ESP OPEL GT-R 1973 Owner's Manual
[x] Cancel search | Manufacturer: OPEL, Model Year: 1973, Model line: GT-R, Model: OPEL GT-R 1973Pages: 625, PDF Size: 17.22 MB
Page 241 of 625
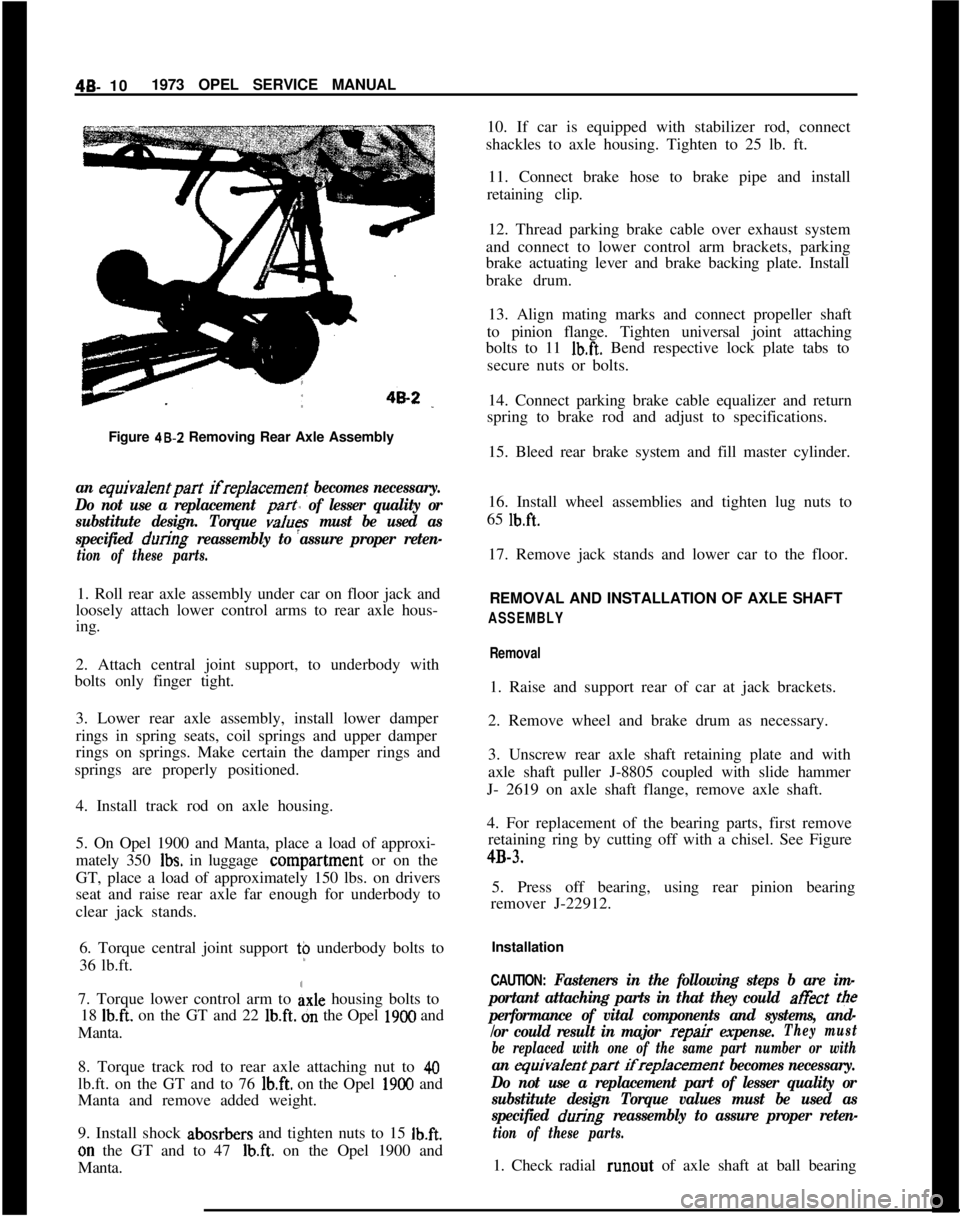
4B- 101973 OPEL SERVICE MANUAL
Figure 48-Z Removing Rear Axle Assemblyan equiva/entpart ifreplacement becomes necessary.
Do not use a replacement
part of lesser quality or
substitute design. Torque
values must be used as
specified
during reassembly to assure proper reten-
tion of these parts.1. Roll rear axle assembly under car on floor jack and
loosely attach lower control arms to rear axle hous-
ing.
2. Attach central joint support, to underbody with
bolts only finger tight.
3. Lower rear axle assembly, install lower damper
rings in spring seats, coil springs and upper damper
rings on springs. Make certain the damper rings and
springs are properly positioned.
4. Install track rod on axle housing.
5. On Opel 1900 and Manta, place a load of approxi-
mately 350
Ibs. in luggage conipartment or on the
GT, place a load of approximately 150 lbs. on drivers
seat and raise rear axle far enough for underbody to
clear jack stands.
6. Torque central joint support t$ underbody bolts to
36 lb.ft.
7. Torque lower control arm to
Axle housing bolts to
18
Ib.ft. on the GT and 22 lb.ft. dn the Opel 1900 and
Manta.
8. Torque track rod to rear axle attaching nut to
40lb.ft. on the GT and to 76
lb.ft. on the Opel 1900 and
Manta and remove added weight.
9. Install shock abosrbers and tighten nuts to 15
Ib.ft.on the GT and to 47
Ib.ft. on the Opel 1900 and
Manta.10. If car is equipped with stabilizer rod, connect
shackles to axle housing. Tighten to 25 lb. ft.
11. Connect brake hose to brake pipe and install
retaining clip.
12. Thread parking brake cable over exhaust system
and connect to lower control arm brackets, parking
brake actuating lever and brake backing plate. Install
brake drum.
13. Align mating marks and connect propeller shaft
to pinion flange. Tighten universal joint attaching
bolts to 11
Ib.ft. Bend respective lock plate tabs to
secure nuts or bolts.
14. Connect parking brake cable equalizer and return
spring to brake rod and adjust to specifications.
15. Bleed rear brake system and fill master cylinder.
16. Install wheel assemblies and tighten lug nuts to
65
lb.ft.17. Remove jack stands and lower car to the floor.
REMOVAL AND INSTALLATION OF AXLE SHAFT
ASSEMBLY
Removal1. Raise and support rear of car at jack brackets.
2. Remove wheel and brake drum as necessary.
3. Unscrew rear axle shaft retaining plate and with
axle shaft puller J-8805 coupled with slide hammer
J- 2619 on axle shaft flange, remove axle shaft.
4. For replacement of the bearing parts, first remove
retaining ring by cutting off with a chisel. See Figure4B-3.
5. Press off bearing, using rear pinion bearing
remover J-22912.
Installation
CAUTION: Fasteners in the following steps b are im-
portant attaching parts in that they could at&t
tee
performance of vital components and systems, and-
/or could result in major
repair expense.They must
be replaced with one of the same part number or with
an equivalentpart ifreplacement becomes necessary.
