check engine SSANGYONG MUSSO 1998 Workshop Repair Manual
[x] Cancel search | Manufacturer: SSANGYONG, Model Year: 1998, Model line: MUSSO, Model: SSANGYONG MUSSO 1998Pages: 1463, PDF Size: 19.88 MB
Page 1054 of 1463
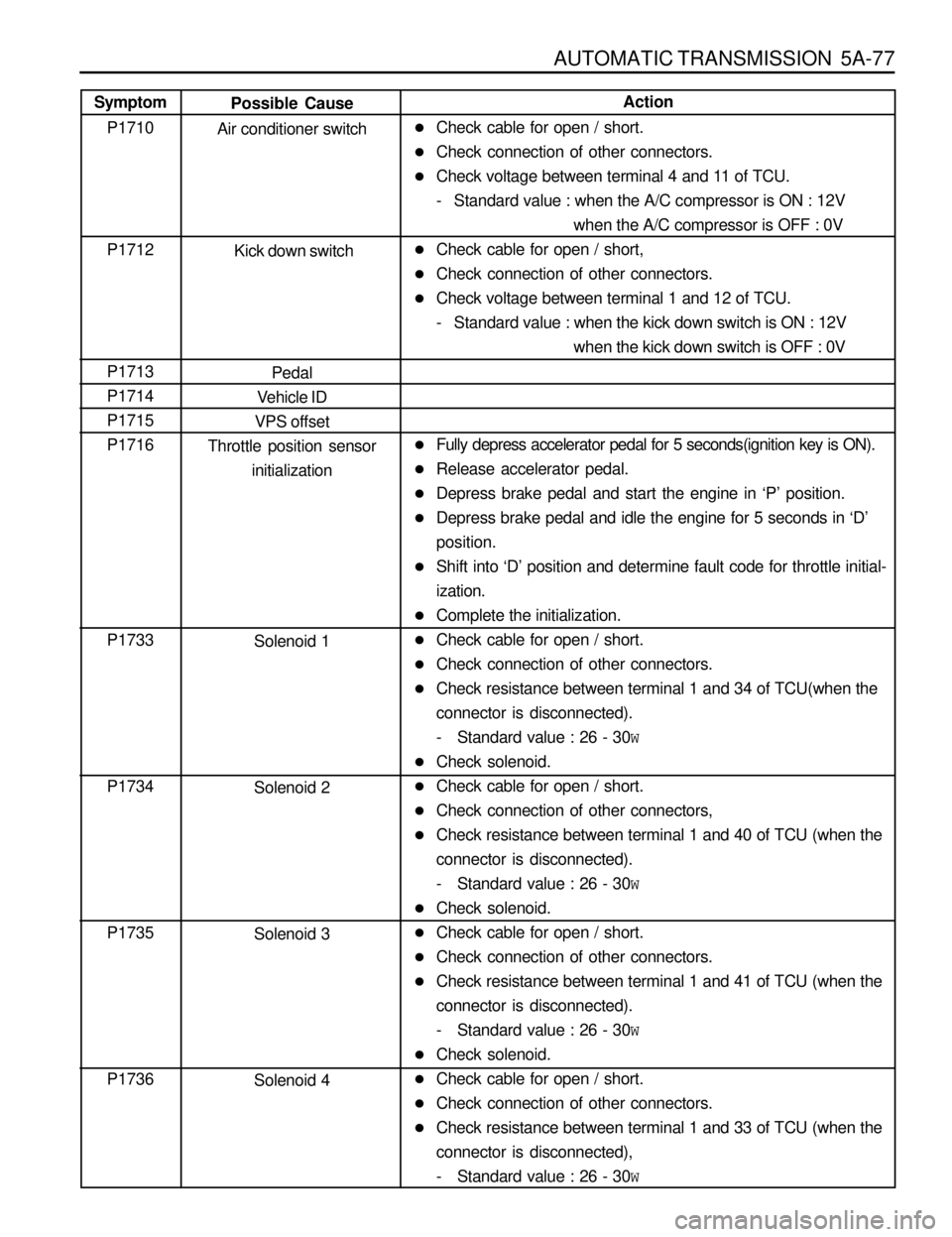
AUTOMATIC TRANSMISSION 5A-77
Action
lCheck cable for open / short.
lCheck connection of other connectors.
lCheck voltage between terminal 4 and 11 of TCU.
- Standard value : when the A/C compressor is ON : 12V
when the A/C compressor is OFF : 0V
lCheck cable for open / short,
lCheck connection of other connectors.
lCheck voltage between terminal 1 and 12 of TCU.
- Standard value : when the kick down switch is ON : 12V
when the kick down switch is OFF : 0V
lFully depress accelerator pedal for 5 seconds(ignition key is ON).
lRelease accelerator pedal.
lDepress brake pedal and start the engine in ‘P’ position.
lDepress brake pedal and idle the engine for 5 seconds in ‘D’
position.
lShift into ‘D’ position and determine fault code for throttle initial-
ization.
lComplete the initialization.
lCheck cable for open / short.
lCheck connection of other connectors.
lCheck resistance between terminal 1 and 34 of TCU(when the
connector is disconnected).
- Standard value : 26 - 30
W
lCheck solenoid.
lCheck cable for open / short.
lCheck connection of other connectors,
lCheck resistance between terminal 1 and 40 of TCU (when the
connector is disconnected).
- Standard value : 26 - 30
W
lCheck solenoid.
lCheck cable for open / short.
lCheck connection of other connectors.
lCheck resistance between terminal 1 and 41 of TCU (when the
connector is disconnected).
