key RENAULT KANGOO 1997 KC / 1.G Sheet Metal Work Workshop Manual
[x] Cancel search | Manufacturer: RENAULT, Model Year: 1997, Model line: KANGOO, Model: RENAULT KANGOO 1997 KC / 1.GPages: 255
Page 3 of 255
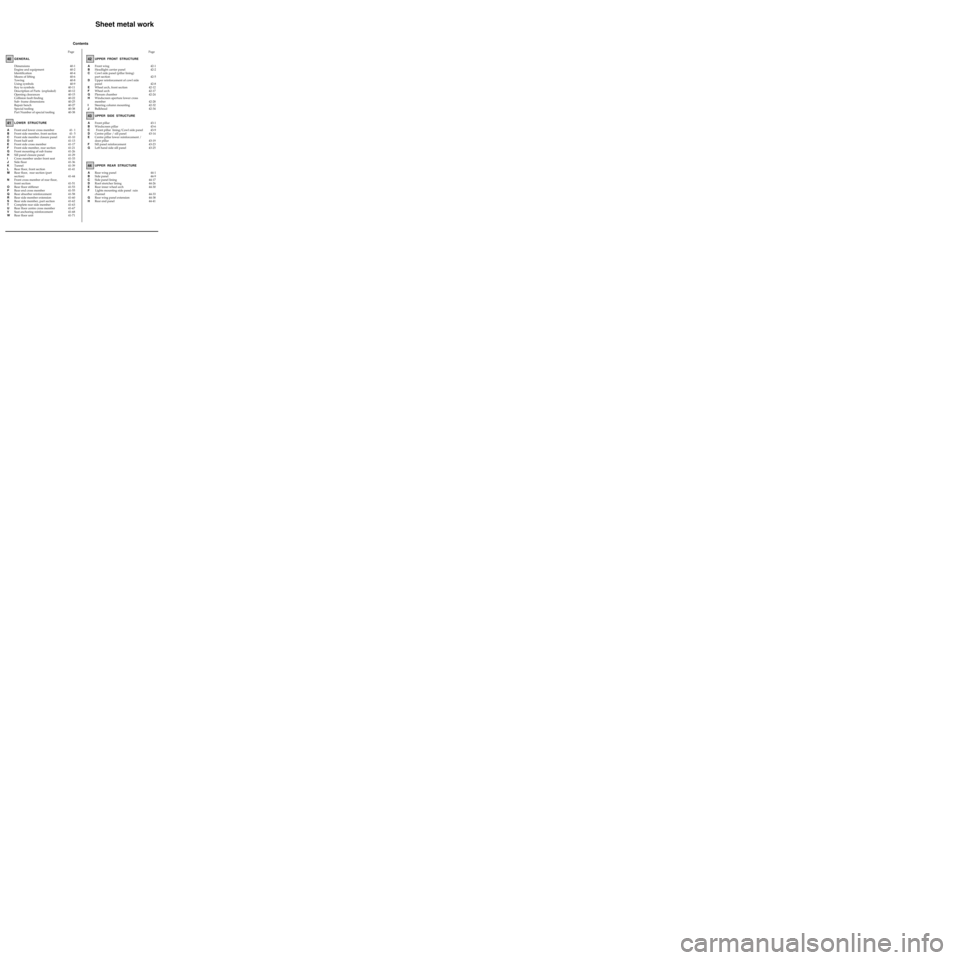
Contents
GENERAL
Dimensions
Engine and equipment
Identification
Means of lifting
Towing
Using symbols
Key to symbols
Description of Parts (exploded)
Opening clearances
Collision fault finding
Sub- frame dimensions
Repair bench
Special tooling
Part Number of special tooling40-1
40-2
40-4
40-6
40-8
40-9
40-11
40-12
40-15
40-22
40-25
40-27
40-38
40-38
LOWER STRUCTURE
41- 1
41- 5
41-10
41-13
41-17
41-21
41-26
41-29
41-33
41-36
41-39
41-41
41-44
41-51
41-53
41-55
41-58
41-60
41-62
41-63
41-67
41-68
41-71UPPER FRONT STRUCTUREPage Page40
41
42
Sheet metal work
UPPER SIDE STRUCTURE43
AFront end lower cross member
BFront side member, front section
CFront side member closure panel
DFront half unit
EFront side cross member
FFront side member, rear section
GFront mounting of sub frame
HSill panel closure panel
ICross member under front seat
JSide floor
KTunnel
LRear floor, front section
MRear floor, rear section (part
section)
NFront cross member of rear floor,
front section
ORear floor stiffener
PRear end cross member
QRear absorber reinforcement
RRear side member extension
SRear side member, part section
TComplete rear side member
URear floor centre cross member
VSeat anchoring reinforcement
WRear floor unit42-1
42-2
42-5
42-8
42-12
42-17
42-24
42-28
42-32
42-34 AFront wing
BHeadlight carrier panel
CCowl side panel (pillar lining)
part section
DUpper reinforcement of cowl side
panel
EWheel arch, front section
FWheel arch
GPlenum chamber
HWindscreen aperture lower cross
member
ISteering column mounting
JBulkhead
43-1
43-6
43-9
43-14
43-19
43-23
43-25 AFront pillar
BWindscreen pillar
C Front pillar lining/Cowl side panel
DCentre pillar / sill panel
ECentre pillar lower reinforcement /
door pillar
FSill panel reinforcement
GLeft hand side sill panel
UPPER REAR STRUCTURE
44
44-1
44-9
44-17
44-26
44-30
44-33
44-38
44-41 ARear wing panel
BSide panel
