NISSAN 300ZX 1984 Z31 Propeller Shaft And Differential Carrier Workshop Manual
Manufacturer: NISSAN, Model Year: 1984, Model line: 300ZX, Model: NISSAN 300ZX 1984 Z31Pages: 15, PDF Size: 0.66 MB
Page 1 of 15
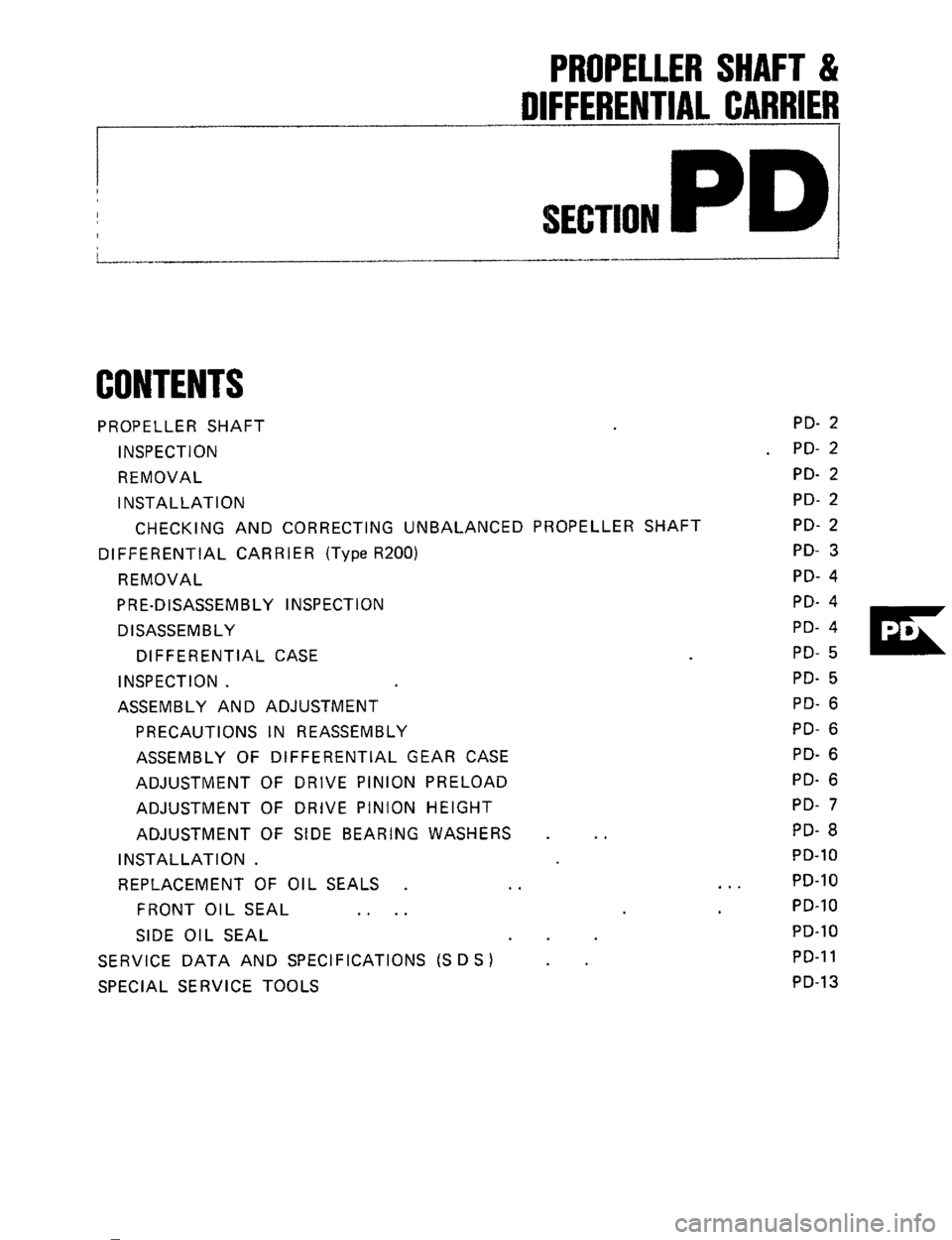
PROPELLER SHAFT &
DIFFERENTIAL CARRIER
I
SECTION PD
CONTENTS
PROPELLER SHAFT
INSPECTION
REMOVAL
I NSTALLATI ON
CHECKING AND CORRECTING UNBALANCED PROPELLER SHAFT
DIFFERENTIAL CARRIER (Type R200)
REMOVAL
PRE-DISASSEMBLY INSPECTION
DISASSEMBLY
DIFFERENTIAL CASE
INSPECTION.
ASSEMBLY AND ADJUSTMENT
PRECAUTIONS IN REASSEMBLY
ASSEMBLY OF DIFFERENTIAL GEAR CASE
ADJUSTMENT OF DRIVE PINION PRELOAD
ADJUSTMENT OF DRIVE PINION HEIGHT
ADJUSTMENT OF SIDE BEARING WASHERS
. ..
INSTALLATION .
REPLACEMENT OF OIL SEALS . ..
FRONT OIL SEAL .. ..
SIDE OIL SEAL
SERVICE DATA AND SPECIFICATIONS (S D S)
SPECIAL SERVICE TOOLS
PD- 2
PD- 2
PD- 2
PD- 2
PD- 2
PD- 3
PD- 4
PD- 4
PD- 4
PD- 5
PD- 5
PD- 6
PD- 6
PD- 6
PD- 6
PD- 7
PD- 8
PD-10
PD-10
PD-10
PD-10
PD-11
PD-13
Page 2 of 15
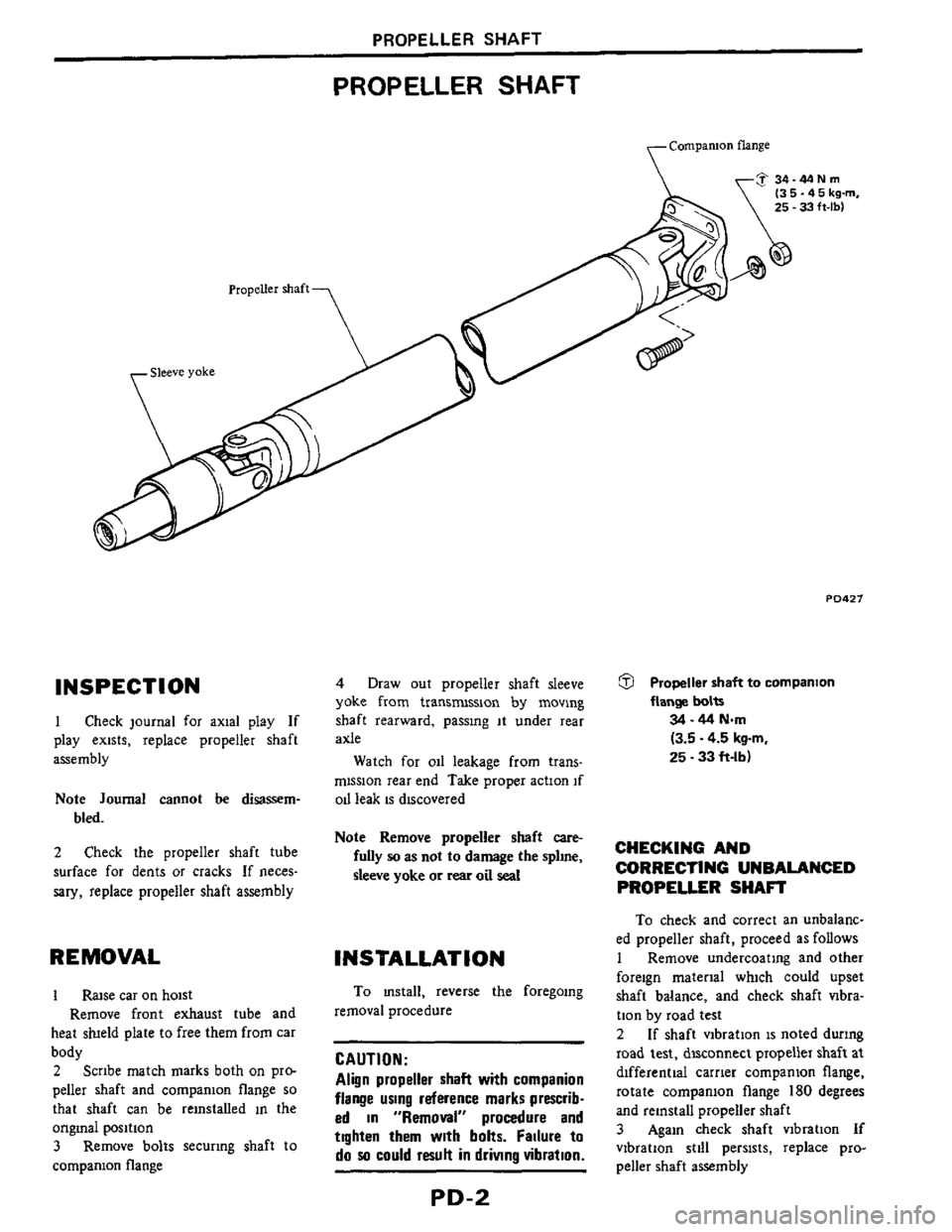
PROPELLER SHAFT
PROPELLER SHAFT
TCompanion flange
INSPECTION
I Check JOU~M~ for axial play If
play exists, replace propeller shaft
assembly
Note Journal cannot be disassem-
bled.
