check engine RENAULT SCENIC 2011 J95 / 3.G Engine And Peripherals EDC16 Injection Workshop Manual
[x] Cancel search | Manufacturer: RENAULT, Model Year: 2011, Model line: SCENIC, Model: RENAULT SCENIC 2011 J95 / 3.GPages: 236, PDF Size: 1.32 MB
Page 198 of 236

13B - 198
DIESEL INJECTION
Fault finding - Interpretation of commands13B
V10 MR-372-J84-13B150$752.mif
EDC16 INJECTION
Program No.: C1
Vdiag No: 44, 48 and 4C
* Opening Cyclic Ratio. AC004
CONTINUED
Turbocharger control circuit check (continued)
4) Turbocharging operation check:
a) Connect vacuum pump to the hoses connected to the turbocharger control diaphragm,
– Apply a vacuum pressure of 800 mbar:
If there is a leak, replace the turbocharger (diaphragm included).
b) Check the movement of the control rod (See MR 364, 12B, Mechanical, Turbocharging).
If the control rod is sticking, replace the turbocharger.
c) Engine cold and switched off:
– Remove the turbocharger inlet duct and check that the compressor turns freely on the axis.
d) If the fault is still present:
– Check that the exhaust manifold is not leaking.
– Check that the exhaust is not blocked.
Carry out the necessary repairs.
5) Computer output check (solenoid valve connected):
This operation can only be carried out if the checks indicated in step no. 2 are not conclusive.
Using a voltmeter:
– Connect the voltmeter earth to track 2 of the solenoid valve and the positive cable to track 1.
– Clear any solenoid valve fault then run command AC004:
The voltmeter should display ten cycles of two successive voltages ~ =battery voltage X OCR* current.
either: ~2.5V (OCR for 20 %) then ~8.7V (OCR for 70 %).
Or using an oscilloscope (range 5 V/division and with time base 1 ms/division):
– Connect the earth of the oscilloscope to the battery earth and the positive test pin to track 2 of the solenoid valve.
– Clear any solenoid valve faults, then run command AC004:
the oscilloscope should display a square wave signal of 12.5 V in amplitude at a frequency of 140 Hz
(with an OCR alternating from ~ 20 to ~ 70 %).
– If the measurement is correct, replace the solenoid valve.
– If the measurement does not show any control or continuous voltage, contact the Techline.
AFTER REPAIRRestart the conformity check from the beginning.
Page 201 of 236
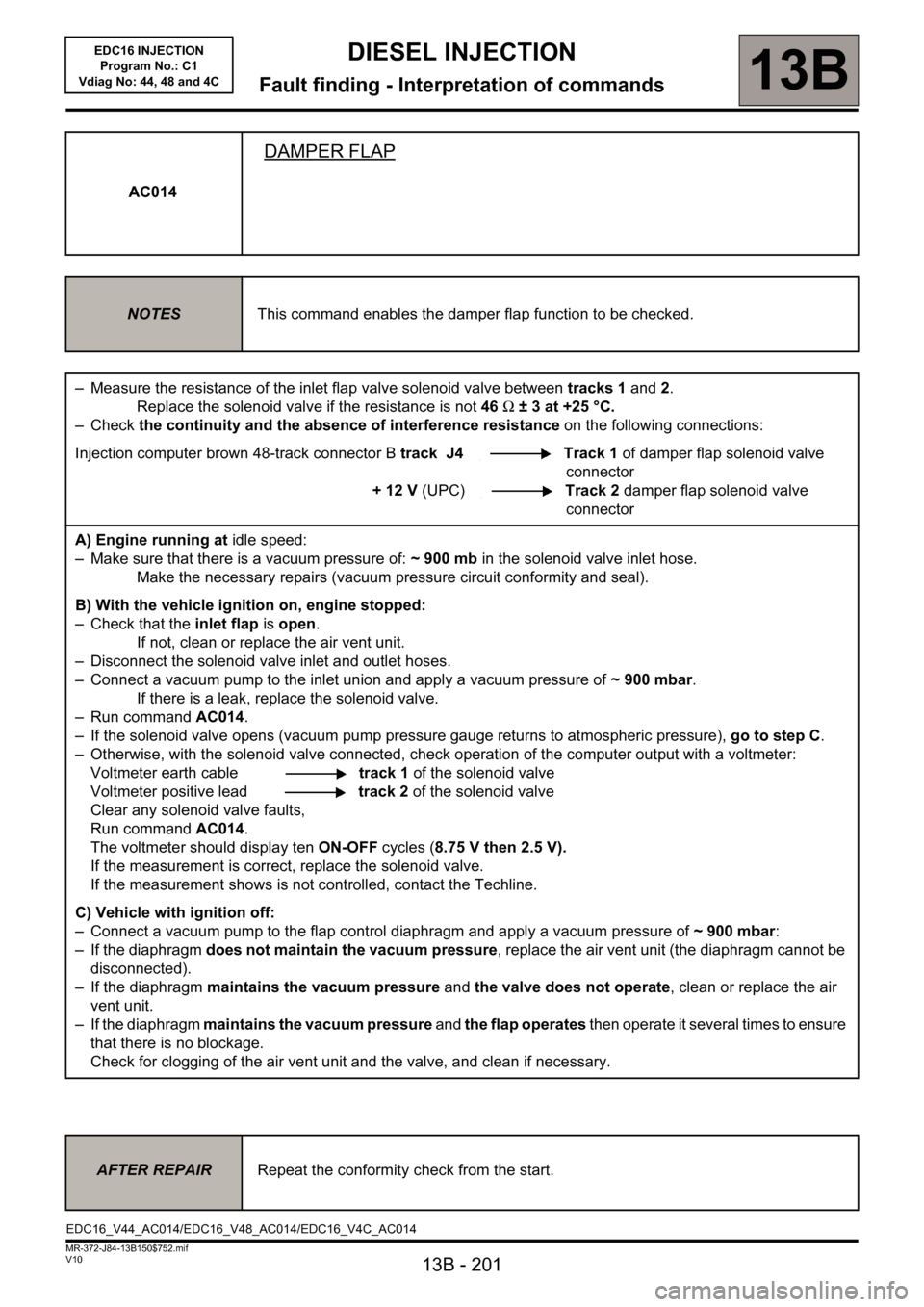
13B - 201
DIESEL INJECTION
Fault finding - Interpretation of commands13B
V10 MR-372-J84-13B150$752.mif
EDC16 INJECTION
Program No.: C1
Vdiag No: 44, 48 and 4C
AC014
DAMPER FLAP
NOTESThis command enables the damper flap function to be checked.
– Measure the resistance of the inlet flap valve solenoid valve between tracks 1 and 2.
