SUBARU LEGACY 1999 Service Repair Manual
Manufacturer: SUBARU, Model Year: 1999, Model line: LEGACY, Model: SUBARU LEGACY 1999Pages: 1456, PDF Size: 59.93 MB
Page 681 of 1456
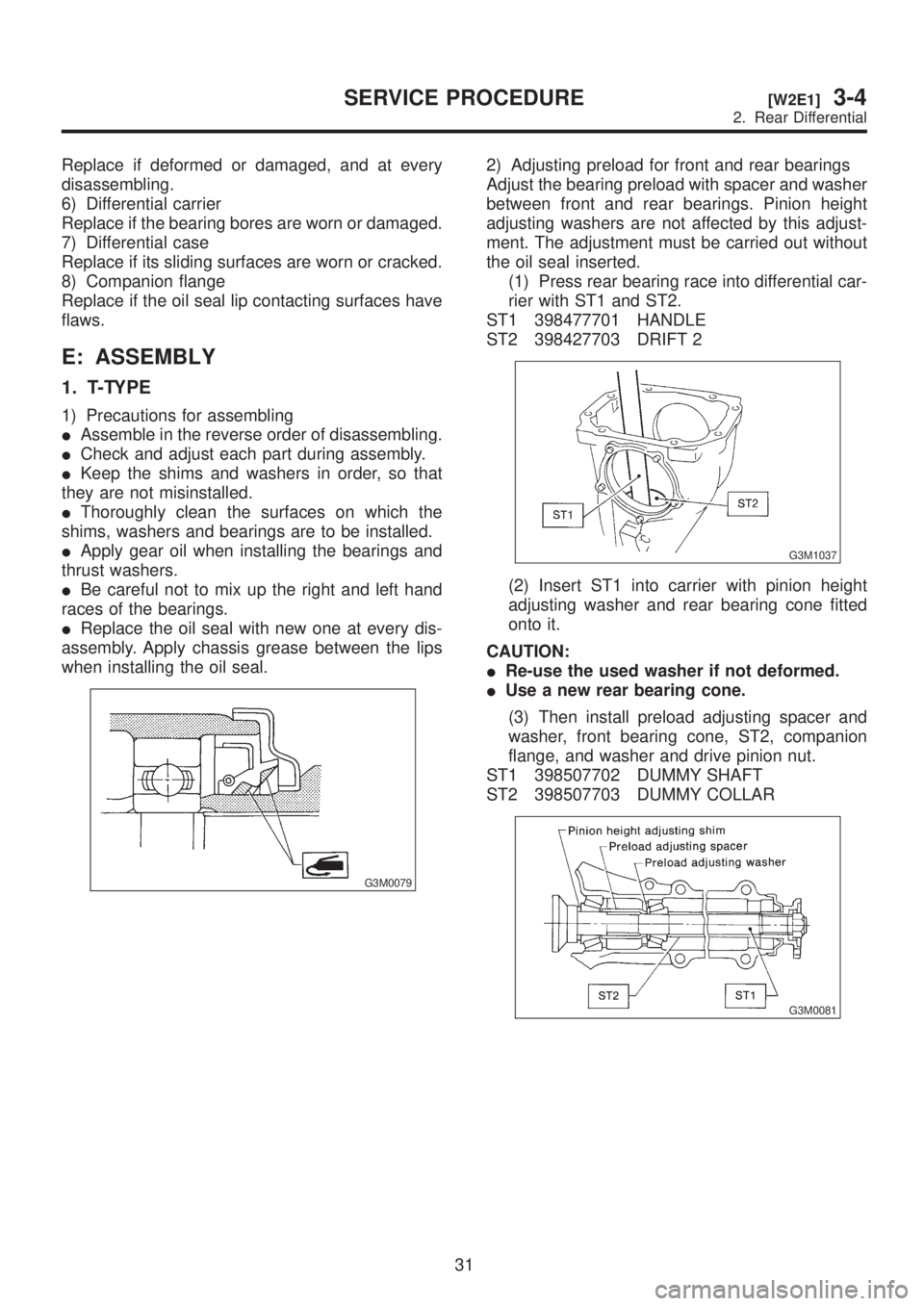
Replace if deformed or damaged, and at every
disassembling.
6) Differential carrier
Replace if the bearing bores are worn or damaged.
7) Differential case
Replace if its sliding surfaces are worn or cracked.
8) Companion flange
Replace if the oil seal lip contacting surfaces have
flaws.
E: ASSEMBLY
1. T-TYPE
1) Precautions for assembling
IAssemble in the reverse order of disassembling.
ICheck and adjust each part during assembly.
IKeep the shims and washers in order, so that
they are not misinstalled.
IThoroughly clean the surfaces on which the
shims, washers and bearings are to be installed.
IApply gear oil when installing the bearings and
thrust washers.
IBe careful not to mix up the right and left hand
races of the bearings.
IReplace the oil seal with new one at every dis-
assembly. Apply chassis grease between the lips
when installing the oil seal.
G3M0079
2) Adjusting preload for front and rear bearings
Adjust the bearing preload with spacer and washer
between front and rear bearings. Pinion height
adjusting washers are not affected by this adjust-
ment. The adjustment must be carried out without
the oil seal inserted.
(1) Press rear bearing race into differential car-
rier with ST1 and ST2.
ST1 398477701 HANDLE
ST2 398427703 DRIFT 2
G3M1037
(2) Insert ST1 into carrier with pinion height
adjusting washer and rear bearing cone fitted
onto it.
CAUTION:
IRe-use the used washer if not deformed.
IUse a new rear bearing cone.
(3) Then install preload adjusting spacer and
washer, front bearing cone, ST2, companion
flange, and washer and drive pinion nut.
