NISSAN ALMERA N16 2003 Electronic Repair Manual
Manufacturer: NISSAN, Model Year: 2003, Model line: ALMERA N16, Model: NISSAN ALMERA N16 2003Pages: 3189, PDF Size: 54.76 MB
Page 261 of 3189
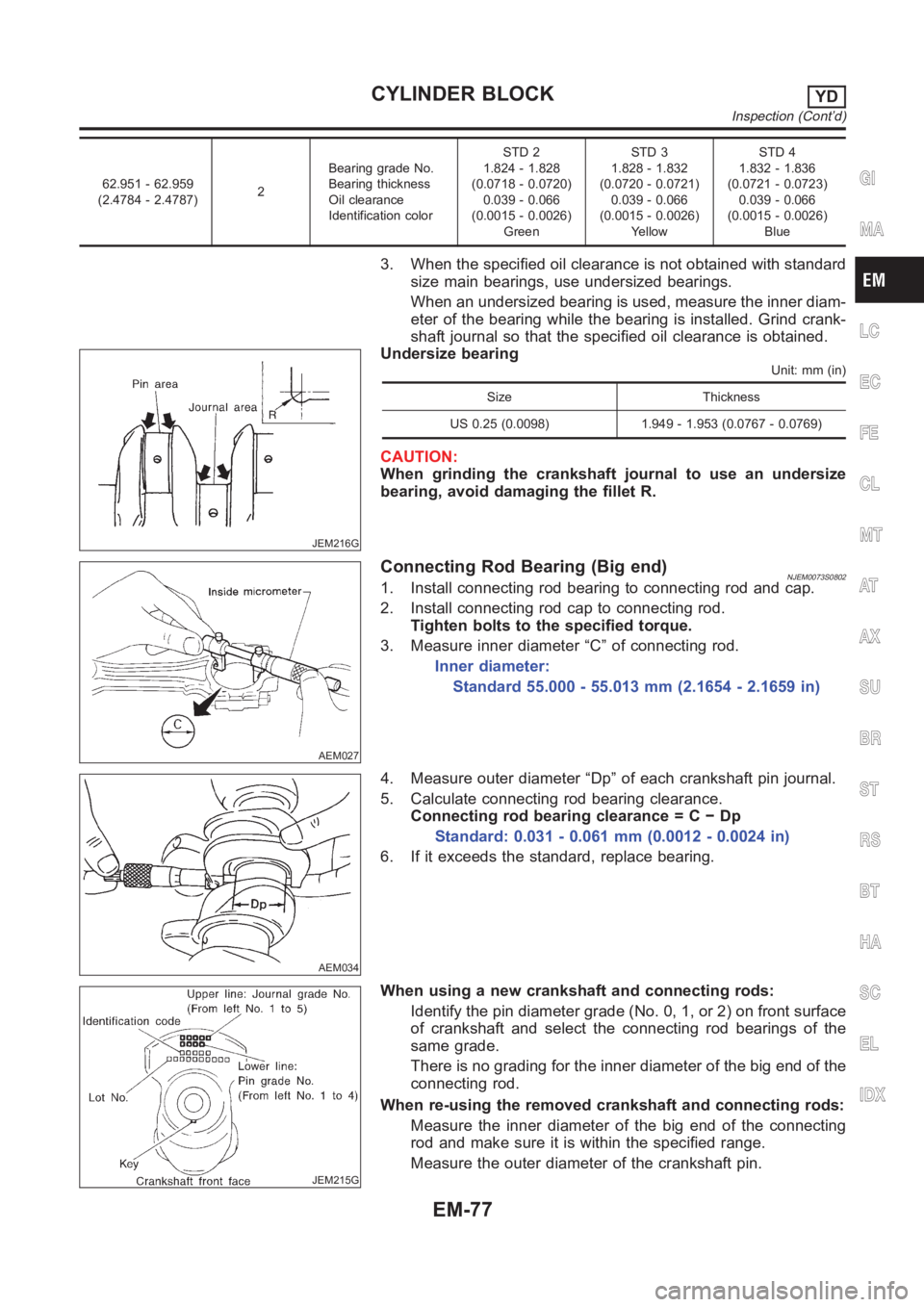
62.951 - 62.959
(2.4784 - 2.4787)2Bearing grade No.
Bearing thickness
Oil clearance
Identification colorSTD 2
1.824 - 1.828
(0.0718 - 0.0720)
0.039 - 0.066
(0.0015 - 0.0026)
GreenSTD 3
1.828 - 1.832
(0.0720 - 0.0721)
0.039 - 0.066
(0.0015 - 0.0026)
YellowSTD 4
1.832 - 1.836
(0.0721 - 0.0723)
0.039 - 0.066
(0.0015 - 0.0026)
Blue
3. When the specified oil clearance is not obtained with standard
size main bearings, use undersized bearings.
When an undersized bearing is used, measure the inner diam-
eter of the bearing while the bearing is installed. Grind crank-
shaft journal so that the specified oil clearance is obtained.
JEM216G
Undersize bearingUnit: mm (in)
Size Thickness
US 0.25 (0.0098) 1.949 - 1.953 (0.0767 - 0.0769)
CAUTION:
When grinding the crankshaft journal to use an undersize
bearing, avoid damaging the fillet R.
AEM027
Connecting Rod Bearing (Big end)NJEM0073S08021. Install connecting rod bearing to connecting rod and cap.
2. Install connecting rod cap to connecting rod.
Tighten bolts to the specified torque.
3. Measure inner diameter “C” of connecting rod.
Inner diameter:
Standard 55.000 - 55.013 mm (2.1654 - 2.1659 in)
AEM034
4. Measure outer diameter “Dp” of each crankshaft pin journal.
5. Calculate connecting rod bearing clearance.
Connecting rod bearing clearance = C − Dp
Standard: 0.031 - 0.061 mm (0.0012 - 0.0024 in)
6. If it exceeds the standard, replace bearing.
JEM215G
When using a new crankshaft and connecting rods:
Identify the pin diameter grade (No. 0, 1, or 2) on front surface
of crankshaft and select the connecting rod bearings of the
same grade.
There is no grading for the inner diameter of the big end of the
connecting rod.
When re-using the removed crankshaft and connecting rods:
Measure the inner diameter of the big end of the connecting
rod and make sure it is within the specified range.
Measure the outer diameter of the crankshaft pin.