Replace the solenoid valve if the resistance is not 46 Ω ± 3 at +25 °C.
–Check the continuity and the absence of interference resistance on the following connections:
Injection computer brown 48-track connector B track J4 Track 1 of damper flap solenoid valve
connector
+ 12 V (UPC)Track 2 damper flap solenoid valve
connector
A) Engine running at idle speed:
– Make sure that there is a vacuum pressure of: ~ 900 mb in the solenoid valve inlet hose.
Make the necessary repairs (vacuum pressure circuit conformity and seal).
B) With the vehicle ignition on, engine stopped:
– Check that the inlet flap is open.
If not, clean or replace the air vent unit.
– Disconnect the solenoid valve inlet and outlet hoses.
– Connect a vacuum pump to the inlet union and apply a vacuum pressure of ~ 900 mbar.
If there is a leak, replace the solenoid valve.
– Run command AC014.
– If the solenoid valve opens (vacuum pump pressure gauge returns to atmospheric pressure), go to step C.
– Otherwise, with the solenoid valve connected, check operation of the computer output with a voltmeter:
Voltmeter earth cabletrack 1 of the solenoid valve
Voltmeter positive leadtrack 2 of the solenoid valve
Clear any solenoid valve faults,
Run command AC014.
The voltmeter should display ten ON-OFF cycles (8.75 V then 2.5 V).
If the measurement is correct, replace the solenoid valve.
If the measurement shows is not controlled, contact the Techline.
C) Vehicle with ignition off:
– Connect a vacuum pump to the flap control diaphragm and apply a vacuum pressure of ~ 900 mbar:
– If the diaphragm does not maintain the vacuum pressure, replace the air vent unit (the diaphragm cannot be
disconnected).
– If the diaphragm maintains the vacuum pressure and the valve does not operate, clean or replace the air
vent unit.
– If the diaphragm maintains the vacuum pressure and the flap operates then operate it several times to ensure
that there is no blockage.
Check for clogging of the air vent unit and the valve, and clean if necessary.
AFTER REPAIRRepeat the conformity check from the start.
EDC16_V44_AC014/EDC16_V48_AC014/EDC16_V4C_AC014
Page 202 of 236
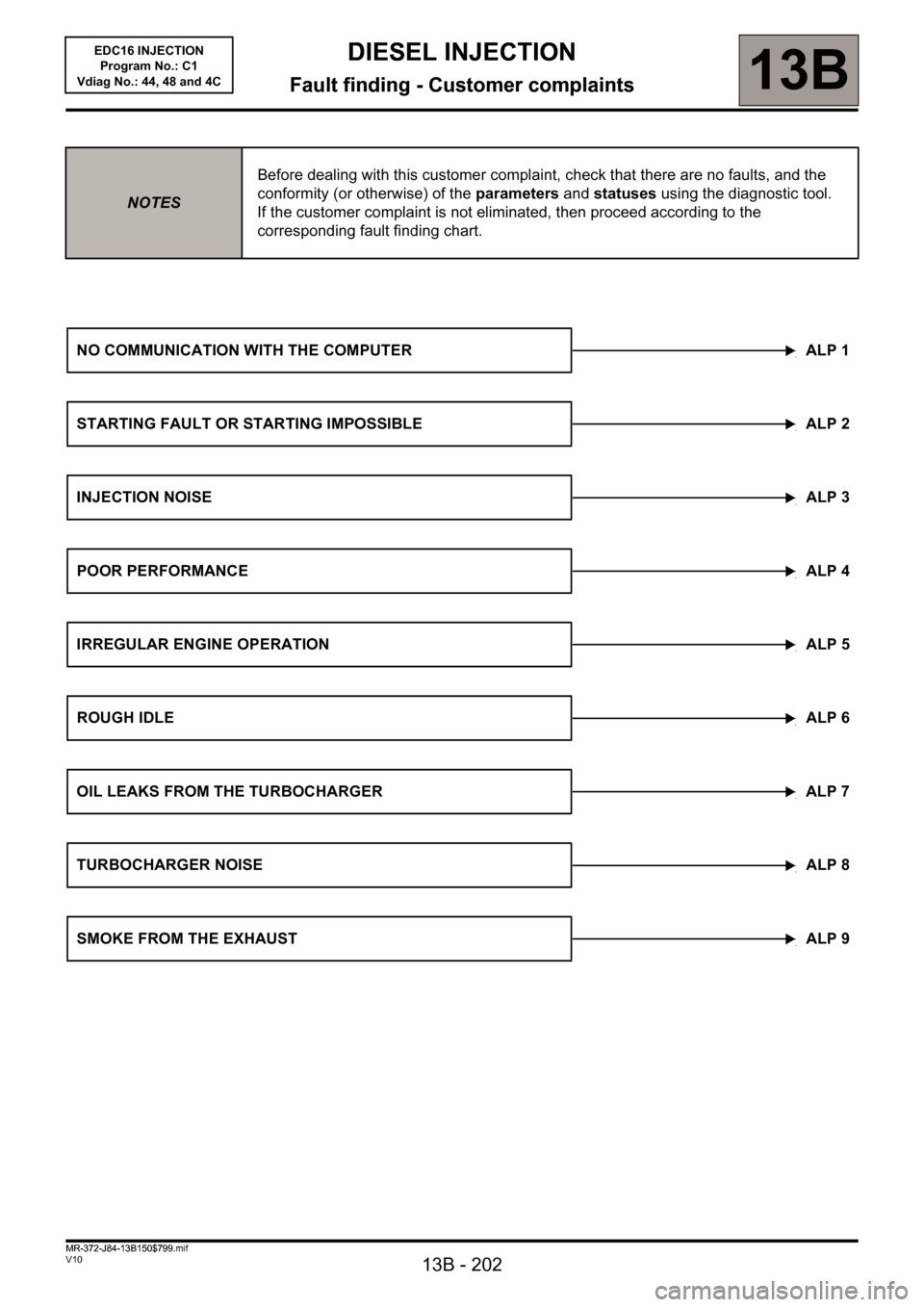
13B - 202
DIESEL INJECTION
Fault finding - Customer complaints13B
V10 MR-372-J84-13B150$799.mif
EDC16 INJECTION
Program No.: C1
Vdiag No.: 44, 48 and 4CDIESEL INJECTION
Fault finding - Customer complaints
NOTESBefore dealing with this customer complaint, check that there are no faults, and the
conformity (or otherwise) of the parameters and statuses using the diagnostic tool.
If the customer complaint is not eliminated, then proceed according to the
corresponding fault finding chart.
