NISSAN ALMERA N16 2003 Electronic Repair Manual
Manufacturer: NISSAN, Model Year: 2003, Model line: ALMERA N16, Model: NISSAN ALMERA N16 2003Pages: 3189, PDF Size: 54.76 MB
Page 221 of 3189
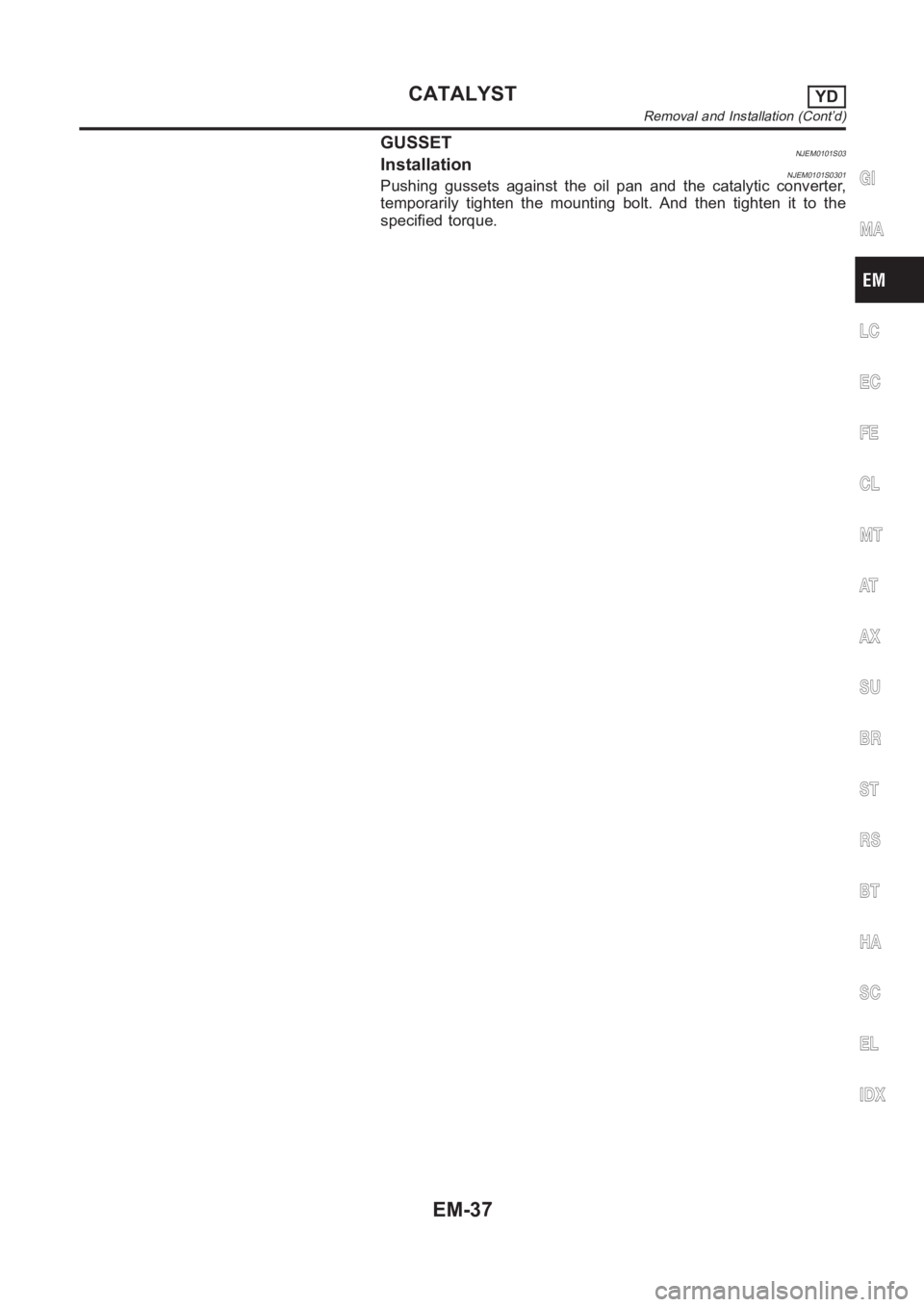
GUSSETNJEM0101S03InstallationNJEM0101S0301Pushing gussets against the oil pan and the catalytic converter,
temporarily tighten the mounting bolt. And then tighten it to the
specified torque.GI
MA
LC
EC
FE
CL
MT
AT
AX
SU
BR
ST
RS
BT
HA
SC
EL
IDX
CATALYSTYD
Removal and Installation (Cont’d)
EM-37
Page 222 of 3189
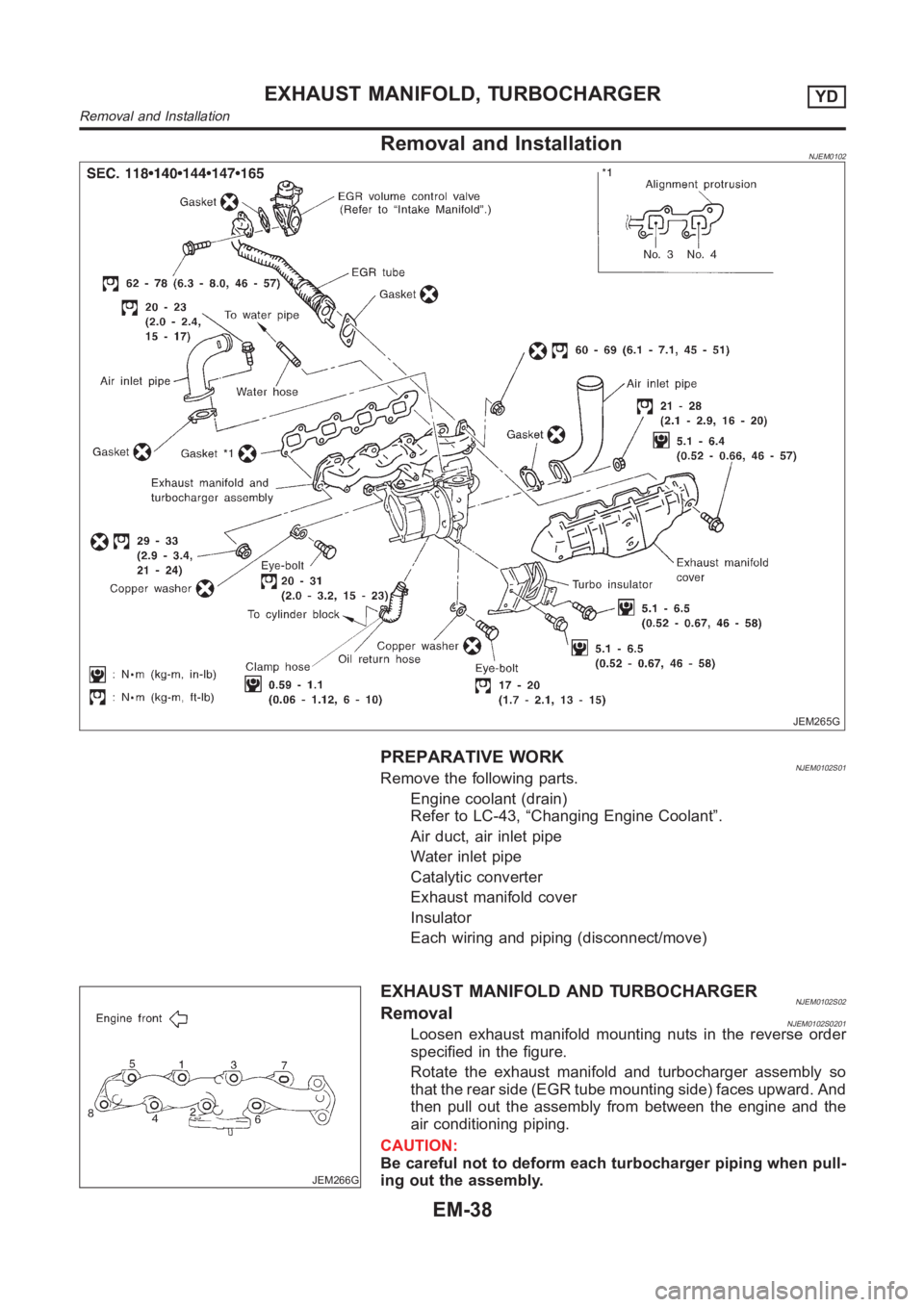
Removal and InstallationNJEM0102
JEM265G
PREPARATIVE WORKNJEM0102S01Remove the following parts.
Engine coolant (drain)
Refer to LC-43, “Changing Engine Coolant”.
Air duct, air inlet pipe
Water inlet pipe
Catalytic converter
Exhaust manifold cover
Insulator
