check engine RENAULT KANGOO 1997 KC / 1.G Engine And Peripherals Owner's Guide
[x] Cancel search | Manufacturer: RENAULT, Model Year: 1997, Model line: KANGOO, Model: RENAULT KANGOO 1997 KC / 1.GPages: 208
Page 141 of 208
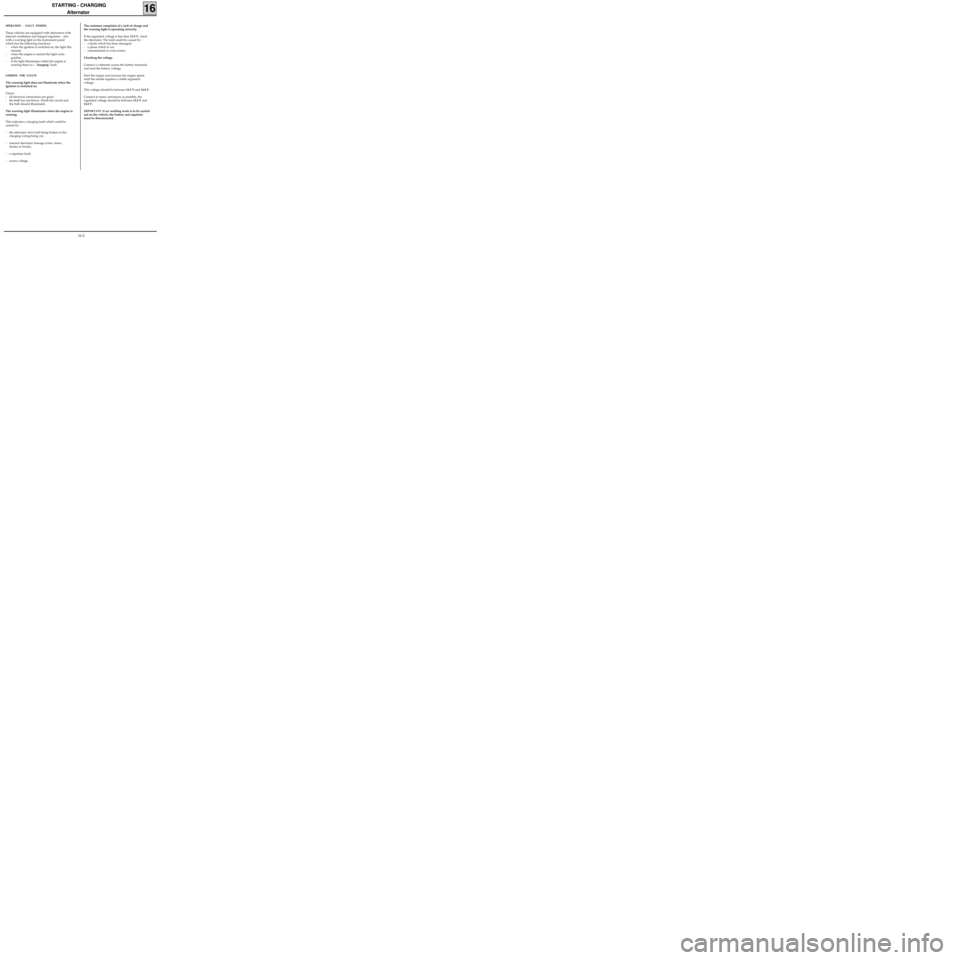
STARTING - CHARGING
Alternator
16
OPERATION - FAULT FINDING
These vehicles are equipped with alternators with
internal ventilation and integral regulator, also
with a warning light on the instrument panel
which has the following functions :
- when the ignition is switched on, the light illu-
minates
- when the engine is started the light extin-
guishes,
- if the light illuminates whilst the engine is
running there is a "charging "fault.
LOOKING FOR FAULTS
The warning light does not illuminate when the
ignition is switched on.
Check:
- all electrical connections are good.
- the bulb has not blown. (Earth the circuit and
the bulb should illuminate).
The warning light illuminates when the engine is
running.
This indicates a charging fault which could be
caused by :
- the alternator drive belt being broken or the
charging wiring being cut,
- internal alternator damage (rotor, stator,
diodes or brush),
- a regulator fault,
- excess voltage.The customer complains of a lack of charge and
the warning light is operating correctly.
If the regulated voltage is less than 13.5 V, check
the alternator. The fault could be caused by :
- a diode which has been damaged,
- a phase which is cut,
- contaminated or worn tracks.
Checking the voltage
Connect a voltmeter across the battery terminals
and read the battery voltage.
Start the engine and increase the engine speed
until the needle registers a stable regulated
voltage.
This voltage should be between 13.5 V and 14.8 V.
Connect as many consumers as possible, the
regulated voltage should be between 13.5 V and
14.8 V.
IMPORTANT: if arc welding work is to be carried
out on the vehicle, the battery and regulator
must be disconnected.
