check engine SSANGYONG MUSSO 1998 Workshop Repair Manual
[x] Cancel search | Manufacturer: SSANGYONG, Model Year: 1998, Model line: MUSSO, Model: SSANGYONG MUSSO 1998Pages: 1463, PDF Size: 19.88 MB
Page 1226 of 1463
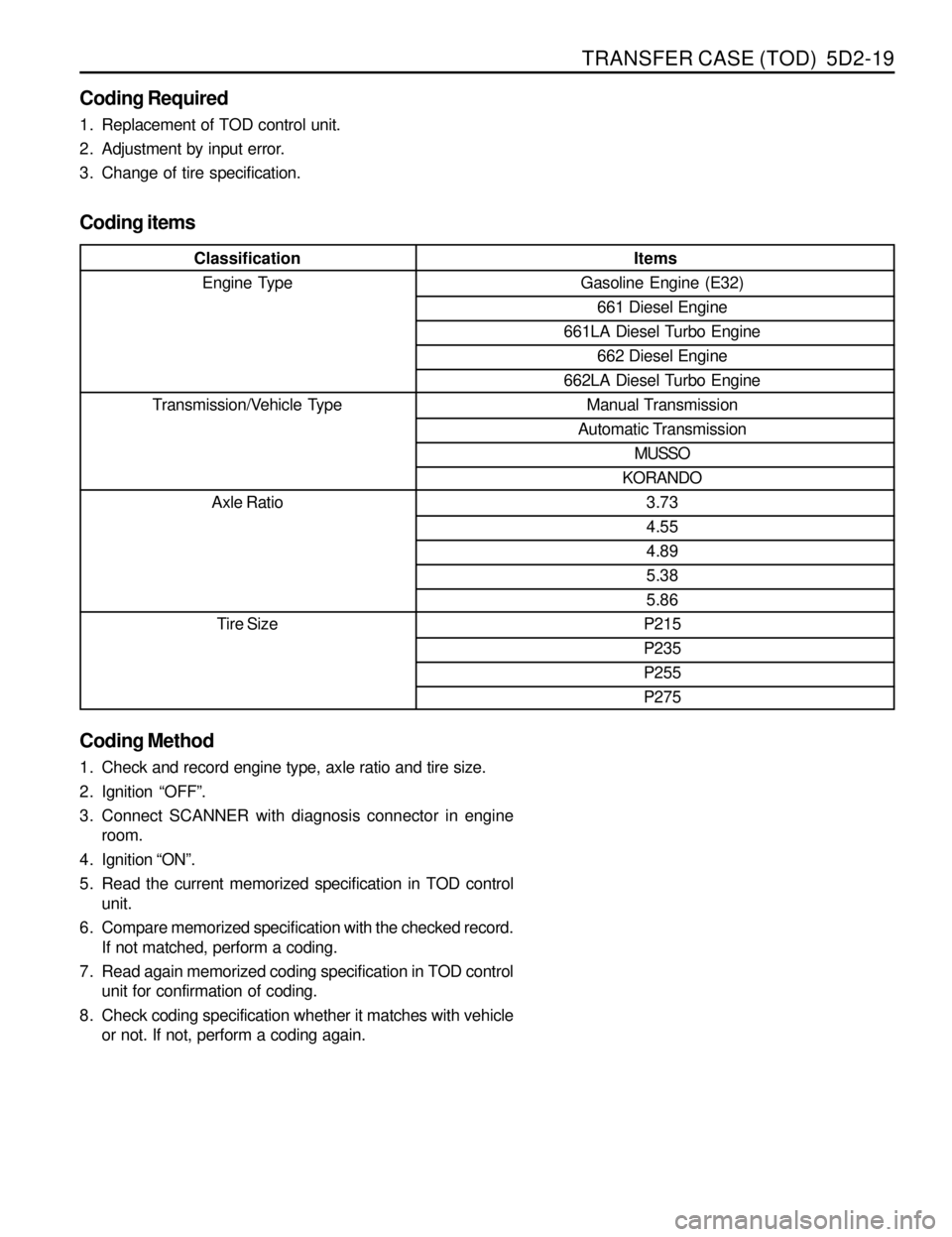
TRANSFER CASE (TOD) 5D2-19
Classification
Engine Type
Transmission/Vehicle Type
Axle Ratio
Tire Size
Coding Required
1. Replacement of TOD control unit.
2. Adjustment by input error.
3. Change of tire specification.
Items
Gasoline Engine (E32)
661 Diesel Engine
661LA Diesel Turbo Engine
662 Diesel Engine
662LA Diesel Turbo Engine
Manual Transmission
Automatic Transmission
MUSSO
KORANDO
3.73
4.55
4.89
5.38
5.86
P215
P235
P255
P275
Coding Method
1. Check and record engine type, axle ratio and tire size.
2. Ignition “OFF”.
3. Connect SCANNER with diagnosis connector in engine
room.
4. Ignition “ON”.
5. Read the current memorized specification in TOD control
unit.
6. Compare memorized specification with the checked record.
If not matched, perform a coding.
7. Read again memorized coding specification in TOD control
unit for confirmation of coding.
8. Check coding specification whether it matches with vehicle
or not. If not, perform a coding again.
