ESP OPEL GT-R 1973 User Guide
[x] Cancel search | Manufacturer: OPEL, Model Year: 1973, Model line: GT-R, Model: OPEL GT-R 1973Pages: 625, PDF Size: 17.22 MB
Page 189 of 625
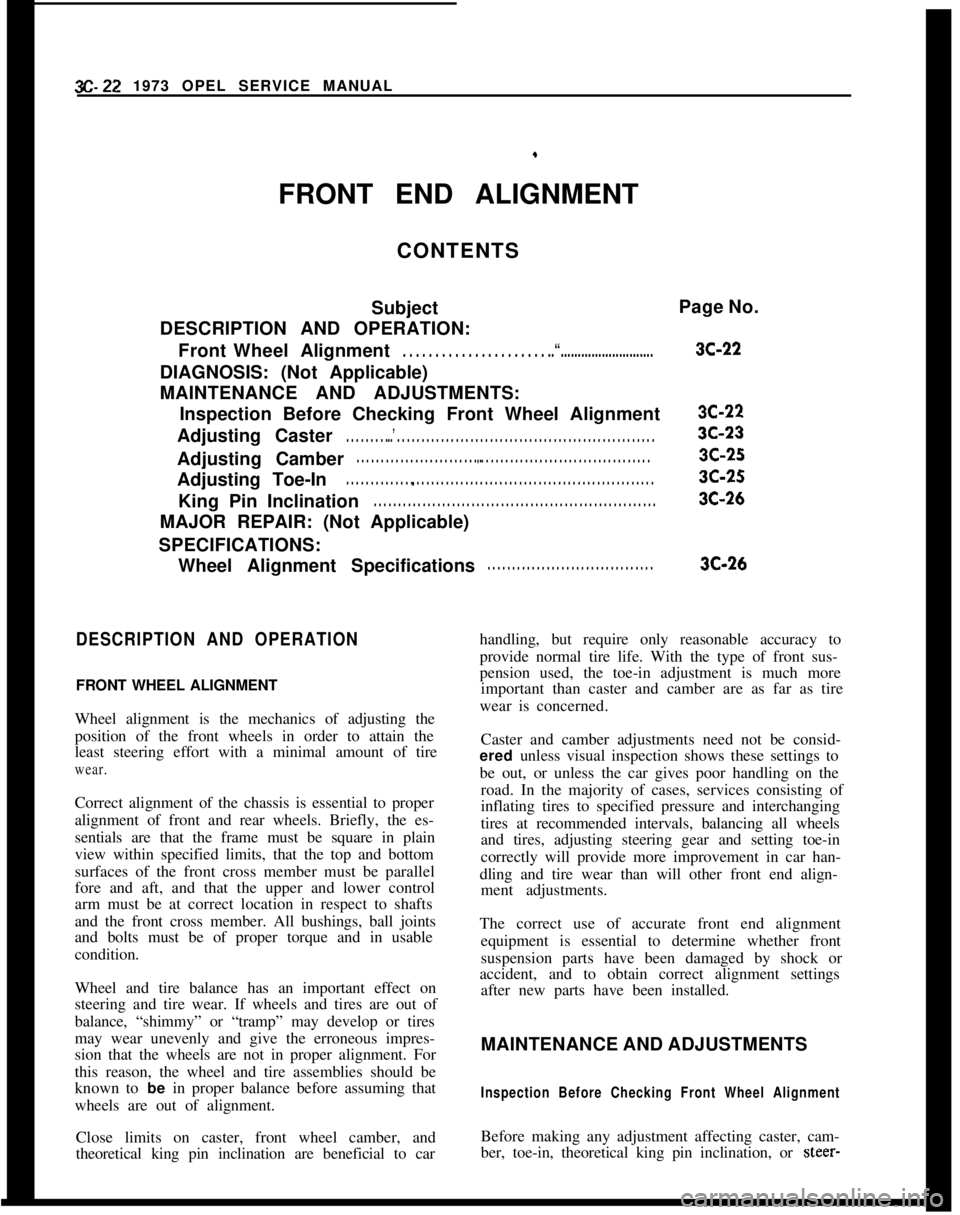
3C-22 1973 OPEL SERVICE MANUAL.
FRONT END ALIGNMENT
CONTENTS
SubjectPage No.
DESCRIPTION AND OPERATION:
FrontWheelAlignment
. . . . . . . . . . . . . . . . . . . . . . ..“...........................DIAGNOSIS: (Not Applicable)
MAINTENANCE AND ADJUSTMENTS:
Inspection Before Checking Front Wheel Alignment
AdjustingCaster
. . . . . . . . ...’ . . . . . . . . . . . . . . . . . . . . . . . . . . . . . . . . . . . . . . . . . . . . . . . . . . . . .Adjusting Camber
. . . . . . . . . . . . . . . . . . . . . . . . . . * . . . . . . . . . . . . . . . . . . . . . . . . . . . . . . . . . . .Adjusting Toe-In
. . . . . . . . . . . . . . * . . . . . . . . . . . . . . . . . . . . . . . . . . . . . . . . . . . . . . . . . . . . . . . . .King Pin Inclination
. . . . . . . . . . . . . . . . . . . . . . . . . . . . . . . . . . . . . . . . . . . . . . . . . . . . . . . . . .MAJOR REPAIR: (Not Applicable)
SPECIFICATIONS:3C-223C-223C-233C-253C-253C-26
Wheel Alignment Specifications
. . . . . . . . . . . . . . . . . . . . . . . . . . . . . . . . . .3C-26
DESCRIPTION AND OPERATIONFRONT WHEEL ALIGNMENT
Wheel alignment is the mechanics of adjusting the
position of the front wheels in order to attain the
least steering effort with a minimal amount of tire
wear.handling, but require only reasonable accuracy to
provide normal tire life. With the type of front sus-
pension used, the toe-in adjustment is much more
important than caster and camber are as far as tire
wear is concerned.
Correct alignment of the chassis is essential to proper
alignment of front and rear wheels. Briefly, the es-
sentials are that the frame must be square in plain
view within specified limits, that the top and bottom
surfaces of the front cross member must be parallel
fore and aft, and that the upper and lower control
arm must be at correct location in respect to shafts
and the front cross member. All bushings, ball joints
and bolts must be of proper torque and in usable
condition.Caster and camber adjustments need not be consid-
ered unless visual inspection shows these settings to
be out, or unless the car gives poor handling on the
road. In the majority of cases, services consisting of
inflating tires to specified pressure and interchanging
tires at recommended intervals, balancing all wheels
and tires, adjusting steering gear and setting toe-in
correctly will provide more improvement in car han-
dling and tire wear than will other front end align-
ment adjustments.
Wheel and tire balance has an important effect on
steering and tire wear. If wheels and tires are out of
balance, “shimmy” or “tramp” may develop or tires
may wear unevenly and give the erroneous impres-
sion that the wheels are not in proper alignment. For
this reason, the wheel and tire assemblies should be
known to be in proper balance before assuming that
wheels are out of alignment.The correct use of accurate front end alignment
equipment is essential to determine whether front
suspension parts have been damaged by shock or
accident, and to obtain correct alignment settings
after new parts have been installed.