16-2
Page 142 of 208
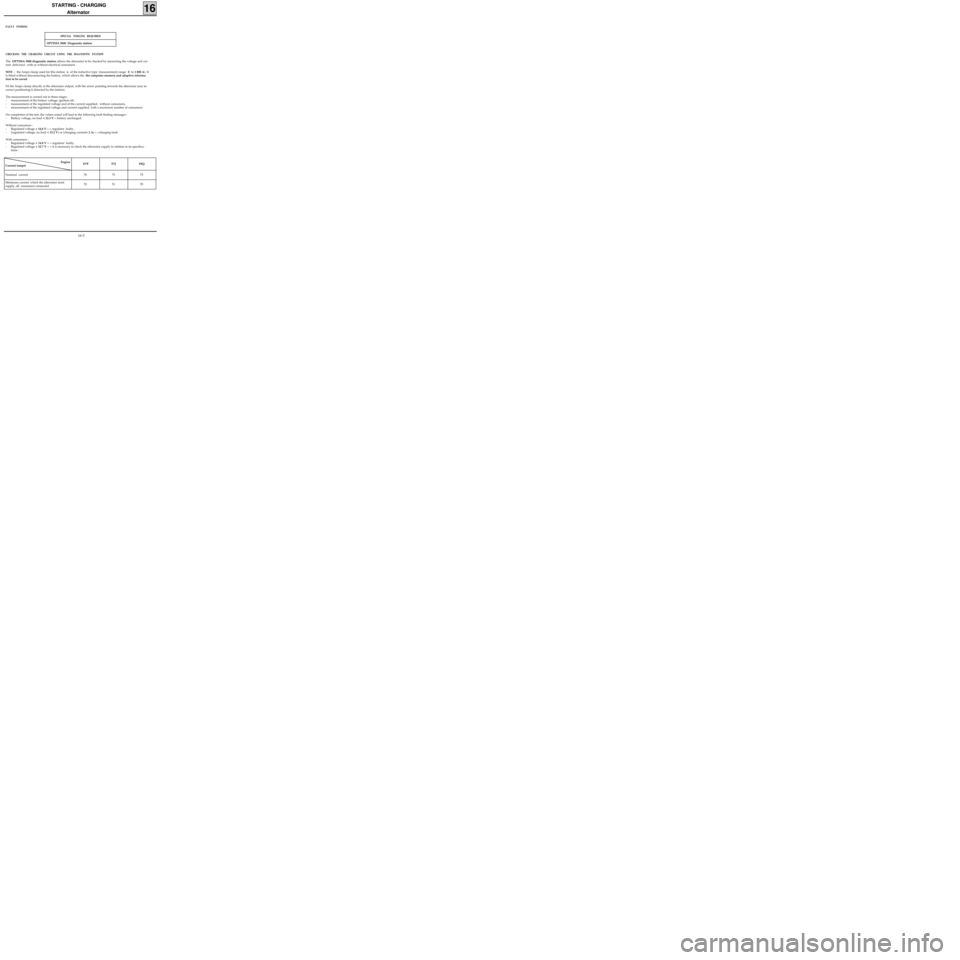
STARTING - CHARGING
Alternator
16
OPTIMA 5800 Diagnostic station
CHECKING THE CHARGING CIRCUIT USING THE DIAGNOSTIC STATION
The OPTIMA 5800 diagnostic station allows the alternator to be checked by measuring the voltage and cur-
rent delivered , with or without electrical consumers .
NOTE : the Amps clamp used for this station is of the inductive type (measurement range: 0 to 1 000 A). It
is fitted without disconnecting the battery, which allows the the computer memory and adaptive informa-
tion to be saved.
Fit the Amps clamp directly at the alternator output, with the arrow pointing towards the alternator (any in-
correct positioning is detected by the station).
The measurement is carried out in three stages :
- measurement of the battery voltage, ignition off,
- measurement of the regulated voltage and of the current supplied, without consumers,
- measurement of the regulated voltage and current supplied, with a maximum number of consumers.
On completion of the test, the values noted will lead to the following fault finding messages :
- Battery voltage, no load < 12.3 V = battery uncharged.
Without consumers :
- Regulated voltage > 14,8 V = > regulator faulty ,
- (regulated voltage, no load < 13.2 V) or (charging current< 2 A) = >charging fault.