- Standard value : 26 - 30
W
lCheck solenoid.
lCheck cable for open / short.
lCheck connection of other connectors.
lCheck resistance between terminal 1 and 33 of TCU (when the
connector is disconnected),
- Standard value : 26 - 30
W
Possible Cause
Air conditioner switch
Kick down switch
Pedal
Vehicle ID
VPS offset
Throttle position sensor
initialization
Solenoid 1
Solenoid 2
Solenoid 3
Solenoid 4 Symptom
P1710
P1712
P1713
P1714
P1715
P1716
P1733
P1734
P1735
P1736
Page 1056 of 1463
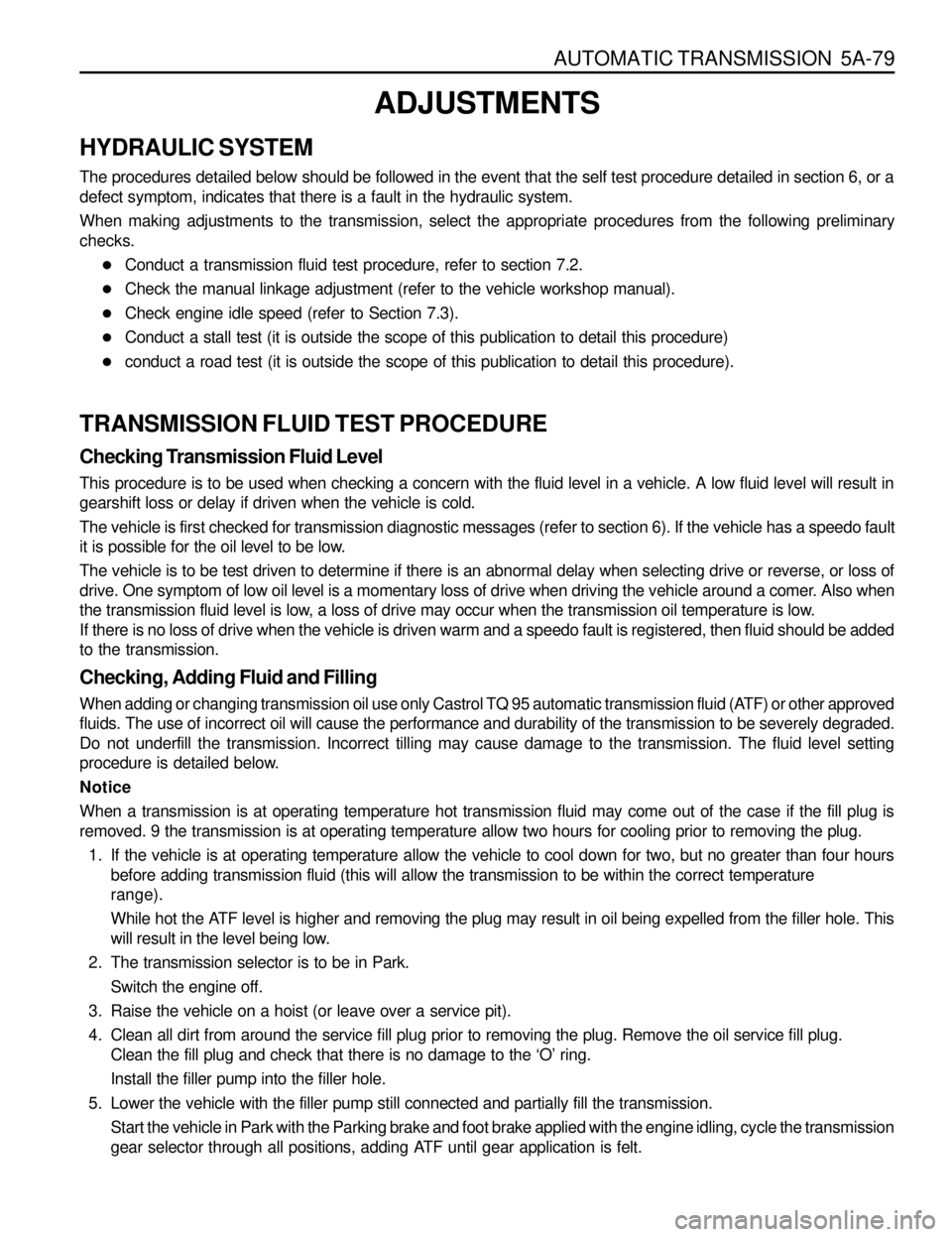
AUTOMATIC TRANSMISSION 5A-79
ADJUSTMENTS
HYDRAULIC SYSTEM
The procedures detailed below should be followed in the event that the self test procedure detailed in section 6, or a
defect symptom, indicates that there is a fault in the hydraulic system.
When making adjustments to the transmission, select the appropriate procedures from the following preliminary
checks.
lConduct a transmission fluid test procedure, refer to section 7.2.
lCheck the manual linkage adjustment (refer to the vehicle workshop manual).
lCheck engine idle speed (refer to Section 7.3).
lConduct a stall test (it is outside the scope of this publication to detail this procedure)
lconduct a road test (it is outside the scope of this publication to detail this procedure).
TRANSMISSION FLUID TEST PROCEDURE
Checking Transmission Fluid Level
This procedure is to be used when checking a concern with the fluid level in a vehicle. A low fluid level will result in
gearshift loss or delay if driven when the vehicle is cold.
The vehicle is first checked for transmission diagnostic messages (refer to section 6). If the vehicle has a speedo fault
it is possible for the oil level to be low.
The vehicle is to be test driven to determine if there is an abnormal delay when selecting drive or reverse, or loss of
drive. One symptom of low oil level is a momentary loss of drive when driving the vehicle around a comer. Also when
the transmission fluid level is low, a loss of drive may occur when the transmission oil temperature is low.
If there is no loss of drive when the vehicle is driven warm and a speedo fault is registered, then fluid should be added
to the transmission.
Checking, Adding Fluid and Filling
When adding or changing transmission oil use only Castrol TQ 95 automatic transmission fluid (ATF) or other approved
fluids. The use of incorrect oil will cause the performance and durability of the transmission to be severely degraded.
Do not underfill the transmission. Incorrect tilling may cause damage to the transmission. The fluid level setting
procedure is detailed below.
Notice
When a transmission is at operating temperature hot transmission fluid may come out of the case if the fill plug is
removed. 9 the transmission is at operating temperature allow two hours for cooling prior to removing the plug.
1. If the vehicle is at operating temperature allow the vehicle to cool down for two, but no greater than four hours
before adding transmission fluid (this will allow the transmission to be within the correct temperature
range).
While hot the ATF level is higher and removing the plug may result in oil being expelled from the filler hole. This
will result in the level being low.
2. The transmission selector is to be in Park.
Switch the engine off.
3. Raise the vehicle on a hoist (or leave over a service pit).
4. Clean all dirt from around the service fill plug prior to removing the plug. Remove the oil service fill plug.
Clean the fill plug and check that there is no damage to the ‘O’ ring.
Install the filler pump into the filler hole.
5. Lower the vehicle with the filler pump still connected and partially fill the transmission.
Start the vehicle in Park with the Parking brake and foot brake applied with the engine idling, cycle the transmission
gear selector through all positions, adding ATF until gear application is felt.
