RENAULT SCENIC 2011 J95 / 3.G Engine And Peripherals EDC16 Injection Workshop Manual
Manufacturer: RENAULT, Model Year: 2011, Model line: SCENIC, Model: RENAULT SCENIC 2011 J95 / 3.GPages: 236, PDF Size: 1.32 MB
Page 211 of 236
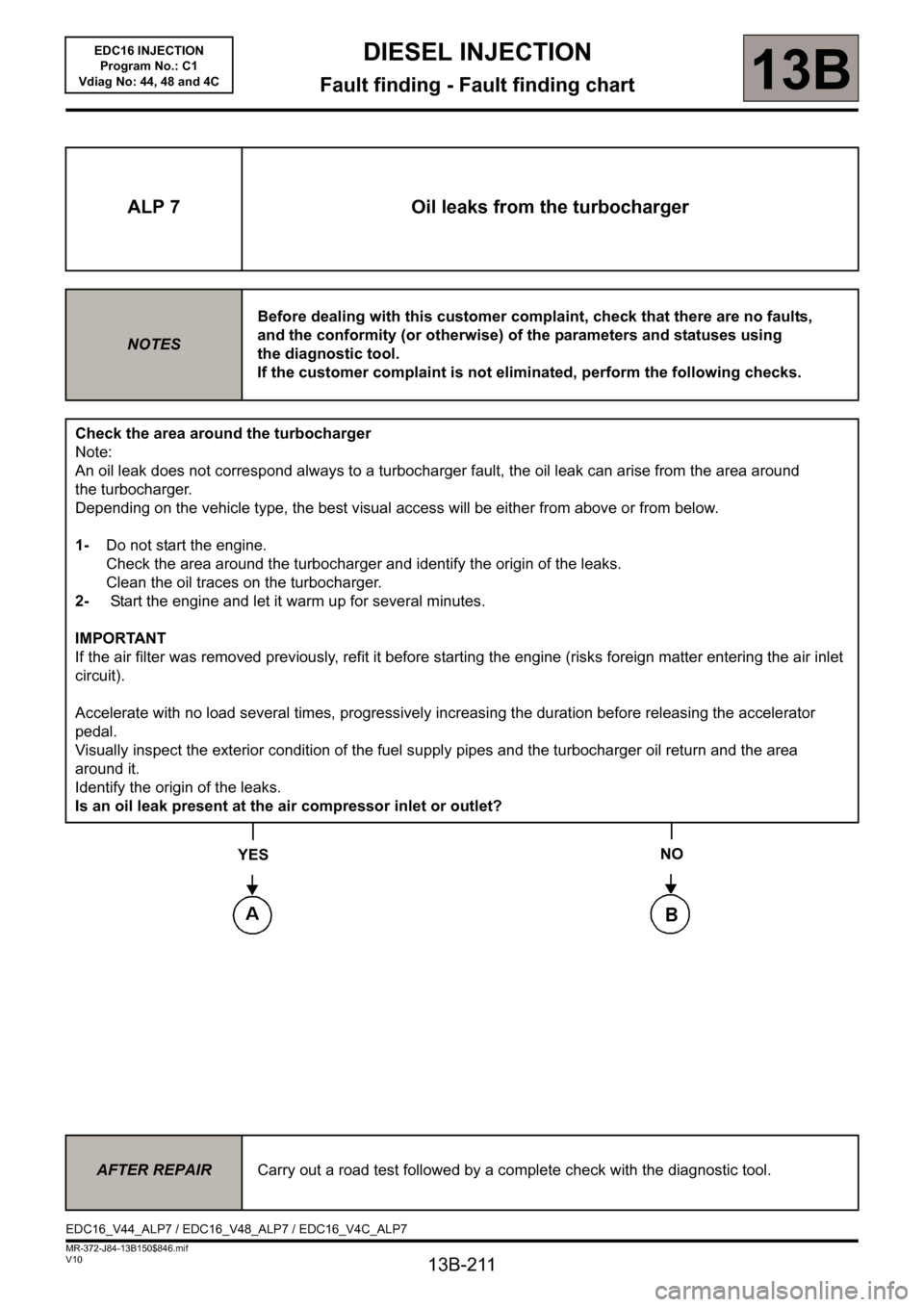
13B-211
MR-372-J84-13B150$846.mif
V10
DIESEL INJECTION
Fault finding - Fault finding chart13B
ALP 7 Oil leaks from the turbocharger
NOTESBefore dealing with this customer complaint, check that there are no faults,
and the conformity (or otherwise) of the parameters and statuses using
the diagnostic tool.
If the customer complaint is not eliminated, perform the following checks.
Check the area around the turbocharger
Note:
An oil leak does not correspond always to a turbocharger fault, the oil leak can arise from the area around
the turbocharger.
Depending on the vehicle type, the best visual access will be either from above or from below.
1-Do not start the engine.
Check the area around the turbocharger and identify the origin of the leaks.
Clean the oil traces on the turbocharger.
2- Start the engine and let it warm up for several minutes.
IMPORTANT
If the air filter was removed previously, refit it before starting the engine (risks foreign matter entering the air inlet
circuit).
Accelerate with no load several times, progressively increasing the duration before releasing the accelerator
pedal.
Visually inspect the exterior condition of the fuel supply pipes and the turbocharger oil return and the area
around it.
Identify the origin of the leaks.
Is an oil leak present at the air compressor inlet or outlet?
YES
NO
AFTER REPAIRCarry out a road test followed by a complete check with the diagnostic tool.