Coding items
Page 1228 of 1463
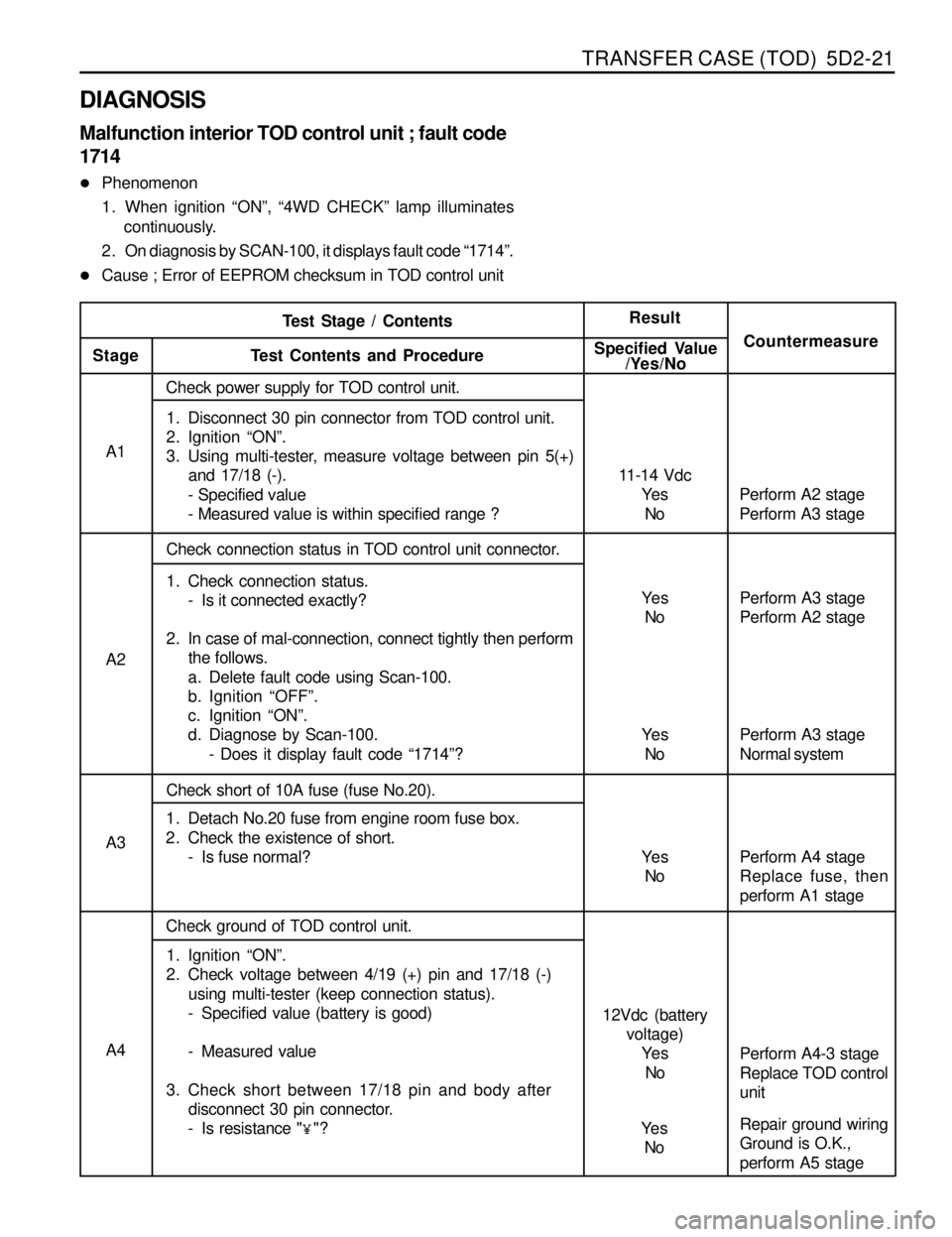
TRANSFER CASE (TOD) 5D2-21
DIAGNOSIS
Malfunction interior TOD control unit ; fault code
1714
lPhenomenon
1. When ignition “ON”, “4WD CHECK” lamp illuminates
continuously.
2. On diagnosis by SCAN-100, it displays fault code “1714”.
lCause ; Error of EEPROM checksum in TOD control unit
Test Stage / Contents
Result
Stage Test Contents and ProcedureSpecified Value
/Yes/NoCountermeasure
Check power supply for TOD control unit.
1. Disconnect 30 pin connector from TOD control unit.
2. Ignition “ON”.
3. Using multi-tester, measure voltage between pin 5(+)
and 17/18 (-).
- Specified value
- Measured value is within specified range ?11-14 Vdc
Ye s
NoPerform A2 stage
Perform A3 stage
Check connection status in TOD control unit connector.
1. Check connection status.
- Is it connected exactly?
2. In case of mal-connection, connect tightly then perform
the follows.
a. Delete fault code using Scan-100.
b. Ignition “OFF”.
c. Ignition “ON”.
d. Diagnose by Scan-100.
- Does it display fault code “1714”?Ye s
No
Ye s
No
Check short of 10A fuse (fuse No.20).
1. Detach No.20 fuse from engine room fuse box.
2. Check the existence of short.
- Is fuse normal? Yes
No
Check ground of TOD control unit.
1. Ignition “ON”.
2. Check voltage between 4/19 (+) pin and 17/18 (-)
using multi-tester (keep connection status).
- Specified value (battery is good)
- Measured value
3. Check short between 17/18 pin and body after
disconnect 30 pin connector.