GI
MA
LC
EC
FE
CL
MT
AT
AX
SU
BR
ST
RS
BT
HA
SC
EL
IDX
CYLINDER BLOCKYD
Inspection (Cont’d)
EM-77
Page 262 of 3189
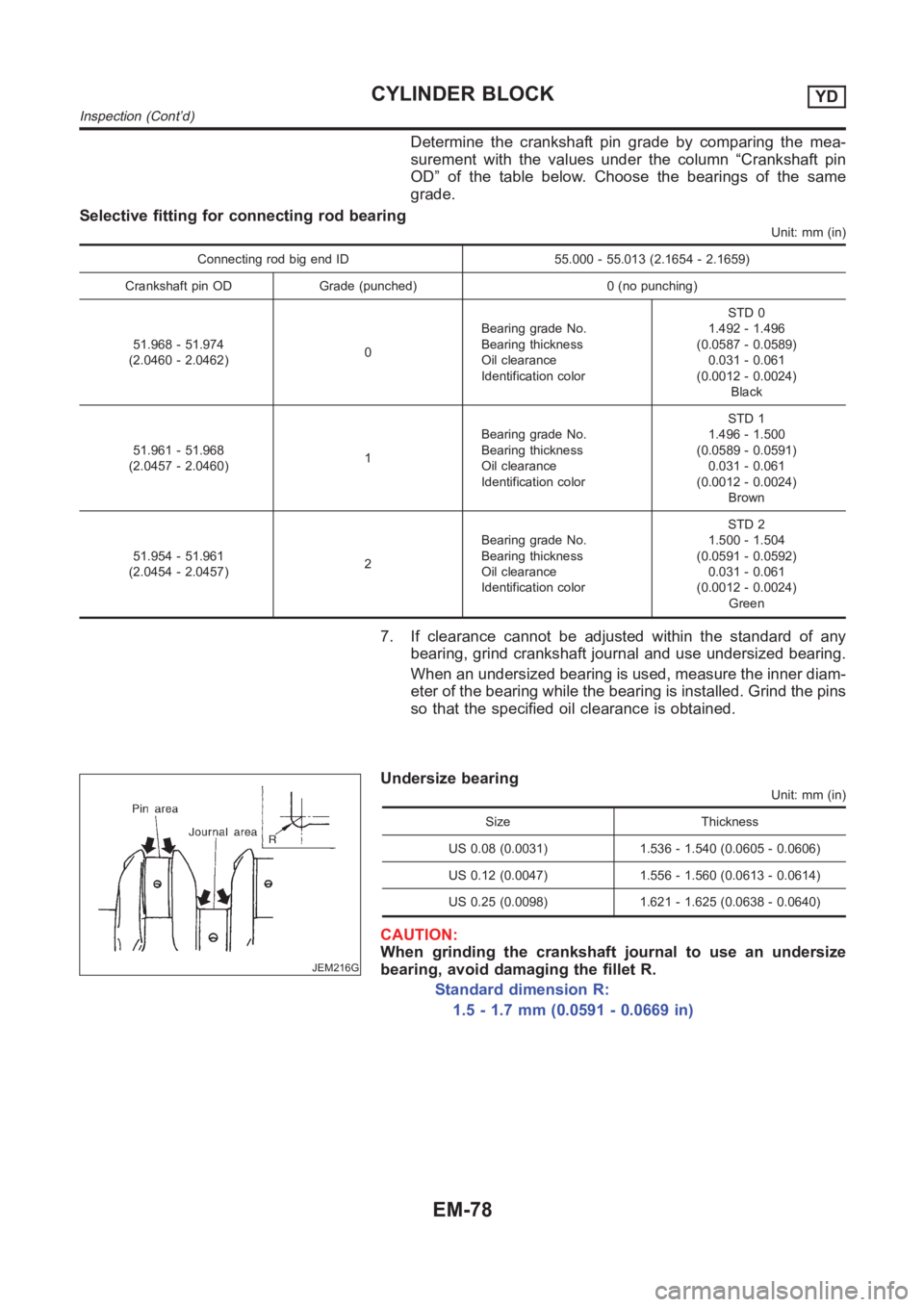
Determine the crankshaft pin grade by comparing the mea-
surement with the values under the column “Crankshaft pin
OD” of the table below. Choose the bearings of the same
grade.
Selective fitting for connecting rod bearing
Unit: mm (in)
Connecting rod big end ID 55.000 - 55.013 (2.1654 - 2.1659)
Crankshaft pin OD Grade (punched) 0 (no punching)
51.968 - 51.974
(2.0460 - 2.0462)0Bearing grade No.
Bearing thickness
Oil clearance
Identification colorSTD 0
1.492 - 1.496
(0.0587 - 0.0589)
0.031 - 0.061
(0.0012 - 0.0024)
Black
51.961 - 51.968
(2.0457 - 2.0460)1Bearing grade No.
Bearing thickness
Oil clearance
Identification colorSTD 1
1.496 - 1.500
(0.0589 - 0.0591)
0.031 - 0.061
(0.0012 - 0.0024)
Brown
51.954 - 51.961
(2.0454 - 2.0457)2Bearing grade No.
Bearing thickness
Oil clearance
Identification colorSTD 2
1.500 - 1.504
(0.0591 - 0.0592)
0.031 - 0.061
(0.0012 - 0.0024)
Green
7. If clearance cannot be adjusted within the standard of any
bearing, grind crankshaft journal and use undersized bearing.
When an undersized bearing is used, measure the inner diam-
eter of the bearing while the bearing is installed. Grind the pins
so that the specified oil clearance is obtained.
JEM216G
Undersize bearingUnit: mm (in)
Size Thickness
US 0.08 (0.0031) 1.536 - 1.540 (0.0605 - 0.0606)
US 0.12 (0.0047) 1.556 - 1.560 (0.0613 - 0.0614)
US 0.25 (0.0098) 1.621 - 1.625 (0.0638 - 0.0640)
CAUTION:
When grinding the crankshaft journal to use an undersize
bearing, avoid damaging the fillet R.