ST1 398507702 DUMMY SHAFT
ST2 398507703 DUMMY COLLAR
G3M0081
31
[W2E1]3-4SERVICE PROCEDURE
2. Rear Differential
Page 682 of 1456
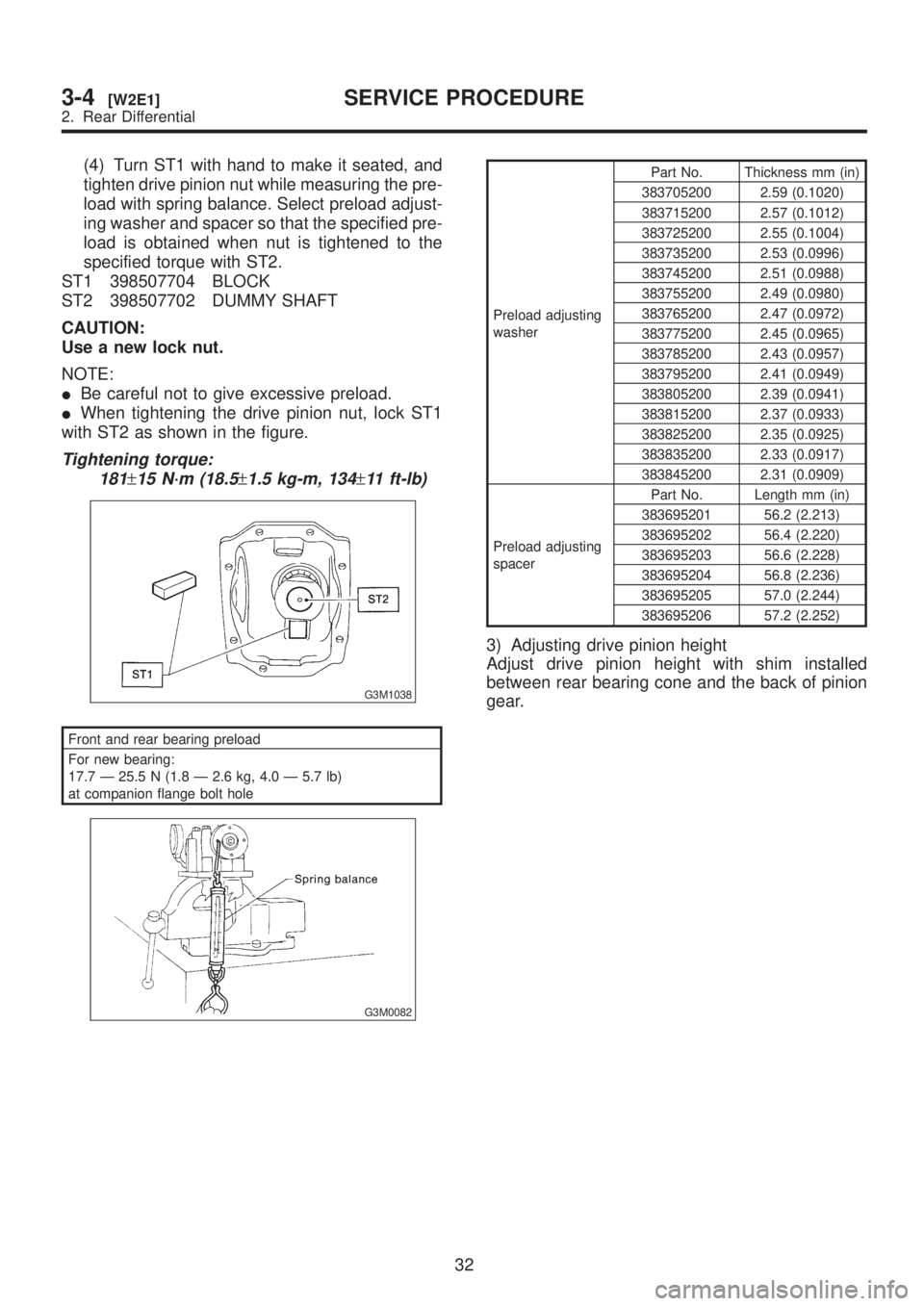
(4) Turn ST1 with hand to make it seated, and
tighten drive pinion nut while measuring the pre-
load with spring balance. Select preload adjust-
ing washer and spacer so that the specified pre-
load is obtained when nut is tightened to the
specified torque with ST2.
ST1 398507704 BLOCK
ST2 398507702 DUMMY SHAFT
CAUTION:
Use a new lock nut.
NOTE:
IBe careful not to give excessive preload.
IWhen tightening the drive pinion nut, lock ST1
with ST2 as shown in the figure.
Tightening torque:
181
±15 N´m (18.5±1.5 kg-m, 134±11 ft-lb)
G3M1038
Front and rear bearing preload
For new bearing:
17.7 Ð 25.5 N (1.8 Ð 2.6 kg, 4.0 Ð 5.7 lb)
at companion flange bolt hole
G3M0082
Preload adjusting
washerPart No. Thickness mm (in)
383705200 2.59 (0.1020)
383715200 2.57 (0.1012)
383725200 2.55 (0.1004)
383735200 2.53 (0.0996)
383745200 2.51 (0.0988)
383755200 2.49 (0.0980)
383765200 2.47 (0.0972)
383775200 2.45 (0.0965)
383785200 2.43 (0.0957)
383795200 2.41 (0.0949)
383805200 2.39 (0.0941)
383815200 2.37 (0.0933)
383825200 2.35 (0.0925)
383835200 2.33 (0.0917)
383845200 2.31 (0.0909)
Preload adjusting
spacerPart No. Length mm (in)
383695201 56.2 (2.213)
383695202 56.4 (2.220)
383695203 56.6 (2.228)
383695204 56.8 (2.236)
383695205 57.0 (2.244)
383695206 57.2 (2.252)
3) Adjusting drive pinion height
Adjust drive pinion height with shim installed
between rear bearing cone and the back of pinion
gear.
32
3-4[W2E1]SERVICE PROCEDURE
2. Rear Differential
Page 683 of 1456
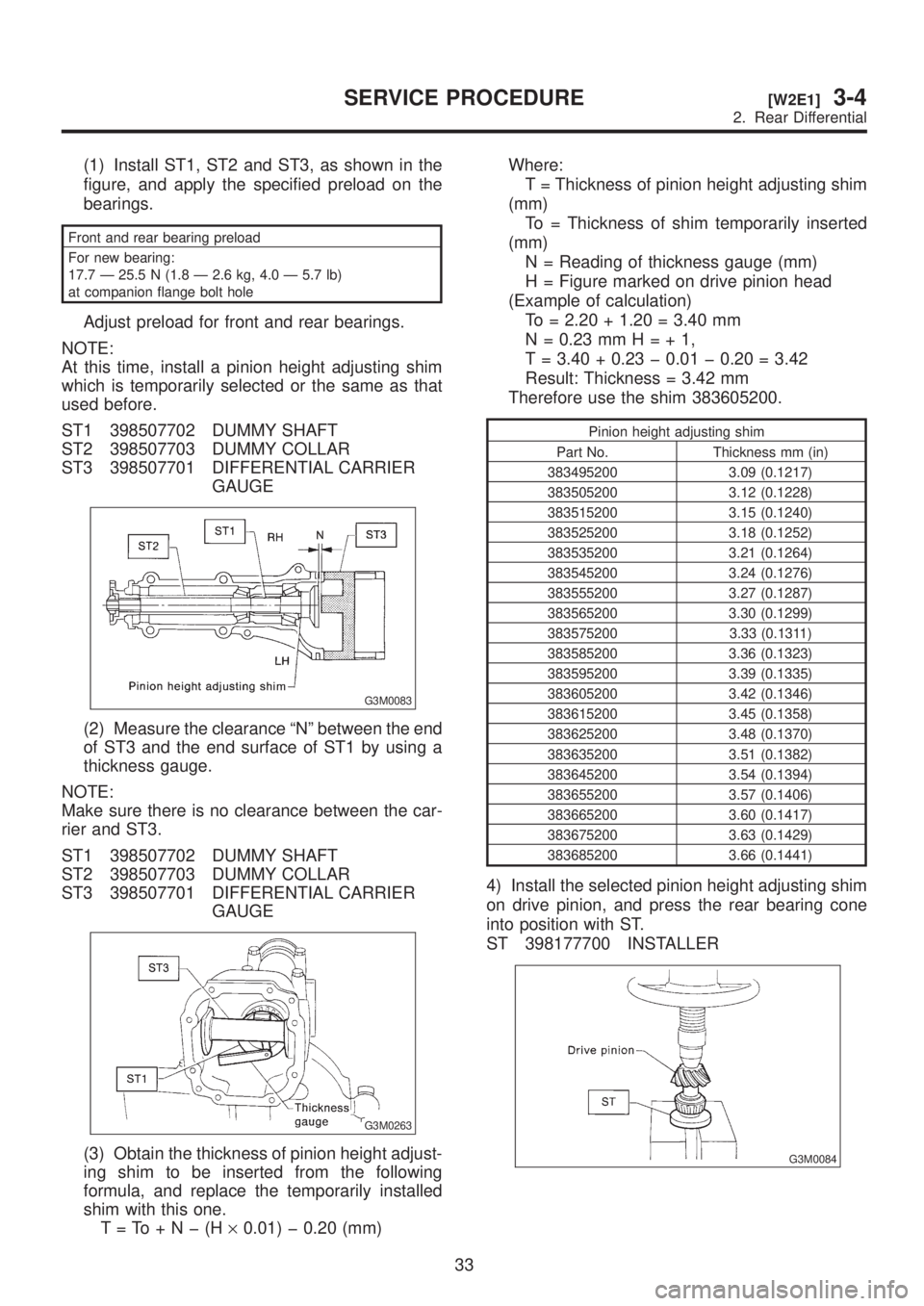
(1) Install ST1, ST2 and ST3, as shown in the
figure, and apply the specified preload on the
bearings.