MAINTENANCE AND ADJUSTMENTS
Inspection Before Checking Front Wheel AlignmentClose limits on caster, front wheel camber, andBefore making any adjustment affecting caster, cam-
theoretical king pin inclination are beneficial to carber, toe-in, theoretical king pin inclination, or
steer-
Page 193 of 625
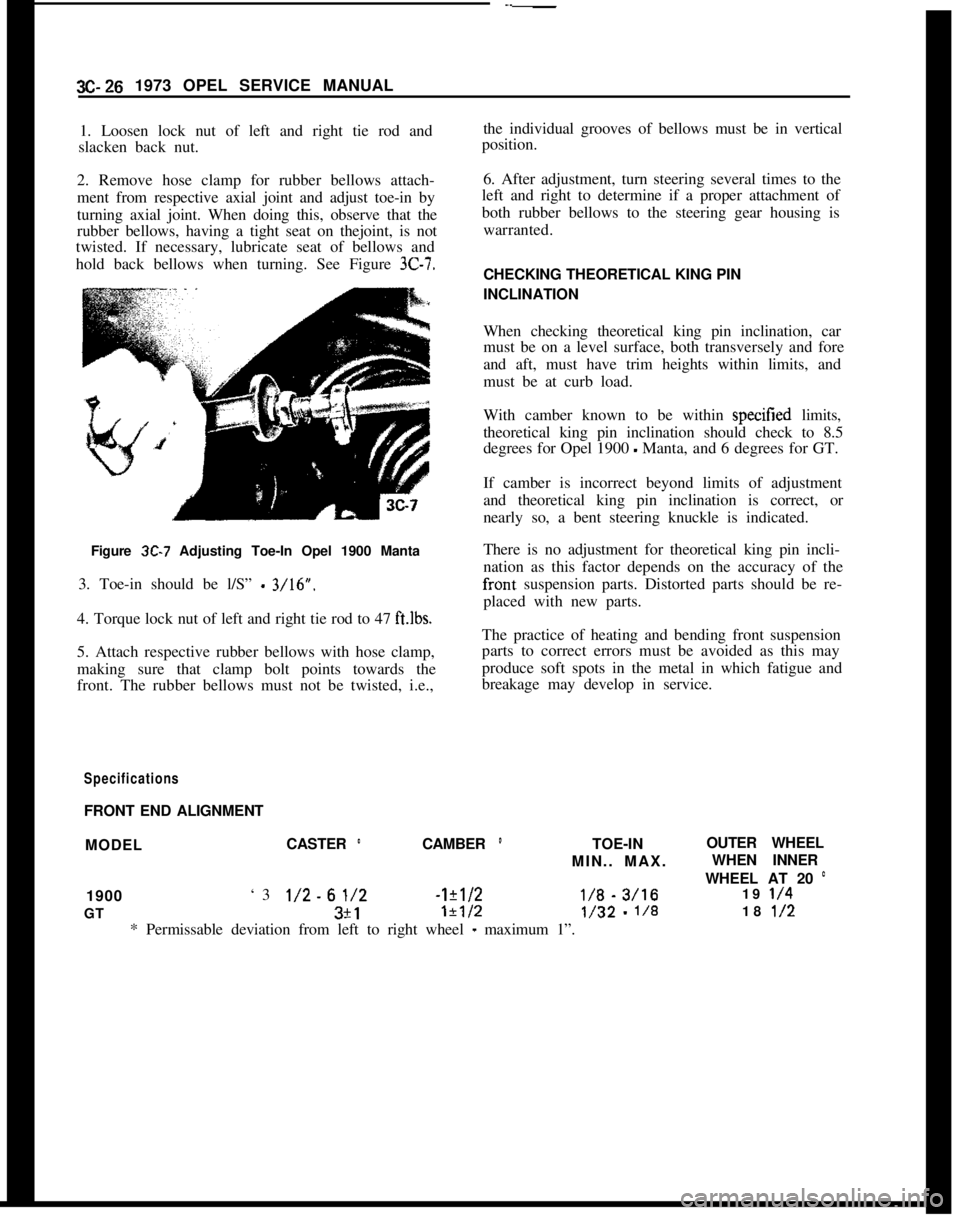
3C-26 1973 OPEL SERVICE MANUAL
1. Loosen lock nut of left and right tie rod and
slacken back nut.
2. Remove hose clamp for rubber bellows attach-
ment from respective axial joint and adjust toe-in by
turning axial joint. When doing this, observe that the
rubber bellows, having a tight seat on thejoint, is not
twisted. If necessary, lubricate seat of bellows and
hold back bellows when turning. See Figure 3C-7.Figure
3C-7 Adjusting Toe-In Opel 1900 Manta
3. Toe-in should be l/S”
- 3/16”.
4. Torque lock nut of left and right tie rod to 47
ft.lbs.5. Attach respective rubber bellows with hose clamp,
making sure that clamp bolt points towards the
front. The rubber bellows must not be twisted, i.e.,
SpecificationsFRONT END ALIGNMENTthe individual grooves of bellows must be in vertical
position.
6. After adjustment, turn steering several times to the
left and right to determine if a proper attachment of
both rubber bellows to the steering gear housing is
warranted.
CHECKING THEORETICAL KING PIN
INCLINATION
When checking theoretical king pin inclination, car
must be on a level surface, both transversely and fore
and aft, must have trim heights within limits, and
must be at curb load.
With camber known to be within specitied limits,
theoretical king pin inclination should check to 8.5
degrees for Opel 1900
- Manta, and 6 degrees for GT.
If camber is incorrect beyond limits of adjustment
and theoretical king pin inclination is correct, or
nearly so, a bent steering knuckle is indicated.
There is no adjustment for theoretical king pin incli-
nation as this factor depends on the accuracy of the
fronts suspension parts. Distorted parts should be re-
placed with new parts.
The practice of heating and bending front suspension
parts to correct errors must be avoided as this may
produce soft spots in the metal in which fatigue and
breakage may develop in service.
MODELCASTER
’CAMBER ’TOE-INOUTER WHEEL
MIN.. MAX.WHEN INNER
WHEEL AT 20
’1900‘3
l/2-61/2-1?1/2I/% - 3/1619 l/4GT3+1
1+1/2l/32 - l/818 l/2* Permissable deviation from left to right wheel
- maximum 1”.
Page 198 of 625
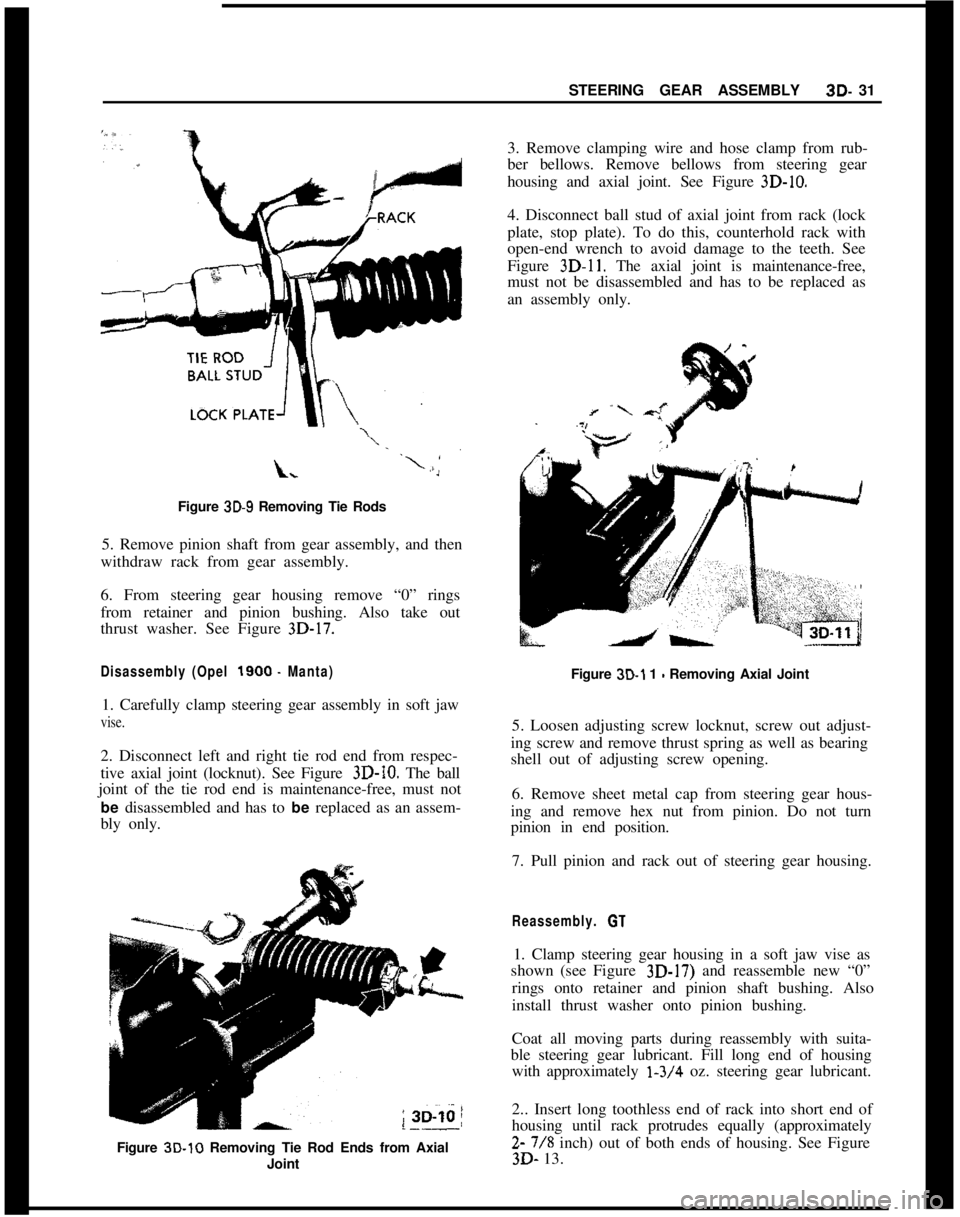
STEERING GEAR ASSEMBLY3D- 31
Figure 3D-9 Removing Tie Rods
5. Remove pinion shaft from gear assembly, and then
withdraw rack from gear assembly.