Standard dimension R:
1.5 - 1.7 mm (0.0591 - 0.0669 in)
CYLINDER BLOCKYD
Inspection (Cont’d)
EM-78
Page 263 of 3189
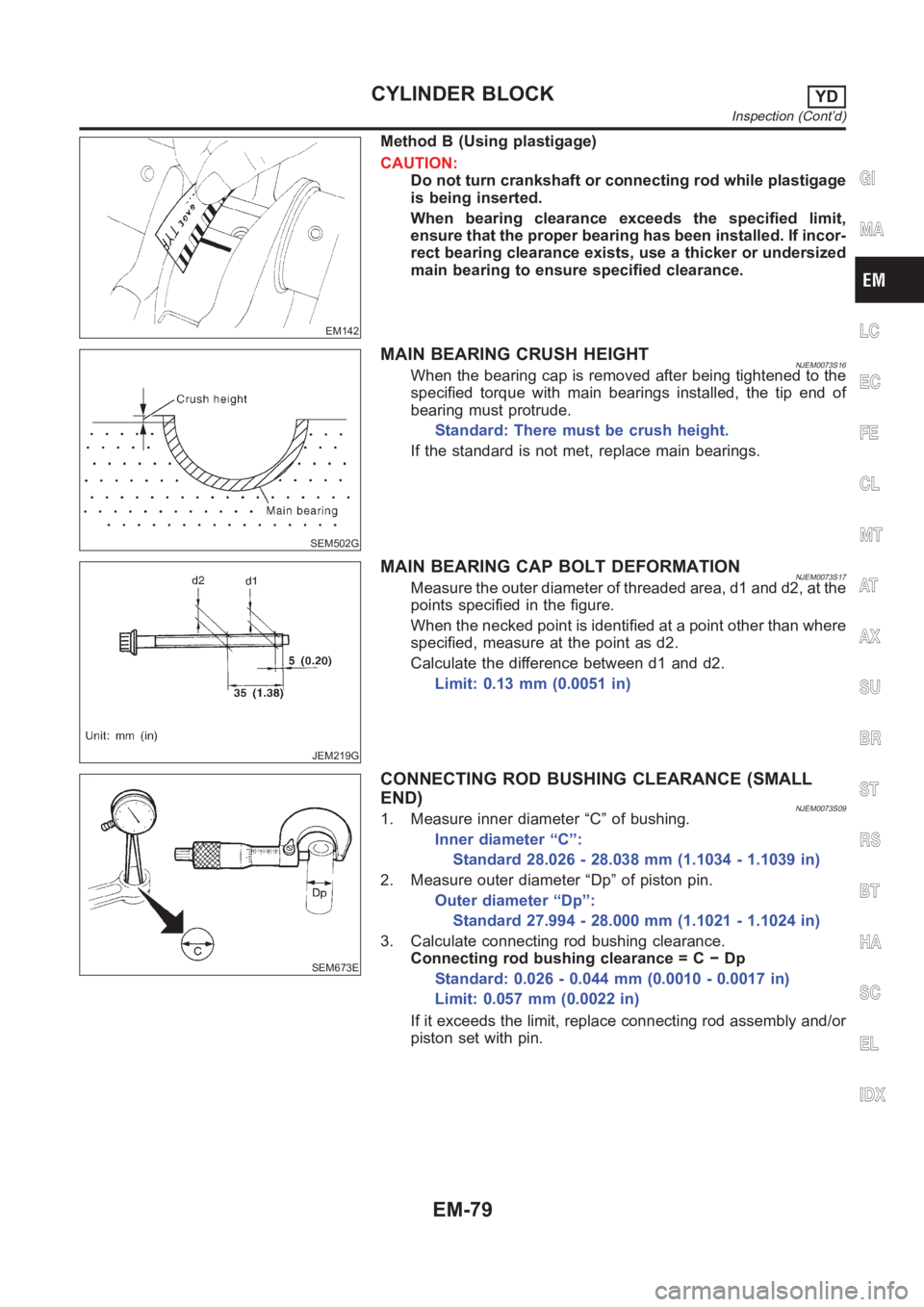
EM142
Method B (Using plastigage)
CAUTION:
Do not turn crankshaft or connecting rod while plastigage
is being inserted.
When bearing clearance exceeds the specified limit,
ensure that the proper bearing has been installed. If incor-
rect bearing clearance exists, use a thicker or undersized
main bearing to ensure specified clearance.
SEM502G
MAIN BEARING CRUSH HEIGHTNJEM0073S16When the bearing cap is removed after being tightened to the
specified torque with main bearings installed, the tip end of
bearing must protrude.
Standard: There must be crush height.
If the standard is not met, replace main bearings.
JEM219G
MAIN BEARING CAP BOLT DEFORMATIONNJEM0073S17Measure the outer diameter of threaded area, d1 and d2, at the
points specified in the figure.
When the necked point is identified at a point other than where
specified, measure at the point as d2.
Calculate the difference between d1 and d2.
Limit: 0.13 mm (0.0051 in)
SEM673E
CONNECTING ROD BUSHING CLEARANCE (SMALL
END)
NJEM0073S091. Measure inner diameter “C” of bushing.
Inner diameter “C”:
Standard 28.026 - 28.038 mm (1.1034 - 1.1039 in)
2. Measure outer diameter “Dp” of piston pin.
Outer diameter “Dp”:
Standard 27.994 - 28.000 mm (1.1021 - 1.1024 in)
3. Calculate connecting rod bushing clearance.
Connecting rod bushing clearance = C − Dp
Standard: 0.026 - 0.044 mm (0.0010 - 0.0017 in)
Limit: 0.057 mm (0.0022 in)
If it exceeds the limit, replace connecting rod assembly and/or
piston set with pin.
GI
MA
LC
EC
FE
CL
MT
AT
AX
SU
BR
ST
RS
BT
HA
SC
EL
IDX
CYLINDER BLOCKYD
Inspection (Cont’d)
EM-79
Page 264 of 3189
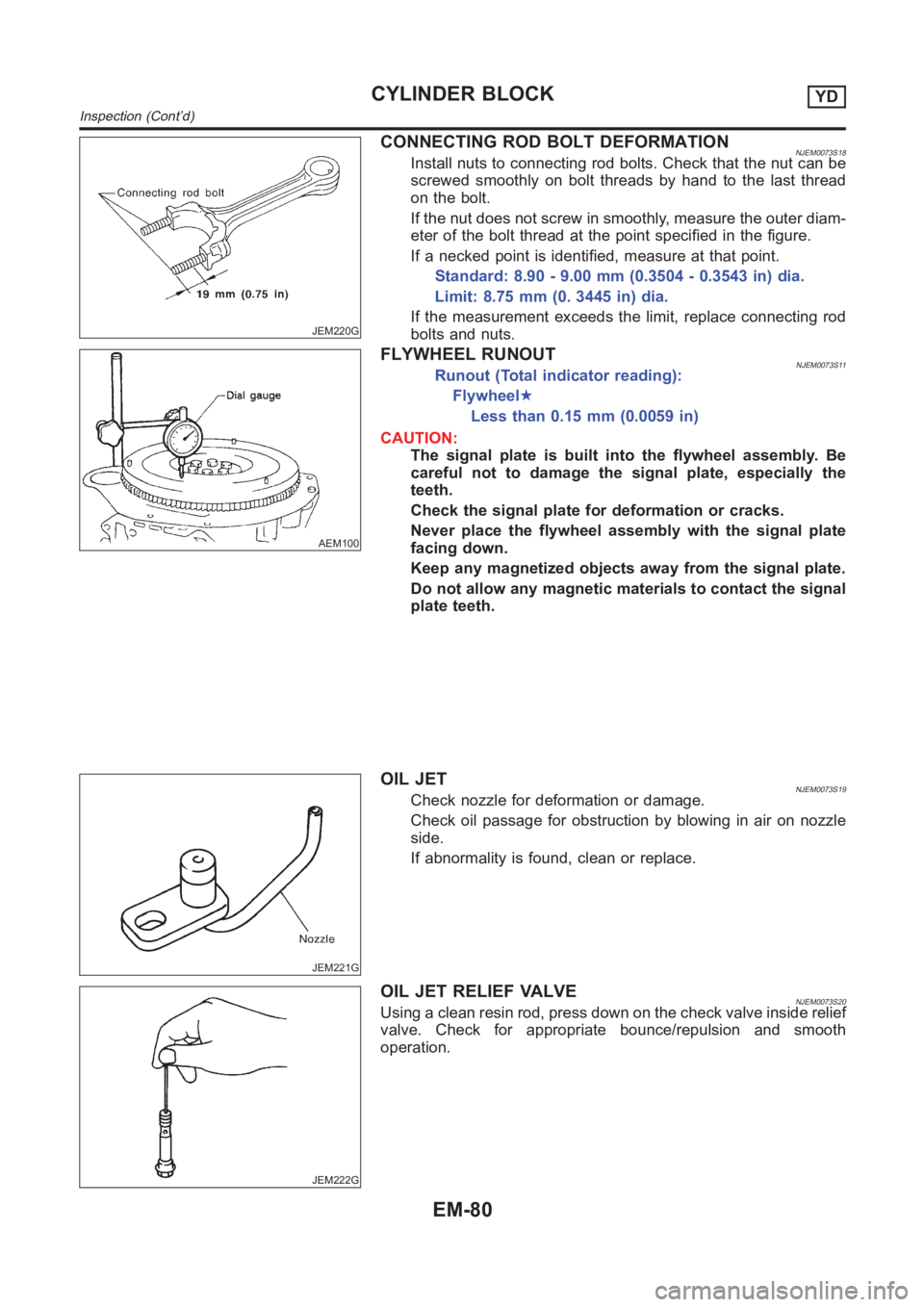
JEM220G
CONNECTING ROD BOLT DEFORMATIONNJEM0073S18Install nuts to connecting rod bolts. Check that the nut can be
screwed smoothly on bolt threads by hand to the last thread
on the bolt.
