ignition SSANGYONG MUSSO 1998 Workshop Repair Manual
[x] Cancel search | Manufacturer: SSANGYONG, Model Year: 1998, Model line: MUSSO, Model: SSANGYONG MUSSO 1998Pages: 1463, PDF Size: 19.88 MB
Page 955 of 1463
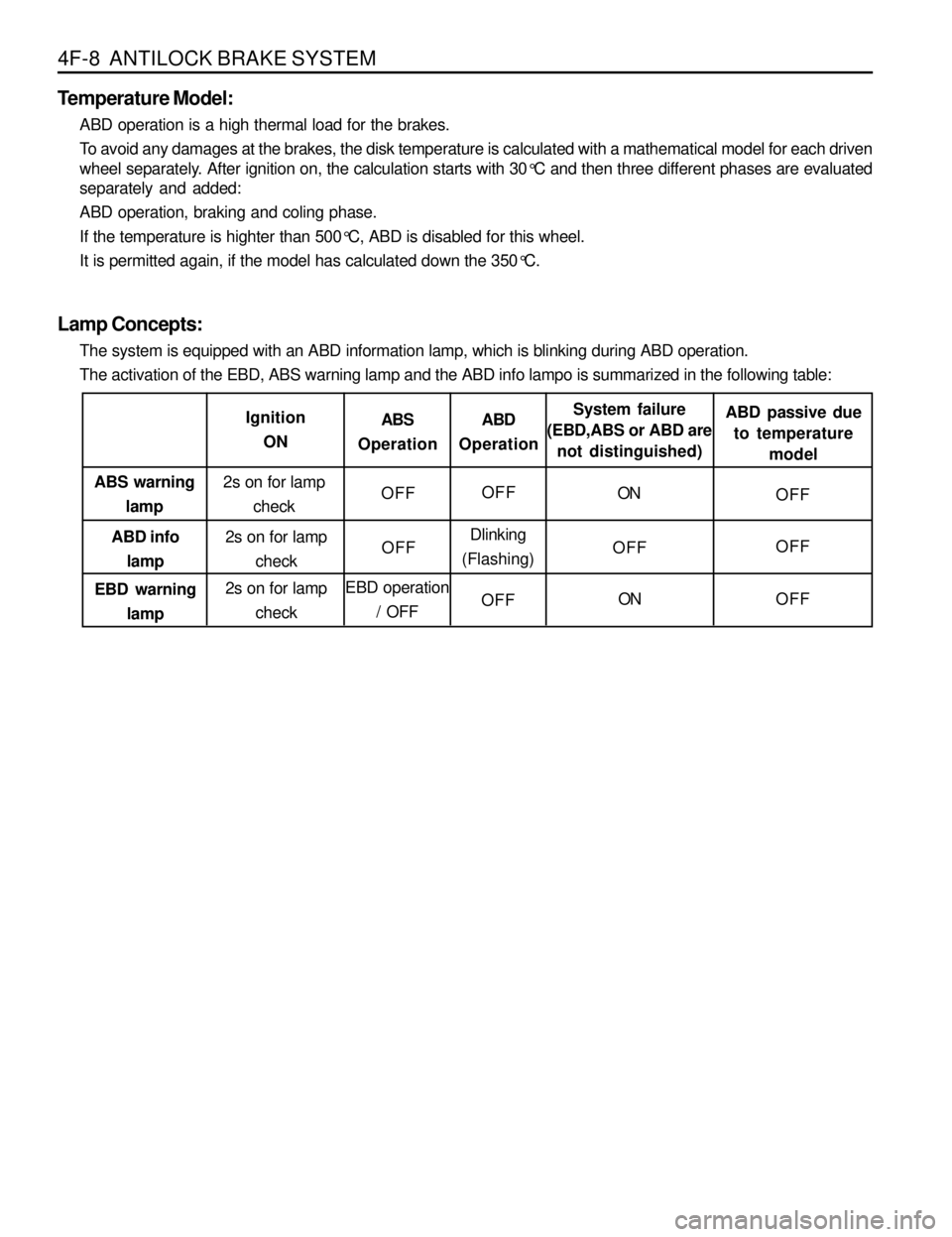
4F-8 ANTILOCK BRAKE SYSTEM
Temperature Model:
ABD operation is a high thermal load for the brakes.
To avoid any damages at the brakes, the disk temperature is calculated with a mathematical model for each driven
wheel separately. After ignition on, the calculation starts with 30°C and then three different phases are evaluated
separately and added:
ABD operation, braking and coling phase.
If the temperature is highter than 500°C, ABD is disabled for this wheel.
It is permitted again, if the model has calculated down the 350°C.
Lamp Concepts:
The system is equipped with an ABD information lamp, which is blinking during ABD operation.
The activation of the EBD, ABS warning lamp and the ABD info lampo is summarized in the following table:
Ignition
ONABS
OperationABD
OperationSystem failure
(EBD,ABS or ABD are
not distinguished)ABD passive due
to temperature
model
ABS warning
lamp
ABD info
lamp
EBD warning
lamp2s on for lamp
check
2s on for lamp
check
2s on for lamp
checkOFF
EBD operation
/ OFFOFFOFF
Dlinking
(Flashing)
OFFON
OFF
ONOFF
OFF
OFF
Page 956 of 1463
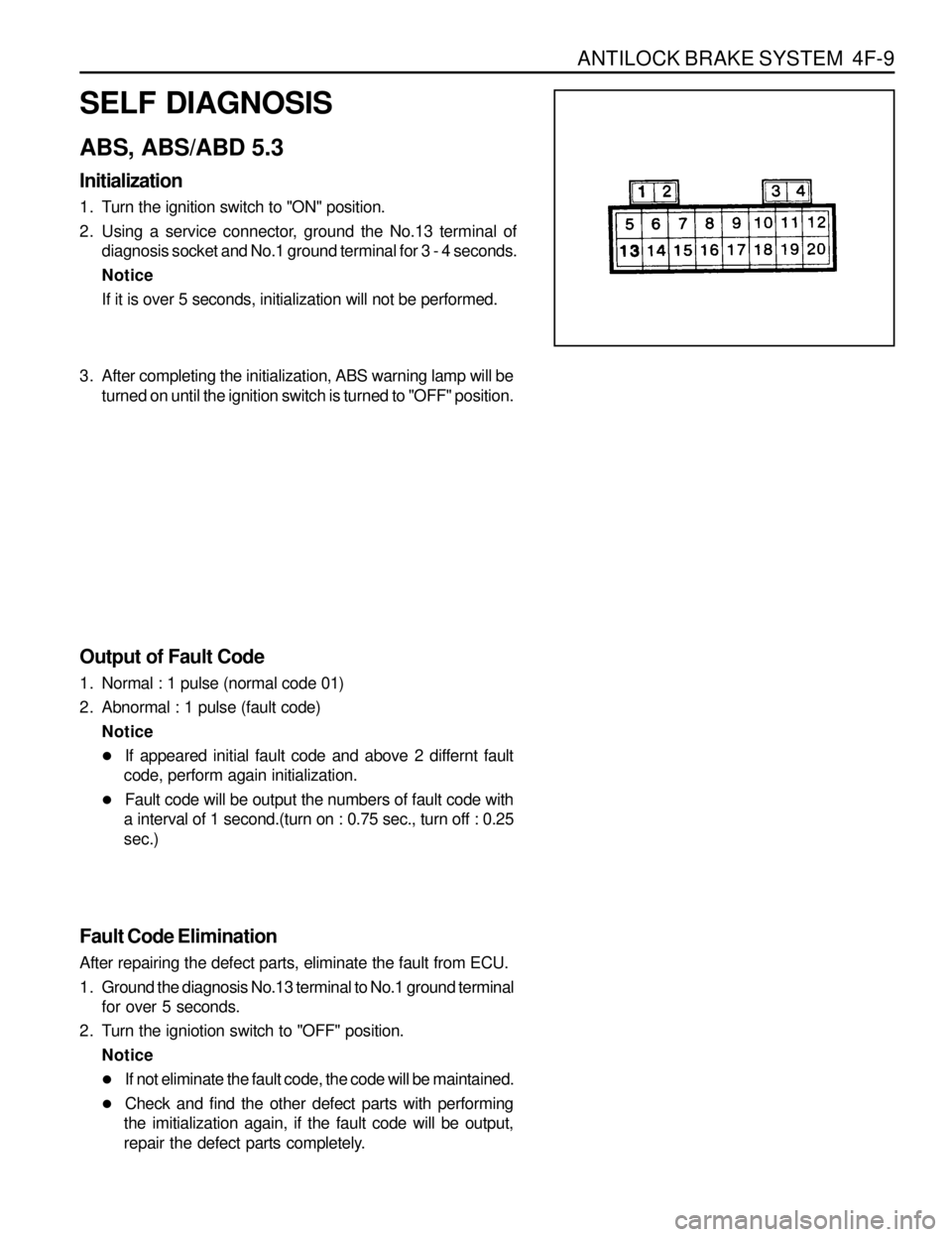
ANTILOCK BRAKE SYSTEM 4F-9
SELF DIAGNOSIS
ABS, ABS/ABD 5.3
Initialization