Do not use a replacement part of lesser quality or
substitute design Torque values must be used as
specified
during reassembly to assure proper reten-
tion of these parts.1. Check radial runout of axle shaft at ball bearing
Page 245 of 625
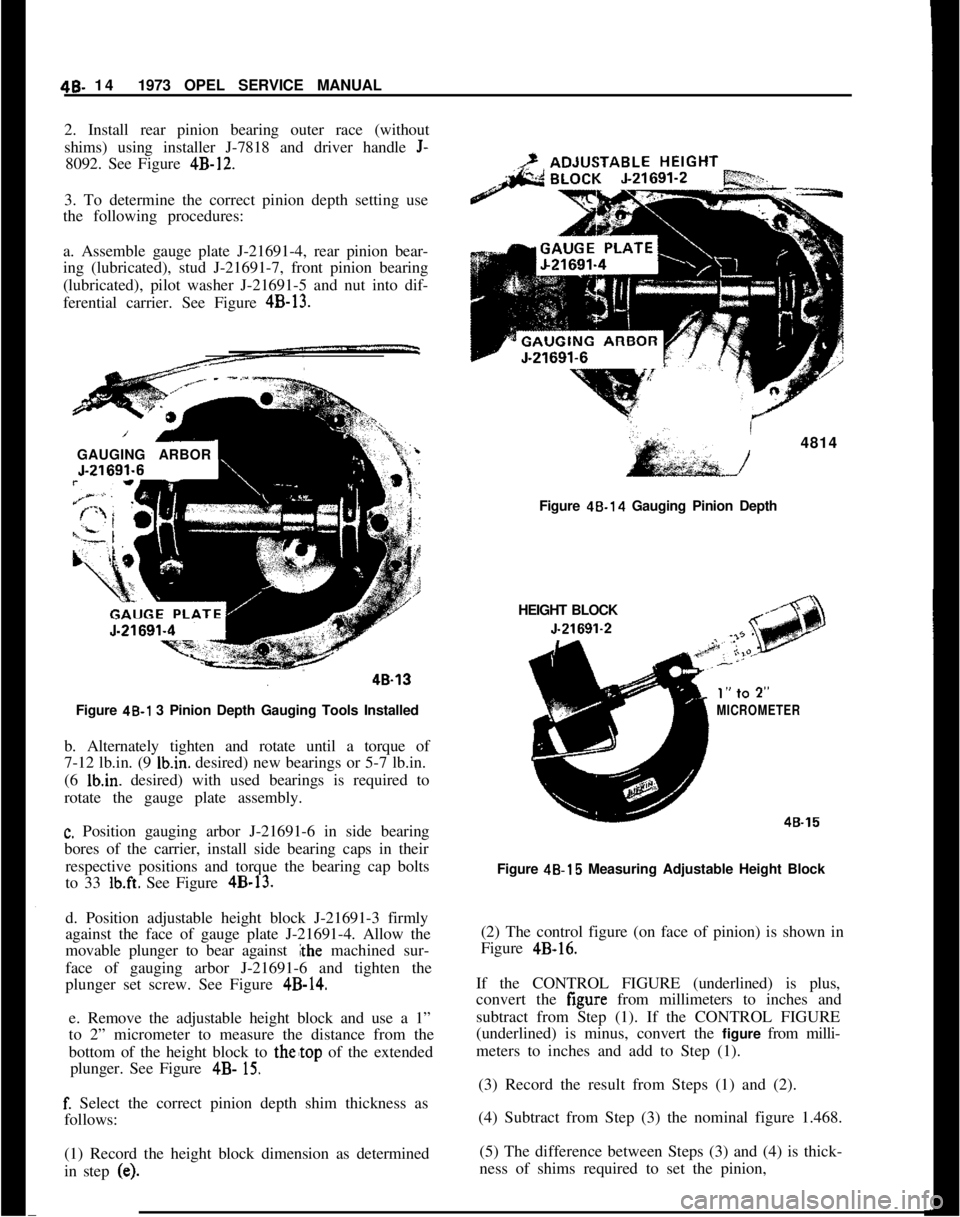
46. 141973 OPEL SERVICE MANUAL
2. Install rear pinion bearing outer race (without
shims) using installer J-7818 and driver handle
J-8092. See Figure 4B-12.
3. To determine the correct pinion depth setting use
the following procedures:
a. Assemble gauge plate J-21691-4, rear pinion bear-
ing (lubricated), stud J-21691-7, front pinion bearing
(lubricated), pilot washer J-21691-5 and nut into dif-
ferential carrier. See Figure 4B-13.
‘1GAUGING ARBOR
Figure 48-l 3 Pinion Depth Gauging Tools Installed
b. Alternately tighten and rotate until a torque of
7-12 lb.in. (9 Ibin. desired) new bearings or 5-7 lb.in.
(6 lb.in. desired) with used bearings is required to
rotate the gauge plate assembly.
c. Position gauging arbor J-21691-6 in side bearing
bores of the carrier, install side bearing caps in their
respective positions and torque the bearing cap bolts
to 33
lb.ft. See Figure 4B-13.
d. Position adjustable height block J-21691-3 firmly
against the face of gauge plate J-21691-4. Allow the
movable plunger to bear against
#the machined sur-
face of gauging arbor J-21691-6 and tighten the
plunger set screw. See Figure
4B-14.e. Remove the adjustable height block and use a 1”
to 2” micrometer to measure the distance from the
bottom of the height block to
thetop of the extended
plunger. See Figure
4B- 15.
f. Select the correct pinion depth shim thickness as
follows:
(1) Record the height block dimension as determined
in step
(e).
I4814
/Figure 48.14 Gauging Pinion Depth
HEIGHT BLOCK
MICROMETER
48-15Figure 4B-15 Measuring Adjustable Height Block
(2) The control figure (on face of pinion) is shown in
Figure
4B-16.If the CONTROL FIGURE (underlined) is plus,
convert the figure from millimeters to inches and
subtract from Step (1). If the CONTROL FIGURE
(underlined) is minus, convert the figure from milli-
meters to inches and add to Step (1).
(3) Record the result from Steps (1) and (2).
(4) Subtract from Step (3) the nominal figure 1.468.