If the nut does not screw in smoothly, measure the outer diam-
eter of the bolt thread at the point specified in the figure.
If a necked point is identified, measure at that point.
Standard: 8.90 - 9.00 mm (0.3504 - 0.3543 in) dia.
Limit: 8.75 mm (0. 3445 in) dia.
If the measurement exceeds the limit, replace connecting rod
bolts and nuts.
AEM100
FLYWHEEL RUNOUTNJEM0073S11Runout (Total indicator reading):
Flywheel★
Less than 0.15 mm (0.0059 in)
CAUTION:
The signal plate is built into the flywheel assembly. Be
careful not to damage the signal plate, especially the
teeth.
Check the signal plate for deformation or cracks.
Never place the flywheel assembly with the signal plate
facing down.
Keep any magnetized objects away from the signal plate.
Do not allow any magnetic materials to contact the signal
plate teeth.
JEM221G
OIL JETNJEM0073S19Check nozzle for deformation or damage.
Check oil passage for obstruction by blowing in air on nozzle
side.
If abnormality is found, clean or replace.
JEM222G
OIL JET RELIEF VALVENJEM0073S20Using a clean resin rod, press down on the check valve inside relief
valve. Check for appropriate bounce/repulsion and smooth
operation.
CYLINDER BLOCKYD
Inspection (Cont’d)
EM-80
Page 265 of 3189
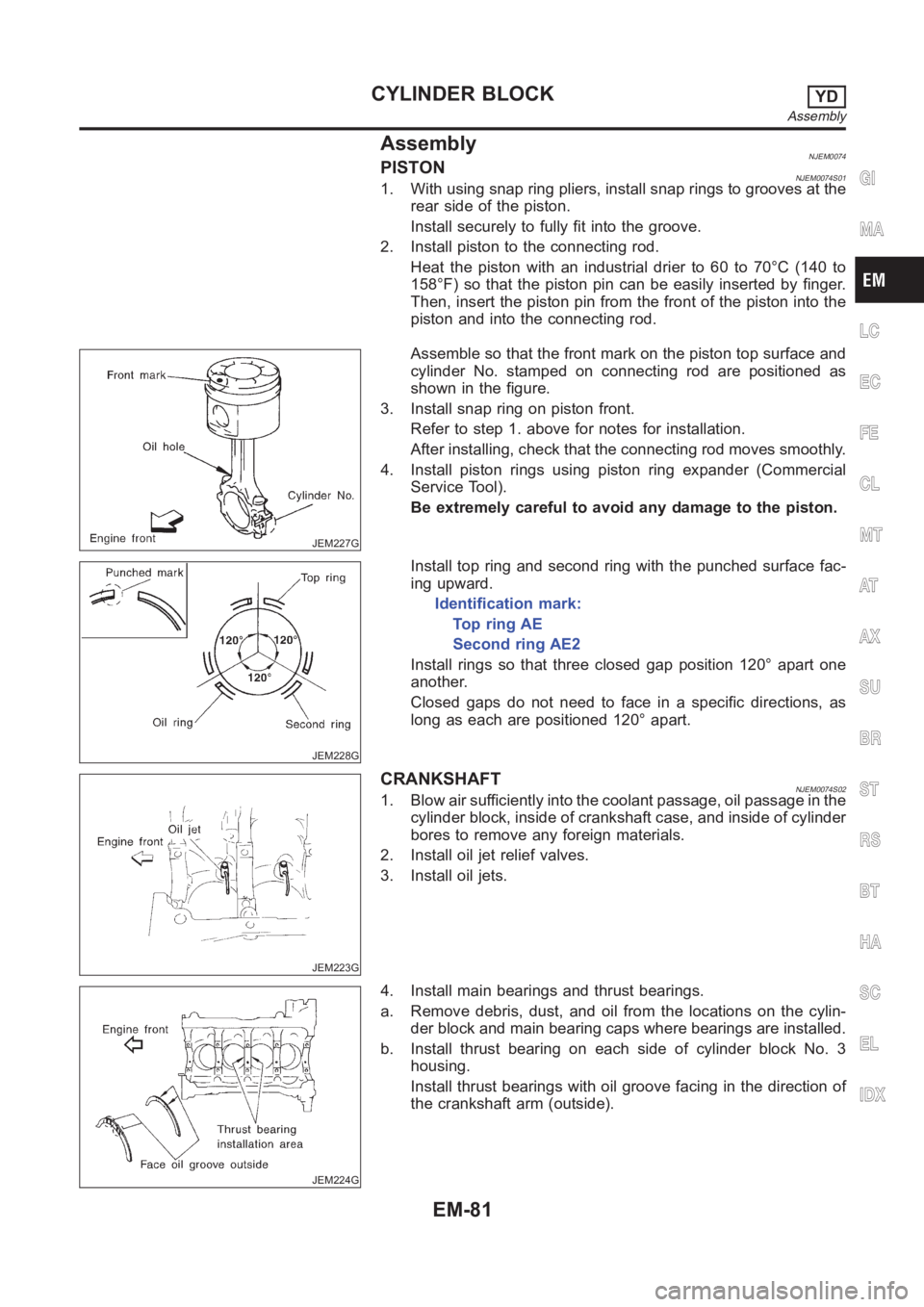
AssemblyNJEM0074PISTONNJEM0074S011. With using snap ring pliers, install snap rings to grooves at the
rear side of the piston.
Install securely to fully fit into the groove.
2. Install piston to the connecting rod.
Heat the piston with an industrial drier to 60 to 70°C (140 to
158°F) so that the piston pin can be easily inserted by finger.
Then, insert the piston pin from the front of the piston into the
piston and into the connecting rod.
JEM227G
Assemble so that the front mark on the piston top surface and
cylinder No. stamped on connecting rod are positioned as
shown in the figure.