Each wiring and piping (disconnect/move)
JEM266G
EXHAUST MANIFOLD AND TURBOCHARGERNJEM0102S02RemovalNJEM0102S0201Loosen exhaust manifold mounting nuts in the reverse order
specified in the figure.
Rotate the exhaust manifold and turbocharger assembly so
that the rear side (EGR tube mounting side) faces upward. And
then pull out the assembly from between the engine and the
air conditioning piping.
CAUTION:
Be careful not to deform each turbocharger piping when pull-
ing out the assembly.
EXHAUST MANIFOLD, TURBOCHARGERYD
Removal and Installation
EM-38
Page 223 of 3189
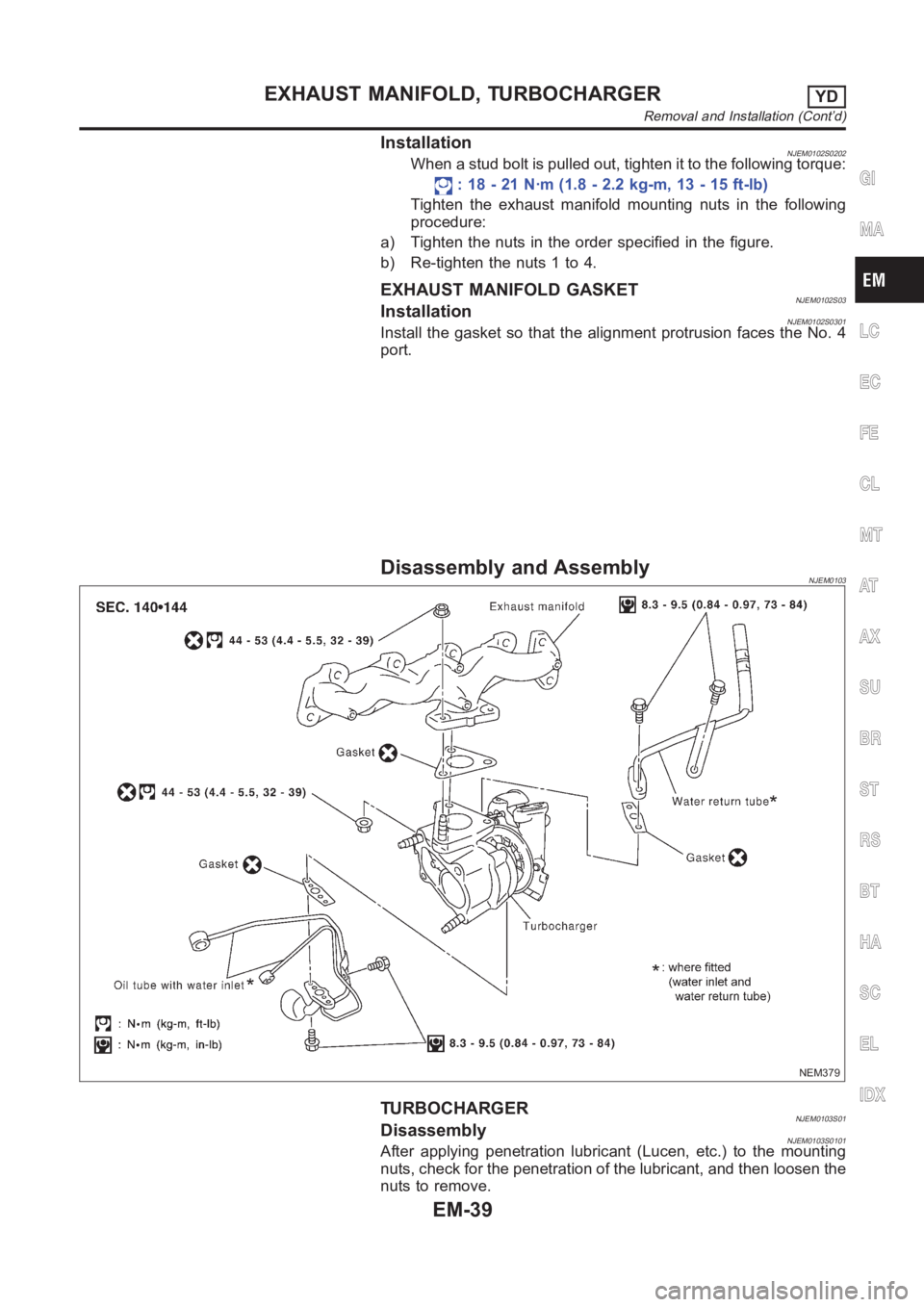
InstallationNJEM0102S0202When a stud bolt is pulled out, tighten it to the following torque:
: 18 - 21 N·m (1.8 - 2.2 kg-m, 13 - 15 ft-lb)
Tighten the exhaust manifold mounting nuts in the following
procedure:
a) Tighten the nuts in the order specified in the figure.