(5) The difference between Steps (3) and (4) is thick-
ness of shims required to set the pinion,
Page 249 of 625
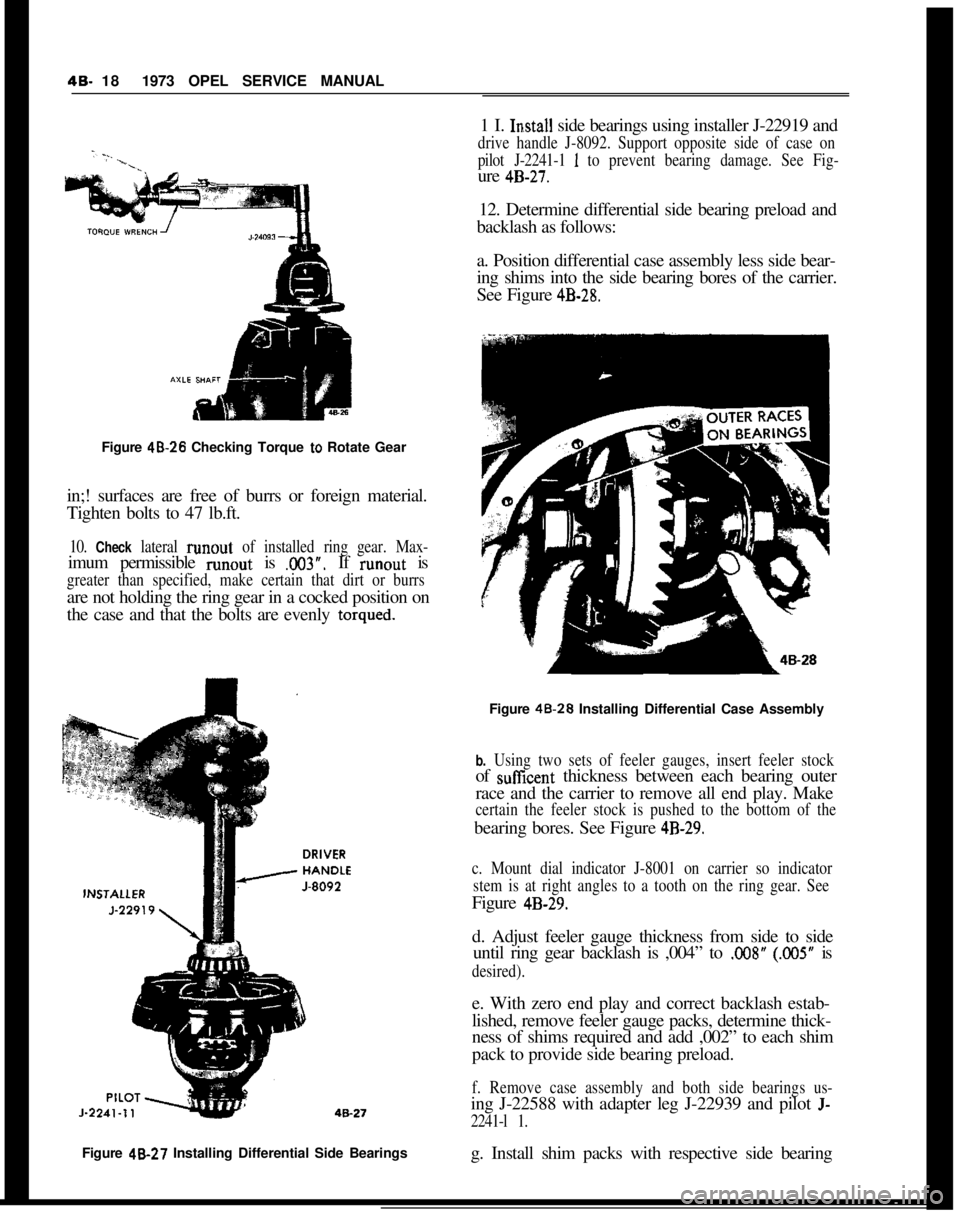
48. 181973 OPEL SERVICE MANUAL
Figure 48.26 Checking Torque
to Rotate Gear
in;! surfaces are free of burrs or foreign material.
Tighten bolts to 47 lb.ft.
10. Check lateral runout of installed ring gear. Max-imum permissible runout is
.003”. If runout is
greater than specified, make certain that dirt or burrsare not holding the ring gear in a cocked position on
the case and that the bolts are evenly
torqued.Figure 48-27 Installing Differential Side Bearings
g. Install shim packs with respective side bearing1 I.
In.stall side bearings using installer J-22919 and
drive handle J-8092. Support opposite side of case on
pilot J-2241-1
1 to prevent bearing damage. See Fig-ure
4B-27.12. Determine differential side bearing preload and
backlash as follows:
a. Position differential case assembly less side bear-
ing shims into the side bearing bores of the carrier.
See Figure
4B-28.Figure 48.28 Installing Differential Case Assembly
b. Using two sets of feeler gauges, insert feeler stockof suffcent thickness between each bearing outer
race and the carrier to remove all end play. Make
certain the feeler stock is pushed to the bottom of thebearing bores. See Figure
4B-29.
c. Mount dial indicator J-8001 on carrier so indicator
stem is at right angles to a tooth on the ring gear. SeeFigure
4B-29.d. Adjust feeler gauge thickness from side to side
until ring gear backlash is ,004” to
.OO8” (.005” is
desired).e. With zero end play and correct backlash estab-
lished, remove feeler gauge packs, determine thick-
ness of shims required and add ,002” to each shim
pack to provide side bearing preload.
f. Remove case assembly and both side bearings us-ing J-22588 with adapter leg J-22939 and pilot
J-
2241-l 1.
Page 250 of 625
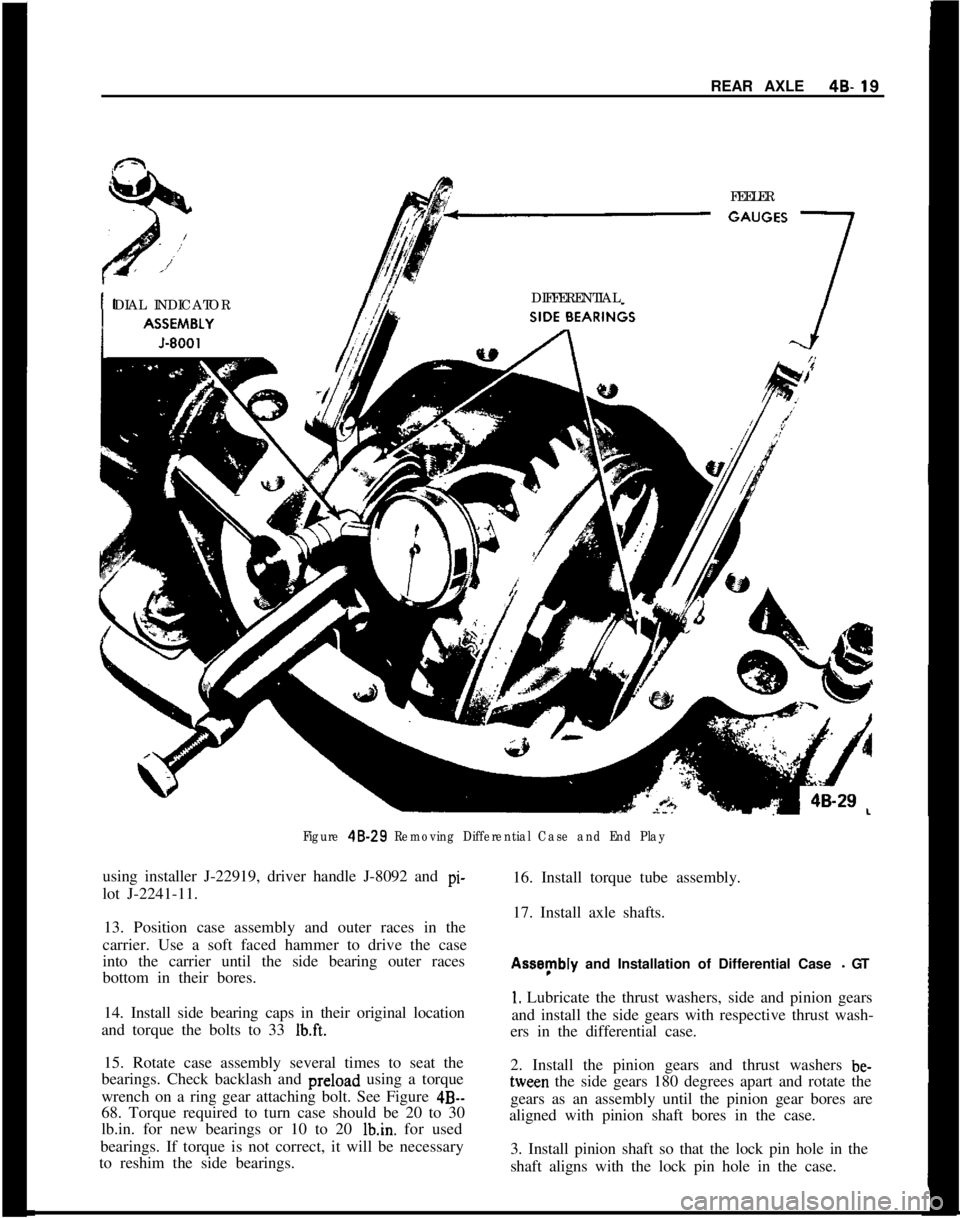
REAR AXLE48.19FEELER
DIAL INDICATORDIFFERENTIAL
Figure 48.29 Removing Differential Case and End Playusing installer J-22919, driver handle J-8092 and pi-
lot J-2241-11.16. Install torque tube assembly.