3. Install snap ring on piston front.
Refer to step 1. above for notes for installation.
After installing, check that the connecting rod moves smoothly.
4. Install piston rings using piston ring expander (Commercial
Service Tool).
Be extremely careful to avoid any damage to the piston.
JEM228G
Install top ring and second ring with the punched surface fac-
ing upward.
Identification mark:
Top ring AE
Second ring AE2
Install rings so that three closed gap position 120° apart one
another.
Closed gaps do not need to face in a specific directions, as
long as each are positioned 120° apart.
JEM223G
CRANKSHAFTNJEM0074S021. Blow air sufficiently into the coolant passage, oil passage in the
cylinder block, inside of crankshaft case, and inside of cylinder
bores to remove any foreign materials.
2. Install oil jet relief valves.
3. Install oil jets.
JEM224G
4. Install main bearings and thrust bearings.
a. Remove debris, dust, and oil from the locations on the cylin-
der block and main bearing caps where bearings are installed.
b. Install thrust bearing on each side of cylinder block No. 3
housing.
Install thrust bearings with oil groove facing in the direction of
the crankshaft arm (outside).
GI
MA
LC
EC
FE
CL
MT
AT
AX
SU
BR
ST
RS
BT
HA
SC
EL
IDX
CYLINDER BLOCKYD
Assembly
EM-81
Page 266 of 3189
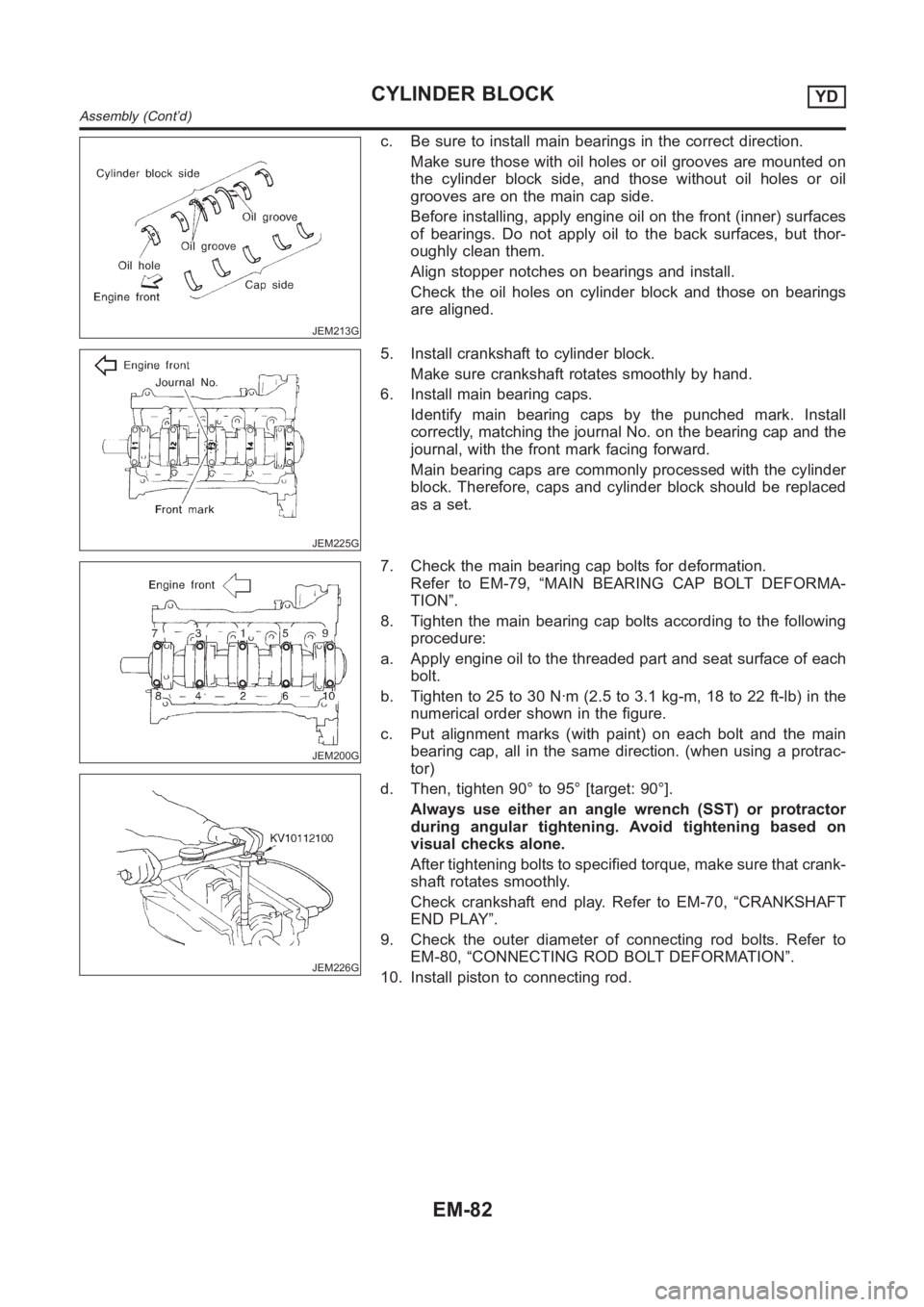
JEM213G
c. Be sure to install main bearings in the correct direction.
Make sure those with oil holes or oil grooves are mounted on
the cylinder block side, and those without oil holes or oil
grooves are on the main cap side.
Before installing, apply engine oil on the front (inner) surfaces
of bearings. Do not apply oil to the back surfaces, but thor-
oughly clean them.
Align stopper notches on bearings and install.
Check the oil holes on cylinder block and those on bearings
are aligned.
JEM225G
5. Install crankshaft to cylinder block.
Make sure crankshaft rotates smoothly by hand.
6. Install main bearing caps.
Identify main bearing caps by the punched mark. Install
correctly, matching the journal No. on the bearing cap and the
journal, with the front mark facing forward.
Main bearing caps are commonly processed with the cylinder
block. Therefore, caps and cylinder block should be replaced
as a set.
JEM200G
JEM226G
7. Check the main bearing cap bolts for deformation.
Refer to EM-79, “MAIN BEARING CAP BOLT DEFORMA-
TION”.
8. Tighten the main bearing cap bolts according to the following
procedure:
a. Apply engine oil to the threaded part and seat surface of each
bolt.
b. Tighten to 25 to 30 N·m (2.5 to 3.1 kg-m, 18 to 22 ft-lb) in the
numerical order shown in the figure.
c. Put alignment marks (with paint) on each bolt and the main
bearing cap, all in the same direction. (when using a protrac-
tor)
d. Then, tighten 90° to 95° [target: 90°].
Always use either an angle wrench (SST) or protractor
during angular tightening. Avoid tightening based on
visual checks alone.
After tightening bolts to specified torque, make sure that crank-
shaft rotates smoothly.
Check crankshaft end play. Refer to EM-70, “CRANKSHAFT
END PLAY”.
