start RENAULT SCENIC 2011 J95 / 3.G Engine And Peripherals Workshop Manual
[x] Cancel search | Manufacturer: RENAULT, Model Year: 2011, Model line: SCENIC, Model: RENAULT SCENIC 2011 J95 / 3.GPages: 198, PDF Size: 0.85 MB
Page 2 of 198
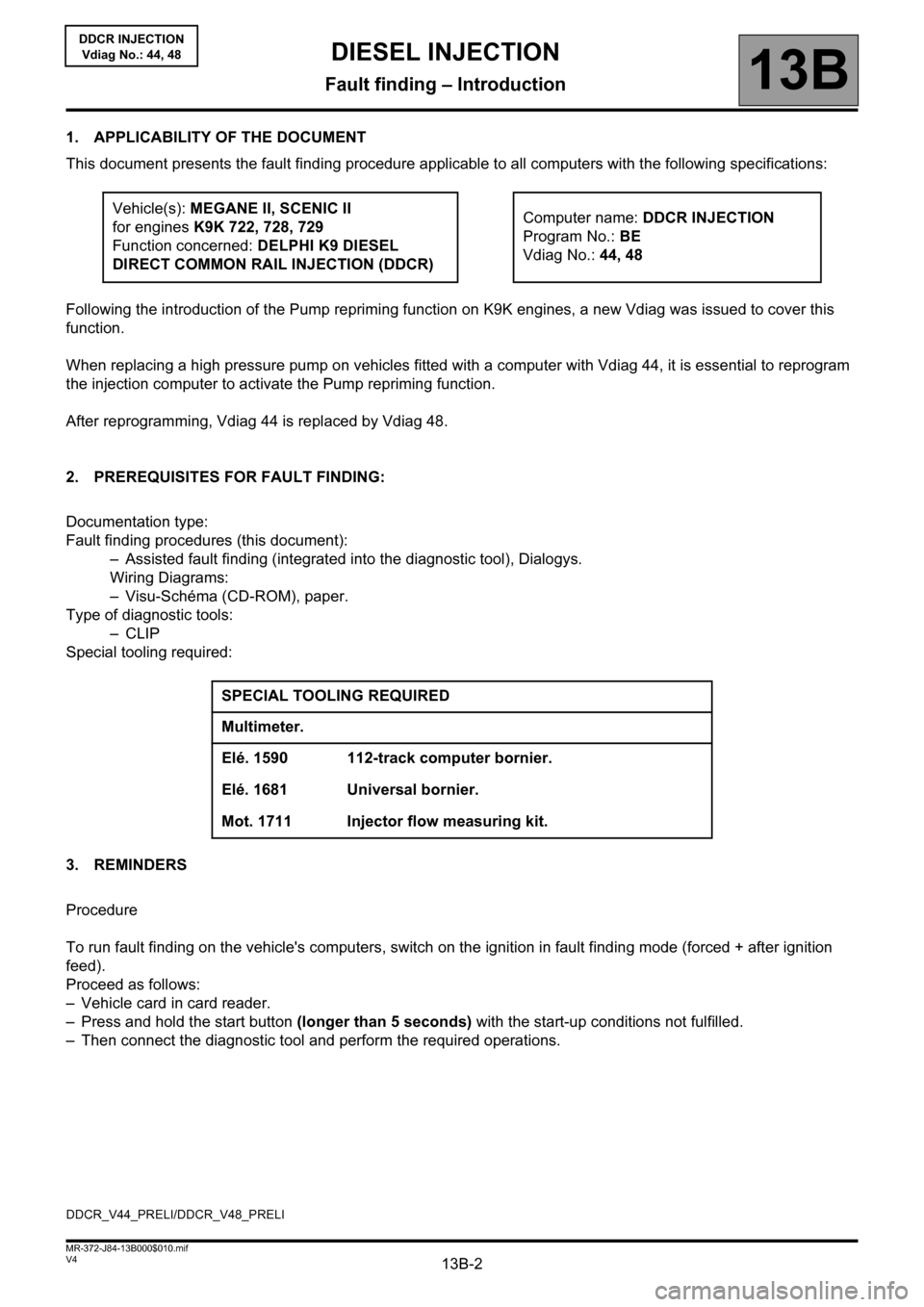
13B-2V4 MR-372-J84-13B000$010.mif
13B
DDCR INJECTION
Vdiag No.: 44, 48
1. APPLICABILITY OF THE DOCUMENT
This document presents the fault finding procedure applicable to all computers with the following specifications:
Following the introduction of the Pump repriming function on K9K engines, a new Vdiag was issued to cover this
function.
When replacing a high pressure pump on vehicles fitted with a computer with Vdiag 44, it is essential to reprogram
the injection computer to activate the Pump repriming function.
After reprogramming, Vdiag 44 is replaced by Vdiag 48.
2. PREREQUISITES FOR FAULT FINDING:
Documentation type:
Fault finding procedures (this document):
– Assisted fault finding (integrated into the diagnostic tool), Dialogys.
Wiring Diagrams:
– Visu-Schéma (CD-ROM), paper.
Type of diagnostic tools:
–CLIP
Special tooling required:
3. REMINDERS
Procedure
To run fault finding on the vehicle's computers, switch on the ignition in fault finding mode (forced + after ignition
feed).
Proceed as follows:
– Vehicle card in card reader.
– Press and hold the start button (longer than 5 seconds) with the start-up conditions not fulfilled.
– Then connect the diagnostic tool and perform the required operations.Vehicle(s): MEGANE II, SCENIC II
for engines K9K 722, 728, 729
Function concerned: DELPHI K9 DIESEL
DIRECT COMMON RAIL INJECTION (DDCR)Computer name: DDCR INJECTION
Program No.: BE
Vdiag No.: 44, 48
SPECIAL TOOLING REQUIRED
Multimeter.
Elé. 1590 112-track computer bornier.
Elé. 1681 Universal bornier.
Mot. 1711 Injector flow measuring kit.
