NISSAN PATROL 1998 Y61 / 5.G Engine Control Owner's Manual
Manufacturer: NISSAN, Model Year: 1998, Model line: PATROL, Model: NISSAN PATROL 1998 Y61 / 5.GPages: 192, PDF Size: 4.28 MB
Page 21 of 192
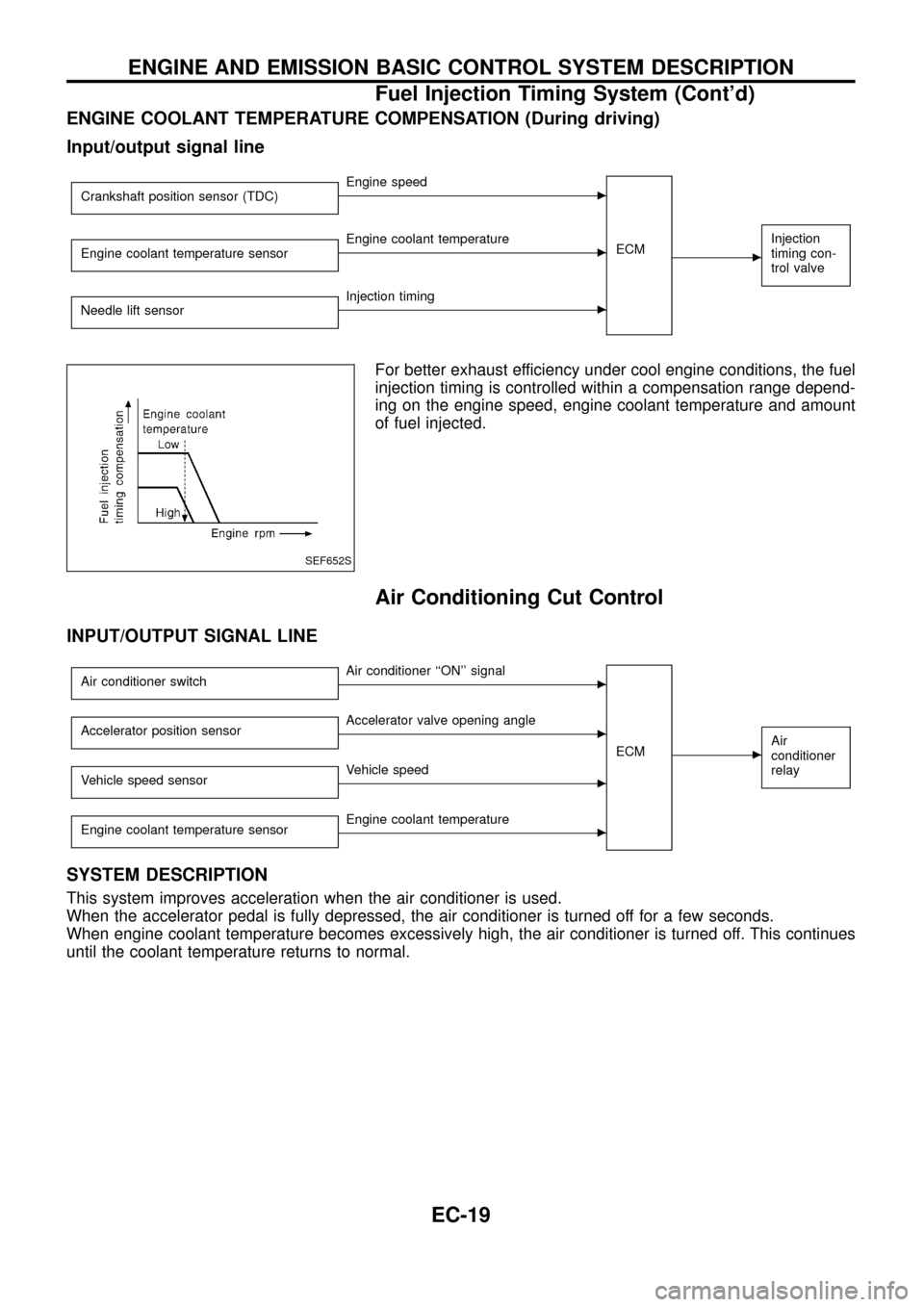
ENGINE COOLANT TEMPERATURE COMPENSATION (During driving)
Input/output signal line
Crankshaft position sensor (TDC)cEngine speed
ECM
c
Injection
timing con-
trol valveEngine coolant temperature sensorcEngine coolant temperature
Needle lift sensor
cInjection timing
For better exhaust efficiency under cool engine conditions, the fuel
injection timing is controlled within a compensation range depend-
ing on the engine speed, engine coolant temperature and amount
of fuel injected.
Air Conditioning Cut Control
INPUT/OUTPUT SIGNAL LINE
Air conditioner switchcAir conditioner ``ON'' signal
ECM
cAir
conditioner
relayAccelerator position sensorcAccelerator valve opening angle
Vehicle speed sensor
cVehicle speed
Engine coolant temperature sensor
cEngine coolant temperature
SYSTEM DESCRIPTION
This system improves acceleration when the air conditioner is used.
When the accelerator pedal is fully depressed, the air conditioner is turned off for a few seconds.
When engine coolant temperature becomes excessively high, the air conditioner is turned off. This continues
until the coolant temperature returns to normal.