17. Install axle shafts.
13. Position case assembly and outer races in the
carrier. Use a soft faced hammer to drive the case
into the carrier until the side bearing outer races
bottom in their bores.Assynbly and Installation of Differential Case
- GT
14. Install side bearing caps in their original location
and torque the bolts to 33
Ib.ft.
1. Lubricate the thrust washers, side and pinion gears
and install the side gears with respective thrust wash-
ers in the differential case.
15. Rotate case assembly several times to seat the
bearings. Check backlash and preload using a torque
wrench on a ring gear attaching bolt. See Figure
4B--68. Torque required to turn case should be 20 to 30
lb.in. for new bearings or 10 to 20 Ibin. for used
bearings. If torque is not correct, it will be necessary
to reshim the side bearings.2. Install the pinion gears and thrust washers be-tween the side gears 180 degrees apart and rotate the
gears as an assembly until the pinion gear bores are
aligned with pinion shaft bores in the case.
3. Install pinion shaft so that the lock pin hole in the
shaft aligns with the lock pin hole in the case.
Page 252 of 625
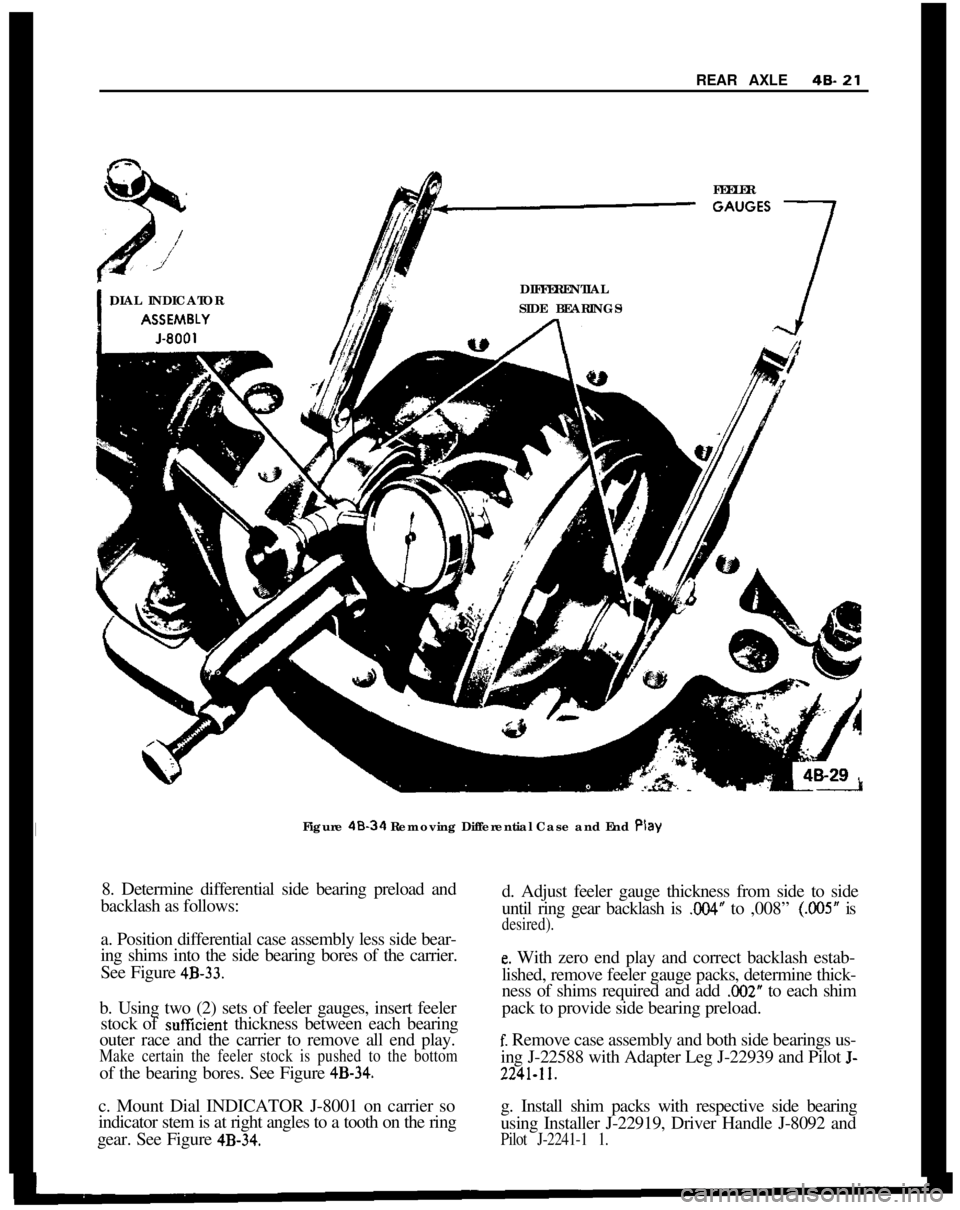
REAR AXLE48.21FEELER
DIFFERENTIAL
DIAL INDICATOR
SIDE BEARINGS
Figure 48.34 Removing Differential Case and End
Play8. Determine differential side bearing preload and
backlash as follows:d. Adjust feeler gauge thickness from side to side
until ring gear backlash is
004” to ,008” (.005” is
desired).a. Position differential case assembly less side bear-
ing shims into the side bearing bores of the carrier.
See Figure
4B-33.b. Using two (2) sets of feeler gauges, insert feeler
stock of sufficient thickness between each bearing
outer race and the carrier to remove all end play.
Make certain the feeler stock is pushed to the bottomof the bearing bores. See Figure
4B-34.
e. With zero end play and correct backlash estab-
lished, remove feeler gauge packs, determine thick-
ness of shims required and add
.002” to each shim
pack to provide side bearing preload.
f. Remove case assembly and both side bearings us-
ing J-22588 with Adapter Leg J-22939 and Pilot
J-
2241-11.c. Mount Dial INDICATOR J-8001 on carrier sog. Install shim packs with respective side bearing
indicator stem is at right angles to a tooth on the ring
using Installer J-22919, Driver Handle J-8092 and
gear. See Figure
4B-34.Pilot J-2241-1 1.