b) Re-tighten the nuts 1 to 4.
EXHAUST MANIFOLD GASKETNJEM0102S03InstallationNJEM0102S0301Install the gasket so that the alignment protrusion faces the No. 4
port.
Disassembly and AssemblyNJEM0103
NEM379
TURBOCHARGERNJEM0103S01DisassemblyNJEM0103S0101After applying penetration lubricant (Lucen, etc.) to the mounting
nuts, check for the penetration of the lubricant, and then loosen the
nuts to remove.
GI
MA
LC
EC
FE
CL
MT
AT
AX
SU
BR
ST
RS
BT
HA
SC
EL
IDX
EXHAUST MANIFOLD, TURBOCHARGERYD
Removal and Installation (Cont’d)
EM-39
Page 224 of 3189
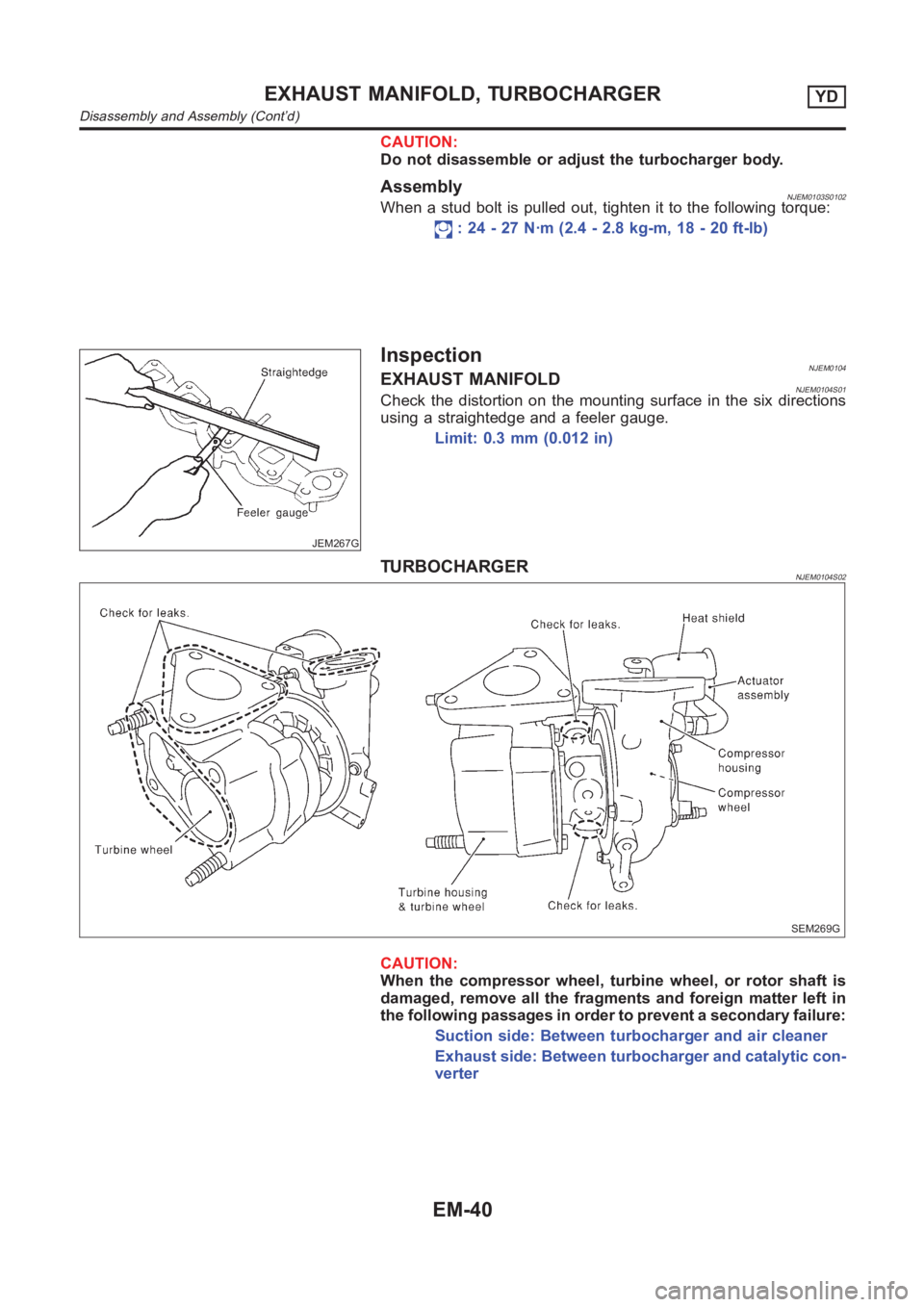
CAUTION:
Do not disassemble or adjust the turbocharger body.