1. Turn the ignition switch to "ON" position.
2. Using a service connector, ground the No.13 terminal of
diagnosis socket and No.1 ground terminal for 3 - 4 seconds.
Notice
If it is over 5 seconds, initialization will not be performed.
3. After completing the initialization, ABS warning lamp will be
turned on until the ignition switch is turned to "OFF" position.
Output of Fault Code
1. Normal : 1 pulse (normal code 01)
2. Abnormal : 1 pulse (fault code)
Notice
lIf appeared initial fault code and above 2 differnt fault
code, perform again initialization.
lFault code will be output the numbers of fault code with
a interval of 1 second.(turn on : 0.75 sec., turn off : 0.25
sec.)
Fault Code Elimination
After repairing the defect parts, eliminate the fault from ECU.
1. Ground the diagnosis No.13 terminal to No.1 ground terminal
for over 5 seconds.
2. Turn the igniotion switch to "OFF" position.
Notice
lIf not eliminate the fault code, the code will be maintained.
lCheck and find the other defect parts with performing
the imitialization again, if the fault code will be output,
repair the defect parts completely.
Page 958 of 1463
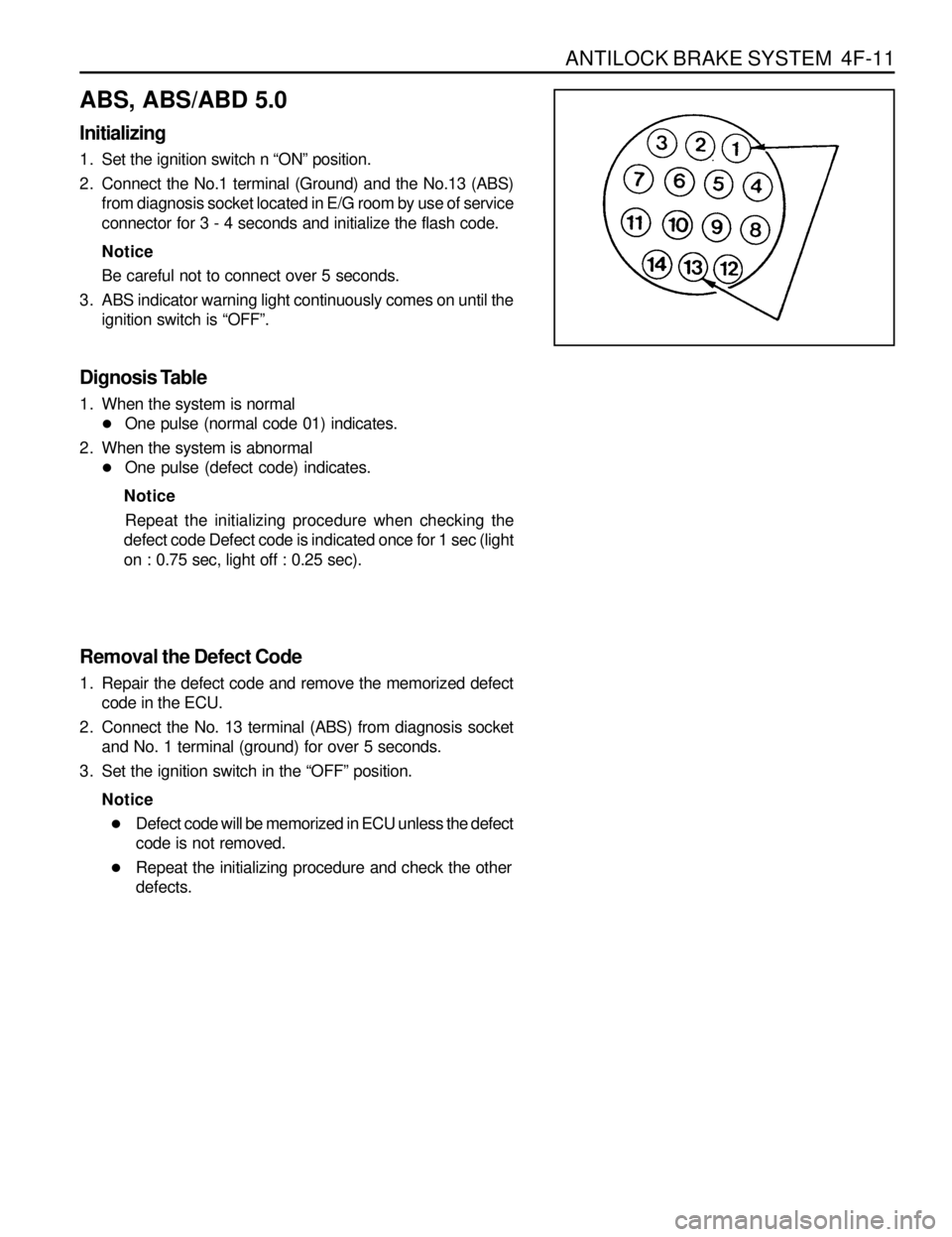
ANTILOCK BRAKE SYSTEM 4F-11
ABS, ABS/ABD 5.0
Initializing
1. Set the ignition switch n “ON” position.
2. Connect the No.1 terminal (Ground) and the No.13 (ABS)
from diagnosis socket located in E/G room by use of service
connector for 3 - 4 seconds and initialize the flash code.