DDCR_V44_PRELI/DDCR_V48_PRELI
DIESEL INJECTION
Fault finding – Introduction
Page 3 of 198
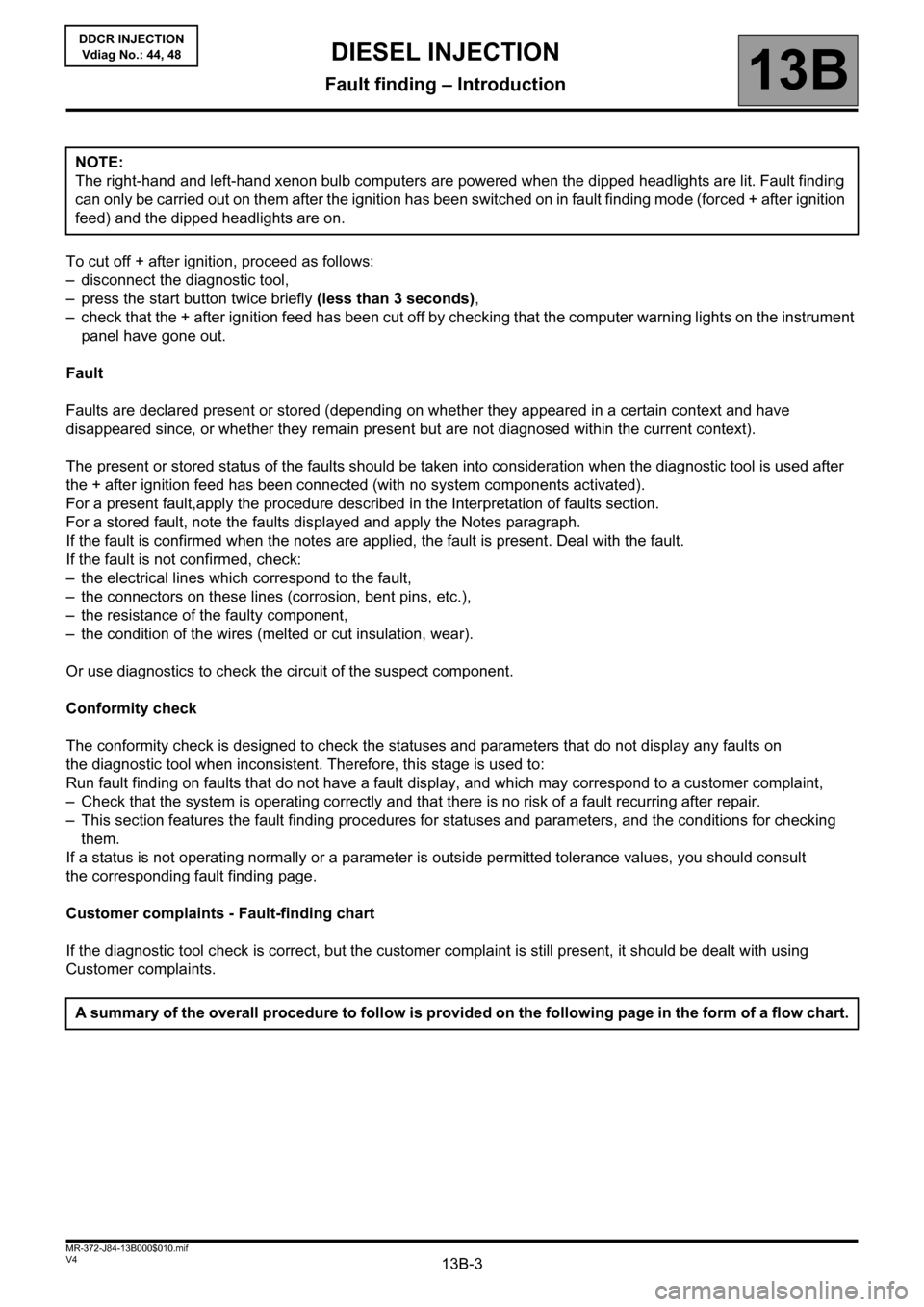
13B-3V4 MR-372-J84-13B000$010.mif
DIESEL INJECTION
Fault finding – Introduction13B
DDCR INJECTION
Vdiag No.: 44, 48
To cut off + after ignition, proceed as follows:
– disconnect the diagnostic tool,
– press the start button twice briefly (less than 3 seconds),
– check that the + after ignition feed has been cut off by checking that the computer warning lights on the instrument
panel have gone out.
Fault
Faults are declared present or stored (depending on whether they appeared in a certain context and have
disappeared since, or whether they remain present but are not diagnosed within the current context).
The present or stored status of the faults should be taken into consideration when the diagnostic tool is used after
the + after ignition feed has been connected (with no system components activated).
For a present fault,apply the procedure described in the Interpretation of faults section.
For a stored fault, note the faults displayed and apply the Notes paragraph.
If the fault is confirmed when the notes are applied, the fault is present. Deal with the fault.
If the fault is not confirmed, check:
– the electrical lines which correspond to the fault,
– the connectors on these lines (corrosion, bent pins, etc.),
– the resistance of the faulty component,
– the condition of the wires (melted or cut insulation, wear).
Or use diagnostics to check the circuit of the suspect component.
Conformity check
The conformity check is designed to check the statuses and parameters that do not display any faults on
the diagnostic tool when inconsistent. Therefore, this stage is used to:
Run fault finding on faults that do not have a fault display, and which may correspond to a customer complaint,
– Check that the system is operating correctly and that there is no risk of a fault recurring after repair.
– This section features the fault finding procedures for statuses and parameters, and the conditions for checking
them.
If a status is not operating normally or a parameter is outside permitted tolerance values, you should consult
the corresponding fault finding page.
Customer complaints - Fault-finding chart
If the diagnostic tool check is correct, but the customer complaint is still present, it should be dealt with using
Customer complaints.NOTE:
The right-hand and left-hand xenon bulb computers are powered when the dipped headlights are lit. Fault finding
can only be carried out on them after the ignition has been switched on in fault finding mode (forced + after ignition
feed) and the dipped headlights are on.
A summary of the overall procedure to follow is provided on the following page in the form of a flow chart.