AssemblyNJEM0103S0102When a stud bolt is pulled out, tighten it to the following torque:
: 24 - 27 N·m (2.4 - 2.8 kg-m, 18 - 20 ft-lb)
JEM267G
InspectionNJEM0104EXHAUST MANIFOLDNJEM0104S01Check the distortion on the mounting surface in the six directions
using a straightedge and a feeler gauge.
Limit: 0.3 mm (0.012 in)
TURBOCHARGERNJEM0104S02
SEM269G
CAUTION:
When the compressor wheel, turbine wheel, or rotor shaft is
damaged, remove all the fragments and foreign matter left in
the following passages in order to prevent a secondary failure:
Suction side: Between turbocharger and air cleaner
Exhaust side: Between turbocharger and catalytic con-
verter
EXHAUST MANIFOLD, TURBOCHARGERYD
Disassembly and Assembly (Cont’d)
EM-40
Page 225 of 3189
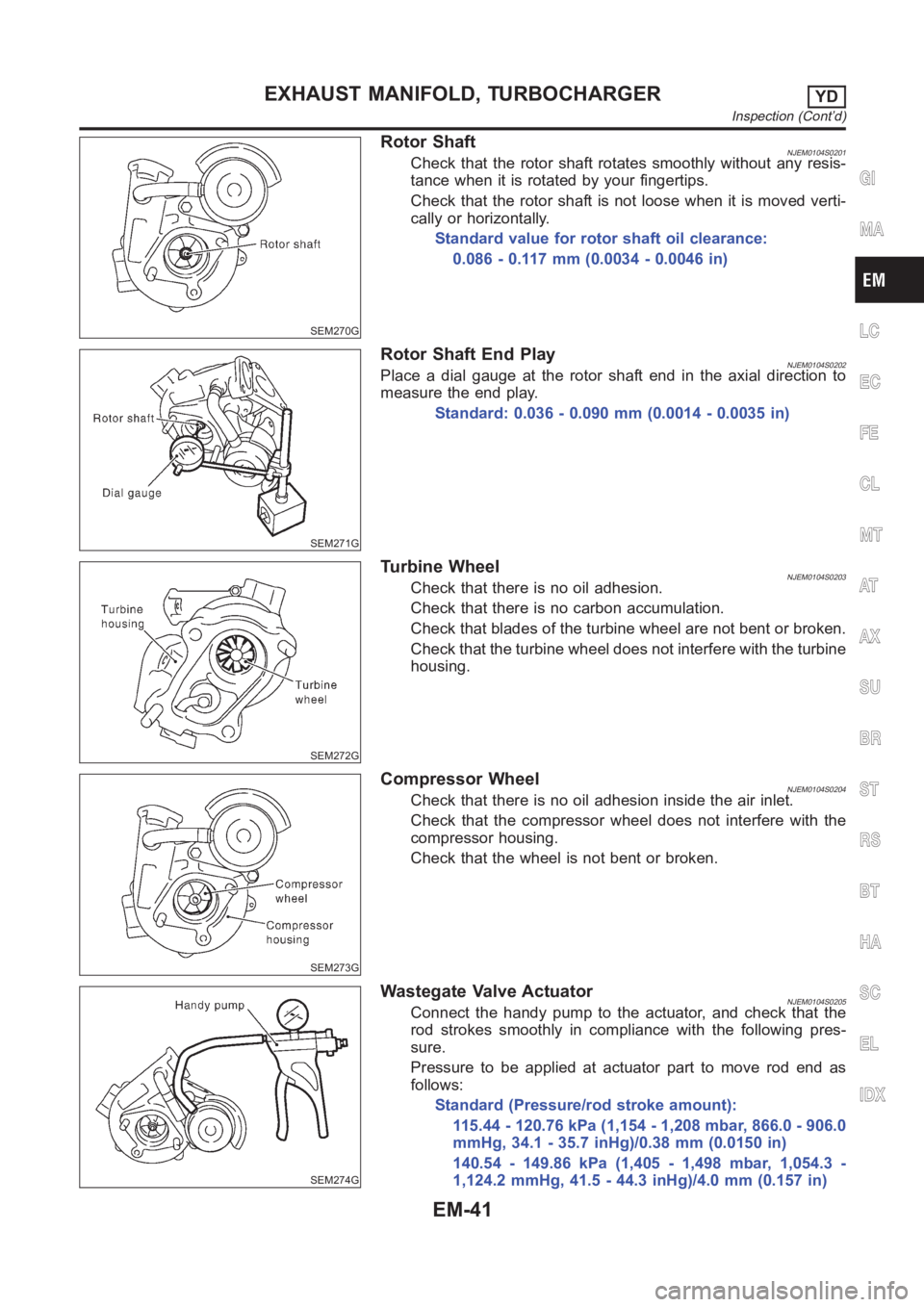
SEM270G
Rotor ShaftNJEM0104S0201Check that the rotor shaft rotates smoothly without any resis-
tance when it is rotated by your fingertips.
Check that the rotor shaft is not loose when it is moved verti-
cally or horizontally.
Standard value for rotor shaft oil clearance:
0.086 - 0.117 mm (0.0034 - 0.0046 in)
SEM271G
Rotor Shaft End PlayNJEM0104S0202Place a dial gauge at the rotor shaft end in the axial direction to
measure the end play.
Standard: 0.036 - 0.090 mm (0.0014 - 0.0035 in)
SEM272G
Turbine WheelNJEM0104S0203Check that there is no oil adhesion.
Check that there is no carbon accumulation.
Check that blades of the turbine wheel are not bent or broken.
Check that the turbine wheel does not interfere with the turbine
housing.
SEM273G
Compressor WheelNJEM0104S0204Check that there is no oil adhesion inside the air inlet.
Check that the compressor wheel does not interfere with the
compressor housing.
Check that the wheel is not bent or broken.
SEM274G
Wastegate Valve ActuatorNJEM0104S0205Connect the handy pump to the actuator, and check that the
rod strokes smoothly in compliance with the following pres-
sure.
