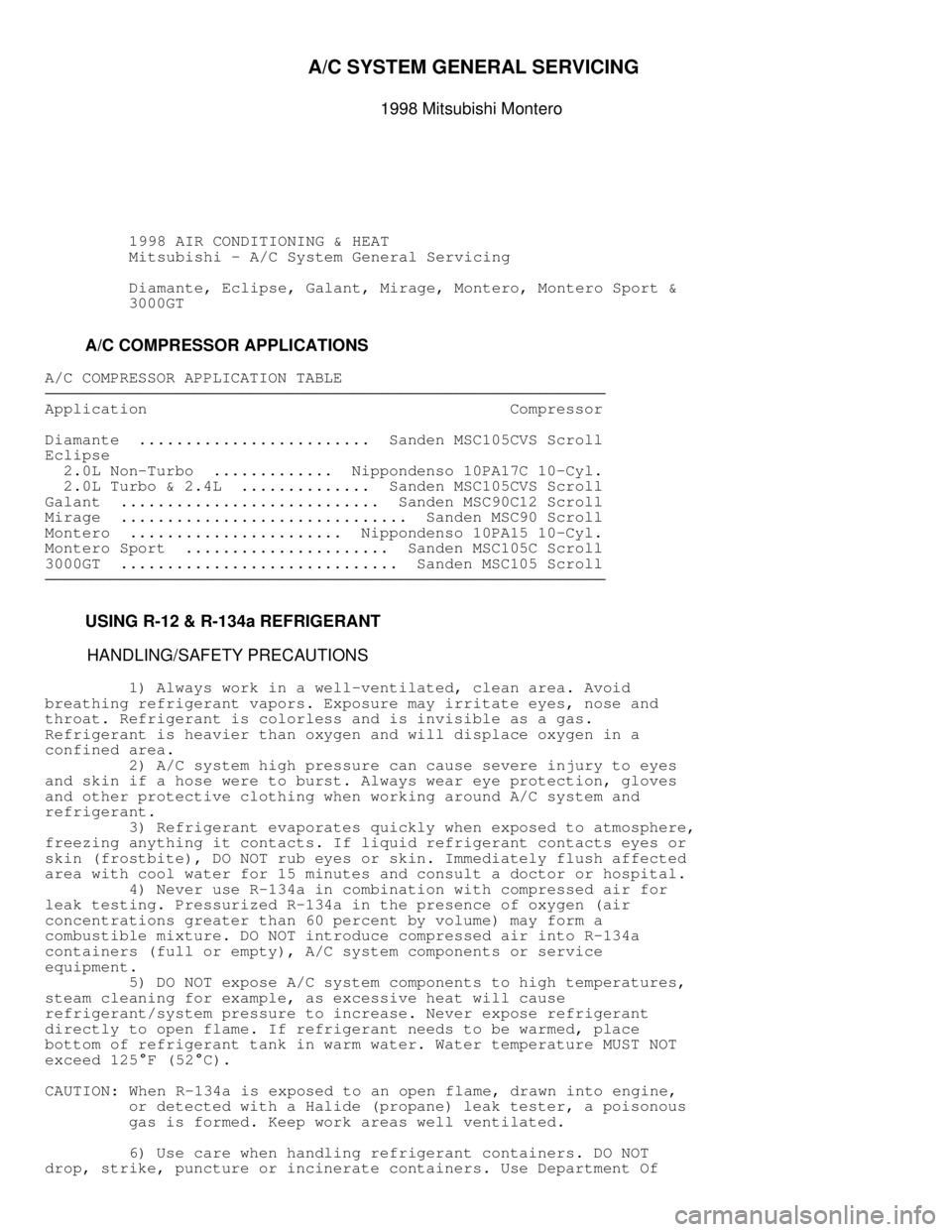
A/C SYSTEM GENERAL SERVICING
1998 Mitsubishi Montero
1998 AIR CONDITIONING & HEAT
Mitsubishi - A/C System General Servicing
Diamante, Eclipse, Galant, Mirage, Montero, Montero Sport &
3000GT
A/C COMPRESSOR APPLICATIONS
A/C COMPRESSOR APPLICATION TABLE \
\
\
\
\
\
Application Compressor
Diamante ......................... Sanden MSC105CVS Scroll
Eclipse
2.0L Non-Turbo ............. Nippondenso 10PA17C 10-Cyl.
2.0L Turbo & 2.4L .............. Sanden MSC105CVS Scroll
Galant ............................ Sanden MSC90C12 Scroll
Mirage ............................... Sanden MSC90 Scroll
Montero ....................... Nippondenso 10PA15 10-Cyl.
Montero Sport ...................... Sanden MSC105C Scroll
3000GT .............................. Sanden MSC105 Scroll
\
\
\
\
\
\
USING R-12 & R-134a REFRIGERANT
HANDLING/SAFETY PRECAUTIONS
1) Always work in a well-ventilated, clean area. Avoid
breathing refrigerant vapors. Exposure may irritate eyes, nose and
throat. Refrigerant is colorless and is invisible as a gas.
Refrigerant is heavier than oxygen and will displace oxygen in a
confined area.
2) A/C system high pressure can cause severe injury to eyes
and skin if a hose were to burst. Always wear eye protection, gloves
and other protective clothing when working around A/C system and
refrigerant.
3) Refrigerant evaporates quickly when exposed to atmosphere,
freezing anything it contacts. If liquid refrigerant contacts eyes or
skin (frostbite), DO NOT rub eyes or skin. Immediately flush affected
area with cool water for 15 minutes and consult a doctor or hospital.
4) Never use R-134a in combination with compressed air for
leak testing. Pressurized R-134a in the presence of oxygen (air
concentrations greater than 60 percent by volume) may form a
combustible mixture. DO NOT introduce compressed air into R-134a
containers (full or empty), A/C system components or service
equipment.
5) DO NOT expose A/C system components to high temperatures,
steam cleaning for example, as excessive heat will cause
refrigerant/system pressure to increase. Never expose refrigerant
directly to open flame. If refrigerant needs to be warmed, place
bottom of refrigerant tank in warm water. Water temperature MUST NOT
exceed 125
F (52C).
CAUTION: When R-134a is exposed to an open flame, drawn into engine,
or detected with a Halide (propane) leak tester, a poisonous
gas is formed. Keep work areas well ventilated.