2 Check the propeller shaft tube
surface for dents or cracks If neces-
sary, replace propeller shaft assembly
REMOVAL
1 Raxe car on hoist
Remove front exhaust tube and
heat siueld plate to free them from car
body
2 Scribe match marks both on pro-
peller shaft and companion flange
so
that shaft can be reinstalled III the
anginal position
3 Remove bolts securing shaft to
companion flange
4 Draw out propeller shaft sleeve
yoke from transmission by moving
shaft rearward, passing it under rear
axle
Watch for oil leakage from trans-
mission rear end Take proper action if
oil leak is dlscovered
Note Remove propeller shaft care-
fully so as not to damage the splme,
sleeve yoke
or rear oil seal
INSTALLATION
To mstall, reverse the foregoing
removal procedure
CAUTION:
Align propeller shah with companion
flange using reference marks prescrib-
ed in
"Remod" procedure and
tlghten them wlth bolts. Failure to
do so could result in driwng vibration.
PO427
@ Propeller shaft to companion
flanga bolts
34-44N.m
(3.5.4.5 kgm,
25 - 33 ft-lb)
CHECKING AND
CORRECTING UNBALANCED PROPELLER SHAFT
To check and correct an unbalanc-
ed propeller shaft, proceed as follows
1 Remove undercoating and other
foreign material whch could upset
shaft balance, and check shaft nbra-
tion by road test
2 If shaft vibration is noted during
road test, disconnect propeller shaft
at
differential carrier companion flange,
rotate companion flange
180 degrees
and reinstall propeller shaft
3 Again check shaft vibration If
vibration still persists, replace pro-
peller shaft assembly
PD-2
Page 3 of 15
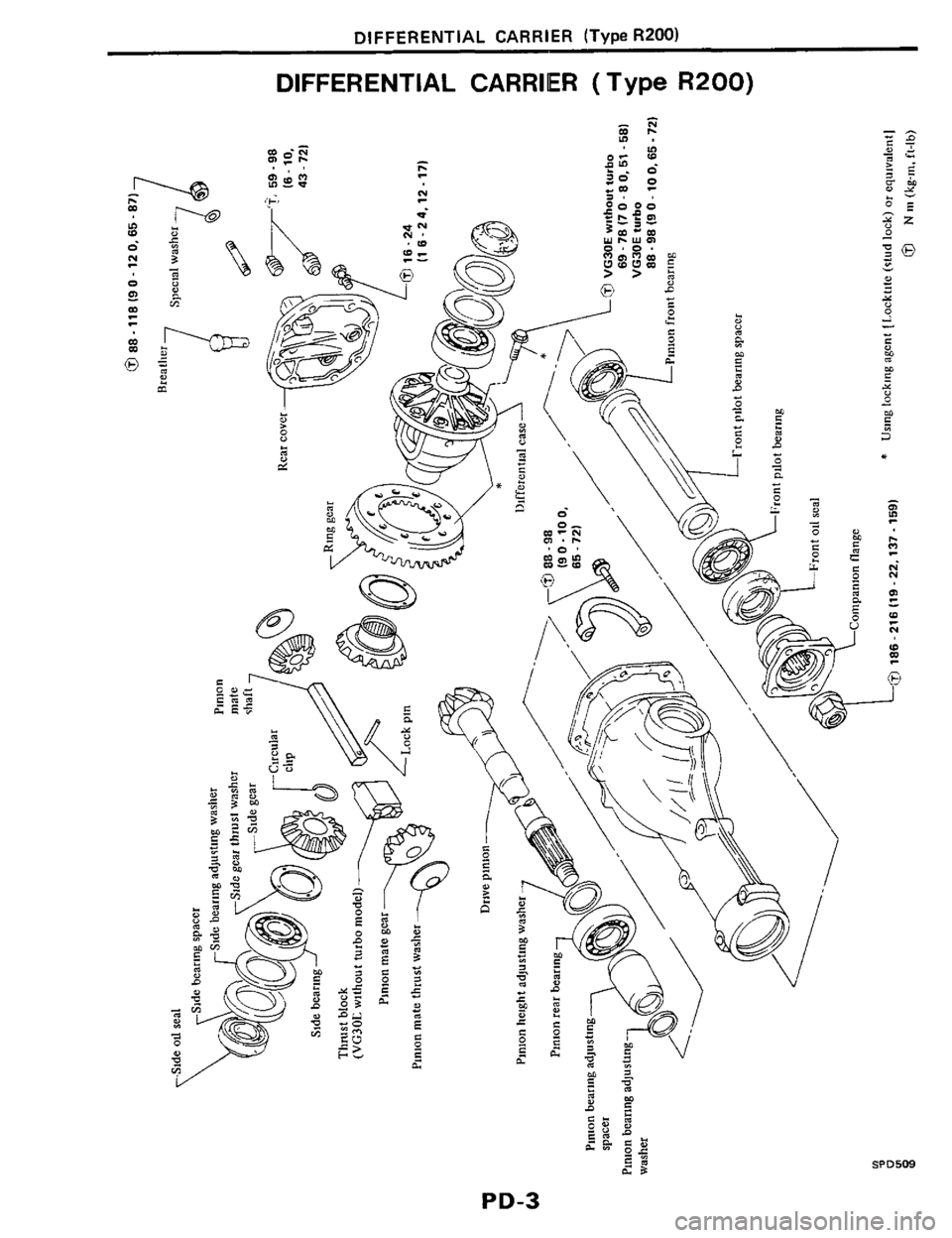
DIFFERENTIAL CARRIER (Type R200)
DIFFERENTIAL CARRIER (Type R200)
*
SPD509
PD-3
Page 4 of 15
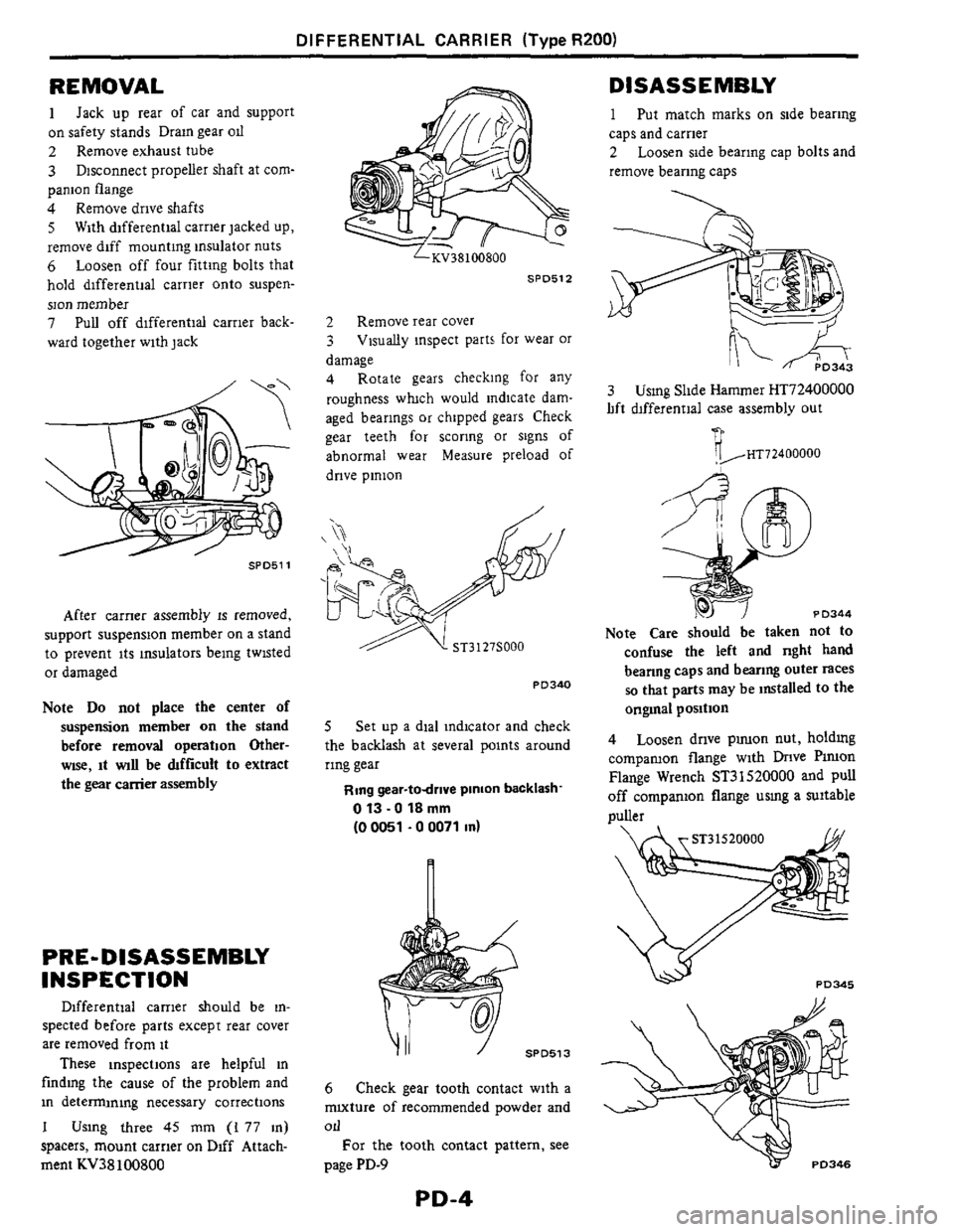
DIFFERENTIAL CARRIER (fvoe R200)
REMOVAL
1
on safety stands Drain gear od
2 Remove exhaust tube
3
panion flange
4 Remove drive shafts
5 With differential carrier jacked up,
remove diff mounting insulator nuts
6 Loosen off four fitting bolts that
hold differential carrier onto suspen-
son member
7 Pull off differential carrier back-
ward together with jack
Jack up rear of car and support
Disconnect propeller shaft at com-
SPD511
After carner assembly IS removed,
support suspension member
on a stand
to prevent its insulators being twisted
or damaged
Note Do not place the center of
suspension member on the stand
before removal operation Other-
wse, it wll be &fficult to extract
the
gear carrier assembly
PRE- DISASSEMBLY
INSPECTION
Differential carrier should be in-
spected before parts except rear cover
are removed from it
These inspections are helpful in
finding the cause of the problem and
in determining necessary corrections
1 Using three 45 mm (I 77 in)
spacers, mount carrier
on Diff Attach-
ment KV38100800
LKV38100800
SPD512
2 Remove rear cover
3 Visually inspect parts for wear or