NO COMMUNICATION WITH THE COMPUTER ALP 1
STARTING FAULT OR STARTING IMPOSSIBLE ALP 2
INJECTION NOISEALP 3
POOR PERFORMANCEALP 4
IRREGULAR ENGINE OPERATION ALP 5
ROUGH IDLE ALP 6
OIL LEAKS FROM THE TURBOCHARGER ALP 7
TURBOCHARGER NOISEALP 8
SMOKE FROM THE EXHAUSTALP 9
MR-372-J84-13B150$799.mif
Page 205 of 236
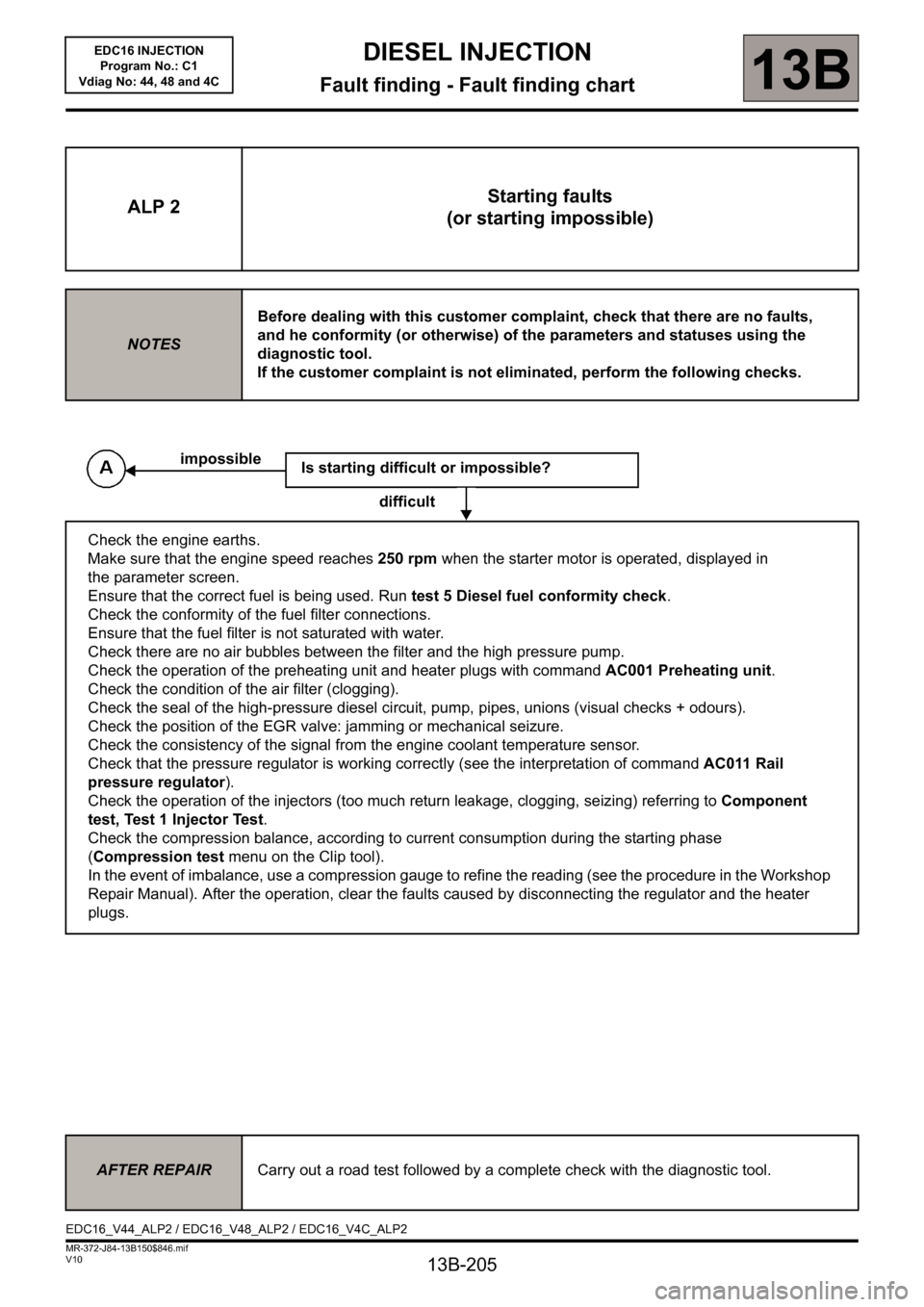
13B-205
MR-372-J84-13B150$846.mif
V10
DIESEL INJECTION
Fault finding - Fault finding chart13B
ALP 2Starting faults
(or starting impossible)
NOTESBefore dealing with this customer complaint, check that there are no faults,
and he conformity (or otherwise) of the parameters and statuses using the
diagnostic tool.
If the customer complaint is not eliminated, perform the following checks.
Is starting difficult or impossible?
difficult
Check the engine earths.
Make sure that the engine speed reaches 250 rpm when the starter motor is operated, displayed in
the parameter screen.
Ensure that the correct fuel is being used. Run test 5 Diesel fuel conformity check.
Check the conformity of the fuel filter connections.
Ensure that the fuel filter is not saturated with water.
Check there are no air bubbles between the filter and the high pressure pump.
Check the operation of the preheating unit and heater plugs with command AC001 Preheating unit.
Check the condition of the air filter (clogging).
Check the seal of the high-pressure diesel circuit, pump, pipes, unions (visual checks + odours).
Check the position of the EGR valve: jamming or mechanical seizure.
Check the consistency of the signal from the engine coolant temperature sensor.
Check that the pressure regulator is working correctly (see the interpretation of command AC011 Rail
pressure regulator).
Check the operation of the injectors (too much return leakage, clogging, seizing) referring to Component
test, Test 1 Injector Test.
Check the compression balance, according to current consumption during the starting phase
(Compression test menu on the Clip tool).
In the event of imbalance, use a compression gauge to refine the reading (see the procedure in the Workshop
Repair Manual). After the operation, clear the faults caused by disconnecting the regulator and the heater
plugs.
impossible
AFTER REPAIRCarry out a road test followed by a complete check with the diagnostic tool.