6) Use care when handling refrigerant containers. DO NOT
drop, strike, puncture or incinerate containers. Use Department Of
Page 102 of 1501
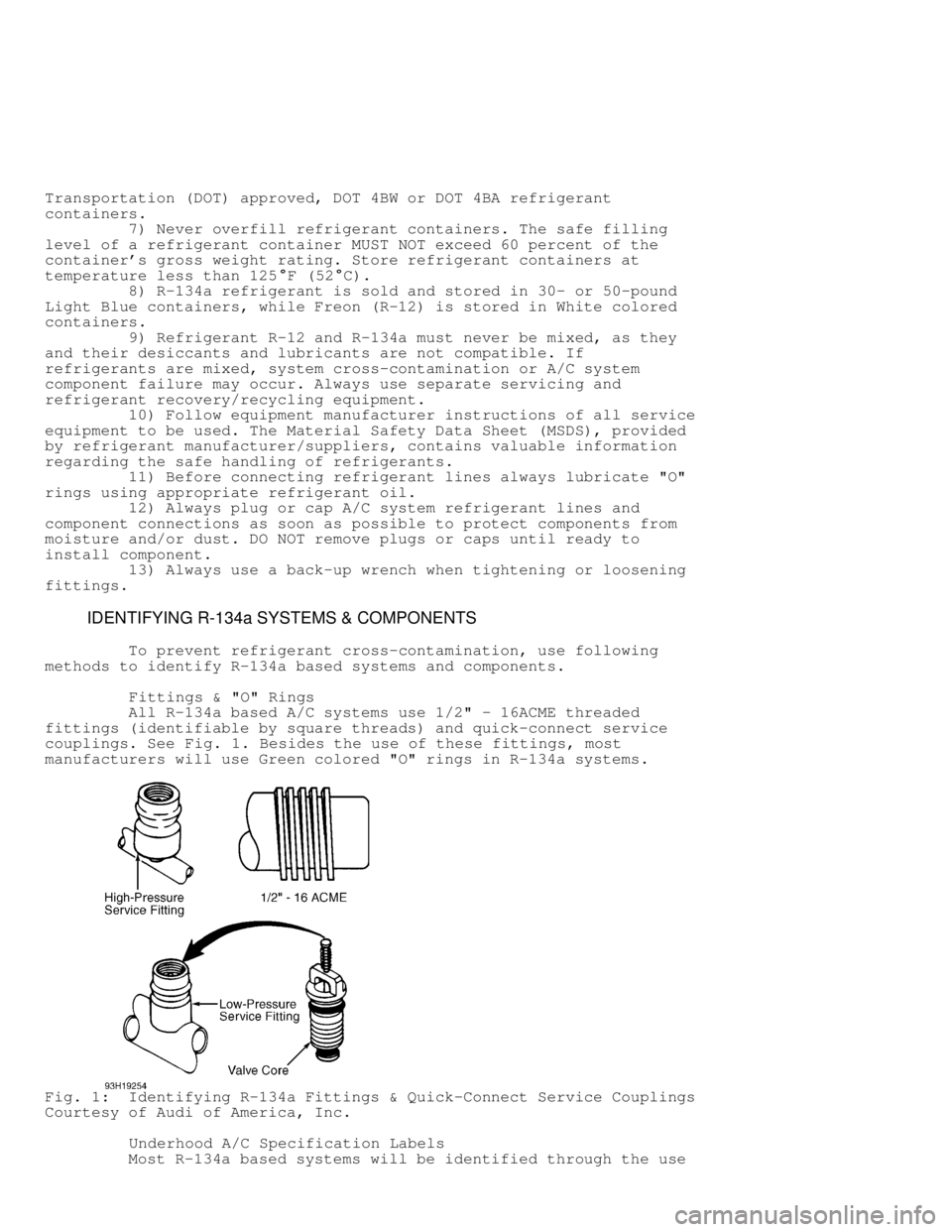
Transportation (DOT) approved, DOT 4BW or DOT 4BA refrigerant
containers.
7) Never overfill refrigerant containers. The safe filling
level of a refrigerant container MUST NOT exceed 60 percent of the
container's gross weight rating. Store refrigerant containers at
temperature less than 125
F (52C).
8) R-134a refrigerant is sold and stored in 30- or 50-pound
Light Blue containers, while Freon (R-12) is stored in White colored
containers.
9) Refrigerant R-12 and R-134a must never be mixed, as they
and their desiccants and lubricants are not compatible. If
refrigerants are mixed, system cross-contamination or A/C system
component failure may occur. Always use separate servicing and
refrigerant recovery/recycling equipment.
10) Follow equipment manufacturer instructions of all service
equipment to be used. The Material Safety Data Sheet (MSDS), provided
by refrigerant manufacturer/suppliers, contains valuable information
regarding the safe handling of refrigerants.
11) Before connecting refrigerant lines always lubricate "O"
rings using appropriate refrigerant oil.
12) Always plug or cap A/C system refrigerant lines and
component connections as soon as possible to protect components from
moisture and/or dust. DO NOT remove plugs or caps until ready to
install component.
13) Always use a back-up wrench when tightening or loosening
fittings.
IDENTIFYING R-134a SYSTEMS & COMPONENTS
To prevent refrigerant cross-contamination, use following
methods to identify R-134a based systems and components.
Fittings & "O" Rings
All R-134a based A/C systems use 1/2" - 16ACME threaded
fittings (identifiable by square threads) and quick-connect service
couplings. See Fig. 1. Besides the use of these fittings, most
manufacturers will use Green colored "O" rings in R-134a systems.
Fig. 1: Identifying R-134a Fittings & Quick-Connect Service Couplings
Courtesy of Audi of America, Inc.
Underhood A/C Specification Labels
Most R-134a based systems will be identified through the use
Page 103 of 1501
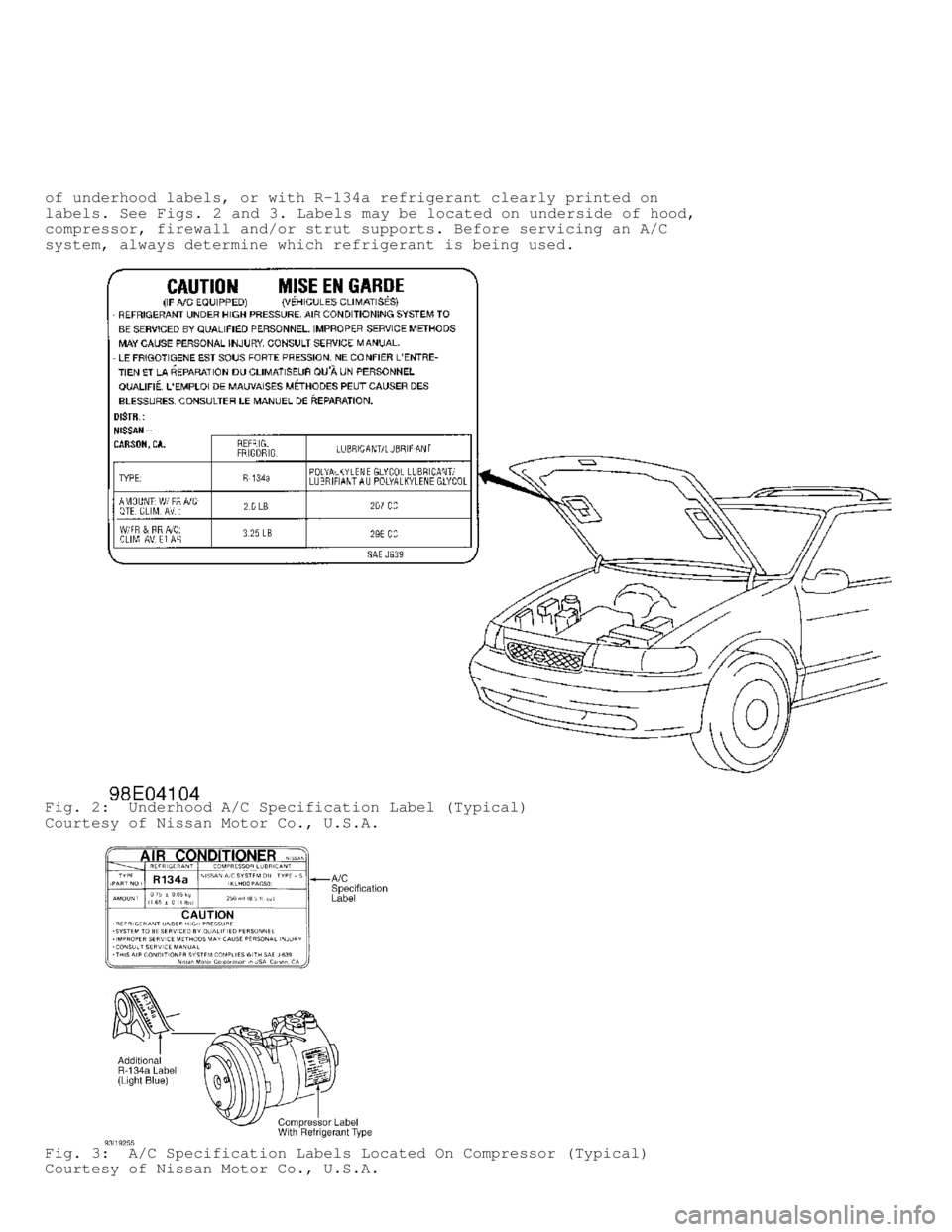
of underhood labels, or with R-134a refrigerant clearly printed on
labels. See Figs. 2 and 3. Labels may be located on underside of hood,
compressor, firewall and/or strut supports. Before servicing an A/C
system, always determine which refrigerant is being used.