With consumers :
- Regulated voltage > 14.8 V = > regulator faulty,
- Regulated voltage < 12.7 V = > it is necessary to check the alternator supply in relation to its specifica-
tions :
Engine
Current (amps)D7F E7J F8Q
Nominal current 70 75 75
Minimum current which the alternator must
supply, all consumers connected 53 51 55
FAULT FINDING
SPECIAL TOOLING REQUIRED
16-3
Page 143 of 208
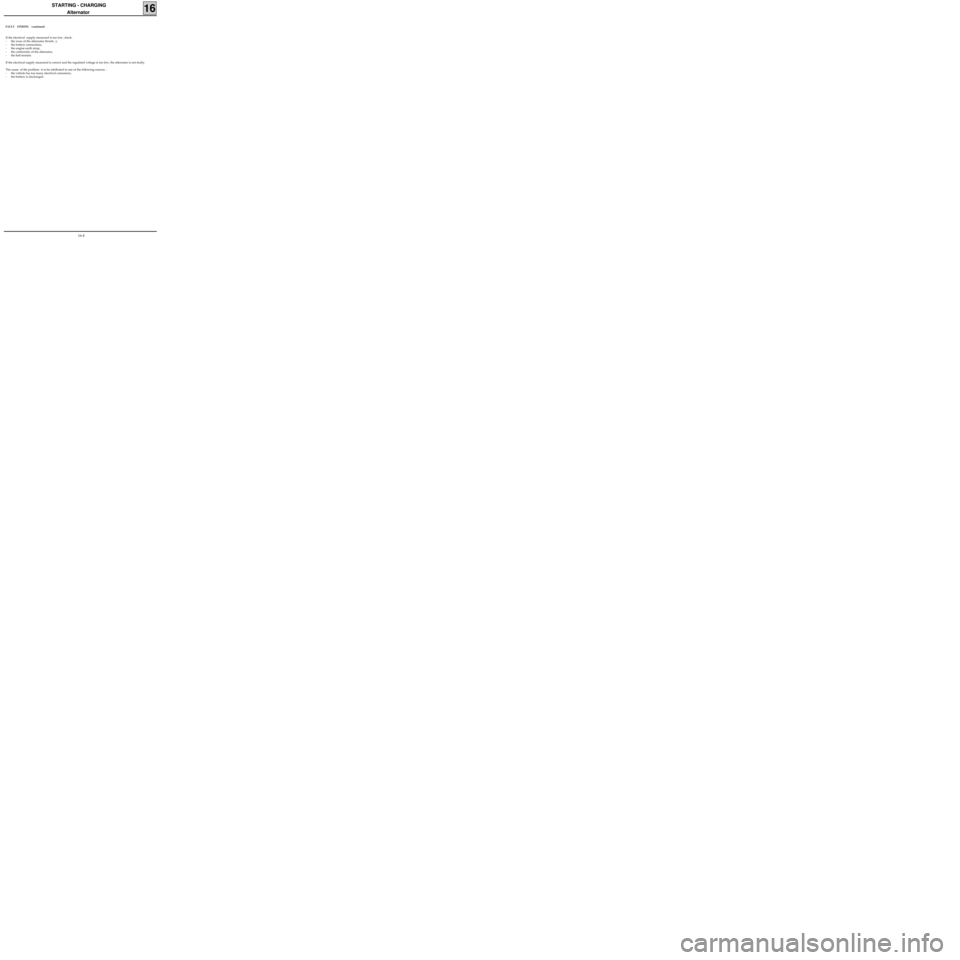
STARTING - CHARGING
Alternator
16
If the electrical supply measured is too low, check:
- the wear of the alternator (brush...),
- the battery connections,
- the engine earth strap,
- the conformity of the alternator,
- the belt tension.
If the electrical supply measured is correct and the regulated voltage is too low, the alternator is not faulty.
The cause of the problem is to be attributed to one of the following sources :
- the vehicle has too many electrical consumers,
- the battery is discharged.
FAULT FINDING (continued)
16-4
Page 144 of 208
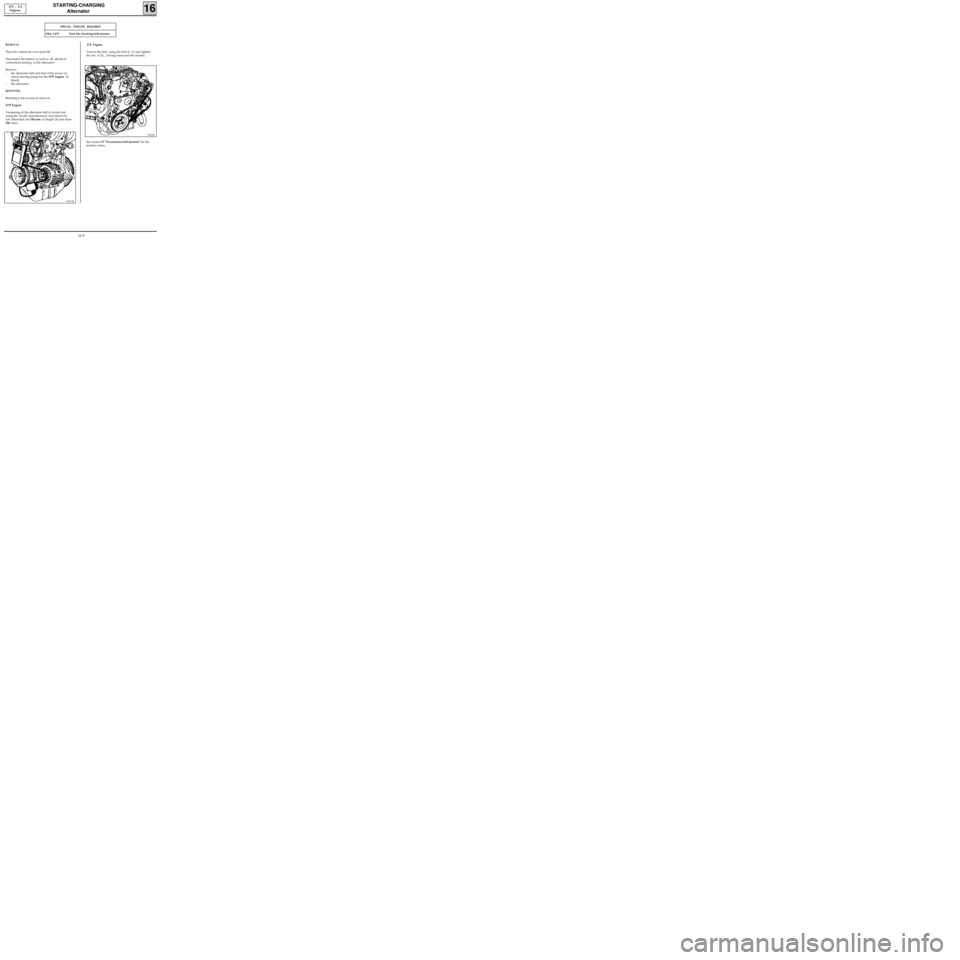
STARTING-CHARGING
Alternator
16
REMOVAL
Place the vehicle on a two post lift .