damage
4 Rotate gears checking for any
roughness whch would indicate dam-
aged bearings or chipped gears Check
gear teeth for scorlng or signs
of
abnormal wear Measure preload of
drive pinion
PD340
5 Set up a dial indicator and check
the backlash at several points around
ring gear
Ring gear-todrive pinion backlash-
0 13 -0 18 mm
(0 0051 . 0 0071 in)
SPD513
6 Check gear tooth contact with a
mxture of recommended powder and
Oll
For the tooth contact pattern, see
page PD-9
PD-4
DlSASS E MBLY
1
caps and carrier
2
remove bearing caps
Put match marks on side bearing
Loosen side bearing cap bolts and
3 Usmg Slide Hammer HT72400000
lift hfferential case assembly out
PD344
Note Care should be taken not to
confuse the left and nght hand
beanng caps and bearing outer races
SO that parts may be installed to the
ongmal position
4 Loosen dnve puuon nut, holdmg
compamon flange with Dnve
Plruon
Flange Wrench ST31520000 and pull
off companion flange usmg a suitable
Duller
Page 5 of 15
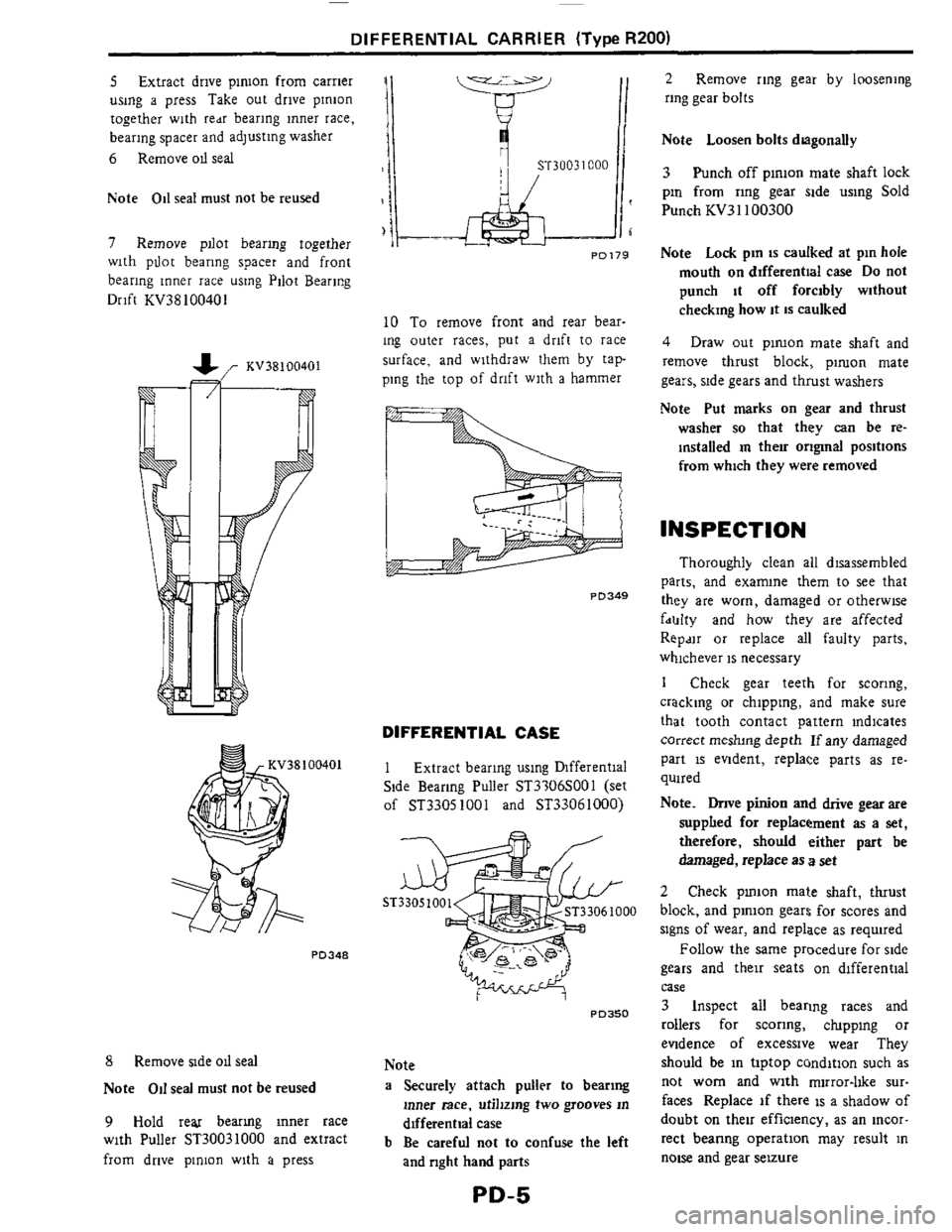
~
~ DIFFERENTIAL
CARRIER (Tvw R200)
5 Extract drive piruon from carrier
using
a press Take out drive pinion
together with red bearing inner race,
bearing spacer and adjusting washer
6 Remove
od seal
Note Oil seal must not be reused
7 Remove pdot bearmg together
with pdot bearing spacer and front
bearing inner race using Pilot Bearing
Drift KV38100401
KV38100401
PD348
8 Remove side od seal
Note Oil seal must
not be reused
9 Hold rear bearmg inner race
with Puller ST30031000 and extract
from drive pinion with
a press
PO179 PO179
10 To remove front and rear bear-
ing outer races, put a drift to race
surface, and withdraw them by tap
ping the top of drift with
a hammer
P D 349
DIFFERENTIAL CASE
1 Extract bearing using Differential
Side Bearing Puller ST3306S001 (set
of ST33051001 and ST33061000)
ST
PD350
Note
a Securely attach puller to bearing
inner race, utilizing two grooves
in
ddferential case
b Be careful not to confuse the left
and nght hand parts
PD-5
2 Remove ring gear by loosening
ring gear bolts
Note
Loosen bolts dlagonally
3 Punch off pinion mate shaft lock
pin from ring gear side using Sold
Punch KV3
1 100300
Note Lock pin is caulked at pin hole
mouth
on differential case Do not
punch it off forcibly without
checking
how it is caulked
4 Draw out pimon mate shaft and
remove thrust block, pimon mate
gears, side gears and thrust washers
Note Put marks on gear and thrust
washer
so that they can be re-
installed in theu oripnal positions
from which they were removed
INSPECTION
Thoroughly clean all disassembled
parts, and examine them to see that
they are worn, damaged
or otherwise
fdulty and how they are affected
Repdir or replace all faulty parts,
whichever is necessary
1 Check gear teeth for scoring,
cracking or chipping, and make sure
that tooth contact pattern indicates
correct