Fig. 2: Underhood A/C Specification Label (Typical)
Courtesy of Nissan Motor Co., U.S.A.
Fig. 3: A/C Specification Labels Located On Compressor (Typical)
Courtesy of Nissan Motor Co., U.S.A.
Page 104 of 1501
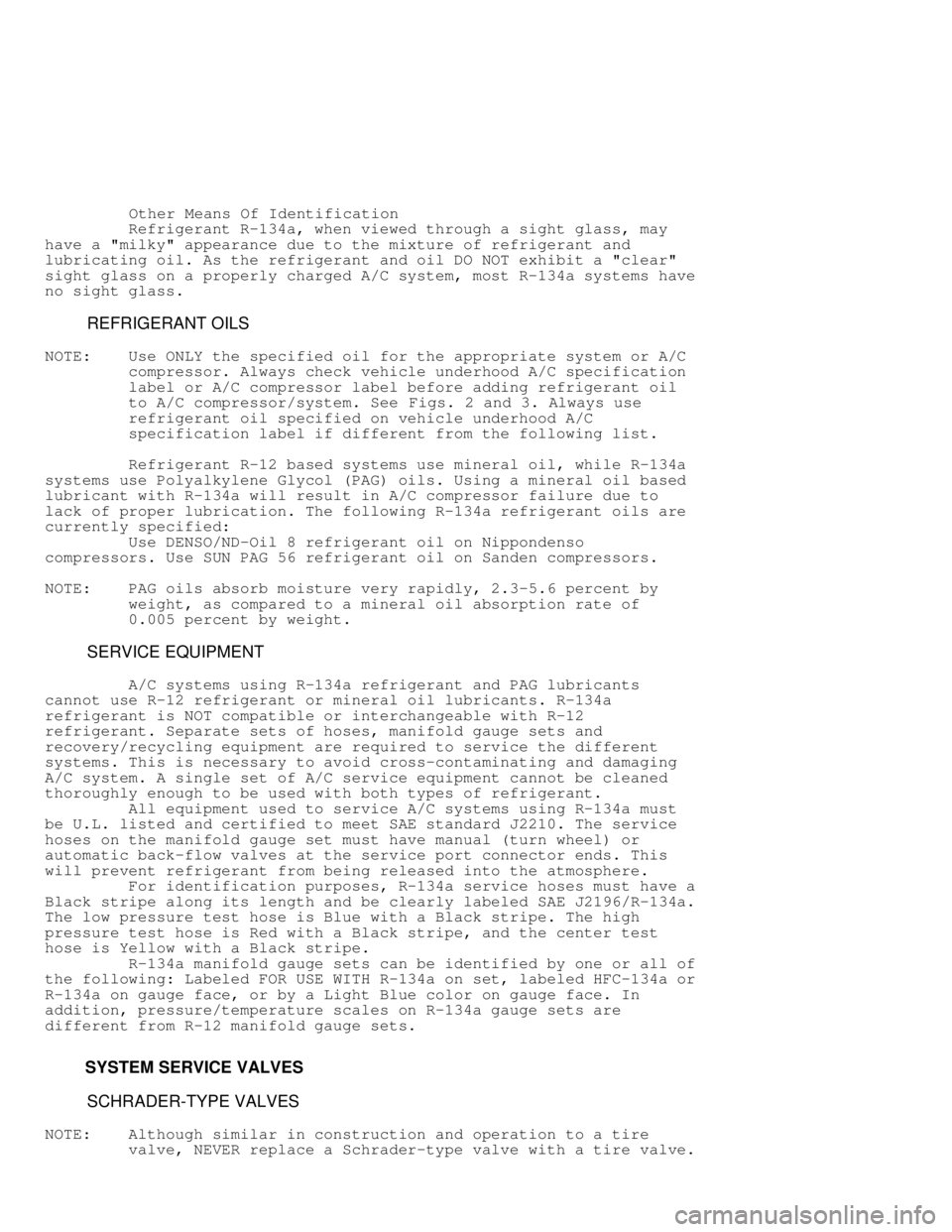
Other Means Of Identification
Refrigerant R-134a, when viewed through a sight glass, may
have a "milky" appearance due to the mixture of refrigerant and
lubricating oil. As the refrigerant and oil DO NOT exhibit a "clear"
sight glass on a properly charged A/C system, most R-134a systems have
no sight glass.
REFRIGERANT OILS
NOTE: Use ONLY the specified oil for the appropriate system or A/C
compressor. Always check vehicle underhood A/C specification
label or A/C compressor label before adding refrigerant oil
to A/C compressor/system. See Figs. 2 and 3. Always use
refrigerant oil specified on vehicle underhood A/C
specification label if different from the following list.
Refrigerant R-12 based systems use mineral oil, while R-134a
systems use Polyalkylene Glycol (PAG) oils. Using a mineral oil based
lubricant with R-134a will result in A/C compressor failure due to
lack of proper lubrication. The following R-134a refrigerant oils are
currently specified:
Use DENSO/ND-Oil 8 refrigerant oil on Nippondenso
compressors. Use SUN PAG 56 refrigerant oil on Sanden compressors.
NOTE: PAG oils absorb moisture very rapidly, 2.3-5.6 percent by
weight, as compared to a mineral oil absorption rate of
0.005 percent by weight.
SERVICE EQUIPMENT
A/C systems using R-134a refrigerant and PAG lubricants
cannot use R-12 refrigerant or mineral oil lubricants. R-134a
refrigerant is NOT compatible or interchangeable with R-12
refrigerant. Separate sets of hoses, manifold gauge sets and
recovery/recycling equipment are required to service the different
systems. This is necessary to avoid cross-contaminating and damaging
A/C system. A single set of A/C service equipment cannot be cleaned
thoroughly enough to be used with both types of refrigerant.