Pressure to be applied at actuator part to move rod end as
follows:
Standard (Pressure/rod stroke amount):
115.44 - 120.76 kPa (1,154 - 1,208 mbar, 866.0 - 906.0
mmHg, 34.1 - 35.7 inHg)/0.38 mm (0.0150 in)
140.54 - 149.86 kPa (1,405 - 1,498 mbar, 1,054.3 -
1,124.2 mmHg, 41.5 - 44.3 inHg)/4.0 mm (0.157 in)
GI
MA
LC
EC
FE
CL
MT
AT
AX
SU
BR
ST
RS
BT
HA
SC
EL
IDX
EXHAUST MANIFOLD, TURBOCHARGERYD
Inspection (Cont’d)
EM-41
Page 226 of 3189
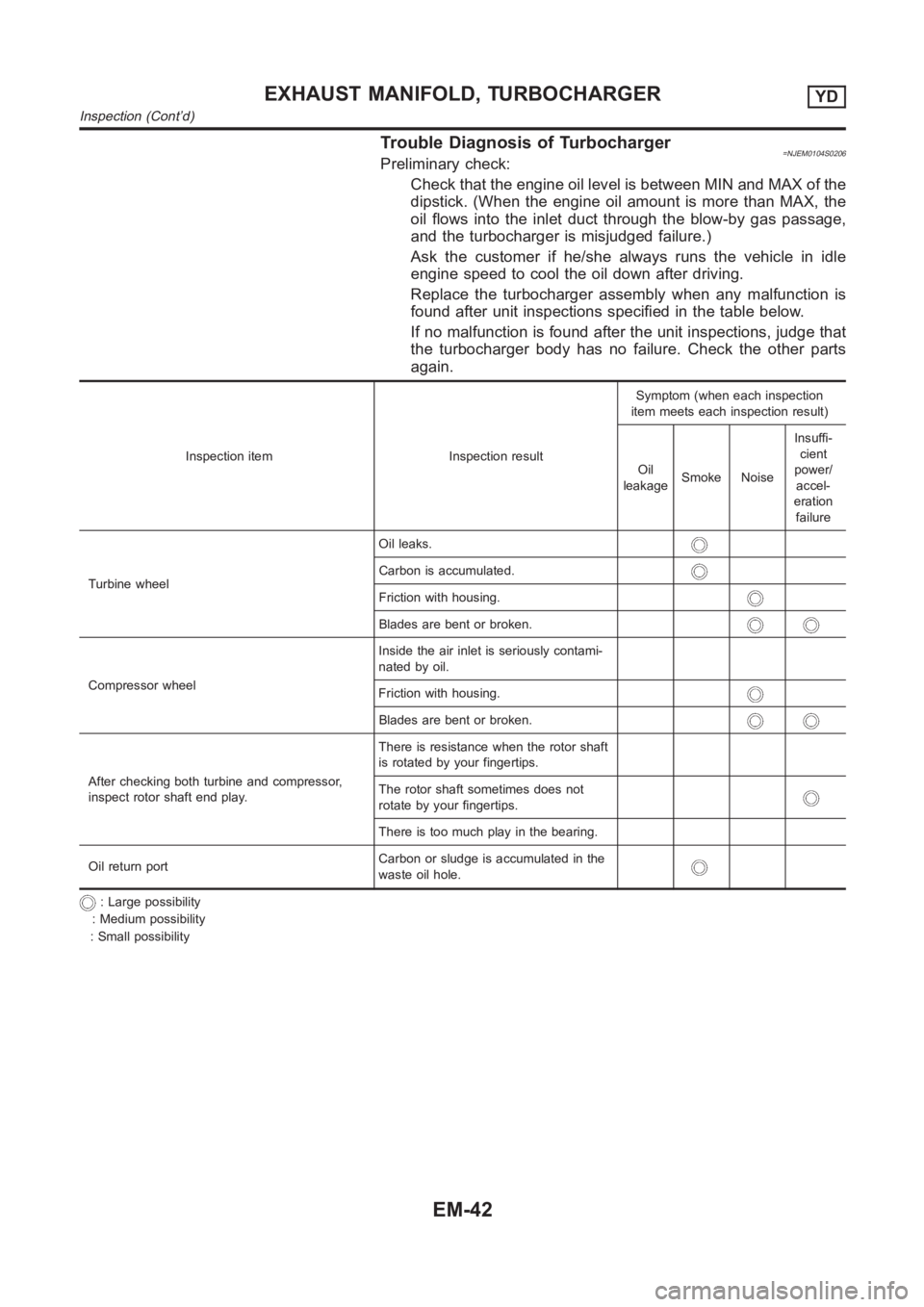
Trouble Diagnosis of Turbocharger=NJEM0104S0206Preliminary check:
Check that the engine oil level is between MIN and MAX of the
dipstick. (When the engine oil amount is more than MAX, the
oil flows into the inlet duct through the blow-by gas passage,
and the turbocharger is misjudged failure.)
Ask the customer if he/she always runs the vehicle in idle
engine speed to cool the oil down after driving.
Replace the turbocharger assembly when any malfunction is
found after unit inspections specified in the table below.
If no malfunction is found after the unit inspections, judge that
the turbocharger body has no failure. Check the other parts
again.
Inspection item Inspection resultSymptom (when each inspection
item meets each inspection result)
Oil
leakageSmoke NoiseInsuffi-
cient
power/
accel-
eration
failure
Turbine wheelOil leaks.
Carbon is accumulated.
Friction with housing.
Blades are bent or broken.
Compressor wheelInside the air inlet is seriously contami-
nated by oil.
Friction with housing.
Blades are bent or broken.
After checking both turbine and compressor,
inspect rotor shaft end play.There is resistance when the rotor shaft
is rotated by your fingertips.
The rotor shaft sometimes does not
rotate by your fingertips.
There is too much play in the bearing.
Oil return portCarbon or sludge is accumulated in the
waste oil hole.