- Is resistance "¥"?12Vdc (battery
voltage)
Ye s
No
Ye s
No A1
A2
A3
A4
Perform A3 stage
Perform A2 stage
Perform A3 stage
Normal system
Perform A4 stage
Replace fuse, then
perform A1 stage
Perform A4-3 stage
Replace TOD control
unit
Repair ground wiring
Ground is O.K.,
perform A5 stage
Page 1230 of 1463
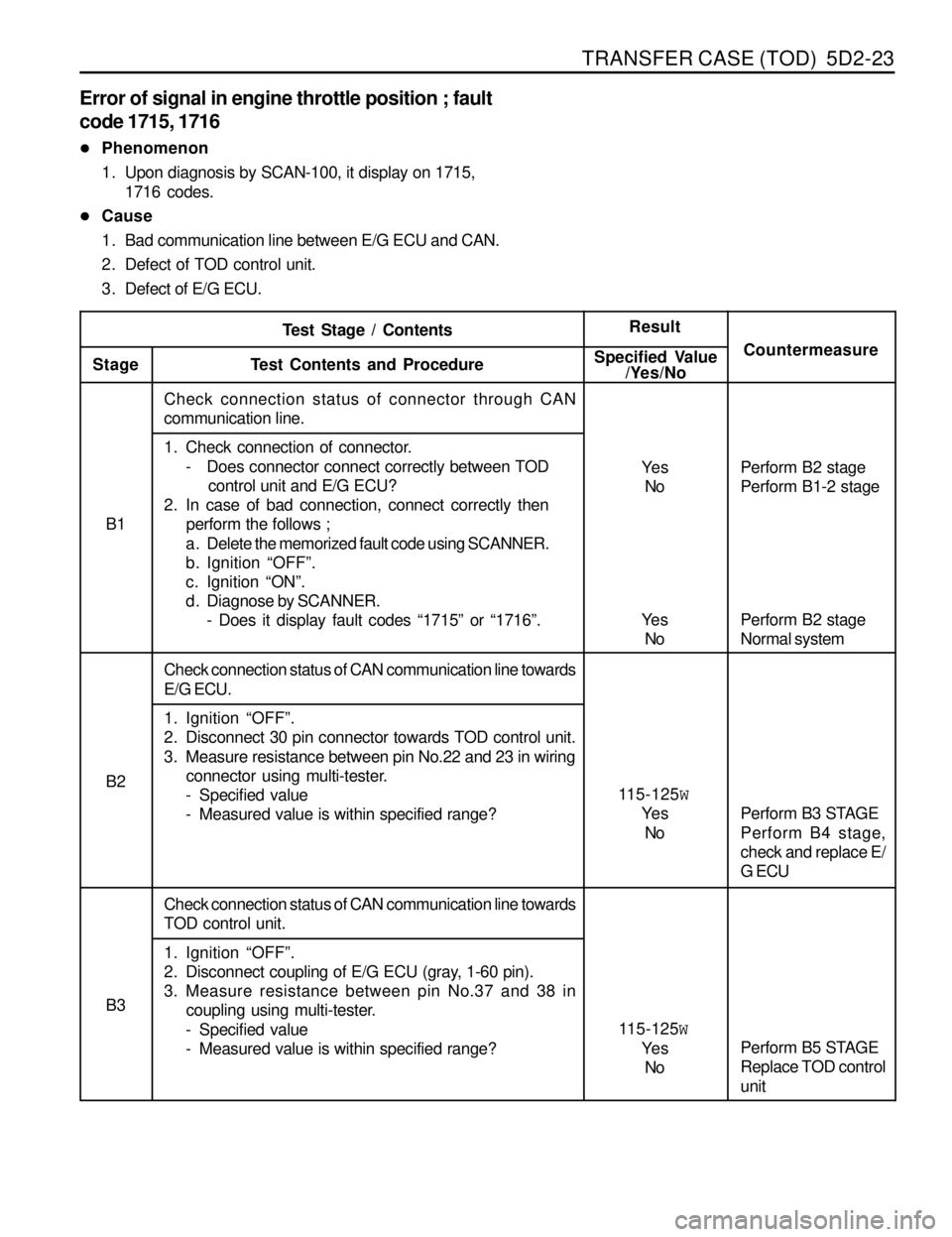
TRANSFER CASE (TOD) 5D2-23
Error of signal in engine throttle position ; fault
code 1715, 1716
lPhenomenon
1. Upon diagnosis by SCAN-100, it display on 1715,
1716 codes.
lCause
1. Bad communication line between E/G ECU and CAN.
2. Defect of TOD control unit.
3. Defect of E/G ECU.
Check connection status of connector through CAN
communication line.
1. Check connection of connector.
- Does connector connect correctly between TOD
control unit and E/G ECU?
2. In case of bad connection, connect correctly then
perform the follows ;
a. Delete the memorized fault code using SCANNER.
b. Ignition “OFF”.
c. Ignition “ON”.
d. Diagnose by SCANNER.
- Does it display fault codes “1715” or “1716”.Ye s
No
B1
Ye s
No
Check connection status of CAN communication line towards
E/G ECU.
1. Ignition “OFF”.
2. Disconnect 30 pin connector towards TOD control unit.
3. Measure resistance between pin No.22 and 23 in wiring
connector using multi-tester.
- Specified value
- Measured value is within specified range? B2
115-125W
Ye s
No
Check connection status of CAN communication line towards
TOD control unit.
1. Ignition “OFF”.
2. Disconnect coupling of E/G ECU (gray, 1-60 pin).