EDC16_V44_ALP2 / EDC16_V48_ALP2 / EDC16_V4C_ALP2
EDC16 INJECTION
Program No.: C1
Vdiag No: 44, 48 and 4C
Page 206 of 236
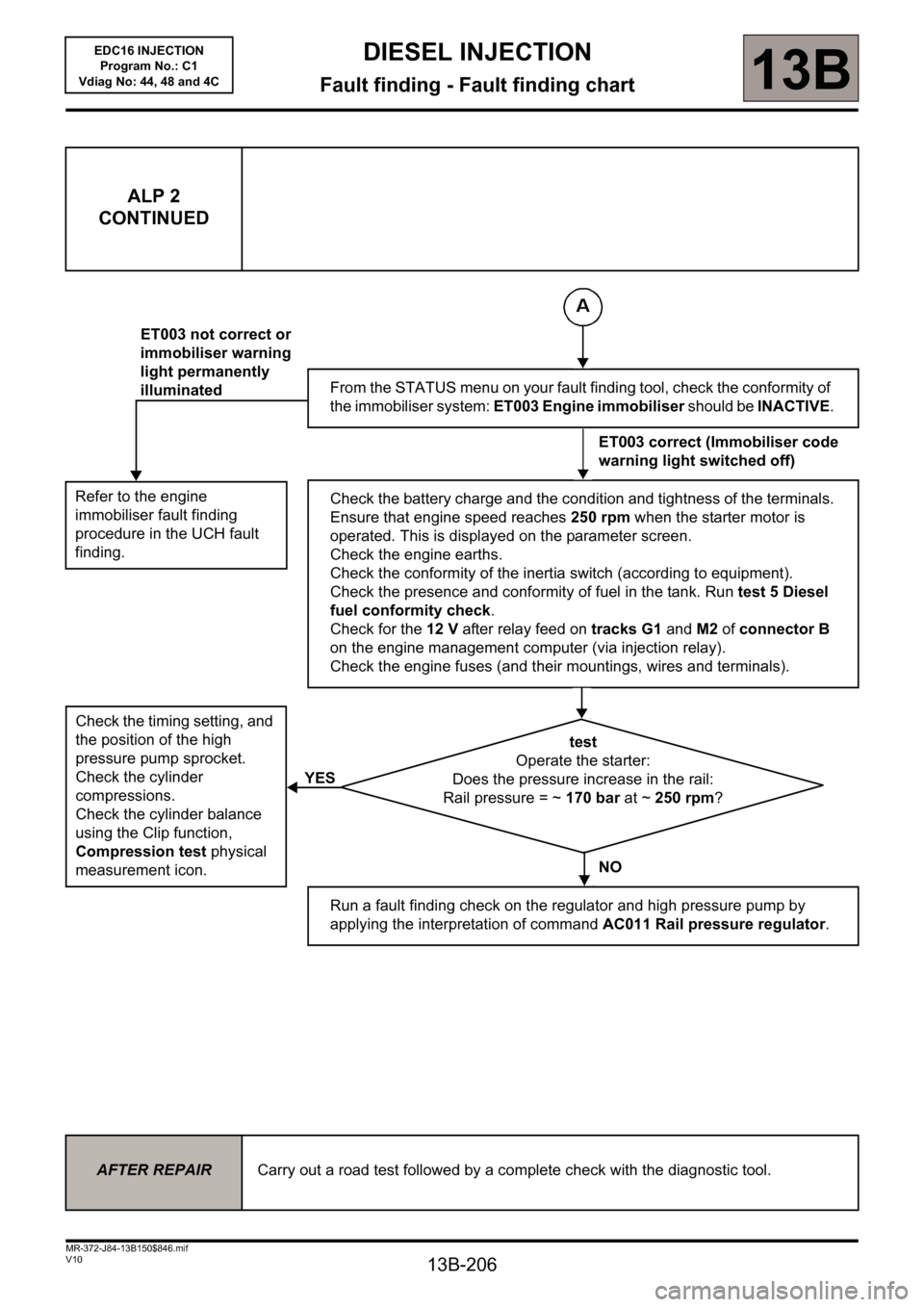
13B-206
MR-372-J84-13B150$846.mif
V10
DIESEL INJECTION
Fault finding - Fault finding chart13B
ALP 2
CONTINUED
Refer to the engine
immobiliser fault finding
procedure in the UCH fault
finding.
Check the timing setting, and
the position of the high
pressure pump sprocket.
Check the cylinder
compressions.
Check the cylinder balance
using the Clip function,
Compression test physical
measurement icon.
ET003 not correct or
immobiliser warning
light permanently
illuminated
YESFrom the STATUS menu on your fault finding tool, check the conformity of
the immobiliser system: ET003 Engine immobiliser should be INACTIVE.
ET003 correct (Immobiliser code
warning light switched off)
Check the battery charge and the condition and tightness of the terminals.
Ensure that engine speed reaches 250 rpm when the starter motor is
operated. This is displayed on the parameter screen.
Check the engine earths.
Check the conformity of the inertia switch (according to equipment).
Check the presence and conformity of fuel in the tank. Run test 5 Diesel
fuel conformity check.
Check for the 12 V after relay feed on tracks G1 and M2 of connector B
on the engine management computer (via injection relay).
Check the engine fuses (and their mountings, wires and terminals).
test
Operate the starter:
Does the pressure increase in the rail:
Rail pressure = ~ 170 bar at ~ 250 rpm?
NO
Run a fault finding check on the regulator and high pressure pump by
applying the interpretation of command AC011 Rail pressure regulator.
AFTER REPAIRCarry out a road test followed by a complete check with the diagnostic tool.
