check engine OPEL FRONTERA 1998 Workshop Manual
[x] Cancel search | Manufacturer: OPEL, Model Year: 1998, Model line: FRONTERA, Model: OPEL FRONTERA 1998Pages: 6000, PDF Size: 97 MB
Page 2309 of 6000
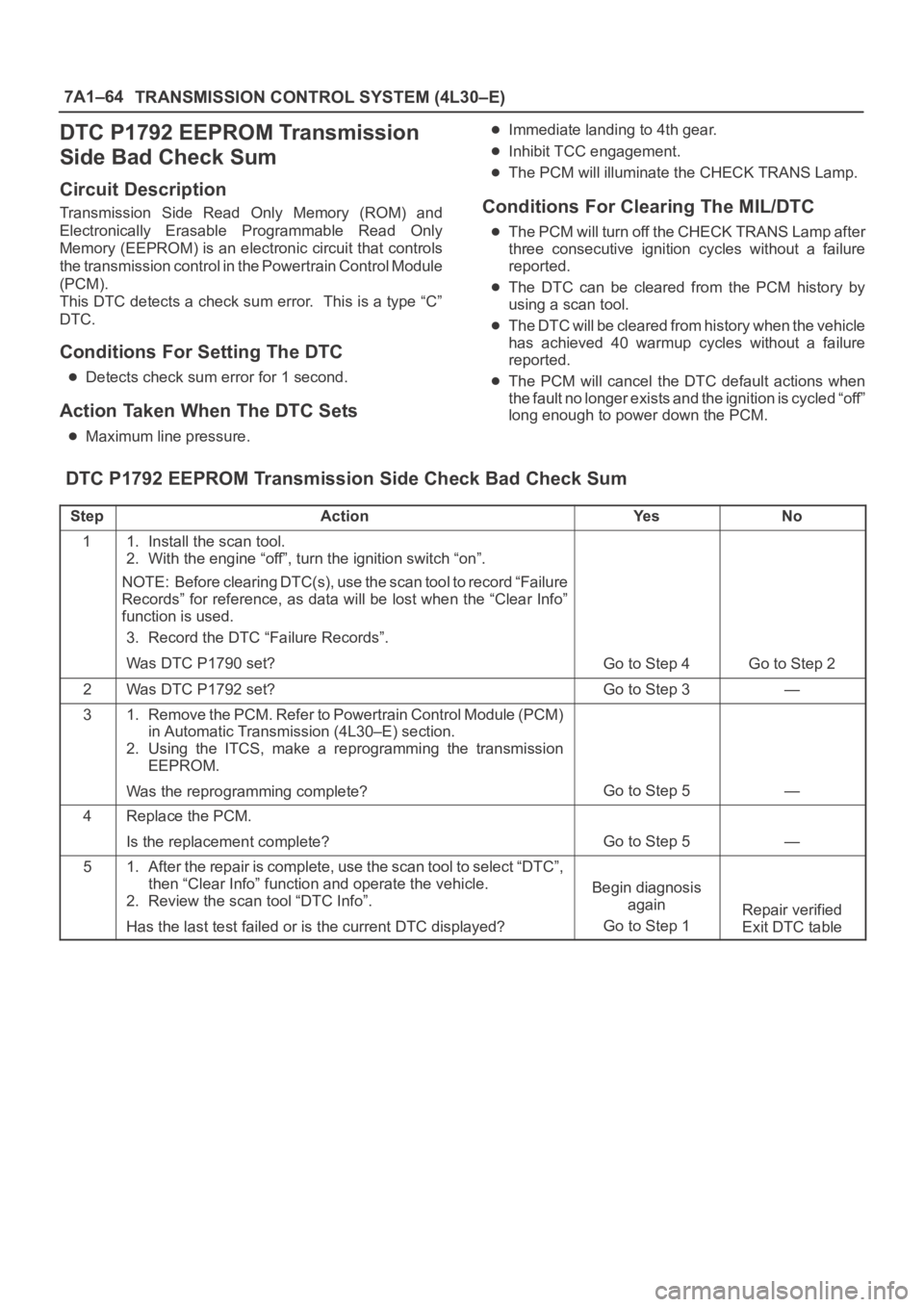
7A1–64
TRANSMISSION CONTROL SYSTEM (4L30–E)
DTC P1792 EEPROM Transmission
Side Bad Check Sum
Circuit Description
Transmission Side Read Only Memory (ROM) and
Electronically Erasable Programmable Read Only
Memory (EEPROM) is an electronic circuit that controls
the transmission control in the Powertrain Control Module
(PCM).
This DTC detects a check sum error. This is a type “C”
DTC.
Conditions For Setting The DTC
Detects check sum error for 1 second.
Action Taken When The DTC Sets
Maximum line pressure.
Immediate landing to 4th gear.
Inhibit TCC engagement.
The PCM will illuminate the CHECK TRANS Lamp.
Conditions For Clearing The MIL/DTC
The PCM will turn off the CHECK TRANS Lamp after
three consecutive ignition cycles without a failure
reported.
The DTC can be cleared from the PCM history by
using a scan tool.
The DTC will be cleared from history when the vehicle
has achieved 40 warmup cycles without a failure
reported.
The PCM will cancel the DTC default actions when
the fault no longer exists and the ignition is cycled “off”
long enough to power down the PCM.
DTC P1792 EEPROM Transmission Side Check Bad Check Sum
StepActionYe sNo
11. Install the scan tool.
2. With the engine “off”, turn the ignition switch “on”.
NOTE: Before clearing DTC(s), use the scan tool to record “Failure
Records” for reference, as data will be lost when the “Clear Info”
function is used.
3. Record the DTC “Failure Records”.
Was DTC P1790 set?
Go to Step 4Go to Step 2
2Was DTC P1792 set?Go to Step 3—
31. Remove the PCM. Refer to Powertrain Control Module (PCM)
in Automatic Transmission (4L30–E) section.
2. Using the ITCS, make a reprogramming the transmission
EEPROM.
Was the reprogramming complete?
Go to Step 5—
4Replace the PCM.
Is the replacement complete?
Go to Step 5—
51. After the repair is complete, use the scan tool to select “DTC”,
then “Clear Info” function and operate the vehicle.
2. Review the scan tool “DTC Info”.
Has the last test failed or is the current DTC displayed?
Begin diagnosis
again
Go to Step 1
Repair verified
Exit DTC table
Page 2310 of 6000

TRANSMISSION CONTROL SYSTEM (4L30–E)7A1–65
DTC P1835 Kickdown Switch Always On
D07RW033
Circuit Description
When the driver presses the accelerator pedal down
fully, the kickdown switch closes, sending a ground
signal to the Powertrain Control Module (PCM).
This information is used to perform shifts at high
engine speed.
When the kickdown switch is closed, the Throttle
Position Sensor (TPS) is already is at 100%.
This DTC detects a closed kickdown switch when TP
angle is less than 70%.