EDC16_V44_ALP7 / EDC16_V48_ALP7 / EDC16_V4C_ALP7EDC16 INJECTION
Program No.: C1
Vdiag No: 44, 48 and 4C
Page 212 of 236
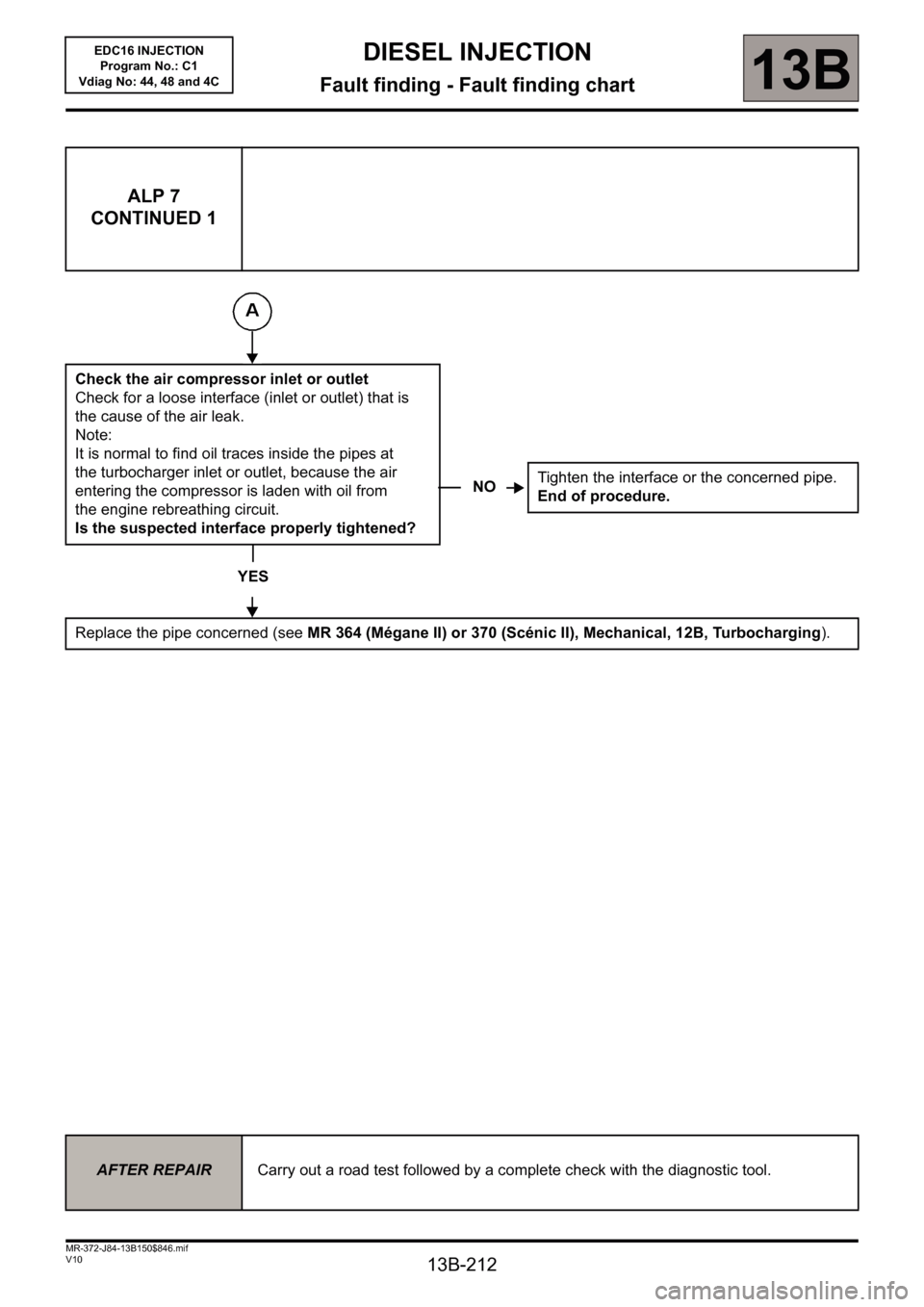
13B-212
MR-372-J84-13B150$846.mif
V10
DIESEL INJECTION
Fault finding - Fault finding chart13B
ALP 7
CONTINUED 1
Check the air compressor inlet or outlet
Check for a loose interface (inlet or outlet) that is
the cause of the air leak.
Note:
It is normal to find oil traces inside the pipes at
the turbocharger inlet or outlet, because the air
entering the compressor is laden with oil from
the engine rebreathing circuit.
Is the suspected interface properly tightened?
YES
Replace the pipe concerned (see MR 364 (Mégane II) or 370 (Scénic II), Mechanical, 12B, Turbocharging).
NOTighten the interface or the concerned pipe.
End of procedure.
AFTER REPAIRCarry out a road test followed by a complete check with the diagnostic tool.
EDC16 INJECTION
Program No.: C1
Vdiag No: 44, 48 and 4C
Page 213 of 236
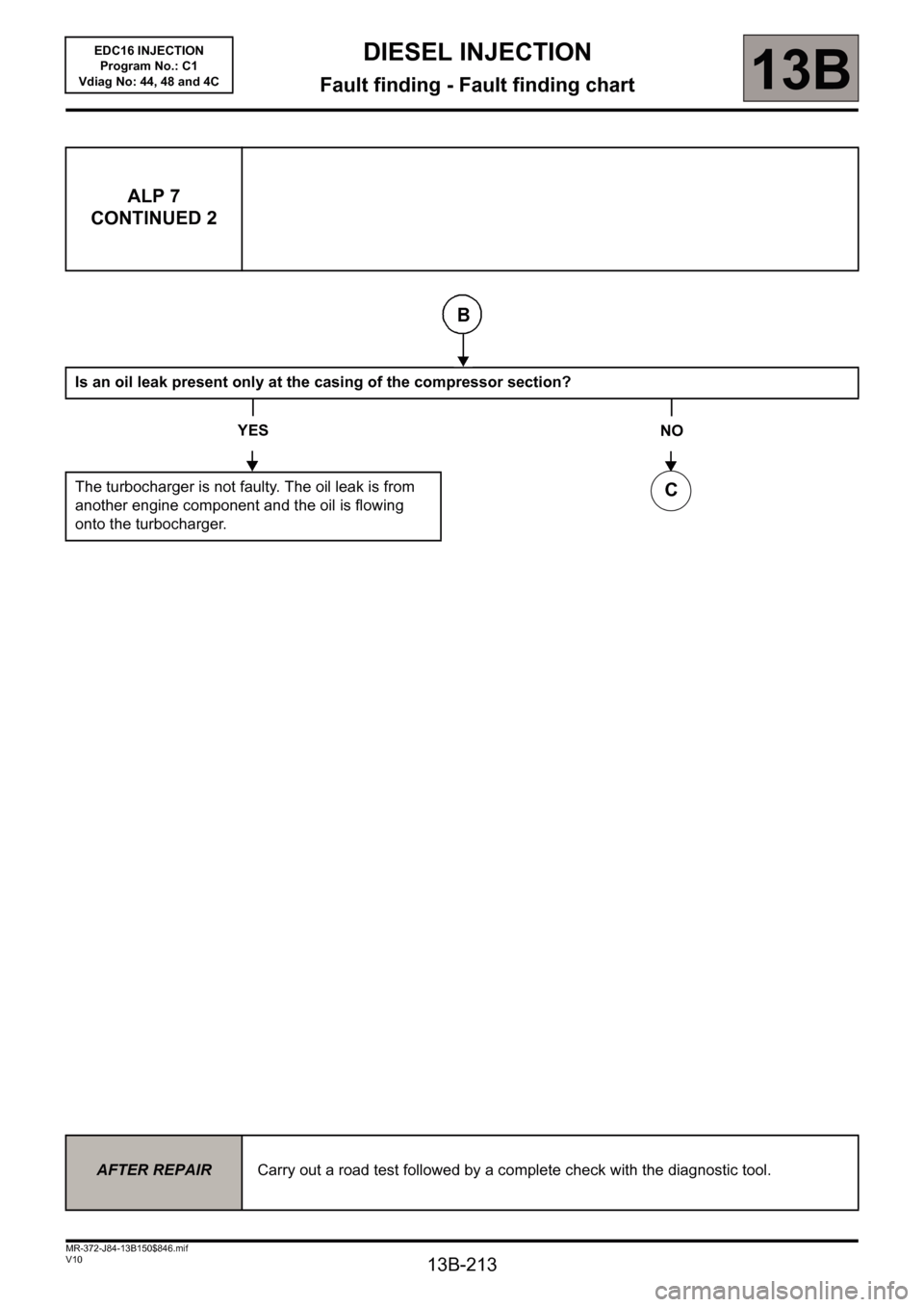
13B-213
MR-372-J84-13B150$846.mif
V10
DIESEL INJECTION
Fault finding - Fault finding chart13B
ALP 7
CONTINUED 2
Is an oil leak present only at the casing of the compressor section?