: Large possibility
: Medium possibility
: Small possibility
EXHAUST MANIFOLD, TURBOCHARGERYD
Inspection (Cont’d)
EM-42
Page 227 of 3189
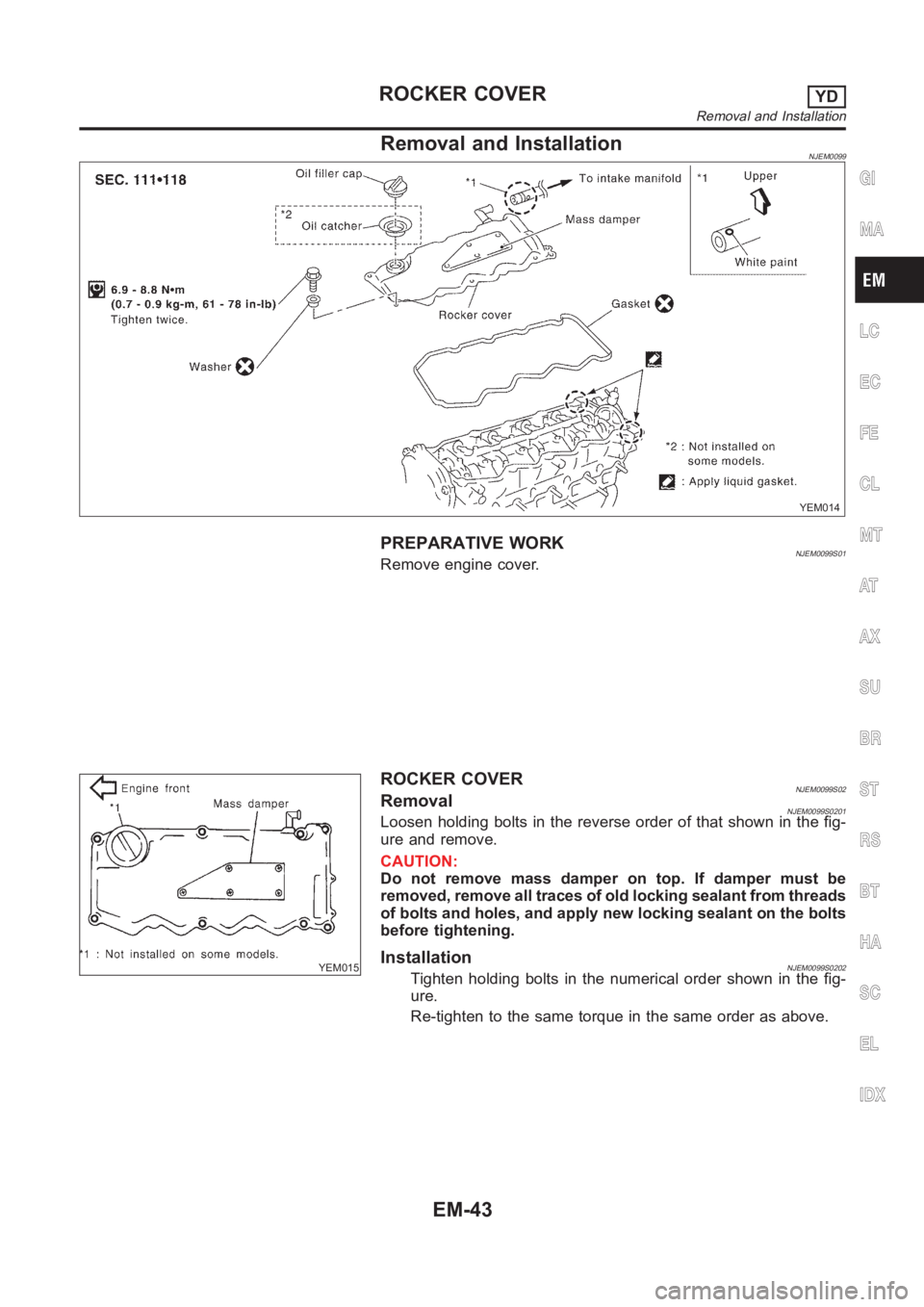
Removal and InstallationNJEM0099
YEM014
PREPARATIVE WORKNJEM0099S01Remove engine cover.
YEM015
ROCKER COVERNJEM0099S02RemovalNJEM0099S0201Loosen holding bolts in the reverse order of that shown in the fig-
ure and remove.
CAUTION:
Do not remove mass damper on top. If damper must be
removed, remove all traces of old locking sealant from threads
of bolts and holes, and apply new locking sealant on the bolts
before tightening.
InstallationNJEM0099S0202Tighten holding bolts in the numerical order shown in the fig-
ure.
Re-tighten to the same torque in the same order as above.
