SSANGYONG MUSSO 1998 Workshop Repair Manual
MUSSO 1998
SSANGYONG
SSANGYONG
https://www.carmanualsonline.info/img/67/57510/w960_57510-0.png
SSANGYONG MUSSO 1998 Workshop Repair Manual
Page 717 of 1463
1F2-68 M161 ENGINE CONTROLS
CAMSHAFT POSITION SENSOR
1 Bolt (M6 X 14)......................................... 9-11Nm
2 Camshaft Position Sensor
Removal & Installation Procedure
1. Disconnect the wiring connector from the camshaft position
sensor.
2. Unscrew the bolt (2) and remove the camshaft position
sensor.
Installation Notice3 Shim
5 O-ring
Tightening Torque 9 - 11 Nm
3. Check the clearance and replace the shim if necessary.
4. Check the O-ring for damage and replace it if necessary.
5. Installation should follow the removal procedure in the
reverse order.
Page 718 of 1463
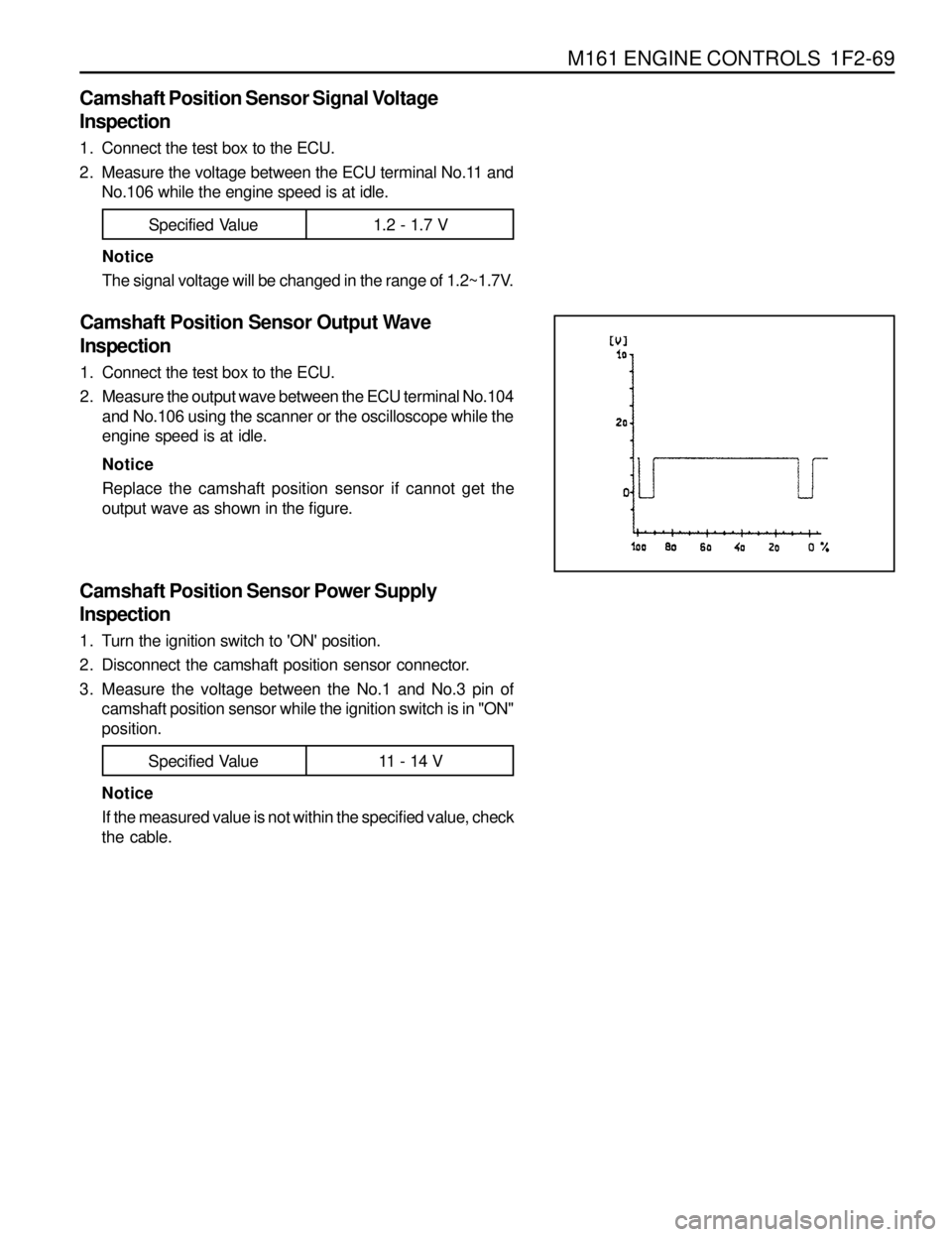
M161 ENGINE CONTROLS 1F2-69
Camshaft Position Sensor Power Supply
Inspection
1. Turn the ignition switch to 'ON' position.
2. Disconnect the camshaft position sensor connector.
3. Measure the voltage between the No.1 and No.3 pin of
camshaft position sensor while the ignition switch is in "ON"
position.
Notice
If the measured value is not within the specified value, check
the cable.Notice
The signal voltage will be changed in the range of 1.2~1.7V.
Camshaft Position Sensor Output Wave
Inspection
1. Connect the test box to the ECU.
2. Measure the output wave between the ECU terminal No.104
and No.106 using the scanner or the oscilloscope while the
engine speed is at idle.
Notice
Replace the camshaft position sensor if cannot get the
output wave as shown in the figure.