SEF652S
ENGINE AND EMISSION BASIC CONTROL SYSTEM DESCRIPTION
Fuel Injection Timing System (Cont'd)
EC-19
Page 22 of 192
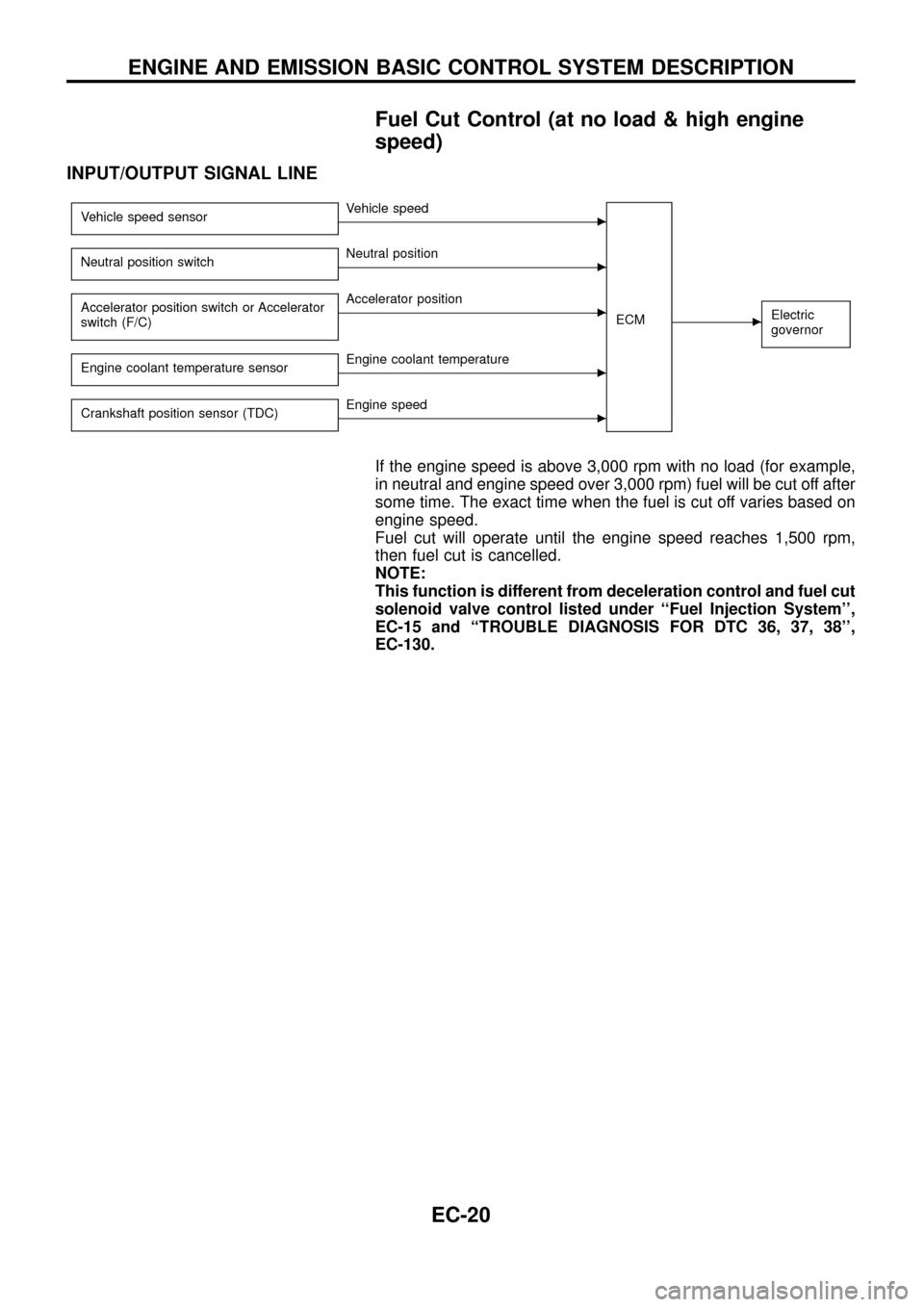
Fuel Cut Control (at no load & high engine
speed)
INPUT/OUTPUT SIGNAL LINE
Vehicle speed sensorcVehicle speed
ECM
cElectric
governor
Neutral position switchcNeutral position
Accelerator position switch or Accelerator
switch (F/C)
cAccelerator position
Engine coolant temperature sensor
cEngine coolant temperature
Crankshaft position sensor (TDC)
cEngine speed
If the engine speed is above 3,000 rpm with no load (for example,
in neutral and engine speed over 3,000 rpm) fuel will be cut off after
some time. The exact time when the fuel is cut off varies based on
engine speed.
Fuel cut will operate until the engine speed reaches 1,500 rpm,
then fuel cut is cancelled.
NOTE:
This function is different from deceleration control and fuel cut