GI
MA
LC
EC
FE
CL
MT
AT
AX
SU
BR
ST
RS
BT
HA
SC
EL
IDX
ROCKER COVERYD
Removal and Installation
EM-43
Page 228 of 3189
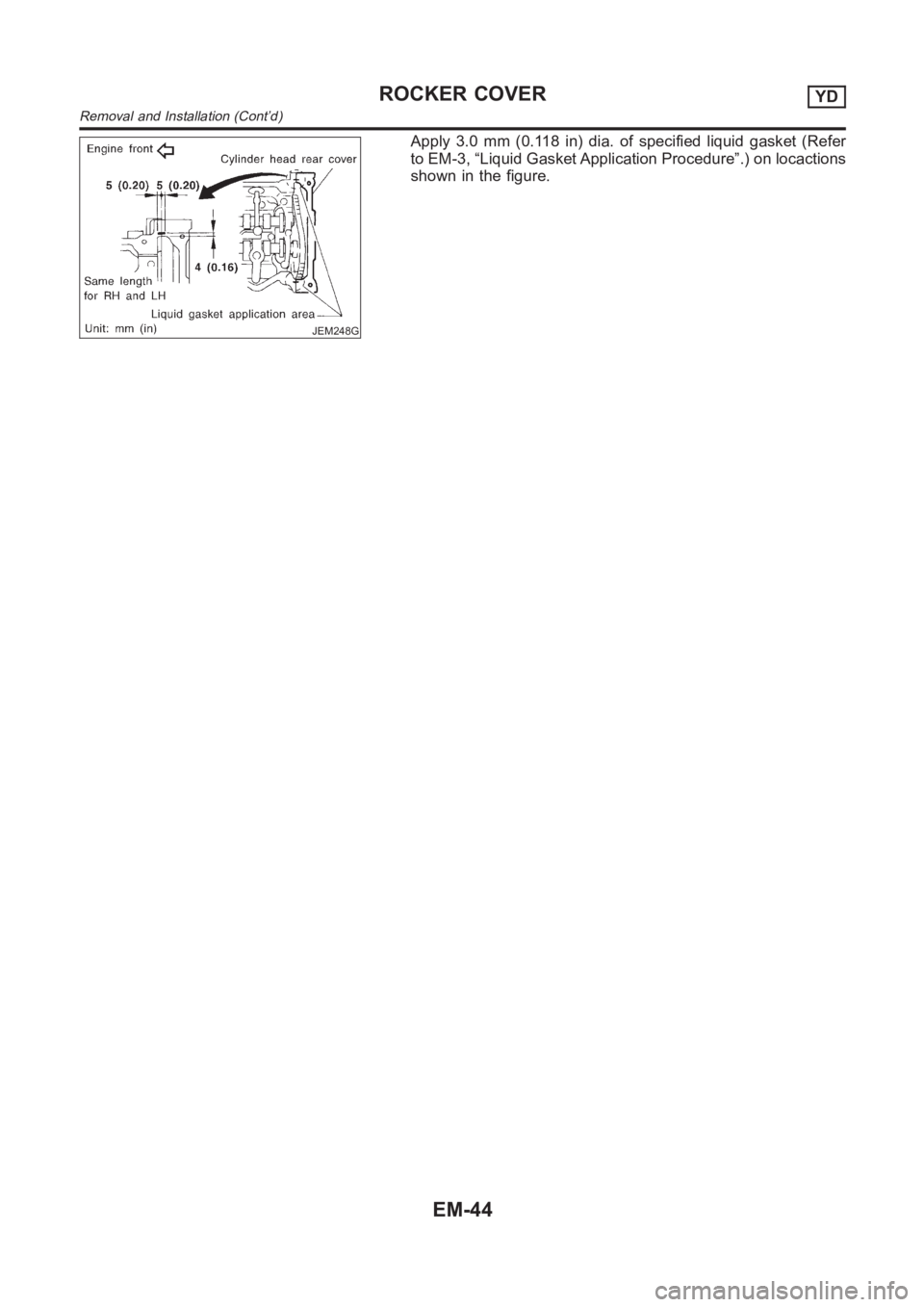
JEM248G
Apply 3.0 mm (0.118 in) dia. of specified liquid gasket (Refer
to EM-3, “Liquid Gasket Application Procedure”.) on locactions
shown in the figure.
ROCKER COVERYD
Removal and Installation (Cont’d)
EM-44
Page 229 of 3189
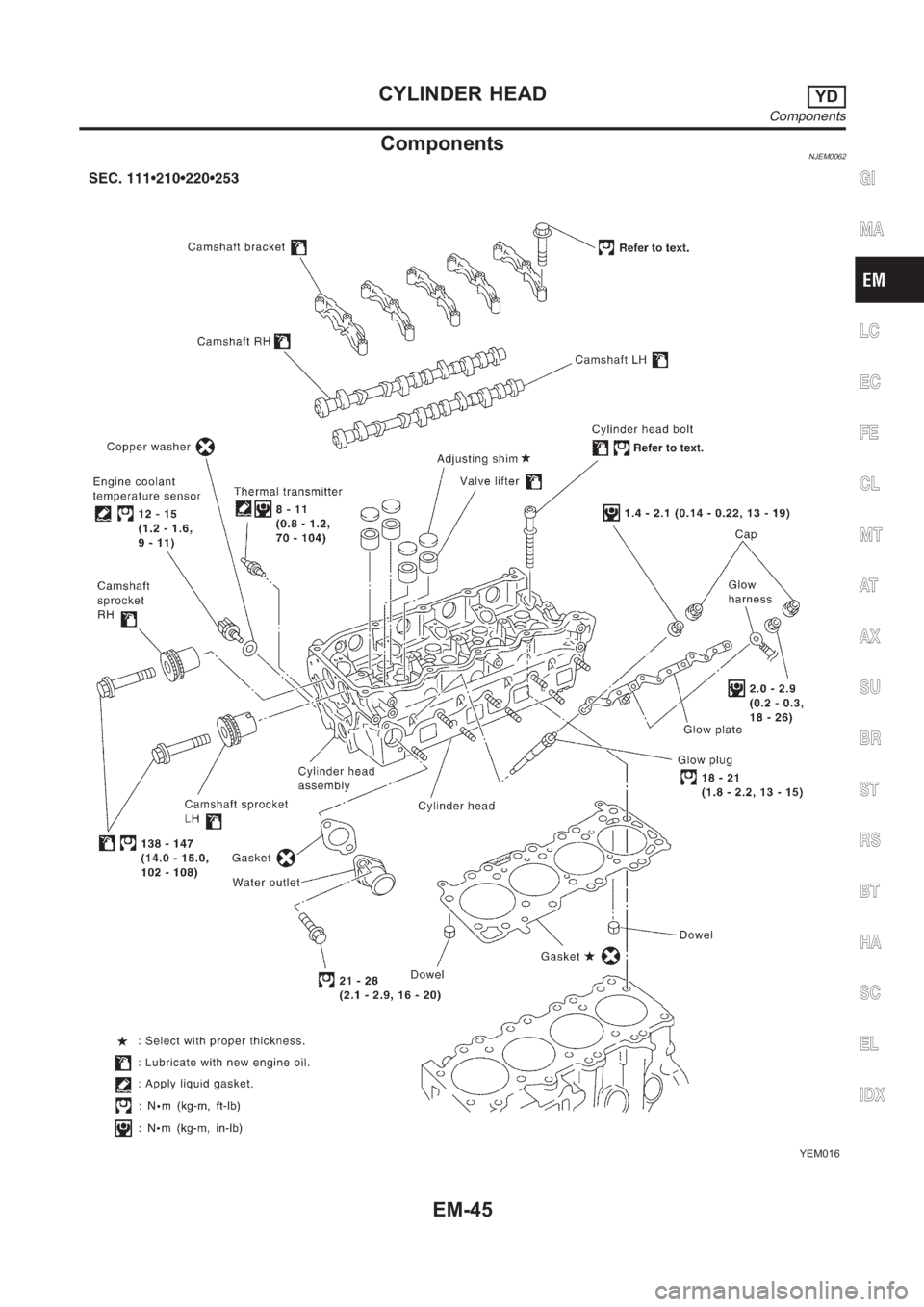
ComponentsNJEM0062
YEM016
GI
MA
LC
EC
FE
CL
MT
AT
AX
SU
BR
ST
RS
BT
HA
SC
EL
IDX
CYLINDER HEADYD
Components
EM-45
Page 230 of 3189
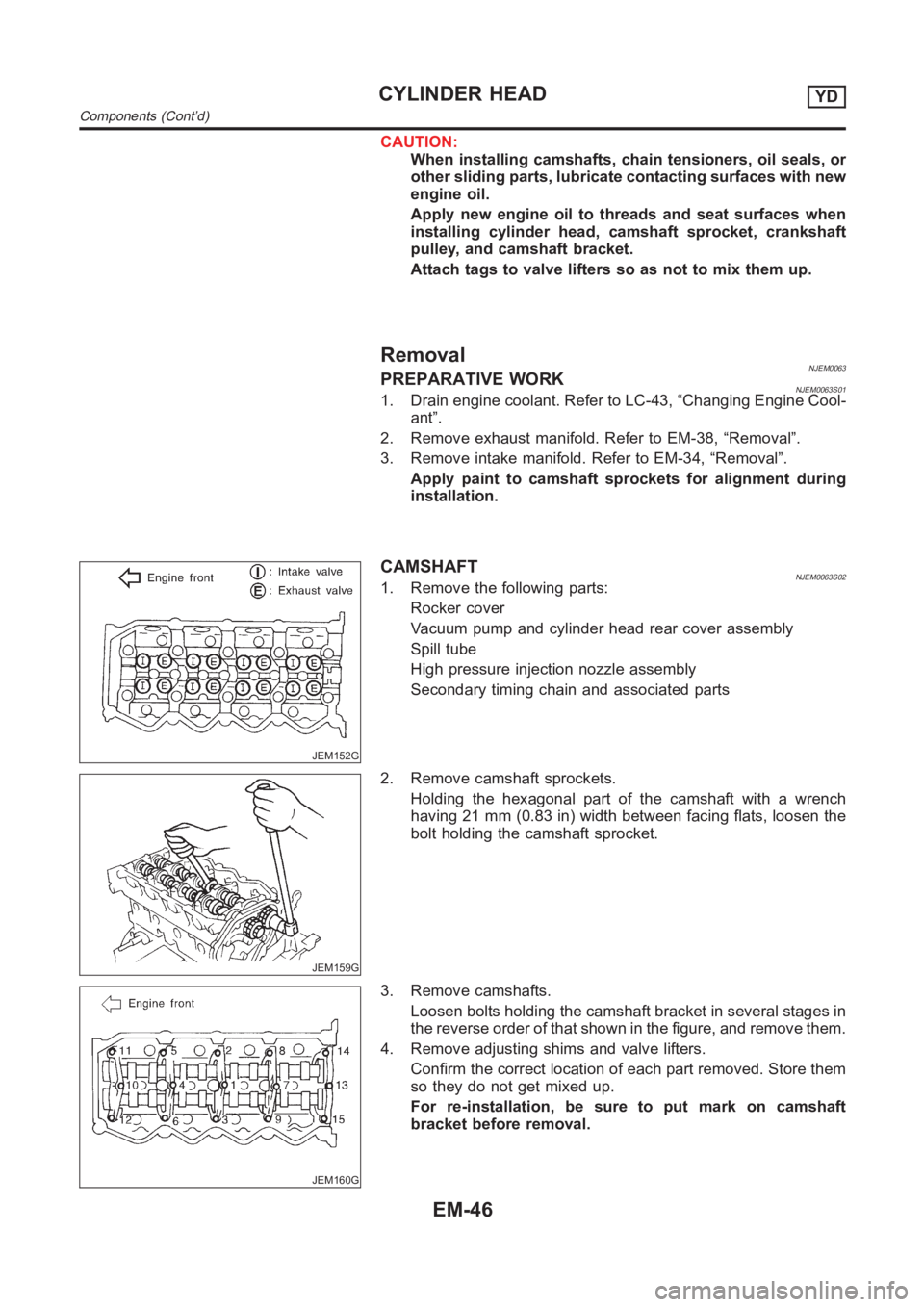
CAUTION:
When installing camshafts, chain tensioners, oil seals, or
other sliding parts, lubricate contacting surfaces with new
engine oil.
Apply new engine oil to threads and seat surfaces when
installing cylinder head, camshaft sprocket, crankshaft
pulley, and camshaft bracket.
Attach tags to valve lifters so as not to mix them up.
RemovalNJEM0063PREPARATIVE WORKNJEM0063S011. Drain engine coolant. Refer to LC-43, “Changing Engine Cool-
ant”.
2. Remove exhaust manifold. Refer to EM-38, “Removal”.
3. Remove intake manifold. Refer to EM-34, “Removal”.
Apply paint to camshaft sprockets for alignment during
installation.
JEM152G
CAMSHAFTNJEM0063S021. Remove the following parts:
Rocker cover
Vacuum pump and cylinder head rear cover assembly
Spill tube
High pressure injection nozzle assembly
Secondary timing chain and associated parts
JEM159G
2. Remove camshaft sprockets.
Holding the hexagonal part of the camshaft with a wrench
having 21 mm (0.83 in) width between facing flats, loosen the
bolt holding the camshaft sprocket.
JEM160G
3. Remove camshafts.
Loosen bolts holding the camshaft bracket in several stages in
the reverse order of that shown in the figure, and remove them.
4. Remove adjusting shims and valve lifters.
Confirm the correct location of each part removed. Store them
so they do not get mixed up.
For re-installation, be sure to put mark on camshaft
bracket before removal.
CYLINDER HEADYD
Components (Cont’d)
EM-46