meslung depth If any damaged
part is endent, replace parts
as re-
quired
Note. Drive pinion and drive gear are
supphed for replacement as a set,
therefore, should either part be
damaged, replace
as a set
2 Check pmion mate shaft, thrust
block, and pmion gears for scores and
signs of wear, and replace as required
Follow the same procedure for side
gears and their seats
on differential
case
3 Inspect all bearing races and
rollers for scoring, clupping or
evldence of excessive wear They
should be in tiptop condition such as
not worn and with rmrror-lke sur-
faces Replace if there
is a shadow of
doubt
on their efficiency, as an incor-
rect beanng operation may result
in
noise and gear seuure
Page 6 of 15
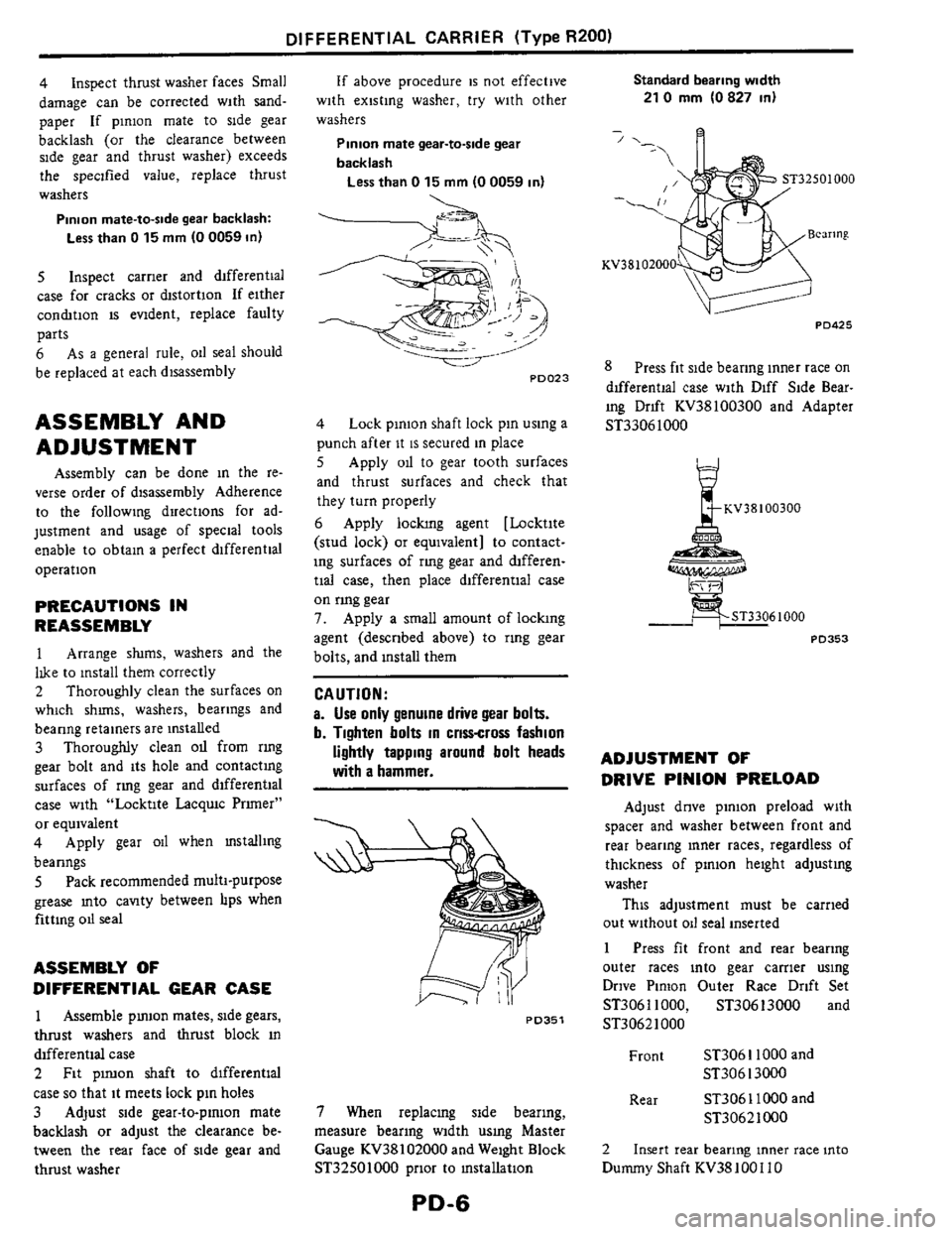
DIFFERENTIAL CARRIER (Type R200)
4 Inspect thrust washer faces Small
damage can be corrected with sand-
paper If pinion mate to side gear
backlash
(or the clearance between
side gear and thrust washer) exceeds
the specified value, replace thrust
washers
Pinion mate-to-side gear backlash:
Less than
0 15 mm (0 0059 in)
5 Inspect carrier and differential
case for cracks or distortion If either
conmtion
1s evident, replace faulty
parts
6 As
a general rule, oil seal should
be replaced at each disassembly
ASSEMBLY AND
ADJUSTMENT
Assembly can be done in the re-
verse order of disassembly Adherence
to the following directions for ad-
justment and usage of special tools
enable to obtain a perfect differential
operation
PRECAUTIONS IN
REASSEMBLY
1 Arrange slums, washers and the
llke to install them correctly
2 Thoroughly clean the surfaces
on
which shuns, washers, bearings and
bearing retainers are installed
3 Thoroughly clean od from rmg
gear bolt and its hole and contacting
surfaces of rmg gear and differential
case with “Locktite Lacquic Prnner”
or equivalent
4 Apply gear oil when mstalling
beanngs
5 Pack recommended multi-purpose
grease mto cavity between hps when
fitting
OII seal
ASSEMBLY OF
DIFFERENTIAL GEAR CASE
1 Assemble pnnon mates, side gears,
thrust washers and thrust block in
dlfferential case
2
Fit puuon shaft to differential
case
so that it meets lock pin holes
3 Adjust side gear-to-pinion mate
backlash or adjust the clearance be-
tween the rear face of side gear and
thrust washer
If above procedure is not effective
with existing washer, try with other
washers
Pinion mate gear-to-side gear
backlash
Less than 0 15 mm (0 0059 in)
-GL~: ~ . x.f-’
PDO23
4 Lock pinion shaft lock pin using a
punch after it
IS secured in place
5 Apply oil to gear tooth surfaces
and thrust surfaces and check that
they turn properly
6 Apply locktng agent [Locktite
(stud lock) or equivalent] to contact-
ing surfaces of rmg gear and differen-
tial case, then place differential case
on rmg gear
7. Apply a small amount of locktng
agent (described above) to rmg gear
bolts, and mstall them
CAUTION:
a.