Page 1057 of 1463
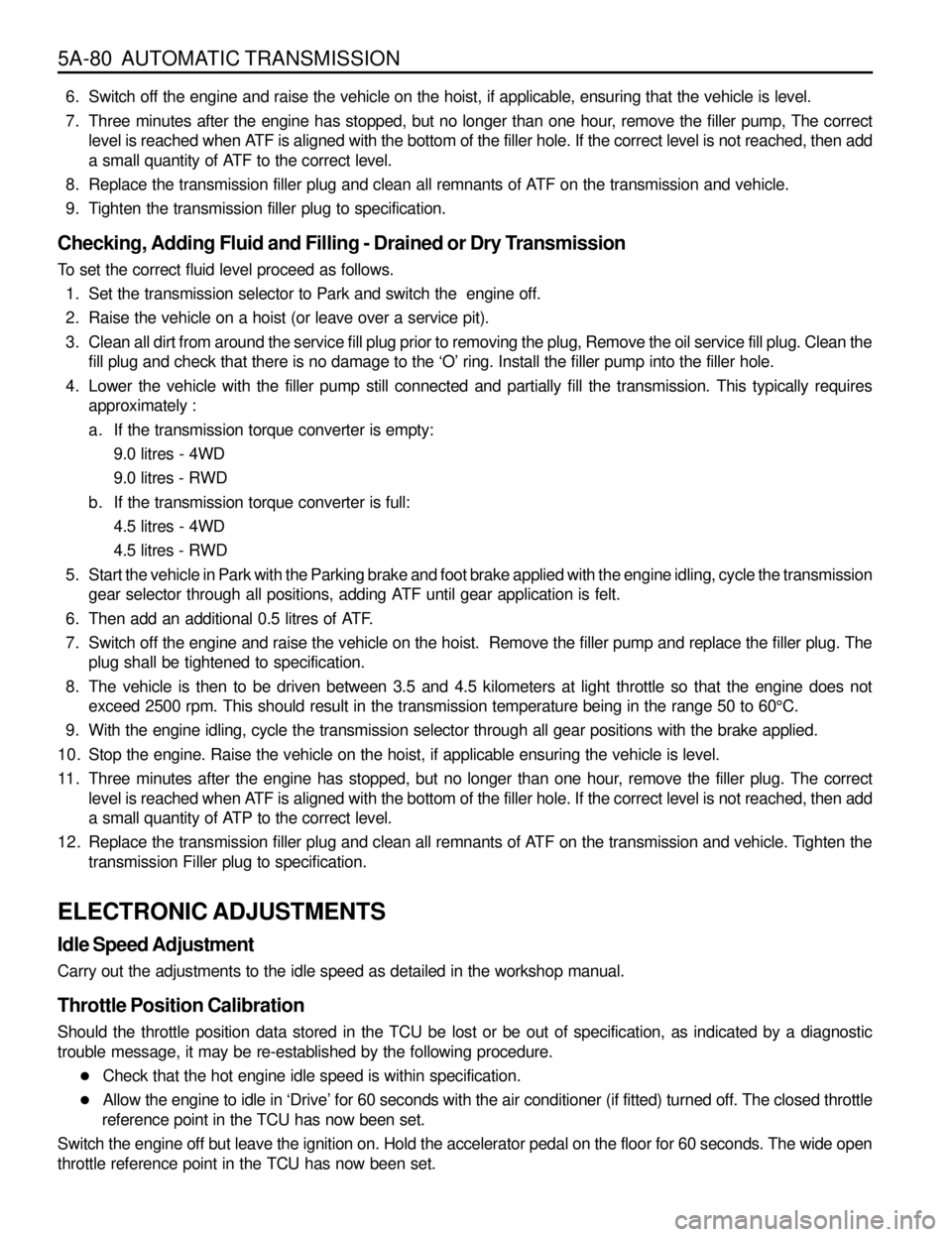
5A-80 AUTOMATIC TRANSMISSION
6. Switch off the engine and raise the vehicle on the hoist, if applicable, ensuring that the vehicle is level.
7. Three minutes after the engine has stopped, but no longer than one hour, remove the filler pump, The correct
level is reached when ATF is aligned with the bottom of the filler hole. If the correct level is not reached, then add
a small quantity of ATF to the correct level.
8. Replace the transmission filler plug and clean all remnants of ATF on the transmission and vehicle.
9. Tighten the transmission filler plug to specification.
Checking, Adding Fluid and Filling - Drained or Dry Transmission
To set the correct fluid level proceed as follows.
1. Set the transmission selector to Park and switch the engine off.
2. Raise the vehicle on a hoist (or leave over a service pit).
3. Clean all dirt from around the service fill plug prior to removing the plug, Remove the oil service fill plug. Clean the
fill plug and check that there is no damage to the ‘O’ ring. Install the filler pump into the filler hole.
4. Lower the vehicle with the filler pump still connected and partially fill the transmission. This typically requires
approximately :
a. If the transmission torque converter is empty:
9.0 litres - 4WD
9.0 litres - RWD
b. If the transmission torque converter is full:
4.5 litres - 4WD
4.5 litres - RWD
5. Start the vehicle in Park with the Parking brake and foot brake applied with the engine idling, cycle the transmission
gear selector through all positions, adding ATF until gear application is felt.
6. Then add an additional 0.5 litres of ATF.
7. Switch off the engine and raise the vehicle on the hoist. Remove the filler pump and replace the filler plug. The
plug shall be tightened to specification.
8. The vehicle is then to be driven between 3.5 and 4.5 kilometers at light throttle so that the engine does not
exceed 2500 rpm. This should result in the transmission temperature being in the range 50 to 60°C.
9. With the engine idling, cycle the transmission selector through all gear positions with the brake applied.
10. Stop the engine. Raise the vehicle on the hoist, if applicable ensuring the vehicle is level.
11. Three minutes after the engine has stopped, but no longer than one hour, remove the filler plug. The correct
level is reached when ATF is aligned with the bottom of the filler hole. If the correct level is not reached, then add
a small quantity of ATP to the correct level.
12. Replace the transmission filler plug and clean all remnants of ATF on the transmission and vehicle. Tighten the
transmission Filler plug to specification.
ELECTRONIC ADJUSTMENTS
Idle Speed Adjustment
Carry out the adjustments to the idle speed as detailed in the workshop manual.