Disconnect the battery as well as all electrical
connections leading to the alternator.
Remove :
- the alternator belt and that of the power as-
sisted steering pump for the D7F engine (if
fitted),
- the alternator.
REFITTING
Refitting is the reverse of removal.
D7F Engine
Tensioning of the alternator belt is carried out
using the locally manufactured tool shown be-
low (threaded rod 100 mm in length (X) and three
M6 nuts).
D7F / E7J
Engines
SPECIAL TOOLING REQUIRED
Mot. 1273 Tool for checking belt tension
10617R
E7J Engine
Tension the belt using the bolt at (1) and tighten
the nut at (2) , having measured the tension.
13363R
See section 07 "Accessories belt tension" for the
tension values.
16-5
Page 145 of 208
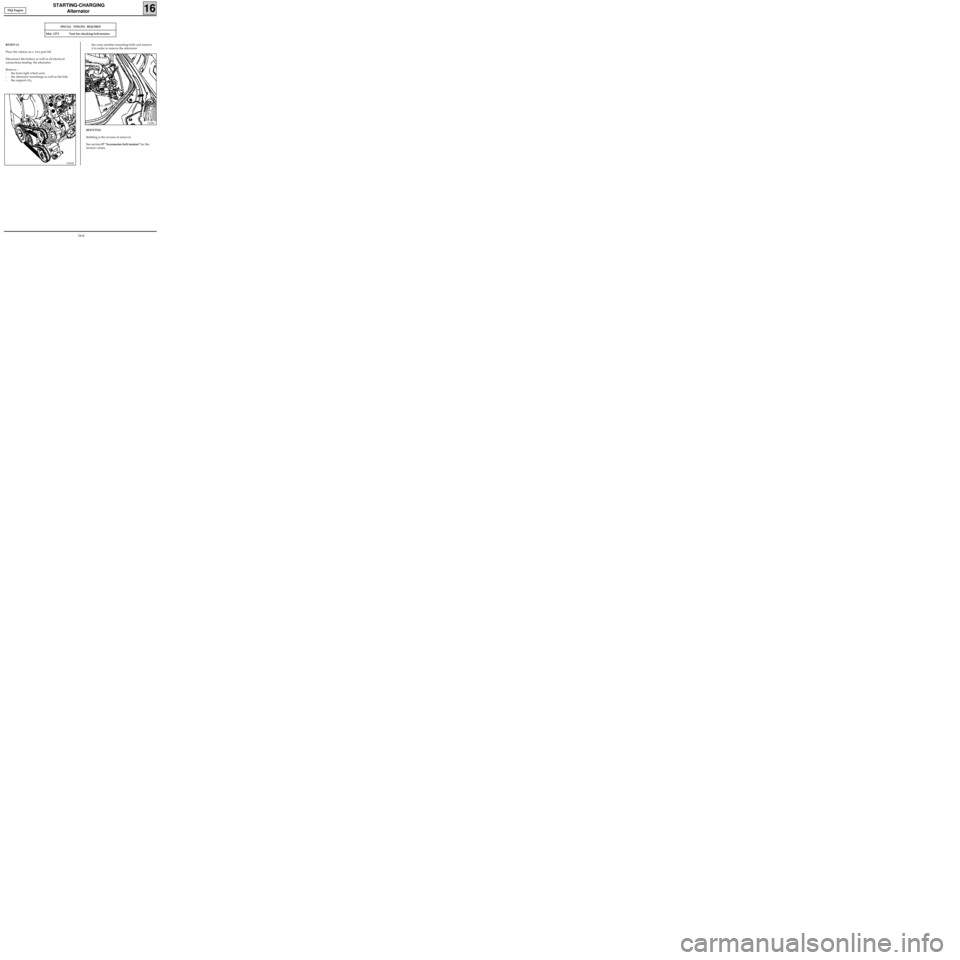
STARTING-CHARGING
Alternator
16
REMOVAL
Place the vehicle on a two post lift.