Use only genuine drive gear bolts.
b. Tighten bolts in criss-cross fashion
lightly tapping around bolt heads
with a hammer.
PD351
7 When replacing side bearing,
measure bearing width using Master
Gauge KV38102000 and Weight Block
ST32501000 prior to installation
PD-6
Standard bearing width
21 0 mm (0 827 in)
PD425
8 Press fit side bearing inner race on
differential case with Diff Side
Bear-
ing Drift KV38100300 and Adapter
ST33061000
KV38100300 !ii
PO353
ADJUSTMENT OF
DRIVE PINION PRELOAD
Adjust dnve pinion preload with
spacer and washer between front and
rear bearing inner races, regardless of
thickness of pinion height adjusting
washer
This adjustment must be carried
out without
oil seal inserted
1 Press fit front and rear bearing
outer races into gear carrier using
Drive Pinion Outer Race Drift Set
ST30611000, ST30613000 and
ST3062
1000
Front ST3061 1000 and
Rear ST3061100Oand
ST306 I3000
ST30621000
2
Dummy Shaft KV38100110
Insert rear bearing inner race into
Page 7 of 15
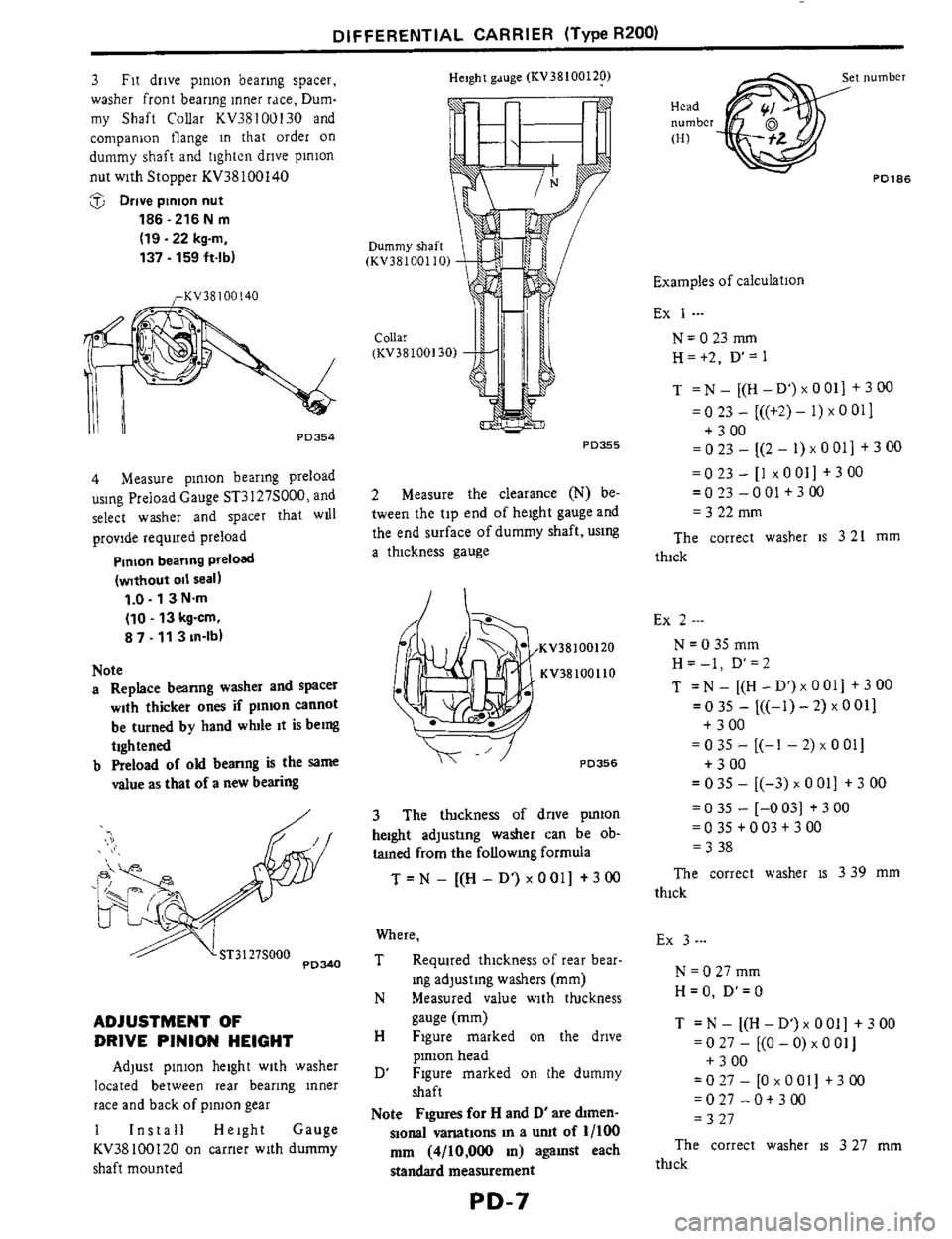
DIFFERENTIAL CARRIER (Type R200)
3 Fit drive pinion bearing spacer,
washer front bearing inner race,
Dum-
my Shaft Collar KV38100130 and
companion flange
in that order on
dummy shaft and tighten drive pinion
nut with Stopper
KV38100140
Drive pinion nut
186 -216 N rn
(19.22 kgm,
137 - 159 ft-lb)
A
rKV38100 I40
4 Measure pinion bearlng preload
using Preload Gauge
ST3127S000, and
select washer and spacer that
WIN
provide required preload
Pinion bearing preload
(without oil seal)
1.0.1 3 Nm
(10 - 13 kgcm,
8 7. 11 3 in-lb)
Note
a Replace beanng washer and spacer
with thicker ones if pinion cannot
be turned by hand while
it is being
tightened
b Reload of old beanng is the same
due as that of a new bearing
ADJUSTMENT OF
DRIVE PINION HEIGHT
Adjust pinion height with washer
located between rear bearing inner
race and back of pinion gear
1 Install Height Gauge
KV38100120 on carrier with dummy
shaft mounted
Haghi gduge (KV3810012?)