Page 262 of 625
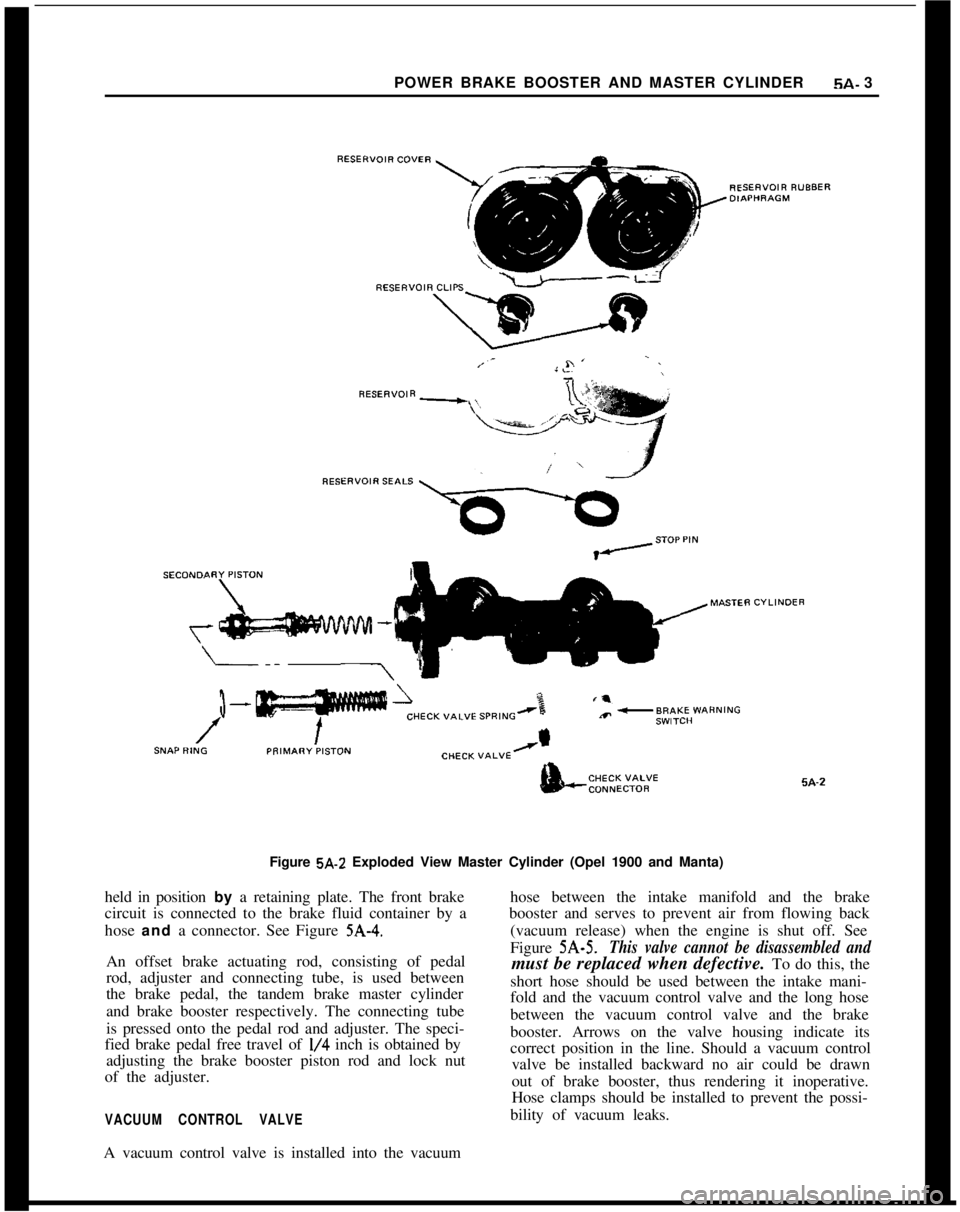
POWER BRAKE BOOSTER AND MASTER CYLINDER5A- 3
Figure 5A-2 Exploded View Master Cylinder (Opel 1900 and Manta)
held in position by a retaining plate. The front brake
circuit is connected to the brake fluid container by a
hose and a connector. See Figure
5A-4.An offset brake actuating rod, consisting of pedal
rod, adjuster and connecting tube, is used between
the brake pedal, the tandem brake master cylinder
and brake booster respectively. The connecting tube
is pressed onto the pedal rod and adjuster. The speci-
fied brake pedal free travel of
l/4 inch is obtained by
adjusting the brake booster piston rod and lock nut
of the adjuster.
VACUUM CONTROL VALVEhose between the intake manifold and the brake
booster and serves to prevent air from flowing back
(vacuum release) when the engine is shut off. See
Figure 5A-5.
This valve cannot be disassembled andmust be replaced when defective. To do this, the
short hose should be used between the intake mani-
fold and the vacuum control valve and the long hose
between the vacuum control valve and the brake
booster. Arrows on the valve housing indicate its
correct position in the line. Should a vacuum control
valve be installed backward no air could be drawn
out of brake booster, thus rendering it inoperative.
Hose clamps should be installed to prevent the possi-
bility of vacuum leaks.
A vacuum control valve is installed into the vacuum
Page 288 of 625
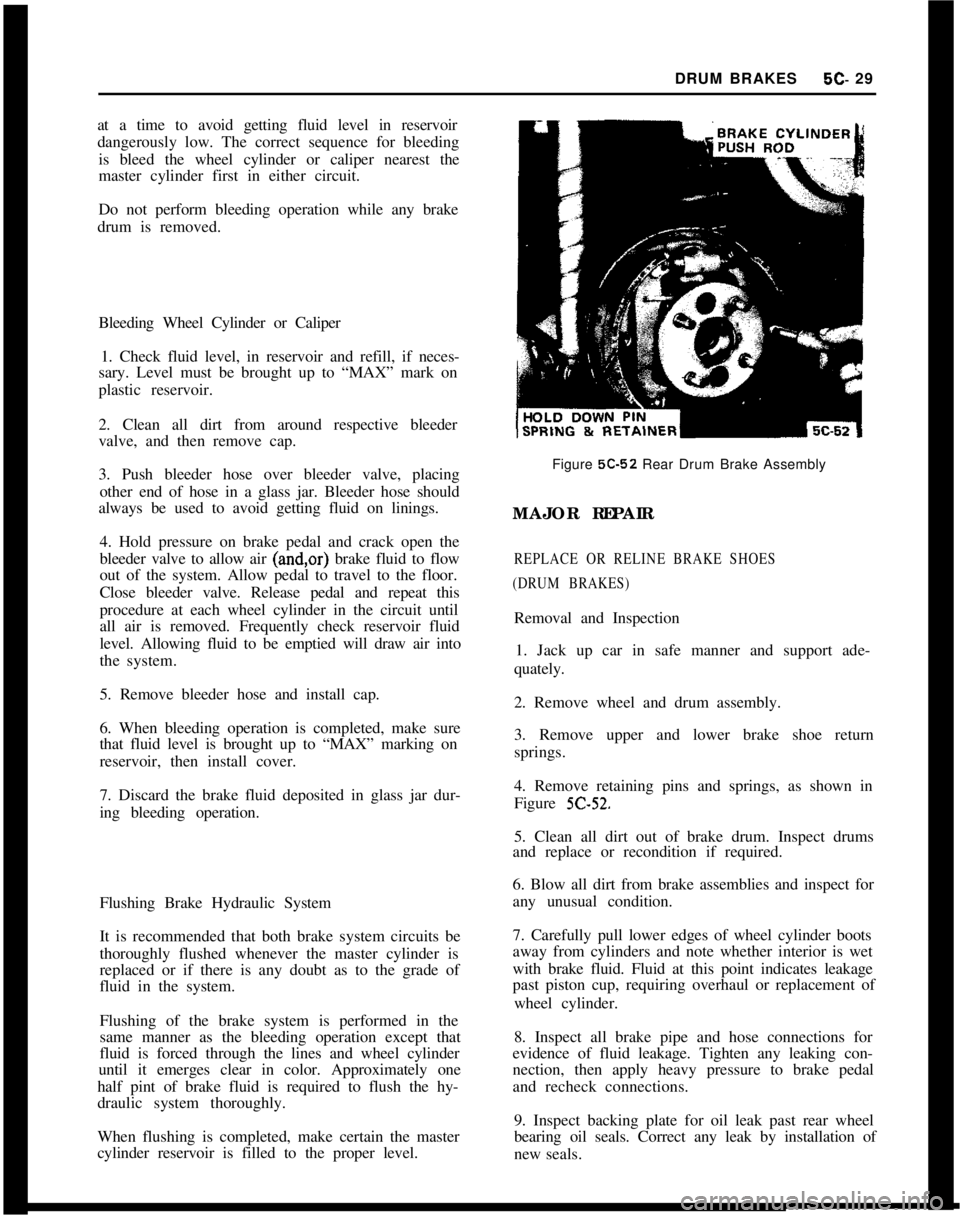
DRUM BRAKESBC- 29
at a time to avoid getting fluid level in reservoir
dangerously low. The correct sequence for bleeding
is bleed the wheel cylinder or caliper nearest the
master cylinder first in either circuit.