Page 7 of 198
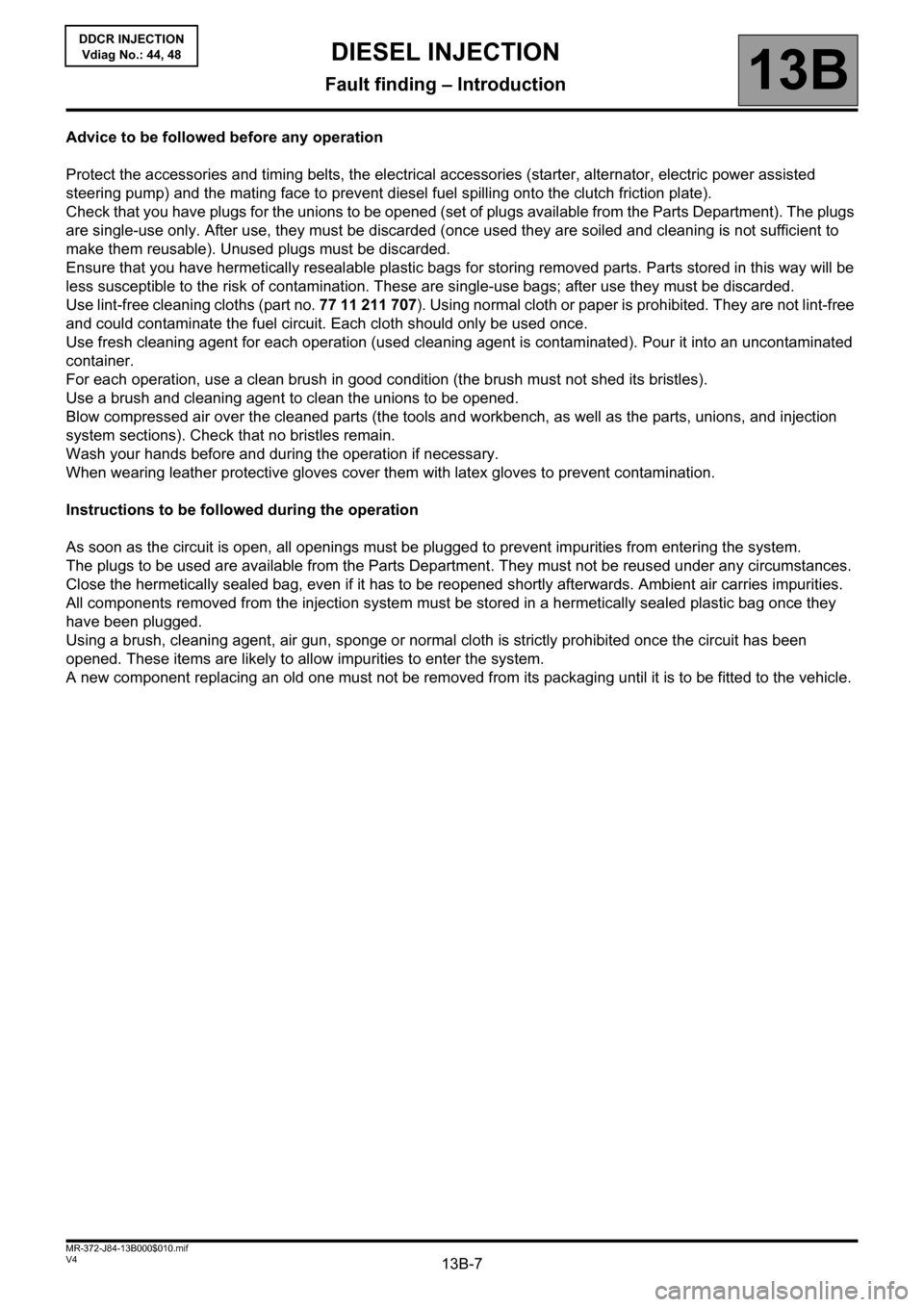
13B-7V4 MR-372-J84-13B000$010.mif
DIESEL INJECTION
Fault finding – Introduction13B
DDCR INJECTION
Vdiag No.: 44, 48
Advice to be followed before any operation
Protect the accessories and timing belts, the electrical accessories (starter, alternator, electric power assisted
steering pump) and the mating face to prevent diesel fuel spilling onto the clutch friction plate).
Check that you have plugs for the unions to be opened (set of plugs available from the Parts Department). The plugs
are single-use only. After use, they must be discarded (once used they are soiled and cleaning is not sufficient to
make them reusable). Unused plugs must be discarded.
Ensure that you have hermetically resealable plastic bags for storing removed parts. Parts stored in this way will be
less susceptible to the risk of contamination. These are single-use bags; after use they must be discarded.
Use lint-free cleaning cloths (part no. 77 11 211 707). Using normal cloth or paper is prohibited. They are not lint-free
and could contaminate the fuel circuit. Each cloth should only be used once.
Use fresh cleaning agent for each operation (used cleaning agent is contaminated). Pour it into an uncontaminated
container.
For each operation, use a clean brush in good condition (the brush must not shed its bristles).
Use a brush and cleaning agent to clean the unions to be opened.
Blow compressed air over the cleaned parts (the tools and workbench, as well as the parts, unions, and injection
system sections). Check that no bristles remain.
Wash your hands before and during the operation if necessary.
When wearing leather protective gloves cover them with latex gloves to prevent contamination.
Instructions to be followed during the operation
As soon as the circuit is open, all openings must be plugged to prevent impurities from entering the system.
The plugs to be used are available from the Parts Department. They must not be reused under any circumstances.
Close the hermetically sealed bag, even if it has to be reopened shortly afterwards. Ambient air carries impurities.
All components removed from the injection system must be stored in a hermetically sealed plastic bag once they
have been plugged.
Using a brush, cleaning agent, air gun, sponge or normal cloth is strictly prohibited once the circuit has been
opened. These items are likely to allow impurities to enter the system.
A new component replacing an old one must not be removed from its packaging until it is to be fitted to the vehicle.
Page 8 of 198
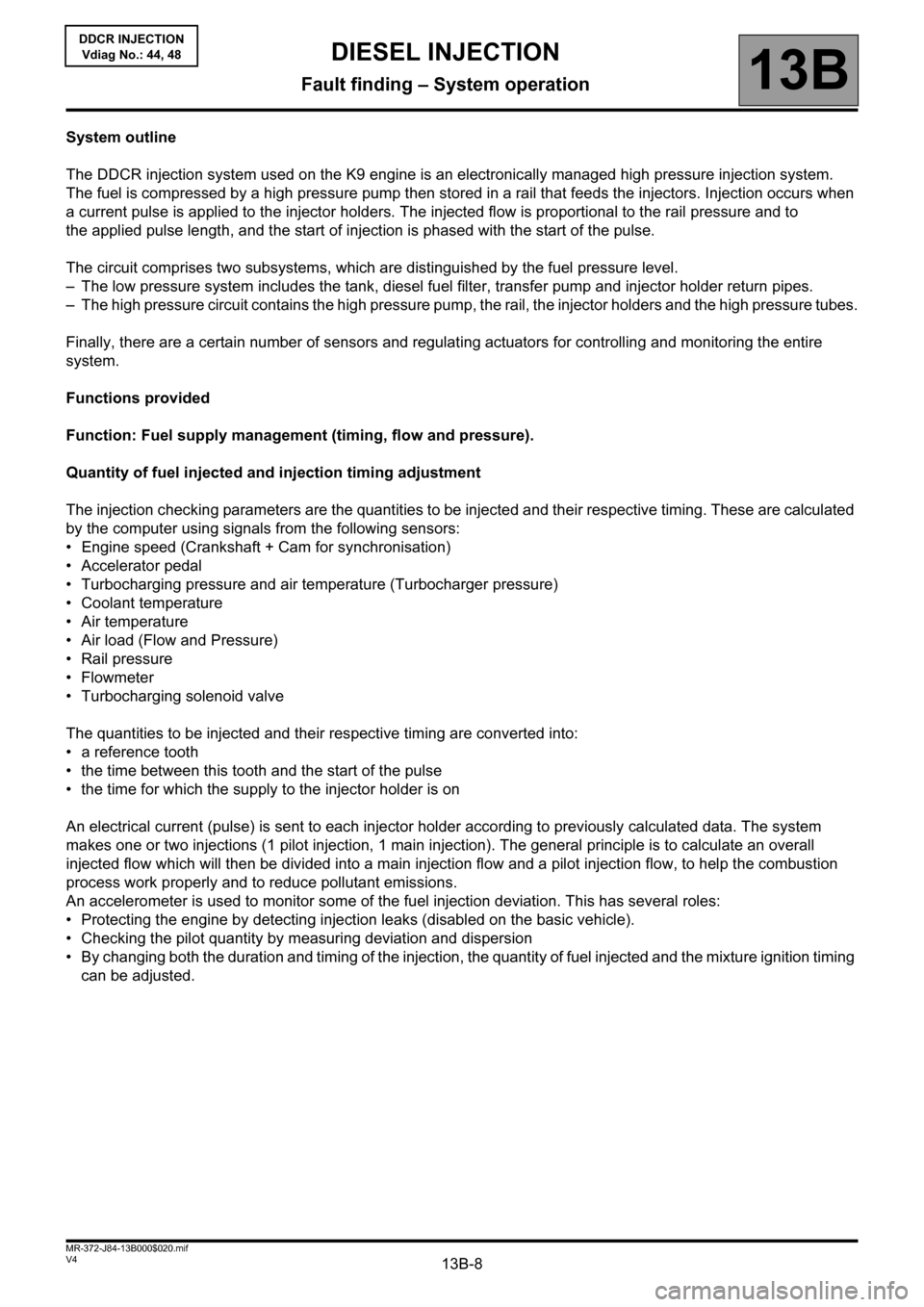
13B-8V4 MR-372-J84-13B000$020.mif
13B
DDCR INJECTION
Vdiag No.: 44, 48
System outline
The DDCR injection system used on the K9 engine is an electronically managed high pressure injection system.