Front and rear bearing preload
For new bearing:
17.7 Ð 25.5 N (1.8 Ð 2.6 kg, 4.0 Ð 5.7 lb)
at companion flange bolt hole
Adjust preload for front and rear bearings.
NOTE:
At this time, install a pinion height adjusting shim
which is temporarily selected or the same as that
used before.
ST1 398507702 DUMMY SHAFT
ST2 398507703 DUMMY COLLAR
ST3 398507701 DIFFERENTIAL CARRIER
GAUGE
G3M0083
(2) Measure the clearance ªNº between the end
of ST3 and the end surface of ST1 by using a
thickness gauge.
NOTE:
Make sure there is no clearance between the car-
rier and ST3.
ST1 398507702 DUMMY SHAFT
ST2 398507703 DUMMY COLLAR
ST3 398507701 DIFFERENTIAL CARRIER
GAUGE
G3M0263
(3) Obtain the thickness of pinion height adjust-
ing shim to be inserted from the following
formula, and replace the temporarily installed
shim with this one.
T=To+Nþ(H´0.01) þ 0.20 (mm)Where:
T = Thickness of pinion height adjusting shim
(mm)
To = Thickness of shim temporarily inserted
(mm)
N = Reading of thickness gauge (mm)
H = Figure marked on drive pinion head
(Example of calculation)
To = 2.20 + 1.20 = 3.40 mm
N = 0.23 mmH=+1,
T = 3.40 + 0.23 þ 0.01 þ 0.20 = 3.42
Result: Thickness = 3.42 mm
Therefore use the shim 383605200.
Pinion height adjusting shim
Part No. Thickness mm (in)
383495200 3.09 (0.1217)
383505200 3.12 (0.1228)
383515200 3.15 (0.1240)
383525200 3.18 (0.1252)
383535200 3.21 (0.1264)
383545200 3.24 (0.1276)
383555200 3.27 (0.1287)
383565200 3.30 (0.1299)
383575200 3.33 (0.1311)
383585200 3.36 (0.1323)
383595200 3.39 (0.1335)
383605200 3.42 (0.1346)
383615200 3.45 (0.1358)
383625200 3.48 (0.1370)
383635200 3.51 (0.1382)
383645200 3.54 (0.1394)
383655200 3.57 (0.1406)
383665200 3.60 (0.1417)
383675200 3.63 (0.1429)
383685200 3.66 (0.1441)
4) Install the selected pinion height adjusting shim
on drive pinion, and press the rear bearing cone
into position with ST.
ST 398177700 INSTALLER
G3M0084
33
[W2E1]3-4SERVICE PROCEDURE
2. Rear Differential
Page 684 of 1456
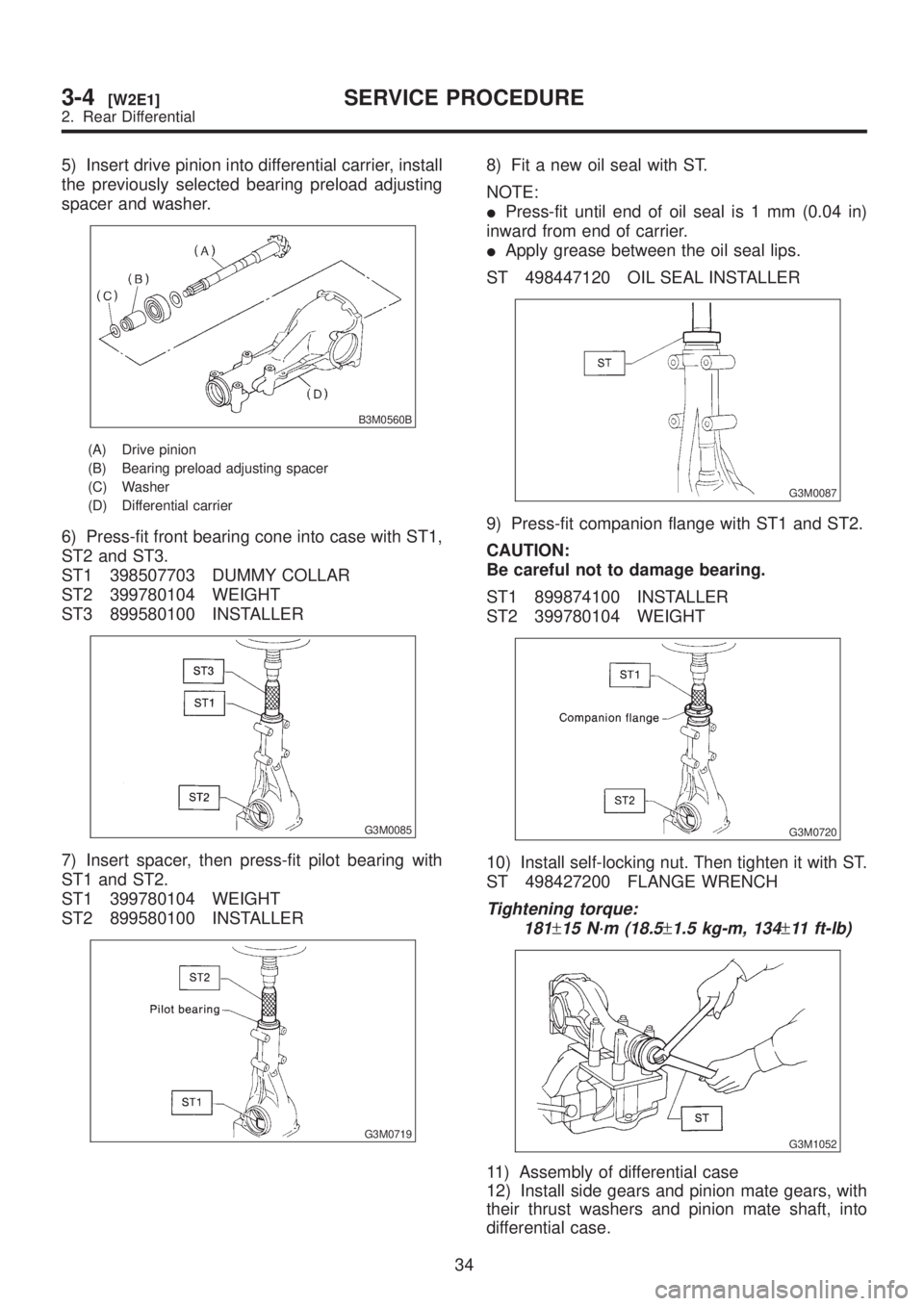
5) Insert drive pinion into differential carrier, install
the previously selected bearing preload adjusting
spacer and washer.