All equipment used to service A/C systems using R-134a must
be U.L. listed and certified to meet SAE standard J2210. The service
hoses on the manifold gauge set must have manual (turn wheel) or
automatic back-flow valves at the service port connector ends. This
will prevent refrigerant from being released into the atmosphere.
For identification purposes, R-134a service hoses must have a
Black stripe along its length and be clearly labeled SAE J2196/R-134a.
The low pressure test hose is Blue with a Black stripe. The high
pressure test hose is Red with a Black stripe, and the center test
hose is Yellow with a Black stripe.
R-134a manifold gauge sets can be identified by one or all of
the following: Labeled FOR USE WITH R-134a on set, labeled HFC-134a or
R-134a on gauge face, or by a Light Blue color on gauge face. In
addition, pressure/temperature scales on R-134a gauge sets are
different from R-12 manifold gauge sets.
SYSTEM SERVICE VALVES
SCHRADER-TYPE VALVES
NOTE: Although similar in construction and operation to a tire
valve, NEVER replace a Schrader-type valve with a tire valve.
Page 105 of 1501
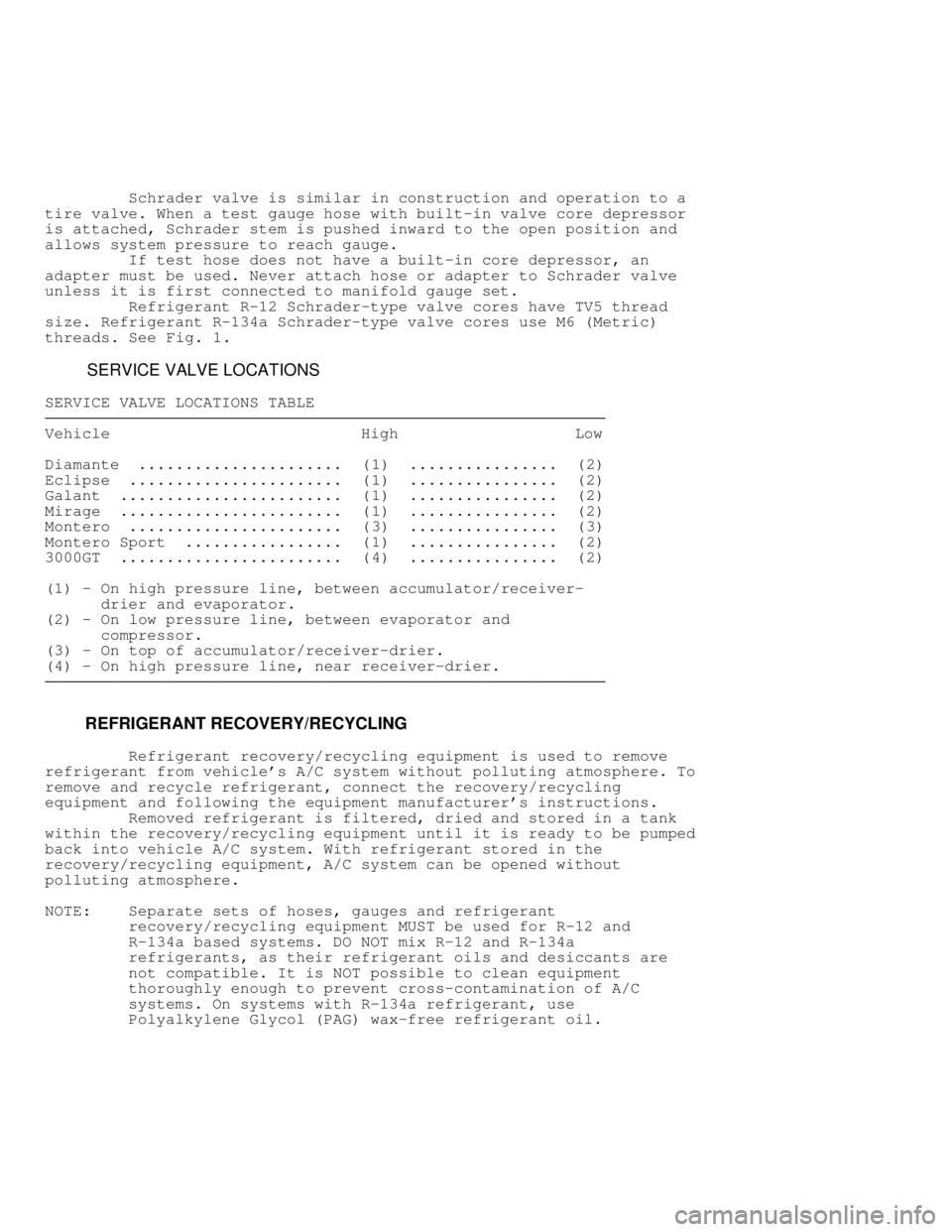
Schrader valve is similar in construction and operation to a
tire valve. When a test gauge hose with built-in valve core depressor
is attached, Schrader stem is pushed inward to the open position and
allows system pressure to reach gauge.
If test hose does not have a built-in core depressor, an
adapter must be used. Never attach hose or adapter to Schrader valve
unless it is first connected to manifold gauge set.
Refrigerant R-12 Schrader-type valve cores have TV5 thread
size. Refrigerant R-134a Schrader-type valve cores use M6 (Metric)
threads. See Fig. 1.
SERVICE VALVE LOCATIONS
SERVICE VALVE LOCATIONS TABLE \
\
\
\
\
\
Vehicle High Low
Diamante ...................... ( 1) ................ ( 2)
Eclipse ....................... ( 1) ................ ( 2)
Galant ........................ ( 1) ................ ( 2)
Mirage ........................ ( 1) ................ ( 2)
Montero ....................... ( 3) ................ ( 3)
Montero Sport ................. ( 1) ................ ( 2)
3000GT ........................ ( 4) ................ ( 2)
( 1) - On high pressure line, between accumulator/receiver-
drier and evaporator.
( 2) - On low pressure line, between evaporator and
compressor.
( 3) - On top of accumulator/receiver-drier.
( 4) - On high pressure line, near receiver-drier.
\
\
\
\
\
\
REFRIGERANT RECOVERY/RECYCLING
Refrigerant recovery/recycling equipment is used to remove
refrigerant from vehicle's A/C system without polluting atmosphere. To
remove and recycle refrigerant, connect the recovery/recycling
equipment and following the equipment manufacturer's instructions.
Removed refrigerant is filtered, dried and stored in a tank
within the recovery/recycling equipment until it is ready to be pumped
back into vehicle A/C system. With refrigerant stored in the
recovery/recycling equipment, A/C system can be opened without
polluting atmosphere.
NOTE: Separate sets of hoses, gauges and refrigerant
recovery/recycling equipment MUST be used for R-12 and
R-134a based systems. DO NOT mix R-12 and R-134a
refrigerants, as their refrigerant oils and desiccants are
not compatible. It is NOT possible to clean equipment
thoroughly enough to prevent cross-contamination of A/C
systems. On systems with R-134a refrigerant, use
Polyalkylene Glycol (PAG) wax-free refrigerant oil.