Notice
Be careful not to connect over 5 seconds.
3. ABS indicator warning light continuously comes on until the
ignition switch is “OFF”.
Dignosis Table
1. When the system is normal
lOne pulse (normal code 01) indicates.
2. When the system is abnormal
lOne pulse (defect code) indicates.
Notice
Repeat the initializing procedure when checking the
defect code Defect code is indicated once for 1 sec (light
on : 0.75 sec, light off : 0.25 sec).
Removal the Defect Code
1. Repair the defect code and remove the memorized defect
code in the ECU.
2. Connect the No. 13 terminal (ABS) from diagnosis socket
and No. 1 terminal (ground) for over 5 seconds.
3. Set the ignition switch in the “OFF” position.
Notice
lDefect code will be memorized in ECU unless the defect
code is not removed.
lRepeat the initializing procedure and check the other
defects.
Page 964 of 1463
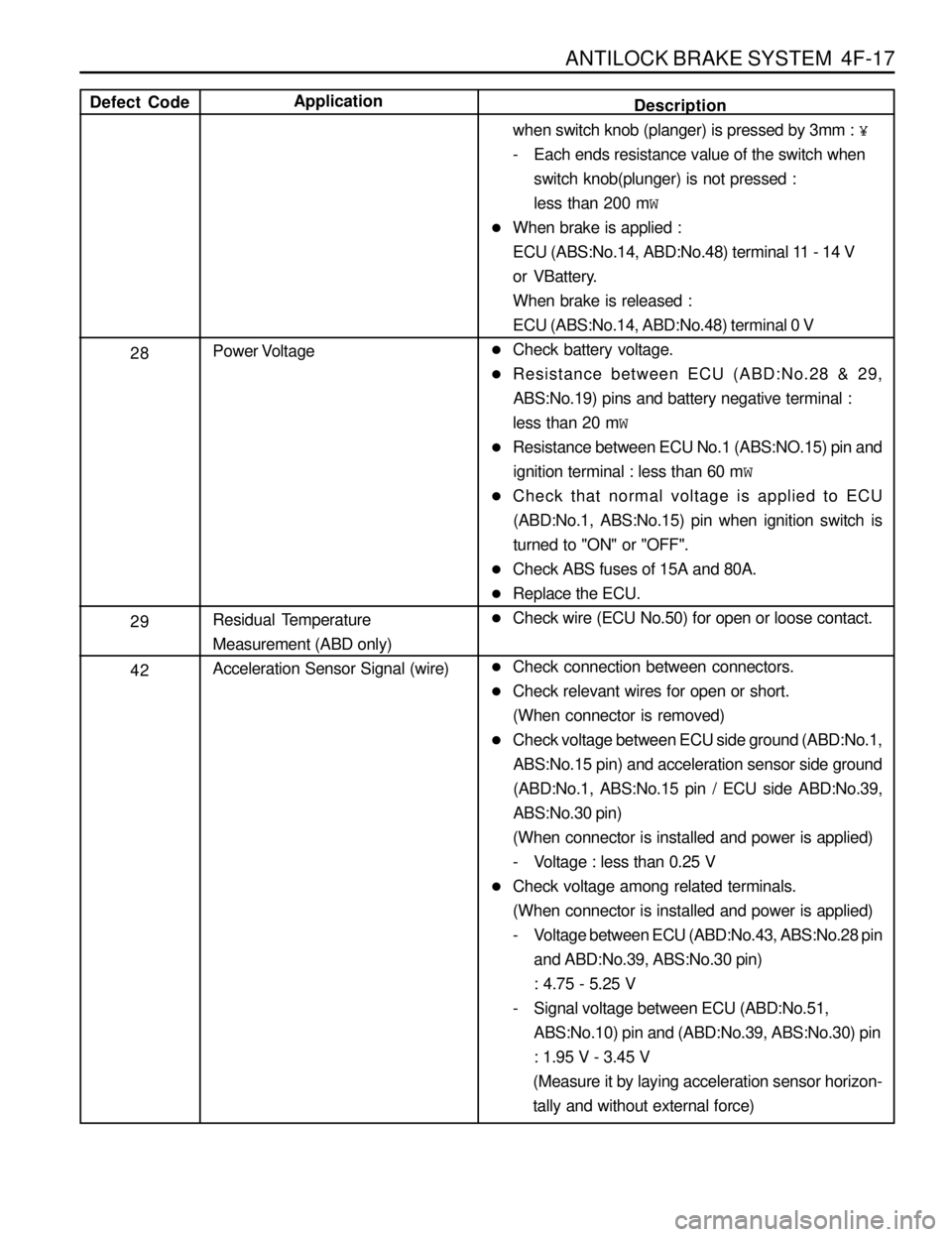
ANTILOCK BRAKE SYSTEM 4F-17
Application
Power Voltage
Residual Temperature
Measurement (ABD only)
Acceleration Sensor Signal (wire)Defect Code
28
29
42Description
when switch knob (planger) is pressed by 3mm : ¥
- Each ends resistance value of the switch when
switch knob(plunger) is not pressed :
less than 200 mW
lWhen brake is applied :
ECU (ABS:No.14, ABD:No.48) terminal 11 - 14 V
or VBattery.
When brake is released :
ECU (ABS:No.14, ABD:No.48) terminal 0 V
lCheck battery voltage.
lResistance between ECU (ABD:No.28 & 29,
ABS:No.19) pins and battery negative terminal :
less than 20 mW
lResistance between ECU No.1 (ABS:NO.15) pin and
ignition terminal : less than 60 mW
lCheck that normal voltage is applied to ECU
(ABD:No.1, ABS:No.15) pin when ignition switch is
turned to "ON" or "OFF".
lCheck ABS fuses of 15A and 80A.
lReplace the ECU.
lCheck wire (ECU No.50) for open or loose contact.
lCheck connection between connectors.
lCheck relevant wires for open or short.
(When connector is removed)
lCheck voltage between ECU side ground (ABD:No.1,
ABS:No.15 pin) and acceleration sensor side ground
(ABD:No.1, ABS:No.15 pin / ECU side ABD:No.39,
ABS:No.30 pin)
(When connector is installed and power is applied)
- Voltage : less than 0.25 V
lCheck voltage among related terminals.