This is a type “D” DTC.
Conditions For Setting The DTC
No TPS DTCs P0122 or P0123.
TP angle is less than 70%.
Kickdown switch is “on”.
All conditions met for 1 second.
Action Taken When The DTC Sets.
Kickdown mode control is off.
The PCM will not illuminate the CHECK TRANS
Lamp.
Conditions For Clearing The DTC
The DTC can be cleared from the PCM history by
using a scan tool.
The DTC will be cleared from history when the vehicle
has achieved 40 warmup cycles without a failure
reported.
The PCM will cancel the DTC default actions when
the fault no longer exists and the ignition is cycled “off”
long enough to power down the PCM.
Diagnostic Aids
Check the wiring harness for a short to ground
between the PCM and kickdown switch.
Check the kickdown switch for failure.
Check kickdown adjustment.
Test Description
The numbers below refer to the step numbers on the
diagnostic chart:
2. This test checks for short to ground or kickdown
switch failure.
4. This test checks for regulation kickdown switch.
Page 2311 of 6000
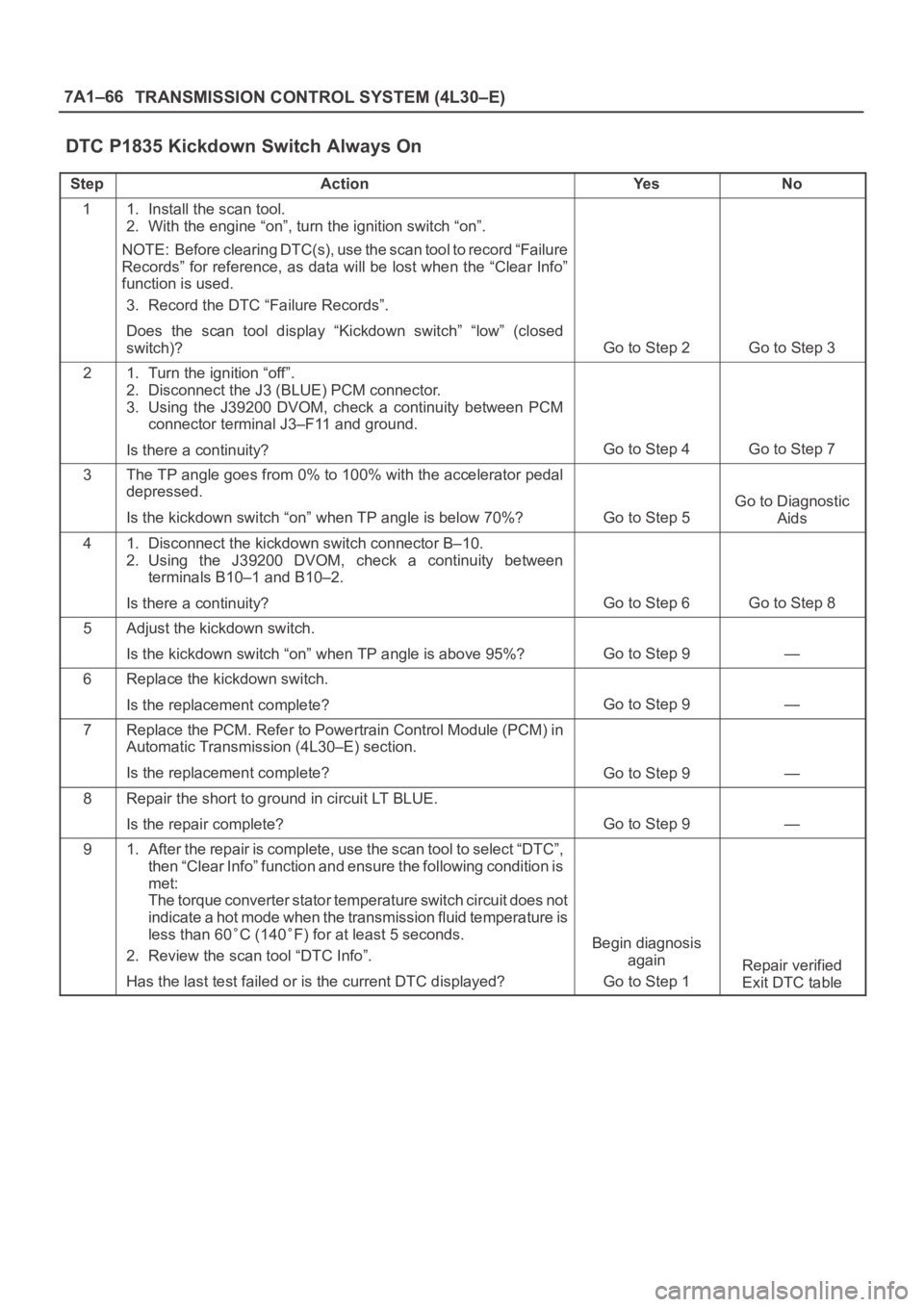
7A1–66
TRANSMISSION CONTROL SYSTEM (4L30–E)
DTC P1835 Kickdown Switch Always On
StepActionYe sNo
11. Install the scan tool.
2. With the engine “on”, turn the ignition switch “on”.
NOTE: Before clearing DTC(s), use the scan tool to record “Failure
Records” for reference, as data will be lost when the “Clear Info”
function is used.
3. Record the DTC “Failure Records”.
Does the scan tool display “Kickdown switch” “low” (closed
switch)?
Go to Step 2Go to Step 3
21. Turn the ignition “off”.
2. Disconnect the J3 (BLUE) PCM connector.
3. Using the J39200 DVOM, check a continuity between PCM
connector terminal J3–F11 and ground.
Is there a continuity?
Go to Step 4Go to Step 7
3The TP angle goes from 0% to 100% with the accelerator pedal
depressed.
Is the kickdown switch “on” when TP angle is below 70%?
Go to Step 5
Go to Diagnostic
Aids
41. Disconnect the kickdown switch connector B–10.
2. Using the J39200 DVOM, check a continuity between
terminals B10–1 and B10–2.
Is there a continuity?
Go to Step 6Go to Step 8
5Adjust the kickdown switch.
Is the kickdown switch “on” when TP angle is above 95%?
Go to Step 9—
6Replace the kickdown switch.
Is the replacement complete?
Go to Step 9—
7Replace the PCM. Refer to Powertrain Control Module (PCM) in
Automatic Transmission (4L30–E) section.
Is the replacement complete?
Go to Step 9—
8Repair the short to ground in circuit LT BLUE.
Is the repair complete?
Go to Step 9—
91. After the repair is complete, use the scan tool to select “DTC”,
then “Clear Info” function and ensure the following condition is
met:
The torque converter stator temperature switch circuit does not
indicate a hot mode when the transmission fluid temperature is
less than 60
C (140F) for at least 5 seconds.