Page 106 of 1501
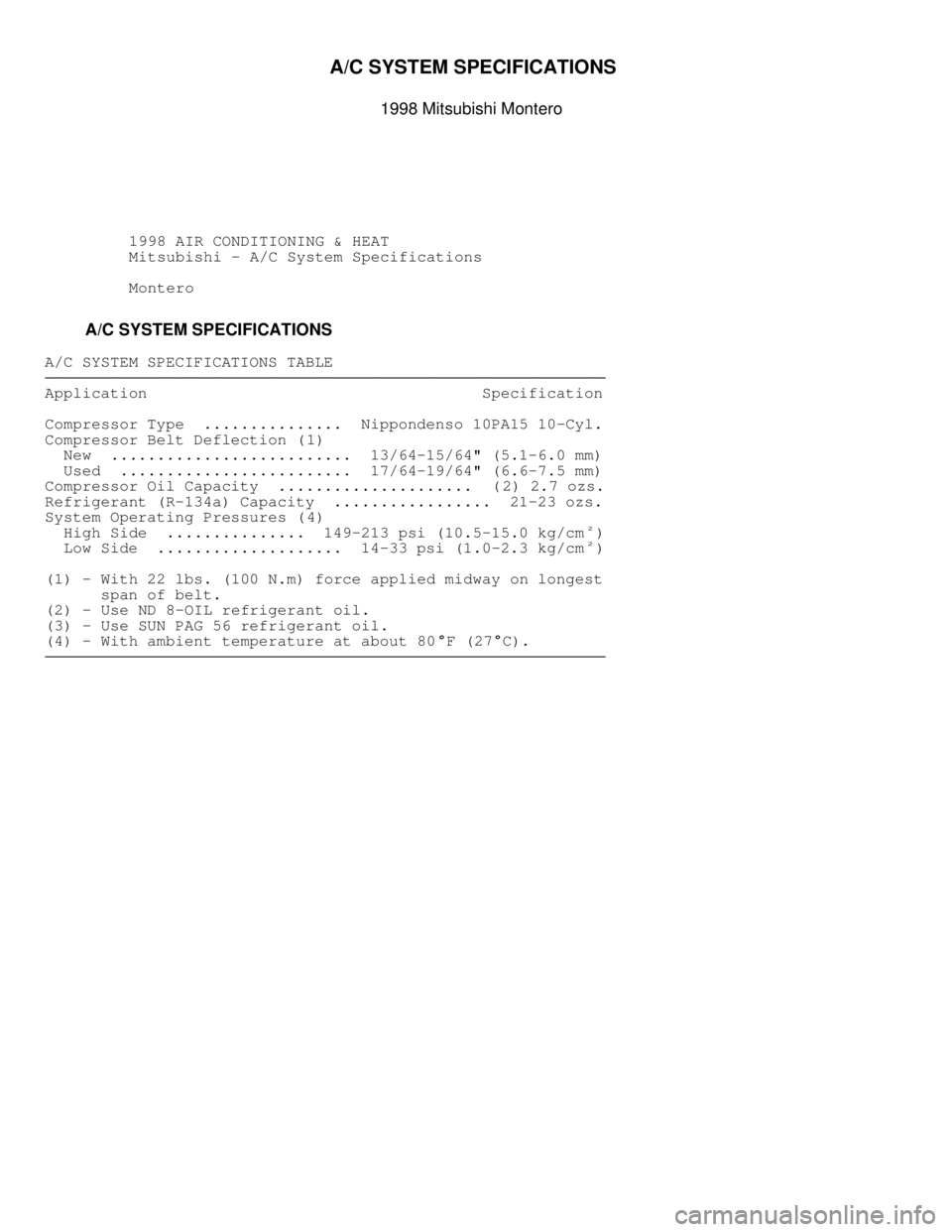
A/C SYSTEM SPECIFICATIONS
1998 Mitsubishi Montero
1998 AIR CONDITIONING & HEAT
Mitsubishi - A/C System Specifications
Montero
A/C SYSTEM SPECIFICATIONS
A/C SYSTEM SPECIFICATIONS TABLE \
\
\
\
\
\
Application Specification
Compressor Type ............... Nippondenso 10PA15 10-Cyl.
Compressor Belt Deflection ( 1)
New .......................... 13/64-15/64" (5.1-6.0 mm)
Used ......................... 17/64-19/64" (6.6-7.5 mm)
Compressor Oil Capacity ..................... ( 2) 2.7 ozs.
Refrigerant (R-134a) Capacity ................. 21-23 ozs.
System Operating Pressures ( 4)
High Side ............... 149-213 psi (10.5-15.0 kg/cm
)
Low Side .................... 14-33 psi (1.0-2.3 kg/cm)
( 1) - With 22 lbs. (100 N.m) force applied midway on longest
span of belt.
( 2) - Use ND 8-OIL refrigerant oil.
( 3) - Use SUN PAG 56 refrigerant oil.
( 4) - With ambient temperature at about 80
F (27C). \
\
\
\
\
\
Page 107 of 1501
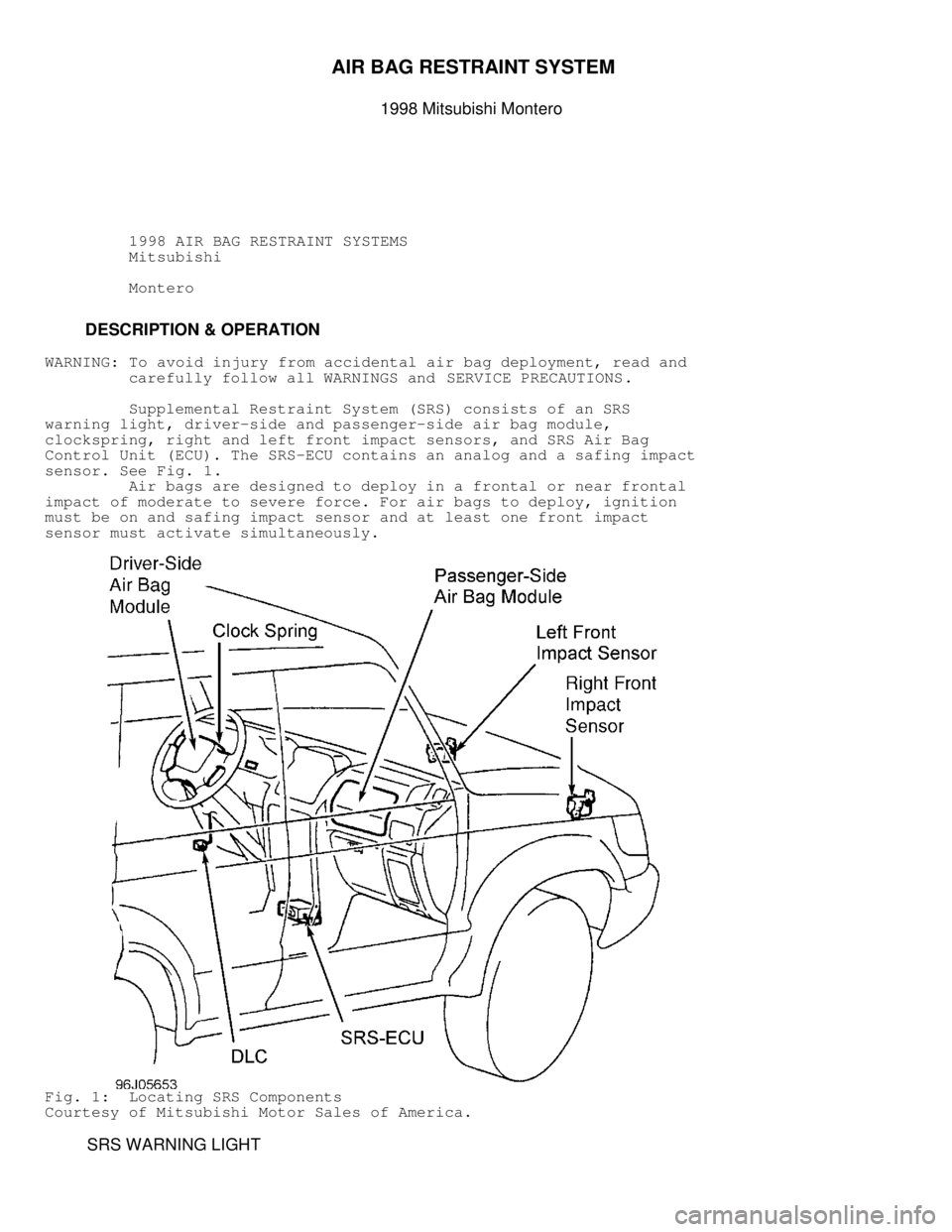
AIR BAG RESTRAINT SYSTEM
1998 Mitsubishi Montero
1998 AIR BAG RESTRAINT SYSTEMS
Mitsubishi
Montero
DESCRIPTION & OPERATION
WARNING: To avoid injury from accidental air bag deployment, read and
carefully follow all WARNINGS and SERVICE PRECAUTIONS.