Throttle Position Calibration
Should the throttle position data stored in the TCU be lost or be out of specification, as indicated by a diagnostic
trouble message, it may be re-established by the following procedure.
lCheck that the hot engine idle speed is within specification.
lAllow the engine to idle in ‘Drive’ for 60 seconds with the air conditioner (if fitted) turned off. The closed throttle
reference point in the TCU has now been set.
Switch the engine off but leave the ignition on. Hold the accelerator pedal on the floor for 60 seconds. The wide open
throttle reference point in the TCU has now been set.
Page 1112 of 1463
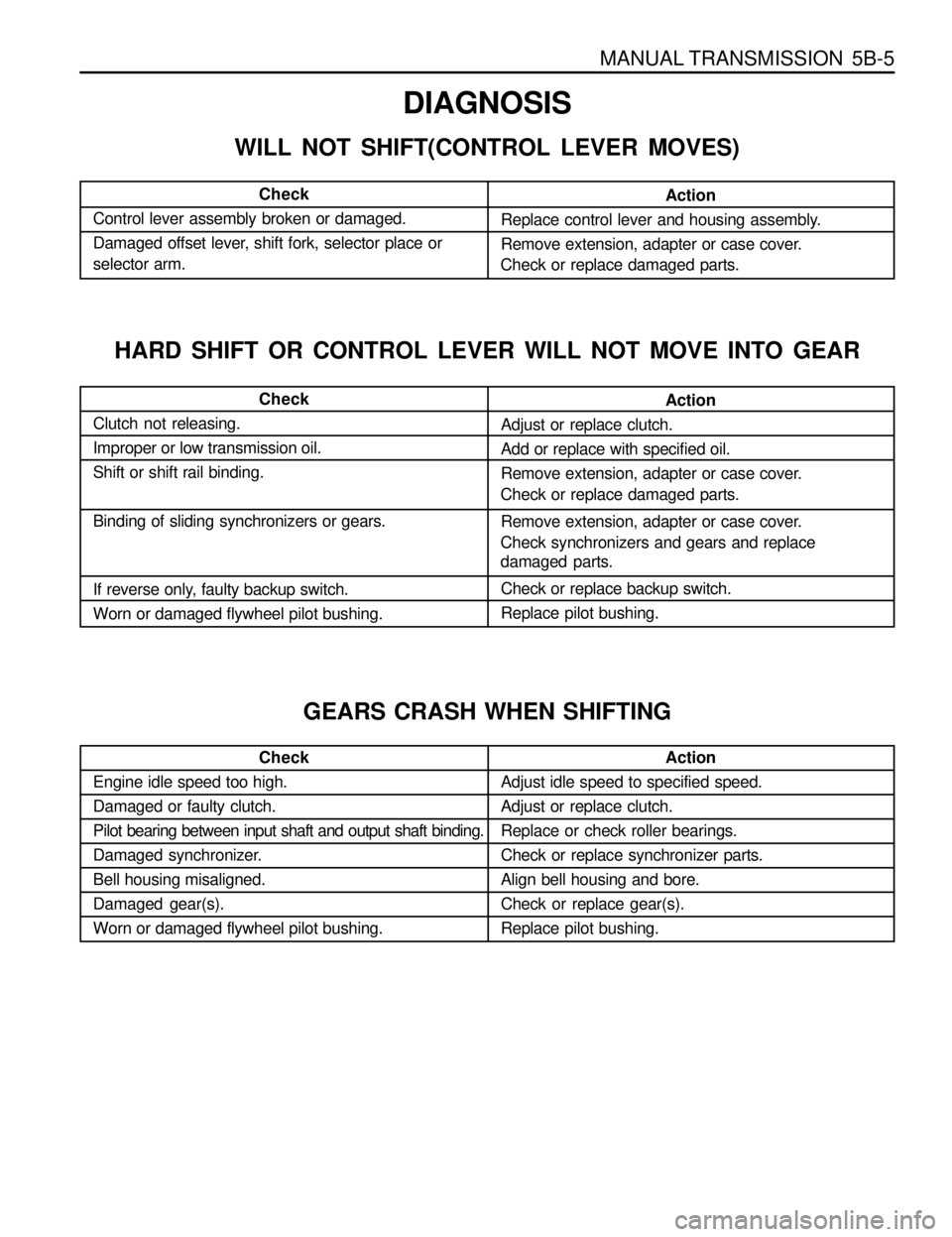
MANUAL TRANSMISSION 5B-5
Check
Clutch not releasing.
Improper or low transmission oil.
Shift or shift rail binding.
Binding of sliding synchronizers or gears.
If reverse only, faulty backup switch.
Worn or damaged flywheel pilot bushing.Check
Control lever assembly broken or damaged.
Damaged offset lever, shift fork, selector place or
selector arm.
DIAGNOSIS
WILL NOT SHIFT(CONTROL LEVER MOVES)
Action
Replace control lever and housing assembly.
Remove extension, adapter or case cover.
Check or replace damaged parts.
HARD SHIFT OR CONTROL LEVER WILL NOT MOVE INTO GEAR
Action
Adjust or replace clutch.
Add or replace with specified oil.
Remove extension, adapter or case cover.
Check or replace damaged parts.
Remove extension, adapter or case cover.
Check synchronizers and gears and replace
damaged parts.
Check or replace backup switch.
Replace pilot bushing.
GEARS CRASH WHEN SHIFTING
Check
Engine idle speed too high.
Damaged or faulty clutch.
Pilot bearing between input shaft and output shaft binding.
Damaged synchronizer.
Bell housing misaligned.
Damaged gear(s).
Worn or damaged flywheel pilot bushing.Action
Adjust idle speed to specified speed.
Adjust or replace clutch.
Replace or check roller bearings.
Check or replace synchronizer parts.
Align bell housing and bore.
Check or replace gear(s).
Replace pilot bushing.