Do not perform bleeding operation while any brake
drum is removed.
Bleeding Wheel Cylinder or Caliper
1. Check fluid level, in reservoir and refill, if neces-
sary. Level must be brought up to “MAX” mark on
plastic reservoir.
2. Clean all dirt from around respective bleeder
valve, and then remove cap.
3. Push bleeder hose over bleeder valve, placing
other end of hose in a glass jar. Bleeder hose should
always be used to avoid getting fluid on linings.
4. Hold pressure on brake pedal and crack open the
bleeder valve to allow air (and,or) brake fluid to flow
out of the system. Allow pedal to travel to the floor.
Close bleeder valve. Release pedal and repeat this
procedure at each wheel cylinder in the circuit until
all air is removed. Frequently check reservoir fluid
level. Allowing fluid to be emptied will draw air into
the system.
5. Remove bleeder hose and install cap.
6. When bleeding operation is completed, make sure
that fluid level is brought up to “MAX” marking on
reservoir, then install cover.
7. Discard the brake fluid deposited in glass jar dur-
ing bleeding operation.
Flushing Brake Hydraulic System
It is recommended that both brake system circuits be
thoroughly flushed whenever the master cylinder is
replaced or if there is any doubt as to the grade of
fluid in the system.
Flushing of the brake system is performed in the
same manner as the bleeding operation except that
fluid is forced through the lines and wheel cylinder
until it emerges clear in color. Approximately one
half pint of brake fluid is required to flush the hy-
draulic system thoroughly.
When flushing is completed, make certain the master
cylinder reservoir is filled to the proper level.Figure
5C-52 Rear Drum Brake Assembly
MAJOR REPAIR
REPLACE OR RELINE BRAKE SHOES
(DRUM BRAKES)Removal and Inspection
1. Jack up car in safe manner and support ade-
quately.
2. Remove wheel and drum assembly.
3. Remove upper and lower brake shoe return
springs.
4. Remove retaining pins and springs, as shown in
Figure
5C-52.5. Clean all dirt out of brake drum. Inspect drums
and replace or recondition if required.
6. Blow all dirt from brake assemblies and inspect for
any unusual condition.
7. Carefully pull lower edges of wheel cylinder boots
away from cylinders and note whether interior is wet
with brake fluid. Fluid at this point indicates leakage
past piston cup, requiring overhaul or replacement of
wheel cylinder.
8. Inspect all brake pipe and hose connections for
evidence of fluid leakage. Tighten any leaking con-
nection, then apply heavy pressure to brake pedal
and recheck connections.
9. Inspect backing plate for oil leak past rear wheel
bearing oil seals. Correct any leak by installation of
new seals.
Page 295 of 625
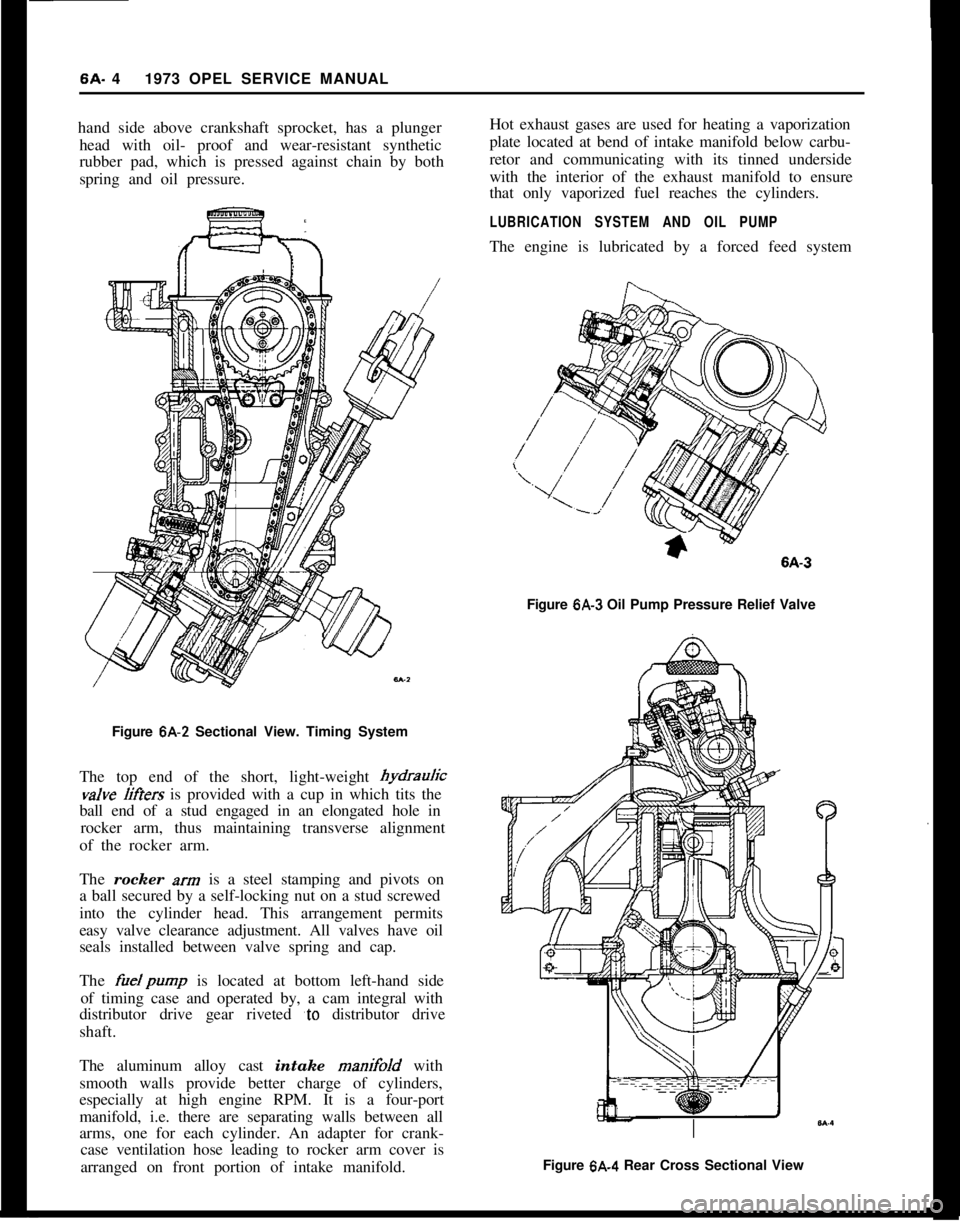
6A. 41973 OPEL SERVICE MANUAL
hand side above crankshaft sprocket, has a plunger
head with oil- proof and wear-resistant synthetic
rubber pad, which is pressed against chain by both
spring and oil pressure.