Supplemental Restraint System (SRS) consists of an SRS
warning light, driver-side and passenger-side air bag module,
clockspring, right and left front impact sensors, and SRS Air Bag
Control Unit (ECU). The SRS-ECU contains an analog and a safing impact\
sensor. See Fig. 1.
Air bags are designed to deploy in a frontal or near frontal
impact of moderate to severe force. For air bags to deploy, ignition
must be on and safing impact sensor and at least one front impact
sensor must activate simultaneously.
Fig. 1: Locating SRS Components
Courtesy of Mitsubishi Motor Sales of America.
SRS WARNING LIGHT
Page 108 of 1501
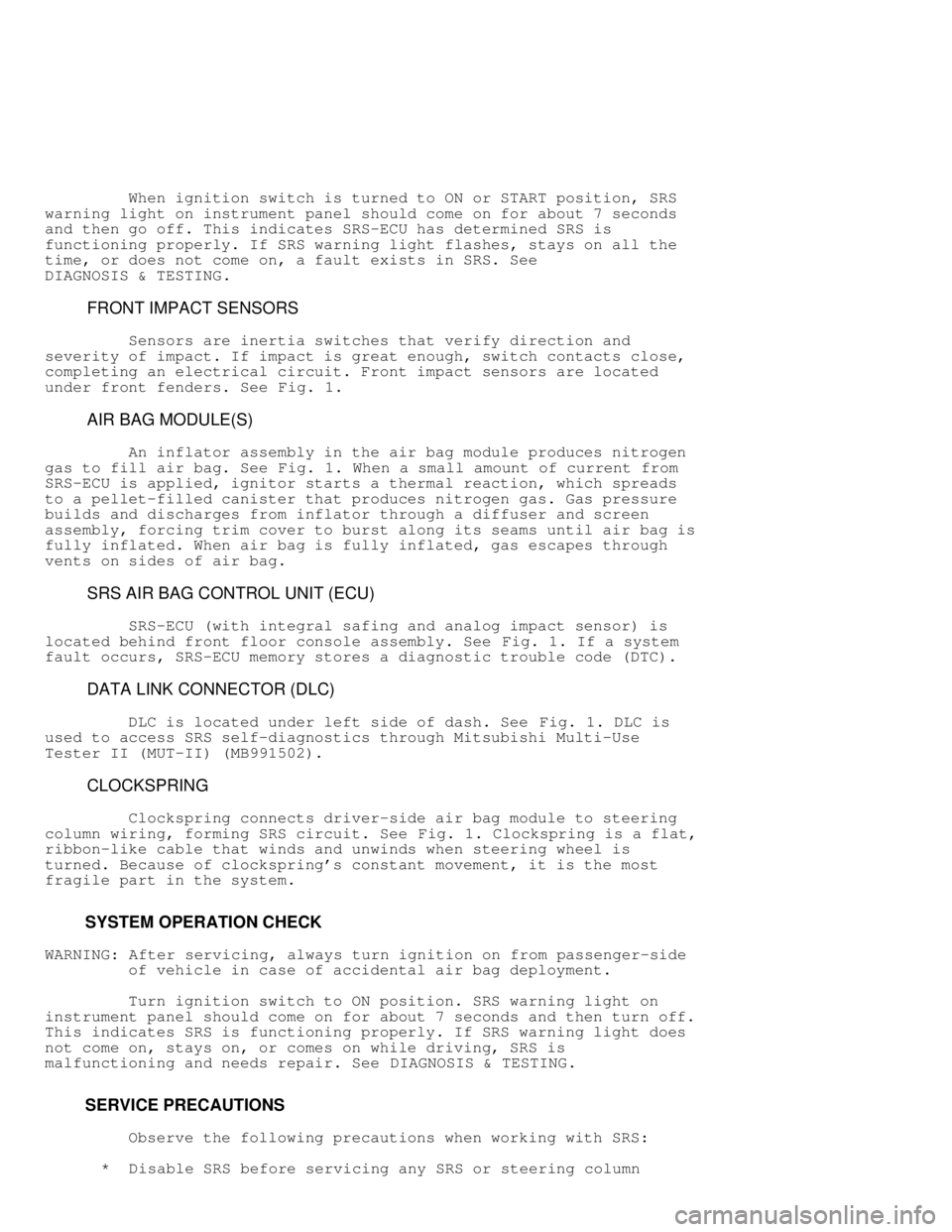
When ignition switch is turned to ON or START position, SRS
warning light on instrument panel should come on for about 7 seconds
and then go off. This indicates SRS-ECU has determined SRS is
functioning properly. If SRS warning light flashes, stays on all the
time, or does not come on, a fault exists in SRS. See
DIAGNOSIS & TESTING.
FRONT IMPACT SENSORS
Sensors are inertia switches that verify direction and
severity of impact. If impact is great enough, switch contacts close,
completing an electrical circuit. Front impact sensors are located
under front fenders. See Fig. 1.
AIR BAG MODULE(S)
An inflator assembly in the air bag module produces nitrogen
gas to fill air bag. See Fig. 1. When a small amount of current from
SRS-ECU is applied, ignitor starts a thermal reaction, which spreads
to a pellet-filled canister that produces nitrogen gas. Gas pressure
builds and discharges from inflator through a diffuser and screen
assembly, forcing trim cover to burst along its seams until air bag is
fully inflated. When air bag is fully inflated, gas escapes through
vents on sides of air bag.