2. Review the scan tool “DTC Info”.
Has the last test failed or is the current DTC displayed?Begin diagnosis
again
Go to Step 1
Repair verified
Exit DTC table
Page 2312 of 6000
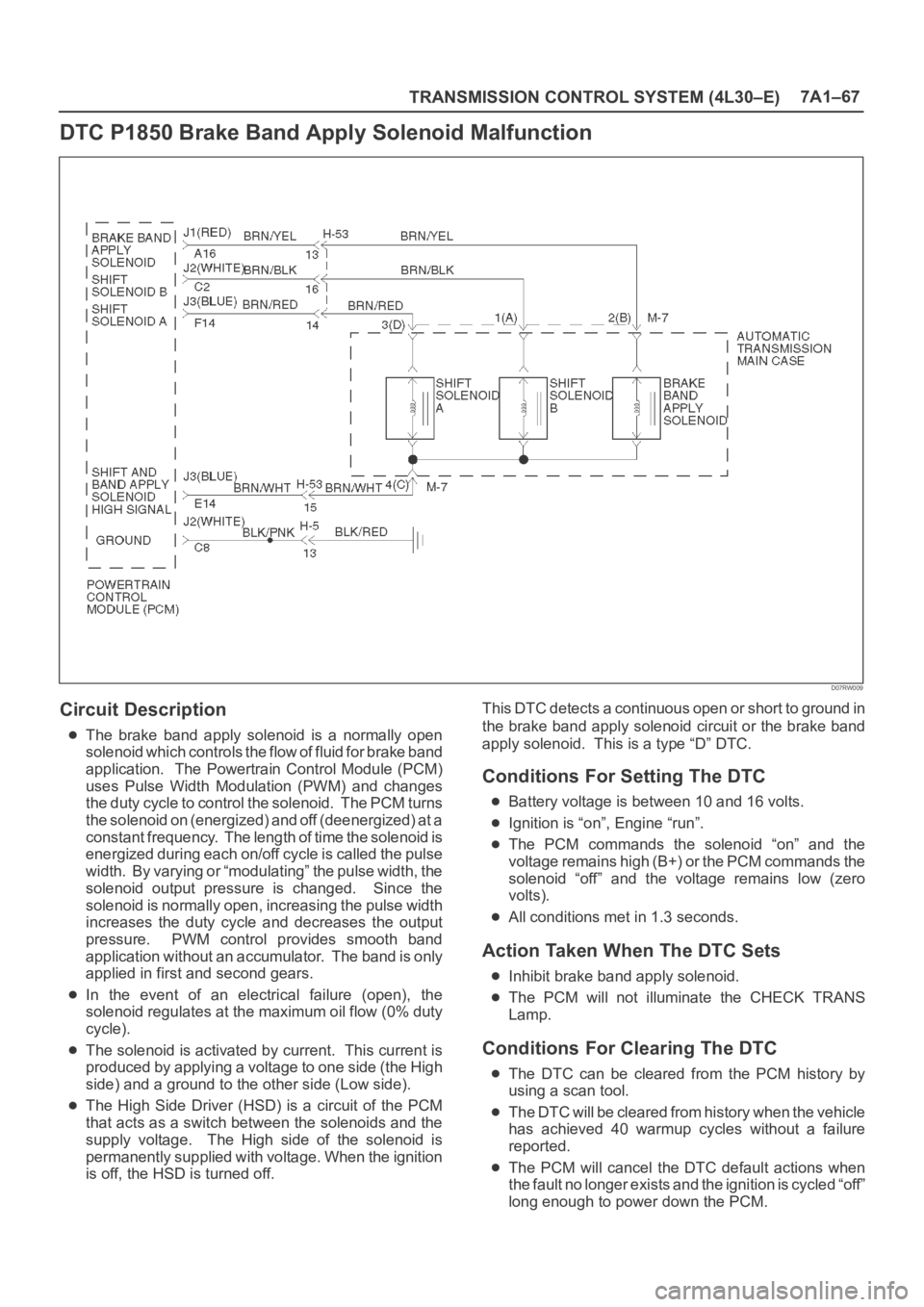
TRANSMISSION CONTROL SYSTEM (4L30–E)7A1–67
DTC P1850 Brake Band Apply Solenoid Malfunction
D07RW009
Circuit Description
The brake band apply solenoid is a normally open
solenoid which controls the flow of fluid for brake band
application. The Powertrain Control Module (PCM)
uses Pulse Width Modulation (PWM) and changes
the duty cycle to control the solenoid. The PCM turns
the solenoid on (energized) and off (deenergized) at a
constant frequency. The length of time the solenoid is
energized during each on/off cycle is called the pulse
width. By varying or “modulating” the pulse width, the
solenoid output pressure is changed. Since the
solenoid is normally open, increasing the pulse width
increases the duty cycle and decreases the output
pressure. PWM control provides smooth band
application without an accumulator. The band is only
applied in first and second gears.
In the event of an electrical failure (open), the
solenoid regulates at the maximum oil flow (0% duty
cycle).
The solenoid is activated by current. This current is
produced by applying a voltage to one side (the High
side) and a ground to the other side (Low side).
The High Side Driver (HSD) is a circuit of the PCM
that acts as a switch between the solenoids and the
supply voltage. The High side of the solenoid is
permanently supplied with voltage. When the ignition
is off, the HSD is turned off.This DTC detects a continuous open or short to ground in
the brake band apply solenoid circuit or the brake band
apply solenoid. This is a type “D” DTC.
Conditions For Setting The DTC
Battery voltage is between 10 and 16 volts.
Ignition is “on”, Engine “run”.
The PCM commands the solenoid “on” and the
voltage remains high (B+) or the PCM commands the
solenoid “off” and the voltage remains low (zero
volts).
All conditions met in 1.3 seconds.
Action Taken When The DTC Sets
Inhibit brake band apply solenoid.
The PCM will not illuminate the CHECK TRANS
Lamp.
Conditions For Clearing The DTC
The DTC can be cleared from the PCM history by
using a scan tool.
The DTC will be cleared from history when the vehicle
has achieved 40 warmup cycles without a failure
reported.
The PCM will cancel the DTC default actions when
the fault no longer exists and the ignition is cycled “off”
long enough to power down the PCM.