Disconnect the battery as well as all electrical
connections leading the alternator.
Remove :
- the front right wheel arch,
- the alternator mountings as well as the belt,
- the support (A),
SPECIAL TOOLING REQUIRED
Mot. 1273 Tool for checking belt tension
13092R
- the cross member mounting bolts and remove
it in order to remove the alternator.
13188S
REFITTING
Refitting is the reverse of removal.
See section 07 "Accessories belt tension" for the
tension values. F8Q Engine
16-6
Page 147 of 208
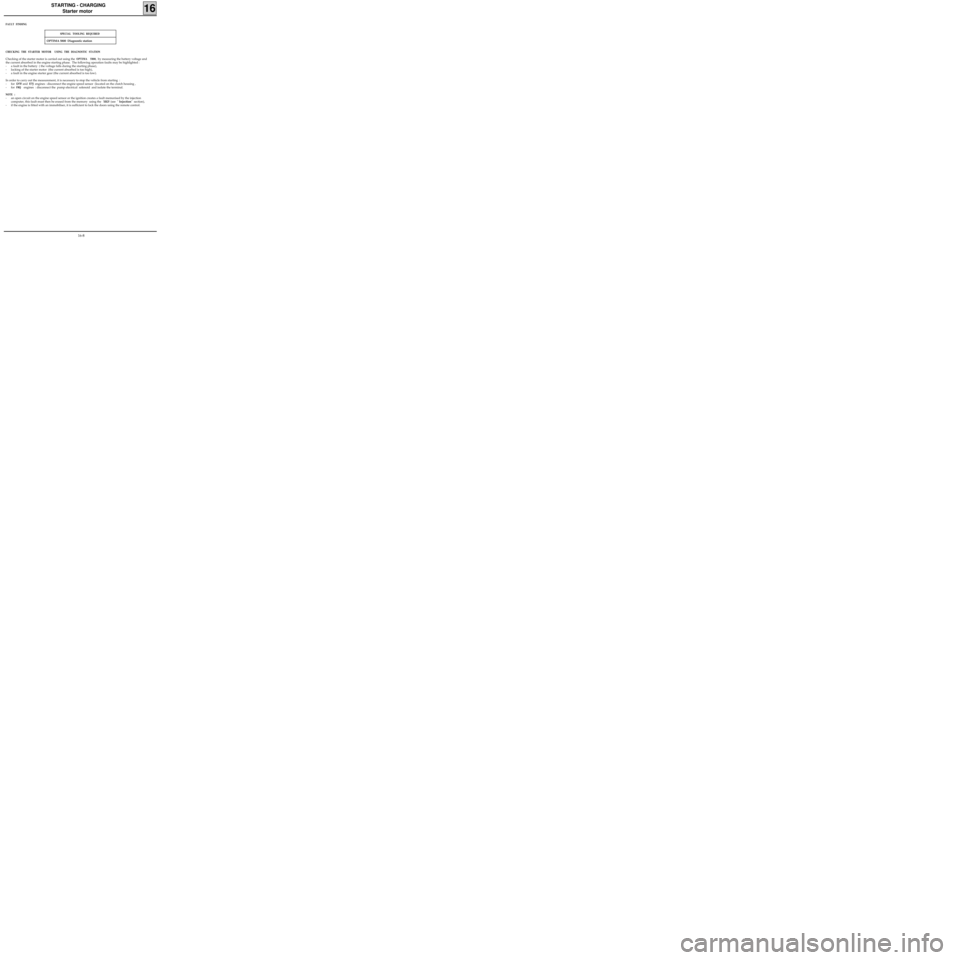
STARTING - CHARGING
Starter motor
16
OPTIMA 5800 Diagnostic station
CHECKING THE STARTER MOTOR USING THE DIAGNOSTIC STATION
Checking of the starter motor is carried out using the OPTIMA 5800, by measuring the battery voltage and
the current absorbed in the engine starting phase. The following operation faults may be highlighted :
- a fault in the battery ( the voltage falls during the starting phase),
- locking of the starter motor (the current absorbed is too high),
- a fault in the engine starter gear (the current absorbed is too low).
In order to carry out the measurement, it is necessary to stop the vehicle from starting :
- for D7F and E7J engines : disconnect the engine speed sensor (located on the clutch housing ,
- for
F8Q engines : disconnect the pump electrical solenoid and isolate the terminal.
NOTE :
- an open circuit on the engine speed sensor or the ignition creates a fault memorised by the injection
computer, this fault must then be erased from the memory using the
XR25 (see "Injection" section),
- if the engine is fitted with an immobiliser, it is sufficient to lock the doors using the remote control.