solenoid valve control listed under ``Fuel Injection System'',
EC-15 and ``TROUBLE DIAGNOSIS FOR DTC 36, 37, 38'',
EC-130.
ENGINE AND EMISSION BASIC CONTROL SYSTEM DESCRIPTION
EC-20
Page 23 of 192
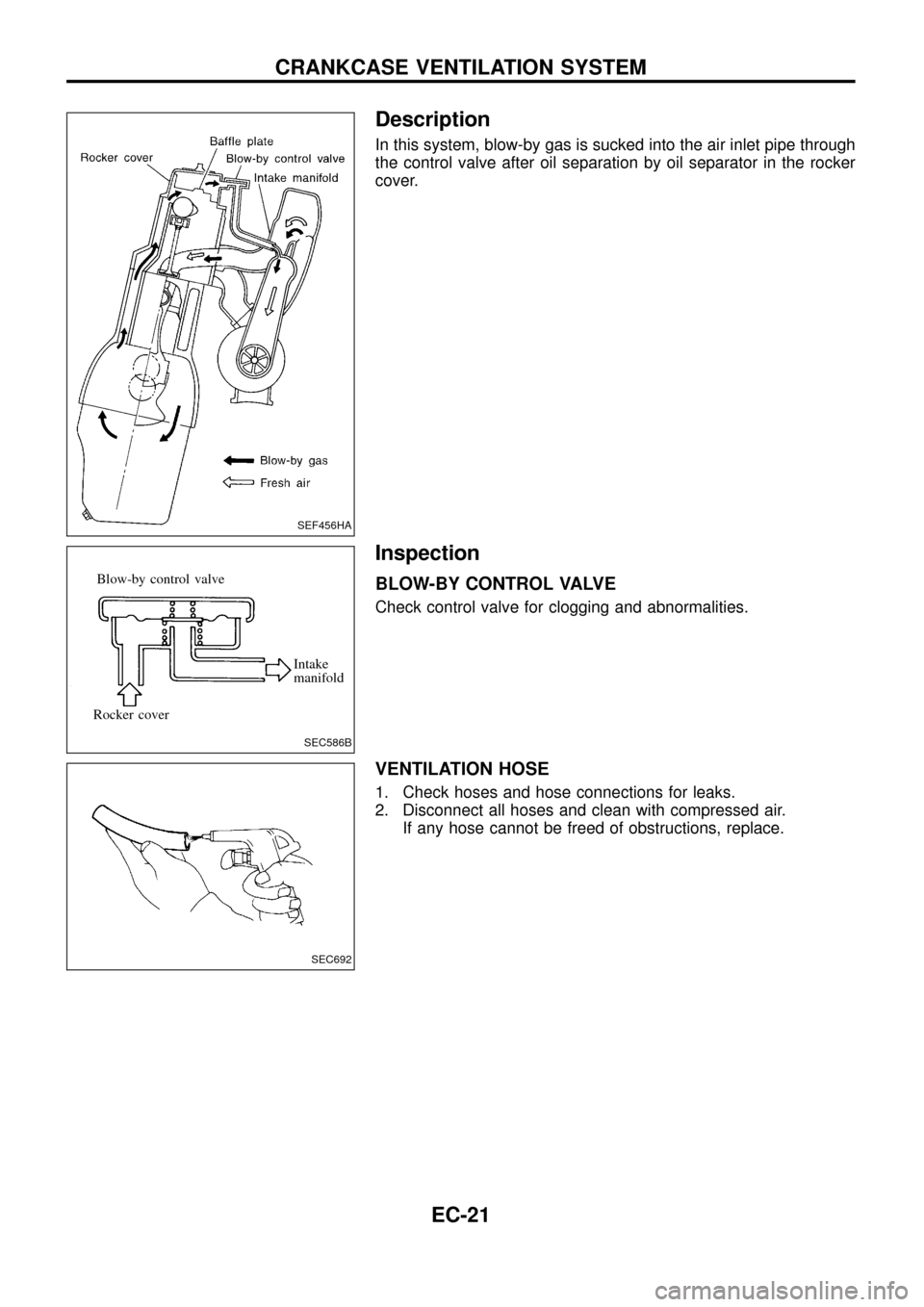
Description
In this system, blow-by gas is sucked into the air inlet pipe through
the control valve after oil separation by oil separator in the rocker
cover.
Inspection
BLOW-BY CONTROL VALVE
Check control valve for clogging and abnormalities.
VENTILATION HOSE
1. Check hoses and hose connections for leaks.
2. Disconnect all hoses and clean with compressed air.
If any hose cannot be freed of obstructions, replace.
SEF456HA
SEC586B
Blow-by control valve
Rocker coverIntake
manifold
SEC692
CRANKCASE VENTILATION SYSTEM
EC-21
Page 24 of 192
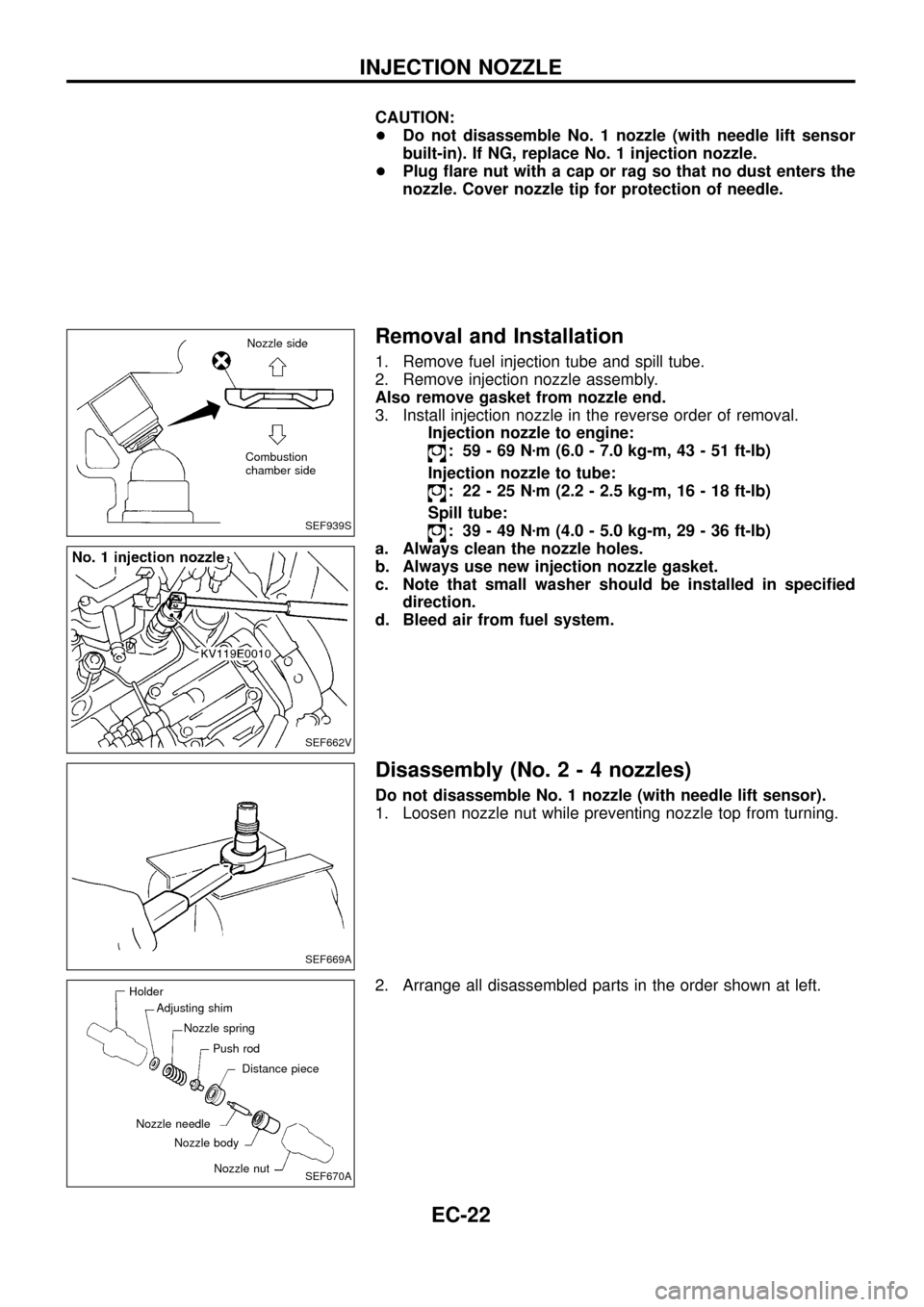
CAUTION:
+Do not disassemble No. 1 nozzle (with needle lift sensor
built-in). If NG, replace No. 1 injection nozzle.