PD355
2 Measure the clearance (N) be-
tween the tip end
of height gauge and
the end surface
of dummy shaft, using
a thickness gauge
3 The thckness of drive pmon
height adlusting washer can be ob-
tamed from the followmg formula
T=N-[(H-D')xOOl] +3M)
Where,
T Required thickness of rear bear-
ing adlusting washers (mm)
N Measured value with ttuckness
H Figure marked on the drive
pinion head
D Figure marked on the dummy
shaft
Note Figures for H and D are dimen-
sional
vanations in a unit of 1/100
mm (4/10,000 m) agdmst each
standard measurement
gauge (mm)
PD-7
Set number
Hcad
number
(HI
PO186
Examples of calculation
Ex
1 -..
N= 0 23 mm
H=t2, D=1
T =N-[(H-D')xO01]+300
= 0 23 - [((t2) - 1) x 0 01 ]
=023 - [(2 - 1)x 0011 t 3 00
=023-[1x001]+300
= 0 23 - 0 01 + 3 M)
=322mm
+ 3 00
The correct washer IS 3 21 mm
thick
Ex 2 --.
N=03Smm
H=-1,
D'=2
T =N- [(H-D')xOOl] t300
= 0 35 - [((-I) - 2) x 0 011
t 3 00
+ 3 00
=03S-[(-1-2)~001]
= 0 3s - [(-3) x 0 011 t 3 00
=035-[-003]+300
=o 3s t 003 t 3 00
=3 38
The correct washer IS 3 39 mm
thick
Ex 3 -..
N =O 27 mm
H=O, D'=O
T =N- [(H-D')xOOl] +300
=027- [(0-O)xOO1]
=027- [OxOOI] t300
=027 -0t 300
= 3 27
f 3 00
The correct washer is 3 27 mm
ttuck
Page 8 of 15
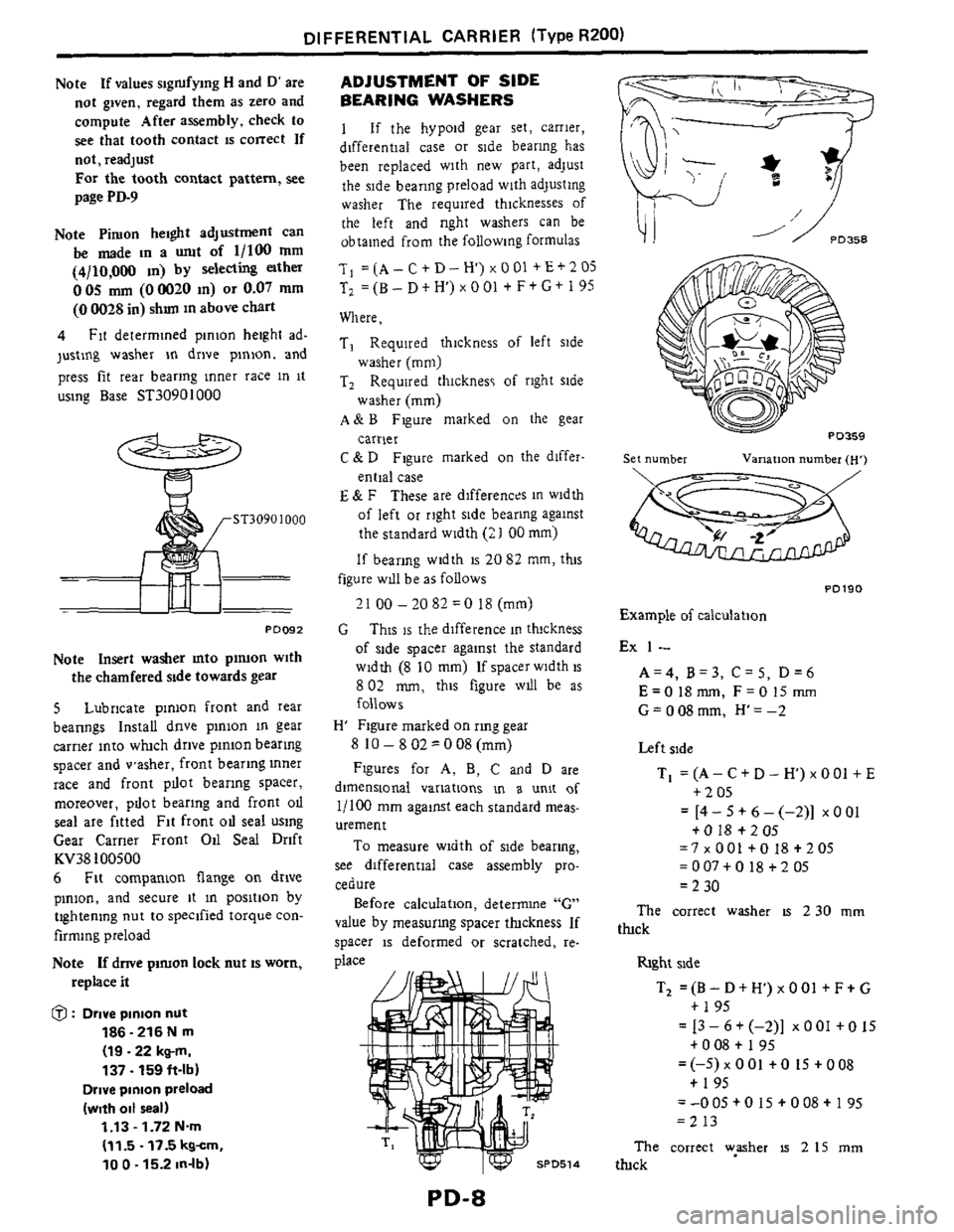
DIFFERENTIAL CARRIER (Type R200)
Note If values sigrufying H and D' are
not given, regard them as zero and
compute After assembly, check to
see that tooth contact
is correct If
not, readjust
For the tooth contact pattern, see
page PD-9
Note Phon height adjustment can
be made
in a ut of 1/1m mm
(4/10,000 m) by seleahg dm
0 05 mm (0 0020 in) or 0.07 mm
(0 0028 in) shm in above chart
4 Fit determined pinion height ad-
justing washer
in drive pinion, and
press
fit rear bearing inner race in it
using Base ST30901000
ST3090 1000
PO092
Note Insert washer mto pinion with
the chamfered side towards gear
5 Lubricate pinion front and rear
beanngs Install dnve pinion in gear
carrier into which drive pinion bearing
spacer and vasher, front bearing inner
race and front pllot bearing spacer,
moreover, pllot bearing and front
oll
seal are fitted Fit front OII seal using
Gear Carrier Front Oil Seal Drift
KV38
100500
6 Fit companion flange on drive
pinion, and secure it in position by
tightening
nut to specified torque con-
firming preload
Note If dnve pimon lock nut IS worn,
replace it
@ : Drive pinion nut
186 - 216 N rn
(19.22 kgm,
137.159 ft-lb)
Drive pinion preload
(with oil real)
1.13 - 1.72 N.m
(11.5.17.5 kgcm,
10 0 - 15.2 in-lb)
ADJUSTMENT OF SIDE
BEARING WASHERS
1 If the hypoid gear set, carrier,
differential case
or side bearing has
been replaced with new
part, adjust
the side bearing preload with adjusting
washer The required thicknesses of
the left and nght washers can be
obtained from the following formulas