EDC16 INJECTION
Program No.: C1
Vdiag No: 44, 48 and 4C
Page 207 of 236
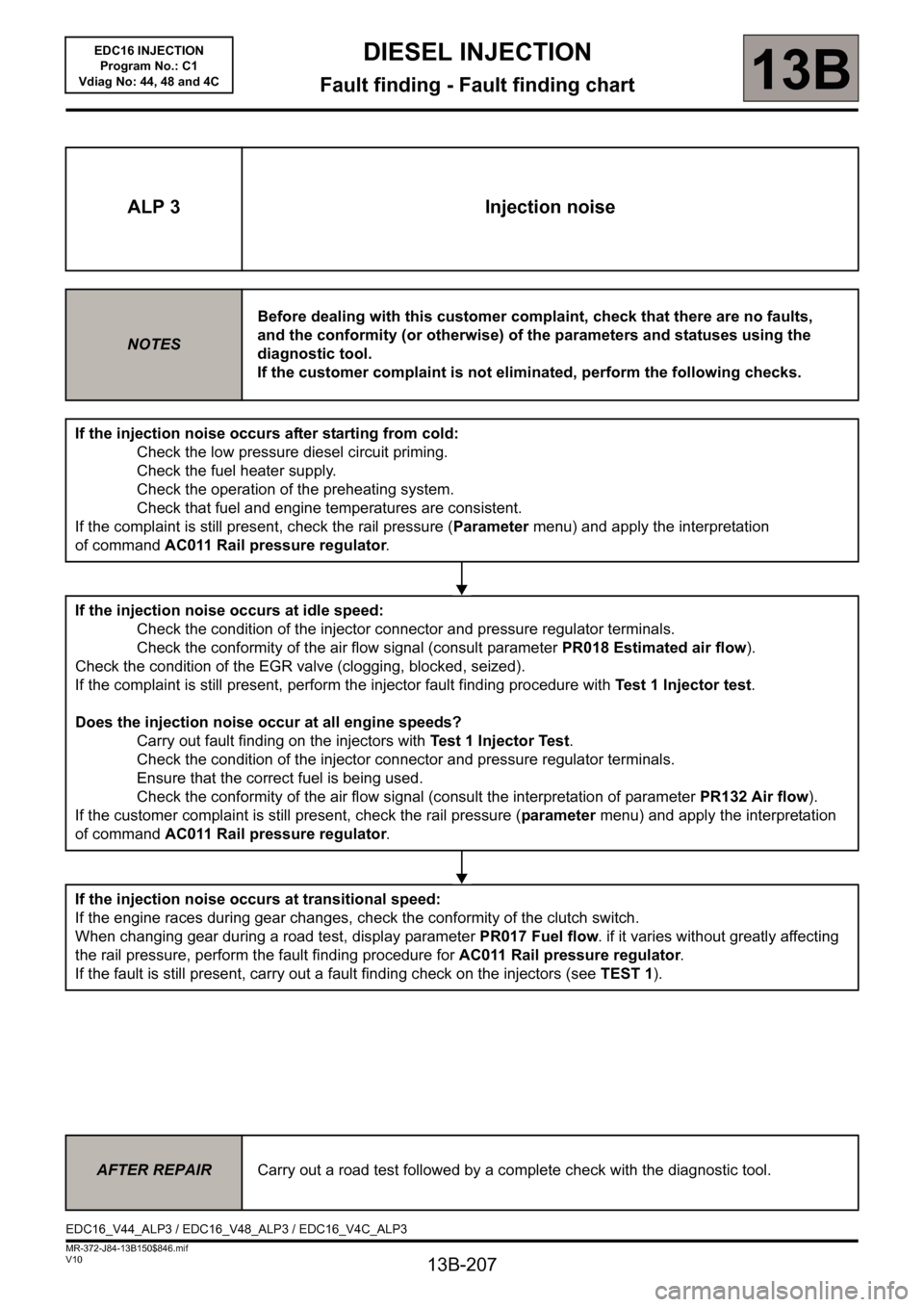
13B-207
MR-372-J84-13B150$846.mif
V10
DIESEL INJECTION
Fault finding - Fault finding chart13B
ALP 3 Injection noise
NOTESBefore dealing with this customer complaint, check that there are no faults,
and the conformity (or otherwise) of the parameters and statuses using the
diagnostic tool.
If the customer complaint is not eliminated, perform the following checks.
If the injection noise occurs after starting from cold:
Check the low pressure diesel circuit priming.
Check the fuel heater supply.
Check the operation of the preheating system.
Check that fuel and engine temperatures are consistent.
If the complaint is still present, check the rail pressure (Parameter menu) and apply the interpretation
of command AC011 Rail pressure regulator.
If the injection noise occurs at idle speed:
Check the condition of the injector connector and pressure regulator terminals.
Check the conformity of the air flow signal (consult parameter PR018 Estimated air flow).
Check the condition of the EGR valve (clogging, blocked, seized).
If the complaint is still present, perform the injector fault finding procedure with Test 1 Injector test.
Does the injection noise occur at all engine speeds?
Carry out fault finding on the injectors with Test 1 Injector Test.
Check the condition of the injector connector and pressure regulator terminals.
Ensure that the correct fuel is being used.
Check the conformity of the air flow signal (consult the interpretation of parameter PR132 Air flow).
If the customer complaint is still present, check the rail pressure (parameter menu) and apply the interpretation
of command AC011 Rail pressure regulator.
If the injection noise occurs at transitional speed:
If the engine races during gear changes, check the conformity of the clutch switch.
When changing gear during a road test, display parameter PR017 Fuel flow. if it varies without greatly affecting
the rail pressure, perform the fault finding procedure for AC011 Rail pressure regulator.
If the fault is still present, carry out a fault finding check on the injectors (seeTEST 1).
AFTER REPAIRCarry out a road test followed by a complete check with the diagnostic tool.
EDC16_V44_ALP3 / EDC16_V48_ALP3 / EDC16_V4C_ALP3EDC16 INJECTION
Program No.: C1
Vdiag No: 44, 48 and 4C
Page 208 of 236
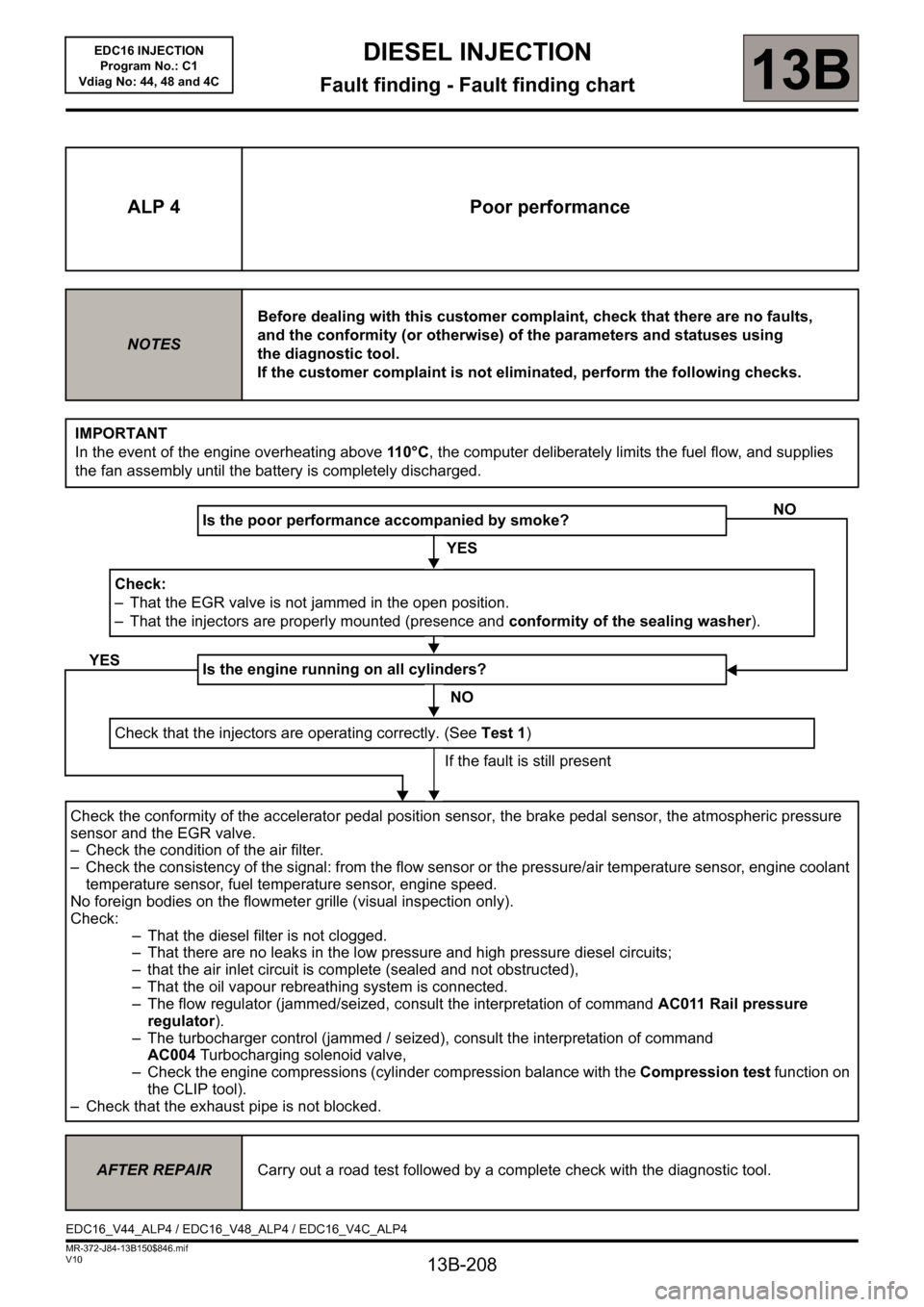
13B-208
MR-372-J84-13B150$846.mif
V10
DIESEL INJECTION
Fault finding - Fault finding chart13B
ALP 4 Poor performance
NOTESBefore dealing with this customer complaint, check that there are no faults,
and the conformity (or otherwise) of the parameters and statuses using
the diagnostic tool.