+Plug ¯are nut with a cap or rag so that no dust enters the
nozzle. Cover nozzle tip for protection of needle.
Removal and Installation
1. Remove fuel injection tube and spill tube.
2. Remove injection nozzle assembly.
Also remove gasket from nozzle end.
3. Install injection nozzle in the reverse order of removal.
Injection nozzle to engine:
: 59-69Nzm (6.0 - 7.0 kg-m, 43 - 51 ft-lb)
Injection nozzle to tube:
: 22-25Nzm (2.2 - 2.5 kg-m, 16 - 18 ft-lb)
Spill tube:
: 39-49Nzm (4.0 - 5.0 kg-m, 29 - 36 ft-lb)
a. Always clean the nozzle holes.
b. Always use new injection nozzle gasket.
c. Note that small washer should be installed in speci®ed
direction.
d. Bleed air from fuel system.
Disassembly (No.2-4nozzles)
Do not disassemble No. 1 nozzle (with needle lift sensor).
1. Loosen nozzle nut while preventing nozzle top from turning.
2. Arrange all disassembled parts in the order shown at left.
SEF939S
Nozzle side
Combustion
chamber side
SEF662V
SEF669A
SEF670A
Holder
Adjusting shim
Nozzle spring
Push rod
Distance piece
Nozzle nut Nozzle body Nozzle needle
INJECTION NOZZLE
EC-22
Page 25 of 192
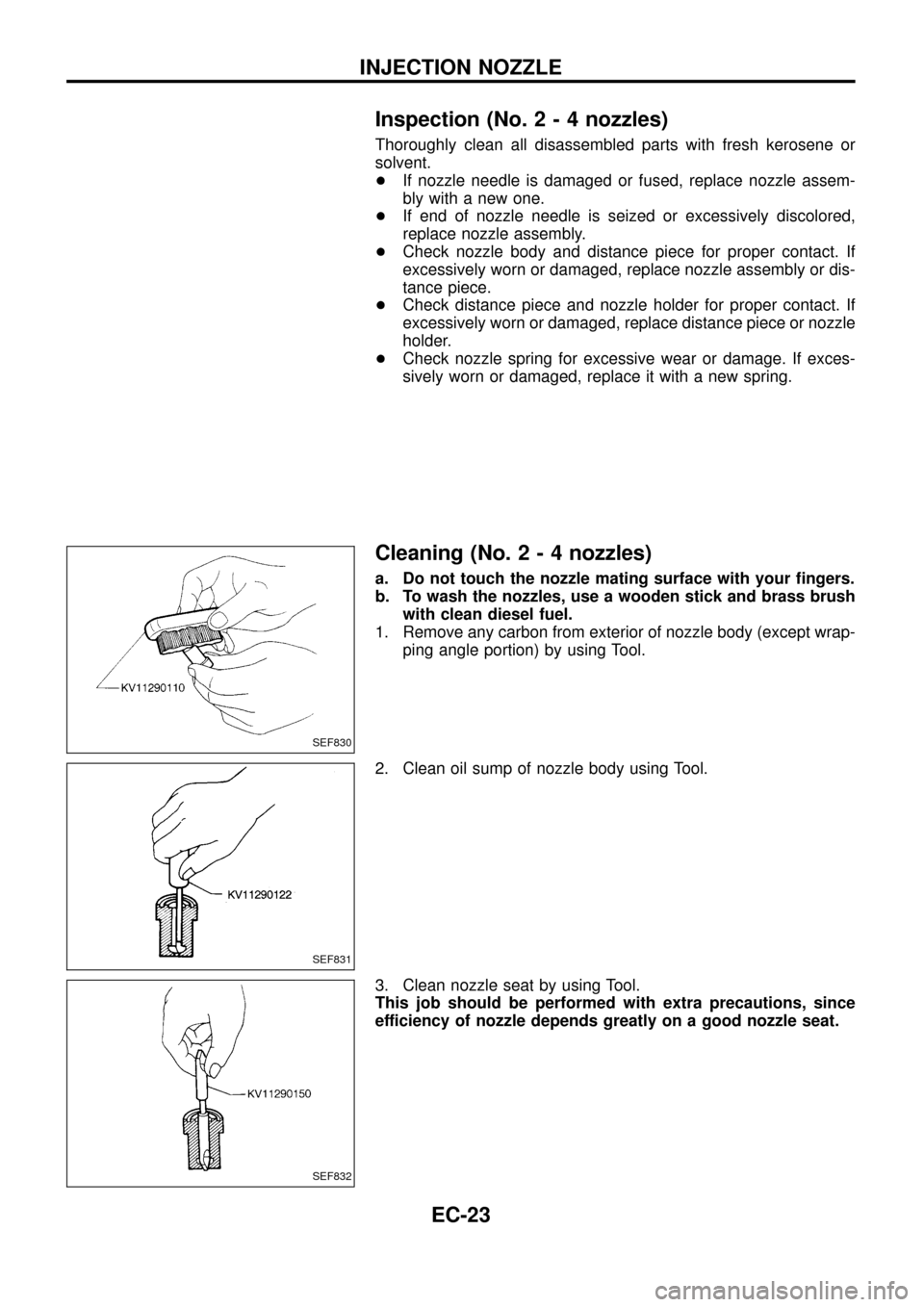
Inspection (No.2-4nozzles)
Thoroughly clean all disassembled parts with fresh kerosene or
solvent.
+If nozzle needle is damaged or fused, replace nozzle assem-
bly with a new one.
+If end of nozzle needle is seized or excessively discolored,
replace nozzle assembly.
+Check nozzle body and distance piece for proper contact. If
excessively worn or damaged, replace nozzle assembly or dis-
tance piece.