Page 2313 of 6000
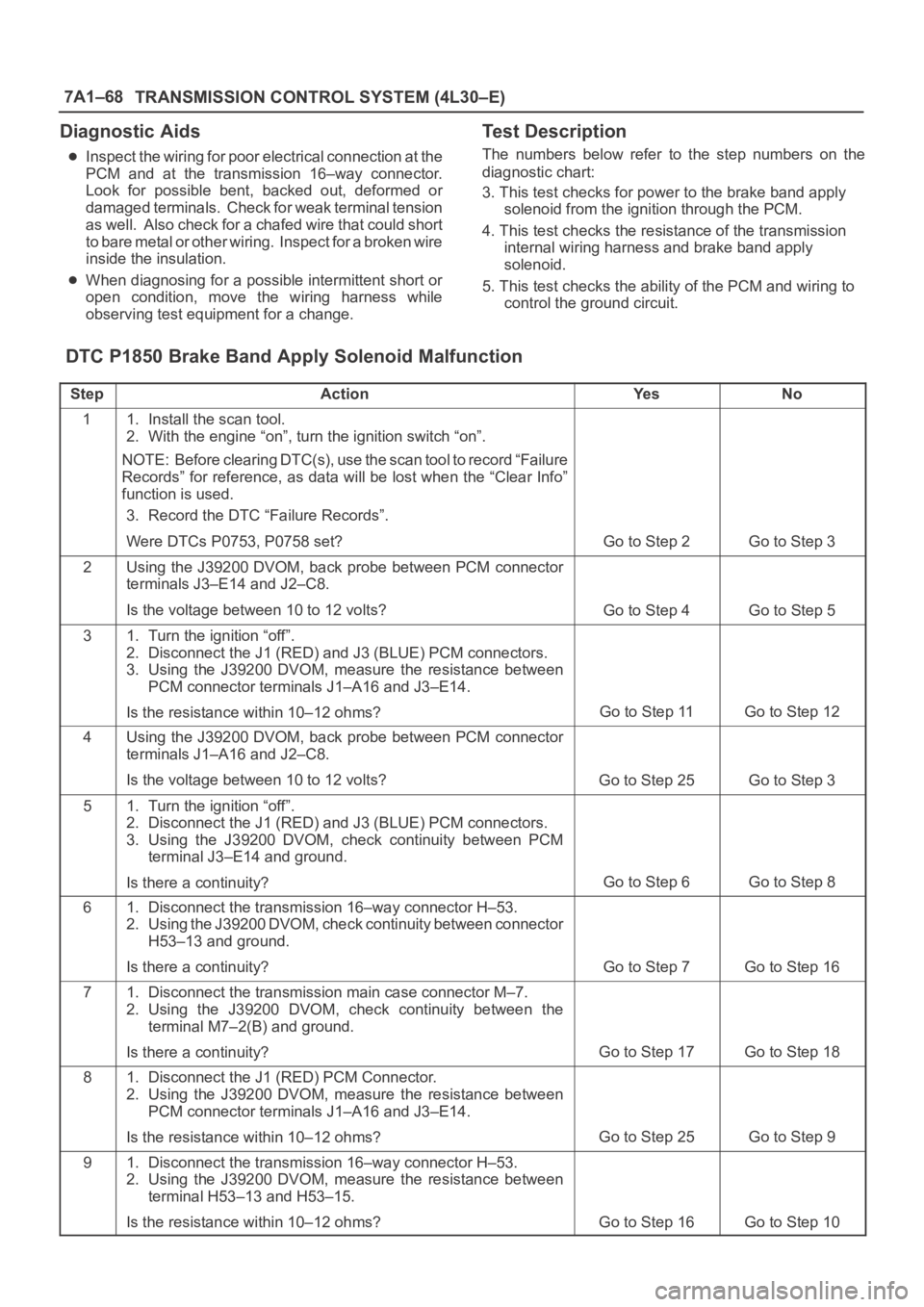
7A1–68
TRANSMISSION CONTROL SYSTEM (4L30–E)
Diagnostic Aids
Inspect the wiring for poor electrical connection at the
PCM and at the transmission 16–way connector.
Look for possible bent, backed out, deformed or
damaged terminals. Check for weak terminal tension
as well. Also check for a chafed wire that could short
to bare metal or other wiring. Inspect for a broken wire
inside the insulation.
When diagnosing for a possible intermittent short or
open condition, move the wiring harness while
observing test equipment for a change.
Test Description
The numbers below refer to the step numbers on the
diagnostic chart:
3. This test checks for power to the brake band apply
solenoid from the ignition through the PCM.
4. This test checks the resistance of the transmission
internal wiring harness and brake band apply
solenoid.
5. This test checks the ability of the PCM and wiring to
control the ground circuit.
DTC P1850 Brake Band Apply Solenoid Malfunction
StepActionYe sNo
11. Install the scan tool.
2. With the engine “on”, turn the ignition switch “on”.
NOTE: Before clearing DTC(s), use the scan tool to record “Failure
Records” for reference, as data will be lost when the “Clear Info”
function is used.
3. Record the DTC “Failure Records”.
Were DTCs P0753, P0758 set?
Go to Step 2Go to Step 3
2Using the J39200 DVOM, back probe between PCM connector
terminals J3–E14 and J2–C8.
Is the voltage between 10 to 12 volts?
Go to Step 4Go to Step 5
31. Turn the ignition “off”.
2. Disconnect the J1 (RED) and J3 (BLUE) PCM connectors.
3. Using the J39200 DVOM, measure the resistance between
PCM connector terminals J1–A16 and J3–E14.
Is the resistance within 10–12 ohms?
Go to Step 11Go to Step 12
4Using the J39200 DVOM, back probe between PCM connector
terminals J1–A16 and J2–C8.
Is the voltage between 10 to 12 volts?
Go to Step 25Go to Step 3
51. Turn the ignition “off”.
2. Disconnect the J1 (RED) and J3 (BLUE) PCM connectors.
3. Using the J39200 DVOM, check continuity between PCM
terminal J3–E14 and ground.
Is there a continuity?
Go to Step 6Go to Step 8
61. Disconnect the transmission 16–way connector H–53.
2. Using the J39200 DVOM, check continuity between connector
H53–13 and ground.
Is there a continuity?
Go to Step 7Go to Step 16
71. Disconnect the transmission main case connector M–7.
2. Using the J39200 DVOM, check continuity between the
terminal M7–2(B) and ground.
Is there a continuity?
Go to Step 17Go to Step 18
81. Disconnect the J1 (RED) PCM Connector.
2. Using the J39200 DVOM, measure the resistance between
PCM connector terminals J1–A16 and J3–E14.
Is the resistance within 10–12 ohms?
Go to Step 25Go to Step 9
91. Disconnect the transmission 16–way connector H–53.
2. Using the J39200 DVOM, measure the resistance between
terminal H53–13 and H53–15.
Is the resistance within 10–12 ohms?