6. From steering gear housing remove “0” rings
from retainer and pinion bushing. Also take out
thrust washer. See Figure
3D-17.
Disassembly (Opel
1900. Manta)1. Carefully clamp steering gear assembly in soft jaw
vise.2. Disconnect left and right tie rod end from respec-
tive axial joint (locknut). See Figure
3D-10. The ball
joint of the tie rod end is maintenance-free, must not
be disassembled and has to be replaced as an assem-
bly only.
Figure 3D-10 Removing Tie Rod Ends from Axial
Joint3. Remove clamping wire and hose clamp from rub-
ber bellows. Remove bellows from steering gear
housing and axial joint. See Figure
3D-10.4. Disconnect ball stud of axial joint from rack (lock
plate, stop plate). To do this, counterhold rack with
open-end wrench to avoid damage to the teeth. See
Figure
3D-11. The axial joint is maintenance-free,
must not be disassembled and has to be replaced as
an assembly only.
Figure
3D-1 1 - Removing Axial Joint
5. Loosen adjusting screw locknut, screw out adjust-
ing screw and remove thrust spring as well as bearing
shell out of adjusting screw opening.
6. Remove sheet metal cap from steering gear hous-
ing and remove hex nut from pinion. Do not turn
pinion in end position.
7. Pull pinion and rack out of steering gear housing.
Reassembly. GT1. Clamp steering gear housing in a soft jaw vise as
shown (see Figure 3D-17) and reassemble new “0”
rings onto retainer and pinion shaft bushing. Also
install thrust washer onto pinion bushing.
Coat all moving parts during reassembly with suita-
ble steering gear lubricant. Fill long end of housing
with approximately
l-3/4 oz. steering gear lubricant.
2.. Insert long toothless end of rack into short end of
housing until rack protrudes equally (approximately
Z- 7/S inch) out of both ends of housing. See Figure3D- 13.
Page 203 of 625
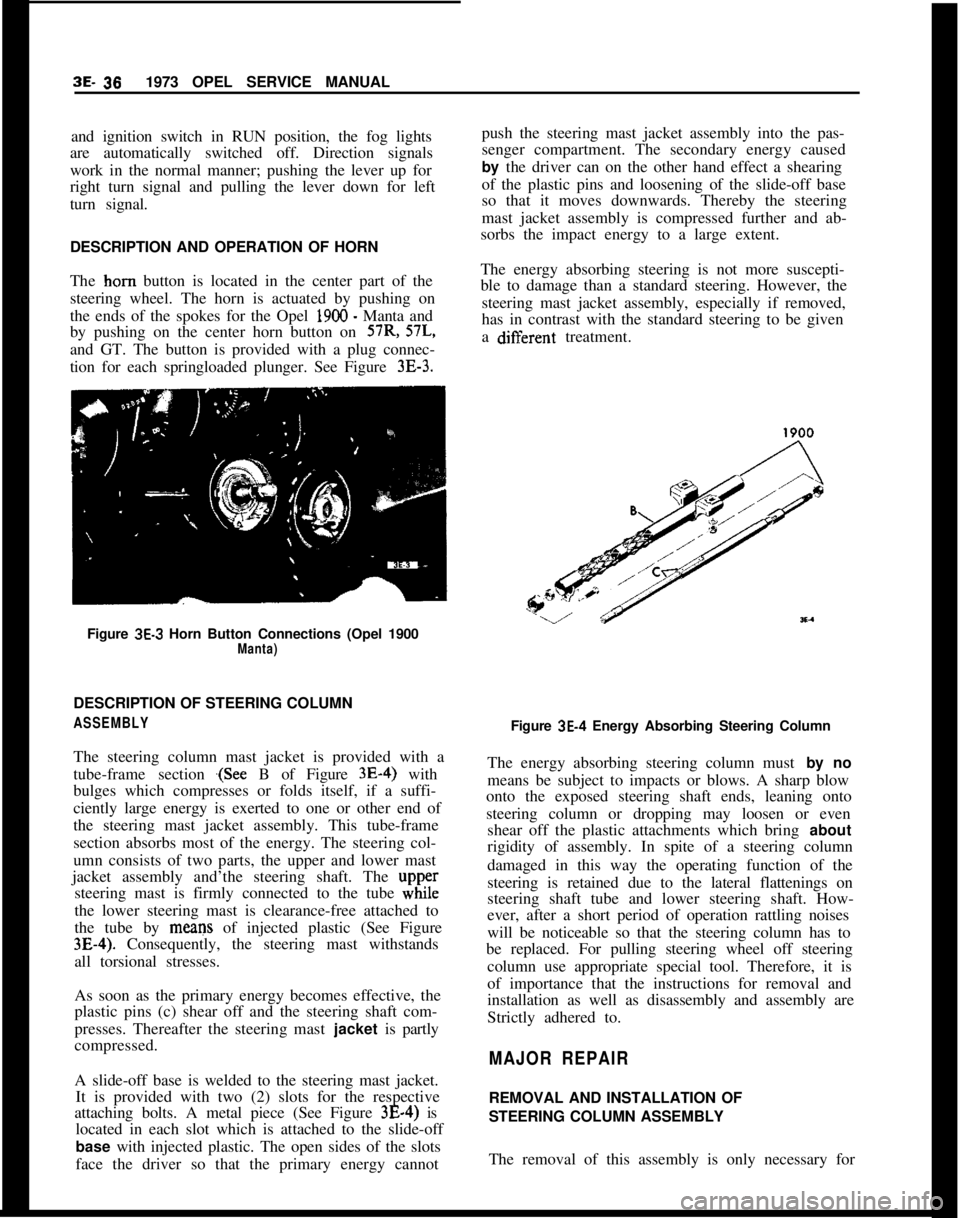
3E- 361973 OPEL SERVICE MANUAL
and ignition switch in RUN position, the fog lights
are automatically switched off. Direction signals
work in the normal manner; pushing the lever up for
right turn signal and pulling the lever down for left
turn signal.
DESCRIPTION AND OPERATION OF HORN
The horn button is located in the center part of the
steering wheel. The horn is actuated by pushing on
the ends of the spokes for the Opel 1900 - Manta and
by pushing on the center horn button on 57R, 57L,
and GT. The button is provided with a plug connec-
tion for each springloaded plunger. See Figure
3E-3.Figure
3E-3 Horn Button Connections (Opel 1900Manta)DESCRIPTION OF STEERING COLUMN
ASSEMBLYThe steering column mast jacket is provided with a
tube-frame section
.(See B of Figure 3E-4) with
bulges which compresses or folds itself, if a suffi-
ciently large energy is exerted to one or other end of
the steering mast jacket assembly. This tube-frame
section absorbs most of the energy. The steering col-
umn consists of two parts, the upper and lower mast
jacket assembly and’the steering shaft. The
upp,ersteering mast is firmly connected to the tube while
the lower steering mast is clearance-free attached to
the tube by means of injected plastic (See Figure
3E-4). Consequently, the steering mast withstands
all torsional stresses.
As soon as the primary energy becomes effective, the
plastic pins (c) shear off and the steering shaft com-
presses. Thereafter the steering mast jacket is partly
compressed.
A slide-off base is welded to the steering mast jacket.