The fuel is compressed by a high pressure pump then stored in a rail that feeds the injectors. Injection occurs when
a current pulse is applied to the injector holders. The injected flow is proportional to the rail pressure and to
the applied pulse length, and the start of injection is phased with the start of the pulse.
The circuit comprises two subsystems, which are distinguished by the fuel pressure level.
– The low pressure system includes the tank, diesel fuel filter, transfer pump and injector holder return pipes.
– The high pressure circuit contains the high pressure pump, the rail, the injector holders and the high pressure tubes.
Finally, there are a certain number of sensors and regulating actuators for controlling and monitoring the entire
system.
Functions provided
Function: Fuel supply management (timing, flow and pressure).
Quantity of fuel injected and injection timing adjustment
The injection checking parameters are the quantities to be injected and their respective timing. These are calculated
by the computer using signals from the following sensors:
• Engine speed (Crankshaft + Cam for synchronisation)
• Accelerator pedal
• Turbocharging pressure and air temperature (Turbocharger pressure)
• Coolant temperature
• Air temperature
• Air load (Flow and Pressure)
• Rail pressure
• Flowmeter
• Turbocharging solenoid valve
The quantities to be injected and their respective timing are converted into:
• a reference tooth
• the time between this tooth and the start of the pulse
• the time for which the supply to the injector holder is on
An electrical current (pulse) is sent to each injector holder according to previously calculated data. The system
makes one or two injections (1 pilot injection, 1 main injection). The general principle is to calculate an overall
injected flow which will then be divided into a main injection flow and a pilot injection flow, to help the combustion
process work properly and to reduce pollutant emissions.
An accelerometer is used to monitor some of the fuel injection deviation. This has several roles:
• Protecting the engine by detecting injection leaks (disabled on the basic vehicle).
• Checking the pilot quantity by measuring deviation and dispersion
• By changing both the duration and timing of the injection, the quantity of fuel injected and the mixture ignition timing
can be adjusted.
DIESEL INJECTION
Fault finding – System operation
Page 12 of 198
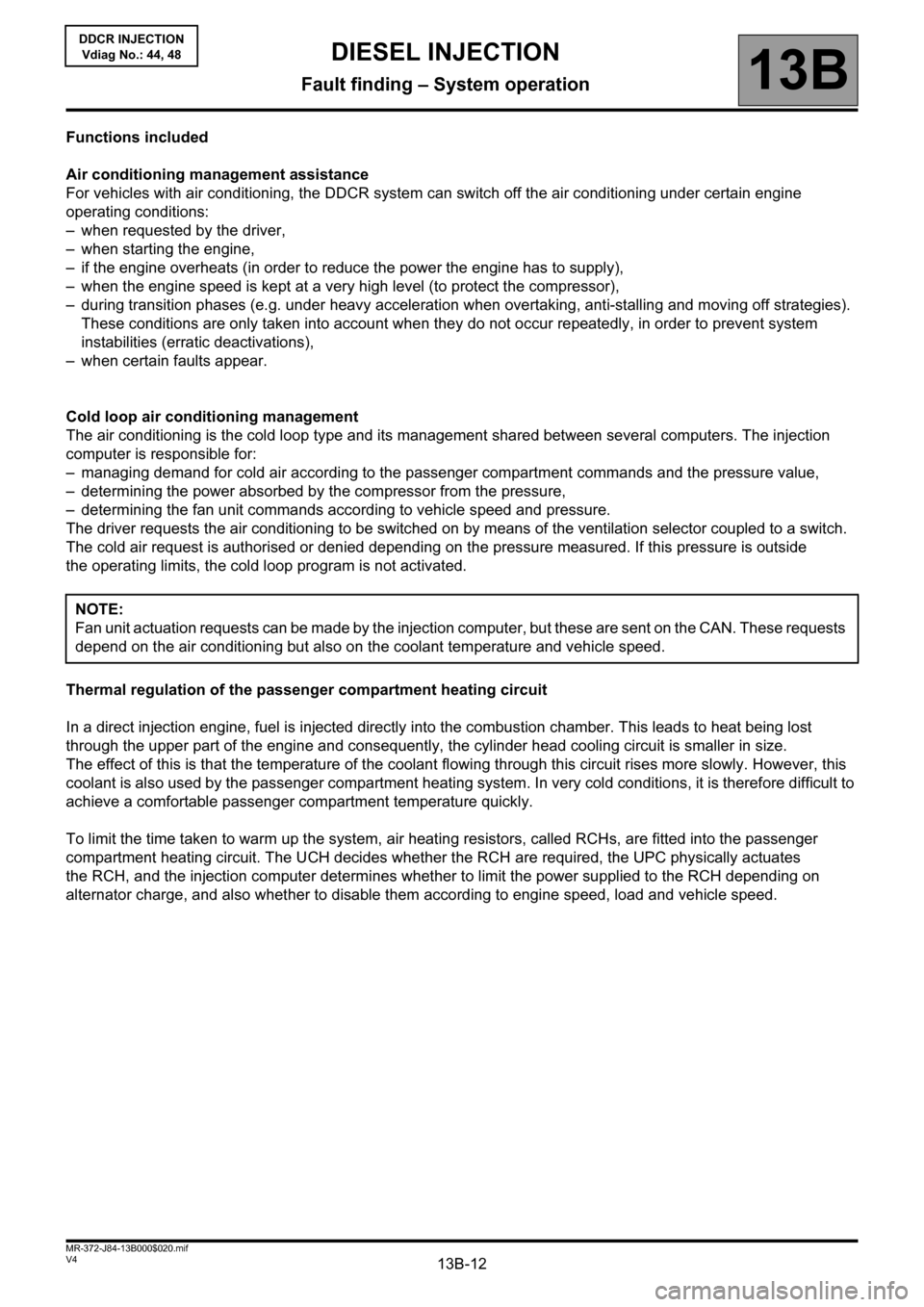
13B-12V4 MR-372-J84-13B000$020.mif
DIESEL INJECTION
Fault finding – System operation13B
DDCR INJECTION
Vdiag No.: 44, 48
Functions included
Air conditioning management assistance
For vehicles with air conditioning, the DDCR system can switch off the air conditioning under certain engine
operating conditions:
– when requested by the driver,
– when starting the engine,
– if the engine overheats (in order to reduce the power the engine has to supply),
– when the engine speed is kept at a very high level (to protect the compressor),
– during transition phases (e.g. under heavy acceleration when overtaking, anti-stalling and moving off strategies).