(When connector is installed and power is applied)
- Voltage between ECU (ABD:No.43, ABS:No.28 pin
and ABD:No.39, ABS:No.30 pin)
: 4.75 - 5.25 V
- Signal voltage between ECU (ABD:No.51,
ABS:No.10) pin and (ABD:No.39, ABS:No.30) pin
: 1.95 V - 3.45 V
(Measure it by laying acceleration sensor horizon-
tally and without external force)
Page 974 of 1463
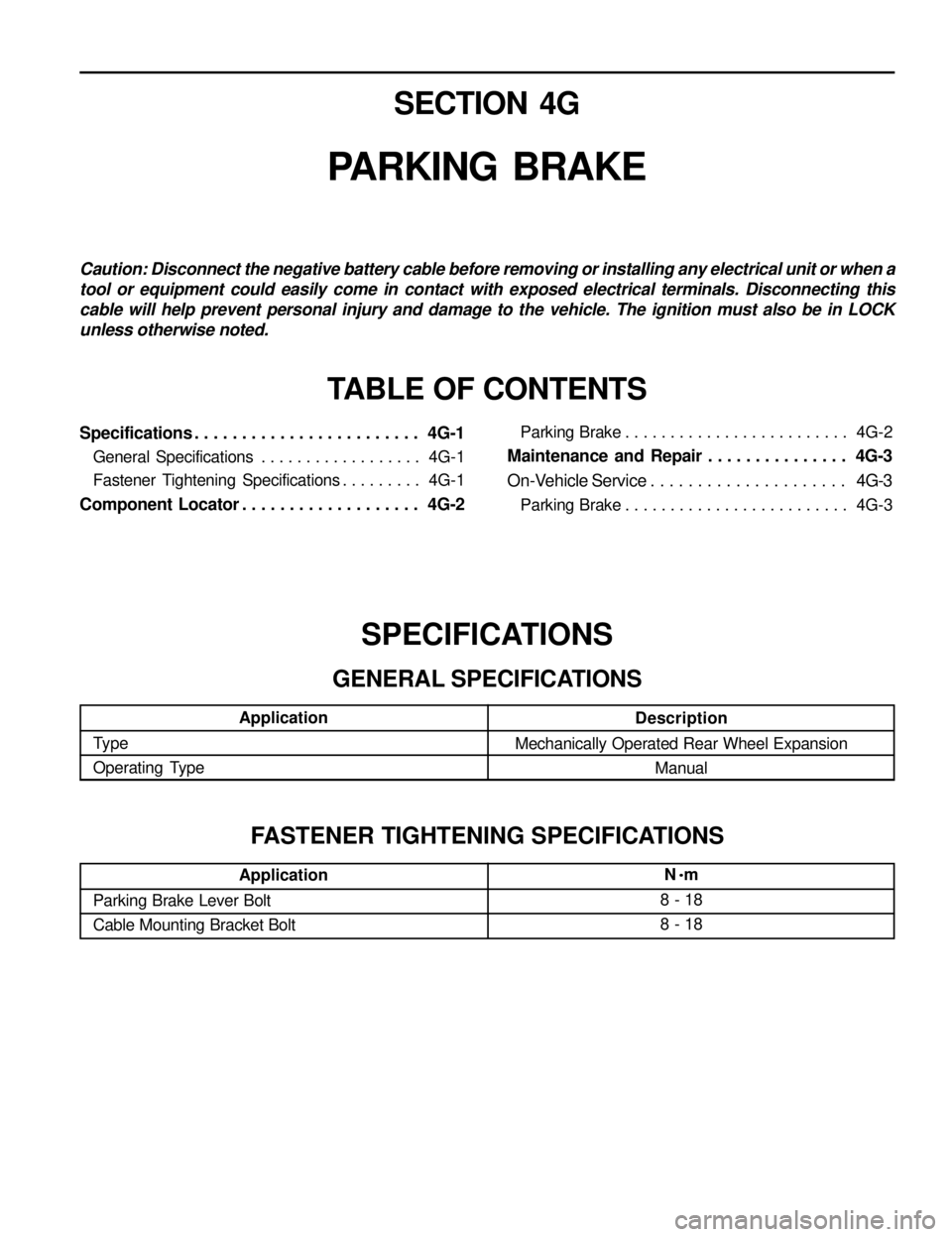
SECTION 4G
PARKING BRAKE
Specifications . . . . . . . . . . . . . . . . . . . . . . . . 4G-1
General Specifications . . . . . . . . . . . . . . . . . . 4G-1
Fastener Tightening Specifications . . . . . . . . . 4G-1
Component Locator . . . . . . . . . . . . . . . . . . . 4G-2
TABLE OF CONTENTS
Parking Brake . . . . . . . . . . . . . . . . . . . . . . . . . 4G-2
Maintenance and Repair . . . . . . . . . . . . . . . 4G-3
On-Vehicle Service . . . . . . . . . . . . . . . . . . . . . 4G-3
Parking Brake . . . . . . . . . . . . . . . . . . . . . . . . . 4G-3
Caution: Disconnect the negative battery cable before removing or installing any electrical unit or when a
tool or equipment could easily come in contact with exposed electrical terminals. Disconnecting this
cable will help prevent personal injury and damage to the vehicle. The ignition must also be in LOCK
unless otherwise noted.
SPECIFICATIONS
GENERAL SPECIFICATIONS
Application
Parking Brake Lever Bolt
Cable Mounting Bracket BoltN
· ·· ·
·m
8 - 18
8 - 18
FASTENER TIGHTENING SPECIFICATIONS
Application
Type
Operating TypeDescription
Mechanically Operated Rear Wheel Expansion
Manual
Page 1038 of 1463
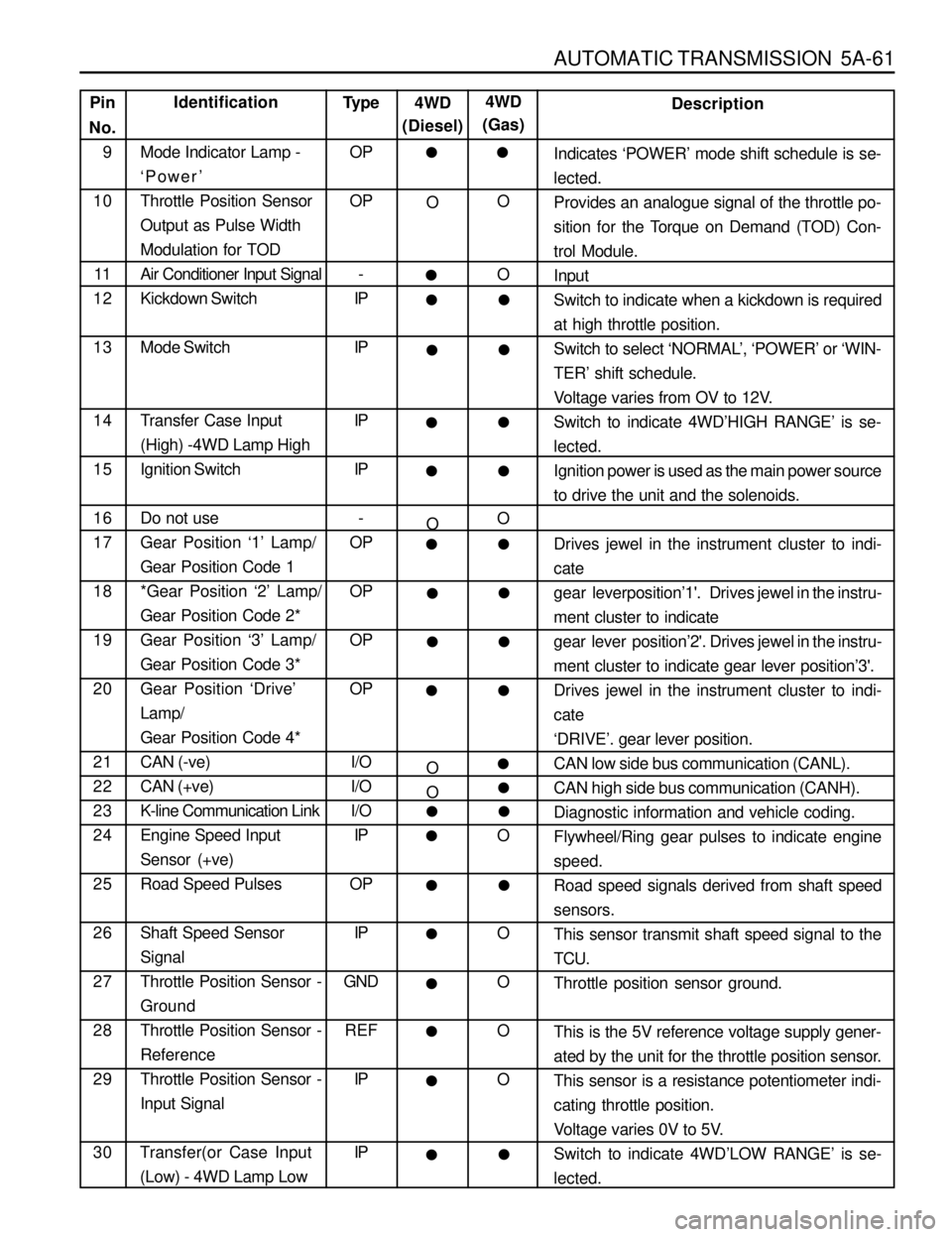
AUTOMATIC TRANSMISSION 5A-61
Pin
No.