CSide panel lining
DRoof stretcher lining
ERear inner wheel arch
FLights mounting side panel rain
channel
GRear wing panel extension
HRear end panel
Page 15 of 255
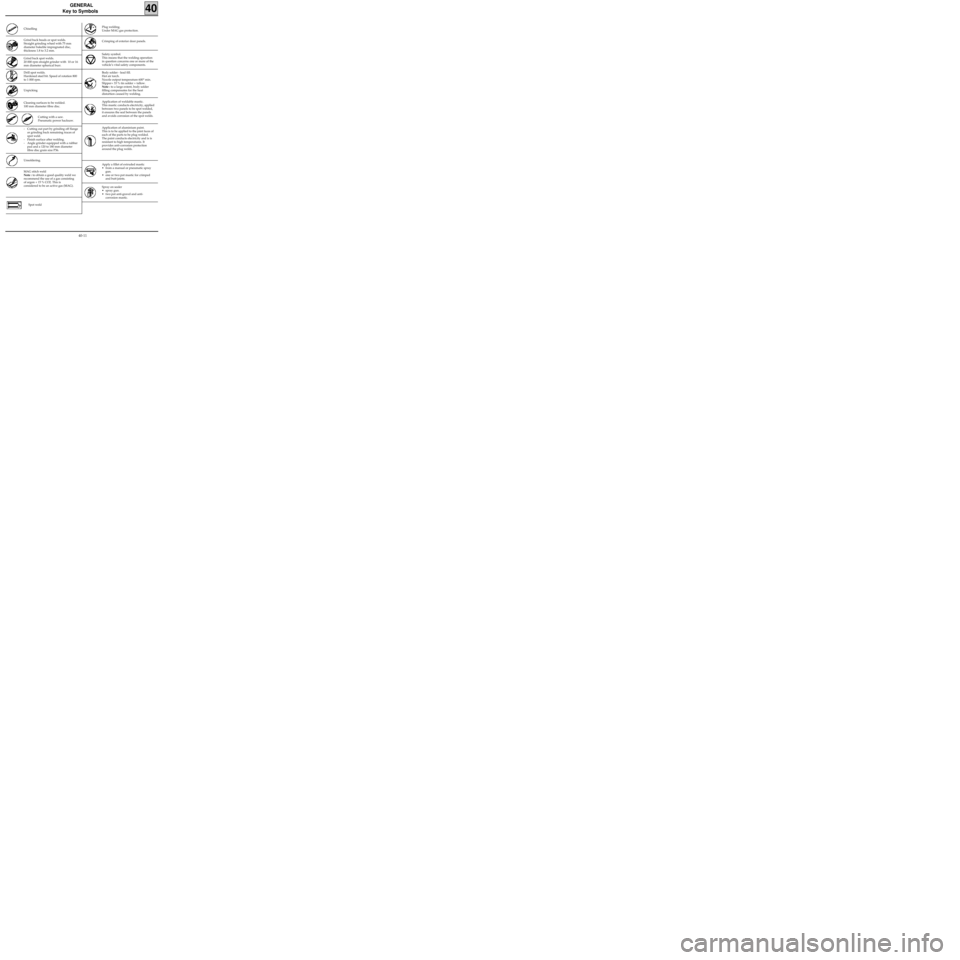
GENERAL
Key to Symbols
40
- Cutting out part by grinding off flange
or grinding back remaining traces of
spot weld.
- Finish surface after welding.
- Angle grinder equipped with a rubber
pad and a 120 to 180 mm diameter
fibre disc grain size P36. Chiselling
Grind back beads or spot welds.
Straight grinding wheel with 75 mm
diameter bakelite impregnated disc,
thickness 1.8 to 3.2 mm.
Grind back spot welds.
20 000 rpm straight grinder with 10 or 16
mm diameter spherical burr.
Drill spot welds.
Hardened steel bit. Speed of rotation 800
to 1 000 rpm.
Unpicking
Cleaning surfaces to be welded.
100 mm diameter fibre disc.
Cutting with a saw.
Pneumatic power hacksaw.
Unsoldering.
Plug welding.
Under MAG gas protection.
Crimping of exterior door panels.
Safety symbol.
This means that the welding operation
in question concerns one or more of the
vehicle’s vital safety components.
Body solder - lead fill.
Hot air torch.
Nozzle output temperature 600° min.
Slipper+ 33 % tin solder + tallow.
Note : to a large extent, body solder
filling compensates for the heat
distortion caused by welding.
Application of weldable mastic.
This mastic conducts electricity, applied
between two panels to be spot welded,
it ensures the seal between the panels
and avoids corrosion of the spot welds.
Application of aluminium paint.
This is to be applied to the joint faces of
each of the parts to be plug welded.
The paint conducts electricity and is is
resistant to high temperatures. It
provides anti-corrosion protection
around the plug welds.
Apply a fillet of extruded mastic
• from a manual or pneumatic spray
gun.
• one or two pot mastic for crimped
and butt joints.
Spray on sealer
• spray gun.
• two pot anti-gravel and anti-
corrosion mastic.
MAG stitch weld
Note : to obtain a good quality weld we
recommend the use of a gas consisting
of argon + 15 % CO2. This is
considered to be an active gas (MAG).
Spot weld
40-11