Page 1113 of 1463
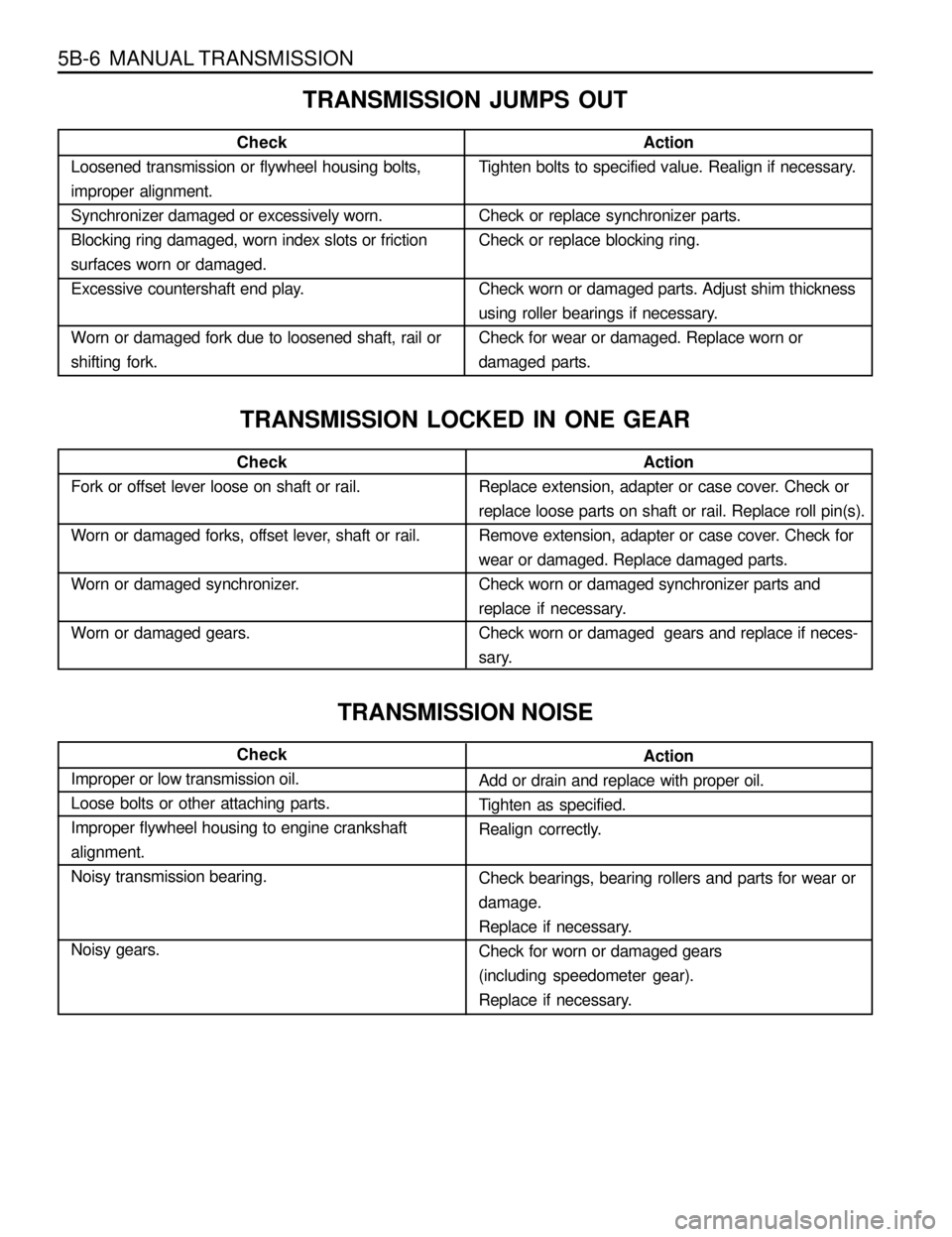
5B-6 MANUAL TRANSMISSION
Check
Loosened transmission or flywheel housing bolts,
improper alignment.
Synchronizer damaged or excessively worn.
Blocking ring damaged, worn index slots or friction
surfaces worn or damaged.
Excessive countershaft end play.
Worn or damaged fork due to loosened shaft, rail or
shifting fork.
TRANSMISSION JUMPS OUT
Action
Tighten bolts to specified value. Realign if necessary.
Check or replace synchronizer parts.
Check or replace blocking ring.
Check worn or damaged parts. Adjust shim thickness
using roller bearings if necessary.
Check for wear or damaged. Replace worn or
damaged parts.
Check
Fork or offset lever loose on shaft or rail.
Worn or damaged forks, offset lever, shaft or rail.
Worn or damaged synchronizer.
Worn or damaged gears.
TRANSMISSION LOCKED IN ONE GEAR
Action
Replace extension, adapter or case cover. Check or
replace loose parts on shaft or rail. Replace roll pin(s).
Remove extension, adapter or case cover. Check for
wear or damaged. Replace damaged parts.
Check worn or damaged synchronizer parts and
replace if necessary.
Check worn or damaged gears and replace if neces-
sary.
Check
Improper or low transmission oil.
Loose bolts or other attaching parts.
Improper flywheel housing to engine crankshaft
alignment.
Noisy transmission bearing.
Noisy gears.
TRANSMISSION NOISE
Action
Add or drain and replace with proper oil.
Tighten as specified.
Realign correctly.
Check bearings, bearing rollers and parts for wear or
damage.
Replace if necessary.
Check for worn or damaged gears
(including speedometer gear).
Replace if necessary.
Page 1153 of 1463

5B-46 MANUAL TRANSMISSION
lCheck the housing face alignment.
- Place the dial indicator on the housing face.
- By rotating the crankshaft one revolution, record the
dial indicator reading.
Notice
If the reading is greater than 0.010 inch, insert the shim
between the engine and clutch housing and adjust the
alignment.
5. Check the following parts :
lPressure plate spring assembly
lDisc
lFlywheel
lInput shaft pilot bearing
Notice
Replace the excessively worn parts.
6. Lubricate the clutch release bearing bore, fork pivot head
during assembly.