3. Measure resistance between pin No.37 and 38 in
coupling using multi-tester.
- Specified value
- Measured value is within specified range? B3
115-125W
Ye s
No Test Stage / Contents
Result
Stage Test Contents and ProcedureSpecified Value
/Yes/NoCountermeasure
Perform B2 stage
Perform B1-2 stage
Perform B2 stage
Normal system
Perform B3 STAGE
Perform B4 stage,
check and replace E/
G ECU
Perform B5 STAGE
Replace TOD control
unit
Page 1265 of 1463
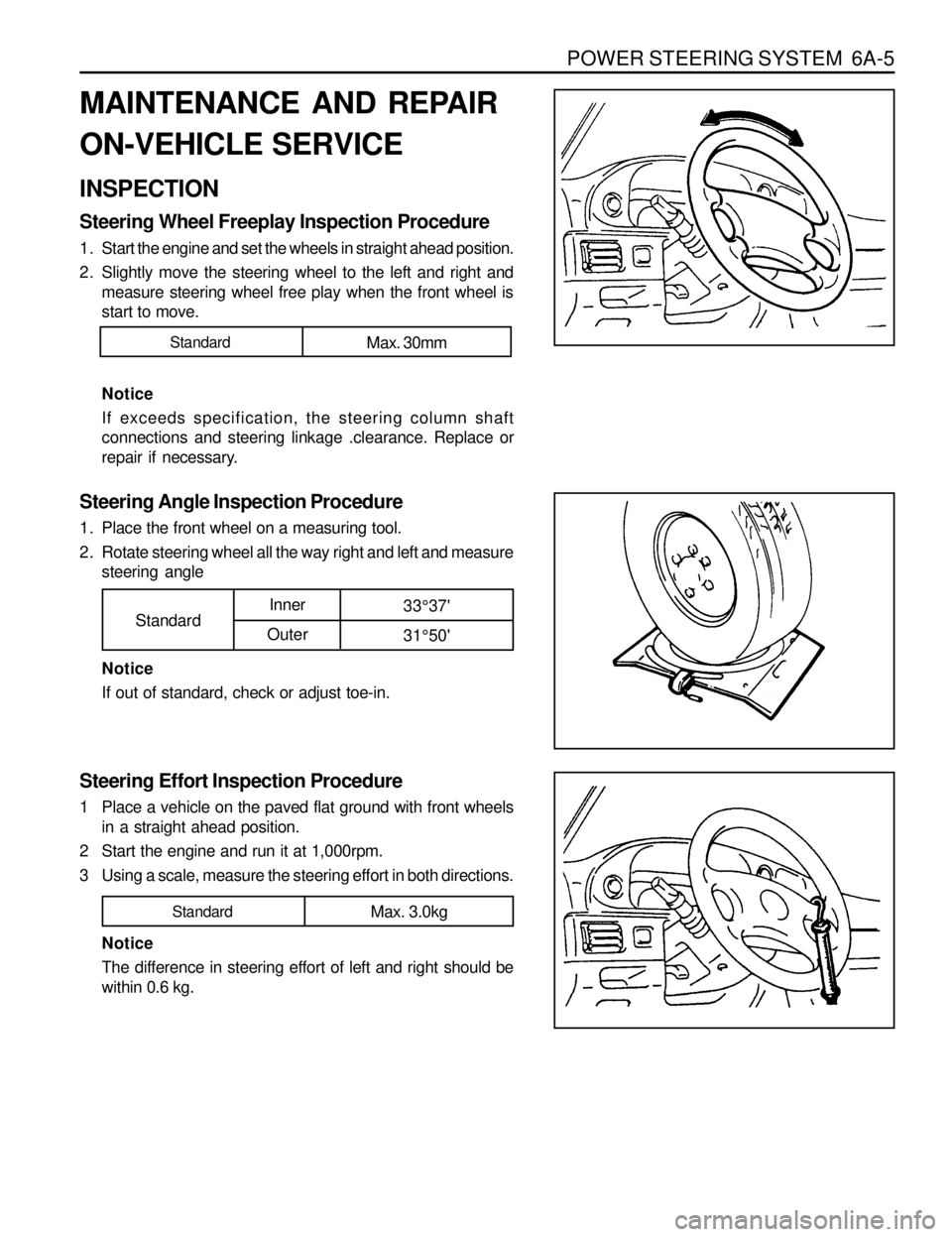
POWER STEERING SYSTEM 6A-5
MAINTENANCE AND REPAIR
ON-VEHICLE SERVICE
INSPECTION
Steering Wheel Freeplay Inspection Procedure
1. Start the engine and set the wheels in straight ahead position.
2. Slightly move the steering wheel to the left and right and
measure steering wheel free play when the front wheel is
start to move.
Notice
If exceeds specification, the steering column shaft
connections and steering linkage .clearance. Replace or
repair if necessary.
Steering Angle Inspection Procedure
1. Place the front wheel on a measuring tool.
2. Rotate steering wheel all the way right and left and measure
steering angle
Notice
If out of standard, check or adjust toe-in.
Standard33°37'
31°50'Inner
Outer
Steering Effort Inspection Procedure
1 Place a vehicle on the paved flat ground with front wheels
in a straight ahead position.
2 Start the engine and run it at 1,000rpm.
3 Using a scale, measure the steering effort in both directions.
Notice
The difference in steering effort of left and right should be
within 0.6 kg.