Specified Value 11 - 14 V
Specified Value 1.2 - 1.7 V
Camshaft Position Sensor Signal Voltage
Inspection
1. Connect the test box to the ECU.
2. Measure the voltage between the ECU terminal No.11 and
No.106 while the engine speed is at idle.
Page 725 of 1463
1F2-76 M161 ENGINE CONTROLS
COOLANT TEMPERATURE SENSOR
1 Artificial Resin Housing
2 Metal Housing
3 NTC (negative temperature coefficient) Resistor
Removal & Installation Procedure
1. Remove the pressure by opening the pressure cap in the
coolant subtank.
2. Disconnect the connector and remove the coolant
temperature sensor.
Installation Notice
Replace the seals with new one.
3. Installation should follow the removal procedure in the
reverse order.
4. Check for leaks at each connections after starting the engine.4 Connector
5 Coolant Temperature Sensor
Tightening Torque 18 - 22 Nm
Page 733 of 1463
1F3-4 OM600 ENGINE CONTROLS
FUEL TANK
1 Fuel Tank
2 The Sender of Fuel Tank
3 2-way Check Valve
4 Pre Filter
5 Front Fuel Filler Neck
6 Rear Fuel Filler Neck
7 Fuel Supply Tube8 Fuel Return Tube
9 Filter Hose
10 Fuel Tank Hose
11 Fuel Filler Cap
1 2 Clip
1 3 Clip
Page 734 of 1463
OM600 ENGINE CONTROLS 1F3-5
VACUUM CONTROL SYSTEM TEST
2 Engine Cut-Off Valve (Ignition Key Switch)
3 Auto-locking Hub Solenoid Valve
4 Engine Stop Valve Unit
5 PLA Vacuum Unit (Idle Speed Adjustment)
6 Engine
7 Vacuum Pump8 30° Thermovalve
9 Fuel Injection Pump
10 Filter with Restriction
11 Check Valve
12 Modulating Pressure Line (Automatic T/M)
Test Data
Idle Speed Increase
Permissible Pressure Drop of SystemAt least 100 rpm at approx. 500mbr
400 - 500mbar approx. 1 min.
Page 741 of 1463
1F3-12 OM600 ENGINE CONTROLS
Test Procedure
1. Remove the fuel filter (1) and keep the filter not to be
damaged from running engine.
2. Remove the vacuum line (2) from ancillaries connection (3).
3. Connect the vacuum tester (4) to the ancillaries connection
(3).
Vacuum Tester 201 589 13 21 00
4 Run the engine at idle and check vacuum pressure after 30
sec.
Notice
If out of standard, replace the vacuum pump.
5. Remove the vacuum tester.
6. Connect the vacuum line to the ancillaries connection.
7. Install the fuel filter.
Standard > 70 mbar
Page 745 of 1463
1F3-16 OM600 ENGINE CONTROLS
Idle Speed
750 - 850 rpm
720 - 820 rpm Engine
OM661LA Engine
OM662LA Engine
Tools Required
667 589 00 21 00 TDC Pulse Generato
Commercial Tool
IDLE SPEED ADJUSTMENT
Service Data
e.g. Bosch, MOT 001.03
Sun, DIT 9000 Digital Tester
Adjustment Procedure
1. Connect the digital tester (1) and TDC pulse sender unit
(11).
2. Run the engine and warm up the coolant to 60~80°C.
TDC pulse generator 667 589 02 21 00
3. Disconnect the vacuum hose (4) from the PLA unit to check
idle speed with tester.
4. Check idle speed with tester.
Notice
To adjust idle speed, loosen the locking nut (6) of PLA unit.
OM 661LA Engine750 - 850rpm
OM 662LA Engine
720 - 820rpm
Page 746 of 1463
OM600 ENGINE CONTROLS 1F3-17
6. After adjustment, tighten the locking nut and place the
position marking with different color of paint.
Notice
If there are no changes in idle speed with PLA unit
adjustment, perform the service at a BOSCH Service Center.
7. Connect the vacuum pump to the PLA vacuum unit and
build up vacuum approx. 500mbar. If engine rpm increases
by approx. 100rpm, It is normal.
Vacuum Pump 001 589 73 21 00
8. Connect the vacuum line (4).
9. Switch on all ancillaries and check the idle speed.
5. Ensure not to damage the idle spring in the governor and
adjust idle speed by turning the PLA unit (5) slowly.
Notice
Do not rotate the PLA unit over ½ turn from the position
marking. If do, idle spring in the governor will be severely
damaged.Clockwise
Counterclockwise
RPM Decrease
RPM Increase
Page 758 of 1463
OM600 ENGINE CONTROLS 1F3-29
7. Check the fuel injection nozzle and adjust opening pressure
if necessary.
Opening pressure adjustment
Disassemble the fuel injection nozzle and replace the steel
washer (2).
Notice
Each 0.05mm thickness of the washer results in a pressure
difference of approx. 3bar.
Page 759 of 1463
1F3-30 OM600 ENGINE CONTROLS
REMOVAL AND INSTALLATION OF INJECTION TIMING DEVICE
Preceding Work : Removal of vacuum pump
1 Cylinder Head Cover
2 Bolt............................................................10Nm
3 Gasket ................................................... Replace
4 Fuel Injection Pump
5 Seal....................................................... Replace
6 Screw Plug.................................................30Nm
7 Oil Pan
8 Locking Pin
9 Injection Timing Device10 Washer
11 Bolt (Left-Hand Thread).............................46Nm
12 Camshaft Sprocket
13 Washer
14 12-Sided Stretch Bolt............Check, 25Nm + 90°
15 Timing Chain
1 6 Seal
17 Chain Tensioner.........................................80Nm