B3M0560B
(A) Drive pinion
(B) Bearing preload adjusting spacer
(C) Washer
(D) Differential carrier
6) Press-fit front bearing cone into case with ST1,
ST2 and ST3.
ST1 398507703 DUMMY COLLAR
ST2 399780104 WEIGHT
ST3 899580100 INSTALLER
G3M0085
7) Insert spacer, then press-fit pilot bearing with
ST1 and ST2.
ST1 399780104 WEIGHT
ST2 899580100 INSTALLER
G3M0719
8) Fit a new oil seal with ST.
NOTE:
IPress-fit until end of oil seal is 1 mm (0.04 in)
inward from end of carrier.
IApply grease between the oil seal lips.
ST 498447120 OIL SEAL INSTALLER
G3M0087
9) Press-fit companion flange with ST1 and ST2.
CAUTION:
Be careful not to damage bearing.
ST1 899874100 INSTALLER
ST2 399780104 WEIGHT
G3M0720
10) Install self-locking nut. Then tighten it with ST.
ST 498427200 FLANGE WRENCH
Tightening torque:
181
±15 N´m (18.5±1.5 kg-m, 134±11 ft-lb)
G3M1052
11) Assembly of differential case
12) Install side gears and pinion mate gears, with
their thrust washers and pinion mate shaft, into
differential case.
34
3-4[W2E1]SERVICE PROCEDURE
2. Rear Differential
Page 685 of 1456
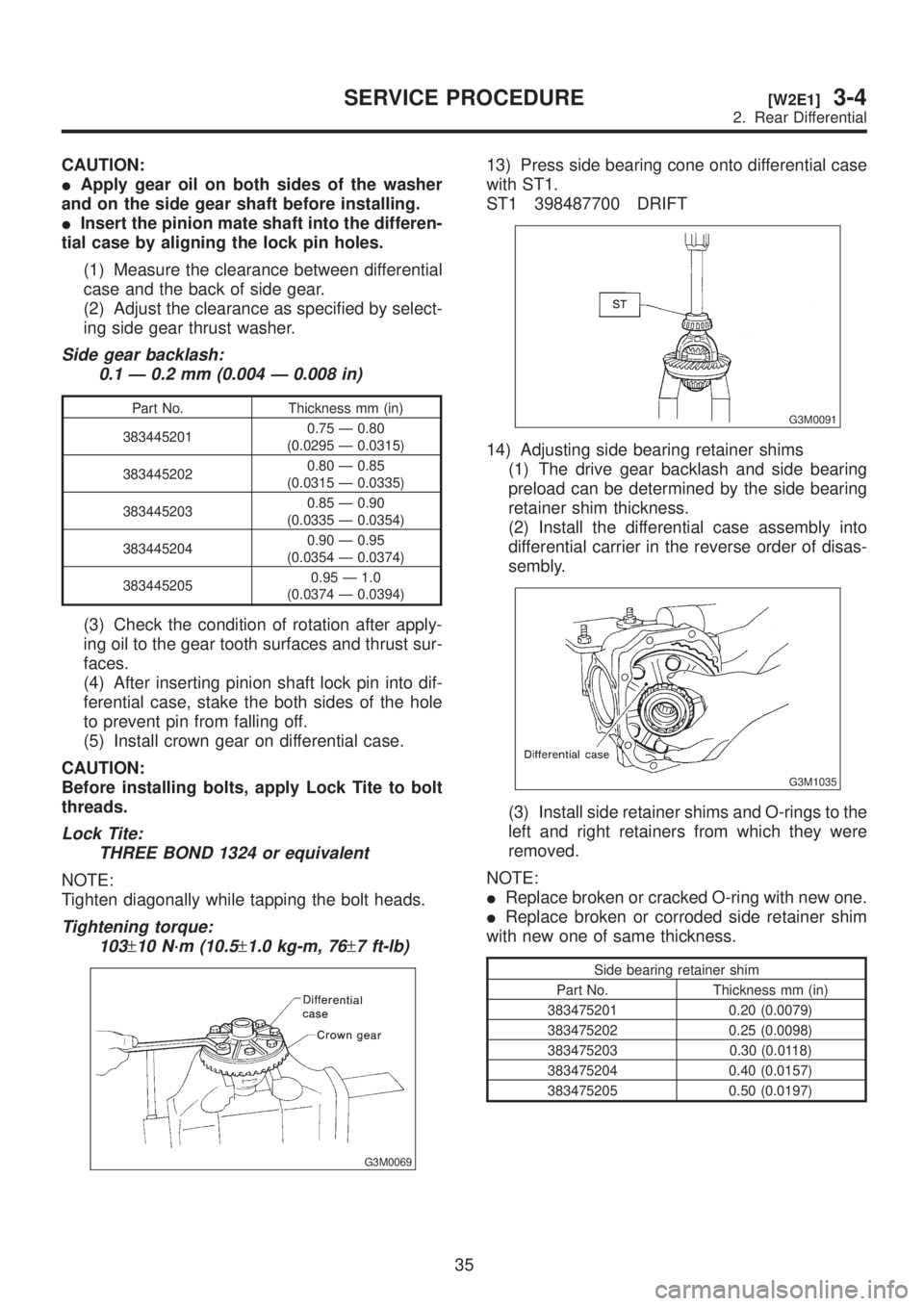
CAUTION:
IApply gear oil on both sides of the washer
and on the side gear shaft before installing.
IInsert the pinion mate shaft into the differen-
tial case by aligning the lock pin holes.
(1) Measure the clearance between differential
case and the back of side gear.
(2) Adjust the clearance as specified by select-
ing side gear thrust washer.
Side gear backlash:
0.1 Ð 0.2 mm (0.004 Ð 0.008 in)
Part No. Thickness mm (in)
3834452010.75 Ð 0.80
(0.0295 Ð 0.0315)
3834452020.80 Ð 0.85
(0.0315 Ð 0.0335)
3834452030.85 Ð 0.90
(0.0335 Ð 0.0354)
3834452040.90 Ð 0.95
(0.0354 Ð 0.0374)
3834452050.95 Ð 1.0
(0.0374 Ð 0.0394)
(3) Check the condition of rotation after apply-
ing oil to the gear tooth surfaces and thrust sur-
faces.
(4) After inserting pinion shaft lock pin into dif-
ferential case, stake the both sides of the hole
to prevent pin from falling off.
(5) Install crown gear on differential case.
CAUTION:
Before installing bolts, apply Lock Tite to bolt
threads.
Lock Tite:
THREE BOND 1324 or equivalent
NOTE:
Tighten diagonally while tapping the bolt heads.
Tightening torque:
103
±10 N´m (10.5±1.0 kg-m, 76±7 ft-lb)
G3M0069
13) Press side bearing cone onto differential case
with ST1.