+Check distance piece and nozzle holder for proper contact. If
excessively worn or damaged, replace distance piece or nozzle
holder.
+Check nozzle spring for excessive wear or damage. If exces-
sively worn or damaged, replace it with a new spring.
Cleaning (No.2-4nozzles)
a. Do not touch the nozzle mating surface with your ®ngers.
b. To wash the nozzles, use a wooden stick and brass brush
with clean diesel fuel.
1. Remove any carbon from exterior of nozzle body (except wrap-
ping angle portion) by using Tool.
2. Clean oil sump of nozzle body using Tool.
3. Clean nozzle seat by using Tool.
This job should be performed with extra precautions, since
efficiency of nozzle depends greatly on a good nozzle seat.
SEF830
SEF831
SEF832
INJECTION NOZZLE
EC-23
Page 26 of 192
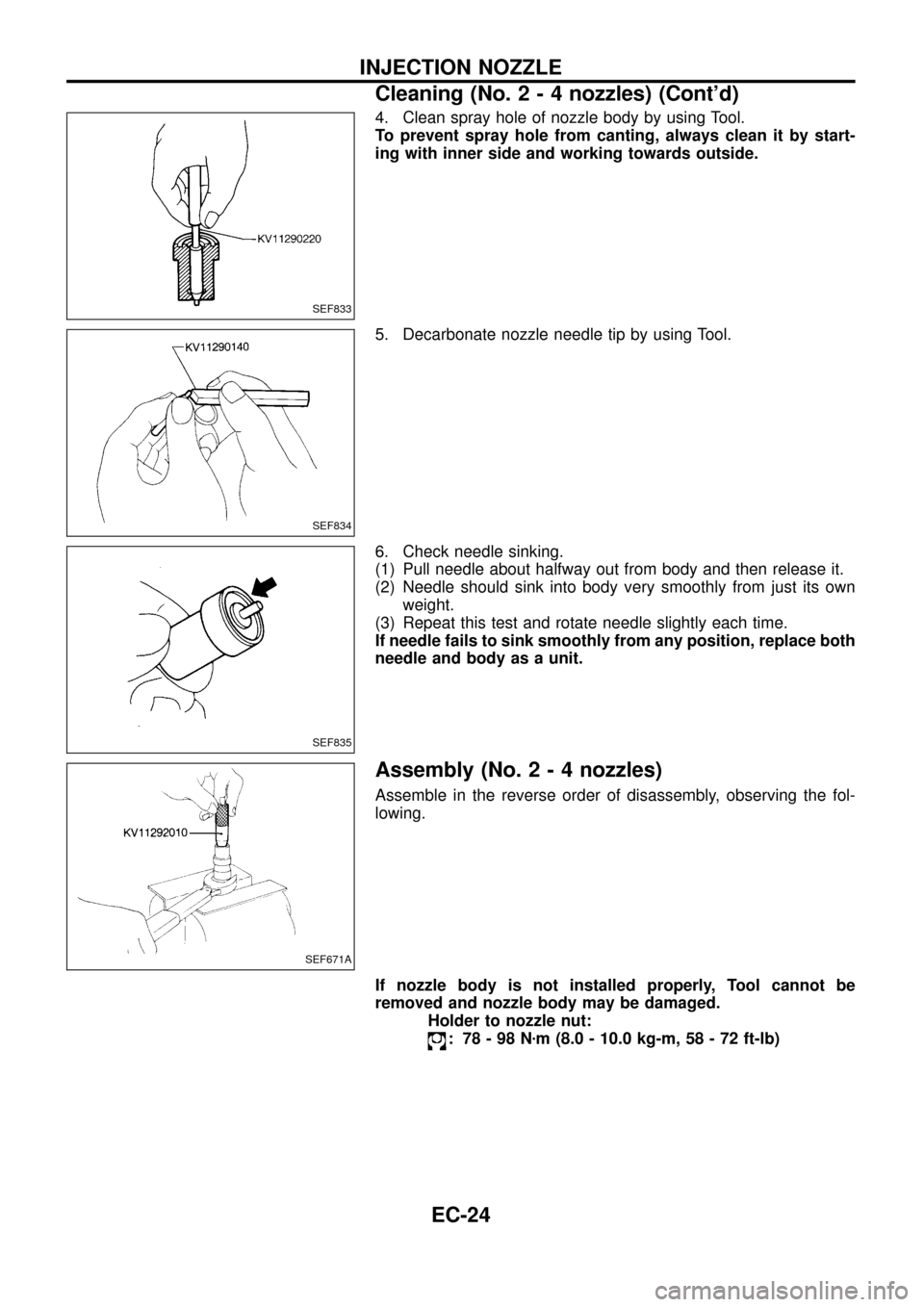
4. Clean spray hole of nozzle body by using Tool.
To prevent spray hole from canting, always clean it by start-
ing with inner side and working towards outside.
5. Decarbonate nozzle needle tip by using Tool.
6. Check needle sinking.
(1) Pull needle about halfway out from body and then release it.
(2) Needle should sink into body very smoothly from just its own
weight.
(3) Repeat this test and rotate needle slightly each time.
If needle fails to sink smoothly from any position, replace both
needle and body as a unit.
Assembly (No.2-4nozzles)
Assemble in the reverse order of disassembly, observing the fol-
lowing.
If nozzle body is not installed properly, Tool cannot be
removed and nozzle body may be damaged.