Figure 6A-2 Sectional View. Timing System
The top end of the short, light-weight hydrauricvalve
liffers is provided with a cup in which tits the
ball end of a stud engaged in an elongated hole in
rocker arm, thus maintaining transverse alignment
of the rocker arm.
The rocker
xrn is a steel stamping and pivots on
a ball secured by a self-locking nut on a stud screwed
into the cylinder head. This arrangement permits
easy valve clearance adjustment. All valves have oil
seals installed between valve spring and cap.
The
fuelpump is located at bottom left-hand side
of timing case and operated by, a cam integral with
distributor drive gear riveted
‘to distributor drive
shaft.
The aluminum alloy cast intake manifold with
smooth walls provide better charge of cylinders,
especially at high engine RPM. It is a four-port
manifold, i.e. there are separating walls between all
arms, one for each cylinder. An adapter for crank-
case ventilation hose leading to rocker arm cover is
arranged on front portion of intake manifold.Hot exhaust gases are used for heating a vaporization
plate located at bend of intake manifold below carbu-
retor and communicating with its tinned underside
with the interior of the exhaust manifold to ensure
that only vaporized fuel reaches the cylinders.
LUBRICATION SYSTEM AND OIL PUMPThe engine is lubricated by a forced feed system
Figure
6A-3 Oil Pump Pressure Relief Valve
Figure 6A.4 Rear Cross Sectional View
Page 298 of 625
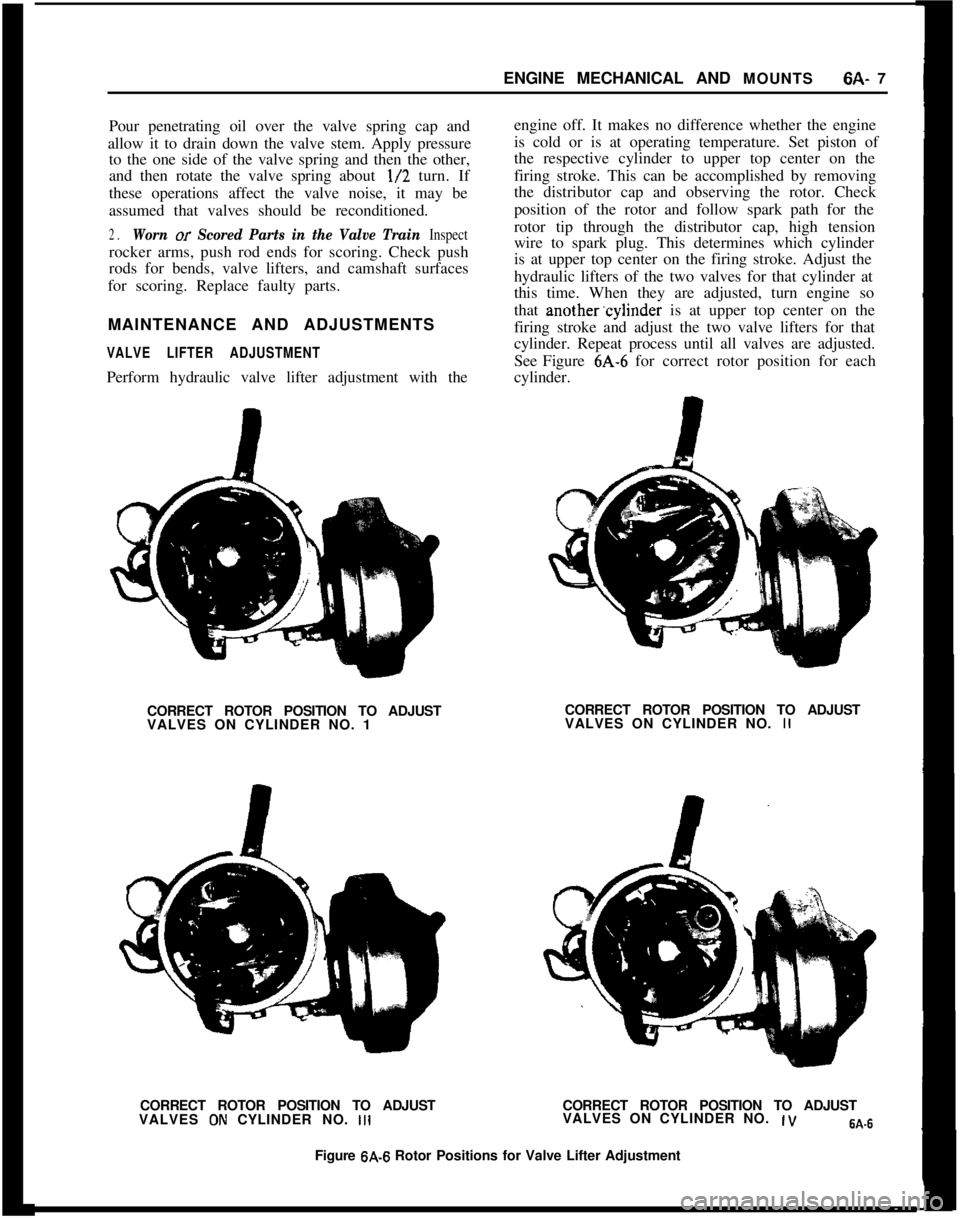
ENGINE MECHANICAL AND MOUNTS6A- 7
Pour penetrating oil over the valve spring cap andengine off. It makes no difference whether the engine
allow it to drain down the valve stem. Apply pressureis cold or is at operating temperature. Set piston of
to the one side of the valve spring and then the other,the respective cylinder to upper top center on the
and then rotate the valve spring about l/2 turn. Iffiring stroke. This can be accomplished by removing
these operations affect the valve noise, it may bethe distributor cap and observing the rotor. Check
assumed that valves should be reconditioned.position of the rotor and follow spark path for the
2.Worn or Scored Parts in the Valve Train Inspectrotor tip through the distributor cap, high tension
rocker arms, push rod ends for scoring. Check pushwire to spark plug. This determines which cylinder
rods for bends, valve lifters, and camshaft surfacesis at upper top center on the firing stroke. Adjust the
for scoring. Replace faulty parts.hydraulic lifters of the two valves for that cylinder at
this time. When they are adjusted, turn engine so
MAINTENANCE AND ADJUSTMENTSthat another.cylinder is at upper top center on the
firing stroke and adjust the two valve lifters for that
VALVE LIFTER ADJUSTMENTcylinder. Repeat process until all valves are adjusted.