YES
The turbocharger is not faulty. The oil leak is from
another engine component and the oil is flowing
onto the turbocharger.
NO
AFTER REPAIRCarry out a road test followed by a complete check with the diagnostic tool.
C
EDC16 INJECTION
Program No.: C1
Vdiag No: 44, 48 and 4C
Page 214 of 236
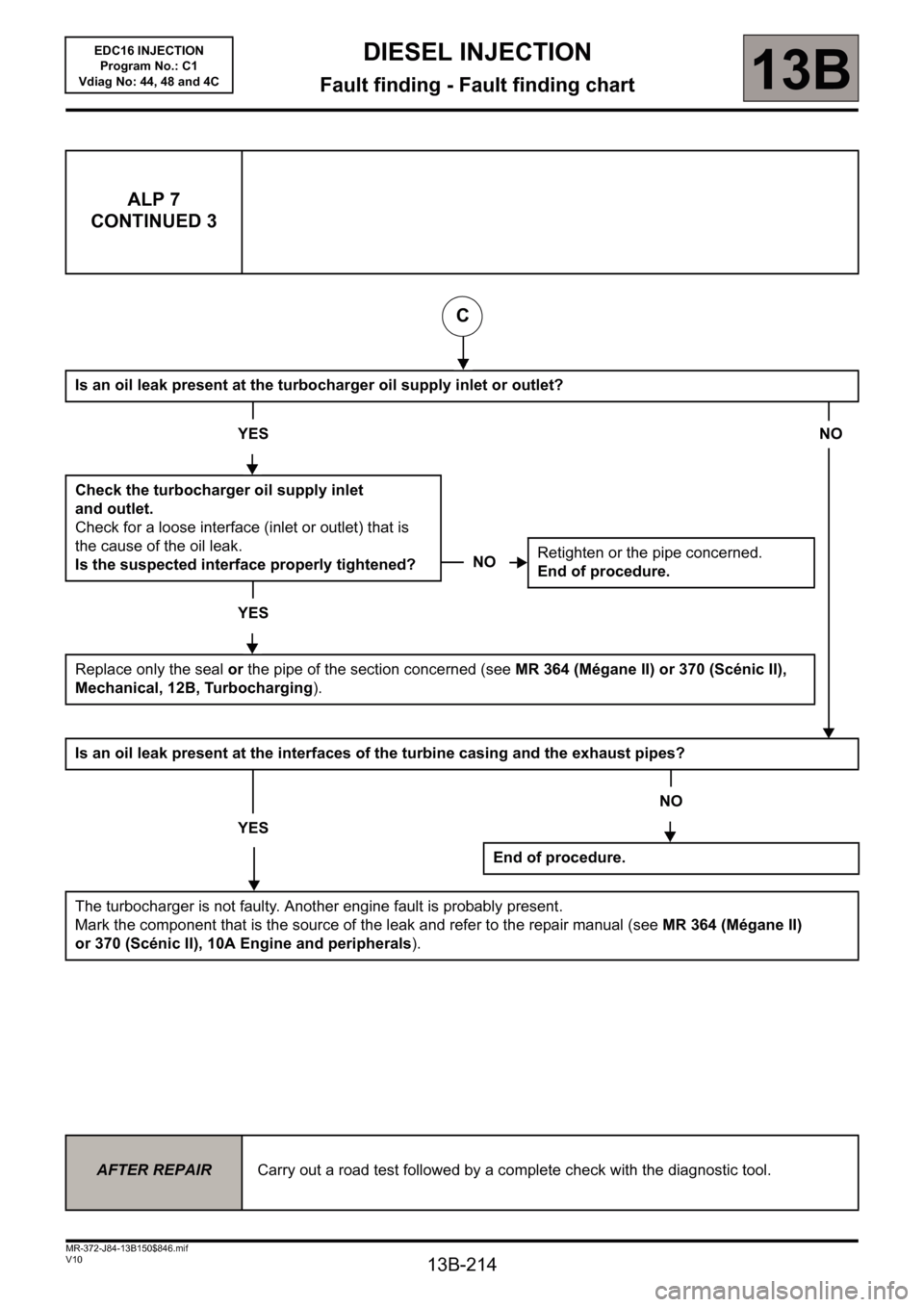
13B-214
MR-372-J84-13B150$846.mif
V10
DIESEL INJECTION
Fault finding - Fault finding chart13B
ALP 7
CONTINUED 3
Is an oil leak present at the turbocharger oil supply inlet or outlet?
YESNO
Check the turbocharger oil supply inlet
and outlet.
Check for a loose interface (inlet or outlet) that is
the cause of the oil leak.