SRS AIR BAG CONTROL UNIT (ECU)
SRS-ECU (with integral safing and analog impact sensor) is
located behind front floor console assembly. See Fig. 1. If a system
fault occurs, SRS-ECU memory stores a diagnostic trouble code (DTC).
DATA LINK CONNECTOR (DLC)
DLC is located under left side of dash. See Fig. 1. DLC is
used to access SRS self-diagnostics through Mitsubishi Multi-Use
Tester II (MUT-II) (MB991502).
CLOCKSPRING
Clockspring connects driver-side air bag module to steering
column wiring, forming SRS circuit. See Fig. 1. Clockspring is a flat,
ribbon-like cable that winds and unwinds when steering wheel is
turned. Because of clockspring's constant movement, it is the most
fragile part in the system.
SYSTEM OPERATION CHECK
WARNING: After servicing, always turn ignition on from passenger-side
of vehicle in case of accidental air bag deployment.
Turn ignition switch to ON position. SRS warning light on
instrument panel should come on for about 7 seconds and then turn off.
This indicates SRS is functioning properly. If SRS warning light does
not come on, stays on, or comes on while driving, SRS is
malfunctioning and needs repair. See DIAGNOSIS & TESTING.
SERVICE PRECAUTIONS
Observe the following precautions when working with SRS:
* Disable SRS before servicing any SRS or steering column
Page 109 of 1501
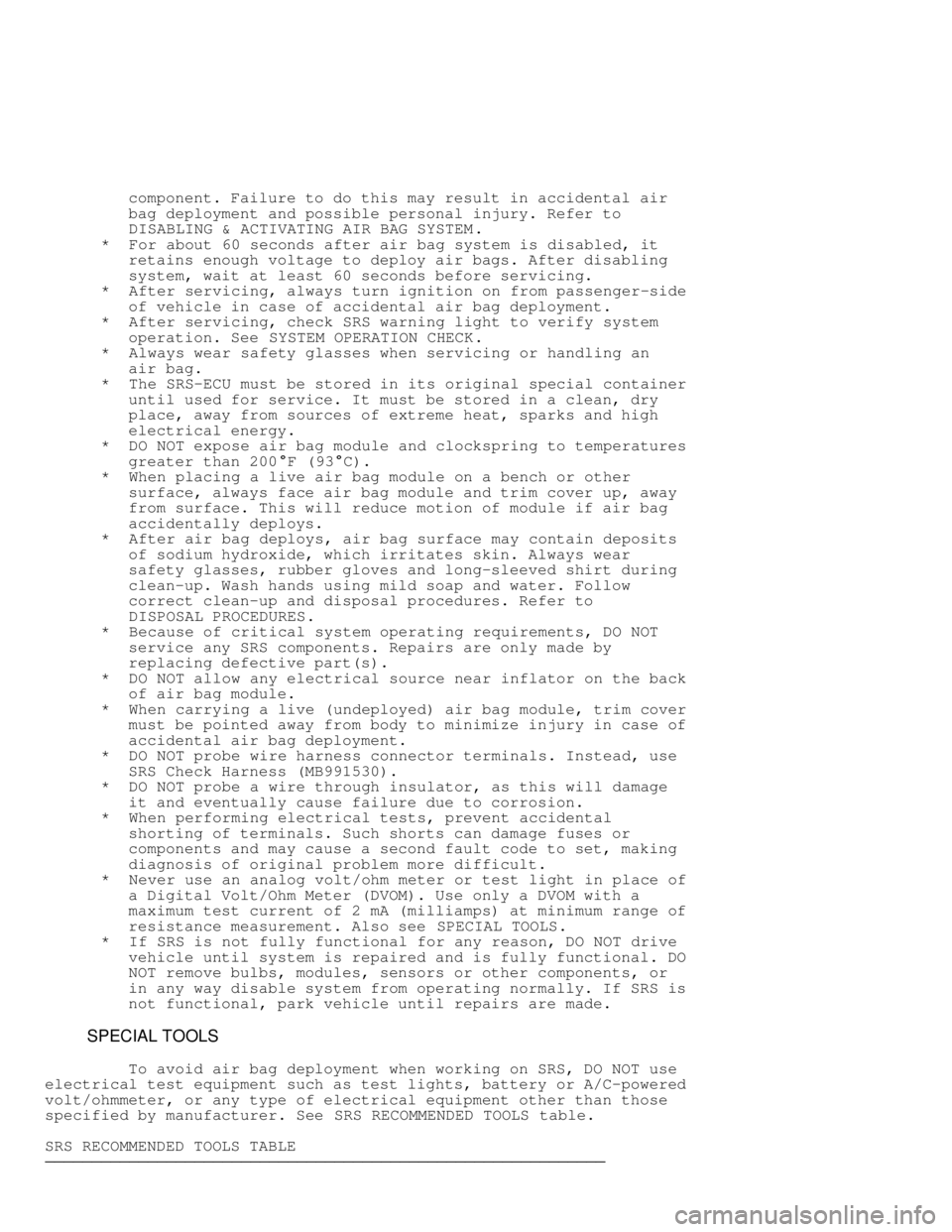
component. Failure to do this may result in accidental air
bag deployment and possible personal injury. Refer to
DISABLING & ACTIVATING AIR BAG SYSTEM .
* For about 60 seconds after air bag system is disabled, it
retains enough voltage to deploy air bags. After disabling
system, wait at least 60 seconds before servicing.
* After servicing, always turn ignition on from passenger-side
of vehicle in case of accidental air bag deployment.
* After servicing, check SRS warning light to verify system
operation. See SYSTEM OPERATION CHECK.
* Always wear safety glasses when servicing or handling an
air bag.
* The SRS-ECU must be stored in its original special container
until used for service. It must be stored in a clean, dry
place, away from sources of extreme heat, sparks and high
electrical energy.
* DO NOT expose air bag module and clockspring to temperatures
greater than 200
F (93 C).
* When placing a live air bag module on a bench or other
surface, always face air bag module and trim cover up, away
from surface. This will reduce motion of module if air bag
accidentally deploys.
* After air bag deploys, air bag surface may contain deposits
of sodium hydroxide, which irritates skin. Always wear
safety glasses, rubber gloves and long-sleeved shirt during
clean-up. Wash hands using mild soap and water. Follow
correct clean-up and disposal procedures. Refer to
DISPOSAL PROCEDURES .
* Because of critical system operating requirements, DO NOT
service any SRS components. Repairs are only made by
replacing defective part(s).
* DO NOT allow any electrical source near inflator on the back
of air bag module.
* When carrying a live (undeployed) air bag module, trim cover
must be pointed away from body to minimize injury in case of
accidental air bag deployment.
* DO NOT probe wire harness connector terminals. Instead, use
SRS Check Harness (MB991530).
* DO NOT probe a wire through insulator, as this will damage
it and eventually cause failure due to corrosion.