9. Check the outer diameter of connecting rod bolts. Refer to
EM-80, “CONNECTING ROD BOLT DEFORMATION”.
10. Install piston to connecting rod.
CYLINDER BLOCKYD
Assembly (Cont’d)
EM-82
Page 267 of 3189
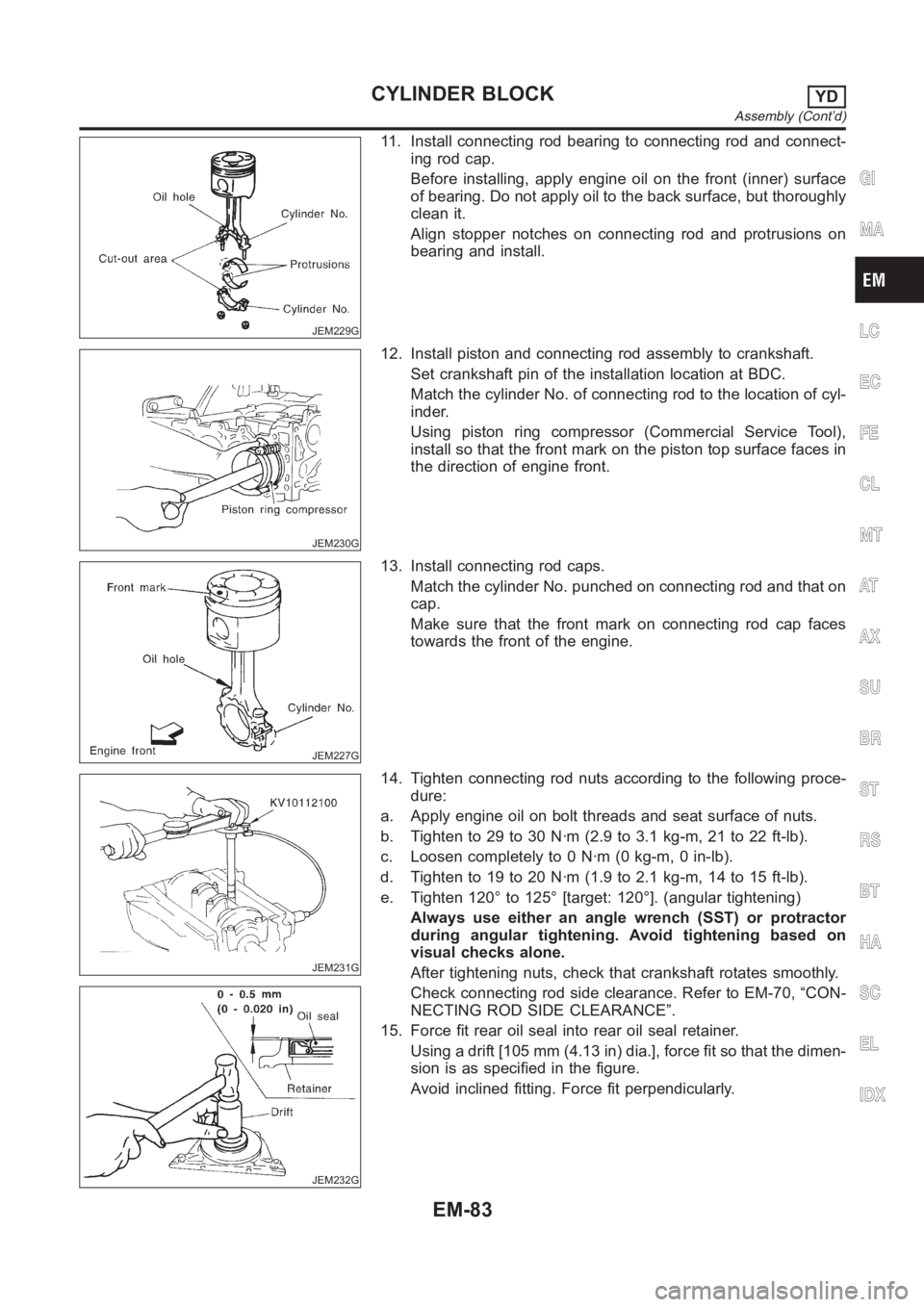
JEM229G
11. Install connecting rod bearing to connecting rod and connect-
ing rod cap.
Before installing, apply engine oil on the front (inner) surface
of bearing. Do not apply oil to the back surface, but thoroughly
clean it.
Align stopper notches on connecting rod and protrusions on
bearing and install.
JEM230G
12. Install piston and connecting rod assembly to crankshaft.
Set crankshaft pin of the installation location at BDC.
Match the cylinder No. of connecting rod to the location of cyl-
inder.
Using piston ring compressor (Commercial Service Tool),
install so that the front mark on the piston top surface faces in
the direction of engine front.
JEM227G
13. Install connecting rod caps.
Match the cylinder No. punched on connecting rod and that on
cap.
Make sure that the front mark on connecting rod cap faces
towards the front of the engine.
JEM231G
JEM232G
14. Tighten connecting rod nuts according to the following proce-
dure:
a. Apply engine oil on bolt threads and seat surface of nuts.
b. Tighten to 29 to 30 N·m (2.9 to 3.1 kg-m, 21 to 22 ft-lb).
c. Loosen completely to 0 N·m (0 kg-m, 0 in-lb).
d. Tighten to 19 to 20 N·m (1.9 to 2.1 kg-m, 14 to 15 ft-lb).
e. Tighten 120° to 125° [target: 120°]. (angular tightening)
Always use either an angle wrench (SST) or protractor
during angular tightening. Avoid tightening based on
visual checks alone.
After tightening nuts, check that crankshaft rotates smoothly.
Check connecting rod side clearance. Refer to EM-70, “CON-
NECTING ROD SIDE CLEARANCE”.
15. Force fit rear oil seal into rear oil seal retainer.
Using a drift [105 mm (4.13 in) dia.], force fit so that the dimen-
sion is as specified in the figure.
Avoid inclined fitting. Force fit perpendicularly.