FAULT FINDING
SPECIAL TOOLING REQUIRED
16-8
Page 149 of 208
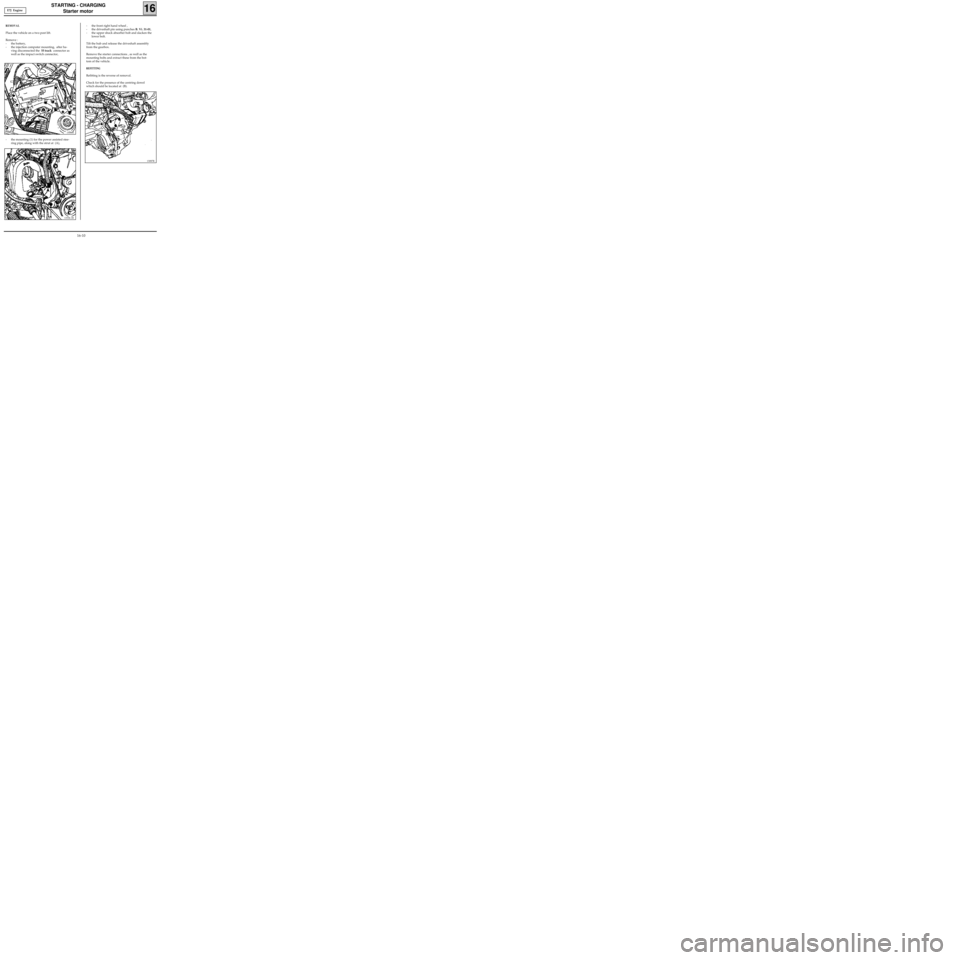
STARTING - CHARGING
Starter motor
16
REMOVAL
Place the vehicle on a two post lift.
Remove :
- the battery,
- the injection computer mounting, after ha-
ving disconnected the 55 track connector as
well as the impact switch connector,
13088S
- the mounting (1) for the power assisted stee-
ring pipe, along with the strut at (A),
13336-1R
- the front right hand wheel ,
- the driveshaft pin using punches B. Vi. 31-01,
- the upper shock absorber bolt and slacken the
lower bolt.
Tilt the hub and release the driveshaft assembly
from the gearbox.
Remove the starter connections , as well as the
mounting bolts and extract these from the bot-
tom of the vehicle.
REFITTING
Refitting is the reverse of removal.
Check for the presence of the centring dowel