These conditions are only taken into account when they do not occur repeatedly, in order to prevent system
instabilities (erratic deactivations),
– when certain faults appear.
Cold loop air conditioning management
The air conditioning is the cold loop type and its management shared between several computers. The injection
computer is responsible for:
– managing demand for cold air according to the passenger compartment commands and the pressure value,
– determining the power absorbed by the compressor from the pressure,
– determining the fan unit commands according to vehicle speed and pressure.
The driver requests the air conditioning to be switched on by means of the ventilation selector coupled to a switch.
The cold air request is authorised or denied depending on the pressure measured. If this pressure is outside
the operating limits, the cold loop program is not activated.
Thermal regulation of the passenger compartment heating circuit
In a direct injection engine, fuel is injected directly into the combustion chamber. This leads to heat being lost
through the upper part of the engine and consequently, the cylinder head cooling circuit is smaller in size.
The effect of this is that the temperature of the coolant flowing through this circuit rises more slowly. However, this
coolant is also used by the passenger compartment heating system. In very cold conditions, it is therefore difficult to
achieve a comfortable passenger compartment temperature quickly.
To limit the time taken to warm up the system, air heating resistors, called RCHs, are fitted into the passenger
compartment heating circuit. The UCH decides whether the RCH are required, the UPC physically actuates
the RCH, and the injection computer determines whether to limit the power supplied to the RCH depending on
alternator charge, and also whether to disable them according to engine speed, load and vehicle speed. NOTE:
Fan unit actuation requests can be made by the injection computer, but these are sent on the CAN. These requests
depend on the air conditioning but also on the coolant temperature and vehicle speed.
Page 18 of 198

13B-18V4 MR-372-J84-13B000$030.mif
13B
DDCR INJECTION
Vdiag No.: 44, 48
COMPUTER REPLACEMENT, PROGRAMMING AND REPROGRAMMING OPERATIONS
Before reprogramming or removing the computer in After-Sales operations, save the following data to the
diagnostic tool:
– The C2I parameters (individual injector correction) and the engine adaptives using command SC003 Save
computer data.
The system can be reprogrammed with the diagnostic socket using the RENAULT CLIP diagnostic tool
(Consult Technical Note 3585A, Computer programming and reprogramming procedure, and follow the
instructions given by the diagnostic tool).
Any time the computer has been reprogrammed
– Use the diagnostic tool command SC001 Enter saved data to restore the C2I and the engine adaptives.
– Use command AC028 Static test to reinitialise the computer (fan assembly, etc.).
– When changing the pump, refer to the high pressure pump replacement procedure (consult Technical Note 5011A,