Page 1157 of 1463
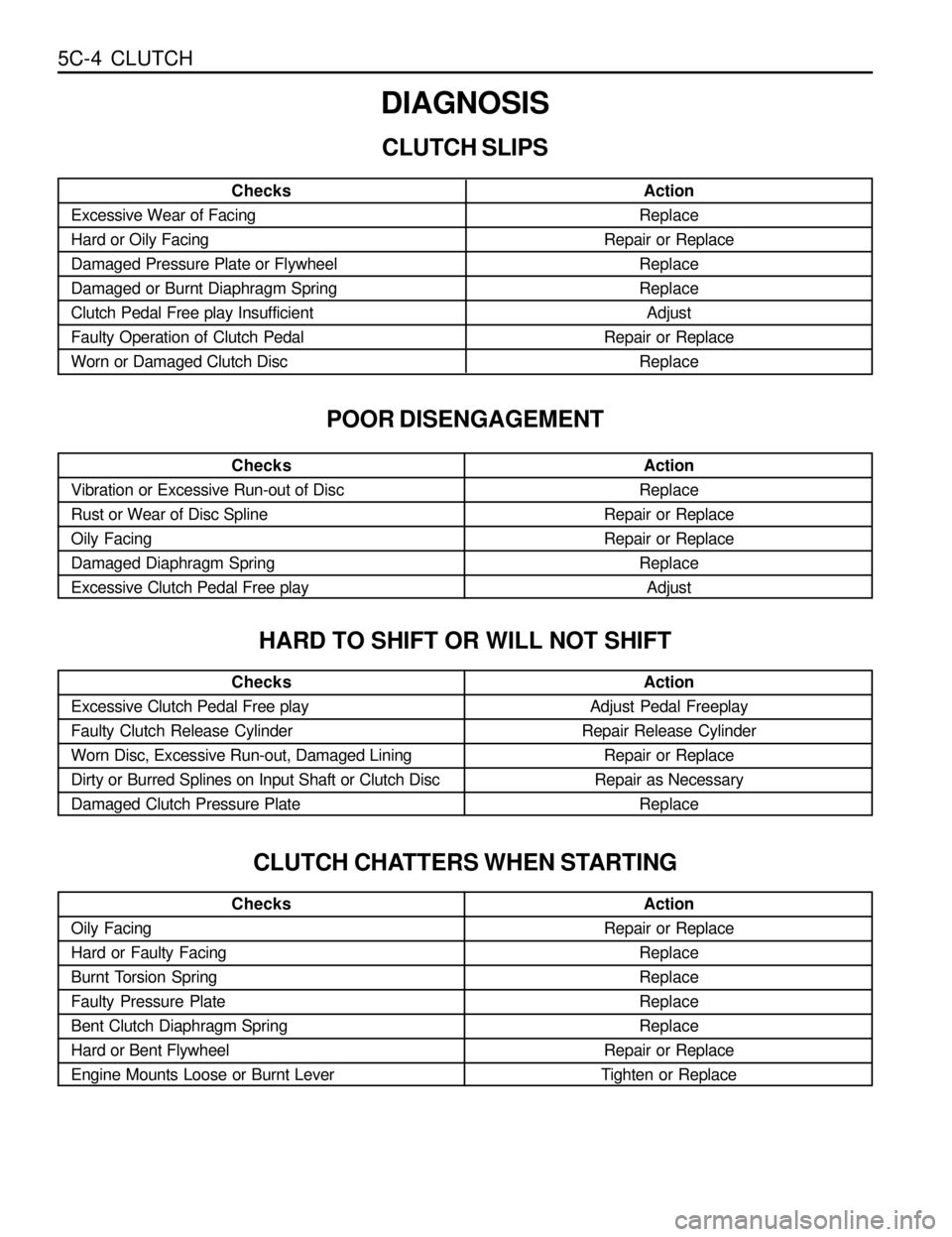
5C-4 CLUTCH
Checks
Oily Facing
Hard or Faulty Facing
Burnt Torsion Spring
Faulty Pressure Plate
Bent Clutch Diaphragm Spring
Hard or Bent Flywheel
Engine Mounts Loose or Burnt LeverAction
Adjust Pedal Freeplay
Repair Release Cylinder
Repair or Replace
Repair as Necessary
Replace Checks
Excessive Clutch Pedal Free play
Faulty Clutch Release Cylinder
Worn Disc, Excessive Run-out, Damaged Lining
Dirty or Burred Splines on Input Shaft or Clutch Disc
Damaged Clutch Pressure PlateChecks
Vibration or Excessive Run-out of Disc
Rust or Wear of Disc Spline
Oily Facing
Damaged Diaphragm Spring
Excessive Clutch Pedal Free play
DIAGNOSIS
CLUTCH SLIPS
Checks
Excessive Wear of Facing
Hard or Oily Facing
Damaged Pressure Plate or Flywheel
Damaged or Burnt Diaphragm Spring
Clutch Pedal Free play Insufficient
Faulty Operation of Clutch Pedal
Worn or Damaged Clutch DiscAction
Replace
Repair or Replace
Replace
Replace
Adjust
Repair or Replace
Replace
POOR DISENGAGEMENT
Action
Replace
Repair or Replace
Repair or Replace
Replace
Adjust
HARD TO SHIFT OR WILL NOT SHIFT
CLUTCH CHATTERS WHEN STARTING
Action
Repair or Replace
Replace
Replace
Replace
Replace
Repair or Replace
Tighten or Replace
Page 1174 of 1463
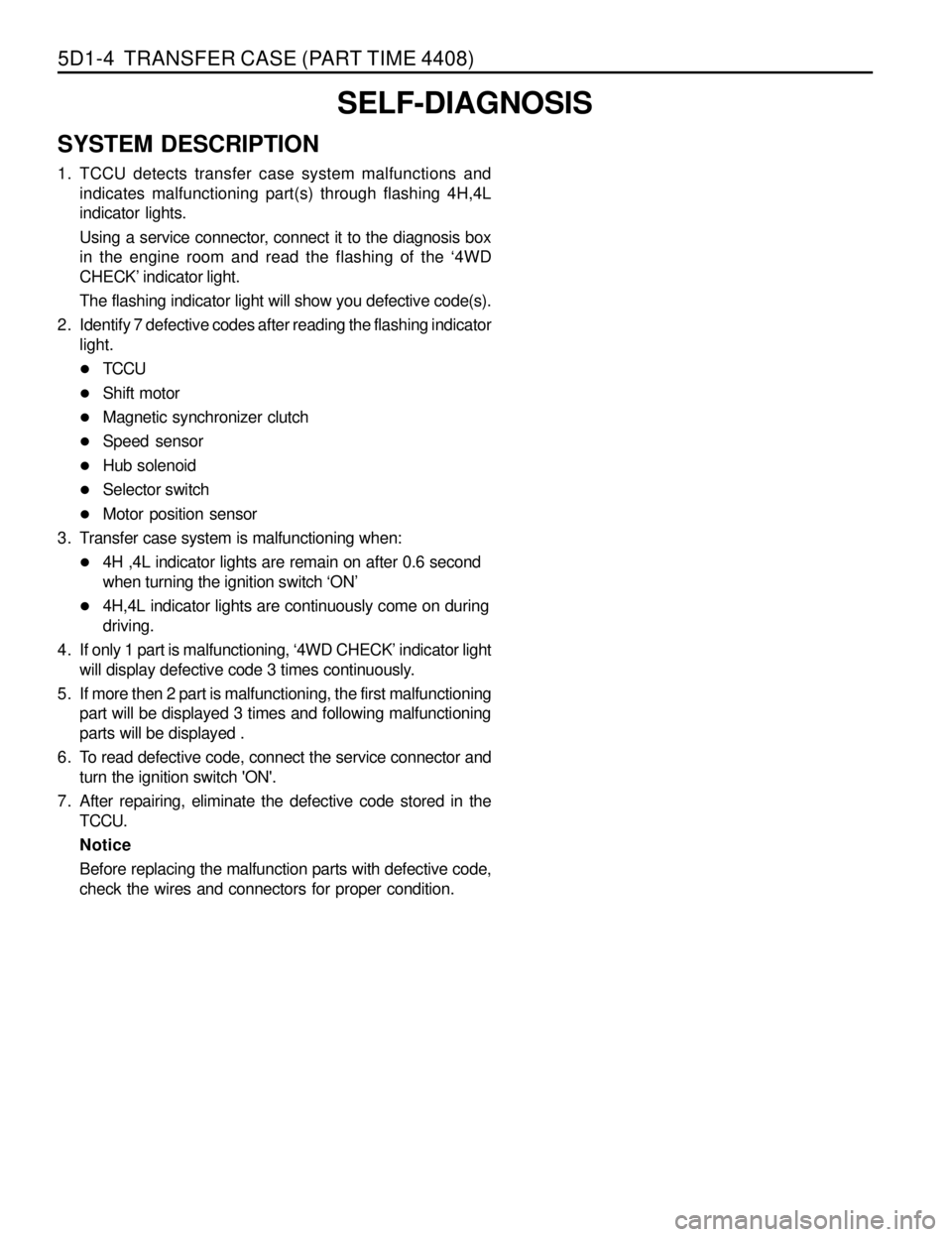
5D1-4 TRANSFER CASE (PART TIME 4408)
SELF-DIAGNOSIS
SYSTEM DESCRIPTION
1. TCCU detects transfer case system malfunctions and
indicates malfunctioning part(s) through flashing 4H,4L