T, =(A-C+D-H)xOOl +E+205
T2 =(B- D t H') x 0 01 t F+ G+ I 95
Where,
Ti Required thickness
of left side
washer (mm)
T2 Required thicknes of right side
washer
(mm)
A& B Figure marked on the gear
carrier
C & D Figure marked on the differ-
ential case
E & F These are differences in width
of left or right side bearing against
the standard width
(21 00 mm)
If bearing width is 20 82 mm, this
21 00 -2082 =O 18 (mm)
This is the difference in thickness
of side spacer against the standard
width (8
10 mm) If spacer width is
8 02 mm, this figure wdl be as
follows
H Figure marked on rmg gear
8
10 - 8 02 = 0 08 (mm)
Figures for A, B, C and D are
dimensional variations m a unit of
l/loO mm against each standard meas-
urement
To measure width of side bearing,
see differential case assembly pro-
cedure
Before calculation, deterrmne "G"
value by measurmg spacer thxkness If
spacer is deformed or scratched, re-
place
figure wlll he as follows
G
PD-8
Sei number Varlanon number (H)
PO190
Example of calculation
Ex
1 --
A=4, B=3, C=5, D=6
E=O18mm, F=OlSmm
G=O08mm, H'=-2
Left side
Ti =(A- Ct D- H)x00l +E
t205
+ 0 18 + 2 OS
- - [4-5+6-(-2)j ~001
=7 x 001 +O 18 + 2 05
= 007 t 0 18 +2 05
= 2 30
The correct washer IS 2 30 mm
thck
hght side
T, = (B - D t H) x 0 01 t F + G
t 195
+ 0 08 + I 95
+ 195
- -13-6+(-2)] xOOltO15
=(-5) x 001 +O IS t 008
=-005 +O 15 + 008+ 195
=213
The correct wpsher
IS 2 15 mm
Uuck
Page 9 of 15
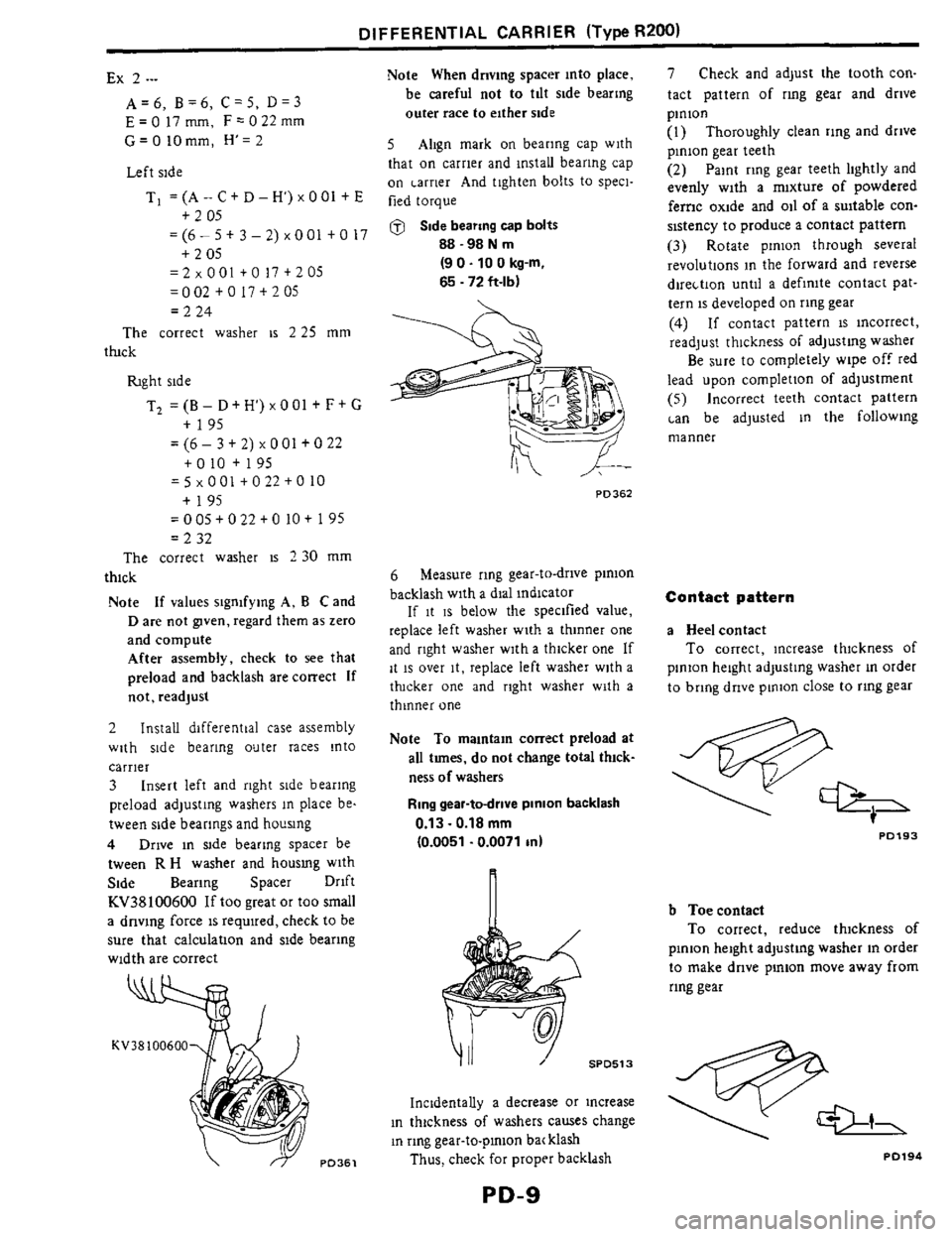
DIFFERENTIAL CARRIER (Type R200)
Ex 2 .--
A=6, B=6, C=5, D=3
E=O17mm, F-022mm
G=OIOmm, H'=2
Left side
Ti =(A - C t D - H') x 001 +E
=(6- 5 t 3 - 2) x 001 t 0 I7
=2 x 001 +O 17 t 2 05
= 0 02 t 0 I7 + 2 05
= 2 24
The correct washer is 2 25 mm
+ 2 05
+ 2 05
thck
fight side
T, = (B- Dt H') x 001 f F+ G
= (6 - 3 t 2) x 001 f 0 22
= 5 x 0 01 + 0 22 + 0 IO
=005+022tO IO+ 195
= 2 32
t 195
+010+195
t 195
The correct washer is 2 30 mm
thick
Note
If values signifying A, B C and
Dare not gwen, regard them as zero
and compute After assembly, check to
see that
preload and backlash are correct
If
not, readjusl
2 Install differential case assembly
with side bearing outer races into
carrier
3 Insert left and right side bearing
preload adjusting washers
in place be.
tween side bearings and hocsing
4 Drive in side bearing spacer be
tween
R H washer and housmg with
Side Bearing Spacer Drift
KV38100600
If too great or too small
a dnving force
is required, check to be
sure that calculation and side bearing
width are correct
Note When driving spacer into place,
be careful not
to tilt side bearing
outer race
to either side
5 Align mark on bearing cap with
that on carrier and install bearing cap
on Larrier And tighten bolts to speci-
fied torque
@ Side bearing cap bolts
88-98Nm
65 - 72 ft-lb)
(9 0.10 0 kg-m.