which should be located at (B).
13087R
E7J Engine
16-10
Page 150 of 208
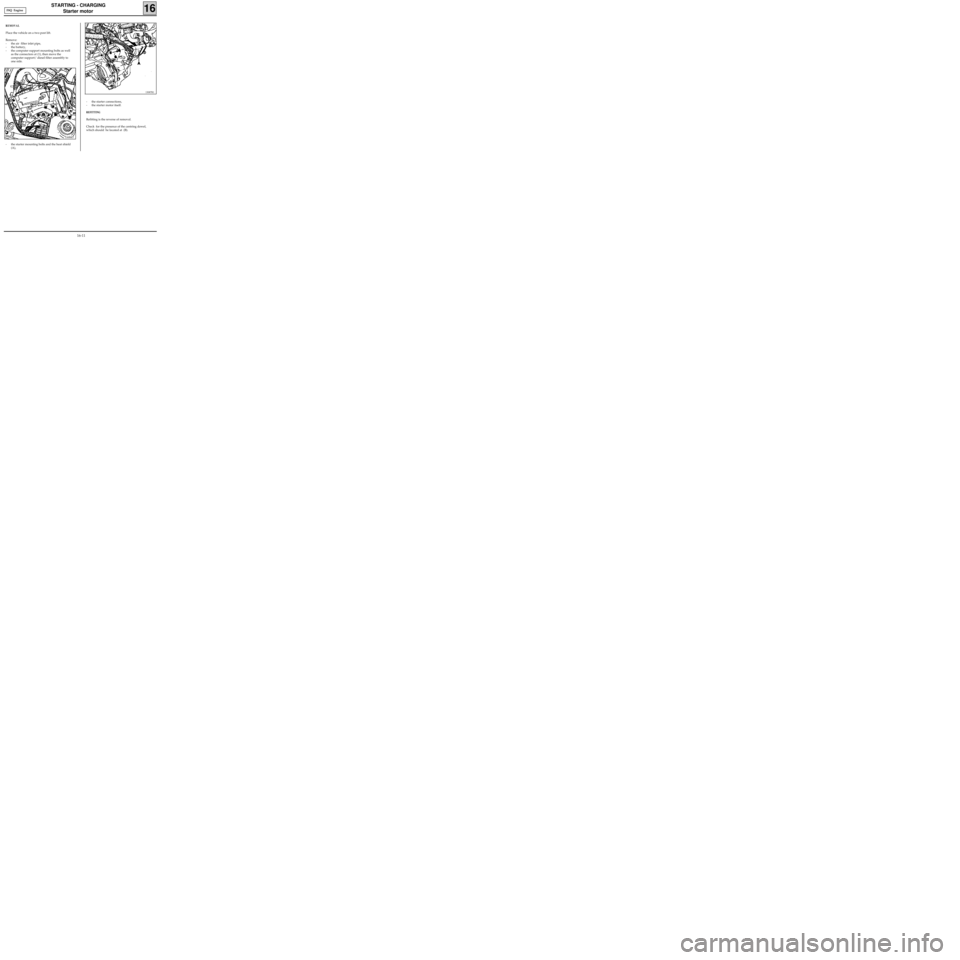
STARTING - CHARGING
Starter motor
16
REMOVAL
Place the vehicle on a two post lift.
Remove:
- the air filter inlet pipe,
- the battery,
- the computer support mounting bolts as well
as the connectors at (1), then move the
computer support/ diesel filter assembly to
one side.
13088R3
- the starter mounting bolts and the heat shield
(A),- the starter connections,
- the starter motor itself.
REFITTING
Refitting is the reverse of removal.
Check for the presence of the centring dowel,
which should be located at (B).
13087R1
F8Q Engine
16-11
Page 163 of 208
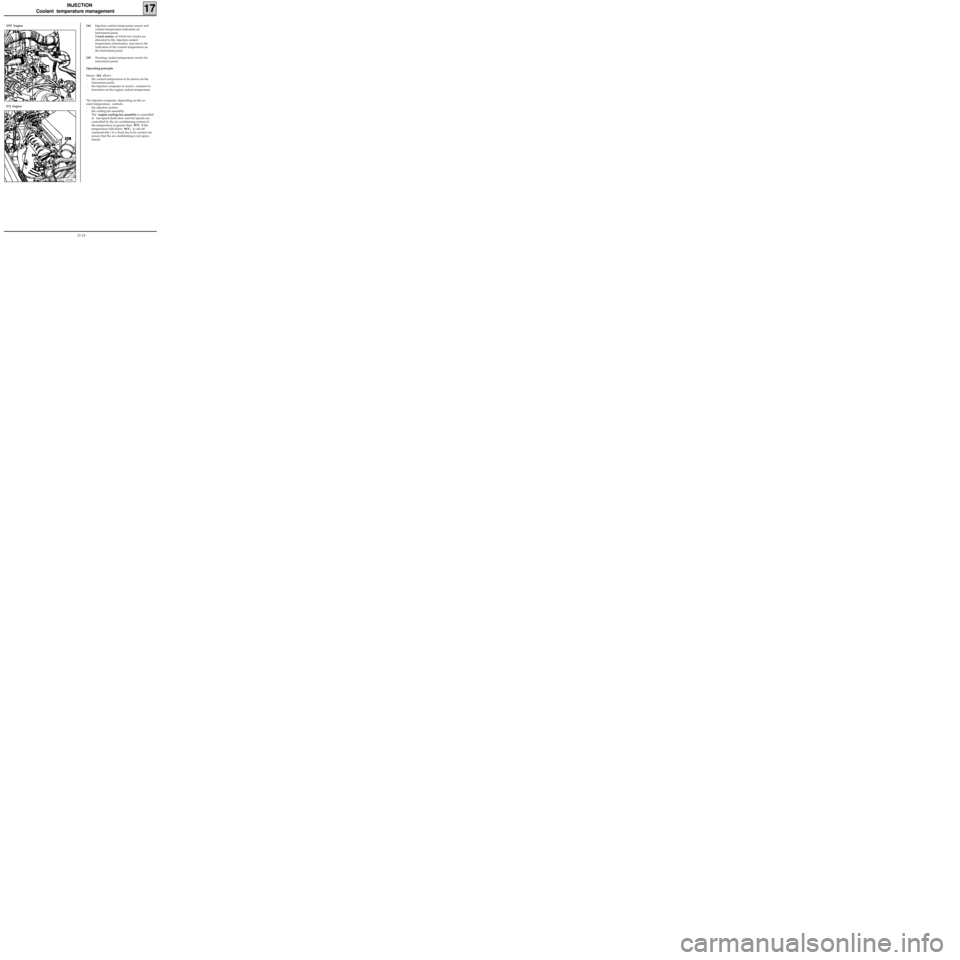
INJECTION
Coolant temperature management
244Injection coolant temperature sensor and
coolant temperature indication on
instrument panel.