ST1 398487700 DRIFT
G3M0091
14) Adjusting side bearing retainer shims
(1) The drive gear backlash and side bearing
preload can be determined by the side bearing
retainer shim thickness.
(2) Install the differential case assembly into
differential carrier in the reverse order of disas-
sembly.
G3M1035
(3) Install side retainer shims and O-rings to the
left and right retainers from which they were
removed.
NOTE:
IReplace broken or cracked O-ring with new one.
IReplace broken or corroded side retainer shim
with new one of same thickness.
Side bearing retainer shim
Part No. Thickness mm (in)
383475201 0.20 (0.0079)
383475202 0.25 (0.0098)
383475203 0.30 (0.0118)
383475204 0.40 (0.0157)
383475205 0.50 (0.0197)
35
[W2E1]3-4SERVICE PROCEDURE
2. Rear Differential
Page 686 of 1456
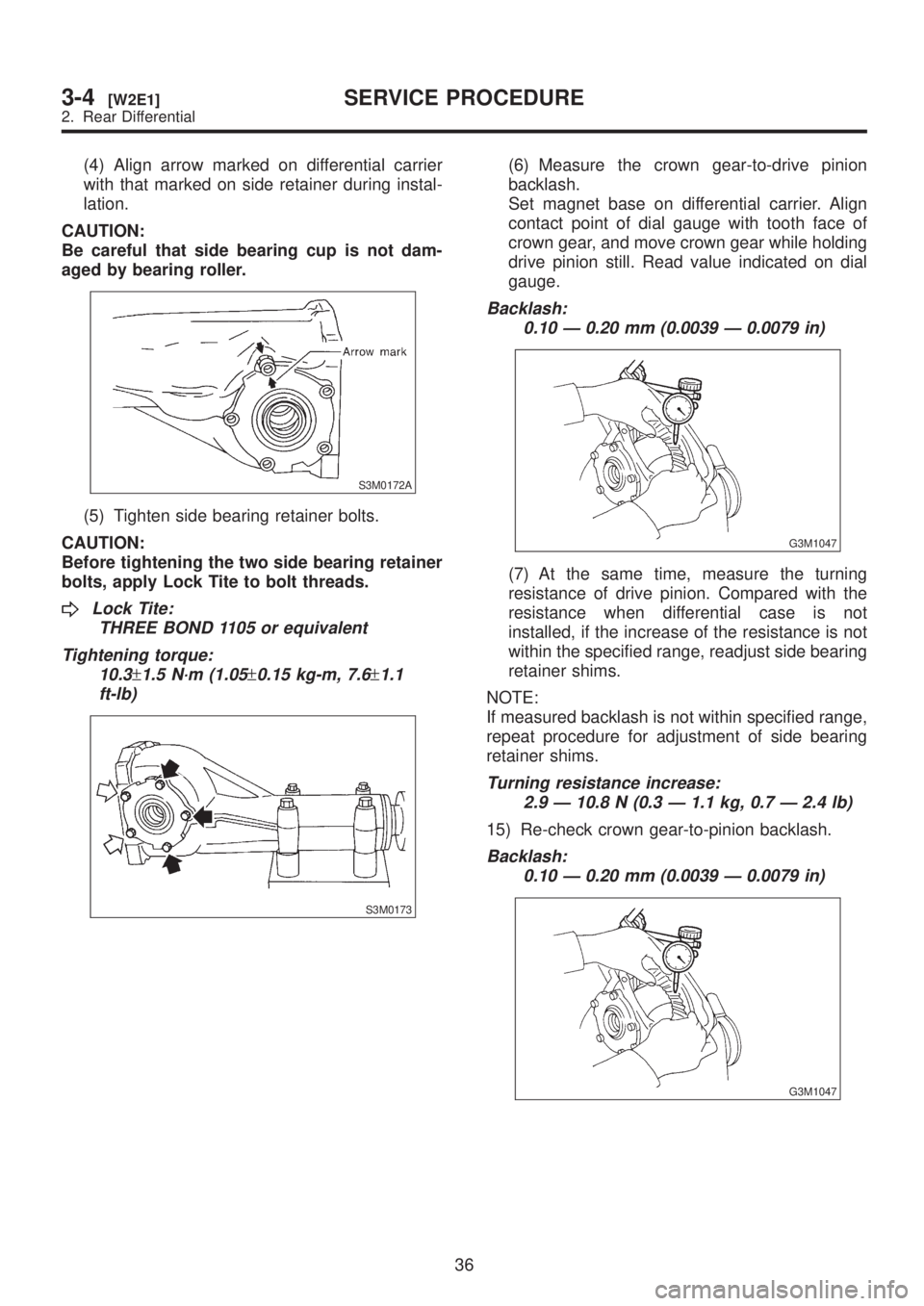
(4) Align arrow marked on differential carrier
with that marked on side retainer during instal-
lation.
CAUTION:
Be careful that side bearing cup is not dam-
aged by bearing roller.
S3M0172A
(5) Tighten side bearing retainer bolts.
CAUTION:
Before tightening the two side bearing retainer
bolts, apply Lock Tite to bolt threads.
Lock Tite:
THREE BOND 1105 or equivalent
Tightening torque:
10.3
±1.5 N´m (1.05±0.15 kg-m, 7.6±1.1
ft-lb)
S3M0173
(6) Measure the crown gear-to-drive pinion
backlash.
Set magnet base on differential carrier. Align
contact point of dial gauge with tooth face of
crown gear, and move crown gear while holding
drive pinion still. Read value indicated on dial
gauge.
Backlash:
0.10 Ð 0.20 mm (0.0039 Ð 0.0079 in)
G3M1047
(7) At the same time, measure the turning
resistance of drive pinion. Compared with the
resistance when differential case is not
installed, if the increase of the resistance is not
within the specified range, readjust side bearing
retainer shims.
NOTE:
If measured backlash is not within specified range,
repeat procedure for adjustment of side bearing
retainer shims.
Turning resistance increase:
2.9 Ð 10.8 N (0.3 Ð 1.1 kg, 0.7 Ð 2.4 lb)
15) Re-check crown gear-to-pinion backlash.