StandardMax. 3.0kg
StandardMax. 30mm
Page 1266 of 1463
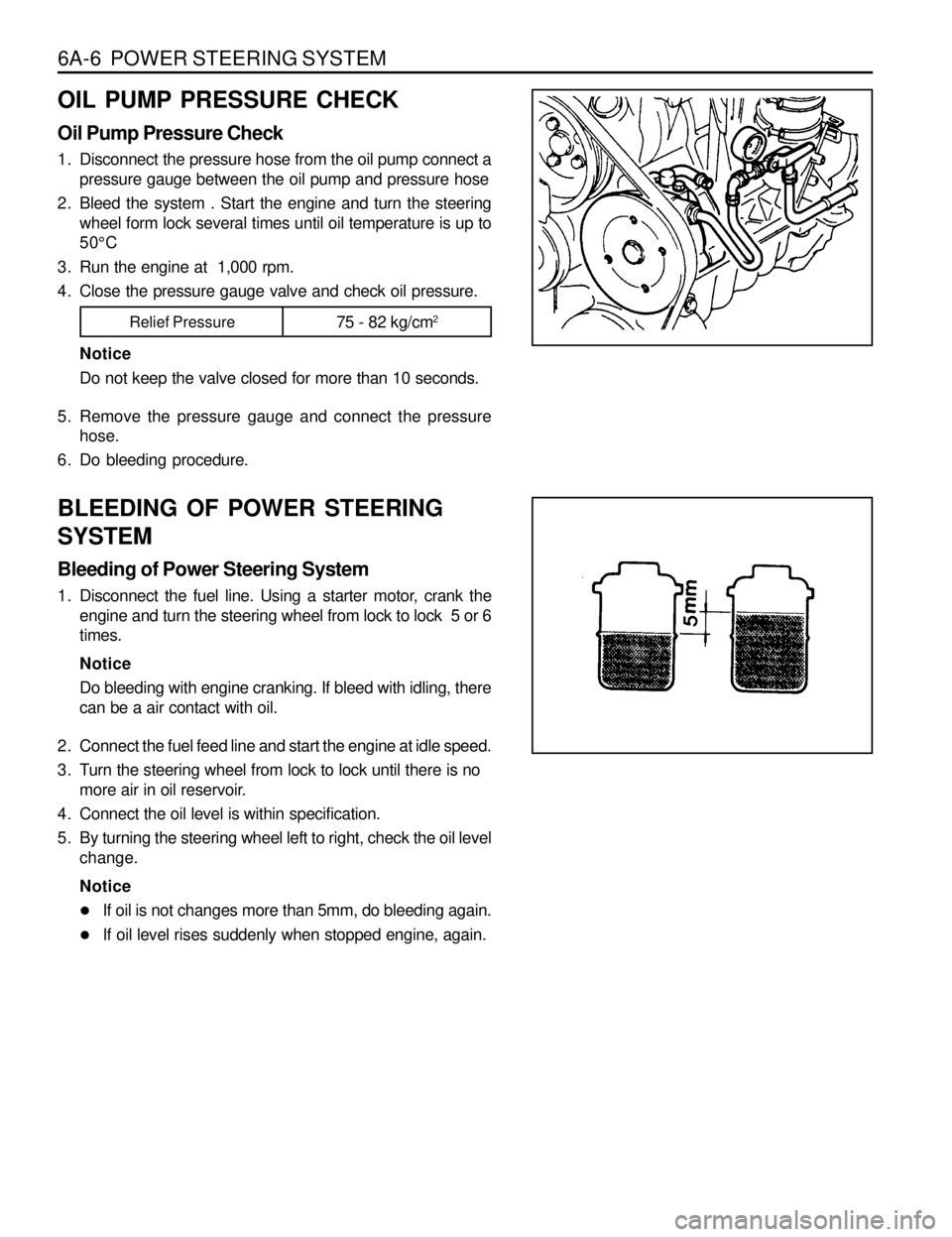
6A-6 POWER STEERING SYSTEM
OIL PUMP PRESSURE CHECK
Oil Pump Pressure Check
1. Disconnect the pressure hose from the oil pump connect a
pressure gauge between the oil pump and pressure hose
2. Bleed the system . Start the engine and turn the steering
wheel form lock several times until oil temperature is up to
50°C
3. Run the engine at 1,000 rpm.
4. Close the pressure gauge valve and check oil pressure.
Notice
Do not keep the valve closed for more than 10 seconds.
5. Remove the pressure gauge and connect the pressure
hose.
6. Do bleeding procedure.
BLEEDING OF POWER STEERING
SYSTEM
Bleeding of Power Steering System
1. Disconnect the fuel line. Using a starter motor, crank the
engine and turn the steering wheel from lock to lock 5 or 6
times.
Notice
Do bleeding with engine cranking. If bleed with idling, there
can be a air contact with oil.
2. Connect the fuel feed line and start the engine at idle speed.
3. Turn the steering wheel from lock to lock until there is no
more air in oil reservoir.
4. Connect the oil level is within specification.
5. By turning the steering wheel left to right, check the oil level
change.
Notice
lIf oil is not changes more than 5mm, do bleeding again.
lIf oil level rises suddenly when stopped engine, again.
Relief Pressure75 - 82 kg/cm2
Page 1286 of 1463
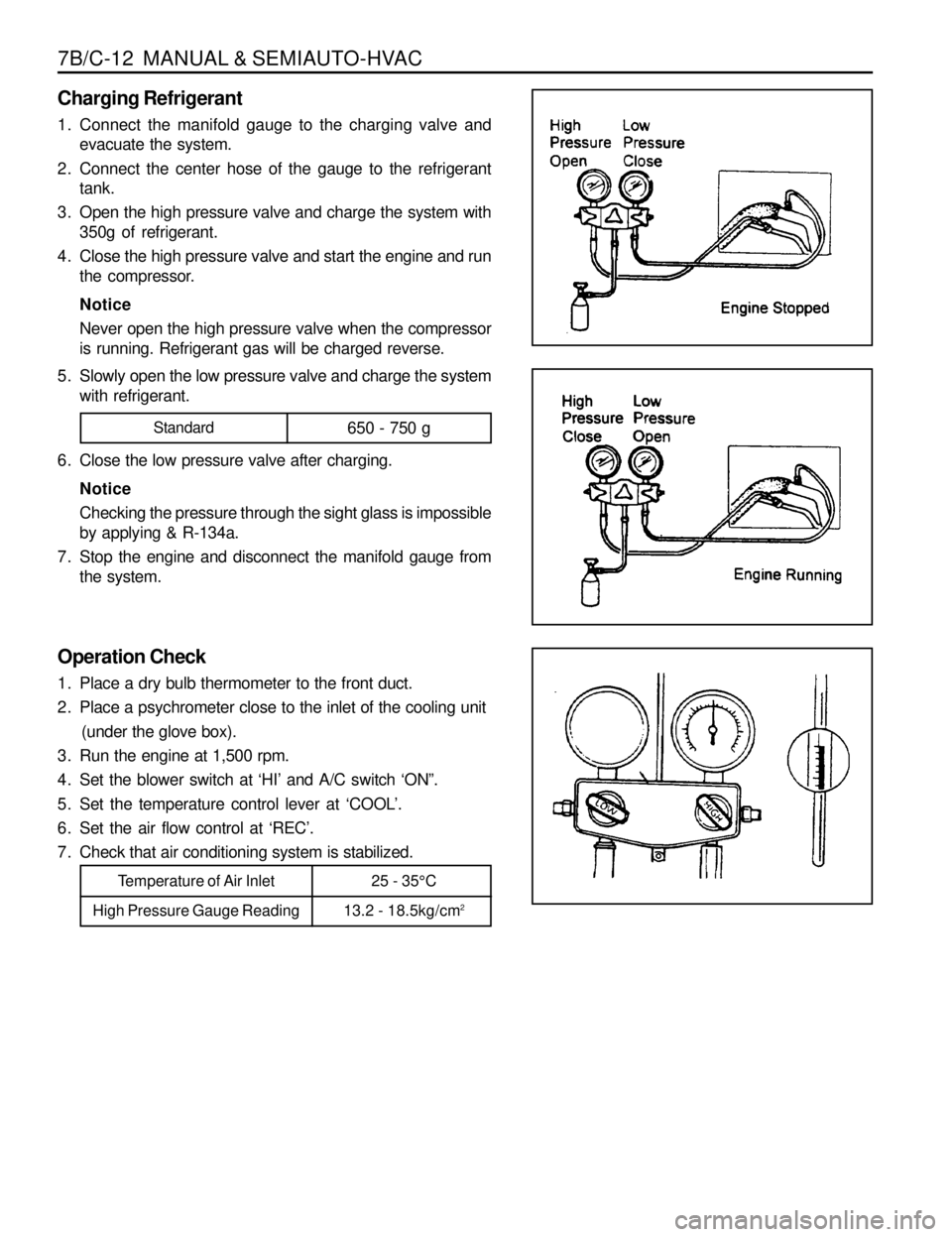
7B/C-12 MANUAL & SEMIAUTO-HVAC
Charging Refrigerant
1. Connect the manifold gauge to the charging valve and
evacuate the system.