Repriming Delphi high pressure pumps on K9K engines).
– Switch the ignition off and then on again.
–Activate the starter without releasing the key until the engine starts (the engine start time can be up to 20
seconds).
– Stop the engine (to initialise the computer) and wait 30 seconds.
– Switch the ignition on again and use the diagnostic tool to carry out the following steps:
– Run command VP010 Enter VIN.
– After injection system programming, stored faults may appear on other computers. Clear the memory of these
computers. IMPORTANT:
Before reprogramming the injection computer, move the main Cruise control/Speed limiter switch to the rest
position. The information about the cruise control or the speed limiter displayed on the instrument panel
disappears.
Otherwise, if the main switch remains in the cruise control or speed limiter position during and after reprogramming,
the Cruise control/Speed limiter function will not be operational.
The procedure for resetting the function is as follows:
Vehicle ignition on.
Main switch in rest position (the computer then detects the rest position).
Switch in Cruise control position to activate the Cruise control function.
Switch in Speed limiter position to activate the Speed limiter function.
IMPORTANT
– Switch on the diagnostic tool (mains or cigarette lighter supply).
– Connect a battery charger.
– Switch off all electrical consumers (lights, interior lights, air conditioning, radio/CD, etc.).
– Wait for the engine to cool (engine coolant temperature below 60°C and air temperature below 50°C).
DIESEL INJECTION
Fault finding – Replacement of components
Page 20 of 198
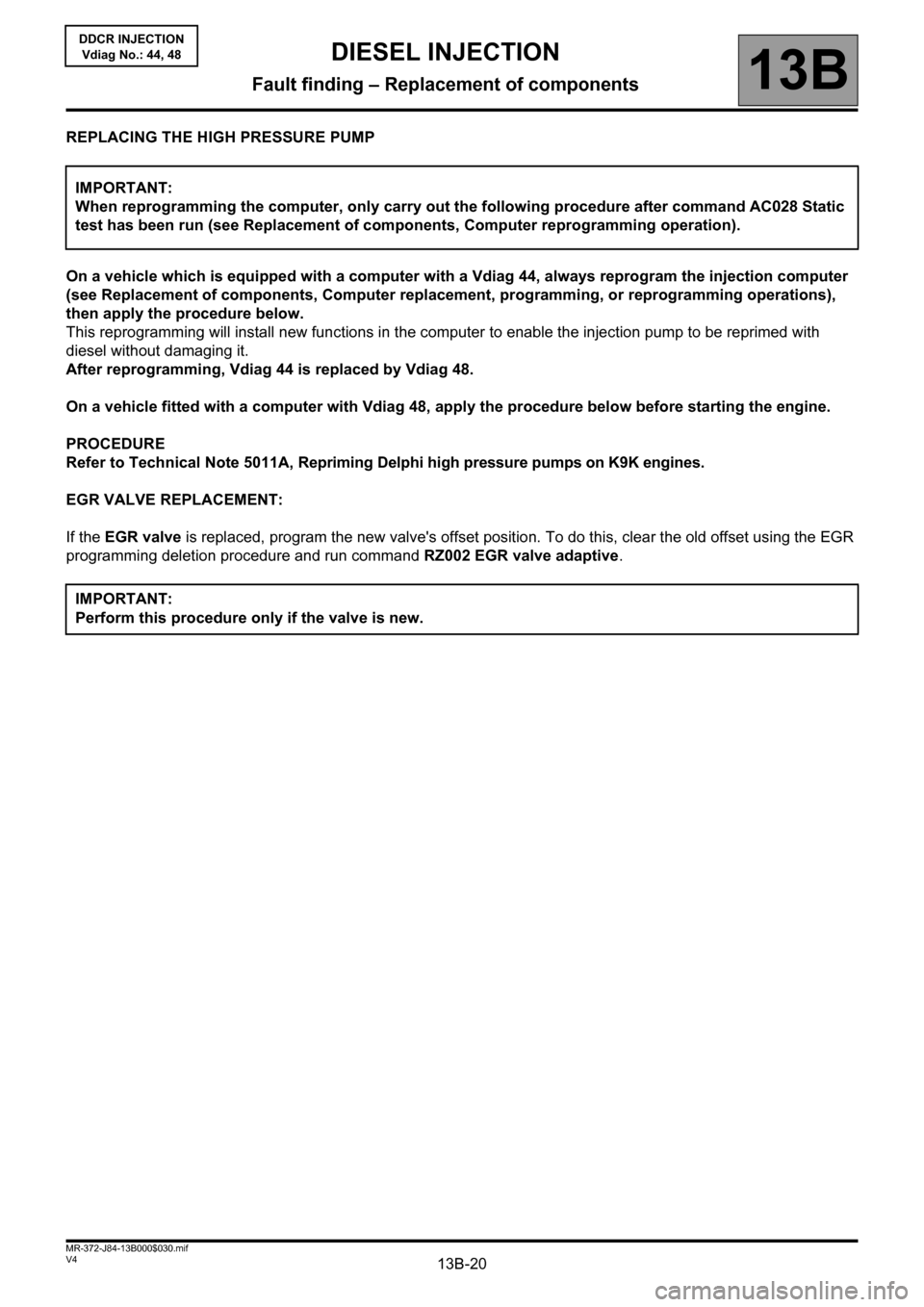
13B-20V4 MR-372-J84-13B000$030.mif
DIESEL INJECTION
Fault finding – Replacement of components13B
DDCR INJECTION
Vdiag No.: 44, 48
REPLACING THE HIGH PRESSURE PUMP
On a vehicle which is equipped with a computer with a Vdiag 44, always reprogram the injection computer
(see Replacement of components, Computer replacement, programming, or reprogramming operations),
then apply the procedure below.
This reprogramming will install new functions in the computer to enable the injection pump to be reprimed with
diesel without damaging it.
After reprogramming, Vdiag 44 is replaced by Vdiag 48.
On a vehicle fitted with a computer with Vdiag 48, apply the procedure below before starting the engine.
PROCEDURE
Refer to Technical Note 5011A, Repriming Delphi high pressure pumps on K9K engines.
EGR VALVE REPLACEMENT:
If the EGR valve is replaced, program the new valve's offset position. To do this, clear the old offset using the EGR
programming deletion procedure and run command RZ002 EGR valve adaptive. IMPORTANT:
When reprogramming the computer, only carry out the following procedure after command AC028 Static
test has been run (see Replacement of components, Computer reprogramming operation).
IMPORTANT:
Perform this procedure only if the valve is new.
Page 27 of 198
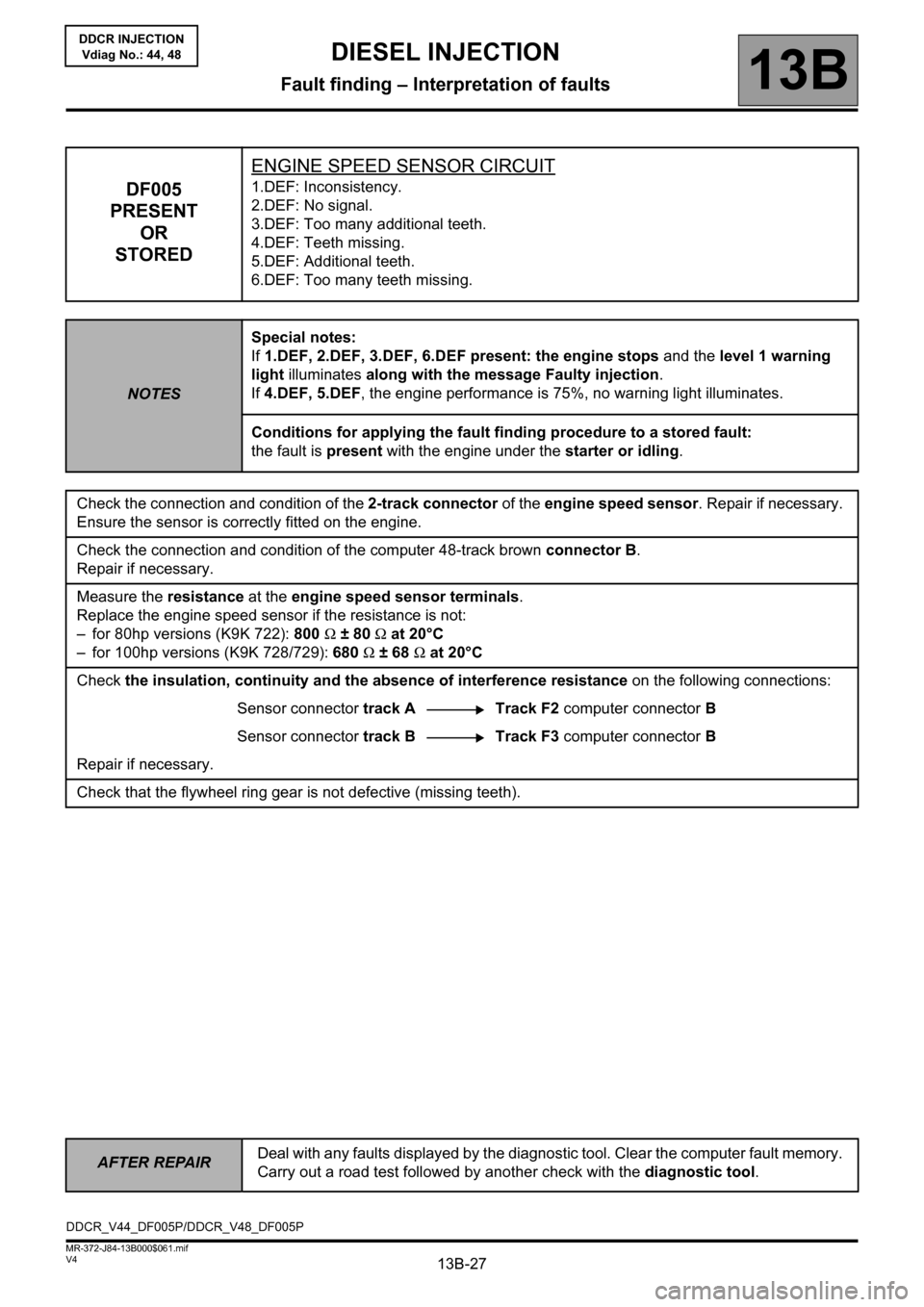
13B-27
AFTER REPAIRDeal with any faults displayed by the diagnostic tool. Clear the computer fault memory.