Backlash:
0.10 Ð 0.20 mm (0.0039 Ð 0.0079 in)
G3M1047
36
3-4[W2E1]SERVICE PROCEDURE
2. Rear Differential
Page 687 of 1456
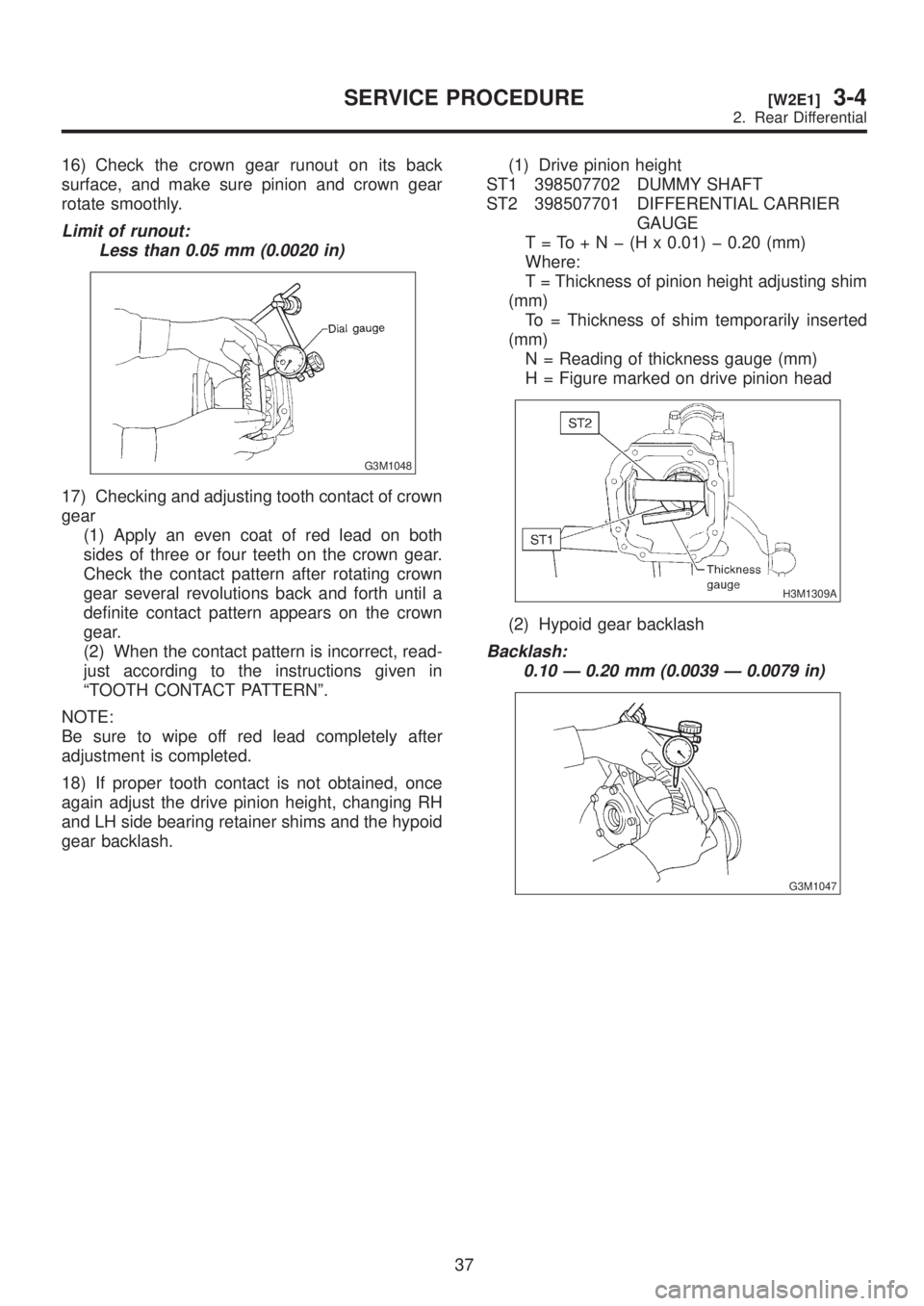
16) Check the crown gear runout on its back
surface, and make sure pinion and crown gear
rotate smoothly.
Limit of runout:
Less than 0.05 mm (0.0020 in)
G3M1048
17) Checking and adjusting tooth contact of crown
gear
(1) Apply an even coat of red lead on both
sides of three or four teeth on the crown gear.
Check the contact pattern after rotating crown
gear several revolutions back and forth until a
definite contact pattern appears on the crown
gear.
(2) When the contact pattern is incorrect, read-
just according to the instructions given in
ªTOOTH CONTACT PATTERNº.
NOTE:
Be sure to wipe off red lead completely after
adjustment is completed.
18) If proper tooth contact is not obtained, once
again adjust the drive pinion height, changing RH
and LH side bearing retainer shims and the hypoid
gear backlash.(1) Drive pinion height
ST1 398507702 DUMMY SHAFT
ST2 398507701 DIFFERENTIAL CARRIER
GAUGE
T=To+Nþ(Hx0.01) þ 0.20 (mm)
Where:
T = Thickness of pinion height adjusting shim
(mm)
To = Thickness of shim temporarily inserted
(mm)
N = Reading of thickness gauge (mm)
H = Figure marked on drive pinion head
H3M1309A
(2) Hypoid gear backlash
Backlash:
0.10 Ð 0.20 mm (0.0039 Ð 0.0079 in)
G3M1047
37
[W2E1]3-4SERVICE PROCEDURE
2. Rear Differential
Page 688 of 1456
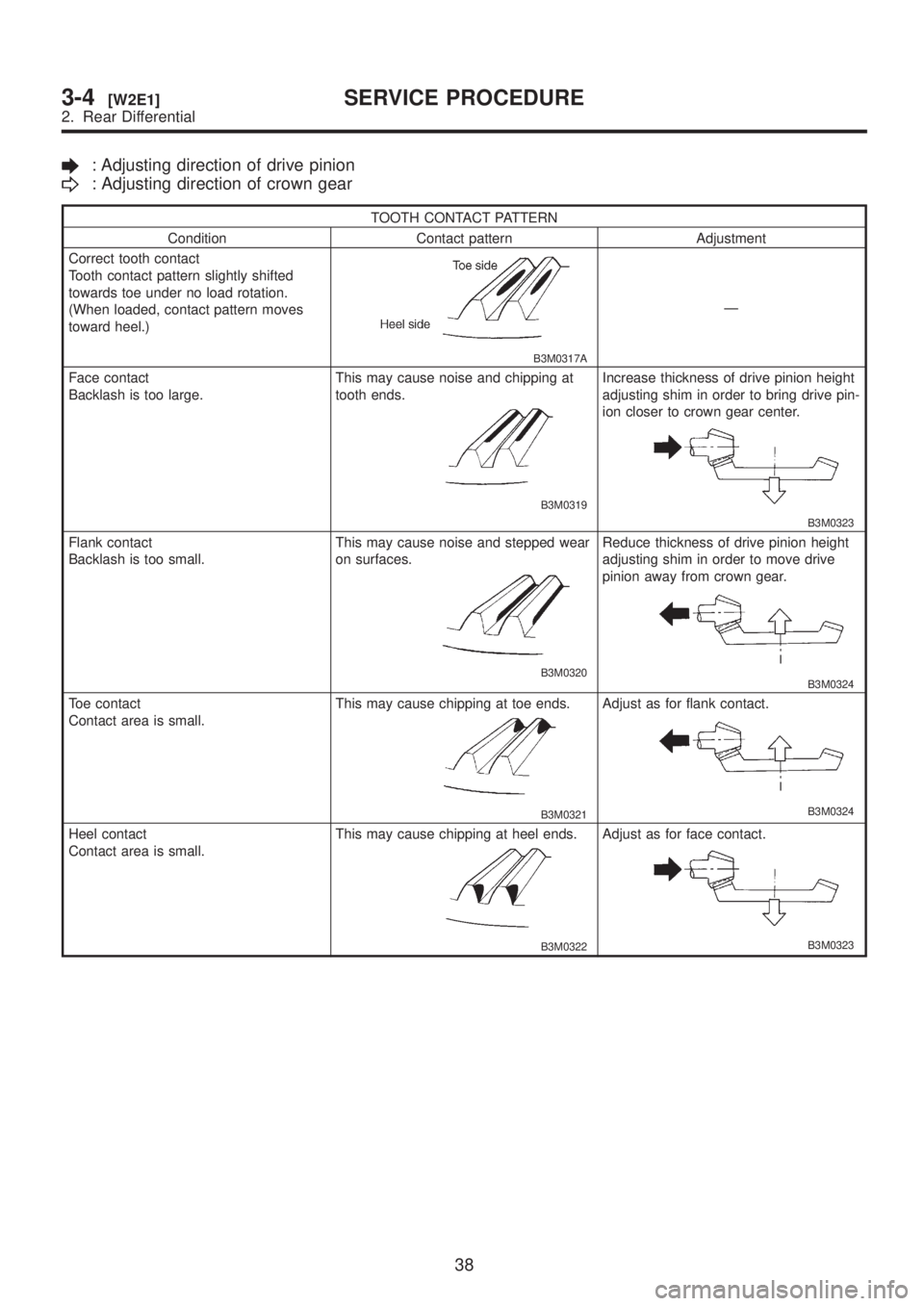
: Adjusting direction of drive pinion
: Adjusting direction of crown gear
TOOTH CONTACT PATTERN
Condition Contact pattern Adjustment
Correct tooth contact
Tooth contact pattern slightly shifted
towards toe under no load rotation.