3 track sensor, of which two tracks are
allocated to the injection coolant
temperature information, and one to the
indication of the coolant temperature on
the instrument panel.
259Warning coolant temperature switch for
instrument panel.
Operating principle
Sensor 244 allows :
- the coolant temperature to be shown on the
instrument panel,
- the injection computer to receive constant in-
formation on the engine coolant temperature
.
The injection computer, depending on the co-
olant temperature, controls :
- the injection system,
- the cooling fan assembly.
The engine cooling fan assembly is controlled
at fast speed (both slow and fast speeds are
controlled by the air conditioning system) if
the temperature is greater than 99°C. If the
temperature falls below 96°C, it cuts off
automatically ( if a check has to be carried out,
ensure that the air conditioning is not opera-
tional).
17
11634R2
D7F Engine
13239R1
E7J Engine
17-13
Page 176 of 208
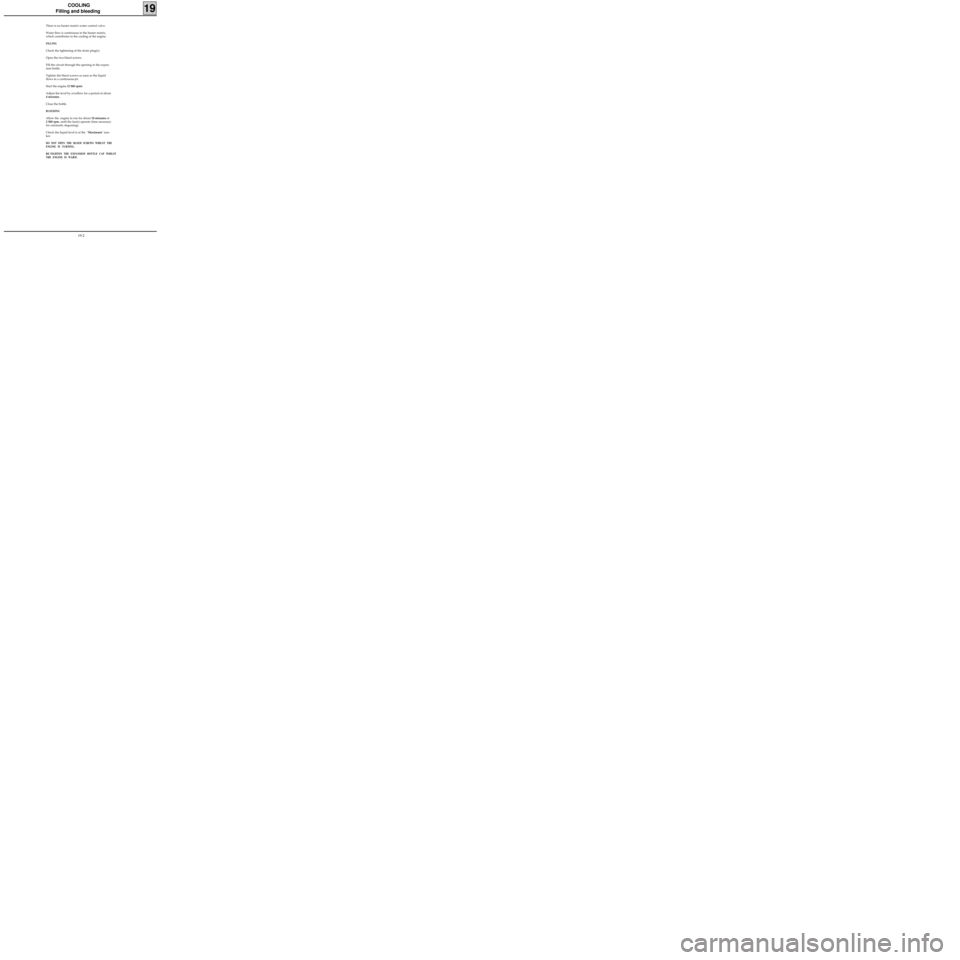
COOLING
Filling and bleeding
19
There is no heater matrix water control valve.
Water flow is continuous in the heater matrix,
which contributes to the cooling of the engine.
FILLING
Check the tightening of the drain plug(s).
Open the two bleed screws.
Fill the circuit through the opening in the expan-
sion bottle.
Tighten the bleed screws as soon as the liquid
flows in a continuous jet.
Start the engine (2 500 rpm).
Adjust the level by overflow for a period of about
4 minutes .
Close the bottle.
BLEEDING
Allow the engine to run for about 10 minutes at
2 500 rpm, until the fan(s) operate (time necessary
for automatic degassing).
Check the liquid level is at the "Maximum" mar-
ker.
DO NOT OPEN THE BLEED SCREWS WHILST THE
ENGINE IS TURNING.
RE-TIGHTEN THE EXPANSION BOTTLE CAP WHILST
THE ENGINE IS WARM.
19-2