Carry out a road test followed by another check with the diagnostic tool.
V4 MR-372-J84-13B000$061.mif
DIESEL INJECTION
Fault finding – Interpretation of faults13B
DDCR INJECTION
Vdiag No.: 44, 48
DF005
PRESENT
OR
STOREDENGINE SPEED SENSOR CIRCUIT1.DEF: Inconsistency.
2.DEF: No signal.
3.DEF: Too many additional teeth.
4.DEF: Teeth missing.
5.DEF: Additional teeth.
6.DEF: Too many teeth missing.
NOTESSpecial notes:
If 1.DEF, 2.DEF, 3.DEF, 6.DEF present: the engine stops and the level 1 warning
light illuminates along with the message Faulty injection.
If 4.DEF, 5.DEF, the engine performance is 75%, no warning light illuminates.
Conditions for applying the fault finding procedure to a stored fault:
the fault is present with the engine under the starter or idling.
Check the connection and condition of the 2-track connector of the engine speed sensor. Repair if necessary.
Ensure the sensor is correctly fitted on the engine.
Check the connection and condition of the computer 48-track brown connector B.
Repair if necessary.
Measure the resistance at the engine speed sensor terminals.
Replace the engine speed sensor if the resistance is not:
– for 80hp versions (K9K 722): 800 Ω ± 80 Ω at 20°C
– for 100hp versions (K9K 728/729): 680 Ω ± 68 Ω at 20°C
Check the insulation, continuity and the absence of interference resistance on the following connections:
Sensor connector track A Track F2 computer connector B
Sensor connector track BTrack F3 computer connector B
Repair if necessary.
Check that the flywheel ring gear is not defective (missing teeth).
DDCR_V44_DF005P/DDCR_V48_DF005P
Page 28 of 198
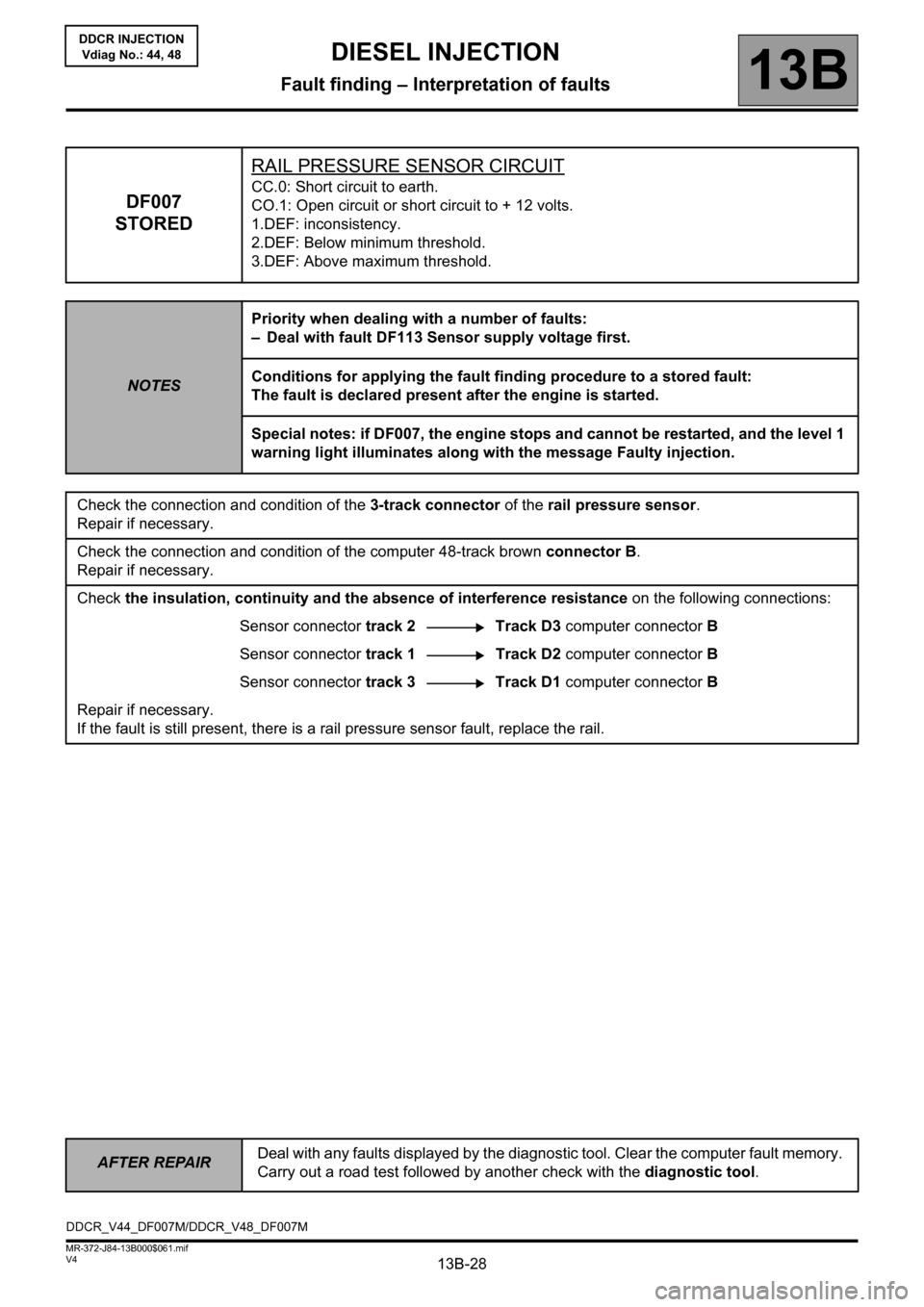
13B-28
AFTER REPAIRDeal with any faults displayed by the diagnostic tool. Clear the computer fault memory.
Carry out a road test followed by another check with the diagnostic tool.
V4 MR-372-J84-13B000$061.mif
DIESEL INJECTION
Fault finding – Interpretation of faults13B
DDCR INJECTION
Vdiag No.: 44, 48
DF007
STOREDRAIL PRESSURE SENSOR CIRCUIT
CC.0: Short circuit to earth.
CO.1: Open circuit or short circuit to + 12 volts.
1.DEF: inconsistency.
2.DEF: Below minimum threshold.
3.DEF: Above maximum threshold.
NOTESPriority when dealing with a number of faults:
– Deal with fault DF113 Sensor supply voltage first.
Conditions for applying the fault finding procedure to a stored fault:
The fault is declared present after the engine is started.
Special notes: if DF007, the engine stops and cannot be restarted, and the level 1
warning light illuminates along with the message Faulty injection.
Check the connection and condition of the 3-track connector of the rail pressure sensor.
Repair if necessary.
Check the connection and condition of the computer 48-track brown connector B.
Repair if necessary.