(When loaded, contact pattern moves
toward heel.)
B3M0317A
Ð
Face contact
Backlash is too large.This may cause noise and chipping at
tooth ends.
B3M0319
Increase thickness of drive pinion height
adjusting shim in order to bring drive pin-
ion closer to crown gear center.
B3M0323
Flank contact
Backlash is too small.This may cause noise and stepped wear
on surfaces.
B3M0320
Reduce thickness of drive pinion height
adjusting shim in order to move drive
pinion away from crown gear.
B3M0324
Toe contact
Contact area is small.This may cause chipping at toe ends.
B3M0321
Adjust as for flank contact.
B3M0324
Heel contact
Contact area is small.This may cause chipping at heel ends.
B3M0322
Adjust as for face contact.
B3M0323
38
3-4[W2E1]SERVICE PROCEDURE
2. Rear Differential
Page 689 of 1456
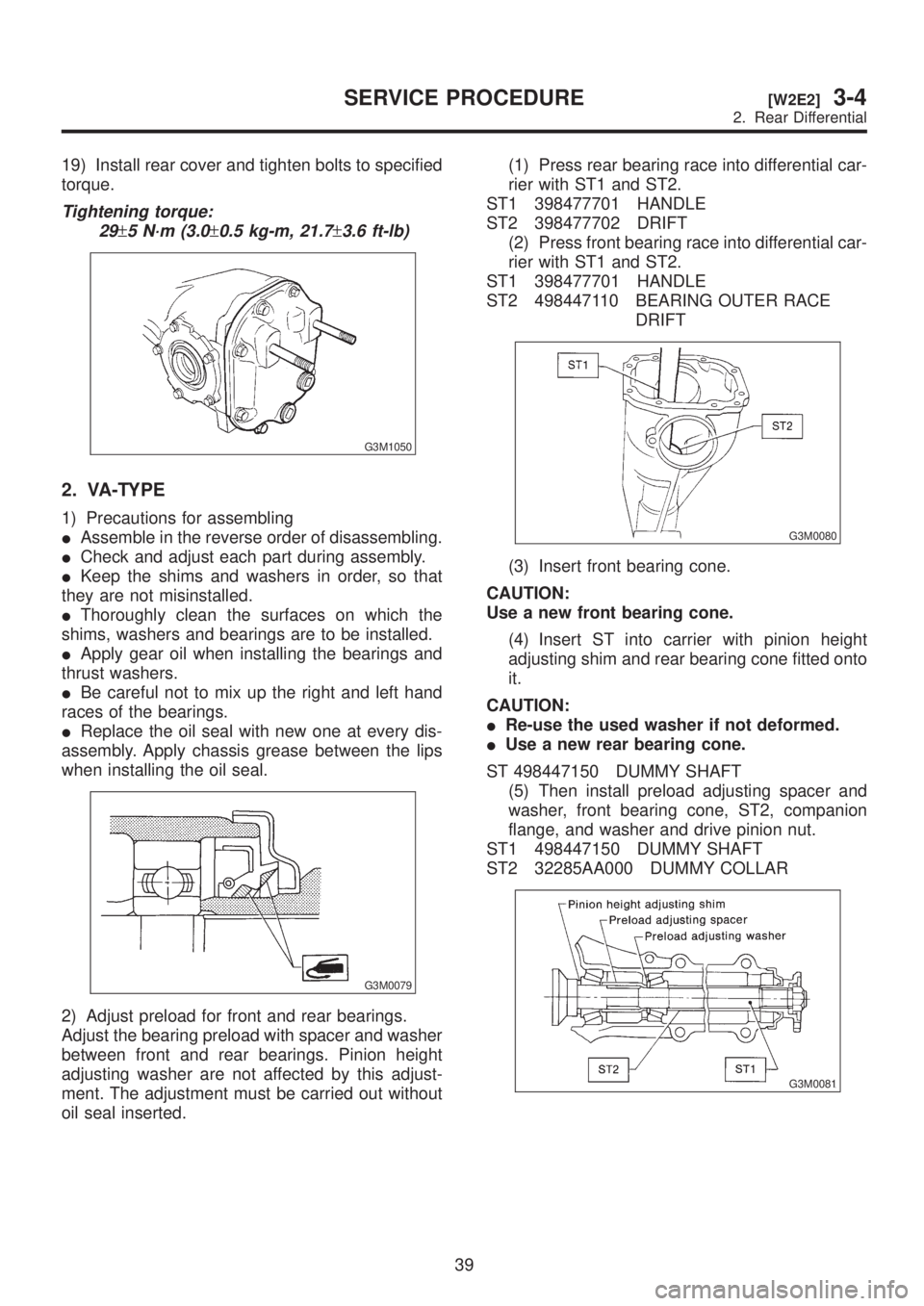
19) Install rear cover and tighten bolts to specified
torque.
Tightening torque:
29
±5 N´m (3.0±0.5 kg-m, 21.7±3.6 ft-lb)
G3M1050
2. VA-TYPE
1) Precautions for assembling
IAssemble in the reverse order of disassembling.
ICheck and adjust each part during assembly.
IKeep the shims and washers in order, so that
they are not misinstalled.
IThoroughly clean the surfaces on which the
shims, washers and bearings are to be installed.
IApply gear oil when installing the bearings and
thrust washers.
IBe careful not to mix up the right and left hand
races of the bearings.
IReplace the oil seal with new one at every dis-
assembly. Apply chassis grease between the lips
when installing the oil seal.
G3M0079
2) Adjust preload for front and rear bearings.
Adjust the bearing preload with spacer and washer
between front and rear bearings. Pinion height
adjusting washer are not affected by this adjust-
ment. The adjustment must be carried out without
oil seal inserted.(1) Press rear bearing race into differential car-
rier with ST1 and ST2.
ST1 398477701 HANDLE
ST2 398477702 DRIFT
(2) Press front bearing race into differential car-
rier with ST1 and ST2.
ST1 398477701 HANDLE
ST2 498447110 BEARING OUTER RACE
DRIFT
G3M0080
(3) Insert front bearing cone.