9
10
11
12
13
14
15
16
17
18
19
20
21
22
23
24
25
26
27
28
29
30Identification
Mode Indicator Lamp -
‘Power’
Throttle Position Sensor
Output as Pulse Width
Modulation for TOD
Air Conditioner Input Signal
Kickdown Switch
Mode Switch
Transfer Case Input
(High) -4WD Lamp High
Ignition Switch
Do not use
Gear Position ‘1’ Lamp/
Gear Position Code 1
*Gear Position ‘2’ Lamp/
Gear Position Code 2*
Gear Position ‘3’ Lamp/
Gear Position Code 3*
Gear Position ‘Drive’
Lamp/
Gear Position Code 4*
CAN (-ve)
CAN (+ve)
K-line Communication Link
Engine Speed Input
Sensor (+ve)
Road Speed Pulses
Shaft Speed Sensor
Signal
Throttle Position Sensor -
Ground
Throttle Position Sensor -
Reference
Throttle Position Sensor -
Input Signal
Transfer(or Case Input
(Low) - 4WD Lamp LowType
OP
OP
-
IP
IP
IP
IP
-
OP
OP
OP
OP
I/O
I/O
I/O
IP
OP
IP
GND
REF
IP
IPDescription
Indicates ‘POWER’ mode shift schedule is se-
lected.
Provides an analogue signal of the throttle po-
sition for the Torque on Demand (TOD) Con-
trol Module.
Input
Switch to indicate when a kickdown is required
at high throttle position.
Switch to select ‘NORMAL’, ‘POWER’ or ‘WIN-
TER’ shift schedule.
Voltage varies from OV to 12V.
Switch to indicate 4WD’HIGH RANGE’ is se-
lected.
Ignition power is used as the main power source
to drive the unit and the solenoids.
Drives jewel in the instrument cluster to indi-
cate
gear leverposition’1'. Drives jewel in the instru-
ment cluster to indicate
gear lever position’2'. Drives jewel in the instru-
ment cluster to indicate gear lever position’3'.
Drives jewel in the instrument cluster to indi-
cate
‘DRIVE’. gear lever position.
CAN low side bus communication (CANL).
CAN high side bus communication (CANH).
Diagnostic information and vehicle coding.
Flywheel/Ring gear pulses to indicate engine
speed.
Road speed signals derived from shaft speed
sensors.
This sensor transmit shaft speed signal to the
TCU.
Throttle position sensor ground.
This is the 5V reference voltage supply gener-
ated by the unit for the throttle position sensor.
This sensor is a resistance potentiometer indi-
cating throttle position.
Voltage varies 0V to 5V.
Switch to indicate 4WD’LOW RANGE’ is se-
lected. 4WD
(Diesel)
O
O
O
O
l
l
l
4WD
(Gas)
O
O
O
O
O
O
O
O
l
l
l
ll
ll
ll
ll
ll
ll
l
l
ll
l
ll
l
l
l
l
ll l
Page 1044 of 1463
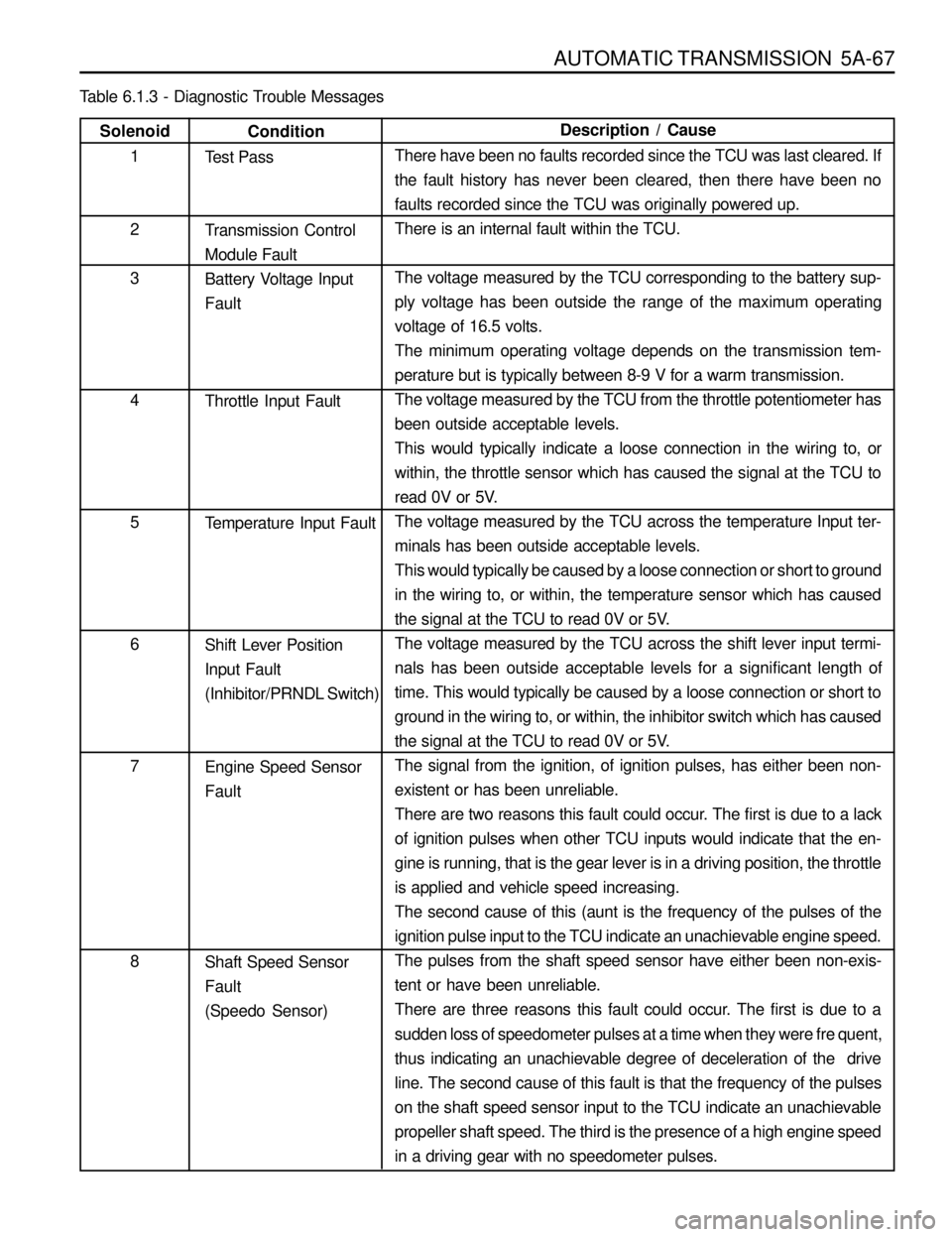
AUTOMATIC TRANSMISSION 5A-67
Table 6.1.3 - Diagnostic Trouble Messages
Description / Cause
There have been no faults recorded since the TCU was last cleared. If
the fault history has never been cleared, then there have been no
faults recorded since the TCU was originally powered up.