Check the insulation, continuity and the absence of interference resistance on the following connections:
Sensor connector track 2 Track D3 computer connector B
Sensor connector track 1Track D2 computer connector B
Sensor connector track 3 Track D1 computer connector B
Repair if necessary.
If the fault is still present, there is a rail pressure sensor fault, replace the rail.
DDCR_V44_DF007M/DDCR_V48_DF007M
Page 36 of 198
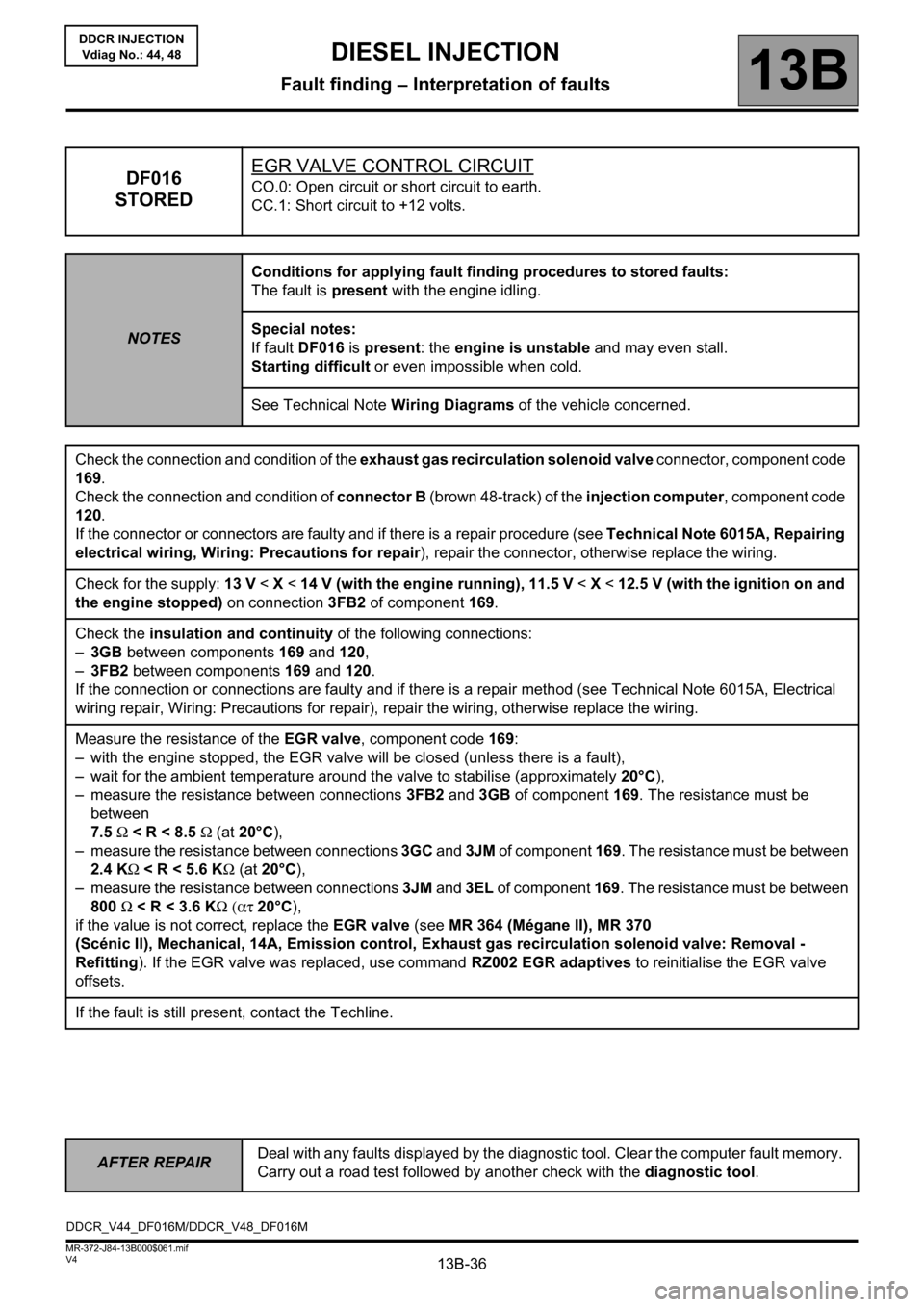
13B-36
AFTER REPAIRDeal with any faults displayed by the diagnostic tool. Clear the computer fault memory.
Carry out a road test followed by another check with the diagnostic tool.
V4 MR-372-J84-13B000$061.mif
DIESEL INJECTION
Fault finding – Interpretation of faults13B
DDCR INJECTION
Vdiag No.: 44, 48
DF016
STOREDEGR VALVE CONTROL CIRCUITCO.0: Open circuit or short circuit to earth.
CC.1: Short circuit to +12 volts.
NOTESConditions for applying fault finding procedures to stored faults:
The fault is present with the engine idling.
Special notes:
If fault DF016 is present: the engine is unstable and may even stall.
Starting difficult or even impossible when cold.
See Technical Note Wiring Diagrams of the vehicle concerned.
Check the connection and condition of the exhaust gas recirculation solenoid valve connector, component code
169.
Check the connection and condition of connector B (brown 48-track) of the injection computer, component code
120.
If the connector or connectors are faulty and if there is a repair procedure (see Technical Note 6015A, Repairing
electrical wiring, Wiring: Precautions for repair), repair the connector, otherwise replace the wiring.
Check for the supply: 13 V < X < 14 V (with the engine running), 11.5 V < X < 12.5 V (with the ignition on and
the engine stopped) on connection 3FB2 of component 169.
Check the insulation and continuity of the following connections:
–3GB between components 169 and 120,
–3FB2 between components 169 and 120.
If the connection or connections are faulty and if there is a repair method (see Technical Note 6015A, Electrical
wiring repair, Wiring: Precautions for repair), repair the wiring, otherwise replace the wiring.
Measure the resistance of the EGR valve, component code 169:
– with the engine stopped, the EGR valve will be closed (unless there is a fault),
– wait for the ambient temperature around the valve to stabilise (approximately 20°C),
– measure the resistance between connections 3FB2 and 3GB of component 169. The resistance must be
between
7.5 Ω
< R < 8.5 Ω (at 20°C),
– measure the resistance between connections 3GC and 3JM of component 169. The resistance must be between
2.4 KΩ < R < 5.6 KΩ (at 20°C),
– measure the resistance between connections 3JM and 3EL of component 169. The resistance must be between
800 Ω < R < 3.6 KΩ (ατ 20°C),
if the value is not correct, replace the EGR valve (see MR 364 (Mégane II), MR 370
(Scénic II), Mechanical, 14A, Emission control, Exhaust gas recirculation solenoid valve: Removal -
Refitting). If the EGR valve was replaced, use command RZ002 EGR adaptives to reinitialise the EGR valve
offsets.
If the fault is still present, contact the Techline.
DDCR_V44_DF016M/DDCR_V48_DF016M