If the customer complaint is not eliminated, perform the following checks.
IMPORTANT
In the event of the engine overheating above 11 0 ° C, the computer deliberately limits the fuel flow, and supplies
the fan assembly until the battery is completely discharged.
Is the poor performance accompanied by smoke?
YES
Check:
– That the EGR valve is not jammed in the open position.
– That the injectors are properly mounted (presence and conformity of the sealing washer).
Is the engine running on all cylinders?
NO
Check that the injectors are operating correctly. (See Test 1)
If the fault is still present
Check the conformity of the accelerator pedal position sensor, the brake pedal sensor, the atmospheric pressure
sensor and the EGR valve.
– Check the condition of the air filter.
– Check the consistency of the signal: from the flow sensor or the pressure/air temperature sensor, engine coolant
temperature sensor, fuel temperature sensor, engine speed.
No foreign bodies on the flowmeter grille (visual inspection only).
Check:
– That the diesel filter is not clogged.
– That there are no leaks in the low pressure and high pressure diesel circuits;
– that the air inlet circuit is complete (sealed and not obstructed),
– That the oil vapour rebreathing system is connected.
– The flow regulator (jammed/seized, consult the interpretation of command AC011 Rail pressure
regulator).
– The turbocharger control (jammed / seized), consult the interpretation of command
AC004Turbocharging solenoid valve,
– Check the engine compressions (cylinder compression balance with the Compression test function on
the CLIP tool).
– Check that the exhaust pipe is not blocked.
NO
YES
AFTER REPAIRCarry out a road test followed by a complete check with the diagnostic tool.
EDC16_V44_ALP4 / EDC16_V48_ALP4 / EDC16_V4C_ALP4
EDC16 INJECTION
Program No.: C1
Vdiag No: 44, 48 and 4C
Page 209 of 236
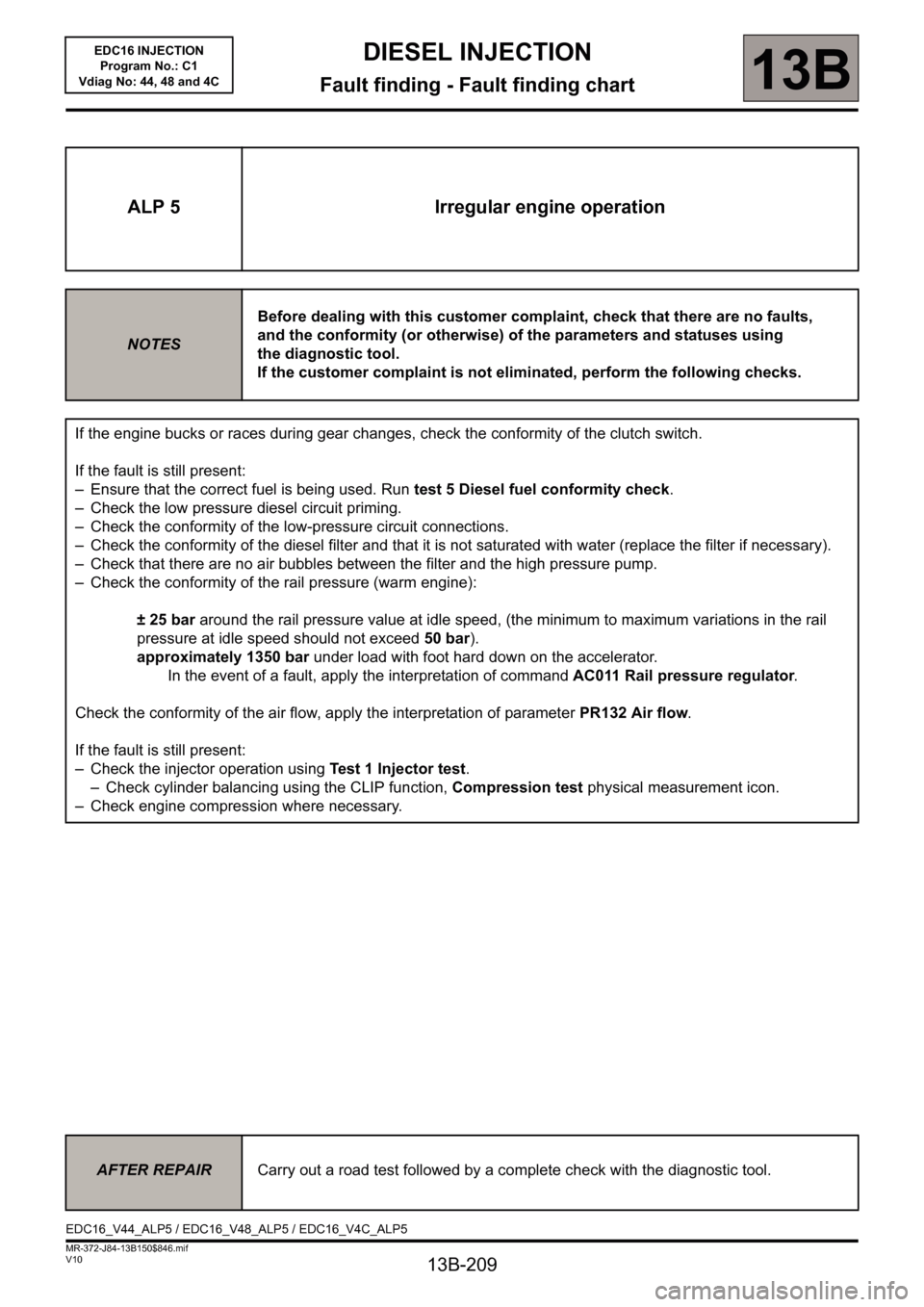
13B-209
MR-372-J84-13B150$846.mif
V10
DIESEL INJECTION
Fault finding - Fault finding chart13B
ALP 5 Irregular engine operation
NOTESBefore dealing with this customer complaint, check that there are no faults,
and the conformity (or otherwise) of the parameters and statuses using
the diagnostic tool.