Holder to nozzle nut:
: 78-98Nzm (8.0 - 10.0 kg-m, 58 - 72 ft-lb)
SEF833
SEF834
SEF835
SEF671A
INJECTION NOZZLE
Cleaning (No.2-4nozzles) (Cont'd)
EC-24
Page 27 of 192
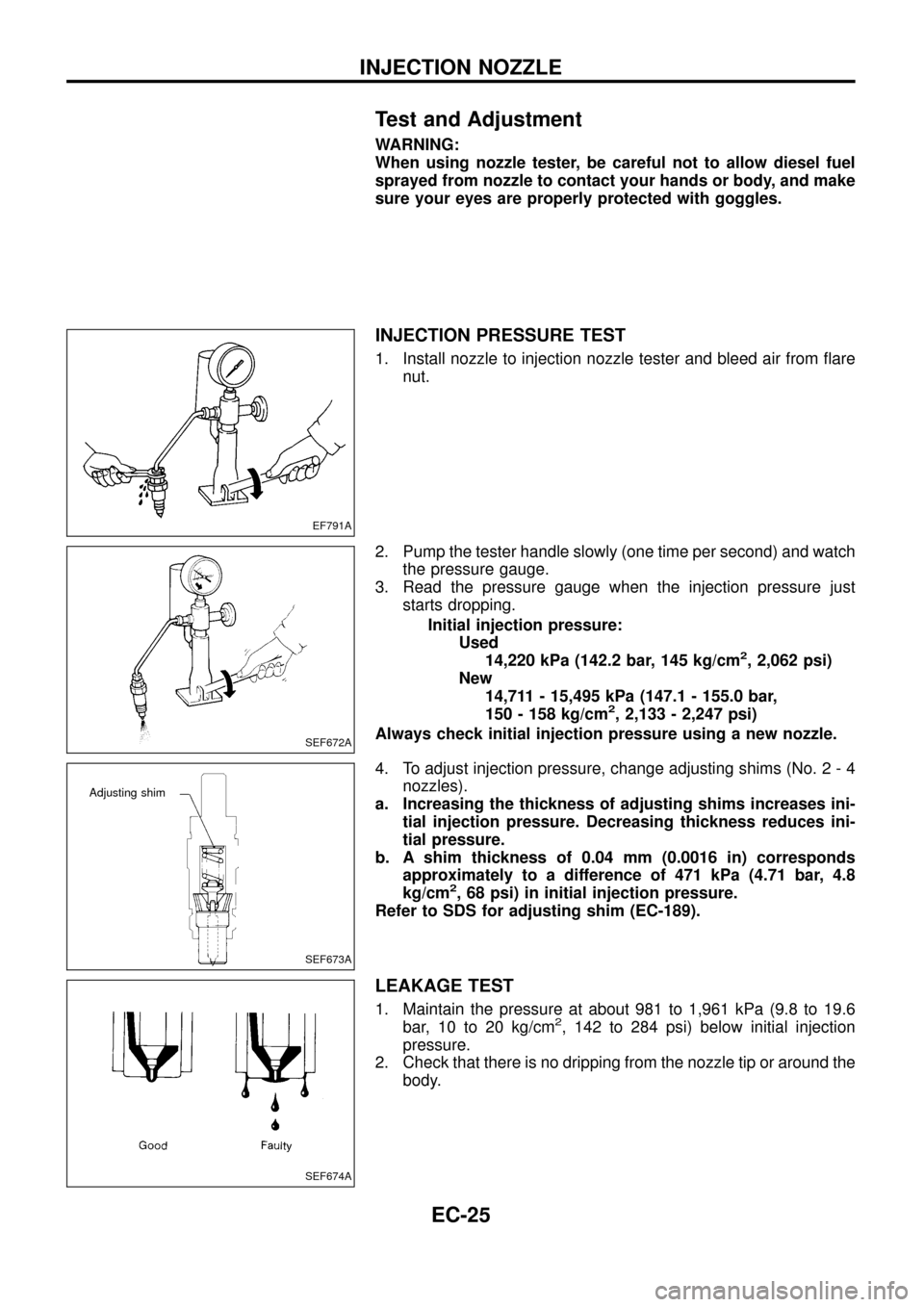
Test and Adjustment
WARNING:
When using nozzle tester, be careful not to allow diesel fuel
sprayed from nozzle to contact your hands or body, and make
sure your eyes are properly protected with goggles.
INJECTION PRESSURE TEST
1. Install nozzle to injection nozzle tester and bleed air from ¯are
nut.
2. Pump the tester handle slowly (one time per second) and watch
the pressure gauge.
3. Read the pressure gauge when the injection pressure just
starts dropping.
Initial injection pressure:
Used
14,220 kPa (142.2 bar, 145 kg/cm
2, 2,062 psi)
New
14,711 - 15,495 kPa (147.1 - 155.0 bar,
150 - 158 kg/cm
2, 2,133 - 2,247 psi)
Always check initial injection pressure using a new nozzle.
4. To adjust injection pressure, change adjusting shims (No. 2 - 4
nozzles).
a. Increasing the thickness of adjusting shims increases ini-
tial injection pressure. Decreasing thickness reduces ini-
tial pressure.
b. A shim thickness of 0.04 mm (0.0016 in) corresponds
approximately to a difference of 471 kPa (4.71 bar, 4.8
kg/cm
2, 68 psi) in initial injection pressure.
Refer to SDS for adjusting shim (EC-189).
LEAKAGE TEST
1. Maintain the pressure at about 981 to 1,961 kPa (9.8 to 19.6
bar, 10 to 20 kg/cm2, 142 to 284 psi) below initial injection
pressure.
2. Check that there is no dripping from the nozzle tip or around the
body.