It is provided with two (2) slots for the respective
attaching bolts. A metal piece (See Figure 3E-4) is
located in each slot which is attached to the slide-off
base with injected plastic. The open sides of the slots
face the driver so that the primary energy cannotpush the steering mast jacket assembly into the pas-
senger compartment. The secondary energy caused
by the driver can on the other hand effect a shearing
of the plastic pins and loosening of the slide-off base
so that it moves downwards. Thereby the steering
mast jacket assembly is compressed further and ab-
sorbs the impact energy to a large extent.
The energy absorbing steering is not more suscepti-
ble to damage than a standard steering. However, the
steering mast jacket assembly, especially if removed,
has in contrast with the standard steering to be given
a difierent treatment.
Figure
3E-4 Energy Absorbing Steering Column
The energy absorbing steering column must by no
means be subject to impacts or blows. A sharp blow
onto the exposed steering shaft ends, leaning onto
steering column or dropping may loosen or even
shear off the plastic attachments which bring about
rigidity of assembly. In spite of a steering column
damaged in this way the operating function of the
steering is retained due to the lateral flattenings on
steering shaft tube and lower steering shaft. How-
ever, after a short period of operation rattling noises
will be noticeable so that the steering column has to
be replaced. For pulling steering wheel off steering
column use appropriate special tool. Therefore, it is
of importance that the instructions for removal and
installation as well as disassembly and assembly are
Strictly adhered to.
MAJOR REPAIRREMOVAL AND INSTALLATION OF
STEERING COLUMN ASSEMBLY
The removal of this assembly is only necessary for
Page 211 of 625
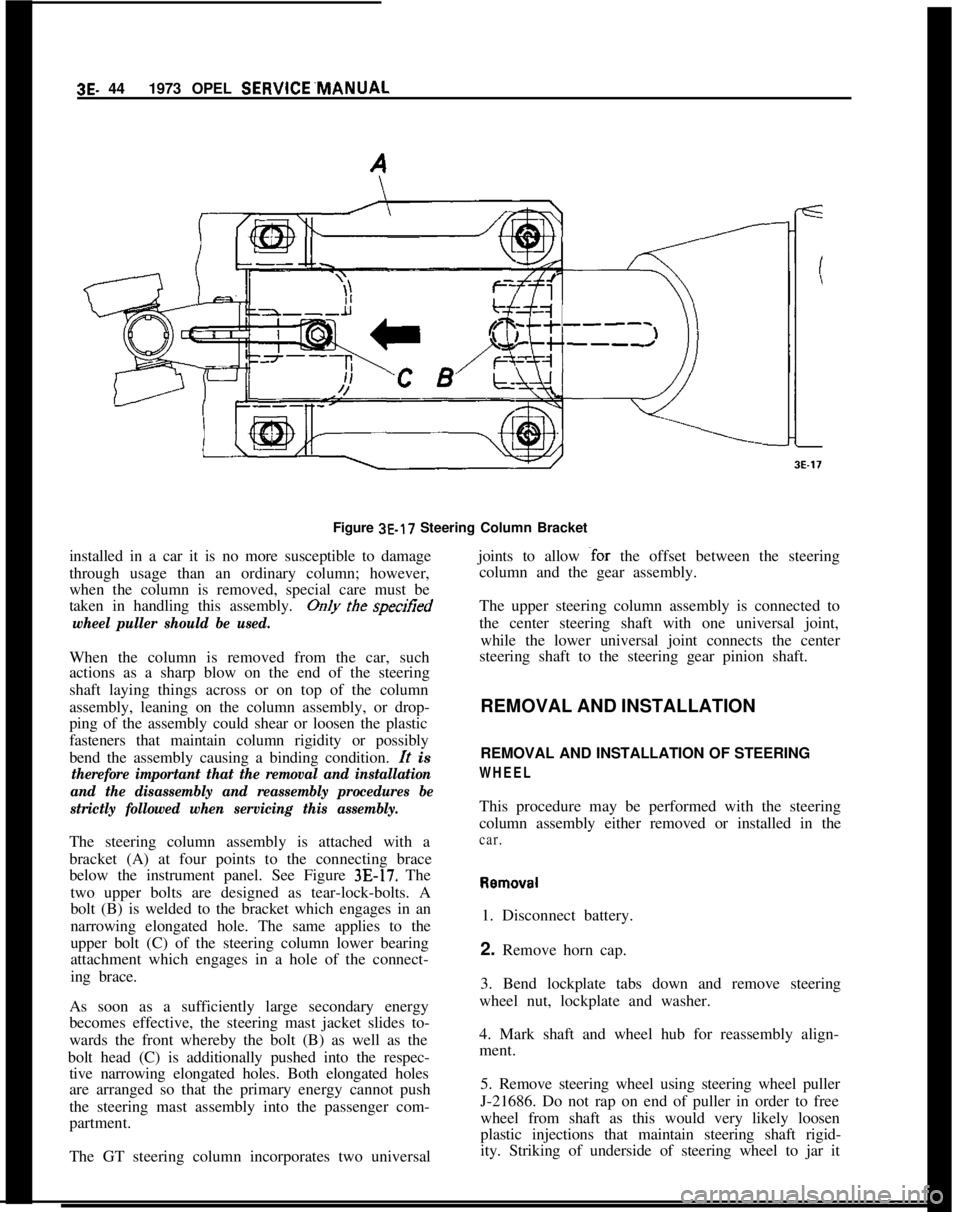
3E. 441973 OPEL SERVICE’MANUAL
Figure 3E-17 Steering Column Bracket
installed in a car it is no more susceptible to damage
through usage than an ordinary column; however,
when the column is removed, special care must be
taken in handling this assembly.Only the speufied
wheel puller should be used.When the column is removed from the car, such
actions as a sharp blow on the end of the steering
shaft laying things across or on top of the column
assembly, leaning on the column assembly, or drop-
ping of the assembly could shear or loosen the plastic
fasteners that maintain column rigidity or possibly
bend the assembly causing a binding condition.
It is
therefore important that the removal and installation
and the disassembly and reassembly procedures be
strictly followed when servicing this assembly.The steering column assembly is attached with a
bracket (A) at four points to the connecting brace
below the instrument panel. See Figure
3E-17. The
two upper bolts are designed as tear-lock-bolts. A
bolt (B) is welded to the bracket which engages in an
narrowing elongated hole. The same applies to the
upper bolt (C) of the steering column lower bearing
attachment which engages in a hole of the connect-
ing brace.
As soon as a sufficiently large secondary energy
becomes effective, the steering mast jacket slides to-
wards the front whereby the bolt (B) as well as the
bolt head (C) is additionally pushed into the respec-
tive narrowing elongated holes. Both elongated holes
are arranged so that the primary energy cannot push
the steering mast assembly into the passenger com-
partment.
The GT steering column incorporates two universaljoints to allow
~for the offset between the steering
column and the gear assembly.
The upper steering column assembly is connected to
the center steering shaft with one universal joint,
while the lower universal joint connects the center
steering shaft to the steering gear pinion shaft.
REMOVAL AND INSTALLATION
REMOVAL AND INSTALLATION OF STEERING
WHEELThis procedure may be performed with the steering
column assembly either removed or installed in the
car.Removal
1. Disconnect battery.
2. Remove horn cap.
3. Bend lockplate tabs down and remove steering
wheel nut, lockplate and washer.
4. Mark shaft and wheel hub for reassembly align-
ment.