If the customer complaint is not eliminated, perform the following checks.
If the engine bucks or races during gear changes, check the conformity of the clutch switch.
If the fault is still present:
– Ensure that the correct fuel is being used. Run test 5 Diesel fuel conformity check.
– Check the low pressure diesel circuit priming.
– Check the conformity of the low-pressure circuit connections.
– Check the conformity of the diesel filter and that it is not saturated with water (replace the filter if necessary).
– Check that there are no air bubbles between the filter and the high pressure pump.
– Check the conformity of the rail pressure (warm engine):
± 25 bar around the rail pressure value at idle speed, (the minimum to maximum variations in the rail
pressure at idle speed should not exceed 50 bar).
approximately 1350 bar under load with foot hard down on the accelerator.
In the event of a fault, apply the interpretation of command AC011 Rail pressure regulator.
Check the conformity of the air flow, apply the interpretation of parameter PR132 Air flow.
If the fault is still present:
– Check the injector operation using Test 1 Injector test.
– Check cylinder balancing using the CLIP function, Compression test physical measurement icon.
– Check engine compression where necessary.
AFTER REPAIRCarry out a road test followed by a complete check with the diagnostic tool.
EDC16_V44_ALP5 / EDC16_V48_ALP5 / EDC16_V4C_ALP5EDC16 INJECTION
Program No.: C1
Vdiag No: 44, 48 and 4C
Page 210 of 236
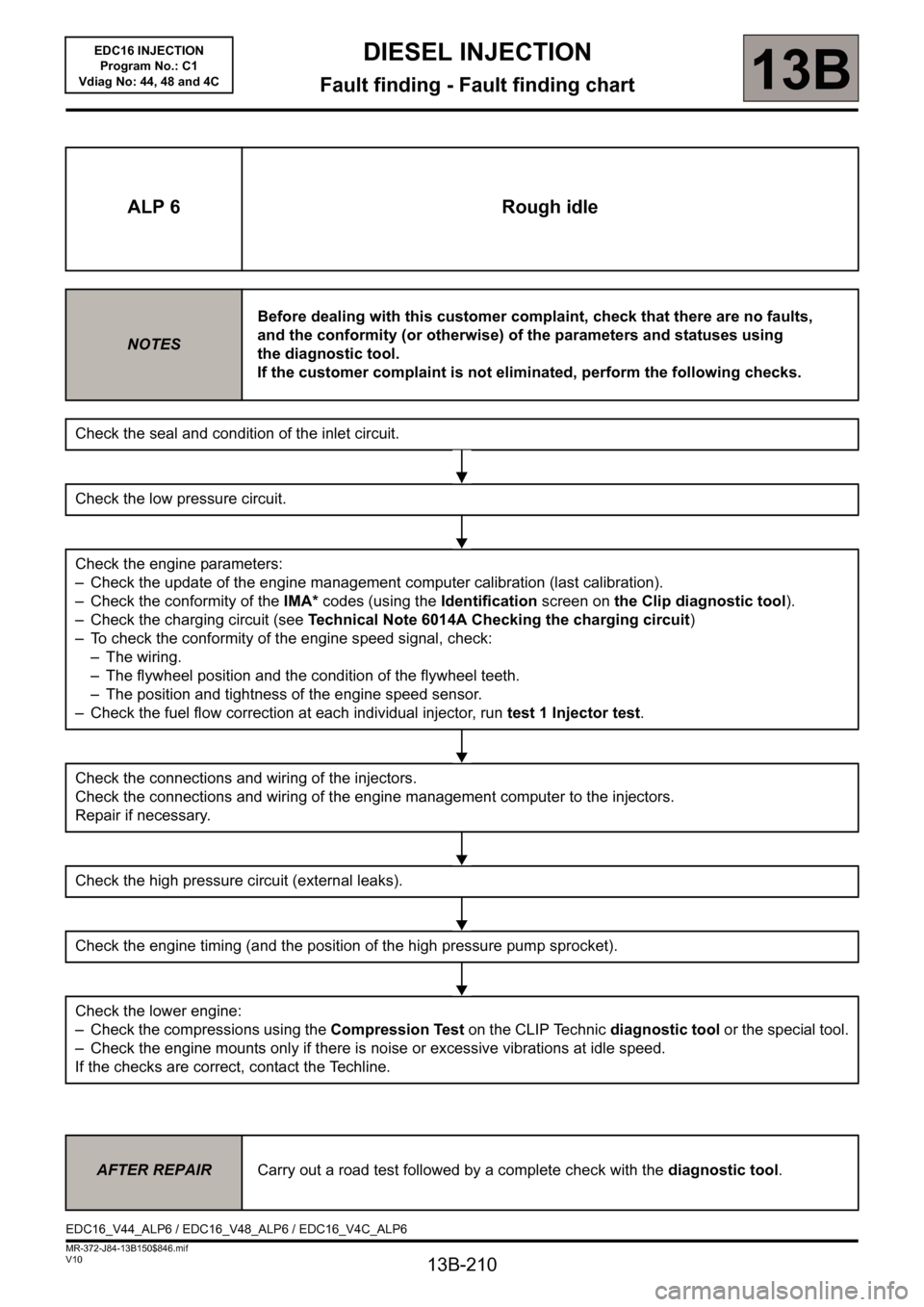
13B-210
MR-372-J84-13B150$846.mif
V10
DIESEL INJECTION
Fault finding - Fault finding chart13B
ALP 6 Rough idle
NOTESBefore dealing with this customer complaint, check that there are no faults,
and the conformity (or otherwise) of the parameters and statuses using
the diagnostic tool.