EF791A
SEF672A
SEF673A
Adjusting shim
SEF674A
INJECTION NOZZLE
EC-25
Page 28 of 192
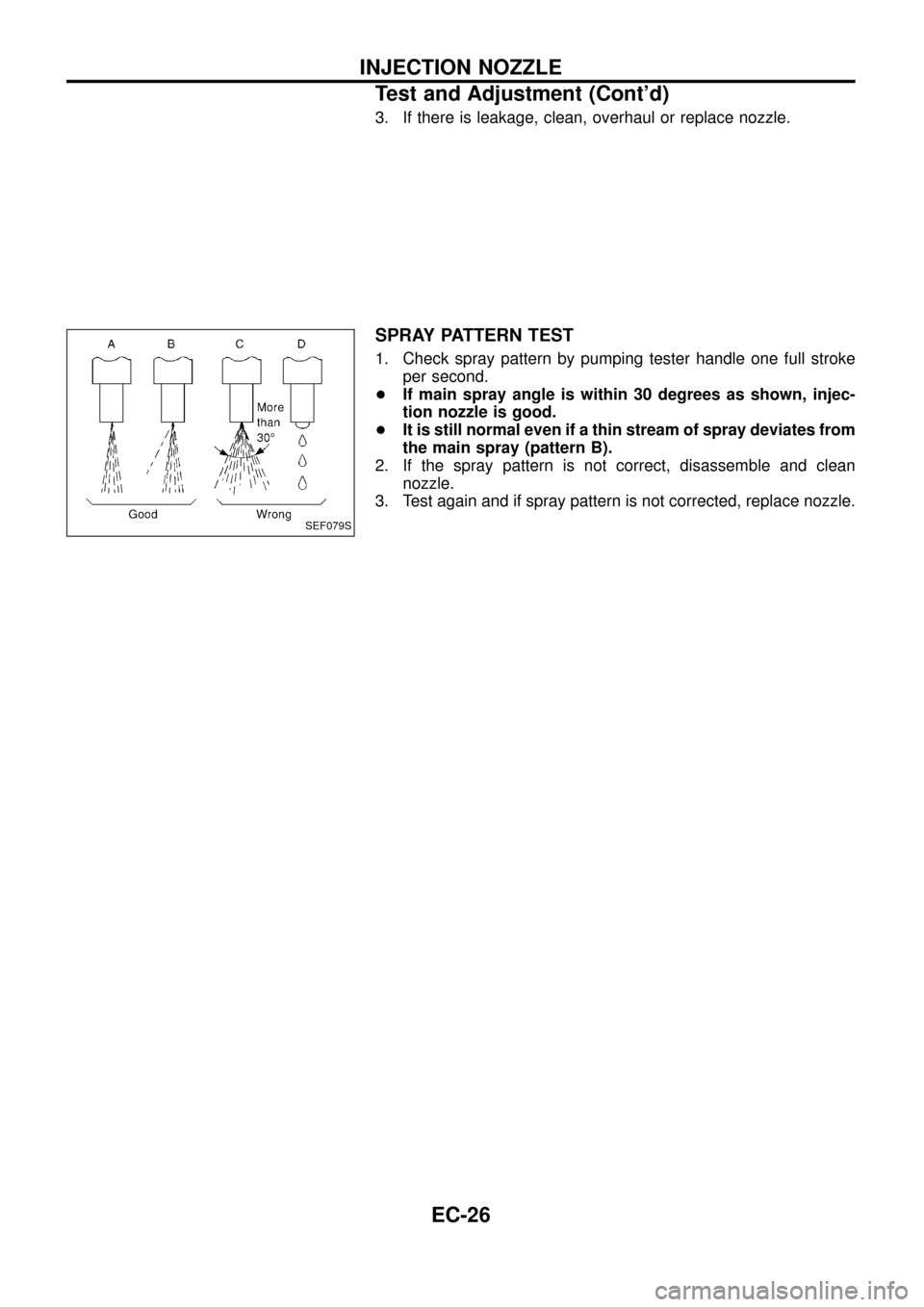
3. If there is leakage, clean, overhaul or replace nozzle.
SPRAY PATTERN TEST
1. Check spray pattern by pumping tester handle one full stroke
per second.
+If main spray angle is within 30 degrees as shown, injec-
tion nozzle is good.
+It is still normal even if a thin stream of spray deviates from
the main spray (pattern B).
2. If the spray pattern is not correct, disassemble and clean
nozzle.
3. Test again and if spray pattern is not corrected, replace nozzle.
SEF079S
INJECTION NOZZLE
Test and Adjustment (Cont'd)