2. Connect the center hose of the gauge to the refrigerant
tank.
3. Open the high pressure valve and charge the system with
350g of refrigerant.
4. Close the high pressure valve and start the engine and run
the compressor.
Notice
Never open the high pressure valve when the compressor
is running. Refrigerant gas will be charged reverse.
5. Slowly open the low pressure valve and charge the system
with refrigerant.
Standard650 - 750 g
6. Close the low pressure valve after charging.
Notice
Checking the pressure through the sight glass is impossible
by applying & R-134a.
7. Stop the engine and disconnect the manifold gauge from
the system.
Operation Check
1. Place a dry bulb thermometer to the front duct.
2. Place a psychrometer close to the inlet of the cooling unit
(under the glove box).
3. Run the engine at 1,500 rpm.
4. Set the blower switch at ‘HI’ and A/C switch ‘ON”.
5. Set the temperature control lever at ‘COOL’.
6. Set the air flow control at ‘REC’.
7. Check that air conditioning system is stabilized.
Temperature of Air Inlet
High Pressure Gauge Reading 25 - 35°C
13.2 - 18.5kg/cm
2
Page 1307 of 1463
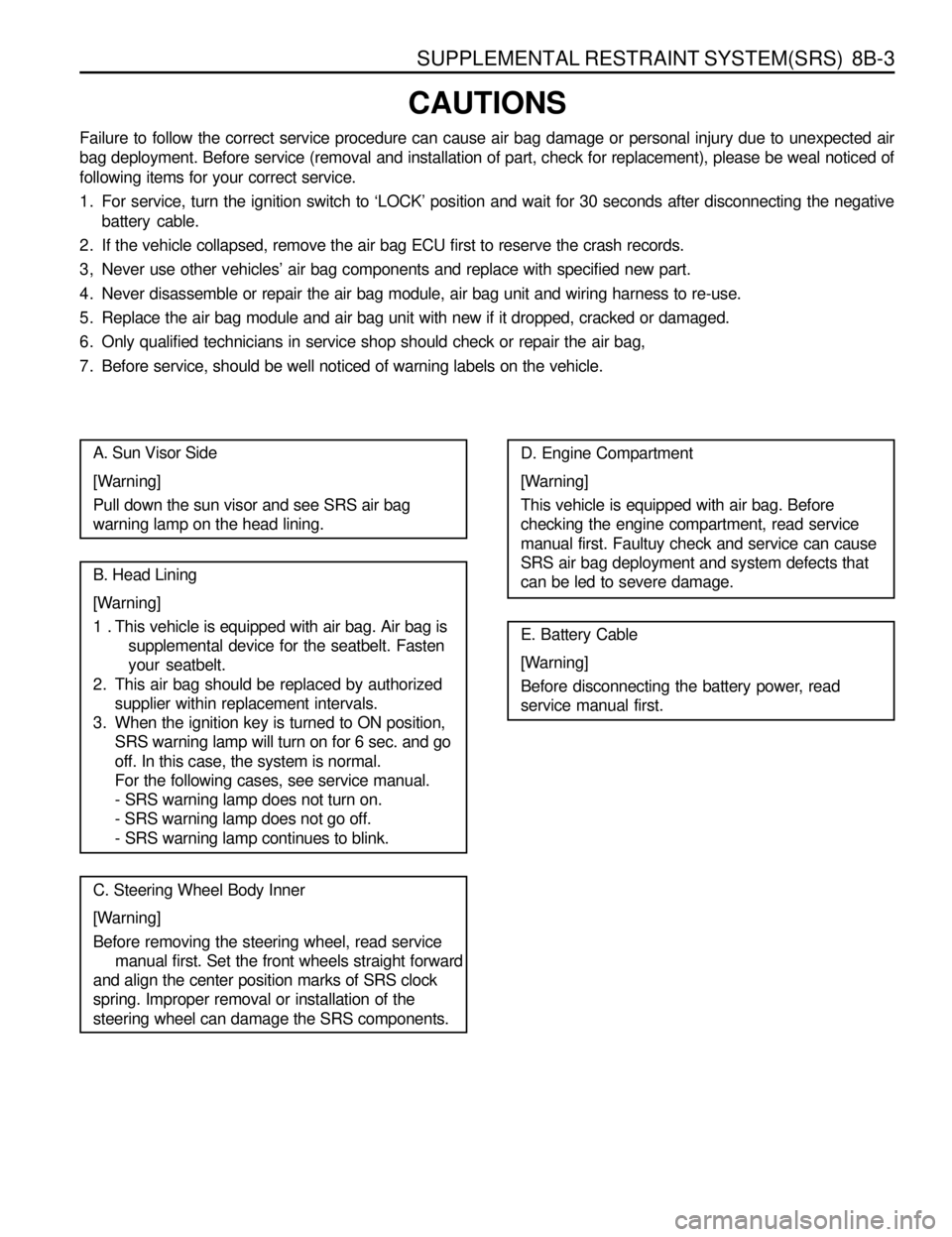
SUPPLEMENTAL RESTRAINT SYSTEM(SRS) 8B-3
CAUTIONS
Failure to follow the correct service procedure can cause air bag damage or personal injury due to unexpected air
bag deployment. Before service (removal and installation of part, check for replacement), please be weal noticed of
following items for your correct service.
1. For service, turn the ignition switch to ‘LOCK’ position and wait for 30 seconds after disconnecting the negative
battery cable.