indicator lights.
Using a service connector, connect it to the diagnosis box
in the engine room and read the flashing of the ‘4WD
CHECK’ indicator light.
The flashing indicator light will show you defective code(s).
2. Identify 7 defective codes after reading the flashing indicator
light.
lTCCU
lShift motor
lMagnetic synchronizer clutch
lSpeed sensor
lHub solenoid
lSelector switch
lMotor position sensor
3. Transfer case system is malfunctioning when:
l4H ,4L indicator lights are remain on after 0.6 second
when turning the ignition switch ‘ON’
l4H,4L indicator lights are continuously come on during
driving.
4. If only 1 part is malfunctioning, ‘4WD CHECK’ indicator light
will display defective code 3 times continuously.
5. If more then 2 part is malfunctioning, the first malfunctioning
part will be displayed 3 times and following malfunctioning
parts will be displayed .
6. To read defective code, connect the service connector and
turn the ignition switch 'ON'.
7. After repairing, eliminate the defective code stored in the
TCCU.
Notice
Before replacing the malfunction parts with defective code,
check the wires and connectors for proper condition.
Page 1175 of 1463
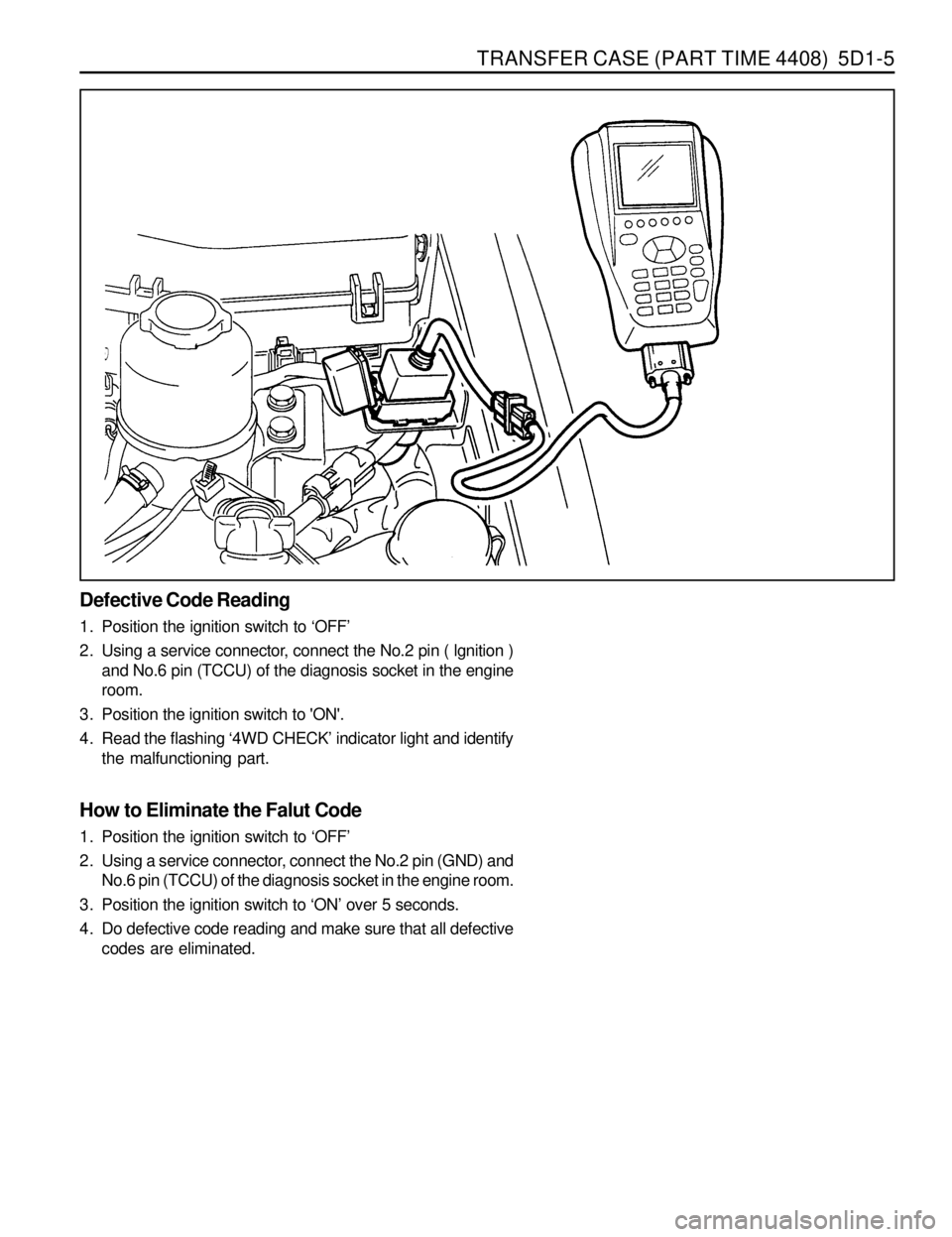
TRANSFER CASE (PART TIME 4408) 5D1-5
Defective Code Reading
1. Position the ignition switch to ‘OFF’
2. Using a service connector, connect the No.2 pin ( lgnition )
and No.6 pin (TCCU) of the diagnosis socket in the engine
room.