5. Remove steering wheel using steering wheel puller
J-21686. Do not rap on end of puller in order to free
wheel from shaft as this would very likely loosen
plastic injections that maintain steering shaft rigid-
ity. Striking of underside of steering wheel to jar it
Page 219 of 625
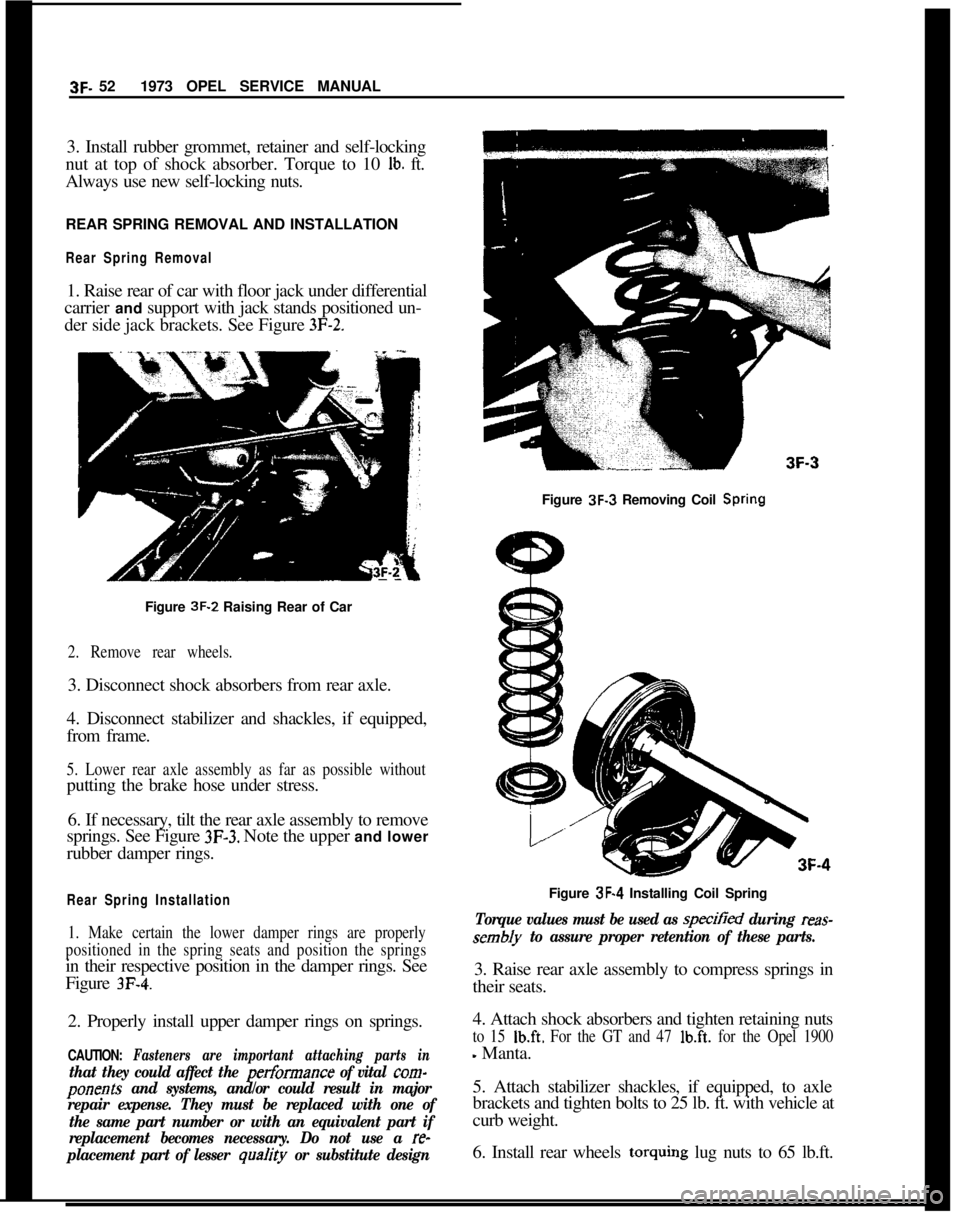
3F. 521973 OPEL SERVICE MANUAL
3. Install rubber grommet, retainer and self-locking
nut at top of shock absorber. Torque to 10 lb. ft.
Always use new self-locking nuts.
REAR SPRING REMOVAL AND INSTALLATION
Rear Spring Removal1. Raise rear of car with floor jack under differential
carrier and support with jack stands positioned un-
der side jack brackets. See Figure
3F-2.Figure 3F-3 Removing Coil
SpringFigure 3F-2 Raising Rear of Car
2. Remove rear wheels.3. Disconnect shock absorbers from rear axle.
4. Disconnect stabilizer and shackles, if equipped,
from frame.
5. Lower rear axle assembly as far as possible withoutputting the brake hose under stress.
6. If necessary, tilt the rear axle assembly to remove
springs. See Figure
3F-3. Note the upper and lower
rubber damper rings.
Rear Spring Installation
1. Make certain the lower damper rings are properly
positioned in the spring seats and position the springsin their respective position in the damper rings. See
Figure
3F-4.2. Properly install upper damper rings on springs.
CAUTION: Fasteners are important attaching parts in
that they could affect the performance of vital corn-
ponents and systems, and/or could result in major
repair expense. They must be replaced with one of
the same part number or with an equivalent part if
replacement becomes necessary. Do not use a
re-
placement part of lesser
qua/ity or substitute designFigure 3F-4 Installing Coil Spring
Torque values must be used as specitied during reas-
sembly to assure proper retention of these parts.3. Raise rear axle assembly to compress springs in
their seats.
4. Attach shock absorbers and tighten retaining nuts
to 15 Ib.ft. For the GT and 47 lb.ft. for the Opel 1900
- Manta.
5. Attach stabilizer shackles, if equipped, to axle
brackets and tighten bolts to 25 lb. ft. with vehicle at
curb weight.
6. Install rear wheels torquing lug nuts to 65 lb.ft.
Page 227 of 625
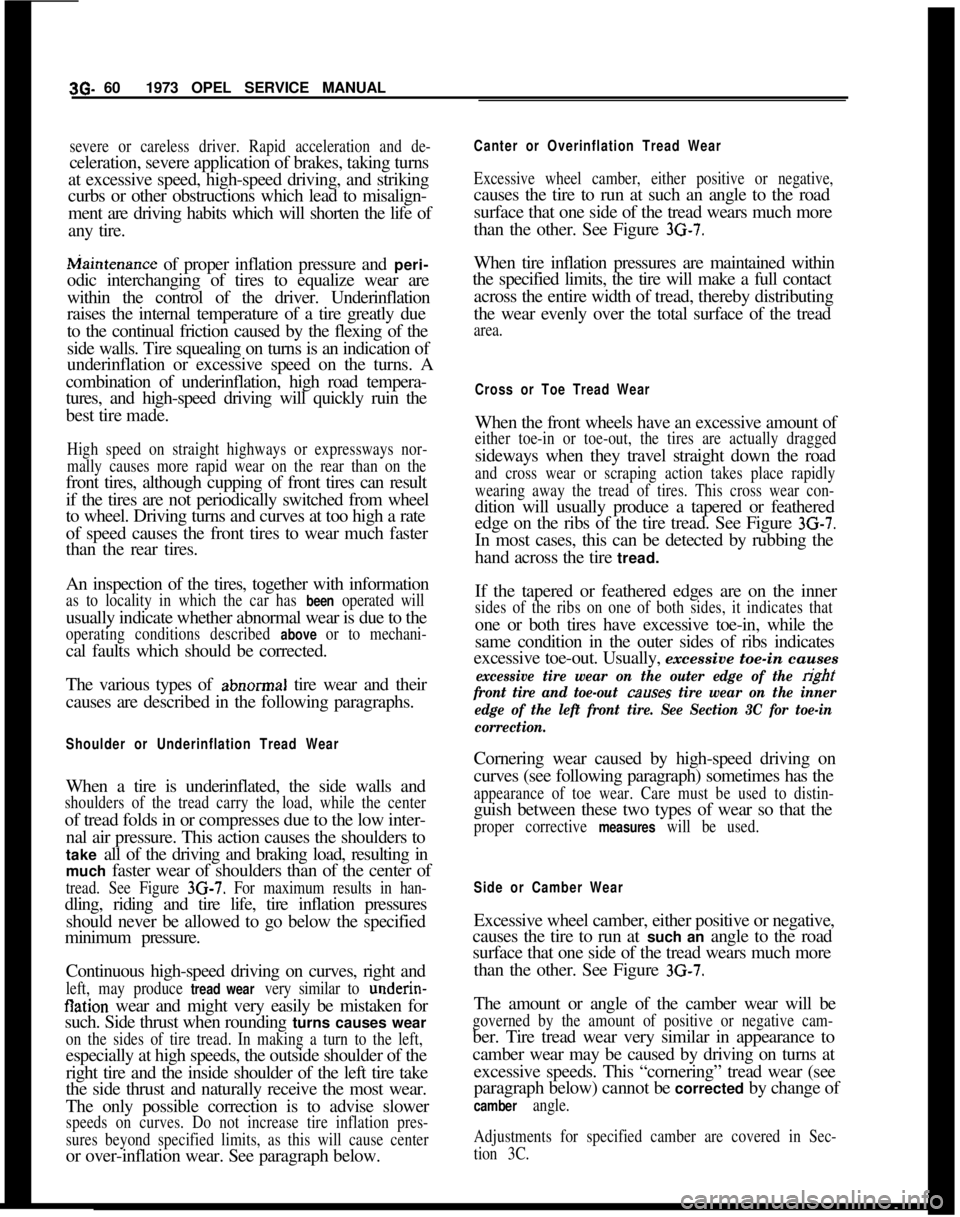
36. 601973 OPEL SERVICE MANUAL
severe or careless driver. Rapid acceleration and de-celeration, severe application of brakes, taking turns
at excessive speed, high-speed driving, and striking
curbs or other obstructions which lead to misalign-
ment are driving habits which will shorten the life of
any tire.hiaintenance of proper inflation pressure and peri-
odic interchanging of tires to equalize wear are
within the control of the driver. Underinflation
raises the internal temperature of a tire greatly due
to the continual friction caused by the flexing of the
side walls. Tire squealing on turns is an indication of
underinflation or excessive speed on the turns. A
combination of underinflation, high road tempera-
tures, and high-speed driving will quickly ruin the
best tire made.