Go to Step 16Go to Step 10
Page 2316 of 6000
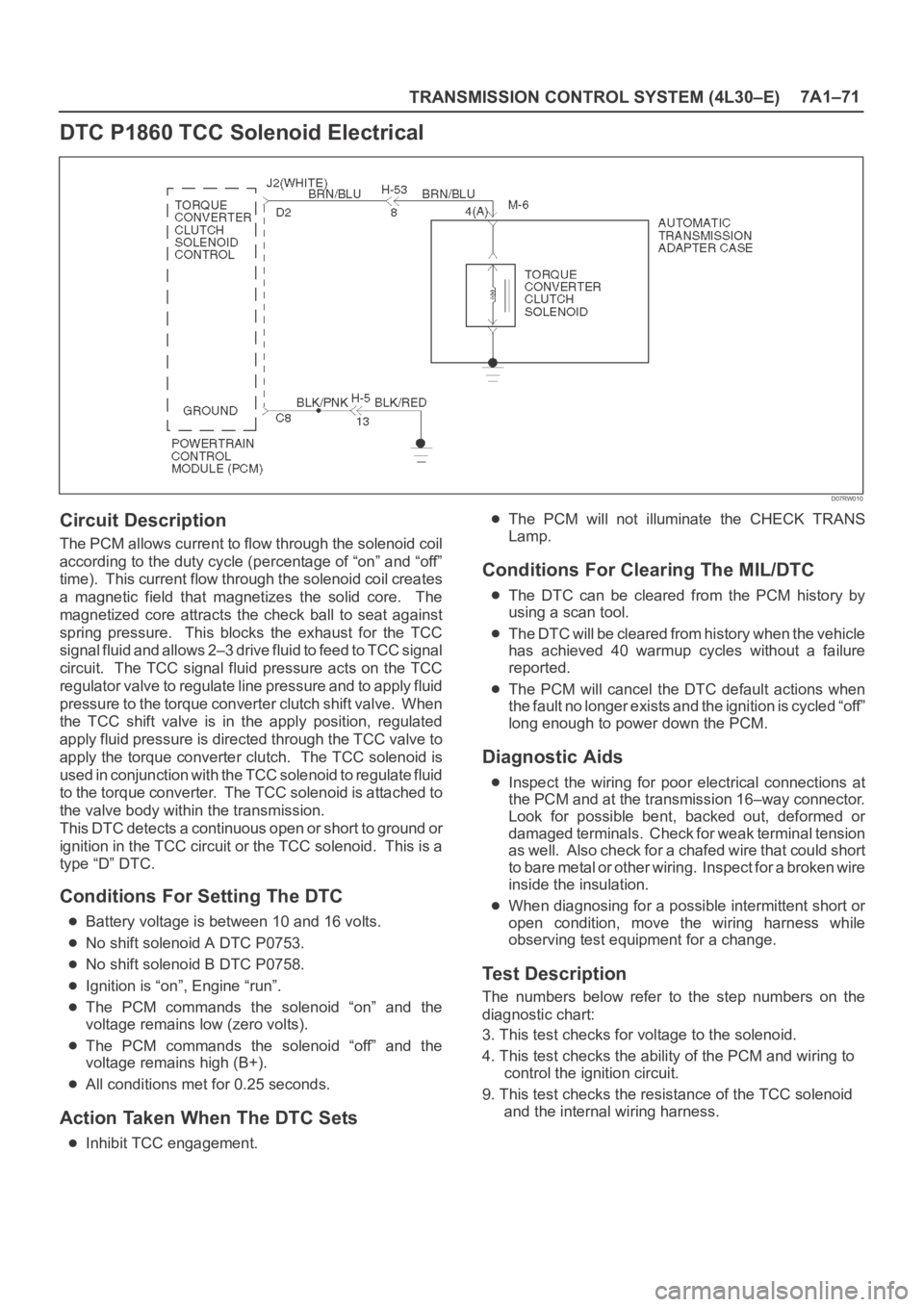
TRANSMISSION CONTROL SYSTEM (4L30–E)7A1–71
DTC P1860 TCC Solenoid Electrical
D07RW010
Circuit Description
The PCM allows current to flow through the solenoid coil
according to the duty cycle (percentage of “on” and “off”
time). This current flow through the solenoid coil creates
a magnetic field that magnetizes the solid core. The
magnetized core attracts the check ball to seat against
spring pressure. This blocks the exhaust for the TCC
signal fluid and allows 2–3 drive fluid to feed to TCC signal
circuit. The TCC signal fluid pressure acts on the TCC
regulator valve to regulate line pressure and to apply fluid
pressure to the torque converter clutch shift valve. When
the TCC shift valve is in the apply position, regulated
apply fluid pressure is directed through the TCC valve to
apply the torque converter clutch. The TCC solenoid is
used in conjunction with the TCC solenoid to regulate fluid
to the torque converter. The TCC solenoid is attached to
the valve body within the transmission.
This DTC detects a continuous open or short to ground or
ignition in the TCC circuit or the TCC solenoid. This is a
type “D” DTC.
Conditions For Setting The DTC
Battery voltage is between 10 and 16 volts.
No shift solenoid A DTC P0753.
No shift solenoid B DTC P0758.
Ignition is “on”, Engine “run”.
The PCM commands the solenoid “on” and the
voltage remains low (zero volts).
The PCM commands the solenoid “off” and the
voltage remains high (B+).
All conditions met for 0.25 seconds.
Action Taken When The DTC Sets
Inhibit TCC engagement.
The PCM will not illuminate the CHECK TRANS
Lamp.
Conditions For Clearing The MIL/DTC
The DTC can be cleared from the PCM history by
using a scan tool.
The DTC will be cleared from history when the vehicle
has achieved 40 warmup cycles without a failure
reported.
The PCM will cancel the DTC default actions when
the fault no longer exists and the ignition is cycled “off”
long enough to power down the PCM.
Diagnostic Aids
Inspect the wiring for poor electrical connections at
the PCM and at the transmission 16–way connector.
Look for possible bent, backed out, deformed or
damaged terminals. Check for weak terminal tension
as we ll. A lso ch eck fo r a ch af e d w ire th at cou l d s ho r t
to bare metal or other wiring. Inspect for a broken wire
inside the insulation.
When diagnosing for a possible intermittent short or
open condition, move the wiring harness while
observing test equipment for a change.
Test Description
The numbers below refer to the step numbers on the
diagnostic chart:
3. This test checks for voltage to the solenoid.
4. This test checks the ability of the PCM and wiring to
control the ignition circuit.
9. This test checks the resistance of the TCC solenoid
and the internal wiring harness.