There is an internal fault within the TCU.
The voltage measured by the TCU corresponding to the battery sup-
ply voltage has been outside the range of the maximum operating
voltage of 16.5 volts.
The minimum operating voltage depends on the transmission tem-
perature but is typically between 8-9 V for a warm transmission.
The voltage measured by the TCU from the throttle potentiometer has
been outside acceptable levels.
This would typically indicate a loose connection in the wiring to, or
within, the throttle sensor which has caused the signal at the TCU to
read 0V or 5V.
The voltage measured by the TCU across the temperature Input ter-
minals has been outside acceptable levels.
This would typically be caused by a loose connection or short to ground
in the wiring to, or within, the temperature sensor which has caused
the signal at the TCU to read 0V or 5V.
The voltage measured by the TCU across the shift lever input termi-
nals has been outside acceptable levels for a significant length of
time. This would typically be caused by a loose connection or short to
ground in the wiring to, or within, the inhibitor switch which has caused
the signal at the TCU to read 0V or 5V.
The signal from the ignition, of ignition pulses, has either been non-
existent or has been unreliable.
There are two reasons this fault could occur. The first is due to a lack
of ignition pulses when other TCU inputs would indicate that the en-
gine is running, that is the gear lever is in a driving position, the throttle
is applied and vehicle speed increasing.
The second cause of this (aunt is the frequency of the pulses of the
ignition pulse input to the TCU indicate an unachievable engine speed.
The pulses from the shaft speed sensor have either been non-exis-
tent or have been unreliable.
There are three reasons this fault could occur. The first is due to a
sudden loss of speedometer pulses at a time when they were fre quent,
thus indicating an unachievable degree of deceleration of the drive
line. The second cause of this fault is that the frequency of the pulses
on the shaft speed sensor input to the TCU indicate an unachievable
propeller shaft speed. The third is the presence of a high engine speed
in a driving gear with no speedometer pulses. Condition
Test Pass
Transmission Control
Module Fault
Battery Voltage Input
Fault
Throttle Input Fault
Temperature Input Fault
Shift Lever Position
Input Fault
(Inhibitor/PRNDL Switch)
Engine Speed Sensor
Fault
Shaft Speed Sensor
Fault
(Speedo Sensor)Solenoid
1
2
3
4
5
6
7
8
Page 1052 of 1463
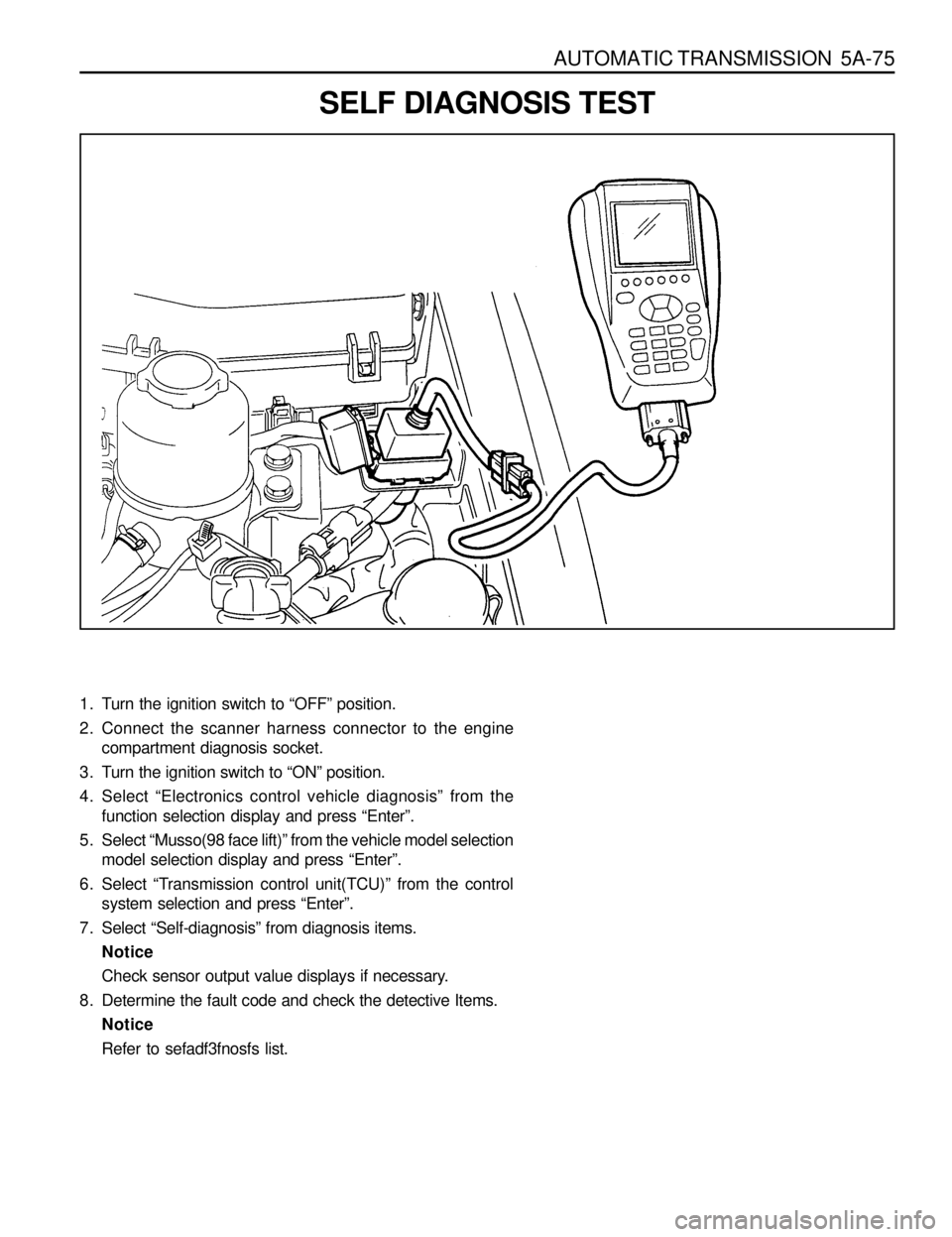
AUTOMATIC TRANSMISSION 5A-75
SELF DIAGNOSIS TEST
1. Turn the ignition switch to “OFF” position.
2. Connect the scanner harness connector to the engine
compartment diagnosis socket.