3. Position the ignition switch to 'ON'.
4. Read the flashing ‘4WD CHECK’ indicator light and identify
the malfunctioning part.
How to Eliminate the Falut Code
1. Position the ignition switch to ‘OFF’
2. Using a service connector, connect the No.2 pin (GND) and
No.6 pin (TCCU) of the diagnosis socket in the engine room.
3. Position the ignition switch to ‘ON’ over 5 seconds.
4. Do defective code reading and make sure that all defective
codes are eliminated.
Page 1178 of 1463
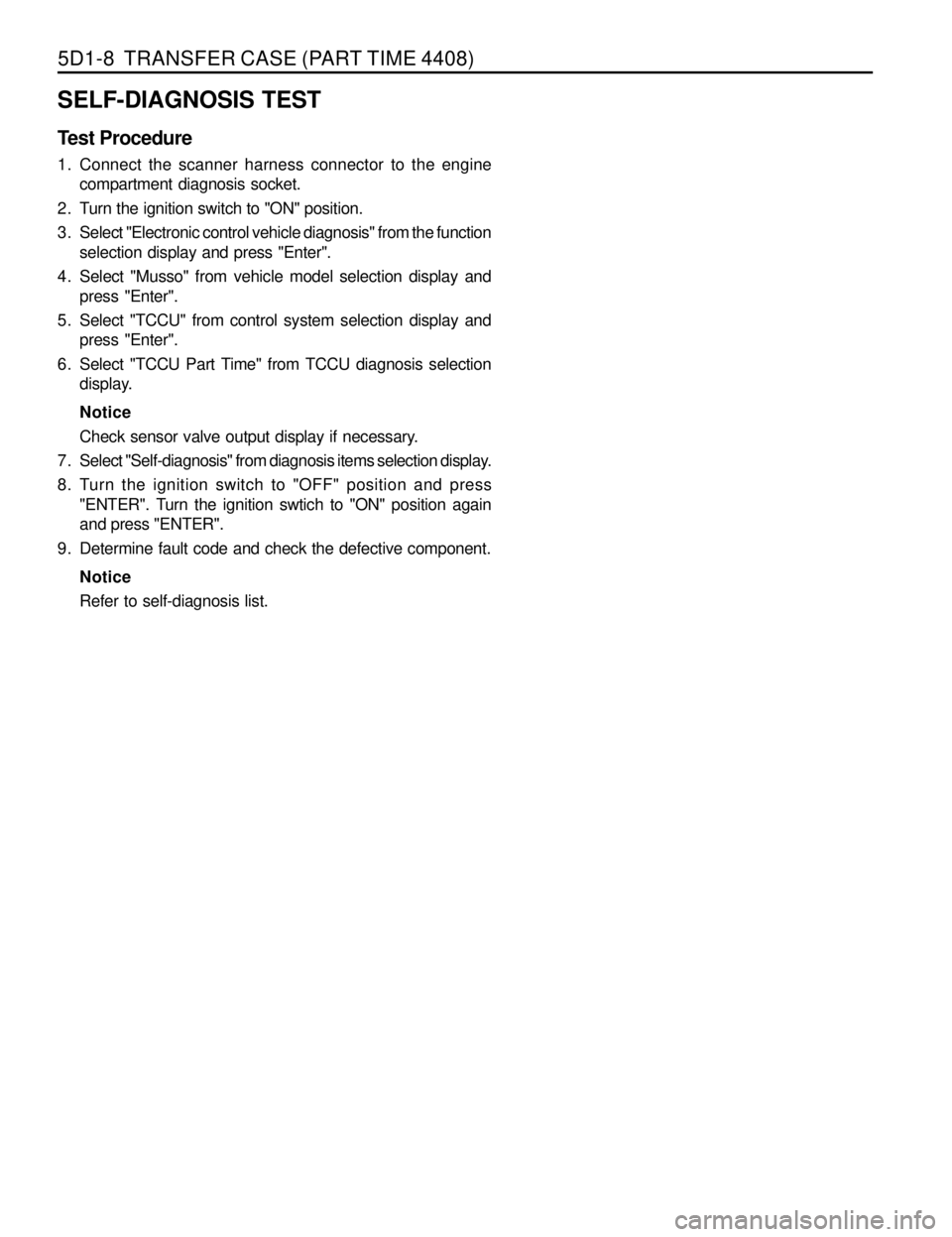
5D1-8 TRANSFER CASE (PART TIME 4408)
SELF-DIAGNOSIS TEST
Test Procedure
1. Connect the scanner harness connector to the engine
compartment diagnosis socket.
2. Turn the ignition switch to "ON" position.
3. Select "Electronic control vehicle diagnosis" from the function
selection display and press "Enter".
4. Select "Musso" from vehicle model selection display and
press "Enter".
5. Select "TCCU" from control system selection display and
press "Enter".
6. Select "TCCU Part Time" from TCCU diagnosis selection
display.
Notice
Check sensor valve output display if necessary.
7 . Select "Self-diagnosis" from diagnosis items selection display.
8. Turn the ignition switch to "OFF" position and press
"ENTER". Turn the ignition swtich to "ON" position again
and press "ENTER".
9. Determine fault code and check the defective component.
Notice
Refer to self-diagnosis list.