See Figure 6A-6 for correct rotor position for each
Perform hydraulic valve lifter adjustment with thecylinder.
CORRECT ROTOR POSITION TO ADJUSTCORRECT ROTOR POSITION TO ADJUST
VALVES ON CYLINDER NO. 1VALVES ON CYLINDER NO. II
CORRECT ROTOR POSITION TO ADJUSTCORRECT ROTOR POSITION TO ADJUST
VALVES
ON CYLINDER NO. IllVALVES ON CYLINDER NO. ,VW-6Figure
6A-6 Rotor Positions for Valve Lifter Adjustment
Page 302 of 625
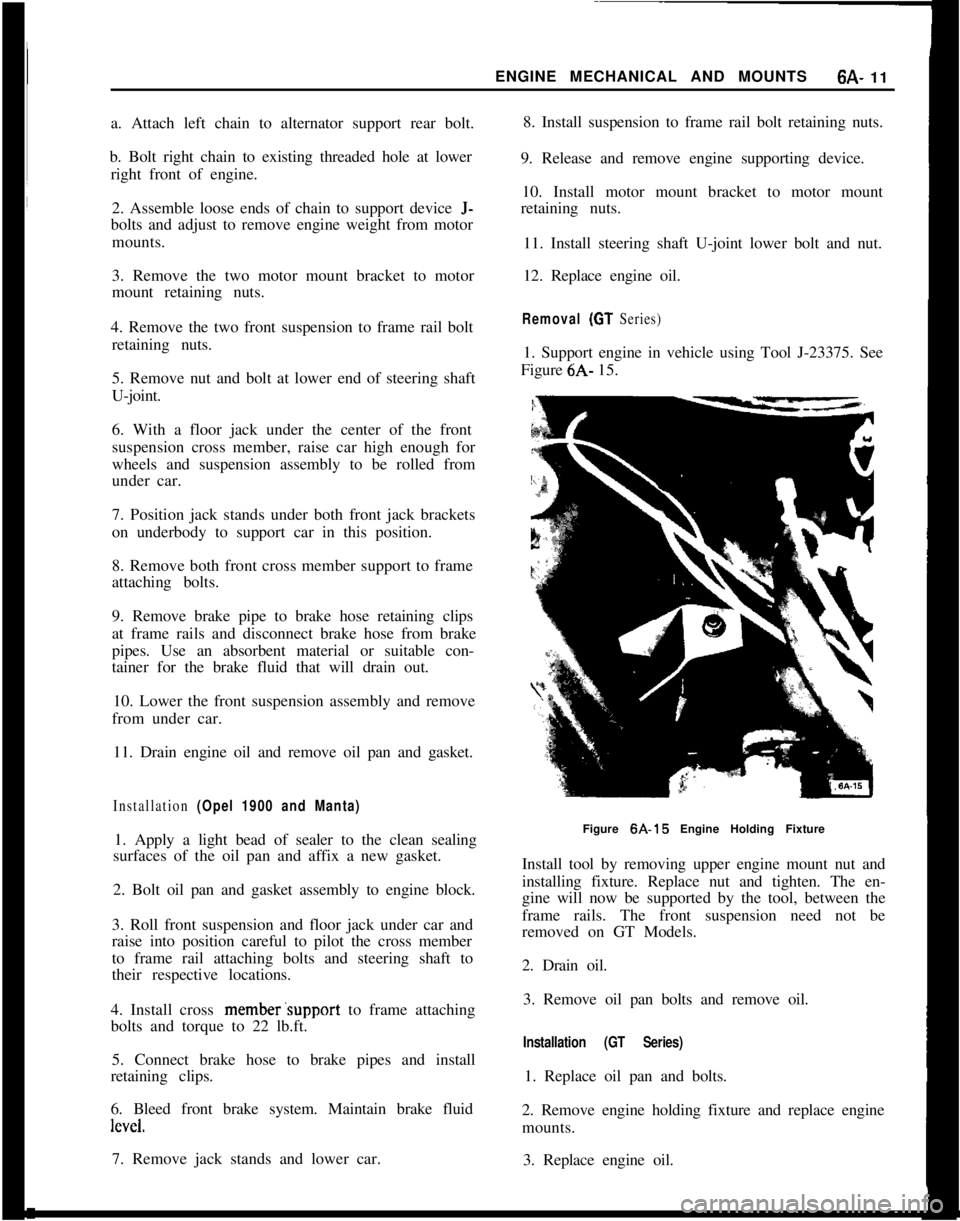
ENGINE MECHANICAL AND MOUNTS6A- 11
a. Attach left chain to alternator support rear bolt.
b. Bolt right chain to existing threaded hole at lower
right front of engine.
2. Assemble loose ends of chain to support device J-bolts and adjust to remove engine weight from motor
mounts.
3. Remove the two motor mount bracket to motor
mount retaining nuts.
4. Remove the two front suspension to frame rail bolt
retaining nuts.
5. Remove nut and bolt at lower end of steering shaft
U-joint.
6. With a floor jack under the center of the front
suspension cross member, raise car high enough for
wheels and suspension assembly to be rolled from
under car.
7. Position jack stands under both front jack brackets
on underbody to support car in this position.
8. Remove both front cross member support to frame
attaching bolts.
9. Remove brake pipe to brake hose retaining clips
at frame rails and disconnect brake hose from brake
pipes. Use an absorbent material or suitable con-
tainer for the brake fluid that will drain out.
10. Lower the front suspension assembly and remove
from under car.
11. Drain engine oil and remove oil pan and gasket.
Installation (Opel 1900 and Manta)1. Apply a light bead of sealer to the clean sealing
surfaces of the oil pan and affix a new gasket.
2. Bolt oil pan and gasket assembly to engine block.
3. Roll front suspension and floor jack under car and
raise into position careful to pilot the cross member
to frame rail attaching bolts and steering shaft to
their respective locations.
4. Install cross member’support to frame attaching
bolts and torque to 22 lb.ft.
5. Connect brake hose to brake pipes and install
retaining clips.
6. Bleed front brake system. Maintain brake fluid1Wd.
7. Remove jack stands and lower car.8. Install suspension to frame rail bolt retaining nuts.
9. Release and remove engine supporting device.
10. Install motor mount bracket to motor mount
retaining nuts.
11. Install steering shaft U-joint lower bolt and nut.
12. Replace engine oil.
Removal (GT Series)1. Support engine in vehicle using Tool J-23375. See
Figure 6A- 15.
Figure 6A-15 Engine Holding Fixture
Install tool by removing upper engine mount nut and
installing fixture. Replace nut and tighten. The en-
gine will now be supported by the tool, between the
frame rails. The front suspension need not be
removed on GT Models.
2. Drain oil.
3. Remove oil pan bolts and remove oil.
Installation (GT Series)1. Replace oil pan and bolts.
2. Remove engine holding fixture and replace engine
mounts.
3. Replace engine oil.