EC-26
Page 29 of 192
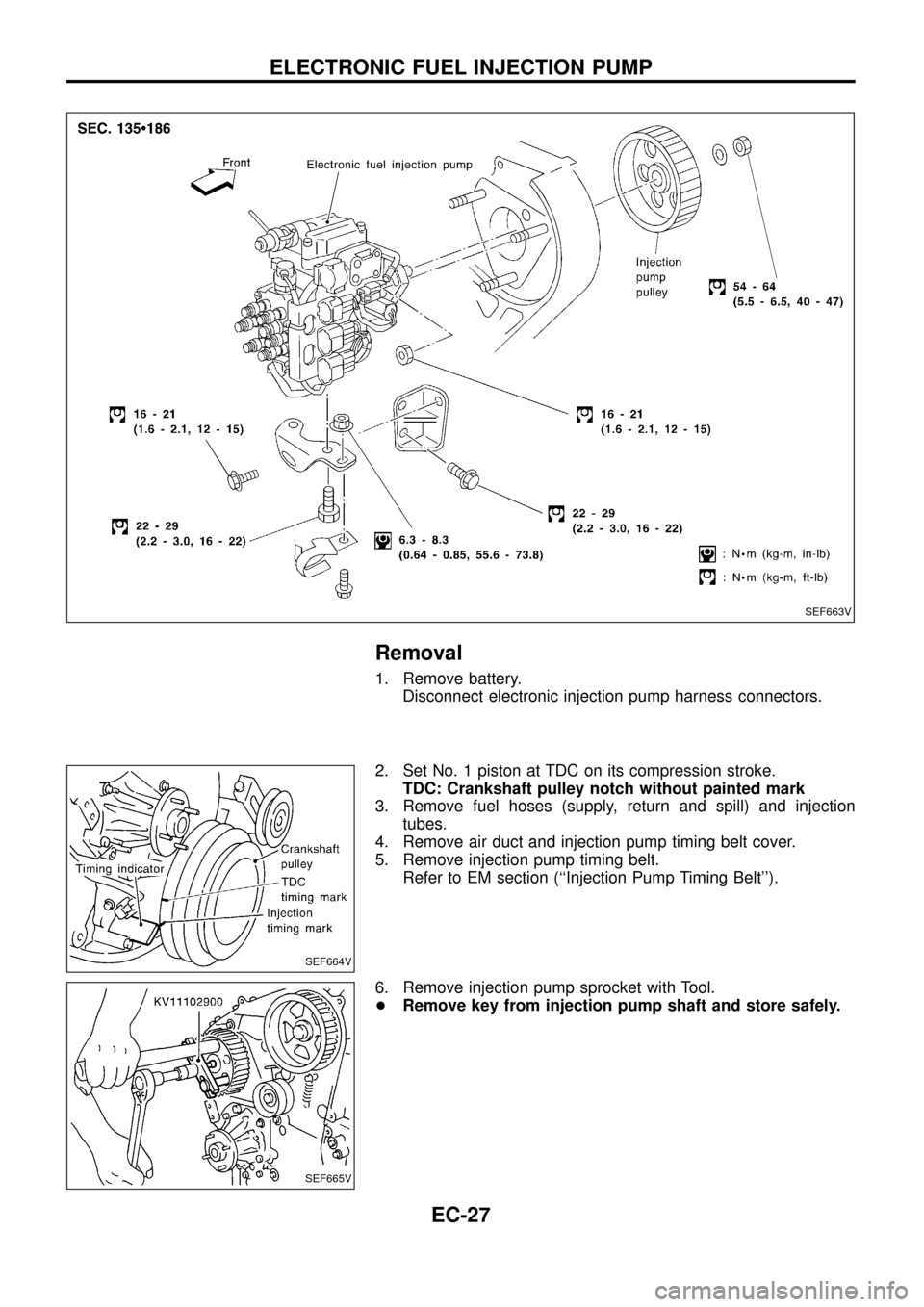
Removal
1. Remove battery.
Disconnect electronic injection pump harness connectors.
2. Set No. 1 piston at TDC on its compression stroke.
TDC: Crankshaft pulley notch without painted mark
3. Remove fuel hoses (supply, return and spill) and injection
tubes.
4. Remove air duct and injection pump timing belt cover.
5. Remove injection pump timing belt.
Refer to EM section (``Injection Pump Timing Belt'').
6. Remove injection pump sprocket with Tool.
+Remove key from injection pump shaft and store safely.
SEF663V
SEF664V
SEF665V
ELECTRONIC FUEL INJECTION PUMP
EC-27
Page 30 of 192
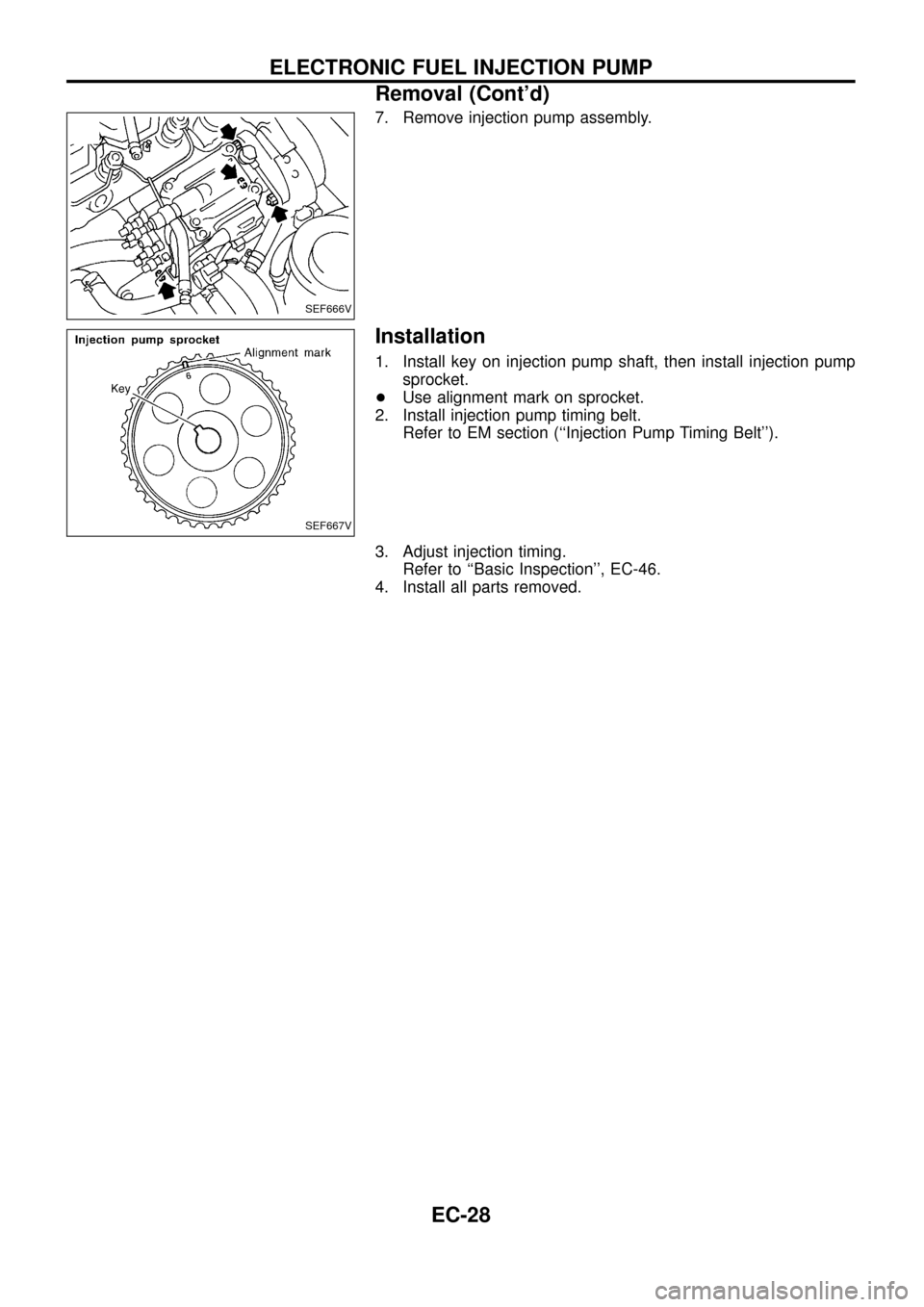
7. Remove injection pump assembly.
Installation
1. Install key on injection pump shaft, then install injection pump
sprocket.
+Use alignment mark on sprocket.
2. Install injection pump timing belt.
Refer to EM section (``Injection Pump Timing Belt'').
3. Adjust injection timing.
Refer to ``Basic Inspection'', EC-46.
4. Install all parts removed.
SEF666V
SEF667V
ELECTRONIC FUEL INJECTION PUMP
Removal (Cont'd)
EC-28