High speed on straight highways or expressways nor-
mally causes more rapid wear on the rear than on thefront tires, although cupping of front tires can result
if the tires are not periodically switched from wheel
to wheel. Driving turns and curves at too high a rate
of speed causes the front tires to wear much faster
than the rear tires.
An inspection of the tires, together with information
as to locality in which the car has been operated willusually indicate whether abnormal wear is due to the
operating conditions described above or to mechani-cal faults which should be corrected.
The various types of
abnormal tire wear and their
causes are described in the following paragraphs.
Shoulder or Underinflation Tread WearWhen a tire is underinflated, the side walls and
shoulders of the tread carry the load, while the centerof tread folds in or compresses due to the low inter-
nal air pressure. This action causes the shoulders to
take all of the driving and braking load, resulting in
much faster wear of shoulders than of the center of
tread. See Figure 3G-7. For maximum results in han-dling, riding and tire life, tire inflation pressures
should never be allowed to go below the specified
minimum pressure.
Continuous high-speed driving on curves, right and
left, may produce tread wear very similar to underin-flation wear and might very easily be mistaken for
such. Side thrust when rounding turns causes wear
on the sides of tire tread. In making a turn to the left,especially at high speeds, the outside shoulder of the
right tire and the inside shoulder of the left tire take
the side thrust and naturally receive the most wear.
The only possible correction is to advise slower
speeds on curves. Do not increase tire inflation pres-
sures beyond specified limits, as this will cause centeror over-inflation wear. See paragraph below.
Canter or Overinflation Tread Wear
Excessive wheel camber, either positive or negative,causes the tire to run at such an angle to the road
surface that one side of the tread wears much more
than the other. See Figure
3G-7.When tire inflation pressures are maintained within
the specified limits, the tire will make a full contact
across the entire width of tread, thereby distributing
the wear evenly over the total surface of the tread
area.
Cross or Toe Tread WearWhen the front wheels have an excessive amount of
either toe-in or toe-out, the tires are actually draggedsideways when they travel straight down the road
and cross wear or scraping action takes place rapidly
wearing away the tread of tires. This cross wear con-dition will usually produce a tapered or feathered
edge on the ribs of the tire tread. See Figure
3G-7.In most cases, this can be detected by rubbing the
hand across the tire tread.
If the tapered or feathered edges are on the inner
sides of the ribs on one of both sides, it indicates thatone or both tires have excessive toe-in, while the
same condition in the outer sides of ribs indicates
excessive toe-out. Usually, excessive toe-in causes
excessive tire wear on the outer edge of the right
front tire and toe-out causes tire wear on the inner
edge of the left front tire. See Section 3C for toe-in
correction.Cornering wear caused by high-speed driving on
curves (see following paragraph) sometimes has the
appearance of toe wear. Care must be used to distin-guish between these two types of wear so that the
proper corrective measures will be used.
Side or Camber WearExcessive wheel camber, either positive or negative,
causes the tire to run at such an angle to the road
surface that one side of the tread wears much more
than the other. See Figure
3G-7.The amount or angle of the camber wear will be
governed by the amount of positive or negative cam-ber. Tire tread wear very similar in appearance to
camber wear may be caused by driving on turns at
excessive speeds. This “cornering” tread wear (see
paragraph below) cannot be corrected by change of
camber angle.
Adjustments for specified camber are covered in Sec-
tion 3C.
Page 228 of 625
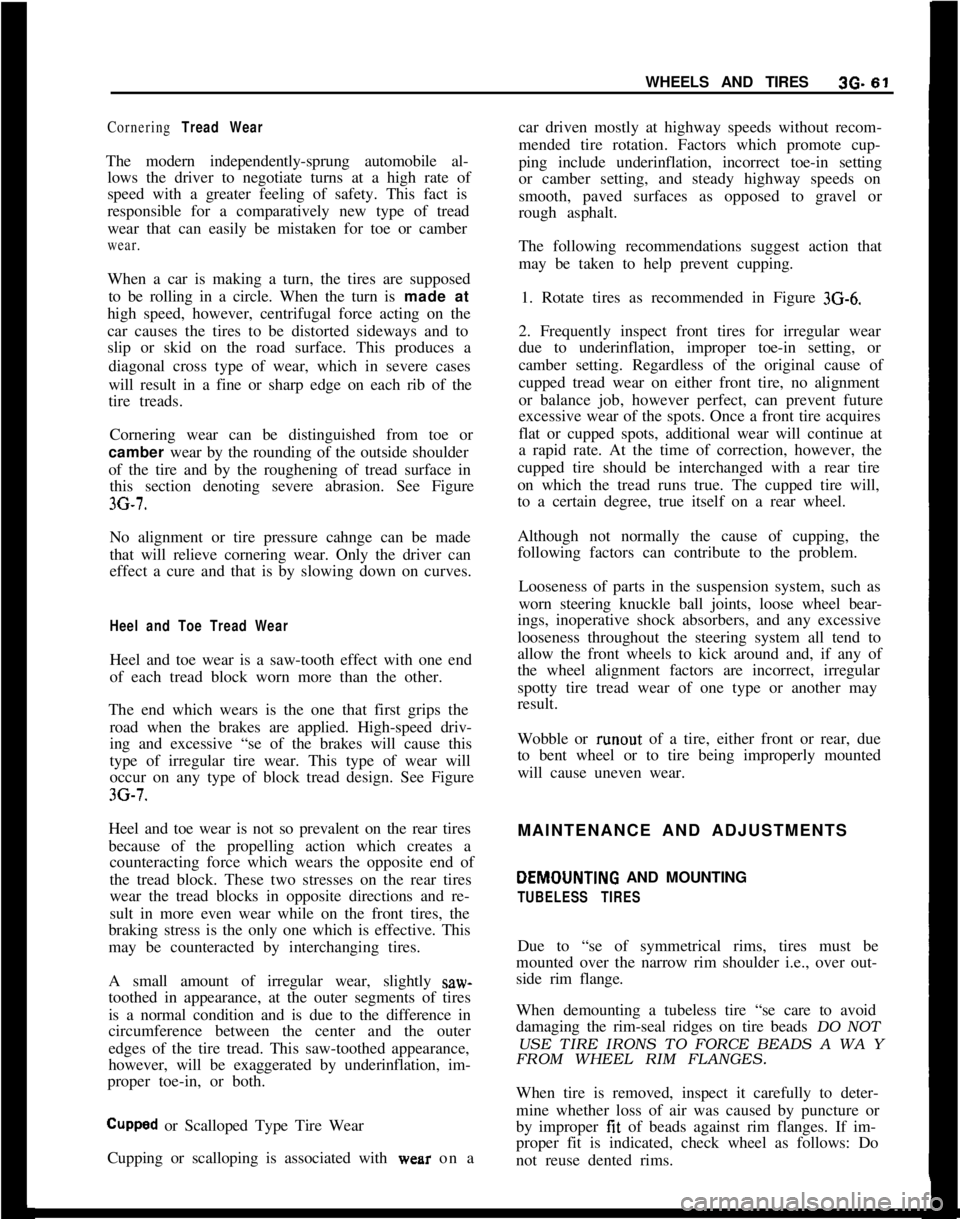
WHEELS AND TIRES3G- 61Cornering Tread WearThe modern independently-sprung automobile al-
lows the driver to negotiate turns at a high rate of
speed with a greater feeling of safety. This fact is
responsible for a comparatively new type of tread
wear that can easily be mistaken for toe or camber
wear.When a car is making a turn, the tires are supposed
to be rolling in a circle. When the turn is made at
high speed, however, centrifugal force acting on the
car causes the tires to be distorted sideways and to
slip or skid on the road surface. This produces a
diagonal cross type of wear, which in severe cases
will result in a fine or sharp edge on each rib of the
tire treads.