CAUTION:
Use a new front bearing cone.
(4) Insert ST into carrier with pinion height
adjusting shim and rear bearing cone fitted onto
it.
CAUTION:
IRe-use the used washer if not deformed.
IUse a new rear bearing cone.
ST 498447150 DUMMY SHAFT
(5) Then install preload adjusting spacer and
washer, front bearing cone, ST2, companion
flange, and washer and drive pinion nut.
ST1 498447150 DUMMY SHAFT
ST2 32285AA000 DUMMY COLLAR
G3M0081
39
[W2E2]3-4SERVICE PROCEDURE
2. Rear Differential
Page 690 of 1456
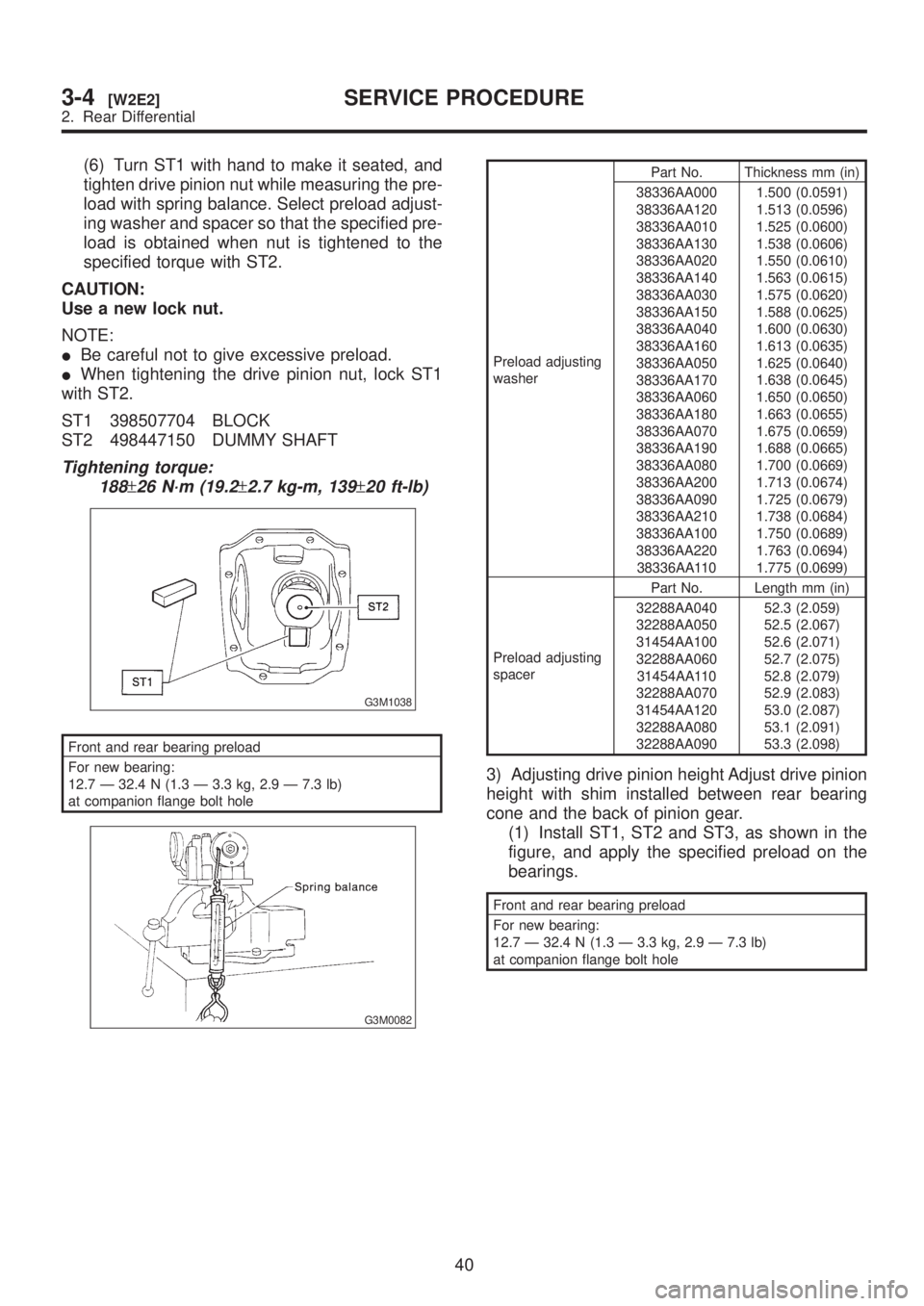
(6) Turn ST1 with hand to make it seated, and
tighten drive pinion nut while measuring the pre-
load with spring balance. Select preload adjust-
ing washer and spacer so that the specified pre-
load is obtained when nut is tightened to the
specified torque with ST2.
CAUTION:
Use a new lock nut.
NOTE:
IBe careful not to give excessive preload.
IWhen tightening the drive pinion nut, lock ST1
with ST2.
ST1 398507704 BLOCK
ST2 498447150 DUMMY SHAFT
Tightening torque:
188
±26 N´m (19.2±2.7 kg-m, 139±20 ft-lb)
G3M1038
Front and rear bearing preload
For new bearing:
12.7 Ð 32.4 N (1.3 Ð 3.3 kg, 2.9 Ð 7.3 lb)
at companion flange bolt hole
G3M0082
Preload adjusting
washerPart No. Thickness mm (in)
38336AA000
38336AA120
38336AA010
38336AA130
38336AA020
38336AA140
38336AA030
38336AA150
38336AA040
38336AA160
38336AA050
38336AA170
38336AA060
38336AA180
38336AA070
38336AA190
38336AA080
38336AA200
38336AA090
38336AA210
38336AA100
38336AA220
38336AA1101.500 (0.0591)
1.513 (0.0596)
1.525 (0.0600)
1.538 (0.0606)
1.550 (0.0610)
1.563 (0.0615)
1.575 (0.0620)
1.588 (0.0625)
1.600 (0.0630)
1.613 (0.0635)
1.625 (0.0640)
1.638 (0.0645)
1.650 (0.0650)
1.663 (0.0655)
1.675 (0.0659)
1.688 (0.0665)
1.700 (0.0669)
1.713 (0.0674)
1.725 (0.0679)
1.738 (0.0684)
1.750 (0.0689)
1.763 (0.0694)
1.775 (0.0699)
Preload adjusting
spacerPart No. Length mm (in)
32288AA040
32288AA050
31454AA100
32288AA060
31454AA110
32288AA070
31454AA120
32288AA080
32288AA09052.3 (2.059)
52.5 (2.067)
52.6 (2.071)
52.7 (2.075)
52.8 (2.079)
52.9 (2.083)
53.0 (2.087)
53.1 (2.091)
53.3 (2.098)
3) Adjusting drive pinion height Adjust drive pinion
height with shim installed between rear bearing
cone and the back of pinion gear.
(1) Install ST1, ST2 and ST3, as shown in the
figure, and apply the specified preload on the
bearings.
Front and rear bearing preload
For new bearing:
12.7 Ð 32.4 N (1.3 Ð 3.3 kg, 2.9 Ð 7.3 lb)
at companion flange bolt hole
40
3-4[W2E2]SERVICE PROCEDURE
2. Rear Differential