* When performing electrical tests, prevent accidental
shorting of terminals. Such shorts can damage fuses or
components and may cause a second fault code to set, making
diagnosis of original problem more difficult.
* Never use an analog volt/ohm meter or test light in place of
a Digital Volt/Ohm Meter (DVOM). Use only a DVOM with a
maximum test current of 2 mA (milliamps) at minimum range of
resistance measurement. Also see SPECIAL TOOLS.
* If SRS is not fully functional for any reason, DO NOT drive
vehicle until system is repaired and is fully functional. DO
NOT remove bulbs, modules, sensors or other components, or
in any way disable system from operating normally. If SRS is
not functional, park vehicle until repairs are made.
SPECIAL TOOLS
To avoid air bag deployment when working on SRS, DO NOT use
electrical test equipment such as test lights, battery or A/C-powered
volt/ohmmeter, or any type of electrical equipment other than those
specified by manufacturer. See SRS RECOMMENDED TOOLS table.
SRS RECOMMENDED TOOLS TABLE
\
\
\
\
\
\
Page 110 of 1501
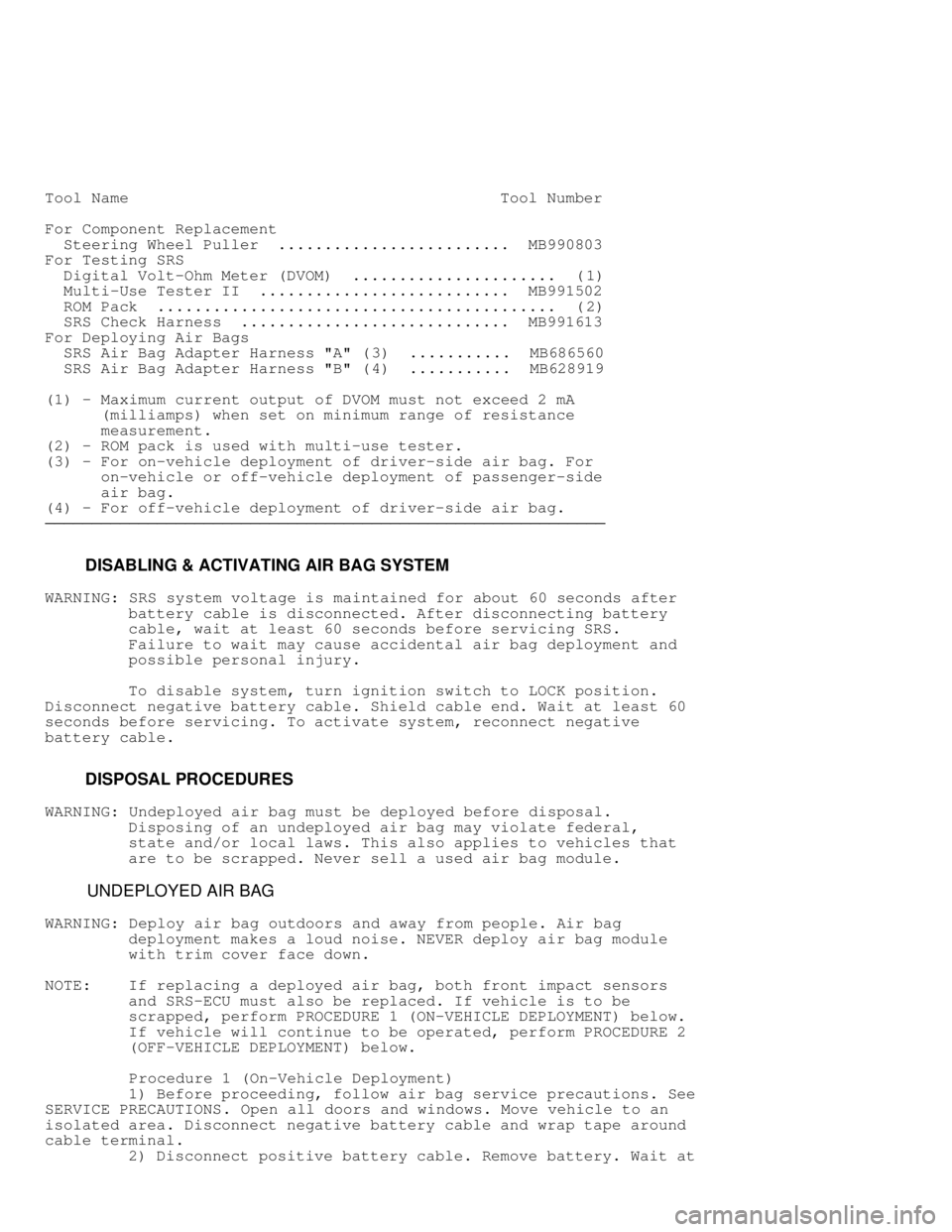
Tool Name Tool Number
For Component Replacement
Steering Wheel Puller ......................... MB990803
For Testing SRS
Digital Volt-Ohm Meter (DVOM) ...................... (1)
Multi-Use Tester II ........................... MB991502
ROM Pack ........................................... ( 2)
SRS Check Harness ............................. MB991613
For Deploying Air Bags
SRS Air Bag Adapter Harness "A" ( 3) ........... MB686560
SRS Air Bag Adapter Harness "B" ( 4) ........... MB628919
( 1) - Maximum current output of DVOM must not exceed 2 mA
(milliamps) when set on minimum range of resistance
measurement.
( 2) - ROM pack is used with multi-use tester.
( 3) - For on-vehicle deployment of driver-side air bag. For
on-vehicle or off-vehicle deployment of passenger-side
air bag.
( 4) - For off-vehicle deployment of driver-side air bag.
\
\
\
\
\
\
DISABLING & ACTIVATING AIR BAG SYSTEM
WARNING: SRS system voltage is maintained for about 60 seconds after
battery cable is disconnected. After disconnecting battery
cable, wait at least 60 seconds before servicing SRS.
Failure to wait may cause accidental air bag deployment and
possible personal injury.
To disable system, turn ignition switch to LOCK position.
Disconnect negative battery cable. Shield cable end. Wait at least 60
seconds before servicing. To activate system, reconnect negative
battery cable.
DISPOSAL PROCEDURES
WARNING: Undeployed air bag must be deployed before disposal.
Disposing of an undeployed air bag may violate federal,
state and/or local laws. This also applies to vehicles that
are to be scrapped. Never sell a used air bag module.
UNDEPLOYED AIR BAG
WARNING: Deploy air bag outdoors and away from people. Air bag
deployment makes a loud noise. NEVER deploy air bag module
with trim cover face down.
NOTE: If replacing a deployed air bag, both front impact sensors
and SRS-ECU must also be replaced. If vehicle is to be
scrapped, perform PROCEDURE 1 (ON-VEHICLE DEPLOYMENT) below.
If vehicle will continue to be operated, perform PROCEDURE 2
(OFF-VEHICLE DEPLOYMENT) below.
Procedure 1 (On-Vehicle Deployment)
1) Before proceeding, follow air bag service precautions. See
SERVICE PRECAUTIONS . Open all doors and windows. Move vehicle to an
isolated area. Disconnect negative battery cable and wrap tape around
cable terminal.
2) Disconnect positive battery cable. Remove battery. Wait at