2. If the vehicle collapsed, remove the air bag ECU first to reserve the crash records.
3, Never use other vehicles’ air bag components and replace with specified new part.
4. Never disassemble or repair the air bag module, air bag unit and wiring harness to re-use.
5. Replace the air bag module and air bag unit with new if it dropped, cracked or damaged.
6. Only qualified technicians in service shop should check or repair the air bag,
7. Before service, should be well noticed of warning labels on the vehicle.
A. Sun Visor Side
[Warning]
Pull down the sun visor and see SRS air bag
warning lamp on the head lining.
B. Head Lining
[Warning]
1 . This vehicle is equipped with air bag. Air bag is
supplemental device for the seatbelt. Fasten
your seatbelt.
2. This air bag should be replaced by authorized
supplier within replacement intervals.
3. When the ignition key is turned to ON position,
SRS warning lamp will turn on for 6 sec. and go
off. In this case, the system is normal.
For the following cases, see service manual.
- SRS warning lamp does not turn on.
- SRS warning lamp does not go off.
- SRS warning lamp continues to blink.
C. Steering Wheel Body Inner
[Warning]
Before removing the steering wheel, read service
manual first. Set the front wheels straight forward
and align the center position marks of SRS clock
spring. Improper removal or installation of the
steering wheel can damage the SRS components.D. Engine Compartment
[Warning]
This vehicle is equipped with air bag. Before
checking the engine compartment, read service
manual first. Faultuy check and service can cause
SRS air bag deployment and system defects that
can be led to severe damage.
E. Battery Cable
[Warning]
Before disconnecting the battery power, read
service manual first.
Page 1314 of 1463

8B-10 SUPPLEMENTAL RESTRAINT SYSTEM(SRS)
1. Position the ignition switch to ‘OFF’.
2. Connect the harness connector of scanner to the diagnosis
socket in engine compartment.
3. Turn the ignition switch to ‘ON’ position.
4. Select “Electronic control vehicle diagnosis” from function
selection display and press ‘Enter’.
5. Select “Musso (’98 model year)” from vehicle model
selection display and press ‘Enter’.
6. Select “Electronic air bag” from control system selection
display and press ‘Enter’.
7. Select “Self-diagnosis” from diagnosis item selection display.
Notice
Check sensor value of output display, if necessary.
8. Determine the fault code and trace defective component.
Notice
Refer to self-diagnosis list.
SELF DIAGNOSIS
Page 1362 of 1463
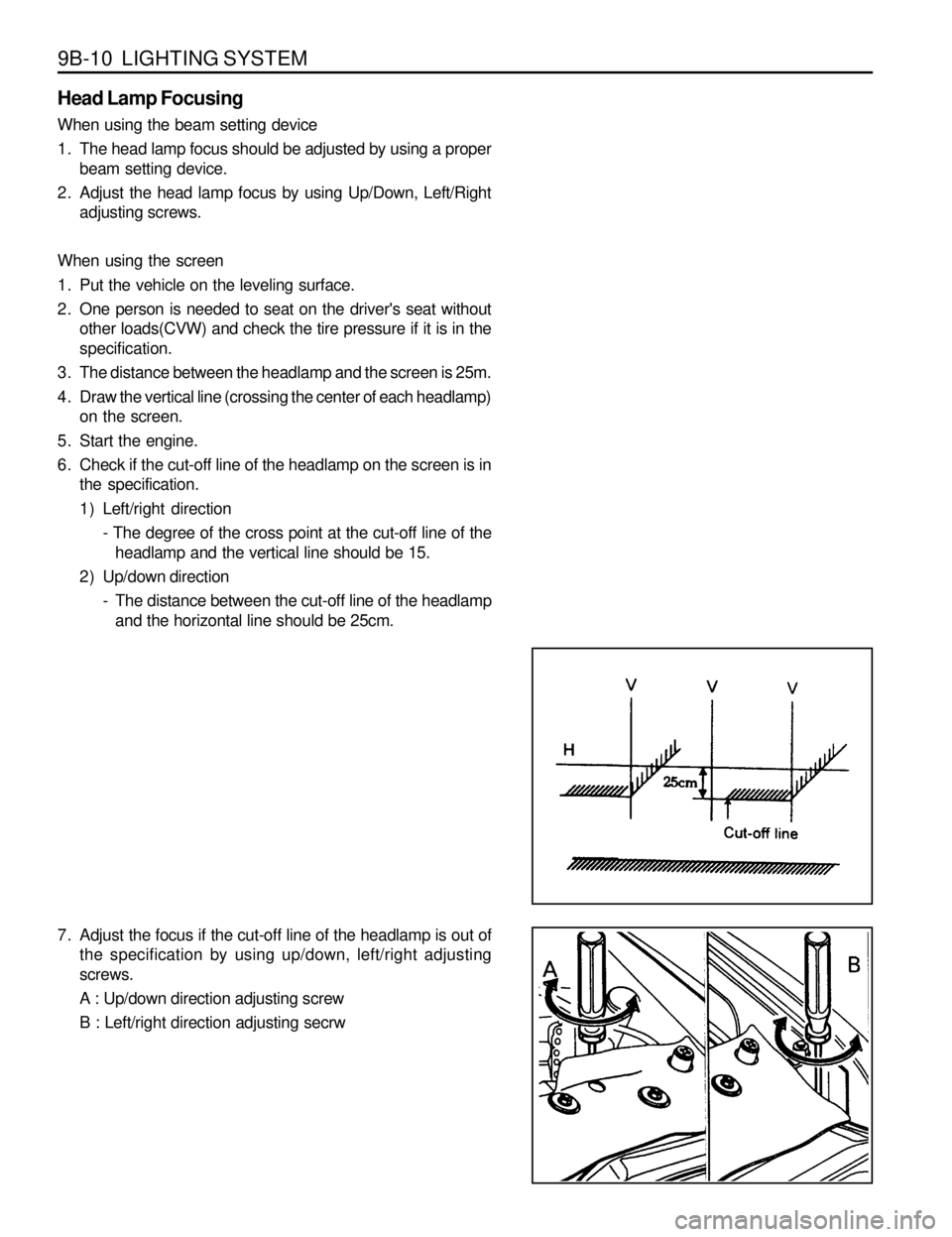
9B-10 LIGHTING SYSTEM
Head Lamp Focusing
When using the beam setting device
1. The head lamp focus should be adjusted by using a proper
beam setting device.