Page 2317 of 6000
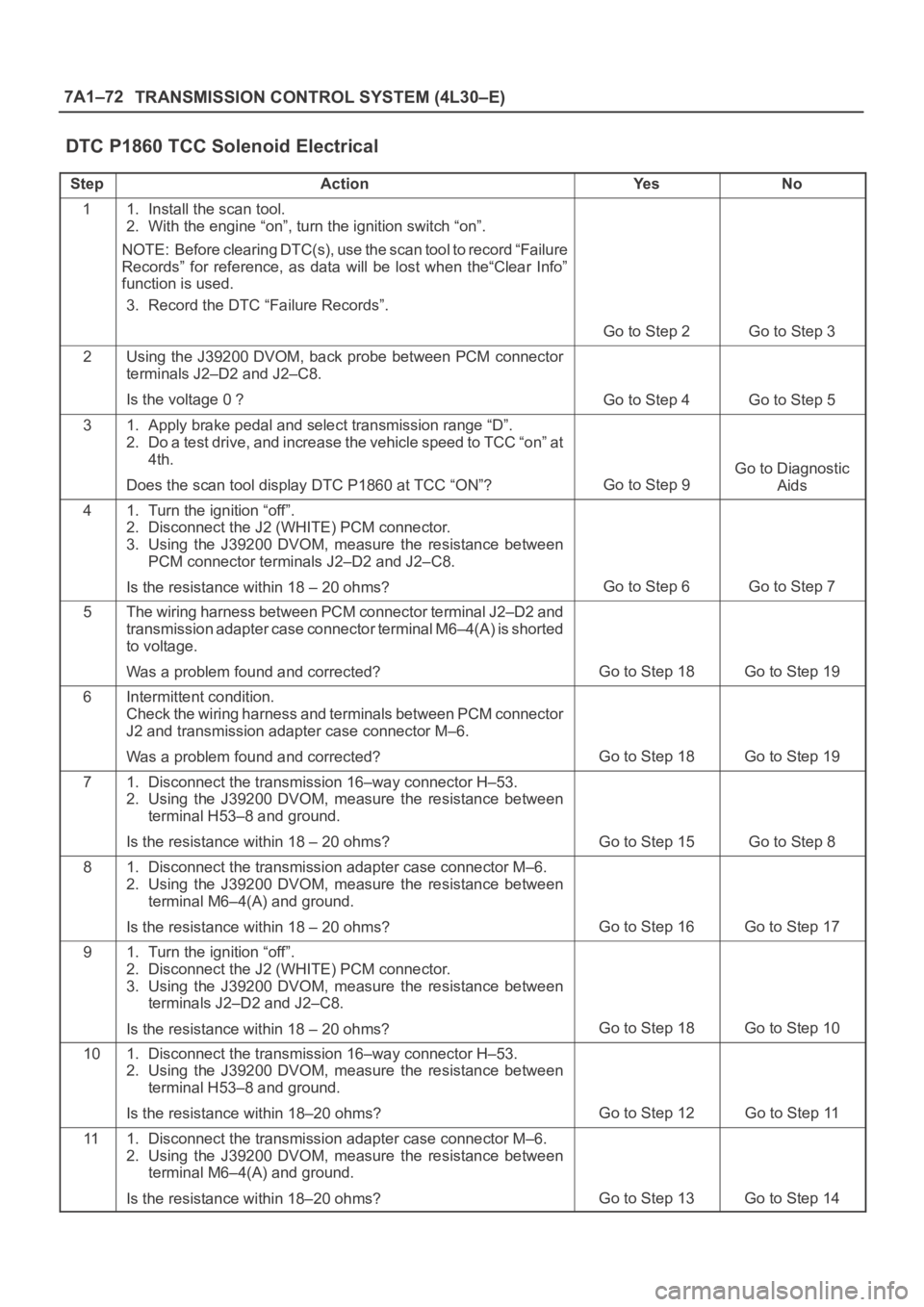
7A1–72
TRANSMISSION CONTROL SYSTEM (4L30–E)
DTC P1860 TCC Solenoid Electrical
StepActionYe sNo
11. Install the scan tool.
2. With the engine “on”, turn the ignition switch “on”.
NOTE: Before clearing DTC(s), use the scan tool to record “Failure
Records” for reference, as data will be lost when the“Clear Info”
function is used.
3. Record the DTC “Failure Records”.
Go to Step 2Go to Step 3
2Using the J39200 DVOM, back probe between PCM connector
terminals J2–D2 and J2–C8.
Is the voltage 0 ?
Go to Step 4Go to Step 5
31. Apply brake pedal and select transmission range “D”.
2. Do a test drive, and increase the vehicle speed to TCC “on” at
4th.
Does the scan tool display DTC P1860 at TCC “ON”?
Go to Step 9
Go to Diagnostic
Aids
41. Turn the ignition “off”.
2. Disconnect the J2 (WHITE) PCM connector.
3. Using the J39200 DVOM, measure the resistance between
PCM connector terminals J2–D2 and J2–C8.
Is the resistance within 18 – 20 ohms?
Go to Step 6Go to Step 7
5The wiring harness between PCM connector terminal J2–D2 and
transmission adapter case connector terminal M6–4(A) is shorted
to voltage.
Was a problem found and corrected?
Go to Step 18Go to Step 19
6Intermittent condition.
Check the wiring harness and terminals between PCM connector
J2 and transmission adapter case connector M–6.
Was a problem found and corrected?
Go to Step 18Go to Step 19
71. Disconnect the transmission 16–way connector H–53.
2. Using the J39200 DVOM, measure the resistance between
terminal H53–8 and ground.
Is the resistance within 18 – 20 ohms?
Go to Step 15Go to Step 8
81. Disconnect the transmission adapter case connector M–6.
2. Using the J39200 DVOM, measure the resistance between
terminal M6–4(A) and ground.
Is the resistance within 18 – 20 ohms?
Go to Step 16Go to Step 17
91. Turn the ignition “off”.
2. Disconnect the J2 (WHITE) PCM connector.
3. Using the J39200 DVOM, measure the resistance between
terminals J2–D2 and J2–C8.
Is the resistance within 18 – 20 ohms?
Go to Step 18Go to Step 10
101. Disconnect the transmission 16–way connector H–53.
2. Using the J39200 DVOM, measure the resistance between
terminal H53–8 and ground.
Is the resistance within 18–20 ohms?
Go to Step 12Go to Step 11
111. Disconnect the transmission adapter case connector M–6.
2. Using the J39200 DVOM, measure the resistance between
terminal M6–4(A) and ground.
Is the resistance within 18–20 ohms?