Cornering wear can be distinguished from toe or
camber wear by the rounding of the outside shoulder
of the tire and by the roughening of tread surface in
this section denoting severe abrasion. See Figure
3G-7.No alignment or tire pressure cahnge can be made
that will relieve cornering wear. Only the driver can
effect a cure and that is by slowing down on curves.
Heel and Toe Tread WearHeel and toe wear is a saw-tooth effect with one end
of each tread block worn more than the other.
The end which wears is the one that first grips the
road when the brakes are applied. High-speed driv-
ing and excessive “se of the brakes will cause this
type of irregular tire wear. This type of wear will
occur on any type of block tread design. See Figure3G-7.
Heel and toe wear is not so prevalent on the rear tires
because of the propelling action which creates a
counteracting force which wears the opposite end of
the tread block. These two stresses on the rear tires
wear the tread blocks in opposite directions and re-
sult in more even wear while on the front tires, the
braking stress is the only one which is effective. This
may be counteracted by interchanging tires.
A small amount of irregular wear, slightly
saw-toothed in appearance, at the outer segments of tires
is a normal condition and is due to the difference in
circumference between the center and the outer
edges of the tire tread. This saw-toothed appearance,
however, will be exaggerated by underinflation, im-
proper toe-in, or both.Cupped or Scalloped Type Tire Wear
Cupping or scalloping is associated with wear on acar driven mostly at highway speeds without recom-
mended tire rotation. Factors which promote cup-
ping include underinflation, incorrect toe-in setting
or camber setting, and steady highway speeds on
smooth, paved surfaces as opposed to gravel or
rough asphalt.
The following recommendations suggest action that
may be taken to help prevent cupping.
1. Rotate tires as recommended in Figure
3G-6.2. Frequently inspect front tires for irregular wear
due to underinflation, improper toe-in setting, or
camber setting. Regardless of the original cause of
cupped tread wear on either front tire, no alignment
or balance job, however perfect, can prevent future
excessive wear of the spots. Once a front tire acquires
flat or cupped spots, additional wear will continue at
a rapid rate. At the time of correction, however, the
cupped tire should be interchanged with a rear tire
on which the tread runs true. The cupped tire will,
to a certain degree, true itself on a rear wheel.
Although not normally the cause of cupping, the
following factors can contribute to the problem.
Looseness of parts in the suspension system, such as
worn steering knuckle ball joints, loose wheel bear-
ings, inoperative shock absorbers, and any excessive
looseness throughout the steering system all tend to
allow the front wheels to kick around and, if any of
the wheel alignment factors are incorrect, irregular
spotty tire tread wear of one type or another may
result.
Wobble or runout of a tire, either front or rear, due
to bent wheel or to tire being improperly mounted
will cause uneven wear.
MAINTENANCE AND ADJUSTMENTSDEMOUNTING AND MOUNTING
TUBELESS TIRESDue to “se of symmetrical rims, tires must be
mounted over the narrow rim shoulder i.e., over out-
side rim flange.
When demounting a tubeless tire “se care to avoid
damaging the rim-seal ridges on tire beads DO NOT
USE TIRE IRONS TO FORCE BEADS A WA Y
FROM WHEEL RIM FLANGES.
When tire is removed, inspect it carefully to deter-
mine whether loss of air was caused by puncture or
by improper
tit of beads against rim flanges. If im-
proper fit is indicated, check wheel as follows: Do
not reuse dented rims.
Page 234 of 625
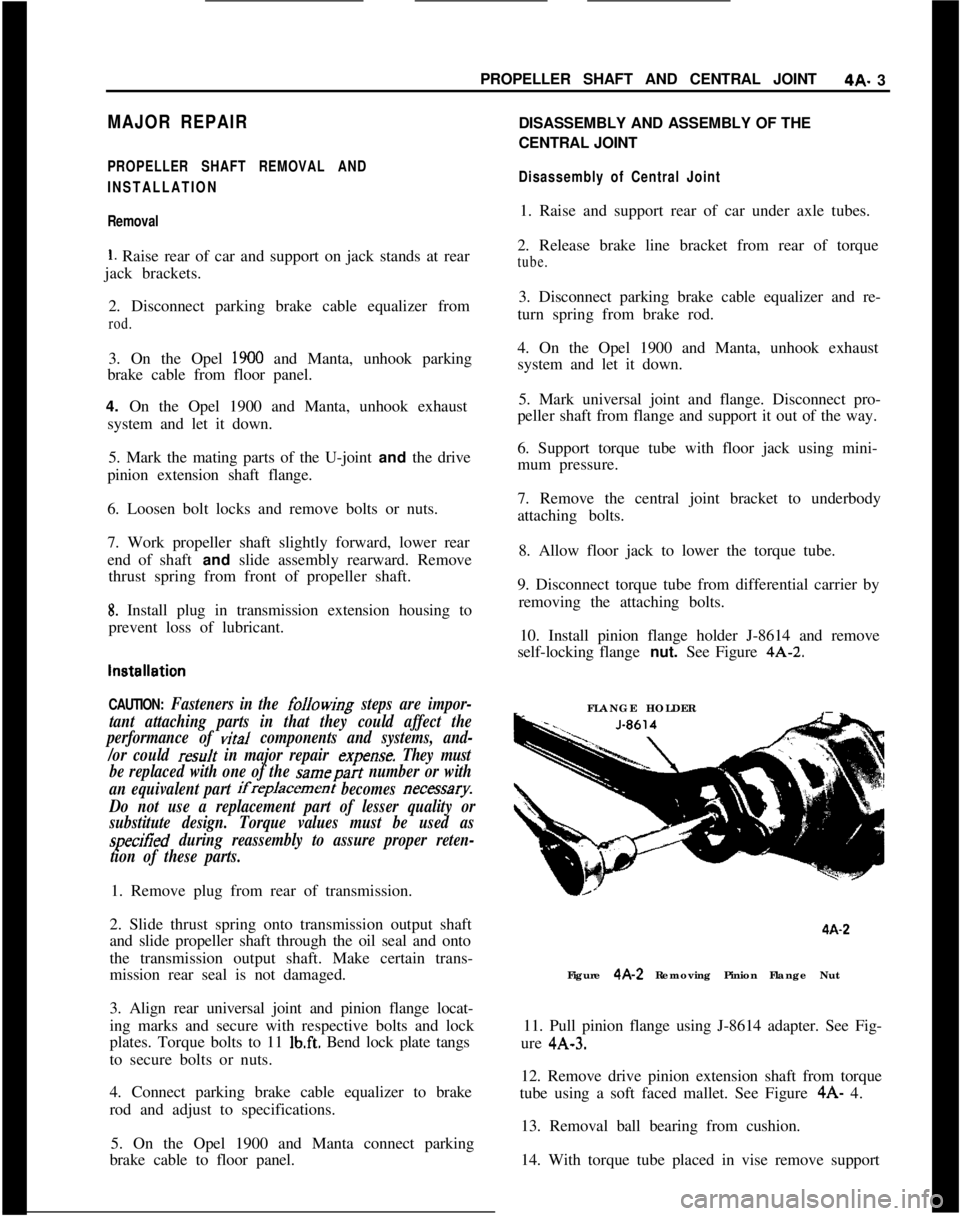
PROPELLER SHAFT AND CENTRAL JOINT4A- 3MAJOR REPAIR
PROPELLER SHAFT REMOVAL AND
INSTALLATION
Removal
1. Raise rear of car and support on jack stands at rear
jack brackets.
2. Disconnect parking brake cable equalizer from
rod.3. On the Opel
1900 and Manta, unhook parking
brake cable from floor panel.
4. On the Opel 1900 and Manta, unhook exhaust
system and let it down.