3. Turn the ignition switch to “ON” position.
4. Select “Electronics control vehicle diagnosis” from the
function selection display and press “Enter”.
5. Select “Musso(98 face lift)” from the vehicle model selection
model selection display and press “Enter”.
6. Select “Transmission control unit(TCU)” from the control
system selection and press “Enter”.
7. Select “Self-diagnosis” from diagnosis items.
Notice
Check sensor output value displays if necessary.
8. Determine the fault code and check the detective Items.
Notice
Refer to sefadf3fnosfs list.
Page 1054 of 1463
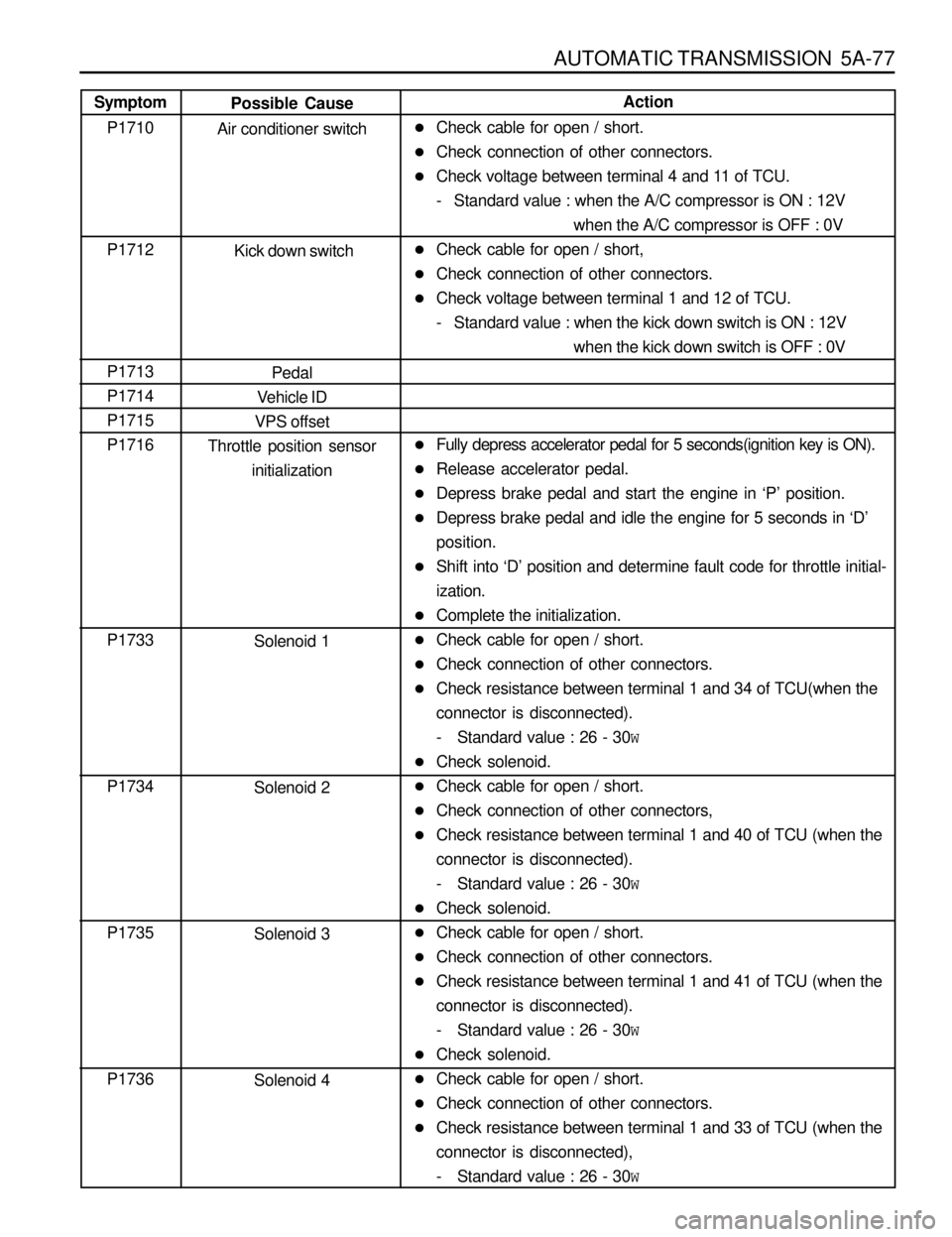
AUTOMATIC TRANSMISSION 5A-77
Action
lCheck cable for open / short.
lCheck connection of other connectors.
lCheck voltage between terminal 4 and 11 of TCU.
- Standard value : when the A/C compressor is ON : 12V
when the A/C compressor is OFF : 0V
lCheck cable for open / short,
lCheck connection of other connectors.
lCheck voltage between terminal 1 and 12 of TCU.
- Standard value : when the kick down switch is ON : 12V
when the kick down switch is OFF : 0V
lFully depress accelerator pedal for 5 seconds(ignition key is ON).
lRelease accelerator pedal.
lDepress brake pedal and start the engine in ‘P’ position.
lDepress brake pedal and idle the engine for 5 seconds in ‘D’
position.
lShift into ‘D’ position and determine fault code for throttle initial-
ization.
lComplete the initialization.
lCheck cable for open / short.
lCheck connection of other connectors.
lCheck resistance between terminal 1 and 34 of TCU(when the
connector is disconnected).
- Standard value : 26 - 30
W
lCheck solenoid.
lCheck cable for open / short.
lCheck connection of other connectors,
lCheck resistance between terminal 1 and 40 of TCU (when the
connector is disconnected).
- Standard value : 26 - 30
W
lCheck solenoid.
lCheck cable for open / short.
lCheck connection of other connectors.
lCheck resistance between terminal 1 and 41 of TCU (when the
connector is disconnected).