GI
MA
LC
EC
FE
CL
MT
AT
AX
SU
BR
ST
RS
BT
HA
SC
EL
IDX
CYLINDER BLOCKYD
Assembly (Cont’d)
EM-83
Page 268 of 3189
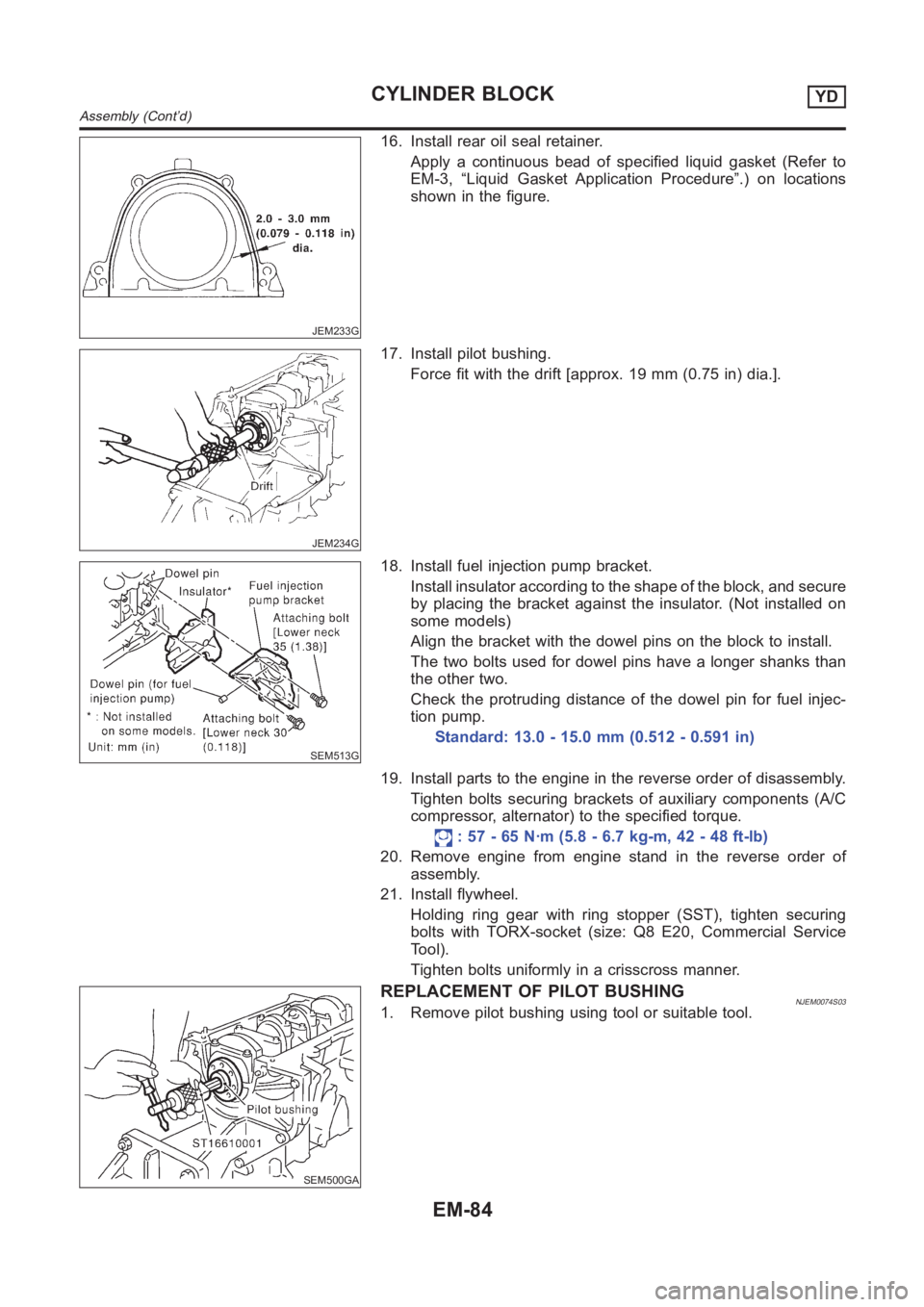
JEM233G
16. Install rear oil seal retainer.
Apply a continuous bead of specified liquid gasket (Refer to
EM-3, “Liquid Gasket Application Procedure”.) on locations
shown in the figure.
JEM234G
17. Install pilot bushing.
Force fit with the drift [approx. 19 mm (0.75 in) dia.].
SEM513G
18. Install fuel injection pump bracket.
Install insulator according to the shape of the block, and secure
by placing the bracket against the insulator. (Not installed on
some models)
Align the bracket with the dowel pins on the block to install.
The two bolts used for dowel pins have a longer shanks than
the other two.
Check the protruding distance of the dowel pin for fuel injec-
tion pump.
Standard: 13.0 - 15.0 mm (0.512 - 0.591 in)
19. Install parts to the engine in the reverse order of disassembly.
Tighten bolts securing brackets of auxiliary components (A/C
compressor, alternator) to the specified torque.
: 57 - 65 N·m (5.8 - 6.7 kg-m, 42 - 48 ft-lb)
20. Remove engine from engine stand in the reverse order of
assembly.
21. Install flywheel.
Holding ring gear with ring stopper (SST), tighten securing
bolts with TORX-socket (size: Q8 E20, Commercial Service
Tool).
Tighten bolts uniformly in a crisscross manner.
SEM500GA
REPLACEMENT OF PILOT BUSHINGNJEM0074S031. Remove pilot bushing using tool or suitable tool.
CYLINDER BLOCKYD
Assembly (Cont’d)