5. Mark the mating parts of the U-joint and the drive
pinion extension shaft flange.
6. Loosen bolt locks and remove bolts or nuts.
7. Work propeller shaft slightly forward, lower rear
end of shaft and slide assembly rearward. Remove
thrust spring from front of propeller shaft.
S. Install plug in transmission extension housing to
prevent loss of lubricant.
installation
CAUTION:
Fasteners in the foJlowing steps are impor-
tant attaching parts in that they could affect the
performance of
vital components and systems, and-
/or could
result in major repair expense. They must
be replaced with one of the
samepart number or with
an equivalent part
ifreplacement becomes oecessary.
Do not use a replacement part of lesser quality or
substitute design. Torque values must be used as
specirid during reassembly to assure proper reten-
tion of these parts.1. Remove plug from rear of transmission.
2. Slide thrust spring onto transmission output shaft
and slide propeller shaft through the oil seal and onto
the transmission output shaft. Make certain trans-
mission rear seal is not damaged.
3. Align rear universal joint and pinion flange locat-
ing marks and secure with respective bolts and lock
plates. Torque bolts to 11
lb.ft. Bend lock plate tangs
to secure bolts or nuts.
4. Connect parking brake cable equalizer to brake
rod and adjust to specifications.
5. On the Opel 1900 and Manta connect parking
brake cable to floor panel.DISASSEMBLY AND ASSEMBLY OF THE
CENTRAL JOINT
Disassembly of Central Joint1. Raise and support rear of car under axle tubes.
2. Release brake line bracket from rear of torque
tube.3. Disconnect parking brake cable equalizer and re-
turn spring from brake rod.
4. On the Opel 1900 and Manta, unhook exhaust
system and let it down.
5. Mark universal joint and flange. Disconnect pro-
peller shaft from flange and support it out of the way.
6. Support torque tube with floor jack using mini-
mum pressure.
7. Remove the central joint bracket to underbody
attaching bolts.
8. Allow floor jack to lower the torque tube.
9. Disconnect torque tube from differential carrier by
removing the attaching bolts.
10. Install pinion flange holder J-8614 and remove
self-locking flange nut. See Figure 4A-2.
FLANGE HOLDER4A-2
Figure 4A-2 Removing Pinion Flange Nut
11. Pull pinion flange using J-8614 adapter. See Fig-
ure 4A-3.
12. Remove drive pinion extension shaft from torque
tube using a soft faced mallet. See Figure 4A- 4.
13. Removal ball bearing from cushion.
14. With torque tube placed in vise remove support
Page 236 of 625
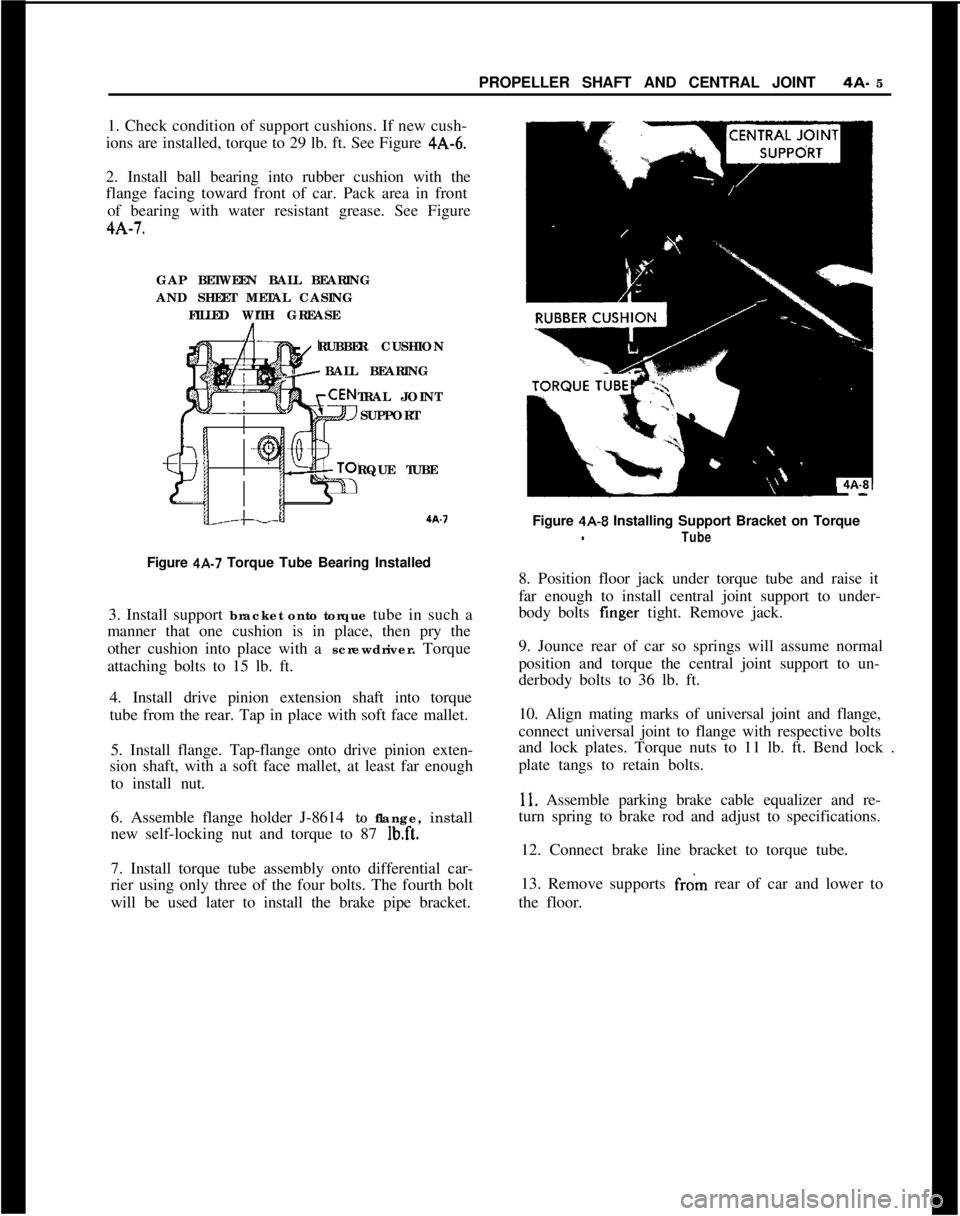
PROPELLER SHAFT AND CENTRAL JOINT4A- 5
1. Check condition of support cushions. If new cush-
ions are installed, torque to 29 lb. ft. See Figure 4A-6.
2. Install ball bearing into rubber cushion with the
flange facing toward front of car. Pack area in front
of bearing with water resistant grease. See Figure4A-7.
GAP BETWEEN BALL BEARING
AND SHEET METAL CASING
FILLED WITH GREASE
RUBBER CUSHION
BALL BEARING
TRAL JOINT
SUPPORT
RQUE TUBEa.7
Figure 4A-7 Torque Tube Bearing Installed
3. Install support bracket onto torque tube in such a
manner that one cushion is in place, then pry the
other cushion into place with a screwdriver. Torque
attaching bolts to 15 lb. ft.
4. Install drive pinion extension shaft into torque
tube from the rear. Tap in place with soft face mallet.
5. Install flange. Tap-flange onto drive pinion exten-
sion shaft, with a soft face mallet, at least far enough
to install nut.
6. Assemble flange holder J-8614 to flange, install
new self-locking nut and torque to 87
lb.ft.7. Install torque tube assembly onto differential car-
rier using only three of the four bolts. The fourth bolt
will be used later to install the brake pipe bracket.Figure
4A-8 Installing Support Bracket on TorquelTube8. Position floor jack under torque tube and raise it
far enough to install central joint support to under-
body bolts finger tight. Remove jack.
9. Jounce rear of car so springs will assume normal
position and torque the central joint support to un-
derbody bolts to 36 lb. ft.
10. Align mating marks of universal joint and flange,
connect universal joint to flange with respective bolts
and lock plates. Torque nuts to 11 lb. ft. Bend lock .
plate tangs to retain bolts.
11. Assemble parking brake cable equalizer and re-
turn spring to brake rod and adjust to specifications.
12. Connect brake line bracket to torque tube.
13. Remove supports
f&n rear of car and lower to
the floor.