Is the suspected interface properly tightened?
YES
Replace only the seal or the pipe of the section concerned (see MR 364 (Mégane II) or 370 (Scénic II),
Mechanical, 12B, Turbocharging).
Is an oil leak present at the interfaces of the turbine casing and the exhaust pipes?
YES
The turbocharger is not faulty. Another engine fault is probably present.
Mark the component that is the source of the leak and refer to the repair manual (see MR 364 (Mégane II)
or 370 (Scénic II), 10A Engine and peripherals).
NORetighten or the pipe concerned.
End of procedure.
NO
End of procedure.
AFTER REPAIRCarry out a road test followed by a complete check with the diagnostic tool.
C
EDC16 INJECTION
Program No.: C1
Vdiag No: 44, 48 and 4C
Page 215 of 236
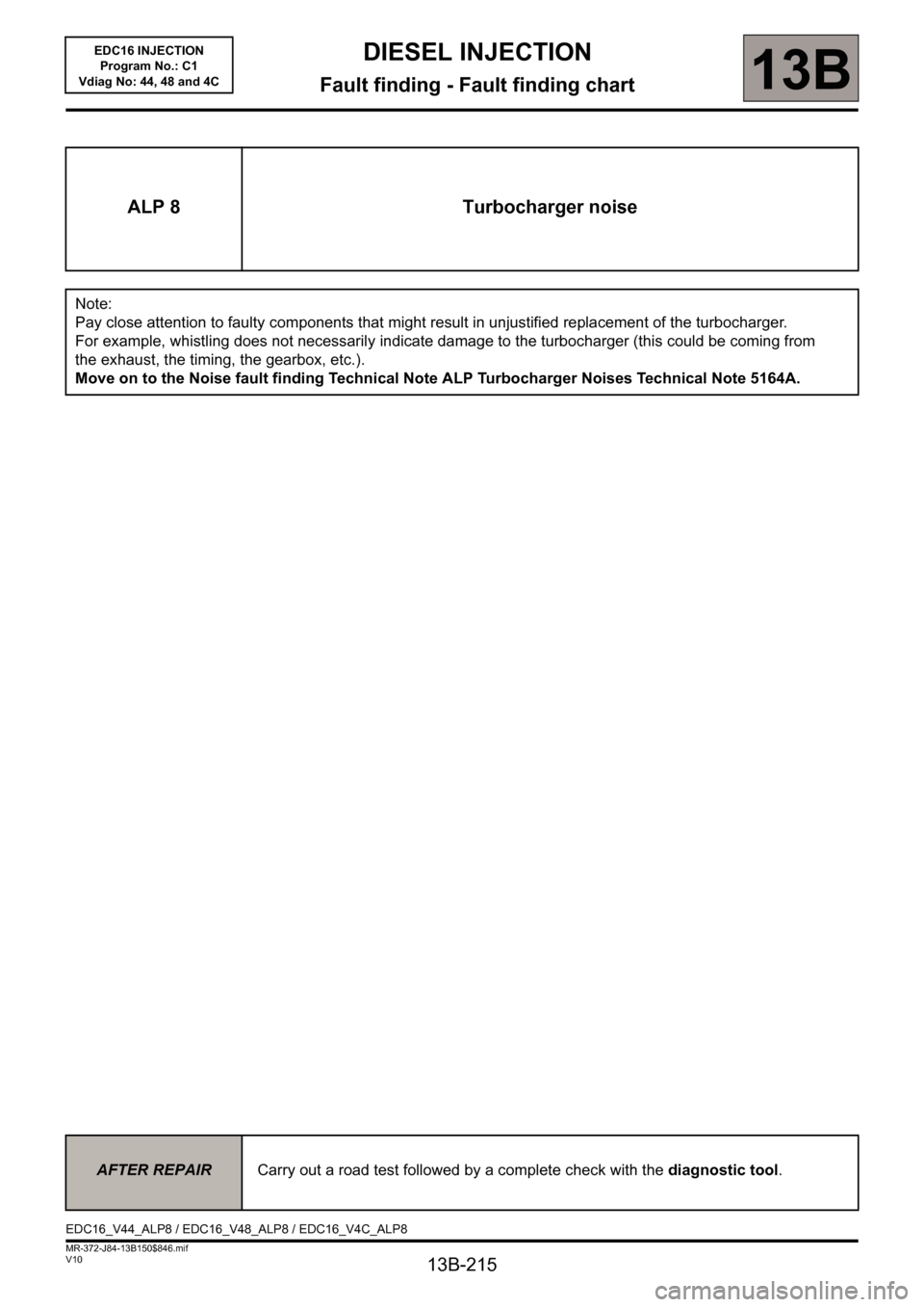
13B-215
MR-372-J84-13B150$846.mif
V10
DIESEL INJECTION
Fault finding - Fault finding chart13B
ALP 8 Turbocharger noise
Note:
Pay close attention to faulty components that might result in unjustified replacement of the turbocharger.
For example, whistling does not necessarily indicate damage to the turbocharger (this could be coming from
the exhaust, the timing, the gearbox, etc.).
Move on to the Noise fault finding Technical Note ALP Turbocharger Noises Technical Note 5164A.
AFTER REPAIRCarry out a road test followed by a complete check with the diagnostic tool.
EDC16_V44_ALP8 / EDC16_V48_ALP8 / EDC16_V4C_ALP8EDC16 INJECTION
Program No.: C1
Vdiag No: 44, 48 and 4C
Page 216 of 236
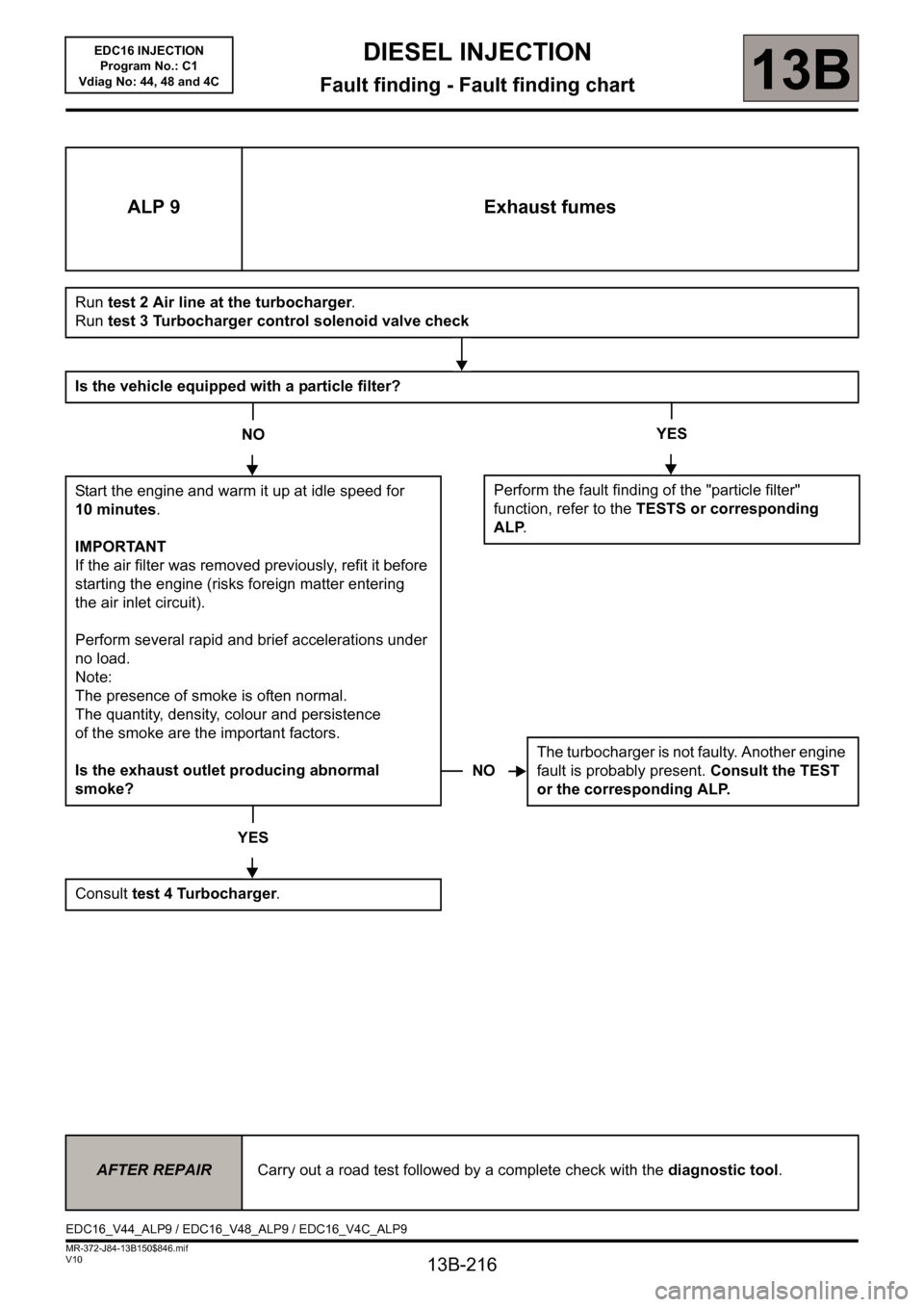
13B-216
MR-372-J84-13B150$846.mif
V10
DIESEL INJECTION
Fault finding - Fault finding chart13B
ALP 9 Exhaust fumes
Run test 2 Air line at the turbocharger.
Run test 3 Turbocharger control solenoid valve check
Is the vehicle equipped with a particle filter?
NO
Start the engine and warm it up at idle speed for
10 minutes.
IMPORTANT
If the air filter was removed previously, refit it before
starting the engine (risks foreign matter entering
the air inlet circuit).
Perform several rapid and brief accelerations under
no load.
Note:
The presence of smoke is often normal.
The quantity, density, colour and persistence
of the smoke are the important factors.
Is the exhaust outlet producing abnormal
smoke?
YES
Consult test 4 Turbocharger.
YES
Perform the fault finding of the "particle filter"
function, refer to the TESTS or corresponding
ALP.
NOThe turbocharger is not faulty. Another engine
fault is probably present. Consult the TEST
or the corresponding ALP.
AFTER REPAIRCarry out a road test followed by a complete check with the diagnostic tool.
EDC16_V44_ALP9 / EDC16_V48_ALP9 / EDC16_V4C_ALP9
EDC16 INJECTION
Program No.: C1
Vdiag No: 44, 48 and 4C
Page 217 of 236
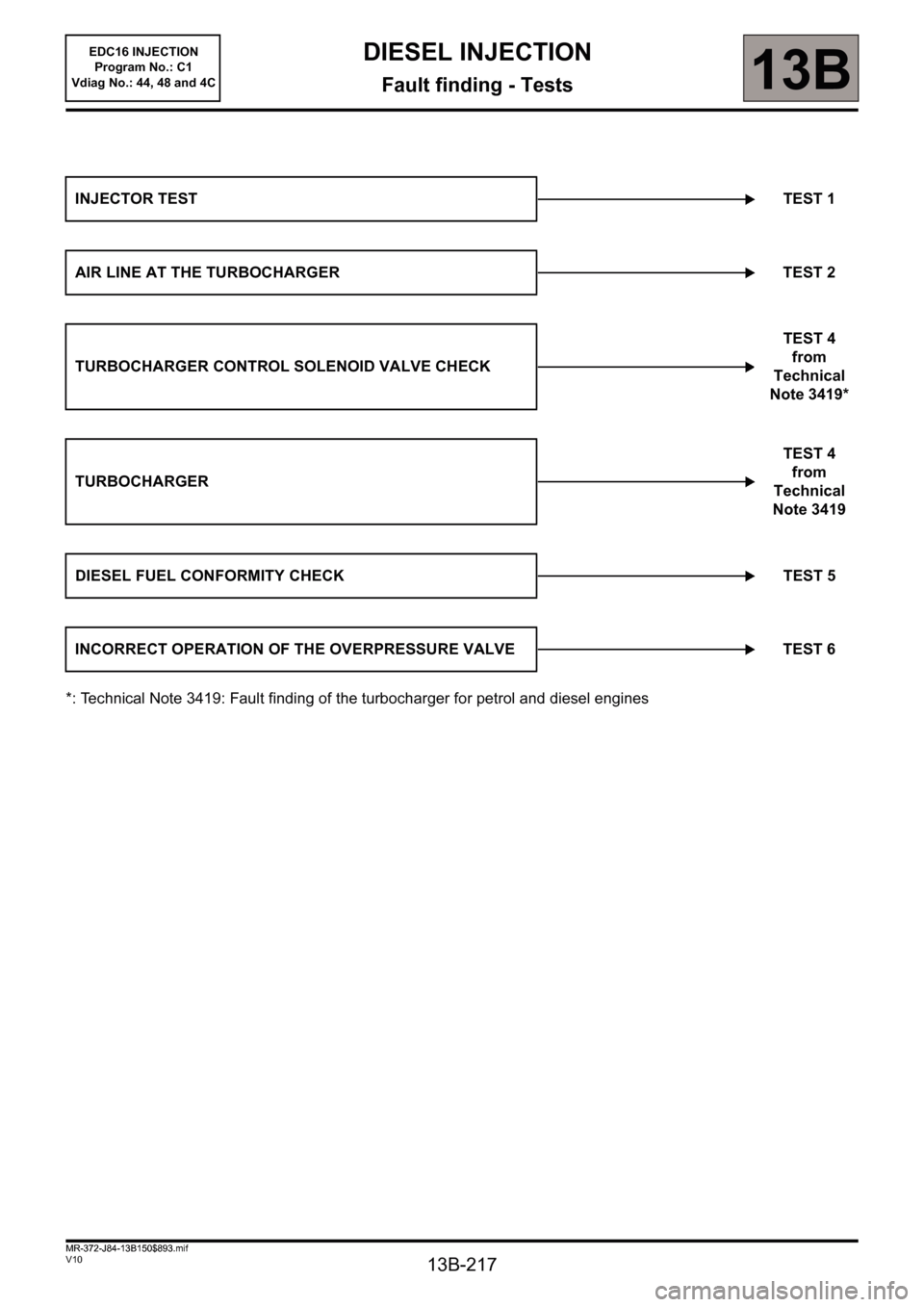
13B-217
MR-372-J84-13B150$893.mif
V10
13B
DIESEL INJECTION
Fault finding - Tests
*: Technical Note 3419: Fault finding of the turbocharger for petrol and diesel enginesINJECTOR TESTTEST 1
AIR LINE AT THE TURBOCHARGER TEST 2
TURBOCHARGER CONTROL SOLENOID VALVE CHECKTEST 4
from
Technical
Note 3419*
TURBOCHARGERTEST 4
from
Technical
Note 3419
DIESEL FUEL CONFORMITY CHECK TEST 5
INCORRECT OPERATION OF THE OVERPRESSURE VALVE TEST 6
EDC16 INJECTION
Program No.: C1
Vdiag No.: 44, 48 and 4C
MR-372-J84-13B150$893.mif
Page 218 of 236
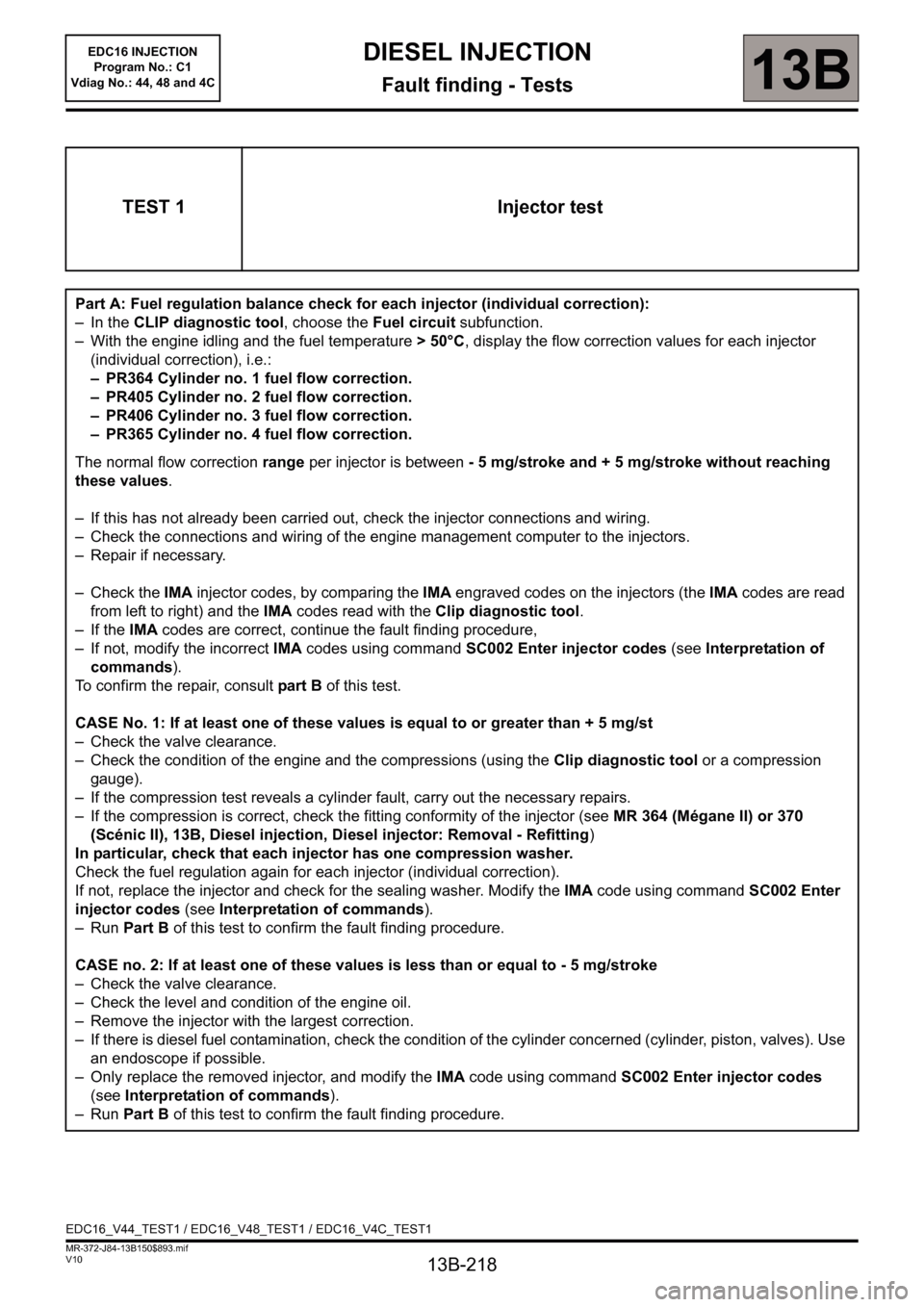
13B-218
MR-372-J84-13B150$893.mif
V10
DIESEL INJECTION
Fault finding - Tests
EDC16 INJECTION
Program No.: C1
Vdiag No.: 44, 48 and 4C
13B
TEST 1 Injector test
Part A: Fuel regulation balance check for each injector (individual correction):
– In the CLIP diagnostic tool, choose the Fuel circuit subfunction.
– With the engine idling and the fuel temperature > 50°C, display the flow correction values for each injector
(individual correction), i.e.:
– PR364 Cylinder no. 1 fuel flow correction.
– PR405 Cylinder no. 2 fuel flow correction.
– PR406 Cylinder no. 3 fuel flow correction.
– PR365 Cylinder no. 4 fuel flow correction.
The normal flow correction range per injector is between - 5 mg/stroke and + 5 mg/stroke without reaching
these values.
– If this has not already been carried out, check the injector connections and wiring.
– Check the connections and wiring of the engine management computer to the injectors.
– Repair if necessary.
– Check the IMA injector codes, by comparing the IMA engraved codes on the injectors (the IMA codes are read
from left to right) and the IMA codes read with the Clip diagnostic tool.
– If the IMA codes are correct, continue the fault finding procedure,
– If not, modify the incorrect IMA codes using command SC002 Enter injector codes (see Interpretation of
commands).
To confirm the repair, consult part B of this test.
CASE No. 1: If at least one of these values is equal to or greater than + 5 mg/st
– Check the valve clearance.
– Check the condition of the engine and the compressions (using the Clip diagnostic tool or a compression
gauge).
– If the compression test reveals a cylinder fault, carry out the necessary repairs.
– If the compression is correct, check the fitting conformity of the injector (see MR 364 (Mégane II) or 370
(Scénic II), 13B, Diesel injection, Diesel injector: Removal - Refitting)
In particular, check that each injector has one compression washer.
Check the fuel regulation again for each injector (individual correction).
If not, replace the injector and check for the sealing washer. Modify the IMA code using command SC002 Enter
injector codes (see Interpretation of commands).
–Run Part B of this test to confirm the fault finding procedure.
CASE no. 2: If at least one of these values is less than or equal to - 5 mg/stroke
– Check the valve clearance.
– Check the level and condition of the engine oil.
– Remove the injector with the largest correction.
– If there is diesel fuel contamination, check the condition of the cylinder concerned (cylinder, piston, valves). Use
an endoscope if possible.
– Only replace the removed injector, and modify the IMA code using command SC002 Enter injector codes
(see Interpretation of commands).
–Run Part B of this test to confirm the fault finding procedure.
EDC16_V44_TEST1 / EDC16_V48_TEST1 / EDC16_V4C_TEST1
Page 219 of 236
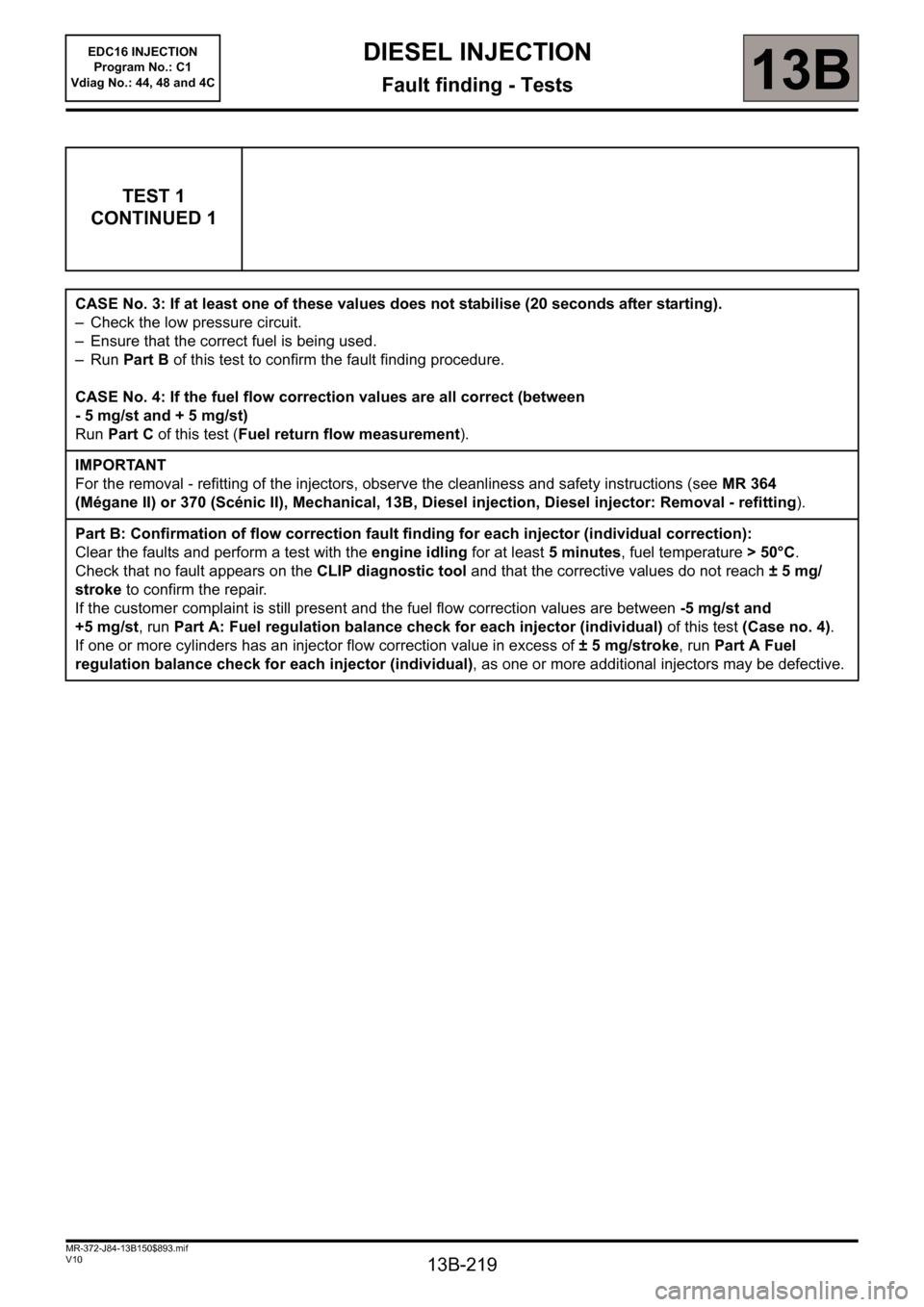
13B-219
MR-372-J84-13B150$893.mif
V10
DIESEL INJECTION
Fault finding - Tests
EDC16 INJECTION
Program No.: C1
Vdiag No.: 44, 48 and 4C
13B
TEST 1
CONTINUED 1
CASE No. 3: If at least one of these values does not stabilise (20 seconds after starting).
– Check the low pressure circuit.
– Ensure that the correct fuel is being used.
–Run Part B of this test to confirm the fault finding procedure.
CASE No. 4: If the fuel flow correction values are all correct (between
- 5 mg/st and + 5 mg/st)
Run Part C of this test (Fuel return flow measurement).
IMPORTANT
For the removal - refitting of the injectors, observe the cleanliness and safety instructions (see MR 364
(Mégane II) or 370 (Scénic II), Mechanical, 13B, Diesel injection, Diesel injector: Removal - refitting).
Part B: Confirmation of flow correction fault finding for each injector (individual correction):
Clear the faults and perform a test with the engine idling for at least 5 minutes, fuel temperature > 50°C.
Check that no fault appears on the CLIP diagnostic tool and that the corrective values do not reach ± 5 mg/
stroke to confirm the repair.
If the customer complaint is still present and the fuel flow correction values are between -5 mg/st and
+5 mg/st, run Part A: Fuel regulation balance check for each injector (individual) of this test (Case no. 4).
If one or more cylinders has an injector flow correction value in excess of ± 5 mg/stroke, run Part A Fuel
regulation balance check for each injector (individual), as one or more additional injectors may be defective.
Page 220 of 236
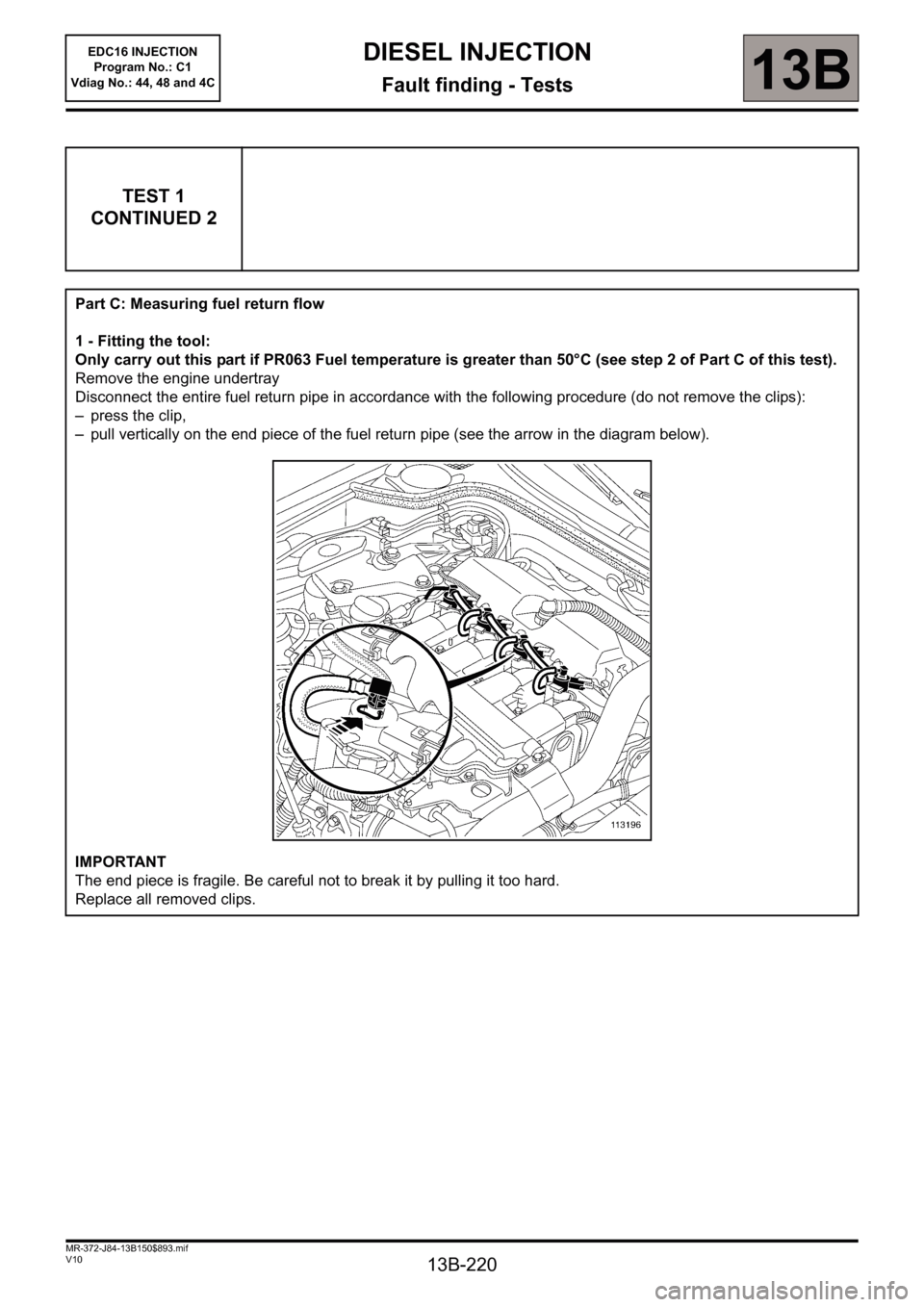
13B-220
MR-372-J84-13B150$893.mif
V10
DIESEL INJECTION
Fault finding - Tests
EDC16 INJECTION
Program No.: C1
Vdiag No.: 44, 48 and 4C
13B
TEST 1
CONTINUED 2
Part C: Measuring fuel return flow
1 - Fitting the tool:
Only carry out this part if PR063 Fuel temperature is greater than 50°C (see step 2 of Part C of this test).
Remove the engine undertray
Disconnect the entire fuel return pipe in accordance with the following procedure (do not remove the clips):
– press the clip,
– pull vertically on the end piece of the fuel return pipe (see the arrow in the diagram below).
IMPORTANT
The end piece is fragile. Be careful not to break it by pulling it too hard.
Replace all removed clips.