If the customer complaint is not eliminated, perform the following checks.
Check the seal and condition of the inlet circuit.
Check the low pressure circuit.
Check the engine parameters:
– Check the update of the engine management computer calibration (last calibration).
– Check the conformity of the IMA* codes (using the Identification screen on the Clip diagnostic tool).
– Check the charging circuit (see Technical Note 6014A Checking the charging circuit)
– To check the conformity of the engine speed signal, check:
– The wiring.
– The flywheel position and the condition of the flywheel teeth.
– The position and tightness of the engine speed sensor.
– Check the fuel flow correction at each individual injector, run test 1 Injector test.
Check the connections and wiring of the injectors.
Check the connections and wiring of the engine management computer to the injectors.
Repair if necessary.
Check the high pressure circuit (external leaks).
Check the engine timing (and the position of the high pressure pump sprocket).
Check the lower engine:
– Check the compressions using the Compression Test on the CLIP Technic diagnostic tool or the special tool.
– Check the engine mounts only if there is noise or excessive vibrations at idle speed.
If the checks are correct, contact the Techline.
AFTER REPAIRCarry out a road test followed by a complete check with the diagnostic tool.
EDC16_V44_ALP6 / EDC16_V48_ALP6 / EDC16_V4C_ALP6EDC16 INJECTION
Program No.: C1
Vdiag No: 44, 48 and 4C
Page 211 of 236
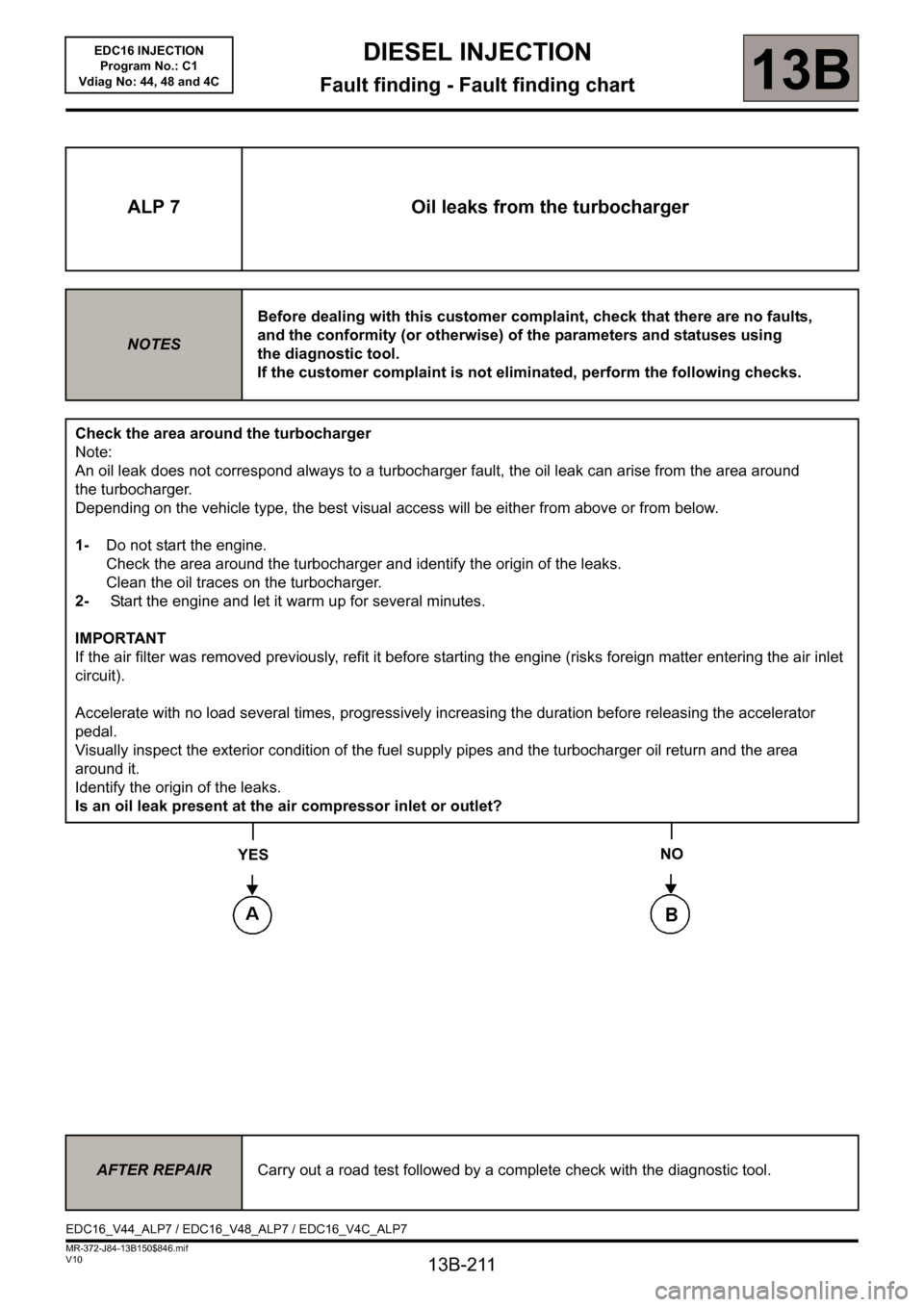
13B-211
MR-372-J84-13B150$846.mif
V10
DIESEL INJECTION
Fault finding - Fault finding chart13B
ALP 7 Oil leaks from the turbocharger
NOTESBefore dealing with this customer complaint, check that there are no faults,
and the conformity (or otherwise) of the parameters and statuses using
the diagnostic tool.
If the customer complaint is not eliminated, perform the following checks.
Check the area around the turbocharger
Note:
An oil leak does not correspond always to a turbocharger fault, the oil leak can arise from the area around
the turbocharger.
Depending on the vehicle type, the best visual access will be either from above or from below.
1-Do not start the engine.
Check the area around the turbocharger and identify the origin of the leaks.
Clean the oil traces on the turbocharger.
2- Start the engine and let it warm up for several minutes.
IMPORTANT
If the air filter was removed previously, refit it before starting the engine (risks foreign matter entering the air inlet
circuit).
Accelerate with no load several times, progressively increasing the duration before releasing the accelerator
pedal.
Visually inspect the exterior condition of the fuel supply pipes and the turbocharger oil return and the area
around it.
Identify the origin of the leaks.
Is an oil leak present at the air compressor inlet or outlet?
YES
NO
AFTER REPAIRCarry out a road test followed by a complete check with the diagnostic tool.
EDC16_V44_ALP7 / EDC16_V48_ALP7 / EDC16_V4C_ALP7EDC16 INJECTION
Program No.: C1
Vdiag No: 44, 48 and 4C