EM-84
Page 269 of 3189
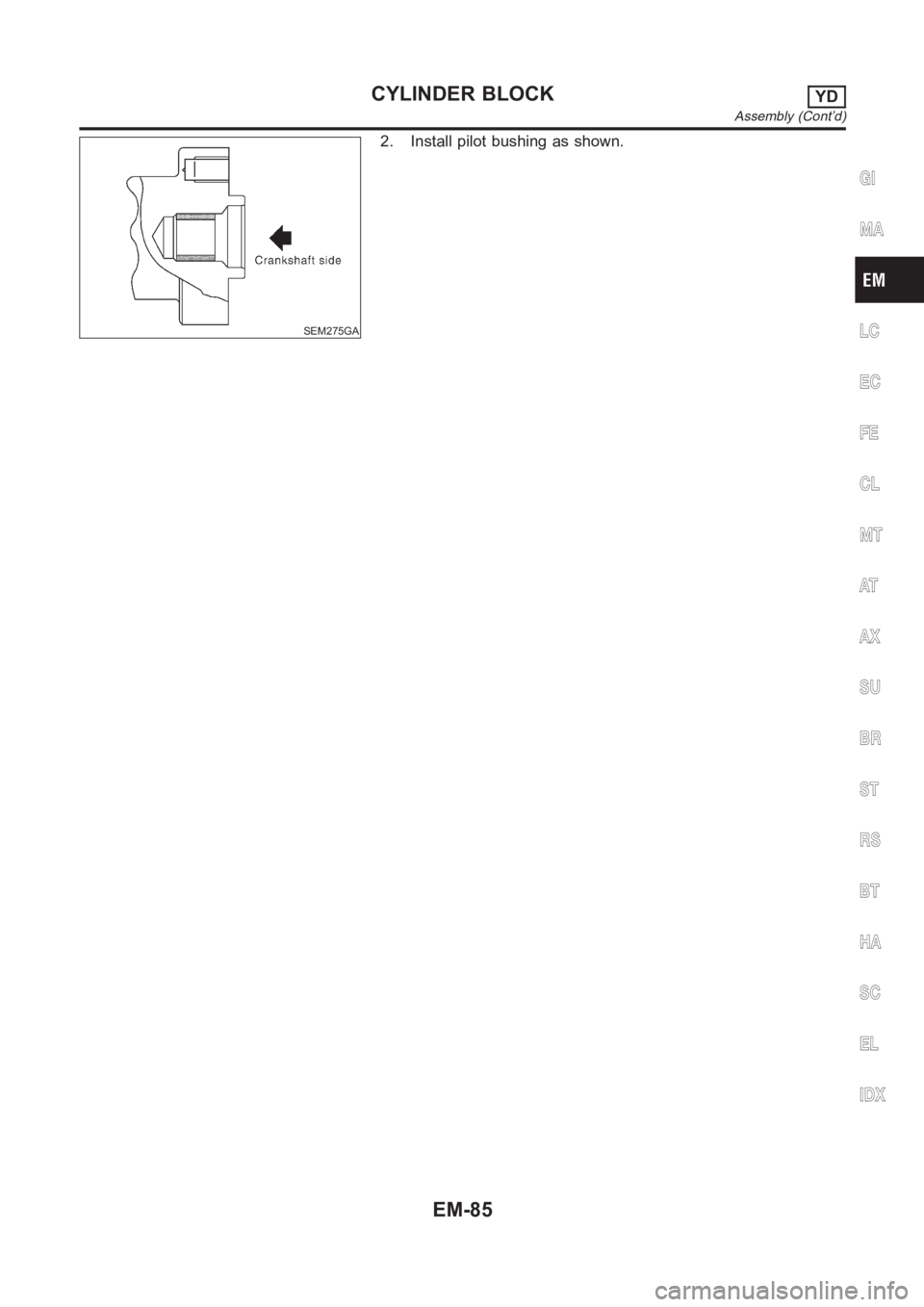
SEM275GA
2. Install pilot bushing as shown.
GI
MA
LC
EC
FE
CL
MT
AT
AX
SU
BR
ST
RS
BT
HA
SC
EL
IDX
CYLINDER BLOCKYD
Assembly (Cont’d)
EM-85
Page 270 of 3189
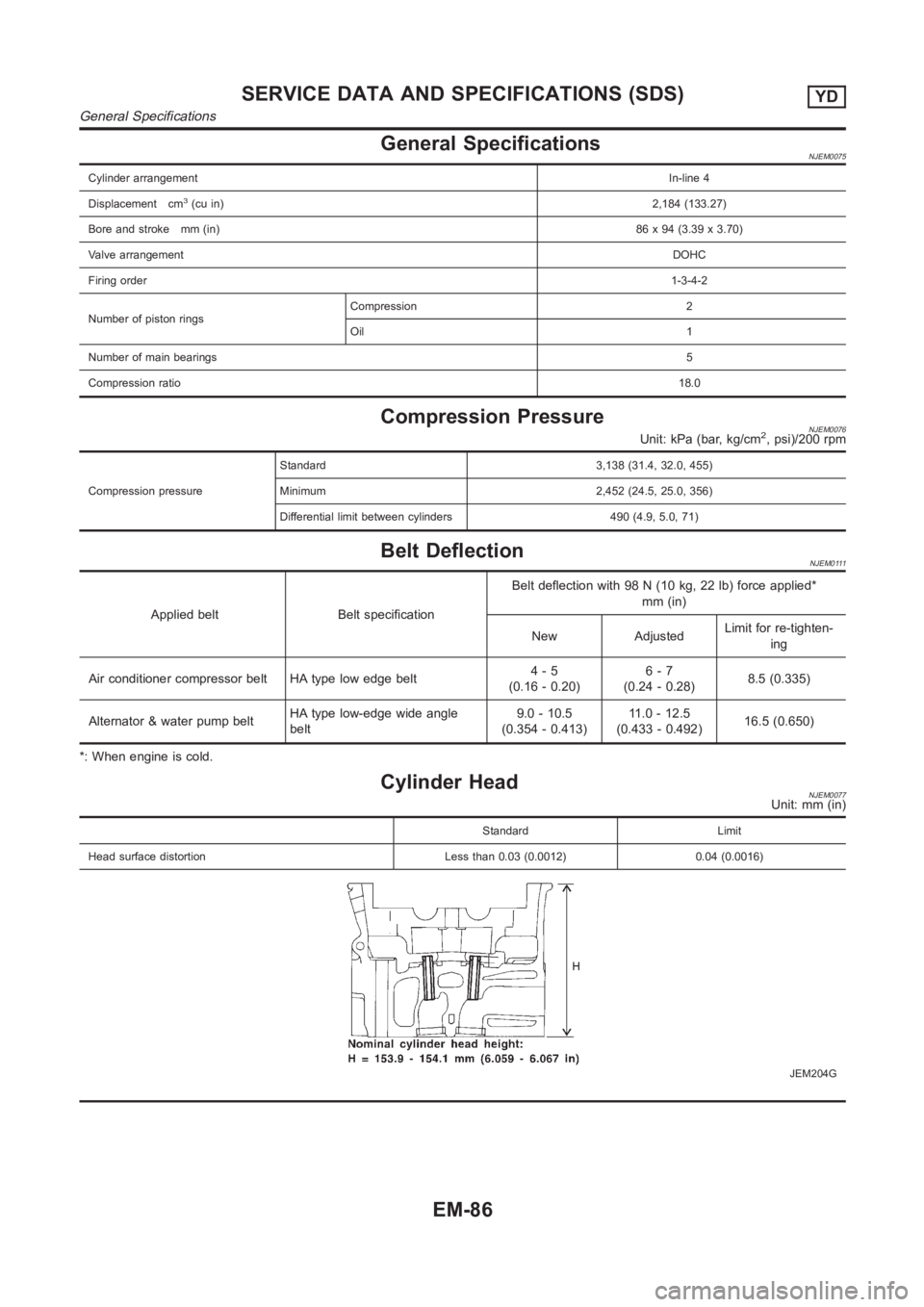
General SpecificationsNJEM0075
Cylinder arrangementIn-line 4
Displacement cm
3(cu in)2,184 (133.27)
Bore and stroke mm (in)86 x 94 (3.39 x 3.70)
Valve arrangementDOHC
Firing order1-3-4-2
Number of piston ringsCompression 2
Oil 1
Number of main bearings5
Compression ratio18.0
Compression PressureNJEM0076Unit: kPa (bar, kg/cm2, psi)/200 rpm
Compression pressureStandard 3,138 (31.4, 32.0, 455)
Minimum 2,452 (24.5, 25.0, 356)
Differential limit between cylinders 490 (4.9, 5.0, 71)
Belt DeflectionNJEM0111
Applied belt Belt specificationBelt deflection with 98 N (10 kg, 22 lb) force applied*
mm (in)
New AdjustedLimit for re-tighten-
ing
Air conditioner compressor belt HA type low edge belt4-5
(0.16 - 0.20)6-7
(0.24 - 0.28)8.5 (0.335)
Alternator & water pump beltHA type low-edge wide angle
belt9.0 - 10.5
(0.354 - 0.413)11 . 0 - 1 2 . 5
(0.433 - 0.492)16.5 (0.650)
*: When engine is cold.
Cylinder HeadNJEM0077Unit: mm (in)
Standard Limit
Head surface distortion Less than 0.03 (0.0012) 0.04 (0.0016)
JEM204G
SERVICE DATA AND SPECIFICATIONS (SDS)YD
General Specifications
EM-86