Go to Step 13Go to Step 14
Page 2331 of 6000
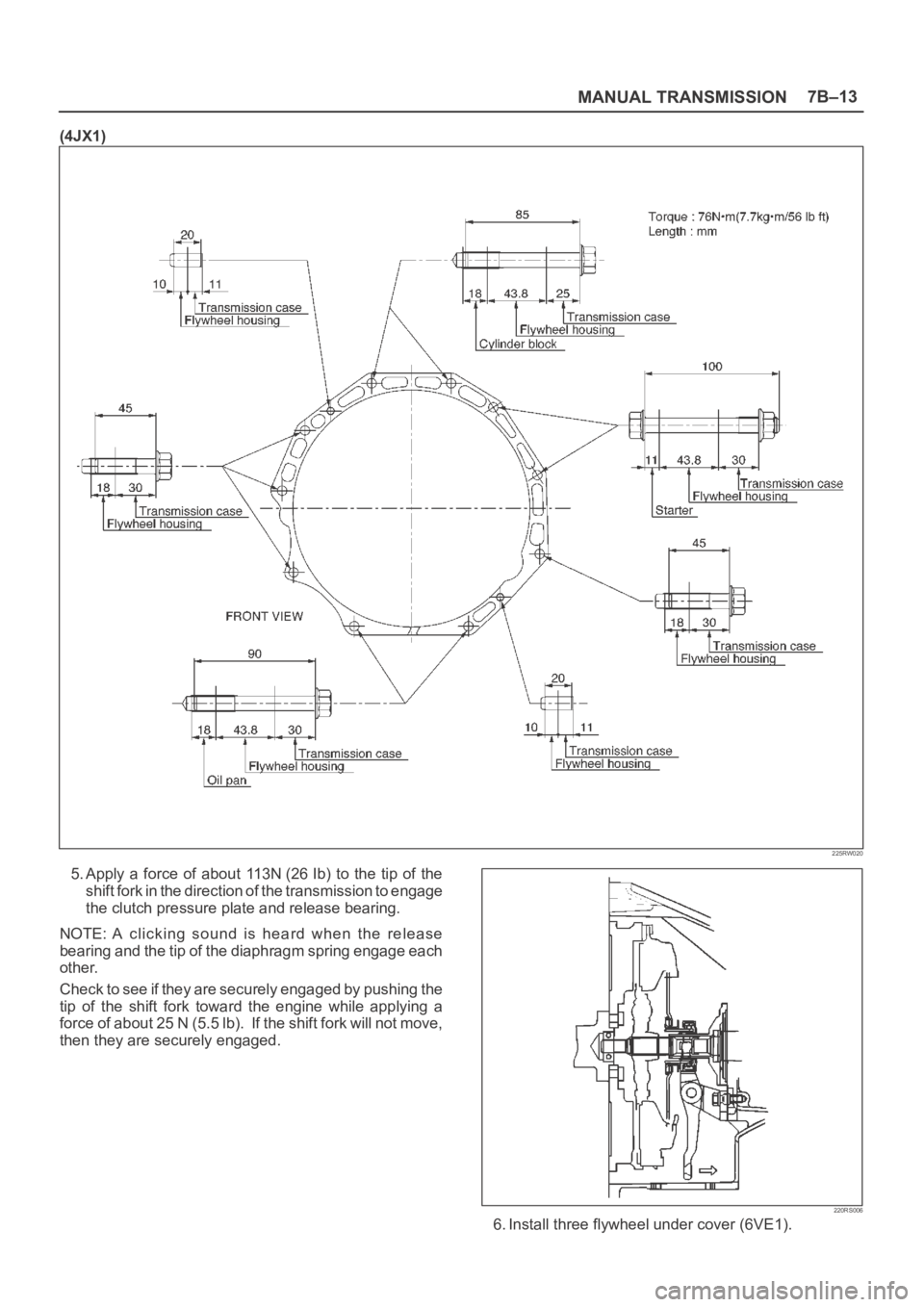
MANUAL TRANSMISSION7B–13
(4JX1)
225RW020
5. Apply a force of about 113N (26 Ib) to the tip of the
shift fork in the direction of the transmission to engage
the clutch pressure plate and release bearing.
NOTE: A clicking sound is heard when the release
bearing and the tip of the diaphragm spring engage each
other.
Check to see if they are securely engaged by pushing the
tip of the shift fork toward the engine while applying a
force of about 25 N (5.5 lb). If the shift fork will not move,
then they are securely engaged.
220RS006
6. Install three flywheel under cover (6VE1).
Page 2360 of 6000
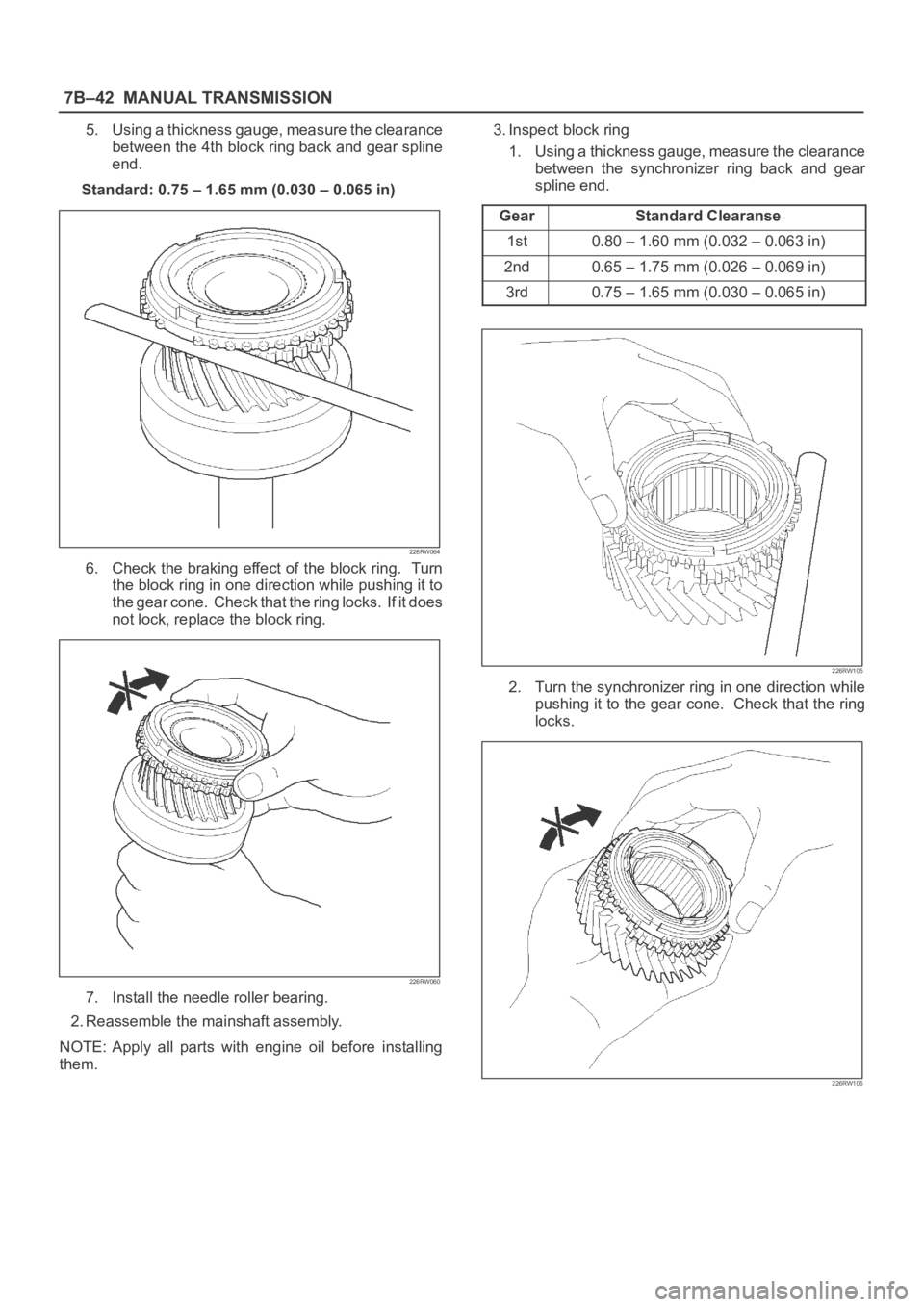
7B–42MANUAL TRANSMISSION
5. Using a thickness gauge, measure the clearance
between the 4th block ring back and gear spline
end.