- Standard value : 26 - 30
W
lCheck solenoid.
lCheck cable for open / short.
lCheck connection of other connectors.
lCheck resistance between terminal 1 and 33 of TCU (when the
connector is disconnected),
- Standard value : 26 - 30
W
Possible Cause
Air conditioner switch
Kick down switch
Pedal
Vehicle ID
VPS offset
Throttle position sensor
initialization
Solenoid 1
Solenoid 2
Solenoid 3
Solenoid 4 Symptom
P1710
P1712
P1713
P1714
P1715
P1716
P1733
P1734
P1735
P1736
Page 1057 of 1463
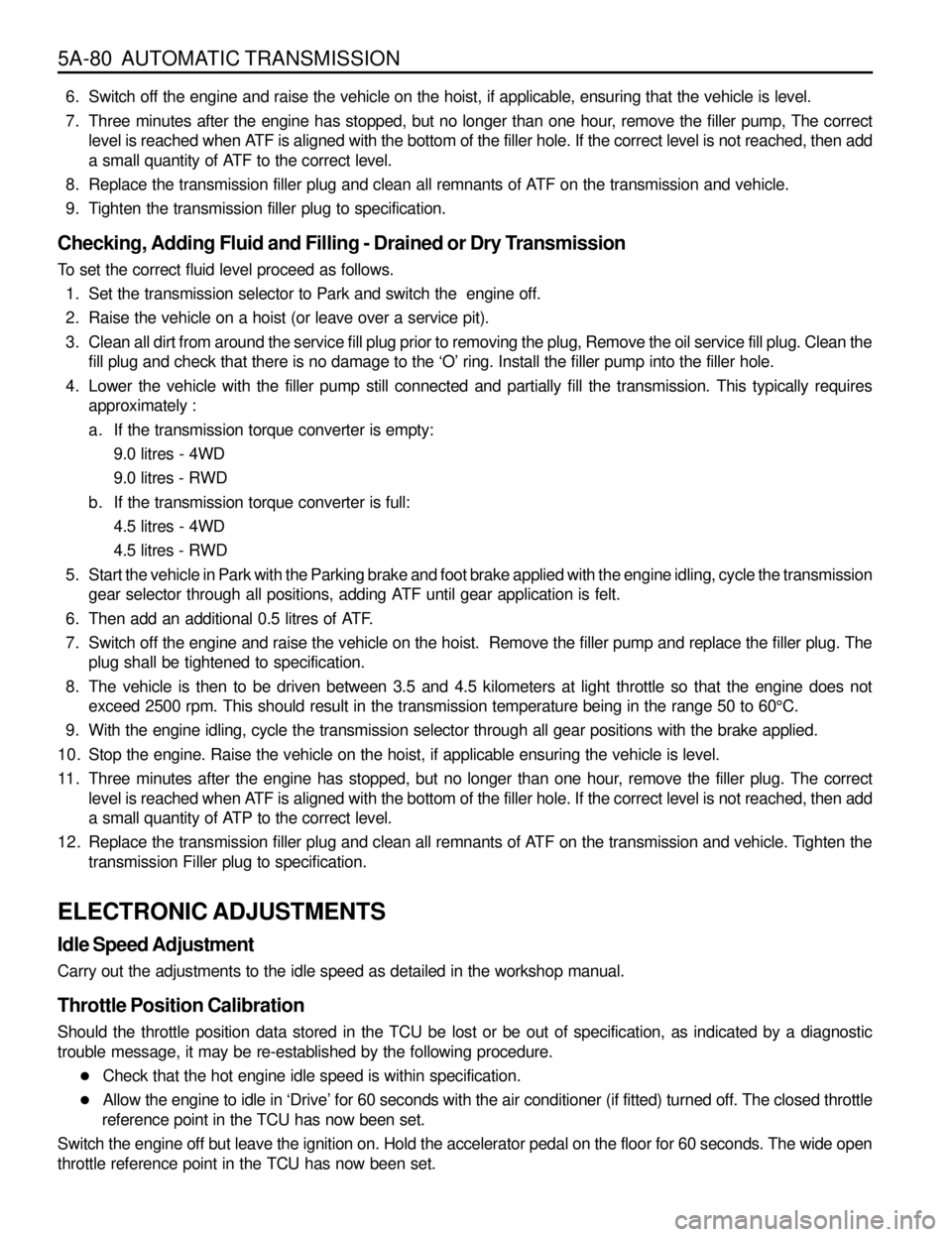
5A-80 AUTOMATIC TRANSMISSION
6. Switch off the engine and raise the vehicle on the hoist, if applicable, ensuring that the vehicle is level.
7. Three minutes after the engine has stopped, but no longer than one hour, remove the filler pump, The correct
level is reached when ATF is aligned with the bottom of the filler hole. If the correct level is not reached, then add
a small quantity of ATF to the correct level.
8. Replace the transmission filler plug and clean all remnants of ATF on the transmission and vehicle.
9. Tighten the transmission filler plug to specification.
Checking, Adding Fluid and Filling - Drained or Dry Transmission
To set the correct fluid level proceed as follows.
1. Set the transmission selector to Park and switch the engine off.
2. Raise the vehicle on a hoist (or leave over a service pit).
3. Clean all dirt from around the service fill plug prior to removing the plug, Remove the oil service fill plug. Clean the
fill plug and check that there is no damage to the ‘O’ ring. Install the filler pump into the filler hole.
4. Lower the vehicle with the filler pump still connected and partially fill the transmission. This typically requires
approximately :
a. If the transmission torque converter is empty:
9.0 litres - 4WD
9.0 litres - RWD
b. If the transmission torque converter is full:
4.5 litres - 4WD
4.5 litres - RWD
5. Start the vehicle in Park with the Parking brake and foot brake applied with the engine idling, cycle the transmission
gear selector through all positions, adding ATF until gear application is felt.
6. Then add an additional 0.5 litres of ATF.
7. Switch off the engine and raise the vehicle on the hoist. Remove the filler pump and replace the filler plug. The
plug shall be tightened to specification.
8. The vehicle is then to be driven between 3.5 and 4.5 kilometers at light throttle so that the engine does not
exceed 2500 rpm. This should result in the transmission temperature being in the range 50 to 60°C.
9. With the engine idling, cycle the transmission selector through all gear positions with the brake applied.
10. Stop the engine. Raise the vehicle on the hoist, if applicable ensuring the vehicle is level.
11. Three minutes after the engine has stopped, but no longer than one hour, remove the filler plug. The correct
level is reached when ATF is aligned with the bottom of the filler hole. If the correct level is not reached, then add
a small quantity of ATP to the correct level.
12. Replace the transmission filler plug and clean all remnants of ATF on the transmission and vehicle. Tighten the
transmission Filler plug to specification.
ELECTRONIC ADJUSTMENTS
Idle Speed Adjustment
Carry out the adjustments to the idle speed as detailed in the workshop manual.
Throttle Position Calibration
Should the throttle position data stored in the TCU be lost or be out of specification, as indicated by a diagnostic
trouble message, it may be re-established by the following procedure.
lCheck that the hot engine idle speed is within specification.
lAllow the engine to idle in ‘Drive’ for 60 seconds with the air conditioner (if fitted) turned off. The closed throttle
reference point in the TCU has now been set.
Switch the engine off but leave the ignition on. Hold the accelerator pedal on the floor for 60 seconds. The wide open
throttle reference point in the TCU has now been set.