2. Adjust the head lamp focus by using Up/Down, Left/Right
adjusting screws.
When using the screen
1. Put the vehicle on the leveling surface.
2. One person is needed to seat on the driver's seat without
other loads(CVW) and check the tire pressure if it is in the
specification.
3. The distance between the headlamp and the screen is 25m.
4. Draw the vertical line (crossing the center of each headlamp)
on the screen.
5. Start the engine.
6. Check if the cut-off line of the headlamp on the screen is in
the specification.
1) Left/right direction
- The degree of the cross point at the cut-off line of the
headlamp and the vertical line should be 15.
2 ) Up/down direction
- The distance between the cut-off line of the headlamp
and the horizontal line should be 25cm.
7. Adjust the focus if the cut-off line of the headlamp is out of
the specification by using up/down, left/right adjusting
screws.
A : Up/down direction adjusting screw
B : Left/right direction adjusting secrw
Page 1436 of 1463
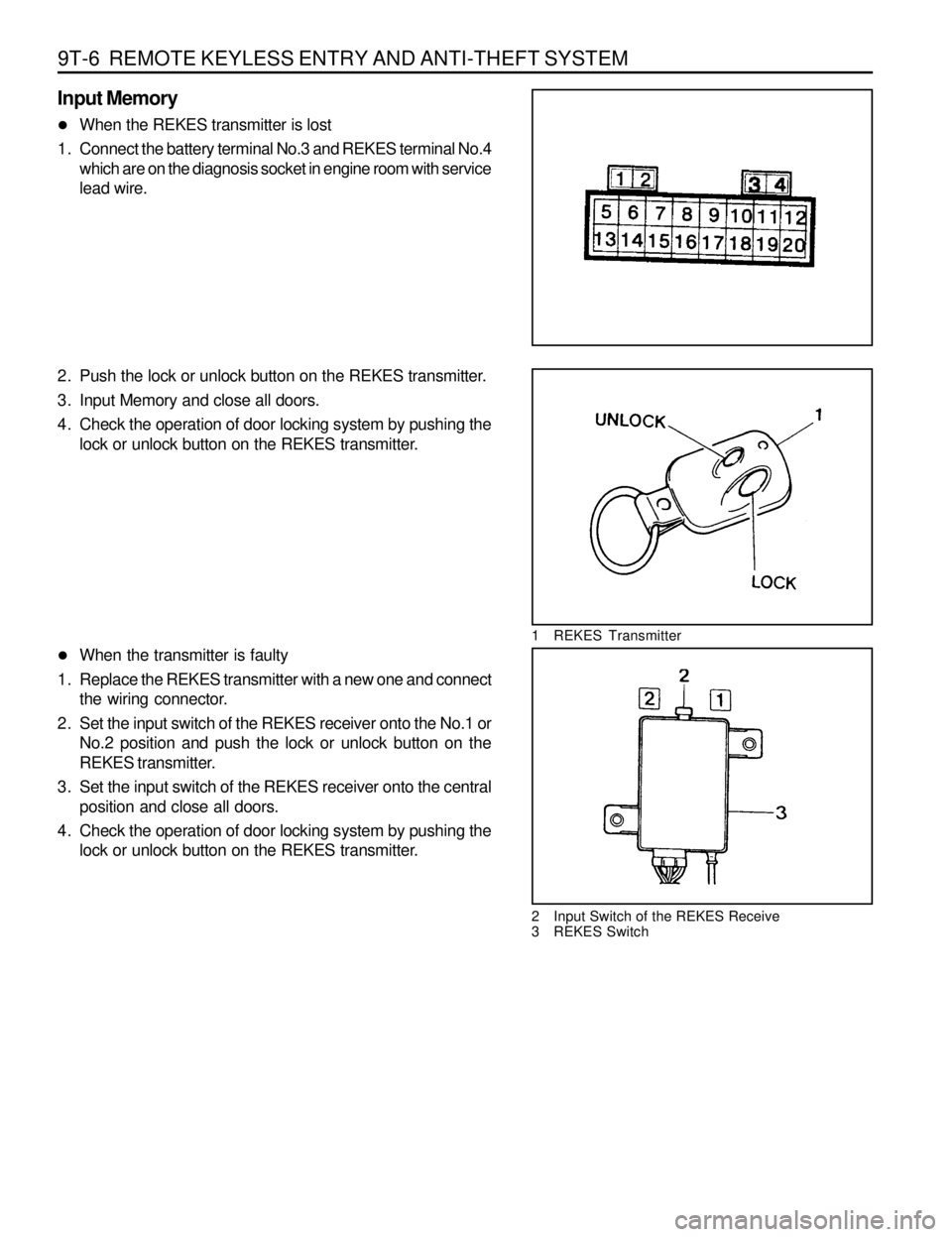
9T-6 REMOTE KEYLESS ENTRY AND ANTI-THEFT SYSTEM
Input Memory
lWhen the REKES transmitter is lost
1. Connect the battery terminal No.3 and REKES terminal No.4
which are on the diagnosis socket in engine room with service
lead wire.
2. Push the lock or unlock button on the REKES transmitter.
3. Input Memory and close all doors.
4. Check the operation of door locking system by pushing the
lock or unlock button on the REKES transmitter.
lWhen the transmitter is faulty
1. Replace the REKES transmitter with a new one and connect
the wiring connector.
2. Set the input switch of the REKES receiver onto the No.1 or
No.2 position and push the lock or unlock button on the
REKES transmitter.
3. Set the input switch of the REKES receiver onto the central
position and close all doors.
4. Check the operation of door locking system by pushing the
lock or unlock button on the REKES transmitter.
1 REKES Transmitter
2 Input Switch of the REKES Receive
3 REKES Switch