PD362
6 Measure ring gear-to-drive pinion
backlash with a dial indicator
If it IS below the specified value,
replace left washer with a thinner one
and right washer with
a thicker one If
it
is over it, replace left washer with a
ttucker one and right washer with a
thinner one
Note To maintain correct preload at
all tunes, do not change total thick-
ness
of washers
Ring gear-todrive pinion backlash
0.13.0.18 mm
(0.0051 .0.0071 in)
SPD513
Incidentally a decrease or increase
in thickness
of washers causes change
in ring gear-to-pinion ba( klash
Thus, check for proprr backldsh
PD-9
7 Check and adjust the tooth con.
tact pattern
of ring gear and drive
pinion
(I) Thoroughly clean ring and drive
pinion gear teeth
(2) Paint ring gear teeth lightly and
evenly with a mixture of powdered
ferric oxide and oil of a suitable con-
sistency to produce a contact pattern
(3) Rotate pinion through several
revolutions in the forward and reverse
direLtion until a definite contact pat-
tern is developed
on ring gear
(4) If contact pattern is incorrect,
readjust thickness
of adjusting washer
Be sure to completely wipe off red
lead upon completion
of adjustment
(5) Incorrect teeth contact pattern
'an be adjusted in the following
manner
Contact pattern
a Heel contact
To correct, increase thickness of
pinion height adjusting washer in order
to bring drive pinion close to ring gear
PO193
b Toecontact
To correct, reduce thickness of
pinion height adjusting washer in order
to make drive pinion move away from
ring gear
PD194
Page 10 of 15
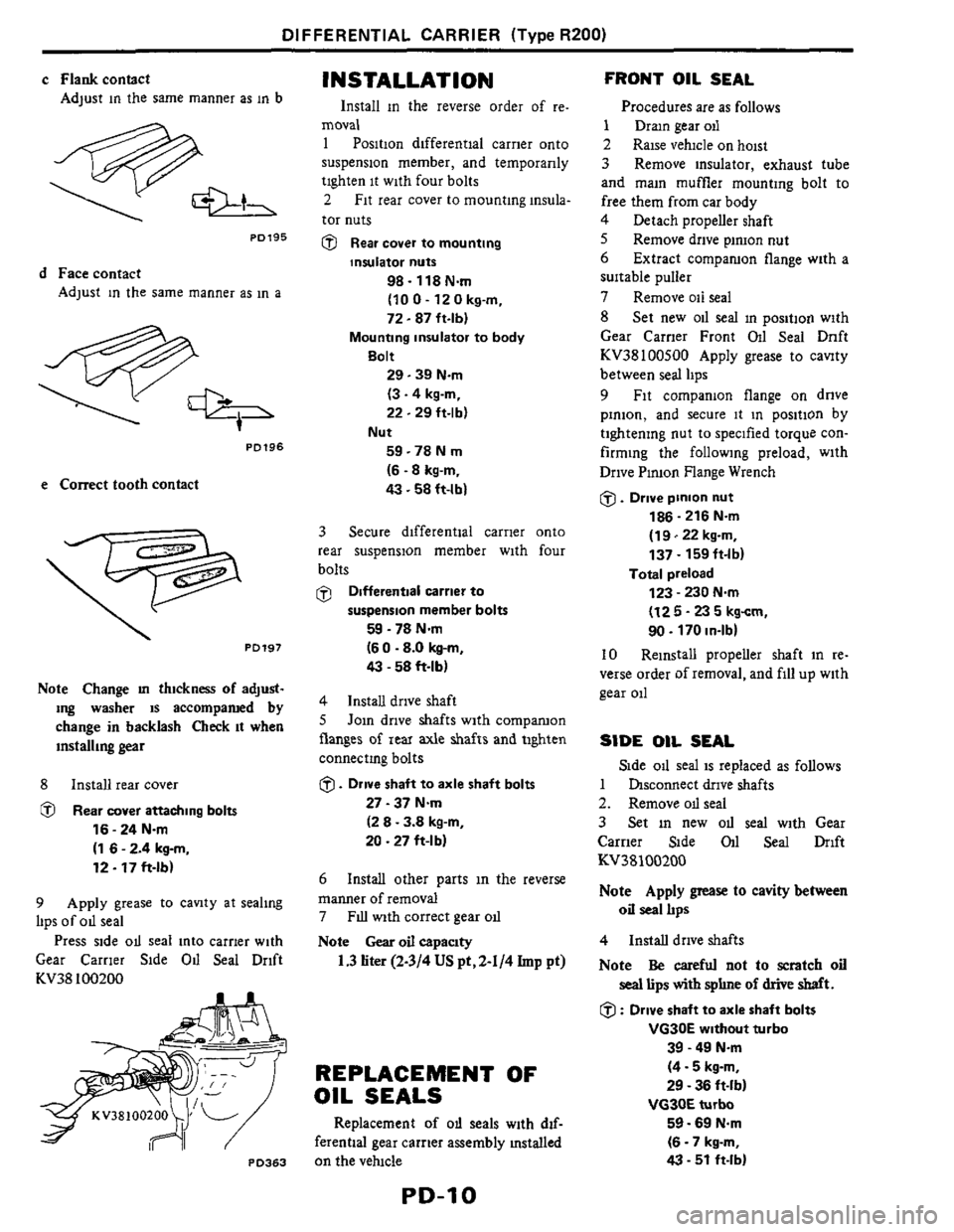
DIFFERENTIAL CARRIER (Type R200)
c Flankcontact
Adjust in the same manner as in b
PO195
d Face contact
Adjust in the same manner as in a
PD196
e Correct tooth contact
. PD197
Note Change m thickness of adjust-
ing washer
is accompamd by
change in backlash Check it when
installing
gear
8 Install rear cover
@ Rear cover attaching bolts
16 - 24 Nm
(1 6 - 2.4 kg-m,
12.17 ft-lb)
9 Apply grease to cavity at sealing
lips of od seal
Press side od seal into carrier with
Gear Carrier Side
Od Seal Drift
KV38 100200
PO363
INSTALLATION
Install in the reverse order of re.
moval
1 Position differential carrier onto
suspension member, and temporarily
tighten
it with four bolts
2 Fit rear cover to mounting insula-
tor nuts
@ Rear cover to mounting
insulator nuts
98.118 Nm
(10 0 - 12 0 kg-m,
72.87 ft-lbl
Mounting insulator to body
Bolt
29.39 Nm
(3.4 kg-m,
22.29 ft-lbl
59 -78 N m
(6.8 kg-m,
43.58 ft-lb)
Nut
3 Secure differential carrier onto
rear suspension member with four
bolts
@ Differentlal carrier to
59 - 78 Nm
(6 0 .8.0 kg-m,
43 - 58 ft-lbl
suspension member bolts
4 Install drive shaft
8 Join drive shafts with comparuon
flanges
of rear axle shafts and tighten
connectmg bolts
0. Drive shaft to axle shaft bolts
27 - 37 Nm
(2 8 - 3.8 kg-m,
20 .27 ft-l b)
6
manner of removal
7
Note Gear oil capaclty
Install other parts in the reverse
FIU with correct gear od
1.3liter(2-3/4USpt,2-1/4Imp pt)
REPLACEMENT OF
OIL SEALS
Replacement of od seals with dif-
ferential gear carrier assembly mstalled
on the velucle
FRONT OIL SEAL
Procedures are as follows
1 Dram gear oil
2 Raise vehicle on hoist
3 Remove insulator, exhaust tube
and main muffler mounting bolt to
free them from car body
4 Detach propeller shaft
8 Remove drive piruon nut
6
suitable puller
7 Remove oil seal
8 Set new oil seal in position with
Gear Carner Front Oil Seal Dnft
KV38100800 Apply grease to canty
between seal lips
9 Fit companion flange on dnve
pinion, and secure it in position by
tightening nut to specified torque con-
firming the following preload, with
Drive Pinion Flange Wrench
0. Drive pinion nut
186 - 216 N.m
(1 9122 kg-m,
137
- 159ft-lb)
123 - 230 Nm
(12 5 - 23 5 kgcm,
90. 170 in-lbl
Extract comparuon flange with a
Total preload
10 Reinstall propeller shaft in re-
verse order of removal, and fill up with
gear oil
SIDE OIL SEAL
1 hsconnect drive shafts
2. Remove od seal
3 Set in new OII seal with Gear
Carrier Side
011 Seal Drift
KV38100200
Note Apply grease to cavity between
oil seal IIps
Side od seal is replaced as follows
4 Install drive shafts
Note
Be careful not to scratch oil
seal lips with sphne of drive shaft.
0 : Drive shaft to axle shaft bolts
39 - 49 N.m
(4.5 kg-m,
29 - 36 ft-lb)
VG3OE turbo
59.69 Nm
(6 - 7 kg-m,
43 - 51 ft-lb)
VG30E without turbo