Standard: 0.75 – 1.65 mm (0.030 – 0.065 in)
226RW064
6. Check the braking effect of the block ring. Turn
the block ring in one direction while pushing it to
the gear cone. Check that the ring locks. If it does
not lock, replace the block ring.
226RW060
7. Install the needle roller bearing.
2. Reassemble the mainshaft assembly.
NOTE: Apply all parts with engine oil before installing
them.3. Inspect block ring
1. Using a thickness gauge, measure the clearance
between the synchronizer ring back and gear
spline end.
Gear
Standard Clearanse
1st0.80–1.60mm (0.032–0.063in)
2nd0.65–1.75mm (0.026–0.069in)
3rd0.75–1.65mm (0.030–0.065in)
226RW105
2. Turn the synchronizer ring in one direction while
pushing it to the gear cone. Check that the ring
locks.
226RW106
Page 2517 of 6000
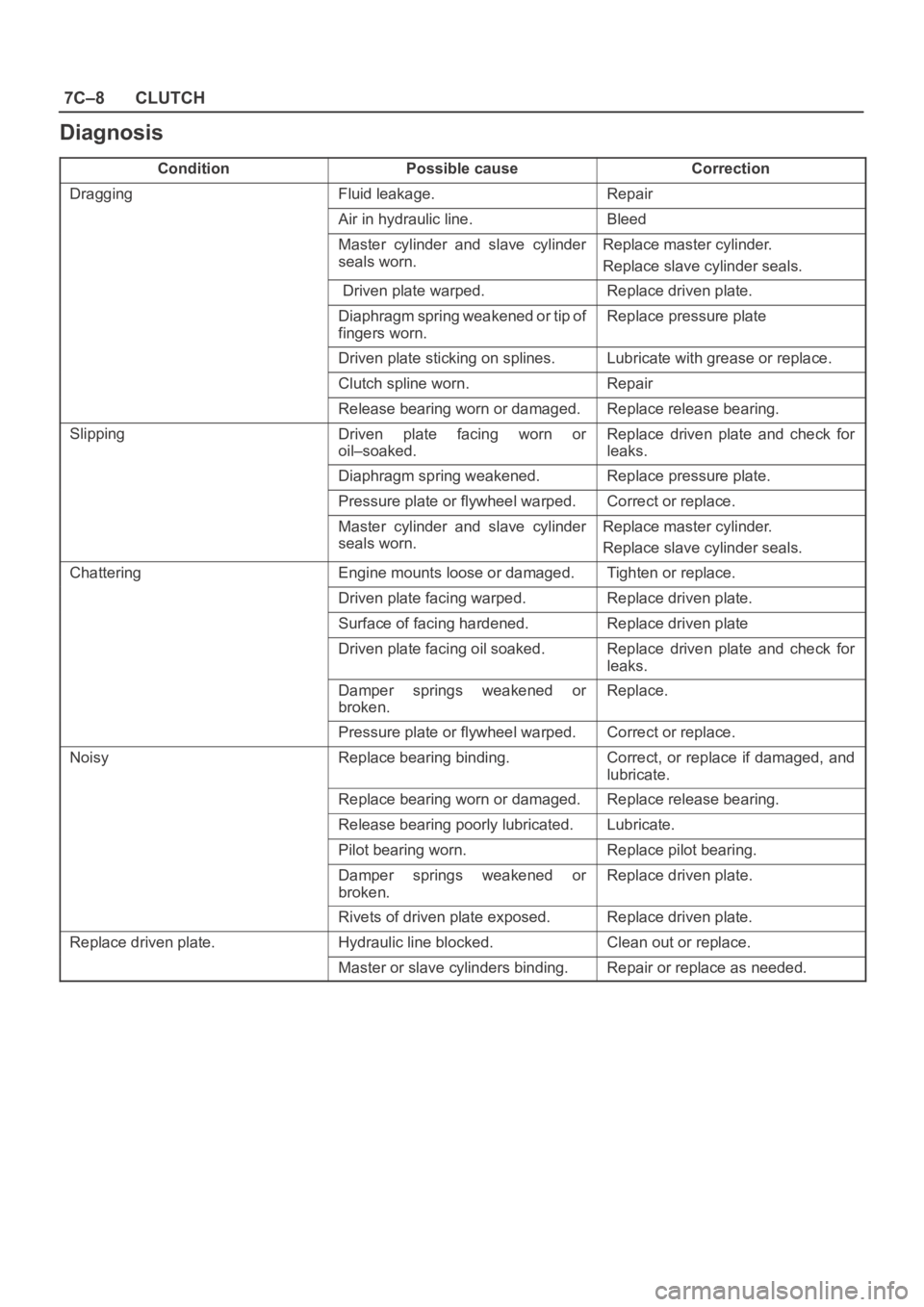
7C–8CLUTCH
Diagnosis
ConditionPossible causeCorrection
DraggingFluid leakage.Repair
Air in hydraulic line.Bleed
Master cylinder and slave cylinder
seals worn. Replace master cylinder.
Replace slave cylinder seals.
Driven plate warped.Replace driven plate.
Diaphragm spring weakened or tip of
fingers worn. Replace pressure plate
Driven plate sticking on splines.Lubricate with grease or replace.
Clutch spline worn. Repair
Release bearing worn or damaged.Replace release bearing.
SlippingDriven plate facing worn or
oil–soaked.Replace driven plate and check for
leaks.
Diaphragm spring weakened.Replace pressure plate.
Pressure plate or flywheel warped.Correct or replace.
Master cylinder and slave cylinder
seals worn.Replace master cylinder.
Replace slave cylinder seals.
ChatteringEngine mounts loose or damaged.Tighten or replace.
Driven plate facing warped.Replace driven plate.
Surface of facing hardened.Replace driven plate
Driven plate facing oil soaked. Replace driven plate and check for
leaks.
Damper springs weakened or
broken. Replace.
Pressure plate or flywheel warped.Correct or replace.
NoisyReplace bearing binding.Correct, or replace if damaged, and
lubricate.
Replace bearing worn or damaged. Replace release bearing.
Release bearing poorly lubricated. Lubricate.
Pilot bearing worn.Replace pilot bearing.
Damper springs weakened or
broken.Replace driven plate.
Rivets of driven plate exposed.Replace driven plate.
Replace driven plate.Hydraulic line blocked.Clean out or replace.
Master or slave